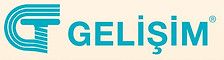


Hidrokarbonlar
Hidrojen ve karbon olmak üzere iki elementten oluşan organik bir bileşiktir. Petrol bileşiminin büyük bir kısmı değişen uzunluklardaki hidrokarbonlardan oluşur.
En küçük hidrokarbon metan, tek bir karbon atomu ve dört hidrojen atomundan oluşur. Bununla birlikte, hidrokarbonlar, zincirler, daireler ve diğer karmaşık şekiller dahil olmak üzere birçok yönden birbirine bağlanmış yüzlerce veya binlerce bireysel atomdan oluşabilir.
Hidrokarbonların özelliklerini sınıflandırmak için birkaç temel türe ayrılırlar.
Alkanlar: Bunlar doymuş hidrokarbonlar olarak adlandırılır. Yani sadece tüm karbon atomları arasında tek bağlar içerirler. Alkanlar, petrol yakıtlarının temelidir ve doğrusal ve dallı formlarda bulunurlar.
Doymamış Hidrokarbonlar: Karbon atomları arasında bir veya daha fazla çift bağa sahip olan hidrokarbonlara alken denir.
Sikloalkanlar: Bir veya daha fazla halka yapısı içeren herhangi bir hidrokarbon.
Aromatik Hidrokarbonlar: Areneler olarak da adlandırılan aromatik hidrokarbonlar, karbon atomlarının birbirini izleyen çift ve tek bağlarla bağlandığı benzersiz bir karbon molekülleri sınıfıdır. Bu molekül sınıfı, karbon atomları arasındaki bağların tek ve çift bağlar arasında bir ara bağ olduğu özel halka yapılarına sahiptir.
Bu sınıftaki moleküller, endüstriyel çözücü «benzen» içerir.
Benzen (C6H6): Diğer hidrokarbonlar gibi benzen de petrolün doğal bir bileşenidir. Oda sıcaklığında renksiz, yanıcı, tatlı kokulu bir sıvıdır ve yüksek oktan sayısına sahip olduğu için çoğu benzin karışımının bir bileşenidir.
Benzen de oldukça kanserojendir ve kemik iliği yetmezliği ve kemik kanserine neden olduğu iyi bilinmektedir. Elbette, “hoş aroması” nedeniyle tıraş sonrası ve diğer kozmetiklerde bir katkı maddesi olarak kullanıldığında kanserojenliği iyi bilinmemektedir.
En büyük benzen kullanımı (% 50), stiren ve polistren plastiklerinin ürünüdür. Ayrıca Naylon üretiminde önemli olan sikloheksan olarak bilinen bir moleküle dönüştürülür. Siklohekzan üretmek için benzenin yaklaşık% 15'i kullanılır. Böcek ilaçlarından kauçuğa kadar her şeyde daha küçük miktarlar kullanılır.
Benzen yapısı iki şekilde çizilebilir. İlkinde, çift bağ karakteri açıkça çizilir. Kısa elli versiyonda, yapıyı göstermek için halkanın içine bir daire çizilir. Benzen içindeki her bir karbon atomuna bağlı tek bir hidrojen vardır.
Aşağıdaki I. ve II. çizimleri eştir. Pratikte III. çizim kullanılır.
Benzen, renksiz, alevlenebilen, kaynama noktası 80,1 °C, erime noktası 5,5 °C olan bir sıvıdır.
Binükleer Aromatik Hidrokarbonlar: Molekülünde iki benzen halkası içeren bileşiklerdir.
Hidrokarbonlar
Hidrojen ve karbon olmak üzere iki elementten oluşan organik bir bileşiktir. Petrol bileşiminin büyük bir kısmı değişen uzunluklardaki hidrokarbonlardan oluşur.
En küçük hidrokarbon metan, tek bir karbon atomu ve dört hidrojen atomundan oluşur. Bununla birlikte, hidrokarbonlar, zincirler, daireler ve diğer karmaşık şekiller dahil olmak üzere birçok yönden birbirine bağlanmış yüzlerce veya binlerce bireysel atomdan oluşabilir.
Hidrokarbonların özelliklerini sınıflandırmak için birkaç temel türe ayrılırlar.
Alkanlar: Bunlar doymuş hidrokarbonlar olarak adlandırılır. Yani sadece tüm karbon atomları arasında tek bağlar içerirler. Alkanlar, petrol yakıtlarının temelidir ve doğrusal ve dallı formlarda bulunurlar.
Doymamış Hidrokarbonlar: Karbon atomları arasında bir veya daha fazla çift bağa sahip olan hidrokarbonlara alken denir.
Sikloalkanlar: Bir veya daha fazla halka yapısı içeren herhangi bir hidrokarbon.
Aromatik Hidrokarbonlar: Areneler olarak da adlandırılan aromatik hidrokarbonlar, karbon atomlarının birbirini izleyen çift ve tek bağlarla bağlandığı benzersiz bir karbon molekülleri sınıfıdır. Bu molekül sınıfı, karbon atomları arasındaki bağların tek ve çift bağlar arasında bir ara bağ olduğu özel halka yapılarına sahiptir.
Bu sınıftaki moleküller, endüstriyel çözücü «benzen» içerir.
Benzen (C6H6): Diğer hidrokarbonlar gibi benzen de petrolün doğal bir bileşenidir. Oda sıcaklığında renksiz, yanıcı, tatlı kokulu bir sıvıdır ve yüksek oktan sayısına sahip olduğu için çoğu benzin karışımının bir bileşenidir.
Benzen de oldukça kanserojendir ve kemik iliği yetmezliği ve kemik kanserine neden olduğu iyi bilinmektedir. Elbette, “hoş aroması” nedeniyle tıraş sonrası ve diğer kozmetiklerde bir katkı maddesi olarak kullanıldığında kanserojenliği iyi bilinmemektedir.
En büyük benzen kullanımı (% 50), stiren ve polistren plastiklerinin ürünüdür. Ayrıca Naylon üretiminde önemli olan sikloheksan olarak bilinen bir moleküle dönüştürülür. Siklohekzan üretmek için benzenin yaklaşık% 15'i kullanılır. Böcek ilaçlarından kauçuğa kadar her şeyde daha küçük miktarlar kullanılır.
Benzen yapısı iki şekilde çizilebilir. İlkinde, çift bağ karakteri açıkça çizilir. Kısa elli versiyonda, yapıyı göstermek için halkanın içine bir daire çizilir. Benzen içindeki her bir karbon atomuna bağlı tek bir hidrojen vardır.
Aşağıdaki I. ve II. çizimleri eştir. Pratikte III. çizim kullanılır.
Benzen, renksiz, alevlenebilen, kaynama noktası 80,1 °C, erime noktası 5,5 °C olan bir sıvıdır.
Binükleer Aromatik Hidrokarbonlar: Molekülünde iki benzen halkası içeren bileşiklerdir.
Hakkında
Kyäni, faydalı bileşenlerden oluşan besin takviyesi ürünlerini; benzersiz iş fırsatıyla birlikte dünya çapında 50'den fazla ülkeye ulaştırmaktadır. İdeal sağlığımızı korumak için günlük olarak Kyäni ürünlerini kullanırız, bu ürünleri başkalarıyla paylaşırız, işimizi inşa etmek ve sürdürmek için neredeyse her gün belirli bir saatimizi işe adarız ve başkalarını da Kyäni fırsatına dahil ederek veya Potato Pak ve Caring Hands programlarına katkı sağlayarak başarımızı başkalarıyla paylaşırız.
Hakkında
Kyäni, faydalı bileşenlerden oluşan besin takviyesi ürünlerini; benzersiz iş fırsatıyla birlikte dünya çapında 50'den fazla ülkeye ulaştırmaktadır. İdeal sağlığımızı korumak için günlük olarak Kyäni ürünlerini kullanırız, bu ürünleri başkalarıyla paylaşırız, işimizi inşa etmek ve sürdürmek için neredeyse her gün belirli bir saatimizi işe adarız ve başkalarını da Kyäni fırsatına dahil ederek veya Potato Pak ve Caring Hands programlarına katkı sağlayarak başarımızı başkalarıyla paylaşırız.
Sayfa Yapım Aşamasındadır.
Sayfa Yapım Aşamasındadır.
Eğitim / Bilgi / Çözüm Platformu
Dolgu Maddeleri
Polimerlere dahil edilen dolgu malzemelerinde ana hedef ekonomiktir.
Ancak, bunun yanında dolgulu malzemeler; özgül ağırlık, baskıya dayanıklılık, eğme direnci, sertlik, ısı dayanıklılığı gibi karakteristik özellikleri de üzerinde taşırlar. Özel bazı katkılar sisteme antistatik ve yanmazlık gibi özelliklerin yanında işlemede kolaylık sağlayan yumuşaklık ve kayganlık gibi artılar da verirler.
Dolgu maddeleri, plastiklerde malzemenin küçülmesini yani çekmesini önler. Bununla beraber, çekme dayanımı ve darbe direnci dolgularla kötüleşir. Bunları düzeltmek için mutlaka özel katkılar gereklidir. Dolgular, proses işleme değerlerini değiştirir.
Dolgu maddeleri seçiminde dikkat edilecek en önemli konular şöyle sıralanabilir. Tanecik büyüklüğü dağılım şekli, dispersiyon özelliği, kimyasal yapısı, yüzey yapısı ve büyüklüğü, yüzeyin katalist etkisi, aşındırma riski, yoğunluğu, yüzey sertliği, transport şekli, sağlık açısından sakıncası, fiyatı.
Dolgu maddeleri kullanımında en önemli husus matrisle çok iyi karıştırılmasıdır. Böylece matrisin dolguyla optimal teması ve tanecikler üzerinde en yüksek oranda dağılımı sağlanmış olur. Dolgu maddeleri, hacim doldurarak zincir moleküllerinin birleşmelerine mani olurlar. Dolgu taneciği ve matris arasında gelişen yan bağlar ile malzeme daha tok ve rijid bir yapıya sahip olabilir.
Bir çok plastik malzemede camlaşma ısısının dolguyla yükselmesini bu olgu açıklar.
Dolgulu Plastik:
Takviyeli plastiklerle aralarındaki en önemli fark çekme direncinin sadece takviyeli plastiklerde artmasıdır. Buna karşılık sertlik dolgu maddeleri ile de artar. Isıya dayanıklılık kürecik şeklindeki dolgularla elyaf şeklindeki takviye malzemeleriyle olduğu kadar fazla artmaz. Buna karşılık yassı tanecik yapısında olan talk ve mika ilavesi ısı dayanımında çok daha etkili olabilir.
Takviyeli plastiklerde mekanik değerlerde olağanüstü artışlar olur.
Dolgulu plastiklerde ise, mekanik değerlerin ısıdan etkilenmesinde azalma yada değişmezlik vardır.
Bunlardan başka dolgulu plastiklerde şu olumlu değişimler gerçekleşir;
-
Yoğunluk, baskı ve eğme değerleri artar.
-
Yüzey sertliği ve kalitesi iyileşir.
-
Üretim maliyet düşer.
-
Plastiğin işlenmesi kolaylaşır.
-
Baskı ve şekillendirme zamanı kısalır.
-
Daha sert bir ürün elde edilir.
-
Isıya daha dayanıklı olur.
-
Çöküntü problemi azalır.
-
Sürünme problemi ortadan kalkar.
-
Yük altında bırakma eğilimi azalır.
-
Eğme ve darbe değerleri iyileşir.
Dikkat edilmesi gerekenler:
Tanecik büyüklüğünün dağılımı uygunluğu, katalitik etkisi yapabileceği, homojen yapı için matrisle çok iyi karışım yapılması gerekliliği, makine ve ekipmanlarını aşındıracağı. Eğer bilinçli çalışılmazsa istenilen avantajların yerine büyük problemlerle karşılaşılabilir.
Plaka yapısında olan talk ve glimer de, malzemeye tokluk vermesi ve yüzey düzgünlüğü sağlaması nedeniyle, kalsit kadar tercihlerin başında görülmektedir.
Petrol fiyatlarındaki aşırı artış, kaynağı petrol olan plastik maddelerin de pahalanmasına neden olmakta ve dolgu maddeleriyle sağlanan ucuzluk daha da önem kazanmaktadır. Yeni araştırma geliştirme çabalarıyla dolgu cinsleri, plastiklerle bağdaşmaları incelenerek daha yüksek dolgu oranlarıyla çözüm aranmaktadır.

Talk
Sulu magnezyum silikattır ve çok yumuşak bir mineraldir. Talk, katı halde metamorfik bir mineraldir. Tam bilimsel adı hidratlı magnezyum silikat olup, kimyasal formülü Mg 3 Si 4 O 10 (OH) 2'dir . Doğada talk genellikle steatit veya sabuntaşı (yüksek talklı kaya) adı verilen bir taşta bulunur, genellikle klorür ve karbonat gibi diğer minerallerle birleştirilir. Talk genellikle mavi, beyaz, gri, kahverengi veya renksizdir. Ayrıca talk, “yumuşak taş” olarak da bilinir. Bu taş, adından da anlaşılacağı gibi, heykelcilikte sıklıkla kullanılan özel bir yumuşaklığa sahiptir.
-
Orta yumuşaklıktadır (Talk, doğadaki diğer minerallere göre en düşük sertliğe sahiptir)
-
Çok pürüzsüz, dokunulduğunda sabun gibi hissettirir
-
İyi elektrik yalıtımı, iyi yalıtım, yüksek erime noktası, düşük termal genleşme değerleri vardır
-
Organik maddelerle kuvvet inert bir kimyasaldır (organik maddelerle birleşebilme özelliği)
Plastik endüstrisinde, Talk, masterbatch üreticisi tarafından dolgu masterbatch üretmek için yaygın olarak kullanılmaktadır . Plastik dolgu maddelerinde yüksek içerikli bir bileşen olarak talk, polipropilen, vinil, plastik, naylon ve polyester gibi çeşitli baz reçinelerin sertliğini artıracaktır. Ayrıca yapışma önleyici, donma önleyici, yağlayıcı, yumuşatıcı vb. olarak da işlev görebilir.
Plastik, kozmetik, kağıt vb. çeşitli endüstrilerde talk, beyaz toz halinde öğütülür ve diğer bileşiklerle karıştırılır, bu nedenle talk pudrası olarak bilinir.
Termoset reçine sistemlerinde kullanıldığı zaman;
-
Elektriksel yalıtkanlığı ve ısı rutubet dayanımı sağlar.
-
Talk dolgu malzemeli sistem mekanik olarak, kolay işlenebilir.
-
Levha ve hamur hazır kalıplama bileşimlerinde dolgu maddesi olarak kullanılabilir.
-
Üründe iyi bir rijidite darbe dayanım dengesini sağlar.
-
Magnezyum hidroksit tabakalarından oluşan ince katmanlı bir yapıya sahiptir.
-
Polietilene talk katılması halinde mekanik özellikler oldukça geniş bir sıcaklık aralığında değişmeden kalır elektrik özelliklerinde ise önemli iyileşmeler olur.
-
Kopma mukavemeti, diğer katkılara kıyasla daha fazla artar.
PP ile yaygın kullanılan dolgu maddesidir. Laminer yapısı nedeni ile talk ısı ile deformasyon sıcaklığını yükselten boyutsal kararlılığı arttıran en önemli dolgu maddelerinden birisidir. Kalsit katılarak maliyetinin düşürülmesi yanında bu yolla malzemenin esnekliği de çok azaldığından, et kalınlığı daha az malzemelerin üretimi mümkün olabilmektedir.
Buna karşılık talk kullanımında, düşük sıcaklıkta darbe dayanımı düşer, kopma dayanım azalır, yüzeyler matlaşır, ısıyla bozunma ise kötü yönde etkilenir.
Talk tozu : Esas olarak magnezyum, silikon ve oksijen elementlerinden oluşan bir mineral olan talktan yapılır. Bir toz olarak nemi iyi emer ve sürtünmeyi azaltmaya yardımcı olur.
Fiyatların artması ve ekonominin zorlaşması durumunda, plastik üretiminde plastik için dolgu maddelerinin kullanılması, üreticilerin büyük miktarda girdi malzemesinden tasarruf etmesine ve dolayısıyla ürün maliyetlerini düşürmesine yardımcı olduğu için etkili bir çözümdür. Ek olarak,üretimde dolgu masterbatch'in kullanımı , işlem süresini kısaltır, böylece üretim kapasitesi optimum verimliliğe ulaşabilir.
Talk dolgu masterbatch : Talk tozu, baz reçine (PP, PE, HD, HIPS, vb.) ve dispersan katkı maddeleri, bağlayıcı katkı maddeleri vb. gibi çeşitli katkı maddelerinden oluşan bir karışımdır.
Talk Kullanımının Önemi : Masterbatch üreticisinin üretim maliyetlerini düşürürken üretkenliği artırmasına yardımcı olan plastik için mükemmel dolgu maddesi olarak kabul edilir . Talk tozu içeren plastik masterbatch, birincil plastiğin (plastik esaslı ürün imalatı için girdi malzemesi) bir parçasının yerini almak için kullanılabilir. Bu, ham petrol miktarını sınırlarken hammadde tasarrufu sağlamayı amaçlayan akıllı bir çözümdür. Plastik üretiminde kaynaklar giderek tükenmektedir. Bir başka büyük etki de talk dolgu maddesinin plastik özelliklerini büyük ölçüde geliştirerek, plastik çıkışlı ürünlerin tüketici pazarında daha yüksek değere sahip olmasına yardımcı olmasıdır.
-
Plastikler için ısı direncini artırır
-
Plastik ürünlerin, diğer ürünlerin yüzeyleriyle temas ettiğinde aşınma ve kayma direncini artırmasına yardımcı olun
-
Plastik büzülmeyi azaltır, ürünün boyutlarının kolayca şekillendirilmesine ve sabitlenmesine yardımcı olur
-
Malzeme yüzeyindeki baskı özelliklerini iyileştir, korona ile yüzey işlemini sınırlar.
-
Plastik için dayanıklılığı artırır
-
Blokaj önleyici plastik, blokaj önleyici katkı maddeleri kullanmadan yüzeyi düzeltir (anti blokaj özelliğini artırır)
Talk dolgu masterbatch masterbatch üreticileri arasında çok popülerdir çünkü torba üfleme, enjeksiyon kalıplama, ekstrüzyon kalıplama, sıkıştırma kalıplama vb. gibi çoğu geleneksel üretim prosesi için ekipmanı veya üretim teknolojisini yükseltmeye veya değiştirmeye gerek kalmadan kullanıma uygundur. Talk pudrası içeren talk dolgu maddeleri her türlü ambalajı (alışveriş poşetleri, yemek poşetleri, çöp poşetleri, şişeler, yemek kapları vb.), içi boş tüpler, tabaklar, elektrikli kapaklar, kaseler, tabaklar vb. üretebilmek için işleme aşamalarından geçmelidir.
Talk kullanımında dikkat edilecek husus : Raporlara göre, sağlığımız için tehlikeli olan silikon dioksit ve asbest içeren endüstriyel talk tozuna maruz kalma nedeniyle talk madencileri arasında akciğer kanseri ve solunumla ilgili hastalıkların insidansı çok yüksektir. Diğer bir problem ise talk pudrasının iyi nem emme özelliğinden dolayı kozmetik tozlarda oldukça popüler olmasıdır. Bu, çok miktarda talk pudrası soluyan bebekler veya kadınlar için bir tehdit oluşturacaktır.
Bununla birlikte, şu anda talk pudrası kullanmanın veya solumanın kanser riskini artıracağına dair açık bir kanıt yoktur. Talk tozu ve akciğer kanseri vakaları arasındaki ilişkiye ilişkin veriler hala çok azdır. Ancak talk dolgu masterbatch üreticileri bu maddeyi üretimde kullanırken yine de dikkatli olmalıdır.
Kaolin
Kaolin ya da kaolen, granit kayaçlardan elde edilen bir kil türüdür. Bazı seramiklerin ve porselenlerin yapımında kullanılır. Türkiye'de arı kil olarak da bilinir. Beyaz ve yumuşak bir toprak türüdür. Granit kayaçlar feldspat minerallerini içerir.
Temel bileşimi alüminyum silikattır. İçinde başka metal atomları da mevcuttur. Normal olarak termoset reçine sistemlerinde dolgu maddesi olarak kullanılan kaolen, ince beyaz tozdur. Yapışı nedeniyle düzgün, çok parlak yüzeyler gerektiğinde kullanılabilir. Son derece ince olarak, akmayı kontrol etmek için de katkı maddesi olarak kullanılabilir. Üstün elektriksel özellikler gerektiğinde kalsine edilmiş kaolen kullanılabilir.
Boya sektörünün vazgeçilmez dolgu maddelerinden biri olan Kaolin; içinde Ca ve Na bulunan doğal bir kil hammaddesidir.
Kaolinit minerali ile karakterize olmuş bir hammaddedir. Endüstriyel kullanımlarda ise ‘kalsine’ edilmiş kaolin kullanılır.
Kalsine Edilmiş Kaolin : Kaolinin doğadan çıkarıldığında, arzu edildiği gibi saflıkta değildir. İçerisinde istenmeyen yapılar ve su da bulunmaktadır. Bu safsızlıklar ve kaolinin içerisinde bulunan bir miktar su, kalsinasyon işlemi ile kaolinden arındırılır. Bu prosese Kalsinasyon işlemi, proses sonrası kaoline de; Kalsine Kaolin denir. Kalsinasyon işlemi ile kaolin; daha üstün optik ve fiziksel özellikler kazanır.
Kalsinasyon: Kalsinasyonun anlamı ön pişirmedir. Malzemenin belirli bir sıcaklığa (900°C - 1100°C lik bir proses) kadra ısıtılması, belirli bir zaman bekletildikten sonra soğutulması işlemidir. Kristal ve kimyasal suyun uzaklaştırılması, Hammadde kristal yapısının değiştirilmesi, Hammadde sertliğinin düşürülmesi ve dolayısı ile kolay öğütmenin sağlanması için malzemelere kalsinasyon uygulanır.
Kalsinasyonda malzeme çapı, işlem süresi, sıcaklık ve atmosferdeki CO2 basıncı oldukça önemlidir. Kalsinasyon 2.5 cm çaplı bir tane yaklaşık 1 saatte kalsine olmaktadır. Tabaka kalınlığı arttıkça içeriye ısı girmesi zorlaşmaktadır.
Kalsine etmekten amaç;
1) Kristal ve kimyasal suyun uzaklaştırılması (Boksitte, killerin ve talkların kalsinasyonu).
2) Hammadde kristal yapısının değiştirilmesi.
3) Hammadde sertliğinin düşürülmesi ve dolayısı ile kolay öğütmenin sağlanması (Kuvarsın kalsinasyonu)
Kalsinasyon prosesinin 2 ana uygulanması vardır.
1) Karbonatlara, Sülfürlere, hidratlara uygulana kalsinasyon (Karbonat sülfat gibi bileşiklerden SO2, CO, CO2 gibi maddeler uzaklaştırılır. Soda kireç camı %72 SiO2, %14 Na2o, %14 CaO içerir. Bu son iki bileşik Na2O ve CaO birleşince kolamanit ve borax meydana gelir).
2) Kırma Öğütme Amaçlı Hammadelere uygulanan kalsinasyon (Kireç taşı (CaCO3)’nın parçalanması sırasında, ayrışma; yüzeyden kademeli olarak mineralin iç yüzeyine ilerlemesiyle meydana gelmektedir.
Kireç taşının ısı tesiri ile parçalanma reaksiyonuna etki eden çeşitli faktörler bulunmaktadır. Bu faktörler genellikle reaksiyonun gerçekleştiği fırın içerisinde meydana gelen kinetik ve fiziksel transfer olayları ile değerlendirilmektedir. Örneğin, mineralin tane boyutu arttıkça parçalanma işlemi zorlaşır. Dolayısıyla daha uzun kalsine işlemi gerekir. Ayrıca, daha büyük parçacık boyutu, fırın içerisindeki ısı dağılımına etki etmektedir. Küçük boyutlu parçacıklar ise büyük parçacıkların oluşturduğu boşluklara yerleşerek fırın içerisindeki yanma alevinin ve gaz akışının engellenmesine neden olmaktadır. Aşırı yanma gerçekleşmeden küçük boyutlardaki parçacıkların kalsine edilebilmesini sağlayan sıcaklıklar, büyük parçacıkların sadece kabuk kısmının kalsine edilebilmesini sağlamaktadır. Sonuç olarak, eğer kontrollü bir tane-boyut dağılımı sağlanırsa, parçacık boyutuna bakılmaksızın kalsine işlemi daha kolay olacaktır.
Kireç taşının kalsinasyonu endüstriyel uygulamalarda, değişik fırınlarda yapılmaktadır. İri parçalı kireç taşları için düşey fırınlar kullanılırken, ince taneli kireç taşları için döner fırınlar kullanılmaktadır. Düzgün tane dağılımı gösteren ince boyutlu kireç taşları için ise akışkan yatak tipi fırınlar kullanılabilir. Kalsinasyon fırınları; katı, sıvı ve gaz yakıtların tümü ile ısıtılabilmektedir).
Kaolin Kullanım Alanları :
Petrol Endüstrisi : Özellikle petrol rafinelerinde petrol ürünlerinin katalitik dönüşümlerinde kataliz olarak kullanılır. Pek çok katalizler yüksek ısı ve basınç altında çalışırlar. Bu nedenle kaolinler yüksek ısı şartlarına uygundur. Katalitik Konverterlerin ( Kordiyorit ) imalatında talk veya sepiyolit ve kaolin karışımı kullanılır.
Plastik Sanayi : Güçlendirici ve maliet düşürücü ve katkı malzemesi olarak özellikle viny’ lerde ve polyesterlerde sık kullanılır. Kaolinin en önemli kullanım alanı; (PVC) kaplanmış teller ve kablolardır. Kalsine kaolin ve silika yüzey modifiye edilmiş kaolinler PVC’ lerin elektrik direncini arttırmak için kullanılır, çünkü onlar hidrofobik özelliğe sahiptir.
Lastik Sanayi : Maliyet düşürücü katkı malzemesi ve güçlendirici olarak en çok kullanılan sert kaolinin tane boyutu ortalama 0.2 µm’ dan küçük ve yumuşak kaolinlerin ortalama tane boyutu 1.0 µm’ dan küçüktür. Lastik sanayinde istenilen kaolinin sudaki pH’ı 4.5 -5.5 arasında ayrıca, Fe ,Mn ve Cu gibi elementlerin çok düşük sınırlar içinde olması istenir.
Boya Sanayi : Su bazlı iç ve dış cephe boyalarında veya esaslı, özellikle sanayi boyalarında titanyum oksit ( anorganik pigment ) , öğütülmüş kalsit tozu ve talk ile birlikte kaolin kullanılır. Titanyum oksit kullanım oranını düşürülerek maliyetlerde iyileştirme yapılır. Su bazlı iç cephe plastik ve latex kalsine edilmiş ve lamine olmayan ( delaminated ) mineral yapısına sahip kaolinler kullanılır. Bu gruptaki boyalar % 50 ila % 70 arasında pigment içerir. Yarı parlak ve parlak su bazlı boyalarda kullanılan kaolinin % 98’ i 2 µm’ dan daha büyüktür. Latex boyalarda pigmentler, bağlayıcı reçinelerle beraber, daha iyi örtücülük sağlayan ve binder’ in kırılma indisine yakın kırılma indisi değeriyle ( >1.50 ) kaolin kullanılır.
Mürekkep Yapımı : Litografik, ofset ve flexografik baskı tekniklerinde ince film içeren yüksek yoğunluktaki mürekkeplerde kaolin kullanılır. Mürekkep filmi 5 ile 15 µm arasında değişir ve parlaklığı korumak için ince taneli kaolin ( 0.2-0.5 µm ) renklendirici pigment ile beraber kullanılır.
İzolasyon Alanında : Kaolin latex sodyum silikatlı duvar kağıdı yapıştırıcılarda, alçı panellerde, su bazlı yapıştırıcılarda ve epoxy bazlı yapıştırıcılarda daha iyi viskozite elde etmek, kolay uygulanması ve kolay yayılabilmesi için kullanılır.
İlaç Sanayii : Bazı ilaçlarda adsorpsiyon özelliğinden dolayı kaolin kullanılır. Kalsine edilmiş kaolin ( % 90’ ı 2µm altı ) diş macunlarında kullanılır. Ayrıca otomobil ve metal parlatıcılarında, oksitlenmiş yüzeyleri temizlenmesinde kaolin kullanılır. Bu sektörde kullanılan kaolinlerde en fazla 2 ppm arsenik ve en fazla 20 ppm ağır metallerin bulunması istenir.
Cam Elyaf Yapımı : Isı izolasyonu ve plastiklerin güçlendirilmesinde kullanılır. Cam elyafın ana hammaddesi silis , kaolin ve kireç taşı ile birlikte borik asit, soda ve sodyum sülfattır. Alüminyum camlarda erime ısısını düşürür, kristalize olmasını önler ve suda diğer kimyasallarda çözünebilirliği azaltır. Cam elyaf üretimi için istenilen kaolinde % 37 Al2O3 % 44 SiO2 enfazla % 1 Fe2O3 % 2 Na2O ve % 1 H2O olmalıdır.
Kağıt Sanayi : % 90-100 saf kaolinit minerali aranırken kuvars minerali içermemelidir. Ayrıca parlaklık en az % 85, tane boyutu % 80 < 2µm ve Brookfield viskozitesi < 7.000 cps olmalıdır.
Seramik Sanayi : Genellikle % 75-80 kaolonit minerali içeren kaolinler tercih edilir. Pişme rengi, viskozitesi, sürtünmeye dayanıklılığı, Fe2O3 ve TiO2 oranlarının çok düşük olması ve % 83-91 oranında parlaklık istenir.
Bentonit
Çeşitli metal atomları içeren bir tür kildir. Alüminyum ve magnezyum bakımından zengin volkanik kül, tüf ve lavların kimyasal ayrışması sonucu oluşmuşlardır. Bentonitin koloidal özelliği ve yüksek plastisitesi nedeniyle dökümde kalıp malzemesi olarak kullanılan kumları bağlayıcı özelliği vardır.
Bentonit başlıca kaplama uygulamalarında kalınlaştırıcı malzeme olarak kullanılır. Dolgu amaçlı olarak kullanılan endüstriyel mineraller, ucuz olmalarının yanı sıra sahip oldukları fiziksel ve fiziko-kimyasal özellikleri ile boyanın kalitesine ve performansına önemli katkılar sağlamaktadır. Dolgu maddelerinin boyaya kazandırdığı özellikler şunlardır:
Daha iyi film oluşturma, hava etkilerine karşı dayanımı artırma, gerçek pigment için bir dayanak oluşturma,
Çabuk çökmeyi önleme, Rutubetin geçiş hızını azaltma. Pigmentlerden daha ucuz olduklarından boyanın maliyetini düşürürler.
Sondaj çamurunun ağdalı bir duruma gelmesini, kırıntıların yukarı taşınmasını su kaçaklarının önlenmesini sağlar.
Yağların rengini açmada kullanılan, Ca-Bentonitlerin asit aktivasyonu ile yüzey alanları ve kristal içindeki boşluklar genişletilir, Fe, Ti, Ca, Na ve K, kil minerallerin kristal kafes yapısından ayrılır, boşluklarında H+ - bağları oluşturularak, ağartma toprağına dönüştürülür ve bitkisel yağların (zeytiyağı, ayçiçeği, mısır, susam, soya, palmiye, kanola, pamuk yağları gibi) rafinasyonunda filtre malzemesi olarak kullanılır.
-
Çok zayıf bağ yapışı nedeniyle kolayca parçalanabilir.
-
Bağlayıcı ve plastik özelliğe sahip bentonit demir tozlarının peletlenmesinde kullanılır.
-
İnşaat mühendisliğinde temel ve baraj yapılarında su ve sıvı sızdırmazlığını elde etmede istifade edilir.
-
Şarap ve meyve sularının berraklaştırılmasında, -Hayvan yemi yapımında değerlendirilir.
-
İlaç, kağıt, lastik sanayiinde dolgu malzemesi olarak kullanılır.
-
Çimento sanayiinde, seramik sanayiinde katkı malzemesi olarak,
-
Petrol rafinasyonunda faydalanılır.
-
Atık suların temizlenmesinde kullanılır.
-
Boya sanayiinde ve yangın söndürücülerde yer alır.
-
Gübre yapımı ve toprak ıslahında kullanılır.

Kalsit (CaCO3)
Kalsit (CaCO3), karbonatlı kayaçları (kireçtaşı, mermer, tebeşir) oluşturan doğada bulunan bir
mineraldir. Çeşitli şekillerde kristal halde bulunan camsı parlaklıkta, renksiz saydam yapıdadır. Kolay öğütülür ve beyaz renkli bir toz elde edilir. Sertliği Moh’s skalasına göre 3, yoğunluğu ise 2,6-2.7 aralığındadır.
Dünyada ticari olarak üretilen kalsit (kalsiyum karbonat) oluşumları,
Beyaz renkli kalkerler
Beyaz renkli, saf kireçtaşları
İri kristalli mermerler
Beyaz tebeşir oluşumlarıdır. Bunların içerisinde beyazlığı en yüksek olanlar iri kristalli mermerlerdir. Ancak öğütmede kullanılan enerji, diğerlerine göre daha fazladır.
Çanakkale Karabiga Bölgesi, Türkiye’de mevcut en iri kristalli kalsit oluşumlarından biridir. Granit kontağında oluşan kalsit yatakları yüksek beyazlıktadır ve öğütülmesi kolaydır, fakat Ege Bölgesi ve Niğde’de bulunan oluşumlara göre beyazlığı daha düşüktür. Bayramiç, Biga, Ezine’de mermer yatakları bulunmaktadır. Balıkesir Erdek ve Manyas’da çok zengin iri kristalli mermer yatakları ve ocakları bulunmaktadır.
Trakya’da Yıldız dağları, Bursa Orhaneli’nde mermer ve Dolomitik mermer yatakları
bulunmaktadır. Bursa Orhangazi, Keles, İnegöl zengin mermer yataklarına sahiptir, fakat üretim çok küçük çapta yapılmaktadır. İzmir Tire, Gölmarmara, Akhisar, Torbalı mermer yatakları bulunmaktadır. Beyazlık derecesi daha önce belirtilenlerden daha düşüktür. Muğla Yatağan ve Kavaklıdere Bölgesi kristal yapısı daha küçük fakat kimyasal yapısı daha saf, öğütülebilirliği kolay çok zengin mermer yataklarına sahiptir ve beyazlığı çok yüksektir. Niğde Bölgesi çok zengin rezerve sahiptir ve buradaki kalsit yatakları Türkiye’deki en beyaz oluşumlardır. Bu bölgede çok hızlı bir şekilde üretim artışı yapan kalsit ocakları bulunmaktadır. Günümüzde birçok üretici Niğde Bölgesi’ndeki bu ocaklardan hammadde temin etmektedir. Son yıllarda bu nedenle Niğde’de yatırımlar çok ciddi bir artış göstermiştir. Yukarıda belirtilen bölgeler, rezervi
10 milyonlarca tonla ifade edilebilen çok zengin rezerve sahip bölgelerdir. Bunların dışında Anadolu’nun hemen her bölgesinde henüz üretim ve rezerv tespiti yapılmayan kalsit oluşumlarına rastlamak mümkündür. Bilinen rezervlerin toplamı yüz milyonlarca ton ile ifade edilebilir. Dikkati çeken en önemli noktalar Türkiye’deki rezervlerin; CaCO3 yüzdesinin yüksek,
silis, demir ve magnezyum gibi safsızlıklarının çok düşük oranda, öğütüldükten sonraki beyazlık derecesinin çok yüksek olmasıdır.
Cevherde beyazlık derecesinin yüksekliği boyada ve plastikte titanyumdioksit ve kağıtta optik beyazlatıcı tasarrufu sağladığı için daima tercih edilmektedir. Mikronize boyutlarda kuru veya yaş sistemde öğütülmüş kalsitler; Kağıt, Boya, Plastik ve kablo, İnşaat, Yapıştırıcılar, Gıda, Seramik, Halı tabanı, yer muşambası, İlaç sektöründe kullanılmaktadır.
Boya Sektöründe Kalsit: Boya sektörü 1,3,5,20,40 mikron boyutlarında kuru öğütülmüş kalsit kullanmaktadır. En fazla talep ettiği ürün grubu ise 5 mikronluk kalsittir. Kalsit, iç ve dış kaplamada kullanılan su bazlı inşaat boyalarında, %25-35 oranında boyaya eklenmektedir. Boyada extender olarak kullanılan kalsit yüzeyi kaplamayı sağlar ve titanyum dioksit tüketimini azaltır. Boya sektöründe kimyasal maddelerdeki fiyat artışı nedeniyle piyasada ekonomik boyalara talep fazlalaşmıştır. Boya sektöründe kalsit tüketimi böylece son beş yılda %50 oranında artmıştır.
Plastik Sektöründe Kalsit: Kalsit, plastik mobilya, boru, otomotiv vb. birçok plastikten mamul ürün üretiminde gerek öğütülmüş olarak doğal halde, gerekse kaplanmış halde kullanılmaktadır. Kaplama çoğunlukla stearik asitle bazen de kalsiyum stearatla yapılmaktadır. Polypropilen (PP), Polyamid (PA), Termoplastik (TPES) ve PVC reçineleri esas itibariyle kalsitin dolgu olarak kullanıldığı plastiklerdir. Plastik sektöründe başta kalsit olmak üzere benzeri dolgu maddelerinin kullanımı her yıl giderek artmıştır. Rengi, saflığı, ucuzluğu gibi birçok nedenle plastik sektöründe dolgu olarak kalsit kullanılmaktadır.
Formüllerde kalsit kullanmanın, maliyeti düşürmenin yanında, mekanik performansı arttırmak, verimi yükseltmek amacıyla %5 ile %50 oranlarında kullanımı söz konusudur. PE'nin MFI ve yoğunluğunda değişim gibi bir takım yan etkileri de vardır Bkz. Kompozitler.
Plastik sektöründe doğrudan kalsit ürün bileşiklerinde kullanmaktan ziyade, daha çok PE ile kompozit malzeme elde edilerek kullanımı tercih edilir. Taşıyıcı ama malzeme matris olarak LDPE, HDPE, PP vs. de tercih edilebilir.
Nihai ürün proseslerinde uygulama esnasında, toz kalsit ürünün doğrudan beslemeden diğer bileşenlere dahil edilerek kullanılması, nihai ürün üzerinde homojen olmayan sonuçlara yol açacaktır. Besleme haznesinde iyi karışıma girmeyeceği için, ekstruzyon hattında dengesiz yoğunluğa sahip eriyik oluşacaktır. Bu da tamamen ürün üzerindeki standartlığı yok edecektir.
Bu nedenle kalsit kullanımlarında, nihai ürün üzerine dahil edilecek oranlara denk gelecek oranlarda daha önceden bir kompozit hazırlanması yerinde olur.
Hazırlanacak bu kompozit malzemenin içine akışkanlığı kolaylaştıracak kayganlaştırıcı (ki makine üzerindeki aşınmaları da bir ölçü bertaraf edecektir), kopan polimerik zincir üzerinde iyileştirici olacak bağlayıcı gibi ek katkılar da kullanılmaktadır.
Bunlar daha çok; PE Wax, Kalsiyum Stearat, Çinko Stearat, özel katkı (ajan) şeklinde karşımıza çıkmaktadır.
Nonwoven Dokumasız Kumaş Üretiminde Kalsit : Üretiminin optimize edilmesi amacıyla kalsiyum karbonat dolgu maddesi kullanılmaya başlanmıştır. Kalsiyum karbonat tozu (CaCO3), plastik reçineler ve diğer özel katkı maddelerinden yapılan kalsiyum karbonat dolgu, dokumasız üretim için en etkili malzeme çözümlerinden biridir. Bu malzemenin uygulanması, son ürünlere çeşitli faydalar sunar:
Kalsiyum karbonat dokumasız kumaştan üretilen ürünlerin, tıbbi ve kişisel bakımdan hijyen, jeotekstil (emme, ayırma, filtreleme, koruma, güçlendirme ve boşaltma gibi teknik endüstrilerde kullanılan kumaşlar) gibi alanlara kadar çeşitlilik gösterdiği alanlardır.
Dokumasız malzemelere kalsit dolgusu eklemenin avantajları :
-
Ürün yüzeylerinin iyileştirilmesi sağlar
-
Parlaklığı azaltarak, yüzeyi daha mat ve daha opak hale getirerek kumaş yapısının daha iyi örtme kabiliyetine yol açar
-
Sınırlı sarılık ile doğal beyaz renk verir
-
Malzeme dokusunun iyileştirilmesi sağlar
-
Rahat ve pamuksu bir his yaratır
-
Dokunulduğunda karbon ayak izini önler
-
Hava filtrasyonu ve yağ emilimi için daha fazla mikro alan oluşturur
-
Artan termal iletkenlik ve fiziksel güç katar
-
İşlem sıcaklığının düşürülmesi sağlar
-
Üretimin daha yüksek üretkenlik elde edilmesinin önünü açar, yani kapasiteyi arttırır.
-
Enerji ve üretim maliyetlerinden tasarruf sağlar.
-
Çoklu baz reçineleriyle (iyi dağılım kabiliyeti sayesinde) kolayca işbirliği yapar ve çeşitli yöntemlerle işlenebilir
Kalsitin dokumasız kumaş üretiminde tavsiye edilen kullanım oranları:
-
ince kumaşlarda %5-20,
-
orta kumaşlarda %20-35,
-
kalın kumaşlarda ise %60'lara ulaşmaktadır.
Son derece iyi bir dispersiyon ve stabilite gerektiğinde,
dolgu masterbatch tipik olarak %78-80 yükleme oranı ve 20-40g/10 dak eriyik akış indeksi ile uygulanır.
Dokunmamış kumaşlar için MF indeks değeri farklı kumaş kalınlığı seviyeleri arasında değişiklik gösterir. Daha ince kumaş daha yüksek bir MFI gerektirirken, daha kalın olanlar için daha düşük bir MFI önerilir.
Dokumasız kumaş ürünlerinde kalsiyum karbonat dolgusunun dozaj oranındaki herhangi bir değişikliğin kademeli olarak yapılması sağlıklıdır.
Kalsit CaCO3 iki gruba ayrılır,
Öğütülmüş kalsiyum karbonat: (GCC) (parçacık boyutları 10-1 mikron ölçeğinde,
üretimi daha yalın olduğundan ucuz)
Çöktürülmüş kalsiyum karbonat: (PCC) (Precipitated Calcium Carbonate).
(parçacık boyutları nanometre ölçeğinde, üretimi kimyasal olduğundan pahalı)
çöktürülmüş kalsiyum karbonat, aynı zamanda saflaştırılmış, rafine veya sentetik kalsiyum karbonat anlamına da gelmektedir. PCC de kireçtaşı, mermer ve tebeşir gibi aynı kimyasal formüle sahiptir (CaCO3). Kalsiyum, karbon ve oksijen atomlarının kendi aralarında üç farklı yönde düzenlenmesi ile üç farklı formda kalsiyum karbonat minerali oluşmaktadır.
Çöktürülmüş kalsiyum karbonatın en yaygın olanı hekzagonal yapıda kalsit olarak bilinenidir. Bazı kalsit mineralleri, skalonahedral, rombohedral ve pirizmatik yapıda olabilirler.
PCC, kimyasal yöntemlerle üretildiğinden dolayı, tanecik şekli, tanecik boyutu ve tanecik boyut dağılımı kontrol altında tutulmakta ve bu nedenlerden dolayı öğütülmüş kalsiyum karbonata (GCC) göre avantajları bulunmaktadır.
Doğal kalsiyum karbonatın kimyasal çöktürme işlemi sonucunda kazanmış olduğu bu yapı,
malzemeye, çarpma dayanımı, parlaklık, opaklık gibi artı özellikler kazandırır; PCC aynı zamanda akış özelliklerini geliştiren tiksotropik ajan olarak da kullanılabilmektedir.
PCC plastik işlemede başta sert plastik, PVC profil olmak üzere, plastik boru ve yumuşak
plastik, PVC kablo üretiminde fonksiyonel dolgu olarak kullanılmaktadır.
PCC Sert plastik üretiminde kullanıldığında: profilin (düşük sıcaklıklarda bile) darbe mukavemetini arttırır. Beyazlık ve parlaklığı yükseltir. Profil yüzey düzgünlüğü iyilileştirir. Üretimde ekstrüzyon tork değerlerini dengeler. Hamurlaşma sıcaklığını düşürerek plastikleşme süresini kısaltır. Ekstrüzyon sırasında oluşan sürtünmeyi azaltarak makine ömrünü uzatır.
PCC yumuşak plastik üretiminde kullanıldığında: kabloya tokluk ve esneklik kazandırır. PVC kablolarda düşük HCI emisyonu içeri olması gerekir, yüksek absorplama ve yüzey alanı özellikleri ile PVC hamurundaki yüksek HCI’yi düşürür. Kablo bileşiğinin elektrik, izolasyon özelliğini olumsuz etkilemez. Kauçuk ve lastik üretiminde kullanıldığında, esneklik ve kopma mukavemetini artırır, yüzey düzgünlüğü sağlar.
Ayrıca; Polipropilen (PP), Polietilen (PE) ve Polyester ürünlerinde de kullanılmaktadır.



Kalsit Kalite Belirleme Terimleri
Aşındırma Değeri: 3,2 lt saf suda dağıtılmış 100 gr kuru CaCO3’ın 6000 devir sonrası aşındırma cihazındaki yapmış olduğu mg olarak ağırlık kaybı olup, kağıt sanayinde önemli bir değerdir.
Dağılma Hızı: CaCO3 tanelerinin kullanıldığı ortamda topaklanmaması, dağılmasıdır. Dolgu sanayinde önemlidir.
Aktivasyon: (Kaplama) CaCO3 taneleri arasındaki boşluğun azaltılması ve düşürülmesi için tanelerin çeşitli alifatiklerle kaplanmasıdır.
Beyazlık Derecesi: Standart MgO beyazlığı ile karşılaştırılması sonucu elde edilen bir değer olup malzemenin ışığı yansıtıcılığının %’sidir. Bu değer kalsit için %96-100, mermer için % 96 ve tebeşir için % 93-96 olmalıdır. Kağıt ve beyazlığın önemli olduğu sanayi dallarında aranır bir özelliktir.
Özgül Yüzey: 1 gr CaCO3’ün toplam yüzeyi cm2 olarak değeridir. Kaplama ve plastik sanayinde aranır.
Antisplit
Kalsit; dukuma çuval bantların incelme yapmasını engellemek ve maliyet düşürme amaçlı kullanılmaya başlanmıştı. Daha sonraları piyasa şartlarının getirmiş olduğu rekabetçi yük ile antisplit masterbatch olarak birçok polimer ürün grubunda kullanılmaya devam edilmektedir.
Antisplit masterbatchler, dolgu katkıları olarak, kalsitin ön işlenmiş bileşiğidir. Yani Kalsit,doğrudan ürün bileşiği formülüne dahil edilebileceği gibi, prosesin kolaylaşması için önceden, antisplit adına bürünebilir. Bu şekilde tanecik formu tozdan granüle dönüşür ve daha temiz bir proses akışına olanak sağlanır.
Yüksek dolgulu bu compoundların masterbatch olarak anılmasının sebebi ise renk masterbatch uygulamalarında olduğu gibi ana taşıyıcı polimere yüksek oranda kalsit yüklenerek (%70 – 80) granül haline getirilmesidir. Granül haline getirilen dolgulu compoundun aynı masterbatch gibi içine kalsit yüklemesi yapılacak son ürüne katılarak son üründe bir kalsitin iyi bir dağılım sağlayarak karışmasını sağlamaktır.
Dolgu malzemelerinin toz olması nedeni ile granül halde son ürün işleyen üreticiler (enjeksiyon, ekstrüzyon film ve profil) işleme hunisine direk katarak karıştırmaya çalışmaları bazı problemler oluşturacaktır.
Bu problemler;
-
Granül haldeki malzemeyle huniye konulan dolguların, granülden önce makineye akması sonucu dolguların yeterince dispersiyon olamaması
-
İyi dispersiyon olmamış dolguların belirli bölgelerde birikerek son ürünün mekaniksek özelliklerini düşürmesi
-
Tam dispersiyon olmamış dolguların üründe renk farklılıkları oluşturması
-
Ürün üretimi için tasarlanmış makinelerde dolgularla direk olarak karşı karşıya kalması neticesinde makinede mekaniksel aşınmalar ve çok büyük hasarlar oluşması neden olur
-
Direk olarak kalsitle karşılaşan makinelerde işleme sırasında yüksek basınçlar oluşması sonucu elektrik tüketiminin artması
-
Toz ürün kullanımının getireceği üretim ve işçilik maliyetleri
Bu problemlerin haricinde daha birçok problem sayılabilir. Ayrıca toz ürünün son üründe katılma oranını belirleme toz ürün ile zor olmaktadır. Dozajlama ile yüklenme ye çalışılsa bile toz sistemlerin dozajlama cihaz maliyetleri, granül dozajlayıcılardan çok daha yüksektir. Antisplit masterbatch kullanmanın getirdiği avantajlar ise;
-
Maliyet avantajı sağlar
-
Dolgu maddelerin son üründe çok daha iyi dağılımı
-
Malzeme işlenirken ısı dayanımı sağlar
-
Malzeme ye sertlik, sıkılık ve tokluk özelliği kazandırır
-
Kalıp çekmesinin düşürür
-
Beyaz ürünlerde titan kullanımının azaltılmasını sağlar
Bu ve bunun gibi birçok avantaj sayesinde özellikle son dönemlerde antisplit masterbatch üretimi ve kullanımı artmıştır. Genellikle poliolefin grubu ürünlerde kullanımı çok fazladır.

Antisplit Üretimi
Antisplit masterbatch yapımında çeşitli katkılar kullanılır. Bunlar PE wax, Çinko stearat, kalsiyum stearat yada bu 3 katkı yerine tek başına yeterli olabilen proses ajanları kullanılmaktadır. PE wax dış kaydırıcı ve dipersiyon ajanı, kalsiyum stearat iç kaydırıcı ve akışkanlık artırıcı, çinko stearat dışkaydırıcı fonksiyon görmektedir. Bunun yanında tek paket sistem olarak tasarlanmış olan proses ajanları hem iç, hem dış kaydırıcı, hem akışkanlık sağlayıcı ve bunun yanında bağlayıcılık özelliği ekleyerek tek başına etkili katkı malzemeleridir. Proses yardımcıları %70 – 80 kalsit yüklemelerine kadar tek başına yeterli gelmektedir ve diğer katkıların toplamının yarısı kadar kullanılabilmektedir.
Antisplit masterbatch üretiminde proses işleme makineside önemli bir etkendir. Burada makinenin ürünü sıkıştırma ve karıştırma kabiliyeti önemlidir. Bu proseslerde genelde tek ve çift vida ekstrüzyon makineleri kullanılmaktadır. Tek vida ekstrüzyon makinelerinin ürünü sıkıştırma ve karıştırma oranı zayıf olduğundan, ürünü bir ön karıştıma yapacak banburi sistemine ihtiyaç duyulmaktadır.
Katkı seçiminde en önemli dikkat edilecek faktör sadece fiyat olmamalıdır. Bir ürünün maliyet avantajı satın alımdaki fiyat ile belirlenmemeli, katkının prosese kattığı avantajlar, kullanım oranları, enerji maliyetlerine getirdiği avantajlar, makineyi koruması ve zorlamaması gibi faktörlerin bütünü bir katkının maliyetini ortaya çıkarır. Sadece ilk satın alım maliyeti dikkate alınarak yapılacak alımlar arka planda oluşturacağı birçok maliyetle size daha pahalıya patlayabilir. Bütün katkıların seçiminde bu konuya dikkat edilmesi hem ürününüze hem maliyetlerinize katkı sağlayacaktır.
Muhtemel antisplit formülü:
.png)
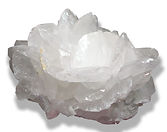
Kalsit (CaCO3)
Kristal Yapı
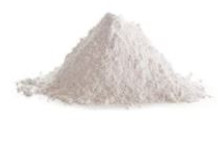
Kalsit (CaCO3)
Öğütülmüş / Toz Yapı
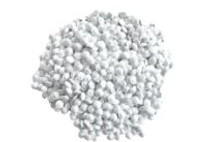
Antisplit
Granül Yapı