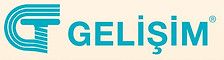


Hidrokarbonlar
Hidrojen ve karbon olmak üzere iki elementten oluşan organik bir bileşiktir. Petrol bileşiminin büyük bir kısmı değişen uzunluklardaki hidrokarbonlardan oluşur.
En küçük hidrokarbon metan, tek bir karbon atomu ve dört hidrojen atomundan oluşur. Bununla birlikte, hidrokarbonlar, zincirler, daireler ve diğer karmaşık şekiller dahil olmak üzere birçok yönden birbirine bağlanmış yüzlerce veya binlerce bireysel atomdan oluşabilir.
Hidrokarbonların özelliklerini sınıflandırmak için birkaç temel türe ayrılırlar.
Alkanlar: Bunlar doymuş hidrokarbonlar olarak adlandırılır. Yani sadece tüm karbon atomları arasında tek bağlar içerirler. Alkanlar, petrol yakıtlarının temelidir ve doğrusal ve dallı formlarda bulunurlar.
Doymamış Hidrokarbonlar: Karbon atomları arasında bir veya daha fazla çift bağa sahip olan hidrokarbonlara alken denir.
Sikloalkanlar: Bir veya daha fazla halka yapısı içeren herhangi bir hidrokarbon.
Aromatik Hidrokarbonlar: Areneler olarak da adlandırılan aromatik hidrokarbonlar, karbon atomlarının birbirini izleyen çift ve tek bağlarla bağlandığı benzersiz bir karbon molekülleri sınıfıdır. Bu molekül sınıfı, karbon atomları arasındaki bağların tek ve çift bağlar arasında bir ara bağ olduğu özel halka yapılarına sahiptir.
Bu sınıftaki moleküller, endüstriyel çözücü «benzen» içerir.
Benzen (C6H6): Diğer hidrokarbonlar gibi benzen de petrolün doğal bir bileşenidir. Oda sıcaklığında renksiz, yanıcı, tatlı kokulu bir sıvıdır ve yüksek oktan sayısına sahip olduğu için çoğu benzin karışımının bir bileşenidir.
Benzen de oldukça kanserojendir ve kemik iliği yetmezliği ve kemik kanserine neden olduğu iyi bilinmektedir. Elbette, “hoş aroması” nedeniyle tıraş sonrası ve diğer kozmetiklerde bir katkı maddesi olarak kullanıldığında kanserojenliği iyi bilinmemektedir.
En büyük benzen kullanımı (% 50), stiren ve polistren plastiklerinin ürünüdür. Ayrıca Naylon üretiminde önemli olan sikloheksan olarak bilinen bir moleküle dönüştürülür. Siklohekzan üretmek için benzenin yaklaşık% 15'i kullanılır. Böcek ilaçlarından kauçuğa kadar her şeyde daha küçük miktarlar kullanılır.
Benzen yapısı iki şekilde çizilebilir. İlkinde, çift bağ karakteri açıkça çizilir. Kısa elli versiyonda, yapıyı göstermek için halkanın içine bir daire çizilir. Benzen içindeki her bir karbon atomuna bağlı tek bir hidrojen vardır.
Aşağıdaki I. ve II. çizimleri eştir. Pratikte III. çizim kullanılır.
Benzen, renksiz, alevlenebilen, kaynama noktası 80,1 °C, erime noktası 5,5 °C olan bir sıvıdır.
Binükleer Aromatik Hidrokarbonlar: Molekülünde iki benzen halkası içeren bileşiklerdir.
Hidrokarbonlar
Hidrojen ve karbon olmak üzere iki elementten oluşan organik bir bileşiktir. Petrol bileşiminin büyük bir kısmı değişen uzunluklardaki hidrokarbonlardan oluşur.
En küçük hidrokarbon metan, tek bir karbon atomu ve dört hidrojen atomundan oluşur. Bununla birlikte, hidrokarbonlar, zincirler, daireler ve diğer karmaşık şekiller dahil olmak üzere birçok yönden birbirine bağlanmış yüzlerce veya binlerce bireysel atomdan oluşabilir.
Hidrokarbonların özelliklerini sınıflandırmak için birkaç temel türe ayrılırlar.
Alkanlar: Bunlar doymuş hidrokarbonlar olarak adlandırılır. Yani sadece tüm karbon atomları arasında tek bağlar içerirler. Alkanlar, petrol yakıtlarının temelidir ve doğrusal ve dallı formlarda bulunurlar.
Doymamış Hidrokarbonlar: Karbon atomları arasında bir veya daha fazla çift bağa sahip olan hidrokarbonlara alken denir.
Sikloalkanlar: Bir veya daha fazla halka yapısı içeren herhangi bir hidrokarbon.
Aromatik Hidrokarbonlar: Areneler olarak da adlandırılan aromatik hidrokarbonlar, karbon atomlarının birbirini izleyen çift ve tek bağlarla bağlandığı benzersiz bir karbon molekülleri sınıfıdır. Bu molekül sınıfı, karbon atomları arasındaki bağların tek ve çift bağlar arasında bir ara bağ olduğu özel halka yapılarına sahiptir.
Bu sınıftaki moleküller, endüstriyel çözücü «benzen» içerir.
Benzen (C6H6): Diğer hidrokarbonlar gibi benzen de petrolün doğal bir bileşenidir. Oda sıcaklığında renksiz, yanıcı, tatlı kokulu bir sıvıdır ve yüksek oktan sayısına sahip olduğu için çoğu benzin karışımının bir bileşenidir.
Benzen de oldukça kanserojendir ve kemik iliği yetmezliği ve kemik kanserine neden olduğu iyi bilinmektedir. Elbette, “hoş aroması” nedeniyle tıraş sonrası ve diğer kozmetiklerde bir katkı maddesi olarak kullanıldığında kanserojenliği iyi bilinmemektedir.
En büyük benzen kullanımı (% 50), stiren ve polistren plastiklerinin ürünüdür. Ayrıca Naylon üretiminde önemli olan sikloheksan olarak bilinen bir moleküle dönüştürülür. Siklohekzan üretmek için benzenin yaklaşık% 15'i kullanılır. Böcek ilaçlarından kauçuğa kadar her şeyde daha küçük miktarlar kullanılır.
Benzen yapısı iki şekilde çizilebilir. İlkinde, çift bağ karakteri açıkça çizilir. Kısa elli versiyonda, yapıyı göstermek için halkanın içine bir daire çizilir. Benzen içindeki her bir karbon atomuna bağlı tek bir hidrojen vardır.
Aşağıdaki I. ve II. çizimleri eştir. Pratikte III. çizim kullanılır.
Benzen, renksiz, alevlenebilen, kaynama noktası 80,1 °C, erime noktası 5,5 °C olan bir sıvıdır.
Binükleer Aromatik Hidrokarbonlar: Molekülünde iki benzen halkası içeren bileşiklerdir.
Hakkında
Kyäni, faydalı bileşenlerden oluşan besin takviyesi ürünlerini; benzersiz iş fırsatıyla birlikte dünya çapında 50'den fazla ülkeye ulaştırmaktadır. İdeal sağlığımızı korumak için günlük olarak Kyäni ürünlerini kullanırız, bu ürünleri başkalarıyla paylaşırız, işimizi inşa etmek ve sürdürmek için neredeyse her gün belirli bir saatimizi işe adarız ve başkalarını da Kyäni fırsatına dahil ederek veya Potato Pak ve Caring Hands programlarına katkı sağlayarak başarımızı başkalarıyla paylaşırız.
Hakkında
Kyäni, faydalı bileşenlerden oluşan besin takviyesi ürünlerini; benzersiz iş fırsatıyla birlikte dünya çapında 50'den fazla ülkeye ulaştırmaktadır. İdeal sağlığımızı korumak için günlük olarak Kyäni ürünlerini kullanırız, bu ürünleri başkalarıyla paylaşırız, işimizi inşa etmek ve sürdürmek için neredeyse her gün belirli bir saatimizi işe adarız ve başkalarını da Kyäni fırsatına dahil ederek veya Potato Pak ve Caring Hands programlarına katkı sağlayarak başarımızı başkalarıyla paylaşırız.
Sayfa Yapım Aşamasındadır.
Sayfa Yapım Aşamasındadır.
Schulungs- / Wissens- / Lösungsplattform
Spritzguss

VİDA / KOVAN
ANA MOTOR
ISITICI / REZİSTANSLAR
POLİMER (ERİYİK)
KALIP SOĞUTMA HATLARI
HAREKETLİ PLAKA
SABİT PLAKALAR
KİLİTLEME MOTORU
BESLEME / DOZAJLAMA
RAM VİDA MOTORU
POLİMER (GRANUL)
KİLİTLEME ÜNİTESİ
KALIP
ENJEKSİYON ÜNİTESİ
Es ist eine Verarbeitungstechnik, bei der das geschmolzene Polymer unter hohem Druck durch einen offenen Kanal (Läufer) in einen Formhohlraum gedrückt wird und die Polymerschmelze die Form einer Form annehmen kann. Spritzgießmaschine und Extruder sind sehr ähnlich. Der Hauptunterschied zwischen den beiden Maschinen ist der Schraubvorgang. In der Extruderschnecke herrscht kontinuierlicher Vorwärtsdruck. Die Schraube der Spritzgießmaschine bewegt nicht nur den Vorwärtsdruck, sondern auch die Rückwärtsbewegung gemäß den Schritten des Formzyklus. Aufgrund dieser Hin- und Herbewegung wird es als "Hin- und Herbewegungsschraube" bezeichnet. Haltedruck: Durch Injizieren des geschmolzenen Polymermaterials in die Form und anschließendes Zurückziehen in wenigen Sekunden (dieser Prozess variiert je nach Formgröße, Rohmaterialtyp) neigt das Polymermaterial dazu, durch die Form zurückzufließen. Um ein Herausfließen aus der Form zu verhindern, dh die Schmelze in der Form zu fixieren, wird der Druck eine Weile fortgesetzt. Dieser Haltedruck wird auch als "Bügeldruck" bezeichnet, was falsch ist. Das Polymermaterial wird in der abgekühlten Form gehalten, bis es sich verfestigt, nachdem die Zyklusperiode abgeschlossen ist, werden die Formen geöffnet und das fertige Produkt / Halbzeug in Form erhalten. Übliche Thermoplaste im Spritzguss sind PP, PC, ABS, N6. Das Spritzgießen wird hauptsächlich für Thermoplaste verwendet, es können jedoch auch Elastomere und Duroplaste extrudiert werden.
Durch Spritzgießen; Eine Vielzahl von Produkten wie Rohrverbindungsstücke, Batteriegehäuse, Zahnbürstenböden, Flaschenverschlüsse, Einwegrasierer, Gabeln, Löffel, Teller, Stoßstangen und Armaturenbretter, Elektrogerätegehäuse, Fernsehschränke, elektrische Schalter und Spielzeug können hergestellt werden. Mit einigen Modifikationen können auch duroplastische Kunststoffe verarbeitet werden. Das Kunststoffmaterial wird mit hohem Druck in eine Form eingespritzt; Das Muster ist das Negativ (umgekehrt) der gewünschten Form.


Schraubenspritzguss: Der am häufigsten verwendete Typ sind Schraubenspritzmaschinen. Es besteht aus vier Grundeinheiten: Ein-Aus-Einheit, Form, Spritzeinheit und Steuereinheit. In den trichterförmigen Tank wird körniger Kunststoffrohstoff gegeben. Kunststoffgranulate, die vom unteren Teil des Trichters auf die Schneckenwelle absteigen, werden durch Drehen der Spiralschraubenwelle zur Einspritzdüse gezogen. Abgesehen vom Zylinder der Schneckenwelle bringen die rundum angeordneten Heizungen den gezogenen Kunststoffrohstoff auf die gewünschte Temperatur. Die Temperatur schmilzt das Kunststoffmaterial und macht es flüssig wie Honig. Der honigartige Kunststoffrohstoff wird durch Passieren der Einspritzdüse in den Hohlraum der geschlossenen Form eingespritzt. Das Teil wird aus der Form abgekühlt.
Kolbenspritzguss: Hubkolbenspritzgussmaschinen werden zum Formen kleiner und einfacher Teile verwendet. Hubkolbenmaschinen werden heutzutage nur noch zur Herstellung sehr kleiner Teile mit einem Gewicht von wenigen Gramm eingesetzt, da das Material nicht homogen erwärmt wird. Wenn eine Hubkolbenmaschine verwendet wird, befinden sich ungefähr 10 Dosierungen Material im Zylinder und dieses Material wird erhitzt und geschmolzen.
Arbeitsprinzip,
(1) die Form wird geschlossen und näher an die Düse gebracht (gleichzeitig wird das geschmolzene Material verdichtet),
(2) Einspritzen von Material in die Form (gleichzeitig für die nächste Füllung
spezielle Fütterungseinstellung erfolgt),
In (3) wird der Kolben eingefahren, Dosiergranulat wird in den Zylinder aufgenommen, der Läufer ist
Es kann als Abreißen, Öffnen der Form und Herausdrücken des Teils aus der Form zusammengefasst werden.

Grundvariablen im Spritzguss
Themen, die bei grundlegenden Variablen berücksichtigt werden müssen, sind unter vier Hauptüberschriften aufgeführt: Temperatur, Druck, Zykluszeiten und Geschwindigkeit.
Temperatur:
Es wird in zwei Unterüberschriften als Materialtemperatur und Formtemperatur gesammelt.
Die Temperatur des Materials sollte für die Art des Materials geeignet und gleichmäßig sein. Die Temperatur des Materials am Nippel muss bekannt sein. Die Materialtemperatur sollte in der Mitte des von den Mischungslieferanten angegebenen Temperaturbereichs liegen. Der beste Weg, um die Schmelztemperatur herauszufinden, besteht darin, sie direkt zu messen. Es gibt zwei Methoden, um diese Messung durchzuführen.
1- Kerntemperaturen mit Immersions- / Stabpyrometer
2- Die Oberflächentemperatur wird mit dem Infrarotpyrometer gemessen. Das Grundprinzip bei der Injektion hängt vom Prinzip ab, den heißen Kunststoff in die Form zu befördern und die Form des Formhohlraums anzunehmen, wodurch die Form gekühlt und gehärtet wird. Die Formtemperatur ist wichtig, da sie die Druckzeit und die Teilequalität beeinflusst. Obwohl Kunststoff in einer heißen Form sehr leicht fließt, ist die Zeit, in der der Druck abgekühlt und ausgeworfen wird, länger. Andererseits ist das Abkühlen des geschmolzenen Kunststoffs in der kalten Form schnell, aber die Fließfähigkeit im Formhohlraum nimmt ab und es kühlt ab und härtet aus, bevor die Form vollständig gefüllt wird.
Die besten Bedingungen zwischen diesen beiden Situationen zu finden; Es ist darauf zu achten, welche Art und Art von Kunststoff verwendet werden soll, welche Fließlänge der Kunststoff hat, welche Wandstärke das Kunststoffteil hat, welche Art von Läufer verwendet werden soll und welche Lauflängen und welche Qualität das gewünschte Teil haben soll . Während des Formenfüllens befindet sich der heißeste geschmolzene Kunststoff am Eingang der Form und am weitesten vom kältesten Kunststoffläufer entfernt. Wenn die Temperatur der Form nicht gut eingestellt werden kann, führt dieser Temperaturunterschied zur Bildung unerwünschter Spannungen, Schwachstellen und Materialverbindungen im Kunststoffteil. Um dies zu verhindern, ist es notwendig, beim Drucken eine gleichmäßige Temperaturverteilung vorzusehen. Dies kann mit den am besten geeigneten Kühlsystemen erreicht werden, die in der Form konstruiert werden sollen. Dies ist möglich, indem die heißen Teile der Form mit kaltem Wasser und die kalten Teile mit heißem Wasser versorgt werden.
Langsam fließendes Wasser hat eine laminare Strömung. Der Formkühlzyklus und die turbulente Strömung sollten jedoch beim Abkühlen bevorzugt werden.
Re <10000 laminare Strömung
Re> 10000 wird als turbulente Strömung ausgedrückt.
Die Formtemperatur ist idealerweise die von Kunststoffherstellern angegebene Temperatur, wie z. B. die Temperatur des Spritzgussmaterials.
Laminare Strömung:
Eine sehr regelmäßige Strömungsbewegung, die durch glatte Strömungslinien angezeigt wird, wird als laminare Strömung bezeichnet. Die Bewegung hochviskoser Flüssigkeiten wie Öl bei niedrigen Geschwindigkeiten ist im Allgemeinen laminar. Eine stark unregelmäßige Flüssigkeitsbewegung tritt normalerweise bei hohen Geschwindigkeiten auf und wird durch die sogenannten turbulenten Strömungsschwankungen angezeigt.

Druck:
Das Kunststoffmaterial wird mit einem bestimmten Druck in den Formhohlraum eingespritzt. Mit diesem Druck wird das Kunststoffmaterial bereitgestellt, um die Form des Formhohlraums anzunehmen. Wenn der Druck entfernt wird, ist der Kunststoff immer noch flüssig und möchte zu seiner vorherigen Geometrie zurückkehren. Aufgrund der Fähigkeit des Kunststoffs, sich sehr leicht zu dehnen und zu dehnen, müssen wir einen übermäßigen Druck auf den Formhohlraum ausüben, damit sich beim Absinken der Materialtemperatur und Abkühlen des Teils keine Lücken am Pressenausgang bilden. Wenn die Form mit Kunststoff gefüllt ist, muss die eingeschlossene Luft in dieser Zeit ausgestoßen werden. Beim Öffnen der Form sind zwei Punkte zu beachten:
1- Um zu verhindern, dass das Teil an der festen Seite der Form haftet (Einspritzseite)
2- Trennen des vom Auswerfersystem geschobenen Teils
Einige Formenbauer behaupten, dass sich die Formen nicht an die Maschinen anpassen können. Mit anderen Worten, wenn die gleichen Form- und Kunststoffbedingungen erfüllt sind, wird gesagt, dass die gleiche Leistung nicht erzielt werden kann, wenn sie an verschiedene Maschinen angeschlossen werden. In gewissem Sinne ist das absurd. Das Material kann die ID der Maschine, auf der es verarbeitet wird, nicht lesen. Wenn also die Bedingungen gleich sind, sollten sie letztendlich gleich sein. Es gibt jedoch einige Unterschiede. Der erste Fehler, den der Bediener, der den Druck abliest, am hydraulischen Pressenkopf gemacht hat, wird als Fehler aufgrund des Drucks auf den Kunststoff angesehen. Die hydraulische Pressarbeit arbeitet nach einem Prinzip, das als Kraftverdoppler bezeichnet wird. Im Kunststoffgeschäft liegt dies im Verhältnis 8: 1 und 12: 1. Es gibt jedoch viele Ausnahmen. Es ist sehr klar, dass bei einem Druck einer Presse mit einem Verhältnis von 8: 1 ein Druck von 1000 kg Kunststoff einem Druck von 8000 kg entspricht. Das in derselben Maschine verwendete Verhältnis von 12: 1 erzeugt einen Druck von 12000 kg. Dieser Druckunterschied führt dazu, dass die Maschine einen Fehler signalisiert. Gemäß diesen Druckverhältnissen sollte jede Maschine nach ihrem eigenen Kraftverdoppler klassifiziert werden, und die Maschine sollte gemäß diesen Daten eingestellt werden, indem eine entsprechende Tabelle erstellt wird.
Viele Maschinen sind computergesteuert und der Informationsprozessor ist
Es liest innerhalb des Bereichs.
Maschinenhersteller verwenden jedoch Ventilsysteme, die in nur 10 Zehntelsekunden aktiviert werden können.
Dieser Unterschied in der Empfindlichkeit führt natürlich dazu, dass die Maschine langsamer wird und Probleme verursacht. Die Ventile dieses Maschinentyps sollten ebenfalls entsprechend ausgewählt werden. Somit werden Fortschritte bei der Kontrolle erzielt. Gemäß der Fingerregel werden, wenn der Druck auf das Material gleich ausgeübt wird, die gleichen Abmessungen in der Form und folglich die gleichen Abmessungen auf dem Teil erhalten.
Einspritzdruck:
Vom Extruder auf die Form ausgeübter Druck, um die Formkammer zu füllen.
Haltedruck: Er wird angewendet, um dem Schrumpfen des Kunststoffmaterials entgegenzuwirken und seine volle Form anzunehmen. Nachdem das Kunststoffmaterial in die Form eingespritzt und die Form vollständig gefüllt ist, versucht es in der zweiten Phase, aus dem Eintrittspunkt in die Form zu entweichen, um diese Bewegung zu verhindern, wird der Haltedruck nach dem Einspritzdruck angelegt. Mit anderen Worten, das Kunststoffmaterial wird so aufbewahrt, dass es nicht entweicht.
Gegendruck:
Es ist definiert als der Widerstand gegen Rückwärtsbewegung der Schraube und hilft, das Material durch Reibung zu erwärmen. Dies ist der Druck, den die Schraube auf dem Kunststoff während der Empfangsphase beim Rückwärtsfahren erzeugt. Dieser Druck stellt sicher, dass die Mischung auf dem optimalen Niveau ist, wenn Farbstoff verwendet wird. Bei übermäßigem Druck wird die Materialstruktur durch Reibungswärme gestört.
Zykluszeit:
Das Intervall, in dem ein Zyklus vom Anfang bis zum Ende abgeschlossen ist, wird als Zykluszeit / -zeit bezeichnet. Wenn sich das Material im geschmolzenen Zustand befindet, ist es erwünscht, die Form sehr gut zu füllen.
Wenn das Material abkühlt, wird es fest genug und die Injektionsmaschine beginnt, sich auf das nächste Teil vorzubereiten. Es spielt keine Rolle, ob das Material einfach abgekühlt wird. Was zählt ist, wie es abkühlt. Wenn wir erklären wollen, was hier gemeint ist: "Bevor der Kunststoff fest wird, braucht er ein kleines Nickerchen." Mit anderen Worten, es ist keine optimale Situation für Kunststoff hinsichtlich der sofortigen Abkühlung. Für niedrige Zykluszeiten sollten Mindestzeiten verwendet werden.
Füllzeit:
Es ist nur die Zeit, die benötigt wird, um die Formkammer zu füllen.
Haltezeit:
Das Teil wird in der Form unter Haltedruck gehalten, um das Schrumpfen zu verringern. Beim Ziehen des Stücks wird neue Schmelze nach innen gefüllt. Die Haltephase wird fortgesetzt, bis der Eingang zum Tor gefriert. Wenn immer mit den gleichen Haltezeiten gearbeitet wird, können Teile mit dem gleichen Gewicht erhalten werden.
Bügelzeit: Es ist nur die Zeit erforderlich, um das Material in der Formkammer zu komprimieren.
Kühlzeit:
Es ist die Zeit, bis das Teil im Inneren der Form eine ausreichende Steifigkeit und Kälte aufweist.
Schimmelöffnungszeit:
Es sollte minimal sein und sich nicht ändern. Die Formöffnungszeit besteht aus dem Öffnen der Form, dem Entfernen des Teils durch den Aufprall der Drücker und der Schließzeit der Form.
Geschwindigkeit:
Die Füllgeschwindigkeit der Formkammer wird als Einspritzgeschwindigkeit bezeichnet. Die hohe Einspritzgeschwindigkeit stellt sicher, dass der Hohlraum mit niedrigviskosem und gut geschmolzenem Material gefüllt ist. Bei kleinen Läufern kann es zu einer hohen Einspritzgeschwindigkeit sowie zu mechanischen und kosmetischen Fehlern im Teil kommen.
Temperatur, Druck, Zykluszeit und Geschwindigkeit sind alle
Es scheint oft, dass die Geschwindigkeit in erster Linie variabel ist. Die Füllgeschwindigkeit hängt direkt von der Schmelzviskosität ab. Dies hängt vom gewünschten Fülldruck ab. Kleine Geschwindigkeitsänderungen wirken sich dramatisch auf die Fähigkeit der Maschine aus, den Formhohlraum zu füllen.
Die Viskosität des Materials hängt von dieser Geschwindigkeit ab; Es ist wahrscheinlich die kritischste Variable und ihre Änderung hat die geringsten Auswirkungen auf andere. Druck ist die zweite Variable, die verwendet werden sollte. Es kann in sehr kurzer Zeit angepasst werden, ohne dass dies Auswirkungen auf den Gesamtprozess hat. Die Änderung der Zykluszeit spiegelt sich sofort in der Schmelztemperatur des Materials wider. Temperaturänderungen ändern leicht die Viskosität. Dies beeinflusst den Druck und die Geschwindigkeit. Die Temperatur ist die am schwierigsten einzustellende Variable. Weil es leicht ist, Kunststoff zu wärmen, aber es ist auch sehr schwierig, ihm Wärme zu entziehen.
Das Spritzgießen, eine der Kunststoffverarbeitungstechniken, hat 7 Grundzyklen.
(1) Plastifizieren: Die Arbeit des Schmelzens von Kunststoffrohstoffen, die bereit sind, in die Form eingespritzt zu werden. Zuerst wird körniges Rohmaterial in den Ofen gebracht, das Rohmaterial wird durch Heizungen und Schraubenreibung geschmolzen, der geschmolzene Kunststoff wird zu dem Schraubenloch vorne geliefert.
(2) Schließen der Form: Mit der Spanneinheit der Maschine werden die beiden Teile der Form übereinander geschlossen und es wird hoher Druck ausgeübt. Der Formraum zwischen den beiden Formplatten (männliche Form und weibliche Form) wird gebildet und das Öffnen und Lösen der Form wird gegen den ausgeübten hohen Druck und die angewendete Geschwindigkeit verhindert.
( 3) Füllen der Form: Zuerst wird die Schraube vom Hydraulikkolben nach vorne gedrückt. Die Schmelze wird in den Kunststoffformhohlraum gefüllt.
(4) Druckanwendung: Der Druck wird erhöht. Das Füllen der Form wird bereitgestellt, um feine Details zu erzeugen.
(5) Halten: Das Teil wird in der Form unter Druck gehalten, um das Schrumpfen zu verringern. Beim Ziehen des Stücks wird neue Schmelze nach innen gefüllt. Die Haltephase wird fortgesetzt, bis der Eingang zum Tor gefriert.
(6) Abkühlen: Nachdem der Läufer gefroren ist, kühlt das Teil ab und schrumpft in der Form. Der Prozess wird fortgesetzt, bis das Teil abgekühlt ist und seine Erweichungstemperatur erreicht hat.
(7) Entformen: Das Teil wird mit Hilfe des Auswerfersystems aus der Form entfernt.
Wie zu sehen ist, finden sechs der sieben Grundzyklen ohne Plastifizierung an der Formeinheit statt.
Einige der Injektionsparameter


Formelemente im Spritzguss
Die Spritzgussform besteht aus vielen Einheiten, die komplex sein können, um dem Einspritzdruck standzuhalten.
Formen bestehen zunächst aus zwei Einheiten als «weiblich» und «männlich». Für beide Geräte stehen verschiedene Elemente zur Verfügung:
Weiblicher Kern:
Es ist der hellste Stahl der Form, in dem die Teilegeometrie verarbeitet wird und in dem sich normalerweise der Eingangstor befindet.
Männlicher Kern:
Stahl, in dem die Teilegeometrie verarbeitet wird und der Formhohlraum mit weiblicher Form, Drückern und anderen beweglichen Elementen gebildet wird, arbeitet.
Trägerin:
Hauptlagerstahl um den weiblichen Kern.
Männlicher Träger:
Hauptlagerstahl um den männlichen Kern.
Zentrierflansch:
Zentriert die Form auf der Spritzgussmaschinenplatte.
Zentrierwellen:
Dies sind die Spindeln, die die weiblichen und männlichen Platten der Form zentrieren.
Runner Bushing:
Es transportiert das geschmolzene Material von der Schnecke der Spritzgießmaschine zur Formtrennlinie.
Weibliche Anschlussplatte:
Dadurch kann die Form an die Spritzgießmaschine angeschlossen werden.
Isolierplatte:
Es unterstützt den Wärmehaushalt der Form durch Reduzierung der Wärmeverluste und spart Kosten.
Kühlkanäle:
Wasserwege im Träger und vorzugsweise im Kern.
Trägerplatte:
Stützeinheit für männliche Trägerplatte, um hohen Drücken standzuhalten.
Auswerferstützplatte:
Platten, mit denen die Drücker verbunden sind, die das Teil entfernen, die die Druckbewegung mit der Vorwärtsbewegung ihrer Stifte versehen
Parallelen:
Es bietet ausreichend Platz für die Bewegung der Auswerferplatte.
Unterstützungsspalte:
Es verhindert das Biegen der Trägerplatte und bietet Widerstand gegen die ausgeübten Drücke.
Axiallagerwellen:
Es verhindert, dass die Drückerplatte die Form / das Teil beschädigt, indem sie in axialer Richtung schwingt.
Drucklagerwellenbuchse:
Sie sorgen dafür, dass sich die Drücker nur in der gewünschten Achse bewegen.
Retraktor:
Gibt die Drückerplatte zurück, wenn sich die Form schließt.
O-Ring:
Es verhindert das Austreten von Kühlmittel aus den Kühlkanälen.
Tolle:
Es wird verwendet, um die in den Kühlkanälen zirkulierende Flüssigkeit zu leiten.
Stecker:
Teile, die so definiert sind, dass sie die Enden bestimmter Kanäle verstopfen, um einen Wasserkreislauf zu bilden.
Schließsysteme im Spritzguss schließen
Die Tatsache, dass der Injektionsprozess kein kontinuierlicher Prozess ist, erfordert, dass die Form geöffnet wird, damit das Produkt austritt, und dass sie für die nächste Presse wieder geschlossen wird. Schließ- / Verriegelungssysteme (Schließeinheit) führen diesen Vorgang durch. Da der Kunststoff mit sehr hohen Drücken in die Form eingespritzt wird, muss die Klemmeinheit die Form während des Einspritz- und Haltedrucks fest geschlossen (verriegelt) halten, um zu verhindern, dass sich die Form öffnet und Grate entstehen. Die Aufgabe dieser Einheit besteht darin, die Form zu schließen und zu öffnen, die Form bei hohem Druck geschlossen zu halten und die Bildung von Graten auf der Formtrennlinie zu verhindern. Es gibt drei Arten von hydraulischen, hydromechanischen und mechanischen Schließsystemen.
(1) Hydraulisches Schließen / Verriegeln
Das System arbeitet mit der Anwendung von Hydraulikkraft.
Der Hydraulikkolben befindet sich auf der beweglichen Seite der Maschine. Die Vorwärtsbewegung der Platte und die ausgeübte Kraft werden durch den auf das Fluid im Schließzylinder ausgeübten Lastdruck gesteuert. Die Bewegungsgeschwindigkeit der Platte wird im Allgemeinen durch das Verhältnis der Einlass- und Auslassgeschwindigkeiten des Fluids gesteuert. Hydraulische Klemmen werden in Spritzgießmaschinen mit hoher Tonnage verwendet.
Typischerweise sind es zwischen 1.300 und 8.900 Kilonewton (150 und 1.000 Tonnen). Die Einheiten sind flexibler als Schnallenklemmen, wenn es darum geht, die Tonnage an bestimmten Positionen während des Hubs einzustellen.
(2) Hydromechanisches Schließen / Verriegeln
Der hydraulische Aktuator steuert die Bewegung des Zylinderklappensystems und seiner Glieder und ermöglicht so das Öffnen und Schließen der beweglichen Platte. Die Verriegelungskraft wird mechanisch durch Öffnen des Drosselsystems bereitgestellt. Ein mechanischer Vorteil ergibt sich aus den Verbindungen in der Konstruktion. Dies geschieht durch Multiplikation von 1/20 der hydraulisch aufgebrachten Kraft. Die Verriegelungskraft kann durch Einstellen der Verriegelungshöhe eingestellt werden. Dies wird erreicht, indem die Verbindungen in der Feststellschraube hin und her gedreht werden. Die Verriegelungsmenge wird aus der Dehnung in den Säulen berechnet. Hydromechanische Klemmen sind für große Tonnagen über 8.900 Kilonewton (1.000 Tonnen) ausgelegt und verwenden Hydraulikzylinder, um die Form schnell in die Schließposition zu bewegen. Mechanische Verriegelungen sorgen für die Kontinuität der geschlossenen Position.
(3) Mechanisches Schließen / Verriegeln
Sie eignen sich im Allgemeinen am besten für Maschinen mit geringer Tonnage. Es funktioniert nach Hydraulikzylindern oder Kugelumlaufspindeln, die von Elektromotoren angetrieben werden. Kippklemmen, die mechanischen Druck liefern, können eine Vielzahl von Ausführungen haben. Grundsätzlich gibt es bewegliche Geräte, die den Kopf mit Gelenkverbindung nach vorne bewegen und mit der Scherentechnik arbeiten. Alle Geräte sind mit dem Hauptantrieb verbunden. Mit mechanischen Gelenkklemmen können Geschwindigkeit und Kraft (Druck) bei Bedarf an verschiedenen Stellen im Zyklus geändert werden.
Formsysteme im Spritzguss
Schraubenmechanismusformen:
Für Teile mit spiralförmigen Nuten an den zylindrischen Innen- und Außenflächen ist eine spezielle Formkonstruktion erforderlich. Die Schraube kann am Teil hervorstehen, was das Design noch komplizierter macht.
Diese Verwirrungen;
(1) Die Schraube ist mit Außengewinde, Innengewinde, intermittierend oder durchgehend,
(2) Schraubenbildung durch Drucken oder Verwenden von Metallteilen, die in das Teil eingesetzt sind,
(3) Die gewünschte Zahnradform kann in der Form vorliegen, dass der Druck von der Form abgezogen werden kann oder nicht. Bei dieser Art von Form wird die Drehung der männlichen oder weiblichen Form berücksichtigt, damit das Teil aus der Form austritt. Um diese Rotationsbewegung bereitzustellen, wird ein System, das eine Rotationsbewegung bereitstellt, auf der sich bewegenden Seite der Form angeordnet.
Hierzu können verschiedene Mechanismen eingesetzt werden.
(1) Feste Ausführung in axialer Richtung, geringe Drehung zum Entfernen des verschraubten männlichen Teils.
(2) Drückerplatten-Design; Der Schraubenbolzen dreht sich, wenn sich der Drücker bewegt.
(3) Das männliche Design, das durch Drehen gezogen wird, zieht das männliche zusätzlich zur Drehbewegung in Richtung der männlichen Platte und das Teil bleibt im Leerlauf.
(4) Rotierende Getriebeplatte Design, verschiedene hydraulisch-pneumatische, elektrische Energiequellen werden verwendet, um diese Art von Formen zu betreiben.
Zahnradsystem, Kette und Kettenrad, Zahnstange und kleines Zahnrad, Zahnstange und Ritzel werden als Antriebssysteme verwendet. Wenn die in Achsenrichtung angebrachte rotierende Außenschraube gedreht wird, wird das Teil ausgeworfen. Der Formhohlraum bleibt konstant. Die äußere Oberfläche des Drucks sollte so sein, dass sich das Stück nicht mit dem Mann dreht, während sich der Mann dreht. Zylindrische Teile mit flachen Außenflächen sind für dieses System nicht geeignet. Da die Formverbindung des Drucks gekühlt und gezogen wird, neigt das Teil dazu, sich im Formhohlraum zu drehen. Die Länge des Gewindeabschnitts des Steckers sollte idealerweise etwas kleiner sein als der Formhohlraum. Wenn der Gewindeabschnitt im Verhältnis zur Tiefe des Formhohlraums zu kurz ist, muss der Auswerferstift in der Mitte der Schraube angebracht werden, damit das Teil nach Abschluss der Schraubenentfernung aus der Form ausgeworfen werden kann.
Zwei Plattenformen:
Es ist die am weitesten verbreitete Spritzgussform in der Formenindustrie. Kurz gesagt besteht es aus männlichen und weiblichen Formen. Die Oberfläche, auf der sich diese beiden Formteile treffen, wird als Formtrennlinie bezeichnet. Sie werden bevorzugt, weil sie die billigsten und einfach zu gestaltenden Formen sind, die dem Benutzer Komfort bieten. Die Formhohlräume sind auf einer Platte montiert und die andere Platte ist auf dieser Platte geschlossen. Ein zentraler vertikaler Läufer wird zu einer festen Platte verarbeitet. Das bewegliche Teil liefert die erforderliche Schließkraft und betätigt die Antriebssysteme.

Drei Plattenformen:
Dieser Typ, der für Formen mit mehreren Kavitäten ausgelegt ist, hat auch eine weitere bewegliche Platte. Die Form besteht aus drei getrennten Platten, und wenn die Form geöffnet wird, werden diese drei Platten voneinander getrennt. Eine Öffnung bietet Platz für das auszuwerfende Teil, während die andere Öffnung Platz für den auszuwerfenden Einstiegsläufer bietet. Die Herstellung nimmt mehr Zeit in Anspruch und ist teurer als eine Zwei-Platten-Form. Bei dieser Art der Konstruktion können zentrale oder axial versetzte Tore verwendet werden. Die Technologie für kastenlose oder Heißkanalformen hat die Tendenz zur Verwendung einer Drei-Platten-Form verringert. Es hat einige Vorteile gegenüber Heißkanalformen.
(1) Dadurch können Material und Farbe während der Verwendung der Form leicht geändert werden. Es bietet einen schnellen Farbwechsel ohne langfristige Verunreinigung des Materials, indem das Angusssystem in jedem Druck gereinigt wird.
(2) Zuverlässigkeit; Dies führt zu einer Verschlechterung der Temperaturregelung in Heißkanalsystemen, zu einer Erwärmung des Systems, zu Stromausfällen und Ausfällen. Drei Plattenformen werden mit mehr mechanischen Teilen betrieben.
(3) Kosten; Formheizungen und Temperaturregelgeräte (Thermoelement, Widerstand) sind sehr teuer.

Kernformen:
Es ist auch als Winkelbewegungswerkzeuge bekannt. Die Hinterschneidungen, die verhindern, dass das Teil aus der Form ausgeworfen wird, sind auf dem Teil ausgebildet, und das Kernsystem wird in den Formen verwendet, um sicherzustellen, dass das Teil ohne Kraft in der Öffnungsrichtung der Form herauskommt. Bei solchen Konstruktionen wird die Bewegung der Teile in der Außenform angestrebt, die von der Presse nicht bewegt werden können. Durch die Verwendung von Nockenwellen oder Winkelstiften wird eine Sekundärbewegung der Formelemente erreicht. Diese Sekundärbewegung wird mit Hilfe von Pneumatik- oder Hydraulikzylindern ausgeführt.

Gefaltete Formen:
Dies sind die Formen, mit denen die Formen, die bei Herstellung mit zwei Kammern eine sehr große Form haben, in Maschinen mit niedrigerer Tonnage arbeiten können. Es kann für Teile mit hohen Produktionsmengen angewendet werden. Diese Mengen können durch die Herstellung von zwei getrennten Formen erreicht werden, aber die Kosten für Teile steigen und die Maschinenkapazität wird durch die Trennung von zwei getrennten Einspritzmaschinen negativ beeinflusst.
wird beeinflussen. Die Nut erstreckt sich bis zur zweiten Kammer und füllt die erste Kammer, nachdem die zweite Kammer gefüllt ist. Wenn die Formplatten getrennt werden, wird die mittlere Platte (weibliche Platte) von den beiden männlichen Platten getrennt und der erste Teil wird von der Form mit getrennt die Hilfe der mechanischen Drückerplatte in der zweiten männlichen Form, und der zweite Teil wird mit Hilfe von hydraulischen Drückern in der ersten männlichen Form von der Form getrennt. Es ist wirtschaftlicher als die Formkosten. In Anbetracht der Kosten des Teils ist es niedriger als die Kosten des Teils, die aus zwei getrennten Formen erhalten werden. Da zwei Teile in einer Zykluszeit aus einer einzigen Form gewonnen werden und die Maschine, die sich auf die Teilekosten auswirkt, unter Berücksichtigung des Stundensatzes, der Arbeitszeit und der Zykluszeit wirtschaftlicher ist.

Umgekehrte Muster:
In einigen Anwendungen kann die feste Seite der Injektionsmaschine männliche Formen und Drücker aufweisen, und eine weibliche Form auf der beweglichen Seite kann ein eingebautes Design aufweisen. Bei dieser Konstruktion werden Drücker mit Hilfe von hydraulischen, pneumatischen Systemen oder Federn mechanisch betätigt. Diese Anwendungen stammen aus Teilekonstruktionen. Es ist ein Formsystem, das im Allgemeinen auf kosmetische Produktteile angewendet werden kann. Wenn keine Spuren auf der sichtbaren Oberfläche des Teils (Laufbahn, Schubspur, Laufkernspuren usw.) erwünscht sind, kann es erwünscht sein, die Form durch das Männchen zuzuführen. In diesem Fall ist es notwendig, die Form in umgekehrter Reihenfolge zu gestalten. Es ist eine Methode, die die Kosten der Form erhöht und den Prozess erschwert. Sie wird nur in besonderen Fällen angewendet.

Heißkanalformen:
Bei einem idealen Spritzverfahren ist es wünschenswert, dass das Formteil eine möglichst gleichmäßige Dichte aufweist, die frei von Läufern und Graten ist. Die auf diese Weise erzielten Materialeinsparungen liegen auf einem beachtlichen Niveau. In Formen mit Heißkanalsystem sorgen elektrische Heizungen, die um den Läufer herum angeordnet sind, dafür, dass der Läufer auf einer bestimmten Temperatur gehalten wird und die Läufer sind
Verhindert das Herauskommen und spart Material. Diese Arten von Formen sind komplexer in der Konstruktion, sie sind teurer und erfordern ernsthafte Erfahrung. Die Arbeitskosten, die zum Reinigen der Grate und Läufer nach dem Entfernen des Teils erforderlich sind, sind in diesem System gering. Heißkanalsysteme haben einen offenen Strömungskanal, einen stabilen Materialfluss, einen unveränderlichen Wärmehaushalt, eine ausreichende Heizleistung, notwendige Maßnahmen gegen Wärmeausdehnung und einen schnellen Farbwechsel. Darüber hinaus bietet es die Vorteile der Läuferreinigung, Arbeitsersparnis durch mangelnde Zerkleinerungsarbeit, geringe Zykluszeit durch kurzen Öffnungsabstand, Materialeinsparung, Einsparung von Maschinenkapazität, hohe Teilequalität.

Cold Runner Formen:
Kaltkanäle werden im Allgemeinen für Teile mit kleineren Größen als diejenigen verwendet, in denen Heißkanäle verwendet werden, und folglich für Formen mit 2 oder mehr Kammern. Zusätzlich zu dem für das Teil aufgewendeten Material wird auch Material für das Läuferteil benötigt, das Schrott sein wird. Das Polymer wird bis zum Austrittspunkt der Injektionsschraube erwärmt und beginnt an dem Punkt abzukühlen, an dem es mit der Form in Kontakt kommt und sich durch Abkühlen auflöst. Das mit der Lauffläche in Kontakt stehende Polymer gefriert und bildet eine Hülle. Diese Hülle hält die Mitte des geschmolzenen Kunststoffs warm und fließt. Da das Abkühlen des Kunststoffs sehr schnell ist und es zu einem Temperatur- und Druckverlust in den Strömungskanälen kommt, bis es das Teil erreicht, werden sie für Teile mit großer Strömungsstrecke nicht bevorzugt. In Heißkanalformen beginnt dieser Temperatur- und Druckverlust, wenn das Teil gefüllt wird.

Spritzgießmaschine und Typen
Dies sind die Maschinen, die beim Spritzgießen von thermoplastischen Materialien verwendet werden. Alle Spritzgießmaschinen bestehen aus zwei Teilen. Eine Injektionseinheit und eine Kompressionseinheit. Es gibt verschiedene Maschinen in verschiedenen Technologien für verschiedene Industrieprodukte. Abgesehen von Basiseinheiten für Injektion und Kompression; Steuereinheit, Antriebssystem, Form und Formelemente sind ebenfalls Komponenten.
Injektionseinheit:
Der Hauptzweck der Einspritzgruppe besteht darin, das Kunststoffmaterial zu schmelzen und in die Form einzuspritzen. Die in die Form eingespritzte Materialmenge muss jedes Mal gleich sein, um Teile mit gleichem Gewicht und gleicher Qualität herzustellen. Dazu muss die Injektionsgruppe in der Lage sein, kontinuierlich homogenes Material bei gleicher Temperatur zu drucken. In den Anfängen der Kunststofftechnologie wurden Kolbeneinspritzmaschinen eingesetzt. In diesen Maschinen wurde Kunststoff nur mit der vom Zylinder empfangenen Wärme geschmolzen. Heutzutage werden Schrauben, die auch als Einspritzkolben dienen, in Maschinen verwendet, die weithin bevorzugt werden. Bei diesen Maschinen dreht sich die Schraube und nimmt gleichzeitig Waren aus dem Trichter. Das Material, das durch die Drehung der Schnecke nach vorne gedrückt wird, sowie die Reibungswärme, die durch die Schraube und die Hülse (manchmal auch als Zylinderofen bezeichnet) erzeugt wird, schmilzt. Das durch Schmelzen vorwärts bewegende Kunststoffmaterial wird im Düsenhohlraum gespeichert. Die Schraube kehrt zurück, bis sie den Materialspalt füllt, dh bis sie die Materialaufnahmeposition erreicht. Der während der Rückwärtsbewegung hinter der Schraube erzeugte Gegendruck hält den Hydraulikkolben auf einem bestimmten Wert konstant. Auf diese Weise wird eine homogenere Mischung erhalten, indem die Rücklaufgeschwindigkeit der Schnecke verringert wird. Nachdem der Plastifizierungsprozess abgeschlossen ist und der Düsenhohlraum mit ausreichend Material gefüllt ist, bewegt sich die Schraube mit hohem Druck wie ein Kolben vorwärts und injiziert das Kunststoffmaterial aus dem Düsenhohlraum in die Form.
Die Hauptaufgaben einer Injektionseinheit:
1- Zum Erhitzen und Schmelzen des Kunststoffmaterials, das aus dem Trichter in den Bienenstock gelangt
2- Injizieren des geschmolzenen Materials in die Form
3- Bereitstellung der erforderlichen Haltedrücke, damit das Material ein festes Produkt in der Form wird
4- Um sich bequem hin und her bewegen zu können
5- Halten Sie die Düse und die Laufbuchse mit der erforderlichen Kraft in Kontakt.
Spann- / Schraubstockeinheit:
Im Injektionsfall findet kein kontinuierlicher Prozess statt. Die Form muss geöffnet werden, damit das Produkt herauskommt, und für den nächsten Druck wieder geschlossen werden. Die Spanneinheit erledigt diese Aufgabe. Da der Kunststoff bei sehr hohen Drücken in die Form eingespritzt wird, muss die Klemmeinheit die Form während des Einspritz- und Haltedrucks fest geschlossen halten, um zu verhindern, dass sich die Form öffnet und Grate entstehen.
Die Hauptaufgaben einer Spanneinheit in einer Spritzgießmaschine sind:
1- Form schließen
2- Um die Form geschlossen zu halten, verriegeln Sie das eingespritzte Material, um daraus ein Produkt zu machen.
3- Öffnen der Form zum Entfernen des Produkts
Steuergerät:
Es braucht ein System, das heißt ein Steuersystem, das alle Funktionen der gesamten Einspritzmaschine überwachen und in einer bestimmten Reihenfolge koordinieren, die Betriebsparameter beobachten und konstant halten und jede Phase des Einspritzzyklus steuern kann. Da alle Funktionen in einer Einspritzmaschine wie in jeder Maschine in einer bestimmten Reihenfolge ausgeführt werden sollten, sollten die Start- und Endzeiten sowie die Positionen jeder Funktion unter Kontrolle gehalten und eingehalten werden.
Vollhydraulische Spritzgießmaschinen :
Alle prozessbedingten Bewegungen (Einfahren, Einspritzen, Öffnen / Schließen der Form) werden von Hydraulikmotoren oder Kolben ausgeführt. Bis in die frühen 1890er Jahre waren vollhydraulische Spritzgießmaschinen der einzige Maschinentyp auf dem Markt und sind bis heute die am meisten bevorzugte Option. Die Vorteile vollhydraulischer Kunststoffspritzgussmaschinen sind:
-
Ideal für die Herstellung von großvolumigen Teilen, hochkomplexen Teilen (Automobilindustrie), Hightech-Bauteilen mit hervorragender Oberfläche oder dickwandigen Teilen.
-
Bevorzugt, um Kernzug- und Ventilschieber zu betätigen
-
Die Preise sind in der Regel niedriger als bei Elektromodellen
-
Schnellerer Return on Investment dank einfacher Verfügbarkeit von Ersatzteilen und geringen Kosten
-
Bessere Einspritzraten, präzise Einspritzung und hohe Prozessstabilität
-
Erhöht durch die Verwendung von Hydraulikspeichern, höhere Einspritzleistung für sehr dünnwandige Teile
-
Hervorragende Spannkraft (bis 55000 kN)
-
Höhere Verschleißfestigkeit von Hydraulikteilen
-
Energieeinsparung, da die Servohydraulik nur bei Bedarf funktioniert - wenn die Maschine keine Teile produziert, sind die Motoren auch im Leerlauf und verbrauchen keine Energie
-
Dies können große Maschinen sein, die wenig Platz beanspruchen
Vollelektrische Spritzgießmaschinen:
Alle prozessbedingten Bewegungen (Einfahren, Einspritzen, Öffnen / Schließen der Form) werden von Elektromotoren (Servomotoren) ausgeführt. Bei solchen Maschinen wird kein Hydrauliksystem verwendet, es sei denn, die Maschine ist mit einem externen Hydraulikaggregat für Bewegungen wie das Ziehen des Kerns ausgestattet. Die Verwendung von Elektromotoren ermöglicht eine sehr energieeffiziente Maschine, da die Motoren nur gestartet werden, wenn Bewegung erforderlich ist. Darüber hinaus erfasst und speichert das innovative Energierückgewinnungssystem kinetische Energie, die zur Stromversorgung der Maschine verwendet werden kann.
Die Geschichte der elektrischen Spritzgießmaschinen, die in den 1980er Jahren als kleine Maschinen begann, deckt heute fast die Hälfte des Marktes ab. Und es kann jeden möglichen Größenbereich und Anwendungsbereich ansprechen.
Vorteile aller elektrischen Kunststoffspritzgussmaschinen:
-
Hohe Wiederholgenauigkeit und Präzision - elektrische Einheiten werden digital gesteuert und daher ist der Herstellungsprozess vorhersehbar und die Positionierungsgenauigkeit extrem hoch (± 0,0001 Zoll).
-
Die Energieeffizienz ist sehr hoch. Energieeinsparung von 30% bis 70% durch Energieverbrauch nur für Maschinenbewegungen
-
Schneller und effizienter Betrieb dank seiner Fähigkeit, sich parallel zu bewegen
-
Früher Start. Kürzere Startzeiten durch weniger Komponenten und Flüssigkeit (Öl), die sich erwärmen müssen
-
Im Allgemeinen leiser Betrieb (<65 dbA)
-
Ideal für die Reinraumproduktion. Saubere Umgebung ohne Hydrauliklecks
-
Kosteneinsparungen während des Produktionszeitraums - niedrigere Betriebskosten aufgrund von Energieeinsparungen, geringerer Austausch von Ölfiltern, geringere Stückkosten und geringere Materialkosten
-
Im Allgemeinen höhere Einspritzgeschwindigkeiten (bis zu 800 mm / s) und schnellere Klemmwirkung
Hybride Spritzgießmaschinen:
Einige Bewegungen werden von Elektromotoren angetrieben, andere von Hydraulik (in einigen seltenen Fällen Luft). Dies ermöglicht es, einige der Vorteile elektrischer Antriebssysteme zu nutzen, ohne die höheren Kosten solcher Systeme zu verursachen. Diese Maschinentypen sind eine sehr gute Lösung für Anwendungen, die die Vorteile der Verwendung beider Systeme in einer Maschine bieten.
Der Einspritzabschnitt besteht vielmehr aus Elektro-, Schraubstock- und Hydrauliksystem für Transport- und Absauggruppen.
Normale elektrische Einspritzmaschinen beschweren sich häufig über Spannsysteme. Die Kompressionsraten sind geringer und können bei hohen Geschwindigkeiten höhere Kosten verursachen. Die Injektion kann schnell sein, aber der Schraubstock ist seine Minus-Seite. Bei normalen hydraulischen Einspritzmaschinen ist der Schraubstock wie gewünscht, aber Beschwerden über die Einspritzgeschwindigkeit sind häufig. Max. Ihre Geschwindigkeit liegt zwischen 100 mm / s und 200 mm / s.
Vertikale Spritzgießmaschinen:
Es funktioniert genauso wie herkömmliche horizontale Maschinen, ist jedoch so positioniert, dass es auf der vertikalen Achse läuft. Dieser Maschinentyp ist in hydraulischen, elektrischen und hybriden Anwendungen erhältlich, um eine Vielzahl von Kundenanforderungen zu erfüllen. Vertikale Spritzgießmaschinen benötigen aufgrund der Richtung der Maschine sehr wenig Bodenfläche. Vertikale Spritzgießmaschinen eignen sich besonders für Einsatzformanwendungen. Komponenten können leicht in die Form geladen und durch Schwerkraft vor dem Überformen an Ort und Stelle gehalten werden. Vertikale Spritzgießmaschinen umfassen üblicherweise einen Shuttle- oder Drehtisch.
Vollelektrische Spritzgießmaschinen:
Alle prozessbedingten Bewegungen (Einfahren, Einspritzen, Öffnen / Schließen der Form) werden von Elektromotoren (Servomotoren) ausgeführt. Bei solchen Maschinen wird kein Hydrauliksystem verwendet, es sei denn, die Maschine ist mit einem externen Hydraulikaggregat für Bewegungen wie das Ziehen des Kerns ausgestattet. Die Verwendung von Elektromotoren ermöglicht eine sehr energieeffiziente Maschine, da die Motoren nur gestartet werden, wenn Bewegung erforderlich ist. Darüber hinaus erfasst und speichert das innovative Energierückgewinnungssystem kinetische Energie, die zur Stromversorgung der Maschine verwendet werden kann.
Die Geschichte der elektrischen Spritzgießmaschinen, die in den 1980er Jahren als kleine Maschinen begann, deckt heute fast die Hälfte des Marktes ab. Und es kann jeden möglichen Größenbereich und Anwendungsbereich ansprechen.
Vorteile aller elektrischen Kunststoffspritzgussmaschinen:
-
Hohe Wiederholgenauigkeit und Präzision - elektrische Einheiten werden digital gesteuert und daher ist der Herstellungsprozess vorhersehbar und die Positionierungsgenauigkeit extrem hoch (± 0,0001 Zoll).
-
Die Energieeffizienz ist sehr hoch. Energieeinsparung von 30% bis 70% durch Energieverbrauch nur für Maschinenbewegungen
-
Schneller und effizienter Betrieb dank seiner Fähigkeit, sich parallel zu bewegen
-
Früher Start. Kürzere Startzeiten durch weniger Komponenten und Flüssigkeit (Öl), die sich erwärmen müssen
-
Im Allgemeinen leiser Betrieb (<65 dbA)
-
Ideal für die Reinraumproduktion. Saubere Umgebung ohne Hydrauliklecks
-
Kosteneinsparungen während der Produktionszeit - niedrigere Betriebskosten aufgrund von Energieeinsparungen, geringerer Austausch von Ölfiltern, geringere Stückkosten und geringere Materialkosten
-
Im Allgemeinen höhere Einspritzgeschwindigkeiten (bis zu 800 mm / s) und schnellere Klemmwirkung