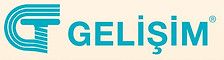


Hidrokarbonlar
Hidrojen ve karbon olmak üzere iki elementten oluşan organik bir bileşiktir. Petrol bileşiminin büyük bir kısmı değişen uzunluklardaki hidrokarbonlardan oluşur.
En küçük hidrokarbon metan, tek bir karbon atomu ve dört hidrojen atomundan oluşur. Bununla birlikte, hidrokarbonlar, zincirler, daireler ve diğer karmaşık şekiller dahil olmak üzere birçok yönden birbirine bağlanmış yüzlerce veya binlerce bireysel atomdan oluşabilir.
Hidrokarbonların özelliklerini sınıflandırmak için birkaç temel türe ayrılırlar.
Alkanlar: Bunlar doymuş hidrokarbonlar olarak adlandırılır. Yani sadece tüm karbon atomları arasında tek bağlar içerirler. Alkanlar, petrol yakıtlarının temelidir ve doğrusal ve dallı formlarda bulunurlar.
Doymamış Hidrokarbonlar: Karbon atomları arasında bir veya daha fazla çift bağa sahip olan hidrokarbonlara alken denir.
Sikloalkanlar: Bir veya daha fazla halka yapısı içeren herhangi bir hidrokarbon.
Aromatik Hidrokarbonlar: Areneler olarak da adlandırılan aromatik hidrokarbonlar, karbon atomlarının birbirini izleyen çift ve tek bağlarla bağlandığı benzersiz bir karbon molekülleri sınıfıdır. Bu molekül sınıfı, karbon atomları arasındaki bağların tek ve çift bağlar arasında bir ara bağ olduğu özel halka yapılarına sahiptir.
Bu sınıftaki moleküller, endüstriyel çözücü «benzen» içerir.
Benzen (C6H6): Diğer hidrokarbonlar gibi benzen de petrolün doğal bir bileşenidir. Oda sıcaklığında renksiz, yanıcı, tatlı kokulu bir sıvıdır ve yüksek oktan sayısına sahip olduğu için çoğu benzin karışımının bir bileşenidir.
Benzen de oldukça kanserojendir ve kemik iliği yetmezliği ve kemik kanserine neden olduğu iyi bilinmektedir. Elbette, “hoş aroması” nedeniyle tıraş sonrası ve diğer kozmetiklerde bir katkı maddesi olarak kullanıldığında kanserojenliği iyi bilinmemektedir.
En büyük benzen kullanımı (% 50), stiren ve polistren plastiklerinin ürünüdür. Ayrıca Naylon üretiminde önemli olan sikloheksan olarak bilinen bir moleküle dönüştürülür. Siklohekzan üretmek için benzenin yaklaşık% 15'i kullanılır. Böcek ilaçlarından kauçuğa kadar her şeyde daha küçük miktarlar kullanılır.
Benzen yapısı iki şekilde çizilebilir. İlkinde, çift bağ karakteri açıkça çizilir. Kısa elli versiyonda, yapıyı göstermek için halkanın içine bir daire çizilir. Benzen içindeki her bir karbon atomuna bağlı tek bir hidrojen vardır.
Aşağıdaki I. ve II. çizimleri eştir. Pratikte III. çizim kullanılır.
Benzen, renksiz, alevlenebilen, kaynama noktası 80,1 °C, erime noktası 5,5 °C olan bir sıvıdır.
Binükleer Aromatik Hidrokarbonlar: Molekülünde iki benzen halkası içeren bileşiklerdir.
Hidrokarbonlar
Hidrojen ve karbon olmak üzere iki elementten oluşan organik bir bileşiktir. Petrol bileşiminin büyük bir kısmı değişen uzunluklardaki hidrokarbonlardan oluşur.
En küçük hidrokarbon metan, tek bir karbon atomu ve dört hidrojen atomundan oluşur. Bununla birlikte, hidrokarbonlar, zincirler, daireler ve diğer karmaşık şekiller dahil olmak üzere birçok yönden birbirine bağlanmış yüzlerce veya binlerce bireysel atomdan oluşabilir.
Hidrokarbonların özelliklerini sınıflandırmak için birkaç temel türe ayrılırlar.
Alkanlar: Bunlar doymuş hidrokarbonlar olarak adlandırılır. Yani sadece tüm karbon atomları arasında tek bağlar içerirler. Alkanlar, petrol yakıtlarının temelidir ve doğrusal ve dallı formlarda bulunurlar.
Doymamış Hidrokarbonlar: Karbon atomları arasında bir veya daha fazla çift bağa sahip olan hidrokarbonlara alken denir.
Sikloalkanlar: Bir veya daha fazla halka yapısı içeren herhangi bir hidrokarbon.
Aromatik Hidrokarbonlar: Areneler olarak da adlandırılan aromatik hidrokarbonlar, karbon atomlarının birbirini izleyen çift ve tek bağlarla bağlandığı benzersiz bir karbon molekülleri sınıfıdır. Bu molekül sınıfı, karbon atomları arasındaki bağların tek ve çift bağlar arasında bir ara bağ olduğu özel halka yapılarına sahiptir.
Bu sınıftaki moleküller, endüstriyel çözücü «benzen» içerir.
Benzen (C6H6): Diğer hidrokarbonlar gibi benzen de petrolün doğal bir bileşenidir. Oda sıcaklığında renksiz, yanıcı, tatlı kokulu bir sıvıdır ve yüksek oktan sayısına sahip olduğu için çoğu benzin karışımının bir bileşenidir.
Benzen de oldukça kanserojendir ve kemik iliği yetmezliği ve kemik kanserine neden olduğu iyi bilinmektedir. Elbette, “hoş aroması” nedeniyle tıraş sonrası ve diğer kozmetiklerde bir katkı maddesi olarak kullanıldığında kanserojenliği iyi bilinmemektedir.
En büyük benzen kullanımı (% 50), stiren ve polistren plastiklerinin ürünüdür. Ayrıca Naylon üretiminde önemli olan sikloheksan olarak bilinen bir moleküle dönüştürülür. Siklohekzan üretmek için benzenin yaklaşık% 15'i kullanılır. Böcek ilaçlarından kauçuğa kadar her şeyde daha küçük miktarlar kullanılır.
Benzen yapısı iki şekilde çizilebilir. İlkinde, çift bağ karakteri açıkça çizilir. Kısa elli versiyonda, yapıyı göstermek için halkanın içine bir daire çizilir. Benzen içindeki her bir karbon atomuna bağlı tek bir hidrojen vardır.
Aşağıdaki I. ve II. çizimleri eştir. Pratikte III. çizim kullanılır.
Benzen, renksiz, alevlenebilen, kaynama noktası 80,1 °C, erime noktası 5,5 °C olan bir sıvıdır.
Binükleer Aromatik Hidrokarbonlar: Molekülünde iki benzen halkası içeren bileşiklerdir.
Hakkında
Kyäni, faydalı bileşenlerden oluşan besin takviyesi ürünlerini; benzersiz iş fırsatıyla birlikte dünya çapında 50'den fazla ülkeye ulaştırmaktadır. İdeal sağlığımızı korumak için günlük olarak Kyäni ürünlerini kullanırız, bu ürünleri başkalarıyla paylaşırız, işimizi inşa etmek ve sürdürmek için neredeyse her gün belirli bir saatimizi işe adarız ve başkalarını da Kyäni fırsatına dahil ederek veya Potato Pak ve Caring Hands programlarına katkı sağlayarak başarımızı başkalarıyla paylaşırız.
Hakkında
Kyäni, faydalı bileşenlerden oluşan besin takviyesi ürünlerini; benzersiz iş fırsatıyla birlikte dünya çapında 50'den fazla ülkeye ulaştırmaktadır. İdeal sağlığımızı korumak için günlük olarak Kyäni ürünlerini kullanırız, bu ürünleri başkalarıyla paylaşırız, işimizi inşa etmek ve sürdürmek için neredeyse her gün belirli bir saatimizi işe adarız ve başkalarını da Kyäni fırsatına dahil ederek veya Potato Pak ve Caring Hands programlarına katkı sağlayarak başarımızı başkalarıyla paylaşırız.
Sayfa Yapım Aşamasındadır.
Sayfa Yapım Aşamasındadır.
Eğitim / Bilgi / Çözüm Platformu
Polimer Katkılara Giriş
Polimerlere Neden Katkı Eklenmelidir:
Öncelikle şunu ifade etmek gerekir ki, polimerlerin %95 'inden fazlasına katkı ilave edilerek stabilizasyon sağlanmazsa, polimer ham haliyle çok zayıf olacak ve amaca hizmet etmeyecektir. Örneğin; PE ve PP gibi saf poliolefinler çok hızlı oksitlenirler . Bu nedenle bunlara dışarıdan katkılar eklenerek işlenebilir hale getirilirler. Saf PVC yüksek sıcaklıkta bozulma olmadan ekstrüde edilemez ve kalıplanamaz, ve süreç sonrasın neredeyse hiçbir amaca hizmet etmeyen çok zayıf mekanik değerlere sahip olur.
En temel amaçla, katkı maddeleri, polimerlerin işlenme zorluklarının bertaraf edilmesi amacıyla kullanılır. Performans değerlerini muhafaza eder ve polimeri korur. Katkı maddeleri ile olumsuz çevresel etkilerden uzaklaşılır.
Hangi polimere, hangi oranda, hangi katkı maddesi:
Kullanılması gereken katkı maddesinin doğası birkaç parametreye bağlıdır. Başta polimerin kimyasal bileşimi, katkı maddeleri ile karşılaştırılabilmelidir. Polimer özelliğini bozmaması için, polimerik yapı ile reaksiyona aktif girmemelidir. Polimerin hangi prosesle iişleneceği kesinlikle bilinmelidir. Isıl süreçte ne kadar sıcaklığa maruz kalacağı tespit edilmelidir. Aksi halde katkı maddesinin bozulması sorunu ortaya çıkabilir. Yada ısıların polimer için uygun olup katkı için uygun olmaması durumunda, ısının yüksek olması halinde katkının yanabileceği, ısının düşük olması halinde süreç sonunda katkının çalışmayarak zayıf kalabileceği öngörülebilmelidir.
Polimerler; ısıya, ışığa, kesmeye, neme maruz kaldıklarında bozulurlar. Üretimin hangi nihayi noktaya hedeflendiği saptanmalıdır. Stabilizasyonun sağlanması için hangi etkenin önüne geçilmek isteniyorsa, eklenecek katkının da bu yöne hizmet için olduğu tespit edilmelidir. (örneğin, suyun içinde çalışacak bir plastik ürün üretiminde, polimere alev geciktirici katkı eklemek biraz anlamsız olacaktır).
Normal zincir büyümesi polimerleri olan poliolefin (PE, PP), polistiren (PS), (PVC) de, Karbon-Klor ve Karbon-Hidrojen bağları çevre sel etkenler tarafından bozulmaya çok yatkındır. Bu nedenle, oksidasyona, ışığa, UV ışınımına, termal bozunuma karşı korunmalıdır.
Aşamalı büyüme polimerlerinde ise bozunmaya elverişli bu bağlar yoktur. Ester , amid, karbonat grupları olarak çok çabuk hidrolize olurlar. Polimerler işlem sırasında nem varlığında moleküler bozulmaya uğrar.
Tipik olarak bir polimer formülünde birden fazla katkı maddesi bulunur. Bu; katkı maddeleri arasındaki karşılıklı etkileşim ile optimal bir formülasyon yazılımı için uygulanır. Ve adeta küçük oranlardaki bu katkılar bir fedakarlık mantığı ile çalışırlar. Tamamen kendilerini korumayı bırakıp yok ederek, polimeri korumaya başlarlar.
Polimere bağlanan bu katkı maddeleri dikkat edilecek olursa zaten, tamamen çevre etkenlerine göre sınıflandırılmış olduğu farkedilecektir. antioksidantlar,, antibakteriyaller, ısı dengeleyiciler, ışık dengeleyeciler , UV kırıcılar gibi.
Ürün amacına hizmet ettiği sürece bir çok katkı maddesi bir ana taşıyıcı polimere proses şartları uyduğunca eklenebilir. Ancak haırlardan çıkartılmamalıdır ki; eklenecek katkıların oranları ne kadar küçük olursa olsun, birim maliyetleri polimerlerden çok daha yüksek olduğundan, üretim maliyetini yükseltirler. Bu nedenle tercih edilecek katkıların maliyetleri de dikkate alınmalıdır.
Katkı maddelerinin polimer zincirde kullanım oranları, temelde taşıdıkları aktif madde oranı ile doğru orantılıdır. Aktif madde oranı yüksek olan bir katkı maddesi kullanım yüzdesinin, aynı amaca hizmet eden ama aktif madde oranı düşük olan bir katkı maddesinin kullanım yüzdesinden düşük olması gerekir. Yüksek oranda katkı maddesi kullanımı, kaş yapayım derken göz çıkartmak deyimi ile eş anlamlıdır. Katkı maddesinin çok yüksek oranda kullanımı maaliyetleri aşırı yükseltebileceği gibi polimerin kendisini de yok edebilir.
Sıvı katkı maddelerinin kullanımı zordur. Örneğin polimer tozu kullanılıyorsa (öğütülmüş PE gibi) buna sıvı katkı ilavesi, karıştırma, yoğurma sürecinde homojen dağılımının, dispersiyonun çok zor olmasından dolayı süreci sıkıntıya sokabilir.
Compound
Ana hammaddenin ısıl dayanımı, darbe dayanımı, renk, sertlik gibi faktörlerini içine çeşitli katkılar katarak artırarak hammadde oluşturulmasına compound denir.
Bu hammadde artık saf bir malzeme değil, katkılar ile özellikler güçlendirilmiş kompozit bir malzemedir doğrudan hammadde olarak kullanır. Masterbatch, ana hammaddenin renk, fiziksel özellikler ve maliyet özelliklerini geliştirilmek için içine pigment, katkılar, ve dolgular karıştırılarak müşteriye granül halde sunulur. Compound ve masterbatch üretim şekilleri açısından benzer olasalar da, kullanım şekilleri yönü ile birbirlerinden ayrılırlar. Compound %100 hammadde olarak kullanılırken, masterbatchler doğrudan hammadde olarak kullanılmaz. Hammaddeye belirli oranlarda karıştırılarak kullanılır.
Compound ve masterbatch üretim şekilleri açısından benzer olsalarda, kullanım şekilleri yönü ile birbirlerinden ayrılırlar. Compound; Ana hammaddenin ısıl dayanımı, darbe dayanımı, sertlik gibi faktörlerini içine çeşitli katkılar katarak artırarak müşteriye istediği özellikte hammadde oluşturulmasına compound denir. Compound sonrasında müşteriye gönderilen hammadde artık saf bir malzeme değil, katkılar ile özellikler güçlendirilmiş kompozit bir malzemedir. Müşteri bu malzemeyi compound üreticisinden alarak hammadde olarak kullanır.
Masterbatch; Ana hammaddenin renk, fiziksel özellikler ve maliyet özelliklerini geliştirilmek için içine pigment, katkılar, ve dolgular karıştırılarak müşteriye granül halde sunulur. Compound dan farklı olarak müşteri bunu hammadde olarak kullanmaz, Hammaddesine belirli oranlarda karıştırarak onun rengini, maliyetini ve fiziksel eksikliklerini gidermeye çalışır.
En temel haliyle bir compound / masterbatch reçetesi bu şekildedir.
%A+%B+%C+%D=%100 ile formül hem compound hem de masterbatch için geçerlidir.
Peki ama nasıl birbirinden ayrılacak;
Bunun cevabı kullanım alanında yatmaktadır. Kullanım sahasına (son prosese) inene kadar, compound ve masterbatch eş anlamlı iki terimdir. Üretim şekilleri açısından tamamen aynıdır.
Yani üretici tarafından yapılan bu karışım, doğrudan extruzyon makinesinde %100 yada kullanılacağı formülde en büyük oranda taşıyıcı hammadde olarak kullanılacaksa compound, çok daha küçük oranlarda (%0,5, %5, %20 vs) kullanılacaksa masterbatch olarak tanımlanacaktır.
Temel ayrım noktası olan nihai kullanıcıda, compound ekstruzyona doğrudan giriyorsa, "compound" olarak yoluna devam eder.
Ancak başka karışım yada taşıyıcı hammaddelere belirli oranlarla katılıyorsa artık kimliğini değiştirir ve, ya renk yada katkı "masterbatch" olur. Başka bir basittanımlama da, yukarıdaki basit tarif formüldeki Boyar Madde mevcut ise Renk Masterbatch, boyar madde yok ( yani C=0) ise Katkı Masterbatch olarak tanımlanması şeklinde yapılabilir.
Compound üretimi; fiziksel özelliği yetersiz gelen plastiğin fiziksel özelliklerini iyileştirmek amacıyla yapılır. Taşıyıcı hammaddesine yüklü oranda katılan dolgular, pigmentler, karbon fiberler gibi malzemeler eklenerek gerçekleştirilir.
Polimer malzeme ile polimer olmayan (daha çok katkı malzemeleri olan Kalsit, Talk, Talaş, vs) malzemenin işlenmesi sırasında çeşitli problemler meydana gelir. Bunlar; daha çok, malzemenin makine içindeki akışkanlığı, malzemelerin birbiri içerisindeki uniform dağılmaması, karıştırılan malzemelerin birbirine bağlanmaması, katkı veya hammaddeki nem dolayısı ile kabarcıklı yapı oluşması şeklinde kendini gösterir.
Ekstruzyonda tanecik büyüklükleri arasındaki farklılıklardan ve erimeyen yapılarından dolayı içinde hava boşlukları oluşturur. Olduğu gibi bu boşluklar polimerik gaz ile dolar ve nihai kullanıcıda, kabarcık, erimeyen tanecik, yüzey pürüzlülüğü, portakal kabuğu görünüm gibi problemler olarak karşımıza çıkar. İnce hassas kalıplamalarda kalıbın dolmaması ile eksik parça, çöküntü görülmesine etken olur.
Dolgu malzemesinin mikron boyutuna ve formül oranına bağlı olarak üretim sürecinde süzgeç tıkanmaları sıklaşabilir. Compound üretimi sürecinde bir, ve sonrasındaki üretim prosesinde de bir olmak üzere çift çekim gerçekleşir.
Ancak compound üretimindeki ekstruzyon hattı ile, enjeksiyon sürecindeki ekstruzyon hatları ve süreçleri eş değildir.
Enjeksiyon sürecinde malzeme her ne kadar ikinci defa ekstrüde oluyor olsa da, ama vida boyu ama çevrim süreci nedeni ile bu ikinci çekim süreci kısadır. Bu nedenle compound üretimi yapılırken, malzeme bir defa çekildikten sonra, tekrar ikinci defa daha ekstrüderde çekilerek çift çekim yapılır ve bu da malzeme içerisinde gaz birikimini, erimeyen tanecik problemini gözle görülür iyileştirir.
Compound yapısı çok daha homojenize olur. Nihai kullanıcıda da artık üçüncü defa ekstüzyona giren malzemede yukarıda bahsi geçen fiziksel problemler pek gözlenmez.
Masterbatchler tüm plastik proseslerinde rahatlıkla kendine yer bulabilirken, compound olarak daha çok enjeksiyon ve diğer "kalıplama" proseslerinde kullanılır.
Taşıyıcı Polimer:
Compound ve masterbatch’in katılacağı hammadde ve son ürünün kullanılacağı yere göre compound hammaddesi belirlenir. Compound üretimi fiziksel özelliği yetersiz gelen plastiğin fiziksel özelliklerini iyileştirmek amacı ile yüklü oranda plastik içine katılan dolgular, pigmentler, karbon fiberler gibi malzemeler ihtiva edilir.
Polimer malzeme ile polimer olmayan malzemenin işlenmesi sırasında çeşitli problemler meydana gelir. Bunlar; daha çok, malzemenin makine içindeki akışkanlığı, malzemelerin birbiri içerisindeki uniform dağılmaması, karıştırılan malzemelerin birbirine bağlanmaması, katkı veya hammaddeki nem dolayısı ile kabarcıklı yapı oluşması şeklinde kendini gösterir.

Renk Masterbatchleri
Plastik ürünler başlangıçta renki ve arzu edilen özelliklerde değildir. Bu nitelikler ana taşıyıcı yapı belirlendikten sonra bileşiğe dahil edilecek katkılarla sağlanır. Ki bunlar masterbatch olarak tanımlanır. Masterbatch kelimesi "ana karışım" anlamına gelmekle birlikte, genellikle "Eritip şekillendirme aşamasında plastik ham maddeye katılan, granül biçimindeki boya" anlamında kullanılan bir terimdir. Organik ve ya inorganik pigment veya katkı maddelerinin bir taşıyıcı polimerik malzemede (termoplastik, kauçuk veya elastomer) yüksek konsantrasyonda homojen şekilde harmanlandığı boyar maddedir. Renk masterbatchleri ve katkı masterbatchleri olmak üzere iki tür masterbatch vardır. Ancak yerleşik tanımlamada masterbatch ifadesi daha çok «renk» için kullanılır. Katkı masterbatchleri de doğrudan «katkı» olarak telafuz edilir. Renk masterbatchleri, ürün üzerinde istenilen renk ve efekti (floresanlık, yaldızlık, sedeflik, opaklık vs) elde etmek için kullanılır. Temelde renk masterbatchlerinin ana variyeti, ürün renklendirmesinde ihtiyaç olan pigmentlerin kullanım pratikliğini sağlamaktır. Yani ürünü asıl renklendiren pigmentdir.
Renk masterbatchleri üç temel bileşene sahiptir. Taşıyıcı hammadde, rengi veren pigment ve prosese yardımcı olacak dispersanlar. Dispersanlar daha çok, proses iyileştiriciler ve ya homojenliği, iletkenliği, UV direncini sağlayıcılar gibi eklenti ve ya katalizör içeriklidirler.
Renk masterbatchleri; siyah, beyaz ve renkli olarak üç temel başlıkta olurlar. Ve ürünün istenilen renkte olması bu üç başlığın sonsuz olabilecek varyasyonda farklı bileşimi ile gerçekleşir. Masterbatcler, genelde ana bileşik üzerine %3 ve altında oranlarla işlenirler, ancak istenilen niteliğe ulaşmak için bu oranın üzerinde de kullanılabilirler. Masterbatchlerde dikkat edilmesi gereken en temel husus; masterbatch taşıyıcı hammaddesinin, ana bileşik hammaddesi ile uyumlu olmasıdır.
Ayrıca ürünü yüzeyinin dokulu, pütürlü, desen izli olması ve kalınlığı da kullanılan renk masterbatchlerinin etkisine tesir edeceği dikkatlerden kaçmamalı. Doğru tercih ve kullanım oranı tespiti için yeni çalışmalarda, renk masterbatchi tedarik etmeden önce, ürünün numunesi tedarikçiye ulaştırılmalı ve önden bir numune alınması yerinde olacaktır.
Renk masterbatch, plastikleri renklendirmek için kullanılan katı veya sıvı bir katkıdır. Bir ısı işlemi sırasında kapsüllenmiş bir pigment veya katkı maddesinin bir taşıyıcı reçineye konsantre edilmiş bir karışımıdır, daha sonra soğutulur ve granüler bir şekle kesilir. Masterbatchler, üreticilerin plastik üretim prosesi sırasında ekonomik olarak ham polimeri renklendirmelerine olanak tanır.
Masterbatch üretimi süreç, «mono» ve «tailor made» olarak iki kısıma ayrılır.
Mono : Üretiminde ana veya en çok sarf oranı olan renkler çalışılır.
Tailor made: Elde dilen mono renklerinin çeşitli kombinasyonlarda eşleştirilmesi, ile elde dilen veya istenilen renklerdeki çalışmadır.
Dikkat edilecek hususlar şu şekilde sıralanabilir.
- Özellikle PVC üretiminde kullanılan dolgular renk tonunu değiştirmektedir.
- Kablo üretim şekillerindeki farklılık boyanın rengini etkilemektedir.
- Makinelerin iyi temizlenmemesi renk sökümüne ve ize neden olmaktadır. Makinelerin durup çalışması daha önceden kalan akış yolu dışındaki alanda var olan malzeme ile temasa neden olabilir. Bu da üründe iz sorunu olarak ortaya çıkar. Makine kirliliğinden şüphelenildiği durumlarda sadece hammadde ile birkaç baskı alınıp, akış hattının temizliği her aşama ile kontrol edilmelidir.
- Makineler 10 dakikadan uzun süre durdurulup tekrar çalıştırıldığında ilk baskılar kontrol edilmelidir. Malzeme uzun süre ısıya maruz kaldığı için yanma gerçekleşebilir.
- Özellikle film üretiminde kullanılan hammadde ve mikron değişikliği olduğu durumlarda mutlaka deneme üretim yapılmalıdır.
- Kullanılan taşıyıcın erime noktasından düşük sıcaklıklarda çalışıldığında nihai üründe erime gerçekleşmeyecektır.
- Nem çeken hammaddeler üretimden önce mutlaka koşullandırılmalıdır.
Pigmentler
Bazı kayaçlar, topraklar ve mineraller yıkama ve öğütme gibi basit işlemlerden geçirildikten sonra "mineral pigment" olarak kullanılabilme özelliği kazanırlar. Aranan özellikler uygun renk, örtme gücü, yağ emme kapasitesi, suda eriyen tuz ihtiva etmemesi gibi hususlardır. Boya toprağının nem oranı, asgari Fe2O3 tenörü, ışığa karşı dayanıklılık gibi özellikleri ve fiyatının uygun olması da önemlidir. İnorganik pigmentlerin kavrularak renklerin koyulaştırılması ve duraylı hale getirilmesi mümkündür. Tabii boya topraklarında renk verici unsur, genellikle mineraller içindeki demir elementidir.
Hematit, gotit, limonit gibi mineraller bozuşma sonucu topraklaşarak okr, amber gibi sarı, kırmızı ve kahverenkli boyaları oluştururlar. Yeşil renkli toprak boyaların kaynağı ise seladonit, garnierit ve glokonit gibi minerallerdir. Vivianite ve azurit mavi boyalar, piroluzit, grafit ve manyetit ise siyah boyalar için kullanılır. Beyaz boyaların üretiminde ise kaolin, barit, tebeşir ve anhidrit kullanılır. Gri tonlar öğütülmüş şeyl katılarak elde edilir.Mineral boyalar sıva, harç, çimento, lastik, muşamba (döşemelik) ve benzeri maddelere renk ve yoğunluk sağlama amacı ile kullanılırlar.
Demirhidroksit ile montmorillonitin karışımından oluşan ve Bolus tabir edilen çok kıymetli bir boya orta çağ boyunca Anadolu'dan götürülüp Paris'te öğütülerek ahşap heykellerin yaldız altı kırmızı astarı olarak asırlarca kullanılmıştır. Yine Anadolu'dan getirilen ve Snopia adı verilen kırmızı bir boya Rembrand'ın tablolarında kullanılmış ve çok aranmıştır. Bolus halen jips ve kireç ile karıştırılarak sulu boya üretiminde kullanılmaktadır.
Pigmentler ve boyalar, plastiklere, tekstil ürünlerine ve diğer birçok malzemeye renk, opaklık ve ışıltı sağlar.
Boyalar, substratla (bileşen veya ayrışan madde) kimyasal olarak bağlanan organik çözünür maddelerdir.
Pigmentler ise genellikle çözünmeyen ve alt katmanla reaksiyona girmeyen organik veya inorganik partikül katılardır.
Pigmentler, dalga boyu seçici absorpsiyonun (emebilme ve soğurma özelliği) sonucu olarak yansıtılan veya iletilen ışığın rengini değiştiren bir malzemedir. Başka bir deyişle, belirli bir renkte görünen bir maddedir çünkü belirli dalga boyundaki ışığı seçici olarak emer. Pigmentleri kullanmanın temel amacı, ister tekstil ister boya olsun, malzemelere renk sağlamaktır. Bazı insanlar genellikle pigmentlerin ve boyaların aynı olduğunu düşünür, ancak oldukça farklıdırlar. Her ikisi arasındaki en büyük fark, çözünürlükleridir.
Bir boya sıvı içinde kendi kendine çözülebilirken, pigmentler bir bağlayıcı yardımıyla bir sıvı içinde çözülebilir. Boyalar öncelikle tekstil ve kağıt endüstrisinde, pigmentler ise renklendirici boyalar, mürekkepler, kozmetikler ve plastikler gibi endüstrilerde kullanılmaktadır.
Formülasyon yöntemlerine bağlı olarak, pigmentler iki türe ayrılabilir:
-
Organik pigmentler
-
İnorganik pigmentler.
Bu iki temel ayrımdan başka iki tip pigment daha vardır:
-
Metalik pigmentler
-
Endüstriyel pigmentlerdir.
Metalik Pigmentler :
Adından da anlaşılacağı üzere metalik pigmentler, çinko ve alüminyum pigmentleri gibi metal pigmentleri içerir.
Endüstriyel Pigmentler :
Endüstriyel uygulamalarda yaygın olarak kullanılan ve organik, inorganik ve metalik pigmentleri içeren pigmentlerdir. Endüstride üç pigment sınıfı vardır: absorpsiyon pigmentleri (sulu boya boyalarında kullanılır), metal efekt pigmentleri (yüzey parlaklığı oluşturmak için kullanılır) ve sedefli pigmentler.
İnorganik Pigmentler :
Adından da tahmin edebileceğiniz gibi, bu tür pigmentler tam tersi organik pigment türüdür. Bu pigmentler aynı zamanda "sentetik pigmentler" olarak da bilinir. Laboratuvarlarda formüle edilirler ve inorganik pigment üreticilerine büyük bir kontrol kapsamı sunarlar. İnorganik pigmentler, oksidasyon gibi nispeten basit kimyasal işlemlerle üretilir.
İnorganik pigment tedarikçileri bu tür pigmentleri esas olarak boya, plastik, sentetik elyaf ve mürekkep endüstrisine tedarik etmektedir. Parlak renklerin gerekli olduğu kullanımlarda, yüksek renk mukavemeti sağladıkları için organik pigmentler kullanılır. İnorganik pigmentler, diğer renkleri açmak ve ayrıca opaklık sağlamak için yaygın olarak kullanılan beyaz opak pigmentleri içerir.
Organik (Doğal) Pigmentler :
Bu tür pigmentler doğal olarak oluşur ve yüzyıllardır kullanılmaktadır. Kimyasal yapıları oldukça basittir. Renklerini veren mineraller ve metaller içerdikleri için organik olarak adlandırılırlar. Organik pigment üreticileri, bunları yıkama, kurutma, toz haline getirme ve bir formülasyonda birleştirmeden oluşan basit bir işlemle üretirler.
İnorganik pigmentlere kıyasla, bu pigmentlerin bu kullanımı daha az sıklıkta ve bu nedenle sınırlı sayıda organik pigment tedarikçisi var. Bu pigmentler, gerekli renk şiddeti çok fazla olmadığında kullanılır.
Organik pigmentler insanlar tarafından kullanılan en eski pigmentler arasındadır. İlk olarak 60 bin yıl önceki kalıntılarda insan cenaze hazırlığında ve yaklaşık 20 bin yıl önceki çok renkli mağara duvarları sanatında kullanıldığı ortaya çıkmıştır. Tarihöncesinde yüzeydeki kil ve kaya birikintilerinden çıkarılan birçok inorganik pigment, uzun süreler boyunca olağanüstü kalıcılık göstermiştir.
Birkaç istisna dışında, inorganik pigmentler, bir mineral elementin oksijen ve oksitler, oksit hidroksitler, sülfitler, sülfatlar, silikatlar ve karbonatlar olarak bilinen kimyasal sınıflara giren diğer elementlerle (çoğunlukla sülfür, silikon veya karbon) kombinasyonlarıdır.
Doğal inorganik pigmentlerle ilgili temel uyarı, bunları içeren herhangi bir boyanın (özellikle siennalar, umber ve ochre'ler) üreticiler arasında önemli ölçüde değişiklik göstereceğidir. 1998'de Daniel Smith, "İspanyol altın aşısı" adı verilen güzel bir toprak pigmenti pazara kazandırmış, ancak kil kaynakları tükendiği ve malzemelerin kaynağı belirlenemediği için üretimi de ortadan kalkmıştır.
Geleneksel olarak doğal inorganik renklerin çoğu; sarı hardal, ham sienna, yanmış sienna, ham kereste, yanmış kereste ve venedik veya kızılderili kırmızısı tonlarındadır.
Bu kategorideki pigmentler şunları içerir:
Kırmızı topraklar:
Hepsi büyük oranlarda demir oksit (koyu mordan açık kırmızı hematit veya günlük pas, turuncudan sarıya lepidokrosit veya koyu kahverengi maghemit ) içeren topraktan (çoğunlukla kilden) yapılan geniş ve çeşitli bir pigment kategorisi işlenmiş ve doğal demir oksit olarak satılır. Pigment rengi donuk sarıdan donuk koyu sarı, donuk turuncu, donuk kırmızı veya koyu kahverengiden neredeyse siyaha kadardır. Renk, ortalama partikül boyutuna, manganez veya diğer elementlerin (rengi koyulaştıran ve matlaştıran) varlığına ve suyun demir oksit kristallerine kimyasal olarak bağlanıp bağlanmadığına bağlıdır. Kırmızı demir oksitler dünyanın her yerinde görülmesine ve antik çağlardan beri pigment olarak kullanılmasına rağmen, şu anda Malaga yakınlarında zengin tortular bulunmaktadır , İspanya (karakteristik kahverengimsi bir tonu olan İspanyol kırmızısı) ve Hürmüz'de, Basra Körfezi'nde (Fars kırmızısı) karşımıza çıkar. Tarihsel olarak, Avrupa'daki sarı kahverengi toprak kaynakları Leghorn veya Siena yakınlarında (Toskana, İtalya) bölgesinde zengindir. Bunlar %50 demir oksit ve %1'den az manganez dioksit içerir.
MÖ 2000 civarında pişirildikten veya cilalandıktan sonra çanak çömleklerin gözle görülür kızarması veya koyulaşması sağlanırdı. Ve bazen kırmızı topraklara eklenen doğal manganez cevherleri, çanak çömlek killerinde veya sırlarda daha koyu kırmızı, mor veya siyah renkler oluşturduğu gözlemlenmişti
Sarı topraklar :
Silika ve kil içeren doğal topraklar, sulu demir oksit formları (sarı kahverengi limonit veya kahverengi sarı ila yeşil sarı götit ) ve eser miktarda alçı veya manganez karbonattır. Kırmızı demir oksitler gibi, dünya çapında bulunurlar ve tarih öncesinden beri pigment, boyar madde olarak kullanılmıştır. Tarihsel olarak en iyi limonit derecelerinden biri olan Fransız toprak boyası, yaklaşık %20 demir oksit içerir ve silika bakımından yüksektir.
Yeşil topraklar :
Büyük miktarlarda silika ve yeşil mineraller olan glokonit ve seladonit içeren killer, esas olarak sulu demir, magnezyum ve alüminyum potasyum silikatlardan oluşur. Renk koyu, grimsi mavi yeşilden koyu, donuk sarımsı yeşile değişir. Tamamen ışığa dayanıklı ve kimyasal olarak atıl, yeşil topraklama veya terre verteantik çağlardan beri dünya çapında kullanılmaktadır. Avrupa'da resimlerde belgelenen ilk kullanım Roma freskleridir; Aynı zamanda Orta Çağ'da et tonları ve gölgeler için bir alt boyamada yaygın olarak kullanılmıştır. Başlangıçta Orta Avrupa'daki (bugünkü Çek Cumhuriyeti), Verona yakınlarındaki (İtalya) veya Fransa'daki yataklardan çıkarılmış olan modern malzemeler, Kıbrıs'taki yüksek kaliteli yataklardan gelmektedir.
Lapis lazuli :
Koyu mavi mineral lazuritin (doğal ultramarin, kimyasal olarak en karmaşık mineral pigmenti) kalsit veya kalkspat ve demir pirit ile karmaşık bir kaya karışımıdır . Ultramarine adı, onu azzuro della magna'dan ayırmak için kullanılan azzuro oltramarino'dan (denizin üzerindeki mavi) tanımlamasından gelir. Lapis, Çin, Tibet ve Orta Asya'da bulunur ve eski Babil ve Mısır kültürlerinde takı, heykel ve resim yapımında kullanılmıştır. Venedik yoluyla Avrupa'ya ithal edilmiş, toz hale getirilmiş ve ortaçağ el yazmalarında ve sanatında çok maliyetli bir kırmızımsı mavi pigment olarak kullanılmak üzere safsızlıklardan ayrılmıştır.
(Lacivertten çok daha açık ve soluk bir mavi)
(Na, Ca)8(AlSiO4)6(SO4,S,Cl)2
Azurit :
Daha az yaygın olan (yeşilimsi mavi) bakır karbonat kristalleridir. Azurit havada kararsızdır. Ancak antik çağda mavi pigment olarak kullanılmıştır, ancak sıklıkla diğer sentetik pigmentler (Mısır mavisi, bakır kalsiyum silikat gibi) tarafından değiştirilmiş veya daha pahalı olan ultramarine alt boya olarak tercih edilmiştir. Kristaller genellikle kaba olarak öğütülür, çünkü parçacık boyutu küçüldükçe renk de koyu maviden zayıf, soluk maviye doğru değişim göstermektedir. Azurit, asitler tarafından ayrıştırılır ve ısı ve bazı yağ araçları ve vernikler ile kararır. Avrupa'da 15. yüzyıldan 17. yüzyıla kadar, kullanılan önemli bir pigment olan azuritin ana kaynağı olan Macaristan'dı. Türkler'in Macaristan fethinden sonra kullanımı azalmıştır.
(Gök mavisi, koyu maviden soluk maviye; iletilen ışıkta soluk mavi)
Malakit :
Dağ yeşili, mineral yeşili veya verdeazzuro ("yeşil gök mavisi") olarak adlandırılan, bakırın yüzey birikintilerinde dünya çapında bulunan sulu bakır karbonatın daha yaygın (yeşil) formudur . Eski Mısırlılar onu yeşil bir pigment olarak kullanmak için bir toza öğütmüş, Roma döneminden beri de genellikle sanatsal kullanımlar için tercih edilmiştir. 18. yüzyılın sonunda tamamen kullanım dışı kalmıştır. Parçacık boyutu küçüldükçe rengi önemli ölçüde açılır ve maviye döner..
(Siyahımsı yeşil ve cam parıltılı, zümrüt yeşili renginde ve ipek parıltılı veya donuk).
Kimyasal Bileşimi: Cu2CO3
Kristal Sistemi: Monoklinik
Kristal Biçimi: Çok nadir ve küçük kristalli, genellikle lifsi ve ışınsal, iğnemsi, kısa-uzun prizmatik; çoğunlukla masif, böbreğimsi
İkizlenme: {100} yüzeyinde olağan
Sertlik: 3.5 - 4
Özgül Ağırlık: 4 - 4.05
Dilinim: {-201}
Renk ve Seffaflık: Parlak yeşil, siyahımsı yeşil; yarı şeffaf-opak
Çizgi Rengi: Soluk yeşil
Parlaklık: İğnemsi kristalleri ipeğimsi, masif olanlar donuk-mat, diğerleri elmas parıltılı, camsı
Ayırıcı Özellikleri: Rengi, böbreğimsi formu ve HCl'de çözünülürlüğü
Bulunuşu: Malakit, bakır yataklarının oksidasyon zonunda oluşan ikincil kökenli tipik bir mineraldir.
Azurit, kuprit ve bakır ile birlikte bulunur. Topluluk oluşturduğu diğer mineraller kalsit, krizokol ve limonit dir.
Sedef :
Organik kökenlidir. Molluskaların (değişik mideye türlerinin) kabuk kısımlarının iç yüzeylerinde çoğunlukla aragonitin konsantrik olarak birikmesiyle oluşur




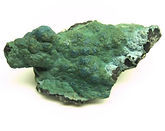
Kırmızı Toprak
Sarı Toprak
Lapis Lazuli
Azurit
Malakit
Renklendirici Formları
Renklendirici (Renk Masterbatc) tercihinde, dikkate alınması gereken bazı ön değerlendirme kriterleri söz konusu olabilir.
Doğru renklendirici seçimindeki bu kriterler;
-
Sağlık ve güvenlik kaygıları
-
Üretim sürecinde kullanım kolaylığı
-
Belirli renklerin kullanım hacminin yanı sıra renk eşleştirme doğruluğu
-
Renk kalitesi sorunlarının bertarafı
-
Maliyetlendirmede olabildiğince en az seviyede etki
gibi başlıklarda olabilir.
Konsantre renklendiriciler (renk masterbatchler):
Dünya çapında plastikler için kullanılan renklendiricilerin yaklaşık %70'i konsantreler şeklindedir. Ve bu oranın neredeyse yarısını da beyaz renk teşkil eder. Renk konsantreleri, renklendiricilerin doğrudan bileşiğe eklendiği önde gelen formdur. Fiziksel yapıları mercimek taneli yada çubuk (spagetti) kesim granül şeklindedir. Hatta granül boyutu 1 milimetrenin altında süper konsantre yapıda olalar da vardır. Üretim sürecinde eriyik işleme sırasında otomatik ölçüm ekipmanı kullanılarak ana (taşıyıcı) polimere kolay entegrasyon sağlar. Herhangi bir dozajlama ünitesi olmayan tesislerde, ekstruzyon öncesinde karışım manuel yada mikser makinalarınca ön harmanlaması söz konusudur. En temelinde konsantre renklendiricilerde taşıyıcı polimer LDPE 'dir. Ancak prosesin yüksek performanslı uygulamalara yönelik olması durumunda, ana polimer ile eşleşik olması tercih edilir (PP, PC vs.). Sürecin hızlı akmasında konsantre renklendiriciler tercih nedenidir.
Konsantrelerdeki normal pigment yüklemeleri %20 - %25 seviyelerindedir. Ancak, %80'e kadar pigment içeren "süper konsantreler" de söz konusudur. standart ürünlere göre uygun maliyetli alternatifler haline geldi, çünkü bunlar için daha az konsantre gerektiriyorlar. Konsantre renklendiricilerin içeriğine UV dengeleyici katkılar gibi ek özelliklerin de eklenmesi ile formulasyonu zenginleştirilebilir. Bu şekilde ekstrüzyonda bu minik oranlı katkıların homojenizasyonu daha sağlam olur. Bu, ürünlerin ana polimer ile daha kolay harmanlanması nedeniyle daha yüksek üretim oranlarının yanı sıra maliyette de tasarrufu sağlar.
Derecelendirme: Maliyet (2x orta) / Nakliye-Taşıma (2x orta) / Hacim (2x orta)
Dispersiyon (3x yüksek) / Dozajlama Kontrol (3x yüksek) / Renk Geçiş Kolaylığı (2x orta)
Sıvı renklendiriciler :
Yaklaşık %80 oranında yüksek pigment yüklemelerine sahiptirler. Sıvı (akışkan) olmaları nedeniyle, işleme makinesinin hazne boğazına otomatik olarak ölçülmesi ve pompalanması için özel ekipmana ihtiyaç duyarlar. gerektirir. Ancak taşıyıcı boru hatlarına çok daha kolay bir şekilde bağlanabilecekleri teknik gelişimler mevcuttur. Pigmentin iyi bir şekilde dağılmasına olanak kılarlar. Ancak pompalama (dozlama) ünitesinin olmaması durumunda, toz polimerlerle homojenize karışımı elde etmek zor olacaktır. Bu da ekstrüzyon sonunda renk dağılımında problemler doğuracak ve sonucu optimize etmek için, ikinci çekim (tekrardan ekstrüde etmek) gerektirecektir.
Derecelendirme: Maliyet (2x orta) / Nakliye-Taşıma (2x orta) / Hacim (2x orta)
Dispersiyon (3x yüksek) / Dozajlama Kontrol (3x yüksek) / Renk Geçiş Kolaylığı (3x yüksek)
Kuru toz renklendiriciler (pigmentler) :
Satın alınabilecek en uygun maliyetli renklendiricilerdir. Ancak, kullanımlarını zorlaştıran dikkatli tartım ve toplu harmanlama ile ana polimere dağılmalarına izin veren ıslatma ünitelerine ihtiyaç duyarlar. Ve aynı zamanda toz formda olmalarından dolayı çevreye etkili zarar verirler. Havada asılı kalmalarından dolayı operatörler üzerinde olumsuz etkisi vardır. Sağlığı etkileyici olmasından dolayı çalışma ortamının kesinlikle havalandırma (emici fan) sistemi olmalıdır.
Derecelendirme: Maliyet (3x yüksek) / Nakliye-Taşıma (1x zayıf) / Hacim (3x yüksek)
Dispersiyon (1x zayıf) / Dozajlama Kontrol (2x orta) / Renk Geçiş Kolaylığı (1x zayıf)
Ön renklendirmeli polimer :
Derecelendirme: Maliyet (1x zayıf) / Nakliye-Taşıma (3x yüksek) / Hacim (1x zayıf)
Dispersiyon (3x yüksek) / Dozajlama Kontrol (1x zayıf) / Renk Geçiş Kolaylığı (3x yüksek)
Katkı Masterbatchleri
Alev Geciktiriciler: Yapısında bromür, klor, azot, alüminyum, antimon ve bor elementlerinden bir veya bir kaçını bulundurlar ve polimerik zincire dahil ederek yanmanın etkisini düşürürler. Bazı yüksek performanslı plastikler aleve dirençli plastikler, alev geciktirici plastik, yanmaz plastik veya kendi kendini söndüren plastik olarak sınıflandırılabilir, bu da onları yangın korumasının önem arz ettiği yerlerde kullanım için uygun hale getirir. Genel olarak termoplastik malzemeler, kelimenin tam anlamıyla tutuşmaz değildir çünkü alevle doğrudan temas halinde yanmaya başlarlar. Ancak plastiklerin çoğu alevi çekildikten sonra yanmaya devam ederken, kendi kendini söndüren plastikler bir süre sonra kendi kendilerine yanmayı durdururlar.
(Libaid-T 2)> PVC kablo kılıfı ve Yanma geciktiricili ve duman bastırıcılı (FRLS) compoundlar da kullanıma uygundur. Yüksek dolgu ( Kalsit, talk, ATH ) yüklemeli PVC kablo kılıfı kompoundlarında dolgu malzemelerinin daha iyi dağılımını sağlar.. Yüksek dolgulu PVC compoundun akış değerlerini artırır. Kablo yüzeyinde pürüzsüz parlak yapı. Yüksek dolgulu yada yanma geciktirici katkılı elastomerlerde etkili bir proses ajanıdır. Otomobil parçası uygulamalarında çok kullanılan PP/EPDM VE PE / EPDM karışımlarında kullanılan metal stearatlara oranla yarısı kadar kullanılarak vizkozitede düşürmede ve akış iyileştirmede çok daha faydalı olmaktadır. Ayrıca malzeme kalıplamasında çok iyi bir kalıp ayırıcı ajan özelliği gösterir. Toz halindeki bütün termoset kalıplama uygulamaları için uygun bir proses ajanıdır. PF, UF ve MF kalıplama kompoundların da katılan bütün katkıların çok iyi dispersiyonunu sağlar. Akış özelliklerini iyileştirir. Özellikle enjeksiyonluk ve yüksek akışkanlı çeşitlerinde kullanımda özellikle tavsiye edilir. Çok karmaşık kalıplar dahil, kalıbın uniform ve kısa sürede tamamının dolamsını sağlar.
Antibakteriyeller: Nem oranı yüksek coğrafi bölgelerde daha çok ürün yüzeyinde oluşabilecek yosunlaşmayı ve buna bağlı bakteri oluşumunun önüne geçer.
Antibloklar: Filmin üretimi sırasındaki bloklaşmayı engeller ve hafif kaydırıcı etki yapar. Yüksek verimde düzgün şekilli, eşit büyüklükte tanecikler oluşmasını sağlayarak akışkanlığı arttırır. Nemi minimuma indirerek balık gözü denilen yüzeydeki küçük delikli yapıların ve lens problemine bağlı oluşan sorunların önüne geçilmesini sağlar.
Antifoglar: Su moleküllerinin yüzey gerilimini artırarak, yüzeyde su damlacıklarının oluşmasını önler. AF katkısının faydalı ömrü; kullanıma, ortama ve iklim şartlarına bağlı olarak 12 ile 18 ay arasında değişebilir. Daha çok sera örtüsü iç yüzeyinde oluşan su damlacıklarının sebep olduğu, güneş yanığı veya mantar türü hastalıkların önüne geçilmesini sağlar, tarım ilaç tasarrufu ve kalite artışına destek olur.
Antigazlar / Nem Alıcılar: Nem; hem prosesi zorlaştırır hemde mekaniksel özelliklerinde zayıflığa sebep olurlar. Antigazlar ve nem alıcılar ısıl işlem esnasında plastiklerin bünyesinde var olan nemi ve gazları absorbe ederek daha homojen eriyik oluşumunu sağlar. Compound prosesinin en önemli problemlerinden biri nem olayıdır. Hem compound hem de compound sonrasında son ürün üreticilerinde etkisini gösterek hem prosesi zorlaştırır hemde mekaniksel özelliklerinde zayıflığa sebep olurlar.
Antistatikler: Plastik ürün üzerindeki statik elektrik oluşumunu engelleyerek, ortamdaki toz ve yabancı maddelerin ürün üzerine yapışmasını engeller.
(Libstat 95)> Yeni nesil, yüksek aktiviteli nitrojen içermeyen GMS içerikli Antistatik ajan ve lubrikanttır. Özellikle geniş çeşit yapısına sahip olan termoplastiklerden PP, PE, PVC gibi malzemeler de statik elektrik kontrolünde uygundur. Yapısı bakımından bitkisel ürünlerden yapıldığından gıda uygulamalarında kullanıma uygundur.
Esanslar: Plastiklerin var olan kokularını yada geri dönüşüm hammaddelerin kötü kokularını bastırmak için kullanılan katkılardır. Tropik, muz, çilek, gül vs. çeşitlilikte olabilirler. Daha çok %1, %2 oranları ile kullanılırlar ve kötü kokuyu bastırmak için tercih edilirler.
Genellikle ikinci kalite diye tabir edilen, daha önce bir kaç defa ürün olup buzulmuş hammaddelerin kullanımında ihtiyaç duyulurlar.
Infra Red Katkılar: Daha çok sera örtülerinde kullanılan bu katkı; güneşten gelen kızıl ötesi (IR) ışınların sera içine daha etkili ve kırılarak girmesini sağlar. Sera içinden radyasyon yolu ile ışının dışarıya kaçışını azaltır. Buna bağlı olarak da; gece-gündüz ısı farkını, bitki üzerindeki güneş yanıklarını,sera içerisinde don riskini azaltır, verim ve kalite artışı sağlar.
Şeffaflaştırıcılar: Polimerik bileşiğin moleküler yapısını düzenler ve puslu olabilecek görüntünün daha şeffaf ve ışık geçirgenliği daha fazla olacak şekilde olmasını sağlar.
Optik Parlatıcılar: Ürün renginin yetersiz olmasında, yüzey ışık yansımasını arttırarak daha parlak görünüm oluşmasını sağlar.
Optik Beyazlatıcılar: (TitanDiOksit)> Organik yapısı yüzey işlemleriyle silikon ve zirkon maddelerle zenginleştirilmiş, kararlı bir kimyasal yapıya sahip üründür. Beyazlığı, parlaklığı, örtücülüğü ve ezimi mükemmel olan, hava koşullarına, tebeşirlenme gibi etkenlere karşı çok iyi dayanım gösteren ve etki veren bir üründür. Suda çözünür.
(Zirtex OB-1)> Polyester fiber, naylon fiber, PP fiber beyazlatma uygulamalarında uygundur. Sert PVC, ABS, EVA, PS, PC gibi plastik uygulamalarda kullanıma uygundur. Polyester ve Naylon polimerizasyonlarında kullanıma uygundur. Su itici özelliğe sahiptir, suda çözünmez ancak ergime sıcaklığı yüksek olan parafin, mineral yağlar ve organik solventler de çözünebilir. Özellikle yüksek sıcaklıklarda işlenen plastiklerin prosesin de kullanıma uygundur.
Işık Yayıcılar: Daha çok LED aydınlatma ürünlerinde yaşanan ışık yayılımı sorunlarının giderilmesi için kullanılır. Işık geçirgenliğini arttırarak LED kullanım ihtiacını azaltır.
Dış Kaydırıcılar: Polimer molekülleri ile kovan/vida arasında meydana gelen sürtünmeyi ve yapışmayı azaltır. Verim artar, metal yüzeyler üzerinde aşınma azalır, sipariş geçişlerinde kovan/vida temizliği daha rahat olur, temizlik sarfı ve duruşu azalır.
(Çinko Stearat)> Plastik endüstrisinde PP, LLDPE, HDPE ve PS malzemelerde dış kaydırıcı, asit temizleyici, kalıp ayırıcı, proses ajanı olarak. Kauçuk ta proses ajanı kalıp ayırıcı olarak, sentetik ve polyester malzemelerde proses iyileştirici olarak, kullanılır.
(Lityum Stearat)> 200 °C üstü proses şartlarında her dış kaydırıcının bozunmadan performans göstermesi zordur. Lityum stearat lar bu yüksek sıcaklıklarda çalışabilen üstün performanslı bir dış kaydırıcıdır.
(PE Wax)> Dünya üzerinde en fazla kullanılan dispersiyon ajanı ve dış kaydırıcıdır. Neredeyse bütün compound ve masterbatch proseslerinin vazgeçilmez dispersiyon ajanıdır. Ancak burada malzeme saflığı ve kalitesi etkilidir.
(Libaid-T 2)> Çok iyi kalıp ayırıcı etki sağlar. Formulasyona PE wax ve metal sterarat gibi geleneksel kaydırıcıları katmanıza gerek kalmaz. Geleneksel kullanılan kaydırıcılara oranla daha az kullanım ve etkili sonuç verir.
İç Kaydırıcılar: Polimer moleküllerinin kendi aralarında olan sürtünmeyi azaltarak homojenizasyonu hızlandırır. Moleküler sürtünmenin düşmesiyle bileşik içindeki farklı polimeriklerin homojen bir yapı oluşturmasına yardımcı olur. Ancak farklı MFI değerlerinde istenilen sonuca ulaşılamayabilir. Ayrıca kaydırıcı katkının viskozitesi de burada önemlidir. ( Viskozite: Akışkan maddelerin akmaya karşı gösterdiği iç dirençtir. Matematiksel olarak viskozite değeri yüksek olan akışkanlardan, daha zor akar olduklarına kanı getirilir. Örnek olarak, süzme balın viskozitesi suyun vizkozitesinden yüksektir. Viskozite sıcaklıkla değişir. Temelde bir çok sıvının viskozitesi sıcaklık arttıkça azalır. Sıcaklık arttıkça moleküller arasındaki çekim kuvvetleri azalır ve moleküller daha serbest hareket eder hale gelir. Bu da akışkanlığı arttırır.
Ayrıca, bir çok sıvıda viskozite basınç arttıkça artar. )
(Kalsiyum Stearat)> Plastik ve kauçuk endüstrisinde iç kaydırıcı olarak kalıp ayırıcı ajan, asit temizleyici, elostomerlerde elestomer proses ajanı, PVC boru, fitting, ve siding üretiminde ekstruder basıncını düşürmek için proses ajanı olarak kullanılır. Bunun dışında kalsiyum stearatlar Poliolefinlerde içkaydırıcı görevi görerek topaklanmayı engelleyici olarak kullanılır.
(Libwax C - Amid Wax)> Yüksek sıcaklık ile işlenen, mühendislik plastiklerinde mükemmel bir kalıp ayırıcı ve dispersiyon sağlayıcıdır. Geleneksel kullanılan kaydırıcılardan çok daha yüksek bir ısı dayanımına sahiptir. Ayrıca geleneksel kaydırıcılardan %50 kadar daha az kullanılarak daha yüksek performans elde edilebilmektedir. Bütün termoplastik ve termosetlerde hem iç hemde dış kaydırıcı özelliği gösterir. Compound ve masterbatch proseslerinde; ABS ve PS malzemenin akış karakteristiğini artırır. İçinde pigment kullanılmış malzemelerde dispersiyon ajanı gibi görev yapar. Poliolefinlerde pigment dispersiyon sağlayıcı olarak kullanılabilir. Poliamidlerde içsel bir kalıp ayaırıcı ajan olarak çalışır. Acetal Plastiklerde kaydırıcı olarak ve kalıp ayırıcı ajan olarak kullanılır.
Pigment Islatıcılar: (Libnol-101)> Titanyum dioksit ve diğer inorganik pigment masterbatch uygulamalarında çok iyi ıslatıcı ve dispersiyon ajanı olarak kullanılır.
(Libnol–400)> Karbon siyahı ve bazı çok özel organik pigmentlerde gibi dispersiyonu güç olan pigmentlerle yapılan masterbatchlerde dispersiyon ajanı ve pigment ıslatıcı olarak kullanılır.
Koku Emiciler: Tüm polimerlerin ısıl işlem esnasında kimyasalların tepkimesiyle koku molekülleri serbest kalır. Bu da ortama koku hissiyatını verir. Koku emiciler, olası kötü kokulara ait koku moleküllerini adsorbe ederler.
Proses Aid / Proses İyileştiriciler: Polimerik bileşik ile kovan/vida arası sürtünmeyi azaltarak üretimi kolaylaştırır. Enerji tasarrufu sağlar. Film yüzeyinde pürüzlenmeyi önler. Proses iyileştirici olarak da adlandırılır.
(Libnol G–7481)> Compound ve masterbach proseslerindeki polymerlere yardımcı olan bir proses ajanıdır ve kesinlikle fiziksel özelliklerinde belirgin değişikliğe yol açmaz. Proses sırasında dolgu dispesiyonunu, akışı özelliklerini ve ayırıcı özelliklerini geliştirir. Düşük buharlaşma ve iyi termal stabiliteye sahip, ester tipi yüksek sıcaklıkta işlenen termoplastikler için mükemmel bir proses ajanıdır. PC, PET/PBT için kalıp ayırıcı ajandır.
(Libaid-T 2) > Multi Fonksiyonel Proses iyileştiricisidir. Özellikle yüksek Dolgu (kalsit, talk, ATH) ve yüksek pigment yüklemeli masterbatch ve compoundlarda pigment ve dolgu malzemelerinin uniform bir şekilde polimer matriksi içerisinde dağılmasını sağlayan multi fonksiyonel proses ajanıdır. Aynı zamanda çok iyi bir bağlayıcıdır. Bu yüzden dolgu ile polimer sistemi arasında iyi bir bağlayıcı olarak görev yapar. Compound yada masterbatch içine katılan katkıların homojen dağılımını ve dolguların ve pigmentlerin ana taşıyıcı polimere daha iyi bağlanmasını sağlar
Dolgulu compoundlarda; Akma sıcaklığını düzenler. Katkı ve dolgu (Kalsit, Talk, ATH) maddelerinde mükemmel dağılım sağlar. Kalıp çekme oranı indirgenir. Yüzey görünüşünü çok iyi yapar. TPE de dâhil birçok sistemde kalıptan ayrılma kolaylığı sağlar. Baskıda çiçeklenme özelliklerini engeller.
Masterbatch üretiminde; Bütün termoplastik olefinlerle uyumludur. Dispersiyonu zor olan organik ve inorganik pigmentlerde dağılımı düzenler. Masterbatchte yüksek pigment yüklemesi ile dağılımın düzenlenmesini sağlar. Granüllerde çok iyi bir yüzey kalitesi sağlar. Akış özelliklerini iyileştirir. Siyah masterbatch te dispersiyonu zor olan karbon siyahının taşıyıcı hammadde de iyi dispersiyonunu sağlar.
Slipler / Kayganlaştırıcılar: Film yüzeylerinin hem birbirine hem de metal yüzeylere yapışmasını engelleyerek kaydırıcı bir etki sağlar. İnce film çekilmesi ve film katlarının kolay açılmasına yardımcı olur. Düşük ısı ile verimlilik sağlar, film yüzey parlaklığı arttırır.
(Lutamid-P 98)> Yüksek saflığa sahip oleamid ajandır. Film katmanları arasında yada iki film arasında sürtünme oranını düşürerek birbiri üzerinden kaymasını sağlar. Matbaa mürekkeplerinde, kapak üretiminde, EVA kopolimerlerde, kauçuk kompoundlarda, kaplamalarda kalıp ayırıcı ajan olarak kullanılmaktadır.
(Libaid-T2 )> Kullanıldıktan sonra diğer geleneksel kaydırıcıların kullanılmasına gerek yoktur. TPE ve TPO compoundlarında, geleneksel kullanılankaydırıcılar ile karşılaştırıldığında daha iyi bir viskozite düşürücüdür.. Katılan dolguların çok ve diğer katkıların çok iyi dispersiyonunu sağlar.
Ultra Viole Katkılar: Dış mekan uygulamalarında kullanılan plastikler ciddi hava etkilerine maruz kalabilir. Bu uygulamalar genellikle, plastiklerin görünümlerine ve mekanik özelliklerine etki edebilen ultraviyole ışınlarının olumsuz etkisine dayanabilen hava koşullarına dayanıklı plastik malzemeye ihtiyaç duyar. Bu nedenle, UV radyasyon dış mekanda kullanılan ve dış mekan unsurlarına maruz kalan malzemeler üzerinde özellikle yüksek etkiye sahip olabildiğinden hava koşullarına dayanıklı plastiklerin bir şekilde UV dirençli özellikte olması genellikle akıllıca bir detaydır.
Bu stabilizör katkılar, düşük dalga boylu güneş ışınlarına karşı (UV) polimer zincirinin oksidasyonunu önler. Bu şekilde güneş ışınlarının zararlı etkilerinden ürünü korur, solmayı engeller, kullanım ömrünü uzatır.
Plastiklerin UV dayanımı genel olarak UV dengeleyiciler, siyah renklendirme (genellikle karbon siyahı kullanılarak) veya koruyucu yüzey kaplamaları (boya veya metal kaplama vb.) gibi katkı maddelerinin kullanımıyla elde edilir. Karbon siyahı katkısı düşük maliyetli ve genellikle çok etkili bir UV dirençli plastik oluşturma yöntemidir. Ek olarak PTFE ve PVDF gibi florlanmış polimerler natürel hallerinde oldukça iyi UV dengesi ortaya koyabilir. UV dirençli plastiklerde;
-
Plastiğin sararması gözlenmez
-
Boyalı plastiklerin sızdırması olmaz
-
Plastik yüzeyi beyazlaşmaz
-
Gerilim çatlağı oluşmaz
-
Kırılganlık gelişimi olmaz
-
Dayanım, esneklik ve sertlik azalması yaşanmaz.
Antiozonan Katkılar: ozon maruziyetinin oluşturduğu bitmiş ürünün bozulmasını yavaşlatmak için plastiğe eklenen malzemelerdir. Antiozonanlar Genellikle ürünün yüzeyine hareket ederek çalışır ve daha sonra yüzeyde bir ozon geçirmez bariyer oluşturur.
Şişirici Katkılar: Bazen kimyasal köpüren ajanlar da denir. Gazı, plastiğe veya reçineye ayırmak için kullanılırlar. Ağırlığı azaltmak, yumuşaklığı artırmak, izolasyon sağlamak, şok emilim özellikleri eklemek veya son üründe esneklik sağlamak için kullanılır.
Kaplin Maddeleri: Polimer ile fiziksel veya kimyasal etkileşimi teşvik ederler.
Plastikleştiriciler / Plastifiyanlar
Plastikleştiriciler nispeten uçucu olmayan organik maddelerdir (özellikle sıvılar). Bir plastik veya elastomere dahil edildiğinde, polimerin esnekliğine, işlenebilirliğine yardımcı olurlar.
Plastikleştiriciler, plastikleştirilmiş malzemenin temel kimyasal karakterini değiştirmeden polimer eriyiğinin viskozitesini, cam geçiş sıcaklığını (Tg), erime sıcaklığını (Tm) ve elastik modülünü azaltarak bir polimerin akışını ve termoplastikliğini arttırır.
Plastikleştiriciler, plastik endüstrisinde en yaygın kullanılan katkı maddeleri arasındadır. Bunlar ayrıca genellikle polimer işlemede kullanılan diğer katkı maddelerinden daha ucuzdur. Plastikleştiriciler çoğunlukla PP ve PE'den sonra hacim olarak üçüncü en büyük polimer olan PVC'de kullanılır. Buna karşılık, PVC geniş bir ürün yelpazesinde kullanılır.
Plastikleştiriciler, PVC (veya sert PVC) borular, dış cephe ve pencere profilleri gibi uygulamalarda, PVC (veya esnek PVC) otomotiv iç giydirme, kablolar, PVC filmler, döşeme, çatı ve duvar kaplamaları vb. alanlarda kullanılırlar. Bununla birlikte, akrilikler, PET, poliolefinler, poliüretanlar, vb. gibi polimerlerde de önemli miktarda plastikleştirici kullanılır. Plastikleştiriciler bazen kauçuklarda da kullanılır, ancak bu durumlarda amaç uzatıcı olmalarıdır.
Plastikleştirme prosesi, iç ve dış olarak iki temel başlık altında toplanır.
İç Plastikleştirme: Bir polimer, polimerin veya monomerin kimyasal olarak modifiye edilmesiyle dahili olarak plastikleştirilebilir, böylece esnekliği arttırılır. İstenen polimerin (yüksek Tg'ye sahip) ve plastikleştiricinin (düşük Tg'ye sahip) monomerlerinin kopolimerizasyonunu içerir, böylece plastikleştirici polimer zincirinin ayrılmaz bir parçası haline gelir. En yaygın kullanılan iç plastikleştirici monomerler: Vinil asetat, Viniliden klorürdür. Ayrıca, reaksiyonun karmaşıklığı daha uzun reaksiyon sürelerine ve artan maliyetlere yol açabilir.
Dahili plastikleştirilmiş malzemeler yüksek sıcaklıklarda sıcaklık bağımlılığı ve boyutsal kararsızlık gösterir.
Dış Plastikleştirme: Bu, en yaygın olarak kullanılan plastikleştirme yöntemidir çünkü düşük maliyetlidir. Sıvı plastikleştiricilerdir, bir ürün yelpazesi için formülasyon geliştirme konusunda formülatöre özgürlük verir (miktara bağlı olarak yarı sertlikten son derece esnekliğe).
En yaygın olarak kullanılan harici plastikleştiriciler, asitlerin veya asit anhidritlerin alkollerle reaksiyonundan oluşan esterleridir.
İki ana dış plastikleştirici grubu vardır:
1- Birincil plastikleştiriciler, polimerin uzamasını, yumuşaklığını ve esnekliğini arttırır. Polimerlerle son derece uyumludurlar ve büyük miktarlarda eklenebilirler.
Örneğin:% 50'ye kadar vinil eldivenler, PVC'yi giyecek kadar esnek ve yumuşak hale getiren plastikleştiriciler söz konusudur.
2- İkincil plastikleştirici , plastikleştirilmiş bir polimerde tipik olarak tek plastikleştirici olarak kullanılamayan bir plastikleştiricidir. İkincil plastikleştiriciler polimer ile sınırlı uyumluluğa ve / veya yüksek uçuculuğa sahip olabilir. Polimeri işlem sıcaklıklarında çözmelerine izin veren fonksiyonel gruplar içerebilir veya içermeyebilir.
İkincil plastikleştiriciler: maliyet azaltma, viskozite azalması, çalışma gücü geliştirme, yüzey yağlanmsının artırımı, düşük sıcaklıkta özellik iyileştirme amaçlarıyla tercih edilirler.
İkincil plastikleştiricilerin bir alt kümesi de uzatıcılardır. Genel amaçlı esnek PVC'nin maliyetlerini azaltmak için yaygın olarak birincil plastikleştiricilerle kullanılırlar. PVC ile sınırlı derecede uyumluluğu olan çoğunlukla düşük maliyetli yağlardır. Maliyeti azaltmak ve bazı durumlarda yangına dayanıklılığı artırmak için eklenirler. Tipik örnekleri arasında naftenik hidrokarbonlar, alifatik hidrokarbonlar, klorlu parafinler (yangına dayanıklılık) bulunur.
Plastikleştirici Kaybı / Eksüdasyonu : Polimer ve plastikleştirici arasındaki uyumsuzluk eksüdasyona neden olabilir. Plastikleştiricinin plastik yüzeyden (veya yakın temasta tutulduğu bir alt tabakaya veya içine) ısı değişimi, nem değişimi, mekanik stres, ayrışma gibi göç etmesine yol açabilecek çeşitli faktörler vardır. Plastikleştirici kaybı daha az esnekliğe, gevrekleşmeye ve çatlamaya neden olabilir.
Plastikleştiricilerin Sınıflandırılması : genellikle kimyasal bileşimlerine göre sınıflandırılır. Yapısal elementlerin (örn. Homolog bir ftalat serisi, adipatlar, vs. içindeki farklı alkoller) plastikleştiricilerin özellikleri ve bunların baz polimerleri üzerindeki etkisini anlamak mümkündür.
Farklı plastikleştiriciler malzemelerin farklı fiziksel ve kimyasal özelliklerini etkiler. Bu nedenle, gereksinimleri karşılamak için özellikleri belirli bir yönde değiştirmek için belirli bir plastikleştiriciye ihtiyaç olacaktır
Polimer modifikasyonu için kullanılan plastikleştiricilerin birkaç genel kimyasal ailesi vardır.
Bunlar arasında en yaygın olarak kullanılanlar:
Ftalat Esterleri : Ortoksilen veya naftalinin oksidasyonu ile elde edilen ftalik anhidrit veya ftalik asidin esterleştirilmesiyle üretilirler. En yaygın olarak kullanılan ftalat plastikleştiriciler şunları içerir:
DEHP: Düşük molekül ağırlıklı ortoftalat. Hala dünyanın en yaygın kullanılan PVC plastikleştiricisi
DINP, DIDP: Yüksek moleküler ağırlıklı orto-ftalatlar
Alifatik dibazik asit Esterleri : Bunlar arasında glutaratlar, adipatlar, azelatlar ve sebecatlar gibi kimyasallar bulunur. Adipik asit ve alkoller gibi alifatik dibazik asitlerden yapılırlar.
Benzoat Esterleri : Benzoik asit ve seçilmiş alkollerin veya diollerin esterleme ürünleridir.
Trimellitat Esterleri : Trimellitik anhidritin (TMA) ve tipik olarak C8 - C10 alkollerin esterleştirilmesiyle üretilirler
Poliesterler : Dikarboksilik asitler ve çift işlevli alkollerin birçok kombinasyonunun reaksiyonu ile oluşurlar.
Sitratlar : Bir mol sitrik asitin üç mol alkol ile reaksiyonundan kaynaklanan tetraesterlerdir. Sitrik asidin yalnız hidroksil grubu asetillenir.
Biyo bazlı Plastikleştiriciler : Epoksitlenmiş soya fasulyesi yağı (ESBO), epoksitlenmiş keten tohumu yağı (ELO), hint yağı, palmiye yağı, diğer bitkisel yağlar, nişastalar, şekerler vb.
Diğerleri : Fosfatlar, Klorlu Parafinler, Alkil Sülfonik Asit Esterleri ve daha fazlasını içerir.
Plastikleştiricilerin Uygulama Alanları : Termoplastik polimerlerde kullanılan plastikleştiricilerin% 90'ından fazlası PVC'de kullanılmaktadır. Plastikleştirilmiş polimer pazarı ve plastikleştirilmiş PVC pazarı büyük ölçüde aynıdır, ancak bazı plastikleştiriciler akrilik polimerler, poliüretanlar, polistiren hatta poliolefinlerde de kullanılır.
Başlıca son kullanımlar şunları içerir:
Film ve Kaplama : Esnek PVC film ve levhadan üretilen ürünler arasında çatı membranları, geomembranlar, döşeme, bagaj, reklam tabelaları, yüzme havuzu astarları ve diğerleri bulunur.
Döşeme : Esnek PVC döşeme ürünleri, esnek levha döşeme, vinil kompozisyon karosu, lüks vinil karo, vinil destekli halı karo içerir.
Tel ve Kablo : Esnek PVC, iyi işlenebilirlik ve kullanışlı bir servis sıcaklığı aralığına sahip iyi bir elektrik izolatörüdür, bu nedenle elektrik iletkenleri için yalıtım ve kılıflama, fiber optik kablolar için yalıtım gibi elektrik uygulamaları için mükemmel bir malzemedir.
Kaplamalı Kumaşlar : PVC sentetik kaplamalı kumaşlar hava koşullarına dayanıklıdır ve mükemmel mukavemet ve dayanıklılığa sahiptir. Mimarlık, yaşam tarzı, spor, reklam, savunma, madencilik, gıda ve tarım, otomobil ve taşımacılığı destekleyen endüstrilerde kullanılır. Ürünler arasında brandalar, çadırlar dış mekan mobilyaları.
Tüketim malları : Giyim, ayakkabı, ambalaj
Tıbbi : Kan torbaları, IV tüpleri, biyolojik tehlike içeren yapılar, diğer tıbbi cihazlar
PVC olmayanlar : Akrilikler, poliüretanlar, polistiren dahil diğer polimerlerde de az miktarda PVC tipi plastikleştiriciler kullanılır. Çoğu plastik PVC ürünleri dayanıklı ürünler, uzun ömürlü ürünlerdir. Ftalatlar, düşük uçuculukları, düşük su çözünürlükleri, güneş ışığına ve aşırı sıcaklıklara karşı iyi direnç, PVC polimer ile iyi uyum ve genellikle biyo-bozunmaya karşı iyi direnç nedeniyle bu tür ürünlerde kullanım için çok uygundur. Örneğin (Esnek PVC çatı kaplama membranları, Geomembranlar, Tel ve kablo yalıtımı). Bu son kullanımlarda ftalat plastikleştiricilerin değiştirilmesi çok zordur. Benzer şekilde, PVC polimeri için nispeten yüksek solvatlama gücü ve nispeten düşük viskoziteleri nedeniyle, ftalat plastikleştiricilerin esnek PVC bileşiklerinde ftalat değiştirmelerinin en azından bazılarına kıyasla daha kolay işlendiği bulunmuştur.
Antioksidantlar
"Antioksidanların görevini anlamak için oksidasyon hakkında temel bir miktar bilgiye ihtiyaç olduğu kesindir. Bu bağlamda, yaşamın en temel tepkimelerinden biri olan oksidasyon, en basit ifadesi ile elektronların bir atomdan diğerine akışından başka bir şey değil. Artı yükün artması (yükseltgenme), atomdan elektronun akıp gitmesiyle olur. Yani atomdan eksi yük azalıp, artı yük artması olayı. Oksijen doğada bulunan en önemli oksidanlardan biri. Yani ortamda oksijen olduğunda tüm elektronlar oksijene doğru akar. Oksidasyonun oksijene benzer bir kelime olması da zaten bu yüzdendir. Konunun en gözle görülür ve çabuk anlaşılır örneklemesi; Demirin paslanmasıdır. Ortamda oksijen varsa, elektronlar demirden oksijene doğru akarlar, böylece demir okside olur yani paslanır. Bu tepkime zincirleme olarak ve artarak devam eder. Ortamda bu aşırı reaktif oksidanları durduracak karşı güç yoksa ortalıkta sağlam molekül kalmayana kadar bu yok oluş devam eder. İşte antioksidanlar, bu karşı güçtür. Polimer zincirinden elektronların kopup, oksijen ile birleşme isteğini dururarak, polimer zincirin muhafazasına katkı sağlarlar."
Antioksidanlar, hem eriyik işleme sırasında oksidasyona karşı hem de ürünün yaşam döngüsü boyunca 'uzun süreli termal stabilizatör' olarak polimer koruması sağlamak için kullanılır . Polimerin hava koşulları ile bozulmasını geciktirir, kullanım ömrünü uzatır. Bu tür uzun vadeli termal stabilizatörler eriyik işleme stabilizatörlerinden farklıdır. Yani, polimer erime noktasının oldukça altındaki sıcaklıklarda işlev görmelidirler.
Termo-mekanik veya termo-oksidatif koşulların neden olduğu bozunmayı önlemek için plastiklere antioksidanlar eklenir. Antioksidanlar bir ürünün ömrünü uzatır, görünüşünü arttırır ve gücünü, sertliğini ve esnekliğini korur. Bu antioksidanların bozunma sürecini kesme şekli yapılarına göre değişir. Plastikler için antioksidanlar olarak çeşitli aminler, fenolikler, fosfitler, tioesterler vb. kullanılır.
(Richfos-168)> Bir çok polimerik malzemede proses sırasında oluşan yüksek ısılarda malzemenin bozunmasını engelleyerek ısı stabilizanı görevi görür. Düşük uçuculuk oranı sayesinde işlenen polimerin gerekli yüksek ısılarda ve zaman diliminde işlenmesini sağlar. PP, PE, PC, ABS ve polyesterlerde kullanıma uygundur
(Richbox-1010)> Uzun süreli yaşlanmalarda sırasında polimer bozulmalarına karşı özellikle etkilidir. Aynı zamanda, bir işlem stabilize edici olarak çok etkilidir. Termoplastik polimer işlemeleri ile karşılaşılan yüksek sıcaklıklarda renk değişimine iyi bir direnç sergiler. Düşük uçuculuğa sağlayan yüksek molekül ağırlıklı antioksidantdır.
(Richbox-1076)> Bir çok polimerik proses ve son kullanımda oluşacak oksidasyon degradasyonunu etkili bir şekilde önler. Anox PP 18, poliolefinler, darbe dayanımlı stirenikler, block copolymerler, elastomerler, PVC ve Poliüretenlarda mükemmel bir stabilizatördür.
(Richnox-1098)> Uzun süreli yaşlanmalarda sırasında polimer bozulmalarına karşı stabilizasyon özelliği sağlayan fenolik antioksidandır. Özellikle PA compound, masterbatch, parça üretimlerinde karşılaşılan yüksek sıcaklıklarda renk değişimine iyi bir direnç sergiler.
Polyacetals, polyesters, polyurethanes, adhesives, elastomers ürünlerde de kullanılabilmektedir.

Ftalatlar
Tipik olarak ortoksilenin oksidasyonu ile elde edilen ftalik anhidridin esterleştirilmesiyle üretilir. Ftalatlar hafif bir kokuyla neredeyse renksiz görünür. Suda çözünürlükleri sınırlıdır, ancak organik çözücülerin çoğunda (mineral yağ vb.) karışabilirler.
-
Ekstraksiyon, buharlaşma ve göçe karşı koydukları için geleneksel bir seçimdir.
-
Ftalatlar dayanıklılık, esneklik, hava koşullarına dayanıklılık sunar ve yüksek sıcaklıklara dayanabilir
-
Ftalatlar diğer plastikleştiricilere kıyasla ekonomiktir
-
PVC gibi polimerlerde, ftalatlar kimyasal olarak bağlanmaz ve plastiklerden süzülür, bu da çevrede meydana gelmelerine neden olur
-
Bazı ftalat plastikleştiriciler, kanserojenler ve / veya gelişimsel toksinler oldukları için sağlık için ciddi riskler oluşturabilirler
-
Bazı ftalatlar insan vücudunda düşük seviyelerde birikebilir.