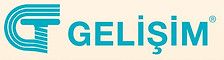


Hydrocarbons
It is an organic compound consisting of two elements, hydrogen and carbon. Most of the petroleum composition consists of hydrocarbons of varying lengths.
The smallest hydrocarbon methane consists of a single carbon atom and four hydrogen atoms. However, hydrocarbons can consist of hundreds or thousands of individual atoms linked together in many ways, including chains, circles, and other complex shapes.
In order to classify the properties of hydrocarbons, they are divided into several basic types.
Alkanes: These are called saturated hydrocarbons. That is, they only contain single bonds between all carbon atoms. Alkanes are the basis of petroleum fuels and exist in linear and branched forms.
Unsaturated Hydrocarbons: Hydrocarbons that have one or more double bonds between carbon atoms are called alkenes.
Cycloalkanes: Any hydrocarbon containing one or more ring structures.
Aromatic Hydrocarbons: Aromatic hydrocarbons , also called arenes, are a unique class of carbon molecules in which carbon atoms are bonded by successive double and single bonds. This class of molecules has special ring structures in which the bonds between carbon atoms are an intermediate bond between single and double bonds.
Molecules in this class contain the industrial solvent "benzene".
Benzene (C6H6): Like other hydrocarbons, benzene is a natural component of petroleum. It is a colorless, flammable, sweet-smelling liquid at room temperature and is a component of most gasoline blends because of its high octane number.
Benzene is also highly carcinogenic and is well known to cause bone marrow failure and bone cancer. Of course, its carcinogenicity is not well known when used as an additive in aftershave and other cosmetics due to its "pleasant aroma".
The largest use of benzene (50%) is the product of styrene and polystyrene plastics. It is also converted into a molecule known as cyclohexane, which is important in Nylon production. About 15% of benzene is used to produce cyclohexane. Smaller amounts are used in everything from pesticides to rubber.
The benzene structure can be drawn in two ways. In the first, the double bond character is drawn explicitly. In the short handed version, a circle is drawn inside the ring to show the structure. There is only one hydrogen bonded to each carbon atom in benzene.
I. and II below. drawings are identical. III in practice. drawing is used.
Benzene is a colorless, flammable liquid with a boiling point of 80.1 ° C and a melting point of 5.5 ° C.
Binuclear Aromatic Hydrocarbons: They are compounds that contain two benzene rings in their molecules.
Hydrocarbons
It is an organic compound consisting of two elements, hydrogen and carbon. Most of the petroleum composition consists of hydrocarbons of varying lengths.
The smallest hydrocarbon methane consists of a single carbon atom and four hydrogen atoms. However, hydrocarbons can consist of hundreds or thousands of individual atoms linked together in many ways, including chains, circles, and other complex shapes.
In order to classify the properties of hydrocarbons, they are divided into several basic types.
Alkanes: These are called saturated hydrocarbons. That is, they only contain single bonds between all carbon atoms. Alkanes are the basis of petroleum fuels and exist in linear and branched forms.
Unsaturated Hydrocarbons: Hydrocarbons that have one or more double bonds between carbon atoms are called alkenes.
Cycloalkanes: Any hydrocarbon containing one or more ring structures.
Aromatic Hydrocarbons: Aromatic hydrocarbons , also called arenes, are a unique class of carbon molecules in which carbon atoms are bonded by successive double and single bonds. This class of molecules has special ring structures in which the bonds between carbon atoms are an intermediate bond between single and double bonds.
Molecules in this class contain the industrial solvent "benzene".
Benzene (C6H6): Like other hydrocarbons, benzene is a natural component of petroleum. It is a colorless, flammable, sweet-smelling liquid at room temperature and is a component of most gasoline blends because of its high octane number.
Benzene is also highly carcinogenic and is well known to cause bone marrow failure and bone cancer. Of course, its carcinogenicity is not well known when used as an additive in aftershave and other cosmetics due to its "pleasant aroma".
The largest use of benzene (50%) is the product of styrene and polystyrene plastics. It is also converted into a molecule known as cyclohexane, which is important in Nylon production. About 15% of benzene is used to produce cyclohexane. Smaller amounts are used in everything from pesticides to rubber.
The benzene structure can be drawn in two ways. In the first, the double bond character is drawn explicitly. In the short handed version, a circle is drawn inside the ring to show the structure. There is only one hydrogen bonded to each carbon atom in benzene.
I. and II below. drawings are identical. III in practice. drawing is used.
Benzene is a colorless, flammable liquid with a boiling point of 80.1 ° C and a melting point of 5.5 ° C.
Binuclear Aromatic Hydrocarbons: They are compounds that contain two benzene rings in their molecules.
About
Kyäni, nutritional supplement products consisting of beneficial ingredients; It delivers to more than 50 countries around the world with unique business opportunities. We use Kyäni products daily to maintain our ideal health, share these products with others, devote a certain amount of time to work almost every day to build and maintain our business, and share our success with others by involving others in the Kyäni opportunity or contributing to the Potato Pak and Caring Hands programs.
About
Kyäni, nutritional supplement products consisting of beneficial ingredients; It delivers to more than 50 countries around the world with unique business opportunities. We use Kyäni products daily to maintain our ideal health, share these products with others, devote a certain amount of time to work almost every day to build and maintain our business, and share our success with others by involving others in the Kyäni opportunity or contributing to the Potato Pak and Caring Hands programs.
Page Under Construction.
Page Under Construction.
Training / Knowledge / Solution Platform
Compatibility in Raw Materials
The selection of raw materials suitable for the appropriate product is essential in product processing. Check whether you are using the appropriate raw material for processing.
One of the factors affecting product properties is additives. These substances can affect the color of the product, ease of processing, UV resistance, ease of processing, etc. affect its properties. If you encounter product features that do not comply with these specifications during processing, inform the unit related to the mixture and ensure that the problem is resolved.
In order for some raw materials to be processed, the raw material must have a physical structure suitable for processing. This structure of the raw material affects the homogeneity and plasticization of the raw material due to its movement in the screw. Some plastic mixtures can be processed as powder, some as granules or broken. Select the structure of the raw material you use in accordance with the processing.
During the preparation of raw materials, raw materials with different properties or foreign materials whose structure we do not know can be mixed into the raw material. This situation usually occurs in the form of mixing of different materials in the crusher during the crushing of previously processed raw materials. In order to avoid this situation, make sure that the machines and environments where the material mixture is made are free of foreign materials and cleaned. In order to obtain a product with the desired properties, a homogeneous structure should be obtained in the mixture of raw materials and additives. While preparing the mixture, make sure that the raw materials and additives are thoroughly mixed and a homogeneous structure is obtained. The humidity of the raw material is one of the important factors that negatively affect the processing of the product.
The raw material must be subjected to drying before processing.
Technical values of raw materials such as thermal, mechanical and physical may differ in different batches within the same raw material type.
For example, Petkim G 03-5 is an LDPE. Working and MFI of this raw material The values of G 03-21T, another batch of the same species, differ.
The values in the concordance tables include the average range of values. Accordingly, there may be differences between batches in raw material compatibility. The most important considerations when evaluating a raw material that is equivalent or compatible with a raw material used starts with checking whether it is in the same polymeric class. It is evaluated whether the process temperatures are appropriate.
The primary criterion to be evaluated after these preliminary checks is the suitability of the MFI value. For more detailed comparisons, softening heat values and densities should be matched. It should not be forgotten that; The most suitable raw material is itself, and even the lot differences among themselves may not give the same compatibility result in one-to-one matches.
Agreed compatibilities are practically non-existent for detecting obvious problems. There are quality control processes to determine many properties of raw materials such as degradation values, resistance to friction, resistance to strength.
Test Standards Applied to Raw Materials
Thermoplastic raw material and product Some of the standards applied in quality controls are:
Melt Flow Index (MFI):
(ISO 1133) It is done with the aim of examining the behavior of the material against temperature before it is processed. The piece obtained as a result of the test is weighed and the unit result of gr/10 min is obtained. This criterion criterion, which appears as the melt flow index, is one of the most basic values to be considered in the preparation of polymeric materials. It is a measurement-control practice and value frequently used in the plastics industry for the quality control of thermoplastics.
A small sample of about 5 grams is heated above its melting or softening point and forced to flow through a thin channel using a piston moved with a specific weight, usually 2.16 kg or 5 kg.
The weight, in grams, of the melt flowing through the capillary in 10 minutes is the melt flow index. With the MFI test, the behavior of the raw material in the process is simulated and suitability or non-compliance is determined in advance.
All Thermoplastics are Macromolecular polymer materials.
Mer in Latin means unit. Polymer means multi-unit. Polymers are made up of Monomers (single units). As the number of monomers increases, the molecular weight increases.
As the molecular weight increases:
Mechanical values increase. Fluidity decreases. (So viscosity - resistance to flow - increases)
The amount of flow of a molten thermoplastic under a certain temperature and load in a certain period of time . (grams / 10 minutes)
As MFI increases:
Viscosity decreases. Mechanical values decrease. Generally High MFI materials are used in injection, low MFI materials are used in extrusion.

Color Measurement and Light Fastness
(lab) For thermoplastic elastomers, these values are measured with colorimetric devices and comparisons are made between colors.
(l) value: lightness and darkness
(a) value: red (+) and green (-)
Value (b): gives yellowness (+) and blue (-).
Light fastness or color fastness to light tests are performed to determine the resistance of printed or pigmented textiles to fading or discoloration due to exposure to sunlight or an artificial light source.
The light fastness of the print depends heavily on the type of pigment used. Prints with high exposure to sunlight, such as banners and compost packaging, require a high degree of lightfastness.
Advanced laboratories typically perform print fading and lightfastness tests of paper, print, and pigmented plastics using a xenon arc lamp source and a tester. Light fastness tests are performed using filtered xenon arc lamps, which more closely simulate sunlight than other artificial light sources. They are the best suited tools for assessing accelerated light aging of pigments, dyes and inks sensitive to the visible wavelengths of sunlight. By installing suitable filters, direct sunlight lighting conditions are recreated in the laboratory environment.
The International Standards Organization (ISO) has published ISO 105-B02 and ISO 105-B06 standards, which should be applied in light fastness tests, and has announced a test method. These standards have also been published in our country by the Turkish Standards Institute (TSE) with the following titles:
TS EN ISO 105-B02 Textile - Color fastness tests - Part B02: Determination of color fastness to artificial light - Xenon arc fading lamp test
TS EN ISO 105-B06 Textile - Color fastness tests - Part B06: Aging with artificial light at high temperature and color fastness - Fading test with xenon arc lamp.
Color Stability Tests:
The color characteristics of a lamp can change over time over the lifetime of these lamps, even if they are produced with consistent color temperatures. Color stability or color stability is explained as the ability of a light source to maintain color properties over time. Changes in lighting color characteristics and color shift over time are considered a malfunction. Color shift or change is when there is a significant change in the spectral output of a light source. This causes a change in color temperature and color rendering properties. Color change may be permanent due to operating conditions or as a result of physical changes in packaging. In the event of a permanent and significant color shift, i.e. deterioration of color stability, this is considered an error, since the specifications guaranteed by the manufacturer have no longer been complied with.
Color stability varies according to the place and form of application. For example, while it is extremely important in a museum or exhibition hall lighting, it is acceptable to a certain extent in street lighting. Color balance is also extremely important in a hospital or food production facility.
The main reasons that impair color stability are packaging materials, fixture structure and application errors. The packaging materials used in the packaging of the luminaires and their production methods damage the color stability over time. Likewise, the silicones or plastics used to mount the fixtures also affect the color change of the product. In addition, the environment in which the luminaire is used also has an effect on color stability.
Gloss Measurement:
(ASTM D 523) The aim is to measure the surface gloss of thermoplastic elastomers. Luster is a measure of how reflective a material is at an angle determined based on its refractive index. A special device is used to make these measurements. The gloss meter sends an incandescent light at an angle to the test surface and measures the reflection of this light with a receiver. These tests use a polished black glass with a refractive index of 1.567 as standard. This glass gives full shine. Bright readings can only be compared between similar materials and test procedures. For example, gloss values for transparent and opaque materials are not compared. The gloss value varies with smoothness and flatness.
A viewing angle of 20 degrees is used to evaluate high-gloss films, a 45-degree angle is used for medium-gloss films, and an angle of 60 or more is used for low-gloss films.
The following standards are taken into account in these tests and analyzes:
TS EN ISO 2813 Paints and varnishes - Determination of gloss of non-metallic paint films at 20, 60 and 85 angles
ASTM D523-14 (2018) Standard test method for specular gloss
ASTM D2457-03 Standard test method for specific gloss of plastic films and solid plastics
ASTM C346-87(2018) Standard test method for specular gloss of 45 degree ceramic materials
BS 2782-5: Method 520A: 1992 Plastic test methods - Optical and color properties, separation - Determination of specular gloss
All of these standards describe a method for measuring the gloss of opaque and clear plastic films and solid plastics at 20, 45, 60 and 75 degrees.
Color Catalog Values and Equivalents:
The equivalents (or closest equivalents) of some colors in the color system catalogs are as follows.

Viscosity
Viscosity is a measure of a fluid's resistance to deformation under surface tension. It can also be defined as the internal resistance of the fluid to flow. All real fluids, except superfluids, resist surface tension. On the other hand, a fluid that has no resistance to surface tension is called an "ideal fluid".
Viscosity A property that slows the flow of a substance. It is a property used to characterize liquid fuels, lubricating oils, paints and many other substances. The opposite of viscosity is also called fluidity. As the viscosity increases, the fluidity decreases.
Viscosity A property that slows the flow of a substance. It is a property used to characterize liquid fuels, lubricating oils, paints and many other substances. The opposite of viscosity is also called fluidity. As the viscosity increases, the fluidity decreases.
Temperature Effect on Viscosity:
The viscosity of most liquids decreases with increasing temperature. According to the hole theory, there are voids in a liquid and the molecules are constantly moving towards the voids. This allows for flow, but moving a molecule into a space requires energy because it needs an activation energy. Since the activation energy is more easily supplied at high temperatures, the liquid flows more easily as the temperature rises.
Effect of Pressure on Viscosity:
On the other hand, with increasing pressure, the viscosity of a liquid increases because increasing the pressure reduces the number of voids in the liquid, and as a result, the movement of molecules becomes more difficult.
DIN Cup 4/DIN CUP 4:
DIN 4mm Standard and Immersion Viscosity Cups It complies with DIN 53211 standard and is suitable for low viscosity liquids. Fixed hole diameter 4 mm. These dip cups are used in the simplest method of measuring viscous.
Ford Cups/Ford Cups :
It is designed in accordance with ASTM D1200, D333 and D365 International Standards. It is used to easily measure the viscosity of paint, ink, lacquer and other liquids. Fixed hole diameters 2.3,4.5 mm
Zahn Cups/Zahn Cups:
It can be used to quickly measure the viscosity of liquids such as Paint, Ink, Varnishes, Syrup and Oil. They are produced according to ASTM D 816, ASTM D 1084 and ASM D 4212.
ISO Flow Cups/ISO Flow Cups:
International Standard ISO 2431, DIN 53224, EN 535; Conforms to ASTM D5125 Paints and varnishes - Used to determine flow time using flow cups.
Kinematic Viscous Test:
Viscosities of liquids or dissolved solids are measured.
Mooney Viscous Test:
(ASTM D1646) The Mooney viscosity value of the rubber is measured.
Ash Determination
Ash test is performed to determine whether a material is saturated or not. With this test, the total filler content of the material is defined. When performing this test, a known amount of sample is taken, weighed and placed in a dried and pre-weighed porcelain crucible. The polymer is burned at temperatures above 500 degrees and weighed after the crucible has cooled. If the ash residue rate remaining in the crucible after it comes to room temperature is above 1 percent, it is accepted as a filler material. If residues are below 1 percent, this is generally the result of unburned additives.
Ash test result is expressed as percent ash. A magnified optical examination of the ash deposit is performed to determine whether the ash is glass, mineral, or a combination of both.
Ash testing is also called ash content analysis and is a very important research and development element in various industries. Advanced laboratories, with highly trained staff, use many different procedures for their ash testing needs, including a variety of industry standards.
With thermogravimetric analyzes applied for polymers and plastics, weight loss caused by heating or cooling and other factors are determined. In this context, high volatile matter rate, medium volatile matter rate, combustible material percentage, ash percentage and proportional composition content are determined.
The following standards are taken into account in ash testing and analysis:
TS EN ISO 3451 Plastics - Determination of ash
ASTM D2584-18 Standard test method for loss of ignition of cured reinforced resins
ASTM D5630-13 Standard test method for ash content in plastics
pH Measurement
pH :
It is a measurement parameter that expresses the degree of acidity and alkalinity of the product.
The expression pH means “Power of Hydrogen”.
pH is the activity of hydrogen ions.
pH is a logarithmic measurement of the concentration of hydronium ions in a solution.
pH is the logarithmic expression of the H+ or OH- concentrations in aqueous solutions.
p in the pH term; They are derived from the mathematical symbol for minus logarithm, and H from the chemical formula of Hydrogen.
In order to express the H+ and OH– concentrations of aqueous solutions with a single scale, the minus logarithm of the H+ ion molar concentration is taken and this is called pH.
If the H+ concentration is higher than the OH– concentration, our substance is acidic; that is, the pH value is lower than 7. If the OH– concentration is higher than the H+ concentration, our substance is basic; that is, the pH value is greater than 7. If equal amounts of OH– and H+ ions are present, the substance is neutral with a pH of 7.
p in the pH term; They are derived from the mathematical symbol for minus logarithm and H from the chemical formula of hydrogen. The definition of pH can be given as the minus logarithm of the hydrogen concentration:
pH = – log10[H+]
Normal rainwater has a pH between 5 and 6 due to the presence of dissolved CO2 that forms carbonic acid.
Acid rain is rainwater with a pH of less than 5 because various nonmetal oxides such as CO2, SO2, SO3, NO, and NO2 dissolve in water and react with it, not only carbonic acid but also sulfuric.
pOH:
pH: logarithmic measure of the concentration of hydronium ions in a solution
pOH: logarithmic measure of the concentration of hydroxide ions in a solution
The acidity of a solution is typically evaluated experimentally by measuring pH. The pOH of a solution is not usually measured, as it is easily calculated from an experimentally determined pH.
The relationship between pH and pOH is:
pH+pOH=14
The change in pH values of liquids in contact with thermoplastic elastomers is measured. pH of a solution acidity or basicity It is a unit of measure describing the degree. It stands for "Power of Hydrogen".
Basically, “p” stands for potential and “H” stands for hydrogen. pH is the measurement of hydrogen ion activity in a solution (water). Whether a solution is acidic or alkaline depends on the activity of the H+ ion.
The pH values of different aqueous (water) solutions can be displayed on a pH rating scale. The scale used to measure the acidity or alkalinity of a solution is a 14-point scale. A value of 7 is neutral, a pH lower than 7 is acidic, and a pH higher than 7 is alkaline.
pH is a logarithmic scale. This means that each pH value below 7 is ten times more acidic than the next higher value. The same is true for pH values above 7, with each being ten times more alkaline than the next lower.
The pH value written on the labels of the water we buy shows the amount of hydrogen in the water. The higher the hydrogen content, the higher the pH value. A high pH value also indicates that the water has a basic structure. Alkaline water is water with a higher pH than normal water and accelerates the removal of harmful acids formed or accumulated in the body from the body.
Since alkaline water has a more basic structure, it ensures that the toxins in our body become neutral and are eliminated. In this way, it helps to cleanse our body.
It helps to get rid of other harmful substances in our body faster.
It also helps the digestive system to work faster and more regularly.
It also helps to maintain the pH balance of our body.
It nourishes our skin, reduces the signs of aging and beautifies the skin.
It helps cells regenerate faster.
It also helps the body's immune system to be stronger as it provides the pH balance.
It also prevents the formation of edema. It also helps to lose weight as it has features such as removing toxins from the body and preventing edema.
Remember that making your body more alkaline is not always a good thing. For example, in people with kidney disease, minerals in alkaline water may begin to build up in their bodies.
Also, drinking large amounts of alkaline water can disrupt the body's normal pH. This can cause a condition called metabolic alkalosis, which can cause nausea, vomiting, hand tremors, muscle twitching, tingling in the face, hands, or feet.
Alkaline Water Recipe:
It is now in your hands to increase the pH balance of the water you drink for a healthy life. You can easily prepare it by taking 1-2 minutes every morning;
into 2lt water,
2 slices of lemon,
half green apple slices,
2 stalks of parsley,
2 mints,
1 stick of cinnamon,
1 cucumber
As a result…
It is true that in some cases, such as reflux, alkaline water is beneficial to your health. But for now, we cannot say that alkaline water is 100% healthy for everyone.
If you do not have kidney problems, you can try drinking alkaline water.
The most important point to remember is; Alkaline or normal, do yourself a favor and drink plenty of water.

Other Tests
Abrasion Test:
(ISO 4649) Applied for determination of resistance to friction. It is frequently applied in rubber, elastomer materials.
Determination of Glass Transition Temperatures (DSC):
(ISO 11357-1/3) The melting and crystallization temperatures and enthalpies of crystalline or semi-crystalline polymers are determined by Differential Scanning Calorimetry tools. Glass transition temperatures (Tg) of amorphous or semi-crystalline polymers are determined with ISO 11357-1/2 standard norms. ( See Also >>> )
Deformation Test:
(ASTM D395) After a force applied to the thermoplastic elastomer material at different times and temperatures, the ability of the material to maintain its elastic properties is measured. The permanent deformation in the material is measured after the applied pressure at a certain temperature and time.
Differential Scanning Calorimetry (DSC):
Thermal analysis technique that allows us to obtain the thermal transitions produced during heating of the analyzed material specific to each material and provides additional information to that obtained with FTIR, thus completing the identity of a polymeric material.
Dynamic Mechanical Analysis ( DMA):
(ASTM D7028 - 07) Dynamic, Mechanical Viscoelastic properties are measured by applying an increasing or decreasing load on the analysis material at a determined frequency.
Determination of Bending Temperature (HDT):
(ISO 75) It is the Determination of Bending Temperature Under Load test and this test is performed by applying a bending force to a prism-shaped sample at a constant temperature increase. Bending Temperature Under Load is the bending temperature of the specimen specified in the norm.
Homogeneity Test:
(ISO 13949) Homogeneous pigment, additive etc. in the structure of the material. It is done with the aim of examining the distribution and possible gaps. 10-15 mic. The cross-sectional piece is examined under a microscope. Deviations that occur in the original state of the material are detected.
Determination of Resistance to Internal Pressure:
(ISO 1167) It is a test method in which the behavior of pipe fittings and pipes against pressure over time is examined under shortened ambient conditions. By applying high pressure conditions to the pipe and its fittings, the changes in the pipe are monitored over a period of 50 years.
Air Conditioning Test:
(ISO4582) Other surface changes such as color change and/or cracking/scratching are analyzed with the simulation created for long-term exposure of the material in environmental conditions such as sunlight, rain, humidity, dew.
In general, the working principles of both cooling systems and air conditioning systems are similar. However, there are significant differences between these two systems, for example in terms of components, design methods, commercial or industrial structures in which they are installed, and their operations. Air conditioning systems are systems used to create and maintain certain temperature, relative humidity and air quality conditions in indoor environments. The purpose is not just to cool the air of the environment. Air conditioning systems are generally installed to maintain personal comfort levels.
In various sectors, air conditioning systems are needed to ensure the correct operation of machinery and equipment that must operate in certain environmental conditions and to carry out certain industrial processes that generate a significant amount of heat that must be disposed of. These systems must be effective regardless of external climatic conditions and include control over four key variables: air temperature, humidity, movement and quality.
There is always a difference between industrial and personal comfort applications. Industrial air conditioning generally requires more precision in terms of temperature and humidity control. Some applications also require a high degree of filtration and removal of contaminants. On the other hand, besides the need to meet personal temperature and humidity requirements, it is important to create ideal weather conditions for people's psychophysiological states.
The basic process underlying air-conditioning systems is the exchange of heat and water vapor between indoor and outdoor environments and people in the air-conditioned space. The power of these systems is different according to the purpose of use. It is generally used for cooling and heating air or water, removing moisture from the air, humidifying the air, filtering the ambient air, mixing indoor and air air and ventilation.
Izot Impact Test:
(ASTM D256) The impact resistance of the material is measured. The kinetic energy required for the material to crack and break is calculated.
Determination of Carbon Black:
(ISO 6964) It is made with the aim of determining the amount of carbon in the structure as % in order to ensure the resistance of the material to UV rays. 1 g of material It includes separation under a stream of nitrogen gas for 45 minutes at 550°C and combustion at 900°C. The amount of carbon cyanide is calculated from the mass difference before and after the process.
Evaluation of the Distribution Degree of Pigment or Carbon Black is also done with the (ISO 18553) standard. Homogeneous pigment distribution in the structure of the material and to examine possible gaps. A microtome section taken with a thickness of 10-15 microns is examined under a microscope.
Capillary Rotational Rheometry :
Determination of the rheological properties of polymeric materials by measuring their creep and deformation resistance. The rheological analysis of these materials also provides us with important information about machinability.
Infrared Spectroscopy Analysis (FTIR):
(ASTM E 1252) The structures and functional groups of polymers are identified with the FTIR-Fourier transform infrared spectroscopy device. It allows to obtain a fingerprint spectrum specific to each material, which gives information about the base polymer of any plastic material, as well as other components present in the material (mineral fillers, copolymers, polymer blends, etc.).
Smell Test:
(VDA 270) Thermoplastic elastomers in furnaces and beakers are graded according to their odor class.
Tensile Strength:
(ISO 527) The behavior of the material against force is examined. Tensile strength and modulus of elasticity are determined. Elongation at break test is also performed within the same standard and the elongation at break of the material is determined as %.
Chromatography (LC-PDA, LC-MS, LC-LS, GC-MS, GC-FID, HS-GC):
Thanks to chromatographic analysis, plastic materials such as UV stabilizers, antioxidants, plasticizers and residual monomers, solvents from ink or adhesives, decomposition substances, etc. measurement of small components.
Determination of moisture:
The moisture of thermoplastic elastomers is determined quantitatively by measuring the weight loss.
Oxygen Induction Time Determination (OIT):
(ISO 11357-6) It is applied to determine the time elapsed until the onset of exothermic oxidation of the material at a certain temperature, in oxygen or air and at atmospheric pressure. The Oxygen Induction Time is the relative value of the material's degradation by oxidation.
Optical Scanning Electron Microscope (SEM):
The number and thickness of layers in multilayer materials, the distribution size of pigment or filler particles in the polymeric matrix, coating defects, interphase morphology between components, etc. It provides information about the structure of the analyzed materials.
Rheological Property Detection:
(ISO 11443) specifies methods for determining the fluidity of plastic melts subjected to shear stresses at rates and temperatures approximating those occurring in plastics processing. It is necessary to test plastic melts in accordance with these methods, because the fluidity of plastic melts often depends not only on temperature but also on other parameters, especially shear speed and shear stress. It is performed to evaluate extrudate swelling caused by spatial effects at the die entrance.
Hardness Determination:
(ISO 2039-2) Shore value is the determination of how much the pointed spring penetrates the material with the applied pressure.
The Shore hardness scale has a wide range from Shore-A (soft, elastomer materials) to Shore-D (rigid, hard materials). There are very different hardness scales in Rockwell, Brinell, Vickers norms.
Fogging Test:
(ISO 6452) The amount of volatile components that can be released to the environment during the use of thermoplastic elastometers are determined.
Soxhlet Extraction:
The liquids in the thermoplastic elastomer are extracted, the liquids dissolved in the solid material are quantitatively measured. With the Soxhlet Extraction Mechanism, the percentage of crosslinking of the thermoplastic vulcanizate is also calculated, and the polymer gel content is determined.
Thermo Gravimetry Analysis (TGA):
(ISO 11358-1) Thermogravimetric analysis is performed to determine the decomposition temperature and rate of the polymer, as well as to determine the amounts of volatile, semi-volatile substances, additives and/or fillers in its structure. Polymer percentages, other organic components, mineral fillers, carbon black, etc., about the composition of a plastic material. Another thermal analysis technique that results in quantitative information about
Flammability Test:
(UL 94) (EN 45545)
There are various standards that classify the flammability of plastics. These classification standards, defined in UL94 and internationally accepted flammability test is performed.
Recently, the newly introduced European standard for fire protection in railway vehicles, numbered EN-45545, has also begun to be preferred, since it classifies both fire style and smoke emissions.
Classification of flame resistant plastics according to UL94 is based on the following criteria:
UL94-HB plastic (horizontal burning): The flammability performance of thermoplastic elastomers is determined by testing in a horizontal flame chamber. The sample (rectangular plastic strip of defined size) is held in a horizontal position and exposed to direct flame at one end for 30 seconds. The flame is then removed and the material must burn slower than the defined burning rate in order to be classified as HB.
UL94-V0 plastic (vertical combustion): The specimen is held in a vertical position and exposed to direct flame for 10 seconds from its lower end. After repeated 10 seconds of ignition, the time required for the combustion to stop after the flame is removed is summed up. The material can be classified as UL94 V0 if the total extinction time is less than 50 seconds and there is no dripping of flame.
UL94-V1 plastic (vertical burning): Installation is the same as described above. The material is classified as UL94 V1 if the total extinction time is less than 250 seconds and there is no dripping of flame.
UL94-V2 plastic (vertical burning): Installation is the same as described above. If the total extinction time is less than 250 seconds and dripping occurs, the material is classified as UL94 V2. V2 plastics is one of the natural, amorphous polyamides due to its chemical structure and as a result it is highly transparent.
UV Aging Test:
(ASTM G 154) With the accelerated UV tester, the changes of thermoplastic elastomers under UV light are observed by accelerated aging.
Vicat Test:
(ISO 306) Deviations that occur in the original state of the material under a voltage and temperature determined by the norm are detected.
Specifies four methods for determining the Vicat softening temperature (VST) of thermoplastic materials:
Method A50 using a force of 10 N and a heating rate of 50 °C/s
Method B50 using a force of 50 N and a heating rate of 50 °C/s
Method A120, Method B120, using a force of 10 N and a heating rate of 120 °C/s
It is carried out using a force of 50 N and a heating rate of 120 °C/s.
The methods mentioned are applicable only to thermoplastics, which give a measure of the temperature at which the thermoplastics begin to soften rapidly.
Aging Test:
(ASTM D471) Some liquid chemicals of thermoplastic elastomers its resistance to the material and their effects on the material are measured. Consumer products contain many materials that react differently to natural sunlight. UV aging testing allows manufacturers to better understand how their products will respond to different light exposures, such as cracking, fading and deterioration.
UV aging tests are performed to evaluate the durability performance of non-metallic materials and organic materials such as plastics, paints, coatings and rubber under conditions such as sunlight, temperature and other climatic conditions. In these tests, laboratory environments are used to simulate natural light source such as sunlight and damage in nature such as rain and snow damage, and to evaluate the degree of color change and fading in accelerated ambient conditions. These tests are important for manufacturers to understand how potential negative UV rays will affect their products.
Accelerated aging is a form of comprehensive testing that uses amplified adverse conditions to increase the aging (aging) rate of products and materials. Reinforced adverse conditions are environmental conditions in nature such as sun, heat, cold, salt water, vibrations and so on. Lab environments simulate accelerated wear and tear. The purpose of these tests is to predict the expected service life of products and materials or to predict unexpected failures that may occur.
Accelerated aging tests of products and materials are performed in many different ways, depending on the type of material or product being tested, its intended use, and the ambient conditions present when the material or product is used. In these tests, the ISO 4892 standard series designed by the International Standards Organization (ISO) and published by the Turkish Standards Institute (TSE) in our country are taken into consideration.
Tear Test:
(ASTM D624) Tear resistance of thermoplastic elastomers is measured.
Density Test:
(ISO 1183) It is the determination of the weight of the material in unit volume. The weighed material is also weighed in a liquid whose density is known beforehand, and its density is found by the calculation method determined in the standard.