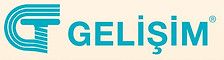


Hidrokarbonlar
Hidrojen ve karbon olmak üzere iki elementten oluşan organik bir bileşiktir. Petrol bileşiminin büyük bir kısmı değişen uzunluklardaki hidrokarbonlardan oluşur.
En küçük hidrokarbon metan, tek bir karbon atomu ve dört hidrojen atomundan oluşur. Bununla birlikte, hidrokarbonlar, zincirler, daireler ve diğer karmaşık şekiller dahil olmak üzere birçok yönden birbirine bağlanmış yüzlerce veya binlerce bireysel atomdan oluşabilir.
Hidrokarbonların özelliklerini sınıflandırmak için birkaç temel türe ayrılırlar.
Alkanlar: Bunlar doymuş hidrokarbonlar olarak adlandırılır. Yani sadece tüm karbon atomları arasında tek bağlar içerirler. Alkanlar, petrol yakıtlarının temelidir ve doğrusal ve dallı formlarda bulunurlar.
Doymamış Hidrokarbonlar: Karbon atomları arasında bir veya daha fazla çift bağa sahip olan hidrokarbonlara alken denir.
Sikloalkanlar: Bir veya daha fazla halka yapısı içeren herhangi bir hidrokarbon.
Aromatik Hidrokarbonlar: Areneler olarak da adlandırılan aromatik hidrokarbonlar, karbon atomlarının birbirini izleyen çift ve tek bağlarla bağlandığı benzersiz bir karbon molekülleri sınıfıdır. Bu molekül sınıfı, karbon atomları arasındaki bağların tek ve çift bağlar arasında bir ara bağ olduğu özel halka yapılarına sahiptir.
Bu sınıftaki moleküller, endüstriyel çözücü «benzen» içerir.
Benzen (C6H6): Diğer hidrokarbonlar gibi benzen de petrolün doğal bir bileşenidir. Oda sıcaklığında renksiz, yanıcı, tatlı kokulu bir sıvıdır ve yüksek oktan sayısına sahip olduğu için çoğu benzin karışımının bir bileşenidir.
Benzen de oldukça kanserojendir ve kemik iliği yetmezliği ve kemik kanserine neden olduğu iyi bilinmektedir. Elbette, “hoş aroması” nedeniyle tıraş sonrası ve diğer kozmetiklerde bir katkı maddesi olarak kullanıldığında kanserojenliği iyi bilinmemektedir.
En büyük benzen kullanımı (% 50), stiren ve polistren plastiklerinin ürünüdür. Ayrıca Naylon üretiminde önemli olan sikloheksan olarak bilinen bir moleküle dönüştürülür. Siklohekzan üretmek için benzenin yaklaşık% 15'i kullanılır. Böcek ilaçlarından kauçuğa kadar her şeyde daha küçük miktarlar kullanılır.
Benzen yapısı iki şekilde çizilebilir. İlkinde, çift bağ karakteri açıkça çizilir. Kısa elli versiyonda, yapıyı göstermek için halkanın içine bir daire çizilir. Benzen içindeki her bir karbon atomuna bağlı tek bir hidrojen vardır.
Aşağıdaki I. ve II. çizimleri eştir. Pratikte III. çizim kullanılır.
Benzen, renksiz, alevlenebilen, kaynama noktası 80,1 °C, erime noktası 5,5 °C olan bir sıvıdır.
Binükleer Aromatik Hidrokarbonlar: Molekülünde iki benzen halkası içeren bileşiklerdir.
Hidrokarbonlar
Hidrojen ve karbon olmak üzere iki elementten oluşan organik bir bileşiktir. Petrol bileşiminin büyük bir kısmı değişen uzunluklardaki hidrokarbonlardan oluşur.
En küçük hidrokarbon metan, tek bir karbon atomu ve dört hidrojen atomundan oluşur. Bununla birlikte, hidrokarbonlar, zincirler, daireler ve diğer karmaşık şekiller dahil olmak üzere birçok yönden birbirine bağlanmış yüzlerce veya binlerce bireysel atomdan oluşabilir.
Hidrokarbonların özelliklerini sınıflandırmak için birkaç temel türe ayrılırlar.
Alkanlar: Bunlar doymuş hidrokarbonlar olarak adlandırılır. Yani sadece tüm karbon atomları arasında tek bağlar içerirler. Alkanlar, petrol yakıtlarının temelidir ve doğrusal ve dallı formlarda bulunurlar.
Doymamış Hidrokarbonlar: Karbon atomları arasında bir veya daha fazla çift bağa sahip olan hidrokarbonlara alken denir.
Sikloalkanlar: Bir veya daha fazla halka yapısı içeren herhangi bir hidrokarbon.
Aromatik Hidrokarbonlar: Areneler olarak da adlandırılan aromatik hidrokarbonlar, karbon atomlarının birbirini izleyen çift ve tek bağlarla bağlandığı benzersiz bir karbon molekülleri sınıfıdır. Bu molekül sınıfı, karbon atomları arasındaki bağların tek ve çift bağlar arasında bir ara bağ olduğu özel halka yapılarına sahiptir.
Bu sınıftaki moleküller, endüstriyel çözücü «benzen» içerir.
Benzen (C6H6): Diğer hidrokarbonlar gibi benzen de petrolün doğal bir bileşenidir. Oda sıcaklığında renksiz, yanıcı, tatlı kokulu bir sıvıdır ve yüksek oktan sayısına sahip olduğu için çoğu benzin karışımının bir bileşenidir.
Benzen de oldukça kanserojendir ve kemik iliği yetmezliği ve kemik kanserine neden olduğu iyi bilinmektedir. Elbette, “hoş aroması” nedeniyle tıraş sonrası ve diğer kozmetiklerde bir katkı maddesi olarak kullanıldığında kanserojenliği iyi bilinmemektedir.
En büyük benzen kullanımı (% 50), stiren ve polistren plastiklerinin ürünüdür. Ayrıca Naylon üretiminde önemli olan sikloheksan olarak bilinen bir moleküle dönüştürülür. Siklohekzan üretmek için benzenin yaklaşık% 15'i kullanılır. Böcek ilaçlarından kauçuğa kadar her şeyde daha küçük miktarlar kullanılır.
Benzen yapısı iki şekilde çizilebilir. İlkinde, çift bağ karakteri açıkça çizilir. Kısa elli versiyonda, yapıyı göstermek için halkanın içine bir daire çizilir. Benzen içindeki her bir karbon atomuna bağlı tek bir hidrojen vardır.
Aşağıdaki I. ve II. çizimleri eştir. Pratikte III. çizim kullanılır.
Benzen, renksiz, alevlenebilen, kaynama noktası 80,1 °C, erime noktası 5,5 °C olan bir sıvıdır.
Binükleer Aromatik Hidrokarbonlar: Molekülünde iki benzen halkası içeren bileşiklerdir.
Hakkında
Kyäni, faydalı bileşenlerden oluşan besin takviyesi ürünlerini; benzersiz iş fırsatıyla birlikte dünya çapında 50'den fazla ülkeye ulaştırmaktadır. İdeal sağlığımızı korumak için günlük olarak Kyäni ürünlerini kullanırız, bu ürünleri başkalarıyla paylaşırız, işimizi inşa etmek ve sürdürmek için neredeyse her gün belirli bir saatimizi işe adarız ve başkalarını da Kyäni fırsatına dahil ederek veya Potato Pak ve Caring Hands programlarına katkı sağlayarak başarımızı başkalarıyla paylaşırız.
Hakkında
Kyäni, faydalı bileşenlerden oluşan besin takviyesi ürünlerini; benzersiz iş fırsatıyla birlikte dünya çapında 50'den fazla ülkeye ulaştırmaktadır. İdeal sağlığımızı korumak için günlük olarak Kyäni ürünlerini kullanırız, bu ürünleri başkalarıyla paylaşırız, işimizi inşa etmek ve sürdürmek için neredeyse her gün belirli bir saatimizi işe adarız ve başkalarını da Kyäni fırsatına dahil ederek veya Potato Pak ve Caring Hands programlarına katkı sağlayarak başarımızı başkalarıyla paylaşırız.
Sayfa Yapım Aşamasındadır.
Sayfa Yapım Aşamasındadır.
Schulungs- / Wissens- / Lösungsplattform
Füllstoffe
Das Hauptziel bei Füllmaterialien, die in Polymeren enthalten sind, ist wirtschaftlich.
Daneben jedoch gefüllte Materialien; Sie tragen auch charakteristische Merkmale wie spezifisches Gewicht, Druckfestigkeit, Biegefestigkeit, Härte und Hitzebeständigkeit. Einige spezielle Additive verleihen dem System Vorteile wie Antistatik und Nichtbrennbarkeit sowie Weichheit und Gleitfähigkeit, was die Verarbeitung erleichtert.
Füllstoffe verhindern das Schrumpfen des Materials bei Kunststoffen. Zugfestigkeit und Schlagzähigkeit verschlechtern sich jedoch mit Füllstoffen. Zur Korrektur sind unbedingt spezielle Zusätze erforderlich. Die Pads ändern die Prozess-Rendering-Werte.
Die wichtigsten Aspekte, die bei der Auswahl von Füllstoffen zu berücksichtigen sind, lassen sich wie folgt auflisten. Partikelgrößenverteilungsmuster, Dispersionsmerkmal, chemische Struktur, Oberflächenstruktur und -größe, Katalysatorwirkung der Oberfläche, Abriebgefahr, Dichte, Oberflächenhärte, Transportart, Gesundheitsgefährdung, Preis.
Der wichtigste Punkt bei der Verwendung von Füllstoffen ist, dass sie sich sehr gut mit der Matrix vermischen. Dadurch wird ein optimaler Kontakt der Matrix mit dem Füllstoff und die höchste Verteilung auf den Partikeln erreicht. Füllstoffe verhindern, dass sich die Kettenmoleküle verbinden, indem sie das Volumen füllen. Durch die seitlichen Bindungen, die zwischen dem Füllstoffpartikel und der Matrix entstehen, kann das Material eine zähere und steifere Struktur aufweisen.
Dieses Phänomen erklärt die Erhöhung der Glastemperatur vieler Kunststoffmaterialien mit der Füllung.
Gefüllter Kunststoff:
Der wichtigste Unterschied zu verstärkten Kunststoffen besteht darin, dass die Zugfestigkeit nur bei verstärkten Kunststoffen ansteigt. Andererseits nimmt die Härte mit Füllstoffen zu. Die Hitzebeständigkeit steigt bei kugelförmigen Füllungen nicht so stark wie bei Faserverstärkungsmaterialien. Andererseits kann die Zugabe von Talkum und Glimmer, die in Form von flachen Partikeln vorliegen, hinsichtlich der Hitzebeständigkeit viel effektiver sein.
Verstärkte Kunststoffe weisen außerordentliche Steigerungen der mechanischen Werte auf.
Bei gefüllten Kunststoffen kommt es zu einer Abnahme oder Invarianz der Wärmeeinwirkung auf die mechanischen Werte.
Abgesehen davon treten bei gefüllten Kunststoffen folgende positive Veränderungen auf;
Dichte-, Kompressions- und Biegewerte steigen.
Oberflächenhärte und -qualität werden verbessert.
Die Produktionskosten sinken.
Die Verarbeitung von Kunststoff wird einfacher.
Die Druck- und Formzeit wird verkürzt.
Es wird ein härteres Produkt erhalten.
Es wird widerstandsfähiger gegen Hitze sein.
Das Kollapsproblem wird reduziert.
Das Kriechproblem ist beseitigt.
Die Neigung zur Unterlast wird reduziert.
Biege- und Schlagwerte werden verbessert.
Dinge zu beachten:
Eignung der Partikelgrößenverteilung, katalytische Wirkung, die Notwendigkeit, sich sehr gut mit der Matrix für eine homogene Struktur zu vermischen, damit die Maschinen und Geräte korrodiert werden. Wenn nicht bewusst gearbeitet wird, können statt der gewünschten Vorteile große Probleme auftreten.
Talkum und Glimmer, die in Form einer Platte vorliegen, werden ebenso wie Calcit bevorzugt, da sie dem Material Zähigkeit und Oberflächenglätte verleihen.
Übermäßiger Anstieg der Ölpreise, die Quelle des Öls Dadurch werden die Kunststoffmaterialien, die in Kunststoffen verwendet werden, teurer und die Billigkeit von Füllstoffen gewinnt noch mehr an Bedeutung. Mit neuen Forschungs- und Entwicklungsanstrengungen werden Füllarten und deren Verträglichkeit mit Kunststoffen untersucht und Lösungen mit höheren Füllgraden gesucht.

Talk
Es ist ein hydratisiertes Magnesiumsilikat und ein sehr weiches Mineral. Talk ist ein festes metamorphes Mineral. Sein vollständiger wissenschaftlicher Name ist hydratisiertes Magnesiumsilikat und seine chemische Formel ist Mg 3 Si 4 O 10 (OH) 2. In der Natur findet man Talkum normalerweise in einem Stein namens Steatit oder Speckstein (Gestein mit hohem Talkum), oft kombiniert mit anderen Mineralien wie Chlorid und Karbonat. Talk ist normalerweise blau, weiß, grau, braun oder farblos. Talk wird auch als "Weichstein" bezeichnet. Dieser Stein hat, wie der Name schon sagt, eine besondere Weichheit, die oft in der Bildhauerei verwendet wird.
Mittelweich (Talk hat die geringste Härte im Vergleich zu anderen Mineralien in der Natur)
Sehr glatt, fühlt sich an wie Seife
Es hat eine gute elektrische Isolierung, gute Isolierung, einen hohen Schmelzpunkt, niedrige Wärmeausdehnungswerte
Stärke mit organischen Substanzen ist eine inerte Chemikalie (Kombinationsfähigkeit mit organischen Substanzen)
In der Kunststoffindustrie wird Talk von den Masterbatch-Herstellern häufig zur Herstellung von Füllstoff-Masterbatch verwendet. Als hochprozentiger Inhaltsstoff in Kunststofffüllstoffen erhöht Talk die Härte verschiedener Basisharze wie Polypropylen, Vinyl, Kunststoff, Nylon und Polyester. Es wirkt auch als Antihaft-, Frostschutz-, Schmiermittel, Weichmacher usw. kann auch als
Plastik, Kosmetik, Papier etc. In verschiedenen Industrien wird Talk zu weißem Pulver gemahlen und mit anderen Verbindungen vermischt, daher wird es als Talkumpuder bezeichnet.
Bei Verwendung in duroplastischen Harzsystemen;
Es bietet elektrische Isolierung und Hitze- und Feuchtigkeitsbeständigkeit.
Das System mit Talkum-Füllmaterial lässt sich leicht maschinell verarbeiten.
Es kann als Füllstoff in platten- und pastenfertigen Formmassen verwendet werden.
Es bietet ein gutes Gleichgewicht zwischen Steifigkeit und Schlagfestigkeit des Produkts.
Es hat eine dünne Schichtstruktur, die aus Schichten von Magnesiumhydroxid besteht.
Wird dem Polyethylen Talkum zugesetzt, bleiben die mechanischen Eigenschaften über einen weiten Temperaturbereich unverändert und die elektrischen Eigenschaften werden deutlich verbessert.
Die Zugfestigkeit steigt stärker als bei anderen Additiven.
Es ist der am häufigsten verwendete Füllstoff bei PP. Talkum ist aufgrund seiner laminaren Struktur einer der wichtigsten Füllstoffe, der bei Wärme die Umformtemperatur erhöht und die Dimensionsstabilität erhöht. Neben der Kostenreduzierung durch Calcitzugabe ist es möglich, Materialien mit geringerer Wandstärke herzustellen, da hierdurch die Flexibilität des Materials stark reduziert wird.
Andererseits nimmt bei der Verwendung von Talkum die Schlagzähigkeit bei niedriger Temperatur ab, die Zugfestigkeit nimmt ab, die Oberflächen werden stumpf und die Wärmezersetzung wird nachteilig beeinflusst.
Talkumpuder: Es wird hauptsächlich aus Talkum hergestellt, einem Mineral, das aus den Elementen Magnesium, Silizium und Sauerstoff besteht. Als Pulver nimmt es Feuchtigkeit gut auf und hilft, die Reibung zu reduzieren.
Bei steigenden Preisen und angeschlagener Wirtschaft ist der Einsatz von Füllstoffen für Kunststoffe in der Kunststoffproduktion eine effektive Lösung, da Hersteller große Mengen an Inputmaterial und damit Produktkosten sparen können. Darüber hinaus verkürzt der Einsatz von Füllstoff-Masterbatch in der Produktion die Verarbeitungszeit, so dass die Produktionskapazität eine optimale Effizienz erreichen kann.
Talkumfüller-Masterbatch: Talkumpulver, Basisharz (PP, PE, HD, HIPS etc.) und Dispergiermitteladditive, Binderadditive etc. Es ist eine Mischung aus verschiedenen Zusatzstoffen wie
Bedeutung der Verwendung von Talkum: Es gilt als der perfekte Füllstoff für Kunststoffe und hilft dem Masterbatch-Hersteller, die Produktivität zu steigern und gleichzeitig die Produktionskosten zu senken. Ein Teil des Primärkunststoffs (Inputmaterial zur Herstellung kunststoffbasierter Produkte) kann durch Talkumpuder enthaltendes Kunststoff-Masterbatch ersetzt werden. Dies ist eine intelligente Lösung, die darauf abzielt, Rohstoffe zu sparen und gleichzeitig die Menge an Rohöl zu begrenzen. Die Ressourcen in der Kunststoffproduktion werden knapp. Ein weiterer wichtiger Effekt ist, dass Talkumfüller die Kunststoffeigenschaften stark verbessert und Produkten mit Kunststoffausgängen zu einem höheren Wert auf dem Verbrauchermarkt verhilft.
Erhöht die Hitzebeständigkeit von Kunststoffen
Helfen Sie Kunststoffprodukten, die Abrieb- und Rutschfestigkeit zu erhöhen, wenn sie mit den Oberflächen anderer Produkte in Kontakt kommen
Reduziert die Kunststoffschrumpfung, hilft beim Formen und Fixieren von Produktabmessungen
Verbessern Sie die Druckeigenschaften auf der Materialoberfläche, begrenzen Sie die Oberflächenbehandlung mit Corona.
Erhöht die Haltbarkeit von Kunststoff
Antiblocking-Kunststoff glättet die Oberfläche ohne Verwendung von Antiblocking-Additiven (erhöht die Antiblocking-Eigenschaft)
Talkumfüller-Masterbatch ist bei Masterbatch-Herstellern sehr beliebt, da es beim Beutelblasen, Spritzgießen, Extrudieren, Formpressen usw. weit verbreitet ist. Es eignet sich für den Einsatz in den meisten traditionellen Herstellungsprozessen, beispielsweise ohne die Notwendigkeit, Geräte oder Fertigungstechnologie aufzurüsten oder zu ersetzen. Talkumpuderhaltige Talkumfüller eignen sich für alle Arten von Verpackungen (Einkaufstüten, Brottüten, Mülltüten, Flaschen, Lebensmittelbehälter etc.), Hohltuben, Teller, Elektrokappen, Schüsseln, Teller etc. Um es herzustellen, muss es die Verarbeitungsstufen durchlaufen.
Vorsicht bei der Verwendung von Talk: Berichten zufolge ist die Inzidenz von Lungenkrebs und Atemwegserkrankungen bei Talkbergarbeitern aufgrund der Exposition gegenüber siliciumdioxid- und asbesthaltigem industriellem Talkstaub, der gesundheitsgefährdend ist, sehr hoch. Ein weiteres Problem ist, dass Talkumpuder wegen seiner guten Feuchtigkeitsaufnahmeeigenschaften in kosmetischen Pudern sehr beliebt ist. Dies stellt eine Gefahr für Babys oder Frauen dar, die große Mengen Talkumpuder einatmen.
Derzeit gibt es jedoch keine eindeutigen Hinweise darauf, dass die Verwendung oder Inhalation von Talkumpuder das Krebsrisiko erhöht. Daten zum Zusammenhang zwischen Talkumpuder und Lungenkrebsfällen sind noch rar. Hersteller von Talkfüller-Masterbatch sollten jedoch dennoch vorsichtig sein, wenn sie dieses Material in der Produktion verwenden.
Kaolin
Kaolin oder Kaolin ist eine Art von Ton, der aus Granitfelsen gewonnen wird. Es wird zur Herstellung von Keramik und Porzellan verwendet. In der Türkei auch als Bienenton bekannt. Es ist ein weißer und weicher Bodentyp. Granitgesteine enthalten Feldspatminerale.
Seine Grundzusammensetzung ist Aluminiumsilikat. Auch andere Metallatome sind darin enthalten. Kaolin wird normalerweise als Füllstoff in duroplastischen Harzsystemen verwendet und ist ein feines weißes Pulver. Es kann verwendet werden, wenn aufgrund seiner Haftung glatte, sehr glänzende Oberflächen erforderlich sind. Extrem fein, kann es auch als Additiv zur Ablaufkontrolle verwendet werden. Kalziniertes Kaolin kann verwendet werden, wenn überlegene elektrische Eigenschaften erforderlich sind.
Kaolin, einer der unverzichtbaren Füllstoffe der Lackindustrie; Es ist ein natürlicher Tonrohstoff, der Ca und Na enthält.
Es ist ein Rohstoff, der durch das Mineral Kaolinit gekennzeichnet ist. In industriellen Anwendungen wird „kalziniertes“ Kaolin verwendet.
Kalziniertes Kaolin: Wenn das Kaolin aus der Natur gewonnen wird, ist es nicht so rein wie gewünscht. Es enthält auch unerwünschte Strukturen und Wasser. Diese Verunreinigungen und etwas Wasser im Kaolin werden durch das Kalzinierungsverfahren aus dem Kaolin gereinigt. Kalzinierungsprozess zu diesem Prozess, Kaolin nach der Verarbeitung; Es wird kalziniertes Kaolin genannt. Kaolin durch Kalzinierungsverfahren; gewinnt überlegene optische und physikalische Eigenschaften.
Kalzinierung: Kalzinieren bedeutet Vorkochen. Es ist der Prozess des Erhitzens des Materials auf eine bestimmte Temperatur (ein Prozess von 900°C - 1100°C) und das Abkühlen nach einer bestimmten Wartezeit. Die Materialien werden kalziniert, um Kristall- und chemisches Wasser zu entfernen, die Kristallstruktur des Rohmaterials zu verändern, die Härte des Rohmaterials zu reduzieren und somit eine leichte Mahlung zu ermöglichen.
Materialdurchmesser, Verarbeitungszeit, Temperatur und atmosphärischer CO2-Druck sind bei der Kalzinierung sehr wichtig. Kalzinierung Ein Korn mit 2,5 cm Durchmesser wird in etwa 1 Stunde kalziniert. Mit zunehmender Schichtdicke wird der Wärmeeintrag ins Innere erschwert.
Der Zweck des Kalzinierens;
1) Entfernung von Kristall- und Chemiewasser (Kalzinieren von Tonen und Talk in Bauxit).
2) Ändern der Kristallstruktur des Rohstoffs.
3) Reduzierung der Härte des Rohmaterials und dadurch leichte Mahlbarkeit (Kalzinieren von Quarz)
Es gibt zwei Hauptanwendungen des Kalzinierungsverfahrens.
1) Kalzinierung angewendet auf Carbonate, Sulfide, Hydrate (Substanzen wie SO2, CO, CO2 werden aus Verbindungen wie Carbonatsulfat entfernt. Natronkalkglas enthält 72 % SiO2, 14 % Na2o, 14 % CaO. Wenn sich diese beiden letzten Verbindungen Na2O und CaO verbinden, entstehen Colamanit und Borax) .
2) Während der Kalzinierung (Kalkstein (CaCO3), der auf das Zerkleinern und Mahlen von Rohstoffen aufgetragen wird, findet eine Zersetzung statt, während sie allmählich von der Oberfläche zur inneren Oberfläche des Minerals fortschreitet.
Es gibt verschiedene Faktoren, die die Zerfallsreaktion von Kalkstein unter Wärmeeinwirkung beeinflussen. Diese Faktoren werden im Allgemeinen durch die kinetischen und physikalischen Übertragungsereignisse bewertet, die in dem Ofen, in dem die Reaktion stattfindet, auftreten. Wenn beispielsweise die Korngröße des Minerals zunimmt, wird der Fragmentierungsprozess schwieriger. Daher ist ein längerer Kalzinierprozess erforderlich. Außerdem beeinflusst die größere Partikelgröße die Wärmeverteilung im Ofen. Kleine Partikel setzen sich in den von großen Partikeln gebildeten Räumen ab, wodurch die Verbrennungsflamme und der Gasfluss im Ofen verhindert werden. Temperaturen, die es ermöglichen, kleine Partikel ohne übermäßige Verbrennung zu kalzinieren, stellen sicher, dass nur der Schalenteil großer Partikel kalziniert werden kann. Folglich wird das Kalzinieren unabhängig von der Partikelgröße einfacher, wenn eine kontrollierte Partikelgrößenverteilung erreicht wird.
Die Kalzinierung von Kalkstein erfolgt in industriellen Anwendungen in verschiedenen Öfen. Vertikalöfen werden für grobkörnige Kalksteine verwendet, während Drehrohröfen für feinkörnige Kalksteine verwendet werden. Wirbelschichtöfen können für feinkörnige Kalksteine mit gleichmäßiger Kornverteilung verwendet werden. Kalzinierungsöfen; kann mit allen festen, flüssigen und gasförmigen Brennstoffen beheizt werden).
Kaolin-Einsatzgebiete:
Petroleum-Industrie : Es wird als Katalyse bei der katalytischen Umwandlung von Erdölprodukten verwendet, insbesondere in Erdölraffinerien. Viele Katalyse arbeiten unter hoher Temperatur und hohem Druck. Daher sind Kaoline für Hochtemperaturbedingungen geeignet. Talk oder Sepiolith bei der Herstellung von Katalysatoren (Cordiorit) und Kaolin-Mischung verwendet wird.
Kunststoffindustrie: Es wird insbesondere in Vinylen und Polyestern häufig als Verstärkungs- und Kostensenkungs- und Zusatzmaterial verwendet. Das wichtigste Kaolin Nutzungsbereich; (PVC) beschichtete Drähte und Kabel. Kalziniertes Kaolin und oberflächenmodifizierte Silikatkaoline werden verwendet, um den elektrischen Widerstand von PVCs zu erhöhen, da sie hydrophobe Eigenschaften haben.
Reifenindustrie: Kostenreduzierendes Additivmaterial und am häufigsten als Booster verwendet Die durchschnittliche Korngröße von Hartkaolin beträgt 0,2 µm' und weiche Kaoline haben eine durchschnittliche Korngröße von weniger als 1,0 µm. Der pH-Wert des gewünschten Kaolins in der Gummiindustrie in Wasser liegt zwischen 4,5 und 5,5.Auch Fe,Mn und Elemente wie Cu in sehr niedrigen Grenzen liegen.
Lackindustrie: Kaolin wird zusammen mit Titanoxid (anorganischem Pigment), gemahlenem Calcitpulver und Talkum in wasserbasierten Innen- und Außenfarben oder in Industrielacken verwendet. Die Kosten werden verbessert, indem der Einsatz von Titanoxid reduziert wird. Wasserbasierter Innenkunststoff und Latex kalzinierte und nicht laminierte Mineralstruktur Kaoline verwendet. in dieser Gruppe Farben enthalten zwischen 50% und 70% Pigment. 98% des in seidenmatten und glänzenden Wasserlacken verwendeten Kaolins sind größer als 2 µm. In Latexfarben wird zusammen mit Pigmenten, Bindeharzen Kaolin verwendet, das eine bessere Deckkraft bietet und einen Brechungsindexwert nahe dem Brechungsindex des Bindemittels (>1,50) hat.
Tintenherstellung: Kaolin wird in hochdichten Tinten mit dünnen Filmen in Lithografie-, Offset- und Flexodrucktechniken verwendet. Der Farbfilm reicht von 5 bis 15 µm und wird zusammen mit einem feinkörnigen Kaolin (0,2-0,5 µm) Farbpigment verwendet, um den Glanz zu erhalten.
Im Isolierbereich: Kaolinlatex-Natriumsilikatwand Es wird in Papierklebstoffen, Gipsplatten, Klebstoffen auf Wasserbasis und Klebstoffen auf Epoxidbasis verwendet, um eine bessere Viskosität, eine einfache Anwendung und ein leichtes Verteilen zu erreichen.
Pharmazeutische Industrie: Kaolin wird aufgrund seiner Adsorptionseigenschaften in einigen Medikamenten verwendet. In Zahnpasten wird kalziniertes Kaolin (90 % weniger als 2 µm) verwendet. Darüber hinaus wird Kaolin in Auto- und Metallpolituren sowie zur Reinigung oxidierter Oberflächen verwendet. Kaolin, das in diesem Sektor verwendet wird maximal 2 ppm Arsen und maximal 20 ppm Schwermetalle sind erforderlich.
Glasfaserherstellung: Es wird zur Wärmedämmung und Verstärkung von Kunststoffen verwendet. Die wichtigsten Rohstoffe für Glasfasern sind Kieselsäure, Kaolin und Kalkstein. Borsäure, Soda und Natriumsulfat. Bei Aluminiumfenstern Es senkt die Schmelztemperatur, verhindert das Auskristallisieren und verringert die Löslichkeit in Wasser und anderen Chemikalien. Glasfaserproduktion Für das gewünschte Kaolin sollten 37 % Al2O3 44 % SiO2 maximal 1 % Fe2O3 2 % Na2O und 1 % H2O sein.
Papierindustrie: Bei der Suche nach 90-100% reinem Kaolinitmineral sollte es kein Quarzmineral enthalten. Außerdem beträgt die Helligkeit mindestens 85%, Korngröße 80% < 2 µm und Brookfield-Viskosität < 7.000 cps.
Keramikindustrie: Allgemein Kaoline, die 75-80% Kaolinitmineralien enthalten, werden bevorzugt. Brennfarbe, Viskosität, Reibungswiderstand, sehr niedrige Fe2O3- und TiO2-Verhältnisse und % Eine Helligkeit von 83-91 Prozent ist erwünscht.
Bentonit
Es ist eine Art Ton, der verschiedene Metallatome enthält. Sie entstanden durch chemische Verwitterung von Vulkanasche, Tuff und aluminium- und magnesiumreicher Lava. Aufgrund seiner kolloidalen Eigenschaft und seiner hohen Plastizität besitzt Bentonit die Eigenschaft, die beim Gießen als Formstoff verwendeten Sande zu binden.
Bentonit wird hauptsächlich als Verdickungsmaterial in Beschichtungsanwendungen verwendet. Industriemineralien, die für Spachtelzwecke verwendet werden, sind nicht nur kostengünstig, sondern leisten mit ihren physikalischen und physikalisch-chemischen Eigenschaften wichtige Beiträge zur Qualität und Leistungsfähigkeit der Farbe. Die Eigenschaften, die die Füllstoffe dem Lack verleihen, sind wie folgt:
Bessere Filmbildung, erhöhte Witterungsbeständigkeit, Basis für echtes Pigment,
Verhindern eines schnellen Zusammenbruchs, Reduzieren der Durchtrittsrate von Feuchtigkeit. Da sie billiger als Pigmente sind, reduzieren sie die Kosten für Farbe.
Es sorgt dafür, dass der Bohrschlamm zähflüssig wird, die Krümel nach oben getragen und Wasseraustritt verhindert wird.
Bei der Säureaktivierung von Ca-Bentoniten, die zur Aufhellung von Ölen verwendet werden, werden Oberflächen und Zwischenräume im Kristall erweitert, Fe, Ti, Ca, Na und K werden aus der Kristallgitterstruktur von Tonmineralen getrennt, H+ - Bindungen werden in ihren Räumen gebildet, in Bleicherde und Pflanzenöle (Olivenöl) umgewandelt Es wird als Filtermaterial bei der Raffination von Sonnenblumen-, Mais-, Sesam-, Soja-, Palm-, Raps-, Baumwollsaatöl verwendet.
Aufgrund seiner sehr schwachen Verbundhaftung kann es leicht auseinanderbrechen.
Es wird zum Pelletieren von Bentonit-Eisenpulvern mit Bindemittel- und Kunststoffeigenschaften verwendet.
Es wird im Tiefbau verwendet, um die Wasser- und Flüssigkeitsundurchlässigkeit von Fundament- und Dammbauwerken zu erreichen.
Es wird bei der Klärung von Wein und Fruchtsäften, bei der Herstellung von Tierfutter verwendet.
Es wird als Füllmaterial in der Pharma-, Papier- und Gummiindustrie verwendet.
In der Zementindustrie, als Zusatzstoff in der Keramikindustrie,
Es wird in der Erdölraffination verwendet.
Es wird zur Reinigung von Abwasser verwendet.
Es wird in der Lackindustrie und in Feuerlöschern verwendet.
Es wird bei der Düngemittelherstellung und Bodenverbesserung verwendet.

Calcit (CaCO 3 )
Calcit (CaCO3) ist ein natürlich vorkommendes Karbonatgestein (Kalkstein, Marmor, Kreide).
Mineral. Farblos, glasig, kristallin in verschiedenen Formen. es ist transparent. Es lässt sich leicht mahlen und man erhält ein weißes Pulver. Seine Härte beträgt 3 auf der Mohs-Skala und seine Dichte liegt im Bereich von 2,6-2,7.
Calcit (Calciumcarbonat)-Formationen, die kommerziell in der Welt produziert werden,
weiße Kalksteine
Weiße, reine Kalksteine
Grobe Kristallmurmeln
Sie sind weiße Kreideformationen. Unter ihnen sind die mit dem höchsten Weißgrad grobe kristalline Marmore. Allerdings ist der Energieaufwand beim Mahlen höher als bei den anderen.
Die Region Çanakkale Karabiga ist eine der größten kristallinen Calcitformationen in der Türkei. Im Granitkontakt gebildete Calcitablagerungen haben einen hohen Weißgrad und sind leicht zu schleifen, aber seine Weiße ist niedriger als die in der Ägäis und Niğde gefundenen Formationen. Marmorvorkommen gibt es in Bayramiç, Biga und Ezine. Balikesir Erdek und In Manyas gibt es sehr reiche große kristalline Marmorbetten und Steinbrüche.
Yıldız-Gebirge in Thrakien, Marmor- und Dolomit-Marmorablagerungen in Bursa Orhaneli
stehen zur Verfügung. Bursa Orhangazi, Keles, İnegöl haben reiche Marmorvorkommen, aber die Produktion erfolgt in sehr kleinem Maßstab. Marmorvorkommen gibt es in İzmir Tyre, Gölmarmara, Akhisar und Torbalı. Der Weißgrad ist niedriger als zuvor angegeben. Die Regionen Muğla Yatağan und Kavaklıdere haben sehr reiche Marmorbetten mit einer kleineren Kristallstruktur, aber einer reineren chemischen Struktur, leicht zu schleifen und einem sehr hohen Weißgrad. Die Region Niğde verfügt über sehr reiche Reserven und die Kalzitvorkommen hier sind die weißesten Formationen in der Türkei. In dieser Region gibt es Calcit-Steinbrüche, die die Produktion sehr schnell steigern. Heute beziehen viele Produzenten Rohstoffe aus diesen Steinbrüchen in der Region Niğde. Aus diesem Grund haben die Investitionen in Niğde in den letzten Jahren deutlich zugenommen. Die oben genannten Regionen
Dies sind Regionen mit sehr reichen Reserven, die in 10 Millionen Tonnen ausgedrückt werden können. Abgesehen davon sind in fast allen Regionen Anatoliens Calcit-Formationen anzutreffen, für die noch keine Produktions- und Reservenbestimmung vorgenommen wurde. Die Summe der bekannten Reserven kann in Hunderten Millionen Tonnen ausgedrückt werden. Die auffälligsten Punkte sind die Reserven in der Türkei; CaCO3 hoher Prozentsatz,
Verunreinigungen wie Kieselsäure, Eisen und Magnesium sind sehr gering und der Weißgrad nach dem Mahlen sehr hoch.
Der hohe Weißgrad im Erz wird immer bevorzugt, weil es Titandioxid bei Lacken und Kunststoffen und optische Aufheller bei Papier spart. Calcite gemahlen in mikronisierten Größen im Trocken- oder Nasssystem; Es wird in Papier, Farbe, Kunststoff und Kabel, Bauwesen, Klebstoffen, Lebensmitteln, Keramik, Teppichboden, Linoleum, Pharmaindustrie verwendet.
Calcit in der Lackindustrie: Die Farbenindustrie verwendet trocken gemahlenen Calcit in den Größen 1,3,5,20,40 Mikrometer. Die am meisten nachgefragte Produktgruppe ist 5 Mikron Calcit. In wasserbasierten Baufarben, die in Innen- und Außenbeschichtungen verwendet werden, wird Calcit in einer Menge von 25-35% dem Anstrich zugesetzt. Calcit, das als Füllstoff in Lacken verwendet wird, sorgt für eine Oberflächenbeschichtung und reduziert den Titandioxidverbrauch. Aufgrund der Verteuerung von Chemikalien im Farbensektor ist der Markt Die Nachfrage nach wirtschaftlichen Farbstoffen ist gestiegen. So ist der Calcitverbrauch in der Lackindustrie in den letzten fünf Jahren um 50 % gestiegen.
Calcit in der Kunststoffindustrie: Calcit, Kunststoffmöbel, Rohre, Automobil usw. Es wird bei der Herstellung vieler Kunststoffprodukte verwendet, sowohl in natürlicher Form als gemahlen als auch in beschichteter Form. Die Beschichtung erfolgt meist mit Stearinsäure und manchmal mit Calciumstearat. Polypropylen (PP), Polyamid (PA), Thermoplastische (TPES) und PVC-Harze sind hauptsächlich Kunststoffe, in denen Calcit als Füllstoff verwendet wird. Der Einsatz ähnlicher Füllstoffe, insbesondere Calcit, in der Kunststoffindustrie nimmt von Jahr zu Jahr zu. Farbe, Calcit wird aus vielen Gründen wie seiner Reinheit und Billigkeit als Füllstoff in der Kunststoffindustrie verwendet.
Es ist möglich, Calcit in Formeln mit einem Anteil von 5% bis 50% zu verwenden, um die mechanische Leistung zu erhöhen und die Effizienz zu erhöhen sowie die Kosten zu senken. PE hat auch einige Nebenwirkungen wie Veränderungen des MFI und der Dichte . Verbundwerkstoffe .
In der Kunststoffindustrie wird es bevorzugt, anstatt es direkt in Calcitproduktverbindungen zu verwenden, indem ein Verbundmaterial mit PE erhalten wird. LDPE, HDPE, PP etc. als Träger aber Materialmatrix. kann auch bevorzugt werden.
Die Einarbeitung des pulverförmigen Calcitprodukts direkt aus dem Feed in andere Komponenten während der Anwendung in den Endproduktprozessen führt zu inhomogenen Ergebnissen am Endprodukt. Da es sich in der Beschickungskammer nicht gut vermischt, bildet sich in der Extrusionslinie eine Schmelze mit unausgeglichener Dichte. Dadurch wird der Standard des Produkts vollständig zerstört.
Aus diesem Grund wäre es bei der Verwendung von Calcit zweckmäßig, im Voraus einen Verbundstoff in Anteilen herzustellen, die den Verhältnissen entsprechen, die in das Endprodukt aufgenommen werden sollen.
In diesem herzustellenden Verbundmaterial werden auch zusätzliche Additive wie ein Schmiermittel verwendet, das die Fließfähigkeit erleichtert (das den Abrieb an der Maschine bis zu einem gewissen Grad beseitigt) und ein Bindemittel, das auf der gebrochenen Polymerkette heilt.
Dies sind meistens; Als spezieller Zusatzstoff (Wirkstoff) erscheinen PE-Wachs, Calciumstearat, Zinkstearat.
Calcit in der Vliesstoffproduktion: Zur Optimierung der Produktion wurde mit dem Einsatz von Calciumcarbonat-Füllstoffen begonnen. Aus Calciumcarbonat-Pulver (CaCO3), Kunstharzen und anderen speziellen Additiven hergestellt, ist Calciumcarbonat-Füllstoff eine der effektivsten Materiallösungen für die Vliesherstellung. Die Anwendung dieses Materials bietet den Endprodukten mehrere Vorteile:
Dies sind Bereiche, in denen Produkte aus Calciumcarbonat-Vliesstoffen von Medizin- und Körperpflege bis hin zu Hygiene, Geotextilien (Gewebe, die in technischen Industrien wie Saugen, Trennen, Filtern, Schutz, Verstärkung und Austrag verwendet werden) reichen.
Vorteile der Zugabe von Calcit-Füllstoff zu Vliesstoffen:
Bietet Verbesserung der Produktoberflächen
Es führt zu einer besseren Deckkraft der Gewebestruktur durch Reduzierung des Glanzes, wodurch die Oberfläche matter und blickdichter wird.
Verleiht eine natürliche weiße Farbe mit begrenztem Gelbstich
Verbessert die Materialstruktur
Erzeugt ein angenehmes und baumwolliges Tragegefühl
Verhindert den CO2-Fußabdruck bei Berührung
Schafft mehr Mikrobereiche für die Luftfilterung und Ölaufnahme
Fügt eine erhöhte Wärmeleitfähigkeit und physikalische Festigkeit hinzu
Ermöglicht die Senkung der Prozesstemperatur
Es ebnet den Weg für eine höhere Produktivität der Produktion, dh es erhöht die Kapazität.
Das spart Energie und Produktionskosten.
Es kooperiert problemlos mit mehreren Basisharzen (dank seiner guten Dispergierbarkeit) und kann auf verschiedene Weise verarbeitet werden
Empfohlene Einsatzraten von Calcit bei der Herstellung von Vliesstoffen:
5-20% in dünnen Stoffen,
20-35% in mittleren Stoffen,
bei dicken Stoffen erreicht er 60%.
Wenn eine extrem gute Dispergierung und Stabilität erforderlich ist,
Der Füllstoff-Masterbatch wird typischerweise mit einer Beladungsrate von 78-80% und einem Schmelzindex von 20-40 g/10 min aufgetragen.
Der MF-Indexwert für Vliesstoffe variiert zwischen verschiedenen Stoffdickenstufen. Dünnerer Stoff erfordert einen höheren MFI, während für dickere Stoffe ein niedrigerer MFI empfohlen wird.
Es ist sinnvoll, die Dosierung von Calciumcarbonat-Füllstoffen in Vliesprodukten schrittweise zu ändern.
Calcit CaCO3 wird in zwei Gruppen unterteilt,
Gemahlenes Calciumcarbonat: (GCC) (Partikelgrößen 10-1 Mikron,
billiger, weil einfacher herzustellen)
Ausgefälltes Calciumcarbonat: (PCC) (Ausgefälltes Calciumcarbonat).
(Partikelgrößen liegen im Nanometerbereich, die Herstellung ist teuer, da chemisch)
Fälltes Calciumcarbonat bedeutet auch gereinigtes, raffiniertes oder synthetisches Calciumcarbonat. PCC hat auch die gleiche chemische Formel wie Kalkstein, Marmor und Kreide (CaCO3). Drei verschiedene Formen von Calciumcarbonat-Mineralien werden durch die Anordnung von Calcium-, Kohlenstoff- und Sauerstoffatomen untereinander in drei verschiedene Richtungen gebildet.
Das am häufigsten ausgefällte Calciumcarbonat ist die hexagonale Form, die als Calcit bekannt ist. Einige Calcitmineralien können skalonaedrisch, rhomboedrisch und pyrismatisch sein.
Da PCC mit chemischen Verfahren hergestellt wird, werden Partikelform, Partikelgröße und Partikelgrößenverteilung unter Kontrolle gehalten und hat aus diesen Gründen Vorteile gegenüber gemahlenem Calciumcarbonat (GCC).
Diese Struktur, die durch den chemischen Fällungsprozess von natürlichem Calciumcarbonat entsteht,
es verleiht dem Material positive Eigenschaften wie Schlagzähigkeit, Glanz, Opazität; PCC kann auch als Thixotropiermittel verwendet werden, das die Fließeigenschaften verbessert.
In der PCC-Kunststoffverarbeitung, insbesondere Hartplastik, PVC-Profil, Kunststoffrohr und Weich
Kunststoff wird als funktioneller Füllstoff bei der Herstellung von PVC-Kabeln verwendet.
Bei der Herstellung von PCC-Hartkunststoffen: erhöht die Schlagzähigkeit des Profils (auch bei tiefen Temperaturen). Erhöht Weißgrad und Helligkeit. Das Profil verbessert die Oberflächenglätte. Es gleicht die Extrusionsdrehmomentwerte in der Produktion aus. Es verkürzt die Plastifizierzeit durch Absenken der Aufschlusstemperatur. Es verlängert die Lebensdauer der Maschine, indem es die Reibung verringert, die während der Extrusion auftritt.
Beim Einsatz von PCC bei der Herstellung von Weichkunststoffen: Es verleiht dem Kabel Zähigkeit und Flexibilität. PVC-Kabel müssen eine niedrige HCl-Emission im Inneren aufweisen, es reduziert den hohen HCl in PVC-Paste mit seinen hohen Absorptions- und Oberflächeneigenschaften. Es beeinträchtigt die elektrischen, isolierenden Eigenschaften der Kabelmasse nicht. Beim Einsatz in der Gummi- und Reifenherstellung Erhöht Flexibilität und Bruchfestigkeit, sorgt für Oberflächenglätte.
Ebenfalls; Es wird auch in Polypropylen (PP), Polyethylen (PE) und Polyesterprodukten verwendet.



Calcit Qualitätsbestimmung Bedingungen
Abriebwert: Dies ist der Gewichtsverlust in mg 100 g trockenem CaCO3, dispergiert in 3,2 lt reinem Wasser nach 6000 Zyklen in der Schleifvorrichtung, was ein wichtiger Wert in der Papierindustrie ist.
Dispersionsrate: Dies ist die Nichtagglomeration und Dispersion von CaCO3-Partikeln in der Umgebung, in der sie verwendet werden. Es ist wichtig in der Abfüllindustrie.
Aktivierung: (Beschichtung) Es handelt sich um die Beschichtung von Körnern mit verschiedenen Aliphaten, um den Abstand zwischen CaCO3-Körnern zu verringern und zu verringern.
Weißheitsgrad: Es ist ein Wert , als ein Ergebnis des Vergleichs mit den Standard - MgO Weißen erhalten und es ist das% der Lichtreflexionsvermögen des Materials. Dieser Wert sollte 96-100% für Calcit, 96% für Marmor und 93-96% für Kreide betragen. Es ist ein Merkmal, das in Branchen gesucht wird, in denen Papier und Weißgrad wichtig sind.
Spezifische Oberfläche: Die Gesamtoberfläche von 1 g CaCO3 in cm2. Es ist in der Beschichtungs- und Kunststoffindustrie gefragt.
antisplit
Calcit; Es wurde eingesetzt, um das Ausdünnen von Klebebändern zu verhindern und die Kosten zu senken. Später, unter der Wettbewerbsbelastung durch die Marktbedingungen, wird es weiterhin in vielen Polymerproduktgruppen als Antisplit-Masterbatch eingesetzt.
Antisplit-Masterbatches sind vorbehandelte Calcit-Compounds als Füllstoffadditive. Mit anderen Worten, Calcit kann direkt in die Produktzusammensetzungsformel aufgenommen werden oder im Voraus als Antisplit bezeichnet werden, um den Prozess zu erleichtern. Auf diese Weise wird die Granulatform von Pulver zu Granulat. Dies führt zu einem saubereren Prozessablauf.
Der Grund, warum diese hochgefüllten Compounds Masterbatch genannt werden, liegt darin, dass sie wie bei Farbmasterbatch-Anwendungen durch Beladen des Hauptträgerpolymers mit hohem Calcit (70 - 80%) granuliert werden. Es ist darauf zu achten, dass die granulierte Füllmasse ebenso wie das Masterbatch dem mit Calcit zu beladenden Endprodukt zugesetzt wird, um eine gute Verteilung des Calcits im Endprodukt zu gewährleisten.
Aufgrund der Tatsache, dass es sich bei den Füllmaterialien um Pulver handelt, versuchen Hersteller, die das Endprodukt in Granulatform (Spritzguss, Extrusionsfolie und Profil) verarbeiten, es direkt in den Verarbeitungstrichter zu mischen, was zu einigen Problemen führt.
Diese Probleme sind;
Unzureichende Verteilung der Füllungen, da die mit dem Granulat in den Trichter eingebrachten Füllungen vor dem Granulat in die Maschine fließen
Schlecht dispergierte Füllstoffe reichern sich an bestimmten Stellen an und mindern die mechanischen Eigenschaften des Endprodukts.
Farbunterschiede im Produkt von nicht vollständig dispergierten Füllungen
Durch direkte Einwirkung von Füllungen in Maschinen, die für die Produktherstellung ausgelegt sind, kommt es in der Maschine zu mechanischem Abrieb und sehr großen Schäden.
Erhöhung des Stromverbrauchs durch hohe Drücke bei der Verarbeitung in Maschinen, die direkt auf Calcit treffen
Produktions- und Arbeitskosten der Verwendung von Pulverprodukten
Abgesehen von diesen Problemen können noch viele weitere Probleme gezählt werden. Außerdem ist es bei dem Pulverprodukt schwierig, die Einarbeitungsrate des Pulverprodukts in das Endprodukt zu bestimmen. Auch beim Versuch, mit Dosieren zu beladen, sind die Dosiergerätekosten von Pulversystemen deutlich höher als bei Granulatdosierern. Die Vorteile der Verwendung von Antisplit-Masterbatch sind:
Bietet Kostenvorteil
Viel bessere Verteilung der Füllstoffe im Endprodukt
Bietet Hitzebeständigkeit während der Verarbeitung des Materials
Es verleiht dem Material Härte, Festigkeit und Zähigkeit.
Reduziert Formschwund
Hilft, den Einsatz von Titan in weißen Produkten zu reduzieren
Aufgrund dieser und vieler weiterer Vorteile hat die Herstellung und Verwendung von Antisplit-Masterbatch in den letzten Jahren zugenommen. Es wird im Allgemeinen in Produkten der Polyolefingruppe verwendet.

Antisplit-Produktion
Bei der Herstellung von Antisplit-Masterbatch werden verschiedene Additive verwendet. Dies sind PE-Wachs, Zinkstearat, Calciumstearat oder Prozesshilfsmittel, die allein anstelle dieser 3 Additive ausreichen können. PE-Wachs fungiert als externes Gleitmittel und Verdünnungsmittel, Calciumstearat fungiert als internes Gleitmittel und Fließfähigkeitsverbesserer und Zinkstearat fungiert als externes Gleitmittel. Darüber hinaus sind die als Einkomponentensystem konzipierten Prozessmittel allein durch die Zugabe von internen und externen Gleitmitteln, Fließfähigkeit und Bindungseigenschaften wirksame Additive. Prozesshilfsmittel allein reichen bis zu 70 – 80 % Calcit-Beladungen aus und können als die Hälfte aller anderen Additive eingesetzt werden.
Auch bei der Herstellung von Antisplit-Masterbatch ist die Prozessmaschine ein wichtiger Faktor. Wichtig ist hier die Fähigkeit der Maschine, das Produkt zu verdichten und zu mischen. Bei diesen Verfahren werden im Allgemeinen Ein- und Doppelschneckenextrusionsmaschinen verwendet. Da das Verdichtungs- und Mischungsverhältnis des Produkts von Einschneckenextrudern gering ist, wird ein Banburi-System benötigt, um das Produkt vorzumischen.
Der wichtigste Faktor, der bei der Auswahl der Zusatzstoffe berücksichtigt werden sollte, sollte nicht nur der Preis sein. Der Kostenvorteil eines Produkts sollte nicht durch den Einkaufspreis, die Vorteile des Zusatzstoffes im Prozess, die Einsatzraten, die Vorteile, die es bei den Energiekosten bringt, den Schutz der Maschine und die Tatsache, dass es nicht erzwingt, bestimmt werden die Gesamtheit der Faktoren zeigt die Kosten eines Additivs. Käufe, die nur unter Berücksichtigung der anfänglichen Anschaffungskosten getätigt werden, können Sie aufgrund der vielen Kosten, die im Hintergrund entstehen, mehr kosten. Die Beachtung dieses Themas bei der Auswahl aller Zusatzstoffe trägt sowohl zu Ihrem Produkt als auch zu Ihren Kosten bei.
Mögliche Antisplit-Formel:
.png)
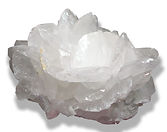
Kalsit (CaCO3)
Kristal Yapı
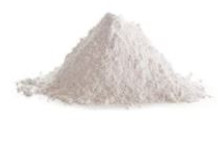
Kalsit (CaCO3)
Öğütülmüş / Toz Yapı
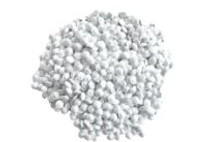
Antisplit
Granül Yapı