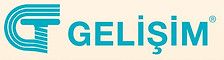


Hydrocarbons
It is an organic compound consisting of two elements, hydrogen and carbon. Most of the petroleum composition consists of hydrocarbons of varying lengths.
The smallest hydrocarbon methane consists of a single carbon atom and four hydrogen atoms. However, hydrocarbons can consist of hundreds or thousands of individual atoms linked together in many ways, including chains, circles, and other complex shapes.
In order to classify the properties of hydrocarbons, they are divided into several basic types.
Alkanes: These are called saturated hydrocarbons. That is, they only contain single bonds between all carbon atoms. Alkanes are the basis of petroleum fuels and exist in linear and branched forms.
Unsaturated Hydrocarbons: Hydrocarbons that have one or more double bonds between carbon atoms are called alkenes.
Cycloalkanes: Any hydrocarbon containing one or more ring structures.
Aromatic Hydrocarbons: Aromatic hydrocarbons , also called arenes, are a unique class of carbon molecules in which carbon atoms are bonded by successive double and single bonds. This class of molecules has special ring structures in which the bonds between carbon atoms are an intermediate bond between single and double bonds.
Molecules in this class contain the industrial solvent "benzene".
Benzene (C6H6): Like other hydrocarbons, benzene is a natural component of petroleum. It is a colorless, flammable, sweet-smelling liquid at room temperature and is a component of most gasoline blends because of its high octane number.
Benzene is also highly carcinogenic and is well known to cause bone marrow failure and bone cancer. Of course, its carcinogenicity is not well known when used as an additive in aftershave and other cosmetics due to its "pleasant aroma".
The largest use of benzene (50%) is the product of styrene and polystyrene plastics. It is also converted into a molecule known as cyclohexane, which is important in Nylon production. About 15% of benzene is used to produce cyclohexane. Smaller amounts are used in everything from pesticides to rubber.
The benzene structure can be drawn in two ways. In the first, the double bond character is drawn explicitly. In the short handed version, a circle is drawn inside the ring to show the structure. There is only one hydrogen bonded to each carbon atom in benzene.
I. and II below. drawings are identical. III in practice. drawing is used.
Benzene is a colorless, flammable liquid with a boiling point of 80.1 ° C and a melting point of 5.5 ° C.
Binuclear Aromatic Hydrocarbons: They are compounds that contain two benzene rings in their molecules.
Hydrocarbons
It is an organic compound consisting of two elements, hydrogen and carbon. Most of the petroleum composition consists of hydrocarbons of varying lengths.
The smallest hydrocarbon methane consists of a single carbon atom and four hydrogen atoms. However, hydrocarbons can consist of hundreds or thousands of individual atoms linked together in many ways, including chains, circles, and other complex shapes.
In order to classify the properties of hydrocarbons, they are divided into several basic types.
Alkanes: These are called saturated hydrocarbons. That is, they only contain single bonds between all carbon atoms. Alkanes are the basis of petroleum fuels and exist in linear and branched forms.
Unsaturated Hydrocarbons: Hydrocarbons that have one or more double bonds between carbon atoms are called alkenes.
Cycloalkanes: Any hydrocarbon containing one or more ring structures.
Aromatic Hydrocarbons: Aromatic hydrocarbons , also called arenes, are a unique class of carbon molecules in which carbon atoms are bonded by successive double and single bonds. This class of molecules has special ring structures in which the bonds between carbon atoms are an intermediate bond between single and double bonds.
Molecules in this class contain the industrial solvent "benzene".
Benzene (C6H6): Like other hydrocarbons, benzene is a natural component of petroleum. It is a colorless, flammable, sweet-smelling liquid at room temperature and is a component of most gasoline blends because of its high octane number.
Benzene is also highly carcinogenic and is well known to cause bone marrow failure and bone cancer. Of course, its carcinogenicity is not well known when used as an additive in aftershave and other cosmetics due to its "pleasant aroma".
The largest use of benzene (50%) is the product of styrene and polystyrene plastics. It is also converted into a molecule known as cyclohexane, which is important in Nylon production. About 15% of benzene is used to produce cyclohexane. Smaller amounts are used in everything from pesticides to rubber.
The benzene structure can be drawn in two ways. In the first, the double bond character is drawn explicitly. In the short handed version, a circle is drawn inside the ring to show the structure. There is only one hydrogen bonded to each carbon atom in benzene.
I. and II below. drawings are identical. III in practice. drawing is used.
Benzene is a colorless, flammable liquid with a boiling point of 80.1 ° C and a melting point of 5.5 ° C.
Binuclear Aromatic Hydrocarbons: They are compounds that contain two benzene rings in their molecules.
About
Kyäni, nutritional supplement products consisting of beneficial ingredients; It delivers to more than 50 countries around the world with unique business opportunities. We use Kyäni products daily to maintain our ideal health, share these products with others, devote a certain amount of time to work almost every day to build and maintain our business, and share our success with others by involving others in the Kyäni opportunity or contributing to the Potato Pak and Caring Hands programs.
About
Kyäni, nutritional supplement products consisting of beneficial ingredients; It delivers to more than 50 countries around the world with unique business opportunities. We use Kyäni products daily to maintain our ideal health, share these products with others, devote a certain amount of time to work almost every day to build and maintain our business, and share our success with others by involving others in the Kyäni opportunity or contributing to the Potato Pak and Caring Hands programs.
Page Under Construction.
Page Under Construction.
Training / Knowledge / Solution Platform
Fillers
The main target in filler materials included in polymers is economic.
However, besides this, filled materials; They also carry characteristic features such as specific gravity, compressive strength, bending resistance, hardness, and heat resistance. Some special additives give the system advantages such as antistatic and non-flammability, as well as softness and lubricity, which facilitates processing.
Fillers prevent the shrinkage of the material in plastics. However, tensile strength and impact resistance worsen with fillers. Special additives are absolutely necessary to correct them. The pads change the process rendering values.
The most important issues to be considered in the selection of fillers can be listed as follows. Particle size distribution pattern, dispersion feature, chemical structure, surface structure and size, catalyst effect of the surface, risk of abrasion, density, surface hardness, transportation type, health hazards, price.
The most important issue in the use of fillers is that they are mixed very well with the matrix. Thus, optimal contact of the matrix with the filler and the highest distribution on the particles are achieved. Fillers prevent the chain molecules from joining by filling the volume. With the side bonds that develop between the filler particle and the matrix, the material can have a tougher and more rigid structure.
This phenomenon explains the increase in the glass temperature of many plastic materials with filling.
Filled Plastic:
The most important difference between them and reinforced plastics is that the tensile strength increases only in reinforced plastics. On the other hand, hardness increases with fillers. Heat resistance does not increase as much with spherical fillings as with fiber reinforcement materials. On the other hand, the addition of talc and mica, which are in the form of flat particles, can be much more effective in heat resistance.
Reinforced plastics have extraordinary increases in mechanical values.
In filled plastics, there is a decrease or invariance in the effect of heat on mechanical values.
Apart from these, the following positive changes occur in filled plastics;
Density, compression and bending values increase.
Surface hardness and quality are improved.
Production cost goes down.
Processing of plastic becomes easier.
Printing and forming time is shortened.
A harder product is obtained.
It will be more resistant to heat.
The collapse problem is reduced.
The creep problem is eliminated.
Tendency to under load is reduced.
Bend and impact values are improved.
Things to pay attention:
Particle size distribution suitability, catalytic effect, the necessity of mixing very well with the matrix for a homogeneous structure, that it will corrode the machinery and equipment. If it is not worked consciously, big problems may be encountered instead of the desired advantages.
Talc and glimer, which are in the form of a plate, are preferred as much as calcite, as they give the material toughness and provide surface smoothness.
Excessive increase in oil prices, the source of oil This causes the plastic materials, which are used in plastic, to become more expensive, and the cheapness provided by fillers gains even more importance. With new research and development efforts, filling types and their compatibility with plastics are examined and solutions are sought with higher filling ratios.

Talc
It is a hydrated magnesium silicate and is a very soft mineral. Talc is a solid metamorphic mineral. Its full scientific name is hydrated magnesium silicate and its chemical formula is Mg 3 Si 4 O 10 (OH) 2. In nature, talc is usually found in a stone called steatite or soapstone (high talc rock), often combined with other minerals such as chloride and carbonate. Talc is usually blue, white, gray, brown or colorless. Talc is also known as "soft stone". This stone, as the name suggests, has a special softness that is often used in sculpture.
Medium soft (Talk has the lowest hardness compared to other minerals in nature)
Very smooth, feels like soap to the touch
It has good electrical insulation, good insulation, high melting point, low thermal expansion values
Strength with organic substances is an inert chemical (ability to combine with organic substances)
In the plastics industry, Talc is widely used by the masterbatch manufacturer to produce filler masterbatch. As a high content ingredient in plastic fillers, talc will increase the hardness of various base resins such as polypropylene, vinyl, plastic, nylon and polyester. It also acts as anti-adhesive, anti-freezing, lubricant, softener, etc. can also function as
Plastic, cosmetics, paper etc. In various industries, talc is ground into white powder and mixed with other compounds, so it is known as talcum powder.
When used in thermoset resin systems;
It provides electrical insulation and heat and moisture resistance.
The system with talc filling material can be easily processed mechanically.
It can be used as a filler in sheet and paste ready molding compositions.
It provides a good balance of rigidity and impact resistance in the product.
It has a thin layered structure consisting of layers of magnesium hydroxide.
If talc is added to polyethylene, the mechanical properties remain unchanged over a wide temperature range, and the electrical properties are significantly improved.
Tensile strength increases more than other additives.
It is the commonly used filler with PP. Due to its laminar structure, talc is one of the most important fillers that increases the deformation temperature with heat and increases the dimensional stability. In addition to reducing the cost by adding calcite, it is possible to produce materials with less wall thickness, since the flexibility of the material is greatly reduced in this way.
On the other hand, in the use of talc, the impact strength decreases at low temperature, the tensile strength decreases, the surfaces become dull, and heat decomposition is adversely affected.
Talc powder: It is mainly made from talc, a mineral composed of the elements magnesium, silicon, and oxygen. As a powder it absorbs moisture well and helps reduce friction.
When prices are rising and the economy is struggling, using fillers for plastic in plastic production is an effective solution as it helps manufacturers save large amounts of input materials and therefore lower product costs. In addition, the use of filler masterbatch in production shortens the processing time, so that the production capacity can reach optimum efficiency.
Talc filler masterbatch: Talc powder, base resin (PP, PE, HD, HIPS, etc.) and dispersant additives, binder additives, etc. It is a mixture of various additives such as
Importance of Using Talc: It is considered the perfect filler for plastic, helping the masterbatch manufacturer increase productivity while reducing production costs. Plastic masterbatch containing talc powder can be used to replace a part of primary plastic (input material for manufacturing plastic-based products). This is a smart solution aimed at saving raw materials while limiting the amount of crude oil. Resources in plastic production are getting depleted. Another major effect is that talc filler greatly improves the plastic properties, helping products with plastic outlets have a higher value in the consumer market.
Increases heat resistance for plastics
Help plastic products increase abrasion and slip resistance when in contact with the surfaces of other products
Reduces plastic shrinkage, helps to easily shape and fix product dimensions
Improve the printing properties on the material surface, limit the surface treatment with corona.
Increases durability for plastic
Anti-blocking plastic smoothes the surface without using anti-blocking additives (increases anti-blocking property)
Talc filler masterbatch is very popular among masterbatch manufacturers because it is widely used in bag blowing, injection molding, extrusion molding, compression molding, etc. It is suitable for use in most traditional manufacturing processes, such as without the need to upgrade or replace equipment or manufacturing technology. Talc fillers containing talcum powder are suitable for all kinds of packaging (shopping bags, lunch bags, garbage bags, bottles, food containers, etc.), hollow tubes, plates, electric caps, bowls, plates, etc. In order to produce it, it must go through the processing stages.
Consideration when using talc: According to reports, the incidence of lung cancer and respiratory diseases is very high among talc miners due to exposure to industrial talc dust containing silicon dioxide and asbestos, which are dangerous to our health. Another problem is that talcum powder is very popular in cosmetic powders because of its good moisture absorption properties. This will pose a threat to infants or women who inhale large amounts of talcum powder.
However, there is currently no clear evidence that using or inhaling talcum powder will increase the risk of cancer. Data on the relationship between talc powder and lung cancer cases are still scarce. However, talc filler masterbatch manufacturers should still be careful when using this material in production.
Kaolin
Kaolin or kaolin is a type of clay obtained from granite rocks. It is used to make some ceramics and porcelain. Also known as bee clay in Turkey. It is a white and soft soil type. Granite rocks contain feldspar minerals.
Its basic composition is aluminum silicate. Other metal atoms are also present in it. Normally used as a filler in thermoset resin systems, kaolin is a fine white powder. It can be used when smooth, very glossy surfaces are required due to its adhesion. Extremely fine, it can also be used as an additive to control run-off. Calcined kaolin can be used when superior electrical properties are required.
Kaolin, one of the indispensable fillers of the paint industry; It is a natural clay raw material containing Ca and Na.
It is a raw material characterized by kaolinite mineral. In industrial uses, 'calcined' kaolin is used.
Calcined Kaolin: When the kaolin is extracted from nature, it is not as pure as desired. It also contains unwanted structures and water. These impurities and some water in the kaolin are purified from the kaolin by the calcination process. Calcination process to this process, post-process kaolin; It is called calcined Kaolin. Kaolin by calcination process; gains superior optical and physical properties.
Calcination: Calcination means pre-cooking. It is the process of heating the material to a certain temperature (a process of 900°C - 1100°C) and cooling it after waiting for a certain time. The materials are calcined to remove crystal and chemical water, to change the crystal structure of the raw material, to reduce the hardness of the raw material and thus to provide easy grinding.
Material diameter, processing time, temperature and atmospheric CO2 pressure are very important in calcination. Calcination A 2.5 cm diameter grain is calcined in about 1 hour. As the layer thickness increases, it becomes more difficult for heat to enter the interior.
The purpose of calcining;
1) Removal of crystal and chemical water (calcination of clays and talc in bauxite).
2) Changing the raw material crystal structure.
3) Reducing the hardness of the raw material and thus providing easy grinding (calcination of quartz)
There are two main applications of the calcination process.
1) Calcination applied to carbonates, sulphides, hydrates (Substances such as SO2, CO, CO2 are removed from compounds such as carbonate sulfate. Soda lime glass contains 72% SiO2, 14% Na2o, 14% CaO. When these last two compounds Na2O and CaO combine, colamanite and borax are formed).
2) During the calcination (Limestone (CaCO3) applied to Crushing and Grinding Raw Materials, decomposition occurs as it gradually progresses from the surface to the inner surface of the mineral.
There are various factors affecting the disintegration reaction of limestone with the effect of heat. These factors are generally evaluated by the kinetic and physical transfer events that occur in the furnace where the reaction takes place. For example, as the grain size of the mineral increases, the fragmentation process becomes more difficult. Therefore, a longer calcining process is required. Also, the larger particle size affects the heat distribution in the furnace. Small-sized particles settle in the spaces formed by large particles, causing the combustion flame and gas flow in the furnace to be prevented. Temperatures that enable small particles to be calcined without excessive combustion ensure that only the shell part of large particles can be calcined. Consequently, calcining will be easier regardless of particle size if a controlled particle-size distribution is achieved.
The calcination of limestone is carried out in industrial applications, in different furnaces. Vertical kilns are used for coarse-grained limestones, while rotary kilns are used for fine-grained limestones. Fluidized bed type furnaces can be used for fine sized limestones with uniform grain distribution. Calcination furnaces; can be heated with all solid, liquid and gaseous fuels).
Kaolin Usage Areas:
Petroleum Industry : It is used as a catalysis in the catalytic transformation of petroleum products, especially in petroleum refineries. Many catalysis operate under high temperature and pressure. Therefore, kaolins are suitable for high temperature conditions. Talc or sepiolite in the manufacture of Catalytic Converters (Cordiorite) and kaolin mixture is used.
Plastic Industry: It is frequently used especially in vinyls and polyesters as a reinforcing and cost reducing and additive material. The most important kaolin usage area; (PVC) coated wires and cables. Calcined kaolin and silica surface modified kaolins are used to increase the electrical resistance of PVCs because they have hydrophobic properties.
Tire Industry: Cost reducing additive material and most commonly used as a booster The average grain size of hard kaolin is 0.2 µm' and soft kaolins have an average grain size of less than 1.0 µm. The pH of the desired kaolin in the rubber industry in water is between 4.5 and 5.5. Also, Fe,Mn and elements such as Cu be within very low limits.
Paint Industry: Kaolin is used together with titanium oxide (inorganic pigment), ground calcite powder and talc in water-based interior and exterior paints or in industrial paints. Costs are improved by reducing the use of titanium oxide. Water-based interior plastic and latex calcined and non-laminated mineral structure kaolins are used. in this group paints contain between 50% and 70% pigment. 98% of the kaolin used in semi-gloss and glossy water-based paints is larger than 2 µm. In latex paints, together with pigments, binding resins, kaolin is used, which provides better covering and has a refractive index value close to the binder's refractive index (>1.50).
Ink Making: Kaolin is used in high-density inks containing thin films in lithographic, offset and flexographic printing techniques. The ink film ranges from 5 to 15 µm and is used together with a fine-grained kaolin (0.2-0.5 µm) coloring pigment to maintain gloss.
In the Insulation Area: Kaolin latex sodium silicate wall It is used in paper adhesives, gypsum panels, water-based adhesives and epoxy-based adhesives to achieve better viscosity, easy application and easy spreading.
Pharmaceutical Industry: Kaolin is used in some drugs due to its adsorption properties. Calcined kaolin (90% less than 2µm) is used in toothpastes. In addition, kaolin is used in automobile and metal polishes and cleaning oxidized surfaces. Kaolin used in this sector maximum 2 ppm arsenic and maximum 20 ppm heavy metals are required.
Glass Fiber Making: It is used for heat insulation and strengthening of plastics. The main raw material of glass fiber is silica, kaolin and limestone. boric acid, soda and sodium sulfate. In aluminum windows It lowers the melting temperature, prevents it from crystallizing and reduces solubility in water and other chemicals. Glass fiber production For the desired kaolin, 37% Al2O3 44% SiO2 should be maximum 1% Fe2O3 2% Na2O and 1% H2O.
Paper Industry: While searching for 90-100% pure kaolinite mineral, it should not contain quartz mineral. In addition, the brightness is at least 85%, grain size 80% < 2µm and Brookfield viscosity < 7,000 cps.
Ceramic Industry: Generally Kaolins containing 75-80% kaolinite minerals are preferred. Firing color, viscosity, resistance to friction, very low Fe2O3 and TiO2 ratios and % A brightness of 83-91 percent is desired.
bentonite
It is a type of clay containing various metal atoms. They were formed as a result of chemical weathering of volcanic ash, tuff and lava rich in aluminum and magnesium. Due to its colloidal property and high plasticity, bentonite has the property of binding the sands used as mold material in casting.
Bentonite is mainly used as a thickening material in coating applications. Industrial minerals used for filling purposes, in addition to being inexpensive, provide important contributions to the quality and performance of the paint with their physical and physico-chemical properties. The properties that the fillers bring to the paint are as follows:
Better film formation, increased weather resistance, a base for real pigment,
Preventing rapid collapse, Reducing the passing rate of moisture. Since they are cheaper than pigments, they reduce the cost of the paint.
It ensures that the drilling mud becomes viscous, the crumbs are carried up and water leaks are prevented.
With the acid activation of Ca-Bentonites, which are used to lighten oils, surface areas and spaces in the crystal are expanded, Fe, Ti, Ca, Na and K are separated from the crystal lattice structure of clay minerals, H+ - bonds are formed in their spaces, converted into bleaching earth and vegetable oils (olive oil) It is used as a filter material in the refining of sunflower, corn, sesame, soybean, palm, canola, cottonseed oils.
Due to its very weak bond adhesion, it can easily break apart.
It is used for pelletizing bentonite iron powders with binder and plastic properties.
It is used in civil engineering to obtain water and liquid impermeability in foundation and dam structures.
It is used in the clarification of wine and fruit juices, in the production of animal feed.
It is used as a filling material in the pharmaceutical, paper and rubber industries.
In the cement industry, as an additive in the ceramic industry,
It is used in petroleum refining.
It is used for cleaning waste water.
It is used in paint industry and fire extinguishers.
It is used in fertilizer making and soil improvement.

Calcite (CaCO 3 )
Calcite (CaCO3) is a naturally occurring carbonate rock (limestone, marble, chalk).
mineral. Colorless, vitreous, crystalline in various forms. it is transparent. It is easily ground and a white powder is obtained. Its hardness is 3 on the Moh's scale and its density is in the range of 2.6-2.7.
Calcite (calcium carbonate) formations produced commercially in the world,
white colored limestones
White, pure limestones
Coarse crystal marbles
They are white chalk formations. Among them, the ones with the highest whiteness are coarse crystalline marbles. However, the energy used in grinding is higher than the others.
Çanakkale Karabiga Region is one of the largest crystalline calcite formations in Turkey. Calcite deposits formed in the granite contact are of high whiteness and are easy to grind, but its whiteness is lower than the formations found in the Aegean Region and Niğde. There are marble deposits in Bayramiç, Biga and Ezine. Balikesir Erdek and There are very rich large crystalline marble beds and quarries in Manyas.
Yıldız Mountains in Thrace, marble and Dolomitic marble deposits in Bursa Orhaneli
are available. Bursa Orhangazi, Keles, İnegöl have rich marble deposits, but production is done on a very small scale. There are marble deposits in İzmir Tire, Gölmarmara, Akhisar and Torbalı. The degree of whiteness is lower than previously stated. Muğla Yatağan and Kavaklıdere Regions have very rich marble beds with a smaller crystal structure but a more pure chemical structure, easy to grind, and a very high whiteness. Niğde Region has very rich reserves and the calcite deposits here are the whitest formations in Turkey. There are calcite quarries in this region that increase production very rapidly. Today, many producers obtain raw materials from these quarries in the Niğde Region. For this reason, investments in Niğde have increased significantly in recent years. The above-mentioned regions
They are regions with very rich reserves that can be expressed in 10 million tons. Apart from these, it is possible to encounter calcite formations in almost every region of Anatolia, for which production and reserve determination have not yet been made. The sum of known reserves can be expressed in hundreds of millions of tons. The most striking points are the reserves in Turkey; CaCO3 high percentage,
impurities such as silica, iron and magnesium are very low, and the degree of whiteness after grinding is very high.
The high degree of whiteness in the ore is always preferred because it saves titanium dioxide in paint and plastic, and optical brightener in paper. Calcites ground in micronized sizes in dry or wet system; It is used in Paper, Paint, Plastic and cable, Construction, Adhesives, Food, Ceramics, Carpet base, linoleum, Pharmaceutical industry.
Calcite in Paint Industry: The paint industry uses dry ground calcite in 1,3,5,20,40 micron sizes. The most demanded product group is 5 micron calcite. Calcite is added to the paint at a rate of 25-35% in water-based construction paints used in interior and exterior coatings. Calcite, which is used as an extender in paint, provides surface coating and reduces titanium dioxide consumption. Due to the increase in the price of chemicals in the paint sector, the market The demand for economical dyes has increased. Thus, calcite consumption in the paint industry has increased by 50% in the last five years.
Calcite in the Plastics Industry: Calcite, plastic furniture, pipe, automotive etc. It is used in the production of many plastic products, both in natural form as ground and in coated form. Coating is mostly done with stearic acid and sometimes with calcium stearate. Polypropylene (PP), Polyamide (PA), Thermoplastic (TPES) and PVC resins are mainly plastics in which calcite is used as a filler. The use of similar fillers, especially calcite, in the plastics industry has increased every year. color, Calcite is used as a filler in the plastics industry for many reasons such as its purity and cheapness.
It is possible to use calcite in formulas at the rate of 5% to 50% in order to increase the mechanical performance and increase the efficiency, as well as reducing the cost. PE also has some side effects such as change in MFI and density . Composites .
In the plastics industry, rather than using it directly in calcite product compounds, it is preferred to use it by obtaining composite material with PE. LDPE, HDPE, PP etc. as carrier but material matrix. may also be preferred.
Incorporating the powdered calcite product directly from the feed into other components during the application in the final product processes will lead to inhomogeneous results on the final product. Since it will not mix well in the feeding chamber, a melt with an unbalanced density will form in the extrusion line. This will completely destroy the standard on the product.
For this reason, in the use of calcite, it would be appropriate to prepare a composite beforehand in proportions corresponding to the ratios to be included on the final product.
In this composite material to be prepared, additional additives such as a lubricant that will facilitate fluidity (which will eliminate the abrasions on the machine to some extent) and a binder that will heal on the broken polymeric chain are also used.
These are mostly; PE Wax, Calcium Stearate, Zinc Stearate appear as a special additive (agent).
Calcite in Nonwoven Non-Woven Fabric Production: Calcium carbonate filler has been started to be used in order to optimize its production. Made from calcium carbonate powder (CaCO3), plastic resins and other special additives, calcium carbonate filler is one of the most effective material solutions for nonwoven manufacturing. The application of this material offers several benefits to end products:
These are areas where products made from calcium carbonate non-woven fabric range from medical and personal care to hygiene, geotextiles (fabrics used in technical industries such as suction, separation, filtration, protection, reinforcement and discharge).
Advantages of adding calcite filler to non-woven materials:
Provides improvement of product surfaces
It leads to better covering ability of the fabric structure by reducing the gloss, making the surface more matte and more opaque.
Gives natural white color with limited yellowness
Improves material texture
Creates a comfortable and cottony feel
Prevents carbon footprint when touched
Creates more micro-areas for air filtration and oil absorption
Adds increased thermal conductivity and physical strength
Allows lowering of process temperature
It paves the way for higher productivity of production, that is, it increases capacity.
It saves energy and production costs.
It cooperates easily with multiple base resins (thanks to its good dispersibility) and can be processed by various methods
Recommended usage rates of calcite in the production of non-woven fabrics:
5-20% in thin fabrics,
20-35% in medium fabrics,
it reaches 60% in thick fabrics.
When extremely good dispersion and stability is required,
The filler masterbatch is typically applied with a loading rate of 78-80% and a melt flow index of 20-40g/10min.
The MF index value for nonwoven fabrics varies between different fabric thickness levels. Thinner fabric requires a higher MFI, while a lower MFI is recommended for thicker fabrics.
It is healthy to make any changes in the dosage rate of calcium carbonate filler in non-woven fabric products gradually.
Calcite CaCO3 is divided into two groups,
Ground calcium carbonate: (GCC) (particle sizes 10-1 micron,
cheaper because it is simpler to manufacture)
Precipitated calcium carbonate: (PCC) (Precipitated Calcium Carbonate).
(particle sizes are on the nanometer scale, it is expensive to manufacture because it is chemical)
Precipitated calcium carbonate also means purified, refined or synthetic calcium carbonate. PCC also has the same chemical formula as limestone, marble and chalk (CaCO3). Three different forms of calcium carbonate minerals are formed by the arrangement of calcium, carbon and oxygen atoms among themselves in three different directions.
The most common precipitated calcium carbonate is the hexagonal form known as calcite. Some calcite minerals can be scalonahedral, rhombohedral and pyrismatic.
Since PCC is produced by chemical methods, particle shape, particle size and particle size distribution are kept under control and for these reasons, it has advantages over ground calcium carbonate (GCC).
This structure, which is gained as a result of the chemical precipitation process of natural calcium carbonate,
it gives the material positive properties such as impact resistance, gloss, opacity; PCC can also be used as a thixotropic agent that improves flow properties.
In PCC plastic processing, especially hard plastic, PVC profile, plastic pipe and soft
plastic is used as a functional filler in the production of PVC cables.
When used in the production of PCC rigid plastics: increases the impact strength of the profile (even at low temperatures). Increases whiteness and brightness. Profile improves surface smoothness. It balances the extrusion torque values in production. It reduces the plasticization time by lowering the pulping temperature. It extends the machine life by reducing the friction that occurs during extrusion.
When PCC is used in the production of soft plastics: It gives toughness and flexibility to the cable. PVC cables must have low HCl emission inside, it reduces the high HCI in PVC paste with its high absorption and surface area properties. It does not adversely affect the electrical, insulating properties of the cable compound. When used in rubber and tire production, Increases flexibility and breaking strength, provides surface smoothness.
Also; It is also used in Polypropylene (PP), Polyethylene (PE) and Polyester products.



Calcite Quality Determination Terms
Abrasion Value: 100 gr dry CaCO3 dispersed in 3.2 lt pure water is the weight loss in mg after 6000 cycles in the abrasive device, which is an important value in the paper industry.
Dispersion Rate: It is the non-agglomeration and dispersion of CaCO3 particles in the environment where they are used. It is important in the filling industry.
Activation: (Coating) It is the coating of grains with various aliphatics in order to reduce and decrease the space between CaCO3 grains.
Whiteness Degree: It is a value obtained as a result of comparison with the standard MgO whiteness and it is the% of the light reflectivity of the material. This value should be 96-100% for calcite, 96% for marble and 93-96% for chalk. It is a sought-after feature in industries where paper and whiteness are important.
Specific Surface: The total surface of 1 gr CaCO3 is the value in cm2. It is sought after in the coating and plastic industry.
Antisplit
Calcite; It was started to be used to prevent the thinning of duct tapes and to reduce costs. Later, with the competitive load brought by the market conditions, it continues to be used in many polymer product groups as antisplit masterbatch.
Antisplit masterbatches are pre-treated compounds of calcite as filler additives. In other words, Calcite can be directly included in the product compound formula, or it can be called antisplit in advance to facilitate the process. In this way, the granule form is from powder to granule. This results in a cleaner process flow.
The reason why these high-filled compounds are called masterbatch is that, as in color masterbatch applications, they are granulated by loading high calcite (70 - 80%) on the main carrier polymer. It is to ensure that the granulated filled compound is added to the final product to be loaded with calcite, just like the masterbatch, to ensure a good dispersion of calcite in the final product.
Due to the fact that the filling materials are powder, manufacturers who process the final product in granular form (injection, extrusion film and profile) try to mix it directly into the processing hopper, which will create some problems.
These problems are;
-
Insufficient dispersion of the fillings due to the fact that the fillings placed in the funnel with the granular material flow into the machine before the granule
-
Poorly dispersed fillers accumulate in certain areas and reduce the mechanical properties of the final product.
-
Color differences in the product of fillings that are not fully dispersed
-
As a result of direct exposure to fillings in machines designed for product production, mechanical abrasions and very large damages occur in the machine.
-
Increase in electricity consumption as a result of high pressures during processing in machines directly encountering calcite
-
Production and labor costs of powder product use
Apart from these problems, many more problems can be counted. In addition, determining the incorporation rate of the powder product in the final product is difficult with the powder product. Even when trying to load with dosing, the dosing device costs of powder systems are much higher than granule dosers. The advantages of using antisplit masterbatch are;
-
Provides cost advantage
-
Much better distribution of fillers in the final product
-
Provides heat resistance while the material is being processed
-
It gives the material hardness, firmness and toughness.
-
Reduces mold shrinkage
-
Helps to reduce the use of titanium in white products
Thanks to this and many other advantages, the production and use of antisplit masterbatch has increased in recent years. It is generally used in polyolefin group products.

Antisplit Production
Various additives are used in the production of antisplit masterbatch. These are PE wax, Zinc stearate, calcium stearate or process agents that can be sufficient alone instead of these 3 additives. PE wax acts as an external lubricant and dilution agent, calcium stearate acts as an internal lubricant and fluidity enhancer, and zinc stearate acts as an external lubricant. In addition, the process agents, designed as a single package system, are effective additives on their own by adding both internal and external lubricants, fluidity and binding properties. Process aids alone are sufficient up to 70 – 80% calcite loadings and can be used as half of the total of other additives.
The process processing machine is also an important factor in the production of antisplit masterbatch. Here, the machine's ability to compact and mix the product is important. In these processes, single and double screw extrusion machines are generally used. Since the compression and mixing ratio of the product of single screw extruders is low, a banburi system is needed to pre-mix the product.
The most important factor to be considered in the selection of additives should not be only the price. The cost advantage of a product should not be determined by the purchase price, the advantages of the additive to the process, the usage rates, the advantages it brings to the energy costs, the protection of the machine and the fact that it does not force the whole of the factors reveal the cost of an additive. Purchases made by considering only the initial purchase cost may cost you more with the many costs it will create in the background. Paying attention to this issue in the selection of all additives will contribute to both your product and your costs.
Possible antisplit formula:
.png)
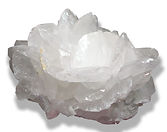
Calcite (CaCO3)
Crystal Structure
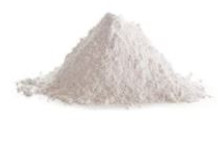
Calcite (CaCO3)
Ground / Powder Structure
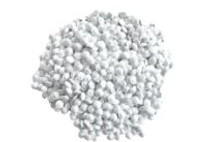
Antisplit
Granular Structure