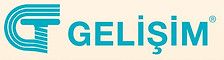


Hydrocarbons
It is an organic compound consisting of two elements, hydrogen and carbon. Most of the petroleum composition consists of hydrocarbons of varying lengths.
The smallest hydrocarbon methane consists of a single carbon atom and four hydrogen atoms. However, hydrocarbons can consist of hundreds or thousands of individual atoms linked together in many ways, including chains, circles, and other complex shapes.
In order to classify the properties of hydrocarbons, they are divided into several basic types.
Alkanes: These are called saturated hydrocarbons. That is, they only contain single bonds between all carbon atoms. Alkanes are the basis of petroleum fuels and exist in linear and branched forms.
Unsaturated Hydrocarbons: Hydrocarbons that have one or more double bonds between carbon atoms are called alkenes.
Cycloalkanes: Any hydrocarbon containing one or more ring structures.
Aromatic Hydrocarbons: Aromatic hydrocarbons , also called arenes, are a unique class of carbon molecules in which carbon atoms are bonded by successive double and single bonds. This class of molecules has special ring structures in which the bonds between carbon atoms are an intermediate bond between single and double bonds.
Molecules in this class contain the industrial solvent "benzene".
Benzene (C6H6): Like other hydrocarbons, benzene is a natural component of petroleum. It is a colorless, flammable, sweet-smelling liquid at room temperature and is a component of most gasoline blends because of its high octane number.
Benzene is also highly carcinogenic and is well known to cause bone marrow failure and bone cancer. Of course, its carcinogenicity is not well known when used as an additive in aftershave and other cosmetics due to its "pleasant aroma".
The largest use of benzene (50%) is the product of styrene and polystyrene plastics. It is also converted into a molecule known as cyclohexane, which is important in Nylon production. About 15% of benzene is used to produce cyclohexane. Smaller amounts are used in everything from pesticides to rubber.
The benzene structure can be drawn in two ways. In the first, the double bond character is drawn explicitly. In the short handed version, a circle is drawn inside the ring to show the structure. There is only one hydrogen bonded to each carbon atom in benzene.
I. and II below. drawings are identical. III in practice. drawing is used.
Benzene is a colorless, flammable liquid with a boiling point of 80.1 ° C and a melting point of 5.5 ° C.
Binuclear Aromatic Hydrocarbons: They are compounds that contain two benzene rings in their molecules.
Hydrocarbons
It is an organic compound consisting of two elements, hydrogen and carbon. Most of the petroleum composition consists of hydrocarbons of varying lengths.
The smallest hydrocarbon methane consists of a single carbon atom and four hydrogen atoms. However, hydrocarbons can consist of hundreds or thousands of individual atoms linked together in many ways, including chains, circles, and other complex shapes.
In order to classify the properties of hydrocarbons, they are divided into several basic types.
Alkanes: These are called saturated hydrocarbons. That is, they only contain single bonds between all carbon atoms. Alkanes are the basis of petroleum fuels and exist in linear and branched forms.
Unsaturated Hydrocarbons: Hydrocarbons that have one or more double bonds between carbon atoms are called alkenes.
Cycloalkanes: Any hydrocarbon containing one or more ring structures.
Aromatic Hydrocarbons: Aromatic hydrocarbons , also called arenes, are a unique class of carbon molecules in which carbon atoms are bonded by successive double and single bonds. This class of molecules has special ring structures in which the bonds between carbon atoms are an intermediate bond between single and double bonds.
Molecules in this class contain the industrial solvent "benzene".
Benzene (C6H6): Like other hydrocarbons, benzene is a natural component of petroleum. It is a colorless, flammable, sweet-smelling liquid at room temperature and is a component of most gasoline blends because of its high octane number.
Benzene is also highly carcinogenic and is well known to cause bone marrow failure and bone cancer. Of course, its carcinogenicity is not well known when used as an additive in aftershave and other cosmetics due to its "pleasant aroma".
The largest use of benzene (50%) is the product of styrene and polystyrene plastics. It is also converted into a molecule known as cyclohexane, which is important in Nylon production. About 15% of benzene is used to produce cyclohexane. Smaller amounts are used in everything from pesticides to rubber.
The benzene structure can be drawn in two ways. In the first, the double bond character is drawn explicitly. In the short handed version, a circle is drawn inside the ring to show the structure. There is only one hydrogen bonded to each carbon atom in benzene.
I. and II below. drawings are identical. III in practice. drawing is used.
Benzene is a colorless, flammable liquid with a boiling point of 80.1 ° C and a melting point of 5.5 ° C.
Binuclear Aromatic Hydrocarbons: They are compounds that contain two benzene rings in their molecules.
About
Kyäni, nutritional supplement products consisting of beneficial ingredients; It delivers to more than 50 countries around the world with unique business opportunities. We use Kyäni products daily to maintain our ideal health, share these products with others, devote a certain amount of time to work almost every day to build and maintain our business, and share our success with others by involving others in the Kyäni opportunity or contributing to the Potato Pak and Caring Hands programs.
About
Kyäni, nutritional supplement products consisting of beneficial ingredients; It delivers to more than 50 countries around the world with unique business opportunities. We use Kyäni products daily to maintain our ideal health, share these products with others, devote a certain amount of time to work almost every day to build and maintain our business, and share our success with others by involving others in the Kyäni opportunity or contributing to the Potato Pak and Caring Hands programs.
Page Under Construction.
Page Under Construction.
Training / Knowledge / Solution Platform
Polymerization
The reactions that lead to the obtaining of polymer units starting from monomer units, the process carried out is called polymerization. In other words; Polymerization is when a large number of identical or different monomers combine with each other through a chemical process to form long chains.
Most commercial polymers have an average molecular weight of 10 to the 4 to the 10 to the 7. Polymer is a mixture of macromolecules with a molecular weight distribution. The viscosity of their melted forms and solutions is quite high. Since the polymerization reaction is exothermic, the resulting heat must be removed from the environment in order to maintain isothermal conditions.
Polymerization process requiring certain catalysts; It is one of the two main processes used in plastic production (the other is polycondensation).
Monomers such as ethylene and propylene are linked together in the polymerization reactor, forming long polymer chains. Since the monomer material in the industrial industry is not in a form that can serve the purpose and be processed, the raw materials to be used are polymers (: polymeric materials). Polymeric materials can be processed at lower temperatures and show much lower resistance to pressure and thermal resistance than the other two.
This situation, which seems to be a disadvantage at first, is judged to be advantageous when realizing that polymeric materials are more preferred. Since they can be processed at lower temperatures and have a lower density, they are lightweight, making them much more integrated with our daily life.
They also have the luxury of appearing at almost every point that our eyes touch. As a matter of fact, we can detect tens, hundreds of polymeric materials in the same environment, while our metal and ceramic material detection does not exceed the fingers of one hand. Polymeric material is available on almost every product, such as pens, computers, chairs, packaging materials, holders, hangers, files, etc.
As stated above, the main reason for this is that the processability of the polymeric material is easy and practical. However, the following situation should not be forgotten; polymeric materials are also not preferred to be used directly in the product process. In daily life, in the field of particle application, a number of additives are included in the content to increase the usability, aesthetics, mechanical and thermal resistance of the product.
Monomer With the polymerization of ethylene, all monomers are combined to obtain a polymer structure, which is a multi-monomer.
Polymers can be classified in various ways, according to their production method and the interests of the users; For example, organic chemists are concerned with the arrangement of atoms in polymer chains; For structural engineering, the tensile strength and density of the polymer are important. There is no single system that can be applied in classification.
There are classifications according to Polymerization Mechanism, Stoichiometry / Addition Process, Structure of Proliferated Particles, Starting Method, Reaction Environment, Product Structure, and Reaction Substance Structure.


Polymer Classes
Polymers can be classified in various ways, according to their production method and the interests of the users; For example, organic chemists are concerned with the arrangement of atoms in polymer chains; For structural engineering, the tensile strength and density of the polymer are important. There is no single system applicable to classification; Some classifications are briefly described in this section.
Classification According to Chemical Bonds:
(1) Thermosets: It does not enter the form of melt that can be re-processed with heat.
(2) Thermoplastics: They can undergo heat treatment over and over. There are no cross links between polymer chains.
Classification According to Obtaining:
(1) Natural polymers: derived from trees.
(2) Synthetic polymers: Polyethylene, which is the simplest synthetic polymer, can be given as an example.
(3) Semi-synthetic / natural polymers: They are obtained by modification of natural polymers.
Classification According to Chemical Properties:
(1) Organic polymers: They contain atoms such as hydrogen, oxygen, nitrogen and halogen gases such as fluorine, chlorine, bromine, iodine, primarily carbon atoms in their structures.
(2) Inorganic polymers: There are 4th and 6th group elements in the periodic table instead of carbon atoms in the polymer main chain. Like Silicon, Boron, Germanium.
Classification According to Physical Properties:
(1) Amorphous polymers: Molecular chains are in the form of wool balls randomly intertwined with each other.
(2) Crystalline polymers: All of the polymer chains have entered a certain order or crystallized.
Classification According to the Synthesis Method:
(1) Condensation polymers: Polymers formed by the reaction of two monomers and release of water.
(2) Chain polymers: They are polymers formed by the synthesis reaction of opening a double bond and joining monomers to each other like rings of a chain.
Classification According to Bond Structure:
(1) Linear polymers: Such as high density polyethylene.
(2) Branched polymers: such as low density polyethylene.
(3) Cross-linked polymers: Like vulcanized rubber.
Classification According to Polymerization Mechanism: Classification is an advantageous method; Because, in this type of classification, important information about reaction rates and molecular weights of polymers can be obtained.
Polymerizations are divided into two basic classes according to the bond-formation mechanism:
(1) step-growth reaction polymerization,
(2) chain-growth reaction polymerization; These in turn are divided into various subgroups according to the structure of the monomers and the polymerization conditions.
The step-reaction polymerization mechanisms can be grouped into six groups:
1. Carbonyl addition-splitting reactions: Direct reaction, intermolecular exchange reaction, acid chloride or acid anhydride reaction, inter-surface condensation reaction, ring and chain formation reaction.
2. Carbonyl addition-substitution reactions.
3. Nucleophilic substitution reactions.
4. Double-bond addition reactions.
5. Free-radical binding
6. Aromatic electrophilic-substitution reactions.
Classification According to Stichiometry:
The classical classification of polymerization is based on stoichiometry. Addition polymerization is defined according to IUPAC as "polymerization carried out by a repeated addition process". In addition polymerization, the monomer units are attached together and the growing chain is the sum of all atoms in the monomers. This separates the total addition polymerization from condensation polymerization; In the second case, a small molecule such as water, hydrogen chloride or ammonia is separated while the monomer combines in polymers.
In this case, the weight of polymers obtained by addition is equal to the sum of the weight of monomer units, while the weight of polymers obtained by condensation is slightly less than the sum of the weights of monomers.
The terms "addition" and "condensation" refer only to the stoichiometric meaning of the reaction; that is, it indicates whether a small molecule such as water is separated in the reaction, but does not describe the mechanism of the reaction. The terms chain-reaction and step-reaction describe the mechanism of the reaction.
Condensation polymerization is done by condensation processes by separating simple molecules (IUPAC); The products formed are called condensation polymer. Esters and amides from simple condensation reactions of monofunctional monomers, polyesters and polyamides are obtained from the reactions of difunctional acids and difunctional alcohols or amines.
Classification According to the Structure of Reproducing Particles: The chemical structure of the active center in the proliferation creates another classification scheme especially for vinyl polymerization. Accordingly, polymerizations are classified as ionic, radical, etc. Ionic reactions are also divided into anionic, cationic and zwitterionic polymerization. Charge transfer complexes are another group of particles that proliferate. Coordination polymerization is also a well-known type of reaction; In the proliferative step, a complex is formed by coordinated binding. This type of polymerization is more appropriate to call addition polymerization. Polymerization with Ziegler-Natta catalysts is typical. If the propagation step affects the stereoregulation of the polymer, the reaction is called stereopecific polymerization.
Classification According to Starting Method:
According to the effect of the applied polymerization method on the starting reaction, polymerizations are divided into various classes as catalyzed, thermal, enzymatic, electrochemical, mechanochemical and radiation-affected. Plasma state can also be used to start. The word catalyst is not used much for initiation reactions. The difference between true catalysts and initiators must be known; Initiators are in the polymer molecule or in other words they are spent during the reaction. If a photon source is used, with or without chemical initiators, it is called photopolymerization.
Classification According to Reaction Environment:
There are important practical and mostly theoretical differences in the behavior of polymerizations according to the environment in which the reaction is carried out. Therefore, the classification made according to the polymerization medium is used a lot. Four polymerization methods are used in industrial applications. These are mass, solution, suspension and emulsion. Surface and solid-state polymerizations are also applied to a limited extent. Polymerizations can also be defined as homogeneous or heterogeneous, depending on the solubility of the raw materials and product.
Classification According to the Structure of the Product: The products obtained at the end of polymerization are divided into various classes. Classifications such as stereoregular, cross-linking, isomerization, ring opening polymerizations, block and graft copolymerization can be made.
The structure of functional groups in polymers can determine the name of a polymerization reaction; such as polyamide formation and polyesterization. The physical properties of the polymers obtained can also be used to describe reactions; Such as pearl polymerization, popcorn polymerization.
Classification According to the Structure of the Reacting Substances: According to the nature of the reactants, polymerization processes are divided into two important classes;
(1) homopolymerization ( They are formed by repeating a single monomer unit.)
(2) copolymerization ( It is a polymer consisting of a mixture of two monomers.)
Apart from this, some simple classifications can be made according to the nature of the reactants: vinyl, diene, allyl, urea-formaldehyde, ethylene oxide polymerization, etc.
Polymerization of PE
Polyethylene (: PE) is a thermoplastic polymer represented by the general formula (C2H4) n obtained by the polymerization of ethylene from ethylene. (Gaseous Ethylene is obtained at the end of the cracking process of crude oil.
A method that is applied very little; It is a method of catalytic dehydrogenation of alcohol (: Ethanol). There are three processing methods.
Ethylene to be polymerized according to any of these methods turns into a solid substance when exposed to high pressure and high temperature while it is in gaseous state. Polymerization can be initiated in a variety of ways; by catalysts, oxygen, thermally or by radiation (radiation). Mostly organic peroxides are used as free radical catalysts in the production of LDPE; these include peroxydicarbonates, hydroperoxides and long chain peroxides. In commercial production, the retention time in the reaction is 3-15 seconds.
1- High Pressure and Temperature Method LDPE (0.910-0.925 g / cm3)
In this process, ethylene is polymerized under 1,000-3,000 Atm atmospheric pressure, between 150-300 ° C by heating with oxygen or other catalysis. Later, when it solidifies, it becomes hard and oily. Melting point
It remains below 110-120 ° C.
On the other hand, it is seen that the rate of branching in molecular chains is high. For example, in a chain of 1000 carbon atoms, about 80 branches are formed. Their density is low. Low density polyethylene is resistant up to 75 ° C and can be used continuously at temperatures up to this degree. Polyethylene in this group is 50-85% transparent. The degree of transparency has to do with density. The higher the density, the higher the transparency.
Low density polyethylene has properties such as being suitable for food technology, being suitable for processing and good mold filling since it is not under tension.
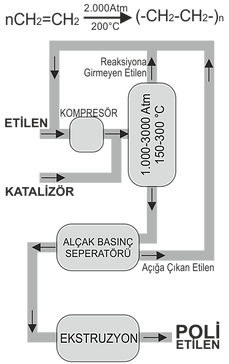
2- Medium Pressure and Temperature Method MDPE (0.926-0.940 g / cm3)
It is polymerized at 1.000-1.500 Atm atmospheric pressure and 100-150 oC.
3- Low Pressure and Temperature Method HDPE (0.941- 0.965 g / cm3)
It is polymerized by heating below 100 ° C and by using special catalysis systems used only for this purpose.
Mass Polymerization
In mass polymerization, there is only monomer in the reaction medium, no solvents and suspending liquids. Charge is only monomer with little additive. In most mass polymerizations, the polymerization initiator is soluble in the monomer. However, there are also mass polymerizations using solid catalysts that are insoluble in monomers, as in the production of high density polyethylene (HDPE) obtained by polymerization of ethylene in the gas phase.
In mass polymerization, as the polymer concentration and molecular weight increase, the viscosity of the medium increases, the mixing efficiency and heat-transfer rate decrease. In mass polymerizations where the conversion amount is limited, the reactor content is transferred to a second container to complete the conversion or remove the excess monomer.
In some mass polymerizations, an inert solvent is added to the initial charge in order to prevent overheating and to control the initiation of polymerization; however, the solvent is gradually replaced by the standard charge. Some mass polymerizations can be initiated like a solution polymerization. For example, poly (hexamethylenadipamide) (nylon 66) is started in an aqueous solution, then completed as a mass polymerization. As the reaction progresses, the diluent water and the water formed as a byproduct in the polymerization are evaporated off. At the end of the process, the amount of water that can remain in the environment is insignificant. Since evaporation of water consumes the heat of polymerization, heat is added to maintain the required ambient temperature.
The separation of the by-product ethylene glycol, which is formed in the production of poly (ethylene terephthalate), is important because the separation rate affects the polymerization rate and time. Since ethylene glycol cannot be separated from the viscous polymer solution under normal conditions, the final stage of the polymerization is carried out in vacuum.
As in poly (vinyl chloride), if the polymer is insoluble in the monomer, at the end of the reaction, a slurry containing the polymer in solid form in the monomer is obtained. In this case, a two-stage process is applied. In the first reactor the conversion is kept at the level of 7-12% and in the second reactor at the level of 80-85%. The polymer slurry is still flowing at low conversions. Polymer precipitates settle together, holding the monomer. At 15-20% conversions, the reactor contains the monomer-swollen polymer in a monomer atmosphere. Mixers prevent the formation of large polymer masses. The active monomer diffused into the precipitated polymer polymerizes, the unreacted monomer is recovered.
Mass polymerization is quite common in commercial applications due to its volume efficiency, low pollution, and no need for solvent recovery and purification processes. Studies to find new technologies on this subject are also continuing.
Solution Polymerization
There is no clear distinction between solution polymerization and mass polymerization; sometimes mass polymerization is classified into solution polymerization. Solution polymerization uses a solvent that dissolves the monomer and polymer; The solvent / monomer ratio is much greater than the 'solvent additives' / monomer ratio in mass polymerization. The solution is a homogeneous phase, its viscosity increases as the molecular weight and concentration of the polymer increases.
Solution polymerization is similar to that of mass polymerization; however, even inert solvents affect the reaction rate or the diffusion process. If the diluent is not inert (properties such as chain transfer, polar effects, etc.), the reaction rate and properties of the polymer change significantly.
If the monomer is a gas, the solvent can only hold part of the monomer. While the soluble monomer is separated as a result of polymerization, some monomer passes into the solvent from the gas phase. The effective mass-transfer rates here depend on the degree of mixing, the reactor pressure, and the viscosity of the polymerization.
The initiator or catalyst used in solution polymerization is soluble or insoluble in the diluent. Insoluble catalysts complex with the monomer and direct it, so that the growing polymer chains, and thus the polymer, have a smooth structure. The Ziegler-type catalyst used in the polymerization of propylene is insoluble in diluent media. Linear polyethylene is also produced with insoluble catalysts. Removal of catalyst from solution after polymerization is a difficult process.
Dilution of monomer and polymer with solvent reduces heat load and viscosity compared to mass polymerization. Some solvents affect the rate, degree, molecular weight distribution, and product properties of polymerization.
Solution polymerizations in which the polymer and its solution are used together are very advantageous, as in the production of protective coatings. This method is widely used in the textile industry. After the unreacted monomer has been separated, the polymer solution is used directly by pouring it into a plasticizer (eg DOP).
In order for the polymer product to be marketed in solid form, it must be separated from its solvent and catalyst. These processes require very expensive equipment and energy consumption. For this reason, studies are carried out to reduce the solvent / monomer ratio in solution polymerizations. The optimum solvent / monomer ratio is determined according to the economic balance between the price of the product obtained from solutions with high viscosity and high polymer and the price of separation and recovery of the solvent. Purification may be required to reuse the solvent.
Suspension (or Precipitate) Polymerization
They entered in the suspension polymerization and the polymer is dispersed in a non-solvent medium (mostly water), agitated vigorously to disperse the monomer in small droplets and keep the dispersed small solid polymer particles suspended. Suspension polymerization is also called "bead" or "pearl" polymerization due to the spherical nature of the polymer particles. The polymer particles are 0.15-5 mm in diameter and settle as soon as mixing is stopped. The initiator often dissolves in the monomer; The polymerization is initiated in monomer droplets and proceeds like a miniature mass reaction. In the case where the monomer is dissolved in the water phase but the polymer is not dissolved, the polymerization is initiated in the aqueous phase. The growing polymer chain collapses into a polymer core, absorbs monomer and initiator radicals, and grows into granular polymer particles.
Suspending agents (stabilizers) prevent the dispersion of the monomer, the assembly of monomer droplets and polymer particles among themselves. The size of the monomer droplets and the size, porosity and bulk density of the polymer particles vary according to the water / monomer ratio, the type and concentration of the initiator, the structure and concentration of the stabilizer, the mixing speed and the polymerization temperature. Suspension polymerization is particularly applied in the polymerization of reactive monomers obtained by radical polymerization. The water swallows the heat immediately; the fluid mixture transmits the heat to the reactor surface. The mixture can be pumped and handled in normal systems.
A disadvantage of suspension polymerization is that it requires an additional process step, which requires separation of the polymer from the diluent, and hence devices. Separation can be done by centrifugation or filtration, then the polymer is dried; This method is a method in which the least energy and device is used. Particle size and density affect separation efficiency and retention of the aqueous phase between polymer particles. There is very little water held in high density polymers. If the polymer is to be impregnated with plasticizers later, the high viscosity of the polymer is also a desirable property. The diluent / monomer ratio must be reduced in order to increase the reactor efficiency and polymer density. Water is mostly used as a diluent in suspension polymerizations. There are suspension polymerizations using organic solvents (with methanol) as well as in the copolymerization of styrene and acrylonitrile.
Emulsion Polymerization
Emulsion polymerization has a dispersing medium, mostly water. Monomer droplets and polymer particles are much smaller than in suspension polymerization; With an emulsifier, a stable environment called "latex" is created. The diameter of the monomer droplets provided by mixing initially is 1-10 mm. The emulsifier distributes a small amount of monomer in clusters called "micelles". As the polymerization progresses, polymer nuclei are formed by the growth of colloidally dispersed polymer particles with a diameter of 0.1-0.3 mm. Moderate mixing is sufficient to distribute the monomer, initiator and polymer homogeneously and carry the heat released to the reactor surface. Vigorous mixing is not suitable as it will cause the coalescence of the polymer particles. Emulsion polymerization is highly complex, and several mechanisms have been suggested for initiating polymer particles. Normally, the viscosity of emulsion polymerization is very low and the fluid medium transfers the heat released to the cooling surfaces of the reactor. This method produces commercial mixtures that can be applied directly, such as paints, paper coverings, carpet backings, and various adhesives.
When the polymer needs to be obtained in solid form, suspension polymerization is often preferred to emulsion polymerization; because the suspended particles are larger, the separation and drying processes are easier. Colloidal dispersed polymer particles must be precipitated so that particles are large enough to separate the polymer from the emulsion. Some elastomers such as butadiene rubbers and acrylic elastomers are produced by emulsion polymerization method. The rubber latex is precipitated to obtain particles suitable for filtering and drying processes.
Inter-Surface Polymerization
Inter-surface polymerization takes place at the surface between two insoluble liquids; One of the solvents dissolves one monomer (A) and the other dissolves another monomer (B). The polymer formed between the surfaces of the solvents is solid. If the liquids are not mixed, a solid polymer film is obtained between the surface. The film can be pulled in the form of a continuous string through the surface. Polymerization continues as the liquid-liquid surface area will be formed again with the removal of the film from the liquids.
By shaking the immiscible liquids, polymers with improved properties can be obtained. The process is generally the reaction between the diacid chloride of a dicarboxylic acid dissolved in an inert solvent and a bisphenol or diamine dissolved in water with an inorganic base. The reaction rate of the process at low temperatures is high.
Large quantities of aromatic amines are produced by this method in Japan and Russia. Inter-surface polymerization is used in the production of polycarbonates in the United States. A typical production of polycarbonate is with phosgene and bisphenol A. Phosgene is added to bisphenol A dispersed in a mixed inert organic solvent and aqueous sodium hydroxide solution. There is a reaction at the surface between organic-aqueous phases. Polycondensation can be catalyzed by a tertiary amine. By terminating the chains with a monofunctional hydroxy compound such as phenol, the molecular weight of the product obtained can be controlled. The polymer dissolves in the organic phase.
Solid-State Polymerization
Solid-state polymerization is used in industry to increase the molecular weight of condensation polymers. There are bifunctional end groups on the condensation polymer chains, unless they react with an impurity or stopper. These end groups can allow polymer molecules to join with each other. Higher molecular weight polymers are obtained by heating some solid polymers such as nylon-66 below their melting point.
Processes
Stack Operation:
In the batch process, all substances are initially put into the reactor and remain together until the end of the reaction. A stable state cannot be reached. During polymerization, the polymerization temperature changes. Often there is an induction period; First, a rapid increase in the polymerization rate and then a decrease with the decrease of the monomer is observed. For this reason, the reactor must be capable of fast heating, sufficient cooling and temperature control. The batch system is suitable for polymerization processes where high conversions are desired. However, problems are encountered in controlling reactions so that each batch contains the same properties. These can be minimized by improved control systems.
Semi-Stack (or Semi-Continuous) Process:
In a semi-batch process, some of the substances can be added in portions or at different times, or some by-products can be removed. In order to control the reaction conditions well, catalyst, monomer, etc. are added according to a set schedule.
In the free radical polymerization of copolymers, it is important to add monomers in portions when their monomer reactivity changes too much; the heat released is evenly distributed.
In some half-batch polymerizations, all substances are initially put into the reactor. However, in order for the reaction to be completed, the resulting by-products may need to be removed from the environment. While these are separated by evaporation, in some cases the heat of polymerization is also removed, in some cases additional heat is required to complete the reaction.
Continuous Operation:
In a continuous process, substances are continuously fed into the reactor by measuring systems and the material is taken continuously. When the polymerization process reaches a stable state, the amount of heat released at any point in the system is constant.
Continuous operation is easy and it is a production method that reduces costs. For this reason, continuous systems are recommended, especially for large volume polymerization processes. For small volumes of specialty products, batch or semi-batch processes are preferred, which are more flexible than continuous processing and allow the production of many different grades of polymer. Some commercial polymers are produced using only batch techniques in order to meet the desired physical properties.
Structure of Polymers
Molecular Weight Averages and Distributions
Just because all polymeric chains in a polymer consist of a single building unit does not mean that all chains are the same. The differences are mainly due to the dimensions of the chains and their deviation from linearity. This is a result of the statistical formation and kinetics of the polymerization process.
Let it be assumed that the polymeric chains formed in the polymerization process are linear and contain different numbers of structural units. The number of building units is called the "degree of polymerization (DP)" and is the most quantitative expression that describes a polymeric chain. In practice, the concept of molecular weight (MW) is used for the same purpose. If the chemical structure of the building unit is known, calculating the molecular weight is quite simple; for polystyrene, for example, the molecular weight of the building unit,
Since M1 = 104 g / g mol, the molecular weight of the polymeric chain is:
MW = M1 x DP
For a polystyrene chain with MW = 100000:
DP = 100000/104 ~ 1000
A polymer is a collection of polymeric chains containing around 1019 different lengths per 1 cm3. The term "average" is needed to describe the molecular weight of the chains in such a polymer.
Structural units in a polymeric chain deviate from the "linear" pattern along the skeletal chain. Side or secondary reactions during polymerization lead to the formation of side chains or branching. Depending on the polymerization conditions, the branches show different shapes. Branches may be in the form of few but long branches, as well as many but short branches; these two cases are examples of two extreme cases. A normal branching is a mixed branching state with long and short side chains.
Amorphous Structure:
Depending on the conformation (shape) of the polymeric chains, polymers exist in two forms: amorphous or crystalline. The word "amorphous" means amorphous and means the absence of a special order for the polymer.
There is no organized order in the molecular structure of an amorphous polymer. Amorphous polymers are mainly made of atactic polymer chains. This causes it to be non-crystalline. Therefore it is a weak structure. Since they are amorphous polymers since they have no degree of crystallinity or crystallinity, they have a low density compared to crystalline polymers. Therefore, the chemical resistance is low and it is transparent. There are weak attractions among polymer chains due to the lack of a patterned structure. Examples of amorphous polymers include polyethylene, PVC, etc. There are. The degree of crystallinity is affected by the polymerization and manufacturing process. Amorphous polymers can have crystallinity with the formation of crystallites or regular areas. These are softer and less resistant to solvent penetration.
All polymers are amorphous in solution at sufficiently high temperatures and some (nearly half) of the major commercial polymers are amorphous. The amorphous shape of a single polymeric chain can be compared to a bead chain that can be arranged in various order. When such a chain is thrown to the ground, it can be scattered but gathered together in the palm of the hand; In these two cases, the detail characteristics of the chain are different, but the general structure is the same.
Cross-linking and Molecular Network (Netting):
Until now, cases have been mentioned where a polymer is a collection of polymeric chains independent of each other, and only intramolecular chemical bonds exist in each chain. Discontinuous physical chemical interactions between chains are very weak and decrease with increasing temperature; The decrease continues until the temperature at which the independent chains move apart and move freely and become fluid.
This type of polymer is also called a "thermo-plastic" or "linear polymer".
Clamped Polymeric Networks (IPN):
Some commercial polymeric systems are produced with the interpenetrating network technology. Although chemical networks are concerned with stable chemical bonds or cross-links, physical networks sometimes form that disappear at high temperatures. The polymeric system is thermoset in chemical networks and thermoplastic type in physical networks.
There are many commercial IPN systems. Some of them are a combination of silicone networks, thermoplastics (PA, PET, PBT, PP, PMO, etc.), conventional elastomers (EPDM, ethylene-acrylate, EVA, etc.), thermoplastic elastomers (TPE) or thermosets (polyurethanes). Another part is the combination products of urethanes with acrylics, epoxy or polyester resins, PS, etc .; in some products they are in three-component systems. They combine with isocyanates and dicyanates, acrylics, PC, PESU and polyester carbonates.
Crystal structure
It shows an ordered order of polymer molecules. Crystalline polymers have an ordered structure made of syndiotactic and isotactic polymer chains. This ordered structure causes the polymer to be translucent. There are also strong attractive forces between molecules. Therefore, it is resistant to chemicals and has a high density compared to amorphous polymers. Although crystalline polymers are well sorted, there may also be amorphous areas. Therefore, these p- olimers are called semi-crystalline materials.
Plastic material such as nylon and other polyamides has crystalline structures. Other examples include linear polyethylene, PET (polyethylene terephthalate), polypropylene, etc. Takes place. These are rigid structures and are less affected by solvent penetration.
Amorphous and Crystal Difference
Geometry / Structure:
Amorphous Solids: Amorphous solids do not have a regular structure; They lack any arrangement or arrangement of atoms or ions, or any geometric shapes.
Crystal Solids: Crystalline solids have precise and regular geometry due to the regular arrangement of atoms or ions.
Melting point:
Amorphous Solids: Amorphous solids do not have a sharp melting point.
Crystal Solids: It has a sharp melting point at which crystal solids turn into a liquid state.
Fusion heat:
Amorphous Solids: Amorphous solids do not have the characteristic heat of fusion, so they are considered supercooled liquids or pseudo-solid.
Crystalline Solids: Crystalline solids have a certain heat of fusion, so they are considered true solids.
Anisotropy and Isotropy:
Amorphous Solids: Amorphous solids are isotropic as they have the same physical properties in all directions.
Crystal Solids: Crystal solids are anisotropic and therefore their physical properties are different in different directions.
Common examples:
Amorphous Solids: Glass, organic polymers, etc. are examples of amorphous solids.
Crystal Solids: Diamond, quartz, silicon, NaCl, ZnS, Cu, Zn, Fe etc. Metallic elements are examples of crystalline solids.
Interparticle forces:
Amorphous Solids: Amorphous solids have covalently bonded networks.
Crystal Solids: Crystal solids have covalent bonds, ionic bonds, Van der Waal's bonds and metallic bonds.
Some Condensation Polymers: Polymerization Methods and Properties
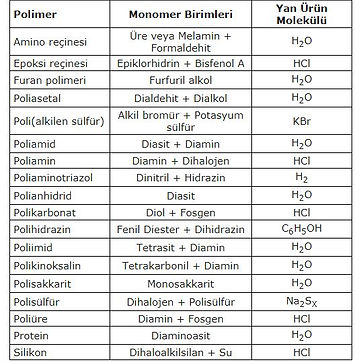

Copolymer / Homopolymer
The polymer chain consisting of one-type units is called homopolymer, and polymers containing two or more monomers are called copolymers.
When a single monomer type goes into polymerization to form a macromolecule we call it homopolymer. In other words, there is a repeating unit. Polystyrene, for example, is a homopolymer in which the repeating unit is styrene residues.
(Some common examples of homopolymers include nylon 6, nylon 11, polyethylene, polypropylene, PVC or polyvinyl chloride, polyacrylonitrile, etc.)
However, copolymers usually consist of random combinations of different monomers to form a random copolymer. However, alternative, block, graft and steroblock copolymers are excluded from this rule. In the alternative copolymer, the monomer units come one after the other. The block copolymer contains long segments of different homopolymers. The graft copolymer, or in other words, the graft copolymer contains a second monomer as a branching on an essentially existing polymer chain.
Also, polymers are defined as linear, branched and network. There is no branching in the linear polymer (A). Graft Copolymers are an example of branched polymers (B). Network polymers are formed when polyfunctional monomers are used instead of difunctional monomers. Network polymers also include crosslinked polymers (C). Because, by cross-linking, polymer chains lose their mobility. For this reason, they cannot be molded as they will not melt or flow. In other words, they fall into the group of thermosetting polymers mentioned above.
The main difference between copolymer and homopolymer is that in copolymers there are two monomers that make the polymer whereas in homopolymer only one monomer repeats and forms the whole polymer. (In a homopolymer, a monomer repeats and forms the entire polymer. On the contrary, there are two monomers in the copolymer that make the polymer. So this is the main difference between copolymer and homopolymer. Also, another difference between copolymer and homopolymer is that there are different types of copolymers depending on how the two monomers are combined. There are several ways to incorporate two monomers, however, this type of coupling variation cannot be seen in a homopolymer.)
Polymers and Brands
The names of polymer compounds are more of a terminology and require some chemistry to pronounce. Due to the long and difficult pronunciation of their pronunciation, they are mostly referred to in the market with the brands given by the inventors or manufacturers. Some of these are as follows;
Phenol-formaldehyde resin >> Bakelite
Para-aramid >> Twaron
Polyethylene terephthalate >> Mylar
Polychloroprene >> Neoprene
Meta-aramid polymer >> Nomex
Polyacrylonitrile >> Orlon
Polyamide >> Nylon
Polyamide 11 and 12 >> Rilsan
Polytetrafluoroethylene >> Teflon
Polyimide >> Ultem
Aromatic polyester >> Vectran
Polytetrafluoroethylene >> Viton
polyphenylene-2, benzobisoxazole >> Zylon


SAP (Super Absorbent Polymer) (Super Absorbent Polymer)
SAP materials are hydrophilic networks that can absorb and retain large amounts of water or aqueous solutions. They can take up to 100,000% of their volume. They can absorb up to 300 to 1000 times their weight in aqueous liquids. Once they start sucking, they trap the fluid and do not release it. Therefore, it is an ideal material for use in products designed to contain liquids such as diapers / diapers, napkins and paper towels, incontinence products, and feminine hygiene pads and liners.
Agricultural covers are made to keep water in the soil, especially in rice paddy fields. The first commercial applications came into our lives in 1978.
The majority are made of sodium polyacrylate and are available in granular form or as fibers. The granular material is a polymer composed of millions of identical sodium acrylate units formed into a chain fence-like structure. These are then bonded together to form the material into a three-dimensional mesh. In its dry state, long polymer chains are wound. When they absorb liquid, they dissolve and the mesh expands. The liquid is then stored in cavities in the molecular network, and the material forms a gel that locks the liquid in.
The main components are acrylic acid, sodium hydroxide (or a similar neutralizing agent) and water plus a crosslinker that forms the bridge connecting one polymer chain to another. This solution is mixed and goes through a polymerization process to form three-dimensional polymer chain networks. And it takes the form of an aqueous gel. The granules are ground and sieved to the desired particle size. At this point, the superabsorbent material can be further crosslinked to give the material-specific absorbent properties.
Many SAP types can be made by making monomer and macromolecular structural changes. Initially, superabsorbent polymers are divided into two main classes as synthetic (petrochemical-based) and natural ones (polysaccharide and polypeptide-based).
However, most of the existing superabsorbents are produced from acrylic acid (AA) by solution or inverse suspension polymerization technique. In addition, the sub-classification criteria are:
-
According to its practical properties (absorption capacity)
-
According to the swelling (suction) speed
-
According to the strength of the swollen (saturated) gel form
-
According to monomer and ionic sensitivity
Superabsorbents have a proven history of safe use and are widely accepted by pediatricians in toxicology, general medicine, nursing, personal hygiene products.
Keeping the skin too wet allows irritation and harmful bacteria to find a living space. They help keep the skin dry, with the functionality of extracting liquid from the skin and absorbing and holding the product in essence. This situation naturally creates more comfort for the user. They help protect against skin irritation in diaper users by reducing skin hydration. In addition to this chain, they help prevent the spread of infections. Retention of liquid in the super absorbent core reduces leakage. It also reduces the risk of urine mixing with fecal matter and contamination with microorganisms, which can lead to the spread of diseases such as diarrhea and gastroenteritis. Many people suffer from a lack of bladder or bowel control as a result of illness, disability, or age. Disposable products containing superabsorbent help many of these individuals and their caregivers maintain a quality of life with greater mobility and independence.

.png)
Polycondensation
Polymerization; It is the most basic of the polymerization works and has been explained above in many details. However, the polymerization reaction is not limited to polymerization only.
Basically, polymerization reactions are gathered under three main headings.
-
Polymerization is the reaction of combining the same monomers to form a chain of monomers (polymer). (Polyacrylonitrile, polyvinylchloride, polyvinylidene chloride, polyvinylalcohol, polyolefin, polytetrafluoroethylene)
-
Polyaddition is the polymerization reactions involving the addition of another molecule with a molecule containing a double bond. (Polyurethane)
-
Polycondensation is a reaction in which monomers have at least two reactive groups, resulting in small molecular weight compounds such as water and ammonia. (Polyester, polyamide 6,6)
+
+

Polycondensation reactions are related to the covalent bonding of monomer molecules, resulting in high molecular weight polymers or a low carbon number alcohol with the release of a small molecule such as water.