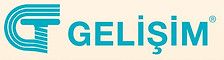


Hydrocarbons
It is an organic compound consisting of two elements, hydrogen and carbon. Most of the petroleum composition consists of hydrocarbons of varying lengths.
The smallest hydrocarbon methane consists of a single carbon atom and four hydrogen atoms. However, hydrocarbons can consist of hundreds or thousands of individual atoms linked together in many ways, including chains, circles, and other complex shapes.
In order to classify the properties of hydrocarbons, they are divided into several basic types.
Alkanes: These are called saturated hydrocarbons. That is, they only contain single bonds between all carbon atoms. Alkanes are the basis of petroleum fuels and exist in linear and branched forms.
Unsaturated Hydrocarbons: Hydrocarbons that have one or more double bonds between carbon atoms are called alkenes.
Cycloalkanes: Any hydrocarbon containing one or more ring structures.
Aromatic Hydrocarbons: Aromatic hydrocarbons , also called arenes, are a unique class of carbon molecules in which carbon atoms are bonded by successive double and single bonds. This class of molecules has special ring structures in which the bonds between carbon atoms are an intermediate bond between single and double bonds.
Molecules in this class contain the industrial solvent "benzene".
Benzene (C6H6): Like other hydrocarbons, benzene is a natural component of petroleum. It is a colorless, flammable, sweet-smelling liquid at room temperature and is a component of most gasoline blends because of its high octane number.
Benzene is also highly carcinogenic and is well known to cause bone marrow failure and bone cancer. Of course, its carcinogenicity is not well known when used as an additive in aftershave and other cosmetics due to its "pleasant aroma".
The largest use of benzene (50%) is the product of styrene and polystyrene plastics. It is also converted into a molecule known as cyclohexane, which is important in Nylon production. About 15% of benzene is used to produce cyclohexane. Smaller amounts are used in everything from pesticides to rubber.
The benzene structure can be drawn in two ways. In the first, the double bond character is drawn explicitly. In the short handed version, a circle is drawn inside the ring to show the structure. There is only one hydrogen bonded to each carbon atom in benzene.
I. and II below. drawings are identical. III in practice. drawing is used.
Benzene is a colorless, flammable liquid with a boiling point of 80.1 ° C and a melting point of 5.5 ° C.
Binuclear Aromatic Hydrocarbons: They are compounds that contain two benzene rings in their molecules.
Hydrocarbons
It is an organic compound consisting of two elements, hydrogen and carbon. Most of the petroleum composition consists of hydrocarbons of varying lengths.
The smallest hydrocarbon methane consists of a single carbon atom and four hydrogen atoms. However, hydrocarbons can consist of hundreds or thousands of individual atoms linked together in many ways, including chains, circles, and other complex shapes.
In order to classify the properties of hydrocarbons, they are divided into several basic types.
Alkanes: These are called saturated hydrocarbons. That is, they only contain single bonds between all carbon atoms. Alkanes are the basis of petroleum fuels and exist in linear and branched forms.
Unsaturated Hydrocarbons: Hydrocarbons that have one or more double bonds between carbon atoms are called alkenes.
Cycloalkanes: Any hydrocarbon containing one or more ring structures.
Aromatic Hydrocarbons: Aromatic hydrocarbons , also called arenes, are a unique class of carbon molecules in which carbon atoms are bonded by successive double and single bonds. This class of molecules has special ring structures in which the bonds between carbon atoms are an intermediate bond between single and double bonds.
Molecules in this class contain the industrial solvent "benzene".
Benzene (C6H6): Like other hydrocarbons, benzene is a natural component of petroleum. It is a colorless, flammable, sweet-smelling liquid at room temperature and is a component of most gasoline blends because of its high octane number.
Benzene is also highly carcinogenic and is well known to cause bone marrow failure and bone cancer. Of course, its carcinogenicity is not well known when used as an additive in aftershave and other cosmetics due to its "pleasant aroma".
The largest use of benzene (50%) is the product of styrene and polystyrene plastics. It is also converted into a molecule known as cyclohexane, which is important in Nylon production. About 15% of benzene is used to produce cyclohexane. Smaller amounts are used in everything from pesticides to rubber.
The benzene structure can be drawn in two ways. In the first, the double bond character is drawn explicitly. In the short handed version, a circle is drawn inside the ring to show the structure. There is only one hydrogen bonded to each carbon atom in benzene.
I. and II below. drawings are identical. III in practice. drawing is used.
Benzene is a colorless, flammable liquid with a boiling point of 80.1 ° C and a melting point of 5.5 ° C.
Binuclear Aromatic Hydrocarbons: They are compounds that contain two benzene rings in their molecules.
About
Kyäni, nutritional supplement products consisting of beneficial ingredients; It delivers to more than 50 countries around the world with unique business opportunities. We use Kyäni products daily to maintain our ideal health, share these products with others, devote a certain amount of time to work almost every day to build and maintain our business, and share our success with others by involving others in the Kyäni opportunity or contributing to the Potato Pak and Caring Hands programs.
About
Kyäni, nutritional supplement products consisting of beneficial ingredients; It delivers to more than 50 countries around the world with unique business opportunities. We use Kyäni products daily to maintain our ideal health, share these products with others, devote a certain amount of time to work almost every day to build and maintain our business, and share our success with others by involving others in the Kyäni opportunity or contributing to the Potato Pak and Caring Hands programs.
Page Under Construction.
Page Under Construction.
Training / Knowledge / Solution Platform
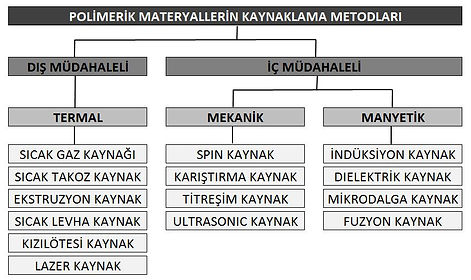
Welding Process in Plastics
Plastic welding is the process of forming a molecular bond between two compatible thermoplastics. Welding provides superior strength and reduces cycle times. Any welding has three main steps: pressing, heating, and cooling. Plastic welding processes are distinguished primarily by their heating method. The allowances for force application and cooling are mechanical considerations that can vary from machine to machine within the general treatment category. It should be kept in mind that very high energy input is required for plasticizing materials in high temperature plastics. The welding method to be used depends on the following factors:
-
Part geometry
-
Part size
-
Type of material.
Plastic welding is basically the process of combining plastic materials with the same metals but with different methods. Plastic welding, as the name suggests, is made to plastic materials, but; it cannot be applied to all. The basic logic is that the material is melted and combined. Or, using an additional plastic, the other two main materials are combined. This welding method can only be applied to thermoplastic materials. This joining method cannot be applied to thermoset materials.
The main reason why plastic welding cannot be applied to thermoset materials is that once these types of plastics are shaped, no matter how much they are heated again, they never melt, they just turn into coal and become unusable. The main reason for this is that while thermoplastic materials have wan der waals atomic bonds, in thermoset plastics, cross-links hold the molecules together. Thus, these materials are both more rigid and once shaped, they cannot be melted and used again. So recycling is impossible.
In thermoplastic materials, on the other hand, there are wan der waals bonds between the molecular chains. This type of ties are less resistant than cross ties. After being shaped, they can be melted repeatedly and shaped and used in other ways. So recycling is possible. Because of these features, they are more environmentally friendly type materials.
To join the two thermoplastic parts, the materials must be chemically compatible. Otherwise, even if both materials melt together, the molecular bond will not be formed. A good example would be to try to weld polyethylene to polypropylene. Both of these semi-crystalline materials have a similar appearance and many common physical properties. However, they are not chemically compatible and therefore cannot be welded together. They will weld themselves like thermoplastics (ie materials with the same chemical properties). For example, one ABS part will weld to another ABS part. Dissimilar thermoplastics can only be compatible if their melt temperature is within 40ºF (6ºC) and they have a similar molecular structure. For example, the ABS part is likely to be welded to an acrylic part because its chemical properties are compatible. Generally speaking, only similar amorphous polymers are likely to be perfectly welded together. The chemical properties of any semi-crystalline material make each one compatible only with itself. When the materials to be welded are compatible, several other factors can affect the weldability of the parts. These factors include hygroscopicity, mold release agents, lubricants, plasticizers, fillers, flame retardants, regrinding, pigments, and resin classes. When the materials to be welded are compatible, several other factors can affect the weldability of the parts. These factors include hygroscopicity, mold release agents, lubricants, plasticizers, fillers, flame retardants, regrinding, pigments, and resin classes. When the materials to be welded are compatible, several other factors can affect the weldability of the parts. These factors include hygroscopicity, mold release agents, lubricants, plasticizers, fillers, flame retardants, regrind, pigments, and resin classes.
In the weld, plastic thermal strain develops near the weld zone due to heating, melting and cooling of the weld zone and nearby base metals. Plastic stress causes permanent deformation of the welded structure after welding. This is called resource-induced deterioration. Weld-induced distortion mode can occur as stress such as bending, rotation or buckling, and in-plane deformation such as out-of-plane deformation. It is very important for the plastic welding process to form a melt layer on the faulting surface to allow intermolecular diffusion to form a molecular bond. In solid state, polymer chains will not flow. Therefore, the joint surface in both parts must be melted to allow the plastic molecules to diffuse across the interface and bond with the molecules of the other part. The warmer the melt, the more molecular motion is achieved and the weld can be made in a shorter cycle time. Amorphous polymers semi-crystalline polymers must be heated above their melting temperature.
The infrared laser source of overlapping thermoplastics uses radiation penetration heating. When the melt zone is produced at the contact interface, the two parts are joined.
In conventional infrared laser welding of plastics, he focused on the so-called Transmission Infrared (TTIr) laser source. Diode lasers have been widely adopted as suitable lasers for this method. It is essential to choose two materials; The other, which is irradiated, is highly permeable, while the other is highly absorbent to laser light. In most true cases of TTIr laser sources, the pigmentation should increase the absorption of radiation in the absorbent part.
Hot Plate Welding
In this process, the facing surfaces of the two parts are heated by conduction, convection and / or radiation through a true heated plate. The two parts are either pressed against the hot plate or kept next to it for a while, then the hot plate is removed and the parts are pressed together to create the weld. Hot Plate welding typically has welding times between 10 and 20 seconds.
The parameters used in hot plate welding are hot plate temperature, pressure during matching (or displacement), pressure during heating, pressure and displacement at the welding stage and matching, heating, replacement and cooling times. These parameters have a dependent effect on weld quality and cannot be set individually.
The hot plate temperature is taken on the surface of the plate. The melt temperature is adjusted according to the hot plate weld variant with the properties of the material including melt viscosity and thermal degradation limits. Traditional hot plate welding uses temperatures 30 to 100 ° C above the melting temperature. The high temperature variant uses temperatures of about 100 to 200 ° C above the melting point, above the decomposition temperature of the material. The non-contact variant uses temperatures from 300 to 400 ° C above its melting point.
Hot Gas Welding
This method is made using an additional material. The welding place is heated with a hot air gun. After the necessary heating is done, the gap is filled with additional plastic. This can be done in a few passes. The hot gas used here can be nitrogen. The main reason for this is to prevent plastic materials from oxidizing at high temperatures. Oxidation does not only happen with metals. Plastic materials also oxidize and become brittle.
If the plastic parts to be welded are too hard, the additional material is put between the materials to be joined. But; If the plastics to be welded are soft thermoplastic, pressure must be applied to the weld seam with an additional pressing device.
A hot gas torch is used to direct hot air to both the joint surface and the welding rod and to heat the materials to softening temperatures. Applying pressure to the joint surface on the heated weld rod binds the materials together to create a finished weld. This technique is not easily automated and is mainly used for repairs of small or complex components or for individual production needs.
There are two common welding techniques used in hot gas welding: hand welding and fast welding.
Hand welding is a technique in which the welding rod is applied directly to the joint by the welder. The hot gas torch is actuated with one hand to pendulum-heat both the welding rod and the connecting surfaces in succession. Pressure is applied to the welding rod and controlled manually without the aid of a nozzle. This technique is suitable for most configurations and can be useful for welding in narrow, constrained spaces or complex joint designs as the application of the weld rod is limited to only accessible welding positions.
Fast welding uses a specially designed nozzle that ensures the hot gas torch and welding rod are one cohesive system. The nozzle makes it easy to apply the welding rod to the connection through a feed pipe. The nozzle heats the welding rod material evenly and allows a controlled pressure application. The base of the nozzle is designed to heat the joint surface and guide the welding rod into the groove. Nozzles are manufactured to fit the feed pipes to specific weld rod shapes and sizes and are available for common sizes round or triangular rods. Fast welding is limited to simple connection design and routing applications due to the size of the nozzle and the maneuverability of the system.
Gas temperature, application pressure, weld feed rate, gas flow rate, and torch orientation all affect the integrity and mechanical properties of the finished weld. Gas temperature and flow rate are controllable parameters based on system inputs. Application pressure, welding travel speed and torch orientation depend on the operator performing the welding. These parameters are interrelated and all have a significant impact on the final quality of the weld.
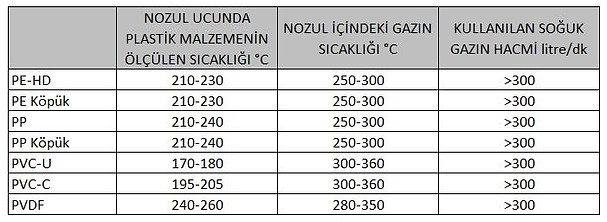
Extrusion Welding
Its biggest advantage is that it has an application rate of approximately five times faster compared to hot gas welding. This application is for achieving high deposit rates in a single pass. Due to the stricter control over welding parameters, much stronger welds can be obtained.
The main disadvantage of this process is that, due to the size of the machine, there may be difficulties in application, and it is almost a necessity to be applied by a more trained operator.
Extrusion welding is used for welding thick walled parts. Welding process is done using welding rod. Extrusion welding equipment is a small extruder. The extruded material is pressed with a welding sleeve. Welding jacket is usually made of Teflon due to its high temperature resistance. The welding jacket should be suitable for the welding seam. The working method is quite similar to hot air welding. However, the results are higher mechanical strength, better welding quality and lower internal stress.
In this welding, a mini hand extruder is used for extrusion work. The barrel temperature of this extruder used can be done electrically with spiral-wound wires (classical method), as well as another barrel heating technique; utilizing the already heated hot gas. Hand extruders are used in traditional apparatus engineering, landfill construction, plastic repairs and many other industries. They are invaluable wherever quality and performance are required.
Another thread is used to pull the welding rod on the screw. In the process, it also passes through the feeding sleeve, which prevents the rod from bending. Once the blade is inserted, it cuts the bar. It is pulled forward by the screwed spiral, compressed and heated by friction inside the barrel (drum).
In the spiral heated version, electrical energy is used to generate the external heat inside the shell required for the plasticizing process. The spiral resistance is wrapped around the entire extruder drum and regulates the temperature of the melting gap with extraordinary precision. The temperature probe placed in the cylinder tube measures the mass temperature. This sends the information to electronic devices, which controls the entire plasticizing process in a closed loop.
In the hot air version, heat penetrates the extrusion unit from the outside, initiating the plasticizing process and helping it continue during operation. The external heat is generated by the hot gas appliance in the form of hot air, which then flows around the hot gas ducts and the extrusion unit in the preheating chamber. Friction heat is also generated by compression and friction. This causes the weld filler metal to plasticize and mix into a homogeneous mass.
Ultimately, the extrudate then exits the nozzle and creeps onto the surface previously softened with hot gas.

Laser Source Welding
It is a non-contact joining method that uses a laser beam to melt plastic in the joint area by transmitting a controlled amount of energy to a precise location. The precision in controlling heat input is based on the ease of adjusting the laser beam size and the methods available to position the beam. Most thermoplastics can be welded using a suitable laser source and suitable joint design.
Laser welding of plastic parts has proven itself as a robust, flexible and precise joining process. It provides highly efficient and flexible assembly from the production of small-scale parts with complex geometries to high-volume industrial production that can be easily integrated into automation lines. This process uses a laser beam to melt plastic in the joint area by transmitting a controlled amount of energy to a precise location. This level of precision in controlling heat input is based on the ease of adjusting beam size and the methods available for precise positioning and moving the beam.
The process is based on the same base material compatibility as other plastic welding techniques, but is often found to be more forgiving of resin chemistry and melt temperature differences than most other plastic welding processes. Almost all thermoplastics can be welded using a suitable laser source and suitable joint design.
There are three main types of lasers commercially available to produce high quality connections in thermoplastic components.
CO2 Laser:
It is a well-established material handling tool, now available with a power output of up to 60kW and most commonly used for cutting metal, plastic and ceramic. CO2 laser radiation (10.6μm wavelength) is rapidly absorbed into the plastic surface layers. At these photon energies (0.12eV), absorption is based on the vibration of molecular bonds. Plastics become hot due to laser inducing resonance frequency in molecules. Therefore, very fast processing of thin plastic film (<0.2 mm) is possible (high speed welding of up to 500 m / min has been proven).
Two polyethylene films can be laser welded at 100 m / min. The CO2 laser beam cannot be transmitted under a silica fiber optic, but can be applied in a complex process using mirrors and gantry or robotic motion.
Nd: YAG Laser:
It is also well built for material processing and recent advances can lead to increases in available power up to 6kW and reductions in laser size.
The degree of energy absorption at the Nd: YAG laser wavelength (1.064µm, 1.2eV photon energy) largely depends on the presence of additives in plastics. If there is no filler or pigment, the laser can penetrate a few millimeters into the material. The absorption coefficient can be increased by additives such as pigments or fillers that directly absorb this photon energy and reverberate or scatter radiation for more efficient mass absorption.
Sources can be made by positioning infrared absorbers to generate heat at a connection interface. This process is commonly referred to as 'transmission laser welding' because laser energy is transmitted to the junction through a portion of the plastic.
The Nd: YAG laser beam can be transmitted down through a silica fiber optic providing easy and flexible operation.
Diode Laser:
Available since early 1997. It is more cost effective compared to CO2 and Nd: YAG lasers. Typically, diode lasers emit radiation with a wavelength of 0.8-0.95 µm.
Therefore, the interaction with plastics is very similar to Nd: YAG laser and its applications overlap.
The beam from a diode laser is usually rectangular, and while this is preferred for some applications it limits the minimum spot size and the maximum power density available. The diode laser source is small and light enough to be mounted on a skid or robot for complex operations.
Nd: YAG and diode lasers can be used to perform transmission laser welding, given that one of the plastics passes through the laser and the other absorbs it. The process provides a means by which plastic parts with different absorption properties can be welded without a melt flash, without streaking on the outer surfaces, and without a small heat-affected zone only.
Transmission Laser Welding (TTLW):
Parts are pre-assembled and interlocked to ensure close contact between mating surfaces. The laser beam is transmitted to the part interface through the upper "transparent" part and is absorbed by the lower absorbent part, which converts IR energy into heat. Heat is conducted from the lower absorbent portion to the upper portion and allows the melt to travel through the interface and form a bond. Precise positioning and clamping of the assembly is important, as close contact is required for heat transfer between parts. Carbon black and specially designed absorbers are mixed into the resin or applied to the surface to absorb IR radiation at the bottom of the assembly. The TTLW welding technique is dependent on the presence of an absorbent material in the sub-component, which limits the process feasibility when a "transparent" or "transparent to color" assembly is required for the production of medical devices, electronic devices and certain consumer goods. Engineers have successfully overcome this hurdle by integrating a recently developed 2 micron laser, which is easily absorbed by clear polymers and provides highly controlled melting thanks to the thickness of optically clear particles. This greatly improves and simplifies the laser welding of transparent polymers for the medical device industry, allowing highly controlled melting thanks to the thickness of the optically clear parts that are easily absorbed by the clear polymers. This greatly improves and simplifies the laser welding of transparent polymers for the medical device industry, allowing highly controlled melting thanks to the thickness of the optically clear parts that are easily absorbed by the clear polymers. This greatly improves and simplifies the laser welding of transparent polymers for the medical device industry.
Contour Welding:
Round parts in particular, the laser beam swirling down under it, reaching speeds of up to 25 m / min. In the meantime, the laser beam is passed over the contour to be welded and the contour is heated. Large three-dimensional components as well as round parts are suitable for the contour welding method. The biggest problem encountered in this method is that stresses can arise in over-volume components, since the contours of the welded parts cannot be heated simultaneously.
Concurrent Source :
The laser beam is created optimally matched to the component. Thus, the contour to be welded is heated simultaneously. The result: very short process times of about 100 ms. The use of this method is extremely suitable for components that are not very complex and are planned to be produced in large numbers. However, if the component geometry changes, the beam shape must also be changed accordingly.
Semi-Simultaneous Welding:
A scanner heats the source contour of a laser beam. Since the laser beam travels at rates of up to 15 m / s (900m / min), it is so fast compared to the cooling process that the contour is heated almost simultaneously. Thanks to the programmable focusing device, it is possible to react very quickly to changing welding contours, which provides a clear advantage over the simultaneous welding method.
Clearweld Process
The laser absorbing additive known as "Clearweld" provides complete independence from the requirements of the conventional transmissive laser welding process. The liquid material is applied to the weld plane before the joining partners are joined. Clearweld absorbs the incoming laser radiation, providing the desired cohesive bond. Unlike other IR absorbing materials, Clearweld becomes completely clear after exposure to radiation and provides color-independent design in the junction area.
In addition to this new advantage, the Clearweld system offers interesting new possibilities for the geometric design of merging partners. Creating multi-layer connections while maintaining high processing speed is also possible in a single operation.
Hybrid Laser
This technology uses a combination of infrared radiation emitted by conventional halogen heating lamps and laser light. This dual light intensity concept has already been proven to increase both processing speed and fault tolerance.
The target applications of hybrid welding technology are not only structural automotive parts, such as head and tail lights and plastic engine parts, but also consumer products and medical applications.

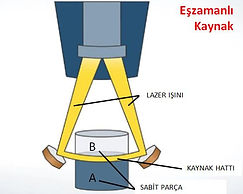

Ultrasonic Welding
It is the joining or reforming of thermoplastics using heat generated from high frequency mechanical motion. It is realized by converting high frequency (20-40 kHz) electrical energy into high frequency mechanical motion. This mechanical action, together with the applied force, creates frictional heat at the joint surfaces (joint area) of the plastic components, as a result the plastic material melts and creates a molecular bond between the parts.
Vibration Source
This process works by linear or orbital motion of one part relative to another. This causes surface friction that leads to heat generation and the formation of a melt layer in the joint. The vibration source typically has weld times of one to five seconds. Vibration welders can machine parts from approximately two inches (50 mm) in diameter to six feet (1800 mm) long.
Infrared (IR) Source
Another non-contact welding method is infrared welding, which uses radiation to transfer heat to plastic parts. It follows the same basic steps as for hot plate welding. Two different approaches have emerged for infrared welding. One of the systems uses an electrically heated metal plate coated with a ceramic in some cases. In the other system, the standard heater plate is replaced with spring loaded infrared emitters compressed on both sides of a moving plate.
IR systems can be used instead of hot surface and vibration welding methods in plastic, many challenging and large parts joining.
When welding is done by heating by means of hot surfaces, plastic can stick on the heater surface. It is necessary to clean the plastic accumulated on the heating surface 2-3 times per shift. Otherwise, the plastic may not be brought to the temperature to be welded or the welding surfaces may become rough. Since heating is performed without contact with the plastic material in IR welding method, there is no time loss caused by cleaning or changing the mold. In addition, thanks to the fast opening and closing times of IR systems, energy and time losses occurring during mold preheating are prevented.
IR systems can be used for welding plastic battery case parts, welding of automobile fuel tank bodies, joining plastic pipes used in infrastructure systems or various units, welding PVC window frames, and melting plastic pins used to join plastic parts.
In summary, the advantages of IR welding application are:
-
Welding complex 2D and 3D part geometries for joining various large plastic parts by heating
-
Do not weld the plastic battery case parts
-
Welding of automobile fuel tank bodies
-
Combining plastic pipes used in infrastructure systems or various units by heating
-
Melting plastic pins used to join plastic parts
-
Wide variety of acceptable welding materials, thermoplastics, polyethylene, PVC, polypropylene, composite reinforced plastics, polyamides PC, PCABS.
-
Low electricity consumption
-
Rapid temperature rise
-
Electrically isolated and low leakage current environment
-
Low maintenance technical devices
-
Non-contact welding process
-
Stronger welds, hermetic sealing.
-
Ability to combine PP GF 30 with different materials such as TPE
This process uses Infrared radiation that is absorbed by the thermoplastic material and converted into heat. As a result, the cracking surface of the plastic part is melted and the components are pressed together. This is a fast, non-contact, particle-free welding method.
Spin Welding
This process works by the rotational motion of one part relative to another. This causes surface friction that leads to heat generation and the formation of a melt layer in the joint. Spin welding typically has weld times of half to five seconds. Spin welders can machine parts up to one and a half inches (12 mm) in diameter using high-speed motors up to nine inches (225 mm) in diameter using high torque motors. The spin welding process consists of generating heat through rotational friction to weld thermoplastic parts with circular joints. The spinning welding machine applies force axially as it rotates a part against its fixed mat. The resulting friction generates heat that melts parts at the interface. When rotation stops, the material cools and solidifies, forming a welded assembly. In cases where parts must be oriented in a certain way relative to each other, the welder stops the rotation in a precise angular direction.
Suitable materials for spin welding are generally the same as those that can be joined by other friction welding processes such as vibration welding. Semi-crystalline thermoplastics are easier to join using spin welding than ultrasonics. Using compatible polymers, spin welding can make reliable hermetic seals.
Joining of dissimilar polymers is possible using the spin-welding process, although this generally produces lower strength weld joints. By designing the weld joint with undercut, the polymer with the lower melting temperature will flow into the undercut and form a mechanical joint.
Material filler and surface contaminants (eg mold release agent) are two factors that will affect consistency and weld repeatability. Spin welding is more tolerant of contaminants than ultrasonic welding. Spin welding is also less affected by hygroscopic polymers, but may still require special handling for critical applications.
Advantages of the spin welding process include high quality permanent joints, hermetic seals, lower equipment costs compared to other processes, ease of assembly, energy efficient operation, immediate use, capture of other parts, far field welding capability, and the elimination of additional materials such as adhesives.

Alternative Welding Process for Thermosets (R&D)
Welding of Thermoset Surface by Thermoplasticization:
On induction welding to join thermoset and thermoplastic composites, Michel van Tooren in his R & D study; applied thermoplastic to a thermoset composite only where it was intended to weld. Application; It was made in nanoparticle scale, cross polymerization grafting. The result is to obtain thermoplastic islets implanted in the thermoset composite and chemically bonded with it. Later, thermoplastic islets were subjected to welding process. And with this study, an alternative application to joints in the form of bonding of thermoplastic surfaces that cannot be welded or pierced and fastened with fasteners has been opened.
R&D Application Principles:
PolyVinylButyral (PVB), a semi-crystalline, low-cost thermoplastic polymer with a melting temperature of 150-170 ° C, has benefited from its excellent bonding and film-forming ability, and its ability to adhere to many surfaces.
Taking advantage of this characteristic, PVB has been used as a bonding layer. In the form of a 14-layer carbon fiber layer, it was laminated to the thermoset composite surface by curing at 180 ° C, and macro-mechanical interlock was achieved.
The formation of islets that partially penetrate the first layer of the thermoset composite surface of PVB resin with a thickness of 10-200 microns.
Ultimately, it has been concluded that the PVB resin surfaces are mutually bonded (welded) to each other very strongly as a result of the induction welding and ultrasonic welding processes. A lap shear strength of 25 MPa was achieved as exemplified by typical carbon fiber / epoxy bonds.
