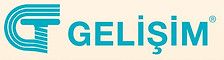


Hydrocarbons
It is an organic compound consisting of two elements, hydrogen and carbon. Most of the petroleum composition consists of hydrocarbons of varying lengths.
The smallest hydrocarbon methane consists of a single carbon atom and four hydrogen atoms. However, hydrocarbons can consist of hundreds or thousands of individual atoms linked together in many ways, including chains, circles, and other complex shapes.
In order to classify the properties of hydrocarbons, they are divided into several basic types.
Alkanes: These are called saturated hydrocarbons. That is, they only contain single bonds between all carbon atoms. Alkanes are the basis of petroleum fuels and exist in linear and branched forms.
Unsaturated Hydrocarbons: Hydrocarbons that have one or more double bonds between carbon atoms are called alkenes.
Cycloalkanes: Any hydrocarbon containing one or more ring structures.
Aromatic Hydrocarbons: Aromatic hydrocarbons , also called arenes, are a unique class of carbon molecules in which carbon atoms are bonded by successive double and single bonds. This class of molecules has special ring structures in which the bonds between carbon atoms are an intermediate bond between single and double bonds.
Molecules in this class contain the industrial solvent "benzene".
Benzene (C6H6): Like other hydrocarbons, benzene is a natural component of petroleum. It is a colorless, flammable, sweet-smelling liquid at room temperature and is a component of most gasoline blends because of its high octane number.
Benzene is also highly carcinogenic and is well known to cause bone marrow failure and bone cancer. Of course, its carcinogenicity is not well known when used as an additive in aftershave and other cosmetics due to its "pleasant aroma".
The largest use of benzene (50%) is the product of styrene and polystyrene plastics. It is also converted into a molecule known as cyclohexane, which is important in Nylon production. About 15% of benzene is used to produce cyclohexane. Smaller amounts are used in everything from pesticides to rubber.
The benzene structure can be drawn in two ways. In the first, the double bond character is drawn explicitly. In the short handed version, a circle is drawn inside the ring to show the structure. There is only one hydrogen bonded to each carbon atom in benzene.
I. and II below. drawings are identical. III in practice. drawing is used.
Benzene is a colorless, flammable liquid with a boiling point of 80.1 ° C and a melting point of 5.5 ° C.
Binuclear Aromatic Hydrocarbons: They are compounds that contain two benzene rings in their molecules.
Hydrocarbons
It is an organic compound consisting of two elements, hydrogen and carbon. Most of the petroleum composition consists of hydrocarbons of varying lengths.
The smallest hydrocarbon methane consists of a single carbon atom and four hydrogen atoms. However, hydrocarbons can consist of hundreds or thousands of individual atoms linked together in many ways, including chains, circles, and other complex shapes.
In order to classify the properties of hydrocarbons, they are divided into several basic types.
Alkanes: These are called saturated hydrocarbons. That is, they only contain single bonds between all carbon atoms. Alkanes are the basis of petroleum fuels and exist in linear and branched forms.
Unsaturated Hydrocarbons: Hydrocarbons that have one or more double bonds between carbon atoms are called alkenes.
Cycloalkanes: Any hydrocarbon containing one or more ring structures.
Aromatic Hydrocarbons: Aromatic hydrocarbons , also called arenes, are a unique class of carbon molecules in which carbon atoms are bonded by successive double and single bonds. This class of molecules has special ring structures in which the bonds between carbon atoms are an intermediate bond between single and double bonds.
Molecules in this class contain the industrial solvent "benzene".
Benzene (C6H6): Like other hydrocarbons, benzene is a natural component of petroleum. It is a colorless, flammable, sweet-smelling liquid at room temperature and is a component of most gasoline blends because of its high octane number.
Benzene is also highly carcinogenic and is well known to cause bone marrow failure and bone cancer. Of course, its carcinogenicity is not well known when used as an additive in aftershave and other cosmetics due to its "pleasant aroma".
The largest use of benzene (50%) is the product of styrene and polystyrene plastics. It is also converted into a molecule known as cyclohexane, which is important in Nylon production. About 15% of benzene is used to produce cyclohexane. Smaller amounts are used in everything from pesticides to rubber.
The benzene structure can be drawn in two ways. In the first, the double bond character is drawn explicitly. In the short handed version, a circle is drawn inside the ring to show the structure. There is only one hydrogen bonded to each carbon atom in benzene.
I. and II below. drawings are identical. III in practice. drawing is used.
Benzene is a colorless, flammable liquid with a boiling point of 80.1 ° C and a melting point of 5.5 ° C.
Binuclear Aromatic Hydrocarbons: They are compounds that contain two benzene rings in their molecules.
About
Kyäni, nutritional supplement products consisting of beneficial ingredients; It delivers to more than 50 countries around the world with unique business opportunities. We use Kyäni products daily to maintain our ideal health, share these products with others, devote a certain amount of time to work almost every day to build and maintain our business, and share our success with others by involving others in the Kyäni opportunity or contributing to the Potato Pak and Caring Hands programs.
About
Kyäni, nutritional supplement products consisting of beneficial ingredients; It delivers to more than 50 countries around the world with unique business opportunities. We use Kyäni products daily to maintain our ideal health, share these products with others, devote a certain amount of time to work almost every day to build and maintain our business, and share our success with others by involving others in the Kyäni opportunity or contributing to the Potato Pak and Caring Hands programs.
Page Under Construction.
Page Under Construction.
Training / Knowledge / Solution Platform
About the Process
Process-related definitions: The process transforms a certain series of inputs into a specific output for the customer, into a sequence of activities that can be defined, measured, and create interdependent value .
- A process is a set of interrelated business activities that include specific inputs and produce certain outputs, characterized by value-added efforts.
- It is a collection of people, equipment, materials, methods and environmental elements that interact with each other to achieve a specific output.
It is the combination of activities that transform business inputs into business outputs.
- Processes are a combination of three main types of activities: Activities that are important to new customers creating value; basically activities that provide work flow across functional, departmental or organizational boundaries; control activities.
- An organizational process means work with a certain beginning and end. In other words, it is the set of sub-jobs and detailed jobs required to do this job.
- Processes, in the simplest terms, are what a business does for its customers.
- Processes are the logical collection of work that creates the product / service of the enterprise.
- A business process is a collection of activities from which one or more kinds of inputs are taken and an output is created from them that will create value for the customer.
- Processes arise from the analysis of successive changes in state, that is, a process is a sequence of activities in which inputs are transformed into outputs through changing the state of one or more related entities.
- It is a work flow in the process logic chain.
- He definitely has a customer. Also, the process itself can be a customer.
- The process has a super-functional structure.
Process Concept: As can be understood from the definitions above, the process can either take place within a certain function or be inter-functional within the enterprise. There are three common features in all processes.
1- Conversion: Processes can transform the input into a more valuable output. In physical transformation, while a concrete product emerges, information is created by processing data in information transformation.
2- Feedback control: Reentering the information resulting from the process as data into the process is called “feedback”. Feedback control prevents the process from getting out of control.
3- Repeatability: It is the feature of a prsoses that works in the same way over and over.
Process Properties: Identifiable: It is the feature of determining the basic elements of the process.
- Measurable: It is the ability to monitor the process with performance criteria / indicators.
- Repeatable: It is the ability to continuously meet customer needs and expectations of the output generated as a result of processing the same and / or changing inputs that set the process in motion.
- Controllable: It is the feature that process managers can always have information about the performance of the process and can carry out corrective actions when necessary.
- Value added: It is the ability of the process to have a positive effect on the quality of the output and the satisfaction of the customer using the output.
Basic Elements of the Process: Suppliers: Persons and / or organizations that supply one or more of the inputs of the process. Suppliers can be internal or external to the organization.
- Inputs: Inputs are the elements that the process uses to achieve the transformation. 3 kinds of inputs can be observed in the processes. 1. Physical inputs (Ex: raw materials, materials, machinery), 2. Support (Ex: training of staff), 3. Information (Ex: Customer expectations)
- Outputs: Each process of the process produces some kind of output. Outputs are the elements that a process produces by transforming.
- Customers: Customers are the points that receive the process outputs.
- Process performance criteria: Indicators used to measure the degree to which the process meets customer needs and expectations.
- Customer needs and expectations: These are the features defined by the customer or on behalf of the customer regarding the products and services that are process outputs.
- Process activities: These are the activities included in the process that transform process inputs into outputs.
Plastic Injection Process
Raw Material Drying Phase: At this stage, the raw material is kept in the drying unit for a sufficient time at a suitable temperature according to the characteristics of the raw material to be used in the process.
Plasticization Phase : At this stage, the dried raw material is opened and the cover of the feeder is opened and pushed towards the heating units with the help of a worm screw. Here, the material melted by passing through heaters at different temperatures moves towards the injection nozzle. The temperature of the heaters is determined by taking into account factors such as the melting temperature of the raw material to be used, the fluidity value, and part wall forehead.
End of Plasticizing Stage: The movement of the endless screw ends and there is enough material in the injecting nozzle. One of the important things to note here is that the amount of material injected into the mold must be the same each time to get the same quality and weight of material each time.
Closing the Mold: Before starting the injection process, the two halves of the mold are safely closed by the clamping unit. Both halves of the mold join with the injection unit and one of these molds can move axially. Thanks to the hydraulic unit, the vise brings the molds together and the injection process starts after this stage.
Beginning of Injection Process: Plastic raw material in small granules reaches the molds by passing through the nozzle with the help of a worm screw after the feeder. Precise determination of the injection time is a difficult process due to the change and complexity of the flow properties of the molten plastic material.
Cooling Stage: The plastic material injected into the mold starts to cool here. As a result of this cooling, the plastic material begins to solidify, taking the shape of the mold it was injected into. Mold cannot be opened during the required cooling period. This time can be calculated according to the wall thickness, thermodynamic and mechanical properties of various plastic materials.
Throwing the Product Out of the Mold: The material that cools and solidifies in the mold after a certain period of time is ejected from the mold by means of a pusher. The pusher is placed on one half of the die and when the die is opened the pusher shaft moves forward, activating the pins. After the part is ejected from the mold, the molds are re-assembled by the clamping unit and prepared for the next injection process.
Process Values
Attention!
All data and information on this page are provided for informational purposes only, including but not limited to material suitability, material properties, performance, operating values and cost.
While the accuracy of the data and information contained in the tables and the value information corresponds to the best, they should not be viewed under any form of binding warranty.
The data and information contained in the tables are for guidance in a polymer selection process and should not be considered as binding specifications.
It is the user's sole responsibility to determine the suitability of this information for any particular use. Before working with any material, users should contact material suppliers for specific information.
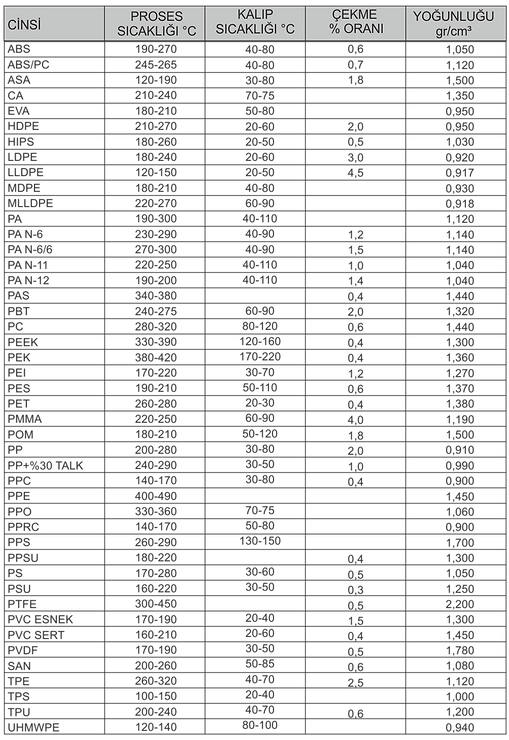
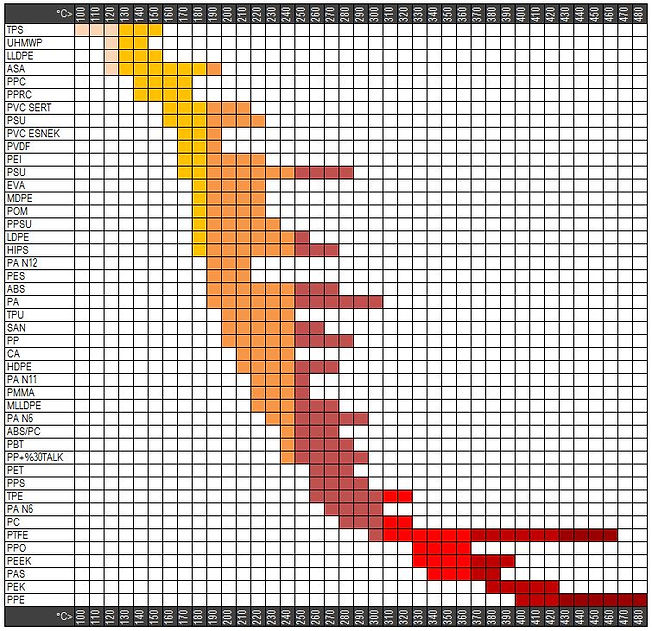
Working Temperatures
Tg (° C): Glass Transition / Glass Transition Temperature
When an amorphous polymer is heated, the temperature at which the polymer structure becomes "viscous liquid or rubbery"; It is called Glass Transition Temperature or Glass Transition Temperature (Tg).
It is also defined as a temperature at which the amorphous polymer has characteristic glassy state properties such as brittleness.
It is measured in ° C or ° F. This temperature depends on the chemical structure of the polymer and is therefore used to describe polymers.
-
Amorphous polymers have only one glass transition temperature (Tg).
-
Crystalline polymers, on the other hand, have a melting point (Tm) and partly a glass transition (Tg) temperature. Because in cases of being semi-crystalline, an amorphous structure is also in question.
The glass transition temperature value depends on the mobility of the polymer chain. With the measurement of this value, the hardness, volume, fracture percentage and elongation are mainly seen. They are used under the (Tg) of some polymers such as polystyrene, poly (methyl methacrylate) , which are hard and fragile, ie in a glassy state. (Tg) s are higher than room temperature.
Some polymers are also used above their (Tg), ie in the form of rubber, for example rubber elastomers such as polyisoprene, polyisobutylene. They are soft and flexible, their (Tg) value lower than room temperature.
Determination of polymers (Tg) is often used for quality control and research and development. It is also an important tool used to change the physical properties of polymer molecules.
To determine the Glass Transition Temperature of plastics:
The most common test method is ASTM E1356. This test method involves the determination of glass transition temperatures of materials using differential scanning calorimetry or differential thermal analysis. This test method can be applied to amorphous materials or partially crystalline materials containing amorphous regions that are stable and do not undergo decomposition or sublimation in the glass transition region.
-
In DTA, the temperature difference between the sample and the reference material is monitored against time or temperature, while the temperature rise / drop of the sample in a particular atmosphere is programmed.
-
In DSC, the difference in heat flow to the sample and the reference is monitored against time or temperature while programming the temperature rise / drop of the sample in a given atmosphere.
Both methods give peaks of endothermic and exothermic transitions with thermal input and show phase changes or the occurrence of reactions. Other methods applied to determine Tg are:
-
Specific heat measurements
-
Thermo mechanical analysis
-
Thermal expansion measurement
-
Micro heat transfer measurement
-
Isothermal compressibility
-
Heat capacity
The most important factor affecting (Tg) is its chemical structure:
-
Molecular weight - In straight chain polymers, it leads to a decrease in chain end concentration, which causes a decrease in free volume in the end group region and an increase in (Tg).
-
Molecular Structure - Addition of the bulky, inelastic side group increases the (Tg) of the material due to reduced mobility,
-
Chemical crosslinking - the increase reduces mobility, causing a decrease in free volume and an increase in (Tg)
-
Pole groups - The presence of polar groups increases intermolecular forces; Inter-chain attraction and cohesion causes an increase in (Tg) by causing a decrease in free volume.
The addition of plasticizer increases the free volume in the polymer structure. The plasticizer gets between the polymer chains and separates them from each other.
This causes the polymer chains to slide more easily from each other. As a result, polymer chains can move at lower temperatures, causing a decrease in the (Tg) of a polymer.
The increase in moisture content causes the formation of hydrogen bonds with polymeric chains that increase the distance between polymeric chains. And so it increases free volume and decreases (Tg).
The entropy value for amorphous material is higher and lower for crystalline material. If the entropy value is high, the (Tg) value is also high.
The increase in ambient pressure leads to a decrease in free volume and ultimately a high (Tg).
The order of temperature breakpoints in the decomposition process of a polymer is as follows:
(Tg) Glass Transition Temperature <(Tc) Crystallization Temperature <(Tm) Melting Temperature

Amorphous and Crystalline Polymers
Polymers (plastic, elastomer or
rubber ) consists of long chains of molecules and can be amorphous or crystalline. The structure of a polymer is defined in terms of crystallinity.
Amorphous polymers have an arbitrary molecular structure that does not have a sharp melting point. Instead, the amorphous material gradually softens as the temperature increases. Amorphous materials are more susceptible to stress failure due to the presence of hydrocarbons.
For example PC , GPPS, PMMA, PVC , ABS
Crystal or Semi-crystalline polymers have a highly ordered molecular structure. These do not soften as the temperature rises, but rather have a defined and narrow melting point. This melting point is generally above the upper range of amorphous thermoplastics. For example, Polyolefins, PEEK , PET , POM etc.
Glass Transition Temperature (Tg) Melting Temperature (Tm) Comparison
At the molecular level, at (Tg), the chains in the amorphous (ie, disordered) regions of the polymer acquire enough thermal energy to start sliding past each other at a noticeable speed. The temperature at which all chain motion takes place is called the melting point (Tm) and is greater than (Tg).
-
(Tg) is a property of the amorphous region, while (Tm) is the property of the crystalline region.
-
Below (Tg) is the irregular amorphous solid where the chain motion freezes and molecules begin to wiggle above (Tg). The more immobile the chain, the higher the value of Tg.
-
While it is an ordered crystalline solid below (Tm) it becomes irregular melt above (Tm).
The operating temperatures of the polymers are defined by these transition temperatures.
DSC:
Differential Scanning Calorimetry.
It is a device that measures the amount of energy absorbed or released by heating, cooling or keeping the polymeric sample at a constant temperature. With the reference, the temperature difference from or away from the sample is shown depending on the temperature or time. If a temperature difference is detected between the sample and the reference, the amount of energy (power) supplied to the sample is changed to keep the temperature the same. In this way, the amount of heat transfer during phase change in the sample is determined.
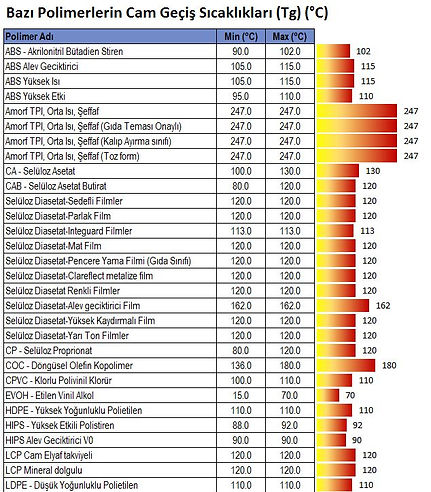

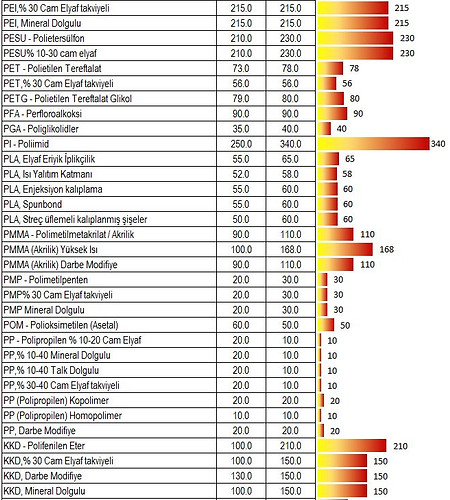
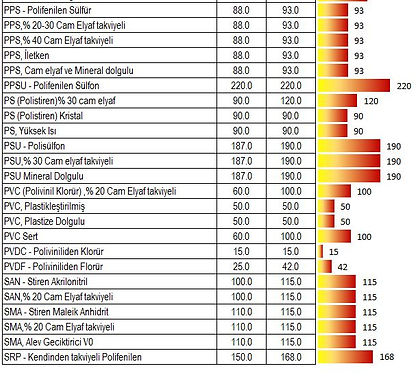