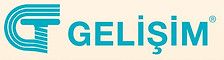


Hydrocarbons
It is an organic compound consisting of two elements, hydrogen and carbon. Most of the petroleum composition consists of hydrocarbons of varying lengths.
The smallest hydrocarbon methane consists of a single carbon atom and four hydrogen atoms. However, hydrocarbons can consist of hundreds or thousands of individual atoms linked together in many ways, including chains, circles, and other complex shapes.
In order to classify the properties of hydrocarbons, they are divided into several basic types.
Alkanes: These are called saturated hydrocarbons. That is, they only contain single bonds between all carbon atoms. Alkanes are the basis of petroleum fuels and exist in linear and branched forms.
Unsaturated Hydrocarbons: Hydrocarbons that have one or more double bonds between carbon atoms are called alkenes.
Cycloalkanes: Any hydrocarbon containing one or more ring structures.
Aromatic Hydrocarbons: Aromatic hydrocarbons , also called arenes, are a unique class of carbon molecules in which carbon atoms are bonded by successive double and single bonds. This class of molecules has special ring structures in which the bonds between carbon atoms are an intermediate bond between single and double bonds.
Molecules in this class contain the industrial solvent "benzene".
Benzene (C6H6): Like other hydrocarbons, benzene is a natural component of petroleum. It is a colorless, flammable, sweet-smelling liquid at room temperature and is a component of most gasoline blends because of its high octane number.
Benzene is also highly carcinogenic and is well known to cause bone marrow failure and bone cancer. Of course, its carcinogenicity is not well known when used as an additive in aftershave and other cosmetics due to its "pleasant aroma".
The largest use of benzene (50%) is the product of styrene and polystyrene plastics. It is also converted into a molecule known as cyclohexane, which is important in Nylon production. About 15% of benzene is used to produce cyclohexane. Smaller amounts are used in everything from pesticides to rubber.
The benzene structure can be drawn in two ways. In the first, the double bond character is drawn explicitly. In the short handed version, a circle is drawn inside the ring to show the structure. There is only one hydrogen bonded to each carbon atom in benzene.
I. and II below. drawings are identical. III in practice. drawing is used.
Benzene is a colorless, flammable liquid with a boiling point of 80.1 ° C and a melting point of 5.5 ° C.
Binuclear Aromatic Hydrocarbons: They are compounds that contain two benzene rings in their molecules.
Hydrocarbons
It is an organic compound consisting of two elements, hydrogen and carbon. Most of the petroleum composition consists of hydrocarbons of varying lengths.
The smallest hydrocarbon methane consists of a single carbon atom and four hydrogen atoms. However, hydrocarbons can consist of hundreds or thousands of individual atoms linked together in many ways, including chains, circles, and other complex shapes.
In order to classify the properties of hydrocarbons, they are divided into several basic types.
Alkanes: These are called saturated hydrocarbons. That is, they only contain single bonds between all carbon atoms. Alkanes are the basis of petroleum fuels and exist in linear and branched forms.
Unsaturated Hydrocarbons: Hydrocarbons that have one or more double bonds between carbon atoms are called alkenes.
Cycloalkanes: Any hydrocarbon containing one or more ring structures.
Aromatic Hydrocarbons: Aromatic hydrocarbons , also called arenes, are a unique class of carbon molecules in which carbon atoms are bonded by successive double and single bonds. This class of molecules has special ring structures in which the bonds between carbon atoms are an intermediate bond between single and double bonds.
Molecules in this class contain the industrial solvent "benzene".
Benzene (C6H6): Like other hydrocarbons, benzene is a natural component of petroleum. It is a colorless, flammable, sweet-smelling liquid at room temperature and is a component of most gasoline blends because of its high octane number.
Benzene is also highly carcinogenic and is well known to cause bone marrow failure and bone cancer. Of course, its carcinogenicity is not well known when used as an additive in aftershave and other cosmetics due to its "pleasant aroma".
The largest use of benzene (50%) is the product of styrene and polystyrene plastics. It is also converted into a molecule known as cyclohexane, which is important in Nylon production. About 15% of benzene is used to produce cyclohexane. Smaller amounts are used in everything from pesticides to rubber.
The benzene structure can be drawn in two ways. In the first, the double bond character is drawn explicitly. In the short handed version, a circle is drawn inside the ring to show the structure. There is only one hydrogen bonded to each carbon atom in benzene.
I. and II below. drawings are identical. III in practice. drawing is used.
Benzene is a colorless, flammable liquid with a boiling point of 80.1 ° C and a melting point of 5.5 ° C.
Binuclear Aromatic Hydrocarbons: They are compounds that contain two benzene rings in their molecules.
About
Kyäni, nutritional supplement products consisting of beneficial ingredients; It delivers to more than 50 countries around the world with unique business opportunities. We use Kyäni products daily to maintain our ideal health, share these products with others, devote a certain amount of time to work almost every day to build and maintain our business, and share our success with others by involving others in the Kyäni opportunity or contributing to the Potato Pak and Caring Hands programs.
About
Kyäni, nutritional supplement products consisting of beneficial ingredients; It delivers to more than 50 countries around the world with unique business opportunities. We use Kyäni products daily to maintain our ideal health, share these products with others, devote a certain amount of time to work almost every day to build and maintain our business, and share our success with others by involving others in the Kyäni opportunity or contributing to the Potato Pak and Caring Hands programs.
Page Under Construction.
Page Under Construction.
Training / Knowledge / Solution Platform
Preliminary information
With the feasibility studies, measurements were made in the field where there is possible oil. By going down to various depths, the volume of the oil deposit was determined by sonar and probe studies. By moving away from the central reference point, after sonar and drilling studies, the size of the oil field and the measurement of the reserve, the return of the reserve, the working process, and the monetary return of the business, it was decided whether the oil was worth extracting.
All these are preliminary assessments that must be taken before the oil that lies beneath the ground/sea can be unearthed. In other words, the existence of oil in a field and its discovery does not mean that that oil can be extracted. The most important decision argument in the oil extraction business is whether it will cover the costs. From the depth of the underground oil, the amount of the reserve, the quality of the oil, the transportation of the oil from the drilling point to the refineries, which require very high costs, are taken into account.
Today, it is likely that there will be oil fields on the territory of many countries. This includes Turkey. However, as stated, whether this oil deposit is worth uncovering is more about the costs of the work. It is a process that requires money from beginning to end, especially from owning oil drilling platforms to leasing them from oil companies.
As it will be remembered, in 2020, the President of Turkey heralded the discovery of a natural gas deposit in the western Black Sea, declared that this natural gas reserve is 320 billion cubic meters and stated that it will be put into use in 2023. It can be seen that Turkey, which has never worked in this field before, is a little far from the seriousness of the job, considering the lack of reserve determination with a single sonar assessment, transportation, transportation, storage facilities before the drilling of the potential reserve, and technical personnel shortage in addition to all these technical equipment. . The work of unearthing fossil fuels, for which World War II was risked and even conventional wars were fought, is a much more serious issue than the statements of the President of Turkey.
The only way followed in countries such as Turkey, which does not have sufficient infrastructure for this business, cannot go beyond tendering the work of extracting the reserves to world companies. In this case, too, the country with the reserve cannot go beyond just getting a share. This does not exceed approximately 20% - 30% of the extracted resource.
The fossil energy source that is somehow unearthed is literally in its raw form. This crude oil needs to be refined to become a usable, purpose-built material today. For this reason, Turkey's only relevant institution is Petkim, which was sold to Azerbaijan Socar company under the name of privatization.
The crude oil brought to the refinery begins to be diluted and separated by a kind of distillation process called cracking, in the simplest terms possible. In this process, which includes many stages, materials that are used today and serve the purpose are started to be produced from each stage (polymers, solvents, flammable gases, heavy tars such as asphalt, polyolefins, polyesters, polystyrenes from sub-products).
Polyolefins: PE, PP, PB, EVA, EVOH
Polyesters: PET, PBT, PC, PTT, PEN
Polyamides: PA6, PA6.6, PA12, PPA
Halogenated polymers: PVC, PTFE, PVDF
Polyacrylates: PAN, PBA, PMA, PMMA
Polystyrenes: PS, ABS, SB, SBS, SAN
Polysulfides: PPS, PSU, PES, PPSU
Biopolymers: PLA, PEA, PVAL, PPOX
Polyether ketones: PAE, PEK, PEEK
Polyimides: PI, PBI, PEI, PBO, PMI
Polyurethanes: PUR, TPA, TPO, TPU, Spandex
Special polymers: LCP, POM, BR, NBR
The subject source polymers enter the packaging process, which may be final, before being placed on the consumer market. After this process, polymer raw materials; It can be in the form of granules or ground powder.
It can be in big-bag sacks for packaging, or it can be in 25 kilo bags generally. According to the facility structure of the user company, the shipment starts from the refinery area by silo-bass tankers, trucks, trains or ships.
Below, more detailed information about the said polymers can be summarized as follows;
LDPE (Low Densty PolyEthylene)
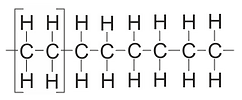
General Properties are high chemical resistance. It is a slippery material with a low coefficient of friction. Moisture absorption is close to zero. Polyethylene is divided into types within itself. The length of their molecules determining the species is their molecular weight. It is a softer and less rigid material compared to polypropylene and PVC. Molecular weight is what characterizes polyethylene.
(1) Low molecular weight (PE-300)
(2) High molecular weight (PE-500)
(3) It can be grouped into three groups as ultra molecular weight (PE-1000).
Especially, Polyethylene 1000 provides a significant economic efficiency with its high impact resistance, high wear resistance and low friction coefficient, which gives 3 times more life. Polyethylene 1000 can be used with a longer life in all chemical environments where it can be used. It resembles PTFE with its self-lubricating, slippery and non-stick properties. Even ice cannot hold on to polyethylene and slips. Especially in the production of flammable materials and in the mining industry, explosion and fire are the main dangers in all environments, especially underground. As the molecular weight increases, significant increases occur in abrasion resistance. Said abrasion resistance is the resistance that will occur when the plastic works by rubbing with a smooth metal surface. Operating Temperatures are between 90 and 150 ° C.
Food industry, truck and silo coating, conveyor chain slides
water tanks, meat cutting machines, paper, textile automotive industry
It is used in the fields.
Ethylene gas is first compressed up to 250-300 atmospheres in the pre-compressor and sent to the second compressor. Here the pressure is raised to 3 500 atmospheres. The pressure of the reactor depends on the design of the factory, the type of catalyst and the grade of the desired product. The compressed ethylene is polymerized in the tube reactor after preheating. Unreacted ethylene at the exit of the reactor is sent to two separators with medium and low pressure. This ethylene is recycled via a booster to the pre-separator and the second compressor. The resulting polyethylene is fed into an extruder; Here necessary additives are added and the final product is granulated. The polymerization rate is very high due to the type of reactor used. Expenses of auxiliary materials such as water, steam and electricity are low and operating flexibility is extraordinary. The quality of the product obtained is very good.
Catalysts in LDPE Process:
Polymerization can be initiated in a variety of ways; by catalysts, oxygen, thermally or radiation (radiation).
In the production of LDPE, mostly organic peroxides are used as free radical catalysts; these include peroxydicarbonates, hydroperoxides and long chain peroxides. In commercial production, the retention time in the reaction is 3-15 seconds.
In recent years, metallocene catalysts containing a single active end have been used in the production of polyolefins. Polymers produced with them differ from those obtained with other catalysts; Their molecular weight distribution is narrow, their impact resistance is high, their elastic return efficiency is high, and their optical properties are very good.
Key Parameters:
The main parameters affecting reaction rate, long chain branching (morphology) and molecular weight are pressure and temperature. The type and amount of initiator also affects the reaction rate and morphology. Oxygen and water are important impurities that can be found in the environment. Apart from these, methanol, ethane, acetylene, CO, CO2, H2, C3 and heavy hydrocarbons are impurities from the monomer. All impurities affect the radical polymerization and change the course of the reaction.
LDPE can be produced by the high pressure autoclave process and the high pressure tube process. The only difference in these two processes is the reactor type.
In the high pressure autoclave process, the reaction pressure is in the range of 150-200 MPa. The autoclave react cover volume is chosen such that the retention time can be 30-60 seconds. Autoclave is an adiabatic, continuous stirred-tank reactor.

There are two common processes used in low density polyethylene polymer production:
(1) Tubular Process
(2) It is Autoclave Process.
Both processes use free radical chemistry.
Low density polyethylene is produced by the polymerization process of ethylene at very high temperatures in a tubular reactor. In this tubular reactor, high pressure polymerization allows further copolymerization of ethylene with polar co-monomers.
Tubular process has an advantage over autoclave process. Tubular lines are more cost effective with less power consumption. Globally, the tubular process has a large share in low density polyethylene production technology.
Resins find their main use in the production of general purpose and high performance applications, including blown and cast film, extrusion and coating, film and sheets, rotational and injection molding, and other applications. Other typical applications of thermoplastics include consumer bags, liners, top wraps, lamination films, agricultural films, extrusion coatings, caps and caps, toys, and many other durable plastic products used in everyday life. They are even used in molded laboratory devices such as pipette washing equipment, bag, tank and general purpose pipe manufacturing.
LDPE Key Features:
Monomer is a resin made of ethylene. It is premium polyethylene produced by Imperial Chemical Industries (ICI) in 1933. The resin was produced using a very high pressure process called free radical polymerization. Even today, thermoplastics are produced in the same way. These resins are available in a wide range of flexibility depending on their manufacturing processes. Despite the high competition among polymers, it remains important as a good plastic quality in the market.
The global production capacity of polyethylene polymer is over 100 million tons. LDPE production capacity has a 20% share in global polyethylene production. 30% of the production areas are in Europe and Asia, and 20% are in North America.
LDPE thermoplastics offer a wide range of uses due to their properties that make them applicable to various products.
It is a high molecular weight polyolefin material. Like all other polyolefins, low density polyethylene is non-toxic, non-polluting and has a high quality fracture resistance. It is lighter than water, is chemically inert and does not dissolve at room temperature.
Overall, it has a milky-white translucent appearance with a combination of flexible material and unique flow properties that has proven its suitability for plastic film applications. Although resins have high ductility and generally have low tensile strength, they lose their strength and tear resistance when exposed to light and oxygen.
The product of these resins is widely used in different end segment industries such as construction, automotive, packaging and others. Polymers are preferred over other polyethylene qualities due to their different properties.
Resins have strength, hardness, and temperature resistance as well as chemicals, both of which make them applicable to produce a variety of goods in different segments. Products made of low density polyethylene are durable and used in our daily life, such as bags, toys, films, laboratory apparatus, toys, etc. Its use in plastic products can be easily described.
-
Resins can be rigid and flexible according to their usage demands.
-
It can be transparent or even translucent and have a waxy surface.
-
They are semi-hard, robust and waterproof.
-
They have a low melting point and also provide good moisture barrier properties.
-
These thermoplastics provide stable electrical properties and good chemical resistance
-
Plastics can be easily processed using low cost methods.
-
Tensile strength 0.20 - 0.40 N / mm 2 and impact strength no fracture
-
Thermal Expansion Coefficient 100 - 220 * 10.6
-
Max Cont Usage Temperature 65 ° C
-
Density 0.917 - 0.930 g / cm 3
-
Excellent resistance to dilute and concentrated acids, alkalis, alcohols, bases and esters
-
It offers good resistance to Oils and Greases, Aldehydes and Ketones.
-
Different types of hydrocarbons such as aliphatic hydrocarbons, Aromatic hydrocarbons and Halogenated hydrocarbons exhibit limited resistance to Oxidizing agents and mineral oils.
-
They have low specific gravity and high impact resistance.
-
It is resistant to strong chemicals and temperatures that increase the durability of the products.
-
It is highly water resistant against low density.
-
Plastics can be easily reused as a liner or shopping bag.
-
Resin can also be an energy source when burned to heat buildings.
-
It is resistant to breakage, which is useful in the production of long-lasting products.
-
For some products, they have poor heat resistance.
-
The high coefficient of thermal expansion provides a limitation in the production of low density polyethylene products.
-
Thermoplastics offer resistance to bad weather conditions.
-
Resins are often subject to stress cracking.
-
It is a kind of PE grade that has difficulty in adhering.
-
Plastics have dangerous environmental impacts, such as landfills destroying green spaces, and are made from non-renewable resources such as crude oil, which puts pressure on resources.
LDPE Usage Areas:
Low Density Polyethylene is a polymer widely used in the production of various containers, wash bottles, dispensing bottles, tubing, plastic bags and various molded laboratory devices. Plastics are used in huge quantities because of their properties that make them applicable to a variety of end-segment products. The main applications of thermoplastics are:
LDPE Pipes:
Low density polyethylene pipe (poly pipe) is the most used pipe for domestic and chemical irrigation purposes. These pipes are mainly used in irrigation to distribute from source to micro pipe. They are very suitable for above-floor installation and because they are not very flexible, the connectors can be used to route supply pipes. It can be used in a wide range of applications from pipes, sprinkler irrigation, drip irrigation, drainage system, agricultural pipes and other irrigation systems. These pipes are used in full flow with nylon insert fittings such as couplings, elbow tee and adapters. Serrated connectors are used with the pipes as they provide a leak-proof and free seal that helps prevent leakage and withstand water pressure easily. The basic characteristics of LDPE pipes can be listed as follows:
-
Pipes do not react at room temperatures except for high oxidation factors.
-
These pipes have a defined range of 0.910 g / cm 0.940
-
Low density polyethylene pipes can withstand 80 - 95 ° C continuously.
-
Tubes are completely translucent or opaque and highly resistant to breakage.
-
The pipe can withstand the maximum temperature of 80 ° C and the lowest temperature of -120 ° C.
-
Melting point of pipes 120 ° C
-
Tensile strength: 1700 psi (11.7 MPA)
-
Density: 0.92 g / cm3
-
It has poor UV resistance.
-
They are translucent with excellent flexibility.
LDPE Film and Sheets:
It is the first polyethylene to be developed and is known for its relatively heat resistance and its hardness and flexibility under the influence of temperature. These properties make it possible to be produced in the form of films and sheets that can then be used to produce other plastic products. This material is one of the fastest growing plastics currently used mainly for film applications, as well as being suitable for injection, blow and rotational molding.
-
Packaging industry - High use in food packaging and textile packaging. The application area is wide for films and layers, product bags in the packaging industry, brad bags, garbage bags, garment bags, grocery bags and shipping bags.
-
Industrial - Tapes, sealants, gaskets, photographic protection, liners, piping systems, composites, automotive parts, shrink films, pallet stretch, greenhouse coatings, tanks and containers, etc. It is used to produce.
-
Medical - Used in Transdermals, Hydrogels and wound care or in the packaging of medicines.
-
Sheets can be translucent and shrinkable.
-
They are resistant to heat and chemicals.
-
Sheets can be easily welded with a plastic welder.
-
They do not stabilize UV
-
These films are conductive films and can be easily colored.
-
They offer ease of adhesion, which means they can be easily heat sealed.
-
Films and sheets are flexible, light and economical.
-
Density: 0.92
-
Forming temperature: 245 ° F
-
Temperature range: 0 ° F - 140 ° F
-
Tensile Strength (PSI) 1600
-
Ultimate Elongation 600%
Technical values and more usage areas of some LDPE brand raw materials:
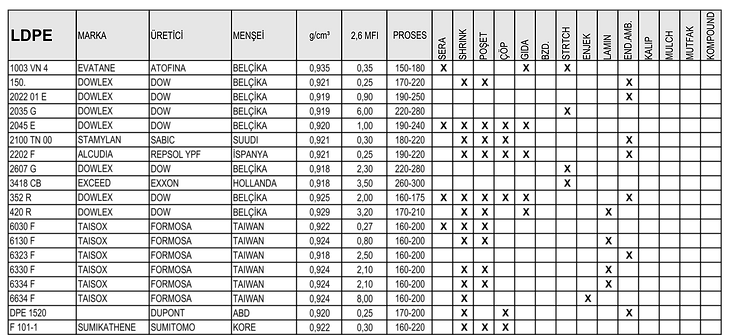
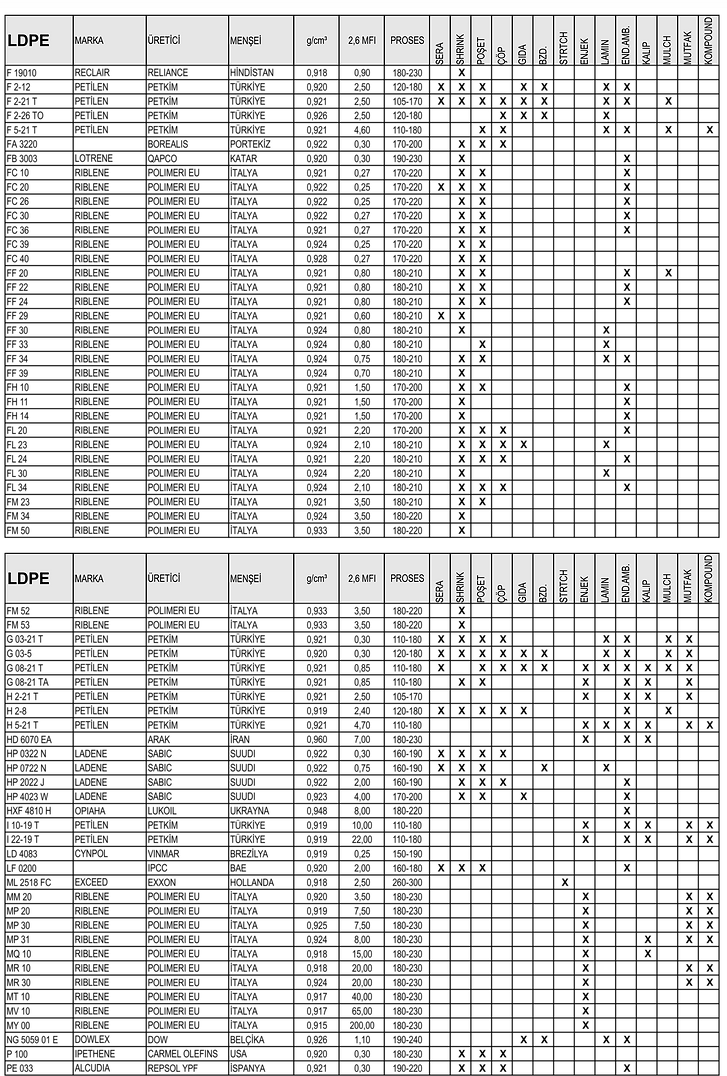

MDPE (Midium Densty PolyEthylene):
MDPE is used to obtain a stronger and more flexible end product than (medium density polyethylene) LDPE.
MDPE is a thermoplastic with a density between 0.926-0.940 g / cm3, less dense than the more commonly used HDPE. When it needs to be mixed with LDPE, it has better chemical resistance than LDPE. But despite all this, it is the least used polyethylene. MDPE is mainly used in gas pipes and fittings, bags, shrink films, packaging films, carrying bags and blown bottles.
-
It is resistant to impacts and falls.
-
It gives better cutting response than HDPE.
-
It shows more resistance to tensile cracking than HDPE.
-
It has medium high heat resistance.
-
Its density is very low compared to HDPE.
-
Complies with Food Processing rules.
ULDPE (Ultra Low Densty PolyEthylene):
ULDPE (ultra low density polyethylene) and VLDPE (very low density polyethylene) are basically LDPEs with a density below 0.880 g / cm3. ULDPEs are mainly used as impact enhancers for other polyolefins. The preference rate is high in the production of irrigation pipes in packaging for food, health and hygiene purposes and general purpose films.
-
Shows flexibility at low temperatures
-
Works very well for liquid containers
-
It has good optical properties.
-
Mainly used by blown and injection molding
-
Complies with Food Processing rules.
mPE (metallocene PolyEthylene):
These polymers are a new generation of high performance polyethylenes (PE), also called Linear Metallocene. They are used in a wide range of film applications such as packaging, agriculture, construction, and building and industrial applications. It offers excellent performance by significantly improving the general properties of PE and providing added value to the produced product. It gives excellent results in the production of packaging for packaging (film for lamination) (stretch film), coatings for extrusion processes, agricultural covers.
-
Highly resistant to impacts, punctures and tears
-
Easy Processing with high resistance to melting
-
Excellent sealing (as demonstrated by SIT and Hot Tack tests)
-
It has excellent optical properties
-
It has a special structure for multi-layer film extrusion.
-
Provides significant reduction in film thickness compared to LDPE, HDPE and LLDPE
-
It is preferred for more efficient and faster packaging processes and better sealing.
-
It is preferred primarily for optical improvements (brightness and transparency) in films.
-
Generally shows significant improvement in mechanical properties
-
Complies with Food Processing rules.
Technical values and more usage areas of some MDPE brand raw materials:

LLDPE (Linear Low Densty PolyEthylene)
Linear low density polyethylene is a polymer with a density greater than 965 kg / m, usually produced at low temperatures. It is produced by adding olefins (butene, hexene or octene) during the polymerization process of ethylene.
Poly-olefins are used in the production of linear low density polyethylene resins because these monomers contain a reactive double bond. These monomers are used accordingly to control the density and physical properties of the resin produced according to user demand. It is produced using two main techniques:
Gas phase polymerization:
In this process, a gas phase reactor is used, which is a kind of fluidized bed of dry polymer particles. These resin particles are maintained as a gas reactor by mixing or passing ethylene gas at high velocity.
In this gas reactor, ethylene along with the co-monomer is fed from the bottom of the fluidized bed into which the catalyst is then injected. In this gas, the reactor pressure is relatively low (up to 2 MPA) and the temperature maintained is around 70 to 110 ° Celsius.
Finally, the molten polymer forms are mixed with stabilizers and extruded linearly into low density pellets. These pellets are also used in the production of plastic products.
It is a process in which linear low density polyethylene is obtained by gas phase polymerization at low pressure from ethylene. In a fluid-bed reactor, using suitable solid catalysts, gas phase polyethylenes covering a wide range can be produced. The product is dry, flows easily and is in the form of granules that do not contain fine particles.
Melting index and molecular weight distribution are controlled by the specific choice of catalysts and operating conditions. The density of the polymer is adjusted by the amount of co-monomer in the product. Catalyst efficiency is very high; This property eliminates a catalyst separation after the reaction. The feature of the process is that it minimizes environmental pollution, fire and explosion hazards; therefore it is very easy to operate and maintain.
Gas ethylene, co-monomer and catalyst are introduced into the reactor; the reactor has a fluidized bed of growing polymer particles; It operates at 20 kg / cm² pressure and around 100 ° C. The reaction gas flowing into the reaction bed is circulated by a single stage centrifugal compressor; Thus, the necessary raw material for the polymerization reaction is provided, while the heat of reaction is removed from the bed. The circulation gas is cooled by passing it through a heat exchanger. The granular product flows intermittently into the product discharge tanks. Here, unreacted gas is separated from the product. The exhaust gas is compressed and sent back to the reactor. Hydrocarbons remaining in the product are swept away with nitrogen. The granular product is formed into pellets in a low energy system. The density of the products polymer is easily controlled in the range of 0.915-0.970 g / cm. The molecular weight distribution is narrow or medium width, relative to the catalyst. The melt flow can be varied from 1 to over 200.
Solution Polymerization:
In this process, linear low density polyethylene resins are produced at relatively low temperatures (70-110 ° C) with low pressure (1-5 MPA) in a saturated hydrocarbon environment.
During the polymerization process, the polymer forms a suspension or a moving slurry. In addition, the reaction medium is removed and the polymer is separated from the hydrocarbon inert medium.
The powder obtained as a result of this process is mixed again with stabilizers and extruded in pellet form. These linear low density polyethylene pellets can also be used in the production of end segment plastic products.
The gas phase polymerization process is better than Solution Polymerization in terms of operating cost involved, temperature maintenance in the process, and ease of flexibility during polymer production.

LLDPE is a type of linear polymer with a series of short branches created by copolymerization of ethylene with different long chain olefins, first produced by DuPont in Canada in 1959. It is like part of the poly-olefin family that has some structural differences from traditional LDPE (Low density polyethylene).
This polymer has proven itself as the third important player in the polyethylene industry, along with LDPE and HDPE. It has 3% of the global polyethylene market. The linear property of the polymer is due to the difference in the production processes of linear density polyethylene and low density polyethylene.
Generally, LLDPE is produced at relatively lower temperatures and pressures (described above) by co-polymerization of ethylene and higher alpha-olefins such as Butene, Hexene or Octene. LLDPE exhibits higher tensile strength, impact and pressure resistance compared to traditional LDPE polymers making it suitable for a wide variety of applications and uses.
Linear low density polyethylene resins are mainly used as film for bags and sheets or in the packaging industry. It is also used in the manufacture of other products such as toys, caps, buckets, plastic containers, bubble wrap and composite films. LLDPE is a type of linear polymer with a significant amount of branches. It is widely used for applications such as injection molding, rotational molding, wires, plates, pipes and ducts. They are also used in the production of goods for end-user industries such as packaging, agriculture, construction, automotive, household, marine and toys.
North America has been the largest consumer of linear-low density polyethylene, followed by the Asia-Pacific regions.
Producer companies of Borealis, Braskem SA, Chevron Phillip Chemical Co., DuPont, ExxonMobil Chemical, INEOS Group, Nova Chemicals and The Dow Chemical Company prioritize the LLDPE market.
LLDPE Key Features:
It offers the balanced hardness and toughness desired by the product, proving to be essential building blocks for the film and packaging industry. The properties of the linear low density material, the balance between physical and chemical properties make them an ideal polymer for the packaging of consumables, heavy-duty shipping sacks, films (blending shrink films and stretch films, etc.), as well as for the production of containers and caps.
-
They offer higher tensile strength, high impact and high puncture resistance.
-
Linear low density polyethylene materials are very flexible and generally stretch themselves under stress conditions.
-
Since these polymers have good environmental stress cracking resistance, they can be easily used to produce thin films.
-
In addition to having good electrical properties, linear low density plastics are extremely resistant to chemicals.
-
They have higher mechanical and improved sealing properties.
-
It has a transparent and glossy appearance that gives a good finish to the end products.
-
Linear low density polymers have low production and conversion costs.
-
Tensile strength 30 MPA and notched impact strength 06+ kJ / m
-
Density 916 g / cm³
-
Maximum operating temperature is 50 ° C.
-
Linear expansion 20 × 10−5 / ° C offered
-
Water absorption level is usually 01%
-
Melting Temperature Polymer range is 120 to 160 ° C.
-
These materials provide high flexibility and long life.
-
It has good resistance to UV rays and chemicals.
-
Linear low density plastics are highly puncture resistant.
-
Linear low density polyethylene materials have robust mechanical properties and less maintenance.
-
They have high tensile strength.
-
It is an excellent environment and material resistant to stress cracking.
-
It is less shiny compared to LDPE.
-
In these materials, the temperature range of thermal bonding is less.
-
Compared to LDPE, it does not offer flexibility in the processing phase.
LLDPE Usage Areas:
LLDPE is widely used to produce a plastic film for a variety of uses.
In this process LLDPE blown film resins are processed in flat drum extruders, the length of these barrels can range from 24: 1 to 30: 1. Since it is not easy to measure the bubble diameter, it is calculated from the flat slab width in a ratio of 2: 1 to 3: 5: 1.
Due to the narrow molecular weight distribution of LLDPE resins, films have to be extruded between wide ranges of 90 to 110 mil. If the die gap is too narrow for resins, the film may be subject to melt and breakage, and if the gap is too wide, there may be stability problems in the produced film. Certain improvements in properties can be made when producing these films by adjusting the LLDPE freezing line height. Better mechanical properties and film clarity can be achieved by lowering its level during production.
The approximate temperature at which linear low density polyethylene resins are melted in the extruder is between 200-230 ° C.
-
It is very flexible, ranging from 0.5 mil thickness to 40 mil, mostly in flexible sheet forms.
-
Linear low density polyethylene films are natural milky in color and translucent in appearance.
-
They have high chemical and impact resistance as well as good water absorption quality.
-
Linear low density offers excellent impact and stress cracking resistance
-
They usually have a density of 93 g / cm 3.
Linear low density films are widely used in various industries such as construction, agriculture and surface protection applications, all types of covers, linoleum and much more. Examples of films produced are cling films, agricultural films, lamination films and blending shrink films etc.
LLDPE Pipe:
LLDPE has certain properties such as excellent stress crack resistance, flexibility, durability and low cost, making them completely suitable for the pipe industry. LLDPE plastics are widely used in pipes containing chemical exposure, aging, high vibration joints, protruding type fittings and other compression fittings.
It can easily withstand exposure to different solutions and chemicals for 500 hours and more. They can even resist cracking when used with compression or pushed to connect fittings. Characteristic features of LLDPE pipes:
-
Higher tensile strength and high burst pressure.
-
They offer superior stress and crack resistance.
-
These tubes have excellent high puncture resistance.
-
Linear low density polyethylene pipe is highly impermeable to gases and moisture.
-
They have superior dielectric properties.
-
It is light, durable and economical.
-
Available in different colors such as black, gray, red, green, blue, yellow, orange, light and purple.
-
Temperature Range for these Tubes: -40 ° F to 150 ° F (-40 ° C to 66 ° C)
-
Vacuum Rating: to 28 '' Hg
-
Diameter Tolerance of These Tubes: ± 0.004 ”
-
Tube Markers: FW features
-
Working Pressure: 3: 1 safety factor
-
Suitable for use with food and beverage, medical and pharmaceutical applications.
LLDPE Bags:
Linear low density polyethylene materials such as HDPE (High density Polyethylene) and LDPE (Low density polyethylene) are also widely used to produce different Poly bags that can be applied to a variety of uses.
Industrial poly bags are often made from these materials as they offer high resistance to breakage and puncture under stressful or other extreme conditions. These plastic bags are used as grocery bags, bags used in clothing stores, heavy-duty bags, shopping bags or large waste disposal bags.
These Poly bags are very flexible, anti-scratch and durable with high impact and tensile strength. These poly bags are more economical than others, as linear low density polyethylene is a low cost material and readily available.
They have a glossy appearance and can be recycled for reuse. Today's linear low density plastic bags are manufactured using largely recycled linear density polyethylene materials.
LLDPE Covers:
Linear low density polyethylene liners or linear low density polyethylene polymer geomembranes are required for a variety of applications due to their strength, flexibility and durability. Their thickness can vary between 0.5 and 2.5 mm, and linear low density liner rolls come in various widths and lengths depending on their thickness.
LLDPE material is an ideal choice for producing plastic liner for the following reasons:
-
These geo-membranes offer a high degree of flexibility. It is beneficial as it allows more flexibility, more adaptation to collapse and different fit.
-
They are strongly resistant to UV rays and chemicals.
-
These shirts are high puncture resistance and more durable than their competitors.
-
These primers are available in two different surface colors, white and black, on demand.
-
It is used as a primer in lagoons, channels, tanks and ponds (holding ponds, agricultural ponds etc.).
-
Linear low density polyethylene liners are widely used for landfill covers and closures.
-
These geo-membranes are used for the mining of heap leach pads.
-
Liners are also used for the treatment of raw water of reservoirs, wastewater, as well as portable water reservoirs.
-
Used as secondary pollutant for aboveground storage tanks and as floating covers for water tanks.
LLDPE Butene-C4 / Hexene-C6 / Octene-C8:
There are a wide variety of linear low density polyethylene (LLDPE) grades, from C8 Octene to C6 Hexene and C4 Butene, ranging from high (up to 0.941 g / cm3) density to very low (0.905 g / cm3) density. LLDPE is used for film extrusion, blow molding, rotary molding and injection molding for food, frozen food packaging, radiant heating tubes, and cosmetic and pharmaceutical applications. Around 80% worldwide, mixed with LDPE and HDPE for improved mechanical and thermal properties. It is used in packaging of food packaging and other products, extrusion coating applications and especially in packaging of paper and cardboard.
Advantages:
-
Multidirectional,
-
Economic
-
Bottom sealing temperature with good mechanical properties
-
Providing big savings in high performance structures
Features:
-
Very flexible,
-
High tensile strength
-
Good chemical resistance
-
Good electrical properties
-
Compliant with Food Processing rules

Metallocene LLDPE
Production of stretch films, stretch head films, milk films, high-strength general purpose films, lamination films, greenhouse, agricultural and other films; it is also used alone or as an additive to other types of polyethylene.
Films made from metallocene polyethylene have excellent mechanical strength and the potential to reduce thickness, the homogeneous composition of the molecules determines the excellent hot seam strength and low melting point, thus enabling faster welds. The use of metallocenes in blow molding and injection molding allows you to produce a film with less turbidity and high gloss. It offers excellent insulating qualities, characterized by high impact resistance.
mLLDPE: It has a density of 0.927 g/cm3 and is a copolymer of hexane. MPE film has unmatched film performance with properties such as hardness, strength and impact resistance. Compared to traditional LLDPE, mLLDPE is a polymer with superior properties: high tensile strength, high toughness, improved puncture resistance and impact resistance, high sealing capacity, excellent transparency and gloss, and easy mixing with other polyolefins.
HDPE (High Densty PolyEthylene)
High density polyethylene is produced mostly by solution in heterogeneous phase and by mass polymerization technologies in gas phase. Solution polymerization method in homogeneous phase is also applied, albeit a little. In any case, the exothermic reaction depends on the ethylene monomer, the <P255> catalyst system and the hydrocarbon diluent. Molecular weight control is achieved by the catalyst and hydrogen used during the rection.
It is a process in which high density polyethylene is obtained from ethylene by solution polymerization at low pressure. Ethylene (and if desired small amounts of co-monomers), catalyst and hydrocarbon diluent are sent to the large polymerization reactor. In the reaction, sludge is formed and the polymer is formed in powder form. Polymerization is done below 10 bar and between 80-90 ° C. Catalyst activity is very high; For this reason, catalyst is added gradually in order to avoid the need for subsequent catalyst separation in large quantities. Since all ethylene is polymerized, there are no ethylene reversal or monomer recovery systems in the process. The hydrocarbon diluent is removed from the product by centrifugation and final drying is done in a nitrogen-powered fluid-bed dryer. Most of the separated diluent is returned to the process. The HDPE powder product obtained is transformed into granule form by coloring or naturally.

HDPE is also called "alketen" or "polyethylene" when used for pipes, a type of thermoplastic made from petroleum. It is the most used plastic in the world. High-density ration polymer is largely used in the production of plastic bottles, corrosion-resistant pipes, geomembranes and plastic lumber.
The distinguishing feature of HDPE that makes it ideal for the packaging industry; It is stronger than standard polyethylene and creates a strong barrier against moisture. Based in China, the whole of Asia is the leading region in high density polyethylene production. It has a 40% share in the global production capacity of the polymer. The second largest region in polymer production is North America with a share of 20%, followed by the Middle East with 17%. The Middle East and China are the fastest growing regions alongside new production capacity. The main driver of the HDPE market is due to the increasing demand in the packaging industry. It is a preferred material in the packaging industry because it is a relatively low cost material. The increasing demand for plastic pipes, which are widely used in place of domestic plumbing, is the most important driving force for this material in the global market.
It was invented in 1953 by the research of Karl Ziegler and Erhard Holzkamp of the Kaiser Wilhelm Institute.
Two years after the invention of this material, high-density polyethylene pipes were invented. Today, high density polyethylene has become the most widely used material in pipes due to its toughness, flexibility and chemical resistance.
Increasing agricultural activities in recent years have increased the demand for high density pipes due to the use of high density drainage pipes in agricultural drainage systems.
HDPE Main Features:
The material is one of the most durable and versatile thermoplastics used on a massive scale in today's plastics market. Due to its convenient properties, bottles, automotive parts, furniture, etc. It is used in the production of a wide variety of materials. The basic properties of the polymer are as follows:
-
Materials have a high strength / density ratio.
-
They are translucent and waxy in appearance.
-
Resins are easily flexible and highly resistant to weather conditions.
-
They have good toughness quality at low temperature.
-
They are extremely resistant to chemicals and are not easily corroded
-
High density polyethylene plastics are light, easily available and economical.
-
They have low moisture absorption.
-
Materials are easy to weld using thermoplastic welding equipment.
-
Tensile Strength 0.20 - 0.40 N / mm² and Notched Impact Strength Unbreakable Kj / m²
-
Thermal expansion coefficient 100-220 x 10-6
-
Max Cont Usage Temperature 65 ° C
-
Density 0.944 - 0.965 g / cm 3
-
The materials are strongly resistant to all kinds of Diluted Acids and Alkalis.
-
They are moderately resistant to oil and grease.
-
It has poor resistance to Hydrocarbons such as Resins, Aliphatic Hydrocarbons, Aromatic Hydrocarbons and Halogenated Hydrocarbons.
-
They are highly resistant to alcohol.
-
It is readily available and a low cost material.
-
High density polyethylene good impact resistance and tensile strength.
-
Resins can be easily processed with all thermoplastic methods.
-
Plastics are highly resistant to chemicals, corrosion and climate changes
-
Plastics made from materials are durable, flexible, strong and light.
-
It has high thermal expansion.
-
Resistant to bad weather conditions
-
Plastics are often subject to stress cracking.
-
Polymers are flammable and show poor temperature capability under certain conditions.
HDPE Usage Areas:
This plastic is one of the most popular in the world. It is a versatile polymer suitable for a wide variety of applications, from heavy-duty moisture resistant membrane in buildings to lightweight, flexible bags and films. Most commonly bottles and caps, fresh produce bags or thin gauge carry bags, etc. Using for.
Properties such as durability, recyclability and excellent vapor and moisture barrier make them applicable for the production of a variety of goods. There are different HDPE derivatives to be used in extrusion, injection, blown film production, pipe production.
HDPE Sheets and Sheets:
It is widely used in the production of sheets used to manufacture various plastic products. The sheets are strong and resistant to chemicals and temperatures with a low coefficient of friction. Their extreme durability makes them perfectly suitable for water tanks, industrial uses or products such as bottles and caps.
Matte sheets; It is primarily used to manufacture items such as cutting boards, as the material provides durability and does not dull the blades.
Straight plates; The smooth layers have a variety of qualities that make it valid for a variety of uses. Uniform high density boards can be easily fabricated and have good chemical resistance, tensile strength, and also high moisture and impact resistance. High density polyethylene flat lining is often used for tank lining. They are mainly used for rotationally molding large complex products such as fuel tanks, garbage containers, pallets, agricultural tanks, highway barriers. Sheets are also widely used in the production of various bags and bottles and in the packaging industry.
Tubular plates and equipment; they have some improved properties than the standard high density coating in terms of weight and performance, making them suitable for pipe fabrication.
High density polyethylene polymer is mainly used in the production of pipes. Resins are used in large quantities in pipe manufacturing as they are more durable, lightweight, weather resistant and provide easy material flow. These pipes are used in various sectors such as municipal, industry, energy, geothermal and landfills.
High density pipes have zero leakage due to the fusion process, forming a monolithic high density polyethylene system, as a result proving to be the most suitable material for pipes and fittings. These pipes are more environmentally friendly as they are non-toxic and highly durable.
-
They do not leak and offer excellent flow properties.
-
They are highly resistant to chemicals, corrosion and abrasion.
-
Tubes and fittings offer strong ductility and toughness.
-
Available in diameters from ½ inch to 63 inch, offering a wide variety of manufacturers.
-
They can withstand frozen water better than conventional metal piping systems.
-
It is highly durable and provides long-term economy, value and dependency.
Antiskit; It is specially produced for marine applications where a sliding or sliding surface is required.
HDPE Bags:
High density polymers are also used to produce very large scale poly bags. The basic properties of the material make them quite suitable for the production of various poly bags. These poly bags are manufactured according to their application and uses. Resins are used in the production of fresh poly bags, brad bags, food bags, thin gauge transport bags and others.
-
HDPE bags are resistant to high and low temperatures.
-
It is an additive-free material, so bags become ideal for packaging products.
-
HDPE bags offer anti-scratch properties that are also suitable for the packaging industry.
-
These bags are harder, stronger and have better moisture holding capacity.
-
Since the material is cloudy and dull, it does not provide clarity to the bags produced.
-
If HDPE bags are notched, it becomes very easy to tear these bags in the direction in which the film is extruded.
HDPE Covers:
High density polyethylene is widely used globally as a geomembrane due to its large availability and low material cost. It is resistant to chemicals, UV and ozone, making it suitable for use in primer production. Linings are mainly used in landfills, wastewater treatment lagoons, animal waste lagoons and mining applications. These liners are available in large rolls that are approximately 22.5 inches wide.
They are durable and UV resistant materials. They have good chemical and temperature resistance.
Apart from all these; They can be used as landfill liners, mining pools and even for the treatment of all water contaminated objects. HDPE Plastics are applicable to various end-segment products such as plastic bottles and caps (water bottles, drinks, etc.), toys (outdoor and indoor playgrounds), chemical containers (shampoo, conditioner) due to their durability, flexibility and lightness. , cleaning products, engine oil, etc.), marine construction and furniture (cabinets, turf furniture, lockers, bathroom countertops) and many other household products used in daily life.
You can find information about HDPE Recycling here.
Technical values and more uses of some HDPE brand raw materials:


Differences Between LLDPE / LDPE / HDPE
High Density Polyethylene (HDPE), Low Density Polyethylene (LDPE) and Linear Low Density Polyethylene (LLDPE) are a different type of polyethylene polymers all used in the end-segment markets to produce plastic products.
They all have specific properties that make them applicable to a variety of different uses. The major difference between these resins is their cellular structure or molecular bond with each other, which indicates how tightly they are formed.
Most Flexible: LLDPE is the most flexible form of plastic used. It is a more refined form of LDPE with greater flexibility, tensile strength, and conformity. Due to its strong and convenient properties, it is widely used for sheets and films. It is widely used for ponds and canals.
Most Commonly Used: LDPE is the most common type of plastic used. Agriculture, construction, containers and lids, coating etc. It is widely used in fields.
The Most Zone Processor: It is the strongest and most durable form of HDPE Polyethylene. It has maximum chemical resistance and is relatively less flexible than other forms of polyethylene plastic resins. HDPE materials have maximum UV resistance which contributes to their toughness quality.

EVA (Ethylene Vinyl Acetate)
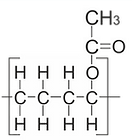
It is also known as polyethylene-vinyl-acetate (PEVA). It is a copolymer of ethylene and vinyl acetate. The weight percentage in this formation ranges from 10% to 40% and the remainder is ethylene.
EVA copolymer is of three different types that differ mainly in their vinyl acetate content and the way the material is used. This porous elastomeric material is about three times more flexible than low LDPE, with a tensile elongation of 750% and a highest melting temperature of 96 ° C. This material is generally non-toxic in nature and exhibits the properties of LDPE, but is generally more brilliant in film applications. They are used for thermoplastic extrusion, film coalescing and foam molding.
It is preferred in the production of Film, Foam, Hot Melt Adhesives, Wire cable, Extrusion Coating, Solar Cell Encapsulation, Injection Molding and Medical Tubing.
Automotive, Packaging and Paper, Paints, Coatings and Adhesives, Electronics and Electricity, Pharmacy, Footwear, Photovoltaic Panel, Agriculture and Medicine.
EVA are thermoplastic resins produced by the co-polymerization process of ethylene and vinyl acetate monomer in a high pressure reactor.
DuPont is the company with the largest EVA production capacity in the world. This is followed by Hanwha Chemical and Exxon Mobil.
-
Vinyl Acetate Modified Polyethylene (Low vinyl acetate density)
-
Thermoplastic Ethylene-Vinyl Acetate (Medium vinyl acetate density)
-
It is in three segments as Ethylene Vinyl Acetate Rubber (High vinyl acetate density).
EVA Key Features:
EVA polymer has properties similar to low density polyethylene polymers with some improvements.
The main properties that EVA resins exhibit are:
-
The material provides good clarity and shine.
-
It is highly resistant to stress cracking and UV rays.
-
Low temperature resistance.
-
High coefficient of friction.
-
It has a distinctive vinegar-like scent.
-
Melting point - 75 ° C
-
Tensile strength, N is 0.05-0.2 / mm 2 and notched impact strength an intermediate Kj / m 2
-
Density at 25 ° C is 0.948 g / ml
-
Flash Point - 260 ° C
-
Thermal expansion coefficient 160-200 x 10-6
-
Stability - Stable, Incompatible with flammable and strong oxidizing agents.
-
They show very good resistance to dilute acids and alkalis, aliphatic hydrocarbons, alcohols, oils and greases.
-
They have poor resistance to Aromatic Hydrocarbons and Halogenated Hydrocarbons.
-
They show excellent thermal adhesion strength.
-
They are a good amount of flexibility even at low temperatures.
-
It is resistant to stretching and cracking.
-
They can be easily processed using traditional thermoplastic techniques.
-
Poor tensile strength compared to its substitutes
-
Lower resistance to heat deformation
-
It has poor chemical resistance and barrier properties compared to its competitors.
EVA Usage Areas:
Generally, EVA is applicable to a number of different end uses such as flexible packaging, heat seal layers, thermal laminations, hose and tubing, blow molded bottles and cap liners.
Since EVA resins can be easily cut from sheets and molded into any desired shape, they are also used to produce complex end-user products. It can be used in the production of orthoses, cigarettes, surfboards, lean boards and even artificial flowers.
They are even used for thermoplastic mouthguards and softening or waterproof leathers.
EVA Foam:
Ethylene vinyl acetate is a type of closed cell foam. It is a soft and durable ethylene and vinyl acetate polymer widely used in flooring. It also has a variety of other uses such as sports equipment, craft, and set design. Since EVA is soft in nature without being spongy, it is often used in the production of flip-flops.
Features Basic properties of EVA foam materials:
-
They are extremely resistant to weather conditions and chemicals and are flexible.
-
Due to their low water absorption feature, they are resistant to spills.
-
They are resistant to chemicals.
-
They do not show toxic properties due to their nature.
EVA foam has good foam production properties. Several methods can be used to manufacture EVA foams and sheets:
-
Foam Stripping: Scum stripping is a method of making thinner foam sheets than raw sheets produced by a foaming machine. Scum stripping is always the first step in the remaining foam production process.
-
Foam Cutting: This process is used to cut foam sheets into blocks and strips. It is a useful and efficient technique for manufacturing EVA foam materials. Sawing machine sheets in foam are cut to the desired length and width. Two types of sawing methods are used, the first being the vertical saw and the second the horizontal saw. The end products of both types of sawing machines are foam sheets, blocks and strips.
-
Special Die Cutting: This die cutting method is used in different industries such as paper packaging where a die made of steel is used to cut the paper box. Likewise, die cutting method is used for foam production. This method is generally preferred in the production of packaging, foam case inserts, foam profiles and foam seal pads.
-
Foam Lamination: Required where EVA foam materials' adhesive adhesive backing, felt surface, fabric and film backing is required. Two types of EVA foam lamination methods are used in the process. The first method is PAS lamination (adhesive lamination) and the second method is heat lamination. While adhesives are used for lamination in adhesive lamination, in the other method, heated foam surface is used for the lamination process.
-
Foam Thermoform: Foam thermoforming is done to achieve more flexible and durable foam. This process is primarily used to make 3D custom foam pieces. Since thermoforming itself is about heating and temperatures, this technique works on the same principles. The machines used in the thermoforming process are adjusted according to the desired temperature and temperature, and special foam parts are created in the molds under heating and pressure.
Benefits of using Eva Foam:
-
They offer ease of work and come in a variety of thicknesses, colors, and densities.
-
It can be easily shaped with the help of heat and even adhered to other materials.
-
These foam materials can be easily dyed.
-
EVA foams can be easily transported, stored and rebuilt.
-
It is easy to clean.
-
EVA foams offer a combination of durability, comfort and usability.
-
These materials are very attractive and easily affordable.
EVA Shoes and Soles:
EVA is an elastic copolymer very similar to rubber and can be used in many household and industrial applications. It is an environmentally friendly material that does not use chlorine in the production process and can be easily recycled into new products (playgrounds, mats, etc.). It is widely used in the production of vegan shoes. Most running and casual shoes are made using EVA. Even a few wealthy brands in the shoe industry such as Timberland, Teva, Keen and Patagonia have adopted the use of EVA in shoe manufacturing.
EVA material is one of the best shock absorbing materials available today. For this reason, most of the leading brand joggers use this in their shoe soles to get a good combination of shock absorption and lightness. EVA materials are widely used for the midsole of shoe parts, the outer sole and insole of sports shoes, as well as the sole of slippers and flip-flops.
The benefits of using EVA in shoe manufacturing are:
-
Provides cushioning and springing in shoes.
-
It increases the resistance of the shoes against hardening and cracking.
-
It does not absorb water and remains flexible even in cold weather.
-
It is also resistant to UV rays.
-
This material is highly resistant to water and corrosion.
-
It offers ease of processing (cutting, gluing, pressing and lamination).
-
EVA sole is anti-vitality (shock cushioning with good tensile strength and high toughness)
-
They provide insulation against cold weather
-
Closed foam sound insulation quality.
PEVA (PolyEthylene Vinyl Acetate)
It is a chlorine-free vinyl that proves to be a direct substitute for Poly Vinyl Chloride (PVC). Since PVC is a known type of carcinogen today, it is avoided wherever possible. Since PEVA is inherently less toxic than PVC, it is used as a substitute for a variety of products (especially household items).
PEVA is used in various household products such as shower curtains, toys, shoes, cosmetic bags, baby bibs, plastic covers, car covers and mattress protection.
Technical values and more usage areas of some EVA branded raw materials:

PP (PolyPropylene)
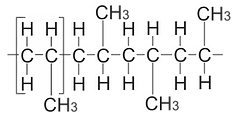
This plastic is milky white in color. It has very good dyeing ability. Its thermal, chemical and electrical properties are neither very good nor very bad, limited. Polypropylene (PP) is similar in many respects to high density polyethylene (HDPE). Rather than forming a long polymer chain of repeating -CH2 components, the porous polypropylene molecule has a series of CH3 groups suspending the main carbon backbone.
Its strength and softening temperature is quite high and it is lighter than water. Like polyethylene, its smell is sharper and more caustic. It has properties similar to PE. Gas is used in the air filters of vehicles, reinforced with asbestos fibers, and is also used in packaging and sack works.
Polypropylene is the first among stereoregular polymers to be produced. Its production started in 1957 and increased rapidly and reached large quantities in a short time.
Polypropylene (PP), also called polypropene, is thermoplastic by nature. It is a linear hydrocarbon polymer expressed as (CnH2n). PP polymer is one of the most versatile polymers and is used both as plastic and fiber.
The polymer has hard properties such as being mechanically robust and resistant to many chemical solvents such as bases and acids. This makes polypropylene plastic ideal for a variety of end-use industries. The main application area of PP plastic is packaging and labeling, textiles, plastic parts and various types of reusable containers.
PP plastic is also preferred by manufacturers for molding household items, automotive products, marine and caravan products. It is also safe to use PP plastics as food containers because they prevent chemicals from leaking into food products.
Polymer can be used in different processing technologies such as Injection Molding, Blow Molding, sheet extrusion and thermoforming.
PP resin is made from propylene, and propylene is the second most produced building block in the petrochemical industry.
PP is obtained by polymerization of propylene with organometallic and stereospecific catalysts (Ziegler-Natta) under controlled temperature and pressure. Depending on the polymerization process applied and the catalysis knitting system used, the molecular structure of the polymer produced shows three different types of stereochemical configurations; these are isotactic, syndiotactic and atactic configurations. In isotactic polypropylene, the most common commercial polymer used, all methylene groups are located on the same side of the polymer backbone; Therefore, a structure that allows crystal formation occurs.
Later developed catalysis technologies are in the direction of minimizing the formation of non-isotactic structures; Thus, it is aimed to remove some of the production steps required to separate the non-isotactic (syndiotactic and atactic) fractions from the product obtained.
It shows superior strength properties against many chemicals. It shows high mechanical and tensile strength. It can be welded due to its structural feature. Its electrical resistance properties are very good. Its low density makes it economical. It consists of two types: Homopolymer (PP-H) and Copolymer (PP-C).
Operating temperatures are 0 to 100 ° C for PP-H and -30 to 90 ° C for PP-C. Its main properties can be high chemical resistance, good impact resistance, good mechanical properties and low density.
In the production of homopolymer and random copolymer, gas propylene, co-monomer and catalyst are put into the reactor. The reactor has a fluidized bed of growing polymer particles; It operates at 35 kg / cm² pressure and around 70 ° C. The reaction gas flowing into the reaction bed is circulated by a single-stage centrifugal compressor; Thus, the necessary raw material for the polymerization reaction is provided, while the heat of reaction is removed from the bed. The circulation gas is cooled by passing it through a heat exchanger. The granular product flows intermittently into the product discharge tanks. Here, unreacted gas is separated from the product and returned to the reactor. In the production of impact-resistant copolymer, the polypropylene resin obtained in the first reactor is taken into the second (impact-resistance) reactor. Gas propylene and ethylene are sent to this reactor to obtain the polymeric rubber phase. The operation of the second reactor is similar to the first; but half the pressure. A centrifugal compressor recycles the gas through the heat exchanger to the fluid-bed reactor.
Impact resistant copolymer product, to discharge tanks
comes and the unreacted gas returns to the reactor.
Hydrocarbons remaining in both productions are swept away with nitrogen.
The granular product is transformed into pellets in a low-energy system by adding appropriate peroxides. Homopolymers with a melting stream of 0.1 to 3000 and an isotactic content of up to 99% can be obtained. In random copolymers, ethylene can be increased up to 12%, the melt flow being varied over a wide range from 0.1 to 100. It is possible to obtain narrow to broad molecular weight distributions.
Areas of use include chemical tanks, valve and pump parts, all kinds of cable insulation and tubing, transformers, relays, antennas, transformers, radar parts, fittings, coil, generator insulations, airtight seals for high voltage insulators, capacitors and transformers Laminated plates are produced for printed circuits.
Catalysts in PP Process:
TiCl3 Based Catalysts: Isotactic polypropylene (regular steric structure) was first obtained by Natta in 1954 with an activator system consisting of TiCl4 and Al (C2H5) 3; TiCl4 in the system was reduced by Al (C2H5) 3 during polymerization and transformed into solid, crystalline TiCl3, and the resulting polymer was provided to contain high percentages of isotactic structure. Later, Hecules discovered the role of hydrogen in the regulation of molecular weight, Esso obtained better results by using AlCl3 in TiCl3 solid solution instead of pure TiCl3. Mitsubishi was able to increase isotacticity up to 92-94% by adding electron donor like carboxylic acid ester to TiCl3; This system is called second generation catalysis blanket. However, the catalyst mesh yield is found to be insufficient for a production in which the residue removal process is removed by reducing the catalyst mesh residue.
MgCl2 Supported Catalysts:
The MgCl2 increases the catalysis mesh yield, there is no need to separate catalysis residue, thus facilitating polymerization in the hydrocarbon slurry. Third generation catalysts have been developed with this invention and further refinements. Thus, higher efficiency, stereospecificity and morphology control can be achieved in simplified processes where the polymerization medium is a monomer.
Metallocene Catalysts:
Single-ended metallocene catalysis patterns have been developed to replace Ziegler-Natta catalysts. Properties such as narrow molecular weight distribution, uniform polymer chains, transparency and density in the polymer obtained are the main characteristics of catalysts in this class.
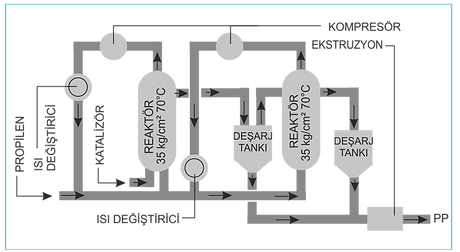
The following steps are fundamental in PP production:
-
First of all, raw materials and additives must be purified. Catalyst material must be prepared. The feedstock used is propylene.
-
The polymerization then takes place either in the gas phase with fluidized bed / stirred reactor or in the liquid phase with the slurry / solution.
-
The polymer particles are then separated from the existing monomers and diluents. Monomer and diluents are recovered and fed back in the process.
China is the leading manufacturer of PP polymer. Its share in global total production is 27%.
The biggest PP producer companies in the world market as of 2017 can be seen below. (million tons / year)

PP Basic Features:
PP is a hard and very durable plastic. The properties of this polymer depend on the molecular weight and distribution of the monomer. PP resin does not encounter stress cracking problems due to its good heat resistance. Besides being translucent, having good fatigue resistance and being semi-rigid, they also offer other physical properties that broaden their use. They have excellent aesthetic properties, so they are used in many places in automotive industries where gloss and gloss are required in parts such as bumpers.
PP resin is resistant to acids, bases, water or detergents. PP plastics can be a good choice for containers as they are resistant to acids and bases. They have a low density, high softening point and offer higher hardness and hardness. Resistant to organic solvents at room temperature.
Polypropylene density residues between 0.895 g / cc are 3 amorphous and 3 crystals per 0.92 g / cc. However, this density can be changed with fillers. It is hard and flexible when copolymerized with ethylene. It is reasonably economical and has good resistance to fatigue.
PP plastics are easy to weld using thermoplastic welding equipment due to their properties. This leads to the fabrication of storage tanks for chemical, water, and other liquid materials. Polypropylene melting point is 160 ° C.
There are three types of PP grades. Which class to choose for an application depends on the following points:
-
Homopolymer: This class is considered as general grade and can be used for a variety of general purposes. Stronger and harder than high distortion temperature (HDT) copolymer. They are durable, hard plastics available in translucent white and other colors.
-
Block Copolymer: It is harder and more durable than homopolymer. Their composition contains from 5% to 15% ethylene with increased impact resistance.
-
Random Copolymer: The chemical composition of random copolymer contains 1% and ethylene. They have better flexibility; The lower melting points and structures consist of co-monomer units randomly arranged along the pp molecule chain.
-
PP material is easily available and inexpensive.
-
Its semi-crystalline structure offers high bending strength.
-
It has good chemical resistance to different bases and acids, and is also very resistant to moisture absorption.
-
It is a good electrical insulator with good fatigue resistance required for the manufacture of various products.
-
They have good impact resistance with strong resistance to fatigue
-
The polymer is also hard and heat resistant
-
They tend to be smooth during processing with excellent aesthetic properties
-
They have a high melting point which makes them widely used for microwave food containers.
-
The high coefficient of thermal expansion limits the high temperature applications of PP material.
-
PP is extremely flammable and difficult to paint as it has poor adhesion properties.
-
They are prone to oxidation and UV degradation.
-
PP polymer has poor resistance to chlorinated solvents and aromatics that affect the use of PP in production processes.
-
It can be used as both plastic and fiber.
-
Higher melting point than polymer polyethylene
-
And it is less stable than polyethylene
-
It has better fatigue resistance than PE and is used as a hinge.
-
PE has less static charge, so it attracts less dust than PP.
PP Usage Area:
PP polymer can be processed by extrusion blow molding, injection molding and general purpose extrusion. Expanded PP (EPP) can be molded by a specialist process. The properties of the polymer make them applicable to various end-use segments of the plastics market.
PP Molding:
It is a technique used to shape plastics using rigid frames and molds. Molding is commonly used in the manufacture of car parts, containers, signs and other high volume items. Plastic molding involves filling the liquid polymer into a hollow mold so that it can take its shape. This process involves a high pressure range and enormous heat. There are different techniques used in plastic molding, including Injection molding, blow molding, rotational molding, and compression molding.
The melt flow rate is an important determinant for polymer processing. Melt Flow Rate (MFR) or Melt Flow Index (MFI) defines the molecular weight of PP. It is an indication of how easily the molten polymer will flow during the molding process. Melting flow rate is high. Filling of the mold is done easily with high MFR.
Two techniques commonly used in PP molding are PP Injection Molding and PP Blow Molding.
-
Injection molding: a process in which materials are injected into molds to produce parts. The use of PP polymer in plastic injection molding is increasing due to its positive properties. PP injection molding is used in various industries to produce goods for different segments due to its key properties such as good chemical and moisture resistance, flexibility in molding and being economical. When PP resin has a medium flow rate, a wide range of products are used in medical products, construction products, consumer products (containers, sports equipment, toys, etc.) and hardware.
-
PP Blow technique: used for the production of large quantities of hollow plastic objects. Primarily, the plastic blow molding technique is used in the production of plastic bottles, jars and containers (both narrow and wide mouthed containers). PP Blow technique, large containers, plastic bottles etc. It is widely used for. PP material is used in blow molding technique due to its properties that facilitate the production process such as good moisture barrier, chemical resistance and stability at high temperatures. 200 ° F) In blow molding process, the preferred properties of PP resin are high molecular weight and low flow grades. PP Blow Molding in various products made of PP material, such as food containers, plastic bottles, milk containers, Ice boxes, and large scale PP Blow molding, channel works, water tanks, fuel tanks, recycling bins and overflow bottles.
PPH (PolyPropyene Homopolymer):
Polypropylene is an economical material that offers a combination of excellent physical, mechanical, thermal and electrical properties not found in other thermoplastics. Compared to low or high density polyethylene, it has lower impact resistance but higher operating temperature and tensile strength.
Polypropylene homopolymer (PPH) is the most widely used. It has a high strength / weight ratio and is harder than copolymer. This, combined with good chemical resistance and weldability, means it is used in many corrosion resistant structures. It is preferred in the production of orthopedics and prosthetic devices, storage tanks, processing and chemical storage devices, medical devices, various covers, biaxially oriented polypropylene (BOPP) films.
-
Has a high strength / weight ratio
-
Excellent chemical resistance
-
It exhibits high performance in thermoforming and corrosive environments
-
Does not absorb moisture
-
It is resistant to most acids, oil solvents and organic solvents.
-
It shows good sealing properties
-
Non toxic
-
Does not stain
-
It has high strength values.
-
High gloss feature in bright molded parts
-
Complies with Food Processing rules.
PPC (PolyPropyene Copolymer):
Polypropylene copolymer (PPC) is slightly softer but has better impact resistance. It is also stronger and more durable than polypropylene homopolymer (PPH). It tends to have a better resistance than homopolymer in terms of stress cracking and lower strength at temperature, although there are slightly lower performance in other properties. Bottle, cap, glass, graduated cylinder tube, pipe, thermoformed plate production are its application areas.
PPC-R (PolyPropyene Copolymer Random):
Unlike PPC, Random PPC has comonomer units arranged in irregular or random shapes along the polypropylene molecule. Generally, it is chosen for applications where a more flexible and transparent product is desired, although it has less impact resistance than PPC.
Technical values and more usage areas of some PP brand raw materials:

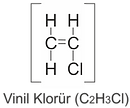
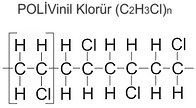
PVC (PolyVinyl Chloride)
Poly (vinyl chloride) is a polymer that has been produced commercially for over fifty years and comes in many types. PVC has a much more common usage area than other plastics due to its ability to blend easily with plasticizers, stabilizers and other additives.
Its resistance to many chemicals, especially strong acids, has made it a preferred material in such applications. Due to its structural feature, it is among the materials that can be welded and bonded. The disadvantage is that it has a low temperature resistance of 60 ° C compared to the materials in its group and its high density. It has a non-flammable feature, that is, they do not ignite when exposed to flame and pulled. It has good electrical arc resistance. In cases where higher temperatures and chemical resistance are required, a special type of CPVC should be used. Operating Temperatures are between -15 and 60 ° C. Chemical tanks, electrical equipment production, water treatment facility pools, pump and valve bodies, pipes are the main areas of use.
A process in which polyvinylchloride (PVC) is produced from vinyl chloride monomer (VCM) by two-stage mass polymerization.
Five types of polymerization processes are used in commercial production of poly (vinyl chloride):
suspension, emulsion, mass, micro suspension and solution polymerization. The most common of these are suspension, emulsion and mass processes.
Suspension Polymerization:
The most commonly used technique to obtain poly (vinyl chloride) from vinyl chloride is suspension polymerization. Since polymerization requires the vinyl chloride droplets to be dispersed in a suspension medium with vigorous stirring, the batch process is applied. Up to 80% of the amount of PVC currently produced is obtained by this technique.
Emulsion Polymerization:
In this process, the monomer is polymerized in an aqueous environment in which a water-soluble initiator and emulsifier are also present.
Mass (or Bulk) Polymerization:
The polymerization mechanism followed in the monomer mass in mass polymerization is the same as the reaction occurring inside each monomer droplet in suspension polymerization; The difference is that there is no suspending medium in the mass process.
Micro Suspension Polymerization:
It is an emulsion polymerization type in which the initiator used is soluble in the monomer. The polymerization reaction takes place in very small droplets; As the polymerization progresses, the monomer passes from the coarse emulsion into the droplets.
Catalysts in PVC Process:
The catalysts used in the production of poly (vinyl chloride) vary according to the type of product to be obtained and the polymerization system applied. Suspension polymerization catalysts of vinyl chloride will be mentioned here.
Commercial free radical initiators are mostly of the monomer soluble type; organic peroxides (RO = O R '), organic peresters, peroxide-carbonates and aliphatic azo compounds (RN = N R'). All of these compounds give free radicals by thermal decomposition. Some important initiators used in PVC polymerization include di-sec-butyl peroxydicarbonate and 2,4-dimethyl valeronitrile. These initiators are soluble in vinyl chloride monomer. The choice of initiator is important as a regular and linear polymerization rate is required for easy control of the process.
Polyvinyl chloride, more commonly abbreviated as PVC and known by this name, is the third largest thermoplastic polymer used in the market. PVC, one of the most valuable products of the chemical industry, is used in many areas from toy making to building materials in the construction industry. PVC is a very hard and tough material and thanks to these mechanical properties, it has a wide range of uses. But it is a material with less chemical resistance.
It is used as water pipes, glass frames, wire and cable insulation, as a water bottle. To increase the impact resistance of PVC, rubber plastics are mixed with PVC. Although PVC is commonly referred to as vinyl, there are other polymers that are members of the vinyl family. (Polyvinyl acetate, Polyvinylidine chloride, Polyvinyl alcohol etc.) PVC is also a modification of polyethylene. Similar in structure to polystyrene, there are chloride ions instead of benzene groups.
It is the most used type of plastic after polyethylene and it is very cheap. It is resistant to high chemical effects and abrasion. There are two types, hard and soft. Pressurized water pipes, sewage pipes, roof rain gutters and downpipes, irrigation and sprinkler pipes, plastic joinery roofing sheets are produced from the hard ones. Soft ones are used as floor tiles in buildings. They are resistant to burning with flame and emit toxic gas with it. It has also been used frequently in door and window construction in recent years. PVC pipes are not used in hot water installations as they soften at 80ºC.
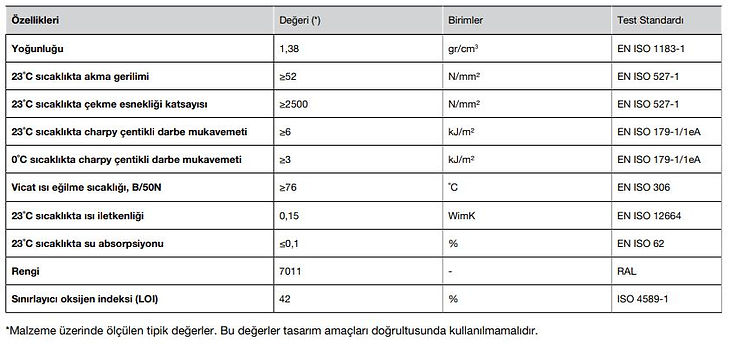
PVC-U 'nun uzun süreli davranış özellikleri :
Hesaplama (EN ISO 15493:2003 sayılı standarda göre)
Aşağıdaki şemada PVC-U malzemesinin uzun süreli davranışı gösterilmektedir.
20°C–60°C arasındaki sıcaklık değerleri için, kırılma çizgileri gösterilir. Bunlar LPL eğrileri (Alt Öngörülebilir Limit) olarak gösterilmektedir. Bu da tanıma göre bütün kırılma noktalarının %97,5’inin eğrilerde veya eğrilerin üzerinde olduğu anlamına gelir.
Tipik olarak PVC-U gibi amorf termoplastikler için hidrostatik mukavemet şemasında hiç dirsek gösterilmemektedir.
Eğriler bir çift logaritmik ölçekte (lineer değil) çizilir. Gerilim veya zaman değerlerini okuduğunuz zaman, lütfen bu durumu hesaba katın.
PVC-U malzemesinden yapılan borular ve bağlantı elemanları için gösterdiğimiz basınç/sıcaklık şeması dahil edilen tasarım faktörü ve 25 yıllık ömürle hidrostatik mukavemet şemasından elde edilir. Hidrostatik mukavemet şeması ekstrapolasyon yöntemiyle EN ISO 9080 standardına göre belirlenmiştir. Aşağıdaki denklemle (4 parametreli model) gerilim, sıcaklık veya zaman 10°C–60°C arasındaki sıcaklık değerlerinde hesaplanabilir.


PVC ne kadar sağlıklı :
1950’li yıllardan beri günlük hayatımıza en fazla girmiş olan PVC ürünlerinin kansere sebep olduğunun belirtildiği tek bir rapor bile yoktur. Çünkü, PVC hammaddesinde sağlık problemine sebep olabilecek tek nokta, tam polimerizasyon işlemi yapılamaması sonucunda insan sağlığını tehdit edecek miktarda reaksiyona girmemiş Vinil Klorür monomerlerinin hammadde içinde kalması olabilir.
Ancak,günümüzde tamamen tam kontrol altında kapali reaktörler içinde yapılan polimerizasyon teknolojisi sayesinde, polimerizasyon işlemi boyunca hammadde içinde reaksiyona girmemiş bir şekilde duran vinil klorür monomerinin miktarı devamlı olarak izlenebilmekte ve vinil klorür monomerinin hammadde içindeki oranı 1 PPM miktarına(milyonda bir) düşene kadar polimerizasyon işlemine devam edilmektedir.
Dünya Sağlık Örgütü’ne akredite laboratuarların gıda maddeleri saklanması ve nakli için onayladığı plastik malzemelerin en başında PVC den mamül ürünler gelmektedir.
Tip alanında kullanılan ameliyat malzemeleri vs gibi ürünlerin saklandığı bütün kap ve tip malzemeleri PVCden yapilmaktadır.
PVC hammaddesinin hastalık yayma konusundaki temiz sicilinin altında yatan gerçek, PVC maddesinin içme suyu ve diğer sivil ara karşı nötr olması yani etkileşime girmemesidir. Bu nedenle PVC hammaddesi suya hiçbir partikül bırakmaz. Ayrıca, klor maddesinin mikrop öldürücü olarak su dezenfeksiyonunda kullanıldığı bilinir.
PVC hammaddesinin üretilmesinden sonra hammaddenin sağlamlığını artırmak için eklenen stabilizatörler içinde kullanımı sağlığa zararlı sayılan ağır metaller türünden maddeler olan Kadmiyum(Cd) ve Kurşun(Pb) maddelerinin stabilizatör olarak kullanımı yasaklanmış ve artık günümüzde hiç kullanılmamaktadır.
Bu ağır metaller yerine artık bugün bütün dünyada stabilizatör olarak Baryum (Ba),Çinko(Zn), Kalsiyum(Ca) ve Kalay(Sn) maddeleri kullanılmaktadır.
PVC 'nin çevre sicili :
PVC Hammaddesi, gerek üretimi için diğer plastik hammaddelerine nazaran çok daha az petrol kullanılması ve gerekse üretimi için diğerlerine nazaran çok daha az enerji gerektirmesi nedeniyle bütün sentetik plastik malzemeler içinde en çevre dostu malzemedir. Çünkü, PVC nin erime noktası diğer hammaddeler içinde en düşüktür.
PVC yi işlemek için diğer plastik malzemelere hem çok daha az enerji ve hem de daha az işlem süresi gerekir. Bu da nihai ürünün maliyetinin PVC’de çok düşük olmasına yol açar.
PVC boruların ömürlerine etki edenler :
Boru hattı projelerinde öngörülen basınç dayanımı ve hizmet ömrünü sağlayabilmeleri için, PVC boruların ilgili standartlarda öngörülen et kalınlığında imal edilmesi ve kesinlikle üretim esnasında % 9'dan fazla kalsit kullanılmaması gerekir. Aksi taktirde, proje tesliminde borular basınç testini geçseler bile, ilerleyen zamanda boruların hizmet ömürleri düşecektir.
Boru hattının kalitesini etkileyen en önemli faktör, birleştirme kalitesidir. Çünkü, bir boru hattı % 70 oranında ek yerlerinden kaçırır. Bunun önüne geçmek için, birleştirilecek iki parçanın çap farkının 0.4 mm'den daha fazla olmaması gerekir. Aksi taktirde, iki parça birbirine bol geçecek ve yapıştırıcı veya O-Ring contası bu boşluğu iyi kapatamayacak ve sonuçta bu noktada zaman içinde sızıntı oluşacaktır. Her firmanın kendi üretim toleransı olduğundan, değişik firmaların ürettiği iki ürünün birleştirilmesi durumunda yapıştırıcının kapatamayacağı kadar bir açıklığın oluşması muhtemeldir. Bu nedenle, mümkün olduğu kadar boru ve ek parçalarının aynı üretici firmadan temin edilmesi uygun olacaktır.
Her çeşit plastik borunun kendine has artıları ve eksileri vardır. En uygun boru tipi, arazinin yapısı, trafik yükü, iklim şartları, istenilen basınç dayanımı ve ortam sıcaklık derecesi gibi faktörler göz önüne alınarak karar verilir. Çünkü, bir boru ne kadar kaliteli üretilirse üretilsin, eğer o proje ve arazi için uygun bir boru tipi değilse sonuç mutlaka olumsuz olacaktır.
PVC boruların alev ile imtihanı :
PVC hammaddesinin yangını üst katlara taşıdığı, yangın sırasında tuz ruhu ve dioksin salgıladığı ve bu nedenle tehlikeli olduğu şeklinde çok yanlış bir inanış vardır. Her yangın çeşidinde yangınla birlikte oluşan gazlar yanan malzemenin cinsine göre toksin emisyonu yaparlar. İnsanlar, bir yangın sırasında tamamen yanmayan ürünlerin ortaya çıkardığı Karbon Monoksitten(CO) zehirlenirler. Karbon monoksit, kokusuz ve çok zehirli bir madde olduğu için insanlar daha karbonmonoksitin varlığını fark edemeden zehirlenmiş olurlar. Ancak PVC hammaddesi erime noktası çok düşük olduğu için hemen tamamen yanar ve PVC'nin yanmasından HCL (Tuz ruhu) açığa çıkar. Yani yangın sırasında insanların zehirlenmesine yol açan Karbon Monoksit gazı PVC hammaddesinin yanmasından oluşmaz. PVC'nin yanması sırasında ortaya çıkan tuz ruhu, aslında zehirleyici bir maddedir. Ancak çok keskin bir kokusu olduğu için 5 PPM gibi çok çok az miktarda bile ortamda bulunmasını insanlar algılarlar ve hemen ortamdan uzaklaşarak zehirlenmekten kurtulurlar.
Bu özelliğiyle PVC hammaddesinin yanması esnasında oluşan bu tuz ruhu aslinda bir yangının haber olarak insanları uyarır.
Bilindiği üzere, teneffüs ettiğimiz havanın içinde %21 oranında serbest oksijen vardır. % 21 den daha az oksijen bulunan ortamda yanabilen maddeler ‘YANICI’ maddeler sınıfına girmektedirler.
Odunun kendiliğinden tutma sıcaklığı 280 °C iken PVC hammaddesinin kendiliğinden tutuşabilmesi için ortam sıcaklığının 450 °C olması gerekir.
PVC hammaddesi, UL 94 yanici maddeler sınıflandırmasına göre CLASS V0 olarak en az tutuşma özelliğine sahip plastik hammaddesi olarak belirlenmiştir.
Aynı şekilde, DIN 4102 Standardi inşaat malzemelerini yanıcılık özelliklerine göre A (Yanıcı olmayan) ve B (Yanıcı) olarak 2 gruba ayırmıştır. Bu standart, Polipropilen ve Polietilen malzemelerini B2 sınıfında (normal yanıcı) olarak gösterirken, PVC'yi B1 (alev söndürücü Flame Retardant) olarak göstermektedir.
Odun yandığı zaman PVC malzemeden üç misli daha fazla ısı yayar.
Bütün plastikten mamül malzemeler gibi, eğer PVC malzemeyi açık aleve tutarsanız PVC malzeme de yanar. Ancak alevi çekerseniz yanma hemen duracaktır. Bunun nedeni, PVC yandığında Hidroklorür (TUZ RUHU) gazı ortaya çıkar ve yanma bölgesinde oksijen miktarını azaltarak hemen durdurur.
PVC hammaddesi içinde en fazla miktarda bulunan Klor maddesi yanmayan bir maddedir.
PVC hammaddesi eğer açık aleve doğrudan tutulmazsa kesinlikle yanmaz. Bu nedenle, Pvc borular, evlerde meydana gelen yangının üst katlara yayılmasında hiçbir katkı yapmaz.
PVC boru ömürleri :
PVC den mamul boru ve ek parçaları kimyasallara ve ağır kullanım ve depolama şartlarına karşı çok iyi direnç gösterirler. Aynı şekilde, kötü hava şartlarında, direkt güneş ışığı altında, yağmur ve rüzgar altında uzun süre durmaktan etkilenmez.
Çünkü, PVC hammaddesinin kimyasal yapısı amorf yapıdır. Yani PVC hammaddesi birbiri içine girmiş bağlardan oluşmuştur.
PVC kristal yapıya sahip değildir. Yani Polietilen ve Polipropilen gibi kırılgan değildir. Ancak %80 oranında kristal yapıya sahiptir.
Kristal yapı ne kadar çok olursa, ürün güneşe karşı dayanımını yitirir ve kırılganlaşır.
Çünkü, Güneş ışığı altında kaldığında Polietilen ve Polipropile gibi hammaddeler içinde moleküller birbirine paralel bağlar ile bağlanır.
PVC hammaddesinde ise moleküller birbirine düzensiz ve birbiri içine girmiş(amorf) bir şekilde bağlanmışlardır ve kristal yapıya sahip değildirler. Bu nedenle PVC baglarını kırmak Polietilen’e göre daha zordur.
Bu nedenle PVC hammaddesinden yapılan boru ve ek parçaları aynı şartlarda Polietilen ve Polipropilen borulara gore çok daha fazla dayanım ömrüne sahiptirler.
Eğer Polietilen ve Polipropilenden mamul boruları güneş ışıgı altında uzun süre bekletirseniz, kristalleşme devam eder ve boru üzerinde boydan boya yarılmalar oluşur. Bu kristal yapıdan ötürü meydana gelir.
Bu nedenle Polietilen hammaddesi içine güneş ışığı altında kristalleşmeyi önlemek için Karbon siyahı denilen maddeden %2.5 oranında koymak gerekir. Karbon siyahı konulmayan hammaddeden imal edilen polietilen hammaddesinden boru yapılırsa bu borular güneş ışığı altında boydan boya yarılacaktır. Aynı şartlarda PVC borulara hiçbir şey olmaz
Sıcaklık arttıkça, PVC Boruların basınç dayanımı azalır.
PVC borular 20°C da 25 yıl 16 bar basınca dayanırken, sıcaklık 40°C’a çıktığında 10 bar basınca dayanabilmektedirler.
Polietilen borular MRS 10MPa ve Polipropilen borular MRS 8MPa değerine sahipken PVC borular MRS 25MPa değerine sahiptir.
Yani aynı çap ve et kalınlığında ve aynı kullanım sıcaklığında PVC borular Polietilen ve Polipropilen borulardan çok daha yüksek basınca dayanırlar.
ABS ( Acrylonitrile Butadiene Styrene )

Acrylonitrile
Butadiene

styrene
Thanks to its strong and durable structure even at low temperatures, it has good resistance to heat and chemicals and is easy to process. It is resistant to high impacts. Breakage after impact is ductile. It is resistant to high temperature and flame. If it is exposed to the sun for a long time, its color, impact resistance and ductility decrease. It is a triple copolymer and has high strength and toughness. It is resistant to external and chemical effects. Tensile strength is 42-50Mpa, specific gravity is 1.05-1.07 Mg / m³, they have no elasticity module and they can withstand temperatures up to 75 ° C. They are used in the production of pipes, auto parts, electronic device cabinets and refrigerator parts.
ABS plastic is a terpolymer formed by the polymerization process of styrene and acrylonitrile in the presence of polybutadiene. Usually the composition contains half the amount of styrene and the balance is split between acrylonitrile and butadiene.
ABS Plastic is a common form of thermoplastic that has been available since 1940 and has become the most popular engineering polymer today. Acrylonitrile is a copolymer of Butadiene and Styrene and generally of medium strength.
It is a terpolymer consisting of three different monomers. It is hard, rigid and has good chemical resistance.
Acrylonitrile Butadiene The three monomers involved in the formation of styrene play a different role in the performance of the material because acrylonitrile provides chemical and thermal stability to the polymer, increases the butadiene durability and strength, and styrene finally gives a beautiful and shiny finish.
It is considered to be the best of the styrenic polymer family due to its toughness and rigidity combined with strong chemical resistance and stability.
It can be applied in various end-segment consumer products such as household appliances (refrigerator, washing machine, etc.), luggage, camera bodies, tool boxes, battery boxes, packaging cases, radio, various furniture parts.
It is a strong and durable material with high melting point. This Polymer has been manufactured to meet the specific requirements of its primary customers based on its qualities. By changing the ratio of the basic three monomers (Acrylonitrile Butadiene Styrene) of the ABS material, different derivatives can be obtained, the density of which can be changed according to usage.
The main properties of this material are as follows:
-
Excellent resistance to chemicals and different plasticizers.
-
They offer medium strength and can be tough, tough or tough depending on their use.
-
Acrylonitrile butadiene styrene materials have high tensile and impact strength as well as hardness.
-
These resins show excellent performance even at high and low temperatures.
-
They provide dimensional stability and outstanding formability.
-
Acrylonitrile butadiene styrene polymers are electroplable and offer creep resistance
-
They have high ductility.
-
It is easily available at low cost.
-
Tensile strength 46 MPA (6600 PSI) and notched impact strength 10 - 20 Kj / m2
-
Thermal expansion coefficient 70 - 90 * 10-6
-
Use a maximum Resume temperature of 80 - 95 ° C
-
Density 1.0 - 1.05g / cm3
-
Glass transition 105 ° C (221 ° F)
-
ABS resins offer excellent resistance to Dilute Acids and Dilute Alkalis.
-
Its resistance to oil and grease is very good.
-
ABS polymers offer moderate resistance to Aliphatic Hydrocarbons
-
They are poorly resistant to Aromatic Hydrocarbons, Halogenated Hydrocarbons and Alcohols.
-
Besides being a tough and rigid material, it has high impact resistance,
-
Having good electrical properties,
-
Good chemical resistance,
-
Easy to process,
-
It is easy to manufacture and can be dyed,
-
It is a light material.
Acrylonitrile butadiene styrene is usually polymerized from acrylonitrile, butadiene and styrene through the emulsion process. Acrylonitrile is a synthetic monomer produced from propylene and ammonia; Butadiene is a petroleum hydrocarbon derived from the C4 fraction of the steam-cleaved styrene monomer, made by the dehydrogenation of ethyl benzene, a hydrocarbon obtained in the reaction of ethylene and benzene. It can also be formed by a patented process known as continuous mass polymerization.
The emulsion process has been globally chosen to derive acrylonitrile butadiene styrene, where the nitrile group of acrylonitrile monomers develop a kind of polar affinity with each other and helps to contribute to the toughness of the polymer.
Also, the presence of polybutadiene provides physical strength to the plastic product through a general rubber hardening process. Due to the large number of rubbery polybutadiene particles interspersed, the material can absorb more mechanical energy and be plastically deformed without breaking.
Because it is thermoplastic, it means it can be easily processed under different temperature conditions. When it can be heated, it is allowed to cool and can then be reheated to form other plastic shapes without any distortion.
Processing plastics at different temperatures improves their basic properties. Processing of acrylonitrile butadiene styrene at high temperatures gives the product a better look and finish. It also increases the heat and chemical resistance capability of the material.
This polymer is a thermoplastic material that can be easily recycled and used with untreated materials to create new plastic products.
The used and commonly produced derivatives are:
-
High Gloss Acrylonitrile Butadiene Styrene,
-
Low Brightness Acrylonitrile Butadiene Styrene,
-
High Effective Acrylonitrile Butadiene Styrene,
-
General Purpose Acrylonitrile Butadiene Styrene,
-
High Flow Acrylonitrile Butadiene Styrene
-
Plate is Acrylonitrile Butadiene.
China is one of the most dominant countries in both the production and consumption of ABS plastic resins. 40% of the global total market share belongs to China. Other major regions contributing to global production include Europe 10%, North America 8%, South America 1%, and the Middle East and Africa 1%.
Leading leading companies in the market: Chi Mei, LG Chemicals, Styron, Kumho Petrochemical, INEOS Styrolution, Asahi Kasei, Sabic, China Petroleum and Chemical, Formosa plastic, Elix Polymers, BASF, Toray, Ampa, Rochling, Dow Chemicals, PolyOne.
ABS Disadvantages:
Although acrylonitrile butadiene styrene has many properties that make it a good thermoplastic, this material has a few properties that do not favor it as a plastic. It is easily flammable when exposed to high temperature fire.
Combustion of acrylonitrile butadiene styrene produces some very dangerous toxic products such as carbon monoxide and hydrogen cyanide. It also has bad weather conditions and poor solvent resistance.
-
Low solvent resistance,
-
Low elongation coefficient,
-
Continuous service temperature is low.
ABS Usage Areas:
ABS is one of the most widely used plastics and can be seen in everyday essentials such as electronics, hardware, kitchen appliances, toys, and many other end use products. The injection molding properties of these materials aid in the production of products in complex and precise shapes, such as musical instruments, medical devices, automotive parts and sporting goods. It is suitable for the production of a wide variety of products in various segments.
It is a widely used thermoplastic capable of meeting the required properties for both standard resins and engineering resins at a reasonable price. The main advantage of choosing ABS as a thermoplastic is that it is a combination of strength and hardness of acrylonitrile and styrene polymers along with the hardness of polybutadiene. It is perfectly resistant to chemicals and strongly prevents chemical degradation from any alkali and acidic agent. Their strong chemical bonding nature gives the plastic some degree of thermal stability that prevents the plastic from degrading even at very high temperatures.
Acrylonitrile butadiene styrene is a type of amorphous solid with no specific melting point. This property of ABS makes it a suitable material for injection molding to produce a range of products. Acrylonitrile butadiene styrene material proves to be advantageous because it has aesthetic appearance, makes the plastic look brighter and is easy to paint, but also offers various product manufacturing options.
ABS Filament:
Acrylonitrile butadiene styrene can be easily extruded into thin filaments and is also used as a material for 3D printers. It is the most preferred material for 3D printing because it is more durable and has the ability to withstand even higher temperatures.
This polymer is given more importance in 3D printing because of its strong, easy-to-economical properties and its ability to help modify post-printing parts, which are highly suitable for printing. Its hardness and strength, and its strong resistance to heat, is the reason for preference in the 3D printing process. Using this ABS material in this process provides a beautiful and smooth finish to the end product. ABS is primarily used for 3D printing by professionals, hobbyists, and educators. Models, concept models and figures, all kinds of gadgets, etc. It has been an ideal choice for 3D filament used for printing.
ABS Pipes:
Plastic pipes are widely used in both developed and developing countries. Growing infrastructure activities have accelerated the demand for plastic pipes worldwide. Plastic pipes are inexpensive, lightweight and non-corrosive.
They can keep hot water warm and won't condense from cold water like metal pipes. Plastic tubing generally consists of two commonly used plastic materials: acrylonitrile butadiene styrene (ABS) and polyvinyl chloride (PVC).
ABS pipes are widely used in construction and infrastructure development activities as they are easier and cheaper to install, provide smooth flow, are lightweight, do not rust or wear easily, are resistant to mechanical damage, can easily sustain and even withstand temperature changes.
Properties of ABS Plastic Piping Systems
-
It is easier to install and cheaper than metal pipe systems.
-
Acrylonitrile butadiene styrene pipes provide excellent flow thanks to the smooth inner coating.
-
They are resistant to mechanical or chemical damage.
-
They are lightweight and will not rust or corrode.
-
It can perform well even in strange temperatures.
ABS Sheet, Sheet:
Acrylonitrile butadiene styrene material is also widely used in plastic sheet manufacturing. These plates are used to produce a variety of products for the final segment plastics market. ABS can be easily thermoformed to the mold for production.
This material is used in sheet production as it offers exceptional formability, high tensile strength and hardness, easy ductility, and is also resistant to many chemicals and plasticizers.
These sheets are also used for aircraft interior trim, cassette holders, boxes and trays made of plastic, automotive parts, electronics and luggage, etc. It can also be used in the production of products. Acrylonitrile butadiene styrene plastic coating consists of two types; Black plastic wrap and White plastic wrap. As black plastic sheeting, white ABS sheets are widely used for automotive, electronics and other end segment plastic products used in everyday life, black plastic sheeting is mainly used in gardens, furniture and flooring, so it is made to better suit their application. The properties of ABS sheets and sheets are as follows;
-
These layers offer excellent chemical and stress cracking resistance.
-
Acrylonitrile butadiene styrene provides products with a smooth and shiny finish.
-
Black plates are resistant to UV rays, white plates are not.
-
ABS plastic sheets have good impact resistance, formability, hardness and toughness according to the demands of their users.
-
They have high tensile and impact strength.
-
Excellent performance at high and low temperatures.
-
High Ductility.
-
It lends easily to the dielectric source.
-
Resistant to chemicals and plasticizers
-
Exceptional formability.
MABS (Methyl-methacrylate Acrylonitrile Butadiene Styrene):
Compared to ABS, MABS has a more homogeneous polymerization, better melt processability, a lighter color and more stability against ultraviolet light. In addition, MABS has a lower heat distortion temperature. Medical containers and components. Parts and components for copiers and printers are mostly application areas.
-
It has excellent transparency
-
Has high impact resistance
-
Good chemical resistance
-
Used for injection molding, blow molding and extrusion processes
-
High preference for dye and printing

PS (PolyStyrene)
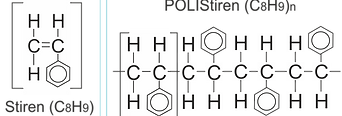
It was originally discovered by Eduard Simon, a pharmacist from Berlin. sweet gum tree Liquidambar styrene resin is a fatty substance given name was storaks from the distillery in Turkey. After a few days of discovery, Simon found that the styrene produced from the monomer thickened due to oxidation to form a gel called "Styroloxyd".
In 1845, chemist John Blyth and another German chemist August Wilhelm Von Hofmann represented the same conversion of styrene in the absence of oxygen. This substance was named "metastyrol". Later analysis showed that the chemical properties of both substances produced were the same.
Later, in 1866, Marcelin Berthelot rightly analyzed the formation of metathyrol / meal from styrene by the polymerization process.
After 80 years of time lag, it was discovered, based on the thesis of the German organic chemist "Hermann Staudinger (1881-1965)", that heating the styrene led to a chain reaction producing several macromolecules called PS plastics.
This plastic has an amorphous structure. It has a bright and clear image. It had a type called expanding polystyrene, which is very suitable for energy absorption. It is very resistant to food and drink. Many as buttons, light switches, bottles, cups, CD and DVD lids, and packaging material.
used. It is also possible to produce polystyrene foam. Polystyrene, which has a very wide usage area, is a cheap and hard thermoplastic polymer. In fact, we can say that it is the most used plastic after polyethylene. Polystyrene, which has an aromatic polymer chain, is synthesized from aromatic styrene monomer. Styrene monomer is a liquid hydrocarbon molecule produced by the petrochemical industry. It is one of the most common plastics in our daily life. It is a modification of polyethylene. It contains a benzene ring inside the polyethylene chain.
Glass clear, easy to color, bright hard surface, solid and crisp, tasteless and odorless, very good electrical properties, weldable, brittle, but easily processed and cheap. It is easily flammable and continues to burn brightly outside of the flame. It has a sweet scent that does the job strongly. It is a good insulating foil for building elements used in electronics. Foamed (styropor) is used in heat and sound insulation, shaped foamed PS packaging, mold model casting and steel concrete structures, toys, kitchenware.
Monomer is a synthetic polymer made of styrene. PS is made by polymerization of styrene, a type of building block material used to produce various plastic products. It also occurs naturally (strawberry, cinnamon, coffee, and beer).
This plastic polymer is a natural transparent thermoplastic available in both solid and rigid foam material. Generally used PS material is clear, hard and fragile in terms of its properties. Plastic is widely used to produce a variety of end-segment products. The solid form of plastic is widely used to produce products that require clarity. These are usually electronic devices, auto parts, garden pots, equipment, etc., with a combination of colorants, additives, and other forms of plastic. It is used to produce such products.
PS is made of foam material and is called Expanded Polystyrene (EPS) or Extruded Polystyrene (XPS), which are known for their insulating and cushioning properties. The solid form of this material is widely used for medical device applications, daily items such as smoke detectors, CDs, food containers, coffee cups. The foam form of the polymer is also widely preferred as a packaging material for various products.
It is produced by the polymerization process like other plastic polymers. This polymer occurs when styrene monomers bond with each other during polymerization. In this process, the carbon bond of the vinyl group is broken and forms a new carbon bond, as well as to the carbon of another styrene monomer in the chain. The newly formed bond is much stronger than the previous one, so it becomes difficult to de-polymerize the polymer. First of all, it is produced in two different forms:
-
Atactic PS: It is an important commercially produced PS form. Atactic PS is randomly distributed on both sides of the polymer chain to produce phenyl groups. This random positioning prevents the chains from aligning and provides enough regularity to achieve the desired crystallinity. This plastic polymer has a glass transition temperature of 90 ° C and the polymerization process is strongly initiated by free radicals.
-
The "Ziegler-Natta polymerization" process is used to produce syndiotactic PS. In this polymerization process, phenyl groups are placed on alternative sides of the hydrocarbon backbone. This is a highly crystalline form of PS polymer produced with a transition temperature of 270 ° C. These PS types are currently produced under the brand name XAREC by Idemitsu Corporation using metallocene catalyst for the polymerization reaction.
Generally, four polymerization processes and three foaming methods are used in polymer production. The three processes initially used are Mass Suspension, Emulsion and Solution Polymerization.
The second is closed mold foaming of EPS, EPS extrusion and direct injection extrusion of GPPS.
It is a process in which styrene is obtained by dehydrogenation from benzene, ethylbenzene by alkylation reaction and ethylbenzene. Benzene and ethylene are reacted with a heterogeneous catalyst in a reactor with recirculating ethylbenzene. The reactor outlet is separated from unreacted benzene in a pre-fractionation column and passes from the bottom to the crude ethylbenzene distillation system. The benzene from the top returns to the reactor. In the distillation unit, the benzene, ethylbenzene and the heavy in the crude ethylbenzene mixture are separated from each other. The heavy is distilled again and the drawn polyethylbenzene is returned to the reactor. The purity of the obtained ethylbenzene is suitable for polymerization-purity styrene production. In the styrene production section, fresh ethylbenzene, returning ethylbenzene and superheated steam are taken into the dehydrogenation reactor inside the catalyst. The effective variables controlling the yield are reaction pressure and temperature.
There are three columns in the section where the styrene monomer is obtained. The small amount of benzene and toluene formed by cracking in the dehydrogenation reactor is removed in the first column and returned to the ethylbenzene system. In the second column the styrene is separated from the ethylbenzene fed to the reactor; a high-efficiency column is used here. In the third column, called the finishing column, the styrene monomer is cleaned from the small amounts of tar and polymer generated during the processes. In distillations, a sulfur-free inhibitor is used to minimize polymer formation. There are no streams to pollute the environment.
PS Key Features:
It is a versatile form of plastic used to make a variety of end-segment plastic products. PS polymer is a type of clear, amorphous, non-polar material that can be easily processed and transformed into a large number of semi-finished products such as foams, films, and sheets. In terms of volume, it is one of the largest plastics used due to its properties such as:
-
It has high impact and heat resistance.
-
These polymers are a good electrical insulator with excellent optical clarity.
-
PS has strong chemical resistance to diluted acids and bases.
-
It is a viscous liquid above the temperature of glass and provides easy fabrication to many finished products.
-
They can be easily expanded and allow good flow.
-
These materials are inherently strong flame retardant.
-
Chemical formula used for PS (C8H8) n
-
Density - 0.96--1.04 g / cm3
-
Melting point is ~ 240 ° C (464 ° F; 513 K) [4] For isotactic PS
-
Solubility in water insoluble
-
Solubility - Insoluble in acetone
-
Thermal conductivity of the polymer 0.033 W / (M K) (foam, ρ 0.05 g / cm3)
-
The refractive index is 1.6; dielectric constant 2.6 (1 kHz - 1 GHz)
-
It is flammable, but delayed versions are also available.
-
It has poor solvent resistance and can be attacked by many chemicals.
-
Homo-polymers are fragile in nature.
-
It is subject to stress and environmental cracking.
-
They have poor thermal stability.
PS Usage Areas:
It can be applied to various end-user industries to produce a range of goods in different formats. It has become the most widely used polymer in various industries such as:
-
White goods - Used in a range of appliances such as refrigerators, air conditioners, ovens, microwaves, vacuum cleaners and mixers, it is cost-effective and long-lasting.
-
Automotive - PS (solid and foam) is used in the production of many automotive parts, including buttons, instrument panels, trim, energy-absorbing door panels and even sound-damping foam.
-
Electronics - Used in residential and other parts of televisions, computers and different IT equipment where a combination of form, function and aesthetics is required.
-
Food Service - PS has a significant share in the packaging industry compared to its competitors. It is widely used in food packaging as it insulates better, keeps food fresh for a long time and is cost effective.
-
Insulation - Lightweight PS foam proves to be excellent thermal insulation in a range of applications such as building walls, roofing, refrigeration, freezers and even industrial cold storage facilities. It is preferred for insulation because it is more inert, durable and resistant to water damage.
-
Medical - Because of its clarity and ease of sterilization, PS is used for a wide variety of medical uses, including tissue culture trays, test tubes, petri dishes, diagnostic components and other medical test equipment.
-
Packaging - It is a widely used and preferred material in the packaging industry. CD and DVD boxes, foam packaging nuts for goods shipping, consumable packaging, meat and poultry trays, as well as egg cartons, etc. It is widely used to protect consumer products such as.
GPPS (General Properties PolyStyrene):
Also referred to as general purpose crystal clear PS. This form of plastic is completely transparent, rigid and low-cost PS, usually made from styrene monomer. GPPS is a solid form of PS produced in the form of 2-5mm PS pellets. General use polystyrene is relatively strong and weather resistant. It flows easily and makes it suitable for molding in the manufacture of products such as toys, CD-DVD cases and plastic cups. It has a clear and bright appearance.
-
Although relatively brittle, it has good tensile strength
-
Increases productivity thanks to a good balance of flow, heat and molding
-
It is fragile and tough.
-
Is transparent
-
Shows low withdrawal
-
Low cost
-
It has excellent X-ray resistance.
-
It is odorless and tasteless
-
It is easy to process.
Technical values and more usage areas of some PS brand raw materials:

HIPS (High Impact Polystyrene):
High impact polystyrene (HIPS) is more commonly known in the market as (Antishock). It consists of PS and rubber and is therefore opaque and white. It is a versatile, economical and impact resistant plastic that is easy to process and manufacture. It is often used in the processing of pre-production prototypes, as it has excellent dimensional stability and is easy to manufacture, paint and stick. Consumer products such as devices, toys, TV and audio-visual equipment components, instrument panels and accessories in the automotive industry, petrol tanks, Thermoformed plates production are the areas of use.
-
It is solid and tough.
-
Is translucent
-
It has good impact resistance
-
Perfect for processing
-
Shows good dimensional stability
-
It has excellent aesthetic quality
-
Easy to paint and stick
-
Easy to weld ultrasonically
EPS (Expanded PolyStyrene):
It is a kind of rigid and rigid foam. It is generally white in appearance and is produced from pre-expanded PS beads. EPS is one of the most commonly used PS foams in daily life. White foam is often used in hot drinks, refrigerators, insulation and packaging, etc. Is used.
EPS material is cheap and light. It does not lose its basic properties over time and is completely recycled and reused to maintain environmental balance. Due to its positive technical and physical properties such as low weight, hardness and formability, EPS has been introduced for a wide variety of applications. It is even used in the production of molded boards used for building insulation and packaging materials.
EPS is generally used in the form of foam. The word "Styrofoam" is often used to describe EPS foam. This is a kind of trademark used for foam material. The most common foam products used in daily life are cups used in different places for coolers, wine haulers, molded end caps and corners, packaging of boxes, and even water coolers.
It is made of styrene monomer. It is primarily a derivative of ethylene and benzene and is produced using a polymerization process that produces spherical polystyrene beds. Low boiling hydrocarbon (pentane gas) is often added during the process to assist in the expansion of the material.
Produced in three stages
-
Pre-Expansion - When in contact with the steam, the pre-foaming agent in the polystyrene bead begins to boil and the beads expand 40 to 50 times their original volume.
-
Conditioning - After the expansion process, the beads go through a further maturation process to achieve temperature and pressure equilibrium.
-
Molding - The beads are then placed in a mold and reheated with steam. The pre-foamed beads expand further to completely fill the mold cavity and fuse together.
Two molding processes used in EPS production
-
Black Molding - Used to produce large EPS blocks that can be cut and reshaped even more easily according to user demand. These blocks are used in both packaging and construction applications.
-
Shape Molding - It is used to produce parts that require special design features. Generally, this process is used for electronic product packaging where shape molded EPS is largely used.
EPS has been the preferred thermoplastic material for more than half a century due to its performance, technical versatility and cost effectiveness. It is widely used in daily practice. Its lightness, strength, thermal insulation, durability and other properties make it suitable for a range of applications.
-
Lightness. It is an extremely light material as it contains ~ 95% air. This feature makes it a suitable material for the packaging industry as it does not add weight to the product and reduces shipping costs.
-
Durability. The durability of this material provides the effective and reliable form of plastic used for packaging a variety of goods. It is odorless and non-toxic in nature, and its cellular structure makes it more dimensionally stable. This adds value to the product life.
-
Moisture Resistance. It is a closed cell material and does not absorb water easily. EPS is an ideal material for cold chain products as it does not lose its strength even in humid conditions. Since the material is resistant to high humidity, the hygiene requirement is easily met. Due to this feature, it is also used for fishing in buoys and marina buoys. Even if this material is subjected to saturation in water for a long time, it balances with some decrease in its thermal performance to maintain its size, shape, structure and physical appearance.
-
Shock Absorption. It offers an excellent shock absorbing property making it the first choice of packaging material for many products, including appliances, electronics, computers and chemicals.
-
Thermal Efficiency. The high thermal efficiency of EPS material is very helpful in packaging temperature sensitive products. Products stored in EPS containers have a longer life, even at temperatures below or below ambient conditions. It protects the product even from sudden temperature and climate change during transportation. Examples of temperature sensitive products that require EPS containers include seafood, fresh produce, medicines, and a variety of medicinal products.
-
Versatility. Since it can be easily cut and shaped according to the needs, it can be used to produce almost any shape and size. In addition, it is produced in various densities with different physical properties according to the needs of the product. Its compatibility with a large number of products also helps to increase its value from other alternatives.
-
Ease of Use. EPS is considered to be the easiest material to use, especially in the construction industry. Normally available in sheets that can be easily molded into shapes or large form blocks as per need.
-
Density, lb./cu.ft. - 0
-
Compressive strength, psi. - 31-37
-
Tensile strength, psi - 58-61
-
Thermal resistance, R / in. - 2nd
-
Dielectric strength is about 2KV / mm. At frequencies up to 400 MHz, the permeability offered by the material is 1.02-1.04 and the loss factor is less than 5 × 10-4 at 1 MHz and less than 3 × 10-5 at 400 MHz.
-
It is highly resistant to water and aqueous solutions of salts, acids and alkalis. Generally incompatible with organic solvents. UV radiation up to 120-140F has a slight effect on the molded material form. It usually causes the material to yellow but does not affect its physical properties.
-
Provides long-term and stable R-Value.
-
Avoid the growth of mold or mildew.
-
They can be easily recycled.
-
EPS insulation materials can be placed under the classroom.
-
They can also be used for inverted assemblies.
-
Exposure to the sun can spoil the product.
-
Solvent-based materials can cause serious damage.
-
Temperatures above 250 degrees Fahrenheit can melt polystyrene.
-
They are incompatible with certain types of thermoplastics that can cause permanent degradation.
-
It is flammable and requires proper placement.
XPS (eXtruded PolyStyrene):
It is another form of foam that offers improved surface roughness and higher hardness with reduced thermal conductivity. The chemical composition is almost the same type as this EPS, but it is produced with a different technology. EPS, pink, blue and green etc. It is in three basic colors. It is generally used for promotional panels and construction sites.
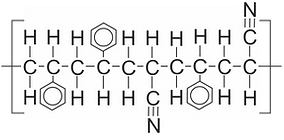
SAN (Styrene AcryloNitrile)
It has been available since the 1940s and was first released in 1950. Its increased toughness relative to the individual styrene made it applicable for a variety of uses. Also, the limitations of SAN led to the use of butadiene (rubber) as a third monomer and triggered the production of ABS (Acrylonitrile-Butadiene-Styrene).
This copolymer plastic resin is a hard, transparent plastic produced by the co-polymerization of styrene and acrylonitrile. It is a combination of the hardness, strength and solvent resistance of polyacrylonitrile with the clarity and hardness of polystyrene.
Styrene-based materials offer excellent qualities such as durability, high performance, versatility of design, ease of manufacture and economy. SAN products provide good hygiene, sanitation, and safety benefits. They also provide good insulation and can also be easily recycled.
It has very good chemical resistance. It is very transparent and has a nice shine. It provides a suitable choice for cosmetic materials. SAN is slightly yellow in color, but also available in different colored variations. While the standard SAN is not suitable for outdoor use, there are also UV resistant grades. Used in refrigerator parts, shelf dividers, light covers, cosmetic packaging, kitchen supplies, automotive parts, battery boxes, kitchenware, home appliances, furniture and medical supplies. It is often used instead of polystyrene due to its higher thermal resistance.
SAN consists of 70 to 30 units of two units, styrene units and acrylonitrile units. These two compounds are mixed in bulk liquid form or as a solution of water-based emulsion or suspension.
The polymerization process of these compounds is carried out under the influence of free radical initiators. The plastic material obtained from this process resists heat and solvents better than a single form of polystyrene.
Major companies producing SAN resins are Samsung Cheil Industries, Chi Mei, INEOS, China National Petroleum, SABIC Innovative Plastics, Toray Industries, Formosa Plastics, Styron, Techno-Polymer, and Petro China.
SAN Key Features:
SAN resins have a similar use to polystyrene. Like polystyrene, these are optically transparent, brittle and have mechanical behavior. Some of the main properties exhibited by this co-polymer are as follows:
-
It shows high strength and chemical resistance.
-
Provides good flow and dimensional stability.
-
It is extremely resistant to heat.
-
It allows good flow.
-
It is resistant to stress, oil and food stains.
-
It has a glass transition temperature above 100 ° C.
-
It is used for general purpose.
-
Its Tensile Strength is 3.40 - 3.90 N / mm² and its Notched Impact Strength is 250 Kj / m².
-
Thermal expansion coefficient 70 x 10-6
-
Maximum Continuous Use Temperature for SAN is 55 ° C
-
Density 1.08 g / cm 3
-
It is extremely resistant to dilute acids and alkalis.
-
It exhibits very good resistance to oil and grease.
-
Moderately resistant to aliphatic Hydrocarbons and alcohols.
-
These resins have poor resistance to Aromatic Hydrocarbons and Halogenated Hydrocarbons.
-
It has improved chemical resistance compared to polystyrene.
-
It provides better toughness and hardness to the products produced.
-
These polymers are dimensionally stable.
-
They offer ease of processing.
-
It is highly resistant to chemicals and stress cracking.
-
It absorbs higher water compared to polystyrene.
-
It shows lower thermal capacity and impact resistance.
-
It requires high processing temperature.
-
It quickly turns yellow and is flammable with high smoke generation.
-
It has been diagnosed as one of the causes of cancer. It is carcinogenic.
SAN Usage Areas:
Styrene Acrylonitrile can be applied to a number of uses in various industries. Polystyrene is generally preferred for its better properties. These resins are used in different end segment markets including:
-
They are used in televisions, cables, radios, air conditioners, computers and other people using electronic devices.
-
It is used in the production and packaging of various household items such as detergents, containers, clothes, toothbrushes and bathroom fixtures.
-
SAN used a large plastic polymer for packaging cosmetics such as compact boxes and lipstick tubes.
-
Automotive trim, tractor components, automotive tool lenses and battery cases etc. It is widely used in the manufacture of automotive parts, including.
-
SAN resins are used in the manufacture of fixed products that are widely used daily, such as weighing scales, calculators, printers, writing and drawing equipment.
-
The physical and mechanical properties of SAN polymers make them suitable for manufacturing a variety of general use products such as bottle caps, rotary switches, dust caps, marine appliances and personal care products packaging.

PET (PolyEthylene Terephthalate)
PET was first found in the US in the mid-1940s, when researchers were looking for polymers that could be used to make new textile polymers. Later, these polyesters were branded as "Dacron" by DuPont.
In the late 1950s, researchers found the method of stretching a thin extruded PET sheet to create films that are now commonly used as X-ray or photographic films.
Polyethylene terephthalate, which accounts for 18% of plastic production in the world, ranks third after polyethylene and polypropylene. PET, which is in the polyester group, is a linear thermoplastic polymer and is mostly encountered in areas such as synthetic fiber, food packaging industry and especially bottling. Polyethylene Terephthalate, commonly known as PET or PETE, is the most widely used polymer in the world. It is naturally transparent and semi-crystalline plastic that is widely used for products used in our daily life. PET polymer is called "Polyester" in the textile industry. It is widely used as a fiber for garments as it has an excellent moisture barrier and is also used for large scale bottling and packaging. The biggest share of PET plastic produced is synthetic fiber with 60%, bottle and box with 30%. PET material consists of polymerized monomer ethylene terephthalate units, and when these PET materials are combined with other materials such as glass fiber or carbon nanotubes, their strength increases. As a raw material, PET is recognized as a safe, strong, lightweight, flexible and non-toxic material that can be easily recycled.
PET plastic has become the world's choice in the packaging industry. It stands out in the packaging of many foods and beverages because it is hygienic, strong, light, and preserves the freshness of the products and does not break down. It is mostly used in the packaging of water and carbonated soft drinks.
Polyethylene Terephthalate (PET) is mainly produced by polymerization of ethylene glycol and terephthalic acid. Ethylene glycol and terephthalic acid are considered as building blocks for PET resin. In addition, these resins are heated to a molten liquid that can be easily molded into parts of any shape. The presence of large benzene rings in the process adds hardness and strength to the PET polymer, especially when the polymer chains are aligned with each other.
To be more specific, when the two raw materials of PET-ethylene glycol and terephthalic acid are combined with low vacuum pressure and high temperatures, long chains of the polymer are formed. As the mixture thickens, longer chains are formed and the process is stopped when the suitable chain is obtained. Also, when PET polymer is kept in starch form at different temperatures, it starts to crystallize and become opaque and harder. This crystallized form of PET is used to prepare other products such as containers and trays that can be reheated.
The world PET resin production capacity is over 30 million tons. Chinese manufacturers make 32% of the global total production. China is not only the world's largest producer of PET resin, but also its largest consumer.
PET Basic Features:
PET plastics are engineering plastics with high strength and hardness for a wide variety of applications. It is a thermoplastic that is widely used especially in the packaging and textile industry.
-
It shows good heat resistance and low creep even at high temperatures.
-
It has good stability due to low water absorption.
-
It has low water absorption. (Excluding nylon stockings)
-
It exhibits excellent resistance to chemicals.
-
It has good color stability and wear properties.
-
Tensile Strength 2.5 N / mm and Impact Strength 1.5 - 3.5 KJ / m
-
Thermal expansion coefficient 70 * 10.6
-
Density 1.37 g / cm
-
Polymers are readily available and inexpensive
-
PET polymers are highly resistant to moisture and chemical resistant to organic material and water.
-
It has a high strength / weight ratio.
-
It is highly transparent and unbreakable (does not break like glass packaging).
-
PET materials come in a variety of shapes and colors offering a good choice in producing attractive products.
-
Polyethylene terephthalate can be easily recycled. PET plastic is one of the most recycled plastics and they are reused to make products such as containers, sleeping bag insulation, polyester fabrics, and carpets.
-
Compared to other polymers, PET polymer has lower heat resistance.
-
PET resins are sensitive even to oxidation. For example, they are not used to store beer or wine because these drinks have a long shelf life, so some sort of off-taste may occur.
-
PET plastics are not biodegradable and can be good or bad depending on their use.
PET Usage Areas:
PET Resins are performance polymers. They offer a wide range of applications in the end-segment markets. PET plastic stands out in markets such as Transportation, Automotive, Electrical / Electronics, White Goods, Packaging and Textiles.
Since PET material is an excellent water and moisture barrier, it is widely used in the packaging industry, especially for consumable packaging (water bottles, soft drinks, packaged foods). The high mechanical strength of the polymer enables PET films to be used in tape applications such as a carrier for magnetic tape or backing for pressure sensitive adhesive tapes. Crystallized PET plastics are used to make trays that can withstand both freezing and baking temperatures.
PET resins are heated into a molten liquid and then easily extruded into the desired shape. PET resins made with the combination of glass particles or fibers are more durable and stronger. These resins are used in different sectors according to the needs of the product. Some of the prominent and large-scale applications of PET plastic are:
3D Printing:
Polyethylene terephthalate is a strong and flexible polymer that is well suited for 3D printing. 3D printing requires a combination of flexibility and toughness that can be easily achieved with PET resins. PET is commonly known to emit less odor than any other material such as Acrylonitrile Butadiene Styrene (ABS) or Polylactic Acid (PLA) used for 3D Printing.
Injection Molding:
Polyethylene terephthalate is widely used in plastic injection molding techniques in the form of pellets to produce products with complex shapes. Since PET is hygroscopic, it must be dried before being used in the molding machine. Shrinkage in PET plastic is low, but it also depends on a number of factors such as temperature, holding time, mold wall thickness, mold temperatures and the type of additives used.
CNC Machining:
PET material is widely used as sheet stocks for CNC machines. The CNC machine is used to produce a large number of products where PET material is used as a basic material in the production process.
PET Film and Sheet:
Polyethylene terephthalate is primarily used to produce sheets and films that are later used in the production of plastic products. PET film and sheet are commonly used thermoplastic sheets because they offer a variety of benefits such as:
-
PET Films provide excellent chemical properties together with high barrier properties and tensile strength together with the sheets.
-
They can be easily changed into bottles or other plastic consumables.
-
They offer greater stability and break resistance to the product.
-
These films are lightweight and less expensive.
Bottle :
Most of the PET resins produced are used in the production of PET bottles. These bottles or containers are used for a wide variety of consumer products such as soft drinks, alcoholic beverages, detergents, medicines and cosmetics. PET plastic bottles made can be divided into two broad categories: Bottled water bottles and Carbonated soft drinks. Bottles made of PET resins can be easily recycled and used to produce a new product again. PET bottles are the most used plastic product in the last segment of the plastic market.
The benefits of PET bottles can be listed as follows;
-
It is lightweight, easy to carry and safe to use.
-
They can be easily resealed or recycled to produce new products.
-
PET bottles can be easily molded into different complex shapes.
-
The production of PET bottles using PET resins offers manufacturers a high level of flexibility.
-
They are inexpensive and readily available.
PET-G (PolyEthylene Terephthalate-Glycol):
It is a glycol modification of polyethylene terephthalate. PET-G is a kind of modified version of PET resin, one of the most used polymers. "G" used in PET-G means "modified with glycol" which is added to the PET material composition during the polymerization process. PET-G is clearer, less brittle and easier to use than the basic PET material. It is widely used in the production of water bottles, packaging consumables and a variety of other plastic products. PET-G is often used as a 3D printing filament as it is more durable and easier to use.
Benefits of using PET-G are as follows;
-
It is more durable and easy to use.
-
PETG is clearer and less brittle. Glycol added to PET prevents it from crystallizing and breaking.
-
It is highly durable and sealed
-
It can be easily sterilized.
MEG (MonoEthylene Glycol)
Ethylene Glycol was first prepared from ethylene glycol by saponification in 1859 by the French chemist Charles-Adolphe Wurtz. Later, the United States began semi-commercial ethylene glycol production by ethylene chlorohydrination in 1917.
The first major commercial facility for ethylene glycol production was established in 1925 by Carbide and Carbon Chemicals Co. in South Charleston. Until 1929, this material was widely used by almost all dynamite manufacturers, which led to the product being licensed for use in 1953.
Monoethylene Glycol (MEG) or ethylene glycol is commercially available major glycol. It is produced industrially from ethylene or ethylene oxide. In this MEG production process, two by-products are obtained, diethylene glycol (DEG) and triethylene glycol (TEG).
Polyester fiber used in bottle manufacturing is an important raw material for a number of industrial applications such as fabric and polyethylene terephthalate manufacturing. Other industrial uses include use as coolant, heat transfer agents, antifreeze, and also as a hydrate inhibitor in gas pipelines.
MEG is produced from ethylene via intermediate ethylene oxide. In this process, ethylene oxide reacts with water to produce ethylene glycol according to the desired chemical equation. This process is catalyzed using acids, bases or can take place at high temperatures, even at acidic or neutral pH levels. The highest amount of Ethylene Glycol can be obtained with an excess of water at acidic or neutral pH. Under these conditions, about 90% ethylene glycol can be obtained. The prominent by-products of this process are triethylene glycol, tetramethylene glycol and oligomers diethylene glycol. First of all, the ethylene glycol production process consists of the following steps:
-
Ethylene Oxide Production: In this initial stage, ethylene and oxides are fed together into a multi-tube reactor that forms ethylene oxides (EO). This exothermic reaction, carried out in fixed beds in reactor tubes, usually occurs in the gas phase (using alumina-supported silver catalyst). Steam is generated by the heat of the reaction that occurs during the process.
-
Recovery of Ethylene Oxide: The product obtained from the reactor is fed to the EO absorber to remove the lights and water. Some of the gaseous steam is recycled in the reactor and the remainder is sent to a carbon dioxide removal unit consisting of an absorber and a stripper. At this stage, the carbon dioxide is then separated for use in ethylene carbonate production. In the next stage of this process, the diluted ethylene oxide vapor is removed from the absorber to be fed to the EO stripper. Here it concentrates and saves you from overheads. The raw form of EO is finally condensed and routed to the next part of this process.
-
Production and Purification: Finally, ethylene oxide is reacted with carbon dioxide to form ethylene carbonate. It is also hydrolyzed to form MEG and carbon dioxide. Both processes are carried out in the liquid phase using a homogeneous catalyst.
World MEG production capacity is at the level of 35 million tons. About half of this is realized by Asian countries, mainly China, India and Taiwan. North America produces 6 million tons, and Europe produces 2.5 million tons in total.
MEG Key Features:
It is often referred to as ethylene glycol, which is a colorless, sweet-tasting and odorless organic compound. It is highly used for various end segment industries such as textile industry, packaging industry and others. MEG's properties such as its durability, hydrophobic properties and toughness prove it as an important raw material for a variety of industrial applications. It is widely used in the production of polyester resins, fibers and films. The physical properties of this material allow it to be used as different materials such as coolant, anti-corrosion agent, dewatering agents and chemical intermediates.
-
Chemical formula is C2H6O2
-
Appearance - Clear, colorless liquid
-
Molar mass - 62.07 gmol −1
-
Density -1.1132 g / cm 3
-
Melting point - 12.9 ° C (8.8 ° F; 260.2 K)
-
Boiling point - 197.3 ° C (387.1 ° F; 470.4 K)
-
Vapor pressure 0.06 mmHg (20 ° C) [1]
-
Viscosity - 1.61 × 10−2 Pa • s [2]
-
Solubility in water can be miscible
-
Solubility - Soluble in most organic solvents.
-
MEG is highly toxic.
-
It has a water-like structure, making it miscible with matter.
-
It is an easily available and low cost material.
-
It proves to be a great ingredient in the manufacturing industry, as it has a low freezing and high boiling point.
-
This material has good heat transfer abilities
-
MEG is a type of long-lived compound.
-
It is highly flammable and absorbs water quickly.
-
If the antifreeze leaks, there is a potential threat of burns to cars on a large scale.
-
Improper disposal of MEG, especially on airport runways, can harm the environment.
-
Its sweet taste easily attracts children and pets that can be harmful to health.
MEG Usage Area:
MEG is mainly used as a raw material in different forms to perform a number of industrial processes, including:
-
Coolant and Heat Transfer Agent - Largely ethylene glycol acts as a medium for convective heat transfer as in automobiles and liquid-cooled computers. It is widely used to transport heat in chilled water air conditioners as cooling fluid and in geothermal heat pumps as heating fluid.
-
Antifreeze - The properties of MEG break the hydrogen bond when dissolved in water. It usually freezes at -12 ° C but does not crystallize if stirred and therefore the freezing point drops. This antifreeze feature of MEG is used to de-icing liquids for windshields and aircraft. It is also used in the protection of biological tissues and organs.
-
Pioneer for Polymers - In the plastics industry, MEG is one of the major pioneers of a range of thermoplastic resins. It is highly used as a precursor for polyester fibers and resins.
-
Polyethylene Terephthalate (PET), which is used to make plastic bottles for carbonated soft drinks and bottled water, is also prepared using this material as a precursor.
-
It is used as a dehydrating agent and hydrate inhibition. As a dehydrating agent, it is used to remove water vapor from natural gas before processing in the natural gas industry.
-
As a hydrate inhibition, it is widely used to inhibit the formulation of natural gas hydrates (clathrates) in pipelines that transport natural gas from the remote gas to the processing plant. It can also be recovered with natural gas and reused as an inhibitor.
MEG Prohibited Areas:
-
Portable water Applications.
-
In the formulation of food, medicine and cosmetics.
-
Antifreeze for portable water systems in seasonal homes and recreational water systems.
-
Antifreeze for fire sprinkler systems.
Differences Between MEG and PEG:
-
Molecular Structure: Two important members of the glycol family. Both compounds have commercial application significance. The difference in both of these glycols is due to their chemical structure. Ethylene glycol is a kind of simple linear molecule while polyethylene glycol is a polymeric material.
MEG: Ethylene Glycol - molecular formula of EO (CH2-OH) 2
PEG: Polypropylene Glycol- The molecular formula of PEG is (C2H4O) n + 1H2O.
-
General features :
MEG: an odorless, colorless, sweet compound. It is an organic compound used as a raw material in polyester fiber production and antifreeze formulations. These materials can be toxic if swallowed.
PEG: is a polymeric compound used in chemical, biological, medical, industrial and commercial fields. It is a clear liquid or a water-soluble white solid with a faint odor.
-
Production Method:
MEG: a chemical compound produced using ethylene. In this process, ethylene oxide is produced as an intermediate product and reacts with water to produce EO. Acids and Bases are used as catalysts in this process.
PEG: It is produced by the reaction of ethylene oxide with water with ethylene glycol or glycol oligomers. This process also uses both acids and bases to catalyze this process. The polymerization process can be cationic or anionic depending on the use of the catalyst.
-
Usage Area:
MEG: mainly used as an antifreeze and also as a raw material in the plastic industry in the production of polyesters such as pet. It is also useful in heat transfer, especially in automotive and liquid-cooled computers. Its properties also allow it to be used in chilled water conditioning systems.
PEG: It has lower toxicity, so it is used as a lubricant coating for both aqueous and non-aqueous environments. Used as a base for many skin creams and personal lubricants. It is also used as an ingredient in toothpaste or dispenser, and also as an antifoam agent in food industry applications.
PMMA (PolyMethyl MethAcrylate)
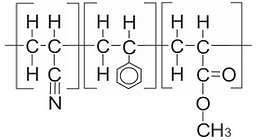
It is a non-degradable form of polyacrylate commonly used for optical components with high clarity and structural hardness. It is a colorless and transparent thermoplastic polymer, better known in the market as acrylic glass or plexiglass.
It is a synthetic resin produced by the polymerization process of methyl methacrylate. It is a transparent, rigid and transparent plastic that is widely used in the production of glass (windows, skylights, laminated signs and airplane canopies, etc.). It is generally preferred as an alternative material to glass and can be an alternative to products in which polycarbonate is used, as it has similar properties with polycarbonate. This plastic, which looks like a crystal, is resistant to weathering in the open air and is half the weight of glass, has a high impact resistance.
This material has proven to be an economical alternative to polycarbonate when tensile strength, transparency, polishing and UV resistance are more important than impact strength and resistance to chemicals and heat. Polycarbonate is preferred because it does not contain harmful bisphenol-A, a subunit found in polycarbonate materials. This resin is also advantageous over others due to its reasonable properties, ease of use and processing, and low cost.
It was first discovered by British chemists Rowland Hill and John Crawford at Imperial Chemical Industries in England in 1930 and the product was registered under the Perspex trademark.
At the same time, Otto Rohm (chemist and industrialist) in Germany worked on producing safety glass by polymerizing methacrylate between two layers of glass. As a resultant polymer, it was separated from the glass and provided a clear plastic sheet which is the trademark of Plexiglas. This product also entered the commercial market in the late 1930s.
Later in the United States, EI du Pont de Nemours & Company (now DuPont) introduced its products under the trade name Lucite and was used most frequently during World War II in the production of aircraft windows and balloon canopies for gun towers.
Although it is preferred due to its cheapness and easy processing, its usage area is somewhat limited due to its fragile structure. PMMA was first used in parachute construction. In addition, it is used in decoration, lighting and making aquariums, tables, sinks and kitchen sinks, in the production of some implants and optical lenses in the human body.
PMMA is one of the members of the large methacrylate ester family with a bonded Alkyl or Aryl group. It is generally produced by emulsion polymerization, solution polymerization, and bulk polymerization.
PMMA material is a methacrylic acid ester belonging to an important family of acrylic resins. First of all, propylene (PP) used in the production process is obtained. Also, propylene and benzene are reacted together to produce cumene or iisopropyl benzene. The cumene produced is then oxidized to cumene hydroperoxide. It is then treated with acid to produce acetone, which is converted into methyl methacrylate (flammable liquid). This liquid is polymerized into bulk liquid or suspended fine water droplets under the action of free radical initiators to form a solid (PMMA plastic).
PMMA is more often identified in the market under the trademarks Plexiglas, Lucite-Perspex.
PMMA Key Features:
-
It is a strong, durable and light material.
-
It has better impact resistance than both glass and polystyrene.
-
It shows superior environmental stability compared to other plastics.
-
It has high thermal and chemical resistance.
-
It has low smoke emission.
-
It has excellent abrasion resistance.
-
It exhibits high strength and durability.
-
It has high light transmission.
-
Density - 1.17 - 1.20 g / cm 3 (less than half the glass)
-
Melting Point - 160 ° C (320 ° F, 433 K)
-
Water Absorption - 0.3-0.4%
-
Ignition Temperature - 460 ° C (860 ° F)
-
Solvency- Easily melts and dissolves in many organic solvents.
-
Impact resistance may remain low in strength compared to other replacement plastic materials. has.
-
It is advantageous over other plastic polymer as it does not contain or release Bisphenol A (BPA) during the hydrolysis process.
-
Even related plastic materials, which are polycarbonate, contain BPA, which is toxic in nature. (BPA is dangerous to health and environment). PMMA is a type of plastic that is non-toxic by nature and does not contain BPA (Bisphenol-A) when it is solid on its own.
-
Generally, fumes emitted during 3D printing ore can be toxic when used in molten form for injection molding. Since it may cause health risks, inhalation should be avoided and the production area should be well ventilated.
PMMA Usage Area:
PMMA is a versatile plastic material that can be used for a wide variety of applications in different fields and different forms.
Thanks to its positive physical, chemical and mechanical properties, it can be used in a range of applications in the following ways:
It is widely used instead of glass due to its transparent and clear structure. This glass replacement material can be applied in the following areas:
-
In the construction of commercial and residential aquariums
-
Viewing PMMA plastic glasses, ports as well as diver's missing pressure hulls. In tracking spheres for submarines
-
Lenses of exterior lights in automobiles and spectator protection panels of ice hockey rinks
-
On aircraft windows, even instead of police vehicles' windows.
-
Lighthouse lenses, glass ceilings, roof coverings of areas such as botanical gardens
-
In different segments to reorient light
-
In laser cut acrylic panels, it carries sunlight to indoor areas with a light pipe.
-
In various artistic applications for decorative purposes
-
In the production of prism-layered plates to direct sunlight from the windows to the floor or ceiling of the room
PTFE (PolyTetraFluoroEthylene)
It is a strong, hard, waxy, non-flammable synthetic resin type produced from the polymerization process. It is widely used under the brands Teflon, Hostaflon and Polyflon to make non-stick pans or things that are slippery.
It has the widest operating temperature among all industrial plastics - 260 to 270 ° C, full endless resistance to moisture and ambient conditions to all chemicals used in the industry, the lowest static and dynamic friction coefficient among all solids, superior electrical insulation, non-stickiness, In addition to non-combustion and such features, it is preferred because of its sufficient mechanical properties and full resistance to all chemical substances.
It was discovered accidentally by Roy Plunkett (American Chemist for EI du Pont de Nemours & Company) in 1938 when he found that a gas TFE refrigerant tank polymerized to a white powder. Later, during the Second World War, it was used as a corrosion resistant coating to protect metal equipment used for transporting radioactive materials.
Due to its slippery nature and high melting point, it did not come into widespread use until it was introduced by DuPont under the trademark Teflon-Coated non-stick cookware in 1960. This is the best known brand for non-stick pans and pots coated with resin material. PTFE is therefore better known with "Teflon", one of DuPont's leading brands.
PTFE is produced by free radical polymerization of tetrafluoroethylene. Since tetrafluoroethylene can decompose into tetrafluoromethane and carbon by explosion, various special apparatus are used to prevent hot spots that can cause harmful side reactions.
The process is initiated by persulfate which is homolized to generate sulfate radicals. The resulting polymer is then terminated with sulfate ester groups, which can be hydrolyzed to produce end groups of the polymer. Since this material is soluble in almost any solvent, the polymerization process (using surfactants such as PFOS) is carried out as an emulsion in water.
PTFE's main raw materials are Chloroform, Fluorspar and hydrochloric acid.
It is primarily available in fine, micronized like powder form and also in aqueous dispersion.
PTFE Key Features:
-
It is extremely resistant to chemicals and weather conditions.
-
It has excellent dielectric properties.
-
It shows high thermal stability with strong flame resistance.
-
Non-stick, low friction resistance.
-
It is compatible with food contact.
-
It has a smooth surface coating effect.
-
It does not get wet and is highly protective against corrosion.
-
Density - 2200 kg / m 3
-
Melting Point - 600 K
-
Thermal Expansion - 112–125 • 10 −6 K −1 [23]
-
Glass Temperature-388K [22]
-
Friction coefficient - 0.05-0.10
PTFE Usage Area:
Today, the main use of PTFE polymer is as a non-stick cookware coatings. It has applications in a range of industrial products, including bearings, pipe liners, and a variety of pump and valve parts.
This material is widely used in a variety of applications in the form of mechanical components and as coating materials. Major end-user industries served by these resins include chemical processing, mechanical, food, household, automotive, electronics and many other things.
With the best non-stick properties and resistance to high temperatures, PTFE is an incredibly versatile material with a wide variety of known applications. PTFE stands out with the following advantages;
-
It is excellent in electrical insulation. Computer applications are used as an insulator for cables and cables.
-
With its low friction property, it is a popular material in mechanical engineering applications, including use in plain bearings, slide plates, gears and other working parts.
-
It is abrasion resistant, non-reactive and tolerant of high temperatures. This feature helps make it suitable for use in industrial pipes and hose assemblies (where chemicals and acids are used).
-
It tolerates high temperatures. Thus, it is widely used in acids and chemicals and in the chemical industry.
-
There is no harm in food contact, so it is an excellent choice for applications in packaging.
-
It is an ideal choice for sealing components in chemically aggressive use.
-
It has an economic structure. It is widely used in parks, supermarkets, bridge construction and even cars.
-
This material has the highest melting point and can resist even at 260 ° C. For this reason, it is widely used in the production of sheets and films, which are more used for a multitude of applications as the end product in the final segment market. It is preferred as a coating material for different uses in various industries such as aviation, electronics and automobiles.
Pure PTFE:
It is one of the most known chemically inert material forms used in many different applications and industries.
It is commonly used in high voltage electrical connectors, circumferential seals, and commercial fishing reels.
Other applications include pump housing, valve seals, cylinder liners, shaft bearing, filter housing, pump and tool construction, electrical industry, laser technology, food and medical technology, and others.
-
It has high chemical resistance over a wide temperature range.
-
Provides excellent thermal stability and electrical insulation.
-
It has an infinite shelf life.
-
It has a low coefficient of friction.
-
Tensile strength - 20-30 MPa
-
Specific weight - 2.14 - 2.19 g / cm 3
-
Friction coefficient - <0.1
-
Water absorption - Zero
Glass Filled PTFE:
It is a combination of glass fiber mixed with pure PTFE form. It helps to increase the compressive strength and reduces deformation under load. It is used in the fields of smoke treatment, roller coatings, machine parts, chemical engineering, pure water production, etching plates.
-
Improved hardness and wear resistance.
-
Lower thermal expansion property with higher coefficient of friction.
-
Not suitable for abrasive filled applications.
-
It has lower resistance to gases and is not conductive.
-
Tensile strength - 31 MPa (4600 PSI)
-
Specific Weight - 2.23 - 2.26 g / cm 3
-
Thermal Conductivity - 10.6 x 10-4 cal / cm-sec- ° C
-
Linear thermal expansion coefficient --7-11.2 x10 -5 ° C (100 ° C)
Bronze Filled PTFE:
It is the addition of bronze to pure PTFE material to provide better dimensional stability and reduce friction with cold flow and wear. Like other PTFE grades, this grade avoids a number of variations that can be manipulated to improve properties for use.
-
It has good electrical and thermal conductivity.
-
It shows improved wear resistance, especially under load.
-
It is very economical and very resistant to chemicals.
-
Specific weight - 2.05 - 2.12 g / cm 3
-
Tensile strength - 13-18 MPa
-
Elongation - 90 - 300%
-
Static and dynamic coefficient of friction - 0.14 - 0.16 and 0.12 - 0.14
Carbon Filled PTFE:
In this grade, carbon is added to the pure form of PTFE, which helps to increase strength and wear resistance. It also helps to provide thermal conductivity and low permeability. It is widely used in the compressor industry, its main use includes wear rings, piston rings and bearing rings. As it is an extremely versatile material, it is also used for high performance seals and wipers.
-
It is a hard wearing material with a very high specific gravity.
-
It exhibits good thermal and electrical conductivity.
-
It has the best wear properties among all grades.
-
It has high deformation resistance.
-
Specific weight - 3.8 - 3.95 g / cm 3
-
Tensile strength - 10-18 MPa
-
Elongation - 100% - 200%
-
Shore D hardness - 65-75
Stainless Steel Filled PTFE:
When steel is added to the pure PTFE material of the polymer, it gains excellent strength and stability even to resist high temperatures and overload. It is a versatile form of quality that can be used in steam and thermal fluid applications. Due to its high wear resistance, it is a very good material to be used in V-Ball type flow controlled ball valve applications.
-
It has increased thermal and electrical conductivity.
-
It has excellent structure under extreme load and temperature.
-
It is resistant to low friction, cold flow and abrasion.
-
Although it is very heavy, it has an extremely difficult wear quality.
-
Specific weight - 3.35 g / cm 3
-
Tensile strength - Min 22 MPa
-
Elongation - Min 220%
-
Shore D hardness - 65-69
Powder PTFE:
PTFE is also available in white powder form, known by the term "fine powder". Teflon fine powder is also the well-known brand name for a powdery material. It is used as a coating material in industry and household goods.
These powders are transformed into usable elements (shapes, wires, tapes, etc.) by the paste extrusion process, followed by post-extrusion heating. This process is used to remove and develop residual solvents of hydrocarbons. This powder is suitable for making touch weight measurements at large actions as it will help reduce friction compared to other lubricants.
It is primarily used as a coating material in different industries. It also has other uses, including wire and cable insulation used in pipes, pipe liners, and films. It is even used for sintered and non-sintered tapes, microporous membranes, heat shrink tubing, profile shapes, bushings, pull / push cables and many other components that require high performance plastic materials. Commonly used Powder coat types are - Polyester, TGIC Polyester, Epoxy, Urethanes, PVDF (polyvinylidene fluoride).
-
More attractive, high quality finish and durability.
-
Being economical and environmentally friendly.
-
Longer corrosion resistance.
-
Physical property of various color or gloss.

PA (PolyAmid)
It is a material widely used in the machinery industry. It is known as nylon. There are types such as Nylon6, Nylon6,6, Nylon11. The worst thing about nylon is its high water absorption. All nylon types are reinforced with fiber. Nylon has a crystalline structure. Nylon6 has a structure that comes to casting. Other nylon types can only be used with injection and extrusion methods that require high pressure, as they flow hard. It is a material with relatively hardness, rigid, slippery and good mechanical strength values. It is not as slippery as polyacetal (POM). Its chemical resistance is medium, it has resistance against some acids and bases. Polyamid 6 has the ability to collect water within its body. These traits have good and bad sides. Its good aspect increases the resistance of the piece against vibration and sudden impacts. Thus, it allows the dynamic stresses that will occur during use of the part to be eliminated within the body. the downside is that it becomes difficult to achieve dimensional stability in the material. It is used in the production of simple gears, bearings, bolts, flanges, pulley belt pulleys, cutting plates, filter plates, trays and all kinds of parts.
Nylon 6 and 6.6 are combined with a wide variety of strengtheners and modifiers to create new materials tailored to the customer and application demand and cost and performance constraints.
PA 6:
It is a white, semi-crystalline thermoplastic, very similar to Nylon 6.6, which is interchangeable in many ways. Its molten viscosity is less than Nylon 6.6 and therefore it is generally slightly easier to handle and is often preferred for molding. It also has a higher impact resistance, but less stiffness and greater water absorption.
Generally used in places where high operating temperatures are required, such as gears, cams, cylinders, bearings, nuts and bolts, electric tool bodies, electrical connectors, automotive fuel tanks, kitchenware.
-
It has good sliding and wear properties
-
It is resistant to many oils, greases and fuels.
-
It shows high strength.
-
It is a good choice for processing.
-
It shows high power.
-
It exhibits good sealing.
-
Easier to handle (molded) than nylon 6.6
-
It is suitable for injection molding.
-
It has a lower mold shrinkage than nylon 6.6.
-
Good resistance to fatigue
-
Extra hardness can be achieved by including glass fiber.
PA 6,6:
Nylon 6.6 is very hard and resistant to breakage, but its dense structure makes it difficult to dye its fibers. However, once dyed, it has a high color fastness and changes shape very little under sunlight. In general, it is the application areas where high operating temperatures are required, such as motor vehicle interiors.
-
It is heat resistant and this is particularly advantageous for preventing torsion
-
It has good sliding and abrasion properties.
-
Resistant to many oils, greases and fuels
-
It has high strength.
-
Has electrical insulation
-
It requires a higher plasticizing temperature than nylon 6.
DEHP (DiEthylHexylPhthalate)

DEHP (DiEthylHexylPhthalate)
DiEtylhexyl Phthalate (DEHP, formula: C6H4 (C8H17COO) 2) is a low molecular weight ortho-phthalate produced by esterifying phthalic anhydride with 2-ethyl-hexanol. It is a non-volatile, colorless and odorless viscous liquid, soluble in oil but absent in water. Due to its low cost and overall good performance, DEHP is widely used as a plasticizer in the manufacture of products made of PVC.
-
Good gelation offers satisfactory electrical properties and helps to produce highly elastic compounds with reasonable cold strength.
-
It has very good flexibility at low temperatures and some resistance to high temperatures.
-
DEHP is listed as a human carcinogen by the IARC.
-
DEHP has been identified as a hormone mimetic and developmental toxin in some studies.
-
In the EU, DEHP is considered a SVHC (a very important substance) under REACH legislation and cannot be used in most products
-
It is easily extracted into non-polar solvents (oils and fats in PVC packaged foods). For this reason, the US Food and Drug Administration (FDA) allows packaging containing DEHP to be used only for foods that consist of predominantly water.
PVC, vinyl chloride and vinyl acetate copolymers, Catheter, tube etc. Medical devices, DEHP is used in the development of formulations ranging from glassy compounds to soft and highly flexible materials. It is the most widely known plasticizer in the world, although its use has been reduced due to concerns about its effects on human health.
Melting point -50 ° C, Boiling point 250-257 ° C at 0.5 kPa.
DINP (DiIsoNonylPhthalate)
Diisononyl phthalate (DINP, formula: C26H42O4) is a high molecular weight orthophthalate produced by esterifying phthalic anhydride with isononyl alcohol in a closed system. It is an almost colorless and odorless oily liquid. It is slightly soluble in water, but in alcohol, hexane, etc. It is soluble, miscible and compatible with all monomeric plasticizers used in PVC compositions.
-
Offers flexibility and durability to vinyl products
-
Good performance at both low and high temperatures
-
Less volatile than DEHP
-
Good solvency leads to good flexible PVC processing properties.
-
It is used extensively in indoor and outdoor applications. Because it is less volatile, it is effective in applications where products are exposed to relatively high temperatures and have greater resistance to degradation.
-
DINP helps vinyl products withstand many weather conditions, making them waterproof and providing high thermal insulation and durability
-
DINP is combined with PVC powder by flooring manufacturers to produce soft and flexible finished products.
Melting point −43 ° C, Boiling point 244-252 ° C at 0.7 kPa,
Flash point 221 ° C (cc)
DINP (DiIsoNonylPhthalate)

DEHP (DiEthylHexylPhthalate)
DiEtylhexyl Phthalate (DEHP, formula: C6H4 (C8H17COO) 2) is a low molecular weight ortho-phthalate produced by esterifying phthalic anhydride with 2-ethyl-hexanol. It is a non-volatile, colorless and odorless viscous liquid, soluble in oil but absent in water. Due to its low cost and overall good performance, DEHP is widely used as a plasticizer in the manufacture of products made of PVC.
-
Good gelation offers satisfactory electrical properties and helps to produce highly elastic compounds with reasonable cold strength.
-
It has very good flexibility at low temperatures and some resistance to high temperatures.
-
DEHP is listed as a human carcinogen by the IARC.
-
DEHP has been identified as a hormone mimetic and developmental toxin in some studies.
-
In the EU, DEHP is considered a SVHC (a very important substance) under REACH legislation and cannot be used in most products
-
It is easily extracted into non-polar solvents (oils and fats in PVC packaged foods). For this reason, the US Food and Drug Administration (FDA) allows packaging containing DEHP to be used only for foods that consist of predominantly water.
PVC, vinyl chloride and vinyl acetate copolymers, Catheter, tube etc. Medical devices, DEHP is used in the development of formulations ranging from glassy compounds to soft and highly flexible materials. It is the most widely known plasticizer in the world, although its use has been reduced due to concerns about its effects on human health.
Melting point -50 ° C, Boiling point 250-257 ° C at 0.5 kPa.
DINP (DiIsoNonylPhthalate)
Diisononyl phthalate (DINP, formula: C26H42O4) is a high molecular weight orthophthalate produced by esterifying phthalic anhydride with isononyl alcohol in a closed system. It is an almost colorless and odorless oily liquid. It is slightly soluble in water, but in alcohol, hexane, etc. It is soluble, miscible and compatible with all monomeric plasticizers used in PVC compositions.
-
Offers flexibility and durability to vinyl products
-
Good performance at both low and high temperatures
-
Less volatile than DEHP
-
Good solvency leads to good flexible PVC processing properties.
-
It is used extensively in indoor and outdoor applications. Because it is less volatile, it is effective in applications where products are exposed to relatively high temperatures and have greater resistance to degradation.
-
DINP helps vinyl products withstand many weather conditions, making them waterproof and providing high thermal insulation and durability
-
DINP is combined with PVC powder by flooring manufacturers to produce soft and flexible finished products.
Melting point −43 ° C, Boiling point 244-252 ° C at 0.7 kPa,
Flash point 221 ° C (cc)
ASA (AcrylonitrileStyreneAcrylate)
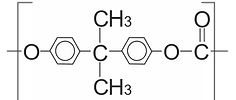
It is produced by adding a grafted acrylic ester elastomer during the copolymerization reaction between styrene and acrylonitrile.
It is resistant to UV, has good fluidity. It is a material similar to ABS.
ASA melts with other thermoplastics leading to weakness strength, such as polyolefins, polystyrenes, and nylons. It is secreted by concentrated acids, aromatic and chlorinated hydrocarbons, esters, ethers and ketones. Toxic smoke is produced when burned.
PBT (PolyButylene Terephthalate)

It is a semi-crystalline polymer used in injection molding. They show very good creep resistance even at high power and temperature. It has properties of resistance to cracking from environmental stress. Due to its low expansion coefficient and low water absorption, it is particularly suitable for engineering applications requiring high dimensional stability.
PC (PolyCarbonate)

It is a high performance thermoplastic with a low specific gravity.
In addition to being an important engineering plastic with its high impact resistance, low moisture absorption rate, good thermal insulation, stability against heat, it has also taken its place among commercial polymers thanks to its easy processing and processability.
It is used in the production of water bottles, high temperature cookware, safety glasses, CDs, DVDs, medical equipment, facade cladding panels, lighting enclosures in automotive.
Polycarbonate is hardly flammable, goes out when pulled from the flame and has an exiting flame. It is glass-clear, easy to color, resistant to climate change, can be used at temperatures up to 120 ° C, does not take water, therefore conducts electricity well, has a very high strength and toughness, and its dimensions are stable. They are also affected by strong acids and bases, and there is a risk of stress rupture and pain. They are used in fine work and electronic building elements, insulation screws, lighting devices, car tail lamps under the effects of heat, and tableware.
Another feature of polycarbonate is that it is very flexible. Typically it can be formed at room temperature, without cracking or breaking, as is the case with an aluminum sheet. Even small angle bends are possible without it, although deformation can be simpler with the application of heat. This property makes polycarbonate sheet stock particularly useful in prototyping applications where sheet metal is not viable (for example, when transparency is required or a non-conductive material with good electrical insulating properties is required).
Properties of Polycarbon:
PC is classified as "thermoplastic" (as opposed to "thermoset") and its name has to do with the way the plastic reacts to heat. Thermoplastic materials become liquid at melting point (155 ° C in case of polyamide). An important beneficial property about thermoplastics is that they can be heated to their melting point, cooled, and reheated without significant degradation. Instead of burning, thermoplastics such as polycarbon liquefaction allow them to be easily injection molded and then recycled.
In contrast, thermoset plastics can only be heated once (typically during the injection molding process). Initial heating causes thermoset materials (similar to 2-part epoxy) to set, causing an irreversible chemical change. If you try to heat the thermoset plastic to a high temperature a second time, it will burn out. This property makes thermoset materials poor candidates for recycling. Polycarbonate is also an amorphous material, meaning it does not show the regular properties of crystalline solids. Typically amorphous plastics tend to soften gradually (i.e. they have a wider range between their glass transition temperatures and their melting points) rather than exhibit a sharp transition from solid to liquid as crystalline polymers. Finally, a polycarbonate copolymer, several different monomers in combination with each other. It consists of the type.
The reason why polycarbonate is used very often; Polycarbonate sheets produce excellent results in application and are preferred in terms of providing easy bending and heat sound insulation. Polycarbonate sheets produced from the original raw material have impact resistance and non-flammability. It is an incredibly useful plastic for applications that require transparency and high impact resistance. It is a lighter alternative to glass and a natural UV filter, so it is often used in glasses.
Unlimited needs are tried to be met with limited energy resources. At this point, keeping the efficiency in energy use at the highest level will provide commercial gain. Therefore, polycarbonate sheets are used in order to benefit more from sunlight, especially in industrial architectures. These plates, which are in various sizes and shapes according to the area of use, are used especially in the roof and wall construction of industrial buildings. Thus, both solar energy is utilized and electricity savings are made.
Features and benefits of polycarbonate sheets;
-
It is beneficial for thermal insulation. The temperature balance inside can be controlled with these plates. Thus, the ambient temperature and the cold or hot air flow outside are prevented.
-
Provides mechanical resistance.
-
It shows resistance to water absorption. Thus, the polycarbonate sheet does not deteriorate and does not absorb water inside.
-
It shows sound insulation properties.
-
It shows fire resistance. It is not flammable.
-
It can be easily applied on all types of sloping roofs.
-
It provides cost savings thanks to its light transmittance.
-
It is resistant to breakage with its high impact strength.
-
Due to its light transmittance, it is preferred in terms of lightness compared to glass materials. It is 6 times lighter than glass.
-
These transparent plates meet the lighting needs.
-
It has a long-lasting and non-tarnishing structure.
Polycarbonate Sheet Application Areas:
It is produced in desired dimensions and dimensions. The company that will make the application provides production from the necessary materials according to the condition of the building to be built.
Boards are produced in flat, curved, sectioned, geometric shapes according to the area of use and are applied in accordance with the desired purpose. These plates have the ability to be interlocked due to their production. Thanks to this feature, it is very easy and fast to install. However, it is important to have more efficiency done by professionals. In addition, together with the various techniques applied at the time of the assembly of the plates, the mounting screws are left at the bottom to prevent visual pollution.
The main areas of use where polycarbonate sheets come across; Billboards, Car parks, Bus stops, Sports halls, Greenhouses, Entrance eaves, Walkways, Passages between buildings, Veranda and terrace roofs, Winter gardens, Factory windows, Facade applications
Corrugated polycarbonate screens with wide application areas are preferred in greenhouses, apartment entrance canopies and solid polycarbonate roof coverings in bus stops, shopping malls, because of their illumination and resistance to unbreakability.In addition, police shields for security purposes are used as a protector in motorcycle front visors.
To put it more accurately, coronavirus in polycarbonate sheets, its use as a protective compartment screen has increased after the covid-19 outbreak pandemic has started. Due to its durability and rigid material, transparent and high light transmittance, it is a preferred material, and it is the most preferred product after pet-g products, especially in the health sector, due to the explosion of demand.
During the polycarbon pandemic process, it continued to be the main material in the production of masks in order to minimize the risk of shopping in pharmacies and markets.
We used polycarbonate as a protector against the negative effects of rain, storm and wind in open areas such as gardens. With the pandemic, we have tended to use it as a protective shield against the danger posed by viruses.
While polycarbon is used in many areas in our daily life with its protection and durability, its use has increased in the fight against pandemics and has gained an important place in protection against external dangers.
According to AZO Materials, polycarbonate was developed simultaneously in the USA and Germany in the mid-20th century. In the modern era, it is produced by a large number of companies, each typically with its own manufacturing process and unique formula.
Trade names include Lexan® (SABIC) or Makrolon® (Bayer) well-known variants (or "resins").
Various industry grades of polycarbonate are available. Most are named by their generic name (polycarbonate) and typically differ by the amount of glass fiber reinforcement they contain and the variance in melt flow between them. Some polycarbonates contain additives such as "ultraviolet stabilizers" that protect the material from prolonged exposure to the Sun. What is meant to be referred to as "Leksan" in our country as a misuse is actually polycarbot.
Injectable polycarbonate may contain other additives such as mold release agents that lubricate the material during processing. Finished polycarbonate is typically sold in rolls, bars, or sheets.
Below; It shows the relative impact strength of Polycarbon compared to the impact resistance of other commonly used plastics such as ABS, Polystyrene (PS) or Nylon.
It shows the relative impact strength of Polycarbon compared to the impact resistance of other commonly used plastics such as ABS, Polystyrene (PS) or Nylon. >>>>

POE (PolyOlefin Elastomer)
POP (PolyOlefin Plastomer)
These are PP elastomers with propylene and ethylene monomer molecular structure integrated in the molecular chain with a wide variety of applications. The ethylene content determines the degree of elasticity and has the advantage of being mixed with all kinds of PE and PP. Stretch hood packaging, Stretch film, interlayer between PE and metallized PP layers, Automatic packaging film, impact enhancer in PE and PP, Masterbatch production increase in filling level, Injection molding application areas where flexibility is required.
-
Very elastic and resistant to drilling
-
It has good optical properties
-
Very low seal initiation temperature (SIT)
-
Immediately after sealing it has high thermal insulation strength
-
Non-slip, increased friction coefficient
-
Very resistant to impact at low temperatures
-
0.865-0.890 g / cm3 density
-
Suitable for extrusion and injection
-
Mixes very well with LDPE, HDPE and PP
-
It complies with food transportation rules.
POM (PolyOxyMethylene)

Acetal has a high crystallinity value. It is hard, rigid and has good moisture, heat and solvent resistance. They remain stable at high temperatures for a long time. They are manufactured as injection molded products with glass fiber. Areas of application include gears, bearings, sleeves, bag buckles. Since special POM production is required for the sterilization of medical supplies, it is not widely used.
Since its density is higher than other plastics, its use in the automotive industry is limited. Because of its high density, its price is also high. For this reason, it is not preferred in packaging, but it is very common in the production of electrical connections and switches, bearings, gears, nipples, and some plumbing connections.
See also >> Conductive Plastics / POM-C
PPE (PolyPhenyleneEther)

It is a linear, non-crystalline polyether. Polyphenylene ether, also known as polyphenylene oxide, is often mixed with polystyrene (PS) to improve its hardness and workability. Although PPE is based on many chemicals, it is easily dissolved by some hydrocarbons.
PPO (PolyPhenylene Oxide)
It is an impact resistant, hard and low moisture absorption polymer. Usually used in modified form. Temperature resistance is very good, it can be used in a wide temperature range (-40 C to +140 ºC). It is an opaque material and has high resistance to water degradation. Submersible and water pumps, meters, lighting bodies, office appliance bodies, connectors are priority areas of use.
TPE (ThermoPlastic Elastomer)

Almost no compounding is required, they do not need reinforcing and stability-enhancing additives, they can be colored, less energy is used for their production, and it is easier to control the quality of part production. The disadvantages of TPEs are that they are high-cost materials, cannot be mixed with cheap additives such as carbon black, and their low resistance to temperature and chemicals.
TPU (Thermoplastic PolyUrethane)
It does not have the heat resistance and compression set resistance of thermoset type polyurethanes, but many other properties are similar. It has superior wear resistance, good low temperature flexibility, excellent oil resistance and is among the best for load carrying capacity.
Shoes, pipes, sports equipment, wire and cable applications, hose, wheels, film gaskets coating applications are its working areas.
PEI (PolyEtherImide)
It is clear viscous liquid. It has the highest cation density among other materials available. Used in papermaking, water treatment, detergent, adhesive, cosmetics
PAS (PolyArylSulfone)
PES (PolyEtherSulfone)
PES and PSU grades are transparent, high temperature amorphous thermoplastics derived from polyethersulfone and polysulfone.
This line of products is used in highly loaded engineering parts that must exhibit great dimensional stability and good mechanical properties in a temperature range from -58 ° F to 428 ° F.
The Ultrasound PES and PSU is designed for use in a variety of demanding applications in market sectors such as automotive, membranes, food service and plumbing. A wide variety of typical applications are: Headlight reflectors, milk membranes, sensors, food trays, water treatment membranes, manifolds. It is ideal for hydrophilic, low protein binding, PES membrane filters, tissue culture media sterilization, life science and microbiology fluid applications, clinical and general filtration.
RUST; It is mainly chemical structure very similar to polyethersulfone (PES).
PVDF (PolyVinyliDene Fluoride)
It is valued for its durability, stability and diverse engineering advantages. For example, if you need a polymer that is resistant to exposure to harsh thermal, chemical or ultraviolet conditions, porous PVDF offers superior stability similar to the performance of fluoropolymers in these environments. It has high chemical corrosion resistance with its low weight and thermal conductivity.
It is resistant to most chemicals and solvents. It is not affected by prolonged exposure to ultraviolet radiation.
PEK (PolyEtherKetone)
PEEK (PolyEtherEtherKetone)

It is a resin suitable for partial crystalline, wire coating and composite materials.
It is a tough, rigid plastic at room temperature, very resistant to abrasion for a long time. To the aquatic environment
and is resistant to solvents. Polyketones in aromatic polyether class
they are used as performance plastics.
Both polymers (PEK-PEEK), which are widely produced in the market, have exceptional strength, heat resistance
and its resistance to chemicals, it is widely used in aircraft and automotive industry.
used. They are polymers that can be used continuously in the range of 240 ° C - 280 ° C.
Polyetheretherketone, used where superior chemical and physical properties are required
It is a high performance thermoplastic polymer.
Polyether ether ketone (PEEK) is a colorless organic thermoplastic polymer in the polyetherketone (PAEK) family used in engineering applications.
PEEK is a semi-crystalline thermoplastic with excellent mechanical and chemical resistance properties held at high temperatures. The processing conditions used for molding the PEEK can affect the crystallinity and hence the mechanical properties. Young's modulus is 3.6 GPa and tensile strength is 90 to 100 MPa. PEEK has a glass transition temperature of about 143 ° C and melts around 343 ° C. Some grades have a useful working temperature of up to 250 ° C. It is highly resistant to thermal degradation and attack by both organic and aqueous media. It is attacked by halogens and strong acids as well as some halogenated compounds and aliphatic hydrocarbons at high temperatures. Completely soluble in concentrated sulfuric acid at room temperature.
Due to its robustness, PEEK is used to manufacture products used in demanding applications such as bearings, piston parts, pumps, HPLC columns, compressor plate valves and cable insulation. It is one of the few plastics compatible with ultra-high vacuum applications. It is widely used in the aerospace, automotive and chemical process industries.
Looking at the physical and chemical properties of PEEK, it is seen that it is semi-crystalline and has a high melting temperature of 343 ° C, thanks to the amorphous and crystalline regions it contains. The glass transition temperature is 143 ° C and is well above the 37 ° C body temperature required in in-vitro and in vivo applications, which makes it possible to continue clinical studies using biomaterials produced from PEEK without any problems.
PSU (PolySUlfone)

Its tensile, compression and friction strengths are very high. This material, which is resistant to acid, base and salt solutions, is not affected by detergents, oils and alcohols. It is used in medical equipment, food production equipment, electrical connections, fuse and switch housings in automotive industry, corrosion-resistant pipes, pumps, camera and watch bodies, battery insulation plates, space and aviation industry.
PTFE (PolyTetraFloroEthilen)

It is a versatile polymer used in a wide variety of medical, electronic, automotive and high technology applications. This allows working in high temperature environments (260 ° C continuously) without reacting to most chemicals and media. Compatible with steam and Ethylene oxide sterilization.
UHMWPE (Ultra High Molecular Weight Poliethylene)

It is a type of polyethylene with a density varying between 0.930-0.935 g / cm3. High molecular weight means that the polymer chains are firmly located or packaged within the crystalline structure. UHMWPE is very hard and has the highest impact resistance among thermoplastic materials. In the defense industry, it is used in many branches of the industry from composite armor plate making to general purpose machines and its use is increasing day by day. Ultra high molecular weight polyethylene (UHMW-PE) is a thermoplastic polyethylene with a molecular mass in the range of 2 to 6 million amu. It is a very hard material with the highest impact strength of any thermoplastic material currently made. UHMW-PE has a low coefficient of friction, high wear resistance and extremely
It has high chemical resistance.