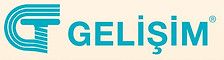


Hidrokarbonlar
Hidrojen ve karbon olmak üzere iki elementten oluşan organik bir bileşiktir. Petrol bileşiminin büyük bir kısmı değişen uzunluklardaki hidrokarbonlardan oluşur.
En küçük hidrokarbon metan, tek bir karbon atomu ve dört hidrojen atomundan oluşur. Bununla birlikte, hidrokarbonlar, zincirler, daireler ve diğer karmaşık şekiller dahil olmak üzere birçok yönden birbirine bağlanmış yüzlerce veya binlerce bireysel atomdan oluşabilir.
Hidrokarbonların özelliklerini sınıflandırmak için birkaç temel türe ayrılırlar.
Alkanlar: Bunlar doymuş hidrokarbonlar olarak adlandırılır. Yani sadece tüm karbon atomları arasında tek bağlar içerirler. Alkanlar, petrol yakıtlarının temelidir ve doğrusal ve dallı formlarda bulunurlar.
Doymamış Hidrokarbonlar: Karbon atomları arasında bir veya daha fazla çift bağa sahip olan hidrokarbonlara alken denir.
Sikloalkanlar: Bir veya daha fazla halka yapısı içeren herhangi bir hidrokarbon.
Aromatik Hidrokarbonlar: Areneler olarak da adlandırılan aromatik hidrokarbonlar, karbon atomlarının birbirini izleyen çift ve tek bağlarla bağlandığı benzersiz bir karbon molekülleri sınıfıdır. Bu molekül sınıfı, karbon atomları arasındaki bağların tek ve çift bağlar arasında bir ara bağ olduğu özel halka yapılarına sahiptir.
Bu sınıftaki moleküller, endüstriyel çözücü «benzen» içerir.
Benzen (C6H6): Diğer hidrokarbonlar gibi benzen de petrolün doğal bir bileşenidir. Oda sıcaklığında renksiz, yanıcı, tatlı kokulu bir sıvıdır ve yüksek oktan sayısına sahip olduğu için çoğu benzin karışımının bir bileşenidir.
Benzen de oldukça kanserojendir ve kemik iliği yetmezliği ve kemik kanserine neden olduğu iyi bilinmektedir. Elbette, “hoş aroması” nedeniyle tıraş sonrası ve diğer kozmetiklerde bir katkı maddesi olarak kullanıldığında kanserojenliği iyi bilinmemektedir.
En büyük benzen kullanımı (% 50), stiren ve polistren plastiklerinin ürünüdür. Ayrıca Naylon üretiminde önemli olan sikloheksan olarak bilinen bir moleküle dönüştürülür. Siklohekzan üretmek için benzenin yaklaşık% 15'i kullanılır. Böcek ilaçlarından kauçuğa kadar her şeyde daha küçük miktarlar kullanılır.
Benzen yapısı iki şekilde çizilebilir. İlkinde, çift bağ karakteri açıkça çizilir. Kısa elli versiyonda, yapıyı göstermek için halkanın içine bir daire çizilir. Benzen içindeki her bir karbon atomuna bağlı tek bir hidrojen vardır.
Aşağıdaki I. ve II. çizimleri eştir. Pratikte III. çizim kullanılır.
Benzen, renksiz, alevlenebilen, kaynama noktası 80,1 °C, erime noktası 5,5 °C olan bir sıvıdır.
Binükleer Aromatik Hidrokarbonlar: Molekülünde iki benzen halkası içeren bileşiklerdir.
Hidrokarbonlar
Hidrojen ve karbon olmak üzere iki elementten oluşan organik bir bileşiktir. Petrol bileşiminin büyük bir kısmı değişen uzunluklardaki hidrokarbonlardan oluşur.
En küçük hidrokarbon metan, tek bir karbon atomu ve dört hidrojen atomundan oluşur. Bununla birlikte, hidrokarbonlar, zincirler, daireler ve diğer karmaşık şekiller dahil olmak üzere birçok yönden birbirine bağlanmış yüzlerce veya binlerce bireysel atomdan oluşabilir.
Hidrokarbonların özelliklerini sınıflandırmak için birkaç temel türe ayrılırlar.
Alkanlar: Bunlar doymuş hidrokarbonlar olarak adlandırılır. Yani sadece tüm karbon atomları arasında tek bağlar içerirler. Alkanlar, petrol yakıtlarının temelidir ve doğrusal ve dallı formlarda bulunurlar.
Doymamış Hidrokarbonlar: Karbon atomları arasında bir veya daha fazla çift bağa sahip olan hidrokarbonlara alken denir.
Sikloalkanlar: Bir veya daha fazla halka yapısı içeren herhangi bir hidrokarbon.
Aromatik Hidrokarbonlar: Areneler olarak da adlandırılan aromatik hidrokarbonlar, karbon atomlarının birbirini izleyen çift ve tek bağlarla bağlandığı benzersiz bir karbon molekülleri sınıfıdır. Bu molekül sınıfı, karbon atomları arasındaki bağların tek ve çift bağlar arasında bir ara bağ olduğu özel halka yapılarına sahiptir.
Bu sınıftaki moleküller, endüstriyel çözücü «benzen» içerir.
Benzen (C6H6): Diğer hidrokarbonlar gibi benzen de petrolün doğal bir bileşenidir. Oda sıcaklığında renksiz, yanıcı, tatlı kokulu bir sıvıdır ve yüksek oktan sayısına sahip olduğu için çoğu benzin karışımının bir bileşenidir.
Benzen de oldukça kanserojendir ve kemik iliği yetmezliği ve kemik kanserine neden olduğu iyi bilinmektedir. Elbette, “hoş aroması” nedeniyle tıraş sonrası ve diğer kozmetiklerde bir katkı maddesi olarak kullanıldığında kanserojenliği iyi bilinmemektedir.
En büyük benzen kullanımı (% 50), stiren ve polistren plastiklerinin ürünüdür. Ayrıca Naylon üretiminde önemli olan sikloheksan olarak bilinen bir moleküle dönüştürülür. Siklohekzan üretmek için benzenin yaklaşık% 15'i kullanılır. Böcek ilaçlarından kauçuğa kadar her şeyde daha küçük miktarlar kullanılır.
Benzen yapısı iki şekilde çizilebilir. İlkinde, çift bağ karakteri açıkça çizilir. Kısa elli versiyonda, yapıyı göstermek için halkanın içine bir daire çizilir. Benzen içindeki her bir karbon atomuna bağlı tek bir hidrojen vardır.
Aşağıdaki I. ve II. çizimleri eştir. Pratikte III. çizim kullanılır.
Benzen, renksiz, alevlenebilen, kaynama noktası 80,1 °C, erime noktası 5,5 °C olan bir sıvıdır.
Binükleer Aromatik Hidrokarbonlar: Molekülünde iki benzen halkası içeren bileşiklerdir.
Hakkında
Kyäni, faydalı bileşenlerden oluşan besin takviyesi ürünlerini; benzersiz iş fırsatıyla birlikte dünya çapında 50'den fazla ülkeye ulaştırmaktadır. İdeal sağlığımızı korumak için günlük olarak Kyäni ürünlerini kullanırız, bu ürünleri başkalarıyla paylaşırız, işimizi inşa etmek ve sürdürmek için neredeyse her gün belirli bir saatimizi işe adarız ve başkalarını da Kyäni fırsatına dahil ederek veya Potato Pak ve Caring Hands programlarına katkı sağlayarak başarımızı başkalarıyla paylaşırız.
Hakkında
Kyäni, faydalı bileşenlerden oluşan besin takviyesi ürünlerini; benzersiz iş fırsatıyla birlikte dünya çapında 50'den fazla ülkeye ulaştırmaktadır. İdeal sağlığımızı korumak için günlük olarak Kyäni ürünlerini kullanırız, bu ürünleri başkalarıyla paylaşırız, işimizi inşa etmek ve sürdürmek için neredeyse her gün belirli bir saatimizi işe adarız ve başkalarını da Kyäni fırsatına dahil ederek veya Potato Pak ve Caring Hands programlarına katkı sağlayarak başarımızı başkalarıyla paylaşırız.
Sayfa Yapım Aşamasındadır.
Sayfa Yapım Aşamasındadır.
Eğitim / Bilgi / Çözüm Platformu
Süreçlerde Yaşanan Sorunlara Genel Bakış
Ekstrüzyon üretiminin başarılı olmasını sağlamak için, her parametre tanımlanmalı, kontrol edilmeli ve izlenmelidir. Bazı değişkenler ekipmana, bazıları çalışma koşullarına bağlıdır. Tüm değişkenler kalıbın kalitesinden, sıcaklıklara ve basınçlara kadar değişir.
Üretim sürecine başlamadan önce bazı önleyici tedbirler alınması yerinde olur.
Sıcaklık, basınç, devir ve amper için kullanılan tüm ekipmanların periyodik bakımları yapılmalıdır.
Sabit bir hammadde prosesi sorunları minimize eder. Bu, hammaddenin nasıl depolandığıyla başlar. Aşırı sıcaklık değişimlerine maruz kalmadan temiz ve kuru bir alanda depolama gerekir. Reçinenin tutarlı olmasını sağlamak için, bazı şirketler malzemeyi ve kayıt yoğunluğunu, eriyik indisini, kesme oranını vizkozite verilerini ve gerilme mukavemetini ölçmek için reçine analizi yaparlar. Çok kuru ise, eriyemeyebilir ve reçine işlenemez. Aynı hammaddenin lot geçişleri bile saklama şartlarının değişmesine etken olabilir.
Tipik ekstrüzyon problemleri birkaç ana kategoriye ayrılır:
Estetik kusurlar (örneğin, çukurlar, siyah teknik özellikler, iğne delikleri, sürükleme işaretleri, kalıp çizgileri, batma izleri) Boyut, şekil kusurları gibi. Bir problem meydana geldiğinde, ilk adım, ekipmanla başlayan üretim sürecinin bileşenlerini incelemektir. Vida tasarımının ve / veya sıcaklığın soruna neden olması ya da kalıbın uygun şekilde yapılmaması ya da ekstrüzyon hattındaki belirli bir bölgenin sıcaklığı yanlış olması sorunun kaynağı olabilir. Ekstruzyon sonrası bitmiş ürün özelliklerine, boyutlarına uymadığı zaman incelenmesi gereken ana değişkenler şunlardır:
Erime basıncı, erime sıcaklığı, kovan sıcaklığı, kalıp sıcaklığı, ısıtıcılar, rezistanslar, soğutma sistemi, vidanın hızı, yapısı, Amperlerde motor yükü
üretim hat hızı, kalıp aşınması veya yanlış tasarım.
Ekstrüzyonda sorunlarla karşılaşıldığında; üretimciler normalde kararlı bir işleminde, düzgün çalışmayan teknik ekipmandan, teknisyenler de mevcut üretim koşullarının (yani, sıcaklık, basınç, malzeme lotu, vb.) yanlış uygulanmışlığından bahsedecektir. Ve sorun çözümüne bu açıdan yaklaşacaktır.
Üreticilerin teknik yaklaşımlara, teknisyenlerin üretim süreçlerine vakıf olmamaları, ekstruzyon sorunlarında ekip çalışmalarının önemini bir kere daha ortaya koymaktadır.
Tarafların, ama proses ama bakım,arıza kayıtlarını sağlıklı bir şekilde tutmamış olmaları ise, adeta «Amerikan'nın tekrar tekrar keşfi» ne yol açacaktır.
Bu bakımdan Ekstrüzyon sorunlarının çözümünde en temel uygulama, kalite kayıtları adı altında tüm gelişmelerin «ortak bir havuzda» tutulması, özellikle sorun giderme zaman çizelgelerinin oluşturulması atılması gereken ilk adımdır.
Ekstrüzyon süreci kelimenin tam anlamı ile bir "kara kutu" işlemidir.
Bir ekstrüderin içinde neler olduğunu gözle görülmez, bu yüzden kovan/ocak içinde neler olup bittiğini tasavvur edebilmek için, ekstrüder bileşenlerine ve bu bileşenlerin taşıdığı değerlere dair bilgiye sahip olmak gerekir.
Vida çapı, boyu, karakteristiği, vidaya dönme hareketini veren motor/redüktör gücü, ısıl işlemin ana argümanı rezistanslar, bulundukları konumlar, ısı değerini ölçen termokulplar, ısıl ya da hareket sensörleri, zamanlama regüleleri soğutma hattı sıcaklıkları vs.
Hepsinden önemlisi bunların oluşturdukları değerlerin okunduğu dijital/analog göstergeler.
Tüm sensörlerin çalıştığından ve okumaların doğru bir şekilde kalibre edildiğinden kesinlikle emin olmalıdır.
Bunlardan başka, operatörlerinin; kurutucular, harmanlayıcılar, granülatörler, konveyörler ve besleyiciler, dişli pompaları, ekran değiştiriciler, kalibratörler, su havuzları ve olukları, lazer göstergeleri, çektirmeler ve sarıcılar hatta kalıp tasımı gibi ekstruzyon öncesi ve sonrası ekipmanlar hakkında da bilgi sahibi olmaları gerekir. Ekstrüzyon problemlerini çözmek için sürecin başından sonuna anlaşılmış olması gerekir. İşin başında malzeme ve ekipman özelliklerini kapsayan bir eğitim gereklidir. Ancak bu genellikle en az etkili ve bazı açılardan en pahalı yöntemdir.
Bir ekstrüderin eğitimsiz personel tarafından uygun olmayan şekilde çalıştırılması, masraflı hasarlara ve hatta işçi yaralanmalarına neden olabilir.
İyi bir proses yönetimi için, sorunsuz üretim yapmış olmak kadar, çıkan sorunların da anında müdahale edilerek geçiştirilmiş olması göstergedir.
En temel sorun çözme işlem basamağı; sorunsuz süreçlerdeki işlem koşulları ile karşılaştırılmasıdır. Bunun için «kalite kayıtları» adıyla da tutulan işlem kayıtlarının tutuluyor olması gerekir.
Bir «sorun giderme zaman çizelgesi» tutuluyor olması işlerin büyük bir kısmını kolaylaştıracaktır.
Sorun Gidermede Zaman Çizelgesi
Proseslerde yaşanan sorunların malzeme/ürün üzerinde ne tür bir değişiklik oluşturduğunun ve hangi müdahalelerle çözümleme yapıldığının tarihsel kayıt dökümandır. Yani tutulan tüm arıza kayıtları ile, proses üzerinde uygulanan tüm değişiklik ve sonuçları raporunun tablolaştırılmış, akış diagramı haline dönüştürülmüş hali.Böyle bir kayıt dökümanı oluşturmuş olmanız, «sorun çözücü» olarak kariyerinize kesinlikle etki edecektir.Zaman çizelgesine, süreç bozukluğunun fark edildiği noktadan itibaren, tüm işlem verilerinin (sıcaklık, basınç, devir, boyut, hangi vida, kalıp, hammadde batch, lot, çözüm süresi, operatör, vardiya vs.) kayıt düşülmesi gerekir. Neler yapıldığı, ne kadar zaman aldığı gibi notlar eklenmelidir. Daha sonra, bu veya benzer bir sorun ile karşılaşıldığında bu veriler önem taşıyacaktır. Sorunun çözülmesi için daha önce neler yapıldığının, neler yapılması gerektiğinin, zamanında müdahale etmenize yardımcı olacaktır.Ancak sorun kaynağının hemen sorun öncesinden değil, çok daha önceden kaynaklanmış olabileceği atlanmamalı, geriye dönük olarak daha uzun tarihsel sürecin değerlendirilmesi gerekli olabileceği unutulmamalıdır.Şurası unutulmamalıdır ki; zaman çizelgeleri, problem çözmede yardımcı bir çalışma metodolojisi sunar. Düşünsel organizeye yardımcı olur. Mutlak problem için çözümler sağlamaz. Zaman çizelgeleri birlikte ekip çalışmasını, gerçeği aramayı, değişik görüşlere açık olmayı ve karşıt görüşlerin ortaya çıkmasına veya farkındalığa destek olur.Kullanımı etkili, basit olan «balık kılçığı» diyagramları tercih edilebilir. Bu diyagramlarda genel uygulama alanı ürün tasarım ve kalite hatalarının önüne geçilmesidir. Sebepler araştırılırken değişik kesimlerin görüşlerinin alınması,herkesin görüşlerini rahatlıkla, çekinmeden söyleyebileceği ortam oluşturulması, sebepler yazılırken tarafsız davranılması, çözülebilir olmalarına özen gösterilmesi, özellikle diyagramın değişen şartlara göre güncel tutulması sorun gidermede yardımcı olacak veri birikimi sağlayacaktır.

Ekstrüzyon Sürecinde Yaşanan Sorunlar
Eriyik Kırılması:
Eriyik kırığı çeşitli görünümlerde olabilir. Kayma çubuk (veya bambu),palmiye ağacı, spiral veya rastgele karışık pürüzlülük şeklinde görülebilir. Genel olarak, eriyik kırığı kafa/meme gerilmelerini içerir ve genellikle polimerik malzemeile ilgilidir. Malzeme veya mekanik yollarla iyileştirilebilir.Kafa akış kanalını düzene sokmak, eriyik kırılmayı durdurmak için her zaman iyi bir fikirdir. Kesme gerilmesinin azaltılması kalıp boşluğunun arttırılması, ekstrüzyon hızınınazaltılması, kafa sıcaklığının arttırılması, eriyik sıcaklığının arttırılması ya da eriyikviskozitesinin azaltılması ile yapılabilir. Viskozite, bir proses yardımcısı veya yağlayıcıkullanılarak azaltılabilir. Eriyik kırılması için diğer yaygın çözüm, kafa sıcaklığının, erimekırılması için kesme gerilmesinin kritik kayma gerilmesinin altına düştüğü noktaya yükseltilmesi için bir ısıtıcı montajıdır. Kafa bölgesindeki eriyiğin kalma süresi o kadar kısadır ki, sıcaklıklar nispeten yüksek olabilir. Kafa bölgesi ısıtıcısı, aynı zamanda, kafa basıncını azaltabilir ve iyi ürün görünümü ve boyutsal toleransları korurken,% 20'ye kadar daha yüksek ekstrüzyon verimi sağlayabilir. Ayrıca, dıştan monte edilmiş transdüserler ile kafanın ultrasonik titreşimi, plastiklerin kesme ile incelmesine neden olur. Bu teknikte sınırlı bilgi mevcuttur, ancak deformasyon oranı yeterince yüksek olduğunda eriyik viskozitesini büyüklük sırasına göre azaltabilir.
Kafa cidarındaki plastik eriyik tabakası çok yüksek frekanslı deformasyona maruz bırakılır, bu da kafa cidarındaki eriyik viskozitesinde büyük bir düşüşe neden olur. Bu uygulama da, kafa basıncını düşürür, şişlik, eriyik kırığı ve kalıp-dudak sarkmasını azaltır.
Düşük Verim:
Her şeyden önce kullanılan malzemenin kuru olup olmadığı kontrol edilmelidir. Vida hızını arttırılması verimi arttırır.
Vida devri sonda olması halinde, kompresyon oranını azaltılması bunua ek olarak filtrelemenin da azaltılması eriyik malzemenin kafadan daha hızlı çıkmasına etken olur. Kafa/kalıp sıcaklığının arttırılması da verime etkidir.
Homojen Eriyik Çıkmaması:
Farklı ham maddeleri işlemek için farklı vida özellikleri gerekmektedir. Eğer ham maddeyi işlemek için kullanılan vida, işleme için uygun değil ise kalıptan çıkan ürün istenilen özellikleri sağlamayacaktır. Vidayı kontrol ederek işlediğiniz ham maddeyi işlemeye uygun vida seçimini yapın. Vida içindeki basıncın gereğinden düşük olması hammaddenin homojenleşmesini ve plastikasyonunu engelleyecektir. Vida içerisindeki basınç vida devrinin arttırılması ile gerçekleştirilir. Vida devrini kontrol ederek uygun miktarda arttırın. İyi tasarlanmamış bir kalıpta ürün homojen bir şekilde çıkmayabilir. İşleme sıcaklığının uygun olmaması
plastikasyonu ve homojenliği önleyeceğinden uygun işleme sıcaklığını sağlayın. Vida devrini kontrol edin.
Isıların Değiştirilememesi:
Isıtıcılar bozuk olabilir. Elektrik bağlantılarında kopma arıza olabilir. Hammaddenin işleme sıcaklığı ısıtıcılar ile sağlanır . Isıtıcılardan birinin veya tamamının çalışmamasının ürünün işleme sıcaklığına ulaşmasını engelleyeceği
unutulmamalıdır. Bu nedenle makine açıldıktan sonra sıcaklık değerlerinin yükselip yükselmediği kontrol edilerek sıcaklık değerleri yükselmeyen bozuk ısıtıcı var ise ısıtıcıları elektrik birimine haber vererek değiştirin. Isıtıcıların ısınmamasının bir diğer sebebi elektrik bağlantısı arızası olabilir. Yine bu gibi durumlarda elektrik ile ilgili birime haber vererek arızanın giderilmesini isteyin.
Üretim Hattının Sık Sık Kopması:
Çekici hızı fazla olabilir. Çekici hızının gereğinden fazla olması çekilirken fazla gerilen ürünün incelmesine ve kopmasına neden olabilmektedir. Bu gibi durumlarda kopmayı ve incelmeyi engelleyecek şekilde çekici hızını düşürün. Çekici normal bir hızda çekmesine rağmen üründe kopma meydana geliyorsa bu durumun makineden kaynaklanan diğer bir sebebi uygun vida devrinin sağlanmamış olmasıdır. Bu durumda vida devrini birim zamanda elde edilecek ham madde miktarına uygun olarak arttırın. Çekici ünitenin hızının çekim sırasında bağımsız olarak artıp azalması veya kesikli olarak durup tekrar çalışmaya başlaması ürünün kopmasına neden olabilir. Bu gibi durumlarda çekicinin pnömatik bağlantıları kontrol edilmelidir. Ürünün kopma nedenlerinden biri de soğutmanın yetersiz oluşudur. Bu gibi durumlarda soğutma sistemi ve kalibre soğutma kanalları kontrol edilmeli, tıkalı soğutma kanalı var ise temizlenerek açılmalıdır. Soğutmanın yetersiz olmasının bir diğer nedeni soğutma suyu
sıcaklığının istenilen değerlerin üstünde olmasıdır. Bu durum, soğutma için kullanılan suyun sistemde yeterince soğutulamamasından kaynaklanabilir. Su soğutmasının çalışıp çalışmadığı kontrol edilmelidir. Chillerin kontrolü atlanmamalıdır. Ürünün işleme sırasındaki kopma nedenlerinden biri de işleme sıcaklıklarının fazla olmasıdır. Bu durumda ürün yeterince soğumamış ve sertleşmemiş olacağından kopabilir. İşleme sıcaklıklarını kontrol ederek uygun işleme sıcaklıklarını sağlayın. Plastikasyonun yetersiz olması ve homojenliğin sağlanamaması ürünün kopmasına neden olan bir diğer etkendir.
Ko-enjeksiyonda Kötü Yapışma Veya Yapışmama Hali:
Erime sıcaklığının ve kafadaki kompresyonun arttırılmasına gerek vardır.
Çok Parlama:
Eriyik sıcaklığını düşürün. Şişirme basıncını düşürün. Mengene kuvvetini arttırın.
Mat/Donuk Yüzey:
Başlangıç ve son sıcaklıkları arttırılması ile eriyik sıcaklığının yükseltilmesi donuk, mat yüzey görünümünü iyileştirecektir. Gerektiği halde kompresyon oranının da arttırılması gerekebilir.
Kaynak Çizgileri:
Kalibre veya kalıp yüzeyinde yabancı malzeme veya deformasyon çizgisi şeklinde görüntü. Eriyik sıcaklığını arttırın. Kafa sıcaklığını arttırın. Baş ve kafa kısımlarını temizleyin. Süzgeci kontrol edin, gerekirse değiştirin. Kalıp ve kalibreyi kontrol edin. Kalıp ya da kalibre üzerinde olabilecek herhangi bir yabancı
maddeyi, kalıp ve kalibreye zarar vermeyecek yumuşak malzemeler ile temizleyin.
Bozuk Kalınlık Dağılımı:
Ürün kalınlığı kafa/kalıp ile belirlenmektedir. Kalıpta ısının homojen dağılmaması, ürün
çıkışının kalıbın bazı noktalarında hızlı bazı noktalarında yavaş olmasına sebep olabilir. Kafa ısılarının kontrolü ve kafa ayarı yapılmalıdır.
Yanma İzleri: İşleme sıcaklıklarının üzerinde ayarlanmış bir sıcaklık değeri, ürün üzerinde yanma izlerinin oluşmasına veya ürünün yanmasına neden olabilir. Bu durum uzun bakım işlerine de sebep olabilir. Bu gibi durumlarda işleme sıcaklık değerlerini kontrol ederek düşürün. Vida hızının gereğinden yavaş olması o bölgede uzun süre kalan ham maddenin aşırı ısınarak yanmasına neden olabilir. Vida hızını uygun değerlere göre arttırın.
Kesme Sorunları:
Uzun süre kullanılan kesiciler bir süre sonra körelerek kesme özelliklerini yitirebilir. Bu gibi durumlarda bıçakların bilenmesi gerekmektedir. Granülatördeki baskı merdanesinin kuvvetinin az olması kesimi engelleyebilir. Bu durumda kesici baskı kuvvetini arttırın.
Kesmede Kırılma:
Ürünü kesmek için kesicinin ürün üzerine yaptığı gereğinden fazla basınç ürünün bu baskıya dayanamayarak kesim bölgelerinden kırılmasına sebep olabilir. Bu gibi durumlarda kesici baskı kuvvetini düşürün. Ürünün kesim sırasında kırılmasının bir diğer nedeni kesicinin kesim sırasında yapmış olduğu hızlı kesim hareketidir. Ürünün kırılmasını engellemek için kesim hızı düşürülmelidir.
Aşırı Tozlanma:
Daha çok girdi hammaddelerinin partikül boyutunun çok küçük, toz olmasından ve yeterince plastikleşmenin yaşanmamasından kaynaklanabilir.
Enjeksiyon Sürecinde Yaşanan Sorunlar
Akış Çizgileri:
Akan eriyik üzerinde bir çizgi variyeti şeklinde görülür. Kalıp boşluğundaki eriyiğin doğru şekilde basınçlanmamasıyla oluşur. Doldurma hızı da bu duruma etkendir. Malzemenin kurutulması, kalıptan gaz çıkışının kontrol edilmesi, enjeksiyon hızının yavaş yavaş arttırılması, ya da kalıp sıcaklığının yükseltilmesi çözüm olabilir. Malzeme ve/veya kalıbın sıcaklığı da kontrol edilmelidir.
Meme ve kovan sıcaklıklarını arttırılmalıdır. Kimi durumlarda kalıp dizaynından da kaynaklanan bir sorundur. Yolluk giriş yerlerinin değiştirilmesi, yolluk girişlerinin genişletilmesi çözüm oluşturacaktır. Yetersiz havalandırma da bu hataya sebep olur. Havalandırma çıkıcıları temiz olmalı ve rutin olarak kontrol edilmelidir. Kaynama çizgilerinin eleminasyonu için doldurma hızı önemlidir. Mümküolduğu kadar hızlı dolum, mümkün olduğu kadar daha fazla miktarda eriyiği kalıp boşluğuna sokar. Malzemenin eriyikliği doldurma esnasında ne kadar fazlaysa bu hatayla karşılaşma riski o kadar azdır.
Bozulmalar:
Parça yoğunluğunun standartlardan düşük olması halidir. Aşırı kuru malzeme kullanımı, kovan ısıları ile kalıp ısıları da etken olabilir. Kalıplanmış parçanın fiziksel yoğunluğu daha önce yapılmış olandan oldukça az olması halinde görülür. Malzemenin aşırı kurutulması da bu hataya bir sebeptir. Malzemeyi kuruması için aşırı bir süre bırakmak (örneğin, en yüksek ısı değerinde birkaç gün bırakmak) bu hataya neden olur. Sıcak yolluklu kalıplarda ısıtıcıların aşırı ısınmasından , soğuk yolluklu kalıplarda ise eritme sırasında malzemeye çok farklı ısı verilmesinden kaynaklanır. Erime sıcaklığını ve makina ya da kalıbın ısıtıcıları kontrol edilmelidir.
Çapaklanmalar:
Kalıp kapanması ile basınç yeterli kalmıyordur ya da enjeksiyon basıncı, kalıp kapama basıncından büyüktür.
Enjeksiyon sürecinin kalıplama çevrim sürecinden fazla olmasıyla, kalıp içine dolan fazla eriyik bu taşmaya yol açar.
Enjeksiyon basıncının ve hızının düşürülmesi, kapama basıncının arttırılması uygulanacak ilk adımlardır.
Meme, kovan ve kalıp sıcaklıklarının da düşürülmesi gerekebilir. Ayrıca vida devrini de düşürerek sorunu giderebilirsiniz. Eğer düzgün bir yükleme kontrolü yapılmazsa, kalıp boşluğu aşırı malzemeyle doldurulabilir bu da bu hatanın oluşmasına sebep olabilir.
Vidanın her çevriminde aynı ilerleme ve gerilmeyi yaparak, aynı hacimdeki malzemeyi, kalıba enjekte etmelidir.
Gümüş İzleri:
Parça yüzeyinde gümüş gibi parlayan izler şeklindedir. Polimerik malzeme çok fazla ısınmış olabilir. Kondense olan gaz kalıp yüzeyinde sıkışıp kalmıştır. Ayrıca soğutma çevrim süresi uygun süre değildir. Soğutma çevriminin ekipmanlarını kontrol etmemiz
gerekir. Ekipmanları durgun akış ve sabit soğutma sıcaklığı için kontrol edilmelidir. Karışımın imalat alanına gelir gelmez kullanılması da bu hataya neden olabilir. İmalat alanında karışım kullanılmadan önce en az 8 saat bekletilmelidir. Böylece malzemenin sıcaklığı, ortam sıcaklığına yaklaşacaktır.
Kabarcıklar:
Parçanın yüzeyinde küçük hava/gaz kabarcıklarının oluşmasıdır.
İyi vakumlama ve ya hava/gaz çıkış sürecinin yeterli kalmamsı etkendir. Ayrıca kullanılan hammaddenin ıslak ve nemli oluşu, hava/gaz oluşumunu arttırır. Soğuk bir depoda veya siloda saklanmış olan malzeme sıcak veya ılık presleme ortamında nemin buharlaşmasına izin verilmeden işlem görürse, buharlaşan su kabarcıkları malzemenin içersinde kabarcıklara sebebiyet verebilirler.
Bu sebeple malzeme üretime girmeden önce, iyice kurutulmalı, veya kuru tutulmalı ve ortam sıcaklığına gelmesi beklenmelidir.
Kalıba Yapışmalar: Kalıp açıldığında, kalıp boşluğundaki emiş bitmemiştir ve parça çekilerek iticilerin olmadığı tarafta yapışık kalmıştır. Parçanın kalıba yapışıp kalması, aşırı tutma basıncı nedeniyle de olabilir. Ayrıca parça hala çok sıcaktır. Kalıp biraz daha soğutulma ihtiyacı duyuyordur. Ya da soğutma çevrim süreci arttırılabilir. En son olarak kalıp dizaynında uygunsuzluk vardır. Konik açıların genişletilmesi gerekebilir. Sadece belirli malzeme kullanımlarında oluşan bir sorunsa polimerik malzemenin cinsine bağlı anlık kalıp ayırıcı gibi aksiyonlar alınabilir. Ek olarak, soğutma suyunun sıcaklığının kontrol edilmesi, kalıp sıcaklığını azaltılması, enjeksiyon kısımlarının temizlenmesi çözüm sağlayacaktır.
Katmanlaşmalar:
Parça sanki ayrı ayrı katmanlardan basılmış gibi görülür ve bu katmanlar kolayca kopmaya, ayrışmaya yol açar. Enjeksiyon hızının düşük ya da kalıbın aşırı soğuk olmasıyla kalıp içinde giren malzeme çok hızla donmaya başlar. arkadan gelen eriyik, donan katmanlarla bağlarını kopartır. Genelde yavaş doldurmalarda parçada, eriyik soğuk katmanlar oluşur. Genel amaçlı renklendiriciler olarak çoğunlukla PE ve PP bazlıdır. Birçok zaman bu renklendiriciler renksiz karışıma uyum sağlayamazlar. Fazla kalıp spreyide bu hataya sebebiyet olabilir. Malzeme kalıba girdiği anda neredeyse donar. Daha fazla malzeme girdiğinde, diğeri nasıl donduysa buda birleşmeyen bir katman olarak donar. Enjeksiyon hızını artırmak bu problemi sona erdirecektir.
Kıvrılma, Çarpılma:
Bitmiş parça istenilen parça kalıp şeklinin dışında olması halidir. Parçanın iç gerilimi nedeni ile parçanın geometrisi bozulmuştur. Düzgün olmayan yolluk girişi dizaynı, yolluk girişi geometrisi, yüksek gerilme içeren dizaynlar ve yolluk girişi lokasyonu hatalı veya yetersiz olan kalıplarda bu sorun oluşabilir. Soğutma zamanı arttıkça parçadaki gerilmeler dudurulmaya başlar.
Eriyik ve kalıp sıcaklığını arttırılması, enjeksiyon hızının düşürülmesi sonuç vermiyorsa, parçanın çok sıkıştırılmış olma ihtimaline karşılık tutuma basıncının azaltılması, enjeksiyon zamanı ile kalıp dolum zamanının uyumluluğu kontrol edilmelidir.
Portakallaşma:
Parça yüzeyinde, portakal kabuğu gibi girinti, çıkıntı oluşması halidir. «mikro pitting» olarak da bilinir. Parçada oluşan ilk yüzey, yüksek miktarda vizkos malzeme tarafından itilmesi ve bunun hızla buruşmasını nedeniyle oluşan hatadır.. Eriyik sıcaklığını ve yolluk ısısı düşüktür. Enjeksiyon basıncında kayıplar vardır, eriyik kalıp için yeterince hızlı girmiyordur. Soğuk olan malzemede aynı doldurma hızını elde etmek için daha yüksek basınç uygulamamız gerekir. Malzemenin eriyik sıcaklığı kontrol edilmelidir. Kısıtlı yollukla birilikte eriyik sıcaklığı yavaşca arttırılmalıdır. Doldurma sırasındaki kafada oluşan basınç kayıplarını karşılamak için kalıp sıcaklığı da arttırılmalıdır. Hızın, kalıp için yeterli olup olmadığı kontrol edilmelidir.
Kötü Koku:
Yanan malzemeden kaynaklıdır. Özellikle kafa, meme bölgesi ısılarının düşürülmesi yerinde olacaktır.
Malzemenin kuru olduğundan emin olun. Tutma basıncının düşürülmesine sonuç verebilir. Erime sıcaklığının en düşük seviyeye ayarlı olması polimerik içindeki düşük proses ısılarına sahip katkıların yanmasına önlem olacaktır.
Kötü Renk Dağılımı:
Eriyik kovan içinde homojen karışmıyordur. Renk konsentrasyonu parça boyunca iyi dağılmamıştır. Parçanın üstünde farklı renk dağılımları gözlenebilir. Hatanın asıl sebebi; eriyik vidadayken renk konsentrasyonu tamamen homojen şekilde karışmamış olmasıdır. Bütün eritme ve karıştırma olayı vidanın dönmesiyle gerçekleşir. Karıştırma olayındaki artım ancak konvensiyonal
vidaların kullanılması ve kovan sıcaklıklarının azaltılması ve arka basıncın arttırılmasıyla olur. Bu malzemeye, eridikçe vidaya daha
fazla mekanik hareket verilmesi gerektiğini gösterir.
Kurt İzleri:
Parçanın üzerine kalıp koyunca ilk baskı sırasında oluşmuş izler şeklinde görülür.
Kalıpçılıkta, kalıbı mümkün olduğunca çabuk doldurmak iyidir ama bu çabukluk düzgün boyutlandırılmış bir yolluk girişi ile sağlanmalıdır. Yolluk girişindeki malzemenin hızı aşırı yüksek olduğundan, kalıp boşluğuna girildiğinde de akış çok hızlıdır. Eriyik hızla kalıp boşluğunu girdiğinde, boşlukta içinde istikrarsızca etrafa, sağa sola fışkırır. Bunu engellemek için fışkırma akışının karşısında bir direnç oluşturmalıdır. Bu da kalıp tasarımı ile ilgilidir.
Matlaşmalar:
Parça üzerinde parmak izi şeklinde ortaya çıkar. Kalıp yüzeyinin yekpare ya da temiz olmaması ile, ısıl işlem malzemeye farklı nüanslarla etki ediyordur. Hatanın asıl sebebi, genelde soğuk slug veya daha soğuk bir malzeme parçanın
içine enjekte edilmiş olmasıdır. Bazı durumlarda malzemenin içinde aşırı miktarda kaydırıcı ve yağlayıcı bulunur ve bunlar kalıp yüzeyine kadar çıkarak yayılırlar. Eğer kalıp yüzeyi uniform değilse o zaman eriyik sıcaklığını düşürülmeli ve problem çıkaran yüzeyin temizliği kontrol edilmelidir. Nozül ve yolluk memesi burcu geçişi engelleyecek faktörleri ortadan kaldırılmalıdır. Nozül
ve yolluk memesi burcu da birbirini tam olarak karşılamalıdır. Eğer bunun dışında bir durum varsa akışta hata olacaktır.
Meme/Kafa Tıkanması:
Kalıp içine malzeme enjekte dilememsi, eriyik malzemenin kalıp girişinde donması şeklinde görülür. Kullanılan polimerik malzeme nemli olabilir. Hava kanallarına (ventil) vakumlama ünitesi eklenmesi faydalıdır. Aynı zamanda tutma basıncının arttırılması da gerekebilir.
Yolluk Girişinde Bozulmalar:
Yolluğun yakınındaki bölgede hata görülmesidir. Yolluk girişinin hemen etrafında mikro jetting oluşmuştur. Kalıp yüzeylerinin polisaj edilmesi gerekebilir. Yolluk kanalları dar veya fazla derin olabilir.
Bu hata ile genelde fiber glas ve mikanın kullanıldığı doldurmalarda, çok abrasif oldukları için karşılaşılmaktadır.
Kalıpta yapılması gereken değişiklik, yollukların geniş fakat derin olmayacak şekilde yapılmasıdır.
Salyalaşma:
Kalıp açıldığında, tel gibi görünen ve uzayan ipliksi parçalardır. Bu nedenle bu soruna «telleşme» de denir.
Bu durum ayrıca kalın fakat yavaş malzeme akımının yolluk burcundan yavaşça akmasıyla da olur. Hatanın asıl sebebi, kovandaki plastiğin basıncı verimli olarak bertaraf edilmemiş olmasıdır. Enjeksiyon basıncının aşırı olması, yolluklardaki bozulma etken olabilir. Birçok ekipman üreticisi bunu engellemek için kalıplama makinasına reverse toper nozülünü yerleştirmişlerdir. Bunlar özellikle salyalaşmayı engellemek için dizayn edilmiştir. Sıcak yolluk kanalları açılmış kalıplarda, eğer kanallar düzgün çalışmıyorsa buda salyalanma ve tel tel olmaya bir sebep olabilir. Tel tel olma belli bir yere kadar no drool nozulleriyle kontrol edilebilir.
Eriyik dekomprasyonu çoğunlukla vidanın zamana bağlı olarak geri çekilmesiyle ayarlanabilir. Dekomprasyon zamanını artırmak tel tel olmayı azaltacaktır.
Siyah Noktacıklar:
En bariz neden kirli hammadde kullanımındandır. Kullanılacak malzeme içinde özellikle renk masterbatchi varsa, Masterbatchin taşıyıcısının uygun olmaması da ekstrüzyon sürecinde yanmaya neden olabilir.
Sürekli Hatalı Baskı:
Genelde ya eksik yada boyutsal hatalı parça basılmasıyla kendini daha çok yarı otomatik makinalarda gösterir. Hatanın temelinde, sabit bir doldurma hızı olmamasından ve eriyik vizkositesi değişimlerinden kaynaklıdır. Vidanın arkasının dolmasından dolayı sızıntı yapan check valflerin iş göremez olması enjeksiyon basıncının da değişken olmasına neden olur. Valfler kontrol edilmeli ve gerekirse değiştirilmelidir. Ayrıca vida dönmesine rağmen, bir sonraki baskı için malzemeyi almama, yarım alma durumları da olabilir. Besleme, boğaz bölgesinde tıkanmalar olabilir. Vakum yükleyici kullanılıyorsa, bu yükleyicinin sensörlerinde, kalibresinde kayma olabilir. Yani temel olarak sistemin besleyici sisteminde bir aksaklık vardır. Bütün ekipman kontrol edilmelidir.
Yanıklar:
Parça üzerinde görülen renkli lekeler şeklindedir. Lekeler, prosesin
içindeki bir yerde yanmadan dolayı oluşur. Çalışma ısıları veya kafada yapışmış kalmış yanık bir parça buna sebiyet verebilir. Eski vidalı, kovanlı makinalar parçada bu tip hataya sebep olabilirler. Çünkü makinanın içinde dikkate alınacak kadar yanmış parça atığı varsa, bunlar parçada bu tip hatanın olmasına sebep olabilir. Bunu engellemenin tek çözümü vida ve kovandaki hataya sebep olan
komponenti bulup temizlemektir. Lekeler, prosesin içindeki bir yerde yanmadan dolayı oluşur. Isıtıcı bantların aşırı ısınması bu hataya sebep olur. Sürekli kontrol yapan ısı kontrol cihazlarını kontrol etmemiz gerekir. Malzeme değişimi de bu hataya sebep olabilir. Yolluk girişindeki aşırı hız artımlarından dolayı malzemenin aşırı ısınması ve yanması gerçekleşebilir.
Hava veya gaz da kalıp içinde sıkışıp kalmasıyla, malzemeyi ısıtır ve yakar. Genelde kalıba da zarar verir. Sıcak hava veya gaz malzemeyi aşırı ısıtır ve bu durum da yanıklara neden olur. Çıkıcı yok veya yetersiz konstrükte edilmiş veya düzgün temizlenmemiş bir çıkıcı söz konusu demektir. Bu hata ayrıca aşırı kapanma kuvvetinden dolayıda olabilir.
Aşırı kuvvetle kapanan kalıbın çıkıcıları işlevsiz kalabilir. Gaz sıkışarak içerde kalır ve kompresyondan dolayı aşırı ısınırak yanmaya sebep olur. Yanıkların engellenmesi iyi havalandırma yani, çıkıcıların temizliği ve iş görmesiyle olur.
Vakum Deformasyonu:
Parçanın kalıptan alınması esnasında daha çok robotik ünitelerdeki vakumlamanın parçanın şekline verdiği değişimdir. Boşaltma esnasında, ilk anda oluşan vakumla parçanın şekil değiştirmesiyle kendini gösterir.
Soğutma çevrim süresinin uygun olmaması en büyük etkendir. Ayrıca itici tarafındaki hava basıncının parça için çok düşük olması da vakum şiddetini arttıracaktır. Bu hata soğutma çevriminin düzgün çalışmayışından, tıkalı olmasından, çalıştırılmamasından veya çıkışı olmayan bir şekilde (yani kör biçimde) çalıştırılmasından kaynaklanır.
Bunu engellemek için soğutma çevrimini çalıştırmadan önce herşeyi düzgün olup olmadığına bakmak gerekir. Havalandırma arttırılırsa bu hatanın önüne geçilebilir.
Yolluk Yapışmaları:
Çevrimde, kalıp açılması sırasında yolluk, yolluk sisteminden ayrılır, kopar ve kalıpa yapışıp kalır. Bunda en büyük etken yolluk bağlantı noktalarının derin olmamasıdır. Parçanın çok sıcak olması da yapışmalara etkendir. Meme ve kovan sıcaklıklarının yada kalıp sıcaklıklarının düşürülmesi, ve ya soğuma zamanının uzatılması çözüm sağlayacaktır.
Kalıp dizaynı üzerinde konik açıların arttırılması gerekebilir. Kalıp ayırıcı kullanımı da bu durumu önleyecektir. Derin bir yolluk memesi konstrüksiyonu yapmalıdır veya daha efektif bir yolluk memesi çekici koymalı, veya en son olarakta ısıtmalı yolluk memesi
kullanmalıdır. Eğer nozül sıcaklığı çok düşükse kalıp açılması sırasında yine kopma olabilir. Bunu engellemek için nozül sıcaklığını artırılmalı, böylece cold slug ve kopma engellenmiş olacaktır.
Üfleme Kalıplama Sürecinde Yaşanan Sorunlar
Şişirme Problemi:
Reçine bileşimini kontrol edin. Ekstruder besleme bölümünde köprüleme boşluklarını önlemek için arka namlu bölgesi sıcaklığını biraz artırın. Hasarlı kalıplarla birlikte oluşacak delikleri önlemek için kalıp kenarlarını ve kıstırmalarını onarın. Doldurma basıncı çok düşük olabilir. Hava sıkışmasını önlemek için, doldurulana kadar dolgu basıncını arttırın. Kalıp kapanma hızı çok hızlı olabilir. Zayıf kaynak oluşumunu önlemek için kalıp kapatma hızını azaltın, Kıstırma çok keskin veya çok sıcak olabilir. Parşömen alanını azaltmayacak şekilde arazi genişliğini artırın. Sıkışma bölgesinde soğumayı artırın. Silindir/kafa kısmının sıcaklığını düşürün. Devir sayısını azaltın
Kabarcıklar / Baloncuklar:
Reçinede nem vardır. Buğulanma meydana gelirse besleme boğazında soğumayı azaltın.
Reçine nemini kontrol edin ve reçine taşıma sisteminin su geçirmez olduğundan emin olun. Arka namlu bölgesi sıcaklığını biraz artırın. Hava sıkışmasını önlemek için, doldurulana kadar dolgu basıncını arttırın.
Kirlenme:
Besleme haznesini sürekli temiz tutun. Toz hava girişlerine filtre takın ve düzenli olarak temizleyin.Reçinedeki kirler yanıklardan kaynaklanmış olabilir, Ekstruzyon süresini kısaltın veya ısıları ayarlayın, eriyik akış yollarının temizliğinden emin olun.
Düzensiz Parison Hacmi:
Düzensiz hacim, düzensiz ağırlık akışından ileri gelir. Bu durum düzensiz parison boyuna da etki eder. Her çevrim sürecinde ağırlık sürekli eşit değildir. Belirli aralıklarla parison gramajlarını kontrol ederek sorunun kaynağı netleştirilmelidir. Ağırlıkların kalıp hacmi ile uyumluluğunu kontrol edin. Çevrim süresi düzensizliği ve ısı oynamaları malzeme miktarını etkileyebilir. Tam teması sağlamak için basınç ayarları uygun olmalıdır. Zayıf parison, kalıp teması gevşekliği, temiz kalıp delikleri olmamasına bağlıdır. Ekstruder profil sıcaklığı daha yüksek eriyik sıcaklığına bu da yüksek parison oluşumuna sebeptir. Kalıp sıcaklığı da bu soruna kaynak teşkil eder. Soğutma düzeneği ve ısıları gözden geçirilmeli. Tavlama koşullarından kaynaklı sorun olabilir. Daha yüksek sıcaklık ve daha yavaş devirlerde çalışın. Silindir sıcaklığını düşürün. Kafa/kalıp sıcaklığını arttırın. Kalıbı/kafayı temizleyin. Aşınmış baskı yatağı ve merkezleme burçlarını kontrol edin.
Boyun Eğriliği:
Şişen parison yanlış kesme ile sonuçlanmıştır. Püskürtme ucu hizalaması bozuk veya hasarlı olabilir. Püskürtme pimini merkezi olduğundan emin olun. Kalıplar yanlış hizalanmış olabilir. Kalıp pimlerini ve burçlarını kontrol edin.
Sarkma:
Yanlış kalıp ayarı kaynaklıdır. Merkez dışı basınç halkası ortalı değildir. Kafa ve manifold ısıtıcılarını kontrol edin.
Hava kanallarını ve kalıp boşluğunun temizliği de önemlidir.
Boru Boylarındaki Eşitsizlik:
Nihai noktada fiziksel sorundur. Herşeyden önce testere bıçağının esneyip, esnemediğini kontrol edin. Daha kalın, daha büyük bıçakları tercih edin.Testere kolu çok hızlı bazen daha yavaş bir şekilde boruya giriyor olabilir. Devrin stabil işlediğinden emin olun. Testere kolu yıpranmış, çapaklı yüzeye dönüşmüş olabilir. Kayma halkalarında aşınma ya da gevşeme bulunabilir.
Çekme veya kesme arabasının sürekli eşit hızla hareket etmemesi de bu duruma etkendir. Çekme hızının sürekli aynı hızla çalıştığından emin olun. Verimi arttırmak adına. çalışma değerleri dışında testere boru kesme kapasitesi üzerinde çalışma temposu olabilir.
Duvar Kalınlığında Düzensizlik:
Kalıptan çıkarılan düzensiz eriyik, dengesiz kalkış hızı, kalıp ve çekme birimlerinin yanlış hizalanması, hizalarının kaymış olması yada terazilerinin bozulması, Kalıp ve pim eşit olarak birbirini merkezlememesi, hatta kalıp ta oluşabilecek boşluk boru duvarlarında düzensizliğe etkendir. Eriyik pompası kullanılıyor ise, pompa devrinin stabil olduğu doğrulanmalı, sonrasında içindeki dişlilerde bir aşınma, yıpranma olup olmadığı tespit edilmelidir.
Çok katmanlı boru üretimi söz konusu ise, yanlış polimer eşleşmesi ile karşı karşıya kalınmış olabilir. Co-Ekstrude sürecinde tercih edilen polimerlerin vizkosite değerleri arasında büyük farklılık olmamalıdır. Aksi takdirde; katmanların kalınlığında farklılıklar oluşacaktır. Bu durumda bir katmanın kalınlığı azalırken, diğer katmanın bu azalan yeri dolduracağı net değildir.
Bir katmanın kalınlığı azalırken diğer katman stabil kalabilir. Bu durumda tüm kesit boyutunda duvar kalınlığının düzensiz olmasına kök neden olacaktır. İki polimerden gelen eriyiğin sıcaklık profilini değiştirmek çözüm oluşturabilir. Ancak en doğru yaklaşım, MFI değerlerinin birbiri ile uyumlu olabilecek hammaddelerin tercihi olmalıdır. Co-Ekstruzyonda zaman içerisinde düzgün dağılmayan basınç da, akan eriyik miktarına doğrudan etki edeceğinden, kalınlık dağılımını olumsuz etkileyecektir. Her ne kadar aynı kalıptan geçecek, kalınlık aynı olacak şeklinde düşünülmüş olsa da, katmanlar kesitinde eriyik dağılımı stabil olmayacaktır.Stabil ilerlemeyen katmanlarda da, eriyik dağılım miktarına bağlı olarak, yer yer mikro ölçekte de olsa çökme, sünme, büzülme gibi etkiler oluşturacak, totalde duvar kalınlığının düzensiz ilerlemesine yol açacaktır. Bu bağlamda Co-Ekstruzyon ünitesi tüm ekstrüderlerin sabit basınçta çalıştığından emin olunmalıdır.
Kullanım sürecinde zamanla oluşabilecek problemleri azaltmak için:
Boru sistemi mümkün olduğunca kısa ve doğrudan olmalıdır. Keskin ve çoklu kıvrımlardan kaçınılmalıdır. Bükümler nazik olmalı ve geniş çaplı olmalıdır, ideal olarak hortum numarası 10 x olmalıdır.
«Y» bağlantılarını kullanılmalı ve «T» eklemlerinden olabildiğince kaçınılmalıdır.
Emme tarafı borusu çalışması asla düşük boyutta olmamalıdır (minimum delik hortumun iç çapına eşit olmalıdır).
Boru hattındaki titreşimli akış etkilerini azaltmak için genleşme derzlerinin boru sistemine takılması fayda sağlayacaktır.
Esnek hortum bağlantıları kullanıldığında, hortumun uygun bir elastometre ile yapıldığından ve sistemin maksimum emme ve deşarj basıncına yeterince uygun olduğundan emin olunmalıdır. Parça değişimi kolaylığı için başlangıç, final noktalarında çıkarılabilir mümkünse esnek parçalar kullanılmalıdır.
Çöküntüler:
Bir nevi eksik baskı olarak görülebilir ancak buna etken olan daha çok tutma basıncının (yanlış tabiri ile ütüleme basıncı) yetersiz kalmasıdır. Parçanın dış duvarları katıdır. Ama parçanın iç yapısındaki bazı molekülleri birbirinden ayırarak boşluklar oluşmuştur. Gereğinden kalın olan kesitler, dar geçiş veya ani genişlemeye sebebiyet veren geçişler de çöküntülere sebep olacaktır.
Geri basıncın arttırılması, enjeksiyon basıncını arttırılması, tutma basıncı ve süresinin arttırılması çözüm olacaktır.
Unutulmamalıdır ki, plastik soğudukça kalıp boşluğunun içinde çekilme yapacaktır. Kalıp boşluğunu iyi ve tam doldurması ve bu çekilmeleri karşılamak için tutma basıncı kontrol edilmelidir. Yetersiz basınç boşluklara neden olur. Plastik soğudukça çekeceği için kalıbın şeklini tam olarak alabilmesi için preşürize edilmesi gerekir.
Bu asınçta çekmeyi kompanse eder. Onun için parçya yeterince tutma basıncı uygulanmalıdır.
Eksik Baskılar:
Eriyik malzemenin, kalıp boşluğunu tam doldurmaması halidir. Enjeksiyon basıncı, enjeksiyon çevrim süreci yetersizdir. Kalıp içerisindeki gaz alma ünitesi çıkışlarının kontrol edilmesi gerekebilir.
Nem de eksik baskıya, boşluğa neden olur. Malzemeyi kurutun. Nem almalı burgu kullanıyorsanız, nem atmayı engelleyen unsurları kontrol edin Havalandırma kanallarına yardımcı vakum ilavesi gerekebilir. Tutma basıncını arttırın.
Düzensiz kalıp dolumu hallerinde yolluk giriş yerlerinin değiştirilmesi sonuç verebilir. Aynı zamanda kalıp sıcaklığının değişmemesinin sağlanması gerekir.
Enjekte edilen malzeme miktarı ile de bu sorun ilintilidir. Enjekte edilen malzeme miktarını ve eriyik yastıklamasını arttırılması çözümdür.
Eksik baskılardaki nedenlerden biri de kalıp dizaynına bağlıdır. Yolluk girişlerinde tıkanma olabilir. Havalandırma kanallarının tıkanıklığını, yerlerinin doğruluğunu kontrol edin. Gerekmesi halinde havalandırma kanallarına ek vakum ilave edilebilir.
Düzgün bir besleme kontrolu yapılmazsa, kalıp boşluğunun aşırı doldurulmasından parça eksik çıkabilir. Vidanın her çevrim için aynı dönmeyi, yani, aynı hacimdeki malzemeyi basması gerekmektedir. Parçanın dizaynında kısa baskıya sebep olan bir faktördür. Keskin geçişlerden ve dar kesitlerden kaçınılmalıdır. Birçok zaman kalıp presin boyutuna göre ayarlanamaz. Kapama tonajı dikkatle ayarlanmalıdır.
İtici İzleri:
Parçanın kovandan itilmesini sağlayan çubukların, parça üzerinde iz bırakması şeklinde görülür. Parçanın sıcaklığı veya itici çubukların kuvveti ayarlanmalıdır. Çubukların parçaya çok hızlı çarpması ya da çaplarının çok küçük olması bu duruma etkendir.
Bu hata parçanın sıcaklığını ve itici çubukların kuvvetlerinin balanse edilmesiyle ortadan kaldırılabilir.
Eğer itici çubukların bağlı olduğu plaka (itici plaka) parçaya çok hızlı vurup düşürüyorsa yine bu hata ortaya çıkar. Bununda çözümü tabiki itici plakanın hızını düşürmekle olur. Eğer kalıp parçanın kalıba yapışmaması için çeşitli modifikasyonlardan geçmişse, bu
seferde parça itici tarafında kalıyorsa o zaman itici çubuklar parçada iz bırakabilir. Bunu engellemek için daha büyük çaplı itici çubuklar kullanılırsa birim alana düşen kuvet azalacağından iz bırakma olasılığı da düşmüş olur.
Boru, Profil Üretim Sürecinde Yaşanan Sorunlar
Sert Yüzey:
içeride veya dışarıda olabilir. Hammadde kuru değildir. Bir iki saat 70-90°C de kuruduğundan emin olun. Kalibratöre yeterli su akışı yoktur. Eriyik sıcaklığının düşük olması da bu soruna neden olur. Ekstruder veya kalıp sıcaklıkları yükseltilmeli.
Şekil Bozukluğu:
Çok yüksek erime sıcaklığı vardır. Ekstruder ve kalıp sıcaklıklarını tekrar gözden geçirin. Ayrıca aşırı ekstruder vida hızı varsa bu sorun oluşabilir. Verimi biraz düşürün. Verime bağlı olarak kalıplar küçük olabilir. Pim çok sıcak olursa yüzeyde termal bozunma görüntüleri oluşacaktır. Pim soğutma ünitesinin doğru çalıştığından emin olun. Şekil bozuklu fiziksel sorunlardan da kaynaklı olabilir.
Eşmerkezlilik için kalıp ölçülerini kontrol edin. Son boru çapından % 3, %5 daha büyük olduğundan emin olun.
Çekme ünitesine ulaştığında boru çok sıcaktır. Önceden yeterli soğutma akışı sağlayın. Çekme ünitesine yüksek verimle akış olabilir. Ekstruzyon devri düşürülmeli ayrıca vakumlu tanklarda uygun vakum ayarı yapılmalıdır.
Yüzeyde Oluşan Çizgiler:
Kafadan kaynaklanan çizgiler olabilir. Kafa/kalıp üzerinde sivri uç, çıkış noktalarını kontrol edin. Gerekirse törpüleme tarzında hafif temizlik uygulayın. Kafada yanmış, yapışmış eriyik de çizgilere neden olabilir. Kalıp çıkış yönünde sıcaklıkları kontrol edin.
Damla İzleri:
Çok hızlı çekme kuvveti uygulanıyordur. Çekme hızını kontrol edin ve ayarlayın. Kalıp girişinde malzeme sıcaklığının çok yüksek olması da etkendir. Su akışını kontrol edin.
Ekstruder Hataları:
Çok yüksek ekstruder verimi alınmaya çalışılıyordur.Ekstruder özellikleri ve garantili ekstruder çıkışını kontrol edin ve
şartname dahilinde ekstruderi çalıştırın. Uygun olmayan ekstrüder sıcaklık ayarları kaynaklı olabilir. Sıcaklık ayarını kullandığınız hammadde üreticisinin önerdiği proses değerlerine göre ayarlayın.
Boru İçinde Jelleşme:
Eriyik içinde yabancı parçacıklar içeriyor olabilir. Kullandığınız hammadde, katkı vs. tedarikçiden bilgi almanız gerekebilir. Ekstrüzyon sırasında kalıptan çıkan bozulmuş reçine de jelleşme yapabilir. Ekstrude süresini, sıcaklıkları kontrol etmeniz gerekecektir.
Yüzeyde Görülen Lekeler:
Kalıp ayarı uygun yapılmamıştır. Kalıp profil yüzeyinde termal dağılım eşit olmayabilir. Kalıp ısısında homojenliğin sağlandığından emin olun. Lekeler soğutma banyolarından sonra kendilerini gösterme eğilimindedir, çekme, itme, indirme işlevini ayarlayın. Kalıptan çıkan düzensiz eriyik ve sıkışmış gazlar leke kaynaklarıdır. Vakumların iyi dengelenmiş, konumlandırılmış olduğundan emin olun.
Sarkmalar:
Eriyik sıcaklığın çok yüksek olması sarkma probleminin ana nedenidir. Eriyik sıcaklığını düşürmek için ekstruder sıcaklığını ve ekstrude süresini gözden geçirin. Kalıp boşluğu sarkmaya uygun şekilde ayarlanmamış olabilir.Eriyiğin sarkmaya olan doğal direnci boru duvar kalınlığı için yeterli değildir. Düşük sarkma gösterecek hammadde kullanın. Hatlarda yeterli soğutma sağlanamıyordur. Soğutma kapasitesi arttırılabilir ya da soğutma banyolarında geçen süre uzatılmalı.
Blown Film Üretim Sürecinde Yaşanan Sorunlar
Balon Zıplaması:
Olası nedenlerin başında çalışma hızı düşüklüğü gelir. İşleme sıcaklığının aşırı yüksek olması da bu duruma etkendir. Çalışma ortamında hava sirkülasyonu fazla olabilir. Bunların yanında; hava halkası açıklığının çevresi boyunca
eşit olmasını sağlanmalı, soğutma havasının sürekli eşit hızda üflenmesi gerekmektedir. Ayrıca, katlama çerçevelerinin konumu da ayar gerektirebilir. Ekstruder veya kulede çalışma sürecinde oluşan vibrasyon balona etki ediyor olabilir. Titreşimlerin izole edilmesi gerekecektir. Nihai olarak, optimum şişirme oranının uygunluğu kontrol edilmelidir.
Kırışık Film:
Muhtemel sebeplerin başında balon şeklinin bozuk olması gelir. Bunun için, film kalınlığının homojen, kafa sıcaklığının eriyik polimer sıcaklığına uygun ve soğutma halkasının temiz ve ayarlı olması gerekir.
Film kalınlığı eşit olacak şekilde kafa ayarı yapılmalıdır. Kafa seviye ayarı kontrol edilmeli. Sıkıştırma merdaneleri
seviye ayarı yapılmalıdır. Balon çapını sınırlama merdaneleri yada boncukları üzerinde pislik birikmiş olabilir.
Kararsız balon durumu halinde, dıştan mekanik destekleme gerekebilir. Nihai olarak sarma merdanelerinin gerginliği kontrol edilmelidir.
Şişirme Problemleri:
Malzemenin kuruluğundan emin olun. Geri dönüştürülmüş malzeme kullanılıyorsa, temizliğinden emin olun. Şişirme probleminin muhteviyatına göre arka basıncı arttırın veya azaltın. Kalıp duvarı kalınlığını arttırın (kafa ayarını tekrar yapın).
Erimeyen Tanecikler:
Hammadde kirli veya prosese uygun olmayan hammadde olabilir. İşleme sıcaklığı çok yüksek olması halinde, yanmış parçacklar film yüzeyine yapışıyor da olabilir. Isıların kontrol edilmesi gerekir.
Ya da ilk uygulamalardan birisi, filtre, süzgeç dolmuş, aşırı kirlidir. Süzgeç telinde yırtılma, delik olup olmadığı kontrol edilmelidir. Süzgeç teli gözenekleri büyüktür, daha ince tel ile değiştir. Kafada dudaklar arasında yanmış parçacıklar birikmiş olabilir, kafa temizliği yapılması gerekecektir. Ekstruder uzun süre çalışmadan beklemiş ise, içeride eriyik yanmış ve vidaya yapışmış olabilir. Gerekirse tüm vida çıkartılıp temizlenmelidir.. Formül, reçete içinde kullanılan masterbatch varsa karışımın iyi yapıldığı, çalışma değerlerinin uyumluluğu tekrar değerlendirilmesi gerekebilir. İlk proses ise yanlış üretim hattı tercihi olabilir, prosesin daha iyi karıştırma özelliğine sahip vidanın olduğu üretim hattına alınması sorunun çözümüne yardımcı olacaktır.
Sert Film Yüzeyi:
Silindir sıcaklıklarının kafa/kalıp sıcaklığının arttırılması yüzey sertliğini gidericidir. Ayrıca ekstrüzyon hızını ve besleme tarafındaki sıcaklıkların azaltılması gerekebilir. Kalıp sıcaklığının arttırılması ve yüksek kompresyon vidaları kullanılması da sert yüzey problemine çözüm sağlar.
Zayıf Yırtılma Mukavemeti:
Şişirme oranını arttırılması gerekebilir. Yırtılma nedenlerinden biri film yüzeyinde çizgiler olmasıdır. Bunun için ekstruderin kafa dudaklarını temizlenmesi ve erimeyen tanecik sorunundaki uygulamalara gözx atılması gerekebilir. Donma çizgisinin çok alçak olması da yırtılma mukavemetine etkidir.
Balon Patlaması:
Kirli hammadeden kaynaklı olabilir. Bu durum erimeyen tanecik sorununu tetikler. Buna ilişikin çözümler, balon patlamısına da çözüm olacaktır. Vidanın çıkartılması, kafanın sökülmesi ve tüm parçaların temizlenmesi gerekebilir.
Film Yüzyinde Çigi Oluşumu:
Öncelikle çizgilerin mekanik etkili fiziksel mi yoksa eriyik kaynaklı kimyasal mı olduğu görülmeli ve çözüm bu istikamette aranmalıdır. Fiziksel çizgilerin temel nedeni kafa ve ya merdaneler üzerinde birikmiş pisliklerdir. Film ile temas eden mekanik parçaların keskin, sert uçları sürtünme etkisiyle çizgi oluşturuyor olabilir. Zımparalama, sıkıştırma, çatlak giderme gibi aksiyonlar alınması gerekebilir. Kafa basıncın yüksek olabilir. Vida devrinin düşürülmesi, çalışma sıcaklıklarının yükseltilmesi kimyasal oluşumlar için çözümdür.
Zayıf Isıl Yapışma:
Isıl yapışma koşullarının uygun olmaması etken olabilir.l Bunun için hammaddenin erime noktasını kontrol edilmeli ve yapıştırma süresinin azalması oranında yapıştırma sıcaklığını arttırmak gerekebilir. Sarılı bobinlerin saklama koşullarında da uygunsuzluk olabilir. Film yüzeyi tozlanmış, nemlenmiş olabilir. En önemli nokta olarak yüzey korona gerilimi düşüktür. Korona olup olmadığı, koronanın şiddeti ölçülmesi gerekir.
Optik Özelliklerin Bozukluğu:
En temel neden hatalı hammadde tercihinde yatar. Proses ısılarının düşük olması, balon soğutmasının yetersizliği de optik bozulmalara yol açar. Isıların arttırılması, donma çizgisinin düşürülmesi, daha soğuk hava ile balon soğutması yapılması çözüm sağlayacaktır.
Flekso Baskı Sürecinde Yaşanan Sorunlar
Baskıda Arkaya Verme:
Mürekkep filmi tam kurumadan baskı yapılması, baskılı malzeme üzerinde solvent kalıntıları olması, bobin sarımının çok sıkı uygulanması filmin arka yüzüne baskı izleri çıkmasına neden olur. Her iki yüzeyi koronalı filmlerde baskılı yüzey diğer yüzeye temas ediyordur. Hızlandırıcı solvent kullanımı gerekebilir. Üniteler arasındaki kurutma sıcaklıklarını ve hava üflemelerini kontrol edilmelidir. Bobin sarım basıncını azaltılmalı, transfer edilen mürekkep film kalınlığının düşürülmesi,
bloklaşma önleyici vernik kullanımı soruna çözüm olacaktır.
Baskıda Çizik Oluşması:
Sıyırıcı rakle bıçak ucunda olmaması gereken yabancı tanecikler buna etkendir. Sıyırıcı bıçağın temizlenmesi yada değişimi gerekir. Ayrıca bıçak ayarları kontrol edilmelidir. Anilox merdane sertliğinin uygunluğu gözden geçirilmeli.
Aşırı Anilox Yıpranması:
Sıyrıcı rakle bıçak üzerinde aşırı basınç olması anilox merdaneleri yıpratır. Aşırı basınca gerek duyulma nedenlerini bularak önlem alınız. Mürekkebin içinden gelen dolgu malzemeleri bıçak ucunun yıpranmasına neden olmaktadır. Yıpranan bıçak ucunun görevini yapamaması durumunda da bıçak basınç ayarlarının artırılması sonucu anilox 'un üzerinde fazla basınç
oluşacağı için yıpranmaya neden olur. Tüm renklerdeki bıçakların durumu ve açılarının kontrol edilmesi gerekir.
Tram Bozukluğu:
Tram noktaları baskı yönünde uzayarak yuvarlak halden oval
balık gözü haline gelmesi durumudur. Baskı klişesi yüksekliği veya kullanılan çift taraflı yapışkan bant kalınlığı ile ilgilidir. Bu nedenle doğru forse ayarı yapılamaz. Klişe kazanı ile baskı kazanı arasında silindir çap farkı oluşur. Klişe toplam yüksekliği (klişe + yapışkan bant) kontrol edilmeli ve istenilen kalınlıkta olması sağlanmalıdır. Baskı forse ayarları tekrar kontrol edilmelidir. Baskı testleri yapılırken optimum forse ayarını bulmak için forse ayar stripleri, çiftleme ve kayma rehberleri kullanılmalıdır. Flexo baskı ünitelerinde silindirler genellikle dişlilerle birbirine bağlantılı durumdadır. Dişli yarıçapları silindir dönüş hızını ve buna bağlı olarak karşı baskı silindiri ile birlikte kalıp silindiri üzerindeki klişe yüzey hızını da belirler, baskı klişesinin toplam kalınlığını, baskı silindiri ile plaka silindirinin dişli yarıçapları belirler. Klişe yüksekliği olması gerekenden daha fazla olursa klişenin çevresel rölyef yüzeyi (basan kısımlar ) baskı silindir yarıçapından daha büyük hale gelir. Bu durumda her iki silindir arasındaki uyum bozulacağı için istenilen hassasiyette bir baskı forse ayarı yapılmaz. Bu durumda baskıyı yapan yuvarlak noktanın tram yapısı bozularak oval şekle dönüşür. Bu durum baskıda tram kirletmelerine yol açarak görüntü kalitesini bozar.
Baskıda Klişelerin Bozulması:
Klişelerin baskı başlangıcından kısa bir süre sonra yumuşaması ve yapışkanlaşması halinde ise sorun, klişenin arka poz, ana poz, ve son poz işlemlerinden sonra yeterli polimerizasyona girmemesinden kaynaklanır. Klişe poza doymamış, lambaların gücü azalmış, vakum folyesi çok kirli veya sararmış folyo verilen pozu engellemiştir. Pozlandırma süreleri tekrar kontrol edilmeli. Pozlandırma lambaları kontrol edilerek eskiyen lambalar değiştirilmelidir. Tüm lambaların aynı anda değiştirilmesi gerekir. Vakum folyesi yenilenmelidir. Sorun klişe baskı yüzeyinde çatlaklar oluşması şeklinde ise ozon oranı çok yüksek olabilir. Kullanılan solvent ve temizleme maddeleri çok agresif yapılı olabilirler. Miadını doldurmuş klişeyi kullanıyor olabilirsiniz. Artık son baskısını yapıyordur. Klişe baskıdan sonra sleeve üzerinde iyi temizlenmemiş halde ve aydınlık ortamda saklanırsa miadı çabuk dolar. Bu nedenle temizlenen klişe üzerinde solvent atığı kalmamalıdır. Klişeler baskıdan sonra ışıktan koruyacak şekilde saklanmalıdır. Mümkün olduğu kadar klişeleri düz konumda tutulmalıdır.
Gittikçe Koyulaşan Baskı:
Baskının ilk başlangıcından itibaren yazılar şişik
ve ara derinlikler kapalı olarak kendini gösterir. Fazla mürekkep transfer eden anilox kullanımı buna etkendir.
Mürekkep ve incelticilerin karışım oranı hatalı olabilir. Mürekkep normal çalışma
şartlarında doğru viskozitede olmayabilir.
Klişeler hatalı montaj yapılmış, klişe bantı altında hava boşluğu kalmıştır. Bu nedenle anilox ve klişe silindiri üzerine fazla basınç biner. Baskı forse ayarı normal olsa bile klişenin yüzeyindeki kalınlık farklılığından dolayı klişe üzerine fazla basınç etki eder.
Ayrıca klişe yapımı sırasındaki poz hataları , vakumsuzluk, negatif filmin
yeterli dansitede olmaması klişe kalitesini etkileyerek bu probleme neden olabilir.
Klişe takımları arasında yenilenenleri varsa, hem yeni parçanın hem de eski parçanın aynı baskıda kullanılması da bu soruna neden olabilir. Çok renkli klişelerde yenileme işinin takım olarak yapılması baskı kalitesinin sürekliliği açısından önemlidir.
Mürekkep Sıçratma:
Baskı sırasında klişenin baskı yapmayan yerlerine (ara hoşluklara ) mürekkep sıçraması halidir.
Ana sebep olarak klişe üzerine fazla mürekkep aktarılmış olmasıdır. Ayrıca anilox merdanesinin forse ayarı da buna etkendir. Anilox'un mürekkep transfer miktarı kontrol edilmeli. Gerekiyorsa anilox değiştirilmelidir. Ayrıca anilox merdane forse ayanda kontrol edilmelidir.
Barkod Baskı Okunmuyor:
Veya istenilen kalite de barkod baskı kalitesi alınamamsının bir çok nedeni olabilir. Ürün üzerinde baskı deseninden çok barkod baskıları daha önemli değerler taşır. Bu sorunun temel nedenleri; çok fazla forse basıncından kaynaklanır.
Barkod rengi yanlış seçilmiş olabilir. Barkod çubukları hassastır. Toplam boyu normalden fazla daraltılmış olabilir. Barkod rengi ile baskı zemin rengi arasında yeterli kontraslık yoktur. Barkodu sınırlayan kenar çizgi veya zemin barkod çubuklarına çok yakın olabilir. Barkodun yönü hatalı olabilir. Barkod doğrulayıcılar bu nedenle okumayı doğru yapamaz ve baskı okunmuyor sonucuna varılabilir. Barkod çubuklarının çözünürlüğü düşük olabilir. Düşük çözünürlük keskin ve doğrusal çubuk hatlarından ziyade, girintili çıkıntılı yapıya neden olur bu da barkod doğrurulayıcının yanlış okuma yapmasına neden olur.
Bayraklanma:
Baskı yapılacak malzeme bobininde daha çok kenarlarda görülen dalgalanma şeklindedir. Baskı makinası üzerindeki malzemenin tansiyonlarının ayarsız olmasından kaynaklanır. Baskı malzemesinin özelliğine göre fazla sıcaklık uygulanıyor olması da bayraklanmaya etkendir. Bobin klavuzları ayarsız veya işlemiyor olabilirler. Makine tansiyon ayarlarını tekrar kontrol edilmesi gerekir. bobin üzerine gelen ön kurutma sıcaklıklarının biraz düşürülmesi tavsiyedir. Ayrıca bobin klavuzlarının temizliği kontrol edilmelidir.
Sıyırıcı rakle bıçakların dalgalı olması da film yüzeyine homojen mürekkep transfer olmasına etki eder. Bu da baskıda koyuluk, aşıklık etkisi yaparak bayraklanma görümüne yol açar.
Kanama, Renk Karışması:
Bir rengin diğer renk ile karışıyor olması halidir.
Baskı materyaline aktarılan ilk renk kurumuyordur. Mürekkep viskozitesi yüksek, mürekkep çok özlü ve kalındır. Solvent seçimi yanlıştır. Solvent dengeleri bozuktur. Öncelikle kurutmayı kontrol edip ayarlayınız ve ilk basılan rengin kurumasını sağlayınız. Mürekkebin viskozitesini kontrol ediniz ve tüm baskı sürecinde kontrollere devam edin. Solvent kullanım oranlarını gözden geçirin.
Bloklaşma:
Malzeme sarımında katlar bobin üzerinde birbirine yapışarak kendini gösterir. Temel neden bobin sarım basınçlarının yüksek olması görülebilir ancak yeterince kurumayan mürekkep de bu yapışmaya etkendir. Mürekkep yavaş kuruyordur ki buna temel etken de ya kurutma ısıları düşüktür, ya da çok yüksek devirde çalışılıyordur. Baskı yüzeyinin nem oranının da kabul edilenden yüksek olması, sarma merdanelerine kadar kuruyamamasına ve sarmada bloklaşmaya etken olur.
Doldurma:
Klişe yüzeyinde mürekkep birikip ince yazı ve resimlerdeki tramların
dolması halidir. Mürekkepte pigment kalıntıları ve yabancı maddeler olabilir. Klişe yapımı yanlış değilse, yolma etkisiyle ufalanan parçacıklar tramları tıkamıştır. Mürekkep viskozitesi, forse çok yüksektir. Aniloks ve bıçak basıncını kontrol edin.
Nonwoven Dokumasız Kumaş Üretim Sürecinde Yaşanan Sorunlar
Fiber damlası :
Taş tozu, ekstrüderin kalıp kafasına sıkışır, bu da ipliğin bir akıma girmemesine neden olur, bu da eşit olmayan iplik çıkışı ve iplik düşmesine neden olur. Bu sorunu çözmenin kolay bir yolu, ekstrüder kalıbını temizlemek ve bir dahaki sefere oluşmasını engellediğinizden emin olmaktır.
Filtre ağı tıkanması :
Bu da düzensiz iplik basıncına ve iplik düşmesine neden oluyor. Üreticiler, filtre ağını temizleyerek ve ağa neyin neden olduğunu bularak uygun bir çözüm bulabilirler. Kalsiyum karbonat dolgu maddesinin yavaş MFI'si kararsız akışa yol açar. MFI, üretim sürecinin verimliliğini belirleyen hayati bir endekstir . Bunu düzeltmek için üreticilerin ekstrüderin sıcaklığında bazı ayarlamalar yapması gerekebilir. Bununla birlikte, uzun vadede, daha iyi MFI için dolgu formülasyonunun yenilenmesi önerilir.
Makine parametreleri üretim malzemeleri için uygun değildir. Bu durumda tek yol makine parametrelerini ayarlamaktır.
Fiber çok yumuşak veya çok sert :
Nihai ürünlerin mekanik özellikleri söz konusu olduğunda, ana neden dokumasız kumaşta kalsiyum karbonat dolgu maddesinin formülünde yatmaktadır . Büyük miktarda dolgu masterbatch, kumaşın sertliğinin olmamasına neden olabilirken, nihai ürünlerin sert yüzeyleri esas olarak bazı katkı gruplarının yokluğundan kaynaklanır.
Zayıf mekanik özellikler :
Bu sorunun ana nedenleri, dokumasız kumaşta kullanılan kalsiyum karbonat dolgu tipi ile kumaşın zayıf yapışma kuvvetine neden olan büyük boyutlu taş tozu partikülü arasındaki uyumsuzluk olabilir. Bu nedenle üreticiler, nihai ürünlerine en iyi şekilde uyduğundan emin olmak için dolgu masterbatch formülünü yeniden kontrol etmelidir.