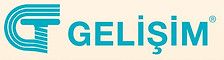


Hidrokarbonlar
Hidrojen ve karbon olmak üzere iki elementten oluşan organik bir bileşiktir. Petrol bileşiminin büyük bir kısmı değişen uzunluklardaki hidrokarbonlardan oluşur.
En küçük hidrokarbon metan, tek bir karbon atomu ve dört hidrojen atomundan oluşur. Bununla birlikte, hidrokarbonlar, zincirler, daireler ve diğer karmaşık şekiller dahil olmak üzere birçok yönden birbirine bağlanmış yüzlerce veya binlerce bireysel atomdan oluşabilir.
Hidrokarbonların özelliklerini sınıflandırmak için birkaç temel türe ayrılırlar.
Alkanlar: Bunlar doymuş hidrokarbonlar olarak adlandırılır. Yani sadece tüm karbon atomları arasında tek bağlar içerirler. Alkanlar, petrol yakıtlarının temelidir ve doğrusal ve dallı formlarda bulunurlar.
Doymamış Hidrokarbonlar: Karbon atomları arasında bir veya daha fazla çift bağa sahip olan hidrokarbonlara alken denir.
Sikloalkanlar: Bir veya daha fazla halka yapısı içeren herhangi bir hidrokarbon.
Aromatik Hidrokarbonlar: Areneler olarak da adlandırılan aromatik hidrokarbonlar, karbon atomlarının birbirini izleyen çift ve tek bağlarla bağlandığı benzersiz bir karbon molekülleri sınıfıdır. Bu molekül sınıfı, karbon atomları arasındaki bağların tek ve çift bağlar arasında bir ara bağ olduğu özel halka yapılarına sahiptir.
Bu sınıftaki moleküller, endüstriyel çözücü «benzen» içerir.
Benzen (C6H6): Diğer hidrokarbonlar gibi benzen de petrolün doğal bir bileşenidir. Oda sıcaklığında renksiz, yanıcı, tatlı kokulu bir sıvıdır ve yüksek oktan sayısına sahip olduğu için çoğu benzin karışımının bir bileşenidir.
Benzen de oldukça kanserojendir ve kemik iliği yetmezliği ve kemik kanserine neden olduğu iyi bilinmektedir. Elbette, “hoş aroması” nedeniyle tıraş sonrası ve diğer kozmetiklerde bir katkı maddesi olarak kullanıldığında kanserojenliği iyi bilinmemektedir.
En büyük benzen kullanımı (% 50), stiren ve polistren plastiklerinin ürünüdür. Ayrıca Naylon üretiminde önemli olan sikloheksan olarak bilinen bir moleküle dönüştürülür. Siklohekzan üretmek için benzenin yaklaşık% 15'i kullanılır. Böcek ilaçlarından kauçuğa kadar her şeyde daha küçük miktarlar kullanılır.
Benzen yapısı iki şekilde çizilebilir. İlkinde, çift bağ karakteri açıkça çizilir. Kısa elli versiyonda, yapıyı göstermek için halkanın içine bir daire çizilir. Benzen içindeki her bir karbon atomuna bağlı tek bir hidrojen vardır.
Aşağıdaki I. ve II. çizimleri eştir. Pratikte III. çizim kullanılır.
Benzen, renksiz, alevlenebilen, kaynama noktası 80,1 °C, erime noktası 5,5 °C olan bir sıvıdır.
Binükleer Aromatik Hidrokarbonlar: Molekülünde iki benzen halkası içeren bileşiklerdir.
Hidrokarbonlar
Hidrojen ve karbon olmak üzere iki elementten oluşan organik bir bileşiktir. Petrol bileşiminin büyük bir kısmı değişen uzunluklardaki hidrokarbonlardan oluşur.
En küçük hidrokarbon metan, tek bir karbon atomu ve dört hidrojen atomundan oluşur. Bununla birlikte, hidrokarbonlar, zincirler, daireler ve diğer karmaşık şekiller dahil olmak üzere birçok yönden birbirine bağlanmış yüzlerce veya binlerce bireysel atomdan oluşabilir.
Hidrokarbonların özelliklerini sınıflandırmak için birkaç temel türe ayrılırlar.
Alkanlar: Bunlar doymuş hidrokarbonlar olarak adlandırılır. Yani sadece tüm karbon atomları arasında tek bağlar içerirler. Alkanlar, petrol yakıtlarının temelidir ve doğrusal ve dallı formlarda bulunurlar.
Doymamış Hidrokarbonlar: Karbon atomları arasında bir veya daha fazla çift bağa sahip olan hidrokarbonlara alken denir.
Sikloalkanlar: Bir veya daha fazla halka yapısı içeren herhangi bir hidrokarbon.
Aromatik Hidrokarbonlar: Areneler olarak da adlandırılan aromatik hidrokarbonlar, karbon atomlarının birbirini izleyen çift ve tek bağlarla bağlandığı benzersiz bir karbon molekülleri sınıfıdır. Bu molekül sınıfı, karbon atomları arasındaki bağların tek ve çift bağlar arasında bir ara bağ olduğu özel halka yapılarına sahiptir.
Bu sınıftaki moleküller, endüstriyel çözücü «benzen» içerir.
Benzen (C6H6): Diğer hidrokarbonlar gibi benzen de petrolün doğal bir bileşenidir. Oda sıcaklığında renksiz, yanıcı, tatlı kokulu bir sıvıdır ve yüksek oktan sayısına sahip olduğu için çoğu benzin karışımının bir bileşenidir.
Benzen de oldukça kanserojendir ve kemik iliği yetmezliği ve kemik kanserine neden olduğu iyi bilinmektedir. Elbette, “hoş aroması” nedeniyle tıraş sonrası ve diğer kozmetiklerde bir katkı maddesi olarak kullanıldığında kanserojenliği iyi bilinmemektedir.
En büyük benzen kullanımı (% 50), stiren ve polistren plastiklerinin ürünüdür. Ayrıca Naylon üretiminde önemli olan sikloheksan olarak bilinen bir moleküle dönüştürülür. Siklohekzan üretmek için benzenin yaklaşık% 15'i kullanılır. Böcek ilaçlarından kauçuğa kadar her şeyde daha küçük miktarlar kullanılır.
Benzen yapısı iki şekilde çizilebilir. İlkinde, çift bağ karakteri açıkça çizilir. Kısa elli versiyonda, yapıyı göstermek için halkanın içine bir daire çizilir. Benzen içindeki her bir karbon atomuna bağlı tek bir hidrojen vardır.
Aşağıdaki I. ve II. çizimleri eştir. Pratikte III. çizim kullanılır.
Benzen, renksiz, alevlenebilen, kaynama noktası 80,1 °C, erime noktası 5,5 °C olan bir sıvıdır.
Binükleer Aromatik Hidrokarbonlar: Molekülünde iki benzen halkası içeren bileşiklerdir.
Hakkında
Kyäni, faydalı bileşenlerden oluşan besin takviyesi ürünlerini; benzersiz iş fırsatıyla birlikte dünya çapında 50'den fazla ülkeye ulaştırmaktadır. İdeal sağlığımızı korumak için günlük olarak Kyäni ürünlerini kullanırız, bu ürünleri başkalarıyla paylaşırız, işimizi inşa etmek ve sürdürmek için neredeyse her gün belirli bir saatimizi işe adarız ve başkalarını da Kyäni fırsatına dahil ederek veya Potato Pak ve Caring Hands programlarına katkı sağlayarak başarımızı başkalarıyla paylaşırız.
Hakkında
Kyäni, faydalı bileşenlerden oluşan besin takviyesi ürünlerini; benzersiz iş fırsatıyla birlikte dünya çapında 50'den fazla ülkeye ulaştırmaktadır. İdeal sağlığımızı korumak için günlük olarak Kyäni ürünlerini kullanırız, bu ürünleri başkalarıyla paylaşırız, işimizi inşa etmek ve sürdürmek için neredeyse her gün belirli bir saatimizi işe adarız ve başkalarını da Kyäni fırsatına dahil ederek veya Potato Pak ve Caring Hands programlarına katkı sağlayarak başarımızı başkalarıyla paylaşırız.
Sayfa Yapım Aşamasındadır.
Sayfa Yapım Aşamasındadır.
Eğitim / Bilgi / Çözüm Platformu
Ön Bilgi
Fizibilite çalışmaları ile olası petrol var olan sahada ölçümler yapıldı. Muhtelif derinliklere inilerek sonar ve sonda çalışmaları ile petrol yatağının hacmi belirlendi. Merkez referans noktasından gitgide uzaklaşılarak sonar ve sondaj çalışmaları ile petrol yatağının büyüklüğü ve rezerv ölçümlerinden sonra rezervin getirisi, çalışma süreci gibi değerlendirmeler ile işin parasal getirisi sonrasında, petrolün çıkartmaya değer olup olmadığına karar verildi.
Tüm bunlar yerin/denizin altında yatan petrolün gün yüzüne çıkartılmaya başlanmadan önce alınması gereken ön değerlendirmeler. Yani bir sahada petrolün var olmuş olması ve bunun keşfi, o petrolün çıkartılabileceği anlamı taşımıyor. Petrolün çıkartılması işinde en önemli karar argümanı illaki maliyetleri karşılayıp karşılamayacağı. Yer altında yatan petrolün derinliğinden, rezervin miktarına, petrolün kalitesinden, sondaj noktasından rafinerilere taşınmasına bir çok yüksek maliyet gerektiren masraflar göz önüne alınmakta.
Bu gün bir çok ülke toprağında petrol yatağı olması muhtemel. Buna Türkiye de dahil. Ancak belirtildiği gibi bu petrol yatağının gün yüzüne çıkartmaya değer olup olmadığı daha çok işin maliyetleri ile ilgili. Özellikle petrol sondaj platformlarına sahip olmaktan, bunları petrol şirketlerinden kiralamaya kadar, başından sonuna para isteyen bir süreç.
Hatırlanacağı gibi 2020 yılında Türkiye Cumhurbaşkanı, batı Karadeniz'de doğal gaz yatağı keşfini müjdelemiş, bu doğal gaz rezervinin 320 milyar metreküp olduğunu açıklamış ve 2023 yılında kullanıma sunulacağını belirtmişti. Daha öncesinde bu alanda hiç bir çalışması olmayan Türkiye'nin, tek bir sonar değerlendirmesi ile rezerv tespitinden, olası rezervin sondajı öncesinde nakliye, taşıma, depolama tesisleri kurulumuna ve tüm bu teknik donanımın yanında teknik personel açığı göz önüne alındığında, işin ciddiyetinden biraz uzak kalındığı görülebilmekte. Uğruna Dünya Savaşı'nın göze alındığı hatta konvansiyonel savaşların bizzat yaşandığı fosil yakıtların gün yüzüne çıkarma işi, Türkiye Cumhurbaşkanı'nın açıklamalarından çok daha ciddi bir mevzu.
Türkiye gibi bu iş için altyapısı yeterli olmayan ülkelerde izlenen yegane yol, rezervin çıkartılması işinin dünya şirketlerine ihale edilmesinden ötesi olamamakta. Bu durumda da, rezerve sahip ülke sadece hisseden pay almaktan öteye gidememekte. Bu da, yaklaşık çıkartılan kaynağın %20 - %30 'unu geçmemekte.
Bir şekilde yeryüzüne çıkartılan fosil enerji kaynağı kelimenin tam anlamı ile ham haldedir. Bu ham petrolün, günümüzde kullanılabilir, amaca hizmet eder bir materyal olması için rafine edilmesi gerekmektedir. Bunun için Türkiye'nin yegane ilgili kurumu, Azerbaycan Socar şirketine özelleştirme adıyla satılan Petkim'dir.
Rafineriye getirilen ham petrol, olabilecek en basit ifade ile, kraking de denilen bir tür damıtma işlemi ile seyreltilmeye, ayrıştırılmaya başlanır. Bir çok aşama içeren bu süreçte, her bir aşamadan günümüzde kullanılan, amaca hizmet eden materyaller üretilmeye başlanır (polimerler, solventler, yanıcı gazlar, asfalt gibi ağır katranlar, alt ürünlerden poliolefinler, polyesterler, polistirenler gibi).
-
Poliolefinler: PE, PP, PB, EVA, EVOH
-
Polyesterler: PET, PBT, PC, PTT, PEN
-
Poliamidler: PA6, PA6.6, PA12, PPA
-
Halojenli polimerler: PVC, PTFE, PVDF
-
Poliakrilatlar: PAN, PBA, PMA, PMMA
-
Polistirenler: PS, ABS, SB, SBS, SAN
-
Polisülfürler: PPS, PSU, PES, PPSU
-
Biyopolimerler: PLA, PEA, PVAL, PPOX
-
Polieter ketonlar: PAE, PEK, PEEK
-
Poliimidler: PI, PBI, PEI, PBO, PMI
-
Poliüretanlar: PUR, TPA, TPO, TPU, Spandex
-
Özel polimerler: LCP, POM, BR, NBR
Konu kaynağı polimerler, tüketim pazarına sunulmadan önce, nihai olabilecek ambalajlama sürecine girer. Bu süreçten sonra polimer ham maddeler; granül boyutunda yada öğütülmüş toz formunda olabilir.
Ambalajlama için big-bag çuvallar olabileceği gibi genellikle 25 kilo torbalarda da olabilir. Kullanıcı firmanın tesis yapısına göre silo-bas tankerler, kamyon, tren ya da gemi ile rafineri sahasından sevkine başlanır.
Aşağıda, söz konusu polimerler hakkında daha detaylı bilgiler şu şekilde özetlenebilir;
LDPE (Low Densty PolyEthylene)
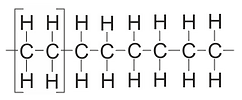
Genel Özellikleri kimyasal mukavemeti yüksek olmalarıdır. Sürtünme katsayısı düşük, kaygan bir malzemedir. Nem emilimi sıfıra yakındır. Polietilen kendi içinde türlere ayrılır. Türleri belirleyen moleküllerinin uzunluğu, moleküler ağırlığıdır. Poliproplen ve PVC’ye nazaran daha yumuşak ve daha az rijit malzemedir. Polietilen’i karakterize eden unsur moleküler ağırlıktır.
(1) Düşük moleküler ağırlık (PE-300)
(2) Yüksek moleküler ağırlık (PE-500)
(3) Ultra moleküler ağırlık (PE-1000) olmak üzere üç grupta toplanabilir.
Özellikle Polietilen 1000 yüksek darbe dayanımı , yüksek aşınma direnci ve düşük sürtünme katsayısı gibi 3 kat daha fazla ömür veren aşınma dayanımı ile belirgin bir ekonomik verimlilik sağlar. Polietilen 1000 kullanılabildiği tüm kimyasal ortamlarda daha uzun ömürle kullanılabilir. Kendinden yağlamalı olması kayganlık ve yapışmama özellikleriyle PTFE’yi andırır. Polietilenin üzerinde buz dahi tutunamaz kayar. Özelikle yanıcı madde üretiminde ve madencilik sektöründe ,başta yer altı olmak üzere tüm ortamlarda patlama ve yangın en temel tehlikedir. Moleküler ağırlık arttıkça aşınma dayanımında belirgin artışlar oluşur. Bahsedilen aşınma dayanımı plastiğin pürüzsüz metal yüzey ile sürtünerek çalışmasında oluşacak dayanımdır. Çalışma Sıcaklıkları 90 ile 150 °C arasındadır.
Gıda endüstrisi, kamyon ve silo kaplama, konveyör zincir kızakları
su tankları, et kesim tezgahları, kağıt, tekstil otomotiv endüstrisi
alanlarında kullanılmaktadır.
Etilen gazı önce ön-kompresörde 250-300 atmosfere kadar sıkıştırılır, ikinci kompresöre gönderilir. Burada basınç 3 500 atmosfere yükseltilir. Reaktörün basıncı fabrikanın dizaynına, katalizörün tipine ve istenilen ürünün derecesine göre değişir. Sıkıştırılan etilen bir ön-ısıtmadan sonra tüp reaktörde polimerleştirilir. Reaktör çıkışında reaksiyona girmemiş etilen, orta ve düşük başınçlı iki ayırıcıya gönderilir. Bu etilen, bir booster yoluyla ön-ayırıcı ve ikinci kompresöre geri-döndürülür. Elde edilen polietilen bir ekstudere verilir; burada gerekli katkı maddeleri ilavesi yapılır ve son ürün granül haline getirilir. Kullanılan reaktör tipinden dolayı polimerizasyon hızı çok yüksektir. Su, buhar, elektrik gibi yardımcı madde harcamaları düşük ve çalışma esnekliği fevkaladedir. Elde edilen ürünün kalitesi çok iyidir.
LDPE Prosesindeki Katalizörler:
Polimerizasyon çeşitli yollarla başlatılabilir; katalizörlerle, oksijenle, ısıl olarak veya ışınla (radyasyonla).
LDPE üretiminde serbest radikal kataliz örü olarak çoğunlukla organik peroksitler kullanılır; bunlar arasında peroksidikarbonatlar, hidroperoksitler ve uzun zincirli peroksitler sayılabilir. Ticari üretimlerde reaksiyondaki alıkonma zamanı 3-15 saniye kadardır.
Son yıllarda poliolefinlerin üretiminde tek aktif uç içeren metallosen katalizörleri kullanılmaya başlanmıştır. Bunlarla üretilen polimerler, diğer katalizörlerle elde edilenlerden farklıdır; molekül ağırlığı dağılımları dar, darbe dirençleri büyük, elastik geri dönüş verimleri yüksek ve optik özellikleri çok iyidir.
Önemli Parametreler:
Reaksiyon hızını, uzun zincirli dallanmaları (morfoloji) ve molekül ağırlığını etkileyen ana parametreler basınç ve sıcaklıktır. Başlatıcının tipi ve miktarı da reaksiyon hızını ve morfolojiyi etkiler. Oksijen ve su ortamda bulunabilecek önemli safsızlıklardır. Bunlardan başka metanol, etan, asetilenler, CO, CO2, H2, C3 ve ağır hidrokarbonlar monomerden gelen safsızlıklardır. Tüm safsızlıklar radikal polimerizasyonunu etkiler ve reaksiyonun yürüyüşünü değiştirir.
LDPE, yüksek basınç otoklav prosesi ve yüksek basınç tüp prosesiyle üretilebilir. Bu iki prosesteki farklılık sadece reaktör tipidir.
Yüksek basınç otoklav prosesinde reaksiyon basıncı 150-200 MPa aralığındadır. Otoklav reakt ör hacmi, alıkonma süresi 30-60 saniye olabilecek şekilde seçilir. Otoklav adyabatik, sürekli karıştırmalı-tank reaktörüdür.

Düşük yoğunluklu polietilen polimer üretiminde kullanılan iki yaygın işlem vardır:
(1) Borulu İşlem
(2) Otoklav İşlemidir.
Her iki işlem de serbest radikal kimyasını kullanır.
Düşük yoğunluklu polietilen, boru şeklindeki bir reaktörde çok yüksek sıcaklıklarda etilenin polimerizasyonu işlemi ile üretilir. Bu boru şeklindeki reaktörde, yüksek basınçlı polimerizasyon, etilenin polar ko-monomerlerle daha fazla kopolimerizasyonuna izin verir.
Boru şeklindeki işlem, otoklav işlemine göre bir avantaja sahiptir. Boru şeklindeki hatlar, daha az güç tüketimi ile daha uygun maliyetlidir. Küresel olarak boru şeklindeki proses, düşük yoğunluklu polietilen üretim teknolojisinde büyük bir paya sahiptir.
Reçineler, üfleme ve dökme film, ekstrüzyon ve kaplama, film ve tabakalar, rotasyonel ve enjeksiyonlu kalıplama ve diğer uygulamalar dahil olmak üzere genel amaçlı ve yüksek performanslı uygulamaların üretiminde temel kullanımlarını bulurlar. Termoplastiklerin diğer tipik uygulamaları arasında tüketici poşetleri, astarları, üst sargılar, laminasyon filmleri, tarımsal filmler, ekstrüzyon kaplamaları, kapaklar ve kapaklar, oyuncaklar ve günlük yaşamda kullanılan diğer birçok dayanıklı plastik ürün bulunur. Hatta pipet yıkama ekipmanı, torba, tank ve genel amaçlı boru imalatı gibi kalıplı laboratuar cihazlarında da kullanılmaktadırlar.
LDPE Temel Özellikleri :
Monomer etilenden yapılmış bir reçinedir. Imperial Chemical Industries (ICI) tarafından 1933 yılında üretilen birinci sınıf polietilendir. Reçine, serbest radikal polimerizasyonu olarak adlandırılan çok yüksek basınçlı bir işlem kullanılarak üretildi. Günümüzde bile termoplastikler aynı yöntemle üretilmektedir. Bu reçineler, üretim süreçlerine bağlı olarak geniş bir esneklik yelpazesinde mevcuttur. Polimerler arasındaki yüksek rekabete rağmen, piyasada iyi bir plastik kalitesi olarak önemini korumaktadır.
Polietilen polimerin küresel üretim kapasitesi 100 milyon ton üzerindedir. LDPE üretim kapasitesi, küresel polietilen üretiminde %20 lik bir paya sahiptir. Üretim bölgelerinin %30 'u Avrupa ve Asya'da, %20 'si Kuzey Amerikadadır.
LDPE termoplastikler, onları çeşitli ürünlere uygulanabilir kılan özellikleri nedeniyle geniş bir kullanım alanı sunar.
Yüksek moleküler ağırlıklı bir poliolefin malzemedir. Diğer tüm poliolefin gibi düşük yoğunluklu polietilen de toksik değildir, kirletici değildir ve yüksek kalitede kırılma direnci vardır. Sudan daha hafiftir, kimyasal olarak inerttir ve oda sıcaklığında çözülmez.
Genel olarak, plastik film uygulamalarına uygunluğunu kanıtlayan esnek bir malzeme ve benzersiz akış özelliklerinin bir kombinasyonu ile süt beyazı yarı saydam bir görünüme sahiptir. Reçinelerin sünekliği yüksek olmasına rağmen, genellikle düşük gerilme mukavemetine sahip olmalarına rağmen, ışığa ve oksijene maruz kaldıklarında mukavemetlerini ve yırtılma direncini kaybederler.
Bu reçinelerin ürünü, inşaat, otomotiv, paketleme ve diğerleri gibi farklı uç segment endüstrilerinde yaygın olarak kullanılmaktadır. Polimerler, farklı özellikleri nedeniyle diğer polietilen kalitelerine göre tercih edilir.
Reçinelerin mukavemeti, sertliği ve her ikisi de kimyasalların yanı sıra sıcaklık direncine sahiptir, bu da onları farklı segmentlerde çeşitli mallar üretmek için uygulanabilir kılar. Düşük yoğunluklu polietilenden üretilen ürünler dayanıklıdır ve günlük hayatımızda kullanılan çanta, oyuncak, film, laboratuar aparatı, oyuncak vb. Plastik ürünlerde kullanımı rahatlıkla tasvir edilebilir.
-
Reçineler, kullanım taleplerine göre sert ve esnek olabilir.
-
Şeffaf veya hatta yarı saydam olabilir ve mumsu bir yüzeye sahip olabilir.
-
Yarı sert, sağlam ve su geçirmezdirler.
-
Düşük bir erime noktasına sahiptirler ve ayrıca iyi nem bariyeri özellikleri sağlarlar.
-
Bu termoplastikler kararlı elektriksel özellikler ve iyi kimyasal direnç sağlar
-
Plastikler düşük maliyetli yöntemlerle kolayca işlenebilir.
-
Çekme dayanımı 0.20 - 0.40 N / mm 2 ve darbe dayanımı kırılma yok
-
Termal Genleşme Katsayısı 100 - 220 * 10.6
-
Max Cont Kullanım Sıcaklığı 65 °C
-
Yoğunluk 0,917 - 0,930 g / cm 3
-
Seyreltik ve konsantre asitlere, alkalilere, alkollere, bazlara ve esterlere karşı mükemmel direnç gösterir
-
Yağlara ve Greslere, Aldehitlere ve Ketonlara karşı iyi direnç sunar.
-
Alifatik hidrokarbonlar, Aromatik hidrokarbonlar ve Halojenlenmiş hidrokarbonlar gibi farklı türdeki hidrokarbonlar , Oksitleyici maddeler ve mineral yağlar için sınırlı direnç sergiler.
-
Düşük özgül ağırlığa ve yüksek darbe dayanımına sahiptirler.
-
Ürünlerin dayanıklılığını artıran güçlü kimyasal ve sıcaklığa dayanıklıdır.
-
Düşük yoğunluğa karşı yüksek derecede suya dayanıklıdır.
-
Plastikler, astar veya alışveriş poşeti olarak kolayca yeniden kullanılabilir.
-
Reçine ayrıca binaları ısıtmak için yakıldığında bir enerji kaynağı olabilir.
-
Uzun süreli kullanımlı ürünlerin üretiminde faydalı olan kırılmaya karşı dayanıklıdır.
-
Bazı ürünler için zayıf ısı direncine sahiptirler.
-
Yüksek termal genleşme katsayısı, düşük yoğunluklu polietilen ürünlerin üretiminde bir sınırlama sağlar.
-
Termoplastikler kötü hava koşullarına dayanıklılık sunar.
-
Reçineler genellikle gerilim çatlamasına maruz kalır.
-
Yapıştırmada güçlük çeken bir çeşit PE sınıfıdır.
-
Plastikler, atık depolama sahalarının yeşil alanları tahrip etmesi gibi tehlikeli çevresel etkilere sahiptir ve kaynaklar üzerinde baskı uygulayan ham petrol gibi yenilenemeyen kaynaklardan yapılmıştır.
LDPE Kullanım Sahaları :
Düşük Yoğunluklu Polietilen, çeşitli kaplar, yıkama şişeleri, dağıtım şişeleri, borular, plastik torbalar ve çeşitli kalıplanmış laboratuar cihazlarının üretiminde yaygın olarak kullanılan bir polimerdir. Plastikler, onları çeşitli son segment ürünler için uygulanabilir kılan özellikleri nedeniyle çok büyük miktarlarda kullanılmaktadır. Termoplastiklerin temel uygulamaları şunlardır:
LDPE Borular :
Düşük yoğunluklu polietilen boru (poli boru) evsel ve kimyasal sulama amaçlı en çok kullanılan borudur. Bu borular temelde kaynaktan mikro boruya dağıtım yapmak için sulamada kullanılır. Zemin üstüne montaj için oldukça uygundurlar ve çok esnek olmadıkları için konektörler besleme borularını yönlendirmek için kullanılabilir. Borular, yağmurlama sulama, damla sulama, drenaj sistemi, tarımsal borular ve diğer sulama sistemlerine kadar geniş bir uygulama yelpazesinde kullanılabilir. Bu borular, kaplinler, dirsek tişörtleri ve adaptörler gibi naylon geçme bağlantı parçalarına sahip tam akışla kullanılır. Sızdırmazlığı engellemeye ve su basıncına kolayca dayanmaya yardımcı olan sızdırmaz ve serbest bir sızdırmazlık sağladıkları için borularla birlikte tırtıklı klemensler kullanılmaktadır. LDPE boruların temel karaktesitik özellikleri şu şekilde sıralanabilir:
-
Borular, yüksek oksidasyon faktörleri dışındaki oda sıcaklıklarında reaksiyon vermez.
-
Bu borular 0.910 g / cm 0.940 tanımlanmış bir aralığı vardır
-
Düşük yoğunluklu polietilen borular, 80 - 95 °C'ye sürekli olarak dayanabilir.
-
Borular tamamen yarı saydam veya opaktır ve kırılmaya karşı oldukça dayanıklıdır.
-
Boru maksimum 80 °C sıcaklığa ve en düşük -120 °C sıcaklığa dayanabilir.
-
Boruların erime noktası 120 °C
-
Çekme mukavemeti: 1700 psi (11,7 MPA)
-
Yoğunluk: 0,92 g / cm3
-
UV direnci zayıftır.
-
Mükemmel esnekliğe sahip yarı saydamdırlar.
LDPE Film ve Levhalar :
Geliştirilen ilk polietilendir ve nispeten ısı direnci ve sıcaklık etkisiyle sertliği ve esnekliği ile bilinir. Bu özellikler, diğer plastik ürünleri üretmek için daha sonra kullanılabilen film ve tabakalar şeklinde üretilebilmelerini mümkün kılar. Bu malzeme, enjeksiyon, üfleme ve rotasyonel kalıplamaya uygun olmasının yanı sıra günümüzde esas olarak film uygulamaları için kullanılan en hızlı büyüyen plastiklerden biridir.
-
Ambalaj endüstrisi - Gıda ambalajlarında ve tekstil ambalajlarında kullanımı yüksektir. Film ve tabakalar, ambalaj endüstrisinde ürün poşetleri, brad poşetleri, çöp poşetleri, giysi poşetleri, market poşetleri ve nakliye poşetleri amacıyla uygulama sahası geniştir.
-
Endüstriyel - Bantlar, sızdırmazlık malzemeleri, contalar, fotografik koruma, astarlar, boru sistemleri, kompozitler, otomotiv parçaları, shrink filmler, palet streç, sera kaplamaları, tanklar ve kaplar vb. Üretmek için kullanılır.
-
Medikal - Transdermaller, Hidrojeller ve yara bakımında veya ilaçların paketlenmesinde kullanılır.
-
Çarşaflar yarı saydam ve daralabilir.
-
Isıya ve kimyasallara dayanıklıdırlar.
-
Levhalar plastik kaynakçı ile kolaylıkla kaynak yapılabilir
-
UV stabilize etmezler
-
Bu filmler iletken filmlerdir ve kolaylıkla renklendirilebilir.
-
Yapışma kolaylığı sunarlar, bu da kolayca ısıyla yapıştırılabilecekleri anlamına gelir.
-
Filmler ve tabakalar esnek, hafif ve ekonomiktir.
-
Yoğunluk: 0,92
-
Şekillendirme sıcaklığı: 245 °F
-
Sıcaklık aralığı: 0 °F - 140 °F
-
Çekme Dayanımı (PSI) 1600
-
Nihai Uzama% 600
Bazı LDPE marka ham maddelerin teknik değerleri ve daha çok kullanım alanları :
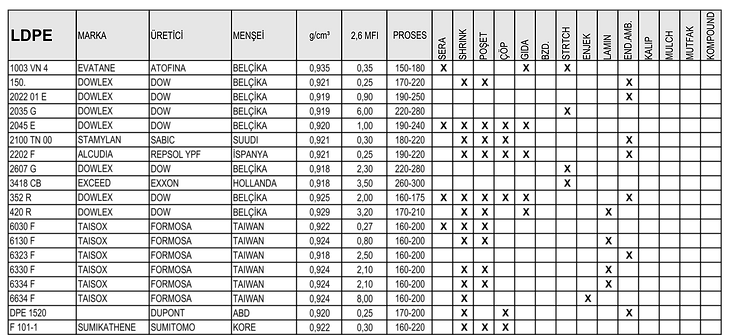
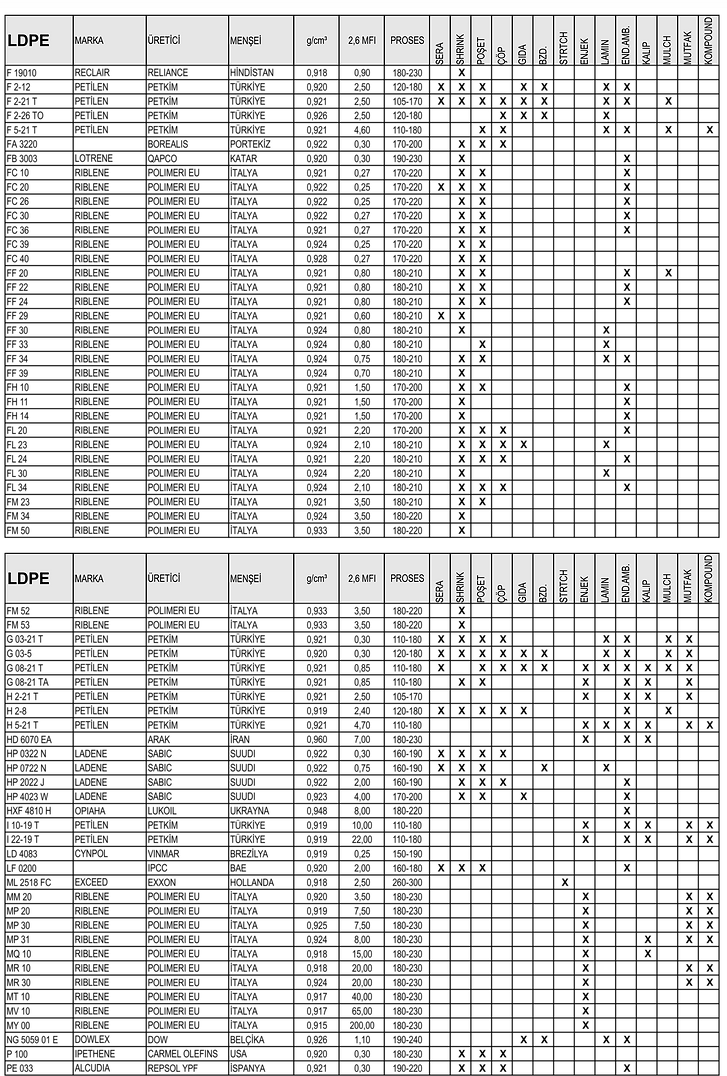

MDPE (Midium Densty PolyEthylene) :
(Orta yoğunluklu polietilen) LDPE'den daha güçlü ve esnek son ürün elde etmek için MDPE kullanılır.
MDPE, daha yaygın olarak kullanılan HDPE’den daha az yoğun olan, 0,926-0,940 g/cm3 arasında bir yoğunluğa sahip bir termoplastiktir. LDPE ile karıştırılması gerektiğinde LDPE'den daha iyi kimyasal dirence sahiptir. Ama tüm bunlara rağmen en az kullanılan polietilendir. MDPE ağırlıklı olarak gaz boruları ve bağlantı parçaları, torbalar, shrink filmler, ambalaj filmleri, taşıma çantaları ve üfleme şişelerde kullanılmaktadır.
-
Darbelere ve düşmelere karşı dayanıklıdır.
-
HDPE’den daha iyi kesme yanıtı verir.
-
HDPE’ye oranla gerilme çatlamalarına karşı daha fazla direnç gösterir.
-
Orta yüksek ısı direncine sahiptir.
-
HDPE’ye göre yoğunluğu oldukça düşüktür.
-
Gıda İşleme kurallarına uyumludur.
ULDPE (Ultra Low Densty PolyEthylene) :
ULDPE (ultra düşük yoğunluklu polietilen) ve VLDPE (çok düşük yoğunluklu polietilen), temelde 0.880 altında g/cm3 yoğunluğa sahip LDPE’lerdir. ULDPE’ler, esas olarak diğer poliolefinler için darbe arttırıcı olarak kullanılır. Gıda, sağlık ve hijyen amaçlı ambalajlama ve genel amaçlı filmlerde, sulama boruları üretiminde tercih oranı yüksektir.
-
Düşük sıcaklıklarda esneklik gösterir
-
Sıvı kaplar için çok iyi çalışır
-
İyi derecede optik özelliklerine sahiptir.
-
Temelde üflemeli ve enjeksiyon kalıplama ile kullanılır
-
Gıda İşleme kurallarına uyumludur.
mPE (metallocene PolyEthylene) :
Bu polimerler, ayrıca Doğrusal Metalosen olarak da adlandırılan yeni nesil yüksek performanslı polietilenlerdir (PE). Ambalaj, tarım, inşaat ve bina ve endüstriyel uygulamalar gibi çok sayıda film uygulamasında kullanılırlar. PE’nin genel özelliklerini önemli ölçüde geliştirerek ve üretilen ürüne katma değer sağlayarak mükemmel performans sunar. Ambalaj için paketleme (laminasyon için film) (stretch film), ekstrüzyon işlemleri için kaplamalar, tarımsal örtülerin üretiminde mükemmel sonuçlar verir.
-
Darbelere, delinmeye ve yırtılmaya karşı yüksek dirençlidir
-
Erimeye karşı yüksek dirençle kolay İşleme süreci vardır
-
Mükemmel sızdırmazlık (SIT ve Hot Tack testleri ile gösterildiği gibi) özelliği gösterir
-
Mükemmel optik özellikleri vardır
-
Çok katmanlı film ekstrüzyonuna özel bir yapıdadır.
-
LDPE, HDPE ve LLDPE ile karşılaştırıldığında film kalınlığında önemli azalma sağlar
-
Daha verimli ve hızlı paketleme işlemleri ve daha iyi sızdırmazlık için tercih edilir
-
Filmlerde optik iyileştirmelerde (parlaklık ve şeffaflık) öncelikli tercih edilir
-
Genel olarak mekanik özelliklerde önemli gelişme gösterir
-
Gıda İşleme kurallarına uyumludur.
Bazı MDPE marka ham maddelerin teknik değerleri ve daha çok kullanım alanları :

LLDPE (Lineer Low Densty PolyEthylene)
Doğrusal düşük yoğunluklu polietilen, genellikle düşük sıcaklıklarda üretilen, yoğunluğu 965 kg / m'den büyük olan bir polimerdir. Etilenin polimerizasyon işlemi sırasında olefinlerin (büten, heksen veya okten) eklenmesiyle üretilir.
Poli-olefinler doğrusal düşük yoğunluklu polietilen reçinelerin üretiminde kullanılır çünkü bu monomerler reaktif bir çift bağ içerir. Bu monomerler, kullanıcı talebine göre üretilen reçinenin yoğunluğunu ve fiziksel özelliklerini kontrol etmek için buna göre kullanılır. İki ana teknik kullanılarak üretilir:
Gaz fazı polimerizasyonu:
Bu işlemde, kuru polimer partiküllerinin bir tür akışkanlaştırılmış yatağı olan bir gaz fazı reaktörü kullanılır. Bu reçine partikülleri, yüksek hızda etilen gazı karıştırılarak veya geçirilerek gaz reaktörü olarak muhafaza edilir.
Bu gaz reaktöründe, ko-monomer ile birlikte etilen, içine daha sonra katalizörün enjekte edildiği akışkan yatağın tabanından beslenir. Bu gazda, reaktör basıncı nispeten düşüktür (2 MPA'ya kadar) ve muhafaza edilen sıcaklık 70 ila 110 ° Celsius civarındadır.
Son olarak, erimiş polimer formları stabilizatörler ile karıştırılır ve linera düşük yoğunluklu peletler şeklinde ekstrüde edilir. Bu peletler ayrıca plastik ürünlerin üretiminde kullanılmaktadır.
Etilenden düşük basınçta, gaz fazı polimerizasyonuyla, lineer alçak yoğunluklu polietilen elde edildiği bir prosestir. Akışkan-yataklı bir reaktörde, uygun katı katalizörler kullanılarak, gaz fazında, geniş bir aralığı kapsayan polietilenler üretilebilir. Ürün kurudur, kolaylıkla akar ve ince tanecikler içermeyen granüller şeklindedir.
Erime indeksi ve molekül ağırlığı dağılımı, özel katalizörler seçimi ve çalışma koşulları ile kontrol edilir. Polimerin yoğunluğu, üründeki ko-monomer miktarı ile ayarlanır. Katalizör verimi çok yüksektir; bu özellik reaksiyondan sonra, bir katalizör ayırma işlemini ortadan kaldırır. Prosesin özelliği, çevre kirlenmesini, yangın ve patlama tehlikelerini en düşük düzeyde tutmasıdır; dolayısıyla çalışması ve bakımı oldukça kolaydır.
Gaz etilen, ko-monomer ve katalizör reaktöre konulur; reaktörde, büyüyen polimer taneciklerinin oluşturduğu bir akışkan yatak vardır; 20 kg/cm² basınç ve 100 °C dolayında çalışır. Reaksiyon yatağına akan reaksiyon gazı, tek kademeli bir santrifüj kompresörüyle sirküle ettirilir; böylece, polimerizasyon reaksiyonu için gerekli ham madde sağlanırken, yataktan reaksiyon ısısı da uzaklaştırılır. Sirkülasyon gazı bir ısı değiştiriciden geçirilerek soğutulur.Granüler ürün, aralıklarla, ürün deşarj tanklarına akar. Burada reaksiyona girmemiş gaz, üründen ayrılır. Çıkan gaz sıkıştırılır ve tekrar reaktöre gönderilir. Üründe kalan hidrokarbonlar azotla süpürülür. Granül ürün düşük enerjili bir sistemde pellet şekline getirilir. Ürünler polimerin yoğunluğu 0.915-0.970 g/cm aralığında kolay kontrol edilir. Molekül ağırlığı dağılımı, katalizöre göre, dar veya orta genişliktedir. Erime akışı 1 den 200 ün üstüne kadar değiştirilebilir.
Çözüm Polimerizasyonu:
Bu işlemde, doğrusal düşük yoğunluklu polietilen reçineler, doymuş bir hidrokarbon ortamı içinde düşük basınç (1-5 MPA) ile birlikte nispeten düşük sıcaklıklarda (70-110 ° C) üretilir.
Polimerizasyon işlemi sırasında, polimer bir süspansiyon veya hareketli bir bulamaç oluşturur. Ayrıca, reaksiyon ortamı çıkarılır ve polimer, hidrokarbon eylemsiz ortamdan ayrılır.
Bu işlem sonucunda elde edilen toz, stabilizatörler ile tekrar karıştırılır ve pelet formunda ekstrüde edilir. Bu doğrusal düşük yoğunluklu polietilen peletler ayrıca son segment plastik ürünlerin üretiminde de kullanılabilir.
Gaz fazı polimerizasyon işlemi, içerdiği işletim maliyeti, işlemdeki sıcaklık bakımı ve polimer üretimi sırasında esneklik kolaylığı açısından Çözelti Polimerizasyonundan daha iyidir.

LLDPE ilk olarak 1959'da Kanada'da DuPont tarafından üretilen, etilenin farklı uzun zincir olefinlerle kopolimerizasyonu ile oluşturulan bir dizi kısa dalı olan bir tür doğrusal polimerdir. Geleneksel LDPE'den (Düşük yoğunluklu polietilen) bazı yapısal farklılıklara sahip olan poli-olefin ailesinin bir parçası gibidir.
Bu polimer, LDPE ve HDPE ile birlikte polietilen sektörünün üçüncü önemli oyuncusu olarak kendini kanıtlamıştır. Küresel polietilen pazarının%3 'üne sahiptir. Polimerin doğrusal özelliği, doğrusal yoğunluklu polietilen ve düşük yoğunluklu polietilenin üretim süreçlerindeki farklılıktan kaynaklanmaktadır.
Genellikle LLDPE, etilenin ve Buten, Heksen veya Okten gibi daha yüksek alfa-olefinlerin ko-polimerizasyonu yoluyla nispeten daha düşük sıcaklıklarda ve basınçlarda üretilir (yukarıda anlatılmıştır). LLDPE çok çeşitli uygulamalar ve kullanımlar için uygun hale getiren geleneksel LDPE polimerlerine kıyasla daha yüksek gerilme mukavemeti, darbe ve basınç direnci sergiler.
Doğrusal düşük yoğunluklu polietilen reçineler, esas olarak torbalar ve tabakalar için film olarak veya ambalaj endüstrisinde kullanılır. Oyuncaklar, kapaklar, kova, plastik kaplar, balonlu ambalajlar ve kompozit filmler gibi diğer ürünlerin imalatında da kullanılmaktadır. LLDPE önemli miktarda dalı olan bir tür doğrusal polimerdir. Enjeksiyon kalıplama, rotasyonel kalıplama, teller, levhalar, borular ve kanallar gibi uygulamalar için yaygın olarak kullanılmaktadır. Bunlar ayrıca paketleme, tarım, inşaat, otomotiv, ev, denizcilik ve oyuncak gibi son kullanıcı endüstrilerinin mallarının üretiminde kullanılır.
Kuzey Amerika, doğrusal-düşük yoğunluklu polietilenin en büyük tüketicisi olmuştur ve bunu Asya-Pasifik bölgeleri takip etmektedir.
LLDPE pazarına Borealis, Braskem SA, Chevron Phillip Chemical Co., DuPont, ExxonMobil Chemical, INEOS Group, Nova Chemicals ve The Dow Chemical Company üretici şirketleri öncelik etmektedir.
LLDPE Temel Özellikleri:
Film ve ambalaj endüstrisi için temel yapı taşları olduklarını kanıtlayarak ürün tarafından arzu edilen dengeli sertlik ve tokluk sunar. Doğrusal düşük yoğunluklu malzemenin özellikleri, fiziksel ve kimyasal özellikleri arasındaki denge, onları sarf malzemelerinin, ağır hizmet tipi nakliye çuvallarının, filmlerin (harmanlama shrink filmleri ve streç filmler vb.) Ambalajlanması ve ayrıca kaplar ve kapakların üretimi için ideal bir polimerdir.
-
Daha yüksek gerilme mukavemeti, yüksek darbe ve yüksek delinme direnci sunarlar.
-
Doğrusal düşük yoğunluklu polietilen malzemeler çok esnektir ve genellikle stres koşulları altında kendilerini uzatırlar.
-
Bu polimerler, iyi çevresel stres çatlama direncine sahip olduklarından, ince filmler üretmek için kolaylıkla kullanılabilirler.
-
Doğrusal düşük yoğunluklu plastikler, iyi elektriksel özelliklere sahip olmanın yanı sıra kimyasallara son derece dirençlidir.
-
Daha yüksek mekanik ve gelişmiş sızdırmazlık özelliklerine sahiptirler.
-
Son ürünlere iyi bir son kat kazandıran şeffaf ve parlak bir görünüme sahiptir.
-
Doğrusal düşük yoğunluklu polimerler, düşük üretim ve dönüştürme maliyetlerine sahiptir..
-
Çekme dayanımı 30 MPA ve çentikli darbe dayanımı 06+ kJ / m
-
Yoğunluk 916 g / cm³
-
Maksimum çalışma sıcaklığı 50 ° C'dir
-
Doğrusal genişletme 20 × 10−5 / ° C teklif edildi
-
Su emme seviyesi genellikle % 01'dir
-
Erime Sıcaklığı Polimer aralığı 120 ila 160 ° C'dir.
-
Bu malzemeler yüksek esneklik ve uzun ömür sağlar.
-
UV ışınlarına ve kimyasallara karşı iyi bir dirence sahiptir.
-
Doğrusal düşük yoğunluklu plastikler, delinmeye karşı oldukça dirençlidir.
-
Doğrusal düşük yoğunluklu polietilen malzemeler sağlam mekanik özelliklere ve daha az bakıma sahiptir.
-
Yüksek çekme mukavemetine sahiptirler.
-
Mükemmel bir ortam ve gerilme çatlağına dayanıklı malzemedir.
-
LDPE'ye kıyasla daha az parlaktır.
-
Bu malzemelerde ısıl yapıştırmanın sıcaklık aralığı daha azdır.
-
LDPE ile karşılaştırıldığında, işleme aşamasında esneklik kolaylığı sunmamaktadır.
LLDPE Kullanım Sahaları:
LLDPE çeşitli kullanımlar için bir plastik film üretmek için yaygın olarak kullanılmaktadır.
Bu işlemde LLDPE üflemeli film reçineleri düz tamburlu ekstrüderlerde işlenir, bu varillerin uzunluğu 24: 1 ila 30: 1 arasında değişebilir. Kabarcık çapını ölçmek kolay olmadığından 2: 1 ile 3: 5: 1 oranındaki düz döşeme genişliğinden hesaplanır.
LLDPE reçinelerin dar moleküler ağırlık dağılımı nedeniyle, filmlerin 90 - 110 mil arasındaki geniş aralıklar arasında ekstrüde edilmesi gerekir. Kalıp boşluğu reçineler için çok darsa, film erimeye ve kırılmaya maruz kalabilir ve boşluk çok genişse üretilen filmde stabilite sorunları olabilir. LLDPE donma hattı yüksekliğinin ayarlanmasıyla bu filmleri üretirken özelliklerde belirli iyileştirmeler yapılabilir. Üretim sırasında seviyesini düşürerek daha iyi mekanik özellikler ve film berraklığı elde edilebilir.
Doğrusal düşük yoğunluklu polietilen reçinelerin ekstrüderde eritildiği yaklaşık sıcaklık 200-230 °C arasındadır.
-
Çok esnektir, çoğunlukla esnek tabaka formlarında 0,5 mil kalınlık ile 40 mil arasında değişir.
-
Doğrusal düşük yoğunluklu polietilen filmler doğal süt rengindedir ve görünüşte yarı saydamdır.
-
İyi su emme kalitesinin yanı sıra yüksek kimyasal ve darbe dayanımına sahiptirler.
-
Doğrusal düşük yoğunluk mükemmel darbe ve gerilme çatlağı direnci sunar
-
Genellikle 93 g / cm 3 yoğunluğa sahiptirleR.
Doğrusal düşük yoğunluklu filmler, inşaat, tarım ve yüzey koruma uygulamaları, her türden örtüler, muşamba ve çok daha fazlası gibi çeşitli endüstrilerde yaygın olarak kullanılmaktadır. Üretilen film örnekleri, streç filmler, zirai filmler, laminasyon filmleri ve harmanlama shrink filmleri vs.'dir.
LLDPE Boru :
LLDPE, mükemmel gerilme çatlağı direnci, esneklik, dayanıklılık ve düşük maliyet gibi belirli özelliklere sahiptir ve bu da onları boru endüstrisi için tamamen uygun kılar. LLDPE plastikler, kimyasal maruziyet, eskime, yüksek titreşimli bağlantılar, çıkıntılı tip bağlantı parçalarına bağlantı ve diğer sıkıştırma bağlantı parçaları içeren borularda yaygın olarak kullanılmaktadır.
Farklı solüsyonlara ve kimyasallara 500 saat ve daha fazla maruz kalmaya kolayca dayanabilir. Hatta sıkıştırma ile kullanıldığında veya bağlantı parçalarını bağlamak için itildiğinde çatlamaya bile direnebilirler. LLDPE boruların karakteristik özellikleri:
-
Daha yüksek gerilme mukavemeti ve yüksek patlama basıncı.
-
Üstün stres ve çatlak direnci sunarlar.
-
Bu tüpler mükemmel yüksek delinme direncine sahiptir.
-
Doğrusal düşük yoğunluklu polietilen boru, gazlara ve neme karşı oldukça geçirimsizdir.
-
Üstün dielektrik özelliklere sahiptirler.
-
Hafif, Dayanıklı ve Ekonomiktir.
-
Siyah, gri, kırmızı, yeşil, mavi, sarı, turuncu, açık ve mor gibi farklı renklerde mevcuttur.
-
Bu Tüpler için Sıcaklık Aralığı: -40 ° F ila 150 ° F (-40 ° C ila 66 ° C)
-
Vakum Değerlendirmesi: 28 ”Hg'ye
-
Bu Tüplerin Çap Toleransı: ± 0,004 ”
-
Tüp İşaretleri: FW özellikleri
-
Çalışma Basıncı: 3: 1 güvenlik faktörü
-
Yiyecek ve içecek, tıbbi ve farmasötik uygulamalar ile kullanım için uygundur.
LLDPE Torbalar :
HDPE (Yüksek yoğunluklu Polietilen) ve LDPE (Düşük yoğunluklu polietilen) gibi, doğrusal düşük yoğunluklu polietilen malzemeler de çeşitli kullanımlara uygulanabilen farklı Poli çantalar üretmek için yaygın olarak kullanılmaktadır.
Endüstriyel poli çantalar, stresli veya diğer aşırı koşullar altında kırılmaya ve delinmeye karşı yüksek direnç sundukları için genellikle bu malzemelerden yapılır. Bu plastik poşetler market poşetleri, giyim mağazalarında kullanılan poşetler, ağır hizmet tipi poşetler, alışveriş poşetleri veya büyük atık bertaraf poşetleri olarak kullanılmaktadır.
Bu Poly çantalar, yüksek darbe ve gerilme mukavemeti ile çok esnektir, çizilmez ve dayanıklıdır. Doğrusal düşük yoğunluklu polietilen düşük maliyetli bir malzeme olduğundan ve kolayca temin edilebildiğinden, bu poli torbalar diğerlerine göre daha ekonomiktir.
Parlak bir görünüme sahiptirler ve tekrar kullanılmak üzere geri dönüştürülebilirler. Günümüzün doğrusal düşük yoğunluklu plastik poşetleri, büyük ölçüde geri dönüştürülmüş doğrusal yoğunluklu polietilen malzemeler kullanılarak üretilmektedir.
LLDPE Örtüler :
Doğrusal düşük yoğunluklu polietilen astarlar veya doğrusal düşük yoğunluklu polietilen polimer jeo-membranlar, mukavemetleri, esneklikleri ve dayanıklılıkları nedeniyle çeşitli uygulamalar için gereklidir. Kalınlıkları 0,5 - 2,5 mm arasında değişebilir ve doğrusal düşük yoğunluklu astar ruloları kalınlıklarına bağlı olarak çeşitli en ve boylarda olurlar.
LLDPE malzeme, aşağıdaki nedenlerden dolayı plastik astar üretmek için ideal bir seçimdir :
-
Bu jeo-membranlar yüksek derecede esneklik sunar. Daha fazla esneklik, çökme ve farklı oturmaya daha fazla uyum sağladığından faydalıdır.
-
UV ışınlarına ve kimyasallara karşı kuvvetli dayanıklıdırlar.
-
Bu gömlekler, rakiplerine göre yüksek delinme direncine ve daha dayanıklıdır.
-
Bu astarlar, talebe göre kullanılan beyaz ve siyah renk olmak üzere iki farklı yüzey renginde mevcuttur.
-
Lagün, Kanal, Tank ve Göletlerde (Tutma havuzları, Tarımsal göletler vb.) Astar olarak kullanılır.
-
Doğrusal düşük yoğunluklu polietilen astarlar, çöplük kapakları ve kapatmalar için yaygın olarak kullanılmaktadır.
-
Bu jeo-membranlar, yığın liç yastıklarının madenciliği için kullanılır.
-
Gömlekler ayrıca rezervuarların, atık suların işlenmemiş sularının arıtılmasında ve ayrıca portatif su rezervuarları olarak kullanılır.
-
Yer üstü depolama tankları için ikincil kirletici olarak ve su depoları için Yüzer kapaklar olarak kullanılır.
LLDPE Büten-C4 / Heksen-C6 / Okten-C8 :
Yüksek (0.941 g/cm3’e kadar) yoğunluktan çok düşük (0.905 g/cm3) yoğunluğa kadar değişiklik gösteren C8 Okten’den C6 Heksen ve C4 Büten’e kadar çok çeşitli doğrusal düşük yoğunluklu polietilen (LLDPE) çeşitleri vardır. LLDPE, gıda, dondurulmuş gıda ambalajı, ışıma ile ısıtma boruları ve kozmetik ve eczacılık uygulamaları için film ekstrüzyon, üflemeli kalıplama, döner kalıplama ve enjeksiyon kalıplama için kullanılır. Dünya çapında yaklaşık %80, daha gelişmiş mekanik ve termal özellikler için LDPE ve HDPE ile karıştırılmıştır. Gıda ambalajlarında ve diğer ürünlerin ambalajlanmasında ve ekstrüzyon kaplama uygulamalarında ve özellikle kağıt ve karton ambalajlanmasında kullanım sahalarıdır.
Avantajları:
-
Çok yönlü,
-
Ekonomik
-
İyi derecede mekanik özelliklere sahip alt sızdırmazlık sıcaklığı
-
Yüksek performanslı yapılarda büyük tasarruf sağlama
Özellikleri:
-
Çok esnek ,
-
Yüksek çekme mukavemeti
-
İyi derecede kimyasal direnç
-
İyi derecede elektriksel özellikler
-
Gıda İşleme kurallarına uyumlu
Bazı LLDPE marka ham maddelerin teknik değerleri ve daha çok kullanım alanları :

Metalosen LLDPE
Strech filmlerin üretimi, strech başlık filmleri, süt filmleri, yüksek mukavemetli genel amaçlı filmler, laminasyon filmleri, sera, tarım ve diğer filmler; ayrıca tek başına veya diğer polietilen türlerine katkı maddesi olarak kullanılır.
Metalosen polietilenden üretilen filmler mükemmel mekanik mukavemete ve kalınlığı azaltma potansiyeline sahiptir, moleküllerin homojen bileşimi mükemmel sıcak dikiş mukavemetini ve düşük erime noktasını belirler, böylece daha hızlı kaynak sağlar. Üfleme ve enjeksiyon kalıplama yönteminde metalosenlerin kullanılması, daha az bulanıklık ve yüksek parlaklığa sahip bir film üretmenizi sağlar. Yüksek darbe direnci ile karakterize, mükemmel yalıtım nitelikleri sunar.
mLLDPE: 0.927 g/ cm3 yoğunlukludur ve bir hekzen kopolimeridir. mPE film sertliği, kuvveti ve darbe dayanımı gibi özellikleri ile eşsiz film performansına sahiptir. mLLDPE'nin geleneksel LLDPE`ye göre: yüksek gerilme mukavemetli, yüksek tokluğa sahip, delinme direnci ve darbe dayanımı iyileştirilmiş, sızdırmazlık kapasitesi yüksek, mükemmel saydamlık ve parlaklık gösteren ve diğer poliolefinlerle kolay karışabilme üstün özelliklerine sahip bir polimerdir.
HDPE (High Densty PolyEthylene)
Yüksek yoğunluklu polietilen, çoğunlukla heterojen fazda çözelti, gaz fazında da kütle polimerizasyonu teknolojileriyle üretilir. Homojen fazda çözelti polimerizasyonu yöntemi de, az da olsa uygulanmaktadır. Her durumda ekzotermik reaksiyon, ortamda bulunan etilen monomeri, <P255> katalizör sistemi ve hidrokarbon seyrelticiye bağlıdır. Molekül ağırlığı kontrolü katalizörle ve reksiyon sırasında kullanılan hidrojenle sağlanır.
Etilenden, düşük basınçta çözelti polimerizasyonuyla, yüksek yoğunluklu polietilenin elde edildiği bir prosestir. Etilen (ve istenirse az miktarlarda ko-monomerler), katalizör ve hidrokarbon seyreltici, büyük polimerizasyon reaktörüne gönderilir. Reaksiyonda çamur meydana gelir ve polimer toz halinde oluşur. Polimerizasyon 10 barın altında ve 80-90 °C aralığında yapılır. Katalizörün aktifliği çok yüksektir; bu nedenle büyük miktarlardaki üretimlerde sonradan katalizör ayrılmasına gerek olmaması için, katalizör azar azar ilave edilir. Etilenin tümü polimerleştiğinden, proseste etilen geri-çevirme veya monomer geri-kazanma sistemleri bulunmaz. Hidrokarbon seyreltici, üründen santrifüjle uzaklaştırılır ve son kurutma, azotla çalışan akışkan-yataklı kurutucuda yapılır. Ayrılan seyrelticinin büyük bir kısmı prosese geri-gönderilir. Elde edilen YYPE toz ürün renklendirilerek veya doğal olarak granul şekline dönüştürülür.

HDPE petrolden yapılmış bir tür termoplastik olan borular için kullanıldığında "alketen" veya "polietilen" olarak da adlandırılır. Dünyada en çok kullanılan plastiktir. Yüksek yoğunluklu rasyonlu polimer büyük ölçüde plastik şişeler, korozyona dayanıklı borular, geomembranlar ve plastik kereste üretiminde kullanılır.
HDPE'yi ambalaj endüstrisi için ideal kılan ayırt edici özelliği; standart polietilenden daha güçlü ve neme karşı güçlü bir bariyer oluşturmasıdır. Çin merkezli olarak tüm Asya, yüksek yoğunluklu polietilen üretiminde lider bölgedir. Polimerin küresel üretim kapasitesinde %40 'lık bir paya sahiptir. Polimer üretiminde ikinci en büyük bölge %20 pay ile Kuzey Amerika'dır ve onu %17 ile Orta Doğu takip etmektedir. Orta Doğu ve Çin, yeni üretim kapasitesinin yanı sıra en hızlı büyüyen bölgelerdir. HDPE pazarının ana itici faktörü, ambalaj endüstrisindeki artan talepten kaynaklanmaktadır. Nispeten düşük maliyetli bir malzeme olduğu için ambalaj endüstrisinde tercih edilen bir malzemedir. Yerel su tesisatı yerine yaygın olarak kullanılan plastik borulara olan talebin artması, küresel pazarda bu malzeme için en önemli itici güçtür.
1953'te Kaiser Wilhelm Enstitüsü'nden Karl Ziegler ve Erhard Holzkamp 'in araştırmaları ile icat edilmiştir.
Bu malzemenin icadından iki yıl sonra, yüksek yoğunluklu polietilen borular icat edildi. Günümüzde yüksek yoğunluklu polietilen, tokluğu, esnekliği ve kimyasal direnci nedeniyle borularda en çok kullanılan malzeme haline gelmiştir.
Son yıllarda artan tarımsal faaliyetler, yüksek yoğunluklu drenaj borularının büyük ölçüde tarımsal drenaj sistemlerinde kullanılması nedeniyle yüksek yoğunluklu borulara olan talebi artırmıştır.
HDPE Temel Özellikleri:
Malzeme, günümüzün plastik pazarında çok büyük ölçekte kullanılan en dayanıklı ve çok yönlü termoplastiklerden biridir. Uygun özelliklerinden dolayı şişe, otomotiv parçaları, mobilya vb. Çok çeşitli malzemelerin üretiminde kullanılır. Polimerin sahip olduğu temel özellikler aşağıdaki gibidir:
-
Malzemeler, yüksek mukavemet / yoğunluk oranına sahiptir.
-
Görünüşe göre yarı saydam ve mumludurlar.
-
Reçineler kolaylıkla esnektir ve hava şartlarına karşı oldukça dayanıklıdır.
-
Düşük sıcaklıkta iyi tokluk kalitesine sahiptirler.
-
Kimyasallara karşı son derece dirençlidirler ve kolayca aşınmazlar
-
Yüksek yoğunluklu polietilen plastikler hafiftir, kolaylıkla temin edilebilir ve ekonomiktir.
-
Düşük nem emme özelliğine sahiptirler.
-
Malzemelerin termoplastik kaynak ekipmanı kullanılarak kaynaklanması kolaydır.
-
Çekme Dayanımı 0.20 - 0.40 N / mm² ve Çentikli Darbe Dayanımı Kırılmaz Kj / m²
-
Termal genleşme katsayısı 100-220 x 10-6
-
Max Cont Kullanım Sıcaklığı 65 ° C
-
Yoğunluk 0,944 - 0,965 g / cm 3
-
Malzemeler her türlü Seyreltik Asit ve Alkalilere karşı güçlü bir şekilde dayanıklıdır.
-
Yağ ve greslere karşı orta derecede dirençlidirler.
-
Reçineler, Alifatik Hidrokarbonlar, Aromatik Hidrokarbonlar ve Halojenlenmiş Hidrokarbonlar gibi Hidrokarbonlara karşı zayıf bir dirence sahiptir.
-
Alkollere karşı oldukça dayanıklıdırlar.
-
Halihazırda temin edilebilir ve düşük maliyetli bir malzemedir.
-
Yüksek yoğunluklu polietilen iyi darbe direnci ve gerilme mukavemeti.
-
Reçineler tüm termoplastik yöntemlerle kolayca işlenebilir.
-
Plastikler kimyasallara, korozyona ve iklim değişikliklerine karşı oldukça dayanıklıdır
-
Malzemelerden üretilen plastikler dayanıklı, esnek, güçlü ve hafiftir.
-
Yüksek ısıl genleşmeye sahiptir.
-
Kötü hava koşullarına dayanıklıdır
-
Plastikler genellikle gerilim çatlamasına maruz kalır.
-
Polimerler yanıcıdır ve belirli koşullarda zayıf sıcaklık kapasitesini gösterir.
HDPE Kullanım Sahaları:
Bu plastik, dünyanın en popüler plastiklerinden biridir. Binalardaki ağır hizmet tipi neme dayanıklı membrandan hafif, esnek torba ve filmlere kadar çok çeşitli uygulamalara uygun çok yönlü bir polimerdir. En çok şişeler ve kapaklar, taze ürün torbaları veya ince ölçülü taşıma torbaları vb. İçin kullanılır.
Dayanıklılık, geri dönüştürülebilirlik ve mükemmel buhar ve nem bariyeri gibi özellikler, onları çeşitli malların üretimi için uygulanabilir kılar. Ekstrüzyonda, enjeksiyonda, şişirme film üretiminde, boru üretiminde kullanılmak üzere farklı HDPE türevleri vardır.
HDPE Levha ve Tabakalar:
Çeşitli plastik ürünler üretmek için kullanılan tabakaların üretiminde yaygın olarak kullanılmaktadır. Levhalar güçlüdür ve düşük sürtünme katsayısı ile kimyasallara ve sıcaklığa dayanıklıdır. Son derece dayanıklı olmaları, onları su depoları, endüstriyel kullanımlar veya şişeler ve kapaklar gibi ürünler için mükemmel şekilde uygun hale getirir.
Mat levhalar; malzeme dayanıklılığı sağladığından ve bıçakları köreltmediğinden, öncelikle kesme tahtaları gibi öğeleri üretmek için kullanılır.
Düz levahalar; pürüzsüz tabakalar, onu çeşitli kullanımlar için geçerli kılan çeşitli niteliklere sahiptir. Düzgün yüksek yoğunluklu levhalar kolaylıkla imal edilebilir ve iyi kimyasal dirence, gerilme direncine sahiptir ve ayrıca yüksek oranda nem ve darbeye dayanıklıdır. Yüksek yoğunluklu polietilen düz kaplama, genellikle tank kaplaması için kullanılır. Esas olarak yakıt tankları, çöp konteynırları, paletler, tarım tankları, otoyol bariyerleri gibi büyük karmaşık ürünleri rotasyonel olarak kalıplamak için kullanılırlar. Levhalar ayrıca çeşitli torba ve şişelerin üretiminde ve ambalaj endüstrisinde yaygın olarak kullanılmaktadır.
Boru levhaları ve ekipmanları; ağırlık ve performans açısından standart yüksek yoğunluklu kaplamadan bazı gelişmiş özelliklere sahiptir, bu da onları boru üretimi için uygun hale getirir.
Boruların üretiminde büyük ölçüde yüksek yoğunluklu polietilen polimer kullanılır. Reçineler, daha dayanıklı, hafif, hava koşullarına dayanıklı ve kolay malzeme akışı sağladıkları için boru imalatında büyük miktarlarda kullanılır. Bu borular belediye, sanayi, enerji, jeotermal ve çöplükler gibi çeşitli sektörlerde kullanılmaktadır.
Yüksek yoğunluklu borular, füzyon işlemi nedeniyle sıfır sızıntıya sahiptir, monolitik yüksek yoğunluklu polietilen sistem oluşturur, sonuç olarak boru ve bağlantı parçaları için en uygun malzeme olduğunu kanıtlar. Bu borular toksik olmadıkları ve oldukça dayanıklı oldukları için daha çevre dostudur.
-
Sızdırmazlar ve mükemmel akış özellikleri sunarlar.
-
Kimyasallara, korozyona ve aşınmaya karşı oldukça dirençlidirler.
-
Borular ve bağlantı parçaları güçlü süneklik ve tokluk sunar.
-
Üreticilere geniş bir çeşitlilik sunan ½ inç ila 63 inç arası çaplarda mevcuttur.
-
Donmuş suya geleneksel metal boru sistemlerinden daha iyi dayanabilirler.
-
Oldukça dayanıklıdır ve uzun vadeli ekonomi, değer ve bağımlılık sağlar.
Antiskit; kayma veya kayma yüzeyinin gerekli olduğu denizcilik uygulamaları için özel olarak üretilmiştir.
HDPE Torbalar:
Yüksek yoğunluklu polimerler ayrıca çok büyük ölçekte poli poşet üretmek için kullanılır. Malzemenin temel özellikleri, onları çeşitli poli poşetlerin üretimi için oldukça uygun hale getirir. Bu poli çantalar, uygulama ve kullanımlarına göre üretilmektedir. Reçineler, taze poli poşetlerin, brad poşetlerin, yiyecek poşetlerinin, ince ölçülü taşıma poşetlerinin ve diğerlerinin üretiminde kullanılır.
-
HDPE çantalar yüksek ve düşük sıcaklıklara dayanıklıdır.
-
Katkısız bir malzemedir, bu nedenle poşetler ürünlerin paketlenmesi için ideal hale gelir.
-
HDPE torbalar, yine ambalaj endüstrisi için uygun olan çizilmez özellikler sunar.
-
Bu torbalar daha sert, daha güçlü ve daha iyi nem tutma kapasitelerine sahip.
-
Materyal bulanık ve donuk olduğundan üretilen poşetlere netlik sağlamaz.
-
HDPE poşetlerin çentikli olması halinde, bu poşetlerin filmin ekstrüde edildiği yönde yırtılması çok kolay hale gelir.
HDPE Örtüler:
Yüksek yoğunluklu polietilen, büyük miktarlarda bulunabilirliği ve düşük malzeme maliyeti nedeniyle küresel olarak geomembran olarak yaygın şekilde kullanılmaktadır. Kimyasallara, UV'ye ve ozona karşı dayanıklıdır, bu da onu astar üretiminde kullanılmaya uygun hale getirir. Astarlar temel olarak çöp sahalarında, atık su arıtma lagünlerinde, hayvan atık lagünlerinde ve madencilik uygulamalarında kullanılmaktadır. Bu astarlar, yaklaşık 22,5 inç genişliğe sahip büyük rulolar halinde mevcuttur.
Dayanıklı ve UV dayanımlı malzemelerdir. İyi kimyasal ve sıcaklık direncine sahiptirler.
Tüm bunlardan başka; Düzenli depolama gömlekleri, maden havuzları olarak ve hatta tüm suyla kirlenmiş cisimlerin arıtılması için kullanılabilirler. HDPE Plastikler, dayanıklılığı, esnekliği ve hafifliği nedeniyle plastik şişe ve kapaklar (su şişeleri, içecekler vb.), Oyuncaklar (açık ve kapalı oyun alanları), kimyasal kaplar (şampuan, saç kremi) gibi çeşitli son segment ürünler için geçerlidir. , temizlik ürünleri, motor yağı vb.), deniz yapımı ve mobilyaları (dolaplar, çim mobilya, kilitli dolaplar, banyo tezgahları) ve günlük yaşamda kullanılan diğer birçok ev ürünü üretiminde tercih edilmektedir.
HDPE Geri dönüşümü hakkında bilgiye buradan ulaşabilirsiniz.
Bazı HDPE marka ham maddelerin teknik değerleri ve daha çok kullanım alanları :


LLDPE / LDPE / HDPE Arasındaki Farklılıklar
Yüksek Yoğunluklu Polietilen (HDPE), Düşük Yoğunluklu Polietilen (LDPE) ve Doğrusal Düşük Yoğunluklu Polietilen (LLDPE), hepsi plastik ürünler üretmek için son segment pazarlarında kullanılan farklı bir tür polietilen polimerlerdir.
Hepsi, onları çeşitli farklı kullanımlara uygulanabilir kılan belirli özelliklere sahiptir. Bu reçineler arasındaki en büyük fark, ne kadar sıkı oluştuklarını gösteren hücresel yapıları veya birbirleriyle olan moleküler bağlarıdır.
En Esnek Olanı : LLDPE kullanılan en esnek plastik şeklidir. Daha fazla esnekliğe, gerilme mukavemetine ve uygunluğa sahip daha rafine bir LDPE formudur. Güçlü ve uygun özelliklerinden dolayı levha ve filmler için yaygın olarak kullanılmaktadır. Göletler ve kanallar için yaygın olarak kullanılır.
En Yaygın Kullanılanı : LDPE kullanılan en yaygın plastik türüdür. Tarım, inşaat, kaplar ve kapaklar, kaplama vb. Alanlarda yaygın olarak kullanılmaktadır.
En Zon İşleneni : HDPE Polietilenin en güçlü ve en dayanıklı şeklidir. Maksimum kimyasal dirence sahiptir ve nispeten diğer polietilen plastik reçineler formlarından daha az esnektir. HDPE malzemeleri , tokluk kalitelerine katkıda bulunan maksimum düzeyde UV direncine sahiptir.

EVA (Ethylene Vinyl Acetate)
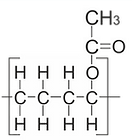
Polietilen-vinil-asetat (PEVA) olarak da bilinir. Bir etilen ve vinil asetat kopolimeridir. Bu oluşumda ağırlık yüzdesi %10 ile %40 arasında değişkendir ve geri kalan kısım etilendir.
EVA kopolimeri, esasen vinil asetat içerikleri ve malzemenin kullanılma şekli bakımından farklılık gösteren üç farklı tiptedir. Bu gözenekli elastomerik malzeme,%750 gerilme uzaması ve en yüksek erime sıcaklığı 96 °C ile düşük LDPE 'den yaklaşık üç kat daha esnektir. Bu malzeme genellikle doğası gereği toksik değildir ve LDPE'nin özelliklerini sergiler, ancak genellikle film uygulamalarında daha fazla parlaklıktadır. Termoplastik ekstrüzyon, film birleştirme ve köpük kalıplama için kullanılırlar.
Film, Köpük, Sıcak Eriyik Yapıştırıcılar, Tel kablo, Ekstrüzyon Kaplama, Güneş Pili Kapsüllemesi, Enjeksiyon Kalıplama ve Medikal Boru üretimlerinde tercih edilir.
Otomotiv, Ambalaj ve Kağıt, Boyalar, Kaplamalar ve Yapıştırıcılar, Elektronik ve Elektrik, Eczacılık, Ayakkabı, Fotovoltaik Panel, Tarım ve Tıp alanlarında yoğunlukla karşımıza çıkar.
EVA, yüksek basınçlı bir reaktörde etilen ve vinil asetat monomerin ko-polimerizasyon işlemiyle üretilen termoplastik reçinelerdir.
DuPont, dünyanın en büyük EVA üretim kapasitesine sahip şirkettir. Bunu, Hanwha Chemical ve Exxon Mobil izler.
-
Vinil Asetat Modifiye Polietilen (Düşük vinil asetat yoğunluğu)
-
Termoplastik Etilen-Vinil Asetat (Orta vinil asetat yoğunluğu)
-
Etilen Vinil Asetat Kauçuk (Yüksek vinil asetat yoğunluğu) olmak üzere üç segmenttedir.
EVA Temel Özellikleri :
EVA polimer, bazı iyileştirmelerle birlikte düşük yoğunluklu polietilen polimerlere benzer özelliklere sahiptir.
EVA reçinelerinin sergilediği temel özellikler şunlardır:
-
Malzeme iyi bir netlik ve parlaklık sağlar.
-
Gerilim çatlamasına ve UV ışınlarına karşı oldukça dayanıklıdır.
-
Düşük sıcaklık direnci.
-
Yüksek sürtünme katsayısı.
-
Kendine özgü sirke benzeri bir kokusu vardır.
-
Erime noktası - 75 ° C
-
Çekme mukavemeti, N 0.05-0.2 olan / mm 2 ve çentikli darbe dayanımı bir ara Kj / m 2
-
25 ° C'de yoğunluk 0.948 g / ml'dir
-
Parlama Noktası - 260 ° C
-
Termal genleşme katsayısı 160-200 x 10-6
-
Kararlılık - Kararlı, Yanıcı ve güçlü oksitleyici maddelerle uyumsuz.
-
Seyreltik Asitlere ve Alkalilere, Alifatik Hidrokarbonlara, Alkollere, Yağlara ve Greslere karşı çok iyi direnç gösterirler.
-
Aromatik Hidrokarbonlara ve Halojenlenmiş Hidrokarbonlara karşı zayıf dirençleri vardır.
-
Mükemmel ısıl yapışma mukavemeti gösterirler.
-
Düşük sıcaklıklarda bile iyi miktarda esnektirler.
-
Esneme ve çatlamaya dayanıklıdır.
-
Geleneksel termoplastik teknikler kullanılarak kolayca işlenebilirler.
-
Yedeklerine kıyasla zayıf gerilme mukavemeti
-
Isı deformasyonuna karşı daha düşük direnç
-
Rakiplerine göre zayıf kimyasal dirence ve bariyer özelliklerine sahiptir.
EVA Kullanım Sahaları :
Genel olarak EVA, esnek ambalajlama, ısıyla yapıştırma katmanları, termal laminasyonlar, hortum ve boru, üflemeli kalıplanmış şişeler ve kapak gömlekleri gibi bir dizi farklı son kullanım için geçerlidir.
EVA reçineleri, tabakalardan kolayca kesilebildiğinden ve istenen herhangi bir şekle kalıplanabildiğinden, karmaşık son kullanıcı ürünleri üretmek için de kullanılmaktadırlar. Ortez, sigara, sörf tahtası, yağsız tahta ve hatta yapay çiçek üretiminde kullanılabilir.
Termoplastik ağız koruyucuları ve yumuşatıcı veya su geçirmez deriler için bile kullanılırlar.
EVA Köpük:
Etilen vinil asetat bir tür kapalı hücreli köpüktür. Döşemede yaygın olarak kullanılan, yumuşak ve dayanıklı bir etilen ve vinil asetat polimeridir. Aynı zamanda spor malzemeleri, zanaat ve set tasarımı gibi başka çeşitli kullanımlara da sahiptir. EVA, süngerimsi olmadan doğası gereği yumuşak olduğu için genellikle parmak arası terlik üretiminde kullanılır.
Özellikler EVA köpük malzemelerin temel özellikleri:
-
Hava şartlarına ve kimyasallara karşı son derece dayanıklı ve esnek olmaları.
-
Düşük su emme özelliğine sahiptir olmasından dolayı dökülmelere dayanıklı olmaları.
-
Kimyasallara dayanıklı olmaları.
-
Doğaları gereği toksik özellik göstermemeleri.
EVA köpük, iyi köpük üretim özelliklerine sahiptir. EVA köpük ve tabakalarının imalatı için şu birkaç yöntem kullanılabilir:
-
Köpük Sıyırma : Köpük sıyırma, köpürtme makinesi ile üretilen ham levhalardan daha ince köpük levhalar yapma yöntemidir. Köpük sıyırma, her zaman geri kalan köpük üretim sürecinin ilk adımıdır.
-
Köpük Kesme : Bu işlem köpük tabakaları bloklar ve şeritler halinde kesmek için kullanılır. EVA köpük malzemelerini imal etmek için kullanışlı ve verimli bir tekniktir. Köpükte testere makinesi sacları istenilen uzunluk ve genişlikte kesilir. Birincisi dikey testere ve ikincisi yatay testere olmak üzere iki tür testere yöntemi kullanılmaktadır. Her iki tür testere makinelerinin son ürünleri köpük tabakalar, bloklar ve şeritlerdir.
-
Özel Kalıp Kesme : Bu kalıp kesme yöntemi, kağıt kutuyu kesmek için çelikten yapılmış kalıbın kullanıldığı kağıt ambalajlar gibi farklı endüstrilerde kullanılır. Aynı şekilde kalıp kesme yöntemi de köpük üretimi için kullanılır. Bu yöntem, genellikle paketleme, köpük kasa ekleri, köpük profilleri ve köpük conta pedleri üretiminde tercih edilir.
-
Köpük Laminasyon : EVA köpük malzemelerinin yapışkan yapışkan arkalık, keçe yüzey, kumaş ve film arkalıklarının gerekli olduğu yerlerde gereklidir. İşlemde iki tür EVA köpük laminasyon yöntemi kullanılmaktadır. İlk yöntem PAS laminasyondur (yapışkan laminasyon) ve ikinci yöntem ısıyla laminasyondur. Yapıştırıcı laminasyonunda laminasyon için yapıştırıcılar kullanılırken diğer yöntemde laminasyon işlemi için ısıtılmış köpük yüzeyden yararlanılır.
-
Köpük Termoform : Köpük ısıl şekillendirme, daha esnek ve dayanıklı köpük elde etmek için yapılır. Bu işlem öncelikle 3 boyutlu özel köpük parçaları yapmak için kullanılır. Isıyla şekillendirmenin kendisi ısıtma ve sıcaklıklarla ilgili olduğundan, bu teknik de aynı prensipler üzerinde çalışır. Termoform işleminde kullanılan makinalar, istenilen ısı ve sıcaklıklara göre ayarlanarak kalıplarda ısıtma ve basınç altında özel köpük parçalar oluşturulur.
Eva Köpük kullanmanın faydaları:
-
Çalışma kolaylığı sunarlar ve çeşitli kalınlık, renk ve yoğunluklarda gelirler.
-
Isı yardımı ile kolaylıkla şekillendirilebilir hatta diğer malzemelere yapıştırılabilir.
-
Bu köpük malzemeler kolaylıkla boyanabilir.
-
EVA köpükleri kolaylıkla taşınabilir, depolanabilir ve yeniden kurulabilir.
-
Temizlemesi kolaydır.
-
EVA köpükleri dayanıklılık, rahatlık ve kullanılabilirliğin bir kombinasyonunu sunar.
-
Bu malzemeler çok çekici ve kolayca karşılanabilir.
EVA Ayakkabı ve Taban:
EVA, kauçuğa çok benzeyen elastik bir kopolimerdir ve birçok ev ve endüstriyel uygulamada kullanılabilir. Üretim sürecinde klor kullanmayan ve geri dönüşümle yeni ürünlere (oyun alanları, paspaslar vb.) kolayca geri dönüştürülebilen çevre dostu bir malzemedir. Vegan ayakkabı üretiminde yaygın olarak kullanılmaktadır. Koşu ve günlük ayakkabıların çoğu EVA kullanılarak üretilmektedir. Ayakkabı endüstrisindeki Timberland, Teva, Keen ve Patagonia gibi birkaç zengin marka bile ayakkabı imalatında EVA kullanımını benimsemiştir.
EVA malzemesi bugün mevcut olan en iyi şok emici malzemelerden biridir. Bu nedenle, önde gelen marka jogger'ların çoğu, şok emilimi ve hafifliğin iyi bir kombinasyonunu elde etmek için bunu ayakkabı tabanlarında kullanır. EVA malzemeleri, ayakkabı parçalarının orta tabanı, spor ayakkabıların dış tabanı ve iç tabanı için ve ayrıca terlik ve parmak arası terlik tabanı olarak yaygın olarak kullanılmaktadır.
Ayakkabı üretiminde EVA kullanmanın faydaları şunlardır :
-
Ayakkabılarda yastıklama ve yaylanma sağlar.
-
Ayakkabının sertleşme ve çatlamaya karşı direncini arttırır.
-
Suyu emmez ve soğuk havalarda bile esnek kalır.
-
Ayrıca UV ışınlarına dayanıklıdır.
-
Bu malzeme suya ve korozyona karşı oldukça dayanıklıdır.
-
İşleme kolaylığı (kesme, yapıştırma, presleme ve laminasyon) sunar.
-
EVA taban canlılığı önleyicidir (iyi gerilme mukavemeti ve yüksek tokluk ile şok yastıklama)
-
Soğuk havaya karşı yalıtım sağlarlar
-
Kapalı köpük ses yalıtım kalitesi.
PEVA (PolyEthylene Vinyl Acetate)
Poli Vinil Klorür (PVC) için doğrudan bir ikame olduğunu kanıtlayan klorsuz bir vinildir. PVC günümüzde bilinen bir kanserojen türü olduğundan, mümkün olan her yerde önlenmektedir. PEVA, doğası gereği PVC'den daha az toksik göründüğünden, çeşitli ürünlerin (özellikle ev eşyaları) ikame edilmesi için kullanılmaktadır.
PEVA, duş perdeleri, oyuncaklar, ayakkabılar, kozmetik çantaları, bebek önlükleri, plastik örtüler, araba örtüleri ve yatak koruması gibi çeşitli ev ürünlerinde kullanılmaktadır.
Bazı EVA marka hammaddelerin teknik değerleri ve daha çok kullanım alanları :

PP (PolyPropylene)
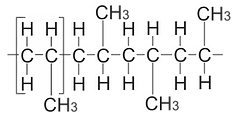
Bu plastik süt beyaz rengindedir. Çok iyi boyanma kabiliyeti vardır. Isı, kimyasal ve elektrik özellikleri ne çok iyi ne çok kötü sınırlı nisbettedir. Polipropilen (PP), birçok açıdan yüksek yoğunluklu polietilenden (HDPE) benzerdir. Tekrarlayan -CH2 bileşenlerinden oluşan uzun bir polimer zinciri oluşturmak yerine, gözenekli polipropilen molekülün, ana karbon omurgasını asan bir dizi CH3 grubu vardır.
Mukavemeti ve yumuşama sıcaklığı oldukça yüksek olup sudan hafiftir. Polietilen gibi kokusu daha keskin ve yakıcıdır. PE ye benzeyen özelliğe sahiptir. Asbest lifleri ile kuvvetlendirilmiş halde taşıtların hava filtrelerinde, gaz kullanılır, ayrıca ambalaj paketleme ve çuval işlerinde kullanılır.
Polipropilen, stereoregüler polimerler arasında ilk üretilen polimerdir. Üretimi 1957'de başlamıştır ve hızla artarak kısa zamanda büyük miktarlara ulaşmıştır.
Polipropen olarak da adlandırılan polipropilen (PP), doğası gereği termoplastiktir. (CnH2n) olarak ifade edilen doğrusal bir hidrokarbon polimeridir. PP polimer en çok yönlü polimerlerden biridir ve hem plastik hem de elyaf olarak kullanılır.
Polimer, mekanik olarak sağlam olması ve bazlar ve asitler gibi birçok kimyasal çözücüye dirençli olması gibi sert özelliklere sahiptir. Bu, polipropilen plastiği çeşitli son kullanım endüstrileri için ideal hale getirir . PP plastiğin ana uygulama alanı paketleme ve etiketleme, tekstiller, plastik parçalar ve çeşitli tiplerdeki yeniden kullanılabilir kaplardır.
PP plastik aynı zamanda ev eşyalarının, otomotiv ürünlerinin, denizcilik ve karavan ürünlerinin kalıplanması için imalatçılar tarafından da tercih edilmektedir. PP plastikleri gıda kabı olarak kullanmak da güvenlidir çünkü kimyasalların gıda ürünlerine sızmasını önler.
Polimer, Enjeksiyon Kalıplama, Şişirme Kalıplama, levha ekstrüzyonu ve ısıyla şekillendirme gibi farklı işleme teknolojilerinde kullanılabilir.
PP reçine propilenden yapılır ve propilen, petrokimya endüstrisinde en çok üretilen ikinci yapı taşıdır .
PP, propilenin kontrol edilen ısı ve basınç altında organometalik ve stereospesifik katalizörlerle (Ziegler-Natta) polimerizasyonuyla elde edilir. Uygulanan polimerizasyon prosesine ve kullanılan kataliz ör sistemine bağlı olarak üretilen polimerin moleküler yapısı üç farklı tipte stereokimyasal konfigürasyon g österir; bunlar izotaktik, sindiyotaktik ve ataktik konfigürasyonlardır. Kullanım alanı en yaygın ticari polimer olan izotaktik polipropilende metilen gruplarının tümü, polimer iskeletinin aynı tarafında bulunur; dolayısıyla kristal oluşumuna olanak veren bir yapı meydana gelir.
Daha sonra geliştirilen kataliz ör teknolojileri izotaktik olmayan yapıların oluşumunu en aza indirecek y öndedir; b öylece izotaktik dışındaki (sindiyotaktik ve ataktik) fraksiyonların, elde edilen üründen ayrılması için gerekli bazı üretim kademelerinin kaldırılması hedeflenmektedir.
Birçok kimyasala karşı üstün dayanım özellikleri gösterir. Yüksek mekanik ve gerilme dayanımı gösterir. Yapısal özelliği gereği kaynak edilebilir. Elektriksel dayanım özellikleri çok iyidir. Düşük yoğunluklu oluşu onu ekonomik yapar. Homopolimer (PP-H) ve Kopolimer (PP-C) olmak üzere iki tipten oluşur.
Çalışma sıcaklıkları PP-H için 0 ile 100°C, PP-C için -30 ile 90 °C 'dir. Temel özellikleri olarak, yüksek kimyasal dayanım, iyi darbe dayanımı, iyi mekanik özellikler ve düşük yoğunluk gösterilebilir.
Homopolimer ve rasgele kopolimer üretiminde gaz propilen, ko-monomer ve katalizör reaktöre konulur. Reaktörde, büyüyen polimer taneciklerinin oluşturduğu akışkan bir yatak vardır; 35 kg/cm² basınç ve 70 °C dolayında çalışır. Reaksiyon yatağına akan reaksiyon gazı, tek-kademeli bir santrifüj kompresörüyle sirküle ettirilir; böylece, polimerizasyon reaksiyonu için gerekli ham madde sağlanırken, yataktan reaksiyon ısısı da uzaklaştırılır. Sirkülasyon gazı bir ısı değiştiriciden geçirilerek soğutulur. Granüler ürün, aralıklarla, ürün deşarj tanklarına akar. Burada reaksiyona girmemiş gaz, üründen ayrılır ve reaktöre geri-döndürülür. Darbe-dirençli kopolimer üretiminde, birinci reaktörde elde edilen polipropilen reçine, ikinci (darbe-direnci) reaktöre alınır. Polimerik kauçuk fazın elde edilmesi için, bu reaktöre gaz propilen ve etilen gönderilir. İkinci reaktörün çalışması birinciye benzer; fakat basıncı yarısı kadardır. Bir santrifüj kompresörü gazı ısı değiştiriciden geçirerek akışkan-yataklı reaktöre geri-çevirir.
Darbe dirençli kopolimer ürün, deşarj tanklarına
gelir ve reaksiyona girmemiş gaz tekrar reaktöre döner.
Her iki üretimde de kalan hidrokarbonlar azot ile süpürülür.
Granüler ürün, uygun peroksitler ilave edilerek, düşük-enerjili bir sistemde pellet şekline dönüştürülür. Erime akışı 0.1 den 3000 e, izotaktik içeriği %99 a kadar ulaşan homopolimerler elde edilebilir. Rasgele kopolimerlerde etilen %12 ye kadar çıkarılabilir, erime akışı 0.1 den 100 e kadar geniş bir aralıkta değiştirilebilir. Dardan genişe molekül ağırlığı dağılımları elde etmek mümkündür.
Kullanım alanları arasında kimyasal tanklar, vana ve pompa parçaları, her türlü kablo izolasyonları ve makaronlar, trafo, röle, anten, transformatör, radar parçaları, bağlantı parçaları, bobin, jeneratör izolasyonları, yüksek gerilim izolatörleri, kapasitör ve transformatörler için hava geçirmez keçeler, , baskı devreleri için lamine levha üretimleri vardır.
PP Prosesindeki Katalizörler:
TiCl3 Bazlı Katalizörler: İzotaktik polipropilen (düzenli sterik yapı), ilk defa Natta tarafından 1954 yılında, TiCl4 ve Al(C2H5)3'den oluşan aktifleyici bir sistemle elde edilmiştir; sistemdeki TiCl4'ün, polimerizasyon sırasında Al(C2H5)3 ile indirgenerek katı, kristalin TiCl3'e dönüşmesiyle, meydana gelen polimerin yüksek yüzdelerde izotaktik yapı içermesi sağlanmıştır. Daha sonra Hecules molekül ağırlığının düzenlenmesinde hidrojenin rolünü keşfetmiş, Esso saf TiCl3 yerine TiCl3 katı çözeltisinde AlCl3 kullanarak daha iyi sonuçlar almıştır. Mitsubishi, TiCl3'e karboksilik asit esteri gibi elektron verici ilave ederek izotaktikliği %92-94'e kadar çıkarabilmişti; bu sisteme ikinci jenerasyon kataliz örü denilmektedir. Yine de kataliz ör verimi, kataliz ör kalıntısını azaltarak kalıntının ayrılması işleminin kaldırıldığı bir üretim için yetersiz bulunmaktadır.
MgCl2 Destekli Katalizörler:
MgCl2 kataliz ör verimini yükseltir, kataliz ör kalıntısını ayırma işlemine gerek olmaz, dolayısıyla hidrokarbon slurry (çamur) içinde polimerizasyonu kolaylaştırır. Bu buluş ve daha başka düzeltmelerle üçüncü jenerasyon katalizörleri geliştirilmiştir. Böylece polimerizasyon ortamının monomer olduğu basitleştirilmiş proseslerde daha yüksek verim, stereospesifiklik ve morfoloji kontrolü sağlanabilir.
Metallosen Katalizörler:
Ziegler-Natta katalizörleri yerine tek-uçlu metallosen kataliz örleri geliştirilmiştir. Elde edilen polimerde dar molekül ağırlığı dağılımı, düzgün polimer zincirleri, şeffaflık ve sıklık gibi özellikler, bu sınıfa giren katalizörlerin başlıca karakteristikleridir.
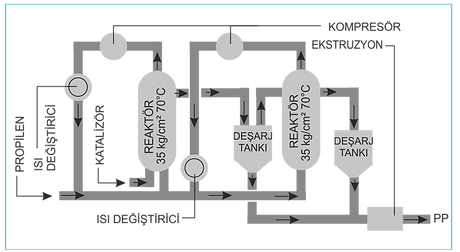
PP üretiminde şu adımlar temeldir:
-
Öncelikle hammadde malzemesi ve katkı maddeleri saflaştırılmalıdır. Katalizör malzemesi hazırlanmalıdır. Kullanılan besleme stoğu propilendir.
-
Daha sonra polimerizasyon ya akışkan yataklı / karıştırmalı reaktörlü gaz fazında ya da bulamaç / çözelti ile sıvı fazda gerçekleşir.
-
Bundan sonra, polimer parçacıkları mevcut monomerlerden ve seyrelticilerden ayrılır. Monomer ve seyrelticiler geri kazanılır ve işlem sırasında tekrar beslenir.
Çin, PP polimerin lider üreticisidir. Küresel toplam üretimdeki payı %27 'dir.
2017 yılı itibaren Dünya pazarındaki en büyük PP üreticisi firmaları aşağıda görülebilir. (milyon ton/yıl)

PP Temel Özellikleri :
PP, sert ve çok sağlam plastiktir. Bu polimerin özellikleri, monomerin moleküler ağırlığına ve dağılımına bağlıdır. PP reçinesi, ısıya dayanıklılığı iyi olduğundan gerilim çatlaması problemleriyle karşılaşmaz. Yarı saydam olmaları, iyi yorulma direncine sahip olmaları ve yarı sert olmalarının yanı sıra sağlam olmaları gibi kullanım alanlarını genişleten başka fiziksel özellikler de sunar. Mükemmel estetik özelliklere sahiptirler, bu nedenle tampon gibi parçalarda parlaklık ve parlaklığın gerekli olduğu otomotiv sektörlerinde pek çok yerde kullanılırlar.
PP reçine aside, bazlara, suya veya deterjanlara dayanıklıdır. PP plastikler, asit ve bazlara dayanıklı olduğu için kaplar için iyi bir seçim olabilir. Düşük yoğunluğa, yüksek yumuşama noktasına sahiptirler ve daha yüksek sertlik ve sertlik sunarlar. Oda sıcaklığında organik çözücülere dayanıklıdır.
0.895 g / cc arasında polipropilen yoğunluk kalıntıları 3 amorf ve 0.92 g / cc için 3 kristalindir. Ancak bu yoğunluk dolgularla değişebilir. Etilen ile kopolimerize edildiğinde sert ve esnektir. Makul ölçüde ekonomiktir ve yorgunluğa karşı iyi bir dirence sahiptir.
PP plastiklerin özellikleri nedeniyle termoplastik kaynak ekipmanı kullanılarak kaynaklanması kolaydır. Bu, kimyasal , su ve diğer sıvı malzemeler için depolama tankları imal etmesine yol açar . Polipropilen erime noktası 160 °C'dir.
Üç tip PP sınıfı mevcuttur. Bir uygulama için hangi sınıfın seçileceği aşağıdaki noktalara bağlıdır:
-
Homopolimer: Bu sınıf genel sınıf olarak kabul edilir ve çeşitli genel amaçlar için kullanılabilir. Yüksek distorsiyon sıcaklığına (HDT) sahip kopolimerden daha güçlü ve serttir. Yarı saydam beyaz ve diğer renklerde bulunan dayanıklı, sert plastiklerdir.
-
Blok Kopolimer: Homopolimerden daha sert ve dayanıklıdır. Bileşimleri, artırılmış darbe direncine sahip% 5 ila% 15 etilen içerir.
-
Rastgele Kopolimer: Rastgele kopolimer kimyasal bileşimi,% 1 ve% etilen içerir. Daha iyi esnekliğe sahipler; daha düşük erime noktaları ve yapıları, pp molekül zinciri boyunca rastgele düzenlenmiş ko-monomer birimlerinden oluşur.
-
PP malzeme kolayca elde edilebilir ve ucuzdur.
-
Yarı kristal yapıları, yüksek eğilme mukavemeti sunar.
-
Farklı bazlara ve asitlere karşı iyi kimyasal dirence sahiptir ve ayrıca nemi emmeye karşı çok dayanıklıdır.
-
Çeşitli ürünlerin imalatı için gerekli olan iyi bir yorulma direnci ile birlikte iyi bir elektrik yalıtkanıdır.
-
Yorulmaya karşı güçlü direnç ile iyi darbe direncine sahiptirler
-
Polimer ayrıca sert ve ısıya dayanıklıdır
-
İşleme sırasında mükemmel estetik özelliklerle pürüzsüz olma eğilimindedirler
-
Mikrodalga gıda kapları için büyük ölçüde kullanılmasını sağlayan yüksek bir erime noktasına sahiptirler.
-
Yüksek termal genleşme katsayısı, PP malzemenin yüksek sıcaklık uygulamalarını sınırlar.
-
PP son derece yanıcıdır ve zayıf yapışma özelliklerine sahip olduğu için boyanması zordur.
-
Oksidasyona ve UV bozulmasına eğilimlidirler.
-
PP polimerin, üretim proseslerinde PP kullanımını etkileyen klorlu çözücülere ve aromatiklere karşı direnci zayıftır.
-
Hem plastik hem de elyaf olarak kullanılabilir.
-
Polimer polietilenden daha yüksek erime noktası
-
Ve polietilenden daha az kararlıdır
-
PE'ye göre daha iyi yorulma direncine sahiptir ve menteşe olarak kullanılır.
-
PE daha az statik yüke sahiptir, bu nedenle PP'den daha az toz çeker.
PP Kullanım Sahası :
PP polimer, ekstrüzyon şişirme, enjeksiyon kalıplama ve genel amaçlı ekstrüzyonla işlenebilir. Genişletilmiş PP (EPP), uzman bir işlemle kalıplanabilir. Polimerin özellikleri, onları plastik pazarının çeşitli son kullanım segmentlerine uygulanabilir kılar.
PP Kalıplama :
Plastikleri sert çerçeveler ve kalıplar kullanarak şekillendirmek için kullanılan bir tekniktir. Kalıplama genellikle araba parçalarının, konteynırların, tabelaların ve diğer yüksek hacimli öğelerin imalatında kullanılır. Plastik kalıplama, sıvı polimerin şeklini alabilmesi için içi boş kalıba doldurulmasını içerir. Bu süreç, yüksek bir basınç aralığı ve muazzam ısı içerir. Plastik kalıplamada Enjeksiyon kalıplama, üflemeli kalıplama, rotasyonel kalıplama ve sıkıştırmalı kalıplama dahil olmak üzere kullanılan farklı teknikler vardır.
Polimerin işlenmesi için eriyik akış hızı önemli bir belirleyicidir. Erime Akış Hızı (MFR) veya Eriyik Akış İndeksi (MFI), PP'nin moleküler ağırlığını tanımlar. Kalıplama işlemi sırasında erimiş polimerin ne kadar kolay akacağının bir göstergesidir. Erime akış hızı yüksektir. Yüksek MFR ile kalıbın dolumu kolaylıkla yapılır.
PP kalıplamada yaygın olarak kullanılan iki teknik, PP Enjeksiyon Kalıplama ve PP Şişirme Kalıplama'dır.
-
Enjeksiyon kalıplama : parçaları üretmek için malzemelerin kalıplara enjekte edildiği bir işlemdir. Plastik enjeksiyon kalıplamada PP polimer kullanımı, olumlu özellikleri nedeniyle artmaktadır. PP enjeksiyon kalıplama, iyi kimyasal ve nem direnci, kalıplamada esneklik ve ekonomik olması gibi temel özellikleri nedeniyle farklı segmentler için mal üretmek için çeşitli endüstrilerde kullanılır. PP reçinesi orta akış hızına sahip olduğunda, tıbbi ürünler, inşaat ürünleri, tüketici ürünleri (kaplar, spor malzemeleri, oyuncaklar vb.) Ve donanımda geniş bir ürün yelpazesi kullanılır.
-
PP Şişirme tekniği : büyük miktarlarda içi boş plastik nesnelerin üretimi için kullanılır. Öncelikle Plastik şişirme tekniği, plastik şişeler, kavanozlar ve kaplar (hem dar hem de geniş ağızlı kaplar) üretiminde kullanılır. PP Şişirme tekniği, büyük kaplar, plastik şişeler vb. İçin yaygın olarak kullanılmaktadır. PP malzeme, iyi nem bariyeri, kimyasal direnç ve yüksek sıcaklıklarda stabilite gibi üretim sürecinde kolaylık sağlayan özelliklerinden dolayı şişirme tekniğinde kullanılmaktadır. 200 ° F) Üflemeli kalıplama işleminde, PP reçinenin tercih edilen özellikleri, yüksek moleküler ağırlık ve düşük akış dereceleridir. PP Şişirme Tekniği, gıda kapları, plastik şişeler, süt kapları, Buz sandıkları gibi PP malzemeden oluşan çeşitli ürünlerde ve büyük ölçekli PP Şişirme kalıplama, kanal işleri, su depoları, yakıt depoları, geri dönüşüm kutuları ve taşma şişeleri.
PPH (PolyPropyene Homopolymer) :
Polipropilen, diğer termoplastiklerde bulunmayan mükemmel fiziksel, mekanik, termal ve elektriksel özelliklerin bir kombinasyonunu sunan ekonomik bir malzemedir. Düşük veya yüksek yoğunluklu polietilen ile karşılaştırıldığında, daha düşük darbe direncine sahiptir ancak çalışma sıcaklığı ve çekme mukavemeti daha yüksektir.
Polipropilen homopolimer (PPH) en yaygın olarak kullanılanıdır. Yüksek mukavemet / ağırlık oranına sahiptir ve kopolimerden daha serttir. Bu, iyi derecede kimyasal direnç ve kaynaklanabilirlik ile birleştiğinde birçok korozyona dirençli yapılarda kullanıldığı anlamına gelir. Ortopedi ve protez cihazları, depolama tankları, İşleme ve kimyasal depolama araçları, tıbbi cihazlar, muhtelif kapak, çift eksenli yönlendirilmiş polipropilen (BOPP) film üretiminde tercih dilir.
-
Yüksek mukavemet / ağırlık oranı vardır
-
Mükemmel kimyasal direnç gösterir
-
Isıl şekillendirme ve aşındırıcı ortamlarda yüksek performans sergiler
-
Nemi emme özelliği yoktur
-
Çoğu asit, yağ çözücü ve organik çözücülere dayanıklıdır.
-
İyi derecede sızdırmazlık özelliği gösterir
-
Toksik değildir
-
Leke yapmaz
-
Yüksek mukavemet değerlerine sahiptir.
-
Parlak kalıplı parçalarda yüksek parlaklık özelliği taşır
-
Gıda İşleme kurallarına uyumludur.
PPC (PolyPropyene Copolymer) :
Polipropilen kopolimer (PPC) biraz daha yumuşaktır, ancak daha iyi darbe direncine sahiptir. Ayrıca polipropilen homopolimerden (PPH) daha güçlü ve daha dayanıklıdır. Diğer özelliklerin performansında hafif düşüklükler olmasına rağmen, gerilme çatlaması ve sıcaklıkta daha düşük mukavemet açısından homopolimerden daha iyi bir dirence sahip olma eğilimindedir. Şişe, kapak, bardak, dereceli silindir tüp, boru, ısıl şekillendirilmiş levha üretimleri uygulama alanlarıdır.
PPC-R (PolyPropyene Copolymer Random) :
PPC’den farklı olarak Random PPC, polipropilen molekülü boyunca düzensiz veya rastgele şekillerde düzenlenmiş komonomer ünitelerine sahiptir. Genel olarak, PPC’den daha az darbe direncine sahip olmakla birlikte, daha eğilebilir ve daha şeffaf bir ürünün istendiği uygulamalar için seçilir.
Bazı PP marka hammaddelerin teknik değerleri ve daha çok kullanım alanları :

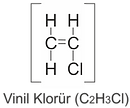
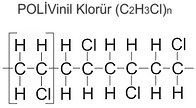
PVC (PolyVinyl Chloride)
Poli(vinil klorür) elli yılı aşkın bir zamandan beri ticari boyutlarda üretilmekte olan bir polimerdir ve pek çok türü vardır. Plastifiyanlar, stabilizörler ve diğer katkı maddeleriyle kolaylıkla karışabilme (blending) özelliğinden dolayı PVC diğer plastiklerden çok daha yaygın kullanım alanına sahiptir.
PVC hammaddesi, % 57 oranında klor (bildiğimiz deniz suyunun elektroliz yoluyla klor, kostik soda ve hidrojen bileşenlerine ayrılması işlemi ile elde edilir) ve % 43 oranında elde edilir. Bu özelliğiyle, PVC hammaddesi, gerek üretim maliyetinin düşüklüğü ve gerekse üretiminde petrol kaynaklarının Polipropilen hammaddelerinde % 97 etilen kullanılmaktadır. Yani PVC dünya petrol rezervlerini daha az kullanmamıza imkan vermekte ve bu nedenle fiyatı diğer hammaddelere göre petrole daha az bağımlılık göstermektedir. Bu şekilde üretilen PVC hammaddesi, kendisinden istenen elastikiyet, yumuşaklık, sertlik, esneklik vb. gibi özellikler kazandırılmak için kimyasal maddeler ilave edilir. Örneğin, eğer PVC hammaddesinden plastik boru yapılacaksa, kırılmamasını sağlamak için esneklik ve yumuşaklık veren kimyasal maddeler katılır. Yumuşatıcılar, polimer zincirleri arasında bağlar oluşturarak sürtünme kuvvetlerini azaltır ve bu zincirlerin kopmasına engel olarak hammaddenin daha esnek bir yapıya kavuşmasına sebep olur. İşte yumuşatıcı (stabilizatör) katılmamış olan (plastikleştirilmemiş) hammaddeye U-PVC adı verilir
Başta kuvvetli asitler olmak üzere birçok kimyasallara dayanıklı olması,bu tür uygulamalarda tercih edilen bir malzeme haline gelmesini sağlamıştır. Yapısal özelliği gereği kaynak edilebilir ve yapıştırılabilir malzemeler arasındadır. Grubu içindeki malzemelere kıyasla 60°C gibi sıcaklık dayanımının düşük olması ve yoğunluğunun yüksek olması dezavantaj oluşturmaktadır. Alevlenmeme özelliği vardır, yani aleve maruz bırakılıp çekildiğinde tutuşmazlar. Elektriksel ark dayanımı iyidir. Daha yüksek sıcaklık ve kimyasal dayanım gerektiren durumlarda özel bir türü olan CPVC kullanılmalıdır. Çalışma Sıcaklıkları -15 ile 60°C arasındadır. Kullanım alanları başında kimyasal tanklar, elektriksel ekipman üretimi, su arıtım tesis havuzları, pompa ve vana gövdeleri, borular gelir.
Vinil klorür monomerden(VCM), iki-kademeli kütle polimerizasyonuyla polivinilklorürün(PVC) üretildiği bir prosestir.
Poli(vinil klorür)ün ticari üretiminde beş tip polimerizasyon prosesi kullanılır:
süspansiyon, emülsiyon, kütle, mikro süspansiyon ve çözelti polimerizasyonu. Bunlardan en çok uygulananları süspansiyon, emülsiyon ve kütle prosesleridir.
Süspansiyon Polimerizasyonu:
Vinil klorürden poli(vinil klorür) elde edilmesinde en çok kullanılan teknik süspansiyon polimerizasyonudur. Polimerizasyon, vinil klorür damlacıklarının şiddetle karıştırılarak bir süspansiyon ortamında dağıtılmasını gerektirdiğinden yığın prosesi uygulanır. Halen üretilmekte olan PVC miktarının %80 kadarı bu teknikle elde edilir.
Emülsiyon Polimerizasyonu:
Bu proseste monomer, suda çözünen bir başlatıcı ve emülsiyon yapıcı bir maddenin de bulunduğu sulu bir ortamda polimerleştirilir.
Kütle (veya Bulk) Polimerizasyonu:
Kütle polimerizasyonunda monomer kütlesinde izlenen polimerizasyon mekanizması, süspansiyon polimerizasyonundaki her bir monomer damlacığının içinde oluşan reaksiyonla aynıdır; aradaki fark, kütle prosesinde süspansiyon yapıcı bir ortamın bulunmamasıdır.
Mikro Süspansiyon Polimerizasyonu:
Kullanılan başlatıcının monomerde çözünür özellikte olduğu bir emülsiyon polimerizasyon tipidir. Polimerizasyon reaksiyonu çok küçük damlacıklar içinde gerçekleşir; polimerizasyon ilerledikçe damlacıkların içine kaba emülsiyondan monomer geçişi olur.
PVC Prosesindeki Katalizörler:
Poli(vinil klorür) üretiminde kullanılan katalizörler, elde edilecek ürünün türüne ve uygulanan polimerizasyon sistemine g öre çeşitlidir. Burada vinil klorürün süspansiyon polimerizasyonu katalizörlerinden bahsedilecektir.
Ticari amaçla kullanılan serbest radikal başlatıcılar, çoğunlukla monomerde çözünen tipte olanlardır; organik peroksitler (R O = O R'), organik peresterler, peroksidi-karbonatlar ve alifatik azo bileşikleri (R N = N R'). Bu bileşiklerin hepsi ısıl parçalanmayla serbest radikaller verirler. PVC polimerizasyonunda kullanılan bazı önemli başlatıcılar arasında di-sek-bütil peroksidikarbonat ve 2,4-dimetil valeronitril sayılabilir. Bu başlatıcılar vinil klorür monomerinde çözünürler. Prosesin kolay kontrol edilebilmesi için düzenli ve doğrusal bir polimerizasyon hızına gereksinim olduğundan başlatıcı seçimi önemlidir.
Daha yaygın olarak PVC olarak kısaltılan ve bu isimle bilinen polivinil klorür piyasada kullanılan üçüncü en büyük termoplastik polimerdir. Kimya endüstrisinin en değerli ürünlerinden biri olan PVC oyuncak yapımından inşaat sektöründeki yapı malzemelerine kadar birçok alanda kullanılır. PVC çok sert ve tok bir malzemedir ve bu mekanik özellikleri sayesinde geniş bir kullanım alanı vardır. Fakat kimyasallara dayanıklılığı az olan bir malzemedir.
Su boruları,cam çerçeveleri,tel ve kablo izolasyonu olarak,su şişesi olarak kullanılır. PVC’nin darbe daynımını arttırmak için ise kauçuk plastikler PVC’yle karıştırılır. PVC genel olarak vinil adıyla anılmasına rağmen, vinil ailesine üye diğer polimerler de vardır. (Polivinil asetat, Polivinildin klorür, Polivinil alkol vs.) PVC de polietilenin modifikasyonudur. Polistirendenki yapıya benzer, benzen grupları yerine klorür iyonları vardır.
Polietilenden sonra en çok kullanılan plastik türü olup oldukça ucuzdur. Mukavemeti yüksek kimyasal etkilere ve aşınmaya karşı dayanıklıdır. Sert ve yumuşak olmak üzere iki türü vardır. Sert olanlardan basınçlı su boruları, pis su boruları, çatı yağmur dereleri ve iniş boruları sulama ve yağmurlama boruları, plastik doğrama çatı kaplama levhaları üretilmektedir. Yumuşak olanları ise yapılarda yer karosu olarak kullanılır. Alevle yanmaya karşı dirençli olup beraberinde zehirli gaz yayarlar. Son yıllarda kapı ve pencere yapımında da sıkça kullanılmaktadır. 80ºC de yumuşadığı için PVC borular sıcak su tesisatında kullanılmazlar.
PVC’den mamul boruların üretim maliyetini düşürmek için dolgu maddesi olarak kalsit maddesi kullanılır. Kalsit maddesi, doğada çok fazla miktarda bulunan ve kimyasal formülü CaCO3 olan Kalsiyum Karbonat (Kireç taşı)’dır. Kalsit, bildiğimiz mermerin ince pudra haline getirilmiş şeklidir. PVC borularda kalsit maddesinin %9’dan fazla kullanılması borunun kırılgan ve dayanıksız olmasına sebep olur. Ayrıca kullanılan kalsit maddesinin sağlık sertifikasının olması gerekir.
(Ayrıca Bakınız: Dolgu Maddeleri-Kalsit)
Yaygın olarak PVC kısaltmasıyla kullanılan polivinil klorür, seri olarak üretilen en önemli ve en eski polimerlerden biridir. Bütün dünyadaki PVC tüketimini yanlızca (PE) ve polipropilen (PP) aşmaktadır. PVC ilk kez on dokuzuncu yüzyılın ortasında üretilmiştir. Bununla birlikte bir endüstriyel üretim sürecine ilk kez 1913 yılında patent verilmiştir. Günümüzde bazı sanayi uygulamaları PVC olmadan gerçekleştirilemez. Ancak, pvc aynı zamanda günlük ürünlerin kullanımında da vazgeçilmez hale gelmiştir.
PVC, ağırlık olarak yaklaşık % 56 klorür içeren bir polimerdir. PVC reçinesi yalnızca katkı maddeleri kullanarak işlenebilen ve kullanılabilen bir malzeme haline gelmektedir. Katkı maddelerinin seçimi özelliklerinde geniş bir değişiklik ve planlanan uygulamada değişiklik sağlamaktadır.
PVC malzemelerin iki sınıfı vardır.
Plastikleştiriciler (Örneğin fitalat gibi) ilave ederek üretilen yumuşak PVC (PVC-P) .
Plastikleştirilmemiş sert olanlar PVC (PVC-U) (Daha çok PVC boru üretiminde)
PVC-U
Amorf termoplastiktir. PVC-U kalıplı parçalar formülün bileşimine son derece bağlıdır, ancak aynı zamanda işleme de bağlıdır. PVC-U malzemesi aşağıdaki belirtilen özelliklere sahiptir:
• Çok yönlü kullanma özelliğine sahiptir.
• Kimyasal ve korozyona dayanıklılığı çok iyidir.
• Fizyolojik olarak zararlı olmadığını kanıtlanmıştır ve gıda maddelerine temas etmeye uygundur.
• İçme suyunun kalitesi üzerinde hiçbir etkisi yoktur.
• Biyolojik olarak inörtür ve mikrobiyal büyümeyi desteklemez.
• Mekanik çekme mukavemeti ve darbeye karşı dayanıklılığı yüksektir.
• Kendiliğinden söner.
• Tangit çimentosunu kullanarak güvenli şekllde çözücü çimentolama yapar.
• Düzgün yüzeyleri sayesinde sürtünme kaybı düşüktür.
PVC-U, hava koşullarına karşı çok dayanıklıdır. Rüzgar ve yağmurun etkisinin yanı sıra doğrudan gelen güneş ışınlarının uzun süreli etkisi de malzemeye yanlızca yüzeysel olarak zarar verebilir.
PVC-U malzemesinin kızılötesi radyasyonla ilgili olarak hava koşullarına karşı dayanıklılığı çok iyi olmasına rağmen, darbeye karşı dayanıklılığının bir bölümünü kaybeder. Olağan dışı uygulamalarda, malzemeyi doğrudan doğruya güneş ışınlarına maruz kalmaktan korumak avantajlı olabilir.
Malzemenin uygulama limitleri kırılganlaşma ve yumuşama sıcaklıklarına, uygulamanın niteliğine ve beklenen hizmet ömrüne bağlıdır.
PVC-U malzemesinin yüksek klor içeriği avantajlı bir yanma davranışına neden olur. Sıcaklık etkilerinden kaynaklanan kendiliğinden tutuşma yalnızca 450°C sıcaklığında meydana gelir.
PVC-U malzemesi bir açık ateşe maruz kaldığında yanar, ancak ateş kaldırıldıktan hemen sonra söner. Oksijen indeksi %42 oranındadır (%21’den daha az oksijenle yanan maddeler yanıcı madde olarak değerlendirilir). Dolayısıyla, PVC-U malzemesi UL94 standardına göre en iyi tutuşabilirlik sınıfı olan VO sınıfına tekabül eder ve DIN 4102-1 sayılı standarda göre 3,2 mm’den daha az duvar kalınlıklarında B1 yapı malzeme sınıfına (zor tutuşur), 3,2 mm’den daha büyük duvar kalınlıklarında B2 yapı malzeme sınıfına (normalde yanıcı) tekabül eder.
PVC-U, bütün değiştirilmemiş termoplastikler gibi iletken değildir. Bu da PVC-U sistemlerinde elektrokimyasal korozyon meydana gelmemesi anlamına gelir. Diğer taraftan, borularda elektrostatik yük oluşabileceğinden dolayı, bu iletken olmama özellikleri hesaba katılmalıdır. Bu durumu patlayıcı gazların görülebileceği yerlerde hesaba katmak özellikle önemlidir.
PVC-U maddesinin nötr, asitli ve alkollü yiyecekler bakımından fizyolojik olarak zararlı olmaması ve içme suyu üzerinde koku, tat veya mikrobiyolojik etkiler bakımından etkili olmaması çeşitli ülkelerdeki tarafsız kuruluşlar tarafından düzenli olarak kontrol edilir ve denetlenir.
PVC-UH
PVC doğal halinde güçlü, yarı-sert bir maddedir. PVC-UH yüksek darbe mukavemetli plastikleştirilmemiş polivinil klorür olarak açıklanabilir.Bu özellik TS 274-3 EN 1452-3 de ekleme parçası malzemesinin MRS değeri 20°C 50 yıllık süre sonunda 25MPadan büyük değil ise PVC-U şeklinde; 25MPadan büyük ise PVC-UH şeklinde işaretlenmelidir. (TS EN 1452-3 Madde 4.3) Bu ibare yalnızca Ek parçalarda kullanılabilir. TS EN ISO 1452-1 Standardına göre PVC mamüller ve formülasyonlar, gerekli en küçük gerilme seviyesine göre (MRS) gösterilmelidir.
(MRS) Değeri: ISO 12162'ye göre (LPL) değeri üzerinde hesaplanır. LPL değeri ISO 9080'e uygun olarak yapılan analizle belirlenir. Burada ISO 1167-1 ve ISO 1167-2'ye göre, su için su deneyi uygulayarak hidrostotik basınç deneyleri yapılır.
Bu deneylerle PVC malzemenin 20 ˚C - 50 yıllık süre sonunda en küçük yüzey gerilme kuvveti (MRS - Minimum reqvest strenght) hesaplamış MRS değeri (25 Mpa)'dan büyük değil ise hammadde PVC-U,
(25Mpa)'dan büyük ise PVC-UH olarak değerlendirilir.
Yüzey mukavemet değeri (MRS), anlaşıldığı gibi, PVC mamuller ve formülasyonuna özel katkı malzemeleri ilavesi ile yükseltilmektedir. Bu formülasyonlar ticari sırdır ve uluslararası akreditasyonlar olan labaratuarlar tarafından onaylanmıştır.
TSE ve KİWA gibi standartlara göre firmalar bu onay olmadan ekleme parçaları üzerinde PVC-UH işaretlemesini kabul etmemektedir. Yukarıdaki açıklamadan anlaşılacağı üzere PVC-UH'nin (MRS) değer PVC-U'dan daha fazladır.
Bu da daha kuvvetli mukavemetli olan mamul formülasyona sahip olduğunu gösterir.
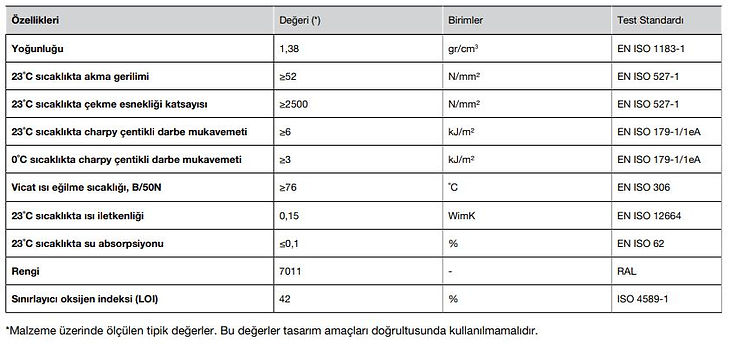
PVC-U 'nun uzun süreli davranış özellikleri :
Hesaplama (EN ISO 15493:2003 sayılı standarda göre)
Aşağıdaki şemada PVC-U malzemesinin uzun süreli davranışı gösterilmektedir.
20°C–60°C arasındaki sıcaklık değerleri için, kırılma çizgileri gösterilir. Bunlar LPL eğrileri (Alt Öngörülebilir Limit) olarak gösterilmektedir. Bu da tanıma göre bütün kırılma noktalarının %97,5’inin eğrilerde veya eğrilerin üzerinde olduğu anlamına gelir.
Tipik olarak PVC-U gibi amorf termoplastikler için hidrostatik mukavemet şemasında hiç dirsek gösterilmemektedir.
Eğriler bir çift logaritmik ölçekte (lineer değil) çizilir. Gerilim veya zaman değerlerini okuduğunuz zaman, lütfen bu durumu hesaba katın.
PVC-U malzemesinden yapılan borular ve bağlantı elemanları için gösterdiğimiz basınç/sıcaklık şeması dahil edilen tasarım faktörü ve 25 yıllık ömürle hidrostatik mukavemet şemasından elde edilir. Hidrostatik mukavemet şeması ekstrapolasyon yöntemiyle EN ISO 9080 standardına göre belirlenmiştir. Aşağıdaki denklemle (4 parametreli model) gerilim, sıcaklık veya zaman 10°C–60°C arasındaki sıcaklık değerlerinde hesaplanabilir.


PVC ne kadar sağlıklı :
1950’li yıllardan beri günlük hayatımıza en fazla girmiş olan PVC ürünlerinin kansere sebep olduğunun belirtildiği tek bir rapor bile yoktur. Çünkü, PVC hammaddesinde sağlık problemine sebep olabilecek tek nokta, tam polimerizasyon işlemi yapılamaması sonucunda insan sağlığını tehdit edecek miktarda reaksiyona girmemiş Vinil Klorür monomerlerinin hammadde içinde kalması olabilir.
Ancak,günümüzde tamamen tam kontrol altında kapali reaktörler içinde yapılan polimerizasyon teknolojisi sayesinde, polimerizasyon işlemi boyunca hammadde içinde reaksiyona girmemiş bir şekilde duran vinil klorür monomerinin miktarı devamlı olarak izlenebilmekte ve vinil klorür monomerinin hammadde içindeki oranı 1 PPM miktarına(milyonda bir) düşene kadar polimerizasyon işlemine devam edilmektedir.
Dünya Sağlık Örgütü’ne akredite laboratuarların gıda maddeleri saklanması ve nakli için onayladığı plastik malzemelerin en başında PVC den mamül ürünler gelmektedir.
Tip alanında kullanılan ameliyat malzemeleri vs gibi ürünlerin saklandığı bütün kap ve tip malzemeleri PVCden yapilmaktadır.
PVC hammaddesinin hastalık yayma konusundaki temiz sicilinin altında yatan gerçek, PVC maddesinin içme suyu ve diğer sivil ara karşı nötr olması yani etkileşime girmemesidir. Bu nedenle PVC hammaddesi suya hiçbir partikül bırakmaz. Ayrıca, klor maddesinin mikrop öldürücü olarak su dezenfeksiyonunda kullanıldığı bilinir.
PVC hammaddesinin üretilmesinden sonra hammaddenin sağlamlığını artırmak için eklenen stabilizatörler içinde kullanımı sağlığa zararlı sayılan ağır metaller türünden maddeler olan Kadmiyum(Cd) ve Kurşun(Pb) maddelerinin stabilizatör olarak kullanımı yasaklanmış ve artık günümüzde hiç kullanılmamaktadır.
Bu ağır metaller yerine artık bugün bütün dünyada stabilizatör olarak Baryum (Ba),Çinko(Zn), Kalsiyum(Ca) ve Kalay(Sn) maddeleri kullanılmaktadır.
PVC 'nin çevre sicili :
PVC Hammaddesi, gerek üretimi için diğer plastik hammaddelerine nazaran çok daha az petrol kullanılması ve gerekse üretimi için diğerlerine nazaran çok daha az enerji gerektirmesi nedeniyle bütün sentetik plastik malzemeler içinde en çevre dostu malzemedir. Çünkü, PVC nin erime noktası diğer hammaddeler içinde en düşüktür.
PVC yi işlemek için diğer plastik malzemelere hem çok daha az enerji ve hem de daha az işlem süresi gerekir. Bu da nihai ürünün maliyetinin PVC’de çok düşük olmasına yol açar.
PVC boruların ömürlerine etki edenler :
Boru hattı projelerinde öngörülen basınç dayanımı ve hizmet ömrünü sağlayabilmeleri için, PVC boruların ilgili standartlarda öngörülen et kalınlığında imal edilmesi ve kesinlikle üretim esnasında % 9'dan fazla kalsit kullanılmaması gerekir. Aksi taktirde, proje tesliminde borular basınç testini geçseler bile, ilerleyen zamanda boruların hizmet ömürleri düşecektir.
Boru hattının kalitesini etkileyen en önemli faktör, birleştirme kalitesidir. Çünkü, bir boru hattı % 70 oranında ek yerlerinden kaçırır. Bunun önüne geçmek için, birleştirilecek iki parçanın çap farkının 0.4 mm'den daha fazla olmaması gerekir. Aksi taktirde, iki parça birbirine bol geçecek ve yapıştırıcı veya O-Ring contası bu boşluğu iyi kapatamayacak ve sonuçta bu noktada zaman içinde sızıntı oluşacaktır. Her firmanın kendi üretim toleransı olduğundan, değişik firmaların ürettiği iki ürünün birleştirilmesi durumunda yapıştırıcının kapatamayacağı kadar bir açıklığın oluşması muhtemeldir. Bu nedenle, mümkün olduğu kadar boru ve ek parçalarının aynı üretici firmadan temin edilmesi uygun olacaktır.
Her çeşit plastik borunun kendine has artıları ve eksileri vardır. En uygun boru tipi, arazinin yapısı, trafik yükü, iklim şartları, istenilen basınç dayanımı ve ortam sıcaklık derecesi gibi faktörler göz önüne alınarak karar verilir. Çünkü, bir boru ne kadar kaliteli üretilirse üretilsin, eğer o proje ve arazi için uygun bir boru tipi değilse sonuç mutlaka olumsuz olacaktır.
PVC boruların alev ile imtihanı :
PVC hammaddesinin yangını üst katlara taşıdığı, yangın sırasında tuz ruhu ve dioksin salgıladığı ve bu nedenle tehlikeli olduğu şeklinde çok yanlış bir inanış vardır. Her yangın çeşidinde yangınla birlikte oluşan gazlar yanan malzemenin cinsine göre toksin emisyonu yaparlar. İnsanlar, bir yangın sırasında tamamen yanmayan ürünlerin ortaya çıkardığı Karbon Monoksitten(CO) zehirlenirler. Karbon monoksit, kokusuz ve çok zehirli bir madde olduğu için insanlar daha karbonmonoksitin varlığını fark edemeden zehirlenmiş olurlar. Ancak PVC hammaddesi erime noktası çok düşük olduğu için hemen tamamen yanar ve PVC'nin yanmasından HCL (Tuz ruhu) açığa çıkar. Yani yangın sırasında insanların zehirlenmesine yol açan Karbon Monoksit gazı PVC hammaddesinin yanmasından oluşmaz. PVC'nin yanması sırasında ortaya çıkan tuz ruhu, aslında zehirleyici bir maddedir. Ancak çok keskin bir kokusu olduğu için 5 PPM gibi çok çok az miktarda bile ortamda bulunmasını insanlar algılarlar ve hemen ortamdan uzaklaşarak zehirlenmekten kurtulurlar.
Bu özelliğiyle PVC hammaddesinin yanması esnasında oluşan bu tuz ruhu aslinda bir yangının haber olarak insanları uyarır.
Bilindiği üzere, teneffüs ettiğimiz havanın içinde %21 oranında serbest oksijen vardır. % 21 den daha az oksijen bulunan ortamda yanabilen maddeler ‘YANICI’ maddeler sınıfına girmektedirler.
Odunun kendiliğinden tutma sıcaklığı 280 °C iken PVC hammaddesinin kendiliğinden tutuşabilmesi için ortam sıcaklığının 450 °C olması gerekir.
PVC hammaddesi, UL 94 yanici maddeler sınıflandırmasına göre CLASS V0 olarak en az tutuşma özelliğine sahip plastik hammaddesi olarak belirlenmiştir.
Aynı şekilde, DIN 4102 Standardi inşaat malzemelerini yanıcılık özelliklerine göre A (Yanıcı olmayan) ve B (Yanıcı) olarak 2 gruba ayırmıştır. Bu standart, Polipropilen ve Polietilen malzemelerini B2 sınıfında (normal yanıcı) olarak gösterirken, PVC'yi B1 (alev söndürücü Flame Retardant) olarak göstermektedir.
Odun yandığı zaman PVC malzemeden üç misli daha fazla ısı yayar.
Bütün plastikten mamül malzemeler gibi, eğer PVC malzemeyi açık aleve tutarsanız PVC malzeme de yanar. Ancak alevi çekerseniz yanma hemen duracaktır. Bunun nedeni, PVC yandığında Hidroklorür (TUZ RUHU) gazı ortaya çıkar ve yanma bölgesinde oksijen miktarını azaltarak hemen durdurur.
PVC hammaddesi içinde en fazla miktarda bulunan Klor maddesi yanmayan bir maddedir.
PVC hammaddesi eğer açık aleve doğrudan tutulmazsa kesinlikle yanmaz. Bu nedenle, Pvc borular, evlerde meydana gelen yangının üst katlara yayılmasında hiçbir katkı yapmaz.
PVC boru ömürleri :
PVC den mamul boru ve ek parçaları kimyasallara ve ağır kullanım ve depolama şartlarına karşı çok iyi direnç gösterirler. Aynı şekilde, kötü hava şartlarında, direkt güneş ışığı altında, yağmur ve rüzgar altında uzun süre durmaktan etkilenmez.
Çünkü, PVC hammaddesinin kimyasal yapısı amorf yapıdır. Yani PVC hammaddesi birbiri içine girmiş bağlardan oluşmuştur.
PVC kristal yapıya sahip değildir. Yani Polietilen ve Polipropilen gibi kırılgan değildir. Ancak %80 oranında kristal yapıya sahiptir.
Kristal yapı ne kadar çok olursa, ürün güneşe karşı dayanımını yitirir ve kırılganlaşır.
Çünkü, Güneş ışığı altında kaldığında Polietilen ve Polipropile gibi hammaddeler içinde moleküller birbirine paralel bağlar ile bağlanır.
PVC hammaddesinde ise moleküller birbirine düzensiz ve birbiri içine girmiş(amorf) bir şekilde bağlanmışlardır ve kristal yapıya sahip değildirler. Bu nedenle PVC baglarını kırmak Polietilen’e göre daha zordur.
Bu nedenle PVC hammaddesinden yapılan boru ve ek parçaları aynı şartlarda Polietilen ve Polipropilen borulara gore çok daha fazla dayanım ömrüne sahiptirler.
Eğer Polietilen ve Polipropilenden mamul boruları güneş ışıgı altında uzun süre bekletirseniz, kristalleşme devam eder ve boru üzerinde boydan boya yarılmalar oluşur. Bu kristal yapıdan ötürü meydana gelir.
Bu nedenle Polietilen hammaddesi içine güneş ışığı altında kristalleşmeyi önlemek için Karbon siyahı denilen maddeden %2.5 oranında koymak gerekir. Karbon siyahı konulmayan hammaddeden imal edilen polietilen hammaddesinden boru yapılırsa bu borular güneş ışığı altında boydan boya yarılacaktır. Aynı şartlarda PVC borulara hiçbir şey olmaz
Sıcaklık arttıkça, PVC Boruların basınç dayanımı azalır.
PVC borular 20°C da 25 yıl 16 bar basınca dayanırken, sıcaklık 40°C’a çıktığında 10 bar basınca dayanabilmektedirler.
Polietilen borular MRS 10MPa ve Polipropilen borular MRS 8MPa değerine sahipken PVC borular MRS 25MPa değerine sahiptir.
Yani aynı çap ve et kalınlığında ve aynı kullanım sıcaklığında PVC borular Polietilen ve Polipropilen borulardan çok daha yüksek basınca dayanırlar.
ABS (Acrylonitrile Butadiene Styrene)

Acrylonitrile
Butadiene

Styrene
Düşük sıcaklıklarda dahi güçlü ve dayanıklı olan yapısı sayesinde ısı ve kimyasallara karşı iyi direnç gösterir ve işlenmesi kolaydır. Yüksek darbelere dayanıklıdır. Darbe sonu kırılması sünektir. Yüksek ısıya ve aleve dayanıklıdır. Uzun süre güneş etkisinde kalırsa rengi, darbe mukavemeti, sünekliliği azalır. Üçlü kopolimer olup mukavemeti ve tokluğu yüksektir. Dış ve kimyasal etkilere dayanıklıdır. Çekme mukavemeti 42- 50Mpa, özgül ağırlığı 1,05-1,07 Mg/m³ tür,elastisite modülü yoktur ve 75°C ye kadar olan ısılara dayanırlar. Boru, oto parçaları, elektronik aygıt kabinleri ve buz dolabı parçaları üretiminde kullanılırlar.
ABS plastik, polibütadien varlığında stiren ve akrilonitrilin polimerizasyon işlemiyle oluşan bir terpolimerdir. Genellikle bileşim, yarım miktarda stiren içerir ve geri kalan denge akrilonitril ve bütadien arasında bölünür.
ABS Plastik, 1940'tan beri mevcut olan yaygın bir termoplastik formudur ve günümüzde en popüler mühendislik polimeri haline gelmiştir. Akrilonitril, Bütadien ve Stirenin bir kopolimeridir ve genellikle orta kuvvete sahiptir.
Üç farklı monomerden oluşan bir terpolimerdir. Sert, rijit ve kimyasal direnci iyidir.
Akrilonitril Bütadien Stiren oluşumunda yer alan üç monomer, malzemenin performansında farklı bir rol oynar, çünkü akrilonitril polimere kimyasal ve termal stabilite sağlar, bütadien dayanıklılığını ve gücünü arttırır ve stiren son olarak güzel ve parlak bir son verir.
Güçlü kimyasal direnç ve stabilite ile birlikte sert ve rijit olması nedeniyle, stirenik polimer ailesinin en iyisi olarak kabul edilir.
Ev aletleri (buzdolabı, çamaşır makinesi vb.), Bavul, kamera gövdeleri, alet kutuları, pil kutuları, paketleme kasaları, radyo, çeşitli mobilya parçaları gibi çeşitli son segment tüketici ürünlerinde uygulanabilir.
Erime noktası yüksek, güçlü ve sağlam bir malzemedir. Bu Polimer, sahip olduğu nitelikler temelinde birincil müşterilerinin özel gereksinimlerini karşılamak için üretilmiştir. ABS malzemenin temel üç monomerinin (Akrilonitril Bütadien Stiren) oranı değiştirilerek yoğunluğu kullanıma göre değiştirilebilir farklı türevleri elde edilebilir.
Bu malzemenin sahip olduğu temel özellikler aşağıdaki gibidir:
-
Kimyasallara ve farklı plastikleştiricilere karşı mükemmel direnç.
-
Orta güç sunarlar ve kullanımlarına göre sert, sert veya sert olabilirler.
-
Akrilonitril bütadien stiren malzemeler, sertliğin yanı sıra yüksek çekme ve darbe dayanımına sahiptir.
-
Bu reçineler, yüksek ve düşük sıcaklıklarda bile mükemmel performans gösterir.
-
Boyutsal kararlılık ve olağanüstü şekillendirilebilirlik sağlarlar.
-
Akrilonitril bütadien stiren polimerleri elektropla edilebilirdir ve sürünme direnci sunar
-
Yüksek sünekliğe sahiptirler.
-
Düşük maliyetle kolaylıkla temin edilebilir.
-
Çekme dayanımı 46 MPA (6600 PSI) ve çentikli darbe dayanımı 10 - 20 Kj / m2
-
Termal genleşme katsayısı 70 - 90 * 10-6
-
Maksimum Devam 80 - 95 ° C sıcaklık kullanın
-
Yoğunluk 1.0 - 1.05g / cm3
-
Cam geçiş 105 ° C (221 ° F)
-
ABS reçineleri, Seyreltik Asitlere ve Seyreltik Alkalilere karşı mükemmel direnç sunar.
-
Yağ ve greslere karşı direnci çok iyidir.
-
ABS polimerleri, Alifatik Hidrokarbonlara orta düzeyde direnç sunar
-
Aromatik Hidrokarbonlara, Halojenlenmiş Hidrokarbonlara ve Alkollere karşı zayıf dirençlidirler.
-
Tok ve rijit bir malzeme olmasının yanında yüksek darbe dayanımının olması,
-
İyi elektriksel özelliklere sahip olması,
-
Kimyasal direncinin iyi olması,
-
Kolay işlenebilmesi,
-
Üretiminin kolay olması ve boyanabilme özelliğinin olması,
-
Hafif bir malzeme olmasıdır.
Akrilonitril bütadien stiren, genellikle akrilonitril, bütadien ve stirenden emülsiyon işlemi yoluyla polimerize edilir. Akrilonitril, propilen ve amonyaktan üretilen sentetik bir monomerdir; butadien, buharla parçalanan stiren monomerinin C4 fraksiyonundan elde edilen bir petrol hidrokarbonudur, etilen ve benzenin reaksiyonunda elde edilen bir hidrokarbon olan etil benzenin dehidrojenasyonu ile yapılır. Sürekli kütle polimerizasyonu olarak bilinen patentli bir işlemle de oluşturulabilir.
Akrilonitril monomerlerinin nitril grubunun birbirleriyle bir tür polar çekim geliştirdiği ve polimerin tokluğuna katkıda bulunmaya yardımcı olduğu akrilonitril bütadien stireni türetmek için küresel olarak emülsiyon işlemi seçilmiştir.
Aynı zamanda polibütadienin varlığı, genel bir kauçuk sertleştirme işlemi yoluyla plastik ürüne fiziksel güç sağlar. Araya serpiştirilmiş çok sayıda kauçuksu polibütadien partikülü nedeniyle, malzeme daha fazla mekanik enerjiyi emebilir ve kırılmadan plastik olarak deforme olabilir.
Termoplastik olduğu için, farklı sıcaklık koşullarında kolayca işlenebileceği anlamına gelir. Isıtılabildiğinde, soğumaya bırakılır ve daha sonra herhangi bir bozulma olmaksızın diğer plastik şekillerini oluşturmak için yeniden ısıtılabilir.
Plastiklerin farklı sıcaklıklarda işlenmesi, temel özelliklerini geliştirir. Akrilonitril bütadien stirenin yüksek sıcaklıklarda işlenmesi, ürüne daha iyi bir görünüm ve bitiş sağlar. Aynı zamanda malzemenin ısı ve kimyasal direnç kabiliyetini de arttırır.
Bu polimer, termoplastik bir malzemedir ve kolayca geri dönüştürülebilir ve yeni plastik ürünler oluşturmak için yeniden işlenmemiş malzemelerle kullanılabilir.
Kullanılan ve yaygın olarak üretilen türevleri şunlardır:
-
Yüksek Parlaklıklı Akrilonitril Bütadien Stiren,
-
Düşük Parlaklıklı Akrilonitril Bütadien Stiren,
-
Yüksek Etkili Akrilonitril Bütadien Stiren,
-
Genel Amaçlı Akrilonitril Bütadien Stiren,
-
Yüksek Akışlı Akrilonitril Bütadien Stiren
-
Plakalı Akrilonitril Butadien'dir.
Çin, ABS plastik reçinelerin hem üretiminde hem de tüketiminde en baskın ülkelerden biridir. Küresel toplam pazar payının %40 'ı Çin'e aittir. Küresel üretime katkıda bulunan diğer büyük bölgeler arasında Avrupa %10, Kuzey Amerika %8, Güney Amerika %1 ve Orta Doğu ve Afrika %1 'lik paya sahiptir.
Pazardaki önde gelen lider şirketler : Chi Mei, LG Chemicals, Styron, Kumho Petrochemical, INEOS Styrolution, Asahi Kasei, Sabic, China Petroleum and Chemical, Formosa plastic, Elix Polymers, BASF, Toray, Ampa, Rochling, Dow Chemicals, PolyOne.
ABS Dezavantajları :
Akrilonitril bütadien stiren, onu iyi bir termoplastik yapan pek çok özelliğe sahip olmasına rağmen, bu malzemenin plastik olarak lehine olmayan birkaç özelliği vardır. Yüksek sıcaklıkta yangına maruz kaldığında kolayca yanıcıdır.
Akrilonitril bütadien stirenin yanması, karbon monoksit ve hidrojen siyanür gibi çok tehlikeli bazı toksik ürünlerin üretilmesine neden olur. Aynı zamanda kötü hava koşullarına sahiptir ve çözücüye karşı direnci zayıftır.
-
Düşük çözücü direncinin olması,
-
Uzama katsayısının düşük olması,
-
Sürekli servis sıcaklığının düşük olmasıdır.
ABS Kullanım Sahaları :
ABS, en yaygın kullanılan plastiklerden biridir ve elektronik, donanım, mutfak aletleri, oyuncaklar gibi günlük temel öğelerde ve diğer birçok son kullanım ürününde görülebilir. Bu malzemelerin enjeksiyon kalıplanacak nitelikleri, müzik aletleri, tıbbi cihazlar, otomotiv parçaları ve spor malzemeleri gibi karmaşık ve hassas şekillerde ürünlerin üretimine yardımcı olur. Çeşitli segmentlerde çok çeşitli ürünlerin üretimi için uygundur.
Hem standart reçineler hem de mühendislik reçineleri için gerekli özellikleri makul bir fiyata karşılama kabiliyetine sahip, yaygın olarak kullanılan bir termoplastiktir. ABS'yi termoplastik olarak seçmenin temel avantajı, polibütadienin sertliği ile birlikte akrilonitril ve stiren polimerlerin mukavemet ve sertliğinin bir kombinasyonu olmasıdır. Mükemmel bir kimyasala dayanıklıdır ve her türlü alkali ve asidik ajandan kimyasal bozulmayı güçlü bir şekilde önler. Güçlü kimyasal bağlar oluşturma doğaları, plastiğe, çok yüksek sıcaklıklarda bile plastiğin bozulmasını önleyen bir dereceye kadar termal stabilite sağlar.
Akrilonitril bütadien stiren, belirli bir erime noktası olmayan bir tür amorf katıdır. ABS'nin bu özelliği, onu bir dizi ürünü üretmek için enjeksiyon kalıplama işlemi için uygun bir malzeme haline getirir. Akrilonitril bütadien stiren malzemenin estetik görünümü, plastiğin daha parlak görünmesini sağlaması ve boyanması kolay olduğu için avantajlı olduğunu kanıtlamakla birlikte çeşitli ürün imalat seçenekleri de sunmaktadır.
ABS Filament :
Akrilonitril bütadien stiren, kolaylıkla ince filamentler halinde ekstrüde edilebilir ve ayrıca 3D yazıcılar için bir malzeme olarak da kullanılır. Daha dayanıklı olması ve daha yüksek sıcaklıklarda bile dayanma kabiliyetine sahip olması nedeniyle 3D baskı için en çok tercih edilen malzemedir.
Bu polimere, güçlü, kolay ekonomik olması ve baskı sonrası parçaların modifiye edilmesine yardımcı olabilmesi gibi baskıya son derece uygun özellikleri nedeniyle 3D baskıda daha fazla önem verilmektedir. Sert ve sağlam ayrıca ısıya güçlü bir şekilde dayanıklı olması, 3D baskı sürecinde tercih nedenidir. Bu ABS malzemenin bu işlemde kullanılması, son ürüne güzel ve pürüzsüz bir son kat sağlar. ABS, öncelikle profesyoneller, hobiler ve eğitimciler tarafından 3B yazdırma için kullanılır. Maketler, konsept modeller ve figürler, her türlü gadget vb. Yazdırmak için kullanılan 3D filament için ideal bir seçim olmuştur.
ABS Borular :
Plastik borular hem gelişmiş hem de gelişmekte olan ülkelerde büyük ölçüde kullanılmaktadır. Büyüyen altyapı faaliyetleri, dünya çapında plastik borulara olan talebi hızlandırmıştır. Plastik borular ucuzdur, hafiftir ve aşınmaz.
Sıcak suyu sıcak tutabilir ve metal borular gibi soğuk sudan yoğuşmazlar. Plastik boru genellikle yaygın olarak kullanılan iki plastik malzemeden oluşur: akrilonitril bütadien stiren (ABS) ve polivinil klorür (PVC).
ABS borular, montajı daha kolay ve daha ucuz olduğundan, düzgün akış sağladığından, hafif olduğundan, paslanmadığından veya kolayca aşınmadığından, mekanik hasarlara karşı dirençli olduğundan, sıcaklık değişimlerini kolayca sürdürebildiğinden ve hatta dayanabildiğinden inşaat ve altyapı geliştirme faaliyetlerinde yaygın olarak kullanılmaktadır.
ABS Plastik Boru Sistemlerinin Özellikleri
-
Metal boru sistemlerine göre montajı daha kolaydır ve daha ucuzdur.
-
Akrilonitril bütadien stiren borular, pürüzsüz iç kaplama sayesinde mükemmel akış sağlar.
-
Mekanik veya kimyasal hasara karşı dayanıklıdırlar.
-
Hafiftirler ve paslanmaz veya aşınmazlar.
-
Garip sıcaklıklarda bile iyi performans gösterebilir.
ABS Levha, Tabaka :
Akrilonitril bütadien stiren malzemesi de plastik levha imalatında yaygın olarak kullanılmaktadır. Bu levhalar, son segment plastik pazarı için çeşitli ürünler üretmek için kullanılır. ABS, üretim için kalıba göre kolayca ısıyla şekillendirilebilir.
Bu malzeme, olağanüstü şekillendirilebilirlik, yüksek gerilme mukavemeti ve sertliği, kolay süneklik sunduğu ve aynı zamanda birçok kimyasala ve plastikleştiriciye dirençli olduğu için levha üretiminde kullanılır.
Bu tabakalar ayrıca uçak iç döşemesi, kaset tutucular, plastikten yapılmış kutular ve tepsiler, otomotiv parçaları, elektronikler ve bagaj vb. Ürünlerin üretiminde de kullanılabilir. Akrilonitril bütadien stiren plastik kaplama iki türden oluşur; Siyah plastik kaplama ve Beyaz plastik kaplama. Siyah plastik kaplama, beyaz ABS levhalar günlük yaşamda kullanılan otomotiv, elektronik ve diğer son segment plastik ürünler için yaygın olarak kullanıldığından, siyah plastik kaplama temel olarak bahçelerde, mobilyalarda ve döşemelerde kullanıldığından, uygulamalarına daha iyi uyacak şekilde yapılmıştır. ABS levha ve tabakaların özellikleri şunlardır;
-
Bu tabakalar mükemmel kimyasal ve gerilme çatlağı direnci sunar.
-
Akrilonitril bütadien stiren, ürünlere pürüzsüz ve parlak bir son kat sağlar.
-
Siyah levhalar UV ışınlarına dayanıklıdır, beyaz levhalar ise değildir.
-
ABS plastik levhalar, kullanıcılarının talebine göre iyi darbe dayanımı, şekillendirilebilirlik, sertlik ve tokluğa sahiptir.
-
Yüksek çekme ve darbe dayanımına sahiptirler.
-
Yüksek ve düşük sıcaklıklarda mükemmel performans.
-
Yüksek Süneklik.
-
Dielektrik kaynağa kolayca ödünç verir.
-
Kimyasallara ve plastikleştiricilere dayanıklı
-
Olağanüstü şekillendirilebilirlik.
MABS (Methyl-methacrylate Acrylonitrile Butadiene Styrene) :
MABS, ABS’ye göre daha homojen bir polimerizasyona, daha iyi eriyik işlenebilirliğine, daha açık bir renge ve ultraviyole ışığa karşı daha fazla kararlılığa sahiptir. Ayrıca MABS daha düşük ısı bozulma sıcaklığına sahiptir. Tıbbi kaplar ve bileşenler. Fotokopi makineleri ve yazıcılar için parça ve bileşenler daha çok uygulama alanlarıdır.
-
Mükemmel şeffaflıktadır
-
Yüksek darbe dayanımı vardır
-
İyi derecede kimyasal direnç gösterir
-
Enjeksiyon kalıplama, üflemeli kalıplama ve ekstrüzyon işlemleri için kullanılır
-
Boya ve baskı için tercihi yüksektir

PS (PolyStyrene)
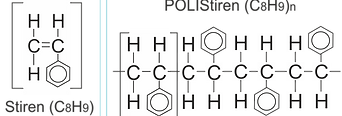
Başlangıçta, Berlin'in bir eczacı olan Eduard Simon tarafından keşfedildi. Türkiye'de tatlı sakız ağacı Liquidambar'ın reçinesi storakstan stirol adı verilen yağlı bir maddeyi damıttı. Birkaç günlük keşiften sonra Simon, monomerden üretilen stirolün oksidasyon nedeniyle kalınlaşarak "Styroloxyd" adını verdiği bir jel formuna dönüştüğünü buldu.
1845'te kimyager John Blyth ve başka bir Alman kimyager August Wilhelm Von Hofmann, oksijen yokluğunda stirolün aynı dönüşümünü temsil etti. Bu madde "metastirol" olarak adlandırıldı. Daha sonra analiz, üretilen her iki maddenin de kimyasal özelliklerinin aynı olduğunu gösterdi.
Daha sonra 1866'da Marcelin Berthelot, polimerizasyon süreciyle stirolden metatirol / yemek oluşumunu haklı olarak analiz etti.
80 yıllık zaman boşluğunun ardından, Alman organik kimyager “Hermann Staudinger (1881-1965)” in tezine dayanarak, stirolün ısıtılmasının, PS plastikler olarak adlandırılan birkaç makromolekül üreten bir zincirleme reaksiyona yol açtığı keşfedildi.
Bu plastik amorf bir yapıdadır. Parlak ve berrak bir görüntüsü vardır. Genişleyen polistiren adı verilen bir cinsi vardı ki enerji sönümlemede çok elverişlidir. Yiyecek ve içeceklere karşı çok dayanıklıdır. Düğme,ışık düğmeleri, şişe, bardak, CD ve DVD kapakları ve paketleme malzemesi olarak çok
kullanılır. Polistiren köpük üretmek de mümkündür. Çok geniş kullanım alanına sahip olan polistiren ucuz ve sert bir termoplastik polimerdir. Hatta polietilenden sonra en çok kullanılan plastiktir diyebiliriz. Aromatik bir polimer zincirine sahip olan polistiren, aromatik stiren monomerinden sentezlenir. Stiren monomeri ise petrokimya endüstrisince üretilen sıvı bir hidrokarbon molekülüdür. Gündelik hayatımızda en çok karşımıza çıkan plastiklerdendir. Polietilenin bir modifikasyonudur. Polietilen zincirinin içine benzen halkası ihtiva etmiş şekildedir.
Cam berraklığında, kolay renklendirile bilen, parlak sert yüzeyli, katı ve gevrek olan, tatsız ve kokusuz, çok iyi elektrik özelliğine sahip, kaynak edilebilen, gevrek olmakla birlikte kolay işlenir ve ucuzdur. Kolay alev alır alevin dışında da parlak bir şekilde yanmaya devam eder. Kuvvetli iş yapar tatlı bir kokusu vardır. Elektronikte kullanılan yapı elemanları için iyi izolasyon folyesidir. Köpüklü (styropor) ısı ve ses izolasyonunda kullanılır, şekilli köpüklendirilmiş PS paketlemede, kalıp model dökümünde ve çelik beton yapılarda, oyuncak, mutfak eşyalarında kullanılır.
Monomer stirenden yapılmış sentetik bir polimerdir. PS, çeşitli plastik ürünler üretmek için kullanılan bir tür yapı taşı malzemesi olan stirenin polimerizasyonu ile yapılır. Aynı zamanda doğal olarak da oluşur (çilek, tarçın, kahve ve bira).
Bu plastik polimer, hem katı hem de sert köpük malzemede mevcut olan doğal şeffaf bir termoplastiktir. Genel olarak kullanılan PS malzemesi berrak, sert ve özellikleri bakımından kırılgandır. Çeşitli son segment ürünleri üretmek için yaygın olarak plastik kullanılır. Katı plastik formu, berraklık gerektiren ürünleri üretmek için yaygın olarak kullanılmaktadır. Bunlar genellikle renklendiriciler, katkı maddeleri ve diğer plastik formlarının bir kombinasyonu ile elektronik cihazlar, otomobil parçaları, bahçe tencere, ekipman vb. Gibi ürünler üretmek için kullanılır.
PS, köpük malzemeden yapılmıştır ve yalıtım ve tamponlama özellikleriyle bilinen Genişletilmiş Polistiren (EPS) veya Ekstrüde Polistiren (XPS) olarak adlandırılır. Bu malzemenin katı formu, tıbbi cihaz uygulamaları, duman dedektörleri, CD'ler, yiyecek kapları, kahve fincanları gibi günlük öğeler için yaygın olarak kullanılır. Polimerin köpük formu da yaygın olarak çeşitli ürünler için ambalaj malzemesi olarak tercih edilmektedir.
Diğer plastik polimerler gibi polimerizasyon süreci ile üretilir . Bu polimer, stiren monomerleri polimerizasyon sırasında birbirleriyle bağlandığında ortaya çıkar. Bu süreçte vinil grubunun karbon bağı bozulur ve yeni bir karbon bağı oluşturur, ayrıca zincirdeki başka bir stiren monomerinin karbonuna bağlanır. Yeni oluşan bağ, bir öncekinden çok daha güçlüdür, bu nedenle polimeri de-polimerize etmek zorlaşır. Öncelikle iki farklı biçimde üretilir:
-
Ataktik PS : Ticari olarak üretilen önemli bir PS formudur. Ataktik PS fenil grupları üretmek için polimer zincirinin her iki tarafına rastgele dağıtılır. Bu rastgele konumlandırma, zincirlerin hizalanmasını önler ve istenen kristalliği elde etmek için yeterli miktarda düzenlilik sağlar. Bu plastik polimer, 90 °C'lik bir cam geçiş sıcaklığına sahiptir ve polimerizasyon süreci, serbest radikaller tarafından güçlü bir şekilde başlatılır.
-
Sindiyotaktik PS : üretmek için “Ziegler-Natta polimerizasyon” işlemi kullanılır. Bu polimerizasyon sürecinde, fenil grupları hidrokarbon omurgasının alternatif taraflarına yerleştirilir. Bu, 270 °C'lik bir geçiş sıcaklığı ile üretilen oldukça kristalli bir PS polimer formudur. Bu PS türleri şu anda, polimerizasyon reaksiyonu için metalosen katalizörü kullanılarak Idemitsu Corporation tarafından XAREC markası altında üretilmektedir.
Genel olarak polimer üretiminde dört polimerizasyon işlemi ve üç köpürtme yöntemi devreye alınır. Başlangıçta kullanılan üç işlem Kütle Süspansiyon, Emülsiyon ve Çözelti Polimerizasyonudur.
İkincisi, EPS'nin kapalı kalıp köpürmesi, EPS ekstrüzyonu ve GPPS'nin doğrudan enjeksiyon ekstrüzyonudur.
Benzenden, alkilasyon reaksiyonuyla etilbenzen ve etilbenzenden de dehidrojenasyonla stirenin elde edildiği bir prosestir. Benzen ve etilen, geri-dönen etilbenzenin de bulunduğu bir reaktörde, heterojen bir katalizörle reaksiyona sokulur. Reaktör çıkışı, bir ön-fraksiyonlama kolonunda reaksiyona girmemiş benzenden ayrılır ve dipten, ham etilbenzen distilasyon sistemine geçer. Tepeden çıkan benzen reaktöre döner. Distilasyon ünitesinde ham etilbenzen karışımındaki benzen, etilbenzen ve ağırlar birbirinden ayrılır. Ağırlar tekrar distillenerek, çeklen polietilbenzen reaktöre döndürülür. Elde edilen etilbenzenin saflığı, polimerizasyon-saflıkla stiren üretimine uygun seviyededir. Stiren üretimi bölümünde, taze etilbenzen, geri-dönen etilbenzen ve aşırı-ısınmış buhar, katalizör içinde bulunan dehidrojenasyon reaktörüne alınır. Verimi kontrol eden etkili değişkenler, reaksiyon basıncı ve sıcaklıktır.
Stiren monomerinin elde edildiği bölümde üç kolon bulunur. Dehidrojenasyon reaktöründe krakingle oluşan az miktardaki benzen ve toluen birinci kolonda uzaklaştırılır ve etilbenzen sistemine döndürülür. İkinci kolonda stirenden, reaktöre beslenen etilbenzen ayrılır; burada yüksek-verimli bir kolon kullanılır. Bitirme kolonu adı verilen üçüncü kolonda stiren monomeri, işlemler sırasında meydana gelen az miktardaki katran ve polimerden temizlenir. Distilasyonlarda, polimer oluşumunu en aza indirmek amacıyla kükürtsüz bir inhibitör kullanılır. Çevreyi kirletecek akımlar yoktur.
PS Temel Özellikleri :
Çeşitli son segment plastik ürünleri yapmak için kullanılan çok yönlü bir plastik formudur. PS polimer, kolaylıkla işlenebilen ve köpükler, filmler ve tabakalar gibi çok sayıda yarı bitmiş ürüne dönüştürülebilen berrak, amorf, polar olmayan bir malzeme türüdür. Hacim açısından, aşağıdaki gibi özelliklerinden dolayı kullanılan en büyük plastiklerden biridir:
-
Darbe ve ısı direnci yüksektir.
-
Bu polimerler, mükemmel optik netliğe sahip iyi bir elektrik yalıtkanıdır.
-
PS, seyreltilmiş asitlere ve bazlara karşı güçlü kimyasal dirence sahiptir.
-
Cam sıcaklığının üzerindeki viskoz bir sıvıdır ve çok sayıda bitmiş ürüne kolay imalat sağlar.
-
Kolayca genişletilebilirler ve iyi akışa izin verirler.
-
Bu malzemeler doğası gereği güçlü alev geciktiricidir.
-
PS için kullanılan kimyasal formül (C8H8) n
-
Yoğunluk - 0,96–1,04 g / cm3
-
Erime noktası ~ 240 ° C'dir (464 ° F; 513 K) [4] İzotaktik PS için
-
Suda çözünmeyenlerde çözünürlük
-
Çözünürlük - Asetonda çözünmez
-
Polimerin ısıl iletkenliği 0.033 W / (M · K) (köpük, ρ 0.05 g / cm3)
-
Kırılma indisi 1.6'dır; dielektrik sabiti 2,6 (1 kHz - 1 GHz)
-
Yanıcıdır, ancak geciktirilmiş çeşitleri de mevcuttur.
-
Solvent direnci zayıftır ve birçok kimyasal tarafından saldırıya uğrayabilir.
-
Homo-polimerler doğası gereği kırılgandır.
-
Strese ve çevresel çatlamaya maruz kalır.
-
Zayıf termal stabiliteye sahiptirler.
PS Kullanım Sahaları :
Farklı biçimlerde bir dizi mal üretmek için çeşitli son kullanıcı endüstrilerine uygulanabilir. Aşağıdakiler gibi çeşitli endüstrilerde en yaygın kullanılan polimer haline gelmiştir:
-
Beyaz eşya - Buzdolapları, klimalar, fırınlar, mikrodalgalar, elektrikli süpürgeler ve karıştırıcılar gibi bir dizi cihazda kullanılmaktadır, uygun maliyetli ve uzun ömürlüdür.
-
Otomotiv - PS (katı ve köpük), düğmeler, gösterge panelleri, trim, enerji emici kapı panelleri ve hatta ses sönümleyici köpük dahil olmak üzere birçok otomotiv parçasının üretiminde kullanılmaktadır.
-
Elektronik - Biçim, işlev ve estetik kombinasyonunun gerekli olduğu televizyonların, bilgisayarların ve farklı BT ekipmanlarının konutlarında ve diğer bölümlerinde kullanılır.
-
Yemek Hizmeti - PS, rakiplerine kıyasla ambalaj sektöründe önemli bir paya sahiptir. Daha iyi yalıttığı, yiyecekleri uzun süre taze tuttuğu ve uygun maliyetli olduğu için gıda ambalajlarında yaygın olarak kullanılmaktadır.
-
Yalıtım - Hafif PS köpüğü, bina duvarı, çatı kaplaması, soğutma, dondurucular ve hatta endüstriyel soğuk depolama tesisleri gibi bir dizi uygulamada mükemmel ısı yalıtımı olduğunu kanıtlamaktadır. Daha inert, dayanıklı ve su hasarına dayanıklı olması nedeniyle yalıtım için tercih edilir.
-
Tıbbi - Netliği ve sterilizasyon kolaylığı nedeniyle PS, doku kültürü tepsileri, test tüpleri, petri kapları, teşhis bileşenleri ve diğer tıbbi test cihazları dahil olmak üzere çok çeşitli tıbbi kullanımlar için kullanılır.
-
Ambalaj- Ambalaj sektöründe çok kullanılan ve tercih edilen bir malzemedir. CD ve DVD kutuları, malların nakliyesi için köpük ambalaj fıstığı, sarf malzemesi ambalajları, et ve kümes hayvanları tepsileri ve ayrıca yumurta kartonları vb. Gibi tüketici ürünlerini korumak için yaygın olarak kullanılmaktadır.
GPPS (General Properties PolyStyrene) :
Genel amaçlı kristal netliğinde PS olarak da adlandırılır. Bu plastik formu tamamen şeffaftır, serttir ve genellikle stiren monomerden yapılan düşük maliyetli PS'dir. GPPS, 2-5 mm PS peletler şeklinde üretilen katı bir PS formudur. Genel kullanım polistiren nispeten güçlü ve kötü hava koşullarına dayanıklıdır. Kolayca akar ve oyuncak, CD-DVD kılıfları ve plastik bardak gibi ürünlerin imalatında kalıplamaya uygun hale getirir. Açık ve parlak bir görünüme sahiptir.
-
Nispeten kırılgan olmasına rağmen iyi çekme mukavemeti vardır
-
İyi bir akış, ısı ve kalıplama dengesi sayesinde verimliliği artırır
-
Kırılgan ve Sert özelliği vardır
-
Şeffaftır
-
Düşük çekilme gösterir
-
Düşük maliyetli
-
Mükemmel X ışını direncine sahiptir.
-
Kokusuz ve tatsızdır
-
İşlemesi kolaydır.
Bazı PS marka hammaddelerin teknik değerleri ve daha çok kullanım alanları :

HIPS (High Impact Polystyrene) :
Yüksek darbe polistiren (HIPS) daha çok (Antişok) olarak piyasa bilinmektedir. PS ve kauçuktan oluşur ve bu sebeple opak ve beyazdır. İşleme ve üretimi kolay, çok yönlü, ekonomik ve darbeye dayanıklı bir plastiktir. Mükemmel boyutsal kararlılığa sahip olduğu ve üretimi, boyaması ve yapıştırması kolay olduğundan üretim öncesi prototiplerin işlenmesinde sıklıkla kullanılır. Cihaz, oyuncak, TV ve görsel-işitsel ekipman için bileşenler gibi tüketici ürünleri, Otomotiv endüstrisinde gösterge panelleri ve aksesuarları, benzin depoları, Isıl şekillendirilmiş levhalar üretimi kullanım sahalarıdır.
-
Katı ve Sert yapılıdır
-
Yarı saydamdır
-
İyi derecede darbe direnci vardır
-
İşleme için mükemmeldir
-
İyi derecede boyutsal kararlılık sergiler
-
Mükemmel estetik kalitesi vardır
-
Boyaması ve yapıştırması kolaydır
-
Ultrasonik olarak kaynak tutması kolaydır
EPS (Expanded PolyStyrene) :
Bir tür sert ve rijit köpüktür. Genellikle beyaz görünümlüdür ve önceden genişletilmiş PS taneciklerinden üretilir. EPS, günlük yaşamda en sık kullanılan PS köpüklerden biridir. Beyaz köpük genellikle sıcak içecekler, buzdolapları, izolasyon ve ambalajlarda vb. Kullanılır.
EPS malzemesi ucuz ve hafiftir. Zamanla temel özelliğini kaybetmez ve çevre dengesini korumak için tamamen geri dönüştürülerek yeniden kullanılır. Düşük ağırlık, sertlik ve şekillendirilebilirlik gibi olumlu teknik ve fiziksel özelliklerinden dolayı EPS, çok çeşitli uygulamalar için kullanıma sunulmuştur. Bina yalıtım ve ambalaj malzemeleri için kullanılan kalıplı levhaların üretiminde bile kullanılır.
EPS, genellikle köpük şeklinde kullanılır. "Strafor" kelimesi genellikle EPS köpüğünün tanımı için kullanılır. Bu köpük malzemenin kullanılan bir tür ticari markasıdır. Günlük yaşamda kullanılan en yaygın köpük ürünleri, soğutucular, şarap nakliyecileri, kalıplanmış uç kapakları ve köşeleri, kutuların ambalajlanması ve hatta su soğutucuları için farklı yerlerde kullanılan bardaklardır.
Stiren monomerden üretilmiştir. Öncelikle bir etilen ve benzen türevidir ve küresel polistiren yatakları üreten bir polimerizasyon işlemi kullanılarak üretilir. Malzemenin genleşmesine yardımcı olmak için işlem sırasında genellikle düşük kaynama noktalı hidrokarbon (pentan gazı) eklenir.
Üç aşamada üretilir
-
Ön Genleşme - Buharla temas ettiğinde polistiren boncukta bulunan ön köpürtücü ajan kaynamaya başlar ve boncuklar orijinal hacimlerinden 40 ila 50 kat genişler.
-
Koşullandırma - Genleşme işleminden sonra boncuklar, sıcaklık ve basınç dengesine ulaşmak için daha da olgunlaşma sürecinden geçer.
-
Kalıplama - Daha sonra boncuklar bir kalıbın içine yerleştirilir ve buharla yeniden ısıtılır. Önceden köpürtülmüş boncuklar, kalıp boşluğunu tamamen doldurmak ve birbirine kaynaşmak için daha fazla genişler.
EPS üretiminde kullanılan iki kalıplama işlemi
-
Siyah Kalıplama- Kullanıcı talebine göre daha da kolay kesilip yeniden şekillendirilebilen büyük EPS blokları üretmek için kullanılır. Bu bloklar hem paketleme hem de inşaat uygulamalarında kullanılmaktadır.
-
Şekil Kalıplama- Özel tasarım özellikleri gerektiren parçaları üretmek için kullanılır. Genellikle bu işlem, şekilli kalıplanmış EPS'nin büyük ölçüde kullanıldığı elektronik ürün ambalajı için kullanılır.
EPS, performansı, teknik çok yönlülüğü ve maliyet etkinliği nedeniyle yarım yüzyıldan fazla süredir tercih edilen termoplastik malzemedir . Günlük uygulamalarda yaygın olarak kullanılmaktadır. Hafifliği, sağlamlığı, ısı yalıtımı, dayanıklılığı ve diğer özellikleri onu bir dizi uygulama için uygun kılar.
-
Hafiflik. ~% 95 hava içerdiği için son derece hafif bir malzemedir. Bu özelliği ürüne ağırlık katmadığı ve nakliye maliyetini düşürdüğü için ambalaj endüstrisi için uygun bir malzeme olmasını sağlar.
-
Dayanıklılık. Bu malzemenin dayanıklılığı, çeşitli malları paketlemek için kullanılan etkili ve güvenilir plastik formunu sağlar. Doğası gereği kokusuz ve toksik değildir ve hücresel yapısı onu boyutsal olarak daha kararlı hale getirir. Bu, ürün ömrüne değer katar.
-
Nem Dayanımı. Kapalı tip hücre malzemesidir ve suyu kolaylıkla emmez. EPS, nemli koşullarda dahi gücünü kaybetmediği için soğuk zincir ürünler için ideal bir malzemedir. Malzeme yüksek neme dayanıklı olduğu için hijyen gereksinimi kolayca karşılanır. Bu özelliğinden dolayı şamandıra ve marina şamandıralarında balık tutmak için de kullanılmaktadır. Bu malzeme suda uzun süre doygunluğa maruz kalsa bile ısıl performansında bir miktar azalma ile boyutunu, şeklini, yapısını ve fiziksel görünümünü korumak için dengeler.
-
Şok Emme. Aletler, elektronik ürünler, bilgisayarlar ve kimyasallar dahil olmak üzere birçok ürün için ambalaj malzemesinin ilk tercihi haline getiren mükemmel bir şok emici özellik sunar.
-
Termal Verimlilik. EPS malzemesinin yüksek termal verimliliği, sıcaklığa duyarlı ürünlerin paketlenmesinde çok yardımcıdır. EPS kaplarda depolanan ürünler, ortam koşullarının altındaki veya altındaki sıcaklıklarda bile daha uzun ömürlüdür. Ürünü nakliye sırasında ani sıcaklık ve iklim değişikliğinden bile korur. EPS kapları gerektiren sıcaklığa duyarlı ürünlere örnek olarak deniz ürünleri, taze ürünler, ilaçlar ve çeşitli tıbbi ürünler verilebilir.
-
Çok yönlülük. İhtiyaca göre kolayca kesilip şekillendirilebildiğinden hemen hemen her şekil ve boyutta üretim yapmak için kullanılabilir. Ayrıca ürünün ihtiyacına göre farklı fiziksel özelliklere sahip çeşitli yoğunluklarda üretilmektedir. Çok sayıda ürünle uyumu da diğer alternatiflerden değerinin artmasına yardımcı olur.
-
Kullanım Kolaylığı. EPS, özellikle inşaat sektöründe kullanımı en kolay malzeme olarak kabul edilmektedir. Normalde, ihtiyaca göre şekillere veya büyük form bloklarına kolayca kalıplanabilen tabakalar halinde bulunur.
-
Yoğunluk, lb./cu.ft. - 0
-
Basınç dayanımı, psi . - 31-37
-
Çekme mukavemeti, psi - 58-61
-
Termal direnç, R / in. - 2
-
Dielektrik dayanımı yaklaşık 2KV / mm'dir . 400 MHz'e kadar olan frekanslarda, malzemenin sunduğu geçirgenlik 1.02-1.04'tür ve kayıp faktörü 1 MHz'de 5 × 10-4'ten az ve 400 MHz'de 3 × 10-5'ten azdır.
-
Suya ve tuzların, asitlerin ve alkalilerin sulu çözeltilerine karşı oldukça dirençlidir. Genellikle organik çözücülerle uyumlu değildir. 120-140F'ye kadar UV radyasyonu, kalıplanmış malzeme formu üzerinde hafif bir etkiye sahiptir. Genellikle malzemenin sararmasına neden olur ancak fiziksel özelliklerini etkilemez.
-
Uzun vadeli ve istikrarlı R-Değeri sağlar.
-
Küf veya küf oluşumunu önleyin.
-
Kolayca geri dönüştürülebilirler.
-
EPS yalıtım malzemeleri sınıfın altına yerleştirilebilir.
-
Ters çevrilmiş montajlar için de kullanılabilirler.
-
Güneşe maruz kalmak ürünü bozabilir.
-
Solvent bazlı malzemeler ciddi hasara neden olabilir.
-
250 Fahrenheit derecesinin üzerindeki sıcaklık polistireni eritebilir.
-
Kalıcı bozunmaya neden olabilecek belirli tür termoplastiklerle uyumsuzdurlar.
-
Yanıcıdır ve uygun yerleştirme gerektirir.
XPS (eXtruded PolyStyrene) :
Azaltılmış termal iletkenlikle gelişmiş yüzey pürüzlülüğü ve daha yüksek sertlik sunan başka bir köpük biçimidir. Bu EPS gibi kimyasal bileşim hemen hemen aynı türdedir, ancak farklı bir teknoloji ile üretilmektedir. EPS, pembe, mavi ve yeşil vb. Olmak üzere üç temel renktedir. Genellikle tanıtım panelleri ve inşaat alanında kullanılır.
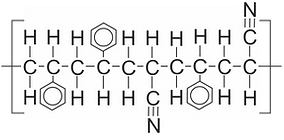
SAN (Styrene AcryloNitrile)
1940'lardan beri mevcuttur ve ilk olarak 1950 yılında piyasaya sürülmüştür. Ayrı ayrı stirene göre artan tokluğu onu çeşitli kullanımlar için uygulanabilir kılmıştır. Ayrıca, SAN'ın sınırlamaları, üçüncü bir monomer olarak bütadienin (kauçuk) kullanılmasına yol açmış ve ABS (Akrilonitril-Bütadien-Stiren) üretimini tetiklemiştir.
Bu kopolimer plastik reçine, stiren ve akrilonitrilin ko-polimerizasyonu ile üretilen sert, şeffaf bir plastiktir. Poliakrilonitrilin sertliği, mukavemeti ve çözücü direnci ile polistirenin berraklığı ve sertliğinin bir kombinasyonudur.
Stiren bazlı malzemeler dayanıklılık, yüksek performans, tasarımın çok yönlülüğü, üretim kolaylığı ve ekonomi gibi mükemmel nitelikler sunar. SAN ürünleri iyi hijyen, sanitasyon ve güvenlik faydaları sağlar. Ayrıca iyi bir yalıtım sağlarlar ve ayrıca kolayca geri dönüştürülebilirler.
Çok iyi kimyasal mukavemeti vardır. Çok saydamdır ve hoş bir parlaklığa sahiptir. Kozmetik malzemeler için uygun bir seçim kazandırmaktadır. SAN, hafifsarı renklidir ama farklı renklendirilmiş varyasyonlarıda mevcuttur. Standart SAN dış mekân kullanımları için uygun değilken, UV dayanıklı sınıfları da vardır. Buzdolabı parçaları, raf ayıraçları, ışık kapakları, kozmetik ambalaj, mutfak malzemelerinde, otomotiv parçaları, akü kutuları, mutfak eşyaları, ev aletleri, mobilya ve tıbbi malzemelerde kullanılır. Isıl direncinin daha yüksek olması nedeniyle genellikle polistiren yerine kullanılır.
SAN, 70 ila 30 oranında iki ünite, stiren üniteleri ve akrilonitril ünitelerinden oluşur. Bu iki bileşik, dökme sıvı formda veya su bazlı emülsiyon veya süspansiyondan oluşan bir çözelti halinde karıştırılır.
Bu bileşiklerin polimerizasyon işlemi, serbest radikal başlatıcıların etkisi altında gerçekleştirilir. Bu işlemin elde edilen plastik malzemesi , ısıya ve çözücülere karşı tek bir polistiren formuna göre daha iyi direnç gösterir.
SAN reçineleri üreten başlıca şirketler Samsung Cheil Industries, Chi Mei, INEOS, China National Petroleum, SABIC Innovative Plastics, Toray Industries, Formosa Plastics, Styron, Techno-Polymer ve Petro China'dır.
SAN Temel Özellikleri :
SAN reçineleri polistirene benzer bir kullanıma sahiptir. Polistiren gibi bunlar da optik olarak şeffaftır, kırılgandır ve mekanik davranışa sahiptir. Bu ko-polimerin sergilediği temel özelliklerden bazıları aşağıdaki gibidir:
-
Yüksek mukavemet ve kimyasal direnç gösterir.
-
İyi akış ve boyutsal kararlılık sağlar.
-
Isıya karşı son derece dayanıklıdır.
-
İyi akışa izin verir.
-
Strese, yağa ve yemek lekelerine karşı dayanıklıdır.
-
100 ° C'nin üzerinde cam geçiş sıcaklığına sahiptir.
-
Genel amaçlı kullanılır.
-
Çekme Dayanımı 3.40 - 3.90 N / mm² ve Çentikli Darbe Dayanımı 250 Kj / m²'dir.
-
Termal genleşme katsayısı 70 x 10-6
-
SAN için Maksimum Devamlı Kullanım Sıcaklığı 55 ° C'dir
-
Yoğunluk 1.08 g / cm 3
-
Seyreltik Asitlere ve Alkalilere karşı son derece dirençlidir.
-
Yağ ve greslere karşı çok iyi direnç sergiler.
-
Alifatik Hidrokarbonlara ve alkollere orta derecede dirençlidir.
-
Bu reçinelerin Aromatik Hidrokarbonlara ve Halojenlenmiş Hidrokarbonlara karşı zayıf direnci vardır.
-
Polistirene göre geliştirilmiş kimyasal direnci vardır.
-
Üretilen ürünlere daha iyi tokluk ve sertlik sağlar.
-
Bu polimerler boyutsal olarak kararlıdır.
-
İşleme kolaylığı sunarlar.
-
Kimyasallara ve gerilme çatlamasına karşı oldukça dayanıklıdır.
-
Polistirene kıyasla daha yüksek su emer.
-
Daha düşük termal kapasite ve darbe dayanımı gösterir.
-
Yüksek işlem sıcaklığına gereksinim duyar.
-
Çabuk sararır ve yüksek duman oluşumu ile yanıcıdır.
-
Kanserin nedenlerinden biri olarak teşhis edilmiştir. Kansorejendir.
SAN Kullanım Sahaları:
Stiren Akrilonitril, çeşitli endüstrilerde bir dizi kullanıma uygulanabilir. Daha iyi özelliklerinden dolayı genellikle polistirene tercih edilir. Bu reçineler, aşağıdakiler dahil farklı son segment pazarlarında kullanılmaktadır:
-
Televizyonlarda, kablolarda, radyolarda, klimalarda, bilgisayarlarda ve elektronik cihazları kullanan diğer kişilerde kullanılırlar.
-
Deterjanlar, kaplar, giysiler, diş fırçası ve banyo armatürleri gibi çeşitli ev eşyalarının üretiminde ve paketlenmesinde kullanılır.
-
SAN, kompakt kutular ve ruj tüpleri gibi kozmetiklerin ambalajlanması için büyük bir plastik polimer kullanmıştır.
-
Otomotiv trim, traktör bileşenleri, otomotiv alet lensleri ve pil kutuları vb. Dahil olmak üzere otomotiv parçalarının imalatında yaygın olarak kullanılmaktadır.
-
SAN reçineleri, tartı, hesap makinesi, yazıcı, yazı ve çizim ekipmanı gibi günlük olarak yaygın olarak kullanılan sabit ürünlerin imalatında kullanılır.
-
SAN polimerlerinin fiziksel ve mekanik özellikleri, onları şişe kapakları, çevirmeli anahtarlar, toz kapağı, denizcilik aletleri ve kişisel bakım ürünlerinin paketlenmesi gibi çeşitli genel kullanım ürünlerinin üretilmesi için uygun hale getirir.

PET (PolyEthylene Terephthalate)
PET ilk olarak ABD'de 1940'ların ortalarında, araştırmacılar yeni tekstil polimerleri yapmak için kullanılabilecek polimer aranırken bulunmuştur. Daha sonra bu polyesterler DuPont tarafından "Dacron" olarak markalanmıştır.
1950'lerin sonlarında, araştırmacılar, artık X-ışını veya fotoğraf filmleri olarak yaygın olarak kullanılan filmler oluşturmak için ince ekstrüde PET tabakasını germenin yöntemini bulmuşlardır.
Dünyadaki plastik üretiminin %18′ini oluşturan polietilen tereftalat, polietilen ve polipropilenden sonra üçüncü sırada yer alır. Poliester grubundan olan PET, doğrusal bir termoplastik polimerdir ve çoğunlukla sentetik elyaf, yiyecek paketleme endüstrisi ve özellikle şişeleme gibi alanlarda karşımıza çıkar. Yaygın olarak PET veya PETE olarak bilinen Polietilen Tereftalat, dünyada en çok kullanılan polimerdir. Günlük yaşamımızda kullanılan ürünler için yaygın olarak kullanılan, doğal olarak şeffaf ve yarı kristal plastiktir. PET polimer, tekstil endüstrisinde "Polyester" olarak adlandırılır. Mükemmel bir nem bariyeri olduğu için giysiler için yaygın olarak bir elyaf olarak kullanılır ve ayrıca büyük ölçekte şişeleme ve paketleme için kullanılır. Üretilen PET plastiğin en büyük payı %60 ile sentetik elyaf, %30 ile şişe, bidondur. PET malzeme polimerize monomer etilen tereftalat birimlerinden oluşur ve bu PET malzemeler cam elyaf veya karbon nanotüpler gibi diğer malzemelerle birleştirildiğinde mukavemetleri artar. Bir hammadde olarak PET, kolayca geri dönüştürülebilen güvenli, güçlü, hafif, esnek ve toksik olmayan bir malzeme olarak kabul edilmektedir.
PET plastik, ambalaj sektöründe dünyanın tercihi haline gelmiştir. Hijyenik, güçlü, hafif, ürünlerin tazeliğini koruduğu ve parçalanmadığı için birçok yiyecek ve içeceğin ambalajlanmasında ön plana çıkmaktadır. En çok su ve gazlı alkolsüz içeceklerin paketlenmesinde kullanılır.
Polietilen Tereftalat (PET) temel olarak etilen glikol ve tereftalik asidin polimerizasyonu ile üretilir. Etilen glikol ve tereftalik asit, PET reçinesi için yapı taşları olarak kabul edilir. Ayrıca bu reçineler, herhangi bir şekle sahip parçalara kolaylıkla kalıplanabilen erimiş bir sıvıya ısıtılır. İşlemde büyük benzen halkalarının varlığı, özellikle polimer zincirleri birbiriyle hizalandığında PET polimerine sertlik ve güç katar.
Daha spesifik olmak gerekirse, PET-etilen glikol ve tereftalik asidin iki hammaddesi düşük vakum basıncı ve yüksek sıcaklıklar ile birleştirildiğinde polimerin uzun zincirleri oluşur. Karışım kalınlaştıkça daha uzun zincirler oluşur ve uygun zincir elde edildiğinde işlem durdurulur. Ayrıca, PET polimeri farklı sıcaklıklarda nişasta formunda tutulduğunda kristalleşmeye ve opak ve daha sert hale gelmeye başlar. Bu kristalize PET formu, yeniden ısıtılabilen kaplar ve tepsiler gibi diğer ürünleri hazırlamak için kullanılır.
Dünya PET reçine üretim kapasitesi 30 milyon tonun üzerindedir. Küresel toplam üretimin %32 'sini de Çin üreticileri yapmaktadır. Çin sadece dünyanın en büyük PET reçine üreticisi değil, aynı zamanda en büyük tüketicisidir de.
PET Temel Özellikleri :
PET plastikleri, çok çeşitli uygulamalar için yüksek mukavemet ve sertliğe sahip mühendislik plastikleridir. Özellikle ambalaj ve tekstil endüstrisinde yaygın olarak kullanılan termoplastiktir.
-
Yüksek sıcaklıklarda bile iyi ısı direnci ve düşük sünme özelliği gösterir.
-
Düşük su emilimi sayesinde iyi stabiliteye sahiptir.
-
Düşük su emme özelliğindedir. (Naylon çoraplar hariç)
-
Kimyasallara karşı mükemmel direnç sergiler.
-
İyi renk kararlılığı ve aşınma özellikleri vardır.
-
Çekme Dayanımı 2,5 N / mm ve Darbe Dayanımı 1,5 - 3,5 KJ / m
-
Termal genleşme katsayısı 70 * 10.6
-
Yoğunluk 1.37 g / cm
-
Polimerler kolayca temin edilebilir ve ucuzdur
-
PET polimerler, neme karşı oldukça dayanıklıdır ve organik malzeme ve suya karşı kimyasal dirençlidir.
-
Yüksek mukavemet / ağırlık oranına sahiptir.
-
Oldukça şeffaftır ve kırılmaz (cam ambalaj gibi kırılmaz).
-
PET malzemeleri, çekici ürünler üretmede iyi bir seçim sunan çeşitli şekil ve renklerde gelir.
-
Polietilen tereftalat kolaylıkla geri dönüştürülebilir. PET plastik en çok geri dönüştürülen plastiklerden biridir ve kaplar, uyku tulumu yalıtımı, polyester kumaşlar ve halılar gibi ürünler yapmak için yeniden kullanılırlar.
-
Diğer polimerlere kıyasla PET polimer daha düşük ısı direncine sahiptir.
-
PET reçineleri oksidasyona karşı bile hassastır. Örneğin, bira veya şarabı saklamak için kullanılmazlar çünkü bu içeceklerin raf ömrü uzundur, öyle ki bir çeşit tat bozulması meydana gelebilir.
-
PET plastikler biyobozunur değildir ve kullanımlarına bağlı olarak iyi veya kötü olabilir.
PET Kullanım Sahaları:
PET Reçineler performans polimerleridir. Son segment pazarlarında geniş bir uygulama yelpazesi sunarlar. PET plastik, Ulaşım, Otomotiv, Elektrikli / Elektronik, Beyaz Eşya, Ambalaj ve Tekstil gibi pazarlarda öne çıkıyor.
PET malzeme mükemmel bir su ve nem bariyeri olduğu için ambalaj endüstrisinde özellikle sarf malzemesi ambalajları (su şişeleri, meşrubatlar, paketlenmiş gıdalar) için yaygın olarak kullanılmaktadır. Polimerin yüksek mekanik mukavemeti, PET filmlerin, manyetik bant için bir taşıyıcı veya basınca duyarlı yapışkan bantlar için destek gibi bant uygulamalarında kullanılmasını sağlar. Kristalize PET plastikler, hem donma hem de fırında pişirme sıcaklıklarına dayanabilen tepsiler yapmak için kullanılır.
PET reçineleri erimiş bir sıvıya ısıtılır ve daha sonra istenen şekle kolayca ekstrüde edilir. Cam partiküllerin veya elyafların kombinasyonu ile yapılan PET reçineleri daha dayanıklı ve güçlüdür. Bu reçineler, ürünün ihtiyacı olan özelliklerine göre farklı sektörlerde kullanılmaktadır. PET plastiğin öne çıkan ve büyük ölçekli uygulamalarından bazıları şunlardır:
3D Baskı :
Polietilen tereftalat, 3D baskı için oldukça uygun olan güçlü ve esnek bir polimerdir. 3D baskı, PET reçineler ile kolayca elde edilebilen bir esneklik ve tokluk kombinasyonu gerektirir. PET'in yaygın olarak, 3D Baskı için kullanılan Akrilonitril Bütadien Stiren (ABS) veya Polilaktik Asit (PLA) gibi diğer herhangi bir malzemeden daha az koku yaydığı bilinmektedir.
Enjeksiyon Kalıplama :
Polietilen tereftalat, karmaşık şekillere sahip ürünler üretmek için peletler şeklinde plastik enjeksiyon kalıplama tekniklerinde yaygın olarak kullanılmaktadır . PET higroskopik olduğundan, kalıplama makinesinde kullanılmadan önce kurutulması gerekir. PET plastiğinde çekme düşüktür, ancak aynı zamanda sıcaklık, tutma süresi, kalıp duvar kalınlığı, kalıp sıcaklıkları ve kullanılan katkı maddelerinin türü gibi bir dizi faktöre de bağlıdır.
CNC İşleme :
PET malzeme, CNC makineler için levha stokları olarak yaygın bir şekilde kullanılmaktadır. CNC makinesi, PET malzemenin üretim sürecinde temel malzeme olarak kullanıldığı çok sayıda ürünü üretmek için kullanılır.
PET Film ve Tabaka :
Polietilen tereftalat, öncelikle plastik ürünlerin üretiminde daha sonra kullanılan tabakalar ve filmler üretmek için kullanılır. PET film ve levha yaygın olarak kullanılan termoplastik levhalardır çünkü aşağıdakiler gibi çeşitli faydalar sunarlar:
-
PET Filmler, levhalarla birlikte yüksek bariyer özellikleri ve çekme mukavemeti ile birlikte mükemmel kimyasal özellikler sağlar.
-
Şişe veya diğer plastik sarf malzemeleri şeklinde kolayca değiştirilebilirler.
-
Ürüne daha fazla istikrar ve kırılma direnci sunarlar.
-
Bu filmler hafiftir ve daha ucuzdur.
PET Şişe :
Üretilen PET reçinelerinin büyük bir kısmı PET şişelerin yapımında kullanılmaktadır. Bu şişeler veya kaplar, alkolsüz içecekler, alkollü içecekler, deterjanlar, ilaçlar ve kozmetikler gibi çok çeşitli tüketim ürünleri için kullanılır. Yapılan PET plastik şişeler iki geniş kategoriye ayrılabilir: Şişelenmiş su şişeleri ve Gazlı alkolsüz içecekler. PET reçinelerden yapılan şişeler kolaylıkla geri dönüştürülebilir ve yeniden yeni bir ürün üretmek için kullanılabilir. PET şişeler, son segment plastik pazarında kullanılan en fazla plastik üründür.
PET şişelerinin faydaları şu şekilde sıralanabilir;
-
Hafiftir, taşınması kolaydır ve kullanımı güvenlidir.
-
Yeni ürünler üretmek için kolayca yeniden mühürlenebilir veya geri dönüştürülebilirler.
-
PET şişeler, farklı karmaşık şekillere kolayca kalıplanabilir.
-
PET reçineler aracılığıyla PET şişelerin üretimi, üreticilere yüksek düzeyde esneklik sunar.
-
Ucuzdurlar ve kolaylıkla temin edilebilirler.
PET-G (PolyEthylene Terephthalate-Glycol) :
Polietilen tereftalatın glikol modifikasyonudur. PET-G, en çok kullanılan polimerlerden biri olan PET reçinenin bir tür modifiye edilmiş halidir. PET-G'de kullanılan "G", polimerizasyon sürecinde PET malzeme bileşimine eklenen "glikolle değiştirilmiş" anlamına gelir. PET-G, temel PET malzemeden daha net, daha az kırılgan ve kullanımı daha kolaydır. Su şişeleri, ambalaj sarf malzemeleri ve çeşitli diğer plastik ürünlerin üretiminde yaygın olarak kullanılmaktadır. PET-G, daha dayanıklı ve kullanımı daha kolay olduğu için genellikle 3D baskı filamenti olarak kullanılır.
PET-G kullanımının faydaları şunlardır;
-
Daha dayanıklı ve kullanımı kolaydır.
-
PETG daha net ve daha az kırılgandır. PET'e eklenen glikol, kristalleşmesini ve kırılmasını önler.
-
Oldukça dayanıklı ve sızdırmazdır
-
Kolayca sterilize edilebilir.
MEG (MonoEthylene Glycol)
Etilen Glikol ilk olarak Fransız kimyager Charles-Adolphe Wurtz tarafından 1859 yılında sabunlaştırma yoluyla etilen glikolden hazırlandı. Daha sonra Amerika Birleşik Devletleri, 1917 yılında etilen klorohidrinasyon yoluyla yarı ticari etilen glikol üretimine başladı.
Etilen glikol üretimine yönelik ilk büyük ticari tesis, 1925 yılında Carbide and Carbon Chemicals Co. tarafından South Charleston'da kuruldu. 1929 yılına kadar bu malzeme hemen hemen tüm dinamit üreticileri tarafından yaygın olarak kullanılmaktaydı ve bu da ürünün kullanımı için 1953 yılında lisanslanmasına yol açtı.
Monoetilen Glikol (MEG) veya etilen glikol, ticari olarak temin edilebilen önemli glikoldür. Endüstriyel olarak etilen veya etilen oksitten üretilir. Bu MEG üretim sürecinde, dietilen glikol (DEG) ve trietilen glikol (TEG) olmak üzere iki yan ürün elde edilir.
Şişe imalatında kullanılan polyester elyaf, kumaş ve polietilen tereftalat imalatı gibi endüstriyel uygulamaların sayısı için önemli bir hammaddedir. Diğer endüstriyel kullanımlar, soğutucu, ısı transfer ajanları, antifriz ve ayrıca gaz boru hatlarında bir hidrat inhibitörü olarak kullanılmasını içerir.
MEG, ara etilen oksit yoluyla etilenden üretilir. Bu işlemde etilen oksit, istenen kimyasal denkleme göre etilen glikol üretmek için su ile reaksiyona girer. Bu işlem asitler, bazlar kullanılarak katalize edilir veya yüksek sıcaklıklarda asidik veya nötr pH seviyesinde bile gerçekleşebilir. En yüksek miktarda Etilen Glikol, asidik veya nötr pH'ta fazla miktarda su ile elde edilebilir. Bu koşullar altında yaklaşık% 90 etilen glikol elde edilebilir. Bu işlemin öne çıkan yan ürünleri trietilen glikol, tetrametilen glikol ve oligomerler dietilen glikoldür. Öncelikle etilen glikol üretim süreci aşağıdaki adımlardan oluşur:
-
Etilen Oksit Üretimi : Bu başlangıç aşamasında, etilen ve oksitler birlikte, etilen oksitleri (EO) oluşturan çok borulu bir reaktöre beslenir. Reaktör tüplerindeki sabit yataklarda gerçekleştirilen bu ekzotermik reaksiyon, genellikle gaz fazında (alümina destekli gümüş katalizör kullanılarak) meydana gelir. Buhar, işlem sırasında oluşan reaksiyonun ısısıyla üretilir.
-
Etilen Oksitin Geri Kazanımı : Reaktörden elde edilen ürün, su ile ışıkların uzaklaştırılması için EO emiciye beslenir. Gaz halindeki buharın bir kısmı reaktörde geri dönüştürülür ve geri kalanı bir emici ve bir sıyırıcıdan oluşan bir karbon dioksit giderme ünitesine gönderilir. Bu aşamada karbondioksit, daha sonra etilen karbonat üretiminde kullanılmak üzere ayrıştırılır.Bu işlemin sonraki aşamasında, seyreltilmiş etilen oksit buharı, EO sıyırıcıya beslenmek üzere emiciden çıkarılır. Burada yoğunlaşır ve genel giderlerden kurtarılır. EO'nun ham formu nihayet yoğunlaştırılır ve bu işlemin bir sonraki bölümüne yönlendirilir.
-
Üretim ve Saflaştırma : Son olarak, etilen oksit, etilen karbonat oluşturmak için karbon dioksit ile reaksiyona sokulur. Ayrıca MEG ve karbon dioksit oluşturmak için hidrolize edilir. Her iki işlem de sıvı fazda homojen bir katalizör kullanılarak gerçekleştirilir.
Dünya MEG üretim kapasitesi 35 milyon ton seviyesindedir. Bunun yaklaşık yarısı Çin, Hindistan ve Tayvan başta olmak üzere Asya ülkeleri tarafından gerçekleştirilir. Kuzey Amerika 6 milyon ton, toplam Avrupa 2,5 milyon tonluk üretim gerçekleştirmektedir.
MEG Temel Özellikleri :
Genellikle renksiz, tatlı tada sahip ve kokusuz organik bileşik olan etilen glikol olarak adlandırılır. Tekstil endüstrisi, ambalaj endüstrisi ve diğerleri gibi çeşitli uç segment endüstrileri için oldukça kullanılır. MEG'in dayanıklılığı, hidrofobik özellikleri ve sağlamlığı gibi özellikleri, onu çeşitli endüstriyel uygulamalar için önemli bir hammadde olarak kanıtlamaktadır. Polyester reçineler, elyaflar ve filmlerin üretiminde yaygın olarak kullanılmaktadır. Bu malzemenin fiziksel özellikleri, soğutucu malzeme, korozyon önleyici madde, susuzlaştırma maddeleri ve kimyasal ara madde gibi farklı malzemeler olarak kullanılmasına izin verir.
-
Kimyasal formül C2H6O2'dir
-
Görünüm - Berrak, renksiz sıvı
-
Molar kütle - 62.07 g • mol −1
-
Yoğunluk -1.1132 g / cm 3
-
Erime noktası - 12.9 ° C (8.8 ° F; 260.2 K)
-
Kaynama noktası - 197.3 ° C (387.1 ° F; 470.4 K)
-
Buhar basıncı 0,06 mmHg (20 ° C) [1]
-
Viskozite - 1,61 × 10−2 Pa • s [2]
-
Suda çözünürlük karışabilir
-
Çözünürlük - Çoğu organik çözücüde çözünür.
-
MEG yüksek toksik seviyeye sahiptir.
-
Suya benzer bir yapıya sahiptir, bu da onu madde ile karışabilir hale getirir.
-
Kolay bulunabilen ve düşük maliyetli bir malzemedir.
-
Düşük donma ve yüksek kaynama noktasına sahip olduğu için imalat endüstrisinde harika bir bileşen olduğunu kanıtlıyor.
-
Bu malzemenin iyi ısı transfer yetenekleri vardır
-
MEG bir çeşit uzun ömürlü bileşiktir.
-
Oldukça yanıcıdır ve suyu hızla emer.
-
Antifriz sızıntı yaparsa, büyük ölçüde arabalarda olası bir yanma tehdidi vardır.
-
MEG'nin özellikle havalimanlarının pistlerinde uygun olmayan şekilde imha edilmesi çevreye zarar verebilir.
-
Tatlı tadı, sağlığa zararlı olabilecek çocukları ve evcil hayvanları kolayca çeker.
MEG Kullanım Sahası :
MEG, temel olarak aşağıdakiler de dahil olmak üzere bir dizi endüstriyel işlemi gerçekleştirmek için farklı biçimlerde hammadde olarak kullanılır:
-
Soğutucu ve Isı Transfer Maddesi - Büyük ölçüde etilen glikol, otomobillerde ve sıvı soğutmalı bilgisayarlarda olduğu gibi konvektif ısı transferi için bir ortam görevi görür. Soğutma sıvısı olarak soğutulmuş su klimalarında ve ısıtma sıvısı olarak jeotermal ısı pompalarında ısıyı taşımak için yaygın olarak kullanılmaktadır.
-
Antifriz - MEG'nin özellikleri, suda çözündüklerinde hidrojen bağını bozar. Genellikle -12 ° C'de donar ancak karıştırılırsa kristalleşmez ve bu nedenle donma noktası düşer. MEG'in bu antifriz özelliği, ön camlar ve uçaklar için sıvıların buzlanmasını gidermek için kullanılır. Biyolojik doku ve organların korunmasında da kullanılır.
-
Polimerler için Öncü - Plastik endüstrisinde, MEG bir dizi termoplastik reçinenin önemli öncülerinden biridir. Polyester elyaflar ve reçineler için bir öncü olarak oldukça kullanılır.
-
Gazlı alkolsüz içecekler ve şişelenmiş su için plastik şişe yapımında kullanılan Polietilen Tereftalat (PET) da bu malzeme öncül olarak kullanılarak hazırlanır.
-
Dehidratasyon ajanı ve hidrat inhibisyonu olarak kullanılır. Dehidre edici bir ajan olarak, doğalgaz endüstrisinde işlenmeden önce doğal gazdaki su buharını gidermek için kullanılır.
-
Bir hidrat inhibisyonu olarak, doğal gazı uzak gazdan işleme tesisine taşıyan boru hatlarında doğal gaz hidratlarının (klatratlar) formülasyonunu inhibe etmek için yaygın olarak kullanılmaktadır. Aynı zamanda doğal gazla geri kazanılabilir ve bir inhibitör olarak yeniden kullanılabilir.
MEG Kullanımına Yasak Sahalar:
-
Taşınabilir su Uygulamaları.
-
Gıda, ilaç ve kozmetiklerin formülasyonunda.
-
Mevsimlik evler ve eğlence amaçlı su sistemlerindeki taşınabilir su sistemleri için antifriz.
-
Yangın sprinkler sistemlerine antifriz.
MEG ile PEG Arasındaki Farklar :
-
Moleküler Yapı: Glikol ailesinin iki önemli üyesidir. Her iki bileşiğin de ticari uygulama önemi vardır. Bu glikollerin her ikisindeki fark, kimyasal yapılarından kaynaklanmaktadır. Etilen glikol bir tür basit doğrusal moleküldür, polietilen glikol ise polimerik bir malzemedir.
MEG : Etilen Glikol - EO'nun moleküler formülü (CH2-OH) 2
PEG : Polipropilen Glikol- PEG'nin moleküler formülü (C2H4O) n + 1H2O'dur.
-
Genel Özellikler :
MEG : kokusuz, renksiz, tatlı bir bileşiktir. Polyester elyaf üretiminde ve antifriz formülasyonlarında hammadde olarak kullanılan organik bir bileşiktir. Bu malzemeler yutulursa toksik olabilir.
PEG : kimyasal, biyolojik, tıbbi, endüstriyel ve ticari gibi alanlarda kullanılan polimerik bir bileşiktir. Berrak bir sıvı veya hafif bir kokuya sahip suda çözünür beyaz bir katıdır.
-
Üretim Şekli :
MEG : bir kimyasal bileşik etilen kullanılarak üretilir. Bu süreçte etilen oksit bir ara ürün olarak üretilir ve EO üretmek için su ile reaksiyona girer. Bu işlemde katalizör olarak Asitler ve Bazlar kullanılır.
PEG : etilen oksitin su ile etilen glikol veya glikol oligomerleri ile reaksiyonu sonucu üretilir. Bu işlemde ayrıca bu işlemi katalize etmek için hem asit hem de bazlar kullanılır. Polimerizasyon işlemi, katalizörün kullanımına bağlı olarak katyonik veya anyonik olabilir.
-
Kullanım Sahası :
MEG : esas olarak bir antifriz olarak ve ayrıca plastik endüstrisinde evcil hayvan gibi polyesterlerin üretiminde hammadde olarak kullanılır. Özellikle otomotivde ve sıvı soğutmalı bilgisayarlarda ısı transferlerinde de faydalıdır. Özellikleri aynı zamanda soğutulmuş su iklimlendirme sistemlerinde kullanılmasını da sağlar.
PEG : Daha düşük toksisiteye sahiptir, bu nedenle hem sulu hem de susuz ortamlar için bir yağlayıcı kaplama olarak kullanılır. Birçok cilt kremi ve kişisel kayganlaştırıcı için temel olarak kullanılır. Aynı zamanda diş macunu veya dağıtıcıda bir bileşen olarak ve ayrıca gıda endüstrisi uygulamalarında köpük önleyici bir ajan olarak kullanılır.
PMMA (PolyMethyl MethAcrylate)
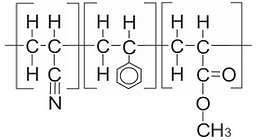
Yüksek düzeyde berraklık ve yapısal sertliğe sahip optik bileşenler için yaygın olarak kullanılan, bozunmayan bir poliakrilat biçimidir. Piyasada daha çok akrilik cam ya da pleksiglas olarak bilinen renksiz ve şeffaf bir termoplastik polimerdir.
Metil metakrilatın polimerizasyon süreci ile üretilen sentetik bir reçinedir. Yaygın olarak camların (pencereler, çatı pencereleri, lamine tabelalar ve uçak kanopileri vb.) üretiminde yaygın olarak kullanılan şeffaf, sert ve şeffaf bir plastik türüdür. Genelde cama alternatif malzeme olarak tercih edilir ve polikarbonatla benzer özelliklere sahip olduğu için polikarbonatın kullanıldığı ürünlere de alternatif olabilir. Kristal gibi parlak görünen, açık havada yıpranmaya karşı dayanıklı,ağırlığı cam ağırlığının yarısı kadar olan bu plastiğin darbe mukavemeti de yüksektir.
Çekme mukavemeti, şeffaflık, parlatma ve UV direnci, darbe mukavemeti ve kimyasallara ve ısıya dirençten daha önemli olduğunda, bu malzemenin polikarbonat için ekonomik bir alternatif olduğu kanıtlanmıştır. Polikarbonat malzemelerde bulunan bir alt birim olan zararlı bisfenol-A içermediği için polikarbonata tercih edilir. Bu reçine aynı zamanda makul özellikleri, kullanım ve işleme kolaylığı ve düşük maliyeti nedeniyle diğerlerine göre avantajlıdır.
İlk olarak İngiliz kimyager Rowland Hill ve John Crawford tarafından İngiltere'deki Imperial Chemical Industries'de, 1930 yılında keşfedildi ve ürün, Perspex ticari markası altında tescil edildi.
Aynı zamanda, Almanya'daki Otto Rohm (kimyager ve sanayici), iki cam tabakası arasında metakrilatın polimerizasyonu yoluyla emniyetli cam üretme üzerine çalışmalar yaptı. Elde edilen bir polimer olarak camdan ayrıldı ve Plexiglas'ın ticari markası olan berrak bir plastik levha sağladı. Bu ürün de 1930'ların sonlarında ticari pazara girdi.
Daha sonra ABD'de EI du Pont de Nemours & Company (şimdi DuPont) kendi ürünlerini Lucite ticari adı altında tanıttı ve en yoğun çalışma sahası olarak, II.Dünya Savaşı sırasında, silah kuleleri için uçak pencereleri ve balon kanopileri üretiminde kullanıldı.
Ucuz olması ve kolay proses edilmesi sayesinde tercih edilse de kırılgan bir yapıya sahip olduğu için kullanım alanı biraz kısıtlıdır. PMMA, ilk olarak paraşüt yapımında kullanılmıştır. bundan başka dekorasyon, ışıklandırma ve akvaryumlar, masa, lavabo ve mutfak evyeleri yapımında, İnsan vücudunda bazı implantların ve optik lenslerin üretiminde kullanılır.
PMMA, bağlı bir Alkil veya Aril grubuna sahip büyük metakrilat ester ailesinin üyelerinden biridir. Genellikle emülsiyon polimerizasyonu, çözelti polimerizasyonu ve yığın polimerizasyonu ile üretilir.
PMMA malzemesi, önemli bir akrilik reçine ailesine ait olan bir metakrilik asit esteridir . Öncelikle üretim sürecinde kullanılan propilen (PP) elde edilir. Ayrıca propilen ve benzen, kümen veya izopropil benzen üretmek için birlikte reaksiyona sokulur. Daha sonra üretilen kümen, kümen hidroperoksite oksitlenir. Daha sonra aseton üretmek için asit ile muamele edilir ve bu da metil metakrilata (yanıcı sıvı) dönüştürülür. Bu sıvı, katı (PMMA plastik) oluşturmak için serbest radikal başlatıcıların etkisi altında dökme sıvı veya süspanse edilmiş ince su damlacıkları şeklinde polimerize edilir.
PMMA, pazarda Plexiglas, Lucite-Perspex ticari markaları altında daha çok tanımlanmaktadır.
PMMA Temel Özellikleri:
-
Güçlü, sağlam ve hafif bir malzemedir.
-
Hem cam hem de polistirenden daha iyi darbe dayanımına sahiptir.
-
Diğer plastiklere kıyasla üstün çevresel kararlılık gösterir.
-
Yüksek termal ve kimyasal direnç sahibidir.
-
Düşük duman emisyonu vardır.
-
Mükemmel aşınma direnci vardır.
-
Yüksek güç ve dayanıklılık sergiler.
-
Yüksek ışık geçirgenliğine sahiptir.
-
Yoğunluk - 1.17 - 1.20 g / cm 3 (bardağın yarısından az)
-
Erime Noktası - 160 ° C (320 ° F, 433 K)
-
Su Emme Oranı -% 0,3-0,4
-
Tutuşma Sıcaklığı - 460 ° C (860 ° F)
-
Solvency- Birçok organik çözücüde kolayca erir ve çözünür.
-
Darbe direnci, diğer ikame plastik malzemelerle karşılaştırıldığında mukavemeti düşük kalabilir. sahiptir.
-
Hidroliz işlemi sırasında Bisfenol A (BPA) içermediği veya serbest bırakmadığı için diğer plastik polimerden avantajlıdır.
-
Polikarbonat olan ilgili plastik malzemeler bile doğada toksik yapan BPA içerir. (BPA'nın sağlık ve çevre için tehlikelidir). PMMA kendi başına katı haldeyken doğası gereği toksik olmayan, BPA (Bisfenol-A) içermeyen bir plastik türüdür.
-
Genellikle, enjeksiyon kalıplama için erimiş formda kullanıldığında 3D baskı cevheri sırasında yayılan dumanları toksik olabilir. Sağlık risklerine neden olabileceğinden, solumaktan kaçınılmalı, üretim sahası iyi havalandırılmalıdır.
PMMA Kullanım Sahası:
PMMA farklı alanlarda ve farklı formlarda çok çeşitli uygulamalar için kullanılabilen çok yönlü bir plastik malzemedir.
Olumlu fiziksel, kimyasal ve mekanik özellikleri sayesinde bir dizi uygulamada aşağıdaki şekillerde kullanılabilir:
Şeffaf ve berrak yapısı nedeniyle yaygın olarak cam yerine kullanılır. Cam yerine geçen bu malzeme aşağıdaki alanlarda uygulanabilir:
-
Ticari ve konut akvaryumlarının yapımında
-
PMMA plastik camları, portları ve ayrıca dalgıçların eksik basınçlı gövdelerini görüntüleme. Denizaltılar için izleme kürelerinde
-
Otomobillerde dış ışıkların lensleri ve buz hokeyi pistlerinin seyirci koruma panellerinde
-
Uçak pencerelerinde hatta polis araçlarının camlarının yerine
-
Deniz feneri mercekleri yapımında, cam tavanlarda, botanik bahçeleri gibi alanların çatı kaplamalarında
-
Işığı yeniden yönlendirmek için farklı segmentlerde
-
Lazerle kesilmiş akrilik panellerde, güneş ışığını bir ışık borusu ile kapalı alanlara taşımakta
-
Dekoratif amaçlı çeşitli sanatsal uygulamalarda
-
Pencerelerden giren güneş ışığını, odanın tabanına veya tavanına yönlendirmede prizma tabakalı levhaların üretiminde
PTFE (PolyTetraFluoroEthylene)
Polimerizasyon işleminden üretilen güçlü, sert, mumlu, yanıcı olmayan bir sentetik reçine türüdür. Teflon, Hostaflon ve Polyflon markaları altında yaygın olarak yapışmaz tavalar veya kaygan yapıdaki şeyler yapmak için kullanılır.
Bütün sanayi plastikleri içinde en geniş çalışma sıcaklığı - 260 ile 270 °C sahip oluşu, sanayide kullanılan bütün kimyasal maddelere neme ve ortam şartlarına tam sonsuz dayanımı, bütün katılar içinde en düşük statik ve dinamik sürtünme katsayısına sahip oluşu, üstün elektriksel izolasyon özelliği , yapışmazlık , yanmama ve bunun gibi özelliklerin yanı sıra, mekanik özelliklerin yeterli oluşu ve tüm kimyasal maddelere karşı tam dayanımlı olması tercih nedenidir.
Roy Plunkett (EI du Pont de Nemours & Company için Amerikan Kimyacısı) tarafından 1938'de bir gaz TFE soğutucu tankının beyaz bir toza polimerize olduğunu bulduğunda tesadüfen keşfedildi. Daha sonra, İkinci Dünya Savaşı sırasında, radyoaktif malzemelerin taşınmasında kullanılan metal ekipmanı korumak için korozyona dayanıklı bir kaplama olarak kullanıldı.
Kaygan yapısı ve yüksek erime noktası nedeniyle, DuPont tarafından 1960 yılında Teflon-Kaplamalı yapışmaz tencere ticari markasıyla piyasaya sürülene kadar yaygın kullanıma girmedi. Bu reçine malzeme ile kaplanmış yapışmaz tava ve tencerelerde en iyi bilinen markadır. PTFE, bu nedenle DuPont 'un önde gelen markalarından biri olan "Teflon" ile daha iyi bilinmektedir.
PTFE tetrafloroetilenin serbest radikal polimerizasyonu ile üretilir. Tetrafloroetilen patlayarak tetraflorometan ve karbona ayrışabildiğinden, zararlı yan reaksiyonlara neden olabilecek sıcak noktaları önlemek için çeşitli özel aparatlar kullanılır.
Proses, sülfat radikalleri üretmek için homolize edilen persülfat tarafından başlatılır. Daha sonra ortaya çıkan polimer, polimerin uç gruplarını üretmek için hidrolize edilebilen sülfat ester grupları ile sonlandırılır. Bu malzeme hemen hemen her çözücüde çözünür olduğundan, polimerizasyon işlemi (PFOS gibi yüzey aktif maddeler kullanılarak) suda bir emülsiyon olarak yürütülür.
PTFE'nin ana hammaddeleri Kloroform, Fluorspar ve hidroklorik asittir.
Öncelikle ince, mikronize gibi toz formunda ve ayrıca sulu dispersiyonda mevcuttur.
PTFE Temel Özellikleri :
-
Kimyasallara ve hava koşullarına karşı son derece dayanıklıdır.
-
Mükemmel dielektrik özelliğe sahiptir.
-
Güçlü alev direnci ile yüksek termal kararlılık gösterir.
-
Yapışmaz, düşük sürtünme direnci vardır.
-
Gıda temasında uyumludur.
-
Pürüzsüz yüzey kaplaması etkisine sahiptir.
-
Islanmaz ve korozyona karşı yüksek derecede koruyucudur.
-
Yoğunluk - 2200 kg / m 3
-
Erime Noktası - 600 K
-
Termal Genleşme - 112–125 • 10 −6 K −1 [23]
-
Cam Sıcaklığı-388K [22]
-
Sürtünme katsayısı - 0.05-0.10
PTFE Kullanım Sahası :
Günümüzde PTFE polimerin başlıca kullanımı, yapışmaz pişirme gereçleri kaplamaları olarak kullanılmaktır. Yataklar, boru gömlekleri ve çeşitli pompa ve valf parçaları da dahil olmak üzere bir dizi endüstriyel üründe uygulaması vardır.
Bu malzeme, mekanik bileşenler şeklinde ve kaplama malzemeleri olarak çeşitli uygulamalarda yaygın olarak kullanılmaktadır. Bu reçinelerin hizmet verdiği başlıca son kullanıcı endüstrileri arasında kimyasal işleme, mekanik, gıda, ev, otomotiv, elektronik ve diğer pek çok şey bulunmaktadır.
En iyi yapışmama özellikleri ve yüksek sıcaklıklara karşı direnci ile PTFE, bilinen çok çeşitli uygulamalara sahip inanılmaz derecede çok yönlü bir malzemedir. PTFE daha çok şu avantajlarla öne çıkar;
-
Elektriksel yalıtkanlıkta mükemmeldir. Bilgisayar uygulamaları kablo ve kablolar için bir izolatör olarak kullanılır.
-
Düşük sürtünme özelliği ile kaymalı yataklar, kayar plakalar, dişliler ve diğer çalışan parçalarda kullanım dahil olmak üzere makine mühendisliği uygulamalarında popüler bir malzemedir.
-
Aşınmaya dayanıklıdır, reaktif değildir ve yüksek sıcaklıklara toleranslıdır. Bu özellik, endüstriyel borularda ve hortum montajlarında (kimyasal ve asitlerin kullanıldığı yerlerde) kullanıma uygun hale getirilmesine yardımcı olur.
-
Yüksek sıcaklıkları tolere eder. Böylece, asitler ve kimyasallar ile kimyasa endüstrisinde çok kullanılır.
-
Gıda temasında sakınca yoktur bu nedenle ambalajlama konusundaki uygulamalar için mükemmel bir seçimdir.
-
Kimyasal olarak agresif kullanımlarda bileşenleri sızdırmaz hale getirmek için ideal bir seçimdir.
-
Ekonomik yapıya sahiptir. Park, süpermarket, köprü yapımında ve hatta otomobillerde bile yaygın olarak kullanılmaktadır.
-
Bu malzeme en yüksek erime noktasına sahip olduğundan ve 260 °C'de bile direnç gösterebilmektedir. Bu nedenle, son segment pazarında son ürün olarak çok sayıda uygulama için daha fazla kullanılan levhaların ve filmlerin üretiminde yaygın olarak kullanılmaktadır. Havacılık, elektronik ve otomobil gibi çeşitli endüstrilerde farklı kullanımlar için kaplama malzemesi olarak tercih edilmektedir.
Saf PTFE:
Pek çok farklı uygulamada ve endüstride kullanılan en bilinen kimyasal olarak inert malzeme formlarından biridir.
Genellikle yüksek voltajlı elektrik konektörlerinde, çevresel contalarda ve ticari olta makaralarında kullanılır.
Diğer uygulamalar arasında pompa muhafazası, valf contaları, silindir kaplamaları, şaft yatağı, filtre muhafazası, pompa ve alet yapımı, elektrik endüstrisi, lazer teknolojisi, gıda ve tıp teknolojisi ve diğerleri bulunur.
-
Geniş sıcaklık aralığına yüksek kimyasal direnç gösterir.
-
Mükemmel termal stabilite ve elektrik yalıtımı sağlar.
-
Sonsuz bir raf ömrüne sahiptir.
-
Düşük sürtünme katsayısı vardır.
-
Çekme mukavemeti - 20-30 MPa
-
Özgül ağırlık - 2,14 - 2,19 g / cm 3
-
Sürtünme katsayısı - <0.1
-
Su emme - Sıfır
Cam Dolgulu PTFE :
Saf PTFE form ile karıştırılan cam elyafın bileşimidir. Basınç dayanımının artmasına yardımcı olur ve yük altında deformasyonu azaltır. Duman arıtma, rulo kaplamalar, makine parçaları, kimya mühendisliği, saf su üretimi, dağlama plakaları sahalarında kullanılır.
-
Geliştirilmiş sertlik ve aşınmaya dayanıklılık.
-
Daha yüksek sürtünme katsayısı ile daha düşük termal genleşme özelliği.
-
Aşındırıcı dolgulu uygulamalar için uygun değildir.
-
Gazlara karşı daha düşük dirençlidir ve iletken değildir.
-
Çekme mukavemeti - 31 MPa (4600 PSI)
-
Özgül Ağırlık - 2,23 - 2,26 g / cm 3
-
Termal İletkenlik - 10.6 x 10-4 cal / cm-sec- ° C
-
Doğrusal termal genleşme katsayısı –7-11,2 x10 -5 ° C (100 ° C)
Bronz Dolgulu PTFE :
Daha iyi boyutsal stabilite sağlamak ve soğuk akış ve aşınmayla birlikte sürtünmeyi azaltmak için saf PTFE malzemeye bronz ilavesidir. Diğer PTFE sınıfları gibi, bu sınıf da kullanıma göre özellikleri iyileştirmek için manipüle edilebilen bir dizi varyasyonu engeller.
-
İyi elektriksel ve termal iletkenliğe sahiptir.
-
Özellikle yük altında gelişmiş aşınma direnci gösterir.
-
Çok ekonomiktir ve kimyasallara karşı oldukça dayanıklıdır.
-
Özgül ağırlık - 2,05 - 2,12 g / cm 3
-
Çekme mukavemeti - 13-18 MPa
-
Uzama -% 90 - 300
-
Statik ve dinamik sürtünme katsayısı - 0.14 - 0.16 ve 0.12 - 0.14
Karbon Dolgulu PTFE :
Bu sınıfta, mukavemeti ve aşınma direncini artırmaya yardımcı olan saf PTFE formuna karbon eklenir. Aynı zamanda ısıl iletkenlik ve düşük geçirgenlik sağlamaya yardımcı olur. Kompresör endüstrisinde yaygın olarak kullanılır, temel kullanım aşınma halkaları, piston halkaları ve yatak halkalarını içerir. Son derece çok yönlü bir malzeme olduğu için yüksek performanslı keçeler ve silecekler için de kullanılır.
-
Özgül ağırlığı çok yüksek olan sert aşınan malzemedir.
-
İyi termal ve elektriksel iletkenlik sergiler.
-
Tüm sınıflar arasında en iyi aşınma özelliklerine sahiptir.
-
Yüksek deformasyon dayanımı vardır.
-
Özgül ağırlık - 3,8 - 3,95 g / cm 3
-
Çekme mukavemeti - 10-18 MPa
-
Uzama -% 100 -% 200
-
Shore D sertliği - 65-75
Paslanmaz Çelik Dolgulu PTFE :
Polimerin saf PTFE malzemesine çelik eklendiğinde, yüksek sıcaklıklara ve aşırı yüke direnmek için bile mükemmel güç ve stabilite kazanır. Buhar ve termik akışkan uygulamalarında kullanılabilen çok yönlü bir kalite şeklidir. Yüksek aşınma direnci nedeniyle V-Ball tipi akış kontrollü küresel vana uygulamalarında kullanılacak oldukça iyi bir malzemedir.
-
Termal ve elektriksel iletkenliği arttırmıştır.
-
Aşırı yük ve sıcaklık altında mükemmel yapıdadır.
-
Düşük sürtünme, soğuk akış ve aşınmaya karşı dirençlidir.
-
Çok ağır olmasına rağmen son derece zor aşınma kalitesine sahiptir.
-
Özgül ağırlık - 3,35 g / cm 3
-
Çekme dayanımı - Min 22 MPa
-
Uzama - Min% 220
-
Shore D sertliği - 65-69
Toz PTFE :
PTFE 'nin "ince toz" terimi ile bilinen beyaz toz formunda da mevcuttur. Teflon ince toz, aynı zamanda toz halindeki bir malzeme için de bilinen marka adıdır. Sanayi ve ev eşyalarında kaplama malzemesi olarak kullanılır.
Bu tozlar, macun ekstrüzyon işlemiyle kullanılabilir öğelere (şekiller, teller, bantlar vb.) dönüştürülür ve bunu takiben ekstrüzyon sonrası ısıtma yapılır. Bu işlem, hidrokarbonların artık çözücülerini uzaklaştırmak ve geliştirmek için kullanılır. Bu toz, diğer yağlayıcılara kıyasla sürtünmeyi azaltmaya yardımcı olacağından, büyük eylemlerde dokunma ağırlığı ölçümleri yapmak için uygundur.
Öncelikle farklı endüstrilerde kaplama malzemesi olarak kullanılır. Ayrıca, borularda, boru astarlarında ve filmlerde kullanılan tel ve kablo yalıtımı dahil olmak üzere başka kullanımları da vardır. Sinterlenmiş ve sinterlenmemiş bantlar, mikro gözenekli membranlar, ısıyla daralan makaronlar, profil şekilleri, burçlar, çekme / itme kabloları ve yüksek performanslı plastik malzeme gerektiren diğer birçok bileşen için bile kullanılmaktadır. Yaygın olarak kullanılan Toz kaplama türleri - Polyester, TGIC Polyester, Epoksi, Üretanlar, PVDF (poliviniliden florür) dir.
-
Daha çekici, yüksek kaliteli kaplama ve dayanıklılık.
-
Ekonomik olma ve çevre dostu özelliği.
-
Daha uzun süre korozyon direnci.
-
Çeşitli renk veya parlaklıkta fiziksel özellik.

PA (PolyAmid)
Makina endüstrisinde çok kullanılan bir malzemedir. Naylon olarak bilinir. Naylon6, Naylon6,6 , Naylon11 gibi çeşitleri vardır. Naylon’un en kötü tarafı su emme özelliğinin yüksek olmasıdır. Tüm naylon çeşitleri, elyaf ile takviye edilir. Naylon kristalin yapıya sahiptir. Naylon6, döküme gelen bir yapıdadır. Diğer Naylon çeşitleri zor aktığından yüksek basınç gerektiren enjeksiyon ve ekstrüzyon yöntemleri ile ancak kullanılır. Nispeten sertlik rijit, kaygan ve iyi mekanik dayanımı değerlerine sahip bir malzemedir. Poliasetal (POM) kadar kaygan bir malzeme değildir. Kimyasal mukavemeti orta değerdedir, bazı asit ve bazlara karşı mukavemeti vardır. Polyamid 6 bünyesinde su toplama özelliğine sahiptir. Bu özelliklerin iyi ve kötü yanları vardır. İyi yönü parçanın titreşim ve ani darbelere karşı dayanımı artırır. Böylece parça kullanım esnasında oluşacak dinamik gerilmelerin bünyede yok edilmesine olanak sağlar. kötü yönü ise malzemede ölçü stabilitesine ulaşmak güçleşir. Basit dişlilerde, yataklarda, civatalarda, flanşlarda, makara kayış kasnaklarında, kesim plakası, filtre plakası, tazgah tablası ve her türlü parça imalatında kullanılır.
Naylon 6 ve 6.6, müşteriye ve uygulamanın talep ve maliyet ve performans kısıtlamalarına göre uyarlanmış yeni malzemeler oluşturmak için çok çeşitli dayanç arttırıcı ve değiştiriciler ile kombine edilir.
PA 6 :
Birçok yönüyle birbirinin yerine kullanılabilen Naylon 6.6’ya çok benzeyen beyaz, yarı kristal bir termoplastiktir. Erimiş haldeki viskozitesi, Naylon 6.6’dan daha azdır ve bu nedenle genellikle işlemesi biraz daha kolaydır ve çoğunlukla kalıplama için tercih edilir. Aynı zamanda daha yüksek bir darbe direncine sahiptir, ancak sertliği daha az ve su emilimi daha fazladır.
Dişliler, Kamlar, Silindirler, Yataklar, Somun ve civatalar, Elektrikli alet gövdeleri, Elektrik konektörleri, Otomotiv yakıt depoları, Mutfak eşyaları gibi genel olarak, yüksek çalışma sıcaklıklarının gerekli olduğu yerlerde kullanılır.
-
İyi derecede sürgülü ve aşınma özellikleri vardır
-
Birçok yağa, grese ve yakıtlara dayanıklıdır.
-
Yüksek mukavemet gösterir.
-
İşleme için iyi bir seçimdir.
-
Yüksek güç gösterir.
-
İyi derecede sızdırmazlık sergiler.
-
Naylon 6.6’dan daha kolay işleme yapılabilir (kalıplanabilir)
-
Enjeksiyon kalıplamada uygundur.
-
Naylon 6.6’dan daha düşük bir kalıp büzülmesine sahiptir.
-
Yorulmaya karşı iyi direnç gösterir
-
Cam elyafı dahil edilerek ekstra sertlik elde edilebilir.
PA 6,6 :
Naylon 6.6 çok sert ve kırılmaya karşı dayanıklıdır, ancak yoğun yapısı liflerinin boyanmasını zorlaştırır. Bununla birlikte, bir kez boyandığında, yüksek bir renk haslığı vardır ve güneş ışığı altında çok az şekil değiştirir. Genel olarak, motorlu taşıt iç parçaları gibi yüksek çalışma sıcaklıklarının gerekli olduğu yer uygulama alanlarıdır.
-
Isıya dayanıklıdır ve bu özellikle burulmanın önlenmesi için avantaj sağlar
-
İyi derecede kayma ve aşınma özellikleri vardır.
-
Birçok yağa, grese ve yakıtlara dayanıklıdır
-
Yüksek mukavemetlidir.
-
Elektrik yalıtımı vardır
-
Naylon 6’dan daha yüksek plastikleştirme sıcaklığına gerek duyar.
DEHP (DiEthylHexylPhthalate)

DiEtilHeksilFtalat (DEHP, formül: C6H4 (C8H17COO) 2 ), ftalik anhidridin 2-etil-heksanol ile esterleştirilmesiyle üretilen düşük moleküler ağırlıklı bir orto-ftalattır. Uçucu olmayan, renksiz ve kokusuz viskoz bir sıvıdır, yağda çözünür, ancak suda yoktur. Düşük maliyeti ve genel olarak iyi performansı nedeniyle, DEHP, PVC'den mamul ürünlerin imalatında plastikleştirici olarak yaygın olarak kullanılmaktadır.
-
İyi jelleşme, tatmin edici elektriksel özellikler sunar ve makul soğuk mukavemete sahip oldukça elastik bileşiklerin üretilmesine yardımcı olur.
-
Düşük sıcaklıklarda oldukça iyi esneklik ve yüksek sıcaklığa karşı biraz direnç gösterir.
-
DEHP, IARC tarafından bir insan kanserojen olarak listelenmiştir
-
DEHP, bazı çalışmalarda hormon taklitçisi ve gelişimsel toksin olarak tanımlanmıştır
-
AB'de DEHP, REACH mevzuatına göre bir SVHC (çok önemli bir madde) olarak kabul edilir ve çoğu üründe kullanılamaz
-
Polar olmayan çözücülere (PVC ile paketlenmiş gıdalardaki yağlar ve yağlar) kolayca özütlenir. Bu nedenle, ABD Gıda ve İlaç İdaresi (FDA) DEHP içeren ambalajın sadece ağırlıklı olarak sudan oluşan gıdalar için kullanılmasına izin vermektedir.
PVC, vinil klorür ve vinil asetat kopolimerleri, Kateter, tüp vb. Tıbbi cihazlar, Camsı bileşimlerden yumuşak ve oldukça esnek malzemelere kadar çeşitli formülasyonların geliştirilmesinde DEHP kullanılır. İnsan sağlığı üzerindeki etkileriyle ilgili endişeler nedeniyle kullanımında azalmaya gidilse de dünyada en yaygın bilinen plastikleştiricidir.
Erime noktası -50°C, Kaynama noktası 0,5 kPa'da 250-257°C 'dir..
DINP (DiIsoNonylPhthalate)

Diisononil ftalat (DINP, formül: C26H42O4), kapalı bir sistemde ftalik anhidridin izononil alkol ile esterleştirilmesiyle üretilen yüksek moleküler ağırlıklı bir ortoftalattır. Neredeyse renksiz ve kokusuz yağlı bir sıvıdır. Suda çok az çözünür fakat alkol, heksan vb. İçinde çözünür, karışabilir ve PVC bileşimlerinde kullanılan tüm monomerik plastikleştiricilerle uyumludur.
-
Vinil ürünlere esneklik ve dayanıklılık sunar
-
Hem düşük hem de yüksek sıcaklıklarda iyi performans
-
DEHP'den daha az uçucu
-
İyi ödeme gücü, iyi esnek PVC işleme özelliklerine yol açar.
-
İç ve dış mekan uygulamalarında yoğun olarak kullanılır. Daha az uçucu olduğu için, ürünlerin nispeten yüksek sıcaklıklara maruz kaldığı ve bozulmaya karşı daha fazla direnç gösterdiği uygulamalarda etkili bulunur.
-
DINP, vinil ürünlerinin birçok hava koşullarına dayanmasına yardımcı olur, su geçirmez hale getirir ve yüksek ısı yalıtımı ve dayanıklılık sağlar
-
DINP, yumuşak ve esnek bitmiş ürünler üretmek için döşeme üreticileri tarafından PVC tozu ile birleştirilmiştir.
Erime noktası −43°C , Kaynama noktası 244-252°C -de 0.7 kPa,
Alevlenme noktası 221°C (cc)
ASA (AcrylonitrileStyreneAcrylate)
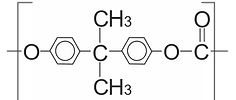
Stiren ve akrilonitril arasındaki kopolimerizasyon reaksiyonu sırasında bir aşılanmış akrilik ester elastomeri eklenerek üretilir.
UV ye dayanıklı, İyi akışkanlıktadır. ABS'ye benzer bir malzemedir.
ASA, poliolefinler, polistrenler ve naylonlar gibi zayıflık mukavemetine yol açan diğer termoplastiklerle erimektedir. Konsantre asitler, aromatik ve klorlu hidrokarbonlar, esterler, eterler ve ketonlar tarafından salgılanır. Yakıldığında zehirli duman oluşur.
Akrilonitril stiren akrilat malzeme, büyük bir tokluğa ve sertliğe, iyi kimyasal dirence ve termal stabiliteye, hava koşullarına, yaşlanmaya ve sararmaya karşı olağanüstü bir dirence ve yüksek parlaklığa sahiptir.
Akrilonitril stiren akrilat (ASA), ilk olarak BASF tarafından yaklaşık 1970 yılında Luran S olarak tanıtıldı. Amaç, ABS'ye benzer ancak daha iyi hava koşullarına dayanıklı bir malzeme yaratmaktı. Bu niteliği nedeniyle, akrilonitril stiren akrilat, otomotiv endüstrisinde ve diğer birçok dış mekan uygulamalarında yoğun bir şekilde kullanılmaktadır.
-
İyi Hava Direnci vardır
-
UV katkılı, UV dayanıklı yüksektir
-
Yüksek Isı Direnci, Yüksek Darbe Dayanımı gösterir
-
Poliolefinler, polistirenler ve naylonlar gibi diğer termoplastiklerle erir ve zayıf mukavemetli kalıplara neden olur
-
Konsantre asitler, aromatik ve klorlu hidrokarbonlar, esterler, eterler ve ketonlar tarafından bozulma gösterir
-
Yandığında zehirli duman çıkartır.
PBT (PolyButylene Terephthalate)

Enjeksiyon kalıplamada kullanılan yarı kristal bir polimerdir. Yüksek güç ve sıcaklıkta bile çok iyi sürünme direnci gösterirler. Çevresel stresten çatlamaya karşı dayanıklılık özellikleri vardır. Düşük genleşme katsayısına ve düşük su emişine sahip olmasından dolayı özellikle yüksek boyut kararlılığı gerektiren mühendislik uygulamaları için uygundur.
PC (PolyCarbonate)

Düşük özgül ağırlığa sahip bir yüksek performans termoplastiğidir.
Yüksek darbe dayanımı, düşük nem kapma oranı, iyi ısı yalıtımı, ısıya karşı kararlılığı ile önemli bir mühendilik plastiği olmasının yanı sıra kolay proses edilmesi ve işlenebirliliği sayesinde ticari polimerler arasında da yerini almıştır.
Su şişeleri, yüksek sıcaklık pişirme kapları, emniyet gözlükleri,CD’ler DVD’ler, tıbbi ekipmanlar, cephe kaplama panelleri, otomotivde genellikle aydınlatma muhafazaları üretiminde kullanılır.
Polikarbonat zor alev alır, alevden çekildiğinde söner ve çıkan bir alevi vardır. Cam berraklığında, kolay renklendirile bilen, iklim değişikliğine dayanıklı, 120°C a kadar olan sıcaklıklarda kullanılabilen, su almayan, bu nedenle elektriği iyi ileten ve mukavemeti ve tokluğu çok yüksek olup boyutları kararlıdır. Kuvvetli asit ve bazlar tarafından da etkilenirler, ayrıca gerilme yırtılmasına ağrama tehlikesi mevcuttur. İnce iş ve elektronik yapı elamanlarında, izolasyon vidalarında, aydınlatma cihazlarında, ısı etkilerinde kalan araba arka lambalarında, sofra takımlarında kullanılırlar.
Polikarbonun bir diğer özelliği de çok esnek olmasıdır. Tipik olarak oda sıcaklığında, alüminyum sacda olduğu gibi çatlama veya kırılma olmaksızın oluşturulabilir. Isı uygulamasıyla deformasyon daha basit olabilse de, onsuz küçük açılı bükümler bile mümkündür. Bu özellik, polikarbon levha stoğunu, sac metalin yaşayabilirliğinin olmadığı prototipleme uygulamalarında özellikle yararlı kılar (örneğin, şeffaflık gerektiğinde veya iyi elektrik yalıtım özelliklerine sahip iletken olmayan bir malzeme gerektiğinde).
Polikarbonun Özellikleri:
PC, "termoplastik" olarak sınıflandırılır ( "termoset" in aksine ) ve isminin plastiğin ısıya tepki verme şekli ile ilgisi vardır. Termoplastik malzemeler erime poin sıvı hale t (Polyamid durumunda 155 ° C). Termoplastiklerle ilgili önemli bir yararlı özellik , erime noktalarına kadar ısıtılabilmeleri, soğutulabilmeleri ve önemli bir bozulma olmadan yeniden ısıtılabilmeleridir. Polikarbon sıvılaştırma gibi termoplastikler yanmak yerine, kolayca enjeksiyonla kalıplanmalarına ve ardından geri dönüştürülmelerine olanak tanır .
Buna karşılık, termoset plastikler yalnızca bir kez ısıtılabilir (tipik olarak enjeksiyon kalıplama işlemi sırasında). İlk ısıtma, termoset malzemelerin (2 parçalı epoksiye benzer) ayarlanmasına neden olarak tersine çevrilemeyen bir kimyasal değişikliğe neden olur. Termoset plastiği ikinci kez yüksek bir sıcaklığa ısıtmaya çalışırsanız, yanacaktır. Bu özellik, termoset malzemeleri geri dönüşüm için kötü adaylar haline getirir. Polikarbon aynı zamanda amorf bir malzemedir, yani kristal katıların düzenli özelliklerini göstermez. Tipik olarak amorf plastikler, kristalin polimerlerde olduğu gibi katıdan sıvıya keskin bir geçiş sergilemekten ziyade kademeli olarak yumuşama (yani cam geçiş sıcaklıkları ile erime noktaları arasında daha geniş bir aralığa sahiptirler) eğilimi gösterirler.Son olarak, Polikarbon bir kopolimer, birbiriyle kombinasyon halinde birkaç farklı monomer türünden oluşur.
Polikarbonun çok sık kullanılmasının nedeni; Polikarbon levhalar uygulama da mükemmel sonuçlar doğurmakta, kolay büküm ve ısı ses izolasyonu sağlaması açısından tercih edilmektedir. Orjinal hammaddeden üretilen polikarbon levhalar darbe dayanıklılığına sahip olmakla beraber alev almama özelliğine sahiptir. Şeffaflık ve yüksek darbe direnci gerektiren uygulamalar için inanılmaz derecede kullanışlı bir plastik olmasıdır. Cama ve doğal bir UV filtresine göre daha hafif bir alternatiftir, bu nedenle genellikle gözlüklerde kullanılır.
Sınırlı enerji kaynakları ile sınırsız ihtiyaçlar karşılanmaya çalışılmaktadır. Bu noktada enerji kullanımındaki verimliliği en üst düzeyde tutmak ticari olarak kazanç sağlayacaktır. Bu yüzden özellikle sanayi mimarilerinde güneş ışığından daha fazla istifade etmek adına polikarbon levhalar kullanılmaktadır. Kullanım alanına göre çeşitli boyutlarda ve şekillerde olan bu levhalar sanayi binalarının özellikle çatı ve duvar yapımında kullanılmaktadır. Böylece hem güneş enerjisinden istifade edilmekte hem de elektrikten tasarruf yapılmaktadır.
Polikarbon levhaların özellikleri ve faydaları ;
-
Isı yalıtımına faydası vardır. İçerideki sıcaklık dengesi bu levhalar ile kontrol altına alınabilir. Böylece ortam sıcaklığı ile dışarıdaki soğuk veya sıcak hava akışı önlenmiş olur.
-
Mekanik direnç sağlar.
-
Su emme direnci gösterir. Böylelikle polikarbon levha bozulmadığı gibi içeriye de su almaz.
-
Ses yalıtımı özelliği gösterir.
-
Yangın direnci gösterir. Yanıcı özellikte değildir.
-
Her türlü eğilimli çatıda kolayca uygulanabilir.
-
Işık geçirgenliği sayesinde maliyetten kazanç sağlar.
-
Yüksek darbe dayanımı ile kırılmalara karşı dayanaklıdır.
-
Işık geçirgenliği nedeniyle cam malzemelere göre hafiflik açısından tercih sebebidir. Camdan 6 kat daha hafiftir.
-
Şeffaf yapıdaki bu levhalar aydınlatma ihtiyacına cevap verir.
-
Uzun ömürlü ve kararmayan bir yapısı vardır.
Polikarbon Levha Uygulama Alanları:
İstenilen boyutlarda ve ebatlarda üretilmektedir. Uygulama yapacak olan firma yapılacak binanın durumuna göre gerekli malzemeden üretim sağlamaktadır.
Kullanım alanına göre levhalar düz, kıvrımlı, kesitli, geometrik şekillerde üretilmekte ve istenilen amaca uygun şekilde uygulanmaktadır. u levhalar üretimi gereği birbirine geçirilme özelliğine sahiptir. Bu özellik sayesinde montajı oldukça kolay ve hızlıdır. Fakat profesyoneller tarafından yapılması daha fazla verimlilik elde edilmesi açısından önemlidir. Ayrıca levhaların montajı anında uygulanan çeşitli teknikler ile birlikte montaj vidaları alt kısımda bırakılarak görsel olarak görüntü kirliliğinin önüne geçilmektedir.
Polikarbon levhaların karşımıza çıktığı başlıca kullanım alanlar; Reklam Panoları, Otoparklar, Otobüs durakları, Spor salonları, Seralar, Giriş saçakları, Yürüyüş yolları, Binalar arası geçitler, Veranda ve teras çatıları, Kış bahçeleri, Fabrika pencereleri, Cephe uygulamaları
Uygulama alanları geniş olan oluklu polikarbon paravan bölmelerde seralarda apartman giriş kanopilerin de ve solid polikarbon ise otobüs duraklarında alışveriş merkezlerinin çatı kaplamalarında aydınlatma ve mukavemet kırılmazlık özelliğinden dolayı tercih edilmektedir.Ayrıca güvenlik amaçlı polis kalkanların da yat camlarında motosiklet ön siperliğinde koruyucu olarak kullanılmaktadır.
Polikarbon levhalarda corono virüs daha doğru bir deyim ile söylemek gerekirse covid-19 salgını pandemesi başladıktan sonra koruyucu bölme paravan olarak kullanımı artmıştır. Özellikle dayanıklılık ve rijit malzeme olması, şeffaf ve ışık geçirgenliği yüksek olması dolayısı ile tercih edilen bir malzeme olması, özellikle sağlık sektöründe maske kullanımında pet-g ürünlerinden sonra en çok tercih edilen ürün olması sebebi ile aşırı talep patlaması olmuştur.
Polikarbon pandemi sürecinde maske yapımında, eczane ve marketlerde alışverişin riskini en aza indirmek için paravan üretiminde ana malzeme olarak koruyuculuğunu sürdürmüştür.
Polikarbonu yine bahçe vb açık alanların yağmur, fırtına, rüzgarın olumsuz etkilerine karşı koruyucu olarak kullanıyorduk. Pandemiyle birlikte virüslerin oluşturduğu tehlikeye karşı da koruyucu bir kalkan olarak kullanmaya yöneldik.
Polikarbon günlük yaşamımızda koruyuculuğu ve dayanıklılığıyla bir çok alanda kullanılırken, pandemiyle mücadelede de kullanımı artarak dış tehlikelere karşı korunmada önemli bir yer edinmiştir.
AZO Materials'a göre polikarbon, 20. yüzyılın ortalarında ABD'de ve Almanya'da eş zamanlı olarak geliştirildi. Modern çağda, her biri tipik olarak kendi üretim sürecine ve benzersiz formülüne sahip çok sayıda firma tarafından üretilmektedir.
Ticari isimler, Lexan® (SABIC) veya Makrolon® (Bayer) iyi bilinen varyantları (veya "reçineleri") içerir.
Çeşitli endüstri sınıflarında polikarbon mevcuttur. Çoğu, jenerik adıyla (polikarbonat) adlandırılır ve tipik olarak, içerdikleri cam elyaf takviye miktarı ve aralarındaki eriyik akışındaki varyansla farklılaşır. Bazı polikarbonlarda, malzemeyi uzun süre Güneşe maruz kalmaktan koruyan "ultraviyole stabilizatörleri" gibi katkı maddeleri bulunur. Hatalı bir kullanım olarak ülkemizde "Leksan" olarak da anılmak istenen aslında polikarbottır.
Enjeksiyonla kalıplanabilir polikarbon, işleme sırasında malzemeyi yağlayan kalıp ayırıcı maddeler gibi başka katkı maddeleri içerebilir. Bitmiş polikarbon tipik olarak silindirler, çubuklar veya tabakalar halinde satılır.
Aşağıda; ABS , Polistiren (PS) veya Naylon gibi diğer yaygın olarak kullanılan plastiklerin darbe dayanımı ile karşılaştırıldığında Polikarbonun bağıl darbe dayanımını göstermektedir .

POE (PolyOlefin Elastomer)
POP (PolyOlefin Plastomer)
Bunlar, çok çeşitli uygulamalara sahip moleküler zincirde entegre edilmiş propilen ve etilen monomer molekül yapısına sahip PP elastomerlerdir. Etilen içeriği elastikiyet derecesini belirler ve her çeşit PE ve PP ile karıştırılma avantajına sahiptir. Stretch hood ambalaj, Streç film, PE ve metalize PP tabakaları arasındaki ara tabaka, Otomatik paketleme filmi, PE ve PP’de darbe arttırıcı, Masterbatch üretimi dolum seviyesinde artış, Esnekliğin gerekli olduğu enjeksiyon kalıplama uygulama alanlarıdır.
-
Çok elastik ve delik delmeye dayanıklıdır
-
İyi derecede optik özelliklere sahiptir
-
Çok düşük sızdırmazlık başlatma sıcaklığı (SIT) vardır
-
Sızdırmazlıktan hemen sonra yüksek ısı yalıtım mukavemeti vardır
-
Kaymaz, artan sürtünme katsayısı
-
Düşük sıcaklıklarda darbeye çok dayanıklıdır
-
0,865-0,890 g/cm3 yoğunluk
-
Ekstrüzyon ve enjeksiyon için uygunluk
-
LDPE, HDPE ve PP ile çok iyi karışım olur
-
Yiyecek taşıma kurallarına uyumludur.
POM (PolyOxyMethylene)

Asetal yüksek kristalinlik değerine sahiptir. Sert,rijit iyi nem, ısı ve çözücü mukavemetine sahiptir. Uzun süre yüksek sıcaklılıklarda kararlı kalırlar. Cam elyafı ile enjeksiyonla kalıplama ürünleri olarak imal edilmektedirler. Uygulama alanları arasında, dişliler, rulmanlar, kovanlar, çanta tokaları sayılabilir. Tıbbi malzemelerin sterilizayonunda, özel POM üretimlerine gereksinim olduğundan kullanımı fazla yaygın değildir.
Yoğunluğu, diğer plastiklere kıyasla yüksek olduğundan otomotiv sanayinde kullanımı sınırlıdır. Yoğunluğu yüksek olduğundan, fiyatı da yüksektir. Bu nedenle ambalajlamada tercih edilmez ancak elektrik bağlantıları ve anahtarları, rulmanlar, dişliler, nipeller, ve bazı sıhhi tesisat bağlantıları üretiminde kullanımı oldukça yaygındır.
Ayrıca bakınız >> İletken Plastikler / POM-C
PPE (PolyPhenyleneEther)

Lineer, kristal olmayan bir polieterdir. Polifenilen oksit olarak da bilinen polifenilen eter, sertliğini ve işlenebilirliğini geliştirmek için genellikle polistiren (PS) ile karıştırılır. PPE, birçok kimyasal maddeye dayanmasına rağmen bazı hidrokarbonlar tarafından kolayca çözünür.
PPO (PolyPhenylene Oxide)
Darbeye dayanıklı, sert ve nem absorpsiyonu düşük bir polimerdir. Genellikle modifiye edilmiş halde kullanılır. Sıcaklık dayanımı çok iyidir, geniş bir sıcaklık aralığında kullanılır ( -40 ºC ile +140 ºC). Opak bir malzemedir ve su ile bozulma dayanımı yüksektir. Kullanım alanları içinde dalgıç ve su pompaları, sayaçlar, aydınlatma gövdeleri, ofis aletleri gövdeleri, konektörler önceliklidir.
TPE (ThermoPlastic Elastomer)

Hemen hemen hiç kompoundinge gerek duymamaları, güçlendirici ve kararlılığı arttırıcı katkı maddelerine ihtiyaç duymamaları, renklendirilebilmeleri, üretimleri için daha az enerji kullanıldığı ve parça üretim kalitesini kontrol etmenin daha kolay olması olarak sayabiliriz. TPE’lerin sakıncalarını ise yüksek maliyetli malzeme olmaları, karbon siyahı gibi ucuz katkı maddeleriyle karıştırılamamaları, sıcaklığa ve kimyasallara karşı düşük dirençleri olarak sayabiliriz.
TPU (Thermoplastic PolyUrethane)
Termoset tipi poliüretanların ısı direnci ve sıkıştırma ayarlı direncine sahip değildir, ancak diğer birçok özellik benzerdir. Üstün aşınma direncine sahiptir, düşük sıcaklık esnekliği iyidir, yağ direnci mükemmeldir ve yük taşıma kapasitesi için en iyiler arasındadır.
Ayakkabı, boru, spor malzemeleri, tel ve kablo uygulamaları, hortum, tekerlekler, film contalar kaplama uygulamaları çalışma alanlarıdır.
PEI (PolyEtherImide)
Berrak viskoz sıvıdır. Mevcut diğer malzemeler arasında en yüksek katyon yoğunluğuna sahiptir. Kağıt yapımı, su arıtımı, deterjan, yapışkan, kozmetik üretiminde kullanılır.
PAS (PolyArylSulfone)
PES (PolyEtherSulfone)
PES ve PSU sınıflar polietersülfon ve polisülfon türetilen saydam, yüksek sıcaklık amorf termoplastiklerdir.
Bu ürün serisi, -58°F ila 428°F arasında bir sıcaklık aralığında büyük boyutsal stabilite ve iyi mekanik özellikler sergilemek zorunda olan yüksek yüklü mühendislik parçalarında kullanılır.
Ultrason PES ve PSU, otomotiv, membranlar, gıda servisi ve sıhhi tesisat gibi pazar sektörlerindeki çeşitli zorlu uygulamalarda kullanılmak üzere tasarlanmıştır. Çok çeşitli tipik uygulamalar şunlardır: Far reflektörleri, süt mebranları, sensörler, yemek tepsileri su arıtma membranları, manifoldlar. Bu hidrofilik, düşük protein bağlayıcı, PES membran filtreler, doku kültürü ortamı sterilizasyonu, yaşam bilimi ve mikrobiyoloji sıvı uygulamaları, klinik ve genel filtrasyon için idealdir.
PAS; esas olarak polietersülfon (PES) ile çok benzer kimyasal yapıdır.
PVDF (PolyVinyliDene Fluoride)
Dayanıklılığı, kararlılığı ve farklı mühendislik avantajları için değerlidir. Örneğin, sert termal, kimyasal veya ultraviyole koşullarına maruz kalmaya dayanıklı bir polimere ihtiyacınız varsa, gözenekli PVDF bu ortamlardaki floropolimerlerin performansına benzer üstün bir stabilite sunar. Düşük ağırlığı ve ısı iletkenliği ile yüksek kimyasal korozyon direncine sahiptir.
Çoğu kimyasal ve çözücülere dayanıklıdır. Ultraviyole radyasyona uzun süre maruz kalmadan etkilenmez.
PEK (PolyEtherKetone)
PEEK (PolyEtherEtherKetone)

Kısmi kristalli, tel kaplama ve kompozit malzemeler için uygun bir reçinedir.
Oda sıcaklığında tok,rijit uzun sürede aşınmaya karşı çok dayanıklı bir plastiktir. Sulu ortama
ve çözücülere karşı mukavemetlidir. Aromatik polieter sınıfında bulunan poliketonlar yüksek
performans plastikleri olarak kullanılırlar.
Piyasada yaygın olarak üretilen her iki polimer de (PEK-PEEK) olağanüstü mukavemeti, ısıya
ve kimyasallara karşı dayanımı sayesinde, uçak ve otomotiv endüstrisinde yaygın olarak
kullanılır. 240°C - 280°C aralığında sürekli kullanılabilecek polimerlerdir.
Polietereterketon, üstün kimyasal ve fiziksel özelliklerin gerekli olduğu durumlarda kullanılan
yüksek performanslı bir termoplastik polimerdir.
Polieter eter keton (PEEK), mühendislik uygulamalarında kullanılan poliareterketon (PAEK) ailesinde renksiz bir organik termoplastik polimerdir.
PEEK, yüksek sıcaklıklarda tutulan mükemmel mekanik ve kimyasal direnç özelliklerine sahip yarı kristalli bir termoplastiktir. PEEK'in kalıplanması için kullanılan işlem koşulları, kristalliği ve dolayısıyla mekanik özellikleri etkileyebilir. Young modülü 3.6 GPa ve gerilme mukavemeti 90 ila 100 MPa'dır. PEEK, yaklaşık 143°C arasında bir cam geçiş sıcaklığına sahiptir ve 343°C civarında erir. Bazı kaliteler 250°C'ye kadar faydalı bir çalışma sıcaklığına sahiptir. Termal bozulmaya ve hem organik hem de sulu ortamların saldırısına karşı oldukça dayanıklıdır. Yüksek sıcaklıklarda halojenler ve güçlü asitlerin yanı sıra bazı halojenlenmiş bileşikler ve alifatik hidrokarbonlar tarafından saldırıya uğrar. Oda sıcaklığında konsantre sülfürik asit içinde tamamen çözünür.
Sağlamlığı nedeniyle PEEK, rulmanlar, piston parçaları, pompalar, HPLC kolonları, kompresör plakası vanaları ve kablo yalıtımı gibi zorlu uygulamalarda kullanılan ürünleri üretmek için kullanılır. Ultra yüksek vakum uygulamalarıyla uyumlu birkaç plastikten biridir. Havacılık, otomotiv ve kimyasal proses endüstrilerinde yaygın olarak kullanılmaktadır.
PEEK’in fiziksel ve kimyasal özelliklerine bakıldığında, yapısında bulundurduğu amorf ve kristalin bölgeler sayesinde yarı-kristalin özellikte olduğu ve 343°C gibi yüksek bir erime sıcaklığına sahip olduğu görülmektedir. Camsı geçiş sıcaklığı 143°C olup, in-vitro ve invivo uygulamalarda gerekli olan 37°C vücut sıcaklığının oldukça üzerindedir ki, bu da PEEK’ten üretilen biyomalzemelerin kullanıldığı klinik çalışmaların sorunsuz bir şekilde devam ettirilebilmesini mümkün kılmaktadır.
PSU (PolySUlfone)

Çekme, basma ve sürtünme dayanımları çok yüksektir. Asit, baz ve tuz çözeltilerine direnç gösteren bu malzeme deterjan, yağ ve alkollerden etkilenmez. Tıbbî araç gereçler, gıda üretim donanım, elektriksel bağlantılar, otomotiv ektöründe sigorta ve anahtar yuvaları, korozyona dayanıklı borular, pompalar, kamera ve saat gövdeleri, batarya yalıtma plakaları, uzay ve havacılık sektöründe kullanılır.
PTFE (PolyTetraFloroEthilen)

Çok çeşitli medikal, elektronik, otomotiv ve yüksek teknoloji uygulamalarında kullanılan çok yönlü bir polimerdir. Bu, kimyasal ve ortamların çoğuna tepkimeye girmeden, yüksek sıcaklıklı ortamlarda (sürekli olarak 260°C) çalışma imkanı sunar. Buhar ve Etilen oksit sterilizasyonu ile uyumludur.
UHMWPE (Ultra High Molecular Weight Poliethylene)

Yoğunluğu 0.930–0.935 g/cm3 arasında değişen bir polietilen çeşididir. Yüksek molekül ağırlığının anlamı polimer zincirlerinin kristal yapı içinde çok sıkı bir biçimde yerleştiği veya paketlendiğidir. UHMWPE çok serttir ve termoplastik malzemeler arasında en yüksek darbe direncine sahiptir. Savunma sanayisinde kompozit zırh plakası yapımından genel amaçlı makinelere endüstrinin bir çok dalında kullanılmakta ve kullanımı gün geçtikçe artmaktadır. Ultra yüksek moleküler ağırlıklı polietilen (UHMW-PE), moleküler kütlesi 2 ila 6 milyon amu aralığında olan bir termoplastik polietilendir. Şu anda yapılmış herhangi bir termoplastik maddenin en yüksek darbe mukavemetine sahip çok sert bir malzemedir. UHMW-PE düşük bir sürtünme katsayısına, yüksek aşınma direncine ve son derece
yüksek kimyasal dirence sahiptir.