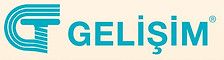


Hydrocarbons
It is an organic compound consisting of two elements, hydrogen and carbon. Most of the petroleum composition consists of hydrocarbons of varying lengths.
The smallest hydrocarbon methane consists of a single carbon atom and four hydrogen atoms. However, hydrocarbons can consist of hundreds or thousands of individual atoms linked together in many ways, including chains, circles, and other complex shapes.
In order to classify the properties of hydrocarbons, they are divided into several basic types.
Alkanes: These are called saturated hydrocarbons. That is, they only contain single bonds between all carbon atoms. Alkanes are the basis of petroleum fuels and exist in linear and branched forms.
Unsaturated Hydrocarbons: Hydrocarbons that have one or more double bonds between carbon atoms are called alkenes.
Cycloalkanes: Any hydrocarbon containing one or more ring structures.
Aromatic Hydrocarbons: Aromatic hydrocarbons , also called arenes, are a unique class of carbon molecules in which carbon atoms are bonded by successive double and single bonds. This class of molecules has special ring structures in which the bonds between carbon atoms are an intermediate bond between single and double bonds.
Molecules in this class contain the industrial solvent "benzene".
Benzene (C6H6): Like other hydrocarbons, benzene is a natural component of petroleum. It is a colorless, flammable, sweet-smelling liquid at room temperature and is a component of most gasoline blends because of its high octane number.
Benzene is also highly carcinogenic and is well known to cause bone marrow failure and bone cancer. Of course, its carcinogenicity is not well known when used as an additive in aftershave and other cosmetics due to its "pleasant aroma".
The largest use of benzene (50%) is the product of styrene and polystyrene plastics. It is also converted into a molecule known as cyclohexane, which is important in Nylon production. About 15% of benzene is used to produce cyclohexane. Smaller amounts are used in everything from pesticides to rubber.
The benzene structure can be drawn in two ways. In the first, the double bond character is drawn explicitly. In the short handed version, a circle is drawn inside the ring to show the structure. There is only one hydrogen bonded to each carbon atom in benzene.
I. and II below. drawings are identical. III in practice. drawing is used.
Benzene is a colorless, flammable liquid with a boiling point of 80.1 ° C and a melting point of 5.5 ° C.
Binuclear Aromatic Hydrocarbons: They are compounds that contain two benzene rings in their molecules.
Hydrocarbons
It is an organic compound consisting of two elements, hydrogen and carbon. Most of the petroleum composition consists of hydrocarbons of varying lengths.
The smallest hydrocarbon methane consists of a single carbon atom and four hydrogen atoms. However, hydrocarbons can consist of hundreds or thousands of individual atoms linked together in many ways, including chains, circles, and other complex shapes.
In order to classify the properties of hydrocarbons, they are divided into several basic types.
Alkanes: These are called saturated hydrocarbons. That is, they only contain single bonds between all carbon atoms. Alkanes are the basis of petroleum fuels and exist in linear and branched forms.
Unsaturated Hydrocarbons: Hydrocarbons that have one or more double bonds between carbon atoms are called alkenes.
Cycloalkanes: Any hydrocarbon containing one or more ring structures.
Aromatic Hydrocarbons: Aromatic hydrocarbons , also called arenes, are a unique class of carbon molecules in which carbon atoms are bonded by successive double and single bonds. This class of molecules has special ring structures in which the bonds between carbon atoms are an intermediate bond between single and double bonds.
Molecules in this class contain the industrial solvent "benzene".
Benzene (C6H6): Like other hydrocarbons, benzene is a natural component of petroleum. It is a colorless, flammable, sweet-smelling liquid at room temperature and is a component of most gasoline blends because of its high octane number.
Benzene is also highly carcinogenic and is well known to cause bone marrow failure and bone cancer. Of course, its carcinogenicity is not well known when used as an additive in aftershave and other cosmetics due to its "pleasant aroma".
The largest use of benzene (50%) is the product of styrene and polystyrene plastics. It is also converted into a molecule known as cyclohexane, which is important in Nylon production. About 15% of benzene is used to produce cyclohexane. Smaller amounts are used in everything from pesticides to rubber.
The benzene structure can be drawn in two ways. In the first, the double bond character is drawn explicitly. In the short handed version, a circle is drawn inside the ring to show the structure. There is only one hydrogen bonded to each carbon atom in benzene.
I. and II below. drawings are identical. III in practice. drawing is used.
Benzene is a colorless, flammable liquid with a boiling point of 80.1 ° C and a melting point of 5.5 ° C.
Binuclear Aromatic Hydrocarbons: They are compounds that contain two benzene rings in their molecules.
About
Kyäni, nutritional supplement products consisting of beneficial ingredients; It delivers to more than 50 countries around the world with unique business opportunities. We use Kyäni products daily to maintain our ideal health, share these products with others, devote a certain amount of time to work almost every day to build and maintain our business, and share our success with others by involving others in the Kyäni opportunity or contributing to the Potato Pak and Caring Hands programs.
About
Kyäni, nutritional supplement products consisting of beneficial ingredients; It delivers to more than 50 countries around the world with unique business opportunities. We use Kyäni products daily to maintain our ideal health, share these products with others, devote a certain amount of time to work almost every day to build and maintain our business, and share our success with others by involving others in the Kyäni opportunity or contributing to the Potato Pak and Caring Hands programs.
Page Under Construction.
Page Under Construction.
Training / Knowledge / Solution Platform
An Overview of the Problems Experienced in the Processes
To ensure the extrusion production is successful, every parameter must be defined, controlled and monitored. Some variables depend on the equipment, some on the operating conditions. All variables vary from mold quality to temperatures and pressures.
Before starting the production process, it would be appropriate to take some preventive measures.
Periodic maintenance of all equipment used for temperature, pressure, cycle and ampere should be done.
A constant raw material process minimizes problems. This starts with how the raw material is stored. Storage is required in a clean and dry area without exposure to extreme temperature changes. To ensure that the resin is consistent, some companies perform resin analysis to measure the material and record density, melt index, shear rate, viscosity data, and tensile strength. If it is too dry, it may not melt and the resin cannot be processed. Even lot shifts of the same raw material may cause changes in storage conditions.
Typical extrusion problems fall into a few main categories:
Aesthetic imperfections (eg dimples, black specifications, pinholes, drag marks, die lines, sting marks) Such as size, shape imperfections. When a problem occurs, the first step is to examine the components of the manufacturing process that start with the equipment. The problem may be that the screw design and / or temperature is causing the problem, or the mold is not made properly, or the temperature of a particular region in the extrusion line is wrong. The main variables that should be examined when they do not match the finished product specifications and dimensions after extrusion are:
Melting pressure, melting temperature, shell temperature, mold temperature, heaters, resistances, cooling system, speed and structure of the screw, engine load in amperes
production line speed, mold wear or wrong design.
When faced with problems in extrusion; Manufacturers will normally refer to technical equipment that is not functioning properly in a stable process, while technicians will refer to improper application of current production conditions (ie temperature, pressure, lot of material, etc.). And it will approach the solution of the problem from this perspective.
The fact that the producers are not familiar with the technical approaches and the technicians are not familiar with the production processes once again reveals the importance of teamwork in extrusion problems.
Failure of the parties to keep their process, maintenance and breakdown records in a healthy way will lead to the "discovery of America over and over again".
In this respect, the most basic application in solving extrusion problems is keeping all developments in a "common pool" under the name of quality records, and especially the first step to create troubleshooting timelines.
The extrusion process is literally a "black box" process.
What is happening inside an extruder is invisible to the naked eye, so in order to envision what is going on inside the barrel / furnace, it is necessary to have knowledge of the extruder components and their values.
Screw diameter, length, characteristic, motor / reducer power that gives the screw the rotational motion, the main argument of heat treatment is the resistances, their location, thermocouples measuring the heat value, thermal or motion sensors, timing regulators, cooling line temperatures, etc.
Most important of all is the digital / analog displays where the values they generate are read.
He must be absolutely sure that all sensors are working and that readings are correctly calibrated.
Apart from these, operators; They also need to know about pre- and post-extrusion equipment such as dryers, blenders, granulators, conveyors and feeders, gear pumps, screen changers, calibrators, water pools and troughs, laser gauges, pullers and wrappers, and even die conveying. To solve extrusion problems, the process must be understood from start to finish. A training covering material and equipment specifications is required at the beginning of the job. However, this is usually the least effective and in some respects the most expensive method.
Improper operation of an extruder by untrained personnel can result in costly damage or even worker injuries.
For a good process management, it is an indication that the problems are avoided by intervening immediately, as well as the trouble-free production.
The most basic problem-solving process step; It is a comparison with the process conditions in the smooth processes. For this, transaction records, which are also kept as "quality records", must be kept.
Maintaining a 'troubleshooting timeline' will make most of the work easier.
Timeline for Troubleshoot
It is a historical record of what kind of change the problems experienced in the processes caused on the material / product and with which interventions the analysis was made. In other words, with all the fault records kept, all changes and results applied on the process are tabulated and transformed into a flow diagram. Having created such a record document will definitely affect your career as a «problem solver». All process data (temperature, pressure, cycle, size, which screw, mold, raw material batch, lot, solution time, operator, shift etc.) should be recorded. Notes such as what was done and how much time it took should be added. Later, this data will be important when this or a similar problem is encountered. What has been done before, what should be done in order to solve the problem, will help you to intervene on time. However, it should not be forgotten that the source of the problem may have originated much earlier, not just before the problem, and it should not be forgotten that it may be necessary to evaluate the longer historical process retrospectively. timelines provide a working methodology helpful in problem solving. It helps the intellectual organization. It does not provide solutions for the absolute problem. Timelines support teamwork, the search for the truth, the openness to different views, and the emergence of opposing views or awareness. “Fishbone” diagrams, which are effective and simple to use, can be preferred. The general application area in these diagrams is to prevent product design and quality errors. Taking the opinions of different segments while investigating the reasons, creating an environment where everyone can express their opinions easily and without hesitation, being impartial while writing the reasons, paying attention to their solubility, especially keeping the diagram updated according to changing conditions will provide data accumulation that will help in troubleshooting.

Problems Experienced in the Extrusion Process
Melt Fracture:
Melt fracture can have various appearances. It can be seen as slip stick (or bamboo), palm tree, spiral or random mixed roughness. Generally, melt fracture involves head / nozzle stresses and is generally associated with polymeric material. It can be cured by material or mechanical means.It is always a good idea to streamline the head flow channel to stop melt fracture. The reduction of shear stress can be done by increasing the mold cavity, decreasing the extrusion speed, increasing the head temperature, increasing the melt temperature, or decreasing the melt viscosity. Viscosity can be reduced by using a processing aid or lubricant. Another common solution for melt fracture is a heater assembly to raise the head temperature to the point where the shear stress for melt fracture falls below the critical shear stress. The residence time of the melt in the head area is so short that the temperatures can be relatively high. The head area heater can also reduce head pressure and provide up to 20% higher extrusion efficiency while maintaining good product appearance and dimensional tolerances. Also, ultrasonic vibration of the head with externally mounted transducers causes plastics to become thinner by shear. Limited information is available in this technique, but when the rate of deformation is high enough it can reduce melt viscosity by order of magnitude.
The plastic melt layer in the head wall is subjected to very high frequency deformation, resulting in a large drop in melt viscosity at the head wall. This application also decreases head pressure, reduces swelling, melt fracture and mold-lip sagging.
Low Efficiency:
First of all, it should be checked whether the material used is dry. Increasing the screw speed increases the efficiency.
In the case of screw rotation probe, reducing the compression ratio in addition to reducing the filtration causes the molten material to exit the head faster. Increasing the head / mold temperature also has an effect on efficiency.
No Homogeneous Melt:
Different screw properties are required to process different raw materials. If the screw used for processing the raw material is not suitable for processing, the product removed from the mold will not meet the desired properties. Select the appropriate screw for processing the raw material you are processing by checking the screw. If the pressure inside the screw is lower than necessary, it will prevent the raw material from homogenization and plasticization. The pressure inside the screw is achieved by increasing the screw speed. Check the screw speed and increase it by the appropriate amount. In a poorly designed mold, the product may not come out homogeneously. The processing temperature is not suitable
Provide appropriate processing temperature as this will prevent plasticization and homogeneity. Check the screw speed.
Failure to Change Temperatures:
Heaters may be defective. There may be a breakdown in electrical connections. The processing temperature of the raw material is provided by heaters. Failure to operate one or all of the heaters will prevent the product from reaching the processing temperature.
should not be forgotten. For this reason, check whether the temperature values increase after the machine is turned on and if there is a defective heater whose temperature values do not increase, change the heaters by informing the electrical unit. Another reason why the heaters do not heat may be an electrical connection failure. Again, in such cases, notify the electricity related unit and ask for the fault to be rectified.
Frequent Breakdowns of the Production Line:
The speed of the hammer may be high. Excessive speed of the hammer can cause thinning and rupture of the product that is overstretched while being pulled. In such cases, reduce the speed of the hammer to prevent tearing and thinning. If the product breaks even though the hammer pulls at a normal speed, another reason for this situation arising from the machine is that the proper screw rotation is not provided. In this case, increase the screw speed in accordance with the amount of raw material to be obtained per unit time. If the speed of the towing unit increases or decreases independently during shooting, or stops intermittently and starts working again, the product may break. In such cases, the pneumatic connections of the tow tractor should be checked. One of the reasons for the product to break is the insufficient cooling. In such cases, the cooling system and calibrated cooling channels should be checked, if there is a clogged cooling channel, it should be cleaned and opened. Another reason for insufficient cooling is cooling water
temperature is above the desired values. This may be due to the water used for cooling not being sufficiently cooled in the system. It should be checked whether the water cooling is working or not. Control of chillers should not be skipped. One of the reasons for the product to rupture during processing is the high processing temperatures. In this case, the product may rupture as it will not be sufficiently cooled and hardened. Ensure proper processing temperatures by controlling processing temperatures. Insufficient plasticization and lack of homogeneity is another factor that causes the product to rupture.
Poor Adhesion or Non-Adhesion in Co-injection:
There is a need to increase the melting temperature and compression in the head.
Very Shine:
Lower the melt temperature. Decrease the inflation pressure. Increase the vice force.
Matt / Dull Surface:
Increasing the initial and final temperatures and increasing the melt temperature will improve the dull, matte surface appearance. If necessary, the compression ratio may also need to be increased.
Welding Lines:
Image in the form of foreign material or deformation line on the caliber or mold surface. Increase the melt temperature. Increase head temperature. Clean the head and head parts. Check the strainer and replace if necessary. Check the mold and caliber. Any foreign that may be on the mold or caliber
Clean the material with soft materials that will not damage the mold and caliber.
Distorted Thickness Distribution:
Product thickness is determined by the head / mold. Non-homogeneous distribution of heat in the mold, the product
It may cause the output to be fast at some points in the mold and slow at some points. Head temperature control and head adjustment should be done.
Traces of Burn: A temperature value set above the processing temperatures may cause burning marks on the product or burning of the product. This can also lead to long maintenance jobs. In such cases, control and lower the processing temperature values. If the speed of the screw is slower than necessary, it may cause the raw material remaining in that area for a long time to overheat and burn. Increase the screw speed according to the appropriate values.
Cutting Problems:
Cutters used for a long time may become blunt after a while and lose their cutting properties. In such cases, the blades must be sharpened. The low force of the pressure roller in the granulator may prevent the cutting. In this case, increase the cutter press force.
Break at Shear:
Excessive pressure exerted by the cutter on the product to cut the product may cause the product to break from the cutting areas by not being able to withstand this pressure. In such cases, reduce the cutter press force. Another reason for the product to break during cutting is the rapid cutting action of the cutter during cutting. The cutting speed should be reduced to prevent the product from breaking.
Excessive Pollination:
It may be caused by the particle size of the input raw materials being too small, dust and not sufficiently plasticizing.
Problems During the Injection Process
Flow Lines:
It appears as a streak on the flowing solution. It occurs when the melt in the mold cavity is not pressurized correctly. Filling speed is also a factor in this situation. The solution may be drying the material, controlling the gas release from the mold, gradually increasing the injection speed, or increasing the mold temperature. The temperature of the material and / or mold should also be controlled.
Nozzle and sleeve temperatures should be increased. In some cases, it is also a problem arising from the mold design. Changing the gating entrances and widening the gutter entrances will create a solution. Insufficient ventilation also causes this error. Vent extractors should be clean and checked routinely. Filling speed is important for elimination of boiling lines. Filling as fast as possible introduces as much melt as possible into the mold cavity. The higher the melt of the material during filling, the less risk of encountering this error.
Distortions:
It is when the density of the parts is lower than the standards. Extremely dry material usage, barrel temperatures and mold temperatures may also be factors. It occurs when the physical density of the molded part is considerably less than what was previously made. Over drying of the material is also a cause of this error. Leaving the material too long to dry (for example, a few days at the highest temperature) causes this error. It is caused by the overheating of the heaters in hot runner molds and by the very different heat given to the material during melting in cold runner molds. Check the melting temperature and the heaters of the machine or mold.
Burrs:
With the mold closing, the pressure is not enough or the injection pressure is greater than the mold closing pressure.
The excess melt filling the mold causes this overflow, as the injection process is more than the molding cycle process.
Decreasing the injection pressure and speed and increasing the closing pressure are the first steps to be taken.
The nozzle, barrel and mold temperatures may also need to be lowered. You can also reduce the speed of the screw to fix the problem. If a proper loading control is not carried out, the mold cavity can be filled with excess material, which can cause this error to occur.
It should inject the same volume of material into the mold by making the same advance and tension in each cycle of the screw.
Silver Traces:
It is in the form of traces that shine like silver on the surface of the piece. The polymeric material may have overheated. The condensed gas is trapped in the mold surface. Also, the cooling cycle time is not an appropriate time. Checking the equipment of the refrigeration cycle
must. Its equipment should be controlled for steady flow and constant cooling temperature. Using the mixture as soon as it arrives at the manufacturing area may also cause this error. Before the mixture is used in the manufacturing area, it should be waited for at least 8 hours. Thus, the temperature of the material will approach the ambient temperature.
Bubbles:
It is the formation of small air / gas bubbles on the surface of the part.
Good vacuuming or not enough air / gas evacuation process is the factor. In addition, the fact that the raw material used is wet and moist increases the formation of air / gas. If the material stored in a cold storage or silo is processed in a hot or warm pressing environment without allowing moisture to evaporate, evaporating water bubbles may cause bubbles in the material.
For this reason, the material should be dried thoroughly, or kept dry and allowed to come to ambient temperature before entering the production.
Adhesions to the Mold: When the mold is opened, the suction in the mold cavity is not finished and the part is pulled and stuck on the side where there are no pushers. Part sticking to the mold can also be due to excessive holding pressure. Also, the piece is still very hot. The mold needs a little more cooling. Or the cooling cycle process can be increased. Finally, there is an inconvenience in mold design. Conical angles may need to be widened. If it is a problem that occurs only in certain material uses, actions such as instant mold release depending on the type of polymeric material can be taken. In addition, controlling the temperature of the cooling water, reducing the temperature of the mold, cleaning the injection parts will provide solutions.
Stratifications:
The piece looks as if it was printed from separate layers, and these layers easily cause detachment and separation. When the injection speed is low or the mold is extremely cold, the material entering the mold starts to freeze very quickly. The melt coming from behind breaks its ties with the frozen layers. Generally, in slow fillings, molten cold layers are formed on the part. It is mostly PE and PP based as general purpose colorants. Most of the time, these colorants cannot adapt to the colorless mixture. Excessive mold spray can cause this error. As soon as the material enters the mold, it almost freezes. As more material enters, it freezes as a non-coalescing layer, just as the other froze. Increasing the injection speed will end this problem.
Curl, Warp:
It is when the finished part is out of the desired part mold shape. The geometry of the part is distorted due to the internal stress of the part. This problem may occur in molds with an irregular gating entrance design, gating entrance geometry, designs with high stresses and defective or insufficient gating entrance locations. As the cooling time increases, the stresses in the part begin to quench.
If increasing the melt and mold temperature and decreasing the injection speed do not give any results, the compatibility of the injection time and the mold filling time should be checked in case the part is too compressed.
Orangeization:
It is a state of indentation and protrusion on the surface of the piece, like an orange peel. Also known as «micro pitting». The first surface formed on the part is the error caused by being pushed by the high amount of viscous material and its rapid wrinkling. The melt temperature and runner temperature are low. There are losses in injection pressure, the melt does not enter quickly enough for the mold. We need to apply higher pressure to achieve the same filling speed with cold material. The melt temperature of the material must be controlled. With the restricted path, the melt temperature should be increased slowly. The mold temperature must also be increased to compensate for the pressure losses in the head during filling. It should be checked whether the speed is sufficient for the mold.
Bad smell:
It is caused by the burning material. In particular, it would be appropriate to reduce the head and breast area temperatures.
Make sure the material is dry. It may result in lowering the holding pressure. Setting the melting temperature to the lowest level will prevent combustion of additives with low process temperatures in the polymer.
Poor Color Distribution:
The melt is not mixed homogeneously in the barrel. The color concentration is not well distributed throughout the part. Different color distributions can be observed on the top of the part. The main cause of the error; The color concentration is not completely homogeneously mixed when the melt is in the screw. The whole melting and mixing process takes place by the rotation of the screw. The increment in mixing can only be achieved by conventional
It happens by using screws and decreasing barrel temperatures and increasing back pressure. This material, the more it melts, the more the screw
indicates that much mechanical action should be given.
Wolf Traces:
When the mold is placed on the part, it is seen as traces formed during the first printing.
In mold making, it is good to fill the mold as quickly as possible, but this quickness must be ensured by a properly sized runner insert. Since the speed of the material in the runner entrance is extremely high, the flow is very fast when entering the mold cavity. As the melt rapidly enters the mold cavity, it sprays around, left and right, in the cavity, unstable. To prevent this, it must create a resistance across the jet stream. This is also about mold design.
Dulling:
It occurs in the form of fingerprints on the part. Since the mold surface is not solid or clean, heat treatment affects the material with different nuances. The root cause of the error is usually a cold slug or part of a colder material.
is that it is injected into it. In some cases, there is an excessive amount of lubricant and lubricant in the material and these spread out to the mold surface. If the mold surface is not uniform, then the melt temperature should be lowered and the cleanliness of the problematic surface should be checked. The factors that will prevent the transition of the nozzle and runner nozzle bushing should be eliminated. Nozzle
and the runner nozzle bushing must match each other exactly. If there is any other situation, there will be an error in the flow.
Nipple / Head Occlusion:
When material is injected into the mold, it is seen as the dilute, molten material freezing at the mold entrance. The polymeric material used can be moist. It is beneficial to add a vacuum unit to the air ducts (valve). It may also be necessary to increase the holding pressure.
Deteriorations in the Runner Entry:
It is the fault seen in the area near the runner. Micro jetting has occurred just around the runner entrance. Mold surfaces may need to be polished. Runner channels may be narrow or too deep.
This error is usually encountered in fillings using fiber glass and mica because they are too abrasive.
The change to be made in the mold is to make the runners wide but not deep.
Drooling:
They are filamentous pieces that look like wires and elongate when the mold is opened. For this reason, this problem is also called "wiring".
This also happens when the thick but slow flow of material flows slowly through the sprue bushing. The main cause of the error is that the pressure of the plastic in the barrel is not effectively removed. Excessive injection pressure, deterioration in runners may be a factor. Many equipment manufacturers have placed the reverse toper nozzle on the molding machine to prevent this. These are specially designed to prevent drooling. In molds with hot runner channels opened, if the channels are not working properly, this may cause swaying and stringing. Stranding can be controlled up to a certain point with no drool nozzles.
Melt decompression can often be adjusted by retracting the screw over time. Increasing the decompression time will reduce the number of strands.
Black Spots:
The most obvious reason is from the use of dirty raw materials. If there is a color masterbatch in the material to be used, the unsuitable Masterbatch carrier may also cause burning during the extrusion process.
Continuous Incorrect Printing:
In general, it shows itself mostly in semi-automatic machines by printing either missing or dimensionally incorrect parts. The root cause of the error is the lack of a constant filling speed and the melt viscosity changes. Failure of leaking check valves due to the filling of the back of the screw causes the injection pressure to fluctuate. Valves should be checked and replaced if necessary. In addition, although the screw rotates, there may be cases of not taking the material for the next print, or taking half. There may be blockages in the feeding, throat area. If using a vacuum loader, this loader may have a deviation of its sensors, caliber. In other words, there is a malfunction in the system's feeder system. All equipment should be checked.
Burns:
It is in the form of colored spots seen on the piece. Stains
It occurs due to combustion somewhere in it. Operating temperatures or a burnt piece on the head may cause this. Old screw, barreled machines can cause this type of error in the part. Because if there is enough burnt part waste in the machine to be considered, these may cause this type of error in the part. The only solution to prevent this is the
find and clean the component. Stains are caused by burning somewhere in the process. Overheating of the heater bands causes this error. We need to check the heat control devices that are constantly in control. Material change can also cause this error. Overheating and burning of the material may occur due to excessive speed increases at the runner entrance.
Air or gas is also trapped in the mold, heating and burning the material. Usually it also damages the mold. Hot air or gas overheats the material, which causes burns. There is no or poorly constructed or not properly cleaned emitter. This error may also be due to excessive closing force.
The ejectors of the mold closing with excessive force may remain dysfunctional. The gas is compressed and stays inside and causes combustion by overheating due to compression. Prevention of burns is by good ventilation, that is, cleaning and working of the extractors.
Vacuum Deformation:
It is the change that the vacuuming in the robotic units gives to the shape of the part during the removal of the part from the mold. During unloading, it manifests itself in the deformation of the part with the vacuum that occurs at the first moment.
The unsuitable cooling cycle time is the biggest factor. In addition, if the air pressure on the propellant side is too low for the part, the vacuum intensity will increase. This error is caused by the refrigeration cycle not working properly, clogged, not operated, or running without output (ie blindly).
To prevent this, it is necessary to check if everything is in order before running the refrigeration cycle. If the ventilation is increased, this error can be prevented.
Runner Adhesion:
In the cycle, during the mold opening, the runner separates from the gating system, breaks and remains stuck to the mold. The biggest factor in this is that the gating connection points are not deep. The fact that the part is too hot also causes adhesions. Reducing the nozzle and barrel temperatures or mold temperatures, or extending the cooling time will provide a solution.
Conical angles may need to be increased on the mold design. The use of mold release agents will also prevent this situation. Make a deep runner nozzle construction, or put a more effective runner nozzle hammer, or finally, a heated runner nozzle.
should use. If the nozzle temperature is too low, rupture may still occur during mold opening. To prevent this, the nozzle temperature should be increased, thus preventing cold slug and rupture.
Problems Experienced in the Blow Molding Process
Blowing Problem:
Check the resin composition. Slightly increase the rear barrel temperature to avoid bridging gaps in the extruder feed section. Repair die edges and pinches to prevent punctures from damaged dies. Filling pressure may be too low. To prevent air entrapment, increase the packing pressure until it is filled. Mold closing speed can be very fast. Reduce die closing speed to avoid poor weld formation, Pinch may be too sharp or too hot. Increase the width of the land so as not to reduce the parchment area. Increase cooling in the jam area. Decrease the temperature of the cylinder / head. Reduce the number of cycles
Bubbles / Bubbles:
There is moisture in the resin. If misting occurs, reduce cooling at the feed throat.
Check the resin moisture and make sure the resin transport system is waterproof. Slightly increase the rear barrel temperature. To prevent air entrapment, increase the packing pressure until it is filled.
Pollution:
Keep the hopper clean at all times. Install filters on the dust air inlets and clean them regularly. Dirt on the resin may be caused by burns, shorten the extrusion time or adjust the temperatures, make sure the melt flow paths are clean.
Irregular Parison Volume:
The irregular volume results from the uneven weight flow. This also affects the irregular parison size. The weight is not always equal in every cycle process. The source of the problem should be clarified by checking the parison weights periodically. Check the compatibility of the weights with the mold volume. Cycle time irregularities and temperature fluctuations can affect the amount of material. Pressure settings must be appropriate to ensure full contact. Due to poor parison, mold contact looseness, no clean mold holes. Extruder profile temperature leads to higher melt temperature, which leads to higher parisoning. Mold temperature is also a source of this problem. The cooling mechanism and its temperatures should be reviewed. There may be a problem due to the annealing conditions. Work at higher temperatures and slower speeds. Decrease cylinder temperature. Increase head / mold temperature. Clean the mold / head. Check for worn thrust bearing and centering bushes.
Neck Curvature:
The intumescent parison resulted in incorrect cutting. The nozzle alignment may be out of order or damaged. Make sure the spray pin is central. Patterns may be misaligned. Check die pins and bushings.
Sag:
Incorrect mold adjustment is due. The off-center pressure ring is not centered. Check head and manifold heaters.
It is also important to clean the air ducts and the mold cavity.
Inequality in Pipe Length:
In the final point it is the physical problem. First of all, check if the saw blade is stretched. Choose thicker, larger blades. The saw arm may enter the pipe too quickly, sometimes slower. Make sure the cycle runs stably. The saw arm may be worn, turned into a burr surface. There may be wear or looseness in the slip rings.
The fact that the pulling or cutting car does not always move at an equal speed is a factor in this situation. Make sure that the draw speed is always running at the same speed. To increase efficiency. Apart from the operating values, the working pace may be above the saw pipe cutting capacity.
Wall Thickness Irregularity:
Irregular melt removed from the mold, unbalanced take-off speed, misalignment of the mold and pulling units, misalignment or distortion of the scale, the mold and the pin not centering each other equally, and even the gap that may occur in the mold causes the irregularity in the pipe walls. If the melt pump is used, it should be verified that the pump speed is stable, and then it should be determined whether there is any wear and tear on the gears inside.
In the case of multilayer tubing, you may have encountered incorrect polymer matching. There should not be a big difference between the viscosity values of the polymers preferred in the co-extruded process. Otherwise; There will be differences in the thickness of the layers. In this case, while the thickness of one layer is decreasing, it is not clear that the other layer will fill this decreasing space.
While the thickness of one layer decreases, the other layer can remain stable. In this case, the uneven wall thickness in the whole section size will be the root cause. Changing the temperature profile of the melt from the two polymers can be a solution. However, the most accurate approach should be the choice of raw materials whose MFI values can be compatible with each other. The pressure that is not uniformly distributed over time in Co-Extrusion will also adversely affect the thickness distribution as it will directly affect the amount of melt flowing. Although it is thought that it will pass through the same mold and the thickness will be the same, the melt distribution will not be stable in the layers section. it will lead to uneven progression of thickness. In this context, it must be ensured that all extruders in the Co-Extrusion unit are operating at constant pressure.
To reduce the problems that may occur over time during the usage process:
The piping system should be as short and direct as possible. Sharp and multiple bends should be avoided. The bends should be gentle and of large diameter, ideally 10 x the hose number.
“Y” joints should be used and “T” joints should be avoided as much as possible.
The suction-side pipe run should never be of low size (the minimum bore should be equal to the inside diameter of the hose).
It will be beneficial to install expansion joints in the piping system to reduce vibratory flow effects in the pipeline.
When flexible hose connections are used, it must be ensured that the hose is constructed with a suitable elastometer and that the system is sufficiently suitable for the maximum suction and discharge pressure. For ease of part replacement, removable flexible parts should be used at the initial and final points, if possible.
Depressions:
It can be seen as a kind of incomplete pressure, but the more holding pressure (incorrectly called ironing pressure) is insufficient. The outer walls of the part are solid. But by separating some molecules in the inner structure of the part, gaps were formed. Sections that are too thick than necessary, narrow passages or transitions that cause sudden expansion will also cause depressions.
Increasing the back pressure, increasing the injection pressure, increasing the holding pressure and time would be the solution.
It should not be forgotten that as the plastic cools down, it will shrink inside the mold cavity. The holding pressure should be controlled in order to fill the mold cavity well and completely and to meet these shrinkage. Insufficient pressure causes gaps. Since the plastic will shrink as it cools, it must be pre -ified in order for the mold to take its full shape.
This compensates for shrinkage in tension. Therefore, sufficient holding pressure must be applied to the part.
Missing Prints:
It is the state of the molten material not filling the mold cavity completely. Injection pressure, injection cycle process is insufficient. It may be necessary to control the degassing unit outlets in the mold.
Moisture also causes incomplete printing, voids. Dry the material. If you are using a dehumidifying auger, check what prevents dehumidification. Ventilation ducts may need to be supplemented with auxiliary vacuum. Increase the holding pressure.
Changing the sprue entry points may yield results in case of irregular mold filling. At the same time, it must be ensured that the mold temperature does not change.
This problem is also related to the amount of material injected. Increasing the amount of material injected and melt cushioning is the solution.
One of the reasons for missing prints is due to the mold design. There may be blockage in the runner entrances. Check the obstruction of the ventilation ducts, the correctness of their location. If necessary, additional vacuum can be added to the ventilation ducts.
If a proper feed check is not carried out, parts may be missing from overfilling the mold cavity. The screw has to press the same rotation for each cycle, that is, the same volume of material. It is a factor that causes short pressure in the design of the part. Sharp transitions and narrow sections should be avoided. Many times the mold cannot be adjusted to the size of the press. The closing tonnage should be carefully adjusted.
Pusher Traces:
It is seen as the rods that push the part from the sleeve leave a mark on the part. The temperature of the part or the force of the pushing rods must be adjusted. The fact that the rods hit the part too fast or their diameters are too small is the factor in this situation.
This error can be eliminated by balancing the temperature of the part and the forces of the push rods.
This error also occurs if the plate (push plate) to which the pushing rods are attached hits and drops the part too quickly. The solution is of course by reducing the speed of the pusher plate. If the mold has undergone various modifications to prevent sticking to the mold, this
If the part remains on the pusher side at a time, then the pusher rods may leave marks on the part. If larger diameter pushing rods are used to prevent this, since the force per unit area will decrease, the possibility of leaving a trace is also reduced.
Problems Experienced in the Pipe and Profile Production Process
Hard Surface:
It can be inside or outside. Raw material is not dry. Make sure it dries at 70-90 ° C for an hour or two. There is not enough water flow to the calibrator. Low melt temperature also causes this problem. Extruder or mold temperatures should be raised.
Deformity:
It has a very high melting temperature. Review extruder and die temperatures. Also, this problem can occur if there is excessive extruder screw speed. Slightly lower the yield. Depending on the yield, the molds can be small. If the pin is too hot, thermal degradation images will occur on the surface. Make sure the pin cooling unit is working properly. It can also be caused by physical problems with deformities.
Check mold dimensions for concentricity. Make sure it is 3%, 5% larger than the final pipe diameter.
The pipe is very hot when it reaches the withdrawal unit. Provide sufficient cooling flow in advance. It can flow to the drawing unit with high efficiency. Extrusion speed should be reduced and appropriate vacuum setting should be made in vacuum tanks.
Lines Forming on the Surface:
There may be lines originating from the head. Spike on head / die, check exit points. If necessary, use a gentle filing method of cleaning. Burnt, sticky melt in the head can also cause streaks. Check temperatures in the direction of die exit.
Drop Traces:
Very fast pulling force is applied. Check and adjust the drawing speed. The high material temperature at the mold entrance is also a factor. Check the water flow.
Extruder Errors:
Trying to get very high extruder efficiency.Check the extruder specifications and the guaranteed extruder output and
run the extruder within specification. It may be due to improper extruder temperature settings. Adjust the temperature setting according to the process values recommended by the raw material manufacturer you are using.
Gelling in the Tube:
It may contain foreign particles in the melt. The raw material you use, additives etc. you may need to get information from the supplier. Deteriorated resin that comes out of the mold during extrusion may also gel. You will need to check the extrude time, temperatures.
Stains Seen on the Surface:
Mold adjustment is not made properly. Thermal distribution on the mold profile surface may not be uniform. Make sure that homogeneity is achieved at mold temperature. Stains tend to show themselves after cooling baths, adjust the function of pulling, pushing, lowering. Irregular melt and trapped gases coming out of the mold are sources of stains. Make sure the vacuums are well balanced and positioned.
Sagging:
Too high melt temperature is the main cause of the sag problem. Review extruder temperature and extrusion time to lower melt temperature. The mold cavity may not be properly adjusted to sag. The natural resistance of the melt to sag is not sufficient for the pipe wall thickness. Use raw materials with low sag. Sufficient cooling cannot be provided in the lines. The cooling capacity can be increased or the time spent in the cooling baths should be extended.
Problems Experienced in Blown Film Production Process
Balloon Jump:
One of the possible reasons is low speed of work. The excessively high processing temperature is also a factor in this situation. Air circulation may be excessive in the working environment. Besides these; along the perimeter of the air ring opening
cooling air must be continuously blown at an equal rate. In addition, the position of the folding frames may require adjustment. The vibration that occurs during the working process in the extruder or tower may be affecting the balloon. Vibrations will need to be isolated. Finally, the suitability of the optimum inflation rate should be checked.
Wrinkled Film:
One of the most likely reasons is the defect of the balloon shape. For this, the film thickness should be homogeneous, the head temperature should be suitable for the melt polymer temperature, and the cooling ring should be clean and adjusted.
Head adjustment should be made so that the film thickness is equal. Head level adjustment should be checked. Clamping rolls
level adjustment should be made. Dirt may have accumulated on the balloon diameter limiting rollers or beads.
In case of unstable balloon situation, external mechanical bracing may be required. Finally, the tension of the winding rolls should be controlled.
Blowing Problems:
Make sure the material is dry. If recycled material is used, make sure it is clean. Increase or decrease the back pressure according to the content of inflation problem. Increase the thickness of the formwork wall (re-adjust the head).
Non-melting Particles:
The raw material may be dirty or unsuitable for the process. Burnt chips may also be sticking to the film surface if the processing temperature is too high. Temperatures need to be controlled.
Or one of the first applications, the filter, the strainer is full and extremely dirty. It should be checked whether there is any tear or hole in the strainer wire. The mesh pores are large, replace it with a thinner wire. Burnt particles may have accumulated on the head between the lips, head cleaning will be required. If the extruder has been idle for a long time, the melt inside may have burnt and stuck to the screw. If necessary, the entire screw should be removed and cleaned. If there is a masterbatch used in the formula, recipe, it may be necessary to reevaluate the mixture is well made and the compatibility of the working values. The first process may be the wrong production line choice, taking the process into the production line with screw with better mixing properties will help solve the problem.
Rigid Film Surface:
Increasing the head / die temperature of the cylinder temperatures is to remove the surface hardness. It may also be necessary to reduce the extrusion speed and temperatures on the feed side. Increasing the mold temperature and using high compression screws also provide a solution to the hard surface problem.
Poor Tear Strength:
It may be necessary to increase the inflation rate. One of the reasons for tearing is that there are streaks on the film surface. For this, it may be necessary to clean the head lips of the extruder and take a look at the applications regarding the non-melting particle problem. The fact that the freezing line is too low also affects the tear strength.
Balloon Burst:
It may be caused by dirty raw materials. This situation triggers the problem of non-melting particles. The solutions related to this will also be a solution to bubble burst. It may be necessary to remove the screw, remove the head, and clean all parts.
Avalanche Formation in the Movie Century:
First of all, it should be seen whether the lines are mechanically effective physical or melt-sourced chemical and the solution should be sought in this direction. The main reason for the physical lines is the dirt accumulated on the head or rollers. The sharp, hard ends of the mechanical parts that come into contact with the film may create lines due to friction effect. Actions such as sanding, compression, crack removal may be required. Your head pressure may be high. Reducing the screw speed and increasing operating temperatures is the solution for chemical formations.
Poor Thermal Adhesion:
The unsuitable thermal bonding conditions may be a factor. For this, the melting point of the raw material should be controlled and it may be necessary to increase the bonding temperature as the bonding time decreases. There may also be unsuitability in the storage conditions of wound bobbins. The film surface may be dusty, damp. The most important point is that its surface corona tension is low. Whether it is a corona or not, the intensity of the corona must be measured.
Disorder of Optical Properties:
The main reason lies in the choice of faulty raw materials. Low process temperatures and insufficient balloon cooling also cause optical deterioration. Increasing the temperatures, lowering the freezing line, cooling the balloon with colder air will provide a solution.
Problems Experienced in Flexo Printing Process
Back-to-Back in Printing:
Printing before the ink film is completely dry, the presence of solvent residues on the printed material, and the tight application of the bobbin winding cause printing marks on the back of the film. In both side treated films, the printed surface is in contact with the other surface. Accelerator solvent usage may be required. Drying temperatures and air flows between the units should be checked. Coil winding pressure should be reduced, reducing the transferred ink film thickness,
The use of anti-blocking varnish will be the solution to the problem.
Scratch Creation on Printing:
Foreign particles that should not be on the scraper squeegee blade cause this. The scraper blade needs to be cleaned or replaced. In addition, blade settings should be checked. The suitability of anilox roll hardness should be reviewed.
Excessive Anilox Wear:
Excessive pressure on the scraper squeegee blade will wear out the anilox rollers. Find out the reasons for the need for excessive pressure and take precautions. The filling materials coming from the ink cause the tip of the blade to wear out. Excessive pressure on the anilox as a result of increasing the blade pressure settings, even if the worn blade tip fails to function.
It causes wear as it will occur. It is necessary to check the condition and angle of the blades of all colors.
Tram Disorder:
The tram points elongate in the direction of the print, from round to oval
It is the case that it becomes a fish eye. It is related to the printing plate height or the thickness of the double-sided adhesive tape used. For this reason, the correct forse setting cannot be made. There is a difference in cylinder diameter between the cliché boiler and the printing boiler. The total height of the cliché (cliché + adhesive tape) should be checked and it should be ensured that it has the desired thickness. Print force settings should be checked again. Forse adjustment strips, doubling and slip guides should be used to find the optimum force setting while performing pressure tests. In flexo printing units, the cylinders are generally interconnected with gears. The gear radii determine the rotation speed of the cylinder and the plate surface speed on the mold cylinder together with the counter pressure cylinder, the total thickness of the printing plate is determined by the toothed radii of the printing cylinder and the plate cylinder. If the plate height is higher than it should be, the circumferential relief surface of the plate (pressing parts) becomes larger than the printing cylinder radius. In this case, since the harmony between the two cylinders will be disrupted, a pressure forse adjustment with the desired precision is not made. In this case, the screen structure of the round point that makes the printing deteriorates and turns into an oval shape. This causes screen soiling in the print, which degrades the image quality.
Cliches in Printing:
If the cliches soften and become sticky shortly after the start of the printing, the problem arises from the insufficient polymerization of the cliché after the back pose, main pose, and final pose. The cliché was not saturated, the power of the lamps decreased, the vacuum foil was very dirty or the yellowed foil prevented the exposure. Exposure times should be checked again. The old lamps should be replaced by checking the exposure lamps. All lamps need to be changed at the same time. The vacuum foil must be renewed. If the problem is cracks on the plate printing surface, the ozone rate may be too high. Solvents and cleaning agents used can be very aggressive. You may be using the outdated cliché. He's doing the last edition now. If it is stored in a bright environment and not cleaned well on the sleeve after printing, it expires quickly. Therefore, there should be no solvent waste left on the cleaned plate. Cliches should be stored in a way that protects them from light after printing. Plates should be kept in straight position as much as possible.
The Darker Pressure:
From the very beginning of the print, the texts are swollen
and intermediate depths manifest as closed. The use of anilox, which transfers excessive ink, is the cause.
The mixing ratio of ink and thinners may be incorrect. Ink normal work
It may not have the correct viscosity.
Cliches were erected incorrectly, and there was an air gap under the cliché tape. Therefore, excessive pressure is put on the anilox and plate cylinder. Even if the printing forse adjustment is normal, there is excessive pressure on the cliché due to the difference in thickness on the surface of the cliché.
In addition, exposure errors during plate making, lack of vacuum, negative film
Lack of sufficient density may cause this problem by affecting the cliché quality.
If there are renewed ones among the cliché sets, using both the new part and the old part in the same print may also cause this problem. It is important for the continuity of the printing quality to perform the renewal work in multi-colored plates as a set.
Ink Splatter:
It is the state of ink splashing on the non-printing parts (intermediate pleasures) of the cliché during printing.
The main reason is that too much ink has been transferred on the cliché. In addition, the force adjustment of the anilox roller is also a factor in this. The ink transfer amount of Anilox should be checked. Anilox should be changed if necessary. In addition, the anilox roller should be checked against the force.
Barcode Print Not Reading:
Or there may be many reasons why barcode printing quality cannot be obtained at the desired quality. Barcode printing carries more important values than the printing pattern on the product. The main reasons for this problem are; It is caused by too much force.
The barcode color may have been selected incorrectly. Barcode sticks are delicate. Total length may be reduced more than normal. There is not enough contrast between the barcode color and the print background color. The border or ground that limits the barcode may be too close to the barcode bars. The direction of the barcode may be wrong. Barcode verifiers therefore do not read correctly and it can be concluded that the print is not read. Barcode bars may have poor resolution. Low resolution results in jagged rather than sharp and linear bar lines, causing the barcode straightener to read inaccurately.
Flagging:
The material to be printed is mostly in the form of ripples seen on the edges. It is caused by the tension of the material on the printing machine not being adjusted. The fact that excessive heat is applied according to the feature of the printing material is also a factor in the flagging. Coil guides may be out of adjustment or not functioning. Machine blood pressure settings need to be checked again. It is recommended to slightly lower the pre-drying temperatures on the bobbin. In addition, the cleanliness of the bobbin guides should be checked.
The waviness of the scraper squeegee blades also affects the homogeneous ink transfer to the film surface. This causes a flagging appearance by making the effect of darkness, amorousness in the print.
Bleeding, Color Mixing:
It is when a color is mixed with another color.
The first color transferred to the printing material does not dry out. Ink viscosity is high, ink is very concise and thick. Solvent selection is wrong. Solvent balances are bad. First, check and adjust the drying and let the first printed color dry. Check the viscosity of the ink and continue checks during the entire printing process. Review solvent usage rates.
Blocking:
In material winding, the layers stick together on the bobbin and show itself. The main reason can be seen that the winding pressures are high, but the ink that does not dry enough also causes this adhesion. Ink dries slowly, which is mainly due to either low drying temperatures or very high speeds. If the moisture content of the printing surface is higher than acceptable, it does not dry up to the winding rollers and causes blocking during wrapping.
Filling:
Ink accumulates on the surface of the cliché, and the screens in fine text and pictures
It is the state of stuffing. There may be pigment residues and foreign matter in the ink. If the cliché making is not wrong, the particles crumbled by the plucking effect blocked the screens. Ink viscosity is very high forse. Check anilox and blade pressure.
Problems Experienced in Nonwoven Non-Woven Fabric Production Process
Fiber drop :
Stone dust is trapped in the die head of the extruder, which causes the thread not to enter a stream, resulting in uneven thread output and thread drop. An easy way to fix this problem is to clean the extruder die and make sure to prevent it from happening next time.
Filter mesh clogging :
This causes uneven yarn pressure and yarn dropout. Manufacturers can find a suitable solution by cleaning the filter mesh and finding out what is causing the mesh. The slow MFI of the calcium carbonate filler leads to unstable flow. MFI is a vital index that determines the efficiency of the production process. To fix this, manufacturers may need to make some adjustments to the extruder's temperature. However, in the long run, it is recommended to renew the filler formulation for better MFI.
Machine parameters are not suitable for production materials. In this case, the only way is to set the machine parameters.
Fiber too soft or too hard :
When it comes to the mechanical properties of the final products, the main reason lies in the formula of the calcium carbonate filler in the non-woven fabric. A large amount of filler masterbatch may result in a lack of stiffness of the fabric, while the rough surfaces of the final products are mainly due to the absence of some additive groups.
Weak mechanical properties :
The main reasons for this problem may be the incompatibility between the type of calcium carbonate filler used in the non-woven fabric and the oversized stone dust particle that causes poor adhesion strength of the fabric. Therefore, manufacturers should recheck the filler masterbatch formula to ensure that it best matches their final product.