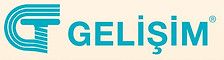


Hidrokarbonlar
Hidrojen ve karbon olmak üzere iki elementten oluşan organik bir bileşiktir. Petrol bileşiminin büyük bir kısmı değişen uzunluklardaki hidrokarbonlardan oluşur.
En küçük hidrokarbon metan, tek bir karbon atomu ve dört hidrojen atomundan oluşur. Bununla birlikte, hidrokarbonlar, zincirler, daireler ve diğer karmaşık şekiller dahil olmak üzere birçok yönden birbirine bağlanmış yüzlerce veya binlerce bireysel atomdan oluşabilir.
Hidrokarbonların özelliklerini sınıflandırmak için birkaç temel türe ayrılırlar.
Alkanlar: Bunlar doymuş hidrokarbonlar olarak adlandırılır. Yani sadece tüm karbon atomları arasında tek bağlar içerirler. Alkanlar, petrol yakıtlarının temelidir ve doğrusal ve dallı formlarda bulunurlar.
Doymamış Hidrokarbonlar: Karbon atomları arasında bir veya daha fazla çift bağa sahip olan hidrokarbonlara alken denir.
Sikloalkanlar: Bir veya daha fazla halka yapısı içeren herhangi bir hidrokarbon.
Aromatik Hidrokarbonlar: Areneler olarak da adlandırılan aromatik hidrokarbonlar, karbon atomlarının birbirini izleyen çift ve tek bağlarla bağlandığı benzersiz bir karbon molekülleri sınıfıdır. Bu molekül sınıfı, karbon atomları arasındaki bağların tek ve çift bağlar arasında bir ara bağ olduğu özel halka yapılarına sahiptir.
Bu sınıftaki moleküller, endüstriyel çözücü «benzen» içerir.
Benzen (C6H6): Diğer hidrokarbonlar gibi benzen de petrolün doğal bir bileşenidir. Oda sıcaklığında renksiz, yanıcı, tatlı kokulu bir sıvıdır ve yüksek oktan sayısına sahip olduğu için çoğu benzin karışımının bir bileşenidir.
Benzen de oldukça kanserojendir ve kemik iliği yetmezliği ve kemik kanserine neden olduğu iyi bilinmektedir. Elbette, “hoş aroması” nedeniyle tıraş sonrası ve diğer kozmetiklerde bir katkı maddesi olarak kullanıldığında kanserojenliği iyi bilinmemektedir.
En büyük benzen kullanımı (% 50), stiren ve polistren plastiklerinin ürünüdür. Ayrıca Naylon üretiminde önemli olan sikloheksan olarak bilinen bir moleküle dönüştürülür. Siklohekzan üretmek için benzenin yaklaşık% 15'i kullanılır. Böcek ilaçlarından kauçuğa kadar her şeyde daha küçük miktarlar kullanılır.
Benzen yapısı iki şekilde çizilebilir. İlkinde, çift bağ karakteri açıkça çizilir. Kısa elli versiyonda, yapıyı göstermek için halkanın içine bir daire çizilir. Benzen içindeki her bir karbon atomuna bağlı tek bir hidrojen vardır.
Aşağıdaki I. ve II. çizimleri eştir. Pratikte III. çizim kullanılır.
Benzen, renksiz, alevlenebilen, kaynama noktası 80,1 °C, erime noktası 5,5 °C olan bir sıvıdır.
Binükleer Aromatik Hidrokarbonlar: Molekülünde iki benzen halkası içeren bileşiklerdir.
Hidrokarbonlar
Hidrojen ve karbon olmak üzere iki elementten oluşan organik bir bileşiktir. Petrol bileşiminin büyük bir kısmı değişen uzunluklardaki hidrokarbonlardan oluşur.
En küçük hidrokarbon metan, tek bir karbon atomu ve dört hidrojen atomundan oluşur. Bununla birlikte, hidrokarbonlar, zincirler, daireler ve diğer karmaşık şekiller dahil olmak üzere birçok yönden birbirine bağlanmış yüzlerce veya binlerce bireysel atomdan oluşabilir.
Hidrokarbonların özelliklerini sınıflandırmak için birkaç temel türe ayrılırlar.
Alkanlar: Bunlar doymuş hidrokarbonlar olarak adlandırılır. Yani sadece tüm karbon atomları arasında tek bağlar içerirler. Alkanlar, petrol yakıtlarının temelidir ve doğrusal ve dallı formlarda bulunurlar.
Doymamış Hidrokarbonlar: Karbon atomları arasında bir veya daha fazla çift bağa sahip olan hidrokarbonlara alken denir.
Sikloalkanlar: Bir veya daha fazla halka yapısı içeren herhangi bir hidrokarbon.
Aromatik Hidrokarbonlar: Areneler olarak da adlandırılan aromatik hidrokarbonlar, karbon atomlarının birbirini izleyen çift ve tek bağlarla bağlandığı benzersiz bir karbon molekülleri sınıfıdır. Bu molekül sınıfı, karbon atomları arasındaki bağların tek ve çift bağlar arasında bir ara bağ olduğu özel halka yapılarına sahiptir.
Bu sınıftaki moleküller, endüstriyel çözücü «benzen» içerir.
Benzen (C6H6): Diğer hidrokarbonlar gibi benzen de petrolün doğal bir bileşenidir. Oda sıcaklığında renksiz, yanıcı, tatlı kokulu bir sıvıdır ve yüksek oktan sayısına sahip olduğu için çoğu benzin karışımının bir bileşenidir.
Benzen de oldukça kanserojendir ve kemik iliği yetmezliği ve kemik kanserine neden olduğu iyi bilinmektedir. Elbette, “hoş aroması” nedeniyle tıraş sonrası ve diğer kozmetiklerde bir katkı maddesi olarak kullanıldığında kanserojenliği iyi bilinmemektedir.
En büyük benzen kullanımı (% 50), stiren ve polistren plastiklerinin ürünüdür. Ayrıca Naylon üretiminde önemli olan sikloheksan olarak bilinen bir moleküle dönüştürülür. Siklohekzan üretmek için benzenin yaklaşık% 15'i kullanılır. Böcek ilaçlarından kauçuğa kadar her şeyde daha küçük miktarlar kullanılır.
Benzen yapısı iki şekilde çizilebilir. İlkinde, çift bağ karakteri açıkça çizilir. Kısa elli versiyonda, yapıyı göstermek için halkanın içine bir daire çizilir. Benzen içindeki her bir karbon atomuna bağlı tek bir hidrojen vardır.
Aşağıdaki I. ve II. çizimleri eştir. Pratikte III. çizim kullanılır.
Benzen, renksiz, alevlenebilen, kaynama noktası 80,1 °C, erime noktası 5,5 °C olan bir sıvıdır.
Binükleer Aromatik Hidrokarbonlar: Molekülünde iki benzen halkası içeren bileşiklerdir.
Hakkında
Kyäni, faydalı bileşenlerden oluşan besin takviyesi ürünlerini; benzersiz iş fırsatıyla birlikte dünya çapında 50'den fazla ülkeye ulaştırmaktadır. İdeal sağlığımızı korumak için günlük olarak Kyäni ürünlerini kullanırız, bu ürünleri başkalarıyla paylaşırız, işimizi inşa etmek ve sürdürmek için neredeyse her gün belirli bir saatimizi işe adarız ve başkalarını da Kyäni fırsatına dahil ederek veya Potato Pak ve Caring Hands programlarına katkı sağlayarak başarımızı başkalarıyla paylaşırız.
Hakkında
Kyäni, faydalı bileşenlerden oluşan besin takviyesi ürünlerini; benzersiz iş fırsatıyla birlikte dünya çapında 50'den fazla ülkeye ulaştırmaktadır. İdeal sağlığımızı korumak için günlük olarak Kyäni ürünlerini kullanırız, bu ürünleri başkalarıyla paylaşırız, işimizi inşa etmek ve sürdürmek için neredeyse her gün belirli bir saatimizi işe adarız ve başkalarını da Kyäni fırsatına dahil ederek veya Potato Pak ve Caring Hands programlarına katkı sağlayarak başarımızı başkalarıyla paylaşırız.
Sayfa Yapım Aşamasındadır.
Sayfa Yapım Aşamasındadır.
Eğitim / Bilgi / Çözüm Platformu
Termoforming (Isıl İşlem)
Termoform, iki aşamalı düz termoplastik levhayı şekillendirmek için bir işlemdir. Süreç, tabakanın ısıtılıp yumuşatılmasıyla başlar ve ardından kalıp boşluğunda şekillendirilir. Malzeme, şekilleneceği sıcaklığa kadar ısıtılır, sonra sıcaklığı kontrol edilebilen bir kalıp üzerinde (veya içinde) şekillendirilir; kalıp soğuyuncaya kadar beklenir ve şekillenmiş parça kalıptan alınır.
Elastomer ve termoset plastiklerler, çapraz bağlanmış yapıları nedeniyle tekrar ısıl işleme giremeyeceklerinden, termoform yöntemlerinde kullanılmazlar.
Termoform yöntemi ile işlenebilen termoplastikler; PP, PS, PVC, LDPE, LLDPE, HDPE, PMMA, ABS.
Termoform, gıda ambalaj endüstrisinde dondurma ve margarin küvetleri, et tepsileri mikrodalga kapları, çerez küvetleri sandviç paketleri vs. üretimlerde tercih edilmektedir.
Termoform ayrıca bazı eczacılık ve elektronik eşya, küçük alet, bağlantı elemanı, oyuncak, tekne gövdesi üretimi için de kullanılır.
Vakumlu, Basınçlı ve Mekanik olmak üzere, biçimlendirme aşamasında kullanılan farklı üç tekniğe sahiptir.
Vakumlu Termoform:
Termoformik plaka, plastik kalıp yüzeyine temas ettiğinde, soğuyarak sertleşir ve termoformik plaka, mamül / yarı mamül formunu alır. Termoform (ısıl şekillendirme), yarı bitmiş termoplastik ürünün yüksek sıcaklıklarda şekillendirilmesi ve şekillendirilmiş parçalar elde edilmesidir. Yarı bitmiş ürün genelde granül veya toz içerikli filmlerden ve levhalardan oluşur.Termoform makinası, ambalajlamada ısıl şekillendirmeişlemi kullanmak üzere tasarlanmıştır. Ambalajlanan ürünler genellikle doğrudan kullanılabilen son ürünlerdir ve daha fazla işlenmeleri gerekmez. Isıl şekillendirme işlemi, yarı bitmiş ürünün (termoformik film/tabaka) ısı enerjisiyle "yeniden şekillendirilmek" üzere makineye verilmesinden oluşur. Film yüzeyine ısı verilir ve yumuşama sağlanır. Kalıp kapanınca ısı kesilir ve kalıp içindeki hava vakumla emilir. Bu esnada yumuşamış film de kalıbın içine çekilerek, kalıp şeklini alır ve soğuyarak şekli muhafaza eder. Isıl işlemli şekillendirmede birçok çeşit ürün kullanılabilir. Bunlara çikolata kutularındaki ince plastik filmler, sıcak veya soğuk içecekler için kullanılan plastik kaplar ve oyuncak ambalajlamadakullanılan bazı ürün ve bileşenler dahildir.


Basınçlı Termoform:
Bu İşleme tekniği de; vakumlu termoform tekniğine benzer bir süreç içerir. Aynı şekilde termoformik plaka önce sıcak hava ile ısıtılır ve kalıp üzerine kapatılır. Ancak bu defa vakum ile kalıp içindeki hava emilmeyerek, plakanın üzerinden kalıp içine doğru yüksek hava basıncı tatbik eilir. Hava basıncı, yumuşak tabakayı kalıp oyuklarına uygun olarak dağılacak şekilde deforme olmaya zorlar. Bu deformasyon ile tabaka kalıp yüzeyine temas ederek, kalıbın şeklini alır ve soğuyarak sertleşir.
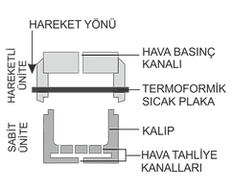

Mekanik Termoform:
Bu süreçte de yine önceden termoformik plaka ısıtılarak işlenebilir yumuşaklığa getirilmesini ve tabakanın doğrudan mekanik bir kuvvetle şekillendirilmesini içerir. Mekanik termoform sürecinde ürün kalıbının erkek formuna da ihtiyaç vardır. Erkek form, yüksek basınçla dişi form kalıbın içine doğru hareket eder ve arada kalan termoformik plakanın, kalıplar arası boşluğa yayılması sağlanır. Mekanik termoform süreci; vakumlu ve basınçlı termoform süreçlerinden daha hassas boyutsal toleranslara ve yüzey detaylandırmalarına imkan sağlar.

Sıkıştırma Kalıplama
Bu yöntem çoğunlukla kalıplama termoset reçineleri (termosetler) için kullanılır , ancak bazı termoplastik parçalar da bu süreç ile üretilebilir. Bir hidrolik pres üzerine monte edilmiş bölünmüş kalıplar arasına katkı maddeleri ve dolgular ile karıştırılmış önceden tartılmış, ısıtılmış bir polimer malzemenin yüksek basınca maruz bırakılmasıyla uygulanır.
Şarj: Mamül/yarı mamüle dönüşecek olan polimerik malzeme «şarj» olarak tanımlanır. Genellikle kalıp alt yarısına yerleştirilmeden önce önceden ısıtılır. Ya da kalıpların kendi ısıtma donanımı vardır. Şarj; toz, pelte, macun, topak, reçine formunda olabilir. Kalıbın üst yarısı aşağı doğru hareket ederek, şarj üzerine baskı uygular ve malzemenin kalıp boşluğunu doldurma yönünde zorlar. Çevrim süreci sonrasında kalıp açılır ve ejektör pimi vasıtasıyla parça çıkarılır. Sıkıştırma kalıplama döngü süresi, enjeksiyon kalıplama döngüsünden daha uzundur.
Bu yöntem daha çok, büyük yassı veya orta dereceli kavisli parçaların kalıplanması için uygundur. Sıkıştırma Kalıplama ile yaygın olarak EP (Epoksi), UF (Ure formaldehit), MF (Melamin Formaldehit), PF (Fenolik) elastomer malzemeler işlenir.
Sıkıştırma Kalıplama sürecinde; elektrik duvar prizleri, sayaç kutuları, tepsiler, devre kesiciler, pişirme kapları, çamaşır kurutma makinesi fan kanadı, elektronik ve pişirme kapları, freze tezgahı ayar tekerleği, otomotiv parçaları, televizyon kabinleri, yemek takımları, cihaz gövdeleri, radyo kutuları, uçak ana güç terminali muhafazası, davlumbazlar, tencere kolları, çamurluklar, yemek takımları tabakları, kepçeler üretilebilir. Bu yöntemde dikkat edilecek en önemli kriter; şekillendirilecek malzemenin miktarının (şarj miktarı) kalıp boşluğunu tam dolduracak şekilde çok iyi kontrol edilmiş olması gerekliliğidir.
Sıkıştırma kalıpla sürecinin temel özellikleri, enjeksiyon kalıplama sürecinden daha basit uygulama yöntemine sahip olması, termoset, elastomer kullanımından dolayı (termoplastiklere nazaran yüksek viskoz malzemeler) daha basit geometriye sahip ürünlerin tercih edilmesi gösterilebilir. Uygulama kalıp genellikle elektrik resistansları, buhar veya sıcak yağ sirkülasyonu ile ısıtılır.

Transfer Kalıplama
Metot esas olarak ısıyla sertleşen termoset reçinelerin kalıplanması için kullanılır , fakat bazı termoplastik parçalar da bu yöntem ile üretilebilir. Sıkıştırma kalıplama sürecinde olduğu gibi, bu süreçte de «şarj» kullanılır. Öncelikle şarj, önceden ısıtılmış ve kalıplama sürecine adını veren transfer haznesine alınır. RAM ekstrüzyon modellemesiyle yüksek basınçla polimerik malzeme kanal (yolluk) boyunca kalıp içine enjekte edilir. Burada, sıkıştırma kalıp sürecinden farklı olarak bir üçüncü kalıp plakası vardır. Toz, pelte, macun, topak, reçine formunda olabiecek şarj, şekillendirme kalıbında donduktan sonra bu üçüncü plaka ayrılır ve yine bir ejektör pimi ile mamül,
yada yarı mamül kalıptan çıkartılır. Kalıplama süreci sonrasında, tarnsfer haznesinde ve kanalda, artık hurda olan eriyikler temizlenir.
Termoset polimerlerin tekrar ısı ile geri dönüşümü olmadığından bu parçalar hurdadır. Transfer kalıplamanın çevrim süresi; sıkıştırma kalıplama çevriminden daha kısadır ve daha karmaşık formlu ürünler elde edilebilir. Ancak enjeksiyon kalıplama çevriminden daha uzun çalışma sürecine sahiptir ve enjeksiyon kalıplama kadar da karmaşık formlu ürünler elde dilemez.
Kelimenin tam anlamı ile; ürün formu ve çevrim süreci açısından, enjeksiyon ile sıkıştırma kalıplamalarının arası bir yöntemdir.Transfer kalıplama ile, kalıp boşluğuna yerleştirilen seramik veya metalik malzemelerin kaplaması yapılabilir, ayrıca radyo ve televizyon kabinleri ve araba gövde parçalarını üretmek için kullanılan bir yöntemdir. EP (Epoksiler), UP (Doymamış Poliesterler), PF (Fenolikler) gibi vinilester, termosetler sıkıştırma kalıplama ile yaygın olarak işlenen malzemelerdir.

Rotasyon Kalıplama
Döner Kalıplama olarak da tanımlanan süreç temel olarak 4 evreden oluşmaktadır
(1) Toz reçinenin kalıp içerisine konur.
(2) Kalıp kapatıldıktan sonra ısıtma işlemi gerçekleştirilir. Isıtma sürecinde kalıp, yatay ve dikey akslar etrafında döndürülür. Plastik bu süreçte erir ve kalıbın yüzeylerine yapışır. Dönme hızı nispeten yavaştır. Bunun nedeni, merkezkaç kuvveti olmayan yerçekiminin kalıp yüzeylerinin düzgün bir şekilde kaplanmasına neden olmasıdır. Sıcak hava konveksiyonunun dönerken kalıbı ısıttığı bir ısıtma bölmesini içeren istasyonda, kalıp içindeki sıcaklıklar, polimer ve kalıplanmış malzemeye bağlı olarak 375 °C kadar ulaşır.
(3) Soğutma sürecine geçilir. Büyük soğutucu fanlar veya su spreyleri ile kalıbın duvarlarına hava üflenir veya/su sıkılarak soğutma gerçekleştirilir.
(4) Ürün kalıptan çıkarılır. Rotasyonal kalıplama yüksek sıcaklıklarda ve düşük basınçlarda yapılan ve genellikle büyük malzemelerin üretilmesinde kullanılan bir kalıplama yöntemidir. Elde edilen malzemenin temiz olmasında Isıtma ve soğutma süreleri, kalıbın döndürülme hızı çok önemlidir.
Bu teknik ile daha çok et kalınlığı sabit olan içi boş ve hacimli ürünler üretilir. Tekne gövdesi, kano, mobilya, konteyner, trafik işaretleri, su deposu, duba, hayvan barınakları ve oyuncakları verilebilir. PE, özellikle HDPE, PP, ABS, PS bu teknikte en sık kullanılan malzemelerdir.
Enjeksiyon kalıplama ve şişirmeli kalıplama ile karşılaştırıldığında, rotasyon kalıpları basit ve daha ucuzdur. Bununla birlikte, üretim döngüsü daha uzun sürer (on dakika veya daha fazla).

Şişirme Kalıplama
Isıtılmış içi boş bir termoplastik borunun kalıp boşluğunun şekline uyan kapalı bir kalıpta şişirildiği bir işlemdir. Kalıplama işi için kullanılacak parça «parison» olarak tanımlanır. Şişirme kalıplama için en çok LDPE, HDPE, PP, PVC, PET kullanılamaktadır. Farklı boyutlarda ve şekillerde varil, depolama tankı, su veya yakıt depoları, geri dönüştürülebilir şişelerde, oyuncak, küvet, küçük teknelerde tek kullanımlık konteyner, kapı, bariyer gibi çeşitlilikte ürün bu yöntemi ile üretilmektedir. Ekstrüzyon şişirme, enjeksiyon şişirme vestreç şişirme şeklinde üç farklı kalıplama süreci vardır.
Ekstrüzyon Şişirme Kalıplama:
Yaygın olarak plastik şişelerin seri üretimi için kullanılır. Plastik malzeme ergitilir ve içi boş bir tüp şeklinde (parison), soğuk metal kalıp içine basılır ve burada basınçlı hava ile şişirilerek kalıbın şeklini alması sağlanır. Parison, iki kalıp yarısının arasına aşağı doğru yönde (dikey olarak) ekstrüde edilir. Parison, istenen boya ulaştığında ekstruzyon işi durur, iki kalıp yarıları birleşerek kapanır. Hava üfleme boşluğundan üflenen hava ile parisonun kalıp yüzeyine tamamen teması sağlanıncaya kadar şişirilir. Kalıbın soğumasıyla, kalıp yarıları açılarak mamül/yarı mamül çıkartılır.
Streç Şişirme Kalıplama:
Bir üfleme borusu vasıtasıyla aşağı doğru yönde gerilen bir parisonun enjeksiyonla kalıplanmasını içerir.
Genişletilmiş parison daha sonra bir üfleme kalıbı içinde şişirilir.
Spesifik moleküler oryantasyon, malzemenin daha yüksek mekanik mukavemetini, sertliğini ve şeffaflığını sağlar. Gazlı içecek kapları üretiminde yaygın tercih edilen bu yöntemde ağırlıklı olarak PET kullanılır.
Enjeksiyon Şişirme Kalıplama:
Polimerik malzemenin, bir üfleme tüpü veya çekirdek çubuk etrafında sıcak enjeksiyon kalıbı içine enjekte edilmesiyle yapılır. Ekstrüzyon üfleme kalıplama ile benzer bir uygulamadır. Karşılaştırma yapmak gerekirse enjeksiyon şişirme işi; daha doğru ve kontrol edilebilir bir işlemdir. Daha geniş polimerik malzeme çeşitliliğinden daha karmaşık ürünlerin üretilmesini sağlar.
Bununla birlikte enjeksiyon şişirme kalıplama üretim oranı, ekstrüzyon şişirme kalıplamadan daha düşüktür.

Torba Vakumlu Kalıplama
Plastik kalıp endüstrisinde otomasyon yaygınlaşırken, günümüzde hala çok sayıda manuel işlem kullanılmaktadır. Örneğin, torba kalıplama, termoset plastik malzemelerin çeşitli dayanıklı takviyeli bileşenlere imal edilmesi için bir yöntemdir, bu da çoğunlukla manuel kontrole dayanan bir işlemdir. Kalıp boşluğunun içindeyken özel bir torbanın plastik bir iş parçası üzerine yerleştirilmesini ve torbanın etrafına vakum veya basınçlı hava basıncı uygulanmasını içerir. Silindirler, hava torbasını basınç torbaya doğru yönlendirilirken sıkar ve işleme yardımcı olmak için sıklıkla ısı verilir. Torbanın kendisi genellikle ayırma filmi veya elastomerik bir malzemeden yapılmış geçirimsiz ve esnek bir örtüdür.
Torba kalıplama ürünleri, kompakt ve güçlü olma eğilimindedir ve kalınlık toleransları enjeksiyonla kalıplama ile sunulanlara benzer. Torba kalıplama , geleneksel olarak inşaat malzemeleri, ekipman muhafazaları, otomotiv gövdeleri, gemi gövdeleri ve çeşitli askeri ürünler gibi yüksek performanslı yapısal bileşenlerin üretimi için kullanılır. Aynı zamanda diğer kalıplama teknikleri ile birlikte kullanılır. Bu makine ve elle çalıştırılan cihaz kombinasyonu, plastik malzemelerin imalatında kalite ve detaylara dikkat edilmesini sağlar.
Standart torba kalıplama işleminde, elastik torba kalıp boşluğundaki plastik malzemeyi kaplar . Ancak, bu gerçekleşmeden önce kalıbın kendisi temizlenmeli, ön işlemden geçirilmeli ve kenarlar boyunca kapatılmalıdır. Kalıp genellikle bir ayırıcı madde ve bir jel yağlayıcı ile kaplanır, ancak tek bir eğri içeren kalıplar bazen bunun yerine plastik bir film ile işlenebilir. Daha pürüzsüz yüzey kalitesi sağlamak için bir takviye cam elyaf tabakası yerleştirilebilir, ancak anahtar takviyesi genellikle bir cam ipliği matından oluşan bir ön kalıptır. Bu preform, gerekli diğer takviye edici maddeler veya katkı maddeleri ile birlikte kalıba yerleştirilmeden önce boyutlandırılır.
Torbalama ve kalıplama :
Kalıp torbalama için hazırlandıktan ve cam elyaf takviyeleri yerleştirildikten sonra, gerçek imalat işlemi başlamaya hazırdır. Standart bir torba kalıplama prosedüründe, operasyonun manuel aşamalarını gerçekleştirmek için genellikle aşağıdaki ekipman gereklidir:
• Sıkışan havayı düzleştirmek için hem kürek hem de disk konfigürasyonlarında metal silindirler
• Yapıştırma reçineleri ve jel kaplamaları uygulamak için uzun saçlı veya kısa saç kıllarına sahip laminasyon silindirleri
• Fırça temizleyicileri ve fırça değiştirmeleri
• Laminasyon ve kaplama fırçaları
Ve katalizör sıvı reçine, tipik olarak kalıp takviye üzerine dağıtıldığı pigmentler, boyalar ve başka katkı maddeleri içeren bileşiktir. Daha sonra tüm karışım geçirimsiz bir torba ile kaplanırken, operatörler torbanın yüzeyi altında düzgün bir reçine dağılımı oluşturmak için tırtıklı el silindirleri uygular. Manuel haddeleme ayrıca, takviyenin kalıplanmış ürünün bozulmasına neden olabilecek hava cepleri olmadan reçineye düzgün bir şekilde bağlanmasını sağlar. Bu reçine takviye bağı, etkili torba kalıplama için çok önemlidir.
Uygulama gerekliliklerine bağlı olarak, donatıya ahşap veya köpük gibi ilave malzemeler ilave edilebilir. Benzer şekilde, metal takviyeler veya destek bileşenleri de reçine takviye bağına tamamen dahil edilebildiği için dahil edilebilir. Tüm ünite daha sonra fırınlama veya kızılötesi ısıtma kullanılarak hızlandırılabilen farklı bir kürleme alanına taşınır. Sertleştikten sonra katılaştırılmış ürün kalıptan çıkarılır veya kalıp onun etrafında parçalanır. Ürün daha sonra kullanıma hazır hale gelmeden önce daha fazla şekillendirme veya son işlemden geçirilebilir.
Torba kalıplama, bileşen tasarımı ve laminasyonunda yüksek düzeyde çok yönlülük sağlayabilir. Bunun bir kısmı, torba kalıplama yoluyla elde edilebilen hassasiyet ve yakın kalınlık toleransından kaynaklanmaktadır. Farklı tiplerde reçine bileşikleri ve takviyeleri kullanmak, kalıplama üzerine belirli fiziksel özellikler kazandırarak çok çeşitli bileşen özelliklerine izin verebilir. Torba kalıplama ayrıca nispeten ucuz malzemelere dayanır ve takım ve işleme maliyetleri düşük olma eğilimindedir. Bununla birlikte, operatör becerisine güvenmek, sürecin ana dezavantajlarından biri olabilir. Uygun eğitim ve güvenlik düzenlemelerine uymak önemlidir, ancak küçük insan hataları bile hatalı kalıplamalara neden olabilir. Muayene ve kalite kontrol de zor olabilir, çünkü tek tek laminatörlere ve elle yuvarlanmaya güvenmek doğal olarak üretim çalışmaları arasında küçük tutarsızlıklar ile sonuçlanır. Son olarak, süreç nispeten yavaş bir süreçtir ve yüksek işçilik maliyetleri gerektirebilir.
Kalenderleme / Haddeleme
Bu işleme süreci; kalenderleme, haddeleme veya perdahlama olarak farklı terimlerle tanımlanabilmektedir.
Toz veya granül haldeki polimerik malzeme uygun miktarda katkı maddeleri ile karıştırılır ve yumuşak hale getirilir. Bu karışım 150-200°C ısınmış haddeler (merdaneler) arasından geçirilir, film veya levha haline dönüştürülür.
İstenilen kalınlığa gelince bir seri soğutma haddesi arasından geçirilir, sertleştirilir ve sonrasında bir taşıyıcı masuraya sarılır.
Haddeleme hattını oluşturan haddeler; karıştırıcı, yumuşatıcı, istenilen kalınlığı gerçekleştiren yani kalibrasyonu yapan, soğutucu ve
yönlendirici gibi farklı amaçlarla tasarlanmaktadır..
Karıştırıcı-yumuşatıcı hadde sistemi en az iki merdaneden oluşur.
Soğutucu ve yönlendirici haddeler ise bir merdaneden meydana gelebilir.
Kalibrasyon haddelerinin arasındaki uzaklık, ürünün kalınlığına göre ayarlanır.
Genellikle haddeleme termoplastik malzemelere ve özellikle ısıl dayanıklılığı düşük polimerlerin işlenmesinde uygulanır. Bunun en tipik bir örneği PVC'dir.
PVC; esnek, yarı sert ve sert olmak üzere üç şekilde kullanılır.
Esnek PVC ile yağmurluk, banyo perdesi, yatak örtüsü,
yarı sert PVC ile masa örtüsü, yer döşemesi, sert PVC ile kredi kartları, tepsiler, işaret levhası vb. üretimler gerçekleştirilir.
Haddeleme ile şekillendirilen diğer polimerik malzemelerin başında;
ABS ve dolgulu PE gelmektedir
Özetle: Kalenderleme bir basınç uygulama prosesidir; malzeme ısıtmalı ve soğutmalı çok sayıdaki silindirler arasından sıkıştırılarak geçirilir ve istenilen kalınlıkta temiz ve parlak levhaya dönüştürülür. Genellikle kauçuk malzemelerden, PVC ve diğer bazı plastiklerden film veya levha üretiminde kullanılan bir işleme yöntemidir. Kalenderlemeden alınan levhalar şekillendirilmek üzere termoforming işlemeye verilir. Metalik malzeme haddeleme işinde, malzeme sıcakken, plastik haddeleme işinde merdaneler sıcak olur. Malzeme üzerine basınç, kalibre merdaneleri ile uygulanır.
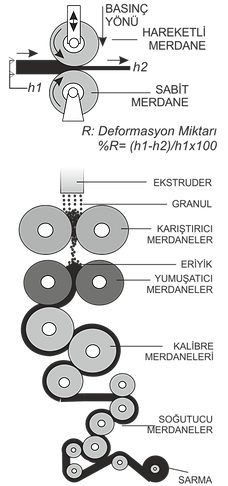
Sıvı Enjeksiyon Kalıplama
Stok malzemelerini bir dizi bileşen ve ürüne kalıplayan endüstriyel bir imalat yöntemidir. Basınçlı çarpma karıştırmasından ziyade mekanik karıştırmaya dayanması ve standart sıvı enjeksiyon kauçuk ve benzeri elastomerik malzemelere odaklanması nedeniyle standart reaksiyon enjeksiyon kalıplama işleminden farklıdır . Mühürler, o-ringler, izolatörler ve elektronik kontaklar dahil olmak üzere çok sayıda çok yönlü ürünü verimli bir şekilde üretebilir.
Sıvı enjeksiyon kalıplamanın çok yönlülüğünün büyük bir kısmı sıvı silikon malzemelerin malzeme özelliklerinden kaynaklanmaktadır . Bu silikonlar yüksek derecede ısı ve alev direnci, çekme mukavemeti ve esneklik gösterir. Ayrıca silikonlar, bitmiş üründe renklendirme veya şeffaflığa izin veren faydalı şekillendirilebilirlik özellikleri sağlar. Kimyasal bileşimlerine bağlı olarak, bu malzemeler aynı zamanda izolatörler veya iletkenler olarak da işlev görebilir. Sıvı silikon üretmek için kullanılan sıvı enjeksiyon işlemi, son derece hassas sonuçlar üretebilen hassas ve farklı bir yöntemdir.
Sıvı enjeksiyon kalıplama süreci: Plastik esaslı malzemelerin bir dizi piston vasıtasıyla dağıtılmış karıştırma ve dağıtımına odaklanır. Genellikle, bir piston, katkı maddeleri ve elyaflarla takviye edilebilen tabanı oluşturan plastik içerirken, diğer piston, karıştırma reaksiyonunu aktive eden bir katalizörü tutar. Bileşik malzeme daha sonra doğrudan kapalı bir kalıba enjekte edilir ve sertleştikten sonra neredeyse bitmiş bileşen kalıplama makinesinden çıkarılır.
Silikonlar ve akrilikler, sıvı enjeksiyonla kalıplamada en yaygın olarak kullanılan malzemelerdir . Makine donanımının sıvı plastikle tıkanmasını önlemeye yardımcı olmak için, enjeksiyon aşaması için yaylı bir pim memesi kullanılabilir. Yay yükleme, enjeksiyon basıncının ekstrüder haznesininkinden daha yüksek olmasını sağlar, böylece kanalın engellenmesini önler. Bilgisayar destekli tasarım araçları, kalıplama işlemini daha verimli hale getirmek için de yararlıdır. Bilgisayar programları, en etkili işleme koşullarını belirlemek, sonuçları değerlendirmek ve entegre cihazları izlemek için simülasyonlar çalıştırabilir. Termal görüntüleme teknolojisi, kalıplama kusurları veya tasarım tutarsızlıkları gibi üretim hatalarını tanımlama potansiyeline de sahiptir.
Sıvı enjeksiyon makineleri : Standart bir sıvı enjeksiyon kalıplama makinesi, ölçülü bir pompalama cihazına ve dinamik veya statik bir karıştırıcı takılı bir enjeksiyon ünitesine dayanır. İdeal olarak, bu sistemler mümkün olduğunca kompakt ve hassas bir şekilde bir araya getirilirken, çevresel bileşenler belirli bir projenin ihtiyaçlarını karşılayacak şekilde yapılandırılmıştır. Tipik bir sıvı enjeksiyon makinesinin temel parçaları şunlardır:
-
Enjektörler: Enjeksiyon cihazı, sıvı silikon kauçuk gibi şekillendirici malzemeyi basınçlı kuvvet altında pompalama bölümüne iter . Operatör genellikle proje parametrelerine göre değişen basınç ve enjeksiyon oranını ayarlayabilir.
-
Ölçüm Birimleri: Ölçüm birimi, iki sıvı malzemeyi dikkatlice orantılı olarak pompalar ve aynı anda sabit bir oranda serbest bırakır.
-
Besleme Tamburları: Malzeme besleme kapları veya pistonları, makinenin pompalama sistemine bağlanır. Karıştırma malzemelerinin tamburlarının yanı sıra, genellikle pigment için ek bir kap vardır.
-
Karıştırıcılar: Ölçüm biriminden geçtikten sonra, sıvı oluşturucu malzemeler statik veya dinamik bir karıştırıcı kullanılarak birleştirilir. Bu karışım daha sonra basınçlandırılır ve kalıba zorlanır.
-
Nozul: Sıvı karışımı kalıba besleyen nozul genellikle bileşiğin sızmasını veya kalıbın aşırı dolmasını önleyen otomatik bir kapatma valfi ile birlikte gelir.
-
Kalıp Kelepçesi: Kalıp sıkıştırma cihazı, enjektör, pompa ve besleme ünitesi ile koordineli olarak tetiklenir. Kalıbı yerine sabitler ve işlem tamamlandığında açar.
Lazer Sinterleme
Milimetreden daha düşük katmalar halinde, bilgisayar destekli üç boyutlu nesnel obje üretimi yapımında kullanılır. Bu süreçte; polimerik malzemelerden başka, seramik ve metalik tozlardan da istifade edilebilir.
Polimerik malzemelerden; silikon ve epoksi kalıpları, naylondan yapılmış fonksiyonel parçalar, yatırım döküm için akrilik stiren parçaları, cam elyaf takviyeli PA, PP, PC, ABS ve yüksek mukavemetli karbon fiber takviyeli PA ile sanatsal nesneler, mimari modeller, diş koruyucu ürünler, seramik malzemelrden kısmen stabilize zirkonyumdan yapılan yatırım döküm kalıpları, uuni kemikler ve doku iskeleleri, protezler,
metalik malzemelerden, bronz parçaları; paslanmaz ve takım çelikleri, Titanyum alaşımlarından yapısal parçalar,
otomotiv ve elektronik endüstrileri için yüksek mukavemetli, düşük ağırlıklı, aşınmaya dayanıklı parçalar için silikon karbon takviyeli alüminyum ve titanyum kompozitler seçmeli lazer sinterleme uygulamaları arasındadır.
Sinterleme: Kullanılacak malzemenin erime ısısı altında ama erime ısısına çok yakın bir değerde ısıtılmasıyla, toz parçacıklarının birleştirilmesini içeren bir yöntemdir.
Süreç; tozun ince ve muntazam tabaka halinde, üretim haznesinin yüzeyine yayılması ile başlar. Burada ince toz tabakasının kalınlığı genellikle 0,1 mm 'den azdır. Üretilecek parçanın bilgisayar destekli tasarım (CAD) modeline göre katman yüzeyi üzerinde, yüksek güçlü lazer ışını taraması yapılır. Lazerin enerjisi, tozun sinterleme sıcaklığına kadar ısındığı tabaka yüzeyinin küçük bir noktasında odaklanır. Tabakanın toz parçacıkları, malzemenin difüzyonundan dolayı birbirlerine ve önceki tabakaya bağlanırlar. Taranan alanın dışında kalan toz tabaka, hiç bozulmadan durur ve üretim haznesindeki sinterlenmiş kesimin desteklenmesini sağlar.
Toz yayma işleminin ardından lazer sinterleme işlemi, nesne oluşturma tamamlanana kadar kat kat tekrarlanır.Süreç tamamlandıktan sonra soğumaya bırakılır. Ve sonrasında sinterlenmiş model üretim haznesinden çıkarılır, üzerine hava üflenerek fazla tozlar modelden uzaklaştırılır.Bu süreçte; ürün konsepti ile imalata geçiş süreci çok kısadır. Çok esnek ve detaylı tasarımlar yapılabilir. Eşsiz modellemeler veya ihtiyaç duyulan çok özel parçalar adet bazında rahatlıkla üretilebilir. Prototipler dijital biçimde saklanır ve gerektiğinde çoğaltılabilir.

Reaksiyon Enjeksiyon Kalıplama
En sade ifade ile Reaksiyon Enjeksiyon Kalıplama (:REK), yüksek basınç uygulanarak, iki veya daha fazla reaktif sıvı bileşenlerin karıştırılması ve düşük basınçta kapalı bir kalıp içine enjekte edilmesi işidir. Başka bir ifade ile, iki veya daha fazla plastiği kalıba sokulmadan önce bir polimere kimyasal olarak bağlayan enjeksiyon kalıplama tekniğinin özel bir alt kümesidir. Kalıplanmış plastikler çok çeşitli endüstriyel ve ticari uygulamalarda kullanılırken, belirli bir kalıplama sürecinin seçilmesi bir projenin kalitesini ve verimliliğini büyük ölçüde etkileyebilir. Genel olarak, enjeksiyon kalıplama işlemi, erimiş plastiği bir tasarım kalıbına zorlayarak termoplastik reçine parçaları üretir. Kullanılan yüksek basınçlar plastiğin kalıbın şekline uymasını sağlayarak parçayı oluşturur. Metal döküm gibi, enjeksiyon kalıplama tipik olarak çok az iş gerektiren veya hiç çalışma gerektirmeyen bileşenler üretir.
REK kullanımını düşünen üreticiler, onu standart enjeksiyon kalıplamadan ayıran belirli özellikleri incelemek isteyebilirler. Merkezi farklılıklardan biri, baz malzemelerinkinden farklı özellikler sağlayabilen plastik polimerizasyonun doğasında yatmaktadır. REK ayrıca büyük parçaları karmaşık şekillerle üretebilir ve bu da hacimli bileşenler gerektiren endüstriyel uygulamalar için çok uygun hale getirir. Benzer şekilde, maliyet verimliliği, üretim döngüsü oranları ve makine tasarımı konuları bu tekniği kullanma kararını etkileyebilir.
REK'de kullanılan plastikler :
Poliüretanlar , poliamidler ve fiber kompozitler reaksiyon enjeksiyonlu kalıplamada en yaygın kullanılan plastik tipleridir . Bu malzemeler, polimerizasyon sırasında kullanılan baz maddelerin veya ilave kimyasalların oranına bağlı olarak değişen özellikler sergiler. Farklı kombinasyonlar, bir ürünün düşük stresle gerilme ve orijinal şekline dönme kabiliyetini belirleyen bir dizi elastomerik nitelik verebilir. Bu aralık, poliüretan imalatında kullanılan başlıca ürünler olan yapısal, katı ve kompozit köpüklerin esnekliğini etkiler.
İşlem erimiş plastik içerdiğinden, REK bir tür sıvı enjeksiyonlu kalıplama olarak düşünülebilir. Sıvılardan birine, ürünün stres-gerinim oranını arttırmak ve termal değişikliklerden genişleme veya daralma derecesini azaltmak için genellikle karbon dolgu maddeleri veya kısa lif reçinesi verilir.
REK süreci :
Standart enjeksiyon kalıplama işleminden farklı prosedürleri içeren çok aşamalı bir işlemdir. Başlamak için, poliizosiyanat ve bir reçine bileşiği gibi iki veya daha fazla tipte erimiş plastik, sıcaklık ve besleme kontrol mekanizmaları ile donatılmış ayrı reaktan tanklarına dökülür. Sıvılar daha sonra ilgili besleme hatlarına bırakılır ve basınçlandırmayı düzenleyen ve plastiği bir karıştırma kafasına sirküle eden bir ölçüm odasına kanalize edilir.
Karıştırma kafası, plastikleri çarpma yoluyla karıştırmak için tipik olarak 1.500 ve 3.000 psi arasında basınçlar uygular. Reaktanlar karıştırıldıktan sonra yüksek hızda kalıba enjekte edilir. Karıştırma kafası kalıp dolduğunda reaktifleri serbest bırakmayı durdurur. Kalıbın içinde ekzotermik bir kimyasal reaksiyon meydana gelir ve plastik polimerizasyona neden olur. Polimer katılaştıktan veya "sertleştikten" sonra, bileşenden kalıptan çıkarılır.
REK makineleri bu işlemi düşük sıcaklıklar kullanarak gerçekleştirir. Erimiş plastiği oluşturmak için gereken ısı dışında, reaksiyon enjeksiyon kalıplama nispeten serin bir işlemdir. Termal enerji yerine REK, polimerizasyon reaksiyonlarının neden olduğu kimyasal enerji üretir. Kullanılan kalıplar tipik olarak çelik, alüminyum veya nikelden yapılır ve düşük ağırlıklı bir presle kenetlenir. Polimerin sertleşme süresi genellikle bir dakikanın altındadır, bu da orta hacimli işlemler için hızlı devir ve hızlı üretim döngülerine neden olur.
REK endüstriyel uygulamaları :
Düşük işleme sıcaklıkları ve düşük enjeksiyon basınçları nedeniyle, REK değişken duvar kalınlığına ve pürüzsüz yüzey yüzeylerine sahip büyük bileşenleri kalıplamak için çok uygundur. Üreticiler aynı zamanda düşük ve orta hacimli projeleri idare etme konusunda yetkin hale getiren nispeten yüksek ciro oranından da yararlanabilirler. Ek olarak, REK parçaları yüksek gerilme mukavemeti, ısı direnci ve aşındırıcı asitlere veya çözücülere karşı direnç gösterir . Bununla birlikte, güneş ışığına uzun süre maruz kalmak polimer bazlı parçaları bozabilir ve polimer esaslı ürünler için takım veya işleme maliyetleri nispeten yüksektir.
Dokumasız (Nonwoven) Kumaş Üretimi
Dokunmamış kumaşlar (Nonwowen) bir çok türde çeşitte değerlendirilmektedir ve özellikle üretim tekniklerine göre kategorize edilirler.
Üretim teknikleri ağırlıklı olarak şunlardır;
-
Melt Blown
-
Spunbond
-
Spunlace
-
Airlaid
-
Kimyasal Yapıştırılmış
-
İğne Delikli - Keçeler
Tek Kullanımlık Bebek Bezleri, Yetişkin İdrar Kaçırma Ürünleri, Tek Kullanımlık Bebek Bezleri, Yetişkin İdrar Kaçırma Ürünleri, Tek Kullanımlık Medikal Tekstiller, yara bantları, sargı bezleri, Yatak ve Döşemelik Astar, yay cepleri, yastık kılıfları, yastık astarları, Halı Altlıkları kullanım alanlarının başında gelir.
Her bir filtrasyon tipi, ürün ve uygulama alanı için, uluslararası standartlara uygun mükemmel filtrasyon özellikleri sağlayan özel nonwoven tipleri bulunmaktadır. Ayrıca, İster toprağı korumak, ister peyzaj üzerinde çalışmak veya ekimi iyileştirmeye yardımcı olmak olsun, dokunmamış kumaşlar geniş bir uygulama sahasına sahiptir. Dokunmamış kumaşların arazi yüzeyine taşınması ve uygulanmasının kolay olması, bu alandaki en büyük avantajlarıdır.
Bunlardan başka nonwoven (dokumasız) kumaşların kullanıldığı sahalar şunlardır;
Filtrasyon :
Araba ve Ev Klimaları, Temiz Oda, Ameliyathane Hava Temizleyicileri, Yüz Maskeleri, Sıvı Filtreleme, Oto Yağ Filtreleri, Makine Filtreleri, Drenaj Filtreleri, Elektrikli Süpürge Torbaları, Endüstriyel Toz Toplama ve Filtreleme
Tarım, Bahçıvanlık :
Malçlar, Kırpma Örtüleri, Böcek Örtüleri, Gölgelendiriciler, Rüzgar Örtüleri, Donmaya Karşı Koruma ve Termal Battaniyeler, Meyve ve Sebzeler İçin Koruyucu Kılıflar
Jeotekstiller :
Bu ürünler daha çok karayollarının, demiryollarının, depo alanlarının, otoparkların, havaalanlarında iniş kalkış pistlerinin, petrol taşıma boruları ve tanklarının inşaatlarında kullanılmaktadır. Bu tür inşaatlarda zemin mekaniğini kuvvetlendirici bir rol oynamaktadır. Zeminin bir noktasına binen ani yüklerin dengeli bir şekilde bütün zemine yayılmasını sağlamaya yardımcı olmaktadırlar. Ayrıca suyu geçirip katı partikülleri geçirmemesi sebebiyle de baraj tabanlarında ya da toprak kaymalarına karşı da zemin kuvvetlendirici olarak kullanılabilmektedir. Peyzaj, Toprak Bölümü, Heyelan Kontrolü, Yüzey veya Zemin Altı Güçlendirme, Drenaj, Filtrasyon, Geo-Membran Koruma Kapağı.
Otomotiv Endüstrisi :
Halı kaplama, İç Mekan Halıları, Bagaj Paspası ve Trimler, Baş ve Kapüşon Gömlekleri, Koltuk ve Kapı İç Mekanları, Ses yalıtımı, Kaput Yerleştirme Pedi, Ön Bileşen ve Gösterge Paneli Yalıtım Yastığı, Kapı İç Yalıtım, Yağ Filtrasyonu, Hava Filtrasyonu, Pil Ayırıcılar.
Ambalaj ve Paketleme :
Genel Ambalaj Torbaları, Alışveriş çantaları, Promosyon ve Hediyelik Çanta ve Ambalajları, Yiyecek ve İçecek Torbaları, Koruyucu Çanta ve Kılıflar, Elektronik Kılıflar, Yedek Parça Kılıfları, Temel Şok Emici Kılıflar ve Kapaklar, Reklam Malzemeleri, Koltuk Başlıkları, Etkinlik Süslemeleri.
İzolasyon ve Yalıtım :
Isı yalıtımı, Ses yalıtımı, Yer ve Duvar Kaplamaları, Çatı kaplama, Fayans Altlığı, Nem bariyeri, Nem Sabitleyici
Melt Blown Nonwoven Uygulaması:
Nonwoven ürünler yapmak için eriyik üfleme tekniği, son yıllarda nonwoven endüstrisinde en hızlı büyüyen tekniklerdenYüksek hızlı hava ile, kalıp ucundan kendiliğinden yapışan ince polimerik iplikçiklerin, bir hareketli bant üzerine (konveyör) yada döner silindirik kasnağın (tambur) üzerine üflenmesi ilkesine dayalı, tek kademe bir prosestir.
Üflenen polimerik iplikçikler, birbirine yüksek rastlantısal dolanma hareketi ağ oluşturur. Eriyik üflemeli ağlar, rastgele elyaf yönlendirme, düşük ila orta ağ mukavemeti gibi çok çeşitli ürün özellikleri sunar. Eriyik üflemeli malzemenin yaklaşık %40 'ı, birleştirilmemiş (monolitik) durumda, %60 'ı kompozit veya laminat malzeme bileşeni olarak kullanılır.
(Melt Blown) Eriyik üfleme işlemi; nonwoven uygulamaları arasında benzersizdir. En basit şekliyle pamuk şeker yapımının yüksek teknolojili versiyonu olarak değerlendirilebilir. Pamuk şekerleme yapılırken şeker eritilir ve döner bir çıkrıktaki küçük açıklıklardan basınç ve merkezkaç kuvveti tarafından iplikçik halinde gerilir. Benzer şekilde eriyik üflemeli sistemde, eksrüde edilmiş polimerik eriğin, kafadan (kalıp ucundan) 220-400 °C sıcaklıkta çıkmak üzereyken, her iki tarafından 300-900 km/s hızla üflenen hava ile sıkıştırılır ( aynı yönde birleştirilir). Hızlı hareket eden hava akımı, erimiş polimeri etkili bir şekilde gerer ve zayıflatır. Rastgele bir kesintili ince iplikçiler halinde katılaştırır. Bu ince polimerik iplikçikler daha sonra rastgele dolaşan bir ağ olarak yoğunlaştırılır ve ısıtılmış merdaneler arasında sıkıştırılır, etkin hava akımı da bu esnada uzaklaşır.
Tipik bir eriyik üfleme prosesi, ekstrüder, eriyik pompası, kalıp, hava kompresörü ve sarma ünitelerinden oluşur.


Melt Blown süreci, operasyonel ve malzeme olmak üzere iki kategoride değerlendirilebilecek değişim sürecine sahiptir. Operasyonel ve malzeme değişkenlerinin üzerinde oynanarak, istenen özelliklere sahip çeşitli meltblown kumaşlar üretilir.
-
Polimer üretim hızı
-
Polimer ve kalıp sıcaklıkları
-
Hava çıkış hızı
-
Hava sıcaklığı
-
Püskürme mesafesi
Bu parametreler, ana kumaş özelliklerini değişmesinde temel, rol oynayıcı basit bileşenlerdir. Bunlar çevrim içi yani çalışma esnasında müdahale edilebilen parametrelerdir.
Polimer ve hava çıkış hızları temel olarak nihai iplikçik çapını, dolanımını ve zayıflama bölgesinin kapsamını kontrol eder.
Hava akış hızı ile bağlantılı olarak polimer / kalıp ve hava sıcaklıkları, kumaşın görünümünü ve tutuşunu, üretimdeki kumaş homojenliğine etkendir.
Püskürme mesafesi (kalıp ucu - tambur mesafesi) genellikle kumaşın açıklığını ve iplikçikler arası termal bağlanmayı etkiler. Mesafe arttıkça iplikçik çapı hafifçe artar.
-
Kalıp deliği boyutu
-
Hava boşluğu
-
Hava açısı
Bu parametreler, ağ toplama tipini belirler. Bunlar çevrim dışı yani çalışma durduğunda müdahale edilebilen parametrelerdir.
Kalıp deliği boyutu, kalıp tasarım parametreleri ve kalıp ayarının fiber boyutunu etkiler. Kalıp deliği boyutu, polimer eriyiğini tıkanmadan geçecek kadar büyük olmalıdır.
Hava boşluğu, hava çıkış basıncını ve aynı zamanda elyafın kırılma derecesini etkiler.
Süreç ham maddeleri :
Temel olarak, uygun bir işlem sıcaklığında düşük eriyik viskozite verebilen ve püskürme mesafesi içinde katılaşabilen polimerler, bu süreçte tercih edilen polimerlerdir. Polimerlerin granül boyutlu olması, hızlı erimesi ve daha eşit bir ısı dağılımı sağlaması açısından tercih edilir.
Polipropilen (PP) tam da istenen bu özellikleri taşır. İşlenmesi kolaydır ve iyi bir ağ oluşturur.
Polietilen (PE) ince iplikçik halinde eritilerek üflenmesi polipropilene göre daha zordur. PE 'nin elastikliği nedeniyle çekilmesi zordur.
PBT ile çok yumuşak, ince iplikçik ağları üretilir.
Naylon 6'nın da işlenmesi kolaydır ve iyi, kaliteli iplikçik ağları oluşturulur.
Naylon 11, çok sıra dışı deri hissi veren ağların oluşumunda tercih edilir.
Polikarbonat (PC) ile çok yumuşak lifli ağlar üretilir.
Polistiren (PS) esasen hiçbir atış kusuru olmayan son derece yumuşak, kabarık bir malzeme üretiminde tercihtir.
Nonwoven Dokumasız Kumaş Türleri:
Genel olarak 4 ana kategoriye ayrılır.
Tek kullanımlık dokunmasız kumaşlar: Bu tür dokunmamış kumaşlar çoğunlukla tek kullanımlık ürünler veya yeniden kullanılabilir ürünler (örneğin, birkaç kez yıkanabilen ve yeniden kullanılabilen toz bezleri) için yapılır.
Genel uygulamalar için dokumasız kumaşlar: Çocuk bezleri ve hijyenik pedler gibi kişisel hijyen ürünlerini içerir; cerrahi önlükler ve örtüler gibi tıbbi ürünler; cerrahi ve endüstriyel maskeler, bandajlar, mendiller ve havlular; özel etkinlikler için önlükler ve hatta kostümler.
Dayanıklı dokunmasız kumaşlar: Perdeler, mobilya döşemeleri, şilte dolguları, havlular, masa örtüleri, battaniyeler ve halı arkalıkları ve şapkalar, astarlar, telalar, ara yüzeyler gibi giyim ve konfeksiyon gibi hem ev eşyalarında hem de ev mobilyalarında yaygın olarak kullanılır. diğer kumaşların takviyesi.
Nonwoven üretiminin optimize edilmesi amacıyla kalsiyum karbonat dolgu maddesi kullanılmaya başlanmıştır. Kalsiyum karbonat tozu (CaCO3), plastik reçineler ve diğer özel katkı maddelerinden yapılan kalsiyum karbonat dolgu, dokumasız üretim için en etkili malzeme çözümlerinden biridir. Bu malzemenin uygulanması, son ürünlere çeşitli faydalar sunar:
Kalsiyum karbonat dokumasız kumaştan üretilen ürünlerin, tıbbi ve kişisel bakımdan hijyen, jeotekstil (emme, ayırma, filtreleme, koruma, güçlendirme ve boşaltma gibi teknik endüstrilerde kullanılan kumaşlar) gibi alanlara kadar çeşitlilik gösterdiği alanlardır.
Dokumasız malzemelere kalsiyum karbonat dolgusu eklemenin avantajları :
-
Ürün yüzeylerinin iyileştirilmesi sağlar
-
Parlaklığı azaltarak, yüzeyi daha mat ve daha opak hale getirerek kumaş yapısının daha iyi örtme kabiliyetine yol açar
-
Sınırlı sarılık ile doğal beyaz renk verir
-
Malzeme dokusunun iyileştirilmesi sağlar
-
Rahat ve pamuksu bir his yaratır
-
Dokunulduğunda karbon ayak izini önler
-
Hava filtrasyonu ve yağ emilimi için daha fazla mikro alan oluşturur
-
Artan termal iletkenlik ve fiziksel güç katar
-
İşlem sıcaklığının düşürülmesi sağlar
-
Üretimin daha yüksek üretkenlik elde edilmesinin önünü açar, yani kapasiteyi arttırır.
-
Enerji ve üretim maliyetlerinden tasarruf sağlar.
-
Çoklu baz reçineleriyle (iyi dağılım kabiliyeti sayesinde) kolayca işbirliği yapar ve çeşitli yöntemlerle işlenebilir
Kalsiyum Karbonaın tavsiye edilen kullanım oranları:
-
ince kumaşlarda %5-20,
-
orta kumaşlarda %20-35,
-
kalın kumaşlarda ise %60'lara ulaşmaktadır.
Son derece iyi bir dispersiyon ve stabilite gerektiğinde,
dolgu masterbatch tipik olarak %78-80 yükleme oranı ve 20-40g/10 dak eriyik akış indeksi ile uygulanır.
Akrilik Lif Üretimi
Yaş çekim yönteminde : üretiminde lif oluşumu koagülasyon banyosu sayesinde meydana gelmektedir.
Dolayısı ile yaş çekim yöntemiyle elde edilen liflerin fiziksel özellikleri büyük oranda koagülasyon banyosu şartları tarafından etkilenmektedir. Bu yüzden koagülasyon banyo parametrelerinin çok iyi bir şekilde kontrol edilmesi gerekmektedir. Bu makalede hem koagülasyon banyosunda meydana gelen difüzyon ve faz değişimi gibi bazı fiziksel olaylar ve hem de bu olayların meydana gelmesinde etkili olan bazı koagülasyon banyo parametreler özetlenmiştir. Ayrıca bunların liflerin fiziksel özellikleri üzerindeki etkisi belirtilmeye çalışılmıştır.
Akrilik lif üretiminde kullanılan poliakrilonitril (PAN) polimerleri akrilonitril monomerlerinin radikal zincir polimerizasyonu ile elde edilmektedir. Poliakrilonitril polimerleri eriyikten lif çekimi için kullanılan yüksek sıcaklıklara kadar ısıtıldığında erimeyip kimyasal yapısında değişiklikler meydana geldiği için eriyikten lif çekimi yöntemine uygun değildir. Dolayısı ile PAN polimerlerinden eriyikten lif çekimi yöntemiyle lif üretmek mümkün olmamaktadır. Ancak poliakrilonitril (PAN) polimerleri; uygun çözücüler içerisinde çözülerek lif çekimi için uygun akışkanlıkta polimer çözeltisi haline getirilebilmektedir. Bu sebeplerden dolayı PAN polimerlerinden lif üretimi çözeltiden lif çekimi yöntemine göre gerçekleştirilmektedir.
PAN polimeri bilinen bir çok çözücüde çözünmemektedir. Çözücü solvent olarak en çok Dimetil Formamid (DMF) ve Dimetil Asetamid (DMAc) solventleri kullanılmaktadır. Bu solventler üretilen liflerinin özelliklerinin belirlenmesinde de rol oynamaktadır.
Hazırlanan polimer çözeltisinden lif çekimi için, üzerinde çok ince delikler olan düze (spinneret) sistemleri kullanılmaktadır. Bu düzeler üzerindeki delik sayısı, kullanılacak çekim yöntemine göre çok büyük değişiklikler göstermektedir. Ayrıca bu delikler düze üzerinde segmentler yani gruplar halinde yerleştirilmiştir. Bu sayede düzelerden fışkırtılan filamentlerin arasına koagülantın daha iyi nüfuz etmesi sağlanmaktadır.
Akrilik Lif Çekiminde Kullanılan Solventler ve Çekim Dopundaki Polimer İçerikleri:

Kuru çekim yönteminde : çekim çözeltisi kulesi içerisine yerleştirilmiş olan düzelerden çekim kulesi içerisine fışkırtılmaktadır.
Aynı zamanda kule içerisine gönderilen ısıtılmış gaz sayesinde dop polimeri içerisindeki solventin büyük oranda uzaklaştırılmasıyla polimerin katılaşarak lif haline gelmesi sağlanmaktadır.
Yaş çekim yönteminde ise çekim çözeltisi, koagülant içeren bir sıvı banyosuna daldırılmış olan düze sisteminden banyo içerisine fışkırtılmaktadır. Banyo içerisindeki nonsolvent ile polimer içerisindeki solventin karşılıklı difüzyonu sayesinde polimerin katılaşarak lif haline dönüşmesi sağlanmaktadır. Yaş çekimle akrilik üretiminde ilk lif formasyonu koagülasyon banyosu içerisinde gerçekleştiği için koagülasyon banyosu parametreleri liflerin bilhassa fiziksel özellikleri üzerinde belirleyici bir rol oynamaktadır .
Hem kuru ve hem de yaş çekimden sonra Akrilik liflerinin gördüğü işlemler esas olarak aynıdır. Ancak bu işlemlerin sıraları veya uygulanma şartları bir miktar farklılık gösterebilmektedir. Bu işlemler yıkama, gerdirme, preparasyon, kurutma, kıvırcıklaştırma, tavlama işlemleridir. Bütün bu işlemlerin liflerin fiziksel özellikleri üzerine etkisi olmaktadır.
Yaş çekim yöntemine göre poliakrilonitril lif üretim tesisi:
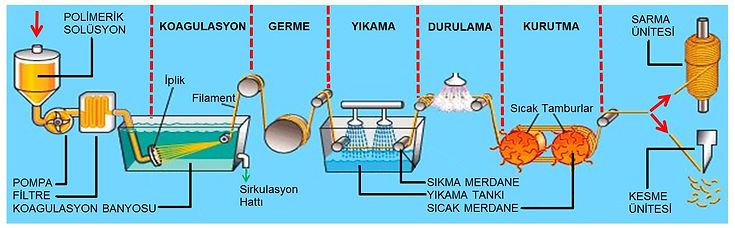
Koagülasyon : düzelerden çok ince sıvı hüzmeleri halinde fışkırtılan polimer çözeltisinin içerisindeki solventin büyük miktarda uzaklaştırılarak polimer maddenin lif formuna dönüştürülmesi işlemidir. Bu işlem için kullanılan koagülasyon banyosu, içeriğinde solvent ve nonsolvent bulunan bir sıvı ortamdır. Koagülasyon banyosunda solvent olarak polimer çekim çözeltisindeki solventin aynısı kullanılmaktadır. Nonsolvent olarak ise büyük çoğunlukla polimerin çözünmediği ancak dop içerisine nüfuz edebilen ve solvent ile karışabilen bir sıvı olan su kullanılmaktadır.
Koagülasyon banyosu, lif üretiminde ilk lif oluşumunun gerçekleştiği aşamadır ve lif özelliklerinin oluşmasında çok önemli bir rol oynamaktadır. Koagülasyon banyosunda polimer maddenin jel halinde lif formuna gelmesi, solvent ile nonsolventin karşılıklı akarak yer değiştirilmesiyle gerçekleşmektedir.
Koagülasyon banyosunda polimer / solvent / nonsolvent etkileşimi sonucunda lif şekillenmekte ve değişik özellikler kazanmaktadır. Bu etkileşimde, koagülasyon banyosunda meydana gelen iki olay özellikle çok önemli rol oynamaktadır. Bunlar Difüzyon ve faz değişimi olaylarıdır. Liflerin yapısının belirlenmesinde bu iki önemli olay birlikte etkili olmaktadır.
Yaş çekimde faz değişimi ve difüzyon hızından dolayı gözenekli bir lif yapısı elde edilir.
Kuru çekimde 0.1µ büyüklüğündeki gözenekler oluşurken, yaş çekimde bu gözenekler 0.3µ civarında olmakta ve daha da büyüyerek 10µ a kadar çıkabilmektedir.
Fışkırtma Hızı : Poliakrilonitril çekim çözeltisinin (dopunun) düzelerden banyo içerisine fışkırtılma hızı (V),
koagülasyon banyosundan çıkış hızından (V1) daha büyüktür.
2 Q V /4 D = π
D: düze delik çapı
Q: debiyi ifade etmektedir.
Bu durum çekim banyosu içerisinde filamentin gerdirilmediği anlamına gelmemektedir. Çünkü filament düzeden çıktığında üzerine etki eden normal basınçtan dolayı, şişmeye ve hızı azalmaya başlayacak ve filamentin serbest hızı (Vf) banyodan çıkış hızından daha düşük (Vf < V1 < (V) ) olacaktır. Dolayısıyla banyo içerisinde filament bir miktar gerdirilmektedir.
Şişme yüzünden koagülasyon banyosu içerisine fışkırtılan filamentin çapı düze delik çapının 10 katına kadar çıkabilmektedir.
Difüzyon olayı : koagülasyon banyosuna fışkırtılan filament içerisindeki solvent ile banyo içerisindeki nonsolventin karşılıklı akarak yer değiştirmesidir. Difüzyon ile polimer dopu içerisindeki solvent miktarı azalmakta ve bu azalma sayesinde filament katı bir jel halini almaktadır. Ayrıca bu difüzyon olayı yaş çekim ile elde edilen liflerin yapısındaki gözeneklerin meydana gelmesine sebep olmaktadır. Daha sonraki işlemlerde bu gözeneklerin bir kısmı elimine edilse de tamamen ortadan kaldırılamamaktadır.
Faz Değişimi : Faz değişiminde düzelerden fışkırtılan solventçe zengin filamentler önce polimer açısından zengin bir jel haline dönüşmekte ve daha sonraki işlemlerde solventin tamamen uzaklaştırılmasıyla katı hale gelmektedir.
Flekso Baskı Ünitesi
Genellikle üfleme film hattını takip eden ikinci kademe dilimleme, kesme üniteleridir.
Ancak ürünler üzerinde baskı olması istenmesi halinde korona ve hemen akabinde baskı (özellikle flekso) üniteleri ikinci kademeyi oluşturur. Ambalaj basımında en yaygın kullanılan baskı şeklidir. Fleksografik baskı, kauçuk esaslı, sentetik veya lamine edilmiş bir malzeme olabilen bir alt tabaka üzerine baskı yapmak için esnek bir kabartma levha kullanan bir yöntemdir. Polyester, OPP, naylon ve PE gibi filmler, kağıtlar, karton levhalar, dokuma olmayan tekstiller, kaplamalı veya kaplanmamış astarlar flekso baskıda kullanılabilecek tabakalardır. Günümüzün flekso baskı makineleri, gerekli baskının bir ayna kabartma görüntüsünü içeren fotopolimer baskı plakalarını
kullanmaktadır.
Flekso baskı tekniğinde; mürekkep haznesindeki mürekkebin tramlı (Aniloks) merdaneye oradan kalıp silindirine aktarılması ve baskı silindiri ile temas halinde aradan geçen baskı yapılacak malzemenin üzerine aktarılması ilkesi vardır.
Mürekkep haznesinden mürekkep bir merdane ile anilox merdaneye taşınır. Mürekkebin fazlası merdane üzerinden rakle bıçağı (doctor blade) ile sıyrılır. baskı temasının üzerine işlenmiş olan klişeye mürekkebi aktarmak için anilox merdaneden sleeve/kazan üzerine
aktarım yapılır. Mürekkebi alan klişe tambur üzerinden geçen baskı malzemesine deseni iletir. Her nekadar basit bir tarif olarak iafade edilmiş olsa da, flekso baskı işlemi tamamen teknik bir süreçtir. Baskı kalitesinin sürekliliği için, mürekkep viskoz değerlerinin sürekli
takibi, rakle bıçaklarının anilox üzerine, aniloxun klişe üzerine, klişenin film üzerine baskı (force) değer ayarları, film kalitesinin (bayraklanma, kırışıklık, korona şiddeti) devamlı kontrollerini, sarma gerilimi ve merdanelerde tansiyon ayarlarının takibini, hizalama referans noktalarının (cross) stabilliği gibi sürekli takip ve ölçüm yapılması gereken hassas noktalara sahiptir. Flekso baskı hatları, çoğunlukla blown film üretim hattından sonra, ikinci kademe üretim hatlarıdır. Ve buradan çıkan ürünler, daha çok poşet, bant, shrink torba gibi dilimleme, sürüm ve kesme ünitelerinde kullanılacak yarı mamül / yarı form niteliğinde ürünlerdir.
Anilox (Tramlı Merdan) :
Flekso sistemde mürekkebi istenilen ölçüde kalıba taşıyan merdanenin ismidir. Son yıllarda dia baskılarının flekso sistemde yapılması sebebiyle çok ince anilox merdaneler devreye girmiştir. Anilox merdaneler 60’lık, 120’lik, 200’lük vs. gibi sayılarla anılır. Rakam büyüdükçe anilox üzerendeki tiflerin sıklığı artar, derinliği azalır. Bu nedenle transfer edilen mürekkep filmi inceldiğinden alınan renk şiddeti azalır. Bu tip ince aniloxlar için daha konsantre mürekkepler hazırlanması gereklidir.
Hazne Merdanesi :
Mürekkebin bulunduğu mürekkep haznesinin içinde dönen, sisteme göre değişen, genellikle kauçuk kaplanmış silindirlerdir.Hazne silindiri mürekkebi sistemin diğer elemanlarına aktarmakla görevlidir. Hazneden kauçuk yardımıyla aldığı mürekkebi temas halinde olduğu tramlı (aniloks) silindire aktarır.
Rakle Bıçağı (Doctor. Blade) :
Mürekkep sıyırma bıçağı. Flekso baskı sisteminin önemli parçalarından birisidir. Hazne içi merdaneden alınan mürekkep aniloks merdane üzerine temas eden rakle ile istenilen film kalınlığından inceltildikten sonra materyal üzerine aktarılır. Aniloks merdane üzerindeki mürekkep kalınlığını rakle basıncı yani forsası belirler.
Baskı Altı Malzemesi (Film) :
Ambalaj dalında film lifsiz organik bir maddenin ince ve elastik bir tabakasıdır. Flexo baskı işinde genellikle; polietilen, polivenil klorür, polipropilen, poliamid, poliester ve kağıt gibi malzemelerden imal edilen rulo halindeki filmler kullanılır.
Flexo Kalıbı (Klişe) :
Flekso baskı makinelerinde kullanılmak üzere değişik malzemeler üzerine basılacak resim ve yazıları aktarmada kullanılan lastik ve fotopolimer malzemelerden fotografik ve dijital yöntemlerden yararlanılarak hazırlanan malzemelere flekso baskı kalıbı denir. Ayrıca polimerik malzemeden fotomekanik usullerle üretilen fotopolimer kalıplar da vardır.
Bu kalıplar genellikle bükülebilir şekilde yapılmaktadır. Fotomekanik yedirme yöntemi ile çinko plakalardan yapılan kalıplarda kullanılabilir.
Kalıp silindiri (Kazan) :
Klişelerin üzerine monte edildiği değişik çaplara sahip silindirlerdir. İşin boyutuna göre çap kalınlıkları değişiklik gösterebilir. Silindirinin çapı ve boyu orantılı bir şekilde taksimatlandırılmıştır.
Bu taksimatlar, montaj sırasında klişenin düz veya diyagonal olarak bağlanmasını kolaylaştırmaktadır.
Sleev (Gömlek) :
Klişelerin üzerine montaj edilerek silindire geçirildikleri araçlardır. Kısa metrajlı ve tekrarlanan işler, klişenin tekrar ayarlanarak monte edilmesine gerek kalmadan ekonomik olarak basılmasını sağlayan araçlardır. Polyester, çelik, nikel, durofleks (üretan) ve kaplı sleev çeşitleri mevcuttur. Bu montaj basınçlı hava ile gömleğin silindire takılması ile yapılır.
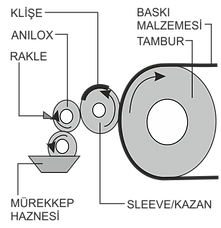
Flekso Baskıda Kullanılan Temel Terimler
Tansiyon:
Flekso baskı makinelerinde materyalin baskı esnasında ki gerginliğidir. Tansiyon değeri sürekli ve kesintisiz baskı için önemlidir. Genellikle kağıt gibi kalın malzemelerde yüksek, (PE, PP,OPP vs) gibi ince malzemelerde ise düşük tansiyon uygulanabilir. Tansiyon ayarında; filmin esneyebilirlik kabiliyeti, ısıya dayanıklılığı, gerilime hassaslığı , kalınlığı ve kağıtlar için gramaj özellikleri dikkate alınması gereken hususlardır.
Viskozite:
Sıvıların akmaya karşı gösterdikleri direnç olarak tarif edilir. Flekso baskıda mürekkep yoğunluğu çok önemlidir. Bu nedenle mürekkebin viskozitesi sürekli olarak denetlenmelidir.
Densite:
Baskı altı malzemelerinin ve mürekkkebin yoğunluğu. Yüksek olması ağırlığı ve çokluğu, düşük olması ise hafifliği ve azlığı.
Forsa:
İki silindirin birbirine veya aralarından geçen baskı materyaline yapmış olduğu basınca forsa denilmektedir. Forsa, silindirlerin birbirlerine yaklaşmaları esnasında aralarında oluşan boşluğun baskı materyali veya mürekkep film tabakası tarafından kullanılması esnasında baskıyı etkilemektedir.
Korona:
Baskı yapılacak malzemelerin yüzeyinin baskı yapılabilir hale getirilmesi yüzey geriliminin ayarlanması işlemidir. Genellikle PE, PP, PVC gibi malzemeler için 36-38 dyn/cm korona uygulanır. Koronanın yüksek olması da düşük olmaması kadar sorun yaratır.
Laminasyon:
İki veya daha fazla malzemenin birbiriyle yapıştırılması işi. Laminasyonun amacı; ambalajın içine konulan gıda maddelerinin bozulmasına neden olabilecek nem, ışık, gaz geçirgenliklerinin azaltarak istenen korunmanın sağlanması ve tüketiciyi cezbedecek albeniyi elde etmektir.
Bloklaşma:
Baskılı işin sıkı sarım, yüksek bombardıman, iki tarafı koronalı malzemeler ve sıcakta bekletilme gibi nedenlerle baskı yapılmamış yüze transfer etmesi ve yapışması sonucunda oluşan, baskının kötü kokmasına da neden olan bir problem.
Adezyon:
Farklı iki madde arasında var olan ve bu iki maddenin birbirine yapışmasını sağlayan çekim kuvvetidir. Flexo baskı işinde; mürekkebin baskı yapılan malzemeye yapışma kabiliyetini ifade eder.
Selofan:
Odundan elde edilen selüloz daha sonra kimyasallarla reaksiyona sokularak viskoz ve daha sonra da selülozhidrat haline getirilerek film şeklinde preslenir.Bu preslenen filme selofan denir.
Şap (Asit) Banyosu:
Çinko kalıbın kimyasallarla yıkanması işlemidir.
Emülsiyon:
Kalıba dökülen hassas madde. (Işığa karşı duyarlı madde)
Shore:
Klişe kalıpların sertlik derecesi.
Rölyef:
Kabartma etkisi
Solvent:
Tiner, neft, terebentin, vernik, glikol, etilalkol gibi sıvı akışkanlar.
Penetrasyon (Nüfuz etme):
Mürekkebin sıvı fazının baskı yüzeyi tarafından emilmesi yoluyla oluşan kuruma şeklidir.
Kanama:
Baskı yapılan yüzeyde renklerin birbirine karışması.
Anilin boya:
Taş kömürü eterinden elde edilen organik boyadır. Flekso baskıda kullanılır.
UVC pozu:
Flekso baskıda kalıp pozlama için kullanılan ve dalga boyu en düşük olan ışık kaynağı. UVC-pozu plaka yüzeyindeki yapışkanlığı ortadan kaldırır.UVC ışığı insan gözüne son derece zararlı olduğundan çıplak gözle bu ışığa direkt olarak bakılmamalıdır.