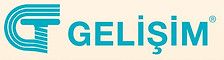


Hydrocarbons
It is an organic compound consisting of two elements, hydrogen and carbon. Most of the petroleum composition consists of hydrocarbons of varying lengths.
The smallest hydrocarbon methane consists of a single carbon atom and four hydrogen atoms. However, hydrocarbons can consist of hundreds or thousands of individual atoms linked together in many ways, including chains, circles, and other complex shapes.
In order to classify the properties of hydrocarbons, they are divided into several basic types.
Alkanes: These are called saturated hydrocarbons. That is, they only contain single bonds between all carbon atoms. Alkanes are the basis of petroleum fuels and exist in linear and branched forms.
Unsaturated Hydrocarbons: Hydrocarbons that have one or more double bonds between carbon atoms are called alkenes.
Cycloalkanes: Any hydrocarbon containing one or more ring structures.
Aromatic Hydrocarbons: Aromatic hydrocarbons , also called arenes, are a unique class of carbon molecules in which carbon atoms are bonded by successive double and single bonds. This class of molecules has special ring structures in which the bonds between carbon atoms are an intermediate bond between single and double bonds.
Molecules in this class contain the industrial solvent "benzene".
Benzene (C6H6): Like other hydrocarbons, benzene is a natural component of petroleum. It is a colorless, flammable, sweet-smelling liquid at room temperature and is a component of most gasoline blends because of its high octane number.
Benzene is also highly carcinogenic and is well known to cause bone marrow failure and bone cancer. Of course, its carcinogenicity is not well known when used as an additive in aftershave and other cosmetics due to its "pleasant aroma".
The largest use of benzene (50%) is the product of styrene and polystyrene plastics. It is also converted into a molecule known as cyclohexane, which is important in Nylon production. About 15% of benzene is used to produce cyclohexane. Smaller amounts are used in everything from pesticides to rubber.
The benzene structure can be drawn in two ways. In the first, the double bond character is drawn explicitly. In the short handed version, a circle is drawn inside the ring to show the structure. There is only one hydrogen bonded to each carbon atom in benzene.
I. and II below. drawings are identical. III in practice. drawing is used.
Benzene is a colorless, flammable liquid with a boiling point of 80.1 ° C and a melting point of 5.5 ° C.
Binuclear Aromatic Hydrocarbons: They are compounds that contain two benzene rings in their molecules.
Hydrocarbons
It is an organic compound consisting of two elements, hydrogen and carbon. Most of the petroleum composition consists of hydrocarbons of varying lengths.
The smallest hydrocarbon methane consists of a single carbon atom and four hydrogen atoms. However, hydrocarbons can consist of hundreds or thousands of individual atoms linked together in many ways, including chains, circles, and other complex shapes.
In order to classify the properties of hydrocarbons, they are divided into several basic types.
Alkanes: These are called saturated hydrocarbons. That is, they only contain single bonds between all carbon atoms. Alkanes are the basis of petroleum fuels and exist in linear and branched forms.
Unsaturated Hydrocarbons: Hydrocarbons that have one or more double bonds between carbon atoms are called alkenes.
Cycloalkanes: Any hydrocarbon containing one or more ring structures.
Aromatic Hydrocarbons: Aromatic hydrocarbons , also called arenes, are a unique class of carbon molecules in which carbon atoms are bonded by successive double and single bonds. This class of molecules has special ring structures in which the bonds between carbon atoms are an intermediate bond between single and double bonds.
Molecules in this class contain the industrial solvent "benzene".
Benzene (C6H6): Like other hydrocarbons, benzene is a natural component of petroleum. It is a colorless, flammable, sweet-smelling liquid at room temperature and is a component of most gasoline blends because of its high octane number.
Benzene is also highly carcinogenic and is well known to cause bone marrow failure and bone cancer. Of course, its carcinogenicity is not well known when used as an additive in aftershave and other cosmetics due to its "pleasant aroma".
The largest use of benzene (50%) is the product of styrene and polystyrene plastics. It is also converted into a molecule known as cyclohexane, which is important in Nylon production. About 15% of benzene is used to produce cyclohexane. Smaller amounts are used in everything from pesticides to rubber.
The benzene structure can be drawn in two ways. In the first, the double bond character is drawn explicitly. In the short handed version, a circle is drawn inside the ring to show the structure. There is only one hydrogen bonded to each carbon atom in benzene.
I. and II below. drawings are identical. III in practice. drawing is used.
Benzene is a colorless, flammable liquid with a boiling point of 80.1 ° C and a melting point of 5.5 ° C.
Binuclear Aromatic Hydrocarbons: They are compounds that contain two benzene rings in their molecules.
About
Kyäni, nutritional supplement products consisting of beneficial ingredients; It delivers to more than 50 countries around the world with unique business opportunities. We use Kyäni products daily to maintain our ideal health, share these products with others, devote a certain amount of time to work almost every day to build and maintain our business, and share our success with others by involving others in the Kyäni opportunity or contributing to the Potato Pak and Caring Hands programs.
About
Kyäni, nutritional supplement products consisting of beneficial ingredients; It delivers to more than 50 countries around the world with unique business opportunities. We use Kyäni products daily to maintain our ideal health, share these products with others, devote a certain amount of time to work almost every day to build and maintain our business, and share our success with others by involving others in the Kyäni opportunity or contributing to the Potato Pak and Caring Hands programs.
Page Under Construction.
Page Under Construction.
Training / Knowledge / Solution Platform

Hydrocarbons
It is an organic compound consisting of two elements, hydrogen and carbon. Most of the petroleum composition consists of hydrocarbons of varying lengths. The smallest hydrocarbon methane consists of a single carbon atom and four hydrogen atoms. However, hydrocarbons can consist of hundreds or thousands of individual atoms linked together in many ways, including chains, circles, and other complex shapes. In order to classify the properties of hydrocarbons, they are divided into several basic types.
Structure of Hydrocarbons
Since hydrocarbons consist only of carbon and hydrogen, their combustion with oxygen can only produce water as a result of the combination of hydrogen and oxygen and carbon dioxide as a result of the combination of carbon and oxygen. The energy produced by burning a hydrocarbon results from breaking both carbon-hydrogen and carbon-carbon bonds and recombining them into carbon-oxygen and hydrogen-oxygen bonds. The structure, the ratio of hydrogen to carbon, and the length of a particular hydrocarbon determine its characteristics. Generally, small-sized hydrocarbons will be gas, while medium-sized linear hydrocarbons will be liquid. Intermediate branched hydrocarbons are low melting point waxes. Long hydrocarbons tend to be semi-solid or solid. Unsaturated hydrocarbons are more likely to be more rigid than their saturated counterparts such as cyclic hydrocarbons.
Hydrocarbons up to 10 carbon atoms and their usage areas are shown in the table.
Hydrocarbons longer than 10 carbon atoms are often broken down into structures with shorter lengths in a process known as "cracking".
Unsaturated Hydrocarbons: Hydrocarbons that have one or more double bonds between carbon atoms are called alkenes.
Cycloalkanes: Any hydrocarbon containing one or more ring structures.
Aromatic Hydrocarbons: Aromatic hydrocarbons , also called arenes, are a unique class of carbon molecules in which carbon atoms are bonded by successive double and single bonds. This class of molecules has special ring structures in which the bonds between carbon atoms are an intermediate bond between single and double bonds.
Benzene (C6H6): Like other hydrocarbons, benzene is a natural component of petroleum. It is a colorless, flammable, sweet-smelling liquid at room temperature and is a component of most gasoline blends, as it has a high octane rating.
Benzene is also highly carcinogenic and is well known to cause bone marrow failure and bone cancer. Of course, its carcinogenicity is not well known when used as an additive in aftershave and other cosmetics due to its "pleasant aroma".
The largest use of benzene (50%) is the product of styrene and polystyrene plastics. It is also converted into a molecule known as cyclohexane, which is important in Nylon production. About 15% of benzene is used to produce cyclohexane. Smaller amounts are used in everything from pesticides to rubber.
Benzene structure can be drawn in two ways. In the first, the double bond character is drawn explicitly. In the short-handed version, a circle is drawn inside the ring to show the structure. There is only one hydrogen bonded to each carbon atom in benzene.
Following the benzene ring representations; I. and II. drawings are identical. III in practice. drawing is used.
Benzene is a colorless, flammable liquid with a boiling point of 80.1 ° C and a melting point of 5.5 ° C. As a starting material in the synthesis of styrene and phenol used in plastic production in the industry, in nylon components, synthetic used in detergent production. In aviation gasoline, the starting material of aniline , which is used to paint, and benzene is used as an insecticide. Benzene is also a good solvent.


Alkanes: (CnH2n + 2)
Alkanes are also known as paraffin, this term is quite confusing because paraffin also refers to a type of wax. Alkanes are called saturated hydrocarbons. That is, they only contain single bonds between all carbon atoms. Alkanes are the basis of petroleum fuels and exist in linear and branched forms.
Generally, the alkanes used in this wax have carbon chains of 20 to 40 carbons. Thus, paraffin wax is a wax made of paraffin or alkanes. Paraffin wax is characterized by low melting point, flexible structure and easy burning. Usually used in candles and crayons.
Alkanes contain only single bonds, that is, they are saturated with hydrogen atoms.
Alkanes get their name from the alkyl group consisting of one carbon and three hydrogens.
Methane: (CH4) It is the simplest hydrocarbon made up of one carbon and four hydrogen molecules. Because it is very small, it is a colorless, odorless gas at room temperature. The odor in "natural gas" used in homes is actually added to methane for safety reasons.
It is the smallest molecular weight hydrocarbon, (CH4) is a colorless gas; also known as marsh gas. Methane is the basic substance of natural gas.
Methane is a tetrahedral form (pyramid with a triangular base) where each hydrogen is equal to all other hydrogen. Methane is often used as fuel for electricity generation and heating. In compressed form, it is used as a vehicle fuel. Methane usually burns at high efficiency, producing only small amounts of carbon monoxide. It occurs naturally in oil, coal deposits, natural gas and marshes. Methane, which is also used in electricity generation, also has the least carbon dioxide emission.


Ethane: (C2H6) has two carbon molecules and six hydrogen molecules. Carbon molecules are linked together by a single bond and each has three hydrogen atoms. Like methane, ethane is a colorless, odorless gas at room temperature. Ethane is mainly used in the production of ethylene and as a fuel. It is also used to prepare ethylene, acetaldehyde and acetic acid. It is used for chemical applications such as polyethylene (a polymer of ethylene and the world's most widely used plastic) as well as producing ethylene glycol, the main component of antifreeze.

Propane: (C3H8) By -product of natural gas processing and petroleum refining. In gas form, it is heavier than air. Propane is a very clean fuel that produces mostly water and carbon dioxide during combustion. As propane expands, it absorbs heat and can act as a coolant, but it is explosive. It is used in sprays as a propellant. It is also used in industrial cooler and thermostat filling. Propane gas is a gas that can liquefy under low pressure. Because of this feature, it is mixed with butane gas and used as fuel in homes and rural areas.

Butane: (C4H10) It is a four-carbon gas. Like propane, it is denser than air gas. It is also used as an aerosol propellant. Butane is euphoric (relaxes emotions and muscles), so it is often abused as a volatile substance. It causes spasms in the airway muscles in the lungs. It appears mostly as lighter gas and aerosol.

Pentane: (C5H12) Usually used as a solvent and sometimes as a fuel. It is a liquid at room temperature and colorless, but evaporates easily. In fact, pentane boils at its body temperature of 37 ° C. Pentane can be found in mixtures of gasoline, but its primary use in the industrial setting is as a "blower" in the formation of polystyrene plastic foams. Isopentane is used in toothpastes such as Aquafresh and Sensodyne.

Hexane: (C6H14) This molecule is an important component of gasoline and gives a different odor to gasoline. Asphalttate is used in solvent formulations, production of leather products, roofs. It is non-toxic, used to extract oils from grains and nuts. However, in general, hexane can remain in foods after processing. Hexane is easier to find, although heptane or octane dissolve the oil better. Since hexane vapor is heavier than air, it can spread on the ground and cause ignition at long distances. Hexane is used in the production of shoes, leather, roof coatings and glue.

Heptane: (C7H16) Used as a solvent, as it is useless as a fuel. It is an important component of rubber cement. It is used as a solvent in paint, to dissolve pigments and even to color, and in fast-drying adhesives. Its melting point is −90.61 ° C and its boiling point is 98.42 ° C. Heptane is the main component of gasoline.

Octane: (C8H18) Octane and its isomers are the main components of gasoline. It is important to remember that iso-octane is what increases the octane value of gasoline. Other hydrocarbons can also be used to increase octane ratings, including toluene and methyl tertiary butyl ether (MTBE). It is used in the aromatization of dimethylbenzene and ethylbenzene. It is used as a solvent.

Nonane: (C9H20) has 35 different isomers. It is used only in fuel due to its high flammability. Its main use is kerosene. It is sometimes used as a solvent and as a carrier in the production of paraffin (wax) and in the preparation and distillation of surfactants.

Dean: (C10H22) Hydrocarbons are considered the last member of this series, although there are many more. The decan has 75 different isomers and they are all flammable. It is primarily used as a fuel and solvent. It is considered as a reference in gas chromatography.

Others: (C11H24 Undecan), (C12H26 Dodecan) (C13H28 Tredecan),
(C14H30 Tetradecan) (C20H42 Eicosan), (C21H44 Heneikozan) (C22H46 Dokozan), (C30H62 Tricontane) (C40H82 Tetracontane), (C50H102 Pentacontane)
Alkenes: (CnH2n)
Alkenes are also called olefins. Like alkanes, this can be confusing because there is also an olefin material.
As in the case of paraffin wax and alkanes, olefin is a type of fiber made only from alkenes. Olefin is usually made of polypropylene or polyethylene and is used in everything from rope to car interiors.
The double bonded structure of alkenes changes their chemistry compared to alkanes. First, alkenes are more acidic than alkanes. Also, they are more reactive than alkanes and easily undergo polymerization reactions. Alkenes are unsaturated, meaning they contain at least one carbon-carbon double bond.
This double bond replaces two hydrogen atoms; This means that alkenes do not have the maximum number of hydrogen atoms per carbon and are therefore called unsaturated.
Alkenes liquefy when they have 15 or more carbon atoms or when they contain more than five carbon atoms and solid matter.
Olefinic compounds are almost non-existent in crude oil and are produced by processes such as thermal or catalytic cracking. This group of compounds are important petrochemical intermediates and monomers because of the double bond in their molecules.
Ethylene (or ethylene) is the simplest alkene hydrocarbon, containing two hydrogen atoms each bonded to each carbon with two carbon atoms bonded by double bonds; C2H4. The molecule cannot rotate around the double bond, so all six atoms are in the same plane.
Etene (Ethylene): (C2H4) Etene is the smallest alkene member. It is a colorless gas at room temperature. Sometimes it is technically incorrect to describe it as "ethylene", but this definition has been taken for granted because it is part of a common parity. Ethane is a very important industrial chemical. First of all, it is the basic raw material of polyethylene plastic production. Polyethylene is used to make everything from shopping bags to packaging materials, lubricants and even some detergents. More than half of the total ethane production is used for polyethylene production. Polyethylene is produced in a process that requires highly pure etene and a metal catalyst. Pyrolysis gasoline from ethylene cracking furnaces consists mainly of C5 and heavier (C5 +) hydrocarbons (See PE Polymerization)

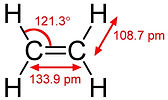

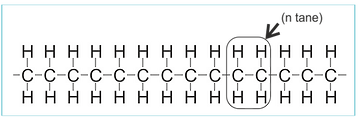
Propene (Propylene): (C3H6) Propylene (or propene) is the simplest alkene molecule after ethylene; C3H6 It is gaseous at room temperature and pressure, is colorless and has a specific odor. It is found in coal gas and is obtained by cracking natural gas or oil. Propene is a colorless gas with a weak, but unpleasant odor that has been described as somewhat sweet. It is a byproduct of petroleum refining, although it can also be produced in a laboratory setting. Propene serves as a raw product for a number of industrial chemicals. Most importantly, it can be polymerized to form polypropylene, which makes up two-thirds of all propane used. Polypropylene ropes are the primary component in a range of textiles, including carpets and thermal underwear. Propend is also used to make acetone and isopropyl alcohol (rubbing alcohol). Polypropylene production is done in the same way as polyethylene production.

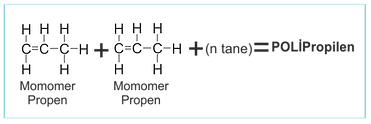

Butene (Butylene): ( C4H8) Butene is a colorless gas containing four structural isomers (different forms), each with slightly sweet odors. Its main use is in the production of polymers for synthetic rubber tires. Isobutylene isomer is used in the production of methyl tert-butyl ether (MBTE) added to gasoline to support octane.
Alkenes on butane are often divided into smaller structures for use in the production of polymers such as polyethylene and polypropylene. The exception is heptene, which is used as an additive in some lubricants.
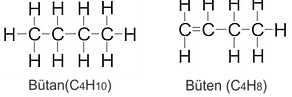
E - Z Isomers
When an alkene has more than one substituent, the double bond geometry is described using E and Z tags. These tags come from the German words entgegen, meaning "opposite", and zusammen, meaning "together".
The closed formulas of the isomers are the same, the three-dimensional arrangement of the atoms in space is different.
In the EZ Isomer, the positions of the large, primary groups attached to the atoms making the (=) bond are compared.

ZButan:

E Butane:
Alkynes: (CnH2n-2)
The formula of the smallest alkyne is C2H2 and the specific name of this compound is acetylene. For this reason, alkynes are also called acetylenes.
In a hydrocarbon, if there is at least one triple bond between two carbons, the hydrocarbon in question is in the alkyne class. The bond angle is 180 ° C. The first three members are gas, the latter are liquid. They are insoluble in water. Liquid ones have densities smaller than water. Following the general trend that alkenes are more reactive than alkanes, alkynes are more reactive than alkenes, making them the most reactive of the three basic classes of hydrocarbons.
Meat (Acetylene): (C2H2) These two carbon molecules are a colorless gas that is exceptionally unstable when pure. But it is also useful in some industrial settings. It can be processed without dissolving, usually by mixing with other ingredients. It is explosive as it is highly reactive. Major uses of acetylene include its conversion to ethylene and a base of acrylic acids as a combustion component in acetylene welding and for the production of polyethylene.

Propin (Methyl Acetylene): (C3H4) It is a three-carbon acion, which is also a colorless gas. It is used as an alternative to acetylene in welding because it can be safely condensed into a liquid for shipping and storage. It is the starting material of various chemical compounds such as propylene, polypropylene plastics and acrylonitrile, isopropyl alcohol, propylene oxide; It is also a valuable petrochemical used in the production of gasoline and a very important polymer used in the production of various materials in our lives (eg automotive construction materials, packaging and electronic materials). Propin has also been researched for use as a rocket fuel for spacecraft intended for low Earth orbit.
Its biggest advantage is that, unlike hydrogen, propine remains a liquid without the need for cryogenic storage.

Processes
Büten-1 Production Process:
Butene-1 is obtained from ethylene by the selective dimerization reaction. The catalyst system is a derivative of titanium and prevents the isomerization of butene-1 to butene-2.
The polymerization purity ethylene is used in the process. The Alfabutol process is simple. Since the working temperature is low (50-60 ° C), there is no need for a heating medium in the reaction section; keep the reactants in liquid phase
a low working pressure is sufficient for Use solvents in the reaction and process.
indestructible; no special or expensive materials are required (construction only
carbon steel is used). Polymerization purity ethylene (in gaseous form) is fed through a dispersant to the reactor in liquid phase conditions. Catalyst is continuously introduced into the reactor solution, where ethylene undergoes the dimerization reaction in the liquid phase. The reaction heat is removed by a conventional air or water-cooled pumping system. The product is taken from the bottom of the reactor; It is in liquid form and mixed with spent catalyst.
The spent catalyst in the product stream is separated in the catalyst removal section and
thrown away (for example, sent to the incinerator); hydrocarbons are divided by fractionation.
goes. There are two columns here. In the first, unreacted ethylene is separated and returned to the reactor. Pure butene-1 is taken from the top of the second column and oligomers (predominantly C6 olefin) from the bottom.
Büten-2 Production Process:
It is a process in which butene-2 and ethylene are produced from propylene by the reaction of triolefin. Propylene, of ethylene and nbutylenes; or other triolefin processes where ethylene, propylene and C5 - C7 olefins are obtained from butylenes.
The propylene (and returning propylene) is heated and fed into the fixed bed metathesis reactor.
fed. In the metathesis reactor, 2 moles of propylene are converted into 1 mol of ethylene and 1 mol of butene-2. The small amount of coke accumulating on the catalyst is cleaned by a periodic regeneration process. The reactor stream passes to the fractionation column; where ethylene separates, unreacted propylene returns and the butylene product passes into the next fractionation. The recycled propylene separates from the propane contained in the previous fractionation column and goes to the reactor. The small amount of C5 + olefins formed in the reaction is separated from the butylene stream and butylene is removed from the top of the arm.
Commercially pure (93%) propylene, 30% ethylene, 58% butylenes (90% butene-2), 9%
propane by-product (80% propane) and
3% C5 + weights are obtained.
Propylene is made by pyrolysis or supplied from the refinery; its concentration can vary over a wide range. The higher the propylene concentration in the feed stream, the higher the efficiency.
Alcohol Production Process:
Ethylene, aluminum, hydrogen, solvents, air and water ethylation, oxidation and
It is a process in which even-numbered straight-chain alpha-alcohols are produced by hydrolysis reactions.
Very pure alumina or alum is also produced as a by-product in the process.
Aluminum powder is mixed as slurry in a suitable solvent and
It is hydrogenated with dry hydrogen in the environment with triethylaluminium (TEA). The resulting product, diethylaluminium hydride, reacts with ethylene to form triethylaluminum. For each mole introduced into the polymerization, 2 moles of triethylaluminum are returned to the hydrogenation stage.
(TEA) reacts with ethylene to form high molecular weight alkylalumines. By decomposition after polymerization, a mixture of alkyl chains from C2 to C22 is obtained. The proliferative reaction is very exothermic; As the proliferating chain and (TEA) react violently with water, the heat released is transferred by a hydrocarbon. For optimum efficiency, the reaction is done at high pressure and low temperature.
The product that grows is converted into alkoxides by oxidizing with dry air under controlled conditions. The oxidation reaction is very exothermic and gives esters, ethers, oxides, aldehydes as byproducts; these are removed with an excess of solvent before hydrolysis.
Hydrolysis: Purified alkoxide is converted into crude alcohols and alumina sludge by reacting with water. After a purification process, the water is separated by drying and 75% Al2O3 CATAPAL alumina with high purity is obtained. When a high purity alum solution is desired, the hydrolysis reaction is carried out with 98% sulfuric acid.
Fractionation: Crude alcohols are dried and distilled; By fractionation, each alcohol can be obtained individually or collected as binary mixtures. High molecular weight alcohols are distilled in vacuum.
Ammonia Production Process:
It is a process where ammonia is obtained from natural gas by methanation reaction. Other hydrocarbons can also be used as raw materials.
After mixing with the return hydrogen, the natural gas is heated and sent to the desulfurizer to desulfurize it, through which the saturator passes; Meanwhile, while heating the natural gas coming from the feed tank, it cools down somewhat.
In the saturator, it mixes with the hot circulating process condensate, the outgoing stream,
the steam / carbon ratio is 2.8 / 1, mixed with a little more steam and hot
In the first reformer, the gas is brought to a temperature of 700-800 ° C and a pressure of 28-45 bar by preheating. The gas mixture is fed to a second reformer unit and the process
heated by air, here its temperature reaches 900-950 ° C. Hot gas is cooled
(by producing superheated high pressure gas) and enters high temperature (HT) and low temperature (LT) converters (5,6); In these units, most of the carbon monoxide turns into carbon dioxide. The cooling process of the process gas in HT and LT converters is provided by heating the circulation water fed to the saturator.
The heat of the gas leaving the LT converter is used for preheating the high pressure boiler feed water (BFW = boiler feed water).
The cold gas exiting the LT converter is taken into a CO2 removal unit;
from here directly to the synthesis gas compressor and then to the methanator
expense. This layout minimizes the need for outside heat. The process gas is dried and comes to the synthesis unit. Conventional catalysts are used in synthesis production. Any ammonia converter unit can be used. After the hot gases leaving the converter are cooled by high pressure boiler feed water and converter feed gas, they pass to the refrigeration unit, from which ammonia is obtained in pure form. The side stream from the circulator comes to a simple refrigeration unit. Here, the unreacted parts condense and leave for use as fuel, while the hydrogen returns to the circulation pump.
Production prices depend on the natural gas price and capital. Raw material and auxiliary material (fuel) cost varies according to the flow chart of the factory and geographic location.
Ammonium Nitrate Production Process:
It is a process in which ammonium nitrate is obtained by the neutralization reaction of nitric acid with ammonia; The product is 99.8% (by weight) ammonium nitrate (AN) solution. In the carnit process, there is no need for external heat, energy efficiency is high and capital is low.
Nitric acid and ammonia gas react in a highly reversible flow system.
inserted; the working pressure is kept higher than the vapor pressure of the solution. No process steam is produced. By adjusting the return rate, the solution return stream is cooled (by a series of heat exchangers), keeping the temperature under control. The hot return solution exits the reactor at 185-190 ° C, flows into the heat exchanger where it releases its heat; This heat is used in the production of 99.8% product solution. Other modifiers in the system are evaporators and they give export steam with 95% solution. In the system
The solution is slightly ammonia. Free ammonia in the product is neutralized by injection of a small amount of nitric acid before pressure reduction. The carnite process is characterized by an isobaric concentration process.
pressure reduction and self-regulation of the adiabatic jet. There is no gas flow; The ammonium nitrate content of the liquid stream is at the level of 400 ppm by weight. The process's own energy is sufficient up to 45% acid solution; Higher concentrations of export steam are obtained.
Aniline Production Process:
It is a reaction from phenol in which aniline is produced by the ammonolysis reaction.
After the phenol taken from the tank is mixed with excess ammonia, it is evaporated, heated and fed to a fixed bed adiabatic reactor. Phenol and ammonia react with the catalyst in the reactor to form aniline and water. The gas stream leaving the reactor is partially condensed, the liquid and gas phases are separated. The gas phase is unreacted ammonia; it is compressed and recycled. The liquid part is distilled after the ammonia has been removed and very pure aniline is obtained. A small amount of unreacted phenol is recovered as the aniline-phenol azeotrope and returned to the reaction. The most important feature of the process is the Halcon SD catalyst; phenol to stoichiometric efficiency
converts to ammonia at a very close level. Therefore, the purification process is very simple and the resulting aniline is exceptionally pure. The life span of a catalyst is quite a long time, like seven years.
Another feature of the process is to change the proportions of the reactants.
is to allow. Thus, predominant production of the by-product diphenylamine is possible. An additional purification system is required to obtain very pure diphenylamine. Even in such an operating state, the life span of the catalyst does not change.
The required capital is much lower than for technology operating on the basis of nitrobenzene reduction; A factory with a capacity of 50 000 t / year was established for 12.6 million dollars (1985). Excessive phenol content, where very pure aniline production is desired
This process is preferred when it is desired to produce with a small amount of capital. Another advantage of using phenol as a raw material is that the hazardous nitriding reaction and acid cleaning stage found in conventional benzene-based technologies.
it is the absence of mesinin. Therefore, there are very few waste problems.
Polyethylene Production Process:
High pressure gas phase polymerization from ethylene, low density
It is a calcic process in which polyethylene is obtained.
Ethylene gas is first compressed in the front compressor up to 250-300 atmospheres, the second
sent to the compressor. Pressure here
It is raised to 3500 atmospheres. The pressure of the reactor depends on the design of the factory, the type of catalyst and the grade of the desired product. The compressed ethylene is polymerized in the tube reactor after a preheating. Unreacted ethylene at the exit of the reactor is sent to two separators with medium and low pressure. This ethylene is returned to the pre-separator and second compressor via a booster.
The resulting polyethylene is fed into an extruder; Here necessary additives are added and the final product is granulated. The polymerization rate is very high due to the type of reactor used. Expenses of auxiliary materials such as water, steam and electricity are low and operating flexibility is extraordinary. The quality of the product obtained is very good. Factories are designed to operate in complete safety.
LLDPE Production Process:
It is a process where linear low density polyethylene and high density polyethylene are obtained by gas phase polymerization at low pressure from ethylene. In a fluidized bed reactor, using suitable solid catalysts, gas phase polyethylenes covering a wide range can be produced. The product is dry, flows easily and is in the form of granules that do not contain fine particles. Melting index and molecular weight
its distribution is controlled by the choice of specific catalysts and operating conditions. The density of the polymer in the product
adjusted by the amount of co-monomer. Catalyst efficiency is very high; This property eliminates a catalyst separation after the reaction.
The feature of the process minimizes environmental pollution, fire and explosion hazards.
is keeping level; therefore it is very easy to operate and maintain.
Gas ethylene, co-monomer and catalyst are introduced into the reactor; in the reactor, growing
there is a fluid-bed formed by polymer particles; 20 kg / cm2
pressure and works around 100 ° C. The reaction gas flowing into the reaction bed is circulated by a single stage centrifugal compressor; Thus, the polymerization reaction
While providing the necessary raw material, reaction heat is removed from the bed.
The circulation gas is cooled through a heat exchanger. The granular product flows intermittently into the product discharge tanks. Here, unreacted gas is separated from the product. The extracted gas is compressed and sent back to the reactor. Hydrocarbons remaining in the product are swept away with nitrogen. The granular product is formed into pellets in a low energy system.
The density of the polymer is easily controlled in the range of 0.915-0.970.
The molecular weight distribution is narrow or medium width, relative to the catalyst.
The melt flow can be varied from 1 to over 200.
Non-Hydrocarbon Components of Petroleum
In addition to hydrocarbons consisting of carbon and hydrogen, there are also compounds containing some other elements in crude oil; These elements are called heteroatoms ("other atoms"). It is not a compound hydrocarbon with heteroatoms bonded carbon and hydrogen. The main heteroatoms found in crude oil are sulfur and nitrogen, as well as very little vanadium, nickel, sodium and potassium.
Sulfur Compounds
The type and amount of sulfur compounds vary between 2-6% by weight, depending on the location of the crude oil. Crude oil containing more than 1% dissolved hydrogen sulfide is classified as “sour” petroleum. Sulfur compounds have their own offensive odor, which makes them immediately detected, making it easier to avoid these compounds, which are particularly dangerous to health.
In crude oil, sulfur exists either as hydrogen sulfide (H2S), as compounds (eg mercaptans, sulfides, disulfides, thiophenes, etc.) or elemental sulfur and has poor thermal stability; During refining, they break down into hydrogen sulphide and simple organic sulfur compounds. Mercaptans are formed by the replacement of a hydrogen atom in hydrogen sulfide with a hydrocarbon group; they are formed during the distillation of crude oil. When two hydrogen atoms in hydrogen sulfide are replaced by hydrocarbon groups, sulfur compounds are formed; such as thiophene (C4H4S). The sulfur compounds in each crude oil differ in amount and type, but their amounts in their heavy fractions are more, more stable and more complex.
Hydrogen sulfide is the most important of the conditions that cause corrosion in refinery process units. Other corrosive compounds are elemental sulfur and mercaptans. Corrosive sulfur compounds are badly smelling.
Pyrophoric iron sulphate is formed by the corrosive effect of sulfur compounds on iron and steel materials used in the construction of refinery equipment, piping systems and tanks. Unwanted substances such as sulfuric acid and sulfur dioxide are released by burning petroleum products containing sulfur compounds.

Oxygenated Compounds
Oxygenated compounds found in petroleum are quite complex and the structures of some of them are not yet fully defined. It is known that in the distillation of petroleum, some compounds are broken down to form cyclic structures called naphthenic acids with carboxylic acids in their side chains, and some phenolic compounds are found at the end of cracking processes. Using the data obtained from refinery streams, it was determined that most of the oxygenated compounds in petroleum are complex carboxylic acids, phenols and cresols, and non-acidic compounds such as esters, amides, ketones and benzofurans are found to be less. Asphalts contain high-oxygen compounds.
Since most of them are acidic, oxygenated compounds must be removed from crude oil and its fractions. The total acid value of crude oil can vary between 0.03-3%. Since S and N are kept under control in the currents given to catalytic processes, oxygenated compounds do not pose a significant problem.
Acidic oxygen compounds:
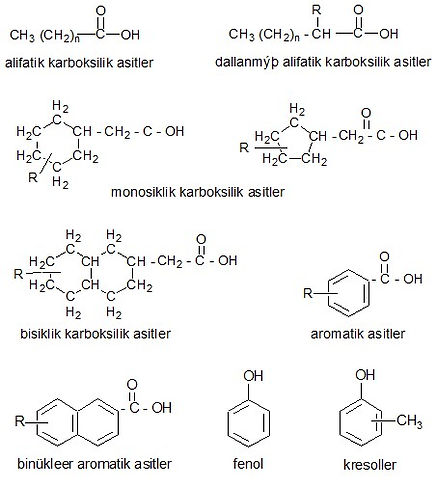
Non-acidic oxygenated compounds:
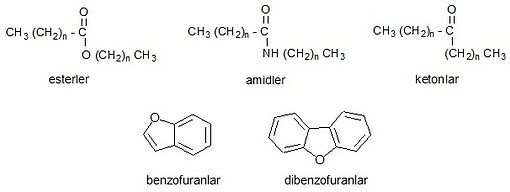
Nitrogenous Compounds
Most crude oils contain less than 0.1% by weight of nitrogen. As nitrogenous compounds are heat resistant, they are found in trace amounts in light refinery streams, while they are more in high-boiling fractions. Nitrogen is in the form of basic compounds in light fractions, in the heavier fractions it is mostly non-basic and may contain trace amounts of Cu, V, Ni metals. Nitrogen oxides are formed in the process furnaces. In catalytic cracking and hydrocracking processes, ammonia and cyanides are formed by the decomposition of nitrogen compounds and cause toxic effects to catalysts; Therefore, the streams given to catalytic processes are passed through the hydrotreating process, reducing the nitrogen content to harmless levels.

For more detailed information about: Prof.Dr. Bilsen Beşergil
You can reach the (Celâl Bayar University) blog page here.