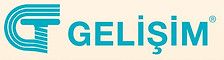


Hydrocarbons
It is an organic compound consisting of two elements, hydrogen and carbon. Most of the petroleum composition consists of hydrocarbons of varying lengths.
The smallest hydrocarbon methane consists of a single carbon atom and four hydrogen atoms. However, hydrocarbons can consist of hundreds or thousands of individual atoms linked together in many ways, including chains, circles, and other complex shapes.
In order to classify the properties of hydrocarbons, they are divided into several basic types.
Alkanes: These are called saturated hydrocarbons. That is, they only contain single bonds between all carbon atoms. Alkanes are the basis of petroleum fuels and exist in linear and branched forms.
Unsaturated Hydrocarbons: Hydrocarbons that have one or more double bonds between carbon atoms are called alkenes.
Cycloalkanes: Any hydrocarbon containing one or more ring structures.
Aromatic Hydrocarbons: Aromatic hydrocarbons , also called arenes, are a unique class of carbon molecules in which carbon atoms are bonded by successive double and single bonds. This class of molecules has special ring structures in which the bonds between carbon atoms are an intermediate bond between single and double bonds.
Molecules in this class contain the industrial solvent "benzene".
Benzene (C6H6): Like other hydrocarbons, benzene is a natural component of petroleum. It is a colorless, flammable, sweet-smelling liquid at room temperature and is a component of most gasoline blends because of its high octane number.
Benzene is also highly carcinogenic and is well known to cause bone marrow failure and bone cancer. Of course, its carcinogenicity is not well known when used as an additive in aftershave and other cosmetics due to its "pleasant aroma".
The largest use of benzene (50%) is the product of styrene and polystyrene plastics. It is also converted into a molecule known as cyclohexane, which is important in Nylon production. About 15% of benzene is used to produce cyclohexane. Smaller amounts are used in everything from pesticides to rubber.
The benzene structure can be drawn in two ways. In the first, the double bond character is drawn explicitly. In the short handed version, a circle is drawn inside the ring to show the structure. There is only one hydrogen bonded to each carbon atom in benzene.
I. and II below. drawings are identical. III in practice. drawing is used.
Benzene is a colorless, flammable liquid with a boiling point of 80.1 ° C and a melting point of 5.5 ° C.
Binuclear Aromatic Hydrocarbons: They are compounds that contain two benzene rings in their molecules.
Hydrocarbons
It is an organic compound consisting of two elements, hydrogen and carbon. Most of the petroleum composition consists of hydrocarbons of varying lengths.
The smallest hydrocarbon methane consists of a single carbon atom and four hydrogen atoms. However, hydrocarbons can consist of hundreds or thousands of individual atoms linked together in many ways, including chains, circles, and other complex shapes.
In order to classify the properties of hydrocarbons, they are divided into several basic types.
Alkanes: These are called saturated hydrocarbons. That is, they only contain single bonds between all carbon atoms. Alkanes are the basis of petroleum fuels and exist in linear and branched forms.
Unsaturated Hydrocarbons: Hydrocarbons that have one or more double bonds between carbon atoms are called alkenes.
Cycloalkanes: Any hydrocarbon containing one or more ring structures.
Aromatic Hydrocarbons: Aromatic hydrocarbons , also called arenes, are a unique class of carbon molecules in which carbon atoms are bonded by successive double and single bonds. This class of molecules has special ring structures in which the bonds between carbon atoms are an intermediate bond between single and double bonds.
Molecules in this class contain the industrial solvent "benzene".
Benzene (C6H6): Like other hydrocarbons, benzene is a natural component of petroleum. It is a colorless, flammable, sweet-smelling liquid at room temperature and is a component of most gasoline blends because of its high octane number.
Benzene is also highly carcinogenic and is well known to cause bone marrow failure and bone cancer. Of course, its carcinogenicity is not well known when used as an additive in aftershave and other cosmetics due to its "pleasant aroma".
The largest use of benzene (50%) is the product of styrene and polystyrene plastics. It is also converted into a molecule known as cyclohexane, which is important in Nylon production. About 15% of benzene is used to produce cyclohexane. Smaller amounts are used in everything from pesticides to rubber.
The benzene structure can be drawn in two ways. In the first, the double bond character is drawn explicitly. In the short handed version, a circle is drawn inside the ring to show the structure. There is only one hydrogen bonded to each carbon atom in benzene.
I. and II below. drawings are identical. III in practice. drawing is used.
Benzene is a colorless, flammable liquid with a boiling point of 80.1 ° C and a melting point of 5.5 ° C.
Binuclear Aromatic Hydrocarbons: They are compounds that contain two benzene rings in their molecules.
About
Kyäni, nutritional supplement products consisting of beneficial ingredients; It delivers to more than 50 countries around the world with unique business opportunities. We use Kyäni products daily to maintain our ideal health, share these products with others, devote a certain amount of time to work almost every day to build and maintain our business, and share our success with others by involving others in the Kyäni opportunity or contributing to the Potato Pak and Caring Hands programs.
About
Kyäni, nutritional supplement products consisting of beneficial ingredients; It delivers to more than 50 countries around the world with unique business opportunities. We use Kyäni products daily to maintain our ideal health, share these products with others, devote a certain amount of time to work almost every day to build and maintain our business, and share our success with others by involving others in the Kyäni opportunity or contributing to the Potato Pak and Caring Hands programs.
Page Under Construction.
Page Under Construction.
Training / Knowledge / Solution Platform
composites
B.C. In 3400, the first composite was developed in Iraq by the Mesopotamians. Ancient society glued wooden strips together at different angles to create plywood.
Following this, in 2181 BC, the Egyptians began making death masks from linen or papyrus dipped in plaster. Later, both communities began to supplement their materials with adobe, pottery and straw to strengthen the boats.
Mongols in the 1200s composite spring engineering began. They did not use composite structures of wood, bamboo, bone, cattle tendons, horn, and silk bonded with pine resin.
After the industrial revolution, synthetic resins began to be obtained in a solid form using polymerization. new experiences began to be gained in composite structures as well. There were developments in the field of bakelite by the chemist Leo Baekeland. Being non-conductive of electricity and being heat resistant meant it could be widely used in many industries.
The 1930s was an incredibly important time for the advancement of composites. Glass fiber was introduced by Owens Corning, who also started the first fiber-reinforced polymer (FRP) industry. Resins designed during this period are still used today, and unsaturated polyester resins were patented in 1936. Two years later, higher performance resin systems became available.
The first carbon fiber was patented in 1961 and later made commercially available. Then, in the mid-1990s, composites began to become increasingly common in manufacturing and construction due to their relatively inexpensive cost compared to previously used materials.
In the mid-2000s, composite structures on the Boeing 787 Dreamliner proved their use for high-strength applications.
Weight savings is one of the main reasons to use composite materials for components instead of traditional ones. While composites are lighter, they can be stronger than other materials; For example, reinforced carbon fiber can be five times stronger than 1020 grade steel and only one-fifth the weight, making it perfect for structural purposes.
Another advantage of using a composite over a conventional material type is its thermal and chemical resistance and electrical insulating properties. Unlike conventional materials, composites can have multiple properties that are often not found in a single material.
Fiber-reinforced composites such as fiber-reinforced plastics (FRP composites) are finding increasing use in the design and manufacture of final products for commercialization.
electrical equipment
space structures
infrastructure
Pipes and tanks
Homes can be framed using plastic laminated beams
A composite material is a combination of two materials with different physical and chemical properties. When combined, they create a material customized to do a particular job, such as being stronger, lighter or electrically resistant. They can also increase strength and stiffness. The reason for their use over conventional materials is that they improve the properties of their base materials and are applicable in many situations.
They are new materials created by combining at least two different materials in such a way that they do not dissolve in each other. The aim is to gain some properties (lightness, strength, flexibility, etc.) that are not available in the main material alone. There is no exchange of atoms between the components that make up the composite structure, and they do not affect each other chemically. Composites generally consist of a base material called "matrix" and a stronger material called "reinforcement".
Biocomposites: They are materials consisting of biodegradable polymers (matrix) and biodegradable reinforcing materials. Biodegradable material is substances that can be degraded by living organisms. Biocomposites (BBC) made from natural biofibers are renewable, lightweight, energetic, biodegradable and environmentally friendly. Today, it can be said that polymer science and technology has focused on composites made from renewable resources. (Go to the relevant topic for more information)
Nanocomposites: A class of materials in which one or more phases that make up the composite are nanoscale (<100 nm) in size. The general idea in the addition of a nanoscale phase is to achieve the desired high performance properties of the material by creating a synergy between the various components. When the particle sizes are at the nanometer level, the interactions at the interface in the composite are very high, so the properties of the material improve tremendously.
The following terms are frequently used when describing the composite manufacturing process:
Part: The finished product you are making.
Stopper: The original item to be copied in fiberglass or other composite materials used to create the mold. The plug can be a real piece or a custom shape made from almost any material.
Pattern: The product from which the part will be made. There are two main types of molds, male and female. A male mold is the same as the copied product and the part is made on the mold. The female or cavity die is the opposite of the item to be copied and the part is made inside the die. The word can also be used to describe the composite manufacturing process: molding a part.
Laminate: A solid piece made from a combination of resin and reinforcement fabric. The term can also be used to describe the process of laying a part: Laminating a part.
Gel Coating: (or Surface Coating) The term gel coating is generally used to describe any resin-based surface coating, although the term technically applies to polyester-based materials. The term surface coating can be used to describe epoxy or polyester materials. Surface coatings are specially formulated, thickened versions of resin that can be applied to the surface of a mold or part to act as a cosmetic and protective coating.
Release Agent: Any material applied to the mold surface prior to part fabrication to help the part come out of the mold. These can be waxes, oils or special release coatings such as PVA.
Flange / Baffle Dam: A temporary fixture that plugs in when creating multi-part moulds. This creates a surface for the materials to be molded, usually perpendicular to the parting plane of symmetry. The flange assists in clamping or bolting the mold sections together and also acts as a mounting point during vacuum bagging operations.
Matrix: It is the main carrier that holds the structure together by preventing the deformation of the composite structure.
Reinforcement: It is the additive material that will characterize the property of the matrix. They are known as fibers. It is used to provide strength resistance, electrical, sound, heat, light conductivity or insulators, hardness or softness, lightness or weight, color aesthetics, but most of all, economy. Generally, carbon, glass, aramid, calcite, talc are used as reinforcements. In addition to all these, the main goal in the production of composite materials is to make the economic conditions more suitable.
For this reason, calcite (CaCO3) is the most used material as reinforcement to increase the existing polymeric density.
Composites are divided into four classes matrixically.
Polymer Matrix Composites (PMC): As there are resins such as epoxies and polyesters, their use in structural production is quite limited; Materials such as glass, aramid and boron have high tensile and compressive strength, but these properties cannot be used in solid state, they break at values below the optimum strength properties when tension is applied.
Metal Matrix Composites (MMC): Composites consisting of a flexible metal matrix and reinforcement materials; Although the matrix is always defined as a metal, it is metals and light metal alloys. The operating temperatures of metal matrix composites are around 200-800 0C; therefore it is suitable for environments requiring high temperature applications.
Ceramic Matrix Composites (CMC): Ceramic or glass matrix CMCs are composites suitable for the production of advanced engineering structural materials. Although high temperature applications are limited, it has a wide range of uses in military, aerospace and commercial (such as energy-efficient systems and transportation).
Carbon-Carbon Composites (CCC) : Both the reinforcement and the matrix phase are carbon. Monolithic graphite is brittle and not a strong material. CCCs are fairly new and expensive; therefore its usage areas are not widespread. The tensile strength and tensile modulus are high and they can maintain these performances up to very high temperatures such as >2000 °C.
The discovery of carbon fibers in the late 1950s led to the development of improved materials now known as carbon-carbon CCC composites. These composites are a family of materials consisting of a carbon (or graphite) matrix reinforced with carbon (or graphite) fibers. Thus, the attractive properties of carbon are combined with the high strength, versatility and toughness of composites. The CCC family is unique in that it is the only basic composite.
Carbon-carbon composites range from simple unidirectional fiber-reinforced structures to complex woven 3-dimensional structures. The variety of carbon fibers and versatile weaving techniques currently available allow the CCC to be tailored to meet complex design requirements. With the choice of fiber type, insertion (or fiber-weave), matrix and composite heat treatment, properties can be tailored to different applications.
In the early 1960s, carbon-carbon composites were developed for high-temperature aerospace applications such as nose cones and rocket nozzles. These composites can be tailored to higher strengths and hardness than other engineering metallic alloys and, unlike metals, can retain these properties at elevated temperatures, as shown in Figure 1.
However, the manufacturing costs of these materials are high and this has limited their use currently primarily to aerospace and military applications. Therefore, an improvement in carbon efficiency will result in a reduction in costs. A pressure increase from ambient to 100 MPa where a 50% carbon yield is achieved increases the carbon yield to 90%. This is the basis for high pressure carbonization and pyrolysis, a technique explored by TWI et al.

Reinforced plastic: Since approximately 90% of composites are produced from polymer (plastic) based matrices, reinforcements to composite materials Also called plastics.
In composite materials, the fibers remain inside the material. They are the matrices that surround the material and are exposed to external factors. For this reason, matrices determine the basic property of composites.


Fundamental Functions of the Matrix
By keeping the matrix fibers together, the bridge acts according to the load transfer to the fibers. It gives rigidity and shape to the structure. The matrix insulates the fibers from each other. Thus, the fibers behave independently of each other in one aspect. This, for example, stops and slows crack propagation.
The matrix provides good surface quality. The matrix protects the fibers against mechanical damage such as abrasion and various chemical effects.
Depending on the properties of the selected matrix material, the performance characteristics of the composite such as ductility and impact resistance are also affected. A more ductile matrix can increase the fracture toughness of the structure. For example, thermoplastic-based composite materials are chosen for high toughness. The properties of the matrix used and its compatibility with the fiber significantly affect the damage modes (mechanisms) that occur.
A matrix must have a high ability to adhere to the fiber. As the adhesion ability increases, the loads move from the matrix to the reinforcement.
sufficient amount can be transferred. In addition, splitting or breakage at the fiber-matrix interface under tension is prevented.
Expected properties from matrices used in composite material production:
1. Having good mechanical properties
2. Good adhesion
3. Good toughness properties
4. It can be listed as being resistant to environmental effects.
Resin Types
A composite structure consists of a thermosetting resin used in conjunction with some type of reinforcement, such as a woven fiberglass fabric. There are three main types of room temperature curing resins used in composite manufacturing: 1- Polyester, 2- E- pox , 3- Vinyl Ester
It is a general purpose resin suitable for a wide variety of applications. As a catalyst to start the curing process Methyl Ethyl Ketone Peroxide (MEKP) should be used. Catalysis rates can be varied with polyester resins to adapt to various environmental conditions. In thin laminates or when spraying gelcoat as a topcoat, the surface may remain tacky and not cure properly if exposed to air. To achieve complete cure, thin laminates or topcoats can either be a solution of styrene wax or a coat over them to seal the air. polyvinyl alcohol (PVA) solution should be sprayed. With the former, the wax "floats" on the surface as the resin cures, acting as a barrier to air. styrene wax After hardening, it should be sanded and PVA should be rinsed with warm water. Also:
They are the most widely used resins in the composite industry.
Cheaper, Easy to use
Offers some corrosion resistance
More forgiving than epoxies
Cures fast
It is tolerant of extreme temperature and catalyst.
It is not as forgiving as polyester resins in its measurements, but epoxies provide greater part strength and dimensional stability. They also adhere to other materials better than polyester resins. Epoxy hardener ratios cannot be changed and adequate temperatures (at least 70 degrees F) must be maintained during the curing process. Epoxy resin systems tend to be more expensive than polyester resins, but are a virtual necessity in some repair applications, such as Sheet Molded Compound (SMC).
For composite parts that require ultimate strength, manufacturers will use an Epoxy Resin. Epoxies generally outperform polyester and vinyl ester for dimensional stability and greater bonding with other materials, in addition to increased strength properties.
Vinyl Ester Resins:
It mostly has qualities that fall between polyester and epoxy resins. However, it surpasses both in the areas of corrosion resistance, temperature resistance (good up to 300 degrees F) and toughness. Common uses include boat hull repair, full tank construction, and chemical storage tank linings. Like polyester resin, MEKP catalyzed by , but the vinyl ester has a shorter shelf life of three months.
Vinyl Ester Resin is considered a hybrid of polyester and epoxy - meaning its processing properties, properties and price often fall between the other two. Where Vinyl Ester differs is in its high corrosion, temperature and elongation resistance.
Composite Production Techniques
Wet Flooring
The component is formed in a mold by applying several coats of reinforcement and wet resin, which are distributed with a roller, until the desired thickness is reached. The resin is then cured using applied heat if necessary to produce the finished component.
This process is widely used in the marine industry to prepare fiberglass reinforced polyester resins. Material costs are relatively low and the process is very flexible. However, it is labor intensive and has the disadvantage of high styrene emissions.
Spray Method
A spray gun is used to apply cut fiber reinforcement and wet resin to a mold until the desired material thickness is achieved. The resin is then cured. The process is faster and cheaper than wet laying, but the mechanical properties are lower.
The process is typically used for large, relatively simple structures such as tubs, hulls, and storage tanks.
Compression Molding (SMC)
( Sheet Molding Compound ) A fiber and resin charge, which is sheet molding compound or bulk molding compound, is placed in a preheated mold, which is then sealed and held under pressure until the resin cures. The process can create a Class A surface finish, and the similarity to the stamping process used for sheet metals has led to applications in the automotive industry.
The high investment in heated tools means the process is only suitable for medium to high volume production.
Mold temperature is between 120-170°C. Molding time and molding pressure; The size of the part varies depending on its thickness and SMC type. The advantages of SMC preforming compound in overall cost/performance return over materials such as steel, aluminum and other zinc metal castings are frequently cited by designers and engineers. Many parts can be combined in a single mold. SMC products are lightweight and have high hardness and strength properties. SMC molding is generally less expensive than the metal molding process as it can be processed with a single piece of equipment as opposed to the multiple equipment required in metal molding. In addition, the construction of SMC molding equipment takes place in a shorter time. The sum of all these advantages makes SMC composite products especially attractive for automobile manufacturers. In today's automobile markets, companies are looking for ways to create economic differences in car and truck models with mass production and faster design/production programs. Based on these advantages, SMC develops impressive performance.
Although the capital investment required to manufacture and mold SMC is quite low compared to metals, it is significantly higher than for other composite processes. Therefore, it is critical that the production of SMC parts depend on the economic course of all expenditures, the volume of production, the cost of the final product and secondary operations. As SMC products have started to replace parts made of traditional materials in the market, it has become important to perform performance and economic analyzes of competing materials accurately and precisely. Investment risks are quite high for SMCs
The demand for SMC applications is also increasing in the home appliance industry. For example, the manufacture of a dishwasher inner door from SMC traditionally combines several different parts with one-stage molding compared to steel door design. The SMC dishwasher cover application proves that SMC can be used in many ways due to its superior performance in a product exposed to a chemical environment. Other SMC home appliance applications include air conditioners, refrigerators, fryers, computers and office supplies.
Injection Molding
The cast molding compound is heated and injected into a heated mold where it is held under pressure until the resin cures. The process is used for relatively small components for which a short cycle time can be achieved. The high tooling cost means the process is only suitable for medium to high volume production.
Resin Transfer Molding (RTM)
(Resin Transfer Molding) A fiber preform or fabric is placed in a heated mold. The reactive resin is mixed and injected into the mold under pressure. Pressure is maintained until the resin cures and the part is removed. The process is suitable for complex, high-load parts and is used in a wide variety of industries. Vacuum assisted resin transfer molding (VARTM) is a variant of the process in which vacuum is applied to the closed mold, allowing the resin to be injected under reduced pressure. The loads on the tools are therefore lower, allowing cheaper, larger tools to be used to fabricate large structures such as hulls or wind turbine blades. Another variant is structural reaction injection molding (SRIM). This uses highly reactive resins such that the mold does not need to be heated to cure the resin, but is often heated to reduce cycle time.
RTM parts allow a large number of parts to be molded per mold per hour, depending on the process and design conditions. Since RTM is a closed mold system, they release less volatile organic matter than open molds. Mold cycle times are shorter than hand lay-up and spraying methods. The cost of RTM molds is cheaper than the molds used in other closed molding methods. Both surfaces of the molded parts are smooth. Filling systems reduce costs, add performance features such as non-flammability and smoke-free properties, better surface appearance and higher fracture strength.
Mold and equipment costs are higher than hand lay-up and spraying methods. RTM is a production method with medium production volume. The process is more complex when it comes to adjusting injection pressures, mold design and manufacturing, and locking and sealing system.
Major RTM applications; truck body parts, automobile body panels, bus panels, spoilers, instrument panels, medical equipment, storage tanks, vehicle seats, chemical pumps, marine parts such as small boats, wind power turbine blades, aircraft parts, bullet bodies, bicycle bodies and are doors.
filament winding
A tow of fiber is passed through a resin bath and applied under tension to a convex mandrel. The mandrel is rotated and the fiber release is moved to place the fibers in the desired geometry until the desired thickness is reached. The composite is then allowed to cure using high temperature if necessary. The process can be automated for high-volume production and is used for tubular structures such as pipes and drive shafts, as well as more specialized structures such as pressure vessels or monocoque bicycle frames. In the last two applications, the mandrel will remain in the component. In one variant of the process, pre-impregnated fiber tow or slit prepreg can be used, which eliminates the need for a resin bath but requires a high temperature curing step.
prepreg
(pre-impregnated fibre) consists of fibres, fabrics or felts impregnated with resin. Thermosetting prepregs contain hardeners in the resin and therefore have a limited shelf life and are usually stored under refrigeration. Before use, the prepreg is brought to room temperature to prevent condensation and the plies are cut into the required shape and direction. These are stacked in a mold of the desired thickness using a cylinder to prevent air from being trapped. The laminate is sealed in an evacuated vacuum bag and then the part is cured in a conventional oven or an autoclave under added pressure. Autoclave processing provides less porosity and superior mechanical properties, but requires a slow cycle time and expensive equipment, especially for large components. Prepreg is used where high mechanical properties are required and high machining cost can be justified. Examples include aerospace structures, sporting goods and wind turbine blades.
Being practical during production, it eliminates the need to use any resin and hardener in addition, and the laying process is also easier due to the adhesion on the mold surface, on top of each other and the fibers do not separate, compared to non-resin-impregnated fibers. In addition, the curing time is shorter than the hand lay-up, vacuum infusion and vacuum bagging methods.
Since the resin pouring process has already taken place, there is no such thing as staying dry or absorbing too much resin. This ensures that standard products are obtained without any loss of strength in the product. Depending on the type of prepreg used, the resin/fiber ratio varies between 35% and 50%.
Production with Prepreg has advantages as well as some disadvantages. First of all, its production methods are quite expensive compared to others. In the autoclave method, the temperature is adjusted around 120-180oC in accordance with the curing graph and at the same time it is carried out under a pressure of 3-7 MPa. In oven production, the curing temperature should be adjusted to suitable temperatures. These types of autoclaves and ovens are quite expensive industrial products.
The storage conditions of the prepregs are also a big challenge for the manufacturer. Although there are varieties that can be stored for up to 4-6 weeks under room conditions, there are generally freezing conditions around -20oC. They also need to be used after taking them out of the freezer.
Pultrusion:
It is a production technology created by combining the glass fiber reinforcement material with a resin suitable for the purpose and pulling it out of a hot mold.
In the system, glass fiber fibers and glass fiber felt are wetted with resin and polymerized in the hot mold to form solid material. It is a suitable method for the production of industrial plates, profiles and electrical industrial plates, profiles.
The fiber tows are taken from a bobbin hanger and fed through a resin bath, then drawn through a heated extrusion die that cures the resin to produce an extruded part with axial reinforcement and constant cross-section. Applications include gratings, stair sections, bridge parts and railings. The process can be automated and uses low-cost raw materials, making it suitable for high-volume applications.
The matrix resins in the pultrusion system are:
Orthophthalic unsaturated Polyester Resins
Isophthalic Unsaturated Polyester Resins
Vinyl Ester Resins
Epoxy resins
Reinforcement materials are:
Fiberglass
Fiberglass Roving
Continue fiberglass
Glass Fiber Woven
surface tulle
fiberglass combi
Glass fiber multiaxiel
Vacuum Infusion:
Vacuum infusion, also called resin infusion, is a manufacturing technique that uses vacuum pressure to drive resin into a laminate. Dry materials are placed in the mold and vacuum pressure is applied before adding the resin. When a complete vacuum is achieved, the resin is pushed into the laminate through the vacuum tube. The vacuum infusion process offers a better fiber-to-resin ratio than manual laying or vacuum bagging.
Vacuum is used to cause a low viscosity resin to impregnate a fibrous preform. Most commonly, it causes the resin to flow over the surface of the preform and then be impregnated through the thickness, minimizing the distance the resin must travel through the preform. The process is well suited to large parts such as boat hulls or wind turbine blades. The tool does not have to carry significant loads during operation.
Vacuum infusion provides a number of improvements over traditionally vacuum-packed parts.
These benefits include:
Better fiber-resin ratio
Less waste resin
Very consistent use of resin
Unlimited installation time
Cleaner
Induction Heating:
For the first time, induction heating can be precisely controlled thanks to the thickness of carbon fiber reinforced thermoplastic composites. During the placement of the composite components to be joined, thin electrically insulating layers (gauze) are placed between the layers where induction heating is not required. The inclusion of thin insulating layers is only necessary in one of the joined parts and only between adjacent non-aligned carbon layers near the joint.
Heating trials have shown that the technique successfully inhibits the generation of alternating electric currents induced during induction heating. To heat and melt the material in the usual way for welding or curing, an electric current is induced between layers where there are no insulating layers (gauze). In this way, the concentration of induction heating throughout the thickness of the material can be precisely controlled. This approach prevents the outer surface of the components from overheating and improves the quality of the connections produced.
The technique can be considered as a candidate welding process that offers advantages over existing state-of-the-art processes, especially when dealing with thick parts (thicker than 4 mm). Tooling costs are also minimized compared to the latest technology. Broader application of the technique should be considered as a focused heating process for applications such as adhesive bonding of thermoset composites, where the focus of heat at the interface can be used to cure an adhesive.
In this technique: Current state-of-the-art induction welding of carbon fiber composites requires a highly thermally conductive heat sink material to be inserted into the composite part closest to the induction coil. This removes excess heat from the surface and allows the weld interface to warm up sufficiently.
Conductive and insulator (insulator) layers are arranged at an angle to see the flow of heat.
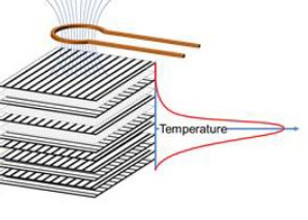

Thermal image after one minute of heating and temperature-time change graph in the lower and upper layers
Thermoplastic composites (TPCs) can be quickly processed by thermoforming making them an attractive option for the aerospace industry, but there has yet to be a significant TPC uptake for structural applications. One of the reasons behind this is the limited technology for engagement. TWI has recently invented a new method to improve the control of induction welding thermoplastic composites without additional preservatives. Adding a thin layer of electrically insulating (gauze) between adjacent layers containing unaligned carbon fibers prevents the formation of electrical paths and volumetric heating is disabled. TWI's technique has the advantage that the heat generated is condensed at the junction interface, eliminating the problem of removing excess heat from the composite surface to prevent thermal damage. and therefore improves control of the process. Joint strengths of up to 32 MPa have been achieved using this technique.
One of the limitations of composites is the assembly of prefabricated parts. In the case of thermoset composites, complex pretreatment and heating mechanisms are needed. Thermoplastic composites contribute better to bonding, but there is always a challenge in ensuring that only the interface is heated without any foreign material in the bonding line.
Recent years have seen a renewed interest in thermoplastic composites, especially for high-end applications such as aerospace. Projected production rates for single-aisle aircraft exceed the current economic production capacity of thermoset composites. Compared to thermosets, thermoplastic composites can offer shorter processing times to meet increased production rates and offer potential additional benefits such as good solvent resistance, unlimited shelf life and better toughness (impact resistance). Thermoplastic composites can be processed more quickly by heating the polymer matrix sufficiently to allow thermoforming, in a process similar in concept to stamping sheet metal components. This makes TPCs an attractive option for the aerospace industry, but there has yet to be a significant TPC uptake for structural applications.
One of the reasons behind this is to participate. Although the use of composites can offer near net shape fabrication, there is usually a need to assemble components for a variety of reasons such as;
more cost-effective
components are too large to be manufactured as a single piece
Hybrid materials are used that require different production conditions
components are made in different physical locations
The bonding methods currently in use have been adapted from those used to join metal structures, as the aircraft industry has relied on considerable performance data and techniques.
Thermosets are traditionally joined using mechanical bonding or adhesive bonding. Mechanical bonding requires producing holes that cut the load-bearing fibers and deliver stress concentrations around the holes. Adhesive bonding is not trouble-free and often requires heating large prefabricated parts in an oven to cure the adhesive in a relatively small joint.
However, unlike thermosets, TPCs can be joined by fusion bonding (welding); a process that does not cause damage by drilling and offers weight savings by removing the fastener and more speed benefits by eliminating the hole drilling step. Welding of thermoplastic composites is any process that heats the interface to a temperature above the glass transition temperature, Tg (for amorphous polymers), or the melting point, Tm (for semicrystalline polymers). Under the application of pressure, the polymer chains can spread across the interface forming a welded joint during cooling. The process can be quick and requires little or no surface preparation.
Since the introduction of thermoplastic composite materials such as APC-2 (AS4 carbon fiber reinforced Polyetheretherketone or PEEK) in the 1980s, many studies have been conducted on the fusion bonding of TPCs. Three of the numerous fusion bonding techniques available have been the subject of many research studies as they are considered the most suitable for industrial applications; induction, resistive implant and ultrasonic .
In induction welding, heat is generated through Joule losses from eddy currents induced in response to the applied alternating magnetic field. The magnetic field is produced by an alternating electric current passing through a conductive working coil. Induced eddy currents can flow in a metal implant placed at the weld interface or in carbon fibers in the main composite materials.
In recent years, induction welding has been applied to join thermoplastic composite materials. Fokker Aerostructures designed and developed the Gulfstream G650 tail section and installed the rudder and elevator Industrialized a new method of induction welding for Fiberforge Corporation also applied the technique to assemble parts on the Sikorsky CH-53K. However, the technique has not yet been widely adopted and one reason is poor control of the process to prevent thermal degradation. . What is needed is a technique that focuses the heat where it is needed without placing additional holders at the weld interface.
Current state-of-the-art induction welding of carbon fiber composites requires a highly thermally conductive heat sink material to be inserted into the composite part closest to the induction coil. This removes excess heat from the surface and allows the weld interface to heat up sufficiently.
It is well known that adjacent non-aligned layers are required for eddy currents to be induced in continuous carbon fiber composites. A layered structure in which all reinforcing fibers are aligned unidirectionally in the same direction will not be volumetrically heated by induction as a closed electrical path cannot be created. Fortunately, most structural composite applications use a quasi-isotropic arrangement to achieve the required mechanical performance and therefore can be volumetrically heated by induction.
If the adjacent non-aligned layers of the semi-isotropic laminate are separated sufficiently to prevent contact between the carbon fibers in the adjacent layers, closed electrical paths can no longer be formed and thus volumetric heating is disabled. This separation can be achieved by placing a thin electrically insulating layer (gauze) between adjacent layers containing misaligned carbon fibers (Figure 1). This technique, which uses a special combination of parameters and properties, has the advantage that the heat generated is concentrated around the joint interface rather than near the top surface of the composite, where the proximity of the induction coil is greatest. This focuses the heat where it is needed, and eliminates the problem of removing excess heat from the composite surface to prevent thermal damage. The heat required to produce the welded joint is generated by removing the insulating layers near the weld interface. Also, since the intensity of the current induced in the conductive material decreases exponentially from the surface, the insulating layers only need to be placed in one of the joined parts; closest to the work coil.
The heat generated by using this technique is sufficient to fuse thermoplastic composites and also be used for adhesive curing; A process used to join thermoset composites.
To demonstrate the focused heating effect, two thermoplastic composite laminates were fabricated, each containing three layers of Carbon/PEEK in the 0/90 direction. A laminate ("conductor") has been conventionally manufactured to allow adjacent unaligned plies to contact. The other laminate ("Insulator") was laid using a thin layer of insulation between adjacent non-aligned layers. The material used for the insulation layer was a 10 gsm non-woven glass fiber surface tissue. A layer of PEEK film was placed on both sides of the insulation layer during production; Additional PEEK was required to wet the glass insulation layer during consolidation of the laminate.
When placed side by side in the configuration shown in Figure 2; The "insulator" on the "conductor" and therefore the heating closer to the work coil was concentrated at the interface between the two laminates. The two laminates were shifted 45 degrees to allow the surface temperature of the sub-laminate to be measured using a thermal image camera. A Cheltenham Induction Heating TR1 1kW induction power supply was used to apply an alternating electromagnetic field through a four-turn solenoid coil at 165 kHz for 60 seconds. Temperature at the two locations marked in Figure 2 was measured at ten-second intervals during tests using a FLIR T250 thermal image camera.
Typical Composite materials
Fiberglass : It is the foundation of the composite industry. It is lightweight, has moderate tensile strength and is easy to use.
Carbon Fiber : It is found everywhere from auto racing to aviation. Although more expensive than Fiberglass and Kevlar, it has the highest tensile, compressive, flexural and bending strengths in the industry. Carbon Fiber is often used for projects that require higher levels of strength, such as load bearing parts.
Ceramic matrix composite: Ceramic dispersed in a ceramic matrix. These are better than regular ceramics as they are resistant to thermal shock and breakage.
Metal matrix composite: A metal spread across a matrix
Reinforced Concrete: Concrete reinforced with a high tensile strength material such as steel reinforcing bars
Glass fiber reinforced concrete : Concrete poured into a glass fiber structure with a high zirconia content
Translucent concrete : Concrete surrounding the optical fibers
Engineered wood: Manufactured wood combined with other inexpensive materials. An example would be chipboard. This composite may also contain a special material such as a coating.
Plywood: wood designed by gluing multiple thin layers of wood together at different angles
Engineered bamboo: Strips of bamboo fiber glued together to make a board. This is a useful composite as it has higher compressive, tensile and flexural strengths than wood.
Hardwood: A square consisting of many wooden pieces put together, usually of hardwood. It is sold as a decorative piece.
Wood-plastic composite: either wood fiber or bulk flour in plastic
Cement-bound wood fiber : Pieces of mineralized wood cast in cement. This composite has insulating and acoustic properties
Fiberglass: Fiberglass combined with a relatively inexpensive and flexible plastic
Carbon Fiber Reinforced Polymer : Carbon fiber set made of high strength to weight ratio plastic
Sandwich panel: Various composites layered on top of each other
Composite honeycomb: Selection of composites in many hexagons to create a honeycomb shape.
Papier mache: Adhesive paper. These are found in crafts
Plastic coated paper : Paper coated with plastic to increase durability . An example of where this is used is playing cards
Syntactic foams: Lightweight materials created by filling metal, ceramic, or plastic with micro-balloons. These balloons are made using glass, carbon or plastic.
Steel vest : It is one of the first high-strength synthetic fibers to be accepted in the fiber-reinforced plastics industry. Its biggest features are its high impact and abrasion resistance. Ideal for parts where high impact and wear is expected, such as canoes, airframe panels and pressure vessels.
PVA : Polyvinyl Alcohol is sprayed onto thin laminations or topcoats to keep air out while the part cures. The PVA should then be rinsed with warm water.
Styrene Wax : Another solution is to keep air out of your part during the curing process. Unlike PVA, paraffin remains on the surface of the resin as it cures. Styrene wax needs to be sanded after it hardens.
MEK-P (Methyl ethyl ketone peroxide): It is in the Organic Peroxides group. It is an accelerator or heat activated colorless chemical oil that regulates the gel and curing of polyester resin and vinylester resin. It is obtained from the reaction of methyl ethyl ketone and hydrogen peroxide. It initiates cross-linking reactions between resin and reactive monomers such as styrene. Methyl ethyl ketone peroxide (MEK-P) is active at room temperature to cure polyester and vinylesters. MEK-P is used as a hardener in the manufacture of resins, synthetic rubber and other petrochemical plastics. Methyl Ethyl Ketone Peroxide is required for all polyester resins, gel coats and vinyl ester resins. Different concentrations of MEK-P are required to catalyze different types of resins. It is also used for curing benzoyl peroxide resin in hot mold. Although the catalysts are not a part of the chemical reaction, they provide the necessary energy to start the polymerization process. All peroxides are derivatives of some form of hydrogen peroxide. It is widely used in the vulcanization of polymers. It is a highly toxic substance used as a solvent. It is a strong oxidizing agent and corrosive. Unlike other corrosive substances, it is a substance that can cause death as a result of multi-organ failure in addition to corrosive esophagitis findings. MEK-P exposure leads to free radical formation, which results in lipid peroxidation. Lipid peroxidation can cause dysfunction at the cellular level, especially liver failure and multi-organ failure.
Kevlar (poly paraphenylene terephthalamide): Aramid fibers, usually carbon fiber and glass fiber It is widely used to reinforce composite materials in combination with For high performance composites, the matrix is usually it is epoxy resin . Typical applications include F1 Race cars for monocoque trunks , helicopter rotor blades, tennis , Ping pong , badminton and squash rackets , canoes , cricket sticks and grass hockey , ice Hockey and lacrosse has sticks.

As the strongest fiber and most crystalline structure, Kevlar-149 is an alternative in certain parts of aircraft construction. Kevlar, which is especially used in the front parts of aircraft wings, shows more strength in bird strikes than carbon or glass fiber.
Kevlar is sometimes found in structural components of automobiles, especially Ferrari F40 It is used in high value performance cars such as
Kevlar, low thermal conductivity and suspension due to its high strength compared to other materials for cryogenic frequently used in the field. Often times, a gasket is used to minimize any heat leakage to the paramagnetic material. paramagnetic salt container a superconducting magnet Used to hang from mandrel. It is also used as a thermal separation or structural support where low heat leaks are desired.
Kevlar is used in a variety of military munitions and materials, as well as in helmets, to help absorb the explosion of a grenade.
Kevlar when bent , the resulting fiber tensile strength about 3,620 MPa and relative density It is 1.44. The polymer owes its high strength to many interchain bonds.
[CO-C 1-6, H 4 -CO-NH-C 6 H 4 -NH-] is formulated with n.
Kevlar retains its strength and flexibility down to cryogenic temperatures (−196 °C); in fact, it is slightly stronger at lower temperatures. At higher temperatures, the tensile strength immediately decreases by about 10-20%, and after a few hours the strength gradually decreases further.
Kevlar production, water-insoluble polymer synthesis and spinning concentrate needed to keep it in solution during from the use of sulfuric acid It is expensive because of the difficulties caused by it.
Various grades of Kevlar are available:
Kevlar K-29: Used in industrial applications such as cables, tires and brake pads.
Kevlar K49 : It is a high module used in cable and rope products.
Kevlar K100 : It is the colored version of Kevlar.
Kevlar K119 : It is more resistant to elongation, stretching and fatigue.
Kevlar K129 : Shows higher strength for ballistic applications.
Kevlar K149 : It is preferred for ballistic, armor and aerospace applications.
Kevlar AP: 15% higher tensile strength than Kevlar K-29.
Kevlar KM2 : Shows improved ballistic resistance for armor applications.
Kevlar XP : It is a combination of lighter resin and KM2 plus fiber.
Biocomposites
A composite is a new material with different properties, consisting of two or more physically different phases (or substances) and unlike any of them. One of the phases is the matrix and the other is the reinforcement materials used to strengthen the matrix. The purpose of the matrix is to hold the fibers together and transfer the applied load to the fibers.
It also protects the fibers from environmental and mechanical damage. The matrix material may be a thermoset or thermoplastic polymer, but must be made from renewable resources.
Biocomposites are materials consisting of biodegradable polymers (matrix) and biodegradable reinforcing materials. Biodegradable material is substances that can be degraded by living organisms.
The fillers used in biocomposites are generally biofibers. Biocomposites made from natural biofibers are renewable, lightweight, biodegradable and environmentally friendly. Today, polymer science and technology is focused on composites made from renewable resources.
Biocomposites produced from renewable resources have gained a universal importance due to their biodegradable nature and have been the subject of extensive research for their use in various fields due to being environmentally friendly materials.
Biocomposites produced from renewable resources have gained universal importance due to their biodegradable nature; Since it is environmentally friendly materials, it has been the subject of many and comprehensive researches for its use in various fields.
BBCs are composites with a wide range of applications in biomedical, agriculture, packaging and other related engineering fields.
Various factors limiting the use of natural polymers and biofibers include incompatibility or insufficient compatibility with the hydrophobic polymer matrix, thermal sensitivity and flammability.

Production Techniques of Biocomposites:
It is mostly based on manufacturing processes of plastics or composites; such as press molding, hand lay-up, filament winding, pultrusion, extrusion, injection molding, compression molding, resin transfer molding and sheet molding.
The compounding step of biocomposites is extremely important in the production of biocomposites by various processes. The purpose of compounding is to prepare material (such as pellets) with properties suitable for subsequent injection, molding, extrusion or other processes. In compounding, polymers, fillers, fibers and additives are generally mixed, a good dispersion is ensured, and it is aimed to obtain granules in suitable form and processable properties.
Compounding and Extrusion of Thermoplastic Polymers and Natural Fibers:
During compounding, the thermoplastic polymer heats up and melts, either by external heating or by mechanical interaction in the extruder; At this stage, wood fiber (usually in flour form) is added along with other additives.
Blend of Thermoplastic Fibers and Natural Fibers:
Long flax, hemp, kenaf and cotton fibers are common fibers in the automotive industry; they are often mixed with thermoplastic fibers and used as reinforcement material.
Thermoset Polymer Matrix Biocomposites:
Commercial biocomposites with thermoset polymer matrix are scarce, but work in this area continues. Manufacturing techniques are similar to conventional composite processes.
Biodegradable Composites Containing Lignocellulosic Fibers:
Important factors in the development of biodegradable composites are the selection of the right lignocellulosic fibers blend and the appropriate biopolymer matrix, the determination of appropriate surface treatments when necessary, and the application of inexpensive but fast fabrication techniques.