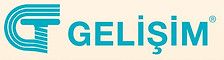


Hydrocarbons
It is an organic compound consisting of two elements, hydrogen and carbon. Most of the petroleum composition consists of hydrocarbons of varying lengths.
The smallest hydrocarbon methane consists of a single carbon atom and four hydrogen atoms. However, hydrocarbons can consist of hundreds or thousands of individual atoms linked together in many ways, including chains, circles, and other complex shapes.
In order to classify the properties of hydrocarbons, they are divided into several basic types.
Alkanes: These are called saturated hydrocarbons. That is, they only contain single bonds between all carbon atoms. Alkanes are the basis of petroleum fuels and exist in linear and branched forms.
Unsaturated Hydrocarbons: Hydrocarbons that have one or more double bonds between carbon atoms are called alkenes.
Cycloalkanes: Any hydrocarbon containing one or more ring structures.
Aromatic Hydrocarbons: Aromatic hydrocarbons , also called arenes, are a unique class of carbon molecules in which carbon atoms are bonded by successive double and single bonds. This class of molecules has special ring structures in which the bonds between carbon atoms are an intermediate bond between single and double bonds.
Molecules in this class contain the industrial solvent "benzene".
Benzene (C6H6): Like other hydrocarbons, benzene is a natural component of petroleum. It is a colorless, flammable, sweet-smelling liquid at room temperature and is a component of most gasoline blends because of its high octane number.
Benzene is also highly carcinogenic and is well known to cause bone marrow failure and bone cancer. Of course, its carcinogenicity is not well known when used as an additive in aftershave and other cosmetics due to its "pleasant aroma".
The largest use of benzene (50%) is the product of styrene and polystyrene plastics. It is also converted into a molecule known as cyclohexane, which is important in Nylon production. About 15% of benzene is used to produce cyclohexane. Smaller amounts are used in everything from pesticides to rubber.
The benzene structure can be drawn in two ways. In the first, the double bond character is drawn explicitly. In the short handed version, a circle is drawn inside the ring to show the structure. There is only one hydrogen bonded to each carbon atom in benzene.
I. and II below. drawings are identical. III in practice. drawing is used.
Benzene is a colorless, flammable liquid with a boiling point of 80.1 ° C and a melting point of 5.5 ° C.
Binuclear Aromatic Hydrocarbons: They are compounds that contain two benzene rings in their molecules.
Hydrocarbons
It is an organic compound consisting of two elements, hydrogen and carbon. Most of the petroleum composition consists of hydrocarbons of varying lengths.
The smallest hydrocarbon methane consists of a single carbon atom and four hydrogen atoms. However, hydrocarbons can consist of hundreds or thousands of individual atoms linked together in many ways, including chains, circles, and other complex shapes.
In order to classify the properties of hydrocarbons, they are divided into several basic types.
Alkanes: These are called saturated hydrocarbons. That is, they only contain single bonds between all carbon atoms. Alkanes are the basis of petroleum fuels and exist in linear and branched forms.
Unsaturated Hydrocarbons: Hydrocarbons that have one or more double bonds between carbon atoms are called alkenes.
Cycloalkanes: Any hydrocarbon containing one or more ring structures.
Aromatic Hydrocarbons: Aromatic hydrocarbons , also called arenes, are a unique class of carbon molecules in which carbon atoms are bonded by successive double and single bonds. This class of molecules has special ring structures in which the bonds between carbon atoms are an intermediate bond between single and double bonds.
Molecules in this class contain the industrial solvent "benzene".
Benzene (C6H6): Like other hydrocarbons, benzene is a natural component of petroleum. It is a colorless, flammable, sweet-smelling liquid at room temperature and is a component of most gasoline blends because of its high octane number.
Benzene is also highly carcinogenic and is well known to cause bone marrow failure and bone cancer. Of course, its carcinogenicity is not well known when used as an additive in aftershave and other cosmetics due to its "pleasant aroma".
The largest use of benzene (50%) is the product of styrene and polystyrene plastics. It is also converted into a molecule known as cyclohexane, which is important in Nylon production. About 15% of benzene is used to produce cyclohexane. Smaller amounts are used in everything from pesticides to rubber.
The benzene structure can be drawn in two ways. In the first, the double bond character is drawn explicitly. In the short handed version, a circle is drawn inside the ring to show the structure. There is only one hydrogen bonded to each carbon atom in benzene.
I. and II below. drawings are identical. III in practice. drawing is used.
Benzene is a colorless, flammable liquid with a boiling point of 80.1 ° C and a melting point of 5.5 ° C.
Binuclear Aromatic Hydrocarbons: They are compounds that contain two benzene rings in their molecules.
About
Kyäni, nutritional supplement products consisting of beneficial ingredients; It delivers to more than 50 countries around the world with unique business opportunities. We use Kyäni products daily to maintain our ideal health, share these products with others, devote a certain amount of time to work almost every day to build and maintain our business, and share our success with others by involving others in the Kyäni opportunity or contributing to the Potato Pak and Caring Hands programs.
About
Kyäni, nutritional supplement products consisting of beneficial ingredients; It delivers to more than 50 countries around the world with unique business opportunities. We use Kyäni products daily to maintain our ideal health, share these products with others, devote a certain amount of time to work almost every day to build and maintain our business, and share our success with others by involving others in the Kyäni opportunity or contributing to the Potato Pak and Caring Hands programs.
Page Under Construction.
Page Under Construction.
Training / Knowledge / Solution Platform
Thermoforming (Heat Treatment)
Thermoforming is a process for forming a two-stage flat thermoplastic sheet. The process begins with heating and softening the sheet and then forming into the mold cavity. The material is heated to the temperature at which it will be formed, then formed on (or inside) a temperature-controlled mold; The mold is waited until it cools down and the shaped part is removed from the mold.
Elastomer and thermoset plastics cannot be used in thermoforming methods as they cannot be re-heat treated due to their cross-linked structure.
Thermoplastics that can be processed by thermoforming method; PP, PS, PVC, LDPE, LLDPE, HDPE, PMMA, ABS.
Thermoforming, ice cream and margarine tubs, meat trays microwave containers, snack tubs sandwich packs etc. in the food packaging industry It is preferred in productions.
Thermoform is also used for the manufacture of some pharmaceutical and electronic goods, small gadgets, fasteners, toys, boat hulls.
It has three different techniques used in the forming phase, namely Vacuum, Pressurized and Mechanical.
Vacuum Thermoform:
When the thermoformic plate contacts the plastic mold surface, it cools and hardens and the thermoformic plate takes the form of a product / semi-finished product. Thermoforming (thermoforming) is the shaping of the semi-finished thermoplastic product at high temperatures and obtaining shaped parts. The semi-finished product usually consists of granule or powder-containing films and sheets. Thermoforming machine is designed to use the thermoforming process in packaging. Packaged products are generally end products that can be used directly and do not need to be further processed. Thermoforming process consists of feeding the semi-finished product (thermoformic film / sheet) to the machine to "reshape" with heat energy. Heat is applied to the film surface and softening is provided. When the mold is closed, the heat is cut off and the air in the mold is sucked with vacuum. Meanwhile, the softened film is pulled into the mold, takes the shape of the mold and keeps the shape by cooling. Many types of products can be used in heat-treated forming. These include thin plastic films in chocolate boxes, plastic containers for hot or cold drinks, and some products and components used in toy packaging.


Pressure Thermoform:
This Processing technique also; It involves a similar process to the vacuum thermoforming technique. Likewise, the thermoformic plate is first heated with hot air and closed on the mold. However, this time, the air in the mold is not sucked with vacuum, and high air pressure is applied into the mold above the plate. The air pressure forces the soft layer to deform to distribute in accordance with the mold cavities. With this deformation, the layer touches the mold surface, takes the shape of the mold and hardens by cooling.
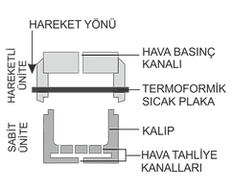

Mechanical Thermoforming:
In this process, it also involves pre-heating the thermoformic plate to make it workable softness and shaping the layer directly with a mechanical force. The male form of the product mold is also needed in the mechanical thermoforming process. The male form moves into the female form with high pressure and the thermoformic plate in between is spread to the space between the molds. Mechanical thermoforming process; It allows more precise dimensional tolerances and surface detailing than vacuum and pressurized thermoforming processes.

Compression Molding
This method is mostly used for molding thermoset resins (thermosets), but some thermoplastic parts can also be produced by this process. It is applied by subjecting a pre-weighed, heated polymer material mixed with additives and fillers to high pressure between split dies mounted on a hydraulic press.
Charge: Polymeric material that will turn into a finished product / semi-finished product is defined as "charge". Usually the mold is preheated before it is placed in its lower half. Or the molds have their own heating equipment. Charge; It can be in the form of powder, gel, paste, pellet, resin. The upper half of the mold moves downward, exerting pressure on the charge and forcing the material in the direction of filling the mold cavity. After the cycle process, the mold is opened and the part is removed by means of the ejector pin. Compression molding cycle time is longer than injection molding cycle.
This method is more suitable for molding large flat or medium curved parts. EP (Epoxy), UF (Ure formaldehyde), MF (Melamine Formaldehyde), PF (Phenolic) elastomer materials are commonly processed by Compression Molding.
In the Compression Molding process; electrical wall outlets, meter boxes, trays, circuit breakers, cooking pots, tumble dryer fan blades, electronics and cooking utensils, milling machine setting wheel, automotive parts, television cabinets, dinnerware, appliance housings, radio boxes, aircraft main power terminal casing, hoods, pot handles, fenders, dinnerware plates, ladles can be produced. The most important criterion to be considered in this method; It is the requirement that the amount (charge amount) of the material to be shaped must be very well controlled to fill the mold cavity completely.
The basic features of the compression molding process, the simpler application method than the injection molding process, the use of thermoset, elastomer (high viscose materials compared to thermoplastics) can be shown to prefer products with simpler geometry. The application mold is generally heated by electric resistances, steam or hot oil circulation.

Transfer Molding
The method is mainly used for molding thermosetting resins, but some thermoplastic parts can also be produced by this method. As in the compression molding process, «charge» is used in this process. First, the charge is taken into the pre-heated transfer chamber, which gives the molding process its name. With RAM extrusion modeling, polymeric material is injected into the mold along the channel (runner) with high pressure. Here, there is a third mold plate different from the compression molding process. After the charge, which may be in the form of powder, gel, paste, lump, resin, is frozen in the forming mold, this third plate is separated and the product is again with an ejector pin,
or the semi-finished product is removed from the mold. After the molding process, the residual scrap melts are cleaned in the transfer chamber and the channel.
These parts are scrap since thermoset polymers are not recycled by heat again. Cycle time of transfer molding; It is shorter than the compression molding cycle and more complex shaped products can be obtained. However, it has a longer working process than the injection molding cycle and cannot produce products with complex forms as well as injection molding.
Literally; In terms of product form and cycle process, it is a method between injection and compression molding. With transfer molding, ceramic or metallic materials placed in the mold cavity can be coated, and it is a method used to produce radio and television cabinets and car body parts. Vinyl esters such as EP (Epoxies), UP (Unsaturated Polyesters), PF (Phenolics), thermosets are materials that are commonly processed by compression molding.

Rotation Molding
The process, also defined as Rotary Molding, basically consists of 4 phases.
(1) Powder resin is put into the mold.
(2) After the mold is closed, the heating process is carried out. During the heating process, the mold is rotated around the horizontal and vertical axes. Plastic melts in this process and sticks to the surfaces of the mold. Rotation speed is relatively slow. This is because gravity without centrifugal force causes the mold surfaces to be uniformly coated. In the station containing a heating chamber where hot air convection heats the mold as it rotates, temperatures within the mold reach up to 375 ° C depending on the polymer and molded material.
(3) The cooling process starts. With large cooling fans or water sprays, air is blown on the walls of the mold or cooling is achieved by spraying / watering.
(4) The product is removed from the mold. Rotational molding is a molding method that is made at high temperatures and low pressures and is generally used in the production of large materials. Heating and cooling times and rotation speed of the mold are very important for the clean material obtained.
With this technique, mostly hollow and bulky products with constant wall thickness are produced. Boat hulls, canoes, furniture, containers, traffic signs, water tank, pontoons, animal shelters and toys can be given. PE, especially HDPE, PP, ABS, PS are the most frequently used materials in this technique.
Compared to injection molding and blow molding, rotation molds are simple and less expensive. However, the production cycle takes longer (ten minutes or more).

Blow Molding
It is a process in which a heated hollow thermoplastic tube is blown in a closed mold that conforms to the shape of the mold cavity. The part to be used for molding is defined as "parison". LDPE, HDPE, PP, PVC, PET are mostly used for blow molding. Various products in different sizes and shapes such as barrels, storage tanks, water or fuel tanks, recyclable bottles, toys, bathtubs, disposable containers, doors, and barriers in small boats are produced by this method. There are three different molding processes: extrusion blow molding, injection blow molding and stretch blow molding.
Extrusion Blow Molding:
It is widely used for mass production of plastic bottles. The plastic material is melted and pressed into a cold metal mold in the form of a hollow tube (parison), where it is inflated with compressed air to take the shape of the mold. The parison is extruded in a downward direction (vertically) between the two die halves. When the parison reaches the desired length, the extrusion work stops, the two mold halves join and close. With the air blown from the air blowing cavity, the parison is inflated until it is in full contact with the mold surface. With the cooling of the mold, the mold halves are opened and the product / semi-finished product is removed.
Stretch Blow Molding:
It involves injection molding a parison that is stretched downwards by means of a lance.
The expanded parison is then inflated in a blow mold.
The specific molecular orientation ensures higher mechanical strength, stiffness and transparency of the material. This method, which is widely preferred in the production of carbonated beverage containers, mainly uses PET.
Injection Blow Molding:
It is made by injecting polymeric material into a hot injection mold around a blow tube or core rod. Extrusion is a similar application to blow molding. For comparison, injection blow molding; it is a more accurate and controllable process. It enables the production of more complex products from a wider variety of polymeric materials.
However, the injection blow molding production rate is lower than extrusion blow molding.

Bag Vacuum Molding
While automation is widespread in the plastic mold industry, a large number of manual processes are still used today. For example, bag molding is a method of fabricating thermoset plastic materials into a variety of durable reinforced components, a process that is mostly based on manual control. It involves placing a special bag on a plastic workpiece while inside the mold cavity and applying vacuum or compressed air pressure around the bag. The rollers squeeze the air bag as the pressure is directed towards the bag and heat is often supplied to aid in the process. The bag itself is usually an impermeable and flexible cover made of release film or an elastomeric material.
Bag molding products tend to be compact and strong, and thickness tolerances are similar to those offered by injection molding. Bag molding is traditionally used for the production of high performance structural components such as building materials, equipment enclosures, automotive bodies, ship hulls, and various military products. It is also used in conjunction with other molding techniques. This combination of machine and hand-operated device ensures attention to quality and detail in the manufacture of plastic materials.
In the standard bag molding process, the elastic bag covers the plastic material in the mold cavity. However, before this happens, the mold itself must be cleaned, pre-treated and sealed along the edges. The mold is usually coated with a release agent and a gel lubricant, but molds containing a single curve can sometimes be treated with a plastic film instead. A layer of reinforcing glass fiber can be placed to provide smoother surface quality, but the key reinforcement is usually a preform consisting of a glass thread mat. This preform is sized before it is placed in the mold, along with any other required reinforcements or additives.
Bagging and molding:
Once the mold is prepared for bagging and the glass fiber reinforcements are placed, the actual manufacturing process is ready to begin. In a standard bag molding procedure, the following equipment is usually required to perform the manual stages of the operation:
Metal cylinders in both paddle and disc configurations to level the trapped air
Laminating rollers with long hair or short hair strands for applying bonding resins and gel coatings
Brush cleaners and brush replacements
Lamination and coating brushes
And the catalyst liquid resin is typically the compound containing pigments, dyes, and other additives that it is dispersed on the mold reinforcement. The operators apply knurled hand rollers to create a uniform distribution of resin under the surface of the bag while the entire mixture is then covered with an impermeable bag. Manual rolling also ensures that the reinforcement is properly bonded to the resin without air pockets that could cause the molded product to deteriorate. This resin reinforcing tie is essential for effective bag molding.
Depending on the application requirements, additional materials such as wood or foam can be added to the reinforcement. Similarly, metal reinforcements or support components can be included as they can be fully incorporated into the resin reinforcing bond. The entire unit is then moved to a different curing area, which can be accelerated using baking or infrared heating. After curing, the solidified product is removed from the mold or the mold breaks up around it. The product can then go through further styling or finishing before it's ready to use.
Bag molding can provide a high level of versatility in component design and lamination. Part of this is due to the precision and close thickness tolerance that can be achieved through bag molding. Using different types of resin compounds and reinforcements can impart certain physical properties upon molding, allowing a wide variety of component properties. Bag molding also relies on relatively inexpensive materials, and tooling and machining costs tend to be low. However, relying on operator skill can be one of the main drawbacks of the process. It is important to adhere to proper training and safety regulations, but even minor human mistakes can result in improper molding. Inspection and quality control can also be difficult because relying on individual laminators and hand rolling naturally results in minor discrepancies between production runs. Finally, the process is relatively slow and may require high labor costs.
Calendering / Rolling
This processing process; It can be defined in different terms as calendering, rolling or calendering.
The polymeric material in powder or granular form is mixed with the appropriate amount of additives and made soft. This mixture is passed through 150-200 ° C heated rolls and turned into film or sheet.
When it reaches the desired thickness, it is passed through a series of cooling rolls, hardened and then wrapped on a carrier roller.
Rolls forming the rolling line; mixer, softener, that performs the desired thickness, i.e. calibrates, cooler and
It is designed for different purposes such as a router ..
The mixer-softener rolling system consists of at least two rolls.
Cooling and guiding rolls may consist of a roll.
The distance between the calibration rolls is adjusted according to the thickness of the product.
It is generally applied to rolling thermoplastic materials and especially in the processing of polymers with low thermal resistance. The most typical example of this is PVC.
PVC; It is used in three ways as flexible, semi-rigid and hard.
Raincoat, bath curtain, bedspread, with flexible PVC
with semi-rigid PVC for tablecloth, flooring, credit cards, trays, sign board, etc. with rigid PVC. productions are carried out.
At the head of other polymeric materials formed by rolling;
Comes with ABS and filled PE
In summary: Calendering is a pressure application process; The material is squeezed through several heated and cooled rollers and transformed into a clean and bright sheet of the desired thickness. It is a processing method generally used in the production of films or sheets from rubber materials, PVC and some other plastics. Plates taken from calendering are given to thermoforming to be shaped. In metallic material rolling, the material is hot, while in plastic rolling, the rollers are hot. Pressure is applied on the material with calibrated rollers.
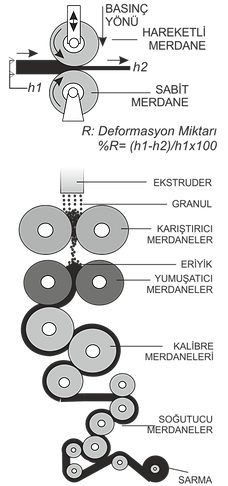
Liquid Injection Molding
It is an industrial manufacturing method that molds stock materials into a range of components and products. It differs from the standard reaction injection molding process in that it is based on mechanical mixing rather than pressure impact mixing and focuses on standard liquid injection rubber and similar elastomeric materials. It can efficiently manufacture a large number of versatile products including seals, o-rings, insulators and electronic contacts.
Much of the versatility of liquid injection molding stems from the material properties of liquid silicone materials. These silicones show a high degree of heat and flame resistance, tensile strength and flexibility. In addition, silicones provide useful formability properties that allow for tinting or transparency in the finished product. Depending on their chemical composition, these materials can also act as insulators or conductors. The liquid injection process used to produce liquid silicone is a sensitive and different method that can produce extremely accurate results.
Liquid injection molding process: It focuses on the dispersed mixing and distribution of plastic-based materials through a series of pistons. Usually, one piston contains plastic forming the base that can be reinforced with additives and fibers, while the other piston holds a catalyst that activates the mixing reaction. The composite material is then injected directly into a closed mold, and after curing, the nearly finished component is removed from the molding machine.
Silicones and acrylics are the most commonly used materials for liquid injection molding. A spring loaded pin nozzle can be used for the injection stage to help prevent machine equipment from clogging with liquid plastic. Spring loading ensures that the injection pressure is higher than that of the extruder chamber, thus preventing the channel from being blocked. Computer aided design tools are also useful for making the molding process more efficient. Computer programs can run simulations to determine the most effective processing conditions, evaluate results, and monitor integrated devices. Thermal imaging technology also has the potential to identify manufacturing defects such as molding defects or design inconsistencies.
Liquid injection machines: A standard liquid injection molding machine is based on a metered pumping device and an injection unit fitted with a dynamic or static mixer. Ideally, these systems are assembled as compact and precise as possible, while the environmental components are configured to meet the needs of a particular project. The key parts of a typical liquid injection machine are:
-
Injectors: The injection device pushes the forming material such as liquid silicone rubber into the pumping section under pressurized force. The operator can usually adjust the pressure and injection rate varying according to the project parameters.
-
Metering Units: The metering unit carefully proportionally pumps two liquid materials and simultaneously releases them at a constant rate.
-
Feeding Drums: Material feeding containers or pistons are connected to the pumping system of the machine. Besides the drums of mixing materials, there is usually an additional container for the pigment.
-
Mixers: After passing through the metering unit, the liquid forming materials are combined using a static or dynamic mixer. This mixture is then pressurized and forced into the mold.
-
Nozzle: The nozzle that feeds the liquid mixture into the mold usually comes with an automatic shut-off valve that prevents the compound from leaking or the mold overfilling.
-
Mold Clamp: It is triggered in coordination with the mold clamping device, injector, pump and feeding unit. It fixes the mold in place and opens it when the process is complete.
Laser Sintering
It is used in the production of computer-aided three-dimensional object object production in layers less than millimeters. In this process; Apart from polymeric materials, ceramic and metallic powders can also be utilized.
From polymeric materials; silicone and epoxy molds, functional parts made of nylon, acrylic styrene parts for investment casting, artistic objects with glass fiber reinforced PA, PP, PC, ABS and high strength carbon fiber reinforced PA, architectural models, dental protective products, from ceramic materials, partially stabilized zirconium investment casting molds, uuni bones and tissue scaffolds, prostheses,
bronze parts made of metallic materials; stainless and tool steels, structural parts from titanium alloys,
Silicon carbon-reinforced aluminum and titanium composites for high-strength, low-weight, wear-resistant parts for the automotive and electronics industries are among the optional laser sintering applications.
Sintering: It is a method that involves the combination of powder particles by heating the material to be used under its melting temperature but very close to its melting temperature.
Process; It starts with the spreading of the powder in a thin and uniform layer on the surface of the production chamber. Here, the thickness of the fine powder layer is generally less than 0.1 mm. High-power laser beam scanning is performed on the layer surface according to the computer-aided design (CAD) model of the part to be produced. The energy of the laser is focused on a small point of the sheet surface where the powder heats up to the sintering temperature. The powder particles of the layer are bound to each other and to the previous layer due to the diffusion of the material. The dust layer outside the scanned area remains intact and supports the sintered section in the production chamber.
Following the powder spreading process, the laser sintering process is repeated multiple times until the object creation is complete. After the process is completed, it is left to cool. And then the sintered model is taken out of the production chamber, air is blown on it and the excess dust is removed from the model. In this process; The transition period to manufacturing with the product concept is very short. Very flexible and detailed designs can be made. Unique modeling or very special parts needed can be easily produced on the basis of pieces. Prototypes are stored in digital form and can be reproduced as needed.

Reaction Injection Molding
In simplest terms, Reaction Injection Molding (: REK) is the job of mixing two or more reactive liquid components by applying high pressure and injecting them into a closed mold at low pressure. In other words, it is a special subset of the injection molding technique that chemically binds two or more plastics to a polymer before being molded. While molded plastics are used in a wide variety of industrial and commercial applications, choosing a specific molding process can greatly affect the quality and efficiency of a project. Generally, the injection molding process produces thermoplastic resin parts by forcing molten plastic into a design mold. The high pressures used create the part by allowing the plastic to conform to the shape of the mold. Like metal casting, injection molding typically produces components that require little or no work.
Manufacturers considering the use of REK may want to examine certain properties that distinguish it from standard injection molding. One of the central differences lies in the nature of plastic polymerization, which can provide properties different from those of base materials. REK can also manufacture large parts with complex shapes, making it well suited for industrial applications requiring bulky components. Similarly, cost efficiency, production cycle rates, and machine design issues can influence the decision to use this technique.
Plastics used in REK:
Polyurethanes , polyamides and fiber composites are the most common types of plastic used in reaction injection molding. These materials exhibit varying properties depending on the proportion of base materials or additional chemicals used during polymerization. The different combinations can give a range of elastomeric properties that determine the ability of a product to stretch with low stress and return to its original shape. This range affects the flexibility of structural, rigid and composite foams, which are the main products used in polyurethane manufacturing.
Since the process involves molten plastic, REK can be considered a form of liquid injection molding. One of the fluids is usually given carbon fillers or short fiber resin to increase the product's stress-strain ratio and reduce the degree of expansion or contraction from thermal changes.
REK process:
It is a multi-step process that involves different procedures than the standard injection molding process. To get started, two or more types of molten plastics, such as polyisocyanate and a resin compound, are poured into separate reactant tanks equipped with temperature and feed control mechanisms. The liquids are then released into the respective feed lines and channeled into a measuring chamber that regulates pressurization and recirculates the plastic to a mixing head.
The mixing head typically applies pressures between 1,500 and 3,000 psi to stir plastics by impact. After mixing the reactants, they are injected into the mold at high speed. The mixing head stops releasing reagents when the mold is full. An exothermic chemical reaction takes place inside the mold and causes plastic polymerization. After the polymer has solidified or "cured", it is removed from the mold from the component.
REK machines perform this process using low temperatures. Apart from the heat required to form the molten plastic, reaction injection molding is a relatively cool process. Instead of thermal energy, REK generates chemical energy caused by polymerization reactions. The dies used are typically made of steel, aluminum or nickel and clamped with a low weight press. The curing time of the polymer is usually under one minute, resulting in fast turnover and fast production cycles for medium volume operations.
REK industrial applications:
Due to low machining temperatures and low injection pressures, REK is well suited for molding large components with variable wall thickness and smooth surface surfaces. Manufacturers can also benefit from the relatively high turnover rate that makes them competent to handle low and medium volume projects. In addition, REK parts exhibit high tensile strength, heat resistance and resistance to corrosive acids or solvents. However, prolonged exposure to sunlight can degrade polymer-based parts, and tooling or machining costs are relatively high for polymer-based products.
Nonwoven Fabric Production
Nonwoven fabrics (Nonwowen) are evaluated in many types and are categorized according to their production techniques.
Production techniques are mainly;
-
Melt Blown
-
Spunbond
-
Spunlace
-
Airlaid
-
Chemical Bonded
-
Needle Punched - Felts
Disposable Baby Nappies, Adult Urinary Incontinence Products, Disposable Baby Nappies, Adult Urinary Incontinence Products, Disposable Medical Textiles, Band-Aids, Bandages, Bed and Upholstery Liners, spring pockets, pillow covers, pillow liners, Carpet Underlays income.
For each filtration type, product and application area, there are special nonwoven types that provide excellent filtration properties in accordance with international standards. In addition, nonwovens have a wide range of applications, whether it is to conserve the soil, work on the landscape, or help improve cultivation. The fact that nonwoven fabrics are transported to the land surface and easy to apply are their biggest advantages in this area.
Other than these, the fields where nonwoven (non-woven) fabrics are used are as follows;
Filtration:
Car and Home Air Conditioners, Clean Room, Operating Room Air Purifiers, Face Masks, Liquid Filtering, Auto Oil Filters, Machine Filters, Drain Filters, Vacuum Cleaner Bags, Industrial Dust Collection and Filtering
Agriculture, Horticulture:
Mulches, Crop Covers, Insect Covers, Shaders, Wind Covers, Frost Protection and Thermal Blankets, Protective Covers for Fruits and Vegetables
Geotextiles:
These products are mostly used in the construction of highways, railways, storage areas, parking lots, airport landing and take-off runways, petroleum transportation pipes and tanks. It plays an important role in strengthening the ground mechanics in such constructions. They help to ensure that sudden loads on one point of the ground are spread over the whole ground in a balanced way. In addition, it can be used as soil reinforcement against the dam bases or landslides because it is water permeable and does not pass solid particles. Landscape, Soil Section, Landslide Control, Surface or Sub-Ground Reinforcement, Drainage, Filtration, Geo-Membrane Protection Cover.
Automotive Industry:
Carpeting, Interior Carpets, Trunk Mat and Trims, Head and Hood Liners, Seat and Door Interiors, Sound Insulation, Bonnet Placement Pad, Front Component and Instrument Panel Insulation Pad, Door Insulation, Oil Filtration, Air Filtration, Battery Separators .
Packaging and Packaging:
General Packaging Bags, Shopping Bags, Promotion and Gift Bags and Packaging, Food and Beverage Bags, Protective Bags and Cases, Electronic Cases, Spare Parts Covers, Basic Shock Absorbing Covers and Covers, Advertising Materials, Headrests, Event Decorations.
Insulation and Insulation:
Thermal insulation, Sound insulation, Floor and Wall Coverings, Roofing, Tile Underlay, Moisture barrier, Moisture Stabilizer
Melt Blown Nonwoven Application:
Melt blowing technique for making nonwoven products is one of the fastest growing techniques in the nonwoven industry in recent years, based on the principle of blowing thin polymeric filaments self-adhering from the die end with high speed air on a moving belt (conveyor) or on a rotating cylindrical pulley (drum). is the process.
The blown polymeric filaments form a network of high random entanglement motion to each other. Melt blown webs offer a wide variety of product properties, such as random fiber orientation, low to medium web strength. Approximately 40% of the meltblown material is used in the unbonded (monolithic) state, 60% as a composite or laminate material component.
(Melt Blown) Melt blowing process; It is unique among nonwoven applications. In its simplest form, it can be considered as a high-tech version of cotton candy making. While cotton candy is being made, the sugar is melted and stretched in strands by pressure and centrifugal force through small openings in a rotating spinning wheel. Similarly, in the melt blown system, the extruded polymeric melt is compressed (combined in the same direction) with air blown from both sides at a speed of 300-900 km / h while it is about to exit the head (die tip) at a temperature of 220-400 ° C. The fast moving air stream effectively stretches and weakens the molten polymer. It solidifies into fine strands with a random interruption. These thin polymeric filaments are then densified into a randomly circulating web and compressed between heated rolls, while the effective air stream is removed.
A typical meltblowing process consists of extruder, melt pump, die, air compressor and winding units.


The Melt Blown process has a change process that can be evaluated in two categories, operational and material. By manipulating operational and material variables, various meltblown fabrics with desired properties are produced.
Polymer production rate
Polymer and mold temperatures
air outlet velocity
Temperature
Spray distance
These parameters are basic components that play a role in changing the main fabric properties. These are parameters that can be intervened online, that is, during operation.
The polymer and air exit rates basically control the final strand diameter, its entanglement and the extent of the weakening zone.
In conjunction with the air flow rate, the polymer / mold and air temperatures affect the appearance and grip of the fabric and the fabric homogeneity in production.
The ejection distance (die tip to drum distance) generally affects the openness of the fabric and the inter-strand thermal bonding. As the distance increases, the filament diameter slightly increases.
Die hole size
Air space
air angle
These parameters determine the network aggregation type. These are offline parameters that can be intervened when the operation is stopped.
Die hole size, die design parameters and die setting affect fiber size. The die hole size should be large enough to pass the polymer melt without clogging.
The air gap affects the air outlet pressure as well as the degree of fiber breakage.
Process raw materials:
Basically, polymers that can yield low melt viscosity at an appropriate processing temperature and solidify within the eruption distance are are the preferred polymers in the process. Polymers are preferred in terms of granular size, rapid melting and providing a more even heat distribution.
Polypropylene (PP) has exactly these desired properties. It is easy to process and forms a good mesh.
Polyethylene (PE) is more difficult to melt and blow into thin filaments than polypropylene. PE is difficult to pull due to its elasticity.
PBT very soft, fine filament nets are produced.
Nylon 6 is also easy to process and creates good, quality filament webs.
Nylon 11 is preferred for the formation of webs with a very unusual leather feel.
Very soft fiber meshes are produced with polycarbonate (PC).
Polystyrene (PS) is essentially the choice in producing an extremely soft, fluffy material with no shot defects.
Nonwoven Non-Woven Fabric Types:
It is generally divided into 4 main categories.
Disposable non-woven fabrics: Such non-woven fabrics are mostly made for disposable products or reusable products (for example, dust cloths that can be washed and reused several times).
Non-woven fabrics for general applications: Includes personal hygiene products such as diapers and sanitary napkins; medical products such as surgical gowns and drapes; surgical and industrial masks, bandages, handkerchiefs and towels; gowns and even costumes for special events.
Durable non-woven fabrics: Widely used in both household goods and home furnishings, such as curtains, furniture upholstery, mattress padding, towels, tablecloths, blankets and carpet backing, and clothing and apparel such as hats, linings, interlinings, interfacings. reinforcement of other fabrics.
In order to optimize the production of nonwovens, calcium carbonate filler has been started to be used. Made from calcium carbonate powder (CaCO3), plastic resins and other special additives, calcium carbonate filler is one of the most effective material solutions for nonwoven manufacturing. The application of this material offers several benefits to end products:
These are areas where products made from calcium carbonate non-woven fabric range from medical and personal care to hygiene, geotextiles (fabrics used in technical industries such as suction, separation, filtration, protection, reinforcement and discharge).
Advantages of adding calcium carbonate filler to non-woven materials:
Improves product surfaces
It reduces the gloss, making the surface more matte and more opaque, leading to a better covering ability of the fabric structure.
Gives natural white color with limited yellowness
Improves material texture
Creates a comfortable and cottony feel
Prevents carbon footprint when touched
Creates more micro-areas for air filtration and oil absorption
Adds increased thermal conductivity and physical strength
Allows lowering of process temperature
It paves the way for higher productivity of production, that is, it increases capacity.
It saves energy and production costs.
It cooperates easily with multiple base resins (thanks to its good dispersibility) and can be processed by various methods
Recommended usage rates of Calcium Carbon:
5-20% in thin fabrics,
20-35% in medium fabrics,
it reaches 60% in thick fabrics.
When extremely good dispersion and stability is required,
The filler masterbatch is typically applied with a loading rate of 78-80% and a melt flow index of 20-40g/10min.
Acrylic Fiber Production
In the age shooting method: Fiber formation in production occurs thanks to the coagulation bath.
Therefore, the physical properties of the fibers obtained by the wet spinning method are greatly affected by the coagulation bath conditions. Therefore, the coagulation bath parameters should be controlled very well. In this article, some physical events such as diffusion and phase change that occur in the coagulation bath and some coagulation bath parameters that are effective in the occurrence of these events are summarized. In addition, the effect of these on the physical properties of the fibers has been tried to be stated.
Polyacrylonitrile (PAN) polymers used in acrylic fiber production are obtained by radical chain polymerization of acrylonitrile monomers. Polyacrylonitrile polymers are not suitable for melt spinning method because they do not melt when heated to high temperatures used for fiber spinning from the melt, and changes in their chemical structure occur. Therefore, it is not possible to produce fiber from PAN polymers by melt spinning method. However, polyacrylonitrile (PAN) polymers; It can be dissolved in suitable solvents and turned into a polymer solution with suitable viscosity for fiber spinning. For these reasons, fiber production from PAN polymers is carried out according to the solution fiber spinning method.
The PAN polymer is insoluble in many known solvents. Dimethyl Formamide (DMF) and Dimethyl Acetamide (DMAc) solvents are mostly used as solvent solvents. These solvents also play a role in determining the properties of the fibers produced.
Spinneret systems with very fine holes are used for fiber spinning from the prepared polymer solution. The number of holes on these nozzles varies greatly depending on the shooting method to be used. In addition, these holes are placed in segments, that is, in groups, on the nozzle. In this way, better penetration of the coagulant between the filaments ejected from the nozzles is ensured.
Solvents Used in Acrylic Fiber Spinning and Polymer Contents in Drawing Dock:

In the dry drafting method: the drafting solution is sprayed into the drafting tower from the nozzles placed in the tower.
At the same time, thanks to the heated gas sent into the tower, the solvent in the dope polymer is largely removed and the polymer solidifies and becomes a fiber.
In the wet drawing method, the aspiration solution is squirted into the bath from the nozzle system immersed in a liquid bath containing coagulant. Thanks to the mutual diffusion of the non-solvent in the bath and the solvent in the polymer, the polymer solidifies and turns into a fiber. Since the first fiber formation takes place in the coagulation bath in wet spinning acrylic production, the coagulation bath parameters play a decisive role especially on the physical properties of the fibers.
The processes of Acrylic fibers after both dry and wet spinning are essentially the same. However, the order of these processes or the conditions of application may differ somewhat. These processes are washing, stretching, preparation, drying, curling and annealing. All these processes have an effect on the physical properties of the fibers.
Polyacrylonitrile fiber production facility according to the wet spinning method:
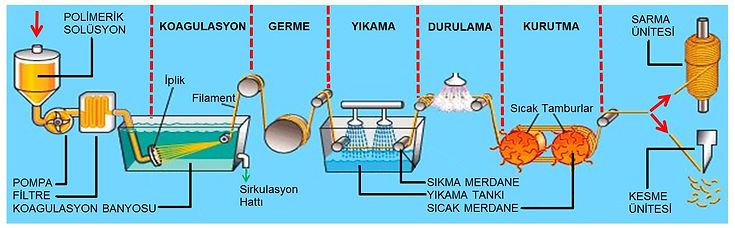
Coagulation : It is the process of converting the polymer material into fiber form by removing a large amount of the solvent in the polymer solution, which is ejected from the nozzles in the form of very thin liquid jets. The coagulation bath used for this process is a liquid medium containing solvent and non-solvent. In the coagulation bath, the same solvent is used as the solvent in the polymer extraction solution. As a non-solvent, water, which is a liquid in which the polymer does not dissolve, but can penetrate into the dope and mix with the solvent, is used.
The coagulation bath is the stage where the first fiber formation takes place in fiber production and plays a very important role in the formation of fiber properties. In the coagulation bath, the polymer material turns into a gel-like fiber, and the solvent and the nonsolvent are exchanged by mutual flow.
As a result of the polymer / solvent / non-solvent interaction in the coagulation bath, the fiber is formed and gains different properties. Two events occurring in the coagulation bath play a particularly important role in this interaction. These are diffusion and phase change events. These two important events are effective together in determining the structure of the fibers.
In wet spinning, a porous fiber structure is obtained due to the phase change and diffusion rate.
While pores in the size of 0.1µ are formed in dry drawing, these pores are around 0.3µ in wet drawing and can reach up to 10µ by enlarging.
Flush Rate: The speed at which the polyacrylonitrile aspiration solution (dope) is squirted from the nozzles into the bath (V),
is greater than the exit velocity (V1) from the coagulation bath.
2 QV /4 D = π
D: nozzle hole diameter
Q: represents the flow rate.
This does not mean that the filament is not stretched in the draft bath. Because when the filament comes out of the plane, due to the normal pressure acting on it, it will start to swell and its speed will decrease and the free speed (Vf) of the filament will be lower than the exit speed from the bath (Vf < V1 < (V) ). Therefore, the filament is stretched a little in the bath.
The diameter of the filament ejected into the coagulation bath due to swelling can be up to 10 times the diameter of the nozzle hole.
Diffusion event: It is the mutual flow of the solvent in the filament sprayed into the coagulation bath and the non-solvent in the bath. With diffusion, the amount of solvent in the polymer dope decreases and thanks to this decrease, the filament becomes a solid gel. In addition, this diffusion phenomenon causes the formation of pores in the structure of the fibers obtained by wet spinning. Although some of these pores are eliminated in later processes, they cannot be completely eliminated.
Phase Change : Solvent-rich filaments ejected from the nozzles during the phase change first turn into a polymer-rich gel and become solid after the solvent is completely removed in subsequent processes.
Flexo Printing Unit
The second stage, generally following the blown film line, is the slicing and cutting units.
However, if printing is desired on the products, the corona and then printing (especially flexo) units constitute the second stage. It is the most widely used printing form in packaging printing. Flexographic printing is a method that uses a flexible embossed sheet to print on a substrate that can be a rubber-based, synthetic or laminated material. Films such as polyester, OPP, nylon and PE, papers, cardboard sheets, non-woven textiles, coated or uncoated liners are the layers that can be used in flexo printing. Today's flexo printing machines produce photopolymer printing plates containing a mirror relief image of the required printing.
uses.
In flexo printing technique; There is the principle of transferring the ink in the ink reservoir to the screened (Anilox) roller from there to the mold roller and transferring it to the printing material that passes in contact with the printing roller.
From the ink reservoir, the ink is conveyed to the anilox roller by a roller. Excess ink is peeled off the roller with a doctor blade. From anilox roller to sleeve / boiler to transfer ink to the plate engraved on the printing contact
the transfer is done. The cliché that receives the ink transmits the pattern to the printing material passing over the drum. Although it is described as a simple recipe, the flexo printing process is a purely technical process. For the continuity of printing quality, the ink viscose values must be
tracking of squeegee blades on anilox, anilox on the cliché, pressure value settings of the cliché on the film, continuous checks of the film quality (flagging, wrinkle, corona intensity), follow-up of the tension of the winding tension and tension on the rollers, the stability of the alignment reference points (cross). It has sensitive points that need to be monitored and measured continuously. Flexo printing lines are second stage production lines, mostly after the blown film production line. And the products that come out of here are semi-finished / semi-form products to be used in slicing, plowing and cutting units, such as bags, bands, shrink bags.
Anilox (Tram Roller):
In the flexo system, it is the name of the roller that carries the ink to the desired size of the mold. In recent years, very thin anilox rollers have been put into use due to the fact that slide prints are made in the flexo system. Anilox rollers are available in 60, 120, 200 etc. referred to as numbers. As the number increases, the density of the lint on the anilox increases and its depth decreases. Therefore, as the transferred ink film gets thinner, the color intensity received decreases. It is necessary to prepare more concentrated inks for such thin aniloxes.
Hopper Roller:
They are generally rubber-coated cylinders that rotate in the ink reservoir where the ink is located, changing according to the system. The reservoir roller is responsible for transferring the ink to the other elements of the system. It transfers the ink it takes from the reservoir with the help of rubber to the anilox roller with which it is in contact.
Squeegee Knife (Doctor. Blade):
Ink stripper blade. It is one of the important parts of flexo printing system. The ink taken from the roller inside the reservoir is thinned to the desired film thickness with a squeegee contacting on the anilox roller and transferred onto the material. The ink thickness on the anilox roller is determined by the squeegee pressure, ie the force.
Underpress Material (Film):
In the packaging branch, the film is a thin and elastic layer of a non-fibrous organic material. In flexo printing business generally; Films in roll form made of materials such as polyethylene, polyvenyl chloride, polypropylene, polyamide, polyester and paper are used.
Flexo Mold (Cliché):
Flexo printing molds are materials prepared by using photographic and digital methods from rubber and photopolymer materials used to transfer pictures and texts to be printed on different materials for use in flexo printing machines. There are also photopolymer molds produced from polymeric materials by photomechanical methods.
These molds are generally made in a bendable manner. It can be used in molds made of zinc plates by photomechanical impregnation method.
Mold cylinder (Boiler):
They are cylinders of different diameters on which cliches are mounted. Diameter thickness may vary depending on the size of the job. The diameter and length of the cylinder are proportioned.
These graduations make it easy to fasten the plate straight or diagonally during assembly.
Sleev (Shirt):
They are tools that are mounted on cliches and passed on to the cylinder. Short and repetitive jobs are the tools that enable the plate to be printed economically without the need to readjust and mount. Polyester, steel, nickel, duroflex (urethane) and coated sleeves are available. This assembly is done by attaching the liner to the cylinder with compressed air.
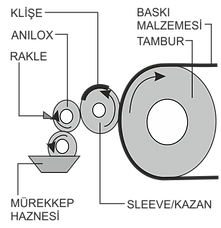
Basic Terms Used in Flexo Printing
Blood pressure:
It is the tension of the material during printing in flexo printing machines. The blood pressure value is important for continuous and uninterrupted pressure. Generally, high tension can be applied in thick materials such as paper, and low tension can be applied in thin materials such as (PE, PP, OPP, etc.). In the blood pressure setting; The stretchability of the film, its heat resistance, its sensitivity to tension, its thickness and the grammage properties for papers should be taken into consideration.
Viscosity:
It is defined as the resistance of liquids to flow. Ink density is very important in flexo printing. For this reason, the viscosity of the ink must be constantly monitored.
Density:
The density of substrates and ink. It is high in weight and abundance, low in light and scarce.
Galley slave:
The pressure exerted by the two cylinders on each other or on the printing material passing between them is called forsa. Forsa affects the printing during the use of the space between the printing material or the ink film layer during the approach of the rollers to each other.
Corona:
Making the surface of the materials to be printed can be printed is the process of adjusting the surface tension. Generally, 36-38 dyn / cm corona is applied for materials such as PE, PP, PVC. High corona creates problems as well as not low.
Lamination:
The job of bonding two or more materials to each other. Purpose of lamination; It is to provide the desired protection by reducing the moisture, light and gas permeability that may cause the spoilage of the foodstuffs placed in the packaging and to achieve the appeal that will attract the consumer.
Blocking:
It is a problem that occurs as a result of the transfer and adhesion of the printed work to the non-printed surface due to tight wrapping, high bombardment, materials with corona on both sides and being kept in heat, which also causes the print to smell bad.
Adhesion:
It is the gravitational force that exists between two different substances and allows these two substances to stick together. In flexo printing business; It refers to the ability of the ink to adhere to the printed material.
Cellophane:
Cellulose obtained from wood is then converted into viscose and then cellulose hydrate by reacting with chemicals and pressed in the form of a film. This pressed film is called cellophane.
Alum (Acid) Bath:
It is the process of washing the zinc mold with chemicals.
Emulsion:
Sensitive substance poured into the mold. (Photosensitive substance)
Shore:
The hardness of cliché molds.
Relief:
Relief effect
Solvent:
Liquid fluids such as thinner, naphtha, turpentine, varnish, glycol, ethyl alcohol.
Penetration (penetration):
It is the form of drying that occurs when the liquid phase of the ink is absorbed by the printing surface.
Bleeding:
The mixing of colors on the printed surface.
Aniline dye:
It is an organic dye obtained from hard coal ether. Used in flexo printing.
UVC exposure:
Light source with the lowest wavelength used for plate exposure in flexo printing. UVC-exposure removes the stickiness on the plate surface. UVC light is extremely harmful to the human eye and should not be viewed directly with the naked eye.