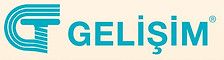


Hydrocarbons
It is an organic compound consisting of two elements, hydrogen and carbon. Most of the petroleum composition consists of hydrocarbons of varying lengths.
The smallest hydrocarbon methane consists of a single carbon atom and four hydrogen atoms. However, hydrocarbons can consist of hundreds or thousands of individual atoms linked together in many ways, including chains, circles, and other complex shapes.
In order to classify the properties of hydrocarbons, they are divided into several basic types.
Alkanes: These are called saturated hydrocarbons. That is, they only contain single bonds between all carbon atoms. Alkanes are the basis of petroleum fuels and exist in linear and branched forms.
Unsaturated Hydrocarbons: Hydrocarbons that have one or more double bonds between carbon atoms are called alkenes.
Cycloalkanes: Any hydrocarbon containing one or more ring structures.
Aromatic Hydrocarbons: Aromatic hydrocarbons , also called arenes, are a unique class of carbon molecules in which carbon atoms are bonded by successive double and single bonds. This class of molecules has special ring structures in which the bonds between carbon atoms are an intermediate bond between single and double bonds.
Molecules in this class contain the industrial solvent "benzene".
Benzene (C6H6): Like other hydrocarbons, benzene is a natural component of petroleum. It is a colorless, flammable, sweet-smelling liquid at room temperature and is a component of most gasoline blends because of its high octane number.
Benzene is also highly carcinogenic and is well known to cause bone marrow failure and bone cancer. Of course, its carcinogenicity is not well known when used as an additive in aftershave and other cosmetics due to its "pleasant aroma".
The largest use of benzene (50%) is the product of styrene and polystyrene plastics. It is also converted into a molecule known as cyclohexane, which is important in Nylon production. About 15% of benzene is used to produce cyclohexane. Smaller amounts are used in everything from pesticides to rubber.
The benzene structure can be drawn in two ways. In the first, the double bond character is drawn explicitly. In the short handed version, a circle is drawn inside the ring to show the structure. There is only one hydrogen bonded to each carbon atom in benzene.
I. and II below. drawings are identical. III in practice. drawing is used.
Benzene is a colorless, flammable liquid with a boiling point of 80.1 ° C and a melting point of 5.5 ° C.
Binuclear Aromatic Hydrocarbons: They are compounds that contain two benzene rings in their molecules.
Hydrocarbons
It is an organic compound consisting of two elements, hydrogen and carbon. Most of the petroleum composition consists of hydrocarbons of varying lengths.
The smallest hydrocarbon methane consists of a single carbon atom and four hydrogen atoms. However, hydrocarbons can consist of hundreds or thousands of individual atoms linked together in many ways, including chains, circles, and other complex shapes.
In order to classify the properties of hydrocarbons, they are divided into several basic types.
Alkanes: These are called saturated hydrocarbons. That is, they only contain single bonds between all carbon atoms. Alkanes are the basis of petroleum fuels and exist in linear and branched forms.
Unsaturated Hydrocarbons: Hydrocarbons that have one or more double bonds between carbon atoms are called alkenes.
Cycloalkanes: Any hydrocarbon containing one or more ring structures.
Aromatic Hydrocarbons: Aromatic hydrocarbons , also called arenes, are a unique class of carbon molecules in which carbon atoms are bonded by successive double and single bonds. This class of molecules has special ring structures in which the bonds between carbon atoms are an intermediate bond between single and double bonds.
Molecules in this class contain the industrial solvent "benzene".
Benzene (C6H6): Like other hydrocarbons, benzene is a natural component of petroleum. It is a colorless, flammable, sweet-smelling liquid at room temperature and is a component of most gasoline blends because of its high octane number.
Benzene is also highly carcinogenic and is well known to cause bone marrow failure and bone cancer. Of course, its carcinogenicity is not well known when used as an additive in aftershave and other cosmetics due to its "pleasant aroma".
The largest use of benzene (50%) is the product of styrene and polystyrene plastics. It is also converted into a molecule known as cyclohexane, which is important in Nylon production. About 15% of benzene is used to produce cyclohexane. Smaller amounts are used in everything from pesticides to rubber.
The benzene structure can be drawn in two ways. In the first, the double bond character is drawn explicitly. In the short handed version, a circle is drawn inside the ring to show the structure. There is only one hydrogen bonded to each carbon atom in benzene.
I. and II below. drawings are identical. III in practice. drawing is used.
Benzene is a colorless, flammable liquid with a boiling point of 80.1 ° C and a melting point of 5.5 ° C.
Binuclear Aromatic Hydrocarbons: They are compounds that contain two benzene rings in their molecules.
About
Kyäni, nutritional supplement products consisting of beneficial ingredients; It delivers to more than 50 countries around the world with unique business opportunities. We use Kyäni products daily to maintain our ideal health, share these products with others, devote a certain amount of time to work almost every day to build and maintain our business, and share our success with others by involving others in the Kyäni opportunity or contributing to the Potato Pak and Caring Hands programs.
About
Kyäni, nutritional supplement products consisting of beneficial ingredients; It delivers to more than 50 countries around the world with unique business opportunities. We use Kyäni products daily to maintain our ideal health, share these products with others, devote a certain amount of time to work almost every day to build and maintain our business, and share our success with others by involving others in the Kyäni opportunity or contributing to the Potato Pak and Caring Hands programs.
Page Under Construction.
Page Under Construction.
Training / Knowledge / Solution Platform
Plastics
Plastic industry is one of the most important sectors today. From basins, buckets, brushes, floor coverings, building insulation coatings, foams, plastic bags used in the markets, water pipes to ballpoint pens, formica furniture coatings to pet soft drink bottles, nylon women's socks to paints, Teflon pans to coatings and varnishes, molds to film strips, fibers to cables. It is possible to come across a product belonging to the plastic industry in almost every object used in daily life, from packaging production to bathroom curtains, from car tires to labels and from automobile production to shipbuilding.
Plastics are actually polymers: long chains of atoms bonded together. These chains consist of many repeating molecular units. Polymers formed by carbon and hydrogen alone or with oxygen, nitrogen, sulfur and chlorine constitute an important part of plastics. British scientist Alexander Parkes found the first natural plastic by mixing Proxylin, which is formed by nitration of cellulose (the building block in the cell wall of plants), mixed with alcohol and camphor. The first plastic based on a synthetic polymer was made using phenol and formaldehyde and was called bakelite.
To classify plastics:
-
Cellulose-based plastics (Celluloid, rayon)
-
Bakelite (Phenol, formaldehyde)
-
Styrofoam, Polyester (PS), PolyVinyl Chloride (PVC)
-
Nylon (Polyamide-PA)
-
Synthetic Rubber
-
Polyethylene, Acrylic, Polyurethane, Polyethyleneterephthalate (PET)
-
Polytetrafluoroethylene (Teflon)
Bakelite :
Bakelite, Phenol Formaldedit Resin.
In 1907, Leo Baekeland invented Bakelite, the first fully synthetic plastic, meaning no molecules have been found in nature. Baekeland sought a synthetic alternative to shellac, a natural electrical insulator, to meet the needs of the rapidly electrifying United States. Bakelite wasn't just a good insulator; it was also durable, heat resistant and, unlike celluloid, ideally suited for mechanical mass production. Marketed as a "thousand-use material," Bakelite can be shaped or molded into almost anything, and offers endless possibilities.
Hyatt and Baekeland's successes caused major chemical companies to invest in the research and development of new polymers, and the new plastics soon joined celluloid and Bakelite. While Hyatt and Baekeland were looking for materials with specific properties, new research programs sought new plastics for their own good and then worried about finding their use.
Making Bakelite is a multi-step process. It begins by heating phenol and formaldehyde in the presence of a catalyst such as hydrochloric acid, zinc chloride or base ammonia. Molded Bakelite is formed in the condensation reaction of phenol and formaldehyde with wood flour or asbestos fiber as filler, under high pressure and heat, within a few minutes of curing time. The result is a hard plastic material.
Bakelite has many important properties. It can be molded very quickly, shortening the production time. Moldings are smooth, hold their shape and are resistant to heat, scratches and destructive solvents. It is also electrically resistant and valued for its low conductivity. It is not flexible.
Phenolic resin products may swell slightly under conditions of extreme humidity or constant humidity. When rubbed or burned, Bakelite has a distinctive acrid, sickly sweet or fishy odor.
Bakelite is generally hard, brittle and brittle and not suitable for use in making articles. To make this polymer material usable, Bakelite B is cured by heating with glycerin for a while. Thus, glycerine molecules enter between the polymer planes, giving it a soft feature.
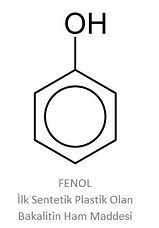
Phenol:
Raw Material of Bakelite, The First Synthetic Plastic. After phenol was discovered, chemists working to understand its properties and find different uses made an important discovery in 1907. US chemist L. Baekeland produced a synthetic furniture polish by reacting phenol with formaldehyde. When the polish did not sell, he decided to make glue from phenol and formaldehyde. By controlling the reaction temperature and pressure, the new material he produced became a strong plastic that could be molded. Baekeland's plastic was very popular because there was no such plastic in those years. Today, the plastic known as phenol-formaldehyde resin has spread all over the world under the name of bakelite. Over the years, hundreds of products such as radios, light switches, pot handles, decorative pots and auto parts were made from bakelite.
Bakelite was registered as “the world's first synthetic plastic” by ACS (American Chemical Society) in 1993. Phenol became an important industrial raw material produced from petroleum, not tar. The lactic acid in sour milk and the citric acid in lemon have been known since Ancient Egypt times to help regenerate the skin. In France, Madame Pompadour protected her skin by bathing in wine. The active ingredient in wine is tartaric acid.
Phenol was first used in the USA in 1903 to clear up acne.
During the First World War, phenol solution was applied to the wounds of soldiers with gunpowder burns. When the soldiers recovered, their skin looked smooth and scars were not noticeable. Realizing this, French doctors began to remove blemishes and wrinkles on women's faces by applying phenol after the war. When the French taught this technique to US doctors, skin peeling became fashionable among movie stars. Today, phenol, citric acid, glycolic acid, lactic acid, malic acid, tartaric acid, salicylic acid or trichloroacetic acid are used to refresh the skin. Almost all plants contain phenolic substances of various sizes, and the common point of all of them is that they contain at least one phenol group. "
Formaldehyde :
It is a colorless, clear liquid chemical substance. Formaldehyde consists of hydrogen, carbon and oxygen atoms. It is an organic compound. Its aqueous solution is syrup-like and its consistency is slightly dark. The phenol formaldehyde formula is formulated with the chemical formula CH2O. Its normal state is gaseous. It is made liquid by processing and from this stage it is defined as Formalin. It is used for commercial purposes by creating a 37% solution. Its density is 0.8153 g/cm³. It is used as a disinfectant in medical laboratory environments. It is also used in the manufacture of some medicines. It also has antimicrobial and bactericidal properties.


Thermoplastics
Depending on the type of monomer used, each polymer type has its own characteristic structure and size.
polymeric materials (plastics); They can be grouped under two main polymer series as thermosets and thermoplastics.
Thermoplastics are defined as polymers that can be melted and recast for an almost infinite number of different uses.
Thermoplastics, which have the simplest molecular structure, have chemically independent macromolecules.
It softens or melts when heated, takes shape when cooled, boils and solidifies.
It can be heated and cooled repeatedly, without serious damage, so it can be reprocessed and recycled.
Typical thermoplastics:
Polyethylene (PE), polypropylene (PP), polyvinylchloride (PVC), polystyrene (PS), acrylic polymers, styrene-acrylonitrile copolymers (SAN), acrylonitrile butadiene styrene (ABS), polycarbonates (PC), fluoropolymers, acetals, polyamides (PA) ), nylons (NA6, NA66)
The most basic components used in the production of thermoplastics are monomer building blocks. For example, polypropylene is produced using propylene monomer, polystyrene is produced using ethylene, and polyvinylchloride is produced using vinyl chloride.
Today, the raw material used in the production of thermoplastics is largely obtained from fossil raw materials. To some extent, bio-based raw materials can also be mentioned.
The demand for thermoplastic materials is high; these are plastics that are easily shaped with heat, which can be reshaped when cooled and then reheated. Thermoplastics are polymers that generally consist of linear or slightly branched structures. The process is reversible; It softens or melts when heated and flows when pressure is applied, and solidifies again when cooled. There are no crosslinks between polymer chains; This structure gives the polymer melt properties.
Generally, when thermoplastics are not loaded (under their own weight), they deteriorate at 65°C-120°C and some varieties at high temperatures such as 260°C.
Therefore, they should be used under a low load at high temperatures. Thermosets, on the other hand, can be continuously exposed to temperatures between 150°C -230°C; some special types of thermoset can withstand up to 260°C. Fillers such as asbestos and glass filler increase the thermal resistance of plastics.
Thermoplastics, which have been on the market for a long time, are an important part of our daily life.
For example, acrylonitrile butadiene styrene (ABS) is a type of thermoplastic used in the manufacture of:
gym equipment
toys
many auto parts
Polycarbonate is used in the manufacture of:
compact discs (CDs)
beverage bottles
food storage containers
eyeglass lenses
Polyethylene, the most common thermoplastic, is used in the manufacture of:
shampoo bottles
plastic shopping bags
bulletproof vests
Thermoset Plastics
It is a group of plastics that turns into a non-melting material when cured by heat or chemical means. As they are cured or cross-linked compounds, they are durable and heat resistant. It is not possible to rework or shape materials in this group.
They solidify when heated (in the presence of a catalyst) and cannot be remelted. Thermoset plastics do not lose their durability and shape when heated. Thermoset plastics are thus very suitable for use in the production of permanent components and large, solid shapes. In addition, these components have extremely good strength properties and do not lose their durability in the face of temperature increase.
When thermoset plastics are heated, the molecules undergo chemical and phase changes, and three-dimensional cross-links (network) are formed between the polymer chains. When the three-dimensional meshes are heated, they do not flow even when pressure is applied, and the polymer cannot be restored by cooling and heating.
Typical thermoset plastics:
Alkyd resins, amino resins, unsaturated polyesters, epoxies, phenol-formaldehyde resins, polybutadiene rubber, polyurethanes, styrene-butadiene copolymers, amino compounds (melamine and urea), unsaturated polyester, polyurethanes, reinforced plastics, styrene-butadiene copolymers, polybuted epoxies and phenolics.
Each type of thermosetting plastic has unique properties. For example, epoxies are flexible and form relatively easily, while exhibiting exceptional resistance to chemicals. Phenolics that are easy to mold are brittle, strong and hard. Thermoset plastics are used in many areas such as electrical insulation materials in vehicle bodies, thanks to their many properties.
Thermosets are used in:
electronic chips
fiber reinforced composites
polymeric coatings
eyeglass lenses
dental fillings
Thermoset plastic products are typically produced by heating a liquid or powder in a mold to cure it. These products can be removed from the mold even before they cool. The reaction used in the production of thermoset plastic products does not always occur as a result of heating, but sometimes arises from the chemical interaction between special materials.
It is not possible to rework or shape materials in this group. When heated (in the presence of a catalyst) they solidify and cannot be remelted; molecules undergo chemical and phase changes, three-dimensional cross-links (network) are formed between polymer chains. When the three-dimensional meshes are heated, they do not flow even when pressure is applied, and the polymer cannot be restored by cooling and heating.
Thermoset Rubbers: They are chemically vulcanized rubbers; they cannot be remelted and remolded without their original characteristics deteriorating or shattering.
Polyurethanes: They are polymers obtained by the reaction of diisocyanates (MDI and/or TDI) with a series of polyols. Depending on the desired finished product, chemical formulations may include other materials such as catalysts, blowing agents and possibly flame retardants. Thanks to these combinations, it is possible to obtain various types of products.
rigid and flexible foams
rigid and flexible inner surface foams
elastomers
adhesives
overlays
sealants
The density of the product depends on the amount of blowing agent used and its flexibility or hardness depends on the type of polyol and diisocyanate used.
Different forms of polyurethane can be used to produce many finished products, often in combination with other materials.
The most known usage areas of polyurethane are:
Building insulation
Refrigerators and freezers
Furniture and bedding
shoes
automobiles
Coatings and adhesives


Elastomers
Elastomers (or synthetic rubbers) are usually thermoset plastics; During curing, crosslinks occur between long polymeric chains. Their most important characteristics are that they are flexible and elastic; When stretched at room temperature (low tension) they stretch at least twice their length and immediately return to their original size when the tension is removed. These properties are provided by special polymer systems; for example, acrylic and polyacrylates; butyl, polybutene and Polyisobutylene polymers; ethylene copolymers; fluoropolymers (such as PTFE); silicone, polyurethane and polyether block amide (PEBA); styrene butadiene rubber (SBR); such as vinyl and polyvinylchloride (PVC) systems.
Polymers that can be elastomers are polyurethane, butyl rubber, silicones and specially treated ethylene-propylene copolymers;
They solidify in a glassy appearance below 0°C and do not turn into a viscous fluid even at high temperatures. They show elastic behavior between the temperature at which they become glassy and the decomposition temperatures. deformation and elastic properties are similar to natural rubber. Thermoset elastomers have properties similar to vulcanized rubber, thermoplastic elastomers are remolable; that is, they are polymers with rubber properties.
Natural Elastomers:
Latex
Vulcanized
Synthetic Elastomers :
Thermoplastic elastomers (Block copolymers (TPE-U, TPE-E, TPE-A, TPE-S), mixed elastomers (TPE-V, TPE-O))
Thermoset elastomers.
Elastomers often contain fillers to meet the desired properties.
It can be easily shaped when softened and turned into resin.
Once cured, it is unaffected by temperature changes and stresses such as stretching or pinching.
It is very resistant to impacts,
Not easy to draw,
It is resistant to corrosion caused by various chemicals,
It is resistant to moisture or water submersion.
Since it does not conduct current, it provides very good insulation in electronics. They are dense and shielding compared to different cables.
They can "blend" into other materials, enhancing certain properties.
Thanks to other types of polymers, they can maintain their hardness at high temperatures.
It can decompose in ozone gas.
Elastomers can be easily combined with many materials such as metal, hard plastic or different types of rubber.
The problem with recycling is that elastomers, which are chemically cross-linked polymers, cannot be melted and reshaped. In this respect, they differ greatly from plastics.
In the current technology, it is possible to blend the crumbled rubber piles and pour them into new rubber matrices, so it is inevitable that the physical properties will deteriorate to a great extent. This explains the efforts and developments in de-hardening processes.
Elastomers are useful and versatile substances that can easily take a variety of rubbery shapes. For this reason, it easily finds application in automotive, sports, electronics and assembly fields.
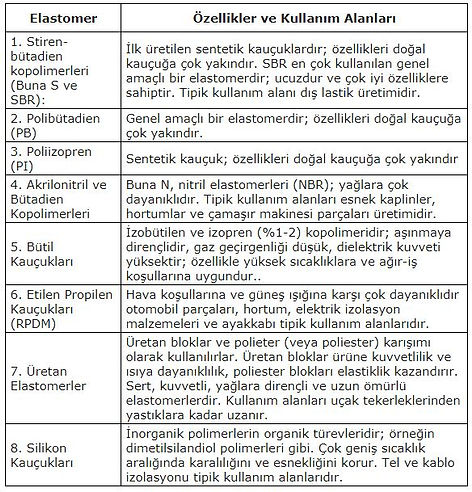
Standard Plastics
It is the most widely used plastic polymer in the world. There are low density (LDPE/LDPE) and high density (HDPE/YYPE) types. This material is resistant to chemicals, abrasions, electrical properties, high impact and notch resistance, and almost zero moisture absorption property. With a linear molecular structure of repeating -CH2-CH2-units, PE is a semi-crystalline polymer that elongates before breaking and increases its hardness. In general, porous PE is considered a strong and lightweight thermoplastic with strong chemical resistance. Products made from standard polyethylene grades typically have pore diameters ranging from 7 to 150 micrometers, although these nominal values can be increased to 300 micrometers with special blends.
Polyethylenes have high impact strength at normal and low temperatures. They are not affected by acids, alkalis and organic solvents. It is pure transparent and lighter than water. It is generally used in thin-film packaging, wrapping and covering works, irrigation and sprinkler pipes and in the production of various inexpensive kitchenware. It catches fire easily and continues to burn spontaneously outside the flame. It has good electrical insulation. It can be used underground as it is not affected by salt and bacteria. It has high electrical resistance. Therefore, it is an important insulation material. Since the coefficient of thermal expansion is high (160*10-6), it is affected by the sun's rays.
Products; Resistant to concentrated acids, alkalis, many organic solvents, it is suitable for continuous service at temperatures of 80°C and intermittently at temperatures of 110°C. It has a linear structure (LLDPE). Its properties are higher tensile strength, impact strength and puncture resistance than LDPE.
PE, PP, PVC, EVA, SAN, PC are the most widely used typical standard plastics.
Polyolefins : It is produced from petroleum or natural gas after the polymerization process. Here, short chemical chains (monomers) come together using a catalyst and form long chains (polymers). Polymers are solid thermoplastics that can be processed in two ways: film extrusion or membrane extrusion or molding. During membrane extrusion, the polymer is molten and compressed by heating, pouring it into thick plates, thin membranes or fibers. The membrane thickness can be adjusted to yield a variety of products, from light food packaging to heavier membranes suitable for agricultural use. The molding process includes the steps of compressing the polymer by heating in an extruder and then pouring it into a mold where it solidifies as desired.
The benefits of polyolefins
Due to their versatility, polyolefins are one of the most common plastics used today. Uses include:
LDPE: stretch film, carrier bags, agricultural films, milk carton linings, electrical cable sheaths, industrial heavy-duty bags.
LDPE: stretch film, industrial packaging film, thin-walled containers and medium and small heavy-duty bags.
HDPE: cases and boxes, bottles (for food products, detergents, cosmetics), food containers, toys, oil tanks, industrial packaging and films, pipes and household goods.
PP: yoghurt containers, margarine containers, dessert and snack packaging, microwave ovenproof containers, carpet fibres, garden furniture, medical packaging and tools, luggage, utensils and pipes.
Engineering Plastics
Engineering thermoplastics are generally a group of plastics that are resistant to heat, chemicals, impact, and flame.
engineering plastics
It is a group of plastic materials with better mechanical and/or thermal properties than the more commonly used commodity plastics (such as polystyrene, PVC, polypropylene, and polyethylene).
Being so expensive, engineering plastics are produced in smaller quantities and tend to be used for smaller objects or low volume applications (such as mechanical parts).
Typical Engineering plastics:
PC used in motorcycle helmets, car bumpers, dashboard trim, etc. ABS used for
PPE, PPO, TPU, PA, PET, POM, PBT, UHMWPE can be sorted.
Engineering plastics have gradually replaced traditional engineering materials such as wood or metal in many applications. In addition to equaling or exceeding them in weight/strength and other properties, engineering plastics are much easier to manufacture, especially in complex shapes.
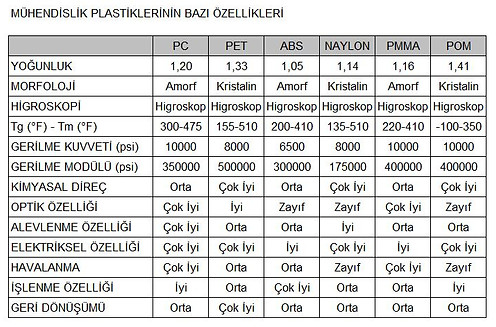

High Performance Plastics
They meet higher requirements than standard and engineering plastics in plastic production. They are more expensive and used in smaller quantities. High-performance plastics differ from standard plastics and engineering plastics mainly by their temperature stability, as well as their chemical resistance and mechanical properties, production quantity and price. The term high-performance plastics refers to high-temperature plastics, high-performance polymers, high-performance thermoplastics, or high-tech plastics. can be interpreted differently. High-temperature plastics name, in areas with continuous service temperatures that are by definition always higher than 150°C. is in use.
Typical high performance plastics:
PEI, PSU, PES, PAS, PVDF, PTFE, PEEK, PPS
Fluoropolymers: It belongs to the category of high-performance plastics. The most well-known member of this category is PTFE. PTFE is one of the smoothest and strongest materials. Its features can be listed as follows.
Chemical inertness: Fluoropolymers can be used in harsh environments. Due to their resistance to chemicals, they are suitable for use in most industrial processes, such as linings of containers and piping, fly ash collection bags and lithium-ion battery packaging.
High electrical conductivity: The insulating properties of these unique polymers have made it possible to shrink circuit boards. This concept lies behind the high-speed, high-frequency radar and communication devices found in the latest defense systems, as well as the new generation of ultra-fast computers.
Flame Retardant Fluoropolymers meet industry standards for electrical properties and flame retardancy. Cable sheaths (robots, personal computers, communications industry, sensitivity to high frequencies, electrical systems in aircraft, etc.), fiber optics, wire sheaths and electrical-electronic components are examples of usage areas.
Low Friction: The friction coefficient of fluoropolymers is very low. For example, PTFE is uniquely used as a support foot in bridges. Where this property is used in abrasive environments, inert fillers are often added to improve wear resistance. For example, today high-performance automobile and aircraft bearings and seals are commonly made from fluoropolymers.
Non-stick: Fluoropolymers are used in daily life due to the advantages of their unique properties. It is used in the coating of kitchen materials (pans, rice cookers, knives, etc.), printer drums, paper transfer parts of photocopiers in homes.
Weather resistance: Fluoropolymers do not suffer a serious loss of performance outdoors. They can be used for a long time without maintenance. They are used in architectural applications such as film in greenhouse applications, film cover in photovoltaic cells and UV resistant paints.
Inert and Inhibitory Properties: Fluoropolymers are used in the biomedical field in catheters and other parts used when performing diagnostic and therapeutic procedures. The superior barrier properties of fluoropolymers are utilized in pharmaceutical packaging, as their high resistance to moisture can protect pharmaceutical products. Fluoropolymers show high resistance to gasoline and this feature is used in parts produced in the automotive industry.
Conductive Plastics
Unmodified plastics generally do not conduct electricity, they are insulators. However, thermoplastics such as PEEK and Acetal can be modified to provide electrical conductivity, anti-static or static dissipative properties. When electrical property requirements exist, the key is usually to determine whether an electrically antistatic or conductive plastic or electrically insulating material is required.
Plastics with electrically conductive properties are classified by their specific surface resistance. This is the resistance of the plastic to the electric flow on the surface. This resistance applied voltage and current amperes, It is expressed by taking the ratio according to Ohm's law.
In order to protect from electrostatic charge (or discharge), antistatic plastics are preferred. Static dissipative plastics can also be used to ensure reliable machining of high-precision components. These significantly reduce the risk of component damage or destruction during production. Electrically active materials are also used in the mechanical engineering industry, conveyor technology and explosion protection. In these applications, electrical charge, which is selectively distributed, is an important factor in preventing explosive discharges.
Antistatic and static dissipative plastics are lighter and have superior weather resistance and It provides many advantages over other materials as they provide good protection against thermomechanical stress.
In addition to being protected from these electrostatic currents, there may be situations where direct transmission of electric current is desired.
Plastics with specific electrical conductive properties are more resistant to outdoor conditions. They have good resistance, offer protection against thermomechanical stress and have a minimum of corrosion resistance. Due to their sensitivity, they have advantages over other materials.
Electrical conductivity is obtained by adding electrically active substances to the polymer. Special conductive carbon black, carbon fibers, carbon nanotubes or inherently conductive materials These are the items.
Plastics with electrically conductive properties are included in the high-performance thermoplastic range. In this context, there is a wide variety of materials and thus a wide range of choices for possible applications in the electronics, automotive, renewable energies and mechanical engineering industries.
According to the electrical conductive plastics performance classification; It can be classified as insulator, antistatic body, conductor, high conductor.
POM-C (PolyOxyMethylene Copolymer) (Polyoxymethylene Copolymer)
Acetal copolymer modified by the addition of a special conductive carbon black It is POM-C material. The addition of carbon black creates excellent electrical conductivity in the material. Carbon black filled POM-C offers excellent chemical resistance, high strength, hardness and scratch resistance. In addition, carbon black filled POM-C has good UV and weather resistance. Its exceptional wear properties also make this special acetal copolymer an ideal solution for moving and frictional applications. Together with POM-C with antistatic additives, these materials cover a comprehensive range from antistatic POM-SD conductivity to static dissipative POM-ESD conductivity and transmitter POM-ESL.
Bio Plastics
Bio-based plastics are made wholly or partially from renewable biological resources. For example, sugar cane is processed to produce ethylene, which can then be used to produce polyethylene. Starch can be processed to produce lactic acid followed by polylactic acid (PLA). The term bioplastic covers plastics derived from renewable resources (bio-based plastics), such as plastics that biodegrade under uncontrolled conditions at the end of their life. While biodegradable plastics can be obtained from renewable resources such as starch, they can also be produced from fossil raw materials such as polycaprolactone. On the other hand, some bio-based plastics such as bio polyethylene, bio polyvinylchloride and bio polyethylene terephthalate have the same structure and material properties as ordinary plastics. In this case, the only difference from its ordinary counterpart is where at least some of its raw material comes from. There are also bio-based plastics that have no ordinary plastic counterparts. Examples are polylactic acid, some polyamides and polyhydroxyalkanoates. These materials have innovative properties that add value to the applications in which they are used.
The properties of bio-based plastics can vary significantly from material to material. Bio-based or partially bio-based durable plastics such as PE, PET or PVC, called "drop bioplastics", have the same properties as their conventional versions. These bio-based plastics cannot be distinguished from conventional plastics outside of scientific analysis.
Bio-based plastics such as starch blends, PLA, bio-PET and bio-PE are mostly used in packaging applications. They are also used in fibers in the textile industry. Bio-based succinic acid is suitable for a variety of applications in sports and footwear, automotive, packaging, agriculture, nonwoven and fiber applications.
Properties can vary considerably from material to material. Bio-based or partially bio-based "substitute bio plastics" such as PE, PET or PVC have the same properties as ordinary types. These bio-based plastics can only be distinguished from known plastic products through scientific analysis.
Natural bio-based polymers:
These polymers are synthesized with the help of living organisms basically in the form in which they were last used. Naturally produced bio-based polymers include:
polysaccharides;
Cellulose / starch;
Proteins;
Bacterial polyhydroxyalkanoates.
Direct industrial use is possible after extraction and purification.
Synthetic bio-based polymers:
Polymers whose monomers are derived from renewable resources but require a chemical transformation to form polymers.
In principle, most ordinary polymers can be synthesized from renewable raw materials. For example, corn starch can be hydrolyzed and used as a fermentation feedstock for bioconversion from polylactic acid (PLA) produced as a result of chemical treatment to lactic acid. Although the source of the polymer is renewable, it is not correct to consider it as 'natural' because it is synthesized in a chemistry laboratory.
Products produced with bio-based equivalents of ordinary polymers (such as bio PE, bio PET, bio PVC) are no different from fossil-based products in terms of mechanical recycling.
Other biopolymers, such as PLA, can be recovered by mechanical recycling, especially if there is a sufficient amount of homogeneous waste material.
Currently, raw material recovery is obtained from polylactic acid polymers (PLA). PLA can be hydrolyzed to the monomer lactic acid.
Oxydegradable Plastics :
Some bioplastics are biodegradable, but so-called 'durable' are the exception. An ordinary plastic based on fossil resources such as polyethylene is not biodegradable. Bio-based counterparts of ordinary plastics such as bio PE, bio PET, bio PA, bio PVC and other bio-based polymers are not biodegradable, just like ordinary plastics. Biodegradability is an intrinsic property of the material related to its molecular structure and is independent of the material's source. Some ordinary plastics with modified structure have been named 'degradable'. For example, they may contain an additive that causes the plastic to degrade under the influence of ultraviolet light and oxygen. These are called 'light-degradable plastics'. Other materials may contain an additive that initiates the decomposition process under certain temperature and humidity conditions. These are called 'oxy-degradable plastics', but the degradation process is not initiated by a microbial action. This degradation process is not in accordance with EN 13432 standard.
Biodegradable Plastics :
Biodegradable plastics are plastics that are decomposed by microorganisms into water, carbon dioxide (or methane) and biomass under certain conditions. As a result of the mineralization of organic structures with the help of microorganisms, the materials turn into carbon dioxide, methane (if the process takes place under anaerobic conditions), water and biomass. Compostable plastics are biodegradable plastics that biodegrade under controlled conditions (temperature, oxygen and humidity) in industrial composting plants. Under these anaerobic composting conditions, methane formation was prevented and only water and CO2 were formed.
The material can be foamed to obtain packaging materials, extruded and injection molded in modified ordinary machines. Different types of fillers can be used in the system, such as wood chips, lime, clay or paper waste (and other organic and inorganic fillers). Fillers can be colored or used in various granulation sizes to change the appearance of the material.
The material can be co-injected with other plastic materials such as LDPE, PP and HDPE. As a result of the coinjection process, a thin plastic film layer is formed on the upper part of this material. It is a completely biodegradable product that, when co-injected with biodegradable plastics, is cheaper than ordinary plastic materials, is completely waterproof, and is colored to resemble ordinary plastic materials.
There are two main classes of biodegradable plastics:
Bio plastics whose components are derived from renewable raw materials.
Plastics derived from petrochemicals containing biodegradable additives that accelerate the biodegradation process.
Biodegradable plastics offer an ideal solution for many single or short-term use applications:
In the process of collecting and diverting organic waste.
In the agricultural and horticultural sectors (for example, as mulch films or plant pots).
In packaging products in food packaging.
In the production of disposable tableware.
Biodegradable plastics are not designed to be disposed of in the environment and should not be allowed to be discharged into the environment.
Biodegradable plastics biodegrade in controlled environments with specified conditions.
Biodegradable plastics, like ordinary plastics, do not biodegrade as efficiently in landfills due to the absence of oxygen and moisture and low temperatures.
The term bioplastic covers plastics derived from renewable resources (bio-based plastics), such as plastics that biodegrade under uncontrolled conditions at the end of their life. While biodegradable plastics can be obtained from renewable resources such as starch, they can also be produced from fossil raw materials such as polycaprolactone. On the other hand, some bio-based plastics such as bio polyethylene, bio polyvinylchloride and bio polyethylene terephthalate have the same structure and material properties as ordinary plastics. In this case, the only difference from its ordinary counterpart is where at least some of its raw material comes from. There are also bio-based plastics that have no ordinary plastic counterparts. Examples are polylactic acid, some polyamides and polyhydroxyalkanoates. These materials have innovative properties that add value to the applications in which they are used.
Epoxy Resins
Epoxy Resins: They can change from low-viscosity liquid to high-melting-point solid, in other words, many materials with unique properties can be produced.
These synthetic resins can be any physical state from low viscous liquids to high melting point solids. When "cross-linked" with many curing materials or hardeners, it can create a whole host of materials with unique properties, making significant contributions to almost any industry.
Epoxy-based materials are widely used, such as coatings, adhesives, and composites using carbon fiber and fiberglass reinforcements. The chemical nature of epoxies and their commercially available derivatives allows the production of curing polymers with numerous properties. In general, epoxies are known for their excellent resistance to abrasion, chemicals and heat, nearly perfect mechanical properties and very good electrical insulating properties. Many properties of epoxies can be modified (for example, while epoxies are typically known to insulate electricity, silver-filled epoxies are also available that conduct electricity well). It offers high thermal insulation and thermal conductivity, as well as high electrical resistance properties for electronic applications:
• Paints and coatings
• Adhesives
• Forming with industrial tools and composites
• Electrical systems and electronic equipment
• Consumer and marine applications
• Aerospace applications
• Biology
• Art