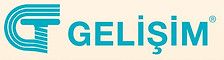


Hydrocarbons
It is an organic compound consisting of two elements, hydrogen and carbon. Most of the petroleum composition consists of hydrocarbons of varying lengths.
The smallest hydrocarbon methane consists of a single carbon atom and four hydrogen atoms. However, hydrocarbons can consist of hundreds or thousands of individual atoms linked together in many ways, including chains, circles, and other complex shapes.
In order to classify the properties of hydrocarbons, they are divided into several basic types.
Alkanes: These are called saturated hydrocarbons. That is, they only contain single bonds between all carbon atoms. Alkanes are the basis of petroleum fuels and exist in linear and branched forms.
Unsaturated Hydrocarbons: Hydrocarbons that have one or more double bonds between carbon atoms are called alkenes.
Cycloalkanes: Any hydrocarbon containing one or more ring structures.
Aromatic Hydrocarbons: Aromatic hydrocarbons , also called arenes, are a unique class of carbon molecules in which carbon atoms are bonded by successive double and single bonds. This class of molecules has special ring structures in which the bonds between carbon atoms are an intermediate bond between single and double bonds.
Molecules in this class contain the industrial solvent "benzene".
Benzene (C6H6): Like other hydrocarbons, benzene is a natural component of petroleum. It is a colorless, flammable, sweet-smelling liquid at room temperature and is a component of most gasoline blends because of its high octane number.
Benzene is also highly carcinogenic and is well known to cause bone marrow failure and bone cancer. Of course, its carcinogenicity is not well known when used as an additive in aftershave and other cosmetics due to its "pleasant aroma".
The largest use of benzene (50%) is the product of styrene and polystyrene plastics. It is also converted into a molecule known as cyclohexane, which is important in Nylon production. About 15% of benzene is used to produce cyclohexane. Smaller amounts are used in everything from pesticides to rubber.
The benzene structure can be drawn in two ways. In the first, the double bond character is drawn explicitly. In the short handed version, a circle is drawn inside the ring to show the structure. There is only one hydrogen bonded to each carbon atom in benzene.
I. and II below. drawings are identical. III in practice. drawing is used.
Benzene is a colorless, flammable liquid with a boiling point of 80.1 ° C and a melting point of 5.5 ° C.
Binuclear Aromatic Hydrocarbons: They are compounds that contain two benzene rings in their molecules.
Hydrocarbons
It is an organic compound consisting of two elements, hydrogen and carbon. Most of the petroleum composition consists of hydrocarbons of varying lengths.
The smallest hydrocarbon methane consists of a single carbon atom and four hydrogen atoms. However, hydrocarbons can consist of hundreds or thousands of individual atoms linked together in many ways, including chains, circles, and other complex shapes.
In order to classify the properties of hydrocarbons, they are divided into several basic types.
Alkanes: These are called saturated hydrocarbons. That is, they only contain single bonds between all carbon atoms. Alkanes are the basis of petroleum fuels and exist in linear and branched forms.
Unsaturated Hydrocarbons: Hydrocarbons that have one or more double bonds between carbon atoms are called alkenes.
Cycloalkanes: Any hydrocarbon containing one or more ring structures.
Aromatic Hydrocarbons: Aromatic hydrocarbons , also called arenes, are a unique class of carbon molecules in which carbon atoms are bonded by successive double and single bonds. This class of molecules has special ring structures in which the bonds between carbon atoms are an intermediate bond between single and double bonds.
Molecules in this class contain the industrial solvent "benzene".
Benzene (C6H6): Like other hydrocarbons, benzene is a natural component of petroleum. It is a colorless, flammable, sweet-smelling liquid at room temperature and is a component of most gasoline blends because of its high octane number.
Benzene is also highly carcinogenic and is well known to cause bone marrow failure and bone cancer. Of course, its carcinogenicity is not well known when used as an additive in aftershave and other cosmetics due to its "pleasant aroma".
The largest use of benzene (50%) is the product of styrene and polystyrene plastics. It is also converted into a molecule known as cyclohexane, which is important in Nylon production. About 15% of benzene is used to produce cyclohexane. Smaller amounts are used in everything from pesticides to rubber.
The benzene structure can be drawn in two ways. In the first, the double bond character is drawn explicitly. In the short handed version, a circle is drawn inside the ring to show the structure. There is only one hydrogen bonded to each carbon atom in benzene.
I. and II below. drawings are identical. III in practice. drawing is used.
Benzene is a colorless, flammable liquid with a boiling point of 80.1 ° C and a melting point of 5.5 ° C.
Binuclear Aromatic Hydrocarbons: They are compounds that contain two benzene rings in their molecules.
About
Kyäni, nutritional supplement products consisting of beneficial ingredients; It delivers to more than 50 countries around the world with unique business opportunities. We use Kyäni products daily to maintain our ideal health, share these products with others, devote a certain amount of time to work almost every day to build and maintain our business, and share our success with others by involving others in the Kyäni opportunity or contributing to the Potato Pak and Caring Hands programs.
About
Kyäni, nutritional supplement products consisting of beneficial ingredients; It delivers to more than 50 countries around the world with unique business opportunities. We use Kyäni products daily to maintain our ideal health, share these products with others, devote a certain amount of time to work almost every day to build and maintain our business, and share our success with others by involving others in the Kyäni opportunity or contributing to the Potato Pak and Caring Hands programs.
Page Under Construction.
Page Under Construction.
Training / Knowledge / Solution Platform
Petroleum Sources and Classification
Petroleum engineers examine drilling costs and their connections to other new or existing reservoirs as new wells are drilled. The daily amount of oil produced in a well at the beginning decreases over time due to the decrease in well pressure, water accumulation in the well and other factors. Since the running costs of each well are almost constant, in such cases the money spent on each barrel produced increases, the economic limit is crossed and ultimately production is stopped.
The product extracted from conventional petroleum reserves is naturally fluid, can be pumped undiluted, and methods other than standard production techniques are not required; Therefore, they are economically positive reserves.
Non-conventional oil reserves, on the other hand, require more production expenditure at varying rates depending on the type; These reserves can be grouped into three general groups,
1. Heavy Oils: These types of resources are similar to crude oil from conventional reserves, except that they are thicker and contain more sulfur and heavy metal impurities. Due to these undesirable properties, the refining steps are higher and therefore expensive.
2. Tar Sands: Obtaining oil from such reserves is done by surface excavation, mining or a suitable collection method.
3. Oil Shales: Much more refining and water is needed for resources from such deposits compared to crude oil extracted from conventional oil deposits.
Every state wants to know 'all the petroleum resources in its territory - existing reserves, discovered resources and potential reserves that may be discovered in the future. Therefore, a classification system covering all resource amounts is needed.
Such a system is vital in determining national resources and needs to be updated periodically over time. Important criteria in the classification system include the following data.
-
Evaluation of the petroleum resource area as a whole
-
Listing of resources and hydrocarbon accumulations in accordance with defined specifications
-
Suggested works and decisions taken at every stage of the work covering the exploration, development and production stages
-
Preparation of a long-term oil work program
-
Evaluating the impact of the oil work program on other industries
A well-prepared petroleum resources classification system should be understandable not only by related technical staff but also by financial institutions, analysts and politicians. How petroleum resources and reserves should be classified has been extensively debated among geophysicists, petroleum engineers, and resource economists for the last 30-40 years. Since the excess of variables in such classifications makes it difficult for all organizations (such as state institutions, international organizations, oil companies) to agree on a single system, various classifications have been made.
In defining resources, estimates are expressed in the following patterns:
Conservative forecast; low estimate
Realistic estimation; well estimate
Optimistic forecast is high estimation
(Original Resources): It is the amount of crude oil 'estimated' originally found in the earth's crust through natural deposits.
Discovered Resources: It is the sum of the gas and oil produced from a deposit until that day and the amount of gas and oil remaining.
Final Reserves (Ultimare Reserves): Explored producible resources; these are total production + future producible resources (reserves)
Reserves: The amount of gas and oil that can be estimated to be economically produced in the future from discovered resources.
Contingent Resources: It is a subclass of discovered non-reproducible resources; Although they can be technically produced, they still do not produce products because they are not economical.
Unrecoverable Resources: A subclass of discovered non-producible resources; Technically and economically, they cannot be produced.
Prospective Resources: These are undiscovered resources that can be produced in the future; Technically and economically, they can be produced.
Undiscovered Unrecoverable Resources: They cannot be produced technically or economically.
Proved Reserves: These are the reserves where the amount of gas and oil that can be recovered can be determined with high precision. The actual amount of production is equal to or more than the estimated proven reserves.
Probable Reserves: It is classified as unproven reserves; are additional or additional reserves. The accuracy of the estimated recoverable amount is lower than the proven reserves. The actual amount of production is greater than or equal to the estimated proven + possible reserves.
Possible Reserves: It is classified as unproven reserves; are additional or additional reserves. The accuracy of the estimated recoverable amount is lower than the possible reserves. The actual amount of production is equal to or greater than the estimated proven + probable + possible reserves.
Developed Reserves: It is hoped that production will be made from existing wells and facilities; It is divided into two categories as improved production reserves and improved non-production reserves.
Undeveloped Reserves: These are the reserves that require a significant amount of expenditure in order to make production. It requires drilling new wells or deepening existing wells to reach different reservoirs or similar studies.)
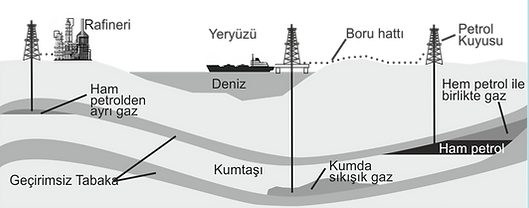

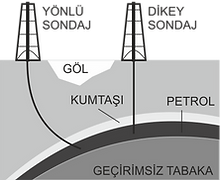
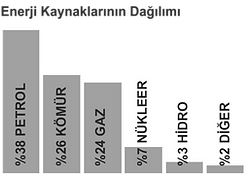
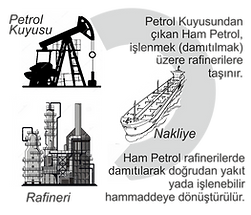
Refinery
Cracking and Petroleum Products:
Almost all petroleum products consist of petroleum distilled in petroleum refineries. Refineries produce petroleum products according to the quality of the crude oil and the need. Oil is generally preferred as energy: various grades of fuel oil and gasoline. Refineries can also produce other chemicals, some of which are used to make plastic or other products. Since it contains petroleum sulfur, most of this sulfur is also decomposed as a petroleum product. Hydrogen and carbon can also be used as products in the form of petroleum coke. Hydrogen is often used as a catalyst in other processes in the refinery or in hydrodesulfurization.
Cracking process; it is a transformation process; It is the process in which lighter hydrocarbons are obtained by breaking down heavy hydrocarbon molecules with heat and pressure (with or without catalysts).
The decomposition process of crude oil, whose main substance is Carbon (: C) and Hydrogen (: H), is simply as follows.
With this separation (: cracking) process, main products are produced under the headings of petrochemicals, naphtha, karosene, asphalt, diesel oil, gasoline, kerosene, tar, paraffin, liquefied natural gas. Calculation and evaluation are made with the "barrel" unit of measurement that we often hear.
Before Cracking Process: Crude oil has large molecular structure, high density, high boiling point, non-volatile, difficult fluidity and difficult to ignite.
After Cracking: Crude oil is converted into forms with smaller molecular structure, lower density, lower boiling point. As it transforms, intermediate products emerge and each time it becomes more volatile, easier to fluid, and more quickly ignited.
The main products of oil refineries:
(1 Barrel = 42 Gallons = 159.5 Lt) 80 percent of a barrel of distilled oil is for fuel purposes. 20 percent is asphalt and other petrochemical products. The approximate percentage distribution of products obtained from a barrel of crude oil is as follows. 43% (: 68.5 Lt) Gasoline 18% (: 29 Lt) Diesel 14% (: 22 Lt) Petrochemicals 11% (: 18 Lt) LPG 9% ( : 14 Lt) Jet Fuel% 5 (: 8 Lt) Asphalt
Asphalt:
It is a black and brown organic substance ranging from stable, durable to solid state.
Properties: The chemical composition of asphalt, which is mainly a hydrocarbon, is quite complex and variable and is obtained from the distillation of petroleum or natural deposits. Asphalt, which is widely used today, is a by-product obtained from petroleum refining. The black substance obtained during the distillation of mineral coal is pitch. Soil and / or stone is added to it.
Asphalt; It is used to cover roads, airports, roof insulation, and provide waterproofing in structures related to water. It has adhesive properties. It is used in paint industry, battery production, coating water channels and bonding clay bricks. Asphalt generally emerged as a result of the oxidation of petroleum. So it is of oil origin. In the form of mud and lakes, it is also found in hard form between rocks underground. Hard ones are extracted from underground as if mining. It is also found in sandstones and clays.
Diesel or Diesel:
It is one of the distillation products of crude oil used in diesel engines.
The third main product taken during the distillation of crude oil at the boiling range of 200-300 ° C is diesel. Diesel oil is diesel engine fuel.
The diesel machine, which is the most sufficient mechanism to convert the heat of combustion to mechanical power, was discovered by Diesel in 1892, approximately 30 years after gasoline and gas machines. One of the reasons for the development of a high compression machine was due to the desire to use cheaper fuels. In terms of thermal efficiency, diesel engine is more efficient than gas and petrol machines. Because it works with a higher compression ratio, since the first produced diesels were heavy-speed and large cylinders, it was possible to use the fuel oil offered on the market by spraying into the cylinder and burning it. However, over time, when diesel manufacturers reduced their machine sizes and increased the number of cycles to produce more power, it became a necessity to produce fuels that would meet this need. Due to the impossibility of producing a separate diesel fuel for each of them, as various machine manufacturers manufactured different types of engines, ASTM had to subject them to a classification.
Fuel oil:
Or fuel oil is a dark colored, low-fluid petroleum product. Fuel Oil, which can be used in electrical, heat or steam systems, is preferred in all kinds of industrial factories, facilities and buildings. It is easily pumped, burns and saves.
Gasoline:
A kind of fuel made from petroleum.
Petrol pumps
Crude gasoline up to 150 ° C,
• Kerosene, kerosene, jet fuel up to 150-250 ° C,
Diesel fuel up to 250-350 ° C,
• After 350 ° C, heavy oils are obtained.
Chemically, gasoline contains more than 120 hydrocarbons, depending on the characteristics of the crude oil. Most of them are saturated hydrocarbons and contain 4 to 12 carbons.
Synthetically, it is possible to obtain gasoline from coal by the method of German chemist Bergius. According to this method, coal is converted into liquid hydrocarbons by catalytic hydrogenation under high pressure.
Fischer-Tropsch combined carbon monoxide and hydrogen catalytically to form a liquid hydrocarbon. With both methods, more expensive and inferior gasoline is obtained. However, there is a possibility that these processes will have commercial significance in the near future.
Gasoline from the breakdown of organic compounds, catalytic or thermal decomposition, provides the high performance required by most of today's engines. Gasoline is mostly used as a fuel in internal combustion engines and to some extent in special stoves, and as a solvent in organic chemistry. Gasoline, which was thrown out in the early days of the oil industry, gained great importance with the development of the automobile industry. The boiling point of engine gasoline is between 32.2 ° C and 210 ° C. In order for it to function fully as an engine fuel, commercial gasoline must be produced with the following characteristics:
1. It should be able to burn without stopping under different load and speed;
2. For the engine to start easily, it should evaporate sufficiently in cold weather;
3. It should not cause clogging by evaporating excessively in hot weather;
4. Eliminate compounds with high boiling points that cause engine soot formation;
5. It should not cause oxidation in the warehouse;
6. It should minimize spark plug clogging and carburetor icing.
The sensitive mixture of gasoline with air in engines is regulated according to the climate and season. The most important factor that determines the quality of gasoline is the octane number. The octane number is a measure of gasoline's ability to resist hit during combustion. If the octane number is too small, the engine hits and suffers damage. If the octane number is too high, unnecessary money is paid because it is not desired to be of high quality. Since automobile engines require various octanes, a large number of gasoline with different octane numbers is introduced to the market. There are slight differences in the energies of the various types of gasoline. If the car runs without hitting a valve, the distances it travels with different gasoline are the same.
Oil :
Or stone oil is a product bought after gasoline in refineries. While it was used only for lighting purposes in the past, it has also started to be used as heating, cooling, tractor fuel and jet fuel.
It is used as jet fuel with the name of kerosene. Kerosene dissolves tar stains. Kerosene is a liquid fuel, never think of it as a gas fuel. Kerosene cannot burn directly. We can pour it on cloth (cloth, rags, etc.) and burn it like that.
Tar:
It is a viscous black liquid obtained from the destructive distillation of organic matter. Most of the tar is derived from coal as a byproduct of coke production, but is also obtained from petroleum, peat or sap in the trunks of some trees such as cypress and juniper.
Tar Types: The word "tar" is used to describe many different substances. Nature-found "tar pits" (for example La Brea Tar Pits in Los Angeles) actually contain asphalt, not tar, and are actually known as asphalt quarries. The tar sand sediments contain different proportions of gum and dense crude oil and sand (or stone), just like the Tar Tunnel in Shropshire, rather than tar. "Rangoon tar", also known as "Burmese Oil" or "Burmese Nefti", is actually petroleum. "Tar" and pitch are sometimes used interchangeably; However, the tar is more solid while the tar is more fluid. The tar is used in making cigarettes. The liquid form of the tar used in cigarettes as seen in the picture on the right.
Naphtha:
It is a product between gasoline and kerosene, obtained by distilling petroleum between 100ºC and 250ºC.
Paraffin Candle:
(Latin parum affinis), a colorless, odorless candle derived from petroleum. Paraffin wax was first produced by Carl Reichenbach in 1829 from wood tar; then from all layers; It was obtained from petroleum after 1867. Synthetic paraffin wax was also made in 1947. It is a byproduct of oil. In addition, the crude oil must be de-waxed. The oily paraffin obtained as a by-product in the refining of crude oil is first melted in hot, then it is cooled to freeze only the paraffin and the paraffin in the form of frozen pulp is separated from its oily parts by filtering. Today, modern paraffin factories also produce paraffin wax on the basis of the above principle. Paraffin waxes made according to new methods contain up to 20% oil. In some cases, the amount of fat is reduced up to 3%. With further purification, the color, odor and taste are further improved. Sulfate acid and clay are used in the purification process. Paraffin waxes are derived from paraffin-based petroleum types such as Poennsylvania crude oil. The melting point of crude paraffin wax varies between 37 and 48 ° C and the melting point of fully refined paraffin wax varies between 48 and 66 ° C. Paraffin wax with a high melting point is mostly alkanes with 26-30 carbons. Synthetic paraffin wax was obtained by the Fischer-Tropsch technique after the Second World War. In this method, the raw material is coal. It turns into hydrocarbons with the catalytic effect of magnetic iron from the mixture of carbon monoxide and H2 obtained from coal. Some of the products obtained are paraffin wax. These are very white and harder than paraffin wax made from petroleum. The molecular weight of synthetic paraffins with 50-55 carbons is around 750 on average. It is used as a substitute for waxes made from petroleum due to some properties. Paper and cardboard dipped in paraffin or coated with paraffin are used for storing liquid and solid foods. Because paraffin waxes do not react. It is used as chemical and electrical insulating material in various branches of industry. It is used in the production of plastic, explosive and electrical materials in textile, pharmacy, cosmetics industry, and in the isolation of vaccine places in viticulture. It has replaced beeswax in candle manufacturing.
Proportional distribution of all oil refining in the world over the continents.

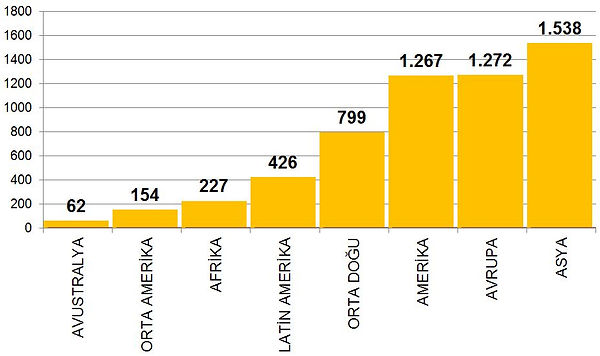
Turkey Petroleum Refineries
Information regarding oil refinery in Turkey which was established up to now, and capacity development to date of entry are given in the following circuit.
Boğaziçi Refinery:
crude oil processing capacity of 40 tons in 1930 near Beykoz / day (13 200 tonnes / year), this refinery private enterprise, "Turkey Naft Industries Inc." It was the first refinery plant established by Yaşua Brothers and processed crude oil from Romania. This refinery was closed in 1934 due to some tax issues.
Raman Experience Refinery:
When oil was discovered in Ramanda in 1940, the useful boilers of the Bosphorus Refinery located in the warehouses of the Diyarbakır Mineral Research and Exploration Institute were moved to the Maymune Strait in order to meet the fuel needs of oil drillings and other vehicles, and so Raman with a capacity of 10 tons / day (3 300 tons / year) established in the summer of 1942. Experience Refinery, which was established in Batman in 1945, served until the Pilot Refinery became operational.
Batman Experience Liquidation:
Another Pilot Refinery was established with the remaining materials and new additions belonging to the Boğaziçi Refinery located in the Diyarbakır MTA warehouse. The crude oil processing capacity of this refinery, which started operation in 1945, was 200 tons / day (66,000 tons / year), and was later transferred to TPAO.
Turkey Petroleum Refineries Corporation (Tüpraş) Batman Refinery:
Processing Capacity: 1.4 million tons / year
Nelson Complexity Value: 1.83
Sales: 538 thousand tons / year
Storage Capacity: 300 thousand mt3
Employed Staff: More than 4 00
In 1951, in line with the positive results obtained from oil exploration activities in the oil fields in Raman and Garzan, in order to make the best use of this national and natural underground oil resource, a modern refinery with a capacity of 1000 tons / day (330 000 tons / year) was established. decided. The construction of this refinery was completed in the middle of 1955 and trial studies started. After six months of work, Parsons Company transferred the refinery to TPAO and from 1956 the refinery started to operate at full capacity. Since 1959, oil exploration fields in Raman and especially Garzan have been developed and oil reserves have been determined, which makes it necessary to increase the annual capacity of the Batman Refinery by 75-100%. With the increasing need for crude oil production and petroleum products, the refinery's capacity was increased to 580 thousand tons / year in 1960, and in 1966 REFORMER and LPG units were added to the existing system to produce high-octane gasoline and LPG gas. With the Expansion Project carried out in 1972, the refinery's capacity was increased to 1.1 million tons / year.
Anadolu Tasfiyehanesi Anonim Şirketi (ATAŞ):
Founded in Mersin in 1958 by Mobil Oil, Shell, Caltex and BP, the name of the company is Anadolu Tasfiyehanesi Anonim Şirketi, and its short name is ATAŞ. The annual capacity of this refinery, which was established with foreign capital in accordance with the provisions of the Petroleum Law, was 3.2 million tons. CALTEX, one of the founders of ATAŞ Company, later left the partnership. In Anadolu Tasfiyehanesi Anonim Şirketi, MOREF (Mobil Refining) holds 51%, Shell 27%, BP-Turk 17% and Marmara Petrol 5%. In 1969, the refinery's capacity was increased to 4.4 million tons / year.
Istanbul Petrol Refinery Corporation (İPRAŞ) (İzmit Refinery):
Turkey Petroleum Corporation (TPAO), Turkey California Texas Oil Corp., which operates in the field of fuel distribution (CALTEX), 80 km from Istanbul, in the area of Tütünçiftlik on the northern shore of the Gulf of İzmit, to establish a refinery with an annual capacity of 1 million tons from the Petroleum Office on 10/12/1959. İstanbul Petrol Rafinerisi A.Ş. (İPRAŞ) was established to meet the petroleum products needs of our industry, civilians and the Turkish Armed Forces, 51% of which was owned by TPAO and the remaining 49% by CALTEX, an international oil company. The refinery was commissioned on August 24, 1961, 16 months after its foundation was laid on April 23, 1960. The 10-year partnership agreement between TPAO and Caltex expired on March 12, 1972, when Caltex's stocks were acquired by TPAO and the refinery became a completely national enterprise.
The Articles of Association of İPRAŞ were transformed into TÜPRAŞ's Articles of Incorporation at the Extraordinary General Assembly Meeting held on October 25, 1983, and TÜPRAŞ's registration and announcement was completed on November 16, 1983.
T urkiye Petrol Refineries Incorporated Company (TUPRAS) Izmit Refinery:
Processing Capacity: 11.3 million tons / year
Nelson Complexity Value: 14.5
Sales: 14.9 million tons / year
Storage Capacity: 3 million mt3
Employed Personnel: More than 2000
İzmir and Batman Refineries and Kırıkkale Refinery, which operate under TPAO, were transferred to TÜPRAŞ. The crude oil processing capacity of Izmit Refinery, which was 1.0 million tons / year in 1961, reached 2.2 million tons / year in 1967 with the 1st Expansion Project, 5.5 million tons / year with the 1st Extension Project in 1972, and the II. At the end of the Bottleneck Removal Project, it reached 7.0 million tons / year, 7.8 million tons / year at the end of the studies carried out in 1980, and 11.3 million tons / year at the end of the Second Extension Project completed in 1982. Euro VI standard makes production in Izmit Refinery, Turkey is situated in the center of the focus about 33% of consumption occurred as consumption of petroleum products. At the Izmit Refinery, the Residuum Upgrading Facility, which transforms 4.2 million tons of heavy black products into approximately 3.5 million tons of more valuable environmentally friendly white products such as gasoline and LPG at EU standards, mostly diesel oil, was completed at the end of 2014. With the activation of the Fuel Oil Conversion Facility, the İzmit Refinery has become one of the refineries with the highest conversion rate in the world, with a Nelson Complexity value of 14.5.
T urkiye Petroleum Refineries Incorporated Company (TUPRAS) Izmir Refinery:
Processing Capacity: 11.9 million tons / year
Nelson Complexity Value: 7.66
Sales: 9.7 million tons / year
Storage Capacity: 2.5 million mt3
Employed Personnel: More than 1400
Turkey in Izmir's Aliaga region to meet the growing demand for petroleum products in August 1967 laid the foundation of İzmir Refinery was commissioned in 1972. Crude oil processing capacity, which was 3 million tons / year in its establishment, increased to 3.8 million tons / year in 1982, 5.0 million tons / year in 1984 and 10 million tons / year at the end of the Expansion Project completed on November 18, 1987 with the Bottleneck Elimination Projects. has reached. In addition, the only machine oil complex of our country with a capacity of 300,000 tons / year is located in the İzmir Refinery. Vacuum, Propane Deasfalting, Furfurol Extraction, Ferrofining, Dewaxing, Hydrogen Units within the scope of the Machine Oil Complex project were put into operation on 23/4/1974. In 1988, the current machine oil production capacity of the İzmir Refinery was increased from 175 thousand tons / year to 300 thousand tons / year.
T urkey Petroleum Refineries Joint Stock Company (TUPRAS) Kirikkale Refinery:
Processing Capacity: 5.4 million tons / year
Nelson Complexity Value: 6.32
Sales: 4 million tons / year
Storage Capacity: 1.3 million mt3
Employed Personnel: more than 900
It was established within the framework of the credit agreement with the commercial agreement signed on 14 August 1977 between TPAO and ROMANIA INDUSTRIAL EXPORT IMPORT in order to meet the petroleum products need of the Central Anatolia Region. Kırıkkale Refinery has been designed to process 5 Million Tons of Kirkuk crude oil with 36 oAPI gravity annually. Crude oil supply of Kırıkkale Refinery is 447 km from Ceyhan Terminal of BOTAŞ. It is made with 24 inch long pipeline. Currently, its maximum capacity is 5.0 million tons / year. Kırıkkale Refinery was commissioned on October 25, 1986.
T urkiye Petrol Rafinerileri Anonim Şirketi (TÜPRAŞ) Körfez Refinery: The Yarımca Facilities, the first complex established by Petkim Petrokimya Holding A.Ş., started production in 1970 with Ethylene, Chlorine Alkali, Vinyl Chloride Monomer, Polyvinyl Chloride, Low Density Polyethylene Plants. Between 1972-1976, the Carbon Black, Styrene, Polystyrene, DDB, BDX, SBR, CBR and Kaprolactam Plants were also commissioned and the Yarımca Facilities were established. PETKİM, which entered into a crisis with the World Petrochemical Industry since 1990, ceased the production of Chlorine Alkali, Ethylene, Styrene, LAB (DDB) and Caprolactam Plants in Yarımca Facilities between 1990-1995. The production of PE, PVC and VCM factories was also terminated in 2001. Half of Plants, the Privatization High Council of the date 05.10.2001 and have been transferred to Turkey Petroleum Refineries Inc. with Decision No. 2001/54 and Gulf Petrochemical and Refinery Directorate has taken its name. Emulsion Styrene Butadiene Rubber (SBR), Solution Butadiene Rubber (CBR), Carbon Black (KS), Polystyrene (PS) and Butadiene Extraction (BDX) Factories continue production.
Nelson Complexity
(Nelson Complexity Index) The value of refineries in the world is measured in a unit called “Nelson Complexity (NK)”. It expresses how much high value-added final product can be produced from one unit of crude oil. The Nelson Index is a frame of reference used to assign values to oil refineries based on their level of complexity.
NKE was developed by Wilbur Nelson in 1960. Because it is difficult to understand the details of how a refinery works without specific industry knowledge, NKE can understand the complexity of the different refiners. It offers an easy methodology to measure and rank.
It is a pure cost index that provides a relative measure of construction costs based on crude oil and upgrading capacity of a particular refinery. Compares the costs of various product units with the cost of a pure crude oil distillation unit. Calculating the index is an attempt to measure the relative cost of a refinery based on the additional cost of various upgrade units and the relative upgrade capacity.
NKE is measured on a scale of 1 to 20; where the lower numbers represent refineries that are simple in nature and produce lower quality fuels such as jet fuel and heating oil. Higher numbers represent more complex and expensive refineries producing large volumes.
The higher a refinery's Nelson Index score, the more complex it is. More complex refineries are capable of processing and producing a wider range of products and therefore have more economic value. This index is used to break down information about refineries in simple terms, easy for people to understand. No special knowledge of the oil and gas industry is needed to contextualize a score.
To determine the Nelson Index for an individual refinery, a score is assigned to each piece of equipment in the refinery and the scores are added together. The more equipment a refinery has, the more versatile and flexible it is. Refineries with low scores can handle oil in a limited range of grades, for example; for example, a refinery with a high Nelson Index may use lower quality raw materials in addition to higher value raw products. This allows refinery managers to take advantage of the cheapest crude oil on the market, rather than forcing them to purchase expensive, quality crude oil for all their production needs. In addition to processing a range of crude grades, a refinery with a high Nelson Index can also produce more oil and gas products. This expands the production potential.
Refineries can adjust production to meet market needs, take advantage of higher prices for certain products, and accelerate production of products that are not currently selling well in the open market. This increases profit potential and keeps refiners in continuous production.
On average, US refineries are the most complex in the world, according to NKE. Refining plays a vital role in preserving the nation's fuel resources. In Europe, for example, many refineries have closed because they cannot produce the quality fuel demanded by modern consumers and because of the costs involved in developing refineries.
Petroleum Industry
About one-third of the world's oil comes from offshore wells. Drilling work is based on the principle that a drill bit attached to the cable end is dropped into the well with a certain acceleration. Today, rotary drilling systems are used in oil exploration and operation. These are land and sea. They are designed in different systems for oil fields. Well-known and practiced drilling types are conventional vertical drilling and directional or inclined (slant, horizontal) drilling.
Conventional (Vertical) Drilling: It is a vertical drilling from the surface to the reservoir where the oil is located. Although these methods are traditional, they are still among the most applied methods.
There are sub-types such as percussion drilling, rotary drilling, impact and rotary drilling.
Directional Drilling: It is a type of drilling that is diverted from the vertical position when drilling a production well, especially in wells drilled in the sea. This type of drilling is applied to beds that cannot be reached vertically. For example, reaching deposits below shallow lakes, protected areas, railroads, or any area where drilling rigs cannot be installed is a common practice. In addition, this method is preferred since long and thin beds cannot be reached by vertical drilling.
Most of the world's oil production is controlled by state institutions, not private companies. More than half of the total world oil reserves are controlled by government agencies in the Middle East. Intertwined with national institutions and global companies, The fact that they have intricate relationships complicates things a bit in this huge industry. To facilitate this, the oil industry can be divided into two main categories: National Petroleum Corporations (NOCs) and International Petroleum Corporations (IOCs). International Oil Companies include familiar names such as ExxonMobil, Royal Dutch Shell, BP Amoco.
Its national institutions are set up like any international oil company.
The main element that distinguishes these two company groups from each other is; international oil companies publish their earnings reports and have stocks.
The world's largest national institutions in terms of reserve size are Saudi Armaco and Iranian Petroleum. The union of these national institutions is defined as OPEC. OPEC founders; Saudi Arabia, Iran, Kuwait, Iraq and Venezuela. Qatar (1961), Libya, Indonesia, Ecuador, United Arab Emirates, Algeria, Nigeria, Gabon and Angola joined later.
Petroleum Refineries production capacities of countries:

Capacities of the World's Largest Oil Refineries:

Capacities of the World's Largest Oil Refining Companies:

Oil and natural gas
Natural gas; Composed of light molecular weight hydrocarbons such as methane (CH4), ethane (C2H6), propane (C3H8)
it is a mix. It can be found underground alone or with oil. Natural
The gas is separated on the surface and the heavy hydrocarbons (butane, pentane, etc.) in it are removed. Natural
gas is the cleanest fossil fuel we use in our homes. When natural gas is burned, carbon dioxide, water vapor and nitrogen oxides are formed.
Oil and natural gas are composed of the same type of hydrocarbon molecules. Only oil is in liquid form.
All hydrocarbons are the same in that they contain hydrogen and carbon atoms, but they differ in the number of carbons they have, their level of saturation, whether linear or cyclonic, aromatic or not. Natural gas can be found alone underground, as well as in oil reservoirs as a gas cap and/or dissolved in oil.
Liquefaction Before Piping:
The most common method of natural gas transportation and distribution is the use of pipelines. The natural gas from the borehole is not pure. It also produces different additives, harmful gases such as hydrogen sulfide and carbon dioxide, which can damage technical equipment. The gas is cleaned several times at the full well outlet, surface separators, as well as during transmission and at compressor stations, before being pumped into the transmission lines. The gas coming out of the well is moist. In this state, the gas must be dried beforehand, as it may cause moisture accumulation, crystallization and blockages in the lines. Cooling is provided by using absorbents in gas cooling facilities or by reducing the pipeline diameter and pressure. In addition, natural gas, which is odorless, is odorized before being pumped into the line to ensure recognizability.
Before the gas is pumped into the line at the compressor station, it is again cooled by air-cooling air conditioners. Condensation is created and the volume of the gas is reduced, making its transportation easier and increasing the line capacity. After being cleaned from additives to the condensation temperature (-161.5 °C), the cooled natural gas turns into a liquid called “liquefied natural gas” (LNG). One of the most important advantages of this technology is that the gas volume is reduced by 600 times during liquefaction. LNG is produced at liquefaction plants (plants) and then transported in special cryogenic tanks: marine tank ships or tank cars. It provides rapid delivery of gas to areas located far from the gas main lines traditionally used for conventional natural gas transmission. Liquefied natural gas can be stored for a long time, making it possible to build up stocks. The first attempts to liquefy natural gas for commercial purposes date back to the early 20th century. In 1917, the first LNG was produced in the USA, but the development of pipeline systems long delayed the development of this technology. The next attempt to produce LNG was made in 1941, but production reached commercial scale only in the mid-1960s. Construction of the first LNG power plant in Russia under the Sakhalin II project started in 2006.
In terms of efficiency, natural gas line pipe diameters are max. It is considered to be 1,420 millimeters.
The enterprise with the world's largest gas transmission system; Russian Gazprom. The length of the lines of the enterprise in Russia is 171,200 kilometers. (Length to circumnavigate the globe four times.)
Liquefied petroleum gas LPG:
LPG, in other words Liquefied Petroleum Gas, is a colorless, odorless, heavier than air and flammable gas obtained during the distillation of crude oil in refineries or by separating the natural gas found on petroleum deposits and liquefied under pressure. In the event of a leak, it has been specifically scented by refineries so that the gas leak can be recognized immediately. The composition of the mix LPG used in our country is generally 70% butane and 30% propane. When one liter of LPG gasses, it reaches a gas volume of approximately 250 liters under normal conditions. LPG is not volatile like natural gas and sinks to the bottom.
Advantages of LPG:
LPG is a fuel that consumers can safely use, provided that the conditions of use are followed. LPG is a type of energy that provides all the benefits of natural gas and does not require any central infrastructure. LPG is an environmentally friendly fuel compared to other energy sources due to its simple chemical structure. LPG is a form of energy that can be packaged and transported. LPG is also an efficient fuel with a high heating value compared to other fuel types. LPG can meet nearly all the energy needs of any living unit.
Usage Areas of LPG:
Heating, Cooking in the kitchen and as fuel in vehicles. With the widespread use of natural gas in our country, its use in vehicles has become increasingly common, while consumption in heating and kitchens has decreased. LPG used in vehicles and also called autogas is slightly different from bottled gas used in the kitchen.
Crude Oil and Natural Gas Unit Conversions

Oil Transportation
Pipeline Transportation:
Pipeline transportation, which has a higher investment cost compared to land and sea transportation; It has advantages such as being fast, safe, environmentally friendly and not affected by atmospheric conditions compared to other transportation types, as well as paying the investment in a shorter time. For this reason, the most economical way of transporting oil and natural gas from production centers to consumption areas is through pipelines.
Pipelines are generally examined in two parts as crude oil pipelines and natural gas pipelines. Crude oil pipelines transport oil from areas with rich deposits to ports or markets. With natural gas pipelines, natural gas is delivered to the markets rapidly.
Approximately 65.8% of the world's proven oil reserves are located in the Ona East Region. While Saudi Arabia, one of the countries in the region, has 25.9% of these reserves and 39% of the regional reserves, Iran has 12.7 billion tons of I4 %. The oil reserves of the Commonwealth of Independent States constitute 5.8% of the world's reserves with 7.8 billion tons.The share of Kazakhstan in the Community is 0.7 billion tons and Azerbaijan's 0.2 billion tons. The transportation of Kazakh and Azeri oil, which makes up the Caspian oil, to the Mediterranean is a topic on the agenda. The way to this is the Baku-Ceyhan line. However, it is not possible to transport all of the Caspian oil to the Mediterranean, which carries 1/6 of the world's oil, via this line. It may be possible to serve the Mediterranean hinterland by using it as a transit route. It is necessary to take lessons from the Iraq-Turkey oil pipeline while the pipelines are being built. The pipeline should not be affected by bilateral relations. to reach the countries of the world other than the countries of the region. It must be transferred for processing directly to the terminal at the distribution center. Any work to be done other than this will be the product of an ideological policy. In this case, it can always be disrupted and cause problems or even not work. The biggest obstacle of oil pipelines is the uncertainty of the future of the unstable region countries and what they will do.
Advantages of Pipeline Transportation:
• Pipelines are not affected by weather and traffic problems.
• It is the transportation method with the highest fixed and lowest variable costs among all transportation types.
• Once installed, it is the cheapest mode of transport.
Disadvantages of Pipeline Transportation:
• A major disadvantage of the pipe farm is its inelastic nature (which is inherent in the overcrowding demand. Once built at great cost, it is not easy to adapt to the increase in demand. The installation cost is high and requires expertise. Changing the carrying capacity brings additional costs. A change in supply or demand The reduction may affect the economic independence of the system by causing a decrease in income.
• Geographical shifts in production or consumption are another limitation; The pipeline built between two places cannot easily adapt to changes.
• Environmental concerns may come to the fore due to the suspicion that the construction of pipe fault routes may harm the natural life.
Highway transports:
Due to its flexibility, it ranks first compared to other transportation methods and is of great importance in international transportation. However, it is the type of transport where competition is most intense.
In road transport, trucks, tankers, trucks, etc. motor vehicles are used.
When the development of road transport is examined, II. It is seen that it has developed rapidly after World War II and is the most useful type of transportation and one of the most used transportation methods in the world.
Considering that each land tanker can carry 8-15 tons of oil, the transportation of 2-3 million barrels of crude oil produced in the Caucasus and Caspian regions by road from the production area to the port complexes where it will be loaded onto ships is not suitable for feasibility calculations. The reasons such as the operating cost, depreciation, enormous amount of vehicle traffic, and fuel consumption of land tankers have made this type of transportation far from being economically acceptable. Ships at the other end of the transport terminal, each capable of carrying 100-300 thousand tons of oil, will have to wait for 10,000-30,000 land tankers, each with a carrying capacity of 10 tons, to load and fill. This situation requires the port tying tax, insurance and other freight transactions for a long period of time, which will make the transportation cost far from being economical.
Road transport is advantageous in terms of accessing almost every endpoint. However, the transport distance must be short. As the distance grows, the economy disappears. For this reason, land transportation is not as suitable for mass transportation as other alternative transportation systems.
Advantages of Road Transport:
• The fact that road transport is carried out on all kinds of roads makes it superior in terms of market area and number it covers.
• Road transport provides access to any country or place with a road connection.
• It does not require an expensive infrastructure.
• It is the most suitable transportation method for door-to-door transportation.
• Terminal requirement is mostly low and investment costs at terminal points are lower than others.
• It does not require any difficulty in loading and unloading by providing fast service, such operations can be done easily even at night.
Disadvantages of Road Transport:
• In road transport, it is not possible to reach places without a road connection.
• Bad weather conditions adversely affect road transport.
• Likewise, road transport is adversely affected by traffic problems.
• There are weight and size limitations in terms of overflow.
• Costs are high due to the high energy consumption.
Maritime transport:
Today, approximately 55% of the world's oil transportation is carried out by tankers, most of which are owned by large oil companies, and oil transportation constitutes more than 50% of the tanker traffic in the world's seas. As a natural consequence of this development, oil pollution in the seas has grown rapidly in parallel with the increasing oil demand and production; In today's world, it has gained a very critical importance, especially when the transportation system of Caspian oil will be delivered to the world markets.
The fact that the Caspian Sea is surrounded by land prevents the direct access to the sea of the oil fields of Azerbaijan and Kazakhstan in the Caspian Basin, where the amount of oil that can be exploited is quite high. In this respect, the transportation of the crude oil to be produced to foreign markets will necessarily be dependent on oil pipelines up to the seashore and on tankers for its subsequent transportation.
The critical choice in question here is how much oil will be transported to the shore by pipelines from which routes and then maritime transportation will be started. When it is aimed to reach the Black Sea by keeping the pipelines short, there is a long sea passage; thus endangering the relevant environmental areas of Turkey, primarily the Black Sea and then the Turkish Straits. The intensity of this maritime transport will bring environmental risks in the straits. In addition, maritime transport is preferred for the transport of low-value products where the speed factor is not very important.
Advantages of Sea Freight:
• Seaway transportation has a great place in international and even intercontinental transportation, as it is an effective and cheap transportation method.
• Sea transportation is the most economical transportation method; The reason for this is that transportation costs are low due to reasons such as the ability to carry large amounts of cargo and low energy consumption.
• Sea transport is seven times cheaper than road and two and a half times cheaper than rail; In terms of fuel consumption, it is four times cheaper than the road and two times cheaper than the railway.
• Considering the competition in the world markets, maritime transport has a very important position in terms of economy.
• The most important advantage is that it enables the transportation of very large volumes of products.
• Its reliability is high.
Disadvantages of Sea Freight:
• Expensive facilities such as ports and piers are needed, the establishment of the transportation network is related to the coast and ports.
• It is a slow transportation method.
Rail Freight:
The operating cost is lower than road transport. Thanks to its suitability for railway transport, its very low energy consumption and high speed, railway transport is an economical transport option especially for long distance transports. However, investments such as the improvement of the existing railway network or the construction of a new railway, the improvement of existing cistern wagons or the purchase of new ones are also factors that negatively affect the economic operation of oil reserves. In addition, export by rail is considered as a risky mode of transportation that may be interrupted due to political and social instability.
rail transport; filling loading and safety measures to be taken are all the same as road transport.
Advantages of Rail Freight:
• Compared to road transport, railways consume less energy in both freight and passenger transport.
• In terms of sound pollution, it is less noisy than roads and airlines.
• Its effect on air, water and soil pollution is less compared to land and airlines.
• Requires less land than highways.
• It is less affected by adverse weather conditions such as fog, frost and rain compared to highways; this is an important factor in terms of safety, comfort and convenience.
• Railway construction cost is cheaper than highway construction cost.
• Since the share of fixed costs in total costs is high in railway transportation, it is the most convenient and economical type of transportation, especially for mass transportation.
Disadvantages of Rail Freight:
• The market area it covers is more limited compared to road transport.
• Since the initial investment costs are high in railway transportation, it is generally established and operated by the state.
Airways transporting :
It is a transportation that is not preferred in the oil sector.


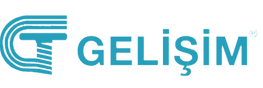
Oil and gas pipe valves
For more information about
Gelişim Valf ve Makina San.Tic.Ltd.Şti.
to the page prepared with their contributions
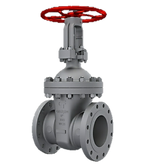
Turkey Crude Oil Pipelines
Iraq-Ceyhan Oil Pipeline:
The Iraq-Turkey Crude Oil Pipeline System transports the crude oil obtained from Kirkuk and other production fields of Iraq to the Ceyhan (Yumurtalık) Marine Terminal.
delivers. The pipeline with an annual transport capacity of 35 million tons was established in 1976.
was commissioned and the first tanker loading was carried out on May 25, 1977.
The capacity of the line was increased to 46.5 million tons/year with the 1st Extension Project, which started in 1983 and was completed in 1984. II, which is parallel to the I. Pipeline and was put into operation in 1987. With the Pipeline, the annual transport capacity has reached 70.9 million tons (500 million barrels).
BOTAŞ owns the part of the line remaining in Turkish territory, and this
It also undertakes the operation, control, maintenance and repair of the part.
Batman-Dortyol Oil Pipeline:
To deliver the crude oil obtained from Batman and its surroundings to the consumption points
The ownership of the line, which was put into operation by Turkish Petroleum Corporation on January 4, 1967, was transferred to BOTAŞ on February 10, 1984. It is Turkey's first commercial pipeline.
It reaches the Iskenderun Bay from Batman and ends in Dörtyol. The length of the pipeline, which has an annual capacity of 3.5 million tons, is 511 km. Crude oil produced in Batman, Diyarbakir and Saril Region is also transported to Dörtyol with the supply lines integrated into the pipeline. There are 14 storage tanks in Batman and Dörtyol Terminal, as well as 4 tanks in Sarıl and 4 tanks in Diyarbakır.
Ceyhan-Kırıkkale Oil Pipeline:
Pipeline meeting the crude oil needs of Kırıkkale Refinery, Turkey
Petrolleri Anonim Ortaklığı in October 1983, was transferred to BOTAŞ.
It was put into operation in September 1986. 24 inch diameter 448 km. The line, which has a capacity of 5 million tons/year, can be increased to 10 million tons/year. its route; Adana, Niğde, Aksaray, Ankara, Kırıkkale. The pipeline system starting from Ceyhan Marine Terminal and ending at Kırıkkale Refinery 2 pumping stations, 1 pigging station, 1 DT (Kırıkkale) Station, 3 50,000 m3 storage tanks, 5 10 m3 slops tank, 1 relief tank of 1,500 m3 and the terminal located at the refinery site.
Şelmo - Batman Crude Oil Pipeline:
The pipe carrying the crude oil produced in the Şelmo field to Batman Terminal
The length of the line is 42 km and its annual capacity is 800,000 tons. It was closed in 2007. The reason for the closure is; pipes rot, corrosion and oil theft is too much. Due to its high cost, its activities were terminated at the request of TPAO.
Baku - Tbilisi - Ceyhan Oil Pipeline:
It is a project designed to transport the crude oil to be produced in the Caspian Region to the world markets. It has a total length of 1,774 km, of which 1,074 km is within the borders of Turkey.
With a capacity of 50 million tons/year, it is Turkey's largest international crude oil pipeline. This line, which starts from the Sangachal terminal on the shore of the Caspian Sea, passes through Georgia and reaches Turkey. It reaches Ardahan, Kars, Gümüşhane, Erzincan, Erzurum, Sivas, Kayseri, Kahramanmaraş, Osmaniye and Adana.
BTC Pipeline Shareholders:
• BP (UK): 30.1%
• State Oil Company of Azerbaijan (SOCAR) (Azerbaijan): 25%
• Chevron (US): 8.9%
• StatoilHydro (Norway): 8.71%
• Turkish Petroleum Corporation (TPAO) (Turkey): 6.53%
• Eni/Agip (Italy): 5%
• Total (France): 5%
• Itochu (Japan): 3.4%
• Inpex (Japan): 2.5%
• ConocoPhillips (US): 2.5%
• Hess Corporation (USA) 2.36%
The most strategic places in pipelines are pumping stations. Damage to the pipeline itself is more difficult and any possible damage can be repaired quickly. However, the failure of one of the pumping stations means that the pipeline cannot be utilized for a long time. Therefore, the pumping stations are kept under strict protection.
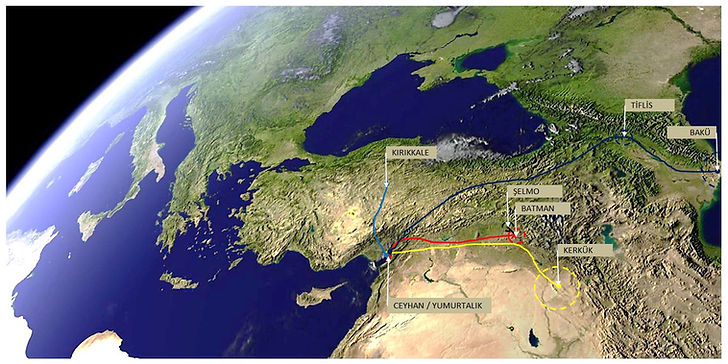
Turkey Natural Gas Pipelines
Turkish Stream Natural Gas Pipeline:
TurkStream opened the line in 2020, connecting the largest gas reserves in Russia directly to the Turkish gas transportation network, creating a reliable energy source for Turkey, Southern and Southeastern Europe. The line, which covers 935 km under the Black Sea between Russkaya compressor Station in Anapa, Russia and Kiyikoy Reception terminal in Kırklareli visa district, consists of two pipes with 81 cm diameter. The deepest point where it proceeds under the sea is at a depth of 2200 meters. The length of each piece of pipe is 12 meters in the line created by joining together. While one of the TurkStream line pipes carries gas to the Turkish market, the other transits to Bulgaria and beyond to the southeast of Europe via Lüleburgaz. Both pipes carry 15.75 billion mt³/year of gas. In other words, the carrying capacity of the line is 31.5 billion mt³/year.
Trans Anatolian Natural Gas Pipeline (TANAP):
It is the pipeline through which 16 billion m³/year natural gas will be transported from the Azerbaijan Shah Deniz natural gas field. 37.5% of the transported gas is distributed to the Turkish market and 62.5% to the European market. The eastern end of the line, which started operating in 2018; It is connected with the South Caucasus Pipeline (SCP) at Ardahan Posof and with the Trans-Adriatic Pipeline (TAP) at Edirne İpsala at its western end. The TANAP between these two terminals is 1850 km long. With this length and 56 inch diameter, it has the title of the longest and largest diameter natural gas pipeline in Turkey, the Middle East and Europe. The TANAP line runs completely parallel to the SGC (Southern Gas Corridor).
Turkey-Russia Blue Stream Natural Gas Pipeline:
With this line, the construction of which was agreed between BOTAŞ and Gazexport in 1997, it was aimed to introduce 16 billion m³/year of natural gas to the Turkish market. The pipeline was built by Blue Stream Pipeline BV, which was established by the partnership of Russian Gazprom, headquartered in the Netherlands, and Italian ENI. The entire line was put into operation in 2005. The line between Russia Izobilnoye and Turkey Ankara consists of three stages.
The financing and construction of the part of the said natural gas pipeline on the territory of the Russian Federation and the Black Sea passage was undertaken by the GAZPROM Company, while the financing and construction of the Turkish section was undertaken by BOTAŞ. Within the scope of the project, the construction of Pressure Reducing and Measuring Station in Samsun - Durusu was completed on 15 October 2002. The part of the Blue Stream Project in Turkey starts from Samsun and reaches Ankara via Amasya, Çorum and Kırıkkale and is connected to the Main Line. The line was put into operation on February 20, 2003, and the official opening ceremony was held on November 17, 2005.

Turkey-Russia Western Natural Gas Pipeline:
As a result of research on alternative energy sources, the project was approved in 1984. Within the scope of the agreement; Since 1987, natural gas has been started to be purchased in gradually increasing amounts, and the maximum amount of 6 billion m³/year was reached in 1993. The line that enters our country from Malkoçlar on the Bulgarian border and reaches Ankara by following the route of Hamitabat, Ambarlı, Istanbul, Izmit, Bursa, Eskişehir is 845 km long. During the process, the capacity of Malkoçlar Measurement Station located on the Bulgarian border was increased from 8 Billion m³/year to 14 Billion m³/year.
Turkey-Iran Eastern Natural Gas Pipeline:
The foundation of the line, which introduces 10 billion m³ of Iranian natural gas to the Turkish market per year, was laid in 1996, and gas purchases began in 2001. The pipe diameters of the approximately 1491 km long line built within this scope vary between 16 and 48 inches. The Eastern Anatolia Natural Gas Main Transmission Line extends from Iran Bazargan measurement station to Doğubayazıt, Turkey, and from there to Ankara via Erzurum, Sivas and Kayseri, and one branch reaches Seydişehir via Kayseri, Konya.
Baku-Tbilisi-Erzurum (BTE) Natural Gas Pipeline:
The line, which will carry 6.6 billion mt³ of gas from the South Caspian Sea of Azerbaijan to the Turkish market, was put into service in 2007.
