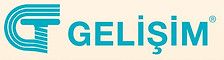


Hidrokarbonlar
Hidrojen ve karbon olmak üzere iki elementten oluşan organik bir bileşiktir. Petrol bileşiminin büyük bir kısmı değişen uzunluklardaki hidrokarbonlardan oluşur.
En küçük hidrokarbon metan, tek bir karbon atomu ve dört hidrojen atomundan oluşur. Bununla birlikte, hidrokarbonlar, zincirler, daireler ve diğer karmaşık şekiller dahil olmak üzere birçok yönden birbirine bağlanmış yüzlerce veya binlerce bireysel atomdan oluşabilir.
Hidrokarbonların özelliklerini sınıflandırmak için birkaç temel türe ayrılırlar.
Alkanlar: Bunlar doymuş hidrokarbonlar olarak adlandırılır. Yani sadece tüm karbon atomları arasında tek bağlar içerirler. Alkanlar, petrol yakıtlarının temelidir ve doğrusal ve dallı formlarda bulunurlar.
Doymamış Hidrokarbonlar: Karbon atomları arasında bir veya daha fazla çift bağa sahip olan hidrokarbonlara alken denir.
Sikloalkanlar: Bir veya daha fazla halka yapısı içeren herhangi bir hidrokarbon.
Aromatik Hidrokarbonlar: Areneler olarak da adlandırılan aromatik hidrokarbonlar, karbon atomlarının birbirini izleyen çift ve tek bağlarla bağlandığı benzersiz bir karbon molekülleri sınıfıdır. Bu molekül sınıfı, karbon atomları arasındaki bağların tek ve çift bağlar arasında bir ara bağ olduğu özel halka yapılarına sahiptir.
Bu sınıftaki moleküller, endüstriyel çözücü «benzen» içerir.
Benzen (C6H6): Diğer hidrokarbonlar gibi benzen de petrolün doğal bir bileşenidir. Oda sıcaklığında renksiz, yanıcı, tatlı kokulu bir sıvıdır ve yüksek oktan sayısına sahip olduğu için çoğu benzin karışımının bir bileşenidir.
Benzen de oldukça kanserojendir ve kemik iliği yetmezliği ve kemik kanserine neden olduğu iyi bilinmektedir. Elbette, “hoş aroması” nedeniyle tıraş sonrası ve diğer kozmetiklerde bir katkı maddesi olarak kullanıldığında kanserojenliği iyi bilinmemektedir.
En büyük benzen kullanımı (% 50), stiren ve polistren plastiklerinin ürünüdür. Ayrıca Naylon üretiminde önemli olan sikloheksan olarak bilinen bir moleküle dönüştürülür. Siklohekzan üretmek için benzenin yaklaşık% 15'i kullanılır. Böcek ilaçlarından kauçuğa kadar her şeyde daha küçük miktarlar kullanılır.
Benzen yapısı iki şekilde çizilebilir. İlkinde, çift bağ karakteri açıkça çizilir. Kısa elli versiyonda, yapıyı göstermek için halkanın içine bir daire çizilir. Benzen içindeki her bir karbon atomuna bağlı tek bir hidrojen vardır.
Aşağıdaki I. ve II. çizimleri eştir. Pratikte III. çizim kullanılır.
Benzen, renksiz, alevlenebilen, kaynama noktası 80,1 °C, erime noktası 5,5 °C olan bir sıvıdır.
Binükleer Aromatik Hidrokarbonlar: Molekülünde iki benzen halkası içeren bileşiklerdir.
Hidrokarbonlar
Hidrojen ve karbon olmak üzere iki elementten oluşan organik bir bileşiktir. Petrol bileşiminin büyük bir kısmı değişen uzunluklardaki hidrokarbonlardan oluşur.
En küçük hidrokarbon metan, tek bir karbon atomu ve dört hidrojen atomundan oluşur. Bununla birlikte, hidrokarbonlar, zincirler, daireler ve diğer karmaşık şekiller dahil olmak üzere birçok yönden birbirine bağlanmış yüzlerce veya binlerce bireysel atomdan oluşabilir.
Hidrokarbonların özelliklerini sınıflandırmak için birkaç temel türe ayrılırlar.
Alkanlar: Bunlar doymuş hidrokarbonlar olarak adlandırılır. Yani sadece tüm karbon atomları arasında tek bağlar içerirler. Alkanlar, petrol yakıtlarının temelidir ve doğrusal ve dallı formlarda bulunurlar.
Doymamış Hidrokarbonlar: Karbon atomları arasında bir veya daha fazla çift bağa sahip olan hidrokarbonlara alken denir.
Sikloalkanlar: Bir veya daha fazla halka yapısı içeren herhangi bir hidrokarbon.
Aromatik Hidrokarbonlar: Areneler olarak da adlandırılan aromatik hidrokarbonlar, karbon atomlarının birbirini izleyen çift ve tek bağlarla bağlandığı benzersiz bir karbon molekülleri sınıfıdır. Bu molekül sınıfı, karbon atomları arasındaki bağların tek ve çift bağlar arasında bir ara bağ olduğu özel halka yapılarına sahiptir.
Bu sınıftaki moleküller, endüstriyel çözücü «benzen» içerir.
Benzen (C6H6): Diğer hidrokarbonlar gibi benzen de petrolün doğal bir bileşenidir. Oda sıcaklığında renksiz, yanıcı, tatlı kokulu bir sıvıdır ve yüksek oktan sayısına sahip olduğu için çoğu benzin karışımının bir bileşenidir.
Benzen de oldukça kanserojendir ve kemik iliği yetmezliği ve kemik kanserine neden olduğu iyi bilinmektedir. Elbette, “hoş aroması” nedeniyle tıraş sonrası ve diğer kozmetiklerde bir katkı maddesi olarak kullanıldığında kanserojenliği iyi bilinmemektedir.
En büyük benzen kullanımı (% 50), stiren ve polistren plastiklerinin ürünüdür. Ayrıca Naylon üretiminde önemli olan sikloheksan olarak bilinen bir moleküle dönüştürülür. Siklohekzan üretmek için benzenin yaklaşık% 15'i kullanılır. Böcek ilaçlarından kauçuğa kadar her şeyde daha küçük miktarlar kullanılır.
Benzen yapısı iki şekilde çizilebilir. İlkinde, çift bağ karakteri açıkça çizilir. Kısa elli versiyonda, yapıyı göstermek için halkanın içine bir daire çizilir. Benzen içindeki her bir karbon atomuna bağlı tek bir hidrojen vardır.
Aşağıdaki I. ve II. çizimleri eştir. Pratikte III. çizim kullanılır.
Benzen, renksiz, alevlenebilen, kaynama noktası 80,1 °C, erime noktası 5,5 °C olan bir sıvıdır.
Binükleer Aromatik Hidrokarbonlar: Molekülünde iki benzen halkası içeren bileşiklerdir.
Hakkında
Kyäni, faydalı bileşenlerden oluşan besin takviyesi ürünlerini; benzersiz iş fırsatıyla birlikte dünya çapında 50'den fazla ülkeye ulaştırmaktadır. İdeal sağlığımızı korumak için günlük olarak Kyäni ürünlerini kullanırız, bu ürünleri başkalarıyla paylaşırız, işimizi inşa etmek ve sürdürmek için neredeyse her gün belirli bir saatimizi işe adarız ve başkalarını da Kyäni fırsatına dahil ederek veya Potato Pak ve Caring Hands programlarına katkı sağlayarak başarımızı başkalarıyla paylaşırız.
Hakkında
Kyäni, faydalı bileşenlerden oluşan besin takviyesi ürünlerini; benzersiz iş fırsatıyla birlikte dünya çapında 50'den fazla ülkeye ulaştırmaktadır. İdeal sağlığımızı korumak için günlük olarak Kyäni ürünlerini kullanırız, bu ürünleri başkalarıyla paylaşırız, işimizi inşa etmek ve sürdürmek için neredeyse her gün belirli bir saatimizi işe adarız ve başkalarını da Kyäni fırsatına dahil ederek veya Potato Pak ve Caring Hands programlarına katkı sağlayarak başarımızı başkalarıyla paylaşırız.
Sayfa Yapım Aşamasındadır.
Sayfa Yapım Aşamasındadır.
Schulungs- / Wissens- / Lösungsplattform
Verbundwerkstoffe
v. Chr. Im Jahr 3400 wurde das erste Komposit im Irak von den Mesopotamiern entwickelt. Die alte Gesellschaft klebte Holzleisten in verschiedenen Winkeln zusammen, um Sperrholz zu erzeugen.
Danach begannen die Ägypter 2181 v. Chr., Totenmasken aus in Gips getauchtem Leinen oder Papyrus herzustellen. Später begannen beide Gemeinden, ihr Material mit Lehm, Töpferwaren und Stroh zu ergänzen, um die Boote zu stärken.
Mongolen im 13. Jahrhundert Verbundfederbau begann. Sie verwendeten keine Verbundstrukturen aus Holz, Bambus, Knochen, Viehsehnen, Horn und Seide, die mit Kiefernharz verbunden waren.
Nach der industriellen Revolution begann man, Kunstharze durch Polymerisation in fester Form zu gewinnen. Auch bei Verbundstrukturen wurden neue Erfahrungen gesammelt. Es gab Entwicklungen im Bereich Bakelit durch den Chemiker Leo Baekeland. Da es nicht elektrisch leitend und hitzebeständig ist, konnte es in vielen Branchen weit verbreitet eingesetzt werden.
Die 1930er Jahre waren eine unglaublich wichtige Zeit für die Weiterentwicklung von Verbundwerkstoffen. Glasfaser wurde von Owens Corning eingeführt, der auch die erste Industrie für faserverstärkte Polymere (FRP) ins Leben rief. Harze, die in dieser Zeit entwickelt wurden, werden noch heute verwendet und ungesättigte Polyesterharze wurden 1936 patentiert. Zwei Jahre später standen leistungsfähigere Harzsysteme zur Verfügung.
Die erste Kohlefaser wurde 1961 patentiert und später kommerziell verfügbar gemacht. Dann, Mitte der 1990er Jahre, begannen Verbundwerkstoffe aufgrund ihrer relativ geringen Kosten im Vergleich zu früher verwendeten Materialien in der Herstellung und im Bau immer häufiger zu werden.
Mitte der 2000er Jahre bewährten sich Verbundstrukturen des Boeing 787 Dreamliner für hochfeste Anwendungen.
Gewichtseinsparungen sind einer der Hauptgründe dafür, anstelle herkömmlicher Verbundwerkstoffe für Komponenten zu verwenden. Obwohl Verbundwerkstoffe leichter sind, können sie stärker sein als andere Materialien; Zum Beispiel können verstärkte Kohlefasern fünfmal stärker sein als 1020er Stahl und nur ein Fünftel des Gewichts, was sie perfekt für strukturelle Zwecke macht.
Ein weiterer Vorteil der Verwendung eines Verbundmaterials gegenüber einem herkömmlichen Materialtyp ist seine thermische und chemische Beständigkeit und seine elektrischen Isoliereigenschaften. Im Gegensatz zu herkömmlichen Materialien können Verbundwerkstoffe mehrere Eigenschaften aufweisen, die oft nicht in einem einzigen Material zu finden sind.
Faserverstärkte Verbundwerkstoffe wie faserverstärkte Kunststoffe (FRP-Verbundwerkstoffe) finden zunehmend Verwendung bei der Entwicklung und Herstellung von Endprodukten für die Kommerzialisierung.
elektrische Ausrüstung
Raumstrukturen
Infrastruktur
Rohre und Tanks
Häuser können mit kunststoffbeschichteten Balken eingerahmt werden
Ein Verbundwerkstoff ist eine Kombination aus zwei Materialien mit unterschiedlichen physikalischen und chemischen Eigenschaften. Zusammen ergeben sie ein Material, das auf eine bestimmte Aufgabe zugeschnitten ist, beispielsweise stärker, leichter oder elektrisch widerstandsfähig ist. Sie können auch die Festigkeit und Steifigkeit erhöhen. Der Grund für ihre Verwendung gegenüber herkömmlichen Materialien besteht darin, dass sie die Eigenschaften ihrer Grundmaterialien verbessern und in vielen Situationen anwendbar sind.
Sie sind neue Materialien, die dadurch entstehen, dass mindestens zwei verschiedene Materialien so kombiniert werden, dass sie sich nicht ineinander auflösen. Ziel ist es, einige Eigenschaften (Leichtigkeit, Festigkeit, Flexibilität usw.) zu erreichen, die das Hauptmaterial allein nicht bietet. Es findet kein Atomaustausch zwischen den Komponenten statt, aus denen die Verbundstruktur besteht, und sie beeinflussen sich nicht chemisch. Verbundwerkstoffe bestehen im Allgemeinen aus einem Basismaterial namens „Matrix“ und einem stärkeren Material namens „Verstärkung“.
Biokomposite: Sie sind Materialien, die aus biologisch abbaubaren Polymeren (Matrix) und biologisch abbaubaren Verstärkungsmaterialien bestehen. Biologisch abbaubares Material sind Stoffe, die von lebenden Organismen abgebaut werden können. Biokomposite (BBC) aus natürlichen Biofasern sind erneuerbar, leicht, energetisch, biologisch abbaubar und umweltfreundlich. Heute kann man sagen, dass sich die Polymerwissenschaft und -technologie auf Verbundwerkstoffe aus nachwachsenden Rohstoffen konzentriert hat. (Weitere Informationen finden Sie im entsprechenden Thema)
Nanokomposite: Eine Klasse von Materialien, bei denen eine oder mehrere Phasen, aus denen der Verbundstoff besteht, eine Größe im Nanobereich (<100 nm) aufweisen. Die allgemeine Idee bei der Zugabe einer nanoskaligen Phase besteht darin, die gewünschten Hochleistungseigenschaften des Materials durch die Schaffung einer Synergie zwischen den verschiedenen Komponenten zu erreichen. Bei Partikelgrößen im Nanometerbereich sind die Wechselwirkungen an der Grenzfläche im Komposit sehr hoch, sodass sich die Materialeigenschaften enorm verbessern.
Bei der Beschreibung des Composite-Herstellungsprozesses werden häufig die folgenden Begriffe verwendet:
Teil: Das fertige Produkt, das Sie herstellen.
Stopper: Der zu kopierende Originalgegenstand aus Glasfaser oder anderen Verbundmaterialien, die zur Herstellung der Form verwendet werden. Der Plug kann ein echtes Stück oder eine Sonderform aus fast jedem Material sein.
Muster: Das Produkt, aus dem das Teil hergestellt wird. Es gibt zwei Haupttypen von Formen, männlich und weiblich. Eine Patrize ist das gleiche wie das kopierte Produkt und das Teil wird auf der Form hergestellt. Die Matrize oder Matrize ist das Gegenteil des zu kopierenden Artikels und das Teil wird in der Matrize hergestellt. Das Wort kann auch verwendet werden, um den Herstellungsprozess von Verbundwerkstoffen zu beschreiben: das Formen eines Teils.
Laminieren: Ein solides Teil aus einer Kombination aus Harz und Verstärkungsgewebe. Der Begriff kann auch verwendet werden, um den Prozess des Verlegens eines Teils zu beschreiben: Laminieren eines Teils.
Gelbeschichtung: (oder Oberflächenbeschichtung) Der Begriff Gelbeschichtung wird im Allgemeinen verwendet, um jede Oberflächenbeschichtung auf Harzbasis zu beschreiben, obwohl der Begriff technisch für Materialien auf Polyesterbasis gilt. Der Begriff Oberflächenbeschichtung kann verwendet werden, um Epoxid- oder Polyestermaterialien zu beschreiben. Oberflächenbeschichtungen sind speziell formulierte, verdickte Versionen von Harz, die auf die Oberfläche einer Form oder eines Teils aufgetragen werden können, um als kosmetische und schützende Beschichtung zu wirken.
Trennmittel: Jedes Material, das vor der Teileherstellung auf die Formoberfläche aufgetragen wird, um das Teil beim Herauskommen aus der Form zu unterstützen. Dies können Wachse, Öle oder spezielle Trennbeschichtungen wie PVA sein.
Flansch/Baffle Dam: Eine temporäre Vorrichtung, die beim Erstellen mehrteiliger Formen eingesteckt wird. Dadurch entsteht eine Oberfläche für die zu formenden Materialien, meist senkrecht zur Trennsymmetrieebene. Der Flansch hilft beim Zusammenspannen oder Verschrauben der Formteile und dient auch als Befestigungspunkt während der Vakuumbeutelvorgänge.
Matrix: Sie ist der Hauptträger, der die Struktur zusammenhält, indem sie die Verformung der Verbundstruktur verhindert.
Verstärkung: Es ist das Additivmaterial, das die Eigenschaft der Matrix charakterisiert. Sie werden als Fasern bezeichnet. Es wird verwendet, um Festigkeit, elektrische, Schall-, Wärme-, Lichtleitfähigkeit oder Isolatoren, Härte oder Weichheit, Leichtigkeit oder Gewicht, Farbästhetik, aber vor allem Wirtschaftlichkeit bereitzustellen. Als Verstärkungen werden im Allgemeinen Kohlenstoff, Glas, Aramid, Calcit, Talk verwendet. Darüber hinaus besteht das Hauptziel bei der Herstellung von Verbundwerkstoffen darin, die wirtschaftlichen Rahmenbedingungen besser zu gestalten.
Aus diesem Grund ist Calcit (CaCO3) das am häufigsten verwendete Material als Verstärkung, um die vorhandene Polymerdichte zu erhöhen.
Verbundwerkstoffe werden matrixartig in vier Klassen eingeteilt.
Polymer Matrix Composites (PMC): Da es Harze wie Epoxide und Polyester gibt, ist ihr Einsatz in der Strukturfertigung recht begrenzt; Materialien wie Glas, Aramid und Bor haben eine hohe Zug- und Druckfestigkeit, diese Eigenschaften können jedoch im festen Zustand nicht verwendet werden, sie brechen bei Werten unterhalb der optimalen Festigkeitseigenschaften, wenn Zug ausgeübt wird.
Metal Matrix Composites (MMC): Verbundwerkstoffe bestehend aus einer flexiblen Metallmatrix und Verstärkungsmaterialien; Obwohl die Matrix immer als Metall definiert wird, handelt es sich um Metalle und Leichtmetalllegierungen. Die Betriebstemperaturen von Metallmatrix-Verbundwerkstoffen liegen bei 200-800 °C; Daher ist es für Umgebungen geeignet, die Hochtemperaturanwendungen erfordern.
Keramikmatrix-Verbundwerkstoffe (CMC): Keramik- oder Glasmatrix-CMCs sind Verbundwerkstoffe, die sich für die Herstellung fortschrittlicher Konstruktionswerkstoffe eignen. Obwohl Hochtemperaturanwendungen begrenzt sind, hat es eine breite Palette von Anwendungen im Militär, in der Luft- und Raumfahrt und im kommerziellen Bereich (wie energieeffiziente Systeme und Transport).
Kohlenstoff-Kohlenstoff-Verbundwerkstoffe (CCC) : Sowohl die Verstärkung als auch die Matrixphase bestehen aus Kohlenstoff. Monolithischer Graphit ist spröde und kein starkes Material. CCCs sind relativ neu und teuer; daher sind seine Einsatzgebiete nicht weit verbreitet. Die Zugfestigkeit und der Zugmodul sind hoch und sie können diese Leistungen bis zu sehr hohen Temperaturen wie >2000 °C aufrechterhalten.
Die Entdeckung von Kohlenstofffasern in den späten 1950er Jahren führte zur Entwicklung verbesserter Materialien, die heute als Kohlenstoff-Kohlenstoff-CCC-Verbundwerkstoffe bekannt sind. Diese Verbundwerkstoffe sind eine Materialfamilie, die aus einer Kohlenstoff- (oder Graphit-) Matrix besteht, die mit Kohlenstoff- (oder Graphit-) Fasern verstärkt ist. So werden die attraktiven Eigenschaften von Carbon mit der hohen Festigkeit, Vielseitigkeit und Zähigkeit von Verbundwerkstoffen kombiniert. Die CCC-Familie ist einzigartig, da sie der einzige Basisverbundstoff ist.
Carbon-Carbon-Verbundwerkstoffe reichen von einfachen unidirektionalen faserverstärkten Strukturen bis hin zu komplexen gewebten 3-dimensionalen Strukturen. Die Vielfalt an Carbonfasern und vielseitigen Webtechniken, die derzeit verfügbar sind, ermöglichen die Anpassung des CCC an komplexe Designanforderungen. Durch die Wahl des Fasertyps, der Einfügung (oder des Fasergewebes), der Matrix- und Verbundwärmebehandlung können die Eigenschaften auf unterschiedliche Anwendungen zugeschnitten werden.
In den frühen 1960er Jahren wurden Kohlenstoff-Kohlenstoff-Verbundwerkstoffe für Hochtemperaturanwendungen in der Luft- und Raumfahrt entwickelt, wie zum Beispiel Nasenkegel und Raketendüsen. Diese Verbundwerkstoffe können auf höhere Festigkeiten und Härten als andere technische Metalllegierungen zugeschnitten werden und können diese Eigenschaften im Gegensatz zu Metallen bei erhöhten Temperaturen beibehalten, wie in Abbildung 1 gezeigt.
Die Herstellungskosten dieser Materialien sind jedoch hoch und dies hat ihre Verwendung derzeit hauptsächlich auf Luft- und Raumfahrt- und Militäranwendungen beschränkt. Daher führt eine Verbesserung der CO2-Effizienz zu einer Reduzierung der Kosten. Eine Druckerhöhung von Umgebungstemperatur auf 100 MPa, bei der eine Kohlenstoffausbeute von 50 % erreicht wird, erhöht die Kohlenstoffausbeute auf 90 %. Dies ist die Grundlage für die Hochdruckkarbonisierung und Pyrolyse, eine Technik, die von TWI et al. erforscht wurde.

Verstärkter Kunststoff: Da ca. 90 % der Verbundwerkstoffe aus Matrices auf Polymerbasis (Kunststoff) hergestellt werden, sind Verstärkungen für Verbundwerkstoffe Auch Kunststoffe genannt.
Bei Verbundwerkstoffen verbleiben die Fasern im Material. Sie sind die Matrizen, die das Material umgeben und äußeren Einflüssen ausgesetzt sind. Aus diesem Grund bestimmen Matrizen die Grundeigenschaft von Kompositen.


Grundlegende Funktionen der Matrix
Durch das Zusammenhalten der Matrixfasern wirkt die Brücke entsprechend der Lastübertragung auf die Fasern und verleiht der Struktur Steifigkeit und Form. Die Matrix isoliert die Fasern voneinander. Somit verhalten sich die Fasern in einem Aspekt unabhängig voneinander. Dadurch wird beispielsweise die Rissausbreitung gestoppt und verlangsamt.
Die Matrix bietet eine gute Oberflächenqualität. Die Matrix schützt die Fasern vor mechanischen Beschädigungen wie Abrieb und verschiedenen chemischen Einflüssen.
Abhängig von den Eigenschaften des gewählten Matrixmaterials werden auch die Gebrauchseigenschaften des Verbundwerkstoffs wie Duktilität und Schlagzähigkeit beeinflusst. Eine duktilere Matrix kann die Bruchzähigkeit der Struktur erhöhen. Beispielsweise werden Verbundwerkstoffe auf thermoplastischer Basis wegen ihrer hohen Zähigkeit gewählt. Die Eigenschaften der verwendeten Matrix und deren Verträglichkeit mit der Faser beeinflussen maßgeblich die auftretenden Schadensmoden (Mechanismen).
Eine Matrix muss eine hohe Haftfähigkeit an der Faser aufweisen. Mit zunehmender Haftfähigkeit wandern die Lasten von der Matrix auf die Bewehrung.
ausreichender Betrag überwiesen werden kann. Außerdem wird ein Aufspalten oder Brechen an der Faser-Matrix-Grenzfläche unter Spannung verhindert.
Erwartete Eigenschaften von Matrizen, die bei der Herstellung von Verbundwerkstoffen verwendet werden:
1. Gute mechanische Eigenschaften haben
2. Gute Haftung
3. Gute Zähigkeitseigenschaften
4. Es kann als resistent gegen Umwelteinflüsse eingestuft werden.
Harzarten
Eine Verbundstruktur besteht aus einem wärmehärtenden Harz, das in Verbindung mit einer Art Verstärkung verwendet wird, wie beispielsweise einem Glasfasergewebe. Es gibt drei Haupttypen von bei Raumtemperatur härtenden Harzen, die bei der Herstellung von Verbundwerkstoffen verwendet werden: 1- Polyester, 2- E- Pocken , 3- Vinylester
Es ist ein Allzweckharz, das für eine Vielzahl von Anwendungen geeignet ist. Als Katalysator, um den Aushärtungsprozess zu starten Methylethylketonperoxid (MEKP) sollte benutzt werden. Die Katalysegeschwindigkeiten können mit Polyesterharzen variiert werden, um sich an verschiedene Umgebungsbedingungen anzupassen. Bei dünnen Laminaten oder beim Spritzen von Gelcoat als Decklack kann die Oberfläche an der Luft klebrig bleiben und nicht richtig aushärten. Um eine vollständige Aushärtung zu erreichen, können dünne Laminate oder Decklacke entweder eine Lösung aus Styrolwachs oder eine Schicht darüber sein, um die Luft abzudichten. Polyvinylalkohol (PVA) Lösung aufgesprüht werden. Bei ersterem "schwimmt" das Wachs beim Aushärten des Harzes auf der Oberfläche und wirkt als Luftbarriere. Styrolwachs Nach dem Aushärten sollte es geschliffen und PVA sollte mit warmem Wasser abgespült werden. Ebenfalls:
Sie sind die am häufigsten verwendeten Harze in der Verbundwerkstoffindustrie.
Günstiger, einfach zu bedienen
Bietet eine gewisse Korrosionsbeständigkeit
Verzeihender als Epoxide
Heilt schnell
Es ist tolerant gegenüber extremen Temperaturen und Katalysatoren.
Es ist in seinen Maßen nicht so nachsichtig wie Polyesterharze, aber Epoxide bieten eine größere Festigkeit und Dimensionsstabilität des Teils. Sie haften auch auf anderen Materialien besser als Polyesterharze. Epoxidhärter Verhältnisse können nicht geändert werden und angemessene Temperaturen (mindestens 70 Grad F) müssen während des Härtungsprozesses aufrechterhalten werden. Epoxidharzsysteme sind tendenziell teurer als Polyesterharze, sind aber bei einigen Reparaturanwendungen, wie beispielsweise Sheet Molded Compound (SMC), praktisch notwendig.
Für Verbundteile, die höchste Festigkeit erfordern, verwenden die Hersteller ein Epoxidharz. Epoxide übertreffen im Allgemeinen Polyester und Vinylester in Bezug auf Dimensionsstabilität und eine bessere Bindung mit anderen Materialien sowie erhöhte Festigkeitseigenschaften.
Vinylester Harze:
Es hat meist Qualitäten, die zwischen Polyester- und Epoxidharzen liegen. Es übertrifft jedoch sowohl in den Bereichen Korrosionsbeständigkeit, Temperaturbeständigkeit (gut bis 300 Grad F) als auch Zähigkeit. Häufige Anwendungen sind die Reparatur von Bootsrümpfen, der Bau von vollen Tanks und die Auskleidung von chemischen Lagertanks. Wie Polyesterharz, MEKP katalysiert durch , aber der Vinylester hat eine kürzere Haltbarkeit von drei Monaten.
Vinylesterharz gilt als Hybrid aus Polyester und Epoxid – das heißt, seine Verarbeitungseigenschaften, Eigenschaften und sein Preis liegen oft zwischen den beiden anderen. Der Unterschied von Vinylester liegt in seiner hohen Korrosions-, Temperatur- und Dehnungsbeständigkeit.
Herstellungstechniken für Verbundwerkstoffe
Nasser Boden
Das Bauteil wird in einer Form geformt, indem mehrere Schichten von Verstärkung und nassem Harz aufgetragen werden, die mit einer Walze verteilt werden, bis die gewünschte Dicke erreicht ist. Anschließend wird das Harz ggf. unter Anwendung von Wärme ausgehärtet, um das fertige Bauteil herzustellen.
Dieses Verfahren wird in der Schifffahrtsindustrie häufig verwendet, um glasfaserverstärkte Polyesterharze herzustellen. Die Materialkosten sind relativ gering und das Verfahren sehr flexibel. Es ist jedoch arbeitsintensiv und hat den Nachteil hoher Styrolemissionen.
Sprühmethode
Mit einer Spritzpistole werden geschnittene Faserverstärkungen und nasses Harz auf eine Form aufgetragen, bis die gewünschte Materialstärke erreicht ist. Das Harz wird dann ausgehärtet. Das Verfahren ist schneller und kostengünstiger als die Nassverlegung, jedoch sind die mechanischen Eigenschaften geringer.
Das Verfahren wird typischerweise für große, relativ einfache Strukturen wie Wannen, Rümpfe und Lagertanks verwendet.
Formpressen (SMC)
(Sheet Molding Compound) Eine Faser- und Harzcharge, die eine Sheet Molding Compound oder Bulk Molding Compound ist, wird in eine vorgeheizte Form gegeben, die dann versiegelt und unter Druck gehalten wird, bis das Harz aushärtet. Das Verfahren kann eine Oberflächengüte der Klasse A erzeugen, und die Ähnlichkeit mit dem Stanzprozess für Bleche hat zu Anwendungen in der Automobilindustrie geführt.
Durch die hohe Investition in beheizte Werkzeuge ist das Verfahren nur für mittlere bis hohe Stückzahlen geeignet.
Die Formtemperatur liegt zwischen 120-170 °C. Formzeit und Formdruck; Die Größe des Teils variiert je nach Dicke und SMC-Typ. Die Vorteile von SMC-Preforming-Compounds in Bezug auf Gesamtkosten-Leistungs-Verhältnis gegenüber Materialien wie Stahl, Aluminium und anderen Zinkmetallgussteilen werden von Konstrukteuren und Ingenieuren häufig genannt. Viele Teile können in einem einzigen Werkzeug kombiniert werden. SMC-Produkte sind leicht und haben hohe Härte- und Festigkeitseigenschaften. SMC-Formen ist im Allgemeinen weniger teuer als das Metallformverfahren, da es mit einer einzigen Ausrüstung verarbeitet werden kann, im Gegensatz zu den beim Metallformen erforderlichen mehreren Ausrüstungen. Darüber hinaus erfolgt der Bau von SMC-Formanlagen in kürzerer Zeit. Die Summe all dieser Vorteile macht SMC-Composite-Produkte für Automobilhersteller besonders attraktiv. Auf den heutigen Automobilmärkten suchen Unternehmen nach Wegen, um mit Massenproduktion und schnelleren Konstruktions-/Produktionsprogrammen wirtschaftliche Unterschiede bei Pkw- und Lkw-Modellen zu schaffen. Aus diesen Vorteilen entwickelt SMC beeindruckende Leistungen.
Obwohl der Kapitalaufwand für die Herstellung und das Formen von SMC im Vergleich zu Metallen recht gering ist, ist er deutlich höher als bei anderen Verbundverfahren. Daher ist es entscheidend, dass die Produktion von SMC-Teilen vom wirtschaftlichen Verlauf aller Ausgaben, dem Produktionsvolumen, den Kosten des Endprodukts und den Nebenoperationen abhängt. Da SMC-Produkte begonnen haben, Teile aus traditionellen Materialien auf dem Markt zu ersetzen, ist es wichtig geworden, Leistungs- und Wirtschaftlichkeitsanalysen von konkurrierenden Materialien genau und präzise durchzuführen. Anlagerisiken sind für SMCs recht hoch
Auch in der Hausgeräteindustrie steigt die Nachfrage nach SMC-Anwendungen. So kombiniert beispielsweise die Herstellung einer Spülmaschinen-Innentür von SMC traditionell mehrere unterschiedliche Teile mit einem einstufigen Spritzguss im Vergleich zur Stahltürkonstruktion. Die Anwendung der SMC-Geschirrspülerabdeckung beweist, dass SMC aufgrund seiner hervorragenden Leistung in einem Produkt, das einer chemischen Umgebung ausgesetzt ist, auf viele Arten verwendet werden kann. Andere Anwendungen von SMC-Haushaltsgeräten umfassen Klimaanlagen, Kühlschränke, Fritteusen, Computer und Bürobedarf.
Spritzguss
Die gegossene Formmasse wird erhitzt und in eine beheizte Form gespritzt, wo sie unter Druck gehalten wird, bis das Harz aushärtet. Das Verfahren wird bei relativ kleinen Bauteilen eingesetzt, bei denen eine kurze Taktzeit erreicht werden kann. Aufgrund der hohen Werkzeugkosten ist das Verfahren nur für mittlere bis hohe Stückzahlen geeignet.
Resin Transfer Moulding (RTM)
(Resin Transfer Moulding) Ein Faservorformling oder Stoff wird in eine erhitzte Form gelegt. Das Reaktionsharz wird gemischt und unter Druck in die Form eingespritzt. Der Druck wird aufrechterhalten, bis das Harz aushärtet und das Teil entfernt wird. Das Verfahren eignet sich für komplexe, hochbelastete Teile und wird in den unterschiedlichsten Branchen eingesetzt. Das vakuumunterstützte Resin Transfer Moulding (VARTM) ist eine Verfahrensvariante, bei der Vakuum an das geschlossene Werkzeug angelegt wird, wodurch das Harz unter reduziertem Druck eingespritzt werden kann. Die Belastungen der Werkzeuge sind daher geringer, so dass kostengünstigere, größere Werkzeuge verwendet werden können, um große Strukturen wie Rümpfe oder Windturbinenblätter herzustellen. Eine weitere Variante ist das Structural Reaction Injection Moulding (SRIM). Dabei werden hochreaktive Harze verwendet, sodass die Form zum Aushärten des Harzes nicht erhitzt werden muss, aber oft erhitzt wird, um die Zykluszeit zu verkürzen.
RTM-Teile ermöglichen je nach Prozess- und Konstruktionsbedingungen eine große Anzahl von Teilen pro Werkzeug und Stunde. Da es sich bei RTM um ein geschlossenes Formensystem handelt, setzen sie weniger flüchtige organische Stoffe frei als offene Formen. Die Zykluszeiten der Form sind kürzer als bei Handauflege- und Spritzverfahren. Die Kosten von RTM-Formen sind niedriger als die von Formen, die bei anderen geschlossenen Formverfahren verwendet werden. Beide Oberflächen der Formteile sind glatt. Füllsysteme reduzieren Kosten, fügen Leistungsmerkmale wie Nichtbrennbarkeit und Rauchfreiheit, bessere Oberflächenoptik und höhere Bruchfestigkeit hinzu.
Die Kosten für Form und Ausrüstung sind höher als bei Handlaminier- und Spritzverfahren. RTM ist ein Produktionsverfahren mit mittlerem Produktionsvolumen. Der Prozess ist komplexer, wenn es um die Einstellung von Einspritzdrücken, Werkzeugkonstruktion und -herstellung sowie Verschluss- und Dichtungssystem geht.
Wichtige RTM-Anwendungen; LKW-Karosserieteile, Autokarosserieteile, Buspaneele, Spoiler, Instrumententafeln, medizinische Geräte, Lagertanks, Fahrzeugsitze, chemische Pumpen, Schiffsteile wie kleine Boote, Windkraftturbinenblätter, Flugzeugteile, Geschosskörper, Fahrradkörper und Türen.
Filamentwicklung
Ein Faserstrang wird durch ein Harzbad geführt und unter Spannung auf einen konvexen Dorn aufgebracht. Der Dorn wird gedreht und die Faserfreigabe wird bewegt, um die Fasern in die gewünschte Geometrie zu bringen, bis die gewünschte Dicke erreicht ist. Der Verbundstoff wird dann, falls erforderlich, unter Verwendung einer hohen Temperatur aushärten gelassen. Der Prozess kann für die Großserienproduktion automatisiert werden und wird für rohrförmige Strukturen wie Rohre und Antriebswellen sowie speziellere Strukturen wie Druckbehälter oder Monocoque-Fahrradrahmen verwendet. Bei den letzten beiden Anwendungen verbleibt der Dorn im Bauteil. In einer Variante des Verfahrens kann ein vorimprägniertes Faserkabel oder geschlitztes Prepreg verwendet werden, wodurch ein Harzbad überflüssig wird, aber ein Hochtemperatur-Härtungsschritt erforderlich ist.
Prepreg
(vorimprägnierte Faser) besteht aus mit Harz imprägnierten Fasern, Geweben oder Filzen. Duroplastische Prepregs enthalten Härter im Harz und sind daher nur begrenzt haltbar und werden in der Regel gekühlt gelagert. Vor der Verwendung wird das Prepreg auf Raumtemperatur gebracht, um Kondensation zu vermeiden, und die Lagen werden in die gewünschte Form und Richtung geschnitten. Diese werden mit einem Zylinder in einer Form der gewünschten Dicke gestapelt, um das Einschließen von Luft zu verhindern. Das Laminat wird in einem evakuierten Vakuumbeutel versiegelt und dann wird das Teil in einem herkömmlichen Ofen oder einem Autoklaven unter zusätzlichem Druck ausgehärtet. Die Autoklavenverarbeitung bietet weniger Porosität und überlegene mechanische Eigenschaften, erfordert jedoch eine langsame Zykluszeit und eine teure Ausrüstung, insbesondere für große Komponenten. Prepreg wird dort eingesetzt, wo hohe mechanische Eigenschaften erforderlich sind und hohe Bearbeitungskosten gerechtfertigt werden können. Beispiele sind Luft- und Raumfahrtstrukturen, Sportartikel und Rotorblätter von Windkraftanlagen.
Praktisch bei der Produktion entfällt die zusätzliche Verwendung von Harz und Härter und auch der Verlegeprozess ist durch die Haftung auf der Formoberfläche übereinander und die Fasertrennung im Vergleich zu Nicht- harzgetränkte Fasern. Darüber hinaus ist die Aushärtezeit kürzer als bei den Methoden Handlaminieren, Vakuuminfusion und Vakuumbeutelverfahren.
Da der Harzgießprozess bereits stattgefunden hat, gibt es kein Trockenbleiben oder zu viel Harz aufsaugen. Dadurch wird sichergestellt, dass Standardprodukte ohne Festigkeitsverlust im Produkt erhalten werden. Je nach verwendetem Prepreg-Typ variiert das Harz/Faser-Verhältnis zwischen 35 % und 50 %.
Die Herstellung mit Prepreg hat sowohl Vorteile als auch einige Nachteile. Erstens sind die Herstellungsmethoden im Vergleich zu anderen ziemlich teuer. Beim Autoklavenverfahren wird die Temperatur entsprechend der Aushärtungskurve um 120-180oC eingestellt und gleichzeitig unter einem Druck von 3-7 MPa gearbeitet. Bei der Ofenherstellung sollte die Härtungstemperatur auf geeignete Temperaturen eingestellt werden. Diese Arten von Autoklaven und Öfen sind ziemlich teure Industrieprodukte.
Auch die Lagerbedingungen der Prepregs stellen den Hersteller vor große Herausforderungen. Obwohl es Sorten gibt, die bis zu 4-6 Wochen unter Raumbedingungen gelagert werden können, herrschen im Allgemeinen Gefrierbedingungen um -20oC. Sie müssen auch verwendet werden, nachdem sie aus dem Gefrierschrank genommen wurden.
Pultrusion:
Es handelt sich um eine Produktionstechnologie, bei der das Glasfaserverstärkungsmaterial mit einem dafür geeigneten Harz kombiniert und aus einer heißen Form gezogen wird.
In der Anlage werden Glasfasern und Glasfaserfilz mit Harz benetzt und im heißen Werkzeug zu festem Material polymerisiert. Es ist ein geeignetes Verfahren zur Herstellung von Industrieplatten, Profilen und elektrischen Industrieplatten, Profilen.
Die Faserkabel werden einem Spulenaufhänger entnommen und durch ein Harzbad geführt, dann durch eine beheizte Extrusionsdüse gezogen, die das Harz aushärtet, um ein extrudiertes Teil mit axialer Verstärkung und konstantem Querschnitt herzustellen. Zu den Anwendungen gehören Gitterroste, Treppenprofile, Brückenteile und Geländer. Der Prozess ist automatisierbar und verwendet kostengünstige Rohstoffe, wodurch er für Großserienanwendungen geeignet ist.
Die Matrixharze im Pultrusionssystem sind:
Orthophthalische ungesättigte Polyesterharze
Isophthalsäure-ungesättigte Polyesterharze
Vinylesterharze
Epoxidharze
Verstärkungsmaterialien sind:
Glasfaser
Glasfaser-Roving
Weiter Fiberglas
Glasfaser gewebt
Oberfläche Tüll
Glasfaser-Kombi
Glasfaser Multiaxial
Vakuuminfusion:
Vakuuminfusion, auch Harzinfusion genannt, ist ein Herstellungsverfahren, bei dem Vakuumdruck verwendet wird, um Harz in ein Laminat zu treiben. Trockene Materialien werden in die Form gegeben und Vakuum wird angelegt, bevor das Harz hinzugefügt wird. Wenn ein vollständiges Vakuum erreicht ist, wird das Harz durch das Vakuumrohr in das Laminat gedrückt. Das Vakuuminfusionsverfahren bietet ein besseres Faser-zu-Harz-Verhältnis als manuelles Legen oder Vakuumieren.
Vakuum wird verwendet, um zu bewirken, dass ein Harz mit niedriger Viskosität einen faserigen Vorformling imprägniert. Am häufigsten führt dies dazu, dass das Harz über die Oberfläche des Vorformlings fließt und dann durch die Dicke imprägniert wird, wodurch die Strecke minimiert wird, die das Harz durch den Vorformling zurücklegen muss. Das Verfahren eignet sich gut für große Teile wie Bootsrümpfe oder Windturbinenblätter. Das Werkzeug muss im Betrieb keine nennenswerten Lasten tragen.
Die Vakuuminfusion bietet eine Reihe von Verbesserungen gegenüber herkömmlich vakuumverpackten Teilen.
Zu diesen Vorteilen gehören:
Besseres Faser-Harz-Verhältnis
Weniger Abfallharz
Sehr konsequenter Einsatz von Harz
Unbegrenzte Installationszeit
Reiniger
Induktionsheizung:
Dank der Dicke von kohlefaserverstärkten thermoplastischen Verbundwerkstoffen kann die Induktionserwärmung erstmals präzise gesteuert werden. Beim Einlegen der zu fügenden Verbundbauteile werden dünne elektrisch isolierende Schichten (Gaze) zwischen die Schichten gelegt, wo keine Induktionserwärmung erforderlich ist. Der Einbau dünner Isolierschichten ist nur in einem der Fügeteile und nur zwischen benachbarten, nicht ausgerichteten Kohlenstoffschichten nahe der Fügestelle notwendig.
Erwärmungsversuche haben gezeigt, dass die Technik erfolgreich die Erzeugung von elektrischen Wechselströmen verhindert, die während der Induktionserwärmung induziert werden. Um das Material wie beim Schweißen oder Aushärten üblich zu erhitzen und zu schmelzen, wird zwischen Schichten, in denen keine Isolierschichten (Gaze) vorhanden sind, ein elektrischer Strom induziert. Auf diese Weise kann die Konzentration der Induktionserwärmung über die Dicke des Materials genau gesteuert werden. Dieser Ansatz verhindert eine Überhitzung der Außenfläche der Bauteile und verbessert die Qualität der hergestellten Verbindungen.
Das Verfahren kann als Schweißverfahren in Betracht gezogen werden, das Vorteile gegenüber bestehenden Verfahren nach dem Stand der Technik bietet, insbesondere bei dicken Teilen (dicker als 4 mm). Auch die Werkzeugkosten werden im Vergleich zur neuesten Technologie minimiert. Eine breitere Anwendung der Technik sollte als fokussierter Erwärmungsprozess für Anwendungen wie das Kleben von duroplastischen Verbundwerkstoffen betrachtet werden, bei denen der Wärmefokus an der Grenzfläche zum Aushärten eines Klebstoffs verwendet werden kann.
In dieser Technik: Beim Induktionsschweißen von Kohlefaser-Verbundwerkstoffen nach dem heutigen Stand der Technik muss ein gut wärmeleitendes Kühlkörpermaterial in das der Induktionsspule am nächsten liegende Verbundteil eingebracht werden. Dies entfernt überschüssige Wärme von der Oberfläche und ermöglicht eine ausreichende Erwärmung der Schweißgrenzfläche.
Leitfähige und Isolator-(Isolator-)Schichten sind in einem Winkel angeordnet, um den Wärmefluss zu sehen.
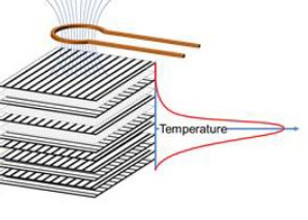

Bir dakikalık ısıtma sonrası termal görüntü ve alt ve üst katmanlardaki sıcaklık-zaman değişim grafiği
Thermoplastische Verbundwerkstoffe (TPCs) können durch Thermoformen schnell verarbeitet werden, was sie zu einer attraktiven Option für die Luft- und Raumfahrtindustrie macht. Einer der Gründe dafür ist die begrenzte Technologie für das Engagement. TWI hat vor kurzem ein neues Verfahren erfunden, um die Kontrolle des Induktionsschweißens von thermoplastischen Verbundwerkstoffen ohne zusätzliche Konservierungsmittel zu verbessern. Das Hinzufügen einer dünnen Schicht elektrisch isolierender (Gaze) zwischen benachbarten Schichten, die nicht ausgerichtete Kohlefasern enthalten, verhindert die Bildung von elektrischen Pfaden und die volumetrische Erwärmung wird deaktiviert. Die Technik von TWI hat den Vorteil, dass die erzeugte Wärme an der Grenzfläche der Verbindungsstelle kondensiert wird, wodurch das Problem beseitigt wird, überschüssige Wärme von der Verbundoberfläche abzuführen, um thermische Schäden zu vermeiden. und verbessert somit die Kontrolle des Prozesses. Mit dieser Technik wurden Fügefestigkeiten von bis zu 32 MPa erreicht.
Eine der Einschränkungen von Verbundwerkstoffen ist die Montage vorgefertigter Teile. Bei duroplastischen Verbundwerkstoffen sind aufwendige Vorbehandlungs- und Erwärmungsmechanismen erforderlich. Thermoplastische Verbundwerkstoffe tragen besser zur Verklebung bei, aber es besteht immer die Herausforderung, sicherzustellen, dass nur die Grenzfläche erwärmt wird, ohne dass Fremdmaterial in der Klebelinie vorhanden ist.
In den letzten Jahren ist das Interesse an thermoplastischen Verbundwerkstoffen, insbesondere für High-End-Anwendungen wie die Luft- und Raumfahrt, erneut gestiegen. Die prognostizierten Produktionsraten für Single-Aisle-Flugzeuge übersteigen die derzeitige wirtschaftliche Produktionskapazität von duroplastischen Verbundwerkstoffen. Im Vergleich zu Duroplasten können thermoplastische Verbundwerkstoffe kürzere Verarbeitungszeiten bieten, um höhere Produktionsraten zu erreichen, und bieten potenzielle zusätzliche Vorteile wie gute Lösungsmittelbeständigkeit, unbegrenzte Haltbarkeit und bessere Zähigkeit (Schlagzähigkeit). Thermoplastische Verbundwerkstoffe können schneller verarbeitet werden, indem die Polymermatrix ausreichend erhitzt wird, um ein Thermoformen zu ermöglichen, ähnlich wie beim Stanzen von Blechkomponenten. Dies macht TPCs zu einer attraktiven Option für die Luft- und Raumfahrtindustrie, aber für strukturelle Anwendungen gibt es noch keine signifikante Verbreitung von TPCs.
Einer der Gründe dafür ist die Teilnahme. Obwohl die Verwendung von Verbundwerkstoffen eine endkonturnahe Fertigung bieten kann, besteht normalerweise die Notwendigkeit, Komponenten aus einer Vielzahl von Gründen zusammenzubauen, wie z.
kostengünstiger
Bauteile sind zu groß um als Einzelstück gefertigt zu werden
Es werden Hybridmaterialien verwendet, die unterschiedliche Produktionsbedingungen erfordern
Komponenten werden an verschiedenen physischen Standorten hergestellt
Die derzeit gebräuchlichen Klebeverfahren wurden von denen zum Verbinden von Metallstrukturen adaptiert, da sich die Flugzeugindustrie auf beträchtliche Leistungsdaten und -techniken verlassen hat.
Duroplaste werden traditionell durch mechanisches Kleben oder Kleben verbunden. Mechanisches Verbinden erfordert das Herstellen von Löchern, die die tragenden Fasern schneiden und Spannungskonzentrationen um die Löcher herum liefern. Das Kleben ist nicht störungsfrei und erfordert oft das Erhitzen großer vorgefertigter Teile in einem Ofen, um den Klebstoff in einer relativ kleinen Fuge auszuhärten.
Im Gegensatz zu Duroplasten können TPCs jedoch durch Schmelzkleben (Schweißen) verbunden werden; ein Prozess, der beim Bohren keine Schäden verursacht und Gewichtseinsparungen durch Entfernen des Befestigungselements und mehr Geschwindigkeitsvorteile durch den Wegfall des Lochbohrschritts bietet. Das Schweißen von thermoplastischen Verbundwerkstoffen ist jeder Prozess, der die Grenzfläche auf eine Temperatur über der Glasübergangstemperatur Tg (für amorphe Polymere) oder dem Schmelzpunkt Tm (für halbkristalline Polymere) erhitzt. Unter Druckbeaufschlagung können sich die Polymerketten beim Abkühlen über die Grenzfläche ausbreiten und eine Schweißverbindung bilden. Das Verfahren kann schnell sein und erfordert wenig oder keine Oberflächenvorbereitung.
Seit der Einführung thermoplastischer Verbundwerkstoffe wie APC-2 (AS4 kohlenstofffaserverstärktes Polyetheretherketon oder PEEK) in den 1980er Jahren wurden viele Studien zum Schmelzbonden von TPCs durchgeführt. Drei der zahlreichen verfügbaren Schmelzverbindungstechniken waren Gegenstand zahlreicher Forschungsstudien, da sie für industrielle Anwendungen am besten geeignet sind; Induktion, Widerstandsimplantat und Ultraschall.
Beim Induktionsschweißen wird Wärme durch Joulesche Verluste aus Wirbelströmen erzeugt, die als Reaktion auf das angelegte magnetische Wechselfeld induziert werden. Das Magnetfeld wird durch einen elektrischen Wechselstrom erzeugt, der durch eine leitfähige Arbeitsspule fließt. Induzierte Wirbelströme können in einem Metallimplantat fließen, das an der Schweißgrenzfläche platziert ist, oder in Kohlenstofffasern in den Hauptverbundwerkstoffen.
In den letzten Jahren wurde Induktionsschweißen angewendet, um thermoplastische Verbundwerkstoffe zu verbinden. Fokker Aerostructures entwarf und entwickelte das Gulfstream G650 Heckteil und installierte das Seiten- und Höhenruder Industrialisierung einer neuen Methode des Induktionsschweißens für Die Fiberforge Corporation wandte die Technik auch zur Montage von Teilen auf dem Sikorsky CH-53K an. Die Technik ist jedoch noch nicht weit verbreitet, und ein Grund ist die schlechte Kontrolle des Prozesses, um eine thermische Zersetzung zu verhindern. . Was benötigt wird, ist eine Technik, die die Wärme dort konzentriert, wo sie benötigt wird, ohne zusätzliche Halter an der Schweißgrenzfläche anzubringen.
Beim Induktionsschweißen von Kohlefaserverbundwerkstoffen nach dem heutigen Stand der Technik muss ein gut wärmeleitendes Kühlkörpermaterial in das der Induktionsspule am nächsten liegende Verbundteil eingebracht werden. Dadurch wird überschüssige Wärme von der Oberfläche abgeführt und die Schweißgrenzfläche kann sich ausreichend erwärmen.
Es ist bekannt, dass benachbarte, nicht ausgerichtete Schichten erforderlich sind, damit Wirbelströme in kontinuierlichen Kohlenstoffaser-Verbundwerkstoffen induziert werden. Eine geschichtete Struktur, bei der alle Verstärkungsfasern unidirektional in die gleiche Richtung ausgerichtet sind, wird nicht durch Induktion volumetrisch erwärmt, da kein geschlossener elektrischer Pfad erzeugt werden kann. Glücklicherweise verwenden die meisten strukturellen Verbundanwendungen eine quasi-isotrope Anordnung, um die erforderliche mechanische Leistung zu erreichen, und können daher durch Induktion volumetrisch erwärmt werden.
Wenn die benachbarten nicht ausgerichteten Schichten des semiisotropen Laminats ausreichend getrennt sind, um einen Kontakt zwischen den Kohlefasern in den benachbarten Schichten zu verhindern, können keine geschlossenen elektrischen Pfade mehr gebildet werden und somit wird die volumetrische Erwärmung deaktiviert. Diese Trennung kann erreicht werden, indem eine dünne elektrisch isolierende Schicht (Gaze) zwischen benachbarten Schichten angeordnet wird, die fehlausgerichtete Kohlenstofffasern enthalten (Abbildung 1). Diese Technik, die eine spezielle Kombination von Parametern und Eigenschaften verwendet, hat den Vorteil, dass die erzeugte Wärme um die Verbindungsgrenzfläche konzentriert wird und nicht in der Nähe der oberen Oberfläche des Verbundwerkstoffs, wo die Nähe der Induktionsspule am größten ist. Dies konzentriert die Wärme dort, wo sie benötigt wird, und beseitigt das Problem, überschüssige Wärme von der Verbundstoffoberfläche abzuführen, um eine thermische Beschädigung zu verhindern. Die zur Herstellung der Schweißverbindung erforderliche Wärme wird durch das Entfernen der Isolierschichten in der Nähe der Schweißnahtstelle erzeugt. Da außerdem die Intensität des in das leitfähige Material induzierten Stroms von der Oberfläche aus exponentiell abnimmt, brauchen die Isolierschichten nur in einem der verbundenen Teile angeordnet zu werden; der Arbeitsspule am nächsten.
Die bei dieser Technik erzeugte Wärme reicht aus, um thermoplastische Verbundwerkstoffe zu verschmelzen und auch zum Aushärten von Klebstoffen verwendet zu werden; Ein Verfahren zum Fügen von duroplastischen Verbundwerkstoffen.
Um den fokussierten Heizeffekt zu demonstrieren, wurden zwei thermoplastische Verbundlaminate hergestellt, die jeweils drei Schichten Carbon/PEEK in 0/90-Richtung enthalten. Ein Laminat ("Leiter") wurde herkömmlich hergestellt, um den Kontakt benachbarter nicht ausgerichteter Lagen zu ermöglichen. Das andere Laminat ("Isolator") wurde unter Verwendung einer dünnen Isolationsschicht zwischen benachbarten nicht ausgerichteten Schichten verlegt. Als Material für die Isolierschicht wurde ein 10 g/m² Glasfaservlies verwendet. Bei der Herstellung wurde auf beiden Seiten der Isolationsschicht eine Schicht PEEK-Folie aufgebracht; Bei der Verfestigung des Laminats war zusätzliches PEEK erforderlich, um die Glasisolierschicht zu benetzen.
Bei Aufstellung nebeneinander in der in Fig. 2 gezeigten Konfiguration; Der "Isolator" auf dem "Leiter" und damit die Erwärmung näher an der Arbeitsspule wurde an der Grenzfläche zwischen den beiden Laminaten konzentriert. Die beiden Laminate wurden um 45 Grad verschoben, damit die Oberflächentemperatur des Unterlaminats unter Verwendung einer Wärmebildkamera gemessen werden konnte. Eine Cheltenham Induction Heating TR1 1kW Induktionsstromversorgung wurde verwendet, um ein elektromagnetisches Wechselfeld durch eine Vierwindungs-Solenoidspule bei 165 kHz für 60 Sekunden anzulegen. Die Temperatur an den beiden in Abbildung 2 markierten Stellen wurde während der Tests mit einer FLIR T250 Wärmebildkamera in Zehn-Sekunden-Intervallen gemessen.
Typisch Kompositmaterialien
Glasfaser : Sie ist die Grundlage der Verbundwerkstoffindustrie. Es ist leicht, hat eine moderate Zugfestigkeit und ist einfach zu bedienen.
Kohlefaser : Es ist überall vom Autorennen bis zur Luftfahrt zu finden. Obwohl es teurer als Fiberglas und Kevlar ist, hat es die höchsten Zug-, Druck-, Biege- und Biegefestigkeiten der Branche. Kohlefaser wird häufig für Projekte verwendet, die eine höhere Festigkeit erfordern, wie z. B. tragende Teile.
Keramikmatrix-Verbundwerkstoff: Keramik, die in einer Keramikmatrix dispergiert ist. Diese sind besser als normale Keramiken, da sie gegen Temperaturschock und Bruch beständig sind.
Metallmatrix-Verbundstoff: Ein Metall, das über eine Matrix verteilt ist
Bewehrter Beton: Mit einem hochfesten Material wie Stahlbewehrungsstäben verstärkter Beton
Glasfaserverstärkter Beton : Beton, der in eine Glasfaserstruktur mit einem hohen Zirkonoxidgehalt gegossen wird
Lichtdurchlässiger Beton: Beton, der die Lichtwellenleiter umgibt
Holzwerkstoffe: Holzwerkstoffe kombiniert mit anderen preiswerten Materialien. Ein Beispiel wäre Spanplatte. Dieser Verbund kann auch ein spezielles Material wie eine Beschichtung enthalten.
Sperrholz: Holz, das durch das Zusammenkleben mehrerer dünner Holzschichten in verschiedenen Winkeln hergestellt wird
Engineered Bambus: Streifen aus Bambusfasern, die zu einem Brett zusammengeklebt werden. Dies ist ein nützlicher Verbundwerkstoff, da er höhere Druck-, Zug- und Biegefestigkeiten als Holz aufweist.
Hartholz: Ein Quadrat, das aus vielen zusammengefügten Holzstücken besteht, normalerweise aus Hartholz. Es wird als Dekorationsstück verkauft.
Holz-Kunststoff-Verbund: entweder Holzfaser oder Schüttmehl in Kunststoff
Zementgebundene Holzfaser: In Zement gegossene mineralisierte Holzstücke. Dieser Verbundstoff hat isolierende und akustische Eigenschaften
Fiberglas: Fiberglas kombiniert mit einem relativ preiswerten und flexiblen Kunststoff
Kohlefaserverstärktes Polymer: Kohlefaser-Set aus Kunststoff mit hohem Festigkeits-Gewichts-Verhältnis
Sandwichplatte: Verschiedene Verbundwerkstoffe übereinander geschichtet
Verbundwaben: Auswahl von Verbundwerkstoffen in vielen Sechsecken, um eine Wabenform zu erzeugen.
Pappmaché: Klebepapier. Diese findet man im Handwerk
Kunststoffbeschichtetes Papier: Mit Kunststoff beschichtetes Papier zur Erhöhung der Haltbarkeit. Ein Beispiel dafür, wo dies verwendet wird, ist das Kartenspielen
Syntaktische Schäume: Leichte Materialien, die durch das Füllen von Metall, Keramik oder Kunststoff mit Mikroballons entstehen. Diese Ballons werden aus Glas, Carbon oder Kunststoff hergestellt.
Stahlweste : Sie ist eine der ersten hochfesten Synthesefasern, die sich in der faserverstärkten Kunststoffindustrie durchgesetzt hat. Seine größten Eigenschaften sind seine hohe Schlag- und Abriebfestigkeit. Ideal für Teile, bei denen hohe Stöße und Abnutzung zu erwarten sind, wie Kanus, Flugzeugzellen und Druckbehälter.
PVA : Polyvinylalkohol wird auf dünne Laminate oder Deckschichten gesprüht, um die Luft während des Aushärtens des Teils fernzuhalten. Das PVA sollte dann mit warmem Wasser gespült werden.
Styrolwachs: Eine andere Lösung besteht darin, die Luft während des Aushärtungsprozesses aus Ihrem Teil herauszuhalten. Im Gegensatz zu PVA verbleibt Paraffin beim Aushärten auf der Oberfläche des Harzes. Styrolwachs muss nach dem Aushärten geschliffen werden.
MEK-P (Methylethylketonperoxid): Es gehört zur Gruppe der organischen Peroxide. Es ist ein Beschleuniger oder hitzeaktiviertes farbloses chemisches Öl, das das Gelieren und Aushärten von Polyesterharz und Vinylesterharz reguliert. Es wird aus der Reaktion von Methylethylketon und Wasserstoffperoxid gewonnen. Es initiiert Vernetzungsreaktionen zwischen Harz und reaktiven Monomeren wie Styrol. Methylethylketonperoxid (MEK-P) ist bei Raumtemperatur aktiv, um Polyester und Vinylester zu härten. MEK-P wird als Härter bei der Herstellung von Harzen, Synthesekautschuk und anderen petrochemischen Kunststoffen verwendet. Methylethylketonperoxid wird für alle Polyesterharze, Gelcoats und Vinylesterharze benötigt. Verschiedene Konzentrationen von MEK-P sind erforderlich, um verschiedene Arten von Harzen zu katalysieren. Es wird auch zum Härten von Benzoylperoxidharz in heißen Formen verwendet. Die Katalysatoren sind zwar nicht Teil der chemischen Reaktion, liefern aber die notwendige Energie, um den Polymerisationsprozess zu starten. Alle Peroxide sind Derivate irgendeiner Form von Wasserstoffperoxid. Es wird häufig bei der Vulkanisation von Polymeren verwendet. Es ist eine hochgiftige Substanz, die als Lösungsmittel verwendet wird. Es ist ein starkes Oxidationsmittel und ätzend. Im Gegensatz zu anderen ätzenden Substanzen handelt es sich um eine Substanz, die zusätzlich zu korrosiven Ösophagitis-Befunden zum Tod durch Multiorganversagen führen kann. Die Exposition mit MEK-P führt zur Bildung freier Radikale, die zu einer Lipidperoxidation führt. Lipidperoxidation kann auf zellulärer Ebene Funktionsstörungen verursachen, insbesondere Leberversagen und Multiorganversagen.
Kevlar (Polyparaphenylenterephthalamid): Aramidfasern, normalerweise Kohlefaser und Glasfaser Es wird häufig zur Verstärkung von Verbundwerkstoffen in Kombination mit Bei Hochleistungsverbundwerkstoffen ist die Matrix normalerweise es ist epoxidharz . Typische Anwendungen sind F1 Rennautos zum Monocoque Stämme, Hubschrauber Rotorblätter, Tennis , Tischtennis , Badminton und quetschen Schläger , Kanus , Kricket Stöcke und Gras Eishockey , Eishockey und Lacrosse hat Stöcke.

Als stärkste Faser und kristalline Struktur ist Kevlar-149 in bestimmten Bereichen des Flugzeugbaus eine Alternative. Kevlar, das insbesondere in den vorderen Teilen von Flugzeugtragflächen verwendet wird, zeigt bei Vogelschlag mehr Festigkeit als Kohle- oder Glasfaser.
Kevlar wird manchmal in Strukturbauteilen von Automobilen gefunden, insbesondere Ferrari F40 Es wird in hochwertigen Performance-Autos verwendet, wie z
Kevlar, niedrig Wärmeleitfähigkeit und Suspension Aufgrund seiner hohen Festigkeit im Vergleich zu anderen Materialien für kryogen im Feld häufig verwendet. Oftmals wird eine Dichtung verwendet, um jegliche Wärmeleckage an das paramagnetische Material zu minimieren. paramagnetisch Salzbehälter ein supraleitender Magnet Wird zum Aufhängen am Dorn verwendet. Es wird auch als thermische Trennung oder strukturelle Unterstützung verwendet, wenn geringe Wärmeverluste erwünscht sind.
Kevlar wird in einer Vielzahl von militärischer Munition und Materialien sowie in Helmen verwendet, um die Explosion einer Granate zu absorbieren.
Kevlar wenn gebogen , die resultierende Faser Zerreißfestigkeit ca. 3.620 MPa und relative Dichte Es ist 1,44. Das Polymer verdankt seine hohe Festigkeit vielen Bindungen zwischen den Ketten.
[CO-C 1-6, H 4 -CO-NH-C 6 H 4 -NH-] wird mit n formuliert.
Kevlar behält seine Festigkeit und Flexibilität bis zu kryogenen Temperaturen (−196 °C); tatsächlich ist es bei niedrigen Temperaturen etwas stärker. Bei höheren Temperaturen nimmt die Zugfestigkeit sofort um ca. 10-20% ab und nach einigen Stunden nimmt die Festigkeit allmählich weiter ab.
Kevlar-Herstellung, wasserunlösliche Polymersynthese und Spinnen benötigtes Konzentrat, um es in Lösung zu halten aus der Verwendung von Schwefelsäure Es ist teuer wegen der damit verbundenen Schwierigkeiten.
Es stehen verschiedene Kevlar-Qualitäten zur Verfügung:
Kevlar K-29: Wird in industriellen Anwendungen wie Kabeln, Reifen und Bremsbelägen verwendet.
Kevlar K49 : Es ist ein Hochmodul, das in Kabel- und Seilprodukten verwendet wird.
Kevlar K100 : Es ist die farbige Version von Kevlar.
Kevlar K119 : Es ist widerstandsfähiger gegen Dehnung, Dehnung und Ermüdung.
Kevlar K129 : Zeigt eine höhere Festigkeit für ballistische Anwendungen.
Kevlar K149: Es wird bevorzugt für ballistische, Panzerungs- und Luft- und Raumfahrtanwendungen verwendet.
Kevlar AP: 15 % höhere Zugfestigkeit als Kevlar K-29.
Kevlar KM2 : Zeigt verbesserten ballistischen Widerstand für Panzerungsanwendungen.
Kevlar XP: Es ist eine Kombination aus leichterem Harz und KM2 plus Faser.
Biokomposite
Ein Verbundwerkstoff ist ein neues Material mit unterschiedlichen Eigenschaften, das aus zwei oder mehr physikalisch unterschiedlichen Phasen (oder Substanzen) besteht und sich von allen unterscheidet. Eine der Phasen ist die Matrix und die andere sind die Verstärkungsmaterialien, die verwendet werden, um die Matrix zu verstärken. Der Zweck der Matrix besteht darin, die Fasern zusammenzuhalten und die aufgebrachte Last auf die Fasern zu übertragen.
Außerdem schützt es die Fasern vor Umwelteinflüssen und mechanischen Beschädigungen. Das Matrixmaterial kann ein duroplastisches oder thermoplastisches Polymer sein, muss jedoch aus nachwachsenden Rohstoffen bestehen.
Biokomposite sind Materialien, die aus biologisch abbaubaren Polymeren (Matrix) und biologisch abbaubaren Verstärkungsmaterialien bestehen. Biologisch abbaubares Material sind Stoffe, die von lebenden Organismen abgebaut werden können.
Die in Biokompositen verwendeten Füllstoffe sind in der Regel Biofasern. Biokomposite aus natürlichen Biofasern sind erneuerbar, leicht, biologisch abbaubar und umweltfreundlich. Heute konzentriert sich die Polymerwissenschaft und -technologie auf Verbundwerkstoffe aus nachwachsenden Rohstoffen.
Aus nachwachsenden Rohstoffen hergestellte Biokomposite haben aufgrund ihrer biologischen Abbaubarkeit eine universelle Bedeutung erlangt und sind aufgrund ihrer umweltfreundlichen Materialien Gegenstand umfangreicher Forschungen für ihren Einsatz in verschiedenen Bereichen.
Aus nachwachsenden Rohstoffen hergestellte Biokomposite haben aufgrund ihrer biologischen Abbaubarkeit universelle Bedeutung erlangt; Da es sich um umweltfreundliche Materialien handelt, war es Gegenstand vieler und umfassender Forschungen für seine Verwendung in verschiedenen Bereichen.
BBCs sind Verbundwerkstoffe mit einem breiten Anwendungsspektrum in der Biomedizin, Landwirtschaft, Verpackung und anderen verwandten technischen Bereichen.
Verschiedene Faktoren, die die Verwendung von natürlichen Polymeren und Biofasern einschränken, umfassen Inkompatibilität oder unzureichende Kompatibilität mit der hydrophoben Polymermatrix, thermische Empfindlichkeit und Entflammbarkeit.

Produktionstechniken von Biokompositen:
Es basiert meist auf Herstellungsverfahren von Kunststoffen oder Verbundwerkstoffen; B. Pressformen, Handauflegen, Filamentwickeln, Pultrusion, Extrusion, Spritzgießen, Formpressen, Harzspritzpressen und Plattenformen.
Der Compoundierungsschritt von Biokompositen ist bei der Herstellung von Biokompositen durch verschiedene Verfahren äußerst wichtig. Der Zweck des Compoundierens besteht darin, Material (wie Pellets) mit Eigenschaften herzustellen, die für nachfolgende Spritz-, Form-, Extrusions- oder andere Prozesse geeignet sind. Beim Compoundieren werden in der Regel Polymere, Füllstoffe, Fasern und Additive vermischt, eine gute Dispergierung gewährleistet und Granulate in geeigneter Form und Verarbeitungseigenschaften angestrebt.
Compoundierung und Extrusion von thermoplastischen Polymeren und Naturfasern:
Während der Compoundierung erwärmt sich das thermoplastische Polymer und schmilzt, entweder durch externe Erwärmung oder durch mechanische Wechselwirkung im Extruder; In diesem Stadium werden Holzfasern (normalerweise in Mehlform) zusammen mit anderen Zusatzstoffen hinzugefügt.
Mischung aus thermoplastischen Fasern und Naturfasern:
Lange Flachs-, Hanf-, Kenaf- und Baumwollfasern sind gängige Fasern in der Automobilindustrie; sie werden oft mit thermoplastischen Fasern vermischt und als Verstärkungsmaterial verwendet.
Duroplastische Polymermatrix-Biokomposite:
Kommerzielle Biokomposite mit duroplastischer Polymermatrix sind rar, aber die Arbeit auf diesem Gebiet geht weiter. Die Herstellungstechniken ähneln herkömmlichen Verbundverfahren.
Biologisch abbaubare Verbundwerkstoffe mit Lignocellulosefasern:
Wichtige Faktoren bei der Entwicklung biologisch abbaubarer Verbundwerkstoffe sind die Auswahl der richtigen Lignocellulosefasermischung und der geeigneten Biopolymermatrix, die Bestimmung geeigneter Oberflächenbehandlungen bei Bedarf und die Anwendung kostengünstiger, aber schneller Herstellungstechniken.