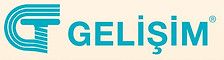


Hidrokarbonlar
Hidrojen ve karbon olmak üzere iki elementten oluşan organik bir bileşiktir. Petrol bileşiminin büyük bir kısmı değişen uzunluklardaki hidrokarbonlardan oluşur.
En küçük hidrokarbon metan, tek bir karbon atomu ve dört hidrojen atomundan oluşur. Bununla birlikte, hidrokarbonlar, zincirler, daireler ve diğer karmaşık şekiller dahil olmak üzere birçok yönden birbirine bağlanmış yüzlerce veya binlerce bireysel atomdan oluşabilir.
Hidrokarbonların özelliklerini sınıflandırmak için birkaç temel türe ayrılırlar.
Alkanlar: Bunlar doymuş hidrokarbonlar olarak adlandırılır. Yani sadece tüm karbon atomları arasında tek bağlar içerirler. Alkanlar, petrol yakıtlarının temelidir ve doğrusal ve dallı formlarda bulunurlar.
Doymamış Hidrokarbonlar: Karbon atomları arasında bir veya daha fazla çift bağa sahip olan hidrokarbonlara alken denir.
Sikloalkanlar: Bir veya daha fazla halka yapısı içeren herhangi bir hidrokarbon.
Aromatik Hidrokarbonlar: Areneler olarak da adlandırılan aromatik hidrokarbonlar, karbon atomlarının birbirini izleyen çift ve tek bağlarla bağlandığı benzersiz bir karbon molekülleri sınıfıdır. Bu molekül sınıfı, karbon atomları arasındaki bağların tek ve çift bağlar arasında bir ara bağ olduğu özel halka yapılarına sahiptir.
Bu sınıftaki moleküller, endüstriyel çözücü «benzen» içerir.
Benzen (C6H6): Diğer hidrokarbonlar gibi benzen de petrolün doğal bir bileşenidir. Oda sıcaklığında renksiz, yanıcı, tatlı kokulu bir sıvıdır ve yüksek oktan sayısına sahip olduğu için çoğu benzin karışımının bir bileşenidir.
Benzen de oldukça kanserojendir ve kemik iliği yetmezliği ve kemik kanserine neden olduğu iyi bilinmektedir. Elbette, “hoş aroması” nedeniyle tıraş sonrası ve diğer kozmetiklerde bir katkı maddesi olarak kullanıldığında kanserojenliği iyi bilinmemektedir.
En büyük benzen kullanımı (% 50), stiren ve polistren plastiklerinin ürünüdür. Ayrıca Naylon üretiminde önemli olan sikloheksan olarak bilinen bir moleküle dönüştürülür. Siklohekzan üretmek için benzenin yaklaşık% 15'i kullanılır. Böcek ilaçlarından kauçuğa kadar her şeyde daha küçük miktarlar kullanılır.
Benzen yapısı iki şekilde çizilebilir. İlkinde, çift bağ karakteri açıkça çizilir. Kısa elli versiyonda, yapıyı göstermek için halkanın içine bir daire çizilir. Benzen içindeki her bir karbon atomuna bağlı tek bir hidrojen vardır.
Aşağıdaki I. ve II. çizimleri eştir. Pratikte III. çizim kullanılır.
Benzen, renksiz, alevlenebilen, kaynama noktası 80,1 °C, erime noktası 5,5 °C olan bir sıvıdır.
Binükleer Aromatik Hidrokarbonlar: Molekülünde iki benzen halkası içeren bileşiklerdir.
Hidrokarbonlar
Hidrojen ve karbon olmak üzere iki elementten oluşan organik bir bileşiktir. Petrol bileşiminin büyük bir kısmı değişen uzunluklardaki hidrokarbonlardan oluşur.
En küçük hidrokarbon metan, tek bir karbon atomu ve dört hidrojen atomundan oluşur. Bununla birlikte, hidrokarbonlar, zincirler, daireler ve diğer karmaşık şekiller dahil olmak üzere birçok yönden birbirine bağlanmış yüzlerce veya binlerce bireysel atomdan oluşabilir.
Hidrokarbonların özelliklerini sınıflandırmak için birkaç temel türe ayrılırlar.
Alkanlar: Bunlar doymuş hidrokarbonlar olarak adlandırılır. Yani sadece tüm karbon atomları arasında tek bağlar içerirler. Alkanlar, petrol yakıtlarının temelidir ve doğrusal ve dallı formlarda bulunurlar.
Doymamış Hidrokarbonlar: Karbon atomları arasında bir veya daha fazla çift bağa sahip olan hidrokarbonlara alken denir.
Sikloalkanlar: Bir veya daha fazla halka yapısı içeren herhangi bir hidrokarbon.
Aromatik Hidrokarbonlar: Areneler olarak da adlandırılan aromatik hidrokarbonlar, karbon atomlarının birbirini izleyen çift ve tek bağlarla bağlandığı benzersiz bir karbon molekülleri sınıfıdır. Bu molekül sınıfı, karbon atomları arasındaki bağların tek ve çift bağlar arasında bir ara bağ olduğu özel halka yapılarına sahiptir.
Bu sınıftaki moleküller, endüstriyel çözücü «benzen» içerir.
Benzen (C6H6): Diğer hidrokarbonlar gibi benzen de petrolün doğal bir bileşenidir. Oda sıcaklığında renksiz, yanıcı, tatlı kokulu bir sıvıdır ve yüksek oktan sayısına sahip olduğu için çoğu benzin karışımının bir bileşenidir.
Benzen de oldukça kanserojendir ve kemik iliği yetmezliği ve kemik kanserine neden olduğu iyi bilinmektedir. Elbette, “hoş aroması” nedeniyle tıraş sonrası ve diğer kozmetiklerde bir katkı maddesi olarak kullanıldığında kanserojenliği iyi bilinmemektedir.
En büyük benzen kullanımı (% 50), stiren ve polistren plastiklerinin ürünüdür. Ayrıca Naylon üretiminde önemli olan sikloheksan olarak bilinen bir moleküle dönüştürülür. Siklohekzan üretmek için benzenin yaklaşık% 15'i kullanılır. Böcek ilaçlarından kauçuğa kadar her şeyde daha küçük miktarlar kullanılır.
Benzen yapısı iki şekilde çizilebilir. İlkinde, çift bağ karakteri açıkça çizilir. Kısa elli versiyonda, yapıyı göstermek için halkanın içine bir daire çizilir. Benzen içindeki her bir karbon atomuna bağlı tek bir hidrojen vardır.
Aşağıdaki I. ve II. çizimleri eştir. Pratikte III. çizim kullanılır.
Benzen, renksiz, alevlenebilen, kaynama noktası 80,1 °C, erime noktası 5,5 °C olan bir sıvıdır.
Binükleer Aromatik Hidrokarbonlar: Molekülünde iki benzen halkası içeren bileşiklerdir.
Hakkında
Kyäni, faydalı bileşenlerden oluşan besin takviyesi ürünlerini; benzersiz iş fırsatıyla birlikte dünya çapında 50'den fazla ülkeye ulaştırmaktadır. İdeal sağlığımızı korumak için günlük olarak Kyäni ürünlerini kullanırız, bu ürünleri başkalarıyla paylaşırız, işimizi inşa etmek ve sürdürmek için neredeyse her gün belirli bir saatimizi işe adarız ve başkalarını da Kyäni fırsatına dahil ederek veya Potato Pak ve Caring Hands programlarına katkı sağlayarak başarımızı başkalarıyla paylaşırız.
Hakkında
Kyäni, faydalı bileşenlerden oluşan besin takviyesi ürünlerini; benzersiz iş fırsatıyla birlikte dünya çapında 50'den fazla ülkeye ulaştırmaktadır. İdeal sağlığımızı korumak için günlük olarak Kyäni ürünlerini kullanırız, bu ürünleri başkalarıyla paylaşırız, işimizi inşa etmek ve sürdürmek için neredeyse her gün belirli bir saatimizi işe adarız ve başkalarını da Kyäni fırsatına dahil ederek veya Potato Pak ve Caring Hands programlarına katkı sağlayarak başarımızı başkalarıyla paylaşırız.
Sayfa Yapım Aşamasındadır.
Sayfa Yapım Aşamasındadır.
Eğitim / Bilgi / Çözüm Platformu
Kompozitler
M.Ö. 3400'de ilk kompozit Irak'ta Mezopotamyalılar tarafından geliştirilmişti. Antik toplum, kontrplak oluşturmak için ahşap şeritleri farklı açılarda üst üste yapıştırdılar.
Bunu takiben, MÖ 2181'de Mısırlılar, alçıya batırılmış keten veya papirüsten ölüm maskeleri yapmaya başladılar. Daha sonra her iki toplum da kerpiç, çanak çömlek ve tekneleri güçlendirmek için malzemelerini samanla takviye etmeye başladılar.
1200'lü yıllarda Moğollar'da kompozit yay mühendisliği başladı. Ahşap, bambu, kemik, sığır tendonları, boynuz ve çam reçinesi ile bağlanmış ipekten kompozit yapılar kullanmıyorlardı.
Sanayi devriminin ardından, sentetik reçineler polimerizasyon kullanılarak katı bir form elde edilmeye başlandı.1900'lerde polyester, fenolik ve vinil gibi çeşitli plastiklerin hayata girmesiyle kompozit yapılarda da yeni yeni tecrübeler edinilmeye başlandı. Kimyager Leo Baekeland tarafından bakalit alanında gelişmeler yaşandı. Elektrik iletmemesi ve ısıya dayanıklı olması, birçok endüstride yaygın olarak kullanılabileceği anlamına geliyordu.
1930 kompozitlerin ilerlemesi için inanılmaz derecede önemli bir zaman oldu. Cam elyaf, aynı zamanda ilk elyaf takviyeli polimer (FRP) endüstrisini başlatan Owens Corning tarafından tanıtıldı. Bu dönemde tasarlanan reçineler bugün hala kullanılmaktadır ve 1936'da doymamış polyester reçinelerin patenti alınmıştır. İki yıl sonra, daha yüksek performanslı reçine sistemleri erişilebilir hale geldi.
İlk karbon fiber 1961'de patentlendi ve daha sonra ticari olarak satışa sunuldu. Daha sonra, 1990'ların ortalarında , kompozitler, daha önce kullanılan malzemelere kıyasla nispeten ucuz maliyetleri nedeniyle imalat ve inşaatta giderek daha yaygın hale gelmeye başladı.
2000'lerin ortalarında Boeing 787 Dreamliner'daki kompozitl yapılar ile, yüksek mukavemetli uygulamalar için kullanımlarının neler olabileceğini bizlere kanıtlandı .
Ağırlık tasarrufu, bileşenler için geleneksel malzemeler yerine kompozit malzemeler kullanmanın ana nedenlerinden biridir. Kompozitler daha hafif olsalar da diğer malzemelerden daha güçlü olabilirler; örneğin, güçlendirilmiş karbon fiber, 1020 kalite çelikten beş kat daha güçlü ve ağırlığın yalnızca beşte biri olabilir, bu da onu yapısal amaçlar için mükemmel kılar.
Konvansiyonel bir malzeme türüne göre bir kompozit kullanmanın bir başka avantajı, termal ve kimyasal direnç ile elektriksel yalıtım özellikleridir. Geleneksel malzemelerden farklı olarak, kompozitler genellikle tek bir malzemede bulunmayan birden fazla özelliğe sahip olabilir.
Fiber takviyeli plastik (FRP kompozitler) gibi fiber takviyeli kompozitler, ticarileştirme için nihai ürünlerin tasarımında ve imalatında artan bir kullanım bulmaktadır.
-
Elektrikli ekipman
-
Uzay yapıları
-
altyapı
-
Borular ve tanklar
-
Evler, plastik lamine kirişler kullanılarak çerçevelenebilir
Kompozit malzeme, farklı fiziksel ve kimyasal özelliklere sahip iki malzemenin birleşimidir. Birleştirildiklerinde, örneğin daha güçlü, daha hafif veya elektriğe dirençli olmak gibi belirli bir işi yapmak için özelleştirilmiş bir malzeme oluştururlar. Ayrıca gücü ve sertliği de artırabilirler. Geleneksel malzemelere göre kullanımlarının nedeni, temel malzemelerinin özelliklerini iyileştirmeleri ve birçok durumda uygulanabilir olmalarıdır.
En az iki farklı malzemenin birbiri içerisinde çözünmeyecek şekilde birleştirilmesiyle oluşturulan yeni malzemelerdir. Amaç, ana malzemede tek başına iken mevcut olmayan bazı özelliklerin (hafiflik, dayanım, esneklik, vs) kazandırılmasıdır. Kompozit yapıyı oluşturan bileşenler arasında atom alışverişi bulunmaz, kimyasal olarak birbirlerini etkilemezler. Kompozitler genel olarak «matris» ismi verilen bir ana malzeme ve «takviye» ismi verilen daha mukavim bir malzemeden oluşur.
Biyokompozitler: Biyobozunabilir (biodegradable) polimerler (matris) ve biyobozunabilir takviye maddelerden oluşan malzemelerdir. Biyobozunabilir madde, canlı organizmalar tarafından bozunabilen maddelerdir. Doğal biyofiberlerden yapılan biyokompozitler (BBC) yenilenebilirdir, hafiftir, enerjilidir, biyobozunabilir ve çevre dostudur. Günümüzde polimer bilimi ve teknolojisi yenilenebilir kaynaklardan yapılan kompozitlere odaklanmıştır denilebilir. (Daha fazla bilgi için ilgili başlığa gidin)
Nanokompozitler: Kompoziti oluşturan bir veya daha çok fazın nano skala (<100 nm) boyutlarında olduğu bir malzemeler sınıfıdır. Nano skala bir fazın ilavesindeki genel düşünce, çeşitli bileşenler arasında bir sinerji yaratılarak malzemeden istenilen yüksek performans özelliklerine ulaşabilmektir. Partikül boyutlarının nanometre seviyeye olması kompozitteki arayüzde etkileşimleri çok yükselir, dolayısıyla malzemenin özellikleri fevkalade gelişir.
Kompozit üretim sürecini açıklarken aşağıdaki terimler sıkça kullanılır:
Parça: Yapmakta olduğunuz bitmiş ürün.
Tapa: Kalıbı oluşturmak için kullanılan, fiberglas veya diğer kompozit malzemelerde kopyalanacak asıl öğe. Fiş, gerçek parça veya neredeyse her tür malzemeden yapılmış özel bir şekil olabilir.
Kalıp: Parçanın yapılacağı ürün. Erkek ve dişi olmak üzere iki ana kalıp türü vardır. Bir erkek kalıp, kopyalanan ürünle aynıdır ve parça, kalıp üzerinde yapılır. Dişi veya boşluk kalıbı, kopyalanacak öğenin tersidir ve parça kalıbın içinde yapılır. Kelime aynı zamanda kompozit üretim sürecini tanımlamak için de kullanılabilir: Bir parçanın kalıplanması.
Laminat: Reçine ve takviye kumaşının bir kombinasyonundan yapılmış katı bir parça. Bu terim aynı zamanda bir parçanın serilmesi sürecini tanımlamak için de kullanılabilir: Bir parçanın laminasyonu.
Jel Kaplama :(veya Yüzey Kaplama) Jel kaplama terimi genellikle herhangi bir reçine bazlı yüzey kaplamasını tanımlamak için genel olarak kullanılır, ancak terim teknik olarak polyester bazlı malzemeler için geçerlidir. Yüzey kaplaması terimi, epoksi veya polyester malzemeleri tanımlamak için kullanılabilir. Yüzey kaplamaları, bir kalıbın veya parçanın yüzeyine kozmetik ve koruyucu bir kaplama görevi görecek şekilde uygulanabilen, özel olarak formüle edilmiş, kalınlaştırılmış reçine versiyonlarıdır.
Ayırıcı Ajan: Parçanın kalıptan çıkmasına yardımcı olmak için parça imalatından önce kalıp yüzeyine uygulanan herhangi bir malzeme. Bunlar mumlar, yağlar veya PVA gibi özel salım kaplamaları olabilir.
Flanş / Bölme Barajı: Çok parçalı kalıplar oluştururken fişe takılan geçici bir fikstür. Bu genellikle, simetrinin ayrılma düzlemine dik olarak, kalıplanacak malzemeler için bir yüzey oluşturur. Flanş, kalıp bölümlerinin birbirine kenetlenmesine veya cıvatalanmasına yardımcı olur ve ayrıca vakumlu torbalama işlemleri sırasında bir montaj noktası görevi görür.
Matris: kompozit yapının deformasyona uğramasını önleyerek, yapıyı bir arada tutan ana taşıyıcıdır.
Takviye: matrisin özelliğini nitelendirecek olan katkı malzemesidir. Fiberler olarak bilinirler. Mukavemet dayanım, elektrik, ses, ısı, ışık iletkenliği yada yalıtkanlıkları, sertlik yada yumuşaklık, hafiflik yada ağırlık, renksel estetiklik ama hepsinden önemlisi ekonomiklik kazandırmak için kullanılır. Genellikle takviye olarak, karbon, cam, aramid, kalsit, talk kullanılır. Tüm bunların yanında kompozit malzeme üretiminde ana hedef ekonomik şartları daha uygun hale getirmek vardır.
Bu nedenle mevcut polimerik yoğunluğun daha arttırılması için kalsit (CaCO3) takviye olarak en çok sarfedilen malzemedir.
Kompozitler, matrissel olarak dört sınıfa ayrılırlar.
Polimer Matrisli Kompozitler (PMC) : Epoksiler ve poliesterler gibi reçineler olduğu gibi yapısal üretimlerde kullanımları oldukça sınırlıdır; Cam, aramid ve boron gibi malzemelerin gerilme ve sıkıştırma kuvveti yüksektir, ancak katı halde bu özelliklerden yararlanılamaz, gerilim uygulandığında, optimum kuvvet özelliklerinin altındaki değerlerde kırılırlar.
Metal Matrisli Kompozitler (MMC) : Esneyebilir bir metal matris ile takviye malzemelerden oluşan kompozitlerdir; matris daima bir metal olarak tanımlanırsa da metaller ve hafif metal alaşımlarıdır. Metal matris kompozitlerin çalışma sıcaklıkları 200-800 0C dolayındadır; bu nedenle yüksek sıcaklık uygulamaları gerektiren ortamlara uygundur.
Seramik Matrisli Kompozitler (CMC) : Seramik veya cam matrisli CMC’ler, ileri mühendislik yapısal malzemelerin üretimlerine uygun kompozitlerdir. Yüksek sıcaklık uygulamaları sınırlı olmasına karşın, askeri, uzay ve ticari (enerji-etkin sistemler ve taşıma gibi) alanlarda geniş bir kullanım alanına sahiptir.
Karbon-Karbon Kompozitler (CCC) : Hem takviye ve hem de matris faz karbondur. Monolitik grafit kırılgandır ve kuvvetli olmayan bir malzemedir. CCC’ler oldukça yenidir ve pahalıdır; dolayısıyla kullanım alanları yaygın değildir. Ggerilme kuvveti ve gerilme modülünün yüksek olması ve bu performanslarını >2000 °C gibi çok yüksek sıcaklıklara kadar koruyabilmeleridir.
1950'lerin sonlarında karbon fiberlerin keşfi ile, şimdi karbon-karbon CCC kompozitler olarak bilinen iyileştirilmiş malzemelerin geliştirilmesine yol açtı. Bu kompozitler, karbon (veya grafit) fiberlerle güçlendirilmiş bir karbon (veya grafit) matrisinden oluşan bir malzeme ailesidir. Böylelikle karbonun çekici özellikleri, kompozitlerin yüksek mukavemeti, çok yönlülüğü ve tokluğu ile birleştirilir. CCC ailesi, tek temel kompozit olmasıyla benzersizdir.
Karbon-karbon kompozitler, basit tek yönlü fiber takviyeli yapılardan karmaşık dokuma 3 boyutlu yapılara kadar çeşitlilik gösterir. Şu anda mevcut olan çeşitli karbon elyafları ve çok yönlü dokuma teknikleri, karmaşık tasarım gereksinimlerini karşılamak için CCC uyarlanmasına izin veriyor. Elyaf tipi, yerleştirme (veya elyaf-dokuma), matris ve kompozit ısıl işlem seçimi ile, özellikler farklı uygulamalara uygun hale getirilebilir.
1960'ların başında, burun konileri ve roket nozulları gibi yüksek sıcaklıklı havacılık uygulamaları için karbon-karbon kompozitler geliştirildi. Bu kompozitler, diğer mühendislik metalik alaşımlarından daha yüksek mukavemetlere ve sertliğe uygun hale getirilebilir ve metallerin aksine, bu özellikleri Şekil 1'de gösterildiği gibi yüksek sıcaklıklarda koruyabilir.
Bununla birlikte, bu malzemelerin imalat maliyetleri yüksektir ve bu, kullanımlarını şu anda öncelikle havacılık ve askeri uygulamalarla sınırlandırmıştır. Bu nedenle, karbon veriminde bir iyileşme ile maliyetlerde azalma sağlanacaktır. % 50 karbon veriminin elde edildiği ortamdan 100 MPa'ya basınç artışı, karbon verimini% 90'a yükseltir. Bu, TWI ve diğerleri tarafından araştırılan bir teknik olan yüksek basınçlı karbonizasyon ve pirolizin temelidir.

Takviyeli plastik : Kompozitlerin yaklaşık % 90’ı polimer (plastik) esaslı matrislerden üretildiklerinden, kompozit malzemelere takviye plastikler de denir.
Kompozit malzemelerde fiberler malzemenin içinde kalır. Malzemeyi sarıp sarmalayan, dış etkenlere maruz kalan matrislerdir. Bu nedenle kompozitlerin temel özelliğini matrisler tayin eder.


Matrisin Temel Fonksiyonları
Matris fiberleri bir arada tutarak fiberlere yük aktarımında köprü göre görür.Yapıya rijitlik ve şekil verir. Matris fiberleri birbirinden izole eder. Böylece fiberler birbirlerinden bir yönü ile bağımsız davranırlar. Bu durum, örneğin, çatlak ilerlemesini durdurur ve yavaşlatır.
Matris iyi yüzey kalitesi sağlar. Matris, aşınma gibi mekanik hasarlara ve çeşitli kimyasal etkilere karşı fiberleri korur.
Seçilen matris malzemenin özelliklerine bağlı olarak, kompozitin süneklik, darbe direnci gibi performans karakteristikleri de etkilenir. Daha sünek bir matris yapının kırılma tokluğunu arttırabilir. Örneğin yüksek tokluk için termoplastik esaslı kompozit malzemeler seçilir. Kullanılan matrisin özellikleri ve fiberle uygunluğu, meydana gelen hasar modlarını (mekanizmaları) önemli ölçüde etkiler.
Bir matrisin fibere yapışma kabiliyeti yüksek olmalıdır. Yapışma kabiliyeti arttıkça, yüklerin matristen takviyeye
yeterli miktarda aktarılması mümkün olur. Ayrıca, gerilme altında fiber-matris ara yüzeyinde ayrılma veya kırılmalar engellenmiş olur.
Kompozit malzeme üretiminde kullanılan matrislerden beklenen özellikler:
1. İyi mekanik özelliklere sahip olması
2. İyi yapışma kabiliyeti olması
3. İyi tokluk özellikleri göstermesi
4. Çevresel etkilere dirençli olması olarak sıralanabilir.
Reçine Çeşitleri
Kompozit bir yapı, dokuma fiberglas kumaş gibi bir tür takviye ile birlikte kullanılan bir ısıyla sertleşen reçineden oluşur. Kompozit imalatta kullanılan üç ana oda sıcaklığında kürleme reçinesi türü vardır: 1- Polyester, 2- Epoksi , 3- Vinil Ester
Çok çeşitli uygulamalar için uygun genel amaçlı bir reçinedir. Kürleme işlemine başlamak için katalizör olarak Metil Etil Keton Peroksit (MEKP) kullanılmalıdır. Katalizasyon oranları, çeşitli çevresel koşullara uyum sağlamak için polyester reçinelerle değiştirilebilir. İnce laminasyonlarda veya son kat olarak jelkot püskürtüldüğünde, yüzey yapışkan kalabilir ve havaya maruz bırakılırsa uygun şekilde kürlenmeyebilir. Tam bir kürlenme elde etmek için, ince laminasyonlar veya son katlar ya stiren balmumu solüsyonu ya da havayı kapatmak için üzerlerine bir kat polivinil alkol (PVA) solüsyonu püskürtülmelidir. İlki ile, reçine sertleşirken balmumu yüzeyde "yüzer" ve havaya bir bariyer görevi görür. Stiren balmumu sertleştikten sonra zımparalanmalı ve PVA ılık suyla durulanmalıdır. Ayrıca:
-
Kompozit endüstrisinde en yaygın kullanılan reçinelerdir.
-
Daha ucuzdur, Kullanımı kolaydır
-
Bir miktar korozyon direnci sunar
-
Epoksilere göre daha bağışlayıcıdır
-
Hızlı kürlenir
-
Aşırı sıcaklığa ve katalizöre toleranslıdır.
Ölçümlerinde polyester reçineler kadar affedici değildir, ancak epoksiler daha fazla parça mukavemeti ve boyutsal stabilite sağlar. Ayrıca diğer malzemelere polyester reçinelerden daha iyi yapışırlar. Epoksi sertleştirici oranları değiştirilemez ve kürleme işlemi sırasında yeterli sıcaklıklar (en az 70 derece F) muhafaza edilmelidir. Epoksi reçine sistemleri, polyester reçinelerden daha pahalı olma eğilimindedir, ancak Levha Kalıplanmış Bileşik (SMC) gibi bazı onarım uygulamalarında sanal bir gerekliliktir.
Nihai mukavemeti gerektiren kompozit parçalar için, imalatçılar bir Epoksi Reçine kullanacaktır. Epoksiler, artan mukavemet özelliklerine ek olarak, boyutsal stabilite ve diğer malzemelerle daha fazla bağlanma için genellikle polyester ve vinil esterden daha iyi performans gösterir.
Vinil Ester Reçineler:
Çoğunlukla polyester ve epoksi reçineleri arasında kalan niteliklere sahiptir. Bununla birlikte, korozyon direnci, sıcaklık direnci (300 derece F'ye kadar iyidir) ve tokluk alanlarında her ikisinin de üstündedir. Yaygın kullanımlar arasında tekne gövdesi onarımı, tam tank yapımı ve kimyasal depolama tankı astarları bulunur. Polyester reçine gibi, MEKP ile katalize edilir , ancak vinil esterin üç aylık raf ömrü daha kısadır.
Vinil Ester Reçinesi, polyester ve epoksinin bir melezi olarak kabul edilir - yani işleme özellikleri, özellikleri ve fiyatı genellikle diğer ikisi arasında kalır. Vinyl Ester'in farklı olduğu yerler, yüksek korozyon, sıcaklık ve uzama direncidir.
Kompozit Üretim Teknikleri
Islak Döşeme
Bileşen, istenen kalınlığa ulaşılıncaya kadar, bir merdane ile dağıtılan birkaç kat takviye ve ıslak reçine uygulanarak bir kalıp içinde oluşturulur. Reçine daha sonra, bitmiş bileşeni üretmek için gerekirse uygulanan ısı kullanılarak kürlenir.
Bu proses, denizcilik endüstrisinde cam elyafı ile güçlendirilmiş polyester reçineleri hazırlamak için yaygın olarak kullanılmaktadır. Malzeme maliyetleri nispeten düşüktür ve süreç çok esnektir. Bununla birlikte, emek yoğundur ve yüksek stiren emisyonlarının dezavantajına sahiptir.
Püskürtme Metodu
Bir kalıba, istenen malzeme kalınlığı oluşana kadar kesilmiş elyaf takviyesi ve ıslak reçine uygulamak için bir püskürtme tabancası kullanılır. Reçine daha sonra kürlenir. İşlem, ıslak döşemeden daha hızlı ve ucuzdur, ancak mekanik özellikler daha düşüktür.
İşlem tipik olarak küvetler, tekne gövdeleri ve depolama tankları gibi büyük, nispeten basit yapılar için kullanılır.
Sıkıştırma Kalıplama (SMC)
(Sheet Molding Compound ) Levha kalıplama bileşiği veya toplu kalıplama bileşiği olan bir elyaf ve reçine yükü, önceden ısıtılmış bir kalıba yerleştirilir, bu daha sonra kapatılır ve reçine sertleşene kadar basınç altında tutulur. İşlem, A Sınıfı bir yüzey kaplaması oluşturabilir ve sac metaller için kullanılan damgalama işlemine benzerlik, otomotiv endüstrisindeki uygulamalara yol açmıştır.
Isıtmalı takımlara yapılan yüksek yatırım, işlemin yalnızca orta ila yüksek hacimli üretim için uygun olduğu anlamına gelir.
Kalıp sıcaklığı 120-170°C arasındadır. Kalıplama süresi ve kalıplama basıncı; parçanın büyüklüğü, kalınlığı ve SMC tipine bağlı olarak değişmektedir. SMC hazır kalıplama bileşiminin, çelik, alüminyum ve diğer çinko metal döküm gibi malzemelere göre toplam maliyet/performans getirisinde sağladığı avantajlar, tasarımcılar ve mühendisler tarafından sıkça ifade edilmektedir. Tek bir kalıpta birçok parça birleştirilebilir. SMC ürünler hafiftir ve yüksek sertlik ve dayanım özelliklerine sahiptir. SMC kalıplama, metal kalıplamada gereken birden fazla ekipmanın aksine tek bir ekipman ile işlenebildiğinden, genellikle metal kalıplama prosesinden daha ucuzdur. Ayrıca SMC kalıplama ekipmanının yapımı da daha kısa sürede gerçekleşir. Tüm bu avantajların toplamı SMC kompozit ürünlerini özellikle otomobil üreticileri için cazip hale getirmektedir. Günümüzün otomobil pazarlarında firmalar, seri üretim ve daha hızlı tasarım/üretim programları ile otomobil ve kamyon modellerinde ekonomik farklılıklar yaratacak yollar aramaktadır. SMC bu avantajlara bağlı olarak etkileyici bir performans geliştirmektedir.
SMC üretimi ve kalıplanması için gereken sermaye yatırımı metallerle karşılaştırıldığında oldukça düşük olmasına rağmen, diğer kompozit proseslerine göre önemli ölçüde yüksektir. Bu yüzden, SMC parçaların üretiminin tüm harcamaların ekonomik seyrine, üretim hacmine, son ürünün ve ikincil işlemlerin maliyetine bağlı olarak yapılması kritik bir noktadır. SMC ürünlerin pazarda geleneksel malzemelerden yapılmış parçaların yerini almaya başlaması nedeniyle, rakip malzemelerin performans ve ekonomik analizlerinin doğru ve kesin bir şekilde yapılması önem kazanmıştır. Yatırım riskleri SMC’ler için oldukça yüksektir
Ev aletleri endüstrisinde de SMC uygulamalarına olan talep artmaktadır. Örneğin, bir bulaşık makinesi iç kapağının SMC’den üretimi geleneksel olarak çelik kapı tasarımı ile karşılaştırıldığında, tek aşamada kalıplama ile birkaç farklı parçayı bir araya getirmektedir. SMC bulaşık makinası kapağı uygulaması, SMC’nin kimyasal bir ortama maruz kalan bir üründe göstermiş oldu¤u üstün performans nedeniyle birçok açıdan kullanılabileceğini, kanıtlamaktadır. Diğer SMC ev aletleri uygulamaları klimalar, buzdolapları, kızartma makineleri, bilgisayar ve büro malzemelerini kapsamaktadır.
Enjeksiyon Kalıplama
Dökme kalıplama bileşiği ısıtılır ve reçine kürlenene kadar basınç altında tutulduğu ısıtılmış bir kalıba enjekte edilir. İşlem, kısa bir döngü süresinin elde edilebildiği nispeten küçük bileşenler için kullanılır. Yüksek alet maliyeti, işlemin yalnızca orta ila yüksek hacimli üretime uygun olduğu anlamına gelir.
Reçine Transfer Kalıplama (RTM)
(Resin Transfer Molding) Isıtılmış bir kalıba bir elyaf preform veya kumaş yerleştirilir. Reaktif reçine karıştırılır ve basınç altında kalıba enjekte edilir. Reçine kürlenene ve parça çıkarılana kadar basınç korunur. Proses, karmaşık, yüksek yüklü parçalar için uygundur ve çok çeşitli endüstrilerde kullanılmaktadır. Vakum destekli reçine transfer kalıplama (VARTM), vakumun kapalı kalıba uygulandığı ve reçinenin düşük basınç altında enjekte edilmesine izin veren prosesin bir varyantıdır. Aletler üzerindeki yükler bu nedenle daha düşüktür ve tekne gövdesi veya rüzgar türbini kanatları gibi büyük yapıları imal etmek için daha ucuz, daha büyük aletlerin kullanılmasına izin verir. Diğer bir varyant, yapısal reaksiyonlu enjeksiyon kalıplamadır (SRIM). Bu, yüksek reaktif reçineleri kullanır, öyle ki kalıbın reçineyi sertleştirmek için ısıtılmasına gerek kalmaz, ancak döngü süresini azaltmak için sıklıkla ısıtılır.
RTM parçaları proses ve tasarım koşullarına bağlı olarak kalıp başına saatte çok sayıda parçanın kalıplanmasına olanak tanımaktadır. RTM kapalı bir kalıp sistemi olması sebebiyle, çalışma ortamına açık kalıplardan daha az uçucu organik madde açığa çıkarırlar. Kalıp devir süreleri el yatırması ve püskürtme yöntemlerine göre daha kısadır. RTM kalıplarının maliyeti diğer kapalı kalıplama yöntemlerinde kullanılan kalıplara oranla daha ucuzdur. Kalıplanmış parçaların her iki yüzeyi de düzgündür. Dolgu sistemleri maliyeti düşürmekte, alevlenmeme ve duman yaymama özellikleri, daha iyi yüzey görünümü ve daha yüksek kırılma dayanımı gibi performans özellikleri katmaktadır.
Kalıp ve ekipman maliyetleri, el yatırması ve püskürtme yöntemlerine göre yüksektir. RTM, orta ölçekli üretim hacmine sahip bir üretim yöntemidir. Enjeksiyon basınçlarının ayarlanması, kal›p tasarımı ve üretimi, kilit ve conta sistemi ele alındığında proses daha karmaşıktır.
Başlıca RTM uygulamaları; kamyon gövde parçaları, otomobil gövde panelleri, otobüs panelleri, spoiler, gösterge panelleri, tıbbi cihazlar, depolama tankları, araç koltukları, kimyasal pompalar, küçük tekneler gibi denizcilik parçaları, rüzgar enerjisi tribün kanatlar›, uçak parçalar›, mermi gövdeleri, bisiklet gövdeleri ve kapılardır.
Filament sargısı
Bir elyaf kıtığı reçine banyosundan geçirilir ve gerilim altında dışbükey bir mandrele uygulanır. Mandrel döndürülür ve lif salımı, istenen kalınlığa ulaşılana kadar istenen geometride lifleri yerleştirmek için hareket ettirilir. Daha sonra gerekirse yüksek sıcaklık kullanılarak kompozitin sertleşmesine izin verilir. İşlem, yüksek hacimli üretim için otomatikleştirilebilir ve borular ve tahrik milleri gibi boru şeklindeki yapıların yanı sıra basınçlı kaplar veya monokok bisiklet çerçeveleri gibi daha özel yapılar için kullanılır. Son iki uygulamada mandrel bileşen içerisinde kalacaktır. Prosesin bir varyantında, reçine banyosuna olan ihtiyacı ortadan kaldıran, ancak yüksek sıcaklıkta bir kürleme aşaması gerektiren önceden emprenye edilmiş elyaf kıtığı veya yarık prepreg kullanılabilir.
Prepreg
(önceden emprenye edilmiş elyaf) reçine ile emprenye edilmiş elyaf, kumaş veya keçelerden oluşur. Isıyla sertleşen prepregler, reçinede sertleştiricileri içerir ve bu nedenle sınırlı bir raf ömrüne sahiptir ve genellikle soğutma altında saklanır. Kullanmadan önce prepreg, yoğunlaşmayı önlemek için oda sıcaklığına getirilir ve katlar gerekli şekil ve yönde kesilir. Bunlar, havanın hapsolmasını önlemek için bir silindir kullanılarak istenen kalınlıkta bir kalıpta istiflenir. Laminat, boşaltılan bir vakum torbasında kapatılır ve daha sonra parça, ilave basınç altında geleneksel bir fırında veya bir otoklavda sertleştirilir. Otoklav işleme, daha az gözeneklilik ve üstün mekanik özellikler sağlar, ancak özellikle büyük bileşenler için yavaş bir döngü süresi ve pahalı ekipman gerektirir. Prepreg, yüksek mekanik özelliklerin gerekli olduğu ve yüksek işleme maliyetinin gerekçelendirilebildiği durumlarda kullanılır. Örnekler arasında havacılık yapıları, spor malzemeleri ve rüzgar türbini kanatları yer alır.
Üretim sırasında pratik olması, ek olarak herhangi bir reçine ve sertleştirici kullanımına gereksinimi ortadan kaldırır ve reçine emdirilmemiş elyafa göre kalıp yüzeyine, birbiri üstüne yapışması ve fiberlerin ayrılmamasından dolayı serim işlemi de daha kolay gerçekleşmektedir. Ayrıca kürleşme süresi de el-yatırması, vakum infüzyon ve vakum torbalama yöntemlerine göre daha kısadır.
Reçine verme işlemi önceden gerçekleşmiş olduğu için kuru kalma yada fazla reçine emme gibi durumlar söz konusu değildir. Bu durum da üründe herhangi bir mukavemet kaybı olmaksızın standart ürünler elde edilmesini sağlar. Kullanılan prepreg çeşidine bağlı olarak reçine/elyaf oranı %35-%50 arasında değişim göstermektedir.
Prepreg’le üretimin avantajları olduğu gibi bazı dezavantajları da vardır. Öncelikle kendisi de üretim yöntemleri de diğerlerine göre oldukça pahalıdır. Otoklav yönteminde sıcaklık, kürleşme grafiğine uygun olarak 120-180oC civarında ayarlanıp aynı zamanda da 3-7 MPa basınç altında gerçekleştirilir. Fırınla üretimde ise yine kürleşme sıcaklığı, uygun sıcaklıklara ayarlanmalıdır. Bu tip otoklav ve fırınlar oldukça pahalı endüstriyel ürünlerdir.
Prepreglerin saklama koşulları da üretici için büyük bir zorluktur. Oda şartlarında 4-6 haftaya kadar saklanabilen çeşitleri olsa da genel olarak -20oC civarında dondurucuda saklanma koşulları vardır. Ayrıca dondurucudan çıkarıldıktan sonra kullanılmaları gerekmektedir.
Pultrüzyon:
Cam elyaf takviye malzemesinin amaca uygun bir reçine ile birleştirilerek sıcak bir kalıptan çekilmesi ile oluşturulan üretim taknolojisidir.
Sistemde, cam elyaf lifleri ve cam elyaf keçenin reçine ile ıslatılıp sıcak kalıbın içinde polimerize edilip katı malzeme oluşturulur. Endüstriyel levha,profiller ve elektrik sanayi levha,profilleri üretimine uygun bir yöntemdir.
Elyaf kıtıkları, bir bobin askısından alınır ve bir reçine banyosundan beslenir, ardından reçineyi, eksenel takviye ve sabit enine kesite sahip bir ekstrüde parça üretmek üzere kürleyen ısıtılmış bir ekstrüzyon kalıbından çekilir. Uygulamalar arasında ızgaralar, merdiven bölümleri, köprü parçaları ve korkuluklar bulunur. İşlem otomatikleştirilebilir ve düşük maliyetli ham maddeler kullanır, bu da onu yüksek hacimli uygulamalar için uygun hale getirir.
Pultrüzyon sisteminde matris reçineler şunlardır:
-
Ortofitalik doymamış Polyester Reçineler
-
İzofitalik Doymamış Polyester Reçineler
-
Vinil Ester Reçineler
-
Epoksi reçineler
Takviye malzemeler şunlardır:
-
Cam Elyafı
-
Cam elyaf Fitil
-
Continue cam elyaf
-
Cam Elyaf Dokumalar
-
Yüzey tülü
-
Cam elyaf combi
-
Cam elyaf multiaxiel
Vakumlu İnfüzyon:
Reçine infüzyonu olarak da adlandırılan vakumlu infüzyon, reçineyi bir laminata sürmek için vakum basıncını kullanan bir imalat tekniğidir. Kuru malzemeler kalıba serilir ve reçine eklenmeden önce vakum basıncı uygulanır. Tam bir vakum elde edildiğinde reçine, vakum tüpü aracılığıyla laminatın içine itilir. Vakumlu infüzyon işlemi, elle yatırma veya vakumlu torbalamadan daha iyi bir fiber-reçine oranı sunar.
Vakum, düşük viskoziteli bir reçinenin lifli bir ön kalıbı emprenye etmesine neden olmak için kullanılır. En yaygın olarak, reçinenin ön kalıbın yüzeyi üzerinden akmasına ve ardından kalınlık boyunca emprenye edilmesine neden olarak reçinenin ön kalıp içinden geçmesi gereken mesafeyi en aza indirir. İşlem, tekne gövdeleri veya rüzgar türbini kanatları gibi büyük parçalara çok uygundur. Takım, işlem sırasında önemli yükler taşımak zorunda değildir.
Vakum infüzyonu, geleneksel olarak vakumla paketlenen parçalara göre bir dizi iyileştirme sağlar.
Bu faydalar şunları içerir:
-
Daha iyi elyaf-reçine oranı
-
Daha az atık reçine
-
Çok tutarlı reçine kullanımı
-
Sınırsız kurulum süresi
-
Temizleyici
İndüksiyon Isıtma:
İlk defa, indüksiyonlu ısıtma, karbon fiber takviyeli termoplastik kompozitlerin kalınlığı sayesinde hassas bir şekilde kontrol edilebiliyor. Birleştirilecek kompozit bileşenlerin yerleştirilmesi sırasında, indüksiyonla ısıtmanın gerekli olmadığı katlar arasına ince elektriksel olarak yalıtkan tabakalar (gazlı bez) yerleştirilir. İnce yalıtım katmanlarının dahil edilmesi, yalnızca birleştirilen parçalardan birinde ve yalnızca eklemin yakınında bitişik hizalı olmayan karbon katmanları arasında gereklidir.
Isıtma denemeleri, tekniğin indüksiyonlu ısıtma sırasında indüklenen alternatif elektrik akımlarının üretilmesini başarıyla engellediğini göstermiştir. Malzemeyi kaynak veya sertleştirme için olağan şekilde ısıtmak ve eritmek için yalıtım katmanlarının (gazlı bez) bulunmadığı katlar arasında elektrik akımı indüklenir. Bu şekilde, malzemenin kalınlığı boyunca indüksiyonla ısıtmanın konsantrasyonu hassas bir şekilde kontrol edilebilir. Bu yaklaşım, bileşenlerin dış yüzeyinin aşırı ısınmasını önler ve üretilen bağlantıların kalitesini iyileştirir.
Teknik, özellikle kalın parçaların (4 mm'den daha kalın) söz konusu olduğu durumlarda, mevcut son teknoloji proseslere göre avantajlar sunan aday bir kaynak işlemi olarak düşünülebilir. Son teknolojiye kıyasla takım maliyetleri de en aza indirilmiştir. Tekniğin daha geniş bir şekilde uygulanması, ısının ara yüzeyde odaklanmasının bir yapıştırıcıyı sertleştirmek için kullanılabildiği, termoset kompozitlerin yapışkanla birleştirilmesi gibi uygulamalar için odaklı bir ısıtma işlemi olarak düşünülmelidir.
Bu teknikte: Karbon fiber kompozitlerin mevcut son teknoloji indüksiyon kaynağı, indüksiyon bobinine en yakın kompozit parçaya yerleştirilmesi için yüksek derecede termal olarak iletken bir ısı emici malzeme gerektirir . Bu, yüzeydeki fazla ısıyı giderir ve kaynak arayüzünün yeterince ısınmasına izin verir.
iİletken ve yalıtkan (izolatör) katlar ısının akışı görülmek için açılı olarak dizilir.
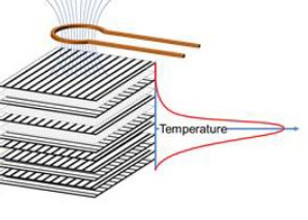

Bir dakikalık ısıtma sonrası termal görüntü ve alt ve üst katmanlardaki sıcaklık-zaman değişim grafiği
Termoplastik kompozitler (TPC'ler), onları havacılık endüstrisi için çekici bir seçenek haline getiren ısıyla şekillendirme ile hızlı bir şekilde işlenebilir, ancak henüz yapısal uygulamalar için önemli bir TPC alımı olmamıştır. Bunun arkasındaki nedenlerden biri, katılım için sınırlı teknolojidir. TWI, yakın zamanda, indüksiyon kaynağı termoplastik kompozitlerinin ilave koruyucu olmadan kontrolünü iyileştirmek için yeni bir yöntem icat etti. Hizalanmamış karbon lifleri içeren bitişik katmanlar arasına ince bir elektriksel olarak yalıtım katmanı (gazlı bez) eklemek, elektrik yollarının oluşmasını önler ve hacimsel ısıtma devre dışı bırakılır. TWI'nin tekniği, üretilen ısının bağlantı arayüzünde yoğunlaşması avantajına sahiptir, bu da termal hasarı önlemek için kompozit yüzeyinden fazla ısının uzaklaştırılması sorununu ortadan kaldırır. ve bu nedenle sürecin kontrolünü geliştirir. Bu teknik kullanılarak 32 MPa'ya kadar eklem güçleri elde edilmiştir.
Kompozitlerin sınırlamalarından biri, prefabrike parçaların birleştirilmesidir. Termoset kompozitler söz konusu olduğunda, karmaşık ön işlem ve ısıtma mekanizmalarına ihtiyaç vardır. Termoplastik kompozitler, birleştirmeye daha iyi katkıda bulunur, ancak yapıştırma hattında yabancı bir malzeme kalmadan sadece arayüzün ısıtılmasını sağlamakta her zaman bir zorluk vardır.
Son yıllarda, özellikle havacılık gibi üst düzey uygulamalar için termoplastik kompozitlere olan ilginin yeniden arttığını gördü. Tek koridorlu uçaklar için öngörülen üretim oranları, termoset kompozitlerin mevcut ekonomik üretim kapasitesini aşıyor. Termosetlerle karşılaştırıldığında, termoplastik kompozitler, artan üretim oranlarını karşılamak için daha kısa işleme süreleri sunabilir ve iyi solvent direnci, sınırsız raf ömrü ve daha iyi tokluk (darbe direnci) gibi potansiyel ek faydalar sunar. Termoplastik kompozitler, konsept olarak sac metal bileşenlerin damgalanmasına benzer bir işlemde, polimer matrisin ısıyla şekillendirmeye izin verecek kadar yeterince ısıtılmasıyla daha hızlı işlenebilir. Bu, TPC'leri havacılık ve uzay endüstrisi için çekici bir seçenek haline getirir, ancak henüz yapısal uygulamalar için önemli bir TPC alımı olmamıştır.
Bunun arkasındaki nedenlerden biri katılmaktır. Kompozitlerin kullanımı net şekle yakın bir imalat sunabilse de, genellikle aşağıdaki gibi çeşitli nedenlerle bileşenlerin birleştirilmesi için bir gereksinim vardır;
-
daha uygun maliyetli
-
bileşenler tek bir parça olarak üretilemeyecek kadar büyük
-
Farklı üretim koşulları gerektiren hibrit malzemeler kullanılır
-
bileşenler farklı fiziksel konumlarda yapılır
Şu anda kullanımda olan bağlama yöntemleri, hava taşıtı endüstrisinin hatırı sayılır performans verilerine ve tekniklere güven duyması nedeniyle metal yapıları birleştirmek için kullanılanlardan uyarlanmıştır.
Termosetler geleneksel olarak mekanik bağlama veya yapışkan bağlama kullanılarak birleştirilir. Mekanik bağlama, yük taşıyan lifleri kesen ve deliklerin etrafına gerilim konsantrasyonları veren deliklerin üretilmesini gerektirir. Yapıştırıcı bağlama sorunsuz değildir ve genellikle yapıştırıcıyı nispeten küçük bir bağlantı noktasında sertleştirmek için büyük prefabrike parçaların bir fırında ısıtılmasını gerektirir.
Bununla birlikte, termosetlerin aksine, TPC'ler füzyon bağlama (kaynak) ile birleştirilebilir; delik açarak hasara neden olmayan ve tutturucunun çıkarılmasıyla ağırlık tasarrufu ve delik delme adımının ortadan kaldırılmasıyla hız açısından daha fazla avantaj sunan bir işlem. Termoplastik kompozitlerin kaynağı, arayüzü cam geçiş sıcaklığının, Tg'nin (amorf polimerler için) veya erime noktasının, Tm'nin (yarı kristalin polimerler için) üzerindeki bir sıcaklığa ısıtan herhangi bir işlemdir. Basınç uygulaması altında, polimer zincirleri, soğutma sırasında kaynaklı bir bağlantı oluşturarak arayüz boyunca yayılabilir . İşlem hızlı olabilir ve çok az yüzey hazırlığı gerektirir veya hiç gerektirmez.
1980'lerde APC-2 (AS4 karbon fiber takviyeli Polietereterketon veya PEEK) gibi termoplastik kompozit malzemelerin piyasaya sürülmesinden bu yana, TPC'lerin füzyon bağlanması üzerine birçok çalışma yapılmıştır. Mevcut sayısız füzyon bağlama tekniğinden üçü, endüstriyel uygulamalar için en uygun oldukları düşünüldüğünden, birçok araştırma çalışmasının konusu olmuştur; indüksiyon, dirençli implant ve ultrasonik .
İndüksiyon kaynağında, uygulanan alternatif manyetik alana yanıt olarak indüklenen girdap akımlarından Joule kayıpları yoluyla ısı üretilir. Manyetik alan, iletken bir çalışma bobininden geçen alternatif bir elektrik akımı ile üretilir. İndüklenen girdap akımları, kaynak arayüzüne yerleştirilmiş bir metal implantta veya ana kompozit malzemelerdeki karbon liflerinde akabilir.
Son yıllarda termoplastik kompozit malzemelerin birleştirilmesi için endüksiyon kaynağı uygulanmıştır. Fokker Aerostructures, Gulfstream G650 kuyruk bölümünü tasarlayıp geliştirdi ve dümen ve asansör için yeni bir endüksiyon kaynağı yöntemini sanayileştirdi . Fiberforge Corporation, Sikorsky CH-53K üzerindeki parçaları birleştirmek için tekniği de uyguladı. Bununla birlikte, teknik henüz geniş çapta benimsenmemiştir ve bunun bir nedeni, ısıl bozulmayı önlemek için sürecin zayıf kontrolüdür . İhtiyaç duyulan şey, kaynak ara yüzüne ilave tutucular yerleştirilmeden ısıyı ihtiyaç duyulan yere odaklayan bir tekniktir.
Karbon fiber kompozitlerin mevcut son teknoloji indüksiyon kaynağı, indüksiyon bobinine en yakın kompozit parçaya yerleştirilmesi için yüksek derecede termal olarak iletken bir ısı emici malzeme gerektirir . Bu, yüzeydeki fazla ısıyı giderir ve kaynak arayüzünün yeterince ısınmasına izin verir.
Sürekli karbon fiber kompozitlerde indüklenecek girdap akımları için bitişik hizalı olmayan katların olması gerektiği iyi bilinmektedir. Tüm takviye liflerinin aynı yönde tek yönlü olarak hizalandığı katmanlı bir yapı, kapalı bir elektrik yolu oluşturulamayacağı için endüksiyonla hacimsel olarak ısınmayacaktır . Neyse ki, yapısal kompozit uygulamalarının çoğu, gerekli mekanik performansa ulaşmak için yarı-izotropik bir yerleşim kullanır ve bu nedenle, indüksiyonla hacimsel olarak ısıtılabilir.
Yarı-izotropik laminatın bitişik hizalı olmayan katları, komşu katmanlardaki karbon lifleri arasındaki teması önlemek için yeterince ayrılırsa, kapalı elektrik yolları artık oluşamaz ve bu nedenle hacimsel ısıtma devre dışı bırakılır. Bu ayırma, hizalı olmayan karbon lifleri içeren bitişik katmanlar arasına ince bir elektriksel olarak yalıtkan katman (gazlı bez) yerleştirilerek elde edilebilir (Şekil 1). Özel bir parametre ve özellik kombinasyonu kullanan bu tekniği, üretilen ısının endüksiyon bobininin yakınlığının en büyük olduğu kompozitin üst yüzeyine yakın olmaktan ziyade eklem arayüzü çevresinde yoğunlaşması avantajına sahiptir. Bu, ısıyı gereken yere odaklar, ve termal hasarı önlemek için kompozit yüzeyinden fazla ısının çıkarılması sorununu ortadan kaldırır. Kaynaklı eklemi üretmek için gereken ısı, kaynak arayüzünün yakınındaki yalıtım katmanlarının çıkarılmasıyla üretilir. Ayrıca, iletken malzemede indüklenen akımın yoğunluğu katlanarak yüzeyden azaldığından, yalıtım katmanlarının sadece birleştirilen parçalardan birine yerleştirilmesi gerekir; iş bobinine en yakın olanı.
Bu tekniğin kullanılmasıyla üretilen ısı, termoplastik kompozitlerin füzyonla birleştirilmesi ve aynı zamanda yapışkan kürleme için kullanılması için yeterlidir; termoset kompozitleri birleştirmek için kullanılan bir işlem.
Odaklanmış ısıtma etkisini göstermek için, her biri 0/90 yönünde üç Karbon / PEEK katı içeren iki termoplastik kompozit laminat üretildi. Bir laminat ("iletken"), bitişik hizalanmamış katların temas etmesine izin verecek şekilde geleneksel şekilde üretildi. Diğer laminat ("İzolatör") bitişik hizalı olmayan katlar arasında ince bir yalıtım katmanı kullanılarak döşendi. Yalıtım tabakası için kullanılan malzeme 10 gsm'lik dokunmamış cam elyaf yüzey dokusuydu. Üretim sırasında yalıtım katmanının her iki tarafına da bir PEEK film katmanı yerleştirildi; laminatın konsolidasyonu sırasında cam yalıtım katmanını ıslatmak için ek PEEK gerekliydi.
Şekil 2'de gösterilen konfigürasyonda yan yana yerleştirildiğinde; "İletken" üzerindeki "izolatör" ve dolayısıyla çalışma bobinine daha yakın olan ısıtma, iki laminat arasındaki arayüzde yoğunlaştırıldı. İki laminat, bir termal görüntü kamerası kullanılarak alt laminatın yüzey sıcaklığının ölçülmesine izin vermek için 45 derece kaydırıldı. Bir Cheltenham İndüksiyonla Isıtma TR1 1kW indüksiyon güç kaynağı, 60 saniye süreyle 165 kHz frekansta dört dönüşlü bir solenoid bobin aracılığıyla alternatif bir elektromanyetik alan uygulamak için kullanıldı. Şekil 2'de işaretlenen iki konumdaki sıcaklık, bir FLIR T250 termal görüntü kamerası kullanılarak testler sırasında on saniyelik aralıklarla ölçülmüştür.
Tipik Kompozit Malzemeler
-
Fiberglas : Kompozit endüstrisinin temelidir. Hafiftir, orta derecede gerilme mukavemetine sahiptir ve kullanımı kolaydır.
-
Karbon Fiber : Otomobil yarışlarından havacılığa kadar her yerde bulunur. Fiberglass ve Kevlar'dan daha pahalı olmasına rağmen, sektördeki en yüksek çekme, basınç, eğilme ve eğilme mukavemetine sahiptir. Karbon Fiber, genellikle yük taşıyan parçalar gibi daha yüksek seviyede mukavemet gerektiren projeler için kullanılır.
-
Seramik matris kompozit: Seramik bir matris içinde yayılmış seramik. Bunlar termal şok ve kırılmaya dirençli oldukları için normal seramiklerden daha iyidir.
-
Metal matris kompozit : Bir matris boyunca metal bir yayılma
-
Betonarme : Çelik takviye çubukları gibi yüksek çekme dayanımlı bir malzeme ile güçlendirilmiş beton
-
Cam elyaf takviyeli beton : Yüksek zirkonya içeriğine sahip cam elyaf bir yapıya dökülen beton
-
Yarı saydam beton : Optik fiberleri çevreleyen beton
-
İşlenmiş ahşap : Diğer ucuz malzemelerle birleştirilmiş üretilmiş ahşap. Bir örnek, sunta olabilir. Bu kompozitte kaplama gibi özel bir malzeme de bulunabilir.
-
Kontrplak : Çok sayıda ince ahşap katmanının farklı açılarda birbirine yapıştırılmasıyla tasarlanmış ahşap
-
Tasarlanmış bambu : Bir tahta yapmak için birbirine yapıştırılmış bambu elyaf şeritleri. Bu, ahşaba göre daha yüksek basınç, çekme ve eğilme mukavemetine sahip olması nedeniyle kullanışlı bir kompozittir.
-
Parke : Genellikle sert ağaçtan bir araya getirilmiş birçok ahşap parçadan oluşan bir kare. Dekoratif parça olarak satılmaktadır.
-
Ahşap-plastik kompozit : Ya ahşap lifi ya da plastikte dökme un
-
Çimento bağlı odun lifi : Çimentoda dökülmüş mineralize ağaç parçaları. Bu kompozitin yalıtkan ve akustik özellikleri vardır
-
Fiberglas : Nispeten ucuz ve esnek olan bir plastikle birleştirilmiş cam elyafı
-
Karbon Fiber takviyeli polimer : Yüksek mukavemet / ağırlık oranına sahip plastikten karbon fiber set
-
Sandviç panel : Üst üste katmanlanmış çeşitli kompozitler
-
Kompozit bal peteği : Bal peteği şekli oluşturmak için birçok altıgende kompozit seçimi.
-
Kartonpiyer : Yapışkanlı kağıt. Bunlar el sanatlarında bulunur
-
Plastik kaplı kağıt : Dayanıklılığı artırmak için plastikle kaplanmış kağıt . Bunun kullanıldığı yere bir örnek iskambil kartlarıdır
-
Sözdizimsel köpükler : Metal, seramik veya plastiklerin mikro balonlarla doldurulmasıyla oluşturulan hafif malzemeler. Bu balonlar cam, karbon veya plastik kullanılarak yapılır.
-
Çelik Yelek : Elyaf takviyeli plastik endüstrisinde kabul gören ilk yüksek mukavemetli sentetik elyaflardan biridir. En büyük özellikleri darbe ve aşınma direncinin yüksek olmasıdır. Kanolar, uçak gövdesi panelleri ve basınçlı kaplar gibi yüksek darbe ve aşınmanın beklendiği parçalar için idealdir.
-
PVA : Polivinil Alkol, parça kürlenirken havayı dışarıda tutmak için ince laminasyonlara veya son katlara püskürtülür. PVA daha sonra ılık su ile durulama yapılmalıdır.
-
Stiren Balmumu : Kürleme işlemi sırasında havayı parçanızdan uzak tutmak için başka bir çözümdür. PVA'nın aksine, parafin, kürlenirken reçinenin yüzeyinde kalır. Stiren balmumunun sertleştikten sonra zımparalanması gerekir.
-
MEK-P (Metil etil keton peroksit) : Organik Peroksitler grubundadır. Hızlandırıcı veya ısıyla aktive olan ve poliester reçinenin ve vinilester reçinenin jel ve kürlenmesini düzenleyen renksiz kimyasal yağdır. Metil etil keton ve hidrojen peroksitin reaksiyonundan elde edilir. Reçine ile stiren gibi reaktif monomerler arasında çapraz bağlanma reaksiyonlarını başlatır. Metil etil keton peroksit (MEK-P) poliester ve vinilesterlerin sertleşmesi için oda sıcaklığında aktiftir. MEK-P, reçineler sentetik kauçuk ve diğer petrokimyasal plastik üretiminde sertleştirici olarak kullanılır. Metil Etil Keton Peroksit tüm polyester reçineler, jel kaplamalar ve vinil ester reçineler için gereklidir. Farklı reçine türlerini katalizlemek için farklı MEK-P konsantrasyonları gereklidir. Ayrıca benzoil peroksit reçinenin sıcak kalıpta sertleştirilmesi amacı ile kullanılmaktadır. Katalizörler kimyasal reaksiyonun bir parçası olmamakla birlikte polimerizasyon prosesinin başlaması için gerekli enerjiyi sağlamaktadır. Bütün peroksitler bir nevi hidrojen peroksit türevidirler. Polimerlerin vulkanizasyonunda yaygın olarak kullanılmaktadır. Solvent olarak kullanılan oldukça toksik bir maddedir. Güçlü bir oksitleyici ajan ve aşındırıcıdır (koroziv). Diğer koroziv maddelerden farklı olarak, koroziv özefajit bulgularına ek olarak çoklu organ yetmezliği sonucunda ölüme sebebiyet verebilen bir maddedir. MEK-P maruziyeti, serbest radikal oluşumuna yol açar ve bu durum lipit peroksidasyonuyla sonuçlanır. Lipit peroksidasyonu ise hücre düzeyinde fonksiyon bozukluğuna, özellikle karaciğer yetmezliği ve çoklu organ yetmezliğine neden olabilmektedir.
-
Kevlar (poli parafenilen tereftalamid) : Aramid elyaflar, genellikle karbon elyaf ve cam elyaf ile kombinasyon halinde kompozit malzemeleri güçlendirmek için yaygın olarak kullanılmaktadır . Yüksek performanslı kompozitler için matris genellikle epoksi reçinesidir . Tipik uygulamalar arasında F1 yarış arabaları için monokok gövdeler , helikopter rotor bıçakları, tenis , masa tenisi , badminton ve squash raketleri , kanolar , kriket sopaları ve çim hokeyi , buz hokeyi ve lakros sopaları bulunur.

En güçlü elyaf ve en kristal yapı olan Kevlar-149, uçak yapımının belirli bölümlerinde bir alternatiftir. Özellikle uçak kanatlarının ön bölümlerinde kullanılan Kevlar, kuş çarpmalarında karbon veya cam elyaftan çak daha fazla mukavemet gösterir.
Kevlar bazen otomobillerin yapısal bileşenlerinde, özellikle Ferrari F40 gibi yüksek değerli performans arabalarında kullanılır.
Kevlar, düşük ısıl iletkenliği ve süspansiyon amaçlı diğer malzemelere göre yüksek mukavemeti nedeniyle kriyojenik alanında sıklıkla kullanılır . Çoğu zaman , paramanyetik malzemeye herhangi bir ısı sızıntısını en aza indirmek için bir paramanyetik tuz muhafazasını süper iletken bir mıknatıs mandrelinden asmak için kullanılır. Ayrıca, düşük ısı sızıntılarının istendiği yerlerde termal bir ayırma veya yapısal destek olarak kullanılır.
Bir el bombasının patlamasını emmeye yardımcı olmak için kasklarda olduğu gibi çeşitli askeri mühimmat ve malzemede de kevlar tercih edilmektedir.
Kevlar eğrildiğinde , elde edilen lifin gerilme mukavemeti yaklaşık 3.620 MPa ve nispi yoğunluğu 1.44'tür. Polimer, yüksek mukavemetini birçok zincirler arası bağa borçludur.
[CO-Cı- 6 , H 4 -CO-NH-C 6 H 4 -NH-] n ile formülüze edilir.
Kevlar, gücünü ve esnekliğini kriyojenik sıcaklıklara (−196 ° C) kadar korur; aslında, düşük sıcaklıklarda biraz daha güçlüdür. Daha yüksek sıcaklıklarda gerilme mukavemeti hemen yaklaşık% 10-20 oranında azalır ve birkaç saat sonra mukavemet kademeli olarak daha da azalır.
Kevlar üretimi, suda çözünmeyen polimeri sentezi ve eğirme sırasında çözelti içinde tutmak için ihtiyaç duyulan konsantre sülfürik asit kullanımından kaynaklanan zorluklar nedeniyle pahalıdır.
Çeşitli Kevlar sınıfları mevcuttur:
Kevlar K-29 : Kablolar, lastikler ve fren balataları gibi endüstriyel uygulamalarda kullanılır .
Kevlar K49 : Kablo ve halat ürünlerinde kullanılan yüksek modüldür.
Kevlar K100 : Kevlar'ın renkli versiyonudur.
Kevlar K119 : Uzamaya, esnemeye ve yorgunluğa daha dirençlidir.
Kevlar K129 : Balistik uygulamalar için daha yüksek mukavemet gösterir.
Kevlar K149 : Balistik, zırh ve havacılık uygulamaları için tercih edilir.
Kevlar AP : Kevlar K-29'dan% 15 daha yüksek çekme dayanımı gösterir.
Kevlar KM2 : Zırh uygulamaları için geliştirilmiş balistik direnç gösterir.
Kevlar XP : Daha hafif reçine ve KM2 artı elyaf kombinasyonudur.
Biyokompozitler
Kompozit, fiziksel olarak farklı iki veya daha fazla fazdan (veya maddeden) meydana gelen ve bunlardan hiç birine benzemeyen, değişik özelliklerdeki yeni bir maddedir. Fazlardan biri matris diğeri matrisi kuvvetlendirmede kullanılan takviye malzemelerdir. Matrisin amacı fiberleri bir arada tutmak ve uygulanan yükü fiberlere transfer etmektir.
Ayrıca, fiberleri çevresel ve mekanik tahribatlardan da korur. Matris malzeme bir termoset veya termoplastik polimer olabilir, ancak yenilenebilir kaynaklardan yapılması gerekir.
Biyokompozit, biyobozunabilir (biodegradable) polimerler (matris) ve biyobozunabilir takviye maddelerden oluşan malzemelerdir. Biyobozunabilir madde, canlı organizmalar tarafından bozunabilen maddelerdir.
Biyokompozitlerde kullanılan dolgu maddeleri genellikle biyofiberlerdir. Doğal biyofiberlerden yapılan biyokompozitler yenilenebilir, hafif, biyobozunabilir ve çevre dostudur. Günümüzde polimer bilimi ve teknolojisi yenilenebilir kaynaklardan yapılan kompozitlere odaklanmıştır durumdadır.
Yenilenebilir kaynaklardan üretilen biyokompozitler biyobozunabilir doğasından dolayı evrensel bir önem kazanmıştır ve çevre dostu malzemeler olmasından dolayı çeşitli alanlarda yararlanılmasına yönelik kapsamlı araştırmalara konu olmuştur.
Yenilenebilir kaynaklardan üretilen biyokompozitler biyobozunabilir doğasından dolayı evrensel bir önem kazanmıştır; çevre dostu malzemeler olduğundan çeşitli alanlarda yararlanılmasına yönelik çok ve kapsamlı araştırmalara konu olmuştur.
BBC’ler biyomedikal, tarım, paketleme ve diğer ilişkili mühendislik alanlarında çok geniş uygulama alanlarına sahip kompozitlerdir.
Doğal polimerler ve biyofiberler kullanımını sınırlayan çeşitli faktörler arasında hidrofobik polimer matrisle uyumsuzluk veya yeteri kadar uyumlu olmama, termal hassasiyet ve alevlenme sayılabilir.

Biyokompozitlerin Üretim Teknikleri:
Çoğunlukla plastikler veya kompozitlerin üretim proseslerine dayanır; örneğin, pres kalıplama, elle yığma (hand lay-up), filament sarma, pultruzyon, ekstruzyon, injeksiyon kalıplama, sıkıştırmayla kalıplama, reçine transfer kalıplama ve levha kalıplama gibi.
Çeşitli proseslerle biyokompozit üretiminde biyokompozitlerin kompaundlama aşaması fevkalade önemlidir. Kompaundlamanın amacı, sonraki injeksiyon, kalıplama, ekstruzyon veya diğer prosesler için uygun özellikler içeren malzeme (pelletler gibi) hazırlamaktır. Kompaunlamada genellikle, polimerler, dolgu maddeleri, fiberler ve katkı maddeleri karıştırılır, iyi bir dispersiyon sağlanır, uygun formda ve proseslenebilecek özelliklerde granüllerin elde edilmesi hedeflenir.
Termoplastik Polimerler ve Doğal Fiberlerin Kompaundlanması ve Ekstruzyonu:
Kompaundlama sırasında termoplastik polimer, ya dışarıdan ısıtmayla veya ekstruderde mekanik etkileşimle ısınır ve ergir; bu aşamada odun fiber (genellikle un formda) diğer katkı maddeleriyle beraber ilave edilir.
Termoplastik Fiberler ve Doğal Fiberler Karışımı:
Uzun keten, kenevir, kenaf ve pamuk fiberler otomotiv endüstrisinde yaygın kullanımı olan fiberlerdir; bunlar genellikle termoplastik fiberlerle karıştırılarak takviye malzeme olarak kullanılır.
Termoset Polimer Matrisli Biyokompozitler:
Ticari amaçlı termoset polimer matrisli biyokompozitler azdır, ancak bu alandaki çalışmalar devam etmektedir. Üretim teknikleri geleneksel kompozit proseslerine benzer.
Lignoselülozik Fiberler İçeren Biyobozunabilir Kompozitler:
Biyobozunabilir kompozitlerin geliştirilmesinde önemli faktörler doğru lignoselülozik fiberler karışımının ve uygun biyopolimer matrisin seçilmesi, gerekli olduğunda uygun yüzey işlemlerinin saptanması, ucuz, fakat hızlı fabrikasyon tekniklerinin uygulanmasıdır.