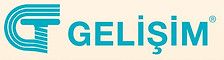


Hydrocarbons
It is an organic compound consisting of two elements, hydrogen and carbon. Most of the petroleum composition consists of hydrocarbons of varying lengths.
The smallest hydrocarbon methane consists of a single carbon atom and four hydrogen atoms. However, hydrocarbons can consist of hundreds or thousands of individual atoms linked together in many ways, including chains, circles, and other complex shapes.
In order to classify the properties of hydrocarbons, they are divided into several basic types.
Alkanes: These are called saturated hydrocarbons. That is, they only contain single bonds between all carbon atoms. Alkanes are the basis of petroleum fuels and exist in linear and branched forms.
Unsaturated Hydrocarbons: Hydrocarbons that have one or more double bonds between carbon atoms are called alkenes.
Cycloalkanes: Any hydrocarbon containing one or more ring structures.
Aromatic Hydrocarbons: Aromatic hydrocarbons , also called arenes, are a unique class of carbon molecules in which carbon atoms are bonded by successive double and single bonds. This class of molecules has special ring structures in which the bonds between carbon atoms are an intermediate bond between single and double bonds.
Molecules in this class contain the industrial solvent "benzene".
Benzene (C6H6): Like other hydrocarbons, benzene is a natural component of petroleum. It is a colorless, flammable, sweet-smelling liquid at room temperature and is a component of most gasoline blends because of its high octane number.
Benzene is also highly carcinogenic and is well known to cause bone marrow failure and bone cancer. Of course, its carcinogenicity is not well known when used as an additive in aftershave and other cosmetics due to its "pleasant aroma".
The largest use of benzene (50%) is the product of styrene and polystyrene plastics. It is also converted into a molecule known as cyclohexane, which is important in Nylon production. About 15% of benzene is used to produce cyclohexane. Smaller amounts are used in everything from pesticides to rubber.
The benzene structure can be drawn in two ways. In the first, the double bond character is drawn explicitly. In the short handed version, a circle is drawn inside the ring to show the structure. There is only one hydrogen bonded to each carbon atom in benzene.
I. and II below. drawings are identical. III in practice. drawing is used.
Benzene is a colorless, flammable liquid with a boiling point of 80.1 ° C and a melting point of 5.5 ° C.
Binuclear Aromatic Hydrocarbons: They are compounds that contain two benzene rings in their molecules.
Hydrocarbons
It is an organic compound consisting of two elements, hydrogen and carbon. Most of the petroleum composition consists of hydrocarbons of varying lengths.
The smallest hydrocarbon methane consists of a single carbon atom and four hydrogen atoms. However, hydrocarbons can consist of hundreds or thousands of individual atoms linked together in many ways, including chains, circles, and other complex shapes.
In order to classify the properties of hydrocarbons, they are divided into several basic types.
Alkanes: These are called saturated hydrocarbons. That is, they only contain single bonds between all carbon atoms. Alkanes are the basis of petroleum fuels and exist in linear and branched forms.
Unsaturated Hydrocarbons: Hydrocarbons that have one or more double bonds between carbon atoms are called alkenes.
Cycloalkanes: Any hydrocarbon containing one or more ring structures.
Aromatic Hydrocarbons: Aromatic hydrocarbons , also called arenes, are a unique class of carbon molecules in which carbon atoms are bonded by successive double and single bonds. This class of molecules has special ring structures in which the bonds between carbon atoms are an intermediate bond between single and double bonds.
Molecules in this class contain the industrial solvent "benzene".
Benzene (C6H6): Like other hydrocarbons, benzene is a natural component of petroleum. It is a colorless, flammable, sweet-smelling liquid at room temperature and is a component of most gasoline blends because of its high octane number.
Benzene is also highly carcinogenic and is well known to cause bone marrow failure and bone cancer. Of course, its carcinogenicity is not well known when used as an additive in aftershave and other cosmetics due to its "pleasant aroma".
The largest use of benzene (50%) is the product of styrene and polystyrene plastics. It is also converted into a molecule known as cyclohexane, which is important in Nylon production. About 15% of benzene is used to produce cyclohexane. Smaller amounts are used in everything from pesticides to rubber.
The benzene structure can be drawn in two ways. In the first, the double bond character is drawn explicitly. In the short handed version, a circle is drawn inside the ring to show the structure. There is only one hydrogen bonded to each carbon atom in benzene.
I. and II below. drawings are identical. III in practice. drawing is used.
Benzene is a colorless, flammable liquid with a boiling point of 80.1 ° C and a melting point of 5.5 ° C.
Binuclear Aromatic Hydrocarbons: They are compounds that contain two benzene rings in their molecules.
About
Kyäni, nutritional supplement products consisting of beneficial ingredients; It delivers to more than 50 countries around the world with unique business opportunities. We use Kyäni products daily to maintain our ideal health, share these products with others, devote a certain amount of time to work almost every day to build and maintain our business, and share our success with others by involving others in the Kyäni opportunity or contributing to the Potato Pak and Caring Hands programs.
About
Kyäni, nutritional supplement products consisting of beneficial ingredients; It delivers to more than 50 countries around the world with unique business opportunities. We use Kyäni products daily to maintain our ideal health, share these products with others, devote a certain amount of time to work almost every day to build and maintain our business, and share our success with others by involving others in the Kyäni opportunity or contributing to the Potato Pak and Caring Hands programs.
Page Under Construction.
Page Under Construction.
Training / Knowledge / Solution Platform
Introduction to Polymer Additives
Why Add Additives To Polymers:
First of all, it should be stated that if stabilization is not achieved by adding additives to more than 95% of the polymers, the polymer will be very weak in its raw form and will not serve the purpose. For example; Pure polyolefins such as PE and PP oxidize very quickly. For this reason, they are made workable by adding external additives. Pure PVC cannot be extruded and molded without high temperature degradation, and has very poor mechanical values that serve almost no purpose after the process.
For the most basic purpose, additives are used to eliminate the processing difficulties of polymers. It preserves its performance values and protects the polymer. Adverse environmental effects are avoided with additives.
Which additive to which polymer, in what ratio:
The nature of the additive to be used depends on several parameters. Initially, the chemical composition of the polymer should be comparable with additives. It should not react actively with the polymeric structure in order not to spoil its polymer property. It should be known exactly with which process the polymer will be processed. It should be determined how much temperature it will be exposed to in the thermal process. Otherwise, the problem of additive deterioration may occur. Or, if the temperatures are suitable for the polymer but not suitable for the additive, it should be predicted that if the temperature is high, the additive may burn, and if the temperature is low, the additive may not work at the end of the process.
Polymers ; They deteriorate when exposed to heat, light, cutting and moisture. It should be determined at which final point the production is aimed. Whatever factor is to be avoided in order to ensure stabilization, it should be determined that the contribution to be added is for this direction. (For example, in the production of a plastic product that will run in water, it would be a little pointless to add a flame retardant additive to the polymer).
In polyolefin (PE, PP), polystyrene (PS), (PVC), which are normal chain growth polymers, Carbon-Chlorine and Carbon-Hydrogen bonds are very prone to deterioration by environmental factors. Therefore, it must be protected against oxidation, light, UV radiation, thermal degradation.
These bonds suitable for degradation do not exist in gradual growth polymers. They hydrolyze very quickly as ester, amide, carbonate groups. Polymers undergo molecular degradation in the presence of moisture during processing.
Typically, a polymer formulation contains more than one additive. It; It is applied for an optimal formulation software with the interaction between additives. And these contributions in almost small proportions work with a sacrifice logic. They begin to protect the polymer, completely ceasing to protect themselves and destroy them.
If attention is paid to these additives attached to the polymer, it will be noticed that they are completely classified according to environmental factors. such as antioxidants, antibacterials, heat stabilizers, light stabilizers, UV breakers.
As long as the product serves its purpose, many additives can be added to a base carrier polymer as the process conditions meet. However, it should not be taken out of memory; No matter how small the rates of additives to be added, they increase the cost of production as their unit costs are much higher than polymers. Therefore, the costs of the preferred additives should also be taken into account.
The rate of use of additives in the polymer chain is basically directly proportional to the active substance ratio they contain. An additive use percentage with a high percentage of active ingredients should be lower than the percentage of use of an additive that serves the same purpose but has a low percentage of active ingredients. The use of high levels of additives is synonymous with the phrase `` making an eyebrow '' and making an eye. Too high use of the additive can increase the costs as well as destroy the polymer itself.
Liquid additives are difficult to use. For example, if polymer powder is used (such as ground PE), the addition of liquid additives to it may cause difficulties due to the homogeneous distribution and dispersion in the mixing and kneading process.
compound
The creation of raw materials by adding various additives to the factors such as heat resistance, impact resistance, color and hardness of the main raw material is called compound.
This raw material is no longer a pure material, it is a composite material reinforced with additives and uses directly as raw material. Masterbatch determines the color, physical properties and cost characteristics of the main raw material. In order to be developed, pigment, additives and fillers are mixed and presented to the customer in granule form. Although compound and masterbatch are similar in terms of production, they differ from each other in terms of usage. While the compound is used as 100% raw material, masterbatches are not used directly as raw materials. It is used by mixing with the raw material in certain proportions.
Although compound and masterbatch are similar in terms of production methods, they differ from each other in terms of usage. compound; It is called compound to create a raw material with the characteristics desired by the customer by adding various additives to the factors such as thermal resistance, impact resistance and hardness of the main raw material. After the compound, the raw material sent to the customer is no longer a pure material, but a composite material that has enhanced properties with additives. The customer buys this material from the compound manufacturer and uses it as raw material.
Masterbatch; Color, physical properties and cost characteristics of the main raw material In order to be developed, pigment, additives and fillers are mixed and presented to the customer in granule form. Unlike Compound, the customer does not use it as a raw material, it mixes it into the raw material in certain proportions and tries to eliminate its color, cost and physical deficiencies.
In its most basic form, a compound / masterbatch recipe is like this.
With %A+%B+%C+%D=100% the formula is valid for both compound and masterbatch.
But how will they be separated from each other?
The answer to this lies in the field of use. Until it reaches the usage area (final process), compound and masterbatch are two synonymous terms. It is exactly the same in terms of production methods.
In other words, this mixture made by the manufacturer will be defined as 100% directly in the extrusion machine or as a compound if it will be used as a carrier raw material in the largest proportion in the formula to be used, and as a masterbatch if it will be used in much smaller proportions (0,5%, 5%, 20%, etc.).
If the compound enters the extrusion directly at the end user, which is the main point of separation, it continues on its way as "compound".
However, if other mixtures or carriers are added to the raw materials at certain rates, it now changes its identity and either color or additive becomes "masterbatch". Another simple definition can be made as Color Masterbatch if the dyestuff in the formula is present, and as Additive Masterbatch if there is no dyestuff (ie C=0).
Compound production; It is made in order to improve the physical properties of the plastic that has insufficient physical properties. Loaded to carrier raw material It is carried out by adding materials such as fillers, pigments, carbon fibers.
Various problems occur during the processing of polymer materials and non-polymer materials (mostly additive materials such as Calcite, Talc, Sawdust, etc.). These; rather, it manifests itself as the fluidity of the material in the machine, the non-uniform distribution of the materials within each other, the non-bonding of the mixed materials, the formation of a bubble structure due to the moisture in the additive or raw material.
In extrusion, it creates air spaces in it due to the differences between the particle sizes and their non-melting structure. As it is, these voids are filled with polymeric gas and problems such as bubbles, non-melting particles, surface roughness, orange peel appearance are encountered by the end user. In fine precision moldings, the lack of filling of the mold causes the appearance of missing parts and collapses.
Depending on the micron size of the filling material and the formula ratio, filter clogging may become more frequent during the production process. Double drafting takes place once in the compound production process, and once in the subsequent production process.
However, the extrusion line in compound production and the extrusion lines and processes in the injection process are not identical.
Although the material is extruded for the second time during the injection process, this second drawing period is short due to the screw length and the cycle time. For this reason, when producing compound, after the material is drawn once, it is drawn again in the extruder for a second time and double-drawn is made, which visibly improves the gas accumulation in the material and the problem of unmelted particles.
The compound structure becomes much more homogenized. In the end user The above-mentioned physical problems are no longer observed in the material that is extruded for the third time.
Masterbatches While it can easily find its place in all plastic processes, it is mostly used as a compound in injection and other "molding" processes.
Carrier Polymer:
Compound raw material is determined according to the raw material to which the compound and masterbatch will be added and the place where the final product will be used. Compound production contains materials such as fillers, pigments, carbon fibers, which are added to the plastic in large proportions, in order to improve the physical properties of the plastic whose physical properties are insufficient.
Various problems occur during the processing of polymer material and non-polymer material. These; rather, it manifests itself as the fluidity of the material in the machine, the non-uniform distribution of the materials within each other, the non-bonding of the mixed materials, the formation of a bubble structure due to the moisture in the additive or raw material.

Color Masterbatches
Plastic products initially did not have the color and desired properties. These qualities are provided by the additives to be included in the compound after the main bearing structure is determined. These are defined as masterbatches. Although the word masterbatch means "main mixture", it is a term generally used to mean "paint in the form of granules that is added to the plastic raw material in the process of melting and shaping". It is a colorant in which organic or inorganic pigments or additives are homogeneously blended in a high concentration polymeric material (thermoplastic, rubber or elastomer). There are two types of masterbatches, color masterbatches and additive masterbatches. However, in the built-in definition, the expression masterbatch is mostly used for "color". Additive masterbatches are also directly pronounced as «additive». Color masterbatches are used to obtain the desired color and effect (fluorescence, gilding, pearlescent, opacity, etc.) on the product. Basically, the main asset of color masterbatches is to provide the practicality of use of the pigments needed in product coloring. In other words, it is the pigment that actually colors the product.
Color masterbatches have three basic components. Carrier raw material, color pigment and dispersants to aid the process. Dispersants are mostly process improvers or additives or catalysts such as homogeneity, conductivity, UV resistance.
Color masterbatches; They are in three main headings as black, white and color. And the desired color of the product is achieved with the different combinations of these three heads in an infinite variation. Masterbatches are generally processed on the main compound at rates of 3% or less, but they can be used above this rate to achieve the desired quality. The most basic point to be considered in masterbatches; The masterbatch carrier raw material is compatible with the main compound raw material.
In addition, it should be noted that the surface of the product is textured, rough, with pattern marks and its thickness will affect the effect of the color masterbatches used. In new studies to determine the correct preference and usage rate, before supplying the color masterbatch, the sample of the product should be delivered to the supplier and it will be appropriate to take a sample from the front.
Color masterbatch is a solid or liquid additive used to color plastics. It is a mixture of an encapsulated pigment or additive concentrated into a carrier resin during a heat treatment, which is then cooled and cut into a granular shape. Masterbatches allow manufacturers to economically color the raw polymer during the plastic production process.
Masterbatch production process is divided into two parts as "mono" and "tailor made".
Mono: In its production, colors with the main or the highest consumption rate are used.
Tailor made: It is the work that is obtained by matching the obtained mono colors in various combinations or with the desired colors.
The points to be considered can be listed as follows.
- Fillers used especially in PVC production change the color tone.
- The difference in cable production patterns affects the color of the paint.
- If the machines are not cleaned well, it causes discoloration and scarring.Stopping and running of the machines can cause contact with material that previously existed in the area other than the flow path. This occurs as a trace problem in the product. In cases where machine contamination is suspected, a few prints should be taken with only the raw material and the cleaning of the flow line should be checked at every stage.
- The first prints should be checked when the machines are stopped for more than 10 minutes and turned on again. Since the material has been exposed to heat for a long time, burning may occur.
- Especially in case of raw material used in film production and micron changes, trial production should be made.
- When working at temperatures lower than the melting point of the carrier used, melting will not occur in the final product.
- Moisture absorbing raw materials must be conditioned before production.
pigments
Some rocks, soils and minerals gain the feature of being used as "mineral pigment" after simple processes such as washing and grinding. The properties sought are suitable color, hiding power, oil absorption capacity, not containing water-soluble salts. It is also important that the dye soil has properties such as moisture content, minimum Fe2O3 grade, resistance to light, and its price. It is possible to darken and stabilize the colors by roasting inorganic pigments. In natural paint soils, the coloring element is usually the iron element in the minerals.
Minerals such as hematite, gotite, limonite become earthy as a result of weathering and form yellow, red and brown dyes such as okr and amber. The source of green colored earth dyes is minerals such as celadonite, garnierite and glauconite. Vivianite and azurite are used for blue dyes, while pyrolusite, graphite and magnetite are used for black dyes. Kaolin, barite, chalk and anhydrite are used in the production of white paints. Gray tones are obtained by adding ground shale. Mineral paints are used to provide color and density to plaster, mortar, cement, rubber, linoleum (upholstery) and similar materials.
A very precious paint, called Bolus, consisting of a mixture of iron hydroxide and montmorillonite, was taken from Anatolia and ground in Paris during the Middle Ages and used as a gilded red lining of wooden sculptures for centuries. Again, a red dye called Snopia, brought from Anatolia, was used in Rembrand's paintings and was highly sought after. Bolus is still used in watercolor production by mixing with gypsum and lime.
Pigments and dyes provide color, opacity and shimmer to plastics, textiles and many other materials.
Dyes are organic soluble substances that chemically bond with the substrate (component or decomposition substance).
Pigments are organic or inorganic particulate solids that are generally insoluble and do not react with the substrate.
Pigments are a material that changes the color of reflected or transmitted light as a result of wavelength-selective absorption. In other words, it is a substance that appears a certain color because it selectively absorbs light of certain wavelengths. The main purpose of using pigments is to provide color to materials, whether textiles or paints. Some people often think that pigments and dyes are the same, but they are quite different. The biggest difference between both is their resolution.
A dye can dissolve in a liquid by itself, while pigments can be dissolved in a liquid with the help of a binder. Dyes are primarily used in the textile and paper industry, while pigments are used in industries such as coloring dyes, inks, cosmetics and plastics.
Depending on the formulation methods, pigments can be divided into two types:
organic pigments
Inorganic pigments.
Apart from these two basic distinctions There are two other types of pigments:
metallic pigments
They are industrial pigments.
Metallic Pigments :
As the name suggests, metallic pigments include metal pigments such as zinc and aluminum pigments.
Industrial Pigments :
They are pigments that are widely used in industrial applications and include organic, inorganic and metallic pigments. There are three classes of pigments in the industry: absorption pigments (used in watercolor paints), metal effect pigments (used to create surface gloss), and pearlescent pigments.
Inorganic Pigments :
As you can guess from the name, this type of pigment is the opposite type of organic pigment. These pigments are also known as "synthetic pigments". They are formulated in laboratories and offer inorganic pigment manufacturers a great scope of control. Inorganic pigments are produced by relatively simple chemical processes such as oxidation.
Inorganic pigment suppliers mainly supply such pigments to the paint, plastics, synthetic fiber and ink industries. In applications where bright colors are required, organic pigments are used because they provide high color strength. Inorganic pigments include white opaque pigments that are commonly used to lighten other colors as well as provide opacity.
Organic (Natural) Pigments:
Such pigments occur naturally and have been used for centuries. Their chemical structure is quite simple. They are called organic because they contain minerals and metals that give them their color. Organic pigment manufacturers produce them by a simple process of washing, drying, pulverizing and combining them into a formulation.
Compared to inorganic pigments, this use of these pigments is less frequent and therefore there is a limited number of organic pigment suppliers. These pigments are used when the required color intensity is not too high.
Organic pigments are among the oldest pigments used by humans. It has been revealed that it was first used in the preparation of human funerals in the remains of 60 thousand years ago and in the art of multi-colored cave walls about 20 thousand years ago. Many inorganic pigments extracted from surface clay and rock deposits in prehistory have demonstrated exceptional persistence over long periods of time.
With few exceptions, inorganic pigments are combinations of a mineral element with oxygen and other elements (mostly sulfur, silicon, or carbon) that fall into the chemical classes known as oxides, oxide hydroxides, sulfides, sulfates, silicates, and carbonates.
The main caveat with natural inorganic pigments is that any paint containing them (especially siennas, umbers and ochers) will vary considerably between manufacturers. In 1998 Daniel Smith brought to the market a beautiful earth pigment called "Spanish gold vaccine", but its production was discontinued as clay resources were depleted and the source of the materials could not be identified.
Most of the traditionally natural inorganic colors; yellow ocher, raw sienna, burnt sienna, raw lumber, burnt lumber, and venetian or Indian red tones.
Pigments in this category include:
Red soils:
A broad and diverse category of pigments made from earth (mostly clay) containing large proportions of iron oxide (deep purple to light red hematite or day rust, orange to yellow lepidocrosite or dark brown maghemite) is sold as processed and natural iron oxide. Pigment color ranges from dull yellow to dull ocher, dull orange, dull red or dark brown to almost black. The color depends on the average particle size, the presence of manganese or other elements (which darken and dull the color), and whether the water is chemically bonded to the iron oxide crystals. Although red iron oxides are found all over the world and have been used as pigments since ancient times, rich deposits are now found near Malaga, in Spain (Spanish red with a characteristic brownish hue) and Hormuz, in the Persian Gulf (Persian red). Historically, the yellow-brown soil resources in Europe are rich in the region of Leghorn or near Siena (Tuscany, Italy). They contain 50% iron oxide and less than 1% manganese dioxide.
After firing or polishing around 2000 BC, the pottery was visibly browned or darkened. And sometimes natural manganese ores added to red soils have been observed to produce deeper red, purple or black colors in pottery clays or glazes.
Yellow soils:
Natural soils containing silica and clay are hydrated forms of iron oxide (yellow brown limonite or brown yellow to green yellow goethite) and traces of gypsum or manganese carbonate. Like red iron oxides, they are found worldwide and have been used as pigments and dyes since prehistory. Historically one of the best limonite grades, French ocher contains about 20% iron oxide and is high in silica.
Green lands:
Clays containing large amounts of silica and the green minerals glauconite and celadonite are composed mainly of hydrated iron, magnesium and aluminum potassium silicates. Color varies from dark, grayish blue green to dark, dull yellowish green. Completely lightfast and chemically inert, green earthing or terre has been used worldwide since verteantic times. The first documented use in painting in Europe is in Roman frescoes; It was also widely used in the Middle Ages as an underpainting for flesh tones and shadows. Originally mined from beds in Central Europe (present-day Czech Republic), near Verona (Italy), or in France, modern materials come from high-quality beds in Cyprus.
lapis lazuli:
It is a complex rock mixture of the dark blue mineral lazurite (natural ultramarine, the most chemically complex mineral pigment) with calcite or calcspar and iron pyrite. The name ultramarine comes from the designation azzuro oltramarino (blue above the sea), which is used to distinguish it from azzuro della magna. Lapis is found in China, Tibet, and Central Asia and was used in ancient Babylonian and Egyptian cultures to make jewelry, sculpture, and painting. imported to Europe via Venice, powdered and separated from impurities for use as a very costly reddish-blue pigment in medieval manuscripts and art.
(A much lighter and pale blue than navy blue)
(Na, Ca)8(AlSiO4)6(SO4,S,Cl)2
Azurite:
Less common (greenish blue) are copper carbonate crystals. Azurite is unstable in air. However, in ancient times it was used as a blue pigment, but often replaced by other synthetic pigments (such as Egyptian blue, copper calcium silicate) or preferred as the more expensive ultramarine undercoat. The crystals are usually coarsely ground because the color changes from dark blue to weak, pale blue as the particle size decreases. Azurite is decomposed by acids and darkens with heat and some oil tools and varnishes. From the 15th to the 17th centuries in Europe, Hungary was the main source of azurite, an important pigment used. Turks in Hungary Its use declined after the conquest.
(Sky blue, dark blue to pale blue; pale blue in transmitted light)
Malachite:
Mountain green, also called mineral green or verdeazzuro ("green sky blue"), is the more common (green) form of hydrated copper carbonate found worldwide in surface deposits of copper. The ancient Egyptians ground it into a powder to use as a green pigment, and since Roman times it has often been used for artistic uses. It fell completely out of use at the end of the 18th century. As the particle size decreases, its color becomes significantly lighter and turns blue.
(Blackish green with glass luster, emerald green and silk glitter or dull).
Chemical Composition: Cu2CO3
Crystal System: Monoclinic
Crystal Form: Very rare and small crystals, usually fibrous and radial, acicular, short-long prismatic; mostly massive, renal
Twinning: usual at surface {100}
Hardness: 3.5 - 4
Specific Gravity: 4 - 4.05
My language: {-201}
Color and Transparency: Bright green, blackish green; translucent-opaque
Line Color: Pale green
Luster: Needle-like crystals are silky, solid ones are dull-matte, others are glassy with diamond luster.
Distinguishing Characteristics: Color, renal form and solubility in HCl
Occurrence: Malachite is a typical secondary origin mineral formed in the oxidation zone of copper deposits.
It is found together with azurite, cuprite and copper. Other minerals that it forms are calcite, chrysocolla and limonite.
Psoriasis:
It is of organic origin. It is mostly formed by the concentric deposition of aragonite on the inner surfaces of the shell parts of mollusca (different stomach species)




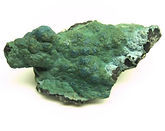
Red Soil
Yellow earth
Lapis Lazuli
Azurite
Malachite
Coloring Forms
In the choice of colorant (Color Masterbatc), there may be some preliminary evaluation criteria to be considered.
These criteria for choosing the right colorant;
-
Health and safety concerns
-
Ease of use in the production process
-
Color matching accuracy as well as the volume of use of certain colors
-
Elimination of color quality problems
-
Minimum impact on costing
may be titles like.
Concentrated colorants (color masterbatches):
Approximately 70% of the colorants used for plastics worldwide are in the form of concentrates. And almost half of this ratio is white. Color concentrates are the leading form in which colorants are added directly to the compound. Their physical structure is in the form of lentil or spaghetti cut granules. There are even super concentrated granules below 1 millimeter. It provides easy integration into the base (carrier) polymer by using automatic measuring equipment during melt processing in the production process. In plants without any dosing unit, the mixture is pre-blended by manual or mixer machines before extrusion. The most basic is the carrier polymer LDPE in concentrated colorants. However, if the process is for high performance applications, it is preferred to be coupled with the parent polymer (PP, PC etc.). Concentrated colorants are preferred in the rapid flow of the process.
Normal pigment loadings in the concentrates are in the order of 20% - 25%. However, there are also "super concentrates" containing up to 80% pigment. They have become cost-effective alternatives to standard products because they require less concentrate for them. The formulation can be enriched by adding additional features such as UV stabilizing additives to the content of concentrated colorants. In this way, the homogenization of these small proportioned additives in extrusion becomes more robust. This results in higher production rates as well as cost savings as the products blend more easily with the main polymer.
Rating: Cost (2x medium) / Transport-Handling (2x medium) / Volume (2x medium)
Dispersion (3x high) / Dosing Control (3x high) / Easy to Change Color (2x medium)
Liquid colorants:
They have high pigment loading of about 80%. Since they are liquid (fluid), they require special equipment for the automatic metering and pumping of the processing machine to the reservoir throat. requires. However, there are technical developments that can be connected to carrier pipelines much more easily. They allow the pigment to be dispersed well. However, in the absence of a pumping (dosing) unit, it will be difficult to obtain a homogenised mixture with powder polymers. This will cause problems in color distribution at the end of extrusion and will require a second shot (re-extruding) to optimize the result.
Rating: Cost (2x medium) / Transport-Handling (2x medium) / Volume (2x medium)
Dispersion (3x high) / Dosing Control (3x high) / Easy to Change Color (3x high)
Dry powder colorants (pigments):
They are the most cost-effective colorants available to buy. However, they require wetting units that allow them to be dispersed into the base polymer by careful weighing and bulk blending, which makes their use difficult. And at the same time, because of their powder form, they cause effective damage to the environment. It has a negative effect on the operators due to their suspension in the air. The working environment should definitely have a ventilation (absorbing fan) system due to its impressive health.
Rating: Cost (3x high) / Transport-Handling (1x weak) / Volume (3x high)
Dispersion (1x weak) / Dosing Control (2x medium) / Color transition ease (1x weak)
Precolored polymer:
Rating: Cost (1x weak) / Transport-Handling (3x high) / Volume (1x weak)
Dispersion (3x high) / Dosing Control (1x weak) / Easy to color transition (3x high)
Additive Masterbatches
Flame Retardants: Contain one or more of bromide, chlorine, nitrogen, aluminum, antimony and boron elements in its structure and reduce the effect of burning by including it in the polymeric chain. Some high performance plastics can be classified as flame resistant plastics, flame retardant plastics, fireproof plastics or self-extinguishing plastics, making them suitable for use where fire protection is important. Generally, thermoplastic materials are not literally flammable because they start to burn in direct contact with the flame. However, while most of the plastics continue to burn after the flame is pulled, the self-extinguishing plastics stop burning on their own after a while.
(Libaid-T 2)> PVC cable sheath and fire retardant and smoke suppressant (FRLS) compounds are also suitable for use. It provides better distribution of filling materials in PVC cable jacket compounds with high filling (Calcite, talc, ATH). It increases the flow values of high-filled PVC compound. Smooth shiny structure on the cable surface. It is an effective processing agent in elastomers with high filling or fire retardant additives. It is much more useful in viscosity reduction and flow improvement by using half of the metal stearates used in PP / EPDM and PE / EPDM mixtures, which are widely used in automobile parts applications. It also shows a very good mold release agent property in material molding. It is a suitable processing agent for all thermoset molding applications in powder form. It provides very good dispersion of all additives included in PF, UF and MF molding compounds. It improves the flow properties. It is especially recommended for injection and high fluid types. Including very complex molds, it ensures that the mold is uniformly and completely filled in a short time.
Antibacterials: It prevents algae and bacteria formation that may occur on the surface of the product in geographical regions with high humidity.
Antiblocks: It prevents blocking during the production of the film and has a light sliding effect. It increases the fluidity by providing the formation of uniformly shaped and equal sized particles with high efficiency. By minimizing the humidity, it prevents the small perforated structures on the surface called fish eye and the problems caused by the lens problem.
Antifogs: By increasing the surface tension of water molecules, they prevent water droplets from forming on the surface. Useful life of the AF additive; It can vary between 12 and 18 months depending on usage, environment and climatic conditions. The greenhouse cover provides prevention of sunburn or fungal diseases caused by water droplets formed on the inner surface of the greenhouse, and supports agricultural medicine savings and quality increase.
Antigases / Dehumidifiers: Moisture; They both complicate the process and cause weakness in mechanical properties. Antigases and dehumidifiers absorb the moisture and gases present in plastics during heat treatment and provide more homogeneous melt formation. One of the most important problems of the compound process is moisture. They make the process more difficult and cause weaknesses in mechanical properties by showing their effect on the end product producers both after the compound and after the compound.
Antistatics: By preventing the formation of static electricity on the plastic product, it prevents dust and foreign substances in the environment from sticking to the product.
(Libstat 95)> It is a new generation, highly active, nitrogen-free GMS containing Antistatic agent and lubricant. Especially materials such as PP, PE, PVC, which are among the thermoplastics with a wide variety of structures, are also suitable for static electricity control. It is suitable for food applications as it is made of herbal products in terms of its structure.
Essences: These are additives used to suppress the existing odors of plastics or bad odors of recycled raw materials. Tropical, banana, strawberry, rose etc. they can be of variety. They are mostly used with 1% and 2% ratios and are preferred to suppress bad odors.
Generally called second quality products, they are needed for the use of frozen raw materials that have been products several times before.
Infra Red Additives: This additive mostly used in greenhouse covers; It allows the infrared (IR) rays coming from the sun to enter the greenhouse more effectively and by refraction. It reduces the escape of the beam from inside the greenhouse through radiation. Accordingly; It reduces day-night temperature difference, sun burns on the plant, frost risk in the greenhouse, and increases efficiency and quality.
Transparencies: It regulates the molecular structure of the polymeric compound and ensures that the image that may be cloudy is more transparent and the light transmittance is higher.
Optical Brighteners: When the product color is insufficient, it increases the surface light reflection and provides a brighter appearance.
Optical Brighteners: (TitanDiOxide)> It is a product with a stable chemical structure, enriched with silicon and zircon materials with its organic structure surface treatments. It is a product with excellent whiteness, brightness, covering and crush, showing very good resistance to weather conditions and factors such as chalking and giving an effect. It is water soluble.
(Zirtex OB-1)> Suitable for polyester fiber, nylon fiber, PP fiber bleaching applications. It is suitable for use in plastic applications such as hard PVC, ABS, EVA, PS, PC. It is suitable for use in polyester and nylon polymerization. It is water-repellent, it is insoluble in water, but paraffin with high melting temperatures, mineral oils and organic solvents can also be dissolved. It is especially suitable for the process of plastics processed at high temperatures.
Light Emitters: They are mostly used to solve the problems of light propagation experienced in LED lighting products. By increasing the light transmittance, it decreases the need for LED usage.
External Lubricants: It reduces the friction and adhesion that occurs between polymer molecules and the barrel / screw. Efficiency increases, wear on metal surfaces is reduced, barrel / screw cleaning becomes more comfortable in order transitions, cleaning consumption and posture are reduced.
(Zinc Stearate)> As external lubricant, acid cleaner, mold release, process agent in PP, LLDPE, HDPE and PS materials in the plastic industry. It is used as a process agent in rubber, as a mold release agent, and as a process improver in synthetic and polyester materials.
(Lithium Stearate) In process conditions> 200 ° C, it is difficult for every external lubricant to perform without degradation. Lithium stearates are a superior performance external lubricant that can operate at these high temperatures.
(PE Wax)> It is the most widely used dispersing agent and external lubricant in the world. It is an indispensable dispersing agent for almost all compound and masterbatch processes. However, material purity and quality are effective here.
(Libaid-T 2)> Provides a very good mold release effect. You do not need to add traditional lubricants such as PE wax and metal sterarate to the formulation. It gives less usage and effective results compared to traditionally used sliders.
Internal Lubricants: It accelerates homogenization by reducing the friction between polymer molecules. It helps the different polymers in the compound to form a homogeneous structure with the decrease of molecular friction. However, the desired result may not be achieved at different MFI values. In addition, the viscosity of the lubricant additive is also important here. ( Viscosity: It is the internal resistance of fluids to flow. Mathematically, it is evident that fluids with a high viscosity value are more difficult to flow. For example, the viscosity of filtered honey is higher than the viscosity of water. Viscosity changes with temperature. Basically, the viscosity of many liquids decreases with increasing temperature. As it increases, the forces of attraction between molecules decrease and the molecules move more freely, which increases the fluidity.
Also, in many liquids, viscosity increases with increasing pressure. )
(Calcium Stearate)> It is used as an internal lubricant in the plastic and rubber industry, as a release agent, acid cleaner, as an elestomer processing agent in elostomers, as a processing agent to reduce the extruder pressure in the production of PVC pipes, fittings, and siding. In addition, calcium stearates are used as an anti-caking agent in polyolefins.
(Libwax C - Amide Wax)> It is an excellent mold release agent and dispersant agent in engineering plastics that are processed at high temperatures. It has a much higher heat resistance than conventional lubricants. In addition, higher performance can be obtained by using up to 50% less than traditional lubricants. It shows both internal and external lubricant properties in all thermoplastics and thermosets. In compound and masterbatch processes; ABS and PS increase the flow characteristics of the material. It acts as a dispersing agent in materials containing pigments. It can be used as pigment dispersing agent in polyolefins. It works as an inherent mold release agent in polyamides. It is used as a lubricant and a mold release agent in Acetal Plastics.
Pigment Wetting Agents (Libnol-101)> Used as a very good wetting and dispersing agent in titanium dioxide and other inorganic pigment masterbatch applications.
(Libnol – 400)> It is used as a dispersing agent and pigment wetting agent in masterbatches made with pigments that are difficult to dispersion, such as carbon black and some very special organic pigments.
Odor Absorbers: During the heat treatment of all polymers, scent molecules are released by the reaction of chemicals. This gives the environment the sense of smell. Odor absorbers adsorb odor molecules of possible malodors.
Process Aid / Process Improvers: It facilitates the production by reducing the friction between the polymeric compound and the barrel / screw. It provides energy savings. It prevents roughness on the film surface. It is also called process improver.
(Libnol G-7481)> It is a process agent that helps polymers in compound and masterbatch processes and it certainly does not cause a significant change in physical properties. It improves filling dispersion, flow properties and separating properties during the process. It is an excellent processing agent for ester-type high temperature thermoplastics with low evaporation and good thermal stability. It is a mold release agent for PC, PET / PBT.
(Libaid-T 2)> It is a multi functional process improver. It is a multi-functional process agent that ensures uniform distribution of pigment and filling materials in the polymer matrix, especially in high fillers (calcite, talc, ATH) and high pigment loaded masterbatches and compounds. It is also a very good binder. Therefore, it acts as a good binder between the filler and the polymer system. Provides homogeneous distribution of additives in compound or masterbatch and better bonding of fillers and pigments to the main carrier polymer.
In filled compounds; It regulates the flow temperature. Provides perfect distribution in additives and fillers (Calcite, Talc, ATH). Die shrinkage rate is reduced. It makes the surface appearance very well. It provides ease of demolding in many systems including TPE. It prevents flowering properties in printing.
In masterbatch production; It is compatible with all thermoplastic olefins. It regulates the distribution in organic and inorganic pigments that are difficult to dispersion. It provides regulation of dispersion with high pigment loading in masterbatch. It provides a very good surface quality in granules. It improves the flow properties. It provides good dispersion of carbon black, which is difficult to dispersion in black masterbatch, as well as the carrier raw material.
Greases / Lubricants: Provides a lubricating effect by preventing film surfaces from sticking to each other and to metal surfaces. It helps to take thin film and to open the film layers easily. Provides efficiency with low temperature, increases film surface gloss.
(Lutamid-P 98)> It is a high purity oleamide agent. It reduces the friction rate between film layers or between two films, allowing it to slide over each other. It is used as a mold release agent in printing inks, cap production, EVA copolymers, rubber compounds, and coatings.
(Libaid-T2)> After use, there is no need to use other traditional sliders. In TPE and TPO compounds, it is a better viscosity reducer compared to conventional lubricants. It provides very good dispersion of added fillers and other additives.
Ultra Violet Additives: Plastics used in outdoor applications can be exposed to severe weather effects. These applications often require a weatherproof plastic material that can withstand the adverse effects of ultraviolet rays, which can affect the appearance and mechanical properties of plastics. Therefore, it is often a smart detail that weather-resistant plastics are somewhat UV-resistant, as UV radiation can have a particularly high effect on materials used outdoors and exposed to outdoor elements.
These stabilizer additives prevent oxidation of the polymer chain against low wavelength sunlight (UV). In this way, it protects the product from the harmful effects of sunlight, prevents fading and extends its service life.
UV resistance of plastics is generally achieved by the use of additives such as UV stabilizers, black coloring (usually using carbon black) or protective surface coatings (paint or metal coating, etc.). Additive carbon black is a low cost and often very effective method of creating UV resistant plastic. In addition, fluorinated polymers such as PTFE and PVDF can exhibit very good UV stability in their natural state. In UV resistant plastics;
-
Yellowing of the plastic is not observed
-
Painted plastics do not leak
-
Plastic surface does not turn white
-
No stress cracks
-
No fragility development
-
There is no decrease in strength, flexibility and hardness.
Antiozonant Additives: These are materials added to plastic to slow the degradation of the finished product caused by ozone exposure. Antiozonants usually work by moving to the surface of the product and then create an ozone-proof barrier on the surface.
Swelling Additives: Sometimes called chemical foaming agents. They are used to separate gas into plastic or resin. It is used to reduce weight, increase softness, provide insulation, add shock absorption properties, or provide flexibility in the final product.
Coupling Materials: They promote physical or chemical interaction with the polymer.
Plasticizers / Plasticizers
Plasticizers are relatively non-volatile organic substances (especially liquids). When incorporated into a plastic or elastomer, they help the polymer's flexibility, processability.
Plasticizers increase the flow and thermoplasticity of a polymer by reducing the viscosity, glass transition temperature (Tg), melting temperature (Tm) and elastic modulus of the polymer melt without changing the basic chemical character of the plasticized material.
Plasticizers are among the most commonly used additives in the plastic industry. They are also generally less expensive than other additives used in polymer processing. Plasticizers are mostly used in PVC, which is the third largest polymer by volume after PP and PE. In contrast, PVC is used in a wide range of products.
In applications such as plasticizers, PVC (or rigid PVC) pipes, exterior and window profiles, PVC (or flexible PVC) automotive interior lining, cables, PVC films, flooring, roof and wall coverings, etc. they are used in areas. However, acrylics, PET, polyolefins, polyurethanes, etc. a significant amount of plasticizer is used in such polymers. Plasticizers are sometimes used in rubbers as well, but in these cases the purpose is to be extenders.
Plasticization process is gathered under two main headings as internal and external.
Internal Plasticization: A polymer can be plasticized internally by chemically modifying the polymer or monomer, thus increasing its flexibility. It involves copolymerization of the desired polymer (high Tg) and plasticizer (low Tg) monomers so that the plasticizer becomes an integral part of the polymer chain. The most commonly used internal plasticizer monomers: Vinyl acetate, Vinylidene chloride. Also, the complexity of the reaction can lead to longer reaction times and increased costs.
Internally plasticized materials show temperature dependence and dimensional instability at high temperatures.
External Plasticization: This is the most widely used method of plasticization because it is low cost. They are liquid plasticizers, giving the formulator freedom to develop formulations for a range of products (from semi-rigid to extremely flexible depending on quantity).
The most commonly used external plasticizers are esters of acids or acid anhydrides formed by reaction with alcohols.
There are two main groups of outer plasticizers:
1- Primary plasticizers increase the elongation, softness and flexibility of the polymer. They are highly compatible with polymers and can be added in large quantities.
For example: up to 50% vinyl gloves are plasticizers that make PVC flexible and soft enough to wear.
2- Secondary plasticizer is a plasticizer that typically cannot be used as the sole plasticizer in a plasticized polymer. Secondary plasticizers may have limited compatibility with the polymer and / or high volatility. It may or may not contain functional groups that allow them to dissolve the polymer at processing temperatures.
Secondary plasticizers: They are preferred for the purposes of cost reduction, viscosity reduction, working strength, increasing surface lubrication, low temperature property improvement.
A subset of secondary plasticizers are extenders as well. They are commonly used with primary plasticizers to reduce the costs of general purpose flexible PVC. They are mostly low cost oils with limited compatibility with PVC. They are added to reduce cost and in some cases increase fire resistance. Typical examples include naphthenic hydrocarbons, aliphatic hydrocarbons, chlorinated paraffins (fire resistance).
Plasticizer Loss / Exudation: Incompatibility between polymer and plasticizer can cause exudation. There are several factors that can cause the plasticizer to migrate from the plastic surface (or into or into a substrate where it is kept in close contact), such as heat exchange, moisture change, mechanical stress, weathering. Loss of plasticizer can result in less elasticity, embrittlement and cracking.
Classification of Plasticizers: usually classified according to their chemical composition. It is possible to understand the properties of structural elements (eg different alcohols in a homologous series of phthalates, adipates, etc.) plasticizers and their effect on base polymers.
Different plasticizers affect different physical and chemical properties of materials. Therefore, a specific plasticizer will be needed to change the properties in a certain direction to meet the requirements.
There are several general chemical families of plasticizers used for polymer modification.
Among them, the most commonly used are:
Phthalate Esters: They are produced by esterification of phthalic anhydride or phthalic acid obtained by oxidation of orthoxylin or naphthalene. The most commonly used phthalate plasticizers include:
DEHP: Low molecular weight orthophthalate. Still the world's most widely used PVC plasticizer
DINP, DIDP: High molecular weight ortho-phthalates
Aliphatic dibasic acid Esters: These include chemicals such as glutarates, adipates, azelates, and sebecates. They are made from aliphatic dibasic acids such as adipic acid and alcohols.
Benzoate Esters: They are the esterification products of benzoic acid and selected alcohols or diols.
Trimellitate Esters: They are produced by esterification of trimellitic anhydride (TMA) and typically C8 - C10 alcohols.
Polyesters: They are formed by the reaction of many combinations of dicarboxylic acids and bifunctional alcohols.
Citrates: Tetraesters resulting from the reaction of one mole of citric acid with three moles of alcohol. Only the hydroxyl group of citric acid is acetylated.
Bio-based Plasticizers: Epoxidized soybean oil (ESBO), epoxidized linseed oil (ELO), castor oil, palm oil, other vegetable oils, starches, sugars etc.
Others: Includes Phosphates, Chlorinated Paraffins, Alkyl Sulphonic Acid Esters, and more.
Application Areas of Plasticizers: More than 90% of the plasticizers used in thermoplastic polymers are used in PVC. The plasticized polymer market and the plasticized PVC market are largely the same, but some plasticizers are also used in acrylic polymers, polyurethanes, polystyrene or even polyolefins.
Major end uses include:
Film and Coating: Products made of flexible PVC film and sheet include roofing membranes, geomembranes, flooring, luggage, advertising signs, swimming pool linings, and others.
Flooring: Flexible PVC flooring products include flexible sheet flooring, vinyl composition tile, luxury vinyl tile, vinyl backed carpet tile.
Wire and Cable: Flexible PVC is a good electrical insulator with good workability and a useful service temperature range, so it is an excellent material for electrical applications such as insulation and sheath for electrical conductors, insulation for fiber optic cables.
Coated Fabrics: PVC synthetic coated fabrics are weather resistant and have excellent strength and durability. It is used in industries that support architecture, lifestyle, sports, advertising, defense, mining, food and agriculture, automobiles, and transportation. Products include tarpaulins, tents, outdoor furniture.
Consumer goods: Clothing, shoes, packaging
Medical: Blood bags, IV tubes, biohazardous structures, other medical devices
Non-PVCs: Small amounts of PVC-type plasticizers are also used in other polymers including acrylics, polyurethanes, polystyrene. Most plastic PVC products are durable products, long-lasting products. Phthalates are well suited for use in such products due to their low volatility, low water solubility, good resistance to sunlight and temperature extremes, good compatibility with PVC polymer and generally good resistance to biodegradation. For example (Flexible PVC roofing membranes, Geomembranes, Wire and cable insulation). It is very difficult to replace phthalate plasticizers in these end uses. Similarly, it has been found that phthalate plasticizers are easier to process phthalate replacements in flexible PVC compounds than at least some, due to their relatively high solvating power and relatively low viscosity for the PVC polymer.
Antioxidants
"It is certain that a basic amount of knowledge about oxidation is needed to understand the role of antioxidants. In this context, oxidation, one of the most fundamental reactions of life, is simply the flow of electrons from one atom to another. The increase in positive charge (oxidation) is the flow of electrons from the atom. I mean, the negative charge of the atom decreases and the positive charge increases. Oxygen is one of the most important oxidants in nature. That is, when there is oxygen in the environment, all electrons flow towards oxygen. This is why oxidation is a word similar to oxygen. The subject is most visible and quickly understood. example; Iron is rusting. If there is oxygen in the environment, electrons flow from iron to oxygen, so the iron oxidizes, that is, it rusts. This reaction continues as a chain and increasing. If there is no counter power to stop these extremely reactive oxidants, this extinction will continue until there is no solid molecule in the environment. That's antioxidants, that's the counterforce. They contribute to the protection of the polymer chain by removing the electrons from the chain and stopping the desire to combine with oxygen.
Antioxidants are used to provide polymer protection both against oxidation during melt processing and as a 'long term thermal stabilizer' throughout the product's life cycle. It delays the deterioration of the polymer by weather conditions and extends its service life. Such long-term thermal stabilizers are different from melt processing stabilizers. That is, they must function at temperatures well below the polymer melting point.
Antioxidants are added to plastics to prevent degradation caused by thermo-mechanical or thermo-oxidative conditions. Antioxidants extend the life of a product, enhance its appearance and maintain its strength, hardness and flexibility. The way these antioxidants interrupt the degradation process varies according to their structure. Various amines, phenolics, phosphites, thioesters, etc., as antioxidants for plastics. used.
(Richfos-168)> In many polymeric materials, it acts as a heat stabilizer by preventing the material from decomposing at high temperatures during the process. Thanks to its low volatility rate, it enables the processed polymer to be processed at the required high temperatures and time period. Suitable for use on PP, PE, PC, ABS and polyesters
(Richbox-1010)> Particularly effective against polymer degradation during long-term aging. It is also very effective as a process stabilizer. It exhibits good resistance to color change at high temperatures encountered with thermoplastic polymer processing. It is a high molecular weight antioxidant that provides low volatility.
(Richbox-1076)> It effectively prevents oxidation degradation that will occur in many polymeric processes and end-uses. Anox PP 18 is an excellent stabilizer in polyolefins, impact styrenics, block copolymers, elastomers, PVC and polyurethanes.
(Richnox-1098)> It is a phenolic antioxidant that provides stabilization feature against polymer deterioration during long-term aging. Especially PA compound, masterbatch exhibits good resistance to color change at high temperatures encountered in the production of parts.
It can also be used in polyacetals, polyesters, polyurethanes, adhesives, elastomers products.

Phthalates
It is typically produced by esterification of phthalic anhydride obtained by the oxidation of orthoxylene. Phthalates appear almost colorless with a faint odor. Their solubility in water is limited, but miscible in most organic solvents (mineral oil, etc.).
-
They are a traditional choice as they resist extraction, evaporation and migration.
-
Phthalates offer durability, flexibility, weatherability and can withstand high temperatures
-
Phthalates are economical compared to other plasticizers
-
In polymers such as PVC, phthalates are not chemically bonded and leached out of plastics, causing them to occur in the environment.
-
Some phthalate plasticizers can pose serious health risks as they are carcinogens and / or developmental toxins.
-
Some phthalates can accumulate in the human body at low levels.