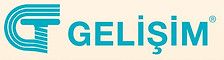


Hydrocarbons
It is an organic compound consisting of two elements, hydrogen and carbon. Most of the petroleum composition consists of hydrocarbons of varying lengths.
The smallest hydrocarbon methane consists of a single carbon atom and four hydrogen atoms. However, hydrocarbons can consist of hundreds or thousands of individual atoms linked together in many ways, including chains, circles, and other complex shapes.
In order to classify the properties of hydrocarbons, they are divided into several basic types.
Alkanes: These are called saturated hydrocarbons. That is, they only contain single bonds between all carbon atoms. Alkanes are the basis of petroleum fuels and exist in linear and branched forms.
Unsaturated Hydrocarbons: Hydrocarbons that have one or more double bonds between carbon atoms are called alkenes.
Cycloalkanes: Any hydrocarbon containing one or more ring structures.
Aromatic Hydrocarbons: Aromatic hydrocarbons , also called arenes, are a unique class of carbon molecules in which carbon atoms are bonded by successive double and single bonds. This class of molecules has special ring structures in which the bonds between carbon atoms are an intermediate bond between single and double bonds.
Molecules in this class contain the industrial solvent "benzene".
Benzene (C6H6): Like other hydrocarbons, benzene is a natural component of petroleum. It is a colorless, flammable, sweet-smelling liquid at room temperature and is a component of most gasoline blends because of its high octane number.
Benzene is also highly carcinogenic and is well known to cause bone marrow failure and bone cancer. Of course, its carcinogenicity is not well known when used as an additive in aftershave and other cosmetics due to its "pleasant aroma".
The largest use of benzene (50%) is the product of styrene and polystyrene plastics. It is also converted into a molecule known as cyclohexane, which is important in Nylon production. About 15% of benzene is used to produce cyclohexane. Smaller amounts are used in everything from pesticides to rubber.
The benzene structure can be drawn in two ways. In the first, the double bond character is drawn explicitly. In the short handed version, a circle is drawn inside the ring to show the structure. There is only one hydrogen bonded to each carbon atom in benzene.
I. and II below. drawings are identical. III in practice. drawing is used.
Benzene is a colorless, flammable liquid with a boiling point of 80.1 ° C and a melting point of 5.5 ° C.
Binuclear Aromatic Hydrocarbons: They are compounds that contain two benzene rings in their molecules.
Hydrocarbons
It is an organic compound consisting of two elements, hydrogen and carbon. Most of the petroleum composition consists of hydrocarbons of varying lengths.
The smallest hydrocarbon methane consists of a single carbon atom and four hydrogen atoms. However, hydrocarbons can consist of hundreds or thousands of individual atoms linked together in many ways, including chains, circles, and other complex shapes.
In order to classify the properties of hydrocarbons, they are divided into several basic types.
Alkanes: These are called saturated hydrocarbons. That is, they only contain single bonds between all carbon atoms. Alkanes are the basis of petroleum fuels and exist in linear and branched forms.
Unsaturated Hydrocarbons: Hydrocarbons that have one or more double bonds between carbon atoms are called alkenes.
Cycloalkanes: Any hydrocarbon containing one or more ring structures.
Aromatic Hydrocarbons: Aromatic hydrocarbons , also called arenes, are a unique class of carbon molecules in which carbon atoms are bonded by successive double and single bonds. This class of molecules has special ring structures in which the bonds between carbon atoms are an intermediate bond between single and double bonds.
Molecules in this class contain the industrial solvent "benzene".
Benzene (C6H6): Like other hydrocarbons, benzene is a natural component of petroleum. It is a colorless, flammable, sweet-smelling liquid at room temperature and is a component of most gasoline blends because of its high octane number.
Benzene is also highly carcinogenic and is well known to cause bone marrow failure and bone cancer. Of course, its carcinogenicity is not well known when used as an additive in aftershave and other cosmetics due to its "pleasant aroma".
The largest use of benzene (50%) is the product of styrene and polystyrene plastics. It is also converted into a molecule known as cyclohexane, which is important in Nylon production. About 15% of benzene is used to produce cyclohexane. Smaller amounts are used in everything from pesticides to rubber.
The benzene structure can be drawn in two ways. In the first, the double bond character is drawn explicitly. In the short handed version, a circle is drawn inside the ring to show the structure. There is only one hydrogen bonded to each carbon atom in benzene.
I. and II below. drawings are identical. III in practice. drawing is used.
Benzene is a colorless, flammable liquid with a boiling point of 80.1 ° C and a melting point of 5.5 ° C.
Binuclear Aromatic Hydrocarbons: They are compounds that contain two benzene rings in their molecules.
About
Kyäni, nutritional supplement products consisting of beneficial ingredients; It delivers to more than 50 countries around the world with unique business opportunities. We use Kyäni products daily to maintain our ideal health, share these products with others, devote a certain amount of time to work almost every day to build and maintain our business, and share our success with others by involving others in the Kyäni opportunity or contributing to the Potato Pak and Caring Hands programs.
About
Kyäni, nutritional supplement products consisting of beneficial ingredients; It delivers to more than 50 countries around the world with unique business opportunities. We use Kyäni products daily to maintain our ideal health, share these products with others, devote a certain amount of time to work almost every day to build and maintain our business, and share our success with others by involving others in the Kyäni opportunity or contributing to the Potato Pak and Caring Hands programs.
Page Under Construction.
Page Under Construction.
Training / Knowledge / Solution Platform
Plastic Occupational Diseases
If plastic production workers experience at least one of these ailments; should immediately notify the occupational physician of the situation:
-
Dryness, cracking, redness and formation of fluid-filled blisters in the skin area
-
Headache, drowsiness, distraction and nausea
-
Unusual feeling of tiredness
-
Feeling of heart palpitations without exertion
-
Frequent chills in your arms or legs, a feeling of goosebumps
-
Frequent irritability or malaise
-
Frequent difficulty in focusing attention on any subject
-
Feeling of memory weakness or your loved ones complaining about your memory
-
Sweating except in exceptional circumstances
-
Difficulty turning your clothes buttons on and off
-
Beginning to have difficulty in understanding a generally read article (newspaper, book)
-
Frequent checking of things you do routinely, like locking the door, checking to see if you have the key
If these complaints occur, do not hesitate to inform your doctor about the situation to find out whether the problem is caused by your profession or not.
Occupational Diseases That May Be Encountered in the Industry
Diseases Caused by Chemical Hazards: There is a significant risk of contact dermatitis due to liquids and powders used in the plastics industry such as unsaturated polyester resins used in fiberglass production, chemically reactive phenol formaldehyde resins and urethanes. Fumes may be produced during thermal reduction of polymers with heat. However, engineering measures can be crucial in overcoming this issue. The presence of a good ventilation system in this regard is also very effective in eliminating risks.
When PVC (PolyVinyl Chloride) and Teflon (Polytetrafluoroethylene) are overheated, polymer smoke fever disease may occur due to the fumes produced. As it is known, a wide variety of plastic products are used in many industries. Many of these plastic products can sometimes be exposed to thermal stress, ie extreme heat. In cases where paint-coated metal plates or sheets or plastic-coated pipes are exposed to high heat during the welding process, volatile gases in toxic amounts are produced.
The table below lists some plastics and the volatile gases they produce when exposed to heat.

The toxic fumes of isocyanates used with polyurethane resins cause chemical pneumonitis and severe asthma. Once a person becomes sensitive to these fumes, he has to change jobs. The same danger exists when working with formaldehyde resins. Very high amounts of styrene vapor are used when producing fiberglass. This causes the diseases listed above. Solvents such as chlorinated hydrocarbons are frequently used in the industry. Inhalation of these can also cause serious hazards, one of the most important of which is narcosis.
Diseases Caused by Physical Hazards: Granulators (pollinators) make a lot of noise when working. This noise is sometimes at such high levels that those who work next to these machines and those who manage these machines encounter temporary and sometimes permanent hearing (hearing) losses.
Burn Accidents: Some additives and catalysts used for plastic production can be extremely reactive when they come into contact with water or air and cause burns. While working with molten plastics or transporting from one place to another, it can always spill and splash, and eventually burns and scalding may occur. In addition, some plastics have a danger of sticking to the skin, in which case the damage caused by burns increases. Organic peroxides are highly irritating and can blind a person, especially if splashed into the eyes. As in every line of business where chemicals are heavily used, the risks of fire and explosion are high in the plastics industry. All machines used in pressure, transfer, injection and spin molding processes are processed using press pressure with a locking force of many tons per square centimeter. As a result of the workers working in these machines getting stuck or hitting the pressure plate of the machine, limb ruptures may occur.
About Occupational Health and Safety
As mentioned, granulators make a lot of noise. Although it varies from country to country, normally a maximum of 85-90 dBA sound exposure for eight hours is possible, followed by a 16-hour rest period under 80dBA. If you are exposed to sound above 85-90 DBA, ear protection equipment should be used, otherwise, hearing problems will definitely occur in the future. In addition to these, at least annual audiometry (audibility) tests should be performed regularly. In addition, personal dosimeters should be available in workplaces where noise is high. These risks can be eliminated by covering the machines with sound-killing materials. The vapors, fumes, odors and dusts of the chemicals used adversely affect the respiratory tract and cause many diseases mentioned before. Local forced draft ventilation systems that work extremely well against these risks are needed. In addition to these, masks and respirators, which are respiratory protective equipment, can be used.
The chemicals used and produced during the production of plastics create fire and explosion hazards. Material Safety Data Sheets (MSDS) of large quantities of chemicals kept in warehouses and small quantities used for processing should be examined to prevent chemicals from posing a hazard. Precautions against fire and explosion should be taken based on the information on the forms. In addition, the fire extinguishing equipment to be used and the places where they should be located should be determined by considering the locations of the chemicals and the types of fire they will cause.
There are two types of recycling processes in the plastics industry. The first is to plasticize the polymer using heat, take the desired shape with mechanical restraint, and keep it in that state by cooling and compression. The second is that the polymerizable material is completely polymerized and cooled by heat or catalyst so that it retains its shape under mechanical restraint.
There are many different conversion process methods used in the industry. Pressure Molding This method involves heating the granular or powdery plastic material in the mold held by the press. After the material turns into plastic with heat, it is ensured that the mold takes its shape by using pressure. If the plastic is a type of plastic that hardens by heating, the press is opened after a short time of heating. If the plastic is a non-heat-hardening type, cooling should be done before the press is opened and the part is removed. One of the dangers to be encountered during the use of the tool is the pinching of the hands under the press. To prevent this, two-hand control systems should be used. In addition, the machine guard parts must be in place according to the manufacturer's instructions. Local ventilation systems should be installed in order not to inhale the chemicals that evaporate during heating. Personal Protective Equipment should be used when necessary.
Since working with hot plastic, the operator must wear heat-proof gloves while removing the shaped plastics from the mold. During the mold change, care should be taken that the upper table is up and fixed.
Injection Molding In injection molding, plastic particles or powders are heated in a barrel. When it becomes liquid, it is poured into the mold with the help of rotating spiral screw. Afterwards, it is expected to cool and harden in the mold. It is the most widely used molding method since many kinds of small, large, simple and complex parts can be produced with this method. The following safety precautions should be taken when using injection molding machines. When the covers of the injection molding machine are open, the hands and head should not be inserted between the vise and scissor arms. Hot working areas of the injection molding machine should not be touched.
While the injection machine is running, no action should be taken on the mold and the moving parts of the machine. The operator should not leave the machine while the machine is running. Work apron should be worn while using the machine. The surfaces of the mold parts should be lubricated against corrosion. The compatibility of the mold to be attached to the machine should be checked for the machine's specifications. The settings of the clamp unit should be made according to the dimensions of the mold used. Make sure that the machine guards are in working condition and in place.
Since the liquefied plastic is at a high temperature, the operator should wear gloves. Local ventilation systems should be installed to prevent inhalation of evaporating chemicals. If necessary, the operator and those working in the environment should use respiratory protection. Plastic Extrusion Plastic extrusion pipe, hose, cable, profile etc. It is a manufacturing method used in the production of plastic materials. The machine used in extrusion is very similar to the injection machine. A motor turns the screw in a sleeve covered with a heater, causing the plastic granules to melt under temperature and pressure. The molten plastic takes shape along the mold and enters the liquid in the form of a long channel to cool. The shape of the mold also determines the shape of the duct. After cooling, it takes shape as solidified. The channel can be marked and then cut at equal intervals. While using this method, splashing of liquid flowing plastic can cause serious burns on the body. Therefore, operators should wear protective fireproof work clothes and gloves. In addition, respiratory protection should be used against smoke inhalation. Hands should be kept away from moving rollers. Calming In this method, the plastic passes between two counter-rotating heated rollers and is then cooled.
Sheets thicker than film are produced by this method. Thin sheets produced by this method are used in the textile and toy industries. When using the Calming/Rolling method, a body barrier should be provided to prevent the operator's arm from being caught between the rollers. The operator should not use loose clothing and gloves that can get caught between the rollers.
Respiratory protection should be used against smoke inhalation. Blow Molding It is a forming method in which the shape of the mold is given by pressing air into a hollow tube with a pipe that goes down to the mouth of the mold. With this method, hollow materials such as bottles are produced. During the use of blow molding machines, care should be taken that the machine guards are in place. Since serious injury may occur in case of contact with the moving parts of the machine, the moving parts should be avoided while the machine is running. Local ventilation systems should be established to prevent inhalation of polymer fumes and respiratory protection should be used if necessary.
Round molds are used in Rotational Molding. It is a method that aims to reduce the effect of gravity by rotating the mold containing powder or liquid plastic, and to distribute the plastic evenly throughout the mold. The heating process is carried out with heaters in the region where the rotational movement is made. With this method, balls and similar shaped toys can be obtained. After the plastic is heated and takes the shape of the mold, the mold and the plastic inside are cooled by using methods such as waiting in the open air or soaking in water. When the time required for the plastic to harden has passed, the mold is opened and the burrs on the product are cleaned. When using this method, heat-proof gloves should be used to avoid direct contact with the heat.
Hands should not be put into the area where the rotational movement is made. The oven door must be closed before starting the rotation process. There should be no material other than mold inside the oven.
In the Cast Film method, the film is obtained by ejecting the hot polymer onto well-polished metal pulleys or by spraying a polymer solution onto the moving belt. In this method, very thin plastic sheets are produced continuously. This method is also used extensively for paper and board coating works. During the use of this method, local ventilation systems should be established to prevent the worker from breathing polymer vapors and respiratory protection should be used when necessary. It should be ensured that the machine guards of the machine used are in place and in working condition.
Thermoforming, that is, thermoforming production method, is to heat the plastic material formed into sheets in the oven and to make it between fluid and non-fluid, then push it towards the mold with compressed air and take the shape of the mold. In addition, in vacuum systems, methods are used in which the leaf takes the shape of the mold by pulling the air inside the mold. The material is separated from the mold by giving air between the mold and the leaf. With this method, food packages, round or rectangular containers and lids can be produced.
Personal Protective Equipment Materials
It has been determined by ILO (International Labor Organization) Article 16 - Occupational Health and Safety Convention that employers have duties regarding the provision and use of Personal Protective Equipment (PPE) materials in the workplace.
PPE materials are equipment that will protect the user against accident risks or adverse health effects. They can be listed as helmets, gloves, eye protection, high-visibility (phosphorescent) clothing, safety shoes, safety belts and respiratory protective equipment.
Making the workplace safe includes providing instructions, procedures, training and supervision to encourage people to work safely and responsibly. Even where engineering controls and safe work systems are in place, some work hazards may still exist. For example, breathing polluted air; materials that may fall on the head and feet, flying particles that may get into the eyes or liquids that may splash abrasive, extremely hot or cold environments, etc. In these cases, PPE materials are required in order to reduce the risk and to protect the health of people from security measures that seem deceptive as if they are unlikely to happen.
PPE materials should be seen as complementary equipment after basic occupational safety has been taken. It should never be considered an essential primary security measure. PPE materials must be provided by the employer to their employees free of charge. For the selection and use of PPE material, employers themselves; Who and what are they exposed to? How long are they exposed? How much exposure are they? should ask questions.
When choosing PPE materials, products with risk compliance and required standards should be preferred. The size, fit and weight of the material should be taken into account. If more than one PPE material is used at the same time, it should be ensured that they can be used together, people should be taught and trained on how to use them. Especially and especially the working personnel should be told why this equipment is necessary, when to use it and what its limitations are.
Vehicles in the workplace Every year, accidents involving vehicles used in the workplace occur, some of which cause deaths. People are tipped over, crushed or crushed into fixed parts by vehicles (eg heavy vehicles, forklifts and tractors), factories and trailers. People fall from vehicles whether they are getting on or off, working at height, or loading or unloading. Unsuitable tools can also damage the working environment due to the exhaust fumes they can produce.
The first answer to the question of what else should employers do is to consider whether there is an easier, safer way to do the job. Risk assessments should consider all workplace moving activities such as loading and unloading.
all vehicles and people moving around workplaces should be carefully observed, and traffic and pedestrian movements should be marked on a plan so they can see where pedestrians and vehicles interact; Improvements that will reduce the contact between pedestrians and vehicles should be determined.
In addition to continuous work, occasional work should also be evaluated. Such as emptying and cleaning the area where the wastes are collected. Work areas should be planned so that pedestrians are safe from vehicles. In other words, although the layout of the machines in the machine park is according to the order of work flow, it should also be determined for work safety. Transitions between departments within the enterprise should be provided with a one-way system, if possible. Where possible there should be separate roads for pedestrians and vehicles. If possible, there should not be a situation that would force to go back.
It should be ensured that the road surfaces are solid and flat. Ensure that there are safe areas for loading and unloading. Where possible, the need for people to climb into vehicles should be eliminated, for example by providing indicators and controls that are accessible from ground level. If possible, the risk of falling should be reduced when people need to climb into a vehicle or trailer by providing well-made ladders, non-slip walkways and handrails.
Employers should never allow exemptions from wearing PPE materials, even for jobs that 'take only a few minutes'.
Employers should check with the supplier which PPE material is suitable, they should explain what work they do and the qualities of the work to the suppliers. Employers should seek further advice from an expert advisor if in doubt.
PPE materials should be properly cared for and stored in a dry, clean cabinet when not in use. If it is reusable, it should be cleaned and kept in good condition. Spare parts of PPE materials (for example, filters of breathing masks) that are disposable units must be available, and the stock must not be allowed to be reset.
Types of PPE materials that can be used
For eyes:
Hazards: Chemical or metal splash, dust, bullets, gas and vapor, radiation.
Options: Safety glasses, goggles, face shields, face shields and visors, visors.
Note: Make sure the eye protection chosen has the correct combination of impact/dust/splash/molten metal eye protection. fit for the task and suit the wearer.

Even though we are not aware of the work glasses we use every day at work, they have passed certain tests. The work glasses that have passed these tests successfully have certain markings in line with the tests made. It is a legal obligation to indicate these markings on the glasses (frame and lens) together with the manufacturer's logo and the CE symbol. As with gas masks and other occupational safety equipment, some products with American standards are sold. This gives rise to the impression that American standards are used in our country. ANSI is the American standard and EN European standards are used in our country.
ANSI: American National Standards Institute
EN: European Standards (European Norm)
Work Glasses Standard Markings All work glasses parts must have passed the EN 166 European standard.
EN 166 is a more comprehensive standard of work glasses standards used in America and Asia. The tests and markings made within the scope of this standard are as follows.
Business glasses frame markings: Eyeglass frames may have one or more of the following markings.
3 – It provides sealing and protection against various liquid droplets and liquid splashes.
4 – It is impermeable to dust and dust particles larger than five microns.
5 – It does not pass dust smaller than five microns.
S – Resistant to small objects striking at 12 m/s.
F – Resistant to small objects hitting at 45 m/s.
B – Resistance to small objects hitting at 120 m/s.
A – Resistance to small objects hitting at 190 m/s.
T – The impact resistance of the glasses is not lost in hot environments and its durability continues.
Since the lenses are the main part of the glasses, the markings and protection standards are more complex than the eye frames.
EN 167 Managements for optical testing
Tests other than EN 168 Optical tests
EN 166 (TS 5560 EN 166)- Safety glasses impact resistance and optical quality
EN 169 ( TS EN 169) - protection from welding rays
EN 170 (TS EN 170)- protection from ultraviolet rays
EN 171 (TS 8435 EN 171)- Protection from infrared rays
EN 172 (TS EN 172)- sun protection
EN 175 Face protection equipment in welding operations
EN 207 Protection against laser
EN 208 Protectors for laser beam alignment
EN 379 Arc welding protective equipment
EN 1731 Cage type eye and face protectors
Signs of Protection from Radiation Rays:
2 – Glasses affect the visibility of colors, provide protection according to EN 170.
3 – Glasses do not affect the appearance of colors, they provide protection according to EN 170.
4 – Infrared (IR) protection for hot environments provides protection according to EN 171.
5 – Ultraviolet protection provides protection according to EN 172. It does not protect from infrared rays.
6 – Ultraviolet protection provides protection according to EN 172. It also provides protection against infrared rays.
Lens Darkness Marks: The work glasses are marked as follows according to their light transmission levels. The darkest glasses are marked with 3.1.
1.2 – It transmits incoming light with a percentage in the range of 74.4% to 100%.
1.7 – It transmits incoming light with a percentage in the range of 43.2% to 58.1%.
2.5 – It transmits incoming light with a percentage in the range of 17.8% to 29.1%.
3.1 – It transmits incoming light with a percentage in the range of 8.0% to 17.8%.
Lens Impact Resistance Marks: These are the protection class marks against burrs, which is one of the main purposes of work glasses. It should be noted that work glasses provide protection against small parts.
F – Resistant to small object impacts up to 45 m/s.
B – Resistance to small object impacts up to 120 m/s.
A – Resistance to small object impacts up to 190 m/s.
T – Temperature resistance for hot work areas.
Glasses Lens Quality: Lens selection should be made according to the wearing time of work glasses. Glasses with high lens quality should be used for long-term use.
1 – High lens quality. It is suitable for use for a long time due to its low level of refraction of light.
2 – Medium lens quality. It is suitable for use at intervals, as the level of refraction is medium. Long use may cause eye discomfort.
3 – Poor lens quality. Since the level of refraction is high, it should be used in emergencies and for a short time. Long-term use may cause dizziness and eye disorders.
For head and neck:
Hazards: Impact from falling or flying objects, risk of head bumps, hair entanglement, chemical drips or splashes, climate or temperature.
Options: Industrial safety helmets, protective caps, hair nets and firefighter helmets.
Note: Some safety helmets include or may be fitted with specially designed eye or hearing protection. Do not forget about neck protection, for example, scarves for use during welding. Replace the head guard if damaged.
TS EN 812 Heads used against impact (Cap)
TS EN 397+A1 Industrial helmet
TS EN 50365 Electrically insulated helmets for use in low voltage facilities
TS EN 12492 Protective caps for mountaineers




For ears:
Hazards: a combination of noise, sound level and exposure time, very loud sounds are a hazard even if they are of short duration.
Options: Earplugs, earplugs, semi-plugged/canal covers.
Note: Provide the right hearing protectors for the type of job and make sure workers know how to wear them. Choose shields that reduce noise to an acceptable level while allowing for safety and communication.
TS EN 352-1 Ear concealers
TS EN 352-2 Earplugs
TS EN 352-3 Protective earmuffs attached to an industrial safety helmet
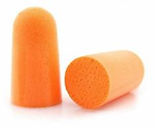



For hands and arms:
Hazards: Abrasion, extreme temperatures, cuts and punctures, impact, chemicals, electric shock, radiation, biological agents, and prolonged immersion in water.
Options: Gloves, cuffed gloves, mittens, and sleeves that cover part or all of the arm.
Note: Avoid gloves when operating machinery such as bench drills where gloves can become jammed. Some materials are quickly penetrated by chemicals, be careful with selection, Barrier creams are not reliable and do not replace proper PPE Wearing gloves for a long time can make the skin hot and sweaty, which can lead to skin problems Using separate cotton inner gloves can help prevent this.
TS EN 420+A1 General Protective Gloves
TS EN 388 Protective Gloves Against Mechanical Risks
TS EN 407 Protective Gloves Against Thermal Risks (Heat and/or Fire)
TS EN ISO 374-1 Protective Gloves for Chemical Risks
TS EN ISO 374-5 Protective Gloves for Microorganismal Risks
TS EN 421 Protective Gloves Against Ionizing Radiation and Radioactive Contamination
TS EN 1149-1-2 Electrostatic Properties, Protective Gloves in the Process of Measuring the Electrical Resistance of the Material
TS EN 14328 Gloves and Sleeves Providing Protection Against the Cuts of Power Operated Knives
TS EN 511 Protective Gloves Against Cold
TS EN 659+A1/AC Protective Gloves for Firefighters
TS EN 1082-1/2 Protective Gloves and Sleeves Against Knife Cuts and Stings
TS EN 12477/A1 Protective Gloves for Welders
TS EN 60903 Protective Gloves for Working Under Electrical Voltage
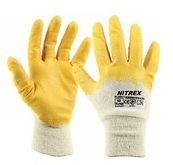



For feet and legs:
Hazards: Wet, hot and cold conditions, electrostatic build-up, slips, cuts and punctures, falling objects, heavy loads, metal and chemical splashes.
Options: Boots and safety boots and shoes with a protective toe and puncture-resistant, midsoles and special shoes, such as foundry boots and saw boots
Note: Shoes can have a variety of sole patterns and materials to help prevent slipping in different conditions, including soles that are oil or chemical resistant. It can also be antistatic, electrically conductive or thermally insulating. Shoes should be selected according to the identified risks.
TS EN ISO 20345 Safety shoes
When tested at an energy level of at least 200 Joules (equivalent to a fall of an object of approximately 20 kg from 1 meter), with protective features from injuries caused by an accident, with a nose guard, at least 15 kN (about 1.5 tons) They are defined as footwear designed to provide protection against compression with a compression force of ).
TS EN ISO 20346 Safety shoes
Footwear designed to provide protection against compression with a compression force of at least 10 kN (1 ton) against impact when tested at an energy level of at least 100 J, fitted with a toe cap, which has protective features from injuries occurring in the event of an accident.
TS EN ISO 20347 Work shoes
Except for any of the mechanical risks (impact or compression), it is a footwear that has protective features from injuries that may occur during an accident. Compared to safety and protective footwear, it does not provide protection against impact and pinching as it does not have a toe protector.
TS EN 50321 Electrically insulated shoes for working in low voltage facilities
Insulating shoes used for working under energy or close to energized parts in facilities not exceeding 1000 V
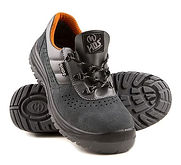


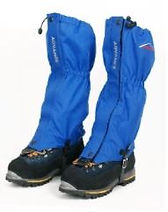
For the lungs:
Hazards: Oxygen-deficient environments, dusts, gases and vapors
Options: respiratory protective equipment (RPE) Some respirators rely on filtering pollutants from the workplace air. These include simple filter face masks and respirators, and power assisted respirators. Users should ensure proper fit of the RPE, for example for tight-fitting respirators (filtering face masks, half and full masks). There are also types of respirators that provide an independent source of breathing air, such as a fresh air hose, a compressed airway, and a self-contained breathing apparatus.
Note: The correct type of respiratory filter should be used as each is only effective for a limited number of substances. Filters only have a limited lifespan. Use only respirators, never filter cartridges, when there is a risk of oxygen deficiency or unconsciousness due to exposure to high levels of noxious fumes. Respiratory equipment will be required if there is a possibility of oxygen deficiency in a confined space or work area.
TS EN 136 General respiratory protective devices
TS EN 140 Half masks and quarter masks
TS EN 143 Dust filters
TS EN 149 - Filtering half masks against particles.
TS EN 14387 Gas filters and combined filters.
TS EN 12941 Reinforced filter devices used with helmets or hoods.
TS EN 12942 Power assisted filter devices with full face masks, half masks or quarter masks.
TS EN 14594 Continuous flow compressed air line breathing apparatus.
TS EN 1835 Devices with compressed air line, helmet or headgear connected for use under limited conditions.

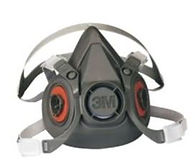

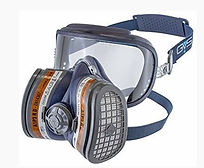
For the whole body:
Hazards: Heat, chemical or metal splashes, spray from pressure leaks or spray guns, contaminated dust, impact or penetration, excessive abrasion, or tangling of your own clothing.
Options: Traditional or disposable coveralls, boiler suits, aprons, chemical suits.
Note: Material selection includes flame retardant, antistatic, chain mail, chemically impermeable and high visibility.
Do not forget about other protection such as seat belts or life jackets. Emergency equipment Careful selection, maintenance, and regular and realistic operator training are required for emergency equipment, such as a compressed air escape respirator, respirators, and safety ropes or harnesses.
EN 340 covers the general performance characteristics of protective clothing on ergonomics, harmlessness, designation of size, aging, compatibility and marking, and information to be provided by the manufacturer with the protective clothing.
EN 343 Protective clothing that provides protection against precipitation (such as rain, snowflakes), fog and ground moisture.
EN 20471 Protective clothing that does not allow the user to be noticed in dangerous situations under the illumination of vehicle headlights.
EN 1149-5 Protective clothing with antistatic properties
EN 1073-2 Protective clothing against radioactive contamination
EN 14127 Reusable and limited use protective clothing protecting against pathogenic organisms
Type 6 (EN 13034) Protective clothing against liquid chemicals.
Type 5 (EN ISO 13982) Protective clothing used against solid particles.
Type 3, Type 4 (EN 14605) Protective clothing for only part of the body against liquid chemicals.
EN 469 Protective clothing for firefighting and rescue work, relief during disasters.
EN ISO 13911 Protective clothing worn during fire fighting and related activities
EN ISO 11611 Protective clothing used in welding works and related processes.
EN ISO 11612 Protective clothing to protect the body from heat and/or flame, excluding hands.
EN 61482-1-2 Protective clothing against heat and flame where electric arc occurs.
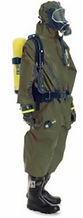





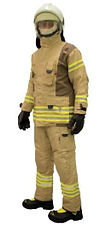
For Falls from Height:
TS EN 354 Fastening device against falling from a certain height
TS EN 355 Personal protective equipment against falling from a height, energy absorbers
TS EN 358 Retaining systems to prevent falling, belts and ropes for working position
TS EN 360 Rewind type fall arresters
TS EN 361 Full body belt systems
TS EN 362 Connectors
TS EN 341 Downloading devices
TS EN 795 Anchor devices
TS EN 813 Seat belt
TS EN 12275 Mountaineering equipment, Attachment rings


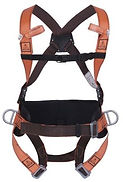

