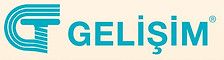


Hidrokarbonlar
Hidrojen ve karbon olmak üzere iki elementten oluşan organik bir bileşiktir. Petrol bileşiminin büyük bir kısmı değişen uzunluklardaki hidrokarbonlardan oluşur.
En küçük hidrokarbon metan, tek bir karbon atomu ve dört hidrojen atomundan oluşur. Bununla birlikte, hidrokarbonlar, zincirler, daireler ve diğer karmaşık şekiller dahil olmak üzere birçok yönden birbirine bağlanmış yüzlerce veya binlerce bireysel atomdan oluşabilir.
Hidrokarbonların özelliklerini sınıflandırmak için birkaç temel türe ayrılırlar.
Alkanlar: Bunlar doymuş hidrokarbonlar olarak adlandırılır. Yani sadece tüm karbon atomları arasında tek bağlar içerirler. Alkanlar, petrol yakıtlarının temelidir ve doğrusal ve dallı formlarda bulunurlar.
Doymamış Hidrokarbonlar: Karbon atomları arasında bir veya daha fazla çift bağa sahip olan hidrokarbonlara alken denir.
Sikloalkanlar: Bir veya daha fazla halka yapısı içeren herhangi bir hidrokarbon.
Aromatik Hidrokarbonlar: Areneler olarak da adlandırılan aromatik hidrokarbonlar, karbon atomlarının birbirini izleyen çift ve tek bağlarla bağlandığı benzersiz bir karbon molekülleri sınıfıdır. Bu molekül sınıfı, karbon atomları arasındaki bağların tek ve çift bağlar arasında bir ara bağ olduğu özel halka yapılarına sahiptir.
Bu sınıftaki moleküller, endüstriyel çözücü «benzen» içerir.
Benzen (C6H6): Diğer hidrokarbonlar gibi benzen de petrolün doğal bir bileşenidir. Oda sıcaklığında renksiz, yanıcı, tatlı kokulu bir sıvıdır ve yüksek oktan sayısına sahip olduğu için çoğu benzin karışımının bir bileşenidir.
Benzen de oldukça kanserojendir ve kemik iliği yetmezliği ve kemik kanserine neden olduğu iyi bilinmektedir. Elbette, “hoş aroması” nedeniyle tıraş sonrası ve diğer kozmetiklerde bir katkı maddesi olarak kullanıldığında kanserojenliği iyi bilinmemektedir.
En büyük benzen kullanımı (% 50), stiren ve polistren plastiklerinin ürünüdür. Ayrıca Naylon üretiminde önemli olan sikloheksan olarak bilinen bir moleküle dönüştürülür. Siklohekzan üretmek için benzenin yaklaşık% 15'i kullanılır. Böcek ilaçlarından kauçuğa kadar her şeyde daha küçük miktarlar kullanılır.
Benzen yapısı iki şekilde çizilebilir. İlkinde, çift bağ karakteri açıkça çizilir. Kısa elli versiyonda, yapıyı göstermek için halkanın içine bir daire çizilir. Benzen içindeki her bir karbon atomuna bağlı tek bir hidrojen vardır.
Aşağıdaki I. ve II. çizimleri eştir. Pratikte III. çizim kullanılır.
Benzen, renksiz, alevlenebilen, kaynama noktası 80,1 °C, erime noktası 5,5 °C olan bir sıvıdır.
Binükleer Aromatik Hidrokarbonlar: Molekülünde iki benzen halkası içeren bileşiklerdir.
Hidrokarbonlar
Hidrojen ve karbon olmak üzere iki elementten oluşan organik bir bileşiktir. Petrol bileşiminin büyük bir kısmı değişen uzunluklardaki hidrokarbonlardan oluşur.
En küçük hidrokarbon metan, tek bir karbon atomu ve dört hidrojen atomundan oluşur. Bununla birlikte, hidrokarbonlar, zincirler, daireler ve diğer karmaşık şekiller dahil olmak üzere birçok yönden birbirine bağlanmış yüzlerce veya binlerce bireysel atomdan oluşabilir.
Hidrokarbonların özelliklerini sınıflandırmak için birkaç temel türe ayrılırlar.
Alkanlar: Bunlar doymuş hidrokarbonlar olarak adlandırılır. Yani sadece tüm karbon atomları arasında tek bağlar içerirler. Alkanlar, petrol yakıtlarının temelidir ve doğrusal ve dallı formlarda bulunurlar.
Doymamış Hidrokarbonlar: Karbon atomları arasında bir veya daha fazla çift bağa sahip olan hidrokarbonlara alken denir.
Sikloalkanlar: Bir veya daha fazla halka yapısı içeren herhangi bir hidrokarbon.
Aromatik Hidrokarbonlar: Areneler olarak da adlandırılan aromatik hidrokarbonlar, karbon atomlarının birbirini izleyen çift ve tek bağlarla bağlandığı benzersiz bir karbon molekülleri sınıfıdır. Bu molekül sınıfı, karbon atomları arasındaki bağların tek ve çift bağlar arasında bir ara bağ olduğu özel halka yapılarına sahiptir.
Bu sınıftaki moleküller, endüstriyel çözücü «benzen» içerir.
Benzen (C6H6): Diğer hidrokarbonlar gibi benzen de petrolün doğal bir bileşenidir. Oda sıcaklığında renksiz, yanıcı, tatlı kokulu bir sıvıdır ve yüksek oktan sayısına sahip olduğu için çoğu benzin karışımının bir bileşenidir.
Benzen de oldukça kanserojendir ve kemik iliği yetmezliği ve kemik kanserine neden olduğu iyi bilinmektedir. Elbette, “hoş aroması” nedeniyle tıraş sonrası ve diğer kozmetiklerde bir katkı maddesi olarak kullanıldığında kanserojenliği iyi bilinmemektedir.
En büyük benzen kullanımı (% 50), stiren ve polistren plastiklerinin ürünüdür. Ayrıca Naylon üretiminde önemli olan sikloheksan olarak bilinen bir moleküle dönüştürülür. Siklohekzan üretmek için benzenin yaklaşık% 15'i kullanılır. Böcek ilaçlarından kauçuğa kadar her şeyde daha küçük miktarlar kullanılır.
Benzen yapısı iki şekilde çizilebilir. İlkinde, çift bağ karakteri açıkça çizilir. Kısa elli versiyonda, yapıyı göstermek için halkanın içine bir daire çizilir. Benzen içindeki her bir karbon atomuna bağlı tek bir hidrojen vardır.
Aşağıdaki I. ve II. çizimleri eştir. Pratikte III. çizim kullanılır.
Benzen, renksiz, alevlenebilen, kaynama noktası 80,1 °C, erime noktası 5,5 °C olan bir sıvıdır.
Binükleer Aromatik Hidrokarbonlar: Molekülünde iki benzen halkası içeren bileşiklerdir.
Hakkında
Kyäni, faydalı bileşenlerden oluşan besin takviyesi ürünlerini; benzersiz iş fırsatıyla birlikte dünya çapında 50'den fazla ülkeye ulaştırmaktadır. İdeal sağlığımızı korumak için günlük olarak Kyäni ürünlerini kullanırız, bu ürünleri başkalarıyla paylaşırız, işimizi inşa etmek ve sürdürmek için neredeyse her gün belirli bir saatimizi işe adarız ve başkalarını da Kyäni fırsatına dahil ederek veya Potato Pak ve Caring Hands programlarına katkı sağlayarak başarımızı başkalarıyla paylaşırız.
Hakkında
Kyäni, faydalı bileşenlerden oluşan besin takviyesi ürünlerini; benzersiz iş fırsatıyla birlikte dünya çapında 50'den fazla ülkeye ulaştırmaktadır. İdeal sağlığımızı korumak için günlük olarak Kyäni ürünlerini kullanırız, bu ürünleri başkalarıyla paylaşırız, işimizi inşa etmek ve sürdürmek için neredeyse her gün belirli bir saatimizi işe adarız ve başkalarını da Kyäni fırsatına dahil ederek veya Potato Pak ve Caring Hands programlarına katkı sağlayarak başarımızı başkalarıyla paylaşırız.
Sayfa Yapım Aşamasındadır.
Sayfa Yapım Aşamasındadır.
Schulungs- / Wissens- / Lösungsplattform
Vorabinformationen
Bei den Machbarkeitsstudien wurden Messungen im Feld durchgeführt, wo es möglich ist, Öl zu finden. Durch Abtauchen in verschiedene Tiefen wurde das Volumen der Öllagerstätte durch Sonar- und Sondenstudien bestimmt. Durch die Abkehr vom zentralen Referenzpunkt, nach Sonar- und Bohrstudien, der Größe des Ölfeldes und der Vermessung der Reserve, der Rendite der Reserve, des Arbeitsprozesses und der monetären Rendite des Unternehmens wurde entschieden, ob das Öl war es wert, gefördert zu werden.
All dies sind vorläufige Einschätzungen, die vorgenommen werden müssen, bevor das unter der Erde/im Meer liegende Öl ausgegraben werden kann. Mit anderen Worten, die Existenz von Öl in einem Feld und seine Entdeckung bedeutet nicht, dass Öl gefördert werden kann. Das wichtigste Entscheidungsargument im Ölförderungsgeschäft ist die Kostendeckung. Aus der Tiefe des unterirdischen Öls werden die Menge der Reserve, die Qualität des Öls, der Transport des Öls von der Bohrstelle zu den Raffinerien, die sehr hohe Kosten erfordern, berücksichtigt.
Heute ist es wahrscheinlich, dass es auf dem Territorium vieler Länder Ölfelder geben wird. Dazu gehört auch die Türkei. Ob es sich jedoch, wie gesagt, lohnt, diese Öllagerstätte aufzudecken, hängt mehr von den Kosten der Arbeiten ab. Es ist ein Prozess, der von Anfang bis Ende Geld erfordert, insbesondere vom Besitz von Ölbohrplattformen bis hin zum Leasing von Ölunternehmen.
Wie man sich erinnern wird, kündigte der Präsident der Türkei im Jahr 2020 die Entdeckung einer Erdgaslagerstätte im westlichen Schwarzen Meer an, erklärte, dass diese Erdgasreserve 320 Milliarden Kubikmeter beträgt und dass sie 2023 in Betrieb genommen werden soll. Es ist ersichtlich, dass die Türkei, die noch nie zuvor in diesem Bereich tätig war, von der Ernsthaftigkeit der Aufgabe etwas entfernt ist, wenn man bedenkt, dass die Reservenbestimmung mit einer einzigen Sonarbewertung, Transport, Transport, Lagereinrichtungen vor der Bohrung der potentielle Reserven und technische Personalknappheit zusätzlich zu all diesen technischen Geräten. Die Arbeit an der Ausgrabung fossiler Brennstoffe, für die der Zweite Weltkrieg riskiert und sogar konventionelle Kriege geführt wurden, ist ein viel ernsteres Thema als die Aussagen des türkischen Präsidenten.
Der einzige Weg in Ländern wie der Türkei, die nicht über ausreichende Infrastruktur für dieses Geschäft verfügt, kann nicht über die Ausschreibung der Arbeit zur Gewinnung der Reserven an Weltkonzerne hinausgehen. Auch in diesem Fall kann das Land mit der Reserve nicht über eine Beteiligung hinausgehen. Dies übersteigt nicht etwa 20 - 30 % der geförderten Ressource.
Die irgendwie ausgegrabene fossile Energiequelle liegt buchstäblich in ihrer rohen Form vor. Dieses Rohöl muss raffiniert werden, um heute ein verwendbares, zweckgebundenes Material zu werden. Aus diesem Grund ist Petkim die einzige relevante Institution in der Türkei, die unter dem Namen Privatisierung an die aserbaidschanische Firma Socar verkauft wurde.
Das in die Raffinerie gebrachte Rohöl wird verdünnt und durch eine Art Destillationsverfahren namens Cracking auf einfachste Weise getrennt. In diesem mehrstufigen Prozess werden ausgehend von jeder Stufe die heute verwendeten und zweckdienlichen Materialien hergestellt (Polymere, Lösungsmittel, brennbare Gase, schwere Teere wie Asphalt, Polyolefine, Polyester, Polystyrole aus Nebenprodukten) .
Polyolefine: PE, PP, PB, EVA, EVOH
Polyester: PET, PBT, PC, PTT, PEN
Polyamide: PA6, PA6.6, PA12, PPA
Halogenierte Polymere: PVC, PTFE, PVDF
Polyacrylate: PAN, PBA, PMA, PMMA
Polystyrole: PS, ABS, SB, SBS, SAN
Polysulfide: PPS, PSU, PES, PPSU
Biopolymere: PLA, PEA, PVAL, PPOX
Polyetherketone: PAE, PEK, PEEK
Polyimide: PI, PBI, PEI, PBO, PMI
Polyurethane: PUR, TPA, TPO, TPU, Spandex
Spezialpolymere: LCP, POM, BR, NBR
Die betreffenden Ausgangspolymere treten in den möglicherweise abschließenden Verpackungsprozess ein, bevor sie auf den Verbrauchermarkt gebracht werden. Nach diesem Prozess Polymer-Rohstoffe; Es kann in Form von Granulat oder gemahlenem Pulver vorliegen.
Es kann in Big-Bag-Säcken zum Verpacken sein oder allgemein in 25-Kilo-Säcken. Je nach Anlagenstruktur des Anwenderunternehmens erfolgt die Verschiffung ab dem Raffineriebereich per Silo-Bass-Tanker, LKW, Bahn oder Schiff.
Im Folgenden können detailliertere Informationen über diese Polymere wie folgt zusammengefasst werden;
LDPE (Low Densty PolyEthylene)
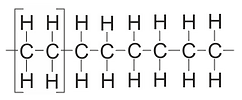
Allgemeine Eigenschaften sind hohe chemische Beständigkeit. Es ist ein rutschiges Material mit einem niedrigen Reibungskoeffizienten. Die Feuchtigkeitsaufnahme ist nahe Null. Polyethylen wird in sich selbst in Typen unterteilt. Die Länge ihrer Moleküle, die die Spezies bestimmen, ist ihr Molekulargewicht. Es ist ein weicheres und weniger steifes Material im Vergleich zu Polypropylen und PVC. Das Molekulargewicht ist das, was Polyethylen auszeichnet.
(1) Niedermolekulargewicht (PE-300)
(2) Hochmolekulares Gewicht (PE-500)
(3) Es kann als Ultra-Molekulargewicht (PE-1000) in drei Gruppen eingeteilt werden.
Insbesondere Polyethylen 1000 bietet mit seiner hohen Schlagfestigkeit, hohen Verschleißfestigkeit und seinem niedrigen Reibungskoeffizienten eine ausgeprägte Wirtschaftlichkeit, die eine dreimal höhere Verschleißfestigkeit ergibt. Polyethylen 1000 kann mit einer längeren Lebensdauer in allen chemischen Umgebungen verwendet werden, in denen es verwendet werden kann. Es ähnelt PTFE mit seinen selbstschmierenden, rutschigen und Antihaft-Eigenschaften. Selbst Eis kann sich nicht an Polyethylen festhalten und rutscht aus. Insbesondere bei der Herstellung brennbarer Materialien und im Bergbau sind Explosion und Feuer die Hauptgefahren in allen Umgebungen, insbesondere im Untergrund. Mit zunehmendem Molekulargewicht treten signifikante Erhöhungen der Abriebfestigkeit auf. Diese Abriebfestigkeit ist die Beständigkeit, die auftritt, wenn der Kunststoff durch Reiben mit einer glatten Metalloberfläche arbeitet. Die Betriebstemperaturen liegen zwischen 90 und 150 ° C.
Lebensmittelindustrie, LKW- und Silobeschichtung, Förderkettenschlitten
Wassertanks, Fleischschneidemaschinen, Papier, Textilindustrie
Es wird in den Feldern verwendet.
Ethylengas wird zuerst im Vorkompressor auf 250 bis 300 Atmosphären komprimiert und dem zweiten Kompressor zugeführt. Hier wird der Druck auf 3 500 Atmosphären erhöht. Der Druck des Reaktors hängt von der Konstruktion der Fabrik, der Art des Katalysators und der Qualität des gewünschten Produkts ab. Das komprimierte Ethylen wird nach dem Vorheizen im Rohrreaktor polymerisiert. Nicht umgesetztes Ethylen am Ausgang des Reaktors wird mit mittlerem und niedrigem Druck zu zwei Abscheidern geschickt. Dieses Ethylen wird über einen Booster zum Vorabscheider und zum zweiten Kompressor zurückgeführt. Das resultierende Polyethylen wird einem Extruder zugeführt; Hier werden notwendige Zusätze hinzugefügt und das Endprodukt granuliert. Die Polymerisationsgeschwindigkeit ist aufgrund des verwendeten Reaktortyps sehr hoch. Die Kosten für Hilfsstoffe wie Wasser, Dampf und Strom sind gering und die Betriebsflexibilität außergewöhnlich. Die Qualität des erhaltenen Produktes ist sehr gut.
Katalysatoren im LDPE-Prozess:
Die Polymerisation kann auf verschiedene Arten initiiert werden; durch Katalysatoren, Sauerstoff, Wärme oder Strahlung (Strahlung).
Bei der Herstellung von LDPE werden meist organische Peroxide als radikalische Katalysatoren verwendet; Dazu gehören Peroxydicarbonate, Hydroperoxide und langkettige Peroxide. In der kommerziellen Produktion beträgt die Retentionszeit in der Reaktion 3 bis 15 Sekunden.
In den letzten Jahren wurden Metallocenkatalysatoren, die ein einziges aktives Ende enthalten, bei der Herstellung von Polyolefinen verwendet. Mit ihnen hergestellte Polymere unterscheiden sich von denen, die mit anderen Katalysatoren erhalten wurden; Ihre Molekulargewichtsverteilung ist eng, ihre Schlagzähigkeit ist hoch, ihre elastische Rückführungseffizienz ist hoch und ihre optischen Eigenschaften sind sehr gut.
Schlüsselparameter:
Die Hauptparameter, die die Reaktionsgeschwindigkeit, die langkettige Verzweigung (Morphologie) und das Molekulargewicht beeinflussen, sind Druck und Temperatur. Die Art und Menge des Initiators beeinflusst auch die Reaktionsgeschwindigkeit und Morphologie. Sauerstoff und Wasser sind wichtige Verunreinigungen, die in der Umwelt vorkommen können. Abgesehen davon sind Methanol, Ethan, Acetylen, CO, CO2, H2, C3 und schwere Kohlenwasserstoffe Verunreinigungen aus dem Monomer. Alle Verunreinigungen beeinflussen die radikalische Polymerisation und verändern den Reaktionsverlauf.
LDPE kann durch das Hochdruckautoklavenverfahren und das Hochdruckrohrverfahren hergestellt werden. Der einzige Unterschied zwischen diesen beiden Prozessen ist der Reaktortyp.
Beim Hochdruckautoklavenverfahren liegt der Reaktionsdruck im Bereich von 150-200 MPa. Das Volumen der Autoklavenreaktionsabdeckung wird so gewählt, dass die Retentionszeit 30-60 Sekunden betragen kann. Der Autoklav ist ein adiabatischer kontinuierlicher Rührkesselreaktor.

Es gibt zwei übliche Verfahren, die bei der Herstellung von Polyethylenpolymeren niedriger Dichte verwendet werden:
(1) Röhrenförmiger Prozess
(2) Es ist ein Autoklavenprozess.
Beide Verfahren verwenden die Chemie der freien Radikale.
Polyethylen niedriger Dichte wird durch das Polymerisationsverfahren von Ethylen bei sehr hohen Temperaturen in einem Rohrreaktor hergestellt. In diesem Rohrreaktor ermöglicht die Hochdruckpolymerisation eine weitere Copolymerisation von Ethylen mit polaren Comonomeren.
Der röhrenförmige Prozess hat einen Vorteil gegenüber dem Autoklavenprozess. Rohrleitungen sind kostengünstiger bei geringerem Stromverbrauch. Weltweit hat das röhrenförmige Verfahren einen großen Anteil an der Produktionstechnologie für Polyethylen niedriger Dichte.
Harze finden ihre Hauptanwendung bei der Herstellung von Allzweck- und Hochleistungsanwendungen, einschließlich Blas- und Gussfolie, Extrusion und Beschichtung, Folie und Blechen, Rotations- und Spritzguss und anderen Anwendungen. Andere typische Anwendungen von Thermoplasten umfassen Verbrauchertaschen, Auskleidungen, Deckfolien, Laminierfolien, landwirtschaftliche Folien, Extrusionsbeschichtungen, Kappen und Kappen, Spielzeug und viele andere haltbare Kunststoffprodukte, die im täglichen Leben verwendet werden. Sie werden sogar in geformten Laborgeräten wie Pipettenwaschanlagen, Beuteln, Tanks und Allzweckrohren verwendet.
LDPE-Hauptmerkmale:
Monomer ist ein Harz aus Ethylen. Es handelt sich um hochwertiges Polyethylen, das 1933 von Imperial Chemical Industries (ICI) hergestellt wurde. Das Harz wurde unter Verwendung eines sehr hohen Druckverfahrens hergestellt, das als radikalische Polymerisation bezeichnet wird. Noch heute werden Thermoplaste auf die gleiche Weise hergestellt. Diese Harze sind je nach Herstellungsverfahren in einem breiten Spektrum an Flexibilität erhältlich. Trotz des starken Wettbewerbs unter Polymeren bleibt es als gute Kunststoffqualität auf dem Markt wichtig.
Die weltweite Produktionskapazität von Polyethylenpolymer beträgt über 100 Millionen Tonnen. Die LDPE-Produktionskapazität hat einen Anteil von 20% an der weltweiten Polyethylenproduktion. 30% der Produktionsflächen befinden sich in Europa und Asien und 20% in Nordamerika.
LDPE- Thermoplaste bieten aufgrund ihrer Eigenschaften, die sie für verschiedene Produkte anwendbar machen, ein breites Anwendungsspektrum.
Es ist ein Polyolefinmaterial mit hohem Molekulargewicht. Wie alle anderen Polyolefine ist Polyethylen niedriger Dichte ungiftig, umweltfreundlich und weist eine hohe Bruchfestigkeit auf. Es ist leichter als Wasser, chemisch inert und löst sich bei Raumtemperatur nicht auf.
Insgesamt hat es ein milchig-weißes durchscheinendes Aussehen mit einer Kombination aus flexiblem Material und einzigartigen Fließeigenschaften, die seine Eignung für Kunststofffolienanwendungen bewiesen hat. Obwohl Harze eine hohe Duktilität und im Allgemeinen eine geringe Zugfestigkeit aufweisen, verlieren sie ihre Festigkeit und Reißfestigkeit, wenn sie Licht und Sauerstoff ausgesetzt werden.
Das Produkt dieser Harze wird häufig in verschiedenen Endsegmentindustrien wie Bauwesen, Automobilindustrie, Verpackung und anderen verwendet. Polymere werden aufgrund ihrer unterschiedlichen Eigenschaften gegenüber anderen Polyethylenqualitäten bevorzugt.
Harze haben Festigkeit, Härte und Temperaturbeständigkeit sowie Chemikalien, die beide für die Herstellung einer Vielzahl von Waren in verschiedenen Segmenten geeignet sind. Produkte aus Polyethylen niedriger Dichte sind langlebig und werden in unserem täglichen Leben verwendet, wie Taschen, Spielzeug, Filme, Laborgeräte, Spielzeug usw. Die Verwendung in Kunststoffprodukten kann leicht beschrieben werden.
-
Harze können je nach Verwendungsbedarf starr und flexibel sein.
-
Es kann transparent oder sogar durchscheinend sein und eine wachsartige Oberfläche haben.
-
Sie sind halbhart, robust und wasserdicht.
-
Sie haben einen niedrigen Schmelzpunkt und bieten auch gute Feuchtigkeitsbarriereeigenschaften.
-
Diese Thermoplaste bieten stabile elektrische Eigenschaften und eine gute chemische Beständigkeit
-
Kunststoffe können mit kostengünstigen Methoden leicht verarbeitet werden.
-
Zugfestigkeit 0,20 - 0,40 N / mm 2 und Schlagfestigkeit kein Bruch
-
Wärmeausdehnungskoeffizient 100 - 220 * 10.6
-
Max. Verbrauchstemperatur 65 ° C.
-
Dichte 0,917 - 0,930 g / cm 3
-
Hervorragende Beständigkeit gegen verdünnte und konzentrierte Säuren, Laugen, Alkohole, Basen und Ester
-
Es bietet eine gute Beständigkeit gegen Öle und Fette, Aldehyde und Ketone.
-
Verschiedene Arten von Kohlenwasserstoffen wie aliphatische Kohlenwasserstoffe, aromatische Kohlenwasserstoffe und halogenierte Kohlenwasserstoffe weisen eine begrenzte Beständigkeit gegenüber Oxidationsmitteln und Mineralölen auf.
-
Sie haben ein geringes spezifisches Gewicht und eine hohe Schlagfestigkeit.
-
Es ist beständig gegen starke Chemikalien und Temperaturen, die die Haltbarkeit der Produkte erhöhen.
-
Es ist sehr wasserdicht gegen geringe Dichte.
-
Kunststoffe können problemlos als Liner oder Einkaufstasche wiederverwendet werden.
-
Harz kann auch eine Energiequelle sein, wenn es zum Heizen von Gebäuden verbrannt wird.
-
Es ist bruchsicher, was bei der Herstellung langlebiger Produkte nützlich ist.
-
Für einige Produkte haben sie eine schlechte Hitzebeständigkeit.
-
Der hohe Wärmeausdehnungskoeffizient begrenzt die Herstellung von Polyethylenprodukten niedriger Dichte.
-
Thermoplaste bieten Beständigkeit gegen schlechte Wetterbedingungen.
-
Harze unterliegen häufig Spannungsrissen.
-
Es ist eine Art PE-Qualität, die nur schwer haften kann.
-
Kunststoffe haben gefährliche Umweltauswirkungen wie Deponien, die Grünflächen zerstören, und werden aus nicht erneuerbaren Ressourcen wie Rohöl hergestellt, was Druck auf die Ressourcen ausübt.
LDPE-Verwendungsbereiche:
Polyethylen niedriger Dichte ist ein Polymer, das häufig bei der Herstellung verschiedener Behälter, Waschflaschen, Ausgabeflaschen, Schläuche, Plastiktüten und verschiedener geformter Laborgeräte verwendet wird. Kunststoffe werden aufgrund ihrer Eigenschaften, die sie für eine Vielzahl von Endsegmentprodukten geeignet machen, in großen Mengen verwendet. Die Hauptanwendungen von Thermoplasten sind:
LDPE-Rohre:
Polyethylenrohr niedriger Dichte (Polyrohr) ist das am häufigsten verwendete Rohr für Haushalts- und chemische Bewässerungszwecke. Diese Rohre werden hauptsächlich zur Bewässerung verwendet, um sie von der Quelle zum Mikrorohr zu verteilen. Sie eignen sich sehr gut für die Installation über dem Boden. Da sie nicht sehr flexibel sind, können die Steckverbinder zum Verlegen von Versorgungsleitungen verwendet werden. Es kann in einer Vielzahl von Anwendungen eingesetzt werden, von Rohren, Sprinklerbewässerung, Tropfbewässerung, Entwässerungssystemen, landwirtschaftlichen Rohren und anderen Bewässerungssystemen. Diese Rohre werden in vollem Durchfluss mit Nyloneinsatzanschlüssen wie Kupplungen, Winkelstück und Adaptern verwendet. Bei den Rohren werden gezackte Steckverbinder verwendet, da sie eine auslaufsichere und freie Abdichtung bieten, die dazu beiträgt, Leckagen zu vermeiden und dem Wasserdruck leicht standzuhalten. Die grundlegenden Eigenschaften von LDPE-Rohren können wie folgt aufgeführt werden:
-
Rohre reagieren bei Raumtemperatur nicht, außer bei hohen Oxidationsfaktoren.
-
Diese Rohre haben einen definierten Bereich von 0,910 g / cm 0,940
-
Rohre aus Polyethylen niedriger Dichte können kontinuierlich 80 - 95 ° C standhalten.
-
Die Röhren sind vollständig durchscheinend oder undurchsichtig und sehr bruchsicher.
-
Das Rohr kann der maximalen Temperatur von 80 ° C und der niedrigsten Temperatur von -120 ° C standhalten.
-
Schmelzpunkt der Rohre 120 ° C.
-
Zugfestigkeit: 17,7 psi (11,7 MPA)
-
Dichte: 0,92 g / cm³
-
Es hat eine schlechte UV-Beständigkeit.
-
Sie sind durchscheinend mit ausgezeichneter Flexibilität.
LDPE Film und Blätter:
Es ist das erste Polyethylen, das entwickelt wurde, und ist bekannt für seine relativ Wärmebeständigkeit sowie seine Härte und Flexibilität unter Temperatureinfluss. Diese Eigenschaften ermöglichen die Herstellung in Form von Filmen und Folien, aus denen dann andere Kunststoffprodukte hergestellt werden können. Dieses Material ist einer der am schnellsten wachsenden Kunststoffe, die derzeit hauptsächlich für Folienanwendungen verwendet werden und für Spritzguss-, Blas- und Rotationsformen geeignet sind.
-
Verpackungsindustrie - Hoher Einsatz in Lebensmittelverpackungen und Textilverpackungen. Der Anwendungsbereich ist breit für Folien und Schichten, Produktbeutel in der Verpackungsindustrie, Bradsäcke, Müllsäcke, Kleidersäcke, Einkaufstüten und Versandtaschen.
-
Industrie - Bänder, Dichtungsmittel, Dichtungen, Lichtschutz, Auskleidungen, Rohrleitungssysteme, Verbundwerkstoffe, Autoteile, Schrumpffolien, Palettenstretch, Gewächshausbeschichtungen, Tanks und Behälter usw. Es wird verwendet, um zu produzieren.
-
Medizinisch - Wird in Transdermalen, Hydrogelen und in der Wundversorgung oder in der Verpackung von Arzneimitteln verwendet.
-
Blätter können durchscheinend und schrumpfbar sein.
-
Sie sind hitze- und chemikalienbeständig.
-
Bleche können einfach mit einem Kunststoffschweißgerät geschweißt werden.
-
Sie stabilisieren UV nicht
-
Diese Filme sind leitfähige Filme und können leicht gefärbt werden.
-
Sie bieten eine leichte Haftung, was bedeutet, dass sie leicht heißversiegelt werden können.
-
Filme und Folien sind flexibel, leicht und wirtschaftlich.
-
Dichte: 0,92
-
Formtemperatur: 245 ° F.
-
Temperaturbereich: 0 ° F - 140 ° F.
-
Zugfestigkeit (PSI) 1600
-
Ultimative Dehnung 600%
Technische Werte und mehr Anwendungsbereiche einiger Rohstoffe der Marke LDPE:
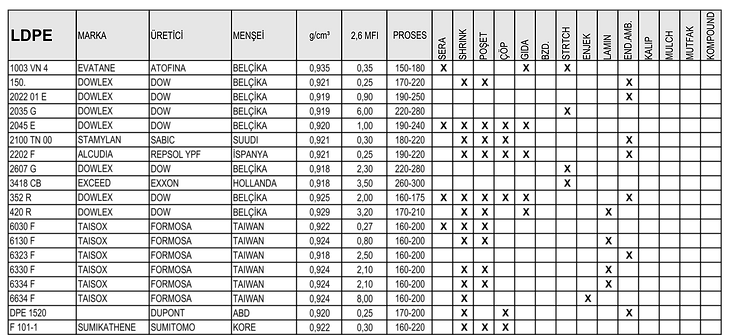
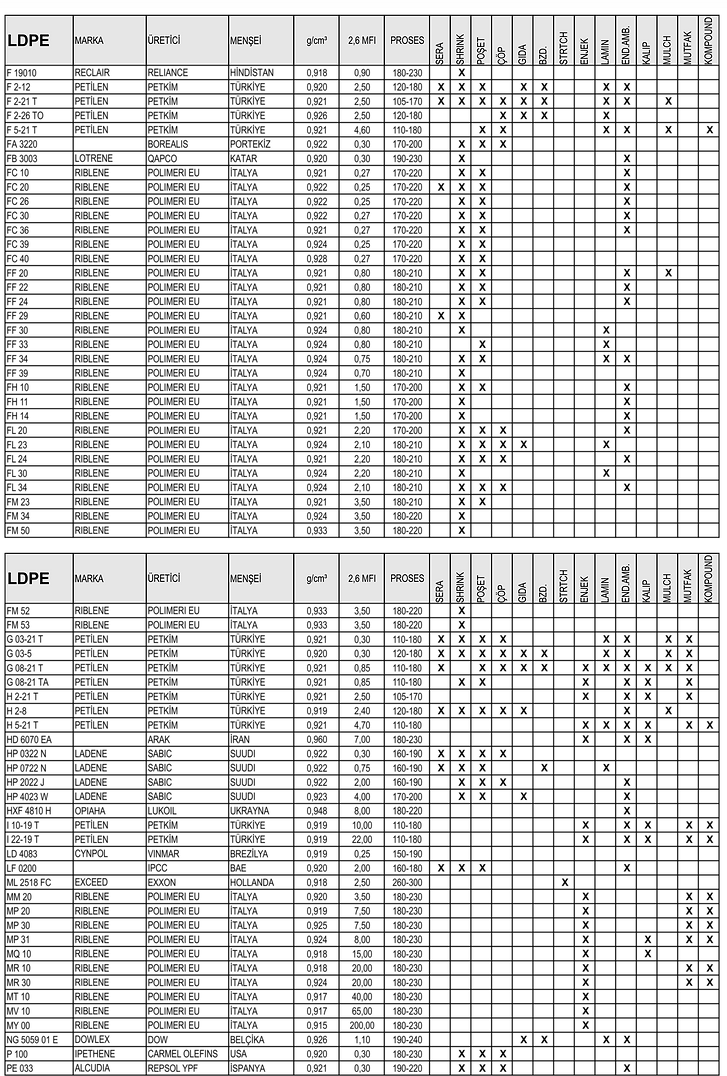

MDPE (Midium Densty PolyEthylen):
MDPE wird verwendet, um ein stärkeres und flexibleres Endprodukt als LDPE (Polyethylen mittlerer Dichte) zu erhalten.
MDPE ist ein Thermoplast mit einer Dichte zwischen 0,926 und 0,940 g / cm³, weniger dicht als das üblicherweise verwendete HDPE. Wenn es mit LDPE gemischt werden muss, hat es eine bessere chemische Beständigkeit als LDPE. Trotz alledem ist es das am wenigsten verwendete Polyethylen. MDPE wird hauptsächlich in Gasleitungen und -armaturen, Beuteln, Schrumpffolien, Verpackungsfolien, Tragetaschen und geblasenen Flaschen verwendet.
-
Es ist stoß- und sturzsicher.
-
Es bietet eine bessere Schnittreaktion als HDPE.
-
Es zeigt eine höhere Beständigkeit gegen Zugrisse als HDPE.
-
Es hat eine mittelhohe Hitzebeständigkeit.
-
Seine Dichte ist im Vergleich zu HDPE sehr gering.
-
Entspricht den Regeln für die Lebensmittelverarbeitung.
ULDPE (Ultra Low Densty PolyEthylen):
ULDPE (Polyethylen mit extrem niedriger Dichte) und VLDPE (Polyethylen mit sehr niedriger Dichte) sind grundsätzlich LDPEs mit einer Dichte unter 0,880 g / cm³. ULDPEs werden hauptsächlich als Schlagverstärker für andere Polyolefine verwendet. Die Präferenzrate ist hoch bei der Herstellung von Bewässerungsrohren in Verpackungen für Lebensmittel-, Gesundheits- und Hygienezwecke sowie für Allzweckfolien.
-
Zeigt Flexibilität bei niedrigen Temperaturen
-
Funktioniert sehr gut für Flüssigkeitsbehälter
-
Es hat gute optische Eigenschaften.
-
Wird hauptsächlich durch Blas- und Spritzguss verwendet
-
Entspricht den Regeln für die Lebensmittelverarbeitung.
mPE (Metallocen PolyEthylen):
Diese Polymere sind eine neue Generation von Hochleistungspolyethylenen (PE), auch lineares Metallocen genannt. Sie werden in einer Vielzahl von Folienanwendungen wie Verpackungen, Landwirtschaft, Bauwesen sowie Bau- und Industrieanwendungen eingesetzt. Es bietet eine hervorragende Leistung, indem es die allgemeinen Eigenschaften von PE erheblich verbessert und dem hergestellten Produkt einen Mehrwert verleiht. Es liefert hervorragende Ergebnisse bei der Herstellung von Verpackungen für Verpackungen (Folien zum Laminieren) (Stretchfolien), Beschichtungen für Extrusionsprozesse und landwirtschaftlichen Abdeckungen.
-
Sehr widerstandsfähig gegen Stöße, Einstiche und Risse
-
Einfache Verarbeitung mit hoher Schmelzbeständigkeit
-
Hervorragende Abdichtung (wie durch SIT- und Hot Tack-Tests gezeigt)
-
Es hat ausgezeichnete optische Eigenschaften
-
Es hat eine spezielle Struktur für die Mehrschichtfolienextrusion.
-
Bietet eine signifikante Reduzierung der Filmdicke im Vergleich zu LDPE, HDPE und LLDPE
-
Es wird für effizientere und schnellere Verpackungsprozesse und eine bessere Versiegelung bevorzugt.
-
Es wird hauptsächlich für optische Verbesserungen (Helligkeit und Transparenz) in Filmen bevorzugt.
-
Zeigt im Allgemeinen eine signifikante Verbesserung der mechanischen Eigenschaften
-
Entspricht den Regeln für die Lebensmittelverarbeitung.
Technische Werte und weitere Anwendungsbereiche einiger Rohstoffe der Marke MDPE:

LLDPE (lineares Polyethylen mit niedrigem Denstygehalt)
Lineares Polyethylen niedriger Dichte ist ein Polymer mit einer Dichte von mehr als 965 kg / m, das üblicherweise bei niedrigen Temperaturen hergestellt wird. Es wird durch Zugabe von Olefinen (Buten, Hexen oder Octen) während des Polymerisationsprozesses von Ethylen hergestellt.
Polyolefine werden zur Herstellung von linearen Polyethylenharzen niedriger Dichte verwendet, da diese Monomere eine reaktive Doppelbindung enthalten. Diese Monomere werden entsprechend verwendet, um die Dichte und die physikalischen Eigenschaften des Harzes zu steuern, das gemäß den Anforderungen des Benutzers hergestellt wird. Es wird mit zwei Haupttechniken hergestellt:
Gasphasenpolymerisation:
Bei diesem Verfahren wird ein Gasphasenreaktor verwendet, der eine Art Fließbett aus trockenen Polymerteilchen ist. Diese Harzteilchen werden als Gasreaktor gehalten, indem Ethylengas mit hoher Geschwindigkeit gemischt oder geleitet wird.
In diesem Gasreaktor wird Ethylen zusammen mit dem Comonomer vom Boden des Fließbettes zugeführt, in das der Katalysator dann injiziert wird. In diesem Gas ist der Reaktordruck relativ niedrig (bis zu 2 MPA) und die aufrechterhaltene Temperatur liegt bei etwa 70 bis 110 ° Celsius.
Schließlich werden die geschmolzenen Polymerformen mit Stabilisatoren gemischt und linear zu Pellets niedriger Dichte extrudiert. Diese Pellets werden auch zur Herstellung von Kunststoffprodukten verwendet.
Es ist ein Verfahren, bei dem lineares Polyethylen niedriger Dichte durch Gasphasenpolymerisation bei niedrigem Druck aus Ethylen erhalten wird. In einem Fließbettreaktor können unter Verwendung geeigneter fester Katalysatoren Gasphasenpolyethylene hergestellt werden, die einen weiten Bereich abdecken. Das Produkt ist trocken, fließt leicht und liegt in Form von Granulaten vor, die keine feinen Partikel enthalten.
Der Schmelzindex und die Molekulargewichtsverteilung werden durch die spezifische Wahl der Katalysatoren und Betriebsbedingungen gesteuert. Die Dichte des Polymers wird durch die Menge an Comonomer im Produkt eingestellt. Die Katalysatoreffizienz ist sehr hoch; Diese Eigenschaft eliminiert eine Katalysatortrennung nach der Reaktion. Das Merkmal des Prozesses ist, dass es die Umweltverschmutzung, die Brand- und Explosionsgefahr minimiert. Daher ist es sehr einfach zu bedienen und zu warten.
Gasethylen, Comonomer und Katalysator werden in den Reaktor eingeführt; der Reaktor hat ein Fließbett aus wachsenden Polymerteilchen; Es arbeitet bei 20 kg / cm² Druck und ca. 100 ° C. Das in das Reaktionsbett strömende Reaktionsgas wird von einem einstufigen Radialverdichter umgewälzt; Somit wird das notwendige Rohmaterial für die Polymerisationsreaktion bereitgestellt, während die Reaktionswärme aus dem Bett entfernt wird. Das Zirkulationsgas wird gekühlt, indem es durch einen Wärmetauscher geleitet wird. Das körnige Produkt fließt intermittierend in die Produktentleerungstanks. Hier wird nicht umgesetztes Gas vom Produkt getrennt. Das Abgas wird komprimiert und in den Reaktor zurückgeführt. Im Produkt verbleibende Kohlenwasserstoffe werden mit Stickstoff weggespült. Das körnige Produkt wird in einem Niedrigenergiesystem zu Pellets geformt. Die Dichte des Produktpolymers kann leicht im Bereich von 0,915 bis 0,970 g / cm gesteuert werden. Die Molekulargewichtsverteilung ist relativ zum Katalysator eng oder mittelgroß. Der Schmelzfluss kann von 1 bis über 200 variiert werden.
Lösungspolymerisation:
Bei diesem Verfahren werden lineare Polyethylenharze niedriger Dichte bei relativ niedrigen Temperaturen (70-110 ° C) mit niedrigem Druck (1-5 MPA) in einer gesättigten Kohlenwasserstoffumgebung hergestellt.
Während des Polymerisationsprozesses bildet das Polymer eine Suspension oder eine sich bewegende Aufschlämmung. Zusätzlich wird das Reaktionsmedium entfernt und das Polymer vom inerten Kohlenwasserstoffmedium abgetrennt.
Das als Ergebnis dieses Verfahrens erhaltene Pulver wird erneut mit Stabilisatoren gemischt und in Pelletform extrudiert. Diese linearen Polyethylenpellets niedriger Dichte können auch zur Herstellung von Kunststoffprodukten für das Endsegment verwendet werden.
Das Gasphasenpolymerisationsverfahren ist hinsichtlich der Betriebskosten, der Temperaturerhaltung im Verfahren und der Leichtigkeit der Flexibilität während der Polymerherstellung besser als die Lösungspolymerisation.

LLDPE ist eine Art lineares Polymer mit einer Reihe von kurzen Verzweigungen, die durch Copolymerisation von Ethylen mit verschiedenen langkettigen Olefinen erzeugt wurden und erstmals 1959 von DuPont in Kanada hergestellt wurden. Es ist wie ein Teil der Polyolefinfamilie, der einige strukturelle Unterschiede zu herkömmlichem LDPE (Polyethylen niedriger Dichte) aufweist.
Dieses Polymer hat sich neben LDPE und HDPE als dritter wichtiger Akteur in der Polyethylenindustrie erwiesen. Es hat 3% des globalen Polyethylenmarktes. Die linearen Eigenschaften des Polymers sind auf die unterschiedlichen Herstellungsverfahren von Polyethylen mit linearer Dichte und Polyethylen mit niedriger Dichte zurückzuführen.
Im Allgemeinen wird LLDPE bei relativ niedrigeren Temperaturen und Drücken durch Copolymerisation von Ethylen und höheren Alpha-Olefinen wie Buten, Hexen oder Octen (oben beschrieben) hergestellt. LLDPE weist im Vergleich zu herkömmlichen LDPE-Polymeren eine höhere Zugfestigkeit, Schlagfestigkeit und Druckbeständigkeit auf, wodurch es für eine Vielzahl von Anwendungen und Anwendungen geeignet ist.
Lineare Polyethylenharze niedriger Dichte werden hauptsächlich als Folien für Beutel und Folien oder in der Verpackungsindustrie verwendet. Es wird auch zur Herstellung anderer Produkte wie Spielzeug, Kappen, Eimer, Kunststoffbehälter, Luftpolsterfolie und Verbundfolien verwendet. LLDPE ist eine Art lineares Polymer mit einer signifikanten Anzahl von Verzweigungen. Es wird häufig für Anwendungen wie Spritzguss, Rotationsformen, Drähte, Platten, Rohre und Kanäle verwendet. Sie werden auch bei der Herstellung von Waren für Endverbraucherindustrien wie Verpackung, Landwirtschaft, Bauwesen, Automobilindustrie, Haushalt, Schifffahrt und Spielzeug verwendet.
Nordamerika war der größte Verbraucher von linearem Polyethylen niedriger Dichte, gefolgt von den Regionen im asiatisch-pazifischen Raum.
Die Erzeugerunternehmen von Borealis, Braskem SA, Chevron Phillip Chemical Co., DuPont, ExxonMobil Chemical, der INEOS Group, Nova Chemicals und The Dow Chemical Company priorisieren den LLDPE-Markt.
LLDPE Hauptmerkmale:
Es bietet die vom Produkt gewünschte ausgewogene Härte und Zähigkeit und ist ein wesentlicher Baustein für die Film- und Verpackungsindustrie. Die Eigenschaften des linearen Materials mit niedriger Dichte, das Gleichgewicht zwischen physikalischen und chemischen Eigenschaften machen es zu einem idealen Polymer für die Verpackung von Verbrauchsmaterialien, Hochleistungs-Versandtaschen, Folien (Mischen von Schrumpffolien und Stretchfolien usw.) sowie für die Herstellung von Behältern und Kappen.
-
Sie bieten eine höhere Zugfestigkeit, hohe Schlagfestigkeit und hohe Durchstoßfestigkeit.
-
Lineare Polyethylenmaterialien niedriger Dichte sind sehr flexibel und dehnen sich im Allgemeinen unter Spannungsbedingungen.
-
Da diese Polymere eine gute Beständigkeit gegen Spannungsrisse in der Umwelt aufweisen, können sie leicht zur Herstellung dünner Filme verwendet werden.
-
Lineare Kunststoffe mit niedriger Dichte haben nicht nur gute elektrische Eigenschaften, sondern sind auch äußerst chemikalienbeständig.
-
Sie haben höhere mechanische und verbesserte Dichtungseigenschaften.
-
Es hat ein transparentes und glänzendes Aussehen, das den Endprodukten ein gutes Finish verleiht.
-
Lineare Polymere niedriger Dichte haben niedrige Produktions- und Umwandlungskosten.
-
Zugfestigkeit 30 MPA und Kerbschlagzähigkeit 06+ kJ / m
-
Dichte 916 g / cm³
-
Die maximale Betriebstemperatur beträgt 50 ° C.
-
Lineare Ausdehnung 20 × 10−5 / ° C angeboten
-
Die Wasseraufnahme beträgt normalerweise 01%
-
Schmelztemperatur Der Polymerbereich liegt zwischen 120 und 160 ° C.
-
Diese Materialien bieten hohe Flexibilität und lange Lebensdauer.
-
Es hat eine gute Beständigkeit gegen UV-Strahlen und Chemikalien.
-
Lineare Kunststoffe mit niedriger Dichte sind sehr pannensicher.
-
Lineare Polyethylenmaterialien niedriger Dichte weisen robuste mechanische Eigenschaften und weniger Wartung auf.
-
Sie haben eine hohe Zugfestigkeit.
-
Es ist eine ausgezeichnete Umgebung und ein Material, das gegen Spannungsrisse beständig ist.
-
Es ist weniger glänzend im Vergleich zu LDPE.
-
Bei diesen Materialien ist der Temperaturbereich der thermischen Bindung geringer.
-
Im Vergleich zu LDPE bietet es keine einfache Flexibilität in der Verarbeitungsphase.
LLDPE-Verwendungsbereiche:
LLDPE wird häufig zur Herstellung einer Kunststofffolie für eine Vielzahl von Anwendungen verwendet.
Bei diesem Verfahren werden LLDPE-Blasfolienharze in Flachtrommelextrudern verarbeitet. Die Länge dieser Fässer kann zwischen 24: 1 und 30: 1 liegen. Da es nicht einfach ist, den Blasendurchmesser zu messen, wird er aus einer flachen Plattenbreite von 2: 1 bis 3: 5: 1 berechnet.
Aufgrund der engen Molekulargewichtsverteilung von LLDPE-Harzen müssen Filme zwischen weiten Bereichen von 90 bis 110 mil extrudiert werden. Wenn der Formhohlraum für Harze zu eng ist, kann der Film schmelzen und brechen, und wenn der Spalt zu groß ist, kann es zu Stabilitätsproblemen bei dem hergestellten Film kommen. Bei der Herstellung dieser Filme können bestimmte Verbesserungen der Eigenschaften vorgenommen werden, indem die Höhe der LLDPE-Gefrierlinie eingestellt wird. Bessere mechanische Eigenschaften und Filmklarheit können erreicht werden, indem das Niveau während der Produktion gesenkt wird.
Die ungefähre Temperatur, bei der lineare Polyethylenharze niedriger Dichte im Extruder geschmolzen werden, liegt zwischen 200 und 230 ° C.
-
Es ist sehr flexibel und reicht von 0,5 mil bis 40 mil, meist in flexiblen Blechformen.
-
Lineare Polyethylenfolien niedriger Dichte haben eine natürliche milchige Farbe und ein durchscheinendes Aussehen.
-
Sie haben eine hohe chemische und Schlagfestigkeit sowie eine gute Wasseraufnahmequalität.
-
Die lineare niedrige Dichte bietet eine hervorragende Schlag- und Spannungsrissbeständigkeit
-
Sie haben üblicherweise eine Dichte von 93 g / cm 3.
Lineare Folien mit niedriger Dichte werden häufig in verschiedenen Branchen wie Bau-, Landwirtschafts- und Oberflächenschutzanwendungen, allen Arten von Abdeckungen, Linoleum und vielem mehr verwendet. Beispiele für hergestellte Filme sind Frischhaltefolien, landwirtschaftliche Folien, Laminierfolien und Mischschrumpffolien usw.
LLDPE-Rohr:
LLDPE hat bestimmte Eigenschaften wie ausgezeichnete Spannungsrissbeständigkeit, Flexibilität, Haltbarkeit und niedrige Kosten, wodurch sie vollständig für die Rohrindustrie geeignet sind. LLDPE-Kunststoffe werden häufig in Rohren verwendet, die Chemikalieneinwirkung, Alterung, stark vibrierende Verbindungen, hervorstehende Armaturen und andere Klemmringverschraubungen enthalten.
Es kann problemlos 500 Stunden und länger verschiedenen Lösungen und Chemikalien ausgesetzt werden. Sie können sogar Rissen widerstehen, wenn sie mit Kompression verwendet oder zum Anschließen von Armaturen gedrückt werden. Charakteristische Merkmale von LLDPE-Rohren:
-
Höhere Zugfestigkeit und hoher Berstdruck.
-
Sie bieten überlegene Spannungs- und Rissbeständigkeit.
-
Diese Röhren haben eine ausgezeichnete hohe Durchstoßfestigkeit.
-
Lineare Polyethylenrohre niedriger Dichte sind für Gase und Feuchtigkeit sehr undurchlässig.
-
Sie haben überlegene dielektrische Eigenschaften.
-
Es ist leicht, langlebig und wirtschaftlich.
-
Erhältlich in verschiedenen Farben wie Schwarz, Grau, Rot, Grün, Blau, Gelb, Orange, Hell und Lila.
-
Temperaturbereich für diese Röhren: -40 ° C bis 66 ° C
-
Vakuumbewertung: bis 28 '' Hg
-
Durchmessertoleranz dieser Rohre: ± 0,004 ”
-
Röhrenmarker: FW-Funktionen
-
Arbeitsdruck: 3: 1 Sicherheitsfaktor
-
Geeignet für Lebensmittel und Getränke sowie für medizinische und pharmazeutische Anwendungen.
LLDPE-Beutel:
Lineare Polyethylenmaterialien niedriger Dichte wie HDPE (Polyethylen hoher Dichte) und LDPE (Polyethylen niedriger Dichte) werden ebenfalls häufig verwendet, um verschiedene Polybeutel herzustellen, die für eine Vielzahl von Anwendungen verwendet werden können.
Industrielle Polybeutel werden häufig aus diesen Materialien hergestellt, da sie unter stressigen oder anderen extremen Bedingungen eine hohe Bruch- und Durchstoßfestigkeit bieten. Diese Plastiktüten werden als Einkaufstüten, Taschen in Bekleidungsgeschäften, Hochleistungstaschen, Einkaufstüten oder große Müllsäcke verwendet.
Diese Poly-Taschen sind sehr flexibel, kratzfest und langlebig mit hoher Schlag- und Zugfestigkeit. Diese Polybeutel sind wirtschaftlicher als andere, da lineares Polyethylen niedriger Dichte ein kostengünstiges Material ist und leicht verfügbar ist.
Sie haben ein glänzendes Aussehen und können zur Wiederverwendung recycelt werden. Die heutigen linearen Plastiktüten mit niedriger Dichte werden aus weitgehend recycelten Polyethylenmaterialien mit linearer Dichte hergestellt.
LLDPE-Abdeckungen:
Lineare Polyethylenauskleidungen niedriger Dichte oder lineare Polyethylenpolymer-Geomembranen niedriger Dichte sind aufgrund ihrer Festigkeit, Flexibilität und Haltbarkeit für eine Vielzahl von Anwendungen erforderlich. Ihre Dicke kann zwischen 0,5 und 2,5 mm variieren, und lineare Auskleidungswalzen mit niedriger Dichte sind je nach Dicke in verschiedenen Breiten und Längen erhältlich.
LLDPE-Material ist aus folgenden Gründen eine ideale Wahl für die Herstellung von Kunststoffauskleidungen:
-
Diese Geomembranen bieten ein hohes Maß an Flexibilität. Dies ist vorteilhaft, da es mehr Flexibilität, mehr Anpassung an das Zusammenfallen und eine andere Passform ermöglicht.
-
Sie sind stark beständig gegen UV-Strahlen und Chemikalien.
-
Diese Shirts sind hoch pannensicher und langlebiger als ihre Konkurrenten.
-
Diese Grundierungen sind auf Anfrage in zwei verschiedenen Oberflächenfarben erhältlich: Weiß und Schwarz.
-
Es wird als Grundierung in Lagunen, Kanälen, Tanks und Teichen (Halteteiche, landwirtschaftliche Teiche usw.) verwendet.
-
Lineare Polyethylenauskleidungen niedriger Dichte werden häufig für Deponiedeckel und -verschlüsse verwendet.
-
Diese Geomembranen werden für den Abbau von Haufenlaugungskissen verwendet.
-
Auskleidungen werden auch zur Aufbereitung von Rohwasser in Stauseen, Abwässern sowie tragbaren Wasserspeichern verwendet.
-
Wird als Sekundärschadstoff für oberirdische Lagertanks und als schwimmende Abdeckung für Wassertanks verwendet.
LLDPE Buten-C4 / Hexen-C6 / Octen-C8:
Es gibt eine Vielzahl von linearen Polyethylenqualitäten niedriger Dichte (LLDPE) von C8-Octen bis C6-Hexen und C4-Buten, die von hoher Dichte (bis zu 0,941 g / cm3) bis zu sehr niedriger Dichte (0,905 g / cm3) reichen. LLDPE wird für die Folienextrusion, das Blasformen, das Rotationsformen und das Spritzgießen für Lebensmittel, Tiefkühlverpackungen, Strahlungsheizrohre sowie kosmetische und pharmazeutische Anwendungen verwendet. Weltweit rund 80%, gemischt mit LDPE und HDPE für verbesserte mechanische und thermische Eigenschaften. Es wird zum Verpacken von Lebensmittelverpackungen und anderen Produkten, für Extrusionsbeschichtungsanwendungen und insbesondere zum Verpacken von Papier und Pappe verwendet.
Vorteile:
-
Multidirektional,
-
Wirtschaftlich
-
Bodendichtungstemperatur mit guten mechanischen Eigenschaften
-
Große Einsparungen bei Hochleistungsstrukturen
Eigenschaften:
-
Sehr flexibel,
-
Hohe Zugfestigkeit
-
Gute chemische Beständigkeit
-
Gute elektrische Eigenschaften
-
Entspricht den Regeln für die Lebensmittelverarbeitung
Technische Werte und weitere Anwendungsbereiche einiger Rohstoffe der Marke LLDPE:

Metalosen LLDPE
Strech filmlerin üretimi, strech başlık filmleri, süt filmleri, yüksek mukavemetli genel amaçlı filmler, laminasyon filmleri, sera, tarım ve diğer filmler; ayrıca tek başına veya diğer polietilen türlerine katkı maddesi olarak kullanılır.
Metalosen polietilenden üretilen filmler mükemmel mekanik mukavemete ve kalınlığı azaltma potansiyeline sahiptir, moleküllerin homojen bileşimi mükemmel sıcak dikiş mukavemetini ve düşük erime noktasını belirler, böylece daha hızlı kaynak sağlar. Üfleme ve enjeksiyon kalıplama yönteminde metalosenlerin kullanılması, daha az bulanıklık ve yüksek parlaklığa sahip bir film üretmenizi sağlar. Yüksek darbe direnci ile karakterize, mükemmel yalıtım nitelikleri sunar.
mLLDPE: 0.927 g/ cm3 yoğunlukludur ve bir hekzen kopolimeridir. mPE film sertliği, kuvveti ve darbe dayanımı gibi özellikleri ile eşsiz film performansına sahiptir. mLLDPE'nin geleneksel LLDPE`ye göre: yüksek gerilme mukavemetli, yüksek tokluğa sahip, delinme direnci ve darbe dayanımı iyileştirilmiş, sızdırmazlık kapasitesi yüksek, mükemmel saydamlık ve parlaklık gösteren ve diğer poliolefinlerle kolay karışabilme üstün özelliklerine sahip bir polimerdir.
HDPE (High Densty PolyEthylene)
Polyethylen hoher Dichte wird hauptsächlich durch Lösung in heterogener Phase und durch Massenpolymerisationstechnologien in der Gasphase hergestellt. Das Lösungspolymerisationsverfahren in homogener Phase wird ebenfalls angewendet, wenn auch nur in geringem Umfang. In jedem Fall hängt die exotherme Reaktion vom Ethylenmonomer, dem <P255> -Katalysatorsystem und dem Kohlenwasserstoffverdünnungsmittel ab. Die Molekulargewichtskontrolle wird durch den Katalysator und den Wasserstoff erreicht, die während der Reaktion verwendet werden.
Es ist ein Verfahren, bei dem Polyethylen hoher Dichte aus Ethylen durch Lösungspolymerisation bei niedrigem Druck erhalten wird. Ethylen (und gegebenenfalls kleine Mengen an Comonomeren), Katalysator und Kohlenwasserstoffverdünnungsmittel werden in den großen Polymerisationsreaktor geschickt. Bei der Reaktion wird Schlamm gebildet und das Polymer wird in Pulverform gebildet. Die Polymerisation erfolgt unter 10 bar und zwischen 80 und 90 ° C. Die Katalysatoraktivität ist sehr hoch; Aus diesem Grund wird der Katalysator allmählich zugegeben, um die Notwendigkeit einer anschließenden Katalysatortrennung in großen Mengen zu vermeiden. Da alles Ethylen polymerisiert ist, gibt es in dem Verfahren keine Ethylenumkehr- oder Monomerrückgewinnungssysteme. Das Kohlenwasserstoffverdünnungsmittel wird durch Zentrifugation aus dem Produkt entfernt und die endgültige Trocknung erfolgt in einem stickstoffbetriebenen Wirbelschichttrockner. Der größte Teil des abgetrennten Verdünnungsmittels wird in den Prozess zurückgeführt. Das erhaltene HDPE-Pulverprodukt wird durch Färben oder auf natürliche Weise in Granulatform umgewandelt.

HDPE wird auch als "Alketen" oder "Polyethylen" bezeichnet, wenn es für Rohre verwendet wird, eine Art Thermoplast aus Erdöl. Es ist der am häufigsten verwendete Kunststoff der Welt. Hochdichtes Rationspolymer wird hauptsächlich zur Herstellung von Kunststoffflaschen, korrosionsbeständigen Rohren, Geomembranen und Kunststoffschnittholz verwendet.
Das Unterscheidungsmerkmal von HDPE, das es ideal für die Verpackungsindustrie macht; Es ist stärker als Standard-Polyethylen und bildet eine starke Barriere gegen Feuchtigkeit. Mit Sitz in China ist ganz Asien die führende Region bei der Herstellung von Polyethylen hoher Dichte. Es hat einen Anteil von 40% an der globalen Produktionskapazität des Polymers. Die zweitgrößte Region in der Polymerproduktion ist Nordamerika mit einem Anteil von 20%, gefolgt vom Nahen Osten mit 17%. Der Nahe Osten und China sind neben neuen Produktionskapazitäten die am schnellsten wachsenden Regionen. Der Haupttreiber des HDPE-Marktes ist die steigende Nachfrage in der Verpackungsindustrie. Es ist ein bevorzugtes Material in der Verpackungsindustrie, da es ein relativ kostengünstiges Material ist. Die steigende Nachfrage nach Kunststoffrohren, die anstelle von Hausinstallationen weit verbreitet sind, ist die wichtigste Triebkraft für dieses Material auf dem Weltmarkt.
Es wurde 1953 durch Forschungen von Karl Ziegler und Erhard Holzkamp vom Kaiser-Wilhelm-Institut erfunden.
Zwei Jahre nach der Erfindung dieses Materials wurden Rohre aus Polyethylen hoher Dichte erfunden. Polyethylen hoher Dichte ist heute aufgrund seiner Zähigkeit, Flexibilität und chemischen Beständigkeit das am häufigsten verwendete Material in Rohren.
Zunehmende landwirtschaftliche Aktivitäten in den letzten Jahren haben die Nachfrage nach Rohren mit hoher Dichte aufgrund der Verwendung von Entwässerungsrohren mit hoher Dichte in landwirtschaftlichen Entwässerungssystemen erhöht.
HDPE Hauptmerkmale:
Das Material ist eines der langlebigsten und vielseitigsten Thermoplaste, die auf dem heutigen Kunststoffmarkt in großem Maßstab eingesetzt werden. Aufgrund seiner praktischen Eigenschaften können Flaschen, Autoteile, Möbel usw. Es wird zur Herstellung einer Vielzahl von Materialien verwendet. Die grundlegenden Eigenschaften des Polymers sind wie folgt:
-
Materialien haben ein hohes Verhältnis von Festigkeit zu Dichte.
-
Sie sehen durchscheinend und wachsartig aus.
-
Harze sind leicht flexibel und sehr witterungsbeständig.
-
Sie haben eine gute Zähigkeit bei niedriger Temperatur.
-
Sie sind extrem chemikalienbeständig und nicht leicht korrodierbar
-
Kunststoffe aus Polyethylen hoher Dichte sind leicht, leicht verfügbar und wirtschaftlich.
-
Sie haben eine geringe Feuchtigkeitsaufnahme.
-
Materialien sind mit thermoplastischen Schweißgeräten leicht zu schweißen.
-
Zugfestigkeit 0,20 - 0,40 N / mm² und Kerbschlagzähigkeit unzerbrechlich Kj / m²
-
Wärmeausdehnungskoeffizient 100-220 x 10-6
-
Max. Verbrauchstemperatur 65 ° C.
-
Dichte 0,944 - 0,965 g / cm 3
-
Die Materialien sind stark beständig gegen alle Arten von verdünnten Säuren und Laugen.
-
Sie sind mäßig beständig gegen Öl und Fett.
-
Es hat eine schlechte Beständigkeit gegen Kohlenwasserstoffe wie Harze, aliphatische Kohlenwasserstoffe, aromatische Kohlenwasserstoffe und halogenierte Kohlenwasserstoffe.
-
Sie sind sehr resistent gegen Alkohol.
-
Es ist leicht verfügbar und ein kostengünstiges Material.
-
Polyethylen hoher Dichte, gute Schlagfestigkeit und Zugfestigkeit.
-
Harze können mit allen thermoplastischen Methoden leicht verarbeitet werden.
-
Kunststoffe sind sehr beständig gegen Chemikalien, Korrosion und Klimaveränderungen
-
Kunststoffe aus Materialien sind langlebig, flexibel, stark und leicht.
-
Es hat eine hohe Wärmeausdehnung.
-
Beständig gegen schlechte Wetterbedingungen
-
Kunststoffe unterliegen häufig Spannungsrissen.
-
Polymere sind brennbar und zeigen unter bestimmten Bedingungen eine schlechte Temperaturbeständigkeit.
HDPE-Verwendungsbereiche:
Dieser Kunststoff ist einer der beliebtesten der Welt. Es ist ein vielseitiges Polymer, das für eine Vielzahl von Anwendungen geeignet ist, von hochbelastbaren feuchtigkeitsbeständigen Membranen in Gebäuden bis hin zu leichten, flexiblen Beuteln und Folien. Am häufigsten Flaschen und Verschlüsse, Frischwarenbeutel oder dünne Tragetaschen usw. Verwenden für.
Eigenschaften wie Haltbarkeit, Recyclingfähigkeit und ausgezeichnete Dampf- und Feuchtigkeitsbarriere machen sie für die Herstellung einer Vielzahl von Waren anwendbar. Es gibt verschiedene HDPE-Derivate, die bei der Extrusion, Injektion, Blasfolienherstellung und Rohrherstellung verwendet werden können.
HDPE-Blätter und Blätter:
Es wird häufig bei der Herstellung von Platten verwendet, die zur Herstellung verschiedener Kunststoffprodukte verwendet werden. Die Bleche sind stark und beständig gegen Chemikalien und Temperaturen mit einem niedrigen Reibungskoeffizienten. Aufgrund ihrer extremen Haltbarkeit eignen sie sich perfekt für Wassertanks, industrielle Anwendungen oder Produkte wie Flaschen und Verschlüsse.
Matte Blätter; Es wird hauptsächlich zur Herstellung von Gegenständen wie Schneidebrettern verwendet, da das Material eine lange Lebensdauer bietet und die Klingen nicht stumpf macht.
Gerade Platten; Die glatten Schichten haben eine Vielzahl von Eigenschaften, die sie für eine Vielzahl von Anwendungen gültig machen. Gleichmäßige Platten mit hoher Dichte können leicht hergestellt werden und weisen eine gute chemische Beständigkeit, Zugfestigkeit sowie eine hohe Feuchtigkeits- und Schlagfestigkeit auf. Für die Tankauskleidung wird häufig eine flache Auskleidung aus Polyethylen hoher Dichte verwendet. Sie werden hauptsächlich zum Rotationsformen großer komplexer Produkte wie Kraftstofftanks, Müllcontainer, Paletten, landwirtschaftliche Tanks und Autobahnbarrieren verwendet. Blätter werden auch häufig bei der Herstellung verschiedener Beutel und Flaschen sowie in der Verpackungsindustrie verwendet.
Rohrplatten und Ausrüstung; Sie haben einige verbesserte Eigenschaften als die Standardbeschichtung mit hoher Dichte in Bezug auf Gewicht und Leistung, wodurch sie für die Rohrherstellung geeignet sind.
Polyethylenpolymer hoher Dichte wird hauptsächlich bei der Herstellung von Rohren verwendet. Harze werden in großen Mengen bei der Rohrherstellung verwendet, da sie haltbarer, leichter, wetterbeständiger und einfacher Materialfluss sind. Diese Rohre werden in verschiedenen Sektoren wie Kommunen, Industrie, Energie, Geothermie und Deponien eingesetzt.
Rohre mit hoher Dichte weisen aufgrund des Schmelzprozesses keine Leckage auf und bilden ein monolithisches Polyethylen-System mit hoher Dichte, was sich als das am besten geeignete Material für Rohre und Formstücke herausstellt. Diese Rohre sind umweltfreundlicher, da sie ungiftig und sehr langlebig sind.
-
Sie lecken nicht und bieten hervorragende Fließeigenschaften.
-
Sie sind sehr beständig gegen Chemikalien, Korrosion und Abrieb.
-
Rohre und Formstücke bieten eine starke Duktilität und Zähigkeit.
-
Erhältlich in Durchmessern von ½ Zoll bis 63 Zoll und bietet eine Vielzahl von Herstellern.
-
Sie halten gefrorenem Wasser besser stand als herkömmliche Metallrohrsysteme.
-
Es ist sehr langlebig und bietet langfristige Wirtschaftlichkeit, Wert und Abhängigkeit.
Antiskit; Es wurde speziell für Schiffsanwendungen hergestellt, bei denen eine Gleit- oder Gleitfläche erforderlich ist.
HDPE-Taschen:
Polymere mit hoher Dichte werden auch verwendet, um Polybeutel in sehr großem Maßstab herzustellen. Die grundlegenden Eigenschaften des Materials machen sie für die Herstellung verschiedener Polybeutel sehr gut geeignet. Diese Polybeutel werden entsprechend ihrer Anwendung und Verwendung hergestellt. Harze werden zur Herstellung von frischen Polybeuteln, Brad-Beuteln, Lebensmittelsäcken, Transportbeuteln mit dünner Stärke und anderen verwendet.
-
HDPE-Beutel sind beständig gegen hohe und niedrige Temperaturen.
-
Da es sich um ein additivfreies Material handelt, eignen sich Beutel ideal zum Verpacken von Produkten.
-
HDPE-Beutel bieten kratzfeste Eigenschaften, die auch für die Verpackungsindustrie geeignet sind.
-
Diese Taschen sind härter, stärker und haben eine bessere Feuchtigkeitsspeicherkapazität.
-
Da das Material trüb und stumpf ist, gibt es den hergestellten Beuteln keine Klarheit.
-
Wenn HDPE-Beutel eingekerbt werden, ist es sehr einfach, diese Beutel in der Richtung zu zerreißen, in der die Folie extrudiert wird.
HDPE-Abdeckungen:
Polyethylen hoher Dichte wird aufgrund seiner hohen Verfügbarkeit und geringen Materialkosten weltweit häufig als Geomembran verwendet. Es ist beständig gegen Chemikalien, UV-Strahlung und Ozon und eignet sich daher für die Primerherstellung. Auskleidungen werden hauptsächlich in Deponien, Lagunen zur Abwasserbehandlung, Lagunen für tierische Abfälle und Bergbauanwendungen verwendet. Diese Liner sind in großen Rollen erhältlich, die ungefähr 22,5 Zoll breit sind.
Sie sind langlebige und UV-beständige Materialien. Sie haben eine gute chemische und Temperaturbeständigkeit.
Abgesehen von all diesen; Sie können als Mülldeponie, Bergbaubecken und sogar zur Behandlung aller wasserverschmutzten Gegenstände verwendet werden. HDPE-Kunststoffe sind aufgrund ihrer Haltbarkeit, Flexibilität und Leichtigkeit für verschiedene Endsegmentprodukte wie Plastikflaschen und -verschlüsse (Wasserflaschen, Getränke usw.), Spielzeug (Spielplätze im Außen- und Innenbereich), Chemikalienbehälter (Shampoo, Conditioner) geeignet. , Reinigungsmittel, Motoröl usw.), Schiffbau und Möbel (Schränke, Rasenmöbel, Schließfächer, Arbeitsplatten für Badezimmer) und viele andere Haushaltsprodukte, die im täglichen Leben verwendet werden.
Informationen zu HDPE Recycling finden Sie hier.
Technische Werte und mehr Anwendungsbereiche einiger Rohstoffe der Marke HDPE:


Unterschiede zwischen LLDPE / LDPE / HDPE
Polyethylen hoher Dichte (HDPE), Polyethylen niedriger Dichte (LDPE) und lineares Polyethylen niedriger Dichte (LLDPE) sind eine andere Art von Polyethylenpolymeren, die alle in den Endsegmentmärkten zur Herstellung von Kunststoffprodukten verwendet werden.
Sie alle haben spezifische Eigenschaften, die sie für eine Vielzahl unterschiedlicher Verwendungszwecke anwendbar machen. Der Hauptunterschied zwischen diesen Harzen ist ihre Zellstruktur oder molekulare Bindung miteinander, was anzeigt, wie eng sie gebildet sind.
Am flexibelsten: LLDPE ist die flexibelste Form von Kunststoff. Es ist eine verfeinerte Form von LDPE mit größerer Flexibilität, Zugfestigkeit und Konformität. Aufgrund seiner starken und praktischen Eigenschaften wird es häufig für Folien und Folien verwendet. Es ist weit verbreitet für Teiche und Kanäle.
Am häufigsten verwendet: LDPE ist die am häufigsten verwendete Kunststoffart. Landwirtschaft, Bauwesen, Behälter und Deckel, Beschichtung usw. Es ist weit verbreitet in Feldern.
Der Prozessor mit den meisten Zonen: Es ist die stärkste und haltbarste Form von HDPE-Polyethylen. Es hat maximale chemische Beständigkeit und ist relativ weniger flexibel als andere Formen von Polyethylenkunststoffharzen. HDPE-Materialien weisen eine maximale UV-Beständigkeit auf, was zu ihren Zähigkeitseigenschaften beiträgt.

EVA (Ethylene Vinyl Acetate)
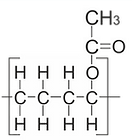
Es ist auch als Polyethylen-Vinylacetat (PEVA) bekannt. Es ist ein Copolymer aus Ethylen und Vinylacetat. Der Gewichtsprozentsatz in dieser Formation reicht von 10% bis 40% und der Rest ist Ethylen.
Es gibt drei verschiedene Arten von EVA-Copolymeren, die sich hauptsächlich in ihrem Vinylacetatgehalt und der Art und Weise, wie das Material verwendet wird, unterscheiden. Dieses poröse Elastomermaterial ist etwa dreimal flexibler als niedriges LDPE mit einer Zugdehnung von 750% und einer höchsten Schmelztemperatur von 96 ° C. Dieses Material ist im Allgemeinen nicht toxisch und weist die Eigenschaften von LDPE auf, ist jedoch bei Filmanwendungen im Allgemeinen brillanter. Sie werden zur thermoplastischen Extrusion, Filmverschmelzung und Schaumformung eingesetzt.
Es wird bei der Herstellung von Folien, Schaumstoffen, Schmelzklebstoffen, Drahtkabeln, Extrusionsbeschichtungen, Verkapselungen von Solarzellen, Spritzgießen und medizinischen Schläuchen bevorzugt.
Automobil, Verpackung und Papier, Farben, Beschichtungen und Klebstoffe, Elektronik und Elektrizität, Pharmazie, Schuhe, Photovoltaik-Panel, Landwirtschaft und Medizin.
EVA sind thermoplastische Harze, die durch das Copolymerisationsverfahren von Ethylen- und Vinylacetatmonomer in einem Hochdruckreaktor hergestellt werden.
DuPont ist das Unternehmen mit der weltweit größten EVA-Produktionskapazität. Es folgen Hanwha Chemical und Exxon Mobil.
-
Vinylacetat-modifiziertes Polyethylen (niedrige Vinylacetatdichte)
-
Thermoplastisches Ethylen-Vinylacetat (mittlere Vinylacetatdichte)
-
Es ist in drei Segmenten als Ethylen-Vinylacetat-Kautschuk (hohe Vinylacetat-Dichte).
EVA Hauptmerkmale:
EVA-Polymer hat ähnliche Eigenschaften wie Polyethylenpolymere niedriger Dichte mit einigen Verbesserungen.
Die Haupteigenschaften von EVA-Harzen sind:
-
Das Material bietet gute Klarheit und Glanz.
-
Es ist sehr beständig gegen Spannungsrisse und UV-Strahlen.
-
Niedrigtemperaturbeständigkeit.
-
Hoher Reibungskoeffizient.
-
Es hat einen charakteristischen essigartigen Duft.
-
Schmelzpunkt - 75 ° C.
-
Die Zugfestigkeit N beträgt 0,05 bis 0,2 / mm 2 und die Kerbschlagzähigkeit ein Zwischenprodukt von Kj / m 2
-
Die Dichte bei 25 ° C beträgt 0,948 g / ml
-
Flammpunkt - 260 ° C.
-
Wärmeausdehnungskoeffizient 160-200 x 10-6
-
Stabilität - Stabil, unverträglich mit brennbaren und starken Oxidationsmitteln.
-
Sie zeigen eine sehr gute Beständigkeit gegen verdünnte Säuren und Laugen, aliphatische Kohlenwasserstoffe, Alkohole, Öle und Fette.
-
Sie sind schlecht beständig gegen aromatische Kohlenwasserstoffe und halogenierte Kohlenwasserstoffe.
-
Sie zeigen eine ausgezeichnete thermische Haftfestigkeit.
-
Sie bieten auch bei niedrigen Temperaturen ein hohes Maß an Flexibilität.
-
Es ist beständig gegen Dehnung und Rissbildung.
-
Sie können leicht mit traditionellen thermoplastischen Techniken verarbeitet werden.
-
Schlechte Zugfestigkeit im Vergleich zu seinen Ersatzstoffen
-
Geringerer Widerstand gegen Wärmeverformung
-
Es hat im Vergleich zu seinen Konkurrenten eine schlechte chemische Beständigkeit und Barriereeigenschaften.
EVA-Nutzungsbereiche:
Im Allgemeinen ist EVA auf eine Reihe verschiedener Endanwendungen anwendbar, wie z. B. flexible Verpackungen, Heißsiegelschichten, Wärmelaminierungen, Schläuche und Schläuche, blasgeformte Flaschen und Verkleidungen.
Da EVA-Harze leicht aus Blechen geschnitten und in jede gewünschte Form gebracht werden können, werden sie auch zur Herstellung komplexer Endverbraucherprodukte verwendet. Es kann zur Herstellung von Orthesen, Zigaretten, Surfbrettern, mageren Brettern und sogar künstlichen Blumen verwendet werden.
Sie werden sogar für thermoplastische Mundschützer und weichmachende oder wasserdichte Leder verwendet.
EVA-Schaum:
Ethylenvinylacetat ist eine Art geschlossenzelliger Schaum. Es ist ein weiches und haltbares Ethylen- und Vinylacetat-Polymer, das häufig in Fußböden verwendet wird. Es hat auch eine Vielzahl anderer Verwendungszwecke wie Sportausrüstung, Handwerk und Bühnenbild. Da EVA von Natur aus weich ist, ohne schwammig zu sein, wird es häufig bei der Herstellung von Flip-Flops verwendet.
Eigenschaften Grundlegende Eigenschaften von EVA-Schaummaterialien:
-
Sie sind extrem witterungs- und chemikalienbeständig und flexibel.
-
Aufgrund ihrer geringen Wasseraufnahme sind sie unempfindlich gegen Verschütten.
-
Sie sind chemikalienbeständig.
-
Sie zeigen aufgrund ihrer Natur keine toxischen Eigenschaften.
EVA-Schaum hat gute Schaumproduktionseigenschaften. Zur Herstellung von EVA-Schäumen und -Blättern können verschiedene Methoden angewendet werden:
-
Scum Stripping: Das Strippen ist eine Methode zur Herstellung dünnerer Schaumstoffplatten als Rohplatten, die mit einer Schaummaschine hergestellt werden. Das Entfernen von Schaum ist immer der erste Schritt im verbleibenden Schaumproduktionsprozess.
-
Schaumschneiden: Mit diesem Verfahren werden Schaumstoffplatten in Blöcke und Streifen geschnitten. Es ist eine nützliche und effiziente Technik zur Herstellung von EVA-Schaummaterialien. Sägemaschinenblätter aus Schaumstoff werden auf die gewünschte Länge und Breite zugeschnitten. Es werden zwei Arten von Sägemethoden verwendet, die erste ist die vertikale Säge und die zweite die horizontale Säge. Die Endprodukte beider Arten von Sägemaschinen sind Schaumstoffplatten, -blöcke und -streifen.
-
Spezielles Stanzen: Diese Stanzmethode wird in verschiedenen Branchen eingesetzt, z. B. bei Papierverpackungen, bei denen eine Stanzung aus Stahl zum Schneiden der Papierbox verwendet wird. Ebenso wird das Stanzverfahren zur Schaumherstellung verwendet. Dieses Verfahren wird im Allgemeinen bei der Herstellung von Verpackungen, Schaumstoffeinlagen, Schaumstoffprofilen und Schaumstoffdichtungskissen bevorzugt.
-
Schaumlaminierung: Erforderlich, wenn der Kleberücken, die Filzoberfläche, der Stoff und der Filmträger von EVA-Schaummaterialien erforderlich sind. Dabei werden zwei Arten von EVA-Schaumlaminierungsmethoden verwendet. Die erste Methode ist die PAS-Laminierung (Klebstoffkaschierung) und die zweite Methode ist die Wärmelaminierung. Während Klebstoffe für die Laminierung bei der Klebstofflaminierung verwendet werden, verwendet das andere Verfahren eine beheizte Schaumoberfläche für den Laminierungsprozess.
-
Schaumthermoformung: Die Schaumthermoformung erfolgt, um einen flexibleren und haltbareren Schaum zu erzielen. Dieser Prozess wird hauptsächlich zur Herstellung von 3D-Schaumstoffteilen verwendet. Da es beim Thermoformen selbst um Erwärmung und Temperaturen geht, arbeitet diese Technik nach denselben Prinzipien. Die im Tiefziehverfahren verwendeten Maschinen werden entsprechend der gewünschten Temperatur und Temperatur eingestellt, und in den Formen werden unter Erwärmung und Druck spezielle Schaumteile erzeugt.
Vorteile der Verwendung von Eva Foam:
-
Sie bieten einfache Arbeit und sind in verschiedenen Stärken, Farben und Dichten erhältlich.
-
Es kann leicht mit Hilfe von Wärme geformt und sogar auf andere Materialien geklebt werden.
-
Diese Schaumstoffe können leicht gefärbt werden.
-
EVA-Schäume können leicht transportiert, gelagert und wieder aufgebaut werden.
-
Es ist leicht zu reinigen.
-
EVA-Schäume bieten eine Kombination aus Haltbarkeit, Komfort und Benutzerfreundlichkeit.
-
Diese Materialien sind sehr attraktiv und leicht erschwinglich.
EVA Schuhe und Sohlen:
EVA ist ein elastisches Copolymer, das Gummi sehr ähnlich ist und in vielen Haushalts- und Industrieanwendungen eingesetzt werden kann. Es ist ein umweltfreundliches Material, das im Produktionsprozess kein Chlor verwendet und leicht zu neuen Produkten (Spielplätze, Matten usw.) recycelt werden kann. Es ist weit verbreitet bei der Herstellung von veganen Schuhen. Die meisten Lauf- und Freizeitschuhe werden mit EVA hergestellt. Sogar einige wohlhabende Marken in der Schuhindustrie wie Timberland, Teva, Keen und Patagonia haben den Einsatz von EVA in der Schuhherstellung übernommen.
EVA-Material ist eines der besten stoßdämpfenden Materialien, die derzeit erhältlich sind. Aus diesem Grund verwenden die meisten führenden Markenjogger dies in ihren Schuhsohlen, um eine gute Kombination aus Stoßdämpfung und Leichtigkeit zu erzielen. EVA-Materialien werden häufig für die Zwischensohle von Schuhteilen, die Außensohle und die Innensohle von Sportschuhen sowie für die Sohle von Hausschuhen und Flip-Flops verwendet.
Die Vorteile der Verwendung von EVA in der Schuhherstellung sind:
-
Bietet Dämpfung und Federung in Schuhen.
-
Es erhöht die Beständigkeit der Schuhe gegen Aushärten und Risse.
-
Es nimmt kein Wasser auf und bleibt auch bei kaltem Wetter flexibel.
-
Es ist auch beständig gegen UV-Strahlen.
-
Dieses Material ist sehr beständig gegen Wasser und Korrosion.
-
Es bietet eine einfache Verarbeitung (Schneiden, Kleben, Pressen und Laminieren).
-
EVA-Sohle ist Anti-Vitalität (Stoßdämpfung mit guter Zugfestigkeit und hoher Zähigkeit)
-
Sie isolieren gegen Kälte
-
Geschlossene Schaumdämmqualität.
PEVA (Polyethylenvinylacetat)
Es ist ein chlorfreies Vinyl, das sich als direkter Ersatz für Polyvinylchlorid (PVC) erweist. Da PVC heute eine bekannte Art von Karzinogen ist, wird es nach Möglichkeit vermieden. Da PEVA von Natur aus weniger giftig als PVC ist, wird es als Ersatz für eine Vielzahl von Produkten (insbesondere Haushaltsgegenstände) verwendet.
PEVA wird in verschiedenen Haushaltsprodukten wie Duschvorhängen, Spielzeug, Schuhen, Kosmetiktaschen, Lätzchen, Plastikbezügen, Autoabdeckungen und Matratzenschutz verwendet.
Technische Werte und weitere Anwendungsbereiche einiger Rohstoffe der Marke EVA:

PP (PolyPropylene)
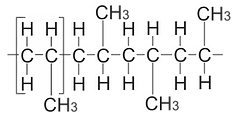
Dieser Kunststoff hat eine milchig weiße Farbe. Es hat eine sehr gute Färbefähigkeit. Seine thermischen, chemischen und elektrischen Eigenschaften sind weder sehr gut noch sehr schlecht, begrenzt. Polypropylen (PP) ähnelt in vielerlei Hinsicht Polyethylen hoher Dichte (HDPE). Anstatt eine lange Polymerkette aus sich wiederholenden -CH2-Komponenten zu bilden, weist das poröse Polypropylenmolekül eine Reihe von CH3-Gruppen auf, die das Hauptkohlenstoffgerüst suspendieren.
Seine Festigkeit und Erweichungstemperatur ist ziemlich hoch und es ist leichter als Wasser. Wie bei Polyethylen ist sein Geruch schärfer und ätzender. Es hat ähnliche Eigenschaften wie PE. Gas wird in Luftfiltern von Fahrzeugen verwendet, die mit Asbestfasern verstärkt sind, und wird auch in Verpackungs- und Sackarbeiten verwendet.
Polypropylen ist das erste unter stereoregulären Polymeren, das hergestellt wird. Die Produktion begann 1957 und nahm rasch zu und erreichte in kurzer Zeit große Mengen.
Polypropylen (PP), auch Polypropen genannt, ist von Natur aus thermoplastisch. Es ist ein lineares Kohlenwasserstoffpolymer, ausgedrückt als (CnH2n). PP-Polymer ist eines der vielseitigsten Polymere und wird sowohl als Kunststoff als auch als Faser verwendet.
Das Polymer hat harte Eigenschaften wie mechanische Robustheit und Beständigkeit gegen viele chemische Lösungsmittel wie Basen und Säuren. Dies macht Polypropylen-Kunststoff ideal für eine Vielzahl von Endverbrauchsindustrien. Der Hauptanwendungsbereich von PP-Kunststoff sind Verpackungen und Etikettierungen, Textilien, Kunststoffteile und verschiedene Arten von Mehrwegbehältern.
PP-Kunststoff wird von Herstellern auch zum Formen von Haushaltsgegenständen, Automobilprodukten, Schiffs- und Wohnwagenprodukten bevorzugt. Es ist auch sicher, PP-Kunststoffe als Lebensmittelbehälter zu verwenden, da sie verhindern, dass Chemikalien in Lebensmittelprodukte gelangen.
Polymer kann in verschiedenen Verarbeitungstechnologien wie Spritzgießen, Blasformen, Blechextrusion und Thermoformen verwendet werden.
PP-Harz wird aus Propylen hergestellt, und Propylen ist der am zweithäufigsten produzierte Baustein in der petrochemischen Industrie.
PP wird durch Polymerisation von Propylen mit metallorganischen und stereospezifischen Katalysatoren (Ziegler-Natta) unter kontrollierter Temperatur und kontrolliertem Druck erhalten. Abhängig vom angewendeten Polymerisationsverfahren und dem verwendeten Katalyse-Stricksystem zeigt die Molekülstruktur des hergestellten Polymers drei verschiedene Arten stereochemischer Konfigurationen; Dies sind isotaktische, syndiotaktische und ataktische Konfigurationen. In isotaktischem Polypropylen, dem am häufigsten verwendeten kommerziellen Polymer, befinden sich alle Methylengruppen auf derselben Seite des Polymergrundgerüsts; Daher tritt eine Struktur auf, die die Kristallbildung ermöglicht.
Später entwickelte Katalyse-Technologien zielen darauf ab, die Bildung nicht-isotaktischer Strukturen zu minimieren. Ziel ist es daher, einige der Produktionsschritte zu entfernen, die erforderlich sind, um die nicht-isotaktischen (syndiotaktischen und ataktischen) Fraktionen von dem erhaltenen Produkt zu trennen.
Es zeigt überlegene Festigkeitseigenschaften gegen viele Chemikalien. Es zeigt eine hohe mechanische und Zugfestigkeit. Es kann aufgrund seiner strukturellen Eigenschaften geschweißt werden. Die elektrischen Widerstandseigenschaften sind sehr gut. Seine geringe Dichte macht es wirtschaftlich. Es besteht aus zwei Typen: Homopolymer (PP-H) und Copolymer (PP-C).
Die Betriebstemperaturen betragen 0 bis 100 ° C für PP-H und -30 bis 90 ° C für PP-C. Seine Haupteigenschaften können eine hohe chemische Beständigkeit, eine gute Schlagfestigkeit, gute mechanische Eigenschaften und eine geringe Dichte sein.
Bei der Herstellung von Homopolymer und statistischem Copolymer werden Gaspropylen, Comonomer und Katalysator in den Reaktor gegeben. Der Reaktor hat ein Fließbett aus wachsenden Polymerteilchen; Es arbeitet bei einem Druck von 35 kg / cm² und etwa 70 ° C. Das in das Reaktionsbett strömende Reaktionsgas wird von einem einstufigen Radialverdichter umgewälzt; Somit wird das notwendige Rohmaterial für die Polymerisationsreaktion bereitgestellt, während die Reaktionswärme aus dem Bett entfernt wird. Das Zirkulationsgas wird gekühlt, indem es durch einen Wärmetauscher geleitet wird. Das körnige Produkt fließt intermittierend in die Produktentleerungstanks. Hier wird nicht umgesetztes Gas vom Produkt abgetrennt und in den Reaktor zurückgeführt. Bei der Herstellung eines schlagfesten Copolymers wird das im ersten Reaktor erhaltene Polypropylenharz in den zweiten (schlagfesten) Reaktor gebracht. Gaspropylen und Ethylen werden in diesen Reaktor geschickt, um die polymere Kautschukphase zu erhalten. Der Betrieb des zweiten Reaktors ist ähnlich dem des ersten; aber der halbe Druck. Ein Radialkompressor führt das Gas durch den Wärmetauscher zum Wirbelschichtreaktor zurück.
Schlagfestes Copolymerprodukt zum Entleeren von Tanks
kommt und das nicht umgesetzte Gas kehrt in den Reaktor zurück.
In beiden Produktionen verbleibende Kohlenwasserstoffe werden mit Stickstoff weggefegt.
Das körnige Produkt wird in einem Niedrigenergiesystem durch Zugabe geeigneter Peroxide in Pellets umgewandelt. Man kann Homopolymere mit einem Schmelzstrom von 0,1 bis 3000 und einem isotaktischen Gehalt von bis zu 99% erhalten. In statistischen Copolymeren kann Ethylen auf bis zu 12% erhöht werden, wobei der Schmelzfluss über einen weiten Bereich von 0,1 bis 100 variiert wird. Es ist möglich, enge bis breite Molekulargewichtsverteilungen zu erhalten.
Zu den Einsatzgebieten gehören Chemietanks, Ventil- und Pumpenteile, alle Arten von Kabelisolierungen und -schläuchen, Transformatoren, Relais, Antennen, Transformatoren, Radarteile, Armaturen, Spulen, Generatorisolierungen, luftdichte Dichtungen für Hochspannungsisolatoren, Kondensatoren und Transformatoren. Laminierte Platten werden für gedruckte Schaltungen hergestellt.
Katalysatoren im PP-Prozess:
Katalysatoren auf TiCl3-Basis: Isotaktisches Polypropylen (reguläre sterische Struktur) wurde erstmals 1954 von Natta mit einem Aktivatorsystem aus TiCl4 und Al (C2H5) 3 erhalten. TiCl 4 im System wurde während der Polymerisation durch Al (C 2 H 5) 3 reduziert und in festes, kristallines TiCl 3 umgewandelt, und das resultierende Polymer wurde bereitgestellt, um hohe Prozentsätze der isotaktischen Struktur zu enthalten. Später entdeckte Hecules die Rolle von Wasserstoff bei der Regulierung des Molekulargewichts. Esso erzielte bessere Ergebnisse durch Verwendung von AlCl3 in fester TiCl3-Lösung anstelle von reinem TiCl3. Mitsubishi war in der Lage, die Isotaktizität durch Zugabe eines Elektronendonors wie Carbonsäureester zu TiCl 3 auf 92 bis 94% zu erhöhen. Dieses System wird als Katalysedecke der zweiten Generation bezeichnet. Es wurde jedoch festgestellt, dass die Katalysatormaschenausbeute für eine Produktion, bei der der Rückstandsentfernungsprozess durch Reduzieren des Katalysatormaschenrückstands entfernt wird, unzureichend ist.
MgCl2-unterstützte Katalysatoren:
MgCl 2 erhöht die Effizienz des Katalyse-Netzes, es besteht keine Notwendigkeit für die Trennung von Katalyse-Netz-Rückständen, wodurch die Polymerisation in Kohlenwasserstoff-Aufschlämmung (Schlamm) erleichtert wird. Mit dieser Erfindung und weiteren Verfeinerungen wurden Katalysatoren der dritten Generation entwickelt. Somit kann eine höhere Effizienz, Stereospezifität und Morphologiekontrolle in vereinfachten Prozessen erreicht werden, bei denen das Polymerisationsmedium ein Monomer ist.
Metallocenkatalysatoren:
Single-Ended-Metallocen-Katalyse-Muster wurden entwickelt, um Ziegler-Natta-Katalysatoren zu ersetzen. Eigenschaften wie enge Molekulargewichtsverteilung, gleichmäßige Polymerketten, Transparenz und Dichte des erhaltenen Polymers sind die Hauptmerkmale von Katalysatoren in dieser Klasse.
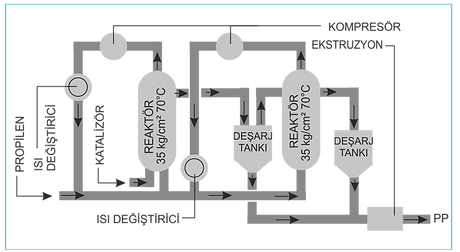
Die folgenden Schritte sind für die PP-Produktion von grundlegender Bedeutung:
-
Zunächst müssen Rohstoffe und Zusatzstoffe gereinigt werden. Katalysatormaterial muss vorbereitet werden. Das verwendete Ausgangsmaterial ist Propylen.
-
Die Polymerisation findet dann entweder in der Gasphase mit Fließbett / Rührreaktor oder in der flüssigen Phase mit der Aufschlämmung / Lösung statt.
-
Die Polymerteilchen werden dann von den vorhandenen Monomeren und Verdünnungsmitteln getrennt. Monomer und Verdünnungsmittel werden gewonnen und dabei zurückgeführt.
China ist der führende Hersteller von PP-Polymeren. Sein Anteil an der weltweiten Gesamtproduktion beträgt 27%.
Die größten PP-Hersteller auf dem Weltmarkt ab 2017 sind unten aufgeführt. (Millionen Tonnen / Jahr)

PP Grundfunktionen:
PP ist ein harter und sehr haltbarer Kunststoff. Die Eigenschaften dieses Polymers hängen vom Molekulargewicht und der Verteilung des Monomers ab. PP-Harz weist aufgrund seiner guten Wärmebeständigkeit keine Spannungsrissprobleme auf. Sie sind nicht nur durchscheinend, haben eine gute Ermüdungsbeständigkeit und sind halbstarr, sondern bieten auch andere physikalische Eigenschaften, die ihre Verwendung erweitern. Sie haben ausgezeichnete ästhetische Eigenschaften und werden daher an vielen Orten in der Automobilindustrie eingesetzt, wo Glanz und Glanz in Teilen wie Stoßstangen erforderlich sind.
PP-Harz ist beständig gegen Säuren, Basen, Wasser oder Reinigungsmittel. PP-Kunststoffe können eine gute Wahl für Behälter sein, da sie gegen Säuren und Basen beständig sind. Sie haben eine niedrige Dichte, einen hohen Erweichungspunkt und bieten eine höhere Härte und Härte. Beständig gegen organische Lösungsmittel bei Raumtemperatur.
Polypropylendichtereste zwischen 0,895 g / cm³ sind 3 amorphe und 3 Kristalle pro 0,92 g / cm³. Diese Dichte kann jedoch mit Füllstoffen geändert werden. Es ist hart und flexibel, wenn es mit Ethylen copolymerisiert wird. Es ist relativ sparsam und hat eine gute Ermüdungsbeständigkeit.
PP-Kunststoffe lassen sich aufgrund ihrer Eigenschaften leicht mit thermoplastischen Schweißgeräten schweißen. Dies führt zur Herstellung von Lagertanks für Chemikalien, Wasser und andere flüssige Materialien. Der Schmelzpunkt von Polypropylen beträgt 160 ° C.
Es gibt drei Arten von PP-Typen. Welche Klasse für eine Anwendung ausgewählt werden soll, hängt von folgenden Punkten ab:
-
Homopolymer: Diese Klasse gilt als allgemeine Klasse und kann für eine Vielzahl allgemeiner Zwecke verwendet werden. Stärker und härter als HDT-Copolymer (High Distortion Temperature). Sie sind haltbare, harte Kunststoffe, die in durchscheinendem Weiß und anderen Farben erhältlich sind.
-
Blockcopolymer: Es ist härter und haltbarer als Homopolymer. Ihre Zusammensetzung enthält 5% bis 15% Ethylen mit erhöhter Schlagzähigkeit.
-
Random Copolymer: Die chemische Zusammensetzung des Random Copolymer enthält 1% und Ethylen. Sie haben eine bessere Flexibilität; Die unteren Schmelzpunkte und Strukturen bestehen aus Komonomereinheiten, die zufällig entlang der pp-Molekülkette angeordnet sind.
-
PP-Material ist leicht verfügbar und kostengünstig.
-
Seine teilkristalline Struktur bietet eine hohe Biegefestigkeit.
-
Es hat eine gute chemische Beständigkeit gegen verschiedene Basen und Säuren und ist auch sehr beständig gegen Feuchtigkeitsaufnahme.
-
Es ist ein guter elektrischer Isolator mit einer guten Ermüdungsbeständigkeit, die für die Herstellung verschiedener Produkte erforderlich ist.
-
Sie haben eine gute Schlagfestigkeit bei starker Ermüdungsbeständigkeit
-
Das Polymer ist auch hart und hitzebeständig
-
Sie neigen dazu, während der Verarbeitung glatt zu sein und ausgezeichnete ästhetische Eigenschaften zu haben
-
Sie haben einen hohen Schmelzpunkt, weshalb sie häufig für Mikrowellen-Lebensmittelbehälter verwendet werden.
-
Der hohe Wärmeausdehnungskoeffizient begrenzt die Hochtemperaturanwendungen von PP-Material.
-
PP ist extrem entflammbar und schwer zu lackieren, da es schlechte Haftungseigenschaften aufweist.
-
Sie neigen zu Oxidation und UV-Abbau.
-
PP-Polymer hat eine geringe Beständigkeit gegenüber chlorierten Lösungsmitteln und Aromaten, die die Verwendung von PP in Produktionsprozessen beeinflussen.
-
Es kann sowohl als Kunststoff als auch als Faser verwendet werden.
-
Höherer Schmelzpunkt als Polymerpolyethylen
-
Und es ist weniger stabil als Polyethylen
-
Es hat eine bessere Ermüdungsbeständigkeit als PE und wird als Scharnier verwendet.
-
PE ist weniger statisch aufgeladen und zieht daher weniger Staub an als PP.
PP-Verwendungsbereich:
PP-Polymer kann durch Extrusionsblasformen, Spritzgießen und Allzweckextrusion verarbeitet werden. Expandiertes PP (EPP) kann durch ein spezielles Verfahren geformt werden. Die Eigenschaften des Polymers machen sie für verschiedene Endanwendungssegmente des Kunststoffmarktes anwendbar.
PP-Formteil:
Es ist eine Technik, mit der Kunststoffe mit starren Rahmen und Formen geformt werden. Formteile werden üblicherweise bei der Herstellung von Autoteilen, Behältern, Schildern und anderen großvolumigen Gegenständen verwendet. Beim Kunststoffformen wird das flüssige Polymer in eine Hohlform gefüllt, damit es seine Form annehmen kann. Dieser Prozess beinhaltet einen hohen Druckbereich und enorme Wärme. Es gibt verschiedene Techniken, die beim Kunststoffformen verwendet werden, einschließlich Spritzgießen, Blasformen, Rotationsformen und Formpressen.
Die Schmelzflussrate ist eine wichtige Determinante für die Polymerverarbeitung. Die Schmelzflussrate (MFR) oder der Schmelzflussindex (MFI) definieren das Molekulargewicht von PP. Dies ist ein Hinweis darauf, wie leicht das geschmolzene Polymer während des Formprozesses fließt. Die Schmelzflussrate ist hoch. Das Befüllen der Form erfolgt problemlos mit hohem MFR.
Zwei Techniken, die üblicherweise beim PP-Formen verwendet werden, sind das PP-Spritzgießen und das PP-Blasformen.
-
Spritzgießen: Ein Prozess, bei dem Materialien in Formen eingespritzt werden, um Teile herzustellen. Die Verwendung von PP-Polymer im Kunststoffspritzguss nimmt aufgrund seiner positiven Eigenschaften zu. Das PP-Spritzgießen wird in verschiedenen Branchen zur Herstellung von Waren für verschiedene Segmente eingesetzt, da es wichtige Eigenschaften wie gute chemische Beständigkeit und Feuchtigkeitsbeständigkeit, Flexibilität beim Formen und Wirtschaftlichkeit aufweist. Wenn PP-Harz eine mittlere Durchflussrate aufweist, wird eine breite Palette von Produkten in Medizinprodukten, Bauprodukten, Konsumgütern (Behältern, Sportgeräten, Spielzeug usw.) und Hardware verwendet.
-
PP-Blas-Technik: Wird zur Herstellung großer Mengen von hohlen Kunststoffgegenständen verwendet. In erster Linie wird die Kunststoffblasformtechnik bei der Herstellung von Plastikflaschen, Gläsern und Behältern (sowohl Schmal- als auch Weithalsbehälter) verwendet. PP Blastechnik, große Behälter, Plastikflaschen etc. Es ist weit verbreitet für. PP-Material wird in der Blasformtechnik aufgrund seiner Eigenschaften verwendet, die den Produktionsprozess erleichtern, wie z. B. gute Feuchtigkeitsbarriere, chemische Beständigkeit und Stabilität bei hohen Temperaturen. 200 ° F) Beim Blasformverfahren sind die bevorzugten Eigenschaften von PP-Harz hohe Molekulargewichte und niedrige Fließqualitäten. PP-Blasformen in verschiedenen Produkten aus PP-Material wie Lebensmittelbehältern, Plastikflaschen, Milchbehältern, Eisboxen und PP-Blasformen in großem Maßstab, Kanalarbeiten, Wassertanks, Kraftstofftanks, Recyclingbehältern und Überlaufflaschen.
PPH (PolyPropyene Homopolymer):
Polypropylen ist ein wirtschaftliches Material, das eine Kombination aus hervorragenden physikalischen, mechanischen, thermischen und elektrischen Eigenschaften bietet, die bei anderen Thermoplasten nicht zu finden sind. Im Vergleich zu Polyethylen niedriger oder hoher Dichte weist es eine geringere Schlagfestigkeit, aber eine höhere Betriebstemperatur und Zugfestigkeit auf.
Am häufigsten wird Polypropylenhomopolymer (PPH) verwendet. Es hat ein hohes Verhältnis von Festigkeit zu Gewicht und ist härter als Copolymer. Dies, kombiniert mit einer guten chemischen Beständigkeit und Schweißbarkeit, bedeutet, dass es in vielen korrosionsbeständigen Strukturen verwendet wird. Es wird bevorzugt bei der Herstellung von Orthopädie- und Prothesengeräten, Lagertanks, Verarbeitungs- und chemischen Lagergeräten, medizinischen Geräten, verschiedenen Abdeckungen und biaxial orientierten Polypropylenfolien (BOPP) verwendet.
-
Hat ein hohes Verhältnis von Festigkeit zu Gewicht
-
Hervorragende chemische Beständigkeit
-
Es zeigt eine hohe Leistung in Tiefzieh- und korrosiven Umgebungen
-
Nimmt keine Feuchtigkeit auf
-
Es ist beständig gegen die meisten Säuren, Öllösungsmittel und organischen Lösungsmittel.
-
Es zeigt gute Versiegelungseigenschaften
-
Ungiftig
-
Färbt nicht
-
Es hat hohe Festigkeitswerte.
-
Hochglanzmerkmal in hellen Formteilen
-
Entspricht den Regeln für die Lebensmittelverarbeitung.
PPC (PolyPropyene Copolymer):
Polypropylencopolymer (PPC) ist etwas weicher, weist jedoch eine bessere Schlagzähigkeit auf. Es ist auch stärker und haltbarer als Polypropylenhomopolymer (PPH). Es neigt dazu, eine bessere Beständigkeit als Homopolymer hinsichtlich Spannungsrissbildung und geringerer Festigkeit bei Temperatur zu haben, obwohl es bei anderen Eigenschaften eine etwas geringere Leistung gibt. Die Herstellung von Flaschen, Kappen, Glas, Messzylinderrohren, Rohren und thermogeformten Platten ist ein Anwendungsbereich.
PPC-R (PolyPropyene Copolymer Random):
Im Gegensatz zu PPC weist Random PPC Comonomereinheiten auf, die in unregelmäßigen oder zufälligen Formen entlang des Polypropylenmoleküls angeordnet sind. Im Allgemeinen wird es für Anwendungen gewählt, bei denen ein flexibleres und transparenteres Produkt gewünscht wird, obwohl es eine geringere Schlagfestigkeit als PPC aufweist.
Technische Werte und mehr Anwendungsbereiche einiger Rohstoffe der Marke PP:

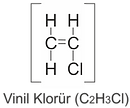
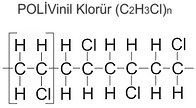
PVC (PolyVinyl Chloride)
Poly (vinylchlorid) ist ein Polymer, das seit über fünfzig Jahren kommerziell hergestellt wird und in vielen Ausführungen erhältlich ist. PVC hat einen viel häufigeren Anwendungsbereich als andere Kunststoffe, da es sich leicht mit Weichmachern, Stabilisatoren und anderen Additiven mischen lässt.
Seine Beständigkeit gegenüber vielen Chemikalien, insbesondere starken Säuren, hat es zu einem bevorzugten Material für solche Anwendungen gemacht. Aufgrund seiner strukturellen Eigenschaften gehört es zu den Materialien, die geschweißt und verklebt werden können. Der Nachteil ist, dass es im Vergleich zu den Materialien seiner Gruppe und seiner hohen Dichte eine niedrige Temperaturbeständigkeit von 60 ° C aufweist. Es hat eine nicht brennbare Eigenschaft, das heißt, sie entzünden sich nicht, wenn sie Flammen ausgesetzt und gezogen werden. Es hat eine gute Lichtbogenbeständigkeit. In Fällen, in denen höhere Temperaturen und chemische Beständigkeit erforderlich sind, sollte ein spezieller CPVC-Typ verwendet werden. Die Betriebstemperaturen liegen zwischen -15 und 60 ° C. Chemietanks, Herstellung elektrischer Geräte, Pools von Wasseraufbereitungsanlagen, Pumpen- und Ventilkörper sowie Rohre sind die Hauptanwendungsbereiche.
Ein Verfahren, bei dem Polyvinylchlorid (PVC) durch zweistufige Massenpolymerisation aus Vinylchloridmonomer (VCM) hergestellt wird.
Bei der kommerziellen Herstellung von Polyvinylchlorid werden fünf Arten von Polymerisationsverfahren verwendet:
Suspension, Emulsion, Masse, Mikrosuspension und Lösungspolymerisation. Am häufigsten sind Suspensions-, Emulsions- und Massenprozesse.
Suspensionspolymerisation:
Die am häufigsten verwendete Technik zur Gewinnung von Polyvinylchlorid aus Vinylchlorid ist die Suspensionspolymerisation. Da bei der Polymerisation die Vinylchloridtröpfchen unter heftigem Rühren in einem Suspensionsmedium dispergiert werden müssen, wird das Batch-Verfahren angewendet. Mit dieser Technik werden bis zu 80% der derzeit produzierten PVC-Menge erhalten.
Emulsionspolymerisation:
Bei diesem Verfahren wird das Monomer in einer wässrigen Umgebung polymerisiert, in der auch ein wasserlöslicher Initiator und Emulgator vorhanden sind.
Massenpolymerisation (oder Massenpolymerisation):
Der Polymerisationsmechanismus, der bei der Massenpolymerisation in der Monomermasse verfolgt wird, ist der gleiche wie die Reaktion, die in jedem Monomertröpfchen bei der Suspensionspolymerisation auftritt; Der Unterschied besteht darin, dass im Massenprozess kein Suspendiermedium vorhanden ist.
Mikrosuspensionspolymerisation:
Es ist ein Emulsionspolymerisationstyp, bei dem der verwendete Initiator in dem Monomer löslich ist. Die Polymerisationsreaktion findet in sehr kleinen Tröpfchen statt; Mit fortschreitender Polymerisation gelangt das Monomer von der Grobemulsion in die Tröpfchen.
Katalysatoren im PVC-Prozess:
Die bei der Herstellung von Polyvinylchlorid verwendeten Katalysatoren variieren je nach Art des zu erhaltenden Produkts und angewendetem Polymerisationssystem. Suspensionspolymerisationskatalysatoren von Vinylchlorid werden hier erwähnt.
Kommerzielle Radikalinitiatoren sind meist vom monomerlöslichen Typ; organische Peroxide (RO = O R '), organische Perester, Peroxidcarbonate und aliphatische Azoverbindungen (RN = N R'). Alle diese Verbindungen ergeben durch thermische Zersetzung freie Radikale. Einige wichtige Initiatoren, die bei der PVC-Polymerisation verwendet werden, umfassen Di-sec-butylperoxydicarbonat und 2,4-Dimethylvaleronitril. Diese Initiatoren sind in Vinylchloridmonomer löslich. Die Wahl des Initiators ist wichtig, da eine regelmäßige und lineare Polymerisationsrate für eine einfache Steuerung des Prozesses erforderlich ist.
Polyvinylchlorid, besser als PVC abgekürzt und unter diesem Namen bekannt, ist das drittgrößte thermoplastische Polymer, das auf dem Markt verwendet wird. PVC, eines der wertvollsten Produkte der chemischen Industrie, wird in vielen Bereichen eingesetzt, von der Spielzeugherstellung bis hin zu Baustoffen in der Bauindustrie. PVC ist ein sehr hartes und zähes Material und dank dieser mechanischen Eigenschaften vielfältig einsetzbar. Es ist jedoch ein Material mit geringerer chemischer Beständigkeit.
Es wird als Wasserleitung, Glasrahmen, Draht- und Kabelisolierung sowie als Wasserflasche verwendet. Um die Schlagfestigkeit von PVC zu erhöhen, werden Gummikunststoffe mit PVC gemischt. Obwohl PVC üblicherweise als Vinyl bezeichnet wird, gibt es andere Polymere, die Mitglieder der Vinylfamilie sind. (Polyvinylacetat, Polyvinylidinchlorid, Polyvinylalkohol usw.) PVC ist auch eine Modifikation von Polyethylen. Ähnlich wie bei Polystyrol gibt es Chloridionen anstelle von Benzolgruppen.
Es ist nach Polyethylen die am häufigsten verwendete Kunststoffart und sehr billig. Es ist beständig gegen hohe chemische Einflüsse und Abrieb. Es gibt zwei Arten, hart und weich. Druckwasserleitungen, Abwasserrohre, Dachregenrinnen und -rohre, Bewässerungs- und Sprinklerrohre sowie Dachböden aus Kunststoffschreinereien werden aus den harten Rohren hergestellt. Weiche werden als Bodenfliesen in Gebäuden verwendet. Sie sind beständig gegen Flammenbrand und geben dabei giftige Gase ab. In den letzten Jahren wurde es auch häufig im Tür- und Fensterbau eingesetzt. PVC-Rohre werden in Heißwasserinstallationen nicht verwendet, da sie bei 80 ° C erweichen.
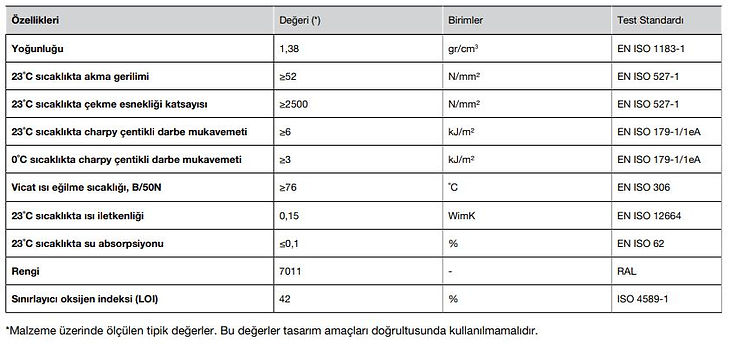
PVC-U 'nun uzun süreli davranış özellikleri :
Hesaplama (EN ISO 15493:2003 sayılı standarda göre)
Aşağıdaki şemada PVC-U malzemesinin uzun süreli davranışı gösterilmektedir.
20°C–60°C arasındaki sıcaklık değerleri için, kırılma çizgileri gösterilir. Bunlar LPL eğrileri (Alt Öngörülebilir Limit) olarak gösterilmektedir. Bu da tanıma göre bütün kırılma noktalarının %97,5’inin eğrilerde veya eğrilerin üzerinde olduğu anlamına gelir.
Tipik olarak PVC-U gibi amorf termoplastikler için hidrostatik mukavemet şemasında hiç dirsek gösterilmemektedir.
Eğriler bir çift logaritmik ölçekte (lineer değil) çizilir. Gerilim veya zaman değerlerini okuduğunuz zaman, lütfen bu durumu hesaba katın.
PVC-U malzemesinden yapılan borular ve bağlantı elemanları için gösterdiğimiz basınç/sıcaklık şeması dahil edilen tasarım faktörü ve 25 yıllık ömürle hidrostatik mukavemet şemasından elde edilir. Hidrostatik mukavemet şeması ekstrapolasyon yöntemiyle EN ISO 9080 standardına göre belirlenmiştir. Aşağıdaki denklemle (4 parametreli model) gerilim, sıcaklık veya zaman 10°C–60°C arasındaki sıcaklık değerlerinde hesaplanabilir.


PVC ne kadar sağlıklı :
1950’li yıllardan beri günlük hayatımıza en fazla girmiş olan PVC ürünlerinin kansere sebep olduğunun belirtildiği tek bir rapor bile yoktur. Çünkü, PVC hammaddesinde sağlık problemine sebep olabilecek tek nokta, tam polimerizasyon işlemi yapılamaması sonucunda insan sağlığını tehdit edecek miktarda reaksiyona girmemiş Vinil Klorür monomerlerinin hammadde içinde kalması olabilir.
Ancak,günümüzde tamamen tam kontrol altında kapali reaktörler içinde yapılan polimerizasyon teknolojisi sayesinde, polimerizasyon işlemi boyunca hammadde içinde reaksiyona girmemiş bir şekilde duran vinil klorür monomerinin miktarı devamlı olarak izlenebilmekte ve vinil klorür monomerinin hammadde içindeki oranı 1 PPM miktarına(milyonda bir) düşene kadar polimerizasyon işlemine devam edilmektedir.
Dünya Sağlık Örgütü’ne akredite laboratuarların gıda maddeleri saklanması ve nakli için onayladığı plastik malzemelerin en başında PVC den mamül ürünler gelmektedir.
Tip alanında kullanılan ameliyat malzemeleri vs gibi ürünlerin saklandığı bütün kap ve tip malzemeleri PVCden yapilmaktadır.
PVC hammaddesinin hastalık yayma konusundaki temiz sicilinin altında yatan gerçek, PVC maddesinin içme suyu ve diğer sivil ara karşı nötr olması yani etkileşime girmemesidir. Bu nedenle PVC hammaddesi suya hiçbir partikül bırakmaz. Ayrıca, klor maddesinin mikrop öldürücü olarak su dezenfeksiyonunda kullanıldığı bilinir.
PVC hammaddesinin üretilmesinden sonra hammaddenin sağlamlığını artırmak için eklenen stabilizatörler içinde kullanımı sağlığa zararlı sayılan ağır metaller türünden maddeler olan Kadmiyum(Cd) ve Kurşun(Pb) maddelerinin stabilizatör olarak kullanımı yasaklanmış ve artık günümüzde hiç kullanılmamaktadır.
Bu ağır metaller yerine artık bugün bütün dünyada stabilizatör olarak Baryum (Ba),Çinko(Zn), Kalsiyum(Ca) ve Kalay(Sn) maddeleri kullanılmaktadır.
PVC 'nin çevre sicili :
PVC Hammaddesi, gerek üretimi için diğer plastik hammaddelerine nazaran çok daha az petrol kullanılması ve gerekse üretimi için diğerlerine nazaran çok daha az enerji gerektirmesi nedeniyle bütün sentetik plastik malzemeler içinde en çevre dostu malzemedir. Çünkü, PVC nin erime noktası diğer hammaddeler içinde en düşüktür.
PVC yi işlemek için diğer plastik malzemelere hem çok daha az enerji ve hem de daha az işlem süresi gerekir. Bu da nihai ürünün maliyetinin PVC’de çok düşük olmasına yol açar.
PVC boruların ömürlerine etki edenler :
Boru hattı projelerinde öngörülen basınç dayanımı ve hizmet ömrünü sağlayabilmeleri için, PVC boruların ilgili standartlarda öngörülen et kalınlığında imal edilmesi ve kesinlikle üretim esnasında % 9'dan fazla kalsit kullanılmaması gerekir. Aksi taktirde, proje tesliminde borular basınç testini geçseler bile, ilerleyen zamanda boruların hizmet ömürleri düşecektir.
Boru hattının kalitesini etkileyen en önemli faktör, birleştirme kalitesidir. Çünkü, bir boru hattı % 70 oranında ek yerlerinden kaçırır. Bunun önüne geçmek için, birleştirilecek iki parçanın çap farkının 0.4 mm'den daha fazla olmaması gerekir. Aksi taktirde, iki parça birbirine bol geçecek ve yapıştırıcı veya O-Ring contası bu boşluğu iyi kapatamayacak ve sonuçta bu noktada zaman içinde sızıntı oluşacaktır. Her firmanın kendi üretim toleransı olduğundan, değişik firmaların ürettiği iki ürünün birleştirilmesi durumunda yapıştırıcının kapatamayacağı kadar bir açıklığın oluşması muhtemeldir. Bu nedenle, mümkün olduğu kadar boru ve ek parçalarının aynı üretici firmadan temin edilmesi uygun olacaktır.
Her çeşit plastik borunun kendine has artıları ve eksileri vardır. En uygun boru tipi, arazinin yapısı, trafik yükü, iklim şartları, istenilen basınç dayanımı ve ortam sıcaklık derecesi gibi faktörler göz önüne alınarak karar verilir. Çünkü, bir boru ne kadar kaliteli üretilirse üretilsin, eğer o proje ve arazi için uygun bir boru tipi değilse sonuç mutlaka olumsuz olacaktır.
PVC boruların alev ile imtihanı :
PVC hammaddesinin yangını üst katlara taşıdığı, yangın sırasında tuz ruhu ve dioksin salgıladığı ve bu nedenle tehlikeli olduğu şeklinde çok yanlış bir inanış vardır. Her yangın çeşidinde yangınla birlikte oluşan gazlar yanan malzemenin cinsine göre toksin emisyonu yaparlar. İnsanlar, bir yangın sırasında tamamen yanmayan ürünlerin ortaya çıkardığı Karbon Monoksitten(CO) zehirlenirler. Karbon monoksit, kokusuz ve çok zehirli bir madde olduğu için insanlar daha karbonmonoksitin varlığını fark edemeden zehirlenmiş olurlar. Ancak PVC hammaddesi erime noktası çok düşük olduğu için hemen tamamen yanar ve PVC'nin yanmasından HCL (Tuz ruhu) açığa çıkar. Yani yangın sırasında insanların zehirlenmesine yol açan Karbon Monoksit gazı PVC hammaddesinin yanmasından oluşmaz. PVC'nin yanması sırasında ortaya çıkan tuz ruhu, aslında zehirleyici bir maddedir. Ancak çok keskin bir kokusu olduğu için 5 PPM gibi çok çok az miktarda bile ortamda bulunmasını insanlar algılarlar ve hemen ortamdan uzaklaşarak zehirlenmekten kurtulurlar.
Bu özelliğiyle PVC hammaddesinin yanması esnasında oluşan bu tuz ruhu aslinda bir yangının haber olarak insanları uyarır.
Bilindiği üzere, teneffüs ettiğimiz havanın içinde %21 oranında serbest oksijen vardır. % 21 den daha az oksijen bulunan ortamda yanabilen maddeler ‘YANICI’ maddeler sınıfına girmektedirler.
Odunun kendiliğinden tutma sıcaklığı 280 °C iken PVC hammaddesinin kendiliğinden tutuşabilmesi için ortam sıcaklığının 450 °C olması gerekir.
PVC hammaddesi, UL 94 yanici maddeler sınıflandırmasına göre CLASS V0 olarak en az tutuşma özelliğine sahip plastik hammaddesi olarak belirlenmiştir.
Aynı şekilde, DIN 4102 Standardi inşaat malzemelerini yanıcılık özelliklerine göre A (Yanıcı olmayan) ve B (Yanıcı) olarak 2 gruba ayırmıştır. Bu standart, Polipropilen ve Polietilen malzemelerini B2 sınıfında (normal yanıcı) olarak gösterirken, PVC'yi B1 (alev söndürücü Flame Retardant) olarak göstermektedir.
Odun yandığı zaman PVC malzemeden üç misli daha fazla ısı yayar.
Bütün plastikten mamül malzemeler gibi, eğer PVC malzemeyi açık aleve tutarsanız PVC malzeme de yanar. Ancak alevi çekerseniz yanma hemen duracaktır. Bunun nedeni, PVC yandığında Hidroklorür (TUZ RUHU) gazı ortaya çıkar ve yanma bölgesinde oksijen miktarını azaltarak hemen durdurur.
PVC hammaddesi içinde en fazla miktarda bulunan Klor maddesi yanmayan bir maddedir.
PVC hammaddesi eğer açık aleve doğrudan tutulmazsa kesinlikle yanmaz. Bu nedenle, Pvc borular, evlerde meydana gelen yangının üst katlara yayılmasında hiçbir katkı yapmaz.
PVC boru ömürleri :
PVC den mamul boru ve ek parçaları kimyasallara ve ağır kullanım ve depolama şartlarına karşı çok iyi direnç gösterirler. Aynı şekilde, kötü hava şartlarında, direkt güneş ışığı altında, yağmur ve rüzgar altında uzun süre durmaktan etkilenmez.
Çünkü, PVC hammaddesinin kimyasal yapısı amorf yapıdır. Yani PVC hammaddesi birbiri içine girmiş bağlardan oluşmuştur.
PVC kristal yapıya sahip değildir. Yani Polietilen ve Polipropilen gibi kırılgan değildir. Ancak %80 oranında kristal yapıya sahiptir.
Kristal yapı ne kadar çok olursa, ürün güneşe karşı dayanımını yitirir ve kırılganlaşır.
Çünkü, Güneş ışığı altında kaldığında Polietilen ve Polipropile gibi hammaddeler içinde moleküller birbirine paralel bağlar ile bağlanır.
PVC hammaddesinde ise moleküller birbirine düzensiz ve birbiri içine girmiş(amorf) bir şekilde bağlanmışlardır ve kristal yapıya sahip değildirler. Bu nedenle PVC baglarını kırmak Polietilen’e göre daha zordur.
Bu nedenle PVC hammaddesinden yapılan boru ve ek parçaları aynı şartlarda Polietilen ve Polipropilen borulara gore çok daha fazla dayanım ömrüne sahiptirler.
Eğer Polietilen ve Polipropilenden mamul boruları güneş ışıgı altında uzun süre bekletirseniz, kristalleşme devam eder ve boru üzerinde boydan boya yarılmalar oluşur. Bu kristal yapıdan ötürü meydana gelir.
Bu nedenle Polietilen hammaddesi içine güneş ışığı altında kristalleşmeyi önlemek için Karbon siyahı denilen maddeden %2.5 oranında koymak gerekir. Karbon siyahı konulmayan hammaddeden imal edilen polietilen hammaddesinden boru yapılırsa bu borular güneş ışığı altında boydan boya yarılacaktır. Aynı şartlarda PVC borulara hiçbir şey olmaz
Sıcaklık arttıkça, PVC Boruların basınç dayanımı azalır.
PVC borular 20°C da 25 yıl 16 bar basınca dayanırken, sıcaklık 40°C’a çıktığında 10 bar basınca dayanabilmektedirler.
Polietilen borular MRS 10MPa ve Polipropilen borular MRS 8MPa değerine sahipken PVC borular MRS 25MPa değerine sahiptir.
Yani aynı çap ve et kalınlığında ve aynı kullanım sıcaklığında PVC borular Polietilen ve Polipropilen borulardan çok daha yüksek basınca dayanırlar.
ABS (Acrylonitrile Butadiene Styrene)

Acrylonitrile
Butadiene

Styrene
Dank seiner starken und langlebigen Struktur auch bei niedrigen Temperaturen ist es gut hitze- und chemikalienbeständig und leicht zu verarbeiten. Es ist beständig gegen starke Stöße. Bruch nach dem Aufprall ist duktil. Es ist beständig gegen hohe Temperaturen und Flammen. Wenn es längere Zeit der Sonne ausgesetzt ist, nehmen Farbe, Schlagfestigkeit und Duktilität ab. Es ist ein Dreifachcopolymer und hat eine hohe Festigkeit und Zähigkeit. Es ist beständig gegen äußere und chemische Einflüsse. Die Zugfestigkeit beträgt 42-50 MPa, das spezifische Gewicht 1,05-1,07 Mg / m³, sie haben kein Elastizitätsmodul und sie können Temperaturen bis zu 75 ° C standhalten. Sie werden zur Herstellung von Rohren, Autoteilen, Schränken für elektronische Geräte und Kühlschrankteilen verwendet.
ABS-Kunststoff ist ein Terpolymer, das durch den Polymerisationsprozess von Styrol und Acrylnitril in Gegenwart von Polybutadien gebildet wird. Normalerweise enthält die Zusammensetzung die Hälfte der Menge an Styrol und der Rest wird zwischen Acrylnitril und Butadien aufgeteilt.
ABS-Kunststoff ist eine gängige Form von Thermoplasten, die seit 1940 erhältlich ist und heute zum beliebtesten technischen Polymer geworden ist. Acrylnitril ist ein Copolymer aus Butadien und Styrol und im Allgemeinen von mittlerer Stärke.
Es ist ein Terpolymer, das aus drei verschiedenen Monomeren besteht. Es ist hart, starr und hat eine gute chemische Beständigkeit.
Acrylnitril-Butadien Die drei an der Bildung von Styrol beteiligten Monomere spielen eine unterschiedliche Rolle für die Leistung des Materials, da Acrylnitril dem Polymer chemische und thermische Stabilität verleiht, die Haltbarkeit und Festigkeit von Butadien erhöht und Styrol schließlich ein schönes und glänzendes Finish ergibt.
Aufgrund seiner Zähigkeit und Steifigkeit in Kombination mit einer starken chemischen Beständigkeit und Stabilität gilt es als das beste Produkt der Styrolpolymerfamilie.
Es kann in verschiedenen Endprodukten des Endsegments wie Haushaltsgeräten (Kühlschrank, Waschmaschine usw.), Gepäck, Kameragehäusen, Werkzeugkästen, Batteriekästen, Verpackungskoffern, Radio und verschiedenen Möbelteilen eingesetzt werden.
Es ist ein starkes und haltbares Material mit hohem Schmelzpunkt. Dieses Polymer wurde hergestellt, um die spezifischen Anforderungen seiner Hauptkunden aufgrund seiner Eigenschaften zu erfüllen. Durch Ändern des Verhältnisses der drei basischen Monomere (Acrylnitril-Butadien-Styrol) des ABS-Materials können verschiedene Derivate erhalten werden, deren Dichte je nach Verwendung geändert werden kann.
Die Haupteigenschaften dieses Materials sind wie folgt:
-
Hervorragende Beständigkeit gegen Chemikalien und verschiedene Weichmacher.
-
Sie bieten mittlere Festigkeit und können je nach Verwendung zäh, zäh oder zäh sein.
-
Acrylnitril-Butadien-Styrol-Materialien weisen eine hohe Zug- und Schlagfestigkeit sowie Härte auf.
-
Diese Harze zeigen auch bei hohen und niedrigen Temperaturen eine hervorragende Leistung.
-
Sie bieten Dimensionsstabilität und hervorragende Formbarkeit.
-
Acrylnitril-Butadien-Styrol-Polymere sind galvanisch einsetzbar und bieten Kriechfestigkeit
-
Sie haben eine hohe Duktilität.
-
Es ist leicht zu geringen Kosten erhältlich.
-
Zugfestigkeit 46 MPA (6600 PSI) und Kerbschlagzähigkeit 10 - 20 Kj / m2
-
Wärmeausdehnungskoeffizient 70 - 90 * 10-6
-
Verwenden Sie eine maximale Resume-Temperatur von 80 - 95 ° C.
-
Dichte 1,0 - 1,05 g / cm³
-
Glasübergang 105 ° C (221 ° F)
-
ABS-Harze bieten eine hervorragende Beständigkeit gegen verdünnte Säuren und verdünnte Alkalien.
-
Die Beständigkeit gegen Öl und Fett ist sehr gut.
-
ABS-Polymere bieten eine mäßige Beständigkeit gegenüber aliphatischen Kohlenwasserstoffen
-
Sie sind schlecht resistent gegen aromatische Kohlenwasserstoffe, halogenierte Kohlenwasserstoffe und Alkohole.
-
Es ist nicht nur ein zähes und starres Material, sondern hat auch eine hohe Schlagfestigkeit.
-
Gute elektrische Eigenschaften haben,
-
Gute chemische Beständigkeit,
-
Einfach zu verarbeiten,
-
Es ist leicht herzustellen und kann gefärbt werden,
-
Es ist ein leichtes Material.
Acrylnitril-Butadien-Styrol wird üblicherweise durch den Emulsionsprozess aus Acrylnitril, Butadien und Styrol polymerisiert. Acrylnitril ist ein synthetisches Monomer, das aus Propylen und Ammoniak hergestellt wird. Butadien ist ein Erdölkohlenwasserstoff, der aus der C4-Fraktion des dampfgespaltenen Styrolmonomers gewonnen wird, das durch Dehydrierung von Ethylbenzol hergestellt wird, einem Kohlenwasserstoff, der bei der Reaktion von Ethylen und Benzol erhalten wird. Es kann auch durch ein patentiertes Verfahren gebildet werden, das als kontinuierliche Massenpolymerisation bekannt ist.
Das Emulsionsverfahren wurde global gewählt, um Acrylnitril-Butadien-Styrol abzuleiten, wobei die Nitrilgruppe der Acrylnitril-Monomere eine Art polare Affinität zueinander entwickelt und zur Zähigkeit des Polymers beiträgt.
Das Vorhandensein von Polybutadien verleiht dem Kunststoffprodukt durch einen allgemeinen Kautschukhärtungsprozess physikalische Festigkeit. Aufgrund der großen Anzahl von dazwischenliegenden gummiartigen Polybutadienpartikeln kann das Material mehr mechanische Energie absorbieren und sich plastisch verformen, ohne zu brechen.
Da es thermoplastisch ist, kann es leicht unter verschiedenen Temperaturbedingungen verarbeitet werden. Wenn es erhitzt werden kann, kann es abkühlen und kann dann ohne Verzerrung wieder erwärmt werden, um andere Kunststoffformen zu bilden.
Die Verarbeitung von Kunststoffen bei unterschiedlichen Temperaturen verbessert ihre grundlegenden Eigenschaften. Die Verarbeitung von Acrylnitril-Butadien-Styrol bei hohen Temperaturen verleiht dem Produkt ein besseres Aussehen und Finish. Es erhöht auch die Wärme- und Chemikalienbeständigkeit des Materials.
Dieses Polymer ist ein thermoplastisches Material, das leicht recycelt und mit unbehandelten Materialien verwendet werden kann, um neue Kunststoffprodukte herzustellen.
Die verwendeten und üblicherweise hergestellten Derivate sind:
-
Hochglänzendes Acrylnitril-Butadien-Styrol,
-
Acrylnitril-Butadien-Styrol mit geringer Helligkeit,
-
Hochwirksames Acrylnitril-Butadien-Styrol,
-
Allzweck-Acrylnitril-Butadien-Styrol,
-
Acrylnitril-Butadien-Styrol mit hohem Durchfluss
-
Platte ist Acrylnitril-Butadien.
China ist eines der dominierenden Länder sowohl bei der Herstellung als auch beim Verbrauch von ABS-Kunstharzen. 40% des weltweiten Gesamtmarktanteils entfallen auf China. Andere wichtige Regionen, die zur globalen Produktion beitragen, sind Europa 10%, Nordamerika 8%, Südamerika 1% und der Nahe Osten und Afrika 1%.
Führende Unternehmen auf dem Markt: Chi Mei, LG Chemicals, Styron, Kumho Petrochemical, INEOS Styrolution, Asahi Kasei, Sabic, China Petroleum and Chemical, Formosa-Kunststoff, Elix Polymers, BASF, Toray, Ampa, Rochling, Dow Chemicals, PolyOne.
ABS Nachteile:
Obwohl Acrylnitril-Butadien-Styrol viele Eigenschaften aufweist, die es zu einem guten Thermoplasten machen, weist dieses Material einige Eigenschaften auf, die es als Kunststoff nicht begünstigen. Es ist leicht entflammbar, wenn es einem Feuer bei hohen Temperaturen ausgesetzt wird.
Bei der Verbrennung von Acrylnitril-Butadien-Styrol entstehen einige sehr gefährliche toxische Produkte wie Kohlenmonoxid und Cyanwasserstoff. Es hat auch schlechte Wetterbedingungen und schlechte Lösungsmittelbeständigkeit.
-
Geringe Lösungsmittelbeständigkeit,
-
Niedriger Dehnungskoeffizient,
-
Die Dauerbetriebstemperatur ist niedrig.
ABS-Einsatzbereiche:
ABS ist einer der am häufigsten verwendeten Kunststoffe und kann in alltäglichen Dingen wie Elektronik, Hardware, Küchengeräten, Spielzeug und vielen anderen Endanwendungsprodukten verwendet werden. Die Spritzgusseigenschaften dieser Materialien unterstützen die Herstellung von Produkten in komplexen und präzisen Formen wie Musikinstrumenten, medizinischen Geräten, Autoteilen und Sportartikeln. Es eignet sich zur Herstellung einer Vielzahl von Produkten in verschiedenen Segmenten.
Es ist ein weit verbreiteter Thermoplast, der in der Lage ist, die erforderlichen Eigenschaften sowohl für Standardharze als auch für technische Harze zu einem angemessenen Preis zu erfüllen. Der Hauptvorteil der Wahl von ABS als Thermoplast besteht darin, dass es eine Kombination aus Festigkeit und Härte von Acrylnitril- und Styrolpolymeren zusammen mit der Härte von Polybutadien ist. Es ist absolut chemikalienbeständig und verhindert stark den chemischen Abbau durch Alkalien und Säuren. Ihre starke chemische Bindung verleiht dem Kunststoff eine gewisse thermische Stabilität, die verhindert, dass sich der Kunststoff auch bei sehr hohen Temperaturen zersetzt.
Acrylnitril-Butadien-Styrol ist eine Art amorpher Feststoff ohne spezifischen Schmelzpunkt. Diese Eigenschaft von ABS macht es zu einem geeigneten Material für das Spritzgießen, um eine Reihe von Produkten herzustellen. Acrylnitril-Butadien-Styrol-Material erweist sich als vorteilhaft, da es ein ästhetisches Aussehen hat, den Kunststoff heller aussehen lässt und leicht zu lackieren ist, aber auch verschiedene Optionen für die Produktherstellung bietet.
ABS-Filament:
Acrylnitril-Butadien-Styrol kann leicht zu dünnen Filamenten extrudiert werden und wird auch als Material für 3D-Drucker verwendet. Es ist das am meisten bevorzugte Material für den 3D-Druck, da es haltbarer ist und noch höheren Temperaturen standhält.
Dieses Polymer gewinnt im 3D-Druck aufgrund seiner starken, leicht zu wirtschaftlichenden Eigenschaften und seiner Fähigkeit, Modifikationen von Nachdruckteilen, die für den Druck sehr gut geeignet sind, zu modifizieren, an Bedeutung. Seine Härte und Festigkeit sowie seine starke Hitzebeständigkeit sind der Grund für die Bevorzugung im 3D-Druckverfahren. Die Verwendung dieses ABS-Materials in diesem Prozess verleiht dem Endprodukt ein schönes und glattes Finish. ABS wird hauptsächlich für den 3D-Druck von Profis, Hobbyisten und Pädagogen verwendet. Modelle, Konzeptmodelle und Figuren, alle Arten von Geräten usw. Es war eine ideale Wahl für 3D-Filamente, die zum Drucken verwendet werden.
ABS-Rohre:
Kunststoffrohre sind sowohl in Industrie- als auch in Entwicklungsländern weit verbreitet. Wachsende Infrastrukturaktivitäten haben die Nachfrage nach Kunststoffrohren weltweit beschleunigt. Kunststoffrohre sind kostengünstig, leicht und nicht korrodierend.
Sie können heißes Wasser warm halten und kondensieren nicht wie Metallrohre aus kaltem Wasser. Kunststoffschläuche bestehen im Allgemeinen aus zwei häufig verwendeten Kunststoffmaterialien: Acrylnitril-Butadien-Styrol (ABS) und Polyvinylchlorid (PVC).
ABS-Rohre werden häufig in Bau- und Infrastrukturentwicklungsaktivitäten eingesetzt, da sie einfacher und billiger zu installieren sind, einen reibungslosen Fluss gewährleisten, leicht sind, nicht leicht rosten oder sich abnutzen, gegen mechanische Beschädigungen beständig sind, Temperaturänderungen leicht aushalten und sogar standhalten können.
Eigenschaften von ABS-Kunststoffrohrsystemen
-
Es ist einfacher zu installieren und billiger als Metallrohrsysteme.
-
Acrylnitril-Butadien-Styrol-Rohre sorgen dank der glatten Innenbeschichtung für einen hervorragenden Fluss.
-
Sie sind beständig gegen mechanische oder chemische Beschädigungen.
-
Sie sind leicht und rosten oder korrodieren nicht.
-
Es kann auch bei seltsamen Temperaturen gut funktionieren.
ABS-Blatt, Blatt:
Acrylnitril-Butadien-Styrol-Material wird auch häufig bei der Herstellung von Kunststoffplatten verwendet. Diese Platten werden zur Herstellung einer Vielzahl von Produkten für den Kunststoffsegmentmarkt des letzten Segments verwendet. ABS kann zur Herstellung leicht in die Form thermogeformt werden.
Dieses Material wird in der Blechherstellung verwendet, da es außergewöhnliche Formbarkeit, hohe Zugfestigkeit und Härte, leichte Duktilität und Beständigkeit gegen viele Chemikalien und Weichmacher bietet.
Diese Blätter werden auch für Flugzeuginnenverkleidungen, Kassettenhalter, Kisten und Tabletts aus Kunststoff, Autoteilen, Elektronik und Gepäck usw. verwendet. Es kann auch zur Herstellung von Produkten verwendet werden. Acrylnitril-Butadien-Styrol-Kunststoffbeschichtung besteht aus zwei Arten; Schwarze Plastikfolie und weiße Plastikfolie. Als schwarze Kunststofffolien werden weiße ABS-Folien häufig für Automobil-, Elektronik- und andere Kunststoffprodukte des Endsegments verwendet, die im Alltag verwendet werden. Schwarze Kunststofffolien werden hauptsächlich in Gärten, Möbeln und Fußböden verwendet, damit sie besser für ihre Anwendung geeignet sind. Die Eigenschaften von ABS-Platten und Platten sind wie folgt;
-
Diese Schichten bieten eine ausgezeichnete Beständigkeit gegen Chemikalien und Spannungsrisse.
-
Acrylnitril-Butadien-Styrol verleiht Produkten ein glattes und glänzendes Finish.
-
Schwarze Platten sind UV-beständig, weiße Platten nicht.
-
ABS-Kunststoffplatten weisen je nach den Anforderungen ihrer Benutzer eine gute Schlagfestigkeit, Formbarkeit, Härte und Zähigkeit auf.
-
Sie haben eine hohe Zug- und Schlagfestigkeit.
-
Hervorragende Leistung bei hohen und niedrigen Temperaturen.
-
Hohe Duktilität.
-
Es eignet sich leicht für die dielektrische Quelle.
-
Beständig gegen Chemikalien und Weichmacher
-
Außergewöhnliche Formbarkeit.
MABS (Methylmethacrylatacrylnitril-Butadien-Styrol):
Im Vergleich zu ABS weist MABS eine homogenere Polymerisation, eine bessere Verarbeitbarkeit der Schmelze, eine hellere Farbe und eine höhere Stabilität gegen ultraviolettes Licht auf. MABS hat auch eine niedrigere Wärmeformbeständigkeitstemperatur. Medizinische Behälter und Komponenten. Teile und Komponenten für Kopierer und Drucker sind meist Anwendungsbereiche.
-
Es hat eine ausgezeichnete Transparenz
-
Hat eine hohe Schlagfestigkeit
-
Gute chemische Beständigkeit
-
Wird für Spritzguss-, Blasform- und Extrusionsprozesse verwendet
-
Hohe Präferenz für Farbstoff und Druck

PS (PolyStyrene)
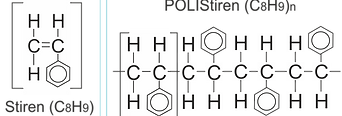
Es wurde ursprünglich von Eduard Simon, einem Apotheker aus Berlin, entdeckt. süßer Gummibaum Liquidambar Styrolharz ist eine fetthaltige Substanz, deren Vorname Storaks aus der Brennerei in der Türkei waren. Nach einigen Tagen der Entdeckung stellte Simon fest, dass sich das aus dem Monomer erzeugte Styrol aufgrund von Oxidation verdickte und ein Gel namens "Styroloxyd" bildete.
Der Chemiker John Blyth und ein anderer deutscher Chemiker August Wilhelm Von Hofmann stellten 1845 die gleiche Umwandlung von Styrol in Abwesenheit von Sauerstoff dar. Diese Substanz wurde "Metastyrol" genannt. Eine spätere Analyse ergab, dass die chemischen Eigenschaften beider hergestellten Substanzen gleich waren.
Später, im Jahr 1866, analysierte Marcelin Berthelot zu Recht die Bildung von Metathyrol / Mehl aus Styrol durch den Polymerisationsprozess.
Nach 80 Jahren Zeitverzögerung wurde auf der Grundlage der These des deutschen organischen Chemikers "Hermann Staudinger (1881-1965)" entdeckt, dass das Erhitzen des Styrols zu einer Kettenreaktion führte, bei der mehrere Makromoleküle namens PS-Kunststoffe erzeugt wurden.
Dieser Kunststoff hat eine amorphe Struktur. Es hat ein helles und klares Bild. Es hatte einen Typ namens expandierendes Polystyrol, der sich sehr gut zur Energieabsorption eignet. Es ist sehr widerstandsfähig gegen Essen und Trinken. Viele wie Knöpfe, Lichtschalter, Flaschen, Tassen, CD- und DVD-Deckel und Verpackungsmaterial.
benutzt. Es ist auch möglich, Polystyrolschaum herzustellen. Polystyrol, das einen sehr großen Anwendungsbereich hat, ist ein billiges und hartes thermoplastisches Polymer. In der Tat können wir sagen, dass es nach Polyethylen der am häufigsten verwendete Kunststoff ist. Polystyrol, das eine aromatische Polymerkette aufweist, wird aus aromatischem Styrolmonomer synthetisiert. Styrolmonomer ist ein flüssiges Kohlenwasserstoffmolekül, das von der petrochemischen Industrie hergestellt wird. Es ist einer der häufigsten Kunststoffe in unserem täglichen Leben. Es ist eine Modifikation von Polyethylen. Es enthält einen Benzolring innerhalb der Polyethylenkette.
Glas klar, leicht zu färben, helle harte Oberfläche, fest und knackig, geschmacks- und geruchsneutral, sehr gute elektrische Eigenschaften, schweißbar, spröde, aber leicht zu verarbeiten und billig. Es ist leicht entflammbar und brennt außerhalb der Flamme weiterhin hell. Es hat einen süßen Duft, der die Arbeit stark macht. Es ist eine gute Isolierfolie für Bauelemente, die in der Elektronik verwendet werden. Foamed (Styropor) wird in der Wärme- und Schalldämmung, in geformten PS-Schaumverpackungen, in Formmodellguss- und Stahlbetonkonstruktionen, in Spielzeug und in Küchengeschirr verwendet.
Monomer ist ein synthetisches Polymer aus Styrol. PS wird durch Polymerisation von Styrol hergestellt, einer Art Bausteinmaterial, das zur Herstellung verschiedener Kunststoffprodukte verwendet wird. Es kommt auch natürlich vor (Erdbeere, Zimt, Kaffee und Bier).
Dieses Kunststoffpolymer ist ein natürlicher transparenter Thermoplast, der sowohl in festem als auch in starrem Schaumstoff erhältlich ist. Allgemein verwendetes PS-Material ist klar, hart und zerbrechlich in Bezug auf seine Eigenschaften. Kunststoff wird häufig zur Herstellung einer Vielzahl von Endsegmentprodukten verwendet. Die feste Form von Kunststoff wird häufig zur Herstellung von Produkten verwendet, die Klarheit erfordern. Dies sind normalerweise elektronische Geräte, Autoteile, Gartentöpfe, Geräte usw. mit einer Kombination aus Farbstoffen, Additiven und anderen Formen von Kunststoff. Es wird verwendet, um solche Produkte herzustellen.
PS besteht aus Schaumstoff und wird als expandiertes Polystyrol (EPS) oder extrudiertes Polystyrol (XPS) bezeichnet, die für ihre isolierenden und dämpfenden Eigenschaften bekannt sind. Die feste Form dieses Materials wird häufig für Anwendungen in medizinischen Geräten verwendet, z. B. für Rauchmelder, CDs, Lebensmittelbehälter und Kaffeetassen. Die Schaumform des Polymers ist auch als Verpackungsmaterial für verschiedene Produkte weit verbreitet.
Es wird durch den Polymerisationsprozess wie andere Kunststoffpolymere hergestellt. Dieses Polymer tritt auf, wenn sich Styrolmonomere während der Polymerisation miteinander verbinden. Bei diesem Verfahren wird die Kohlenstoffbindung der Vinylgruppe aufgebrochen und bildet eine neue Kohlenstoffbindung sowie den Kohlenstoff eines anderen Styrolmonomers in der Kette. Die neu gebildete Bindung ist viel stärker als die vorherige, so dass es schwierig wird, das Polymer zu despolymerisieren. Zunächst wird es in zwei verschiedenen Formen hergestellt:
-
Ataktisches PS: Es ist eine wichtige kommerziell hergestellte PS-Form. Ataktisches PS ist zufällig auf beiden Seiten der Polymerkette verteilt, um Phenylgruppen zu erzeugen. Diese zufällige Positionierung verhindert die Ausrichtung der Ketten und bietet genügend Regelmäßigkeit, um die gewünschte Kristallinität zu erreichen. Dieses Kunststoffpolymer hat eine Glasübergangstemperatur von 90 ° C und der Polymerisationsprozess wird stark durch freie Radikale initiiert.
-
Das "Ziegler-Natta-Polymerisations" -Verfahren wird verwendet, um syndiotaktisches PS herzustellen. Bei diesem Polymerisationsverfahren werden Phenylgruppen auf alternativen Seiten des Kohlenwasserstoffgerüsts angeordnet. Dies ist eine hochkristalline Form von PS-Polymer, die mit einer Übergangstemperatur von 270 ° C hergestellt wird. Diese PS-Typen werden derzeit unter dem Markennamen XAREC von der Idemitsu Corporation unter Verwendung eines Metallocenkatalysators für die Polymerisationsreaktion hergestellt.
Im Allgemeinen werden bei der Polymerherstellung vier Polymerisationsverfahren und drei Schaumverfahren verwendet. Die drei anfänglich verwendeten Verfahren sind Massensuspension, Emulsion und Lösungspolymerisation.
Das zweite ist das Schäumen von EPS in geschlossener Form, die EPS-Extrusion und die Direkteinspritzung von GPPS.
Es ist ein Verfahren, bei dem Styrol durch Dehydrierung aus Benzol, Ethylbenzol durch Alkylierungsreaktion und Ethylbenzol erhalten wird. Benzol und Ethylen werden mit einem heterogenen Katalysator in einem Reaktor mit umlaufendem Ethylbenzol umgesetzt. Der Reaktorauslass wird in einer Vorfraktionierungskolonne von nicht umgesetztem Benzol getrennt und gelangt vom Boden zum rohen Ethylbenzoldestillationssystem. Das Benzol von oben kehrt in den Reaktor zurück. In der Destillationsanlage werden das Benzol, Ethylbenzol und das Schwergewicht im rohen Ethylbenzolgemisch voneinander getrennt. Das Schwer wird wieder destilliert und das gezogene Polyethylbenzol in den Reaktor zurückgeführt. Die Reinheit des erhaltenen Ethylbenzols ist zur Herstellung von Styrol mit Polymerisationsreinheit geeignet. In der Styrolherstellungsabteilung werden frisches Ethylbenzol, zurückkehrendes Ethylbenzol und überhitzter Dampf in den Dehydrierungsreaktor innerhalb des Katalysators gebracht. Die effektiven Variablen, die die Ausbeute steuern, sind Reaktionsdruck und Temperatur.
Es gibt drei Säulen in dem Abschnitt, in dem das Styrolmonomer erhalten wird. Die geringe Menge an Benzol und Toluol, die durch Cracken im Dehydrierungsreaktor gebildet wird, wird in der ersten Säule entfernt und in das Ethylbenzolsystem zurückgeführt. In der zweiten Säule wird das Styrol von dem dem Reaktor zugeführten Ethylbenzol abgetrennt; Hier wird eine hocheffiziente Säule verwendet. In der dritten Säule, der Endbearbeitungssäule, wird das Styrolmonomer von den geringen Mengen an Teer und Polymer gereinigt, die während der Prozesse erzeugt werden. Bei Destillationen wird ein schwefelfreier Inhibitor verwendet, um die Polymerbildung zu minimieren. Es gibt keine Streams, die die Umwelt verschmutzen könnten.
PS Hauptmerkmale:
Es ist eine vielseitige Form von Kunststoff, aus der eine Vielzahl von Kunststoffprodukten für das Endsegment hergestellt wird. PS-Polymer ist eine Art klares, amorphes, unpolares Material, das leicht verarbeitet und in eine große Anzahl von Halbzeugen wie Schäume, Filme und Folien umgewandelt werden kann. In Bezug auf das Volumen ist es einer der größten verwendeten Kunststoffe aufgrund seiner Eigenschaften wie:
-
Es hat eine hohe Schlag- und Wärmebeständigkeit.
-
Diese Polymere sind ein guter elektrischer Isolator mit ausgezeichneter optischer Klarheit.
-
PS hat eine starke chemische Beständigkeit gegenüber verdünnten Säuren und Basen.
-
Es ist eine viskose Flüssigkeit oberhalb der Glastemperatur und ermöglicht die einfache Herstellung vieler fertiger Produkte.
-
Sie können leicht erweitert werden und ermöglichen einen guten Fluss.
-
Diese Materialien sind von Natur aus stark flammhemmend.
-
Chemische Formel für PS (C8H8) n
-
Dichte - 0,96-1,04 g / cm³
-
Der Schmelzpunkt beträgt ~ 240 ° C (464 ° F; 513 K) [4] Für isotaktisches PS
-
Löslichkeit in wasserunlöslich
-
Löslichkeit - Unlöslich in Aceton
-
Wärmeleitfähigkeit des Polymers 0,033 W / (M K) (Schaum, ρ 0,05 g / cm³)
-
Der Brechungsindex beträgt 1,6; Dielektrizitätskonstante 2,6 (1 kHz - 1 GHz)
-
Es ist brennbar, es sind jedoch auch verzögerte Versionen verfügbar.
-
Es hat eine schlechte Lösungsmittelbeständigkeit und kann von vielen Chemikalien angegriffen werden.
-
Homopolymere sind von Natur aus zerbrechlich.
-
Es ist Stress und Umweltrissen ausgesetzt.
-
Sie haben eine schlechte thermische Stabilität.
PS-Nutzungsbereiche:
Es kann auf verschiedene Endverbraucherindustrien angewendet werden, um eine Reihe von Waren in verschiedenen Formaten herzustellen. Es ist das am weitesten verbreitete Polymer in verschiedenen Branchen wie:
-
Weiße Ware - Wird in einer Reihe von Geräten wie Kühlschränken, Klimaanlagen, Öfen, Mikrowellen, Staubsaugern und Mischern verwendet und ist kostengünstig und langlebig.
-
Automobil - PS (Feststoff und Schaum) wird zur Herstellung vieler Automobilteile verwendet, einschließlich Knöpfen, Instrumententafeln, Verkleidungen, energieabsorbierenden Türverkleidungen und sogar schalldämpfendem Schaum.
-
Elektronik - Wird in Wohngebieten und anderen Teilen von Fernsehgeräten, Computern und verschiedenen IT-Geräten verwendet, in denen eine Kombination aus Form, Funktion und Ästhetik erforderlich ist.
-
Food Service - PS hat im Vergleich zu seinen Wettbewerbern einen erheblichen Anteil an der Verpackungsindustrie. Es wird häufig in Lebensmittelverpackungen verwendet, da es besser isoliert, Lebensmittel lange frisch hält und kostengünstig ist.
-
Isolierung - Leichter PS-Schaum hat sich in einer Reihe von Anwendungen wie Gebäudewänden, Dächern, Kühlschränken, Gefriergeräten und sogar industriellen Kühlräumen als hervorragende Wärmedämmung erwiesen. Es wird für die Isolierung bevorzugt, da es inerter, langlebiger und widerstandsfähiger gegen Wasserschäden ist.
-
Medizinisch - Aufgrund seiner Klarheit und einfachen Sterilisation wird PS für eine Vielzahl von medizinischen Anwendungen verwendet, einschließlich Gewebekulturschalen, Reagenzgläsern, Petrischalen, diagnostischen Komponenten und anderen medizinischen Testgeräten.
-
Verpackung - Es ist ein weit verbreitetes und bevorzugtes Material in der Verpackungsindustrie. CD- und DVD-Boxen, Schaumverpackungsmuttern für den Warenversand, Verbrauchsmaterialverpackungen, Fleisch- und Geflügelschalen sowie Eierkartons usw. Es ist weit verbreitet, um Verbraucherprodukte wie zu schützen.
GPPS (Allgemeine Eigenschaften PolyStyren):
Wird auch als kristallklares Allzweck-PS bezeichnet. Diese Form von Kunststoff ist vollständig transparentes, starres und kostengünstiges PS, das üblicherweise aus Styrolmonomer hergestellt wird. GPPS ist eine feste Form von PS, die in Form von 2-5 mm PS-Pellets hergestellt wird. Allgemeine Verwendung Polystyrol ist relativ stark und wetterbeständig. Es fließt leicht und eignet sich zum Formen bei der Herstellung von Produkten wie Spielzeug, CD-DVD-Hüllen und Plastikbechern. Es hat ein klares und helles Aussehen.
-
Obwohl es relativ spröde ist, hat es eine gute Zugfestigkeit
-
Steigert die Produktivität dank eines ausgewogenen Verhältnisses von Durchfluss, Wärme und Formteil
-
Es ist zerbrechlich und zäh.
-
Ist transparent
-
Zeigt eine geringe Auszahlung
-
Kostengünstig
-
Es hat eine ausgezeichnete Röntgenbeständigkeit.
-
Es ist geruchs- und geschmacksneutral
-
Es ist einfach zu verarbeiten.
Technische Werte und mehr Anwendungsbereiche einiger Rohstoffe der Marke PS:

PS (PolyStyren)
Es wurde ursprünglich von Eduard Simon, einem Apotheker aus Berlin, entdeckt. süßer Gummibaum Liquidambar Styrolharz ist eine fetthaltige Substanz, deren Vorname Storaks aus der Brennerei in der Türkei waren. Nach einigen Tagen der Entdeckung stellte Simon fest, dass sich das aus dem Monomer erzeugte Styrol aufgrund von Oxidation verdickte und ein Gel namens "Styroloxyd" bildete.
Der Chemiker John Blyth und ein anderer deutscher Chemiker August Wilhelm Von Hofmann stellten 1845 die gleiche Umwandlung von Styrol in Abwesenheit von Sauerstoff dar. Diese Substanz wurde "Metastyrol" genannt. Eine spätere Analyse ergab, dass die chemischen Eigenschaften beider hergestellten Substanzen gleich waren.
Später, im Jahr 1866, analysierte Marcelin Berthelot zu Recht die Bildung von Metathyrol / Mehl aus Styrol durch den Polymerisationsprozess.
Nach 80 Jahren Zeitverzögerung wurde auf der Grundlage der These des deutschen organischen Chemikers "Hermann Staudinger (1881-1965)" entdeckt, dass das Erhitzen des Styrols zu einer Kettenreaktion führte, bei der mehrere Makromoleküle namens PS-Kunststoffe erzeugt wurden.
Monomer ist ein synthetisches Polymer aus Styrol. PS wird durch Polymerisation von Styrol hergestellt, einer Art Bausteinmaterial, das zur Herstellung verschiedener Kunststoffprodukte verwendet wird. Es kommt auch natürlich vor (Erdbeere, Zimt, Kaffee und Bier).
Dieses Kunststoffpolymer ist ein natürlicher transparenter Thermoplast, der sowohl in festem als auch in starrem Schaumstoff erhältlich ist. Allgemein verwendetes PS-Material ist klar, hart und zerbrechlich in Bezug auf seine Eigenschaften. Kunststoff wird häufig zur Herstellung einer Vielzahl von Endsegmentprodukten verwendet. Die feste Form von Kunststoff wird häufig zur Herstellung von Produkten verwendet, die Klarheit erfordern. Dies sind normalerweise elektronische Geräte, Autoteile, Gartentöpfe, Geräte usw. mit einer Kombination aus Farbstoffen, Additiven und anderen Formen von Kunststoff. Es wird verwendet, um solche Produkte herzustellen.
PS besteht aus Schaumstoff und wird als expandiertes Polystyrol (EPS) oder extrudiertes Polystyrol (XPS) bezeichnet, die für ihre isolierenden und dämpfenden Eigenschaften bekannt sind. Die feste Form dieses Materials wird häufig für Anwendungen in medizinischen Geräten verwendet, z. B. für Rauchmelder, CDs, Lebensmittelbehälter und Kaffeetassen. Die Schaumform des Polymers ist auch als Verpackungsmaterial für verschiedene Produkte weit verbreitet.
Es wird durch den Polymerisationsprozess wie andere Kunststoffpolymere hergestellt. Dieses Polymer tritt auf, wenn sich Styrolmonomere während der Polymerisation miteinander verbinden. Bei diesem Verfahren wird die Kohlenstoffbindung der Vinylgruppe aufgebrochen und bildet eine neue Kohlenstoffbindung sowie den Kohlenstoff eines anderen Styrolmonomers in der Kette. Die neu gebildete Bindung ist viel stärker als die vorherige, so dass es schwierig wird, das Polymer zu despolymerisieren. Zunächst wird es in zwei verschiedenen Formen hergestellt:
-
Ataktisches PS: Es ist eine wichtige kommerziell hergestellte PS-Form. Ataktisches PS ist zufällig auf beiden Seiten der Polymerkette verteilt, um Phenylgruppen zu erzeugen. Diese zufällige Positionierung verhindert die Ausrichtung der Ketten und bietet genügend Regelmäßigkeit, um die gewünschte Kristallinität zu erreichen. Dieses Kunststoffpolymer hat eine Glasübergangstemperatur von 90 ° C und der Polymerisationsprozess wird stark durch freie Radikale initiiert.
-
Das "Ziegler-Natta-Polymerisations" -Verfahren wird verwendet, um syndiotaktisches PS herzustellen. Bei diesem Polymerisationsverfahren werden Phenylgruppen auf alternativen Seiten des Kohlenwasserstoffgerüsts angeordnet. Dies ist eine hochkristalline Form von PS-Polymer, die mit einer Übergangstemperatur von 270 ° C hergestellt wird. Diese PS-Typen werden derzeit unter dem Markennamen XAREC von der Idemitsu Corporation unter Verwendung eines Metallocenkatalysators für die Polymerisationsreaktion hergestellt.
Im Allgemeinen werden bei der Polymerherstellung vier Polymerisationsverfahren und drei Schaumverfahren verwendet. Die drei anfänglich verwendeten Verfahren sind Massensuspension, Emulsion und Lösungspolymerisation.
Das zweite ist das Schäumen von EPS in geschlossener Form, die EPS-Extrusion und die Direkteinspritzungsextrusion von GPPS.
Es ist ein Verfahren, bei dem Styrol durch Dehydrierung aus Benzol, Ethylbenzol durch Alkylierungsreaktion und Ethylbenzol erhalten wird. Benzol und Ethylen werden mit einem heterogenen Katalysator in einem Reaktor mit umlaufendem Ethylbenzol umgesetzt. Der Reaktorauslass wird in einer Vorfraktionierungskolonne von nicht umgesetztem Benzol getrennt und gelangt vom Boden zum rohen Ethylbenzoldestillationssystem. Das Benzol von oben kehrt in den Reaktor zurück. In der Destillationsanlage werden das Benzol, Ethylbenzol und das Schwergewicht im rohen Ethylbenzolgemisch voneinander getrennt. Das Schwer wird wieder destilliert und das gezogene Polyethylbenzol in den Reaktor zurückgeführt. Die Reinheit des erhaltenen Ethylbenzols ist zur Herstellung von Styrol mit Polymerisationsreinheit geeignet. In der Styrolherstellungsabteilung werden frisches Ethylbenzol, zurückkehrendes Ethylbenzol und überhitzter Dampf in den Dehydrierungsreaktor innerhalb des Katalysators gebracht. Die effektiven Variablen, die die Ausbeute steuern, sind Reaktionsdruck und Temperatur.
Es gibt drei Säulen in dem Abschnitt, in dem das Styrolmonomer erhalten wird. Die geringe Menge an Benzol und Toluol, die durch Cracken im Dehydrierungsreaktor gebildet wird, wird in der ersten Säule entfernt und in das Ethylbenzolsystem zurückgeführt. In der zweiten Säule wird das Styrol von dem dem Reaktor zugeführten Ethylbenzol abgetrennt; Hier wird eine hocheffiziente Säule verwendet. In der dritten Säule, die als Endbearbeitungssäule bezeichnet wird, wird das Styrolmonomer von den geringen Mengen an Teer und Polymer gereinigt, die während der Prozesse erzeugt werden. Bei Destillationen wird ein schwefelfreier Inhibitor verwendet, um die Polymerbildung zu minimieren. Es gibt keine Streams, die die Umwelt verschmutzen könnten.
PS Hauptmerkmale:
Es ist eine vielseitige Form von Kunststoff, aus der eine Vielzahl von Kunststoffprodukten für das Endsegment hergestellt wird. PS-Polymer ist eine Art klares, amorphes, unpolares Material, das leicht verarbeitet und in eine große Anzahl von Halbzeugen wie Schäume, Filme und Folien umgewandelt werden kann. In Bezug auf das Volumen ist es einer der größten verwendeten Kunststoffe aufgrund seiner Eigenschaften wie:
-
Es hat eine hohe Schlag- und Wärmebeständigkeit.
-
Diese Polymere sind ein guter elektrischer Isolator mit ausgezeichneter optischer Klarheit.
-
PS hat eine starke chemische Beständigkeit gegenüber verdünnten Säuren und Basen.
-
Es ist eine viskose Flüssigkeit oberhalb der Glastemperatur und ermöglicht die einfache Herstellung vieler fertiger Produkte.
-
Sie können leicht erweitert werden und ermöglichen einen guten Fluss.
-
Diese Materialien sind von Natur aus stark flammhemmend.
-
Chemische Formel für PS (C8H8) n
-
Dichte - 0,96-1,04 g / cm³
-
Der Schmelzpunkt beträgt ~ 240 ° C (464 ° F; 513 K) [4] Für isotaktisches PS
-
Löslichkeit in wasserunlöslich
-
Löslichkeit - Unlöslich in Aceton
-
Wärmeleitfähigkeit des Polymers 0,033 W / (M K) (Schaum, ρ 0,05 g / cm³)
-
Der Brechungsindex beträgt 1,6; Dielektrizitätskonstante 2,6 (1 kHz - 1 GHz)
-
Es ist brennbar, es sind jedoch auch verzögerte Versionen verfügbar.
-
Es hat eine schlechte Lösungsmittelbeständigkeit und kann von vielen Chemikalien angegriffen werden.
-
Homopolymere sind von Natur aus zerbrechlich.
-
Es ist Stress und Umweltrissen ausgesetzt.
-
Sie haben eine schlechte thermische Stabilität.
PS-Nutzungsbereiche:
Es kann auf verschiedene Endverbraucherindustrien angewendet werden, um eine Reihe von Waren in verschiedenen Formaten herzustellen. Es ist das am weitesten verbreitete Polymer in verschiedenen Branchen wie:
-
Weiße Ware - Wird in einer Reihe von Geräten wie Kühlschränken, Klimaanlagen, Öfen, Mikrowellen, Staubsaugern und Mischern verwendet und ist kostengünstig und langlebig.
-
Automobil - PS (Feststoff und Schaum) wird zur Herstellung vieler Automobilteile verwendet, einschließlich Knöpfen, Instrumententafeln, Verkleidungen, energieabsorbierenden Türverkleidungen und sogar schalldämpfendem Schaum.
-
Elektronik - Wird in Wohngebieten und anderen Teilen von Fernsehgeräten, Computern und verschiedenen IT-Geräten verwendet, in denen eine Kombination aus Form, Funktion und Ästhetik erforderlich ist.
-
Food Service - PS hat im Vergleich zu seinen Wettbewerbern einen erheblichen Anteil an der Verpackungsindustrie. Es wird häufig in Lebensmittelverpackungen verwendet, da es besser isoliert, Lebensmittel lange frisch hält und kostengünstig ist.
-
Isolierung - Leichter PS-Schaum hat sich in einer Reihe von Anwendungen wie Gebäudewänden, Dächern, Kühlschränken, Gefriergeräten und sogar industriellen Kühlräumen als hervorragende Wärmedämmung erwiesen. Es wird für die Isolierung bevorzugt, da es inerter, langlebiger und widerstandsfähiger gegen Wasserschäden ist.
-
Medizinisch - Aufgrund seiner Klarheit und einfachen Sterilisation wird PS für eine Vielzahl von medizinischen Anwendungen verwendet, einschließlich Gewebekulturschalen, Reagenzgläsern, Petrischalen, diagnostischen Komponenten und anderen medizinischen Testgeräten.
-
Verpackung - Es ist ein weit verbreitetes und bevorzugtes Material in der Verpackungsindustrie. CD- und DVD-Boxen, Schaumverpackungsmuttern für den Warenversand, Verbrauchsmaterialverpackungen, Fleisch- und Geflügelschalen sowie Eierkartons usw. Es ist weit verbreitet, um Verbraucherprodukte wie zu schützen.
GPPS (Allgemeine Eigenschaften PolyStyren):
Wird auch als kristallklares Allzweck-PS bezeichnet. Diese Form von Kunststoff ist vollständig transparentes, starres und kostengünstiges PS, das üblicherweise aus Styrolmonomer hergestellt wird. GPPS ist eine feste Form von PS, die in Form von 2-5 mm PS-Pellets hergestellt wird. Allgemeine Verwendung Polystyrol ist relativ stark und wetterbeständig. Es fließt leicht und eignet sich zum Formen bei der Herstellung von Produkten wie Spielzeug, CD-DVD-Hüllen und Plastikbechern. Es hat ein klares und helles Aussehen.
-
Obwohl es relativ spröde ist, hat es eine gute Zugfestigkeit
-
Steigert die Produktivität dank eines ausgewogenen Verhältnisses von Durchfluss, Wärme und Formteil
-
Es ist zerbrechlich und zäh.
-
Ist transparent
-
Zeigt eine geringe Auszahlung
-
Kostengünstig
-
Es hat eine ausgezeichnete Röntgenbeständigkeit.
-
Es ist geruchs- und geschmacksneutral
-
Es ist einfach zu verarbeiten.
HIPS (High Impact Polystyrol):
Hochschlagfestes Polystyrol (HIPS) ist auf dem Markt häufiger als (Antischock) bekannt. Es besteht aus PS und Gummi und ist daher undurchsichtig und weiß. Es ist ein vielseitiger, wirtschaftlicher und schlagfester Kunststoff, der einfach zu verarbeiten und herzustellen ist. Es wird häufig bei der Verarbeitung von Prototypen vor der Produktion verwendet, da es eine hervorragende Dimensionsstabilität aufweist und einfach herzustellen, zu lackieren und zu kleben ist. Konsumgüter wie Geräte, Spielzeug, Komponenten für Fernseh- und audiovisuelle Geräte, Instrumententafeln und Zubehör in der Automobilindustrie, Benzintanks und die Herstellung von thermogeformten Platten sind die Einsatzgebiete.
-
Es ist solide und zäh.
-
Ist durchscheinend
-
Es hat eine gute Schlagfestigkeit
-
Perfekt für die Verarbeitung
-
Zeigt gute Dimensionsstabilität
-
Es hat eine ausgezeichnete ästhetische Qualität
-
Einfach zu malen und zu kleben
-
Einfach mit Ultraschall zu schweißen
EPS (Expanded PolyStyrene):
Es ist eine Art starrer und starrer Schaum. Es sieht im Allgemeinen weiß aus und wird aus vorexpandierten PS-Kügelchen hergestellt. EPS ist einer der am häufigsten verwendeten PS-Schäume im täglichen Leben. Weißer Schaum wird häufig in Heißgetränken, Kühlschränken, Isolierungen und Verpackungen usw. verwendet. Wird eingesetzt.
EPS-Material ist billig und leicht. Es verliert im Laufe der Zeit nicht seine grundlegenden Eigenschaften und wird vollständig recycelt und wiederverwendet, um das Umweltgleichgewicht aufrechtzuerhalten. Aufgrund seiner positiven technischen und physikalischen Eigenschaften wie geringes Gewicht, Härte und Formbarkeit wurde EPS für eine Vielzahl von Anwendungen eingeführt. Es wird sogar zur Herstellung von Formplatten für Gebäudeisolierungen und Verpackungsmaterialien verwendet.
EPS wird im Allgemeinen in Form von Schaum verwendet. Das Wort "Styropor" wird häufig verwendet, um EPS-Schaum zu beschreiben. Dies ist eine Art Markenzeichen für Schaumstoff. Die im täglichen Leben am häufigsten verwendeten Schaumprodukte sind Tassen, die an verschiedenen Orten für Kühler, Weintransporter, geformte Endkappen und Ecken, Verpackungen von Kartons und sogar Wasserkühler verwendet werden.
Es besteht aus Styrolmonomer. Es ist in erster Linie ein Derivat von Ethylen und Benzol und wird unter Verwendung eines Polymerisationsverfahrens hergestellt, das kugelförmige Polystyrolbetten erzeugt. Während des Prozesses wird häufig niedrig siedender Kohlenwasserstoff (Pentangas) zugesetzt, um die Expansion des Materials zu unterstützen.
In drei Stufen hergestellt
-
Vorexpansion - Bei Kontakt mit dem Dampf beginnt das Vorschäummittel in der Polystyrolperle zu kochen und die Perlen dehnen sich um das 40- bis 50-fache ihres ursprünglichen Volumens aus.
-
Konditionierung - Nach dem Expansionsprozess durchlaufen die Perlen einen weiteren Reifungsprozess, um ein Temperatur- und Druckgleichgewicht zu erreichen.
-
Formen - Die Perlen werden dann in eine Form gegeben und mit Dampf wieder erhitzt. Die vorgeschäumten Perlen dehnen sich weiter aus, um den Formhohlraum vollständig auszufüllen und miteinander zu verschmelzen.
Zwei Formverfahren für die EPS-Produktion
-
Schwarzes Formteil - Wird verwendet, um große EPS-Blöcke herzustellen, die je nach Benutzeranforderung noch einfacher geschnitten und umgeformt werden können. Diese Blöcke werden sowohl in Verpackungs- als auch in Bauanwendungen verwendet.
-
Formformen - Es wird verwendet, um Teile herzustellen, die spezielle Konstruktionsmerkmale erfordern. Im Allgemeinen wird dieses Verfahren für die Verpackung elektronischer Produkte verwendet, bei denen hauptsächlich formgeformtes EPS verwendet wird.
EPS ist seit mehr als einem halben Jahrhundert aufgrund seiner Leistung, technischen Vielseitigkeit und Kosteneffizienz das bevorzugte thermoplastische Material. Es ist in der täglichen Praxis weit verbreitet. Seine Leichtigkeit, Festigkeit, Wärmedämmung, Haltbarkeit und andere Eigenschaften machen es für eine Reihe von Anwendungen geeignet.
-
Leichtigkeit. Es ist ein extrem leichtes Material, da es ~ 95% Luft enthält. Diese Funktion macht es zu einem geeigneten Material für die Verpackungsindustrie, da es dem Produkt kein Gewicht hinzufügt und die Versandkosten senkt.
-
Haltbarkeit. Die Haltbarkeit dieses Materials bietet die effektive und zuverlässige Form von Kunststoff, der zum Verpacken einer Vielzahl von Waren verwendet wird. Es ist geruchsneutral und ungiftig, und seine Zellstruktur macht es formstabiler. Dies erhöht die Produktlebensdauer.
-
Feuchtigkeitsbeständigkeit. Es ist ein geschlossenzelliges Material und nimmt Wasser nicht leicht auf. EPS ist ein ideales Material für Kühlkettenprodukte, da es auch unter feuchten Bedingungen nicht an Festigkeit verliert. Da das Material gegen hohe Luftfeuchtigkeit beständig ist, wird die Hygieneanforderung leicht erfüllt. Aufgrund dieser Funktion wird es auch zum Angeln in Bojen und Yachthafenbojen verwendet. Selbst wenn dieses Material für eine lange Zeit einer Sättigung in Wasser ausgesetzt ist, gleicht es sich mit einer gewissen Abnahme seiner Wärmeleistung aus, um seine Größe, Form, Struktur und sein physikalisches Erscheinungsbild beizubehalten.
-
Stoßdämpfung. Es bietet eine hervorragende stoßdämpfende Eigenschaft und ist damit die erste Wahl für Verpackungsmaterial für viele Produkte, einschließlich Geräte, Elektronik, Computer und Chemikalien.
-
Thermischen Wirkungsgrad. Der hohe thermische Wirkungsgrad von EPS-Material ist beim Verpacken temperaturempfindlicher Produkte sehr hilfreich. In EPS-Behältern gelagerte Produkte haben eine längere Lebensdauer, selbst bei Temperaturen unter oder unter Umgebungsbedingungen. Es schützt das Produkt auch vor plötzlichen Temperaturen und Klimaveränderungen während des Transports. Beispiele für temperaturempfindliche Produkte, für die EPS-Behälter erforderlich sind, sind Meeresfrüchte, frische Produkte, Arzneimittel und eine Vielzahl von Arzneimitteln.
-
Vielseitigkeit. Da es leicht nach Bedarf geschnitten und geformt werden kann, kann es verwendet werden, um nahezu jede Form und Größe herzustellen. Darüber hinaus wird es in verschiedenen Dichten mit unterschiedlichen physikalischen Eigenschaften entsprechend den Anforderungen des Produkts hergestellt. Die Kompatibilität mit einer Vielzahl von Produkten trägt auch dazu bei, den Wert anderer Alternativen zu steigern.
-
Benutzerfreundlichkeit. EPS gilt als das am einfachsten zu verwendende Material, insbesondere in der Bauindustrie. Normalerweise in Blechen erhältlich, die je nach Bedarf leicht zu Formen oder großen Formblöcken geformt werden können.
-
Dichte, lb./cu.ft. - 0
-
Druckfestigkeit, psi. - 31-37
-
Zugfestigkeit, psi - 58-61
-
Wärmewiderstand, R / in. - 2 ..
-
Die Spannungsfestigkeit beträgt ca. 2 kV / mm. Bei Frequenzen bis zu 400 MHz beträgt die vom Material gebotene Permeabilität 1,02-1,04 und der Verlustfaktor beträgt weniger als 5 × 10-4 bei 1 MHz und weniger als 3 × 10-5 bei 400 MHz.
-
Es ist sehr beständig gegen Wasser und wässrige Lösungen von Salzen, Säuren und Laugen. Im Allgemeinen nicht kompatibel mit organischen Lösungsmitteln. UV-Strahlung bis 120-140F hat einen geringen Einfluss auf die Form des Formmaterials. Es führt normalerweise zu einer Gelbfärbung des Materials, beeinträchtigt jedoch nicht seine physikalischen Eigenschaften.
-
Bietet langfristigen und stabilen R-Wert.
-
Vermeiden Sie das Wachstum von Schimmel oder Mehltau.
-
Sie können leicht recycelt werden.
-
EPS-Isolationsmaterialien können unter dem Klassenzimmer platziert werden.
-
Sie können auch für umgekehrte Baugruppen verwendet werden.
-
Sonneneinstrahlung kann das Produkt verderben.
-
Materialien auf Lösungsmittelbasis können ernsthafte Schäden verursachen.
-
Temperaturen über 250 Grad Fahrenheit können Polystyrol schmelzen.
-
Sie sind mit bestimmten Arten von Thermoplasten nicht kompatibel, die einen dauerhaften Abbau verursachen können.
-
Es ist brennbar und erfordert eine ordnungsgemäße Platzierung.
XPS (eXtrudiertes PolyStyren):
Es ist eine andere Form von Schaum, die eine verbesserte Oberflächenrauheit und eine höhere Härte bei verringerter Wärmeleitfähigkeit bietet. Die chemische Zusammensetzung ist fast die gleiche wie bei diesem EPS, wird jedoch mit einer anderen Technologie hergestellt. EPS, pink, blau und grün etc. Es ist in drei Grundfarben. Es wird in der Regel in Werbetafeln und im Baubereich eingesetzt.
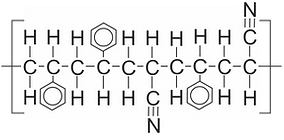
SAN (Styrene AcryloNitrile)
Es ist seit den 1940er Jahren erhältlich und wurde erstmals 1950 veröffentlicht. Seine erhöhte Zähigkeit im Vergleich zum einzelnen Styrol machte es für eine Vielzahl von Anwendungen anwendbar. Die Einschränkungen von SAN führten auch zur Verwendung von Butadien (Kautschuk) als drittes Monomer und lösten die Produktion von ABS (Acrylnitril-Butadien-Styrol) aus.
Dieses Copolymerkunststoffharz ist ein harter, transparenter Kunststoff, der durch Copolymerisation von Styrol und Acrylnitril hergestellt wird. Es ist eine Kombination aus Härte, Festigkeit und Lösungsmittelbeständigkeit von Polyacrylnitril mit der Klarheit und Härte von Polystyrol.
Materialien auf Styrolbasis bieten hervorragende Eigenschaften wie Haltbarkeit, hohe Leistung, Vielseitigkeit des Designs, einfache Herstellung und Wirtschaftlichkeit. SAN-Produkte bieten gute Hygiene-, Hygiene- und Sicherheitsvorteile. Sie bieten auch eine gute Isolierung und können auch leicht recycelt werden.
Es hat eine sehr gute chemische Beständigkeit. Es ist sehr transparent und hat einen schönen Glanz. Es bietet eine geeignete Wahl für kosmetische Materialien. SAN hat eine leicht gelbe Farbe, ist aber auch in verschiedenen Farbvarianten erhältlich. Während das Standard-SAN nicht für den Außenbereich geeignet ist, gibt es auch UV-beständige Typen. Verwendet in Kühlschrankteilen, Regalteilern, Lichtabdeckungen, Kosmetikverpackungen, Küchenbedarf, Autoteilen, Batteriekästen, Küchengeräten, Haushaltsgeräten, Möbeln und medizinischen Artikeln. Aufgrund seiner höheren Wärmebeständigkeit wird es häufig anstelle von Polystyrol verwendet.
SAN besteht aus 70 bis 30 Einheiten von zwei Einheiten, Styroleinheiten und Acrylnitrileinheiten. Diese beiden Verbindungen werden in flüssiger Form oder als Lösung einer Emulsion oder Suspension auf Wasserbasis gemischt.
Der Polymerisationsprozess dieser Verbindungen wird unter dem Einfluss von Radikalinitiatoren durchgeführt. Das bei diesem Verfahren erhaltene Kunststoffmaterial widersteht Wärme und Lösungsmitteln besser als eine einzelne Form von Polystyrol.
Wichtige Unternehmen, die SAN-Harze herstellen, sind Samsung Cheil Industries, Chi Mei, INEOS, China National Petroleum, SABIC Innovative Plastics, Toray Industries, Formosa Plastics, Styron, Techno-Polymer und Petro China.
SAN-Hauptmerkmale:
SAN-Harze haben eine ähnliche Verwendung wie Polystyrol. Diese sind wie Polystyrol optisch transparent, zerbrechlich und haben ein mechanisches Verhalten. Einige der Haupteigenschaften dieses Copolymers sind wie folgt:
-
Es zeigt hohe Festigkeit und chemische Beständigkeit.
-
Bietet gute Fließ- und Dimensionsstabilität.
-
Es ist extrem hitzebeständig.
-
Es ermöglicht einen guten Fluss.
-
Es ist beständig gegen Stress, Öl und Lebensmittelflecken.
-
Es hat eine Glasübergangstemperatur über 100 ° C.
-
Es wird für allgemeine Zwecke verwendet.
-
Seine Zugfestigkeit beträgt 3,40 - 3,90 N / mm² und seine Kerbschlagzähigkeit beträgt 250 Kj / m².
-
Wärmeausdehnungskoeffizient 70 x 10-6
-
Die maximale Dauerbetriebstemperatur für SAN beträgt 55 ° C.
-
Dichte 1,08 g / cm 3
-
Es ist extrem beständig gegen verdünnte Säuren und Laugen.
-
Es zeigt eine sehr gute Beständigkeit gegen Öl und Fett.
-
Mäßig beständig gegen aliphatische Kohlenwasserstoffe und Alkohole.
-
Diese Harze weisen eine geringe Beständigkeit gegenüber aromatischen Kohlenwasserstoffen und halogenierten Kohlenwasserstoffen auf.
-
Es hat die chemische Beständigkeit im Vergleich zu Polystyrol verbessert.
-
Es verleiht den hergestellten Produkten eine bessere Zähigkeit und Härte.
-
Diese Polymere sind formstabil.
-
Sie bieten eine einfache Verarbeitung.
-
Es ist sehr beständig gegen Chemikalien und Spannungsrisse.
-
Es absorbiert im Vergleich zu Polystyrol mehr Wasser.
-
Es zeigt eine geringere Wärmekapazität und Schlagfestigkeit.
-
Es erfordert eine hohe Verarbeitungstemperatur.
-
Es wird schnell gelb und ist bei hoher Rauchentwicklung entflammbar.
-
Es wurde als eine der Ursachen von Krebs diagnostiziert. Es ist krebserregend.
SAN-Nutzungsbereiche:
Styrolacrylnitril kann für eine Reihe von Anwendungen in verschiedenen Branchen eingesetzt werden. Polystyrol wird im Allgemeinen wegen seiner besseren Eigenschaften bevorzugt. Diese Harze werden in verschiedenen Endsegmentmärkten verwendet, darunter:
-
Sie werden in Fernsehgeräten, Kabeln, Radios, Klimaanlagen, Computern und anderen Personen verwendet, die elektronische Geräte verwenden.
-
Es wird zur Herstellung und Verpackung verschiedener Haushaltsgegenstände wie Waschmittel, Behälter, Kleidung, Zahnbürsten und Badarmaturen verwendet.
-
SAN verwendete ein großes Kunststoffpolymer zum Verpacken von Kosmetika wie kompakten Schachteln und Lippenstiftröhrchen.
-
Kfz-Verkleidung, Traktorkomponenten, Kfz-Werkzeuglinsen und Batteriegehäuse usw. Es ist weit verbreitet bei der Herstellung von Autoteilen, einschließlich.
-
SAN-Harze werden zur Herstellung von stationären Produkten verwendet, die täglich weit verbreitet sind, wie z. B. Wiege-, Taschenrechner-, Drucker-, Schreib- und Zeichengeräte.
-
Aufgrund der physikalischen und mechanischen Eigenschaften von SAN-Polymeren eignen sie sich zur Herstellung einer Vielzahl allgemein verwendbarer Produkte wie Flaschenverschlüsse, Drehschalter, Staubkappen, Schiffsgeräte und Verpackungen für Körperpflegeprodukte.

PET (PolyEthylene Terephthalate)
PET wurde erstmals Mitte der 1940er Jahre in den USA gefunden, als Forscher nach Polymeren suchten, mit denen neue textile Polymere hergestellt werden konnten. Später wurden diese Polyester von DuPont als "Dacron" bezeichnet.
In den späten 1950er Jahren fanden die Forscher die Methode, eine dünne extrudierte PET-Folie zu dehnen, um Filme zu erzeugen, die heute üblicherweise als Röntgen- oder Fotofilme verwendet werden.
Polyethylenterephthalat, das weltweit 18% der Kunststoffproduktion ausmacht, liegt nach Polyethylen und Polypropylen an dritter Stelle. PET, das zur Polyestergruppe gehört, ist ein lineares thermoplastisches Polymer und kommt hauptsächlich in Bereichen wie Kunstfasern, Lebensmittelverpackungsindustrie und insbesondere Abfüllung vor. Polyethylenterephthalat, allgemein bekannt als PET oder PETE, ist das weltweit am häufigsten verwendete Polymer. Es ist ein natürlich transparenter und teilkristalliner Kunststoff, der häufig für Produkte verwendet wird, die in unserem täglichen Leben verwendet werden. PET-Polymer wird in der Textilindustrie als "Polyester" bezeichnet. Es wird häufig als Faser für Kleidungsstücke verwendet, da es eine ausgezeichnete Feuchtigkeitsbarriere aufweist und auch zum Abfüllen und Verpacken in großem Maßstab verwendet wird. Der größte Anteil des produzierten PET-Kunststoffs besteht aus synthetischen Fasern mit 60%, Flaschen und Schachteln mit 30%. PET-Material besteht aus polymerisierten Monomer-Ethylenterephthalat-Einheiten, und wenn diese PET-Materialien mit anderen Materialien wie Glasfasern oder Kohlenstoffnanoröhren kombiniert werden, nimmt ihre Festigkeit zu. Als Rohstoff ist PET als sicheres, starkes, leichtes, flexibles und ungiftiges Material anerkannt, das leicht recycelt werden kann.
PET-Kunststoff ist zur weltweiten Wahl in der Verpackungsindustrie geworden. Es zeichnet sich durch die Verpackung vieler Lebensmittel und Getränke aus, da es hygienisch, stark und leicht ist, die Frische der Produkte bewahrt und nicht zerfällt. Es wird hauptsächlich zum Verpacken von Wasser und kohlensäurehaltigen Erfrischungsgetränken verwendet.
Polyethylenterephthalat (PET) wird hauptsächlich durch Polymerisation von Ethylenglykol und Terephthalsäure hergestellt. Ethylenglykol und Terephthalsäure gelten als Bausteine für PET-Harz. Zusätzlich werden diese Harze zu einer geschmolzenen Flüssigkeit erhitzt, die leicht zu Teilen jeder Form geformt werden kann. Das Vorhandensein großer Benzolringe in dem Verfahren verleiht dem PET-Polymer Härte und Festigkeit, insbesondere wenn die Polymerketten miteinander ausgerichtet sind.
Genauer gesagt, wenn die beiden Rohstoffe PET-Ethylenglykol und Terephthalsäure mit niedrigem Vakuumdruck und hohen Temperaturen kombiniert werden, bilden sich lange Ketten des Polymers. Wenn sich die Mischung verdickt, bilden sich längere Ketten und der Prozess wird gestoppt, wenn die geeignete Kette erhalten wird. Wenn PET-Polymer bei verschiedenen Temperaturen in Stärkeform gehalten wird, beginnt es zu kristallisieren und wird undurchsichtig und härter. Diese kristallisierte Form von PET wird verwendet, um andere Produkte wie Behälter und Schalen herzustellen, die wieder erwärmt werden können.
Die weltweite Produktionskapazität für PET-Harze beträgt über 30 Millionen Tonnen. Chinesische Hersteller machen 32% der weltweiten Gesamtproduktion aus. China ist nicht nur der weltweit größte Hersteller von PET-Harz, sondern auch der größte Verbraucher.
PET Grundlegende Merkmale:
PET-Kunststoffe sind technische Kunststoffe mit hoher Festigkeit und Härte für eine Vielzahl von Anwendungen. Es ist ein Thermoplast, der insbesondere in der Verpackungs- und Textilindustrie weit verbreitet ist.
-
Es zeigt auch bei hohen Temperaturen eine gute Wärmebeständigkeit und ein geringes Kriechen.
-
Es hat eine gute Stabilität aufgrund der geringen Wasseraufnahme.
-
Es hat eine geringe Wasseraufnahme. (Ohne Nylonstrümpfe)
-
Es weist eine ausgezeichnete Beständigkeit gegen Chemikalien auf.
-
Es hat gute Farbstabilität und Trageeigenschaften.
-
Zugfestigkeit 2,5 N / mm und Schlagfestigkeit 1,5 - 3,5 KJ / m
-
Wärmeausdehnungskoeffizient 70 * 10.6
-
Dichte 1,37 g / cm
-
Polymere sind leicht verfügbar und kostengünstig
-
PET-Polymere sind sehr feuchtigkeitsbeständig und chemikalienbeständig gegen organisches Material und Wasser.
-
Es hat ein hohes Verhältnis von Festigkeit zu Gewicht.
-
Es ist hochtransparent und unzerbrechlich (bricht nicht wie Glasverpackungen).
-
PET-Materialien sind in verschiedenen Formen und Farben erhältlich und bieten eine gute Wahl für die Herstellung attraktiver Produkte.
-
Polyethylenterephthalat kann leicht recycelt werden. PET-Kunststoff ist einer der am meisten recycelten Kunststoffe und wird zur Herstellung von Produkten wie Behältern, Schlafsackisolierungen, Polyestergeweben und Teppichen wiederverwendet.
-
Im Vergleich zu anderen Polymeren weist PET-Polymer eine geringere Wärmebeständigkeit auf.
-
PET-Harze sind selbst oxidationsempfindlich. Zum Beispiel werden sie nicht zur Lagerung von Bier oder Wein verwendet, da diese Getränke eine lange Haltbarkeit haben, so dass es zu Geschmacksstörungen kommen kann.
-
PET-Kunststoffe sind nicht biologisch abbaubar und können je nach Verwendung gut oder schlecht sein.
PET-Verwendungsbereiche:
PET-Harze sind Leistungspolymere. Sie bieten eine breite Palette von Anwendungen in den Endsegmentmärkten. PET-Kunststoff sticht in Märkten wie Transportwesen, Automobilindustrie, Elektrotechnik / Elektronik, weiße Ware, Verpackung und Textilien hervor.
Da PET-Material eine ausgezeichnete Wasser- und Feuchtigkeitsbarriere darstellt, wird es in der Verpackungsindustrie häufig verwendet, insbesondere für Verbrauchsmaterialverpackungen (Wasserflaschen, alkoholfreie Getränke, verpackte Lebensmittel). Die hohe mechanische Festigkeit des Polymers ermöglicht die Verwendung von PET-Filmen in Bandanwendungen wie einem Träger für Magnetbänder oder einem Träger für Haftklebebänder. Aus kristallisierten PET-Kunststoffen werden Schalen hergestellt, die sowohl Gefrier- als auch Backtemperaturen standhalten.
PET-Harze werden zu einer geschmolzenen Flüssigkeit erhitzt und dann leicht in die gewünschte Form extrudiert. PET-Harze, die aus der Kombination von Glaspartikeln oder Fasern hergestellt werden, sind haltbarer und fester. Diese Harze werden je nach Bedarf des Produkts in verschiedenen Branchen eingesetzt. Einige der wichtigsten und umfangreichsten Anwendungen von PET-Kunststoff sind:
3d Drucken:
Polyethylenterephthalat ist ein starkes und flexibles Polymer, das sich gut für den 3D-Druck eignet. Der 3D-Druck erfordert eine Kombination aus Flexibilität und Zähigkeit, die mit PET-Harzen leicht erreicht werden kann. Es ist allgemein bekannt, dass PET weniger Geruch abgibt als jedes andere Material wie Acrylnitril-Butadien-Styrol (ABS) oder Polymilchsäure (PLA), das für den 3D-Druck verwendet wird.
Spritzguss:
Polyethylenterephthalat wird häufig in Kunststoffspritzgusstechniken in Form von Pellets verwendet, um Produkte mit komplexen Formen herzustellen. Da PET hygroskopisch ist, muss es vor der Verwendung in der Formmaschine getrocknet werden. Die Schrumpfung in PET-Kunststoff ist gering, hängt jedoch auch von einer Reihe von Faktoren ab, wie z. B. Temperatur, Haltezeit, Formwandstärke, Formtemperaturen und Art der verwendeten Additive.
CNC-Bearbeitung:
PET-Material wird häufig als Plattenmaterial für CNC-Maschinen verwendet. Mit der CNC-Maschine werden eine Vielzahl von Produkten hergestellt, bei denen PET-Material als Grundmaterial im Produktionsprozess verwendet wird.
PET Film und Folie:
Polyethylenterephthalat wird hauptsächlich zur Herstellung von Platten und Folien verwendet, die später bei der Herstellung von Kunststoffprodukten verwendet werden. PET-Folien und -Folien sind häufig verwendete thermoplastische Folien, da sie eine Vielzahl von Vorteilen bieten, wie z.
-
PET-Folien bieten hervorragende chemische Eigenschaften zusammen mit hohen Barriereeigenschaften und Zugfestigkeit zusammen mit den Platten.
-
Sie können leicht in Flaschen oder andere Kunststoff-Verbrauchsmaterialien umgewandelt werden.
-
Sie bieten eine größere Stabilität und Bruchfestigkeit des Produkts.
-
Diese Filme sind leicht und kostengünstiger.
Flasche:
Die meisten der hergestellten PET-Harze werden zur Herstellung von PET-Flaschen verwendet. Diese Flaschen oder Behälter werden für eine Vielzahl von Konsumgütern wie Erfrischungsgetränke, alkoholische Getränke, Waschmittel, Medikamente und Kosmetika verwendet. Die hergestellten PET-Plastikflaschen lassen sich in zwei große Kategorien einteilen: Flaschenwasserflaschen und kohlensäurehaltige Erfrischungsgetränke. Flaschen aus PET-Harzen können problemlos recycelt und zur Herstellung eines neuen Produkts verwendet werden. PET-Flaschen sind das am häufigsten verwendete Kunststoffprodukt im letzten Segment des Kunststoffmarktes.
Die Vorteile von PET-Flaschen können wie folgt aufgeführt werden:
-
Es ist leicht, leicht zu tragen und sicher zu bedienen.
-
Sie können leicht wieder versiegelt oder recycelt werden, um neue Produkte herzustellen.
-
PET-Flaschen können leicht in verschiedene komplexe Formen geformt werden.
-
Die Herstellung von PET-Flaschen mit PET-Harzen bietet den Herstellern ein hohes Maß an Flexibilität.
-
Sie sind kostengünstig und leicht verfügbar.
PET-G (Polyethylenterephthalat-Glykol):
Es ist eine Glykolmodifikation von Polyethylenterephthalat. PET-G ist eine Art modifizierte Version von PET-Harz, einem der am häufigsten verwendeten Polymere. "G", das in PET-G verwendet wird, bedeutet "modifiziert mit Glykol", das der PET-Materialzusammensetzung während des Polymerisationsprozesses zugesetzt wird. PET-G ist klarer, weniger spröde und einfacher zu verwenden als das PET-Grundmaterial. Es wird häufig bei der Herstellung von Wasserflaschen, Verpackungsverbrauchsmaterialien und einer Vielzahl anderer Kunststoffprodukte verwendet. PET-G wird häufig als 3D-Druckfilament verwendet, da es haltbarer und einfacher zu verwenden ist.
Die Verwendung von PET-G bietet folgende Vorteile:
-
Es ist langlebiger und einfach zu bedienen.
-
PETG ist klarer und weniger spröde. Dem PET zugesetztes Glykol verhindert, dass es kristallisiert und bricht.
-
Es ist sehr langlebig und versiegelt
-
Es kann leicht sterilisiert werden.
MEG (Monoethylenglykol)
Ethylenglykol wurde erstmals 1859 durch Verseifung durch den französischen Chemiker Charles-Adolphe Wurtz aus Ethylenglykol hergestellt. Später begannen die Vereinigten Staaten 1917 mit der halbkommerziellen Herstellung von Ethylenglykol durch Ethylenchlorhydratation.
Die erste große kommerzielle Anlage zur Herstellung von Ethylenglykol wurde 1925 von Carbide and Carbon Chemicals Co. gegründet. in South Charleston. Bis 1929 wurde dieses Material von fast allen Dynamitherstellern in großem Umfang verwendet, was dazu führte, dass das Produkt 1953 für die Verwendung lizenziert wurde.
Monoethylenglykol (MEG) oder Ethylenglykol ist im Handel erhältliches Hauptglykol. Es wird industriell aus Ethylen oder Ethylenoxid hergestellt. Bei diesem MEG-Produktionsprozess fallen zwei Nebenprodukte an, Diethylenglykol (DEG) und Triethylenglykol (TEG).
Polyesterfasern, die bei der Flaschenherstellung verwendet werden, sind ein wichtiger Rohstoff für eine Reihe industrieller Anwendungen wie die Herstellung von Geweben und Polyethylenterephthalaten. Andere industrielle Anwendungen umfassen die Verwendung als Kühlmittel, Wärmeübertragungsmittel, Frostschutzmittel und auch als Hydratinhibitor in Gasleitungen.
MEG wird aus Ethylen über das Zwischenprodukt Ethylenoxid hergestellt. Bei diesem Verfahren reagiert Ethylenoxid mit Wasser unter Bildung von Ethylenglykol gemäß der gewünschten chemischen Gleichung. Dieser Prozess wird mit Säuren, Basen katalysiert oder kann bei hohen Temperaturen auch bei sauren oder neutralen pH-Werten stattfinden. Die höchste Menge an Ethylenglykol kann mit einem Überschuss an Wasser bei saurem oder neutralem pH erhalten werden. Unter diesen Bedingungen können etwa 90% Ethylenglykol erhalten werden. Die wichtigsten Nebenprodukte dieses Verfahrens sind Triethylenglykol, Tetramethylenglykol und Oligomere Diethylenglykol. Zunächst besteht der Ethylenglykol-Herstellungsprozess aus folgenden Schritten:
-
Ethylenoxidherstellung: In dieser Anfangsphase werden Ethylen und Oxide zusammen in einen Mehrrohrreaktor eingespeist, der Ethylenoxide (EO) bildet. Diese exotherme Reaktion, die in Festbetten in Reaktorrohren durchgeführt wird, findet üblicherweise in der Gasphase statt (unter Verwendung eines Silberkatalysators auf Aluminiumoxidträger). Dampf wird durch die Wärme der Reaktion erzeugt, die während des Prozesses auftritt.
-
Rückgewinnung von Ethylenoxid: Das aus dem Reaktor erhaltene Produkt wird dem EO-Absorber zugeführt, um Licht und Wasser zu entfernen. Ein Teil des gasförmigen Dampfes wird in den Reaktor zurückgeführt und der Rest wird zu einer Kohlendioxidentfernungseinheit geleitet, die aus einem Absorber und einem Stripper besteht. In dieser Stufe wird das Kohlendioxid dann zur Verwendung bei der Ethylencarbonatherstellung abgetrennt. In der nächsten Stufe dieses Verfahrens wird der verdünnte Ethylenoxiddampf aus dem Absorber entfernt, um dem EO-Stripper zugeführt zu werden. Hier konzentriert es sich und erspart Ihnen Gemeinkosten. Die Rohform von EO wird schließlich verdichtet und zum nächsten Teil dieses Prozesses geleitet.
-
Herstellung und Reinigung: Schließlich wird Ethylenoxid mit Kohlendioxid zu Ethylencarbonat umgesetzt. Es wird auch unter Bildung von MEG und Kohlendioxid hydrolysiert. Beide Verfahren werden in flüssiger Phase mit einem homogenen Katalysator durchgeführt.
Die weltweite MEG-Produktionskapazität liegt bei 35 Millionen Tonnen. Etwa die Hälfte davon wird von asiatischen Ländern, hauptsächlich China, Indien und Taiwan, realisiert. Nordamerika produziert 6 Millionen Tonnen und Europa produziert insgesamt 2,5 Millionen Tonnen.
MEG Hauptmerkmale:
Es wird oft als Ethylenglykol bezeichnet, eine farblose, süß schmeckende und geruchlose organische Verbindung. Es wird in hohem Maße für verschiedene Endsegmentindustrien wie die Textilindustrie, die Verpackungsindustrie und andere verwendet. Die Eigenschaften von MEG wie Haltbarkeit, hydrophobe Eigenschaften und Zähigkeit beweisen, dass MEG ein wichtiger Rohstoff für eine Vielzahl industrieller Anwendungen ist. Es wird häufig bei der Herstellung von Polyesterharzen, -fasern und -filmen verwendet. Die physikalischen Eigenschaften dieses Materials ermöglichen die Verwendung als verschiedene Materialien wie Kühlmittel, Korrosionsschutzmittel, Entwässerungsmittel und chemische Zwischenprodukte.
-
Die chemische Formel lautet C2H6O2
-
Aussehen - Klare, farblose Flüssigkeit
-
Molmasse - 62,07 gmol –1
-
Dichte -1,1132 g / cm 3
-
Schmelzpunkt - 12,9 ° C (8,8 ° F; 260,2 K)
-
Siedepunkt - 197,3 ° C (387,1 ° F; 470,4 K)
-
Dampfdruck 0,06 mmHg (20 ° C) [1]
-
Viskosität - 1,61 × 10 –2 Pa • s [2]
-
Die Löslichkeit in Wasser kann mischbar sein
-
Löslichkeit - Löslich in den meisten organischen Lösungsmitteln.
-
MEG ist hochgiftig.
-
Es hat eine wasserähnliche Struktur, die es mit Materie mischbar macht.
-
Es ist ein leicht verfügbares und kostengünstiges Material.
-
Es erweist sich als eine großartige Zutat in der Fertigungsindustrie, da es einen niedrigen Gefrierpunkt und einen hohen Siedepunkt aufweist.
-
Dieses Material hat gute Wärmeübertragungsfähigkeiten
-
MEG ist eine Art langlebige Verbindung.
-
Es ist leicht entflammbar und nimmt schnell Wasser auf.
-
Wenn das Frostschutzmittel ausläuft, besteht die Gefahr von Verbrennungen für Autos in großem Maßstab.
-
Eine unsachgemäße Entsorgung von MEG, insbesondere auf Landebahnen von Flughäfen, kann die Umwelt schädigen.
-
Sein süßer Geschmack zieht leicht Kinder und Haustiere an, die gesundheitsschädlich sein können.
MEG-Verwendungsbereich:
MEG wird hauptsächlich als Rohstoff in verschiedenen Formen verwendet, um eine Reihe industrieller Prozesse durchzuführen, darunter:
-
Kühlmittel und Wärmeübertragungsmittel - Ethylenglykol fungiert größtenteils als Medium für die konvektive Wärmeübertragung wie in Kraftfahrzeugen und flüssigkeitsgekühlten Computern. Es wird häufig zum Transport von Wärme in Kaltwasser-Klimaanlagen als Kühlflüssigkeit und in Erdwärmepumpen als Heizflüssigkeit verwendet.
-
Frostschutzmittel - Die Eigenschaften von MEG lösen die Wasserstoffbindung, wenn sie in Wasser gelöst werden. Es gefriert normalerweise bei -12 ° C, kristallisiert jedoch nicht, wenn es gerührt wird, und daher sinkt der Gefrierpunkt. Diese Frostschutzfunktion von MEG wird zum Enteisen von Flüssigkeiten für Windschutzscheiben und Flugzeuge verwendet. Es wird auch zum Schutz von biologischen Geweben und Organen verwendet.
-
Pionier für Polymere - In der Kunststoffindustrie ist MEG einer der wichtigsten Pioniere einer Reihe von thermoplastischen Harzen. Es wird in hohem Maße als Vorstufe für Polyesterfasern und -harze verwendet.
-
Unter Verwendung dieses Materials als Vorstufe wird auch Polyethylenterephthalat (PET) hergestellt, aus dem Plastikflaschen für kohlensäurehaltige Erfrischungsgetränke und Mineralwasser hergestellt werden.
-
Es wird als Dehydratisierungsmittel und Hydrathemmung verwendet. Als Dehydratisierungsmittel wird es verwendet, um Wasserdampf aus Erdgas zu entfernen, bevor es in der Erdgasindustrie verarbeitet wird.
-
Als Hydrathemmung wird es häufig verwendet, um die Formulierung von Erdgashydraten (Clathraten) in Pipelines zu hemmen, die Erdgas vom entfernten Gas zur Verarbeitungsanlage transportieren. Es kann auch mit Erdgas gewonnen und als Inhibitor wiederverwendet werden.
MEG-Sperrgebiete:
-
Tragbare Wasseranwendungen.
-
Bei der Formulierung von Lebensmitteln, Medizin und Kosmetik.
-
Frostschutzmittel für tragbare Wassersysteme in Saisonhäusern und Freizeitwassersystemen.
-
Frostschutzmittel für Sprinkleranlagen.
Unterschiede zwischen MEG und PEG:
-
Molekülstruktur: Zwei wichtige Mitglieder der Glykolfamilie. Beide Verbindungen haben kommerzielle Anwendungsbedeutung. Der Unterschied zwischen diesen beiden Glykolen ist auf ihre chemische Struktur zurückzuführen. Ethylenglykol ist eine Art einfaches lineares Molekül, während Polyethylenglykol ein Polymermaterial ist.
MEG: Ethylenglykol - Summenformel von EO (CH2-OH) 2
PEG: Polypropylenglykol - Die Summenformel von PEG lautet (C2H4O) n + 1H2O.
-
Allgemeine Merkmale :
MEG: eine geruchlose, farblose, süße Verbindung. Es ist eine organische Verbindung, die als Rohstoff bei der Herstellung von Polyesterfasern und Frostschutzmittelformulierungen verwendet wird. Diese Materialien können beim Verschlucken giftig sein.
PEG: ist eine polymere Verbindung, die in chemischen, biologischen, medizinischen, industriellen und kommerziellen Bereichen verwendet wird. Es ist eine klare Flüssigkeit oder ein wasserlöslicher weißer Feststoff mit einem schwachen Geruch.
-
Produktionsmethode:
MEG: eine chemische Verbindung, die unter Verwendung von Ethylen hergestellt wird. Bei diesem Verfahren wird Ethylenoxid als Zwischenprodukt hergestellt und reagiert mit Wasser unter Bildung von EO. Bei diesem Verfahren werden Säuren und Basen als Katalysatoren verwendet.
PEG: Es entsteht durch Reaktion von Ethylenoxid mit Wasser mit Ethylenglykol oder Glykololigomeren. Dieser Prozess verwendet sowohl Säuren als auch Basen, um diesen Prozess zu katalysieren. Der Polymerisationsprozess kann abhängig von der Verwendung des Katalysators kationisch oder anionisch sein.
-
Anwendungsbereich:
MEG: Wird hauptsächlich als Frostschutzmittel und auch als Rohstoff in der Kunststoffindustrie bei der Herstellung von Polyestern wie Heimtieren verwendet. Es ist auch nützlich bei der Wärmeübertragung, insbesondere in Automobil- und flüssigkeitsgekühlten Computern. Aufgrund seiner Eigenschaften kann es auch in Kaltwasserkonditionierungssystemen eingesetzt werden.
PEG: Es hat eine geringere Toxizität und wird daher als Schmiermittelbeschichtung sowohl für wässrige als auch für nichtwässrige Umgebungen verwendet. Wird als Basis für viele Hautcremes und persönliche Gleitmittel verwendet. Es wird auch als Bestandteil in Zahnpasta oder Spender sowie als Antischaummittel in Anwendungen der Lebensmittelindustrie verwendet.
PMMA (PolyMethyl MethAcrylate)
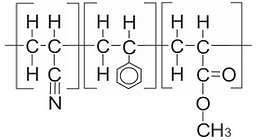
Es ist eine nicht abbaubare Form von Polyacrylat, die üblicherweise für optische Komponenten mit hoher Klarheit und struktureller Härte verwendet wird. Es ist ein farbloses und transparentes thermoplastisches Polymer, das auf dem Markt besser als Acrylglas oder Plexiglas bekannt ist.
Es ist ein Kunstharz, das durch den Polymerisationsprozess von Methylmethacrylat hergestellt wird. Es ist ein transparenter, starrer und transparenter Kunststoff, der häufig bei der Herstellung von Glas verwendet wird (Fenster, Oberlichter, laminierte Schilder und Flugzeugüberdachungen usw.). Es wird im Allgemeinen als alternatives Material zu Glas bevorzugt und kann eine Alternative zu Produkten sein, in denen Polycarbonat verwendet wird, da es ähnliche Eigenschaften wie Polycarbonat aufweist. Dieser Kunststoff, der wie ein Kristall aussieht, ist im Freien witterungsbeständig und halb so schwer wie Glas. Er weist eine hohe Schlagfestigkeit auf.
Dieses Material hat sich als wirtschaftliche Alternative zu Polycarbonat erwiesen, wenn Zugfestigkeit, Transparenz, Polier- und UV-Beständigkeit wichtiger sind als Schlagzähigkeit und Beständigkeit gegen Chemikalien und Hitze. Polycarbonat wird bevorzugt, weil es kein schädliches Bisphenol-A enthält, eine Untereinheit, die in Polycarbonatmaterialien vorkommt. Dieses Harz ist auch aufgrund seiner vernünftigen Eigenschaften, seiner einfachen Verwendung und Verarbeitung und seiner geringen Kosten gegenüber anderen vorteilhaft.
Es wurde erstmals 1930 von den britischen Chemikern Rowland Hill und John Crawford bei Imperial Chemical Industries in England entdeckt und unter der Marke Perspex registriert.
Gleichzeitig arbeitete Otto Rohm (Chemiker und Industrieller) in Deutschland an der Herstellung von Sicherheitsglas durch Polymerisation von Methacrylat zwischen zwei Glasschichten. Als resultierendes Polymer wurde es vom Glas getrennt und lieferte eine durchsichtige Plastikfolie, die das Markenzeichen von Plexiglas ist. Dieses Produkt kam Ende der 1930er Jahre auch auf den kommerziellen Markt.
Später in den USA stellte EI du Pont de Nemours & Company (jetzt DuPont) seine Produkte unter dem Handelsnamen Lucite vor und wurde im Zweiten Weltkrieg am häufigsten bei der Herstellung von Flugzeugfenstern und Ballondächern für Waffentürme verwendet.
Obwohl es aufgrund seiner Billigkeit und einfachen Verarbeitung bevorzugt wird, ist sein Verwendungsbereich aufgrund seiner zerbrechlichen Struktur etwas begrenzt. PMMA wurde erstmals im Fallschirmbau eingesetzt. Darüber hinaus wird es zur Dekoration, Beleuchtung und Herstellung von Aquarien, Tischen, Spülen und Küchenspülen sowie zur Herstellung einiger Implantate und optischer Linsen im menschlichen Körper verwendet.
PMMA gehört zu den Mitgliedern der großen Methacrylatesterfamilie mit einer gebundenen Alkyl- oder Arylgruppe. Es wird im Allgemeinen durch Emulsionspolymerisation, Lösungspolymerisation und Massenpolymerisation hergestellt.
PMMA-Material ist ein Methacrylsäureester, der zu einer wichtigen Familie von Acrylharzen gehört. Zunächst wird Propylen (PP) erhalten, das im Produktionsprozess verwendet wird. Propylen und Benzol werden auch miteinander umgesetzt, um Cumol oder Iisopropylbenzol herzustellen. Das erzeugte Cumol wird dann zu Cumolhydroperoxid oxidiert. Es wird dann mit Säure behandelt, um Aceton zu erzeugen, das in Methylmethacrylat (brennbare Flüssigkeit) umgewandelt wird. Diese Flüssigkeit wird unter Einwirkung von Radikalinitiatoren unter Bildung von Feststoffen (PMMA-Kunststoff) zu Massenflüssigkeit oder suspendierten feinen Wassertröpfchen polymerisiert.
PMMA wird auf dem Markt häufiger unter den Marken Plexiglas, Lucite-Perspex identifiziert.
PMMA-Hauptmerkmale:
-
Es ist ein starkes, haltbares und leichtes Material.
-
Es hat eine bessere Schlagfestigkeit als Glas und Polystyrol.
-
Es zeigt im Vergleich zu anderen Kunststoffen eine überlegene Umweltstabilität.
-
Es hat eine hohe thermische und chemische Beständigkeit.
-
Es hat eine geringe Rauchemission.
-
Es hat eine ausgezeichnete Abriebfestigkeit.
-
Es weist eine hohe Festigkeit und Haltbarkeit auf.
-
Es hat eine hohe Lichtdurchlässigkeit.
-
Dichte - 1,17 - 1,20 g / cm 3 (weniger als die Hälfte des Glases)
-
Schmelzpunkt - 160 ° C (320 ° F, 433 K)
-
Wasseraufnahme - 0,3-0,4%
-
Zündtemperatur - 460 ° C (860 ° F)
-
Löslichkeit - schmilzt leicht und löst sich in vielen organischen Lösungsmitteln.
-
Die Schlagfestigkeit kann im Vergleich zu anderen Ersatzkunststoffen gering bleiben. hast.
-
Es ist gegenüber anderen Kunststoffpolymeren vorteilhaft, da es während des Hydrolyseprozesses kein Bisphenol A (BPA) enthält oder freisetzt.
-
Sogar verwandte Kunststoffe, die Polycarbonat sind, enthalten BPA, das von Natur aus giftig ist. (BPA ist gefährlich für Gesundheit und Umwelt). PMMA ist eine Art Kunststoff, der von Natur aus nicht toxisch ist und kein BPA (Bisphenol-A) enthält, wenn er selbst fest ist.
-
Im Allgemeinen können beim 3D-Druck von Erz entstehende Dämpfe giftig sein, wenn sie in geschmolzener Form zum Spritzgießen verwendet werden. Da dies zu Gesundheitsrisiken führen kann, sollte das Einatmen vermieden und der Produktionsbereich gut belüftet werden.
PMMA-Verwendungsbereich:
PMMA ist ein vielseitiges Kunststoffmaterial, das für eine Vielzahl von Anwendungen in verschiedenen Bereichen und Formen eingesetzt werden kann.
Dank seiner positiven physikalischen, chemischen und mechanischen Eigenschaften kann es in einer Reihe von Anwendungen auf folgende Weise eingesetzt werden:
Aufgrund seiner transparenten und klaren Struktur wird es häufig anstelle von Glas verwendet. Dieses Glasersatzmaterial kann in folgenden Bereichen angewendet werden:
-
Beim Bau von Gewerbe- und Wohnaquarien
-
Anzeigen von PMMA-Plastikgläsern, Anschlüssen sowie fehlenden Druckhüllen des Tauchers. Bei der Verfolgung von Kugeln für U-Boote
-
Linsen von Außenleuchten in Automobilen und Zuschauerschutzplatten von Eishockeyfeldern
-
An Flugzeugfenstern, sogar anstelle von Fenstern von Polizeifahrzeugen.
-
Leuchtturmlinsen, Glasdecken, Dacheindeckungen von Bereichen wie botanischen Gärten
-
In verschiedenen Segmenten, um das Licht neu auszurichten
-
In lasergeschnittenen Acrylplatten trägt es mit einem Lichtleiter Sonnenlicht in Innenräume.
-
In verschiedenen künstlerischen Anwendungen für dekorative Zwecke
-
Bei der Herstellung von prismengeschichteten Platten, um das Sonnenlicht von den Fenstern auf den Boden oder die Decke des Raumes zu lenken
PTFE (PolyTetraFluorethylen)
Es ist ein starker, harter, wachsartiger, nicht brennbarer Kunstharztyp, der durch den Polymerisationsprozess hergestellt wird. Es wird häufig unter den Marken Teflon, Hostaflon und Polyflon verwendet, um Antihaftpfannen oder rutschige Gegenstände herzustellen.
Es hat die höchste Betriebstemperatur unter allen Industriekunststoffen - 260 bis 270 ° C, unendliche Beständigkeit gegen Feuchtigkeit und Umgebungsbedingungen für alle in der Industrie verwendeten Chemikalien, den niedrigsten statischen und dynamischen Reibungskoeffizienten unter allen Feststoffen, überlegene elektrische Isolierung Klebrigkeit, Zusätzlich zur Nichtverbrennung und solchen Merkmalen wird es wegen seiner ausreichenden mechanischen Eigenschaften und vollen Beständigkeit gegenüber allen chemischen Substanzen bevorzugt.
Es wurde versehentlich von Roy Plunkett (amerikanischer Chemiker bei EI du Pont de Nemours & Company) im Jahr 1938 entdeckt, als er feststellte, dass ein Gas-TFE-Kältemitteltank zu einem weißen Pulver polymerisiert wurde. Später, während des Zweiten Weltkriegs, wurde es als korrosionsbeständige Beschichtung zum Schutz von Metallgeräten für den Transport radioaktiver Materialien verwendet.
Aufgrund seiner Rutschfestigkeit und seines hohen Schmelzpunkts wurde es erst in großem Umfang eingesetzt, als es 1960 von DuPont unter dem Markennamen Teflon-Coated Antihaft-Kochgeschirr eingeführt wurde. Dies ist die bekannteste Marke für Antihaftpfannen und -töpfe, die mit Harzmaterial beschichtet sind. PTFE ist daher besser bekannt mit "Teflon", einer der führenden Marken von DuPont.
PTFE wird durch radikalische Polymerisation von Tetrafluorethylen hergestellt. Da sich Tetrafluorethylen durch Explosion in Tetrafluormethan und Kohlenstoff zersetzen kann, werden verschiedene spezielle Geräte verwendet, um heiße Stellen zu verhindern, die schädliche Nebenreaktionen verursachen können.
Der Prozess wird durch Persulfat initiiert, das homolisiert wird, um Sulfatradikale zu erzeugen. Das resultierende Polymer wird dann mit Sulfatestergruppen terminiert, die hydrolysiert werden können, um Endgruppen des Polymers herzustellen. Da dieses Material in nahezu jedem Lösungsmittel löslich ist, wird der Polymerisationsprozess (unter Verwendung von Tensiden wie PFOS) als Emulsion in Wasser durchgeführt.
Die Hauptrohstoffe von PTFE sind Chloroform, Flussspat und Salzsäure.
Es ist hauptsächlich in feiner, mikronisierter Pulverform und auch in wässriger Dispersion erhältlich.
PTFE Hauptmerkmale:
-
Es ist extrem beständig gegen Chemikalien und Wetterbedingungen.
-
Es hat ausgezeichnete dielektrische Eigenschaften.
-
Es zeigt eine hohe thermische Stabilität bei starker Flammwidrigkeit.
-
Antihaft, geringer Reibungswiderstand.
-
Es ist kompatibel mit Lebensmittelkontakt.
-
Es hat einen glatten Oberflächenbeschichtungseffekt.
-
Es wird nicht nass und schützt stark vor Korrosion.
-
Dichte - 2200 kg / m 3
-
Schmelzpunkt - 600 K.
-
Wärmeausdehnung - 112–125 • 10 −6 K −1 [23]
-
Glastemperatur-388K [22]
-
Reibungskoeffizient - 0,05-0,10
PTFE-Verwendungsbereich:
Heute wird PTFE-Polymer hauptsächlich als Antihaft-Kochgeschirrbeschichtung verwendet. Es hat Anwendungen in einer Reihe von Industrieprodukten, einschließlich Lagern, Rohrauskleidungen und einer Vielzahl von Pumpen- und Ventilteilen.
Dieses Material ist in einer Vielzahl von Anwendungen in Form von mechanischen Bauteilen und als Beschichtungsmaterialien weit verbreitet. Zu den wichtigsten Endverbraucherindustrien, die von diesen Harzen bedient werden, gehören chemische Verarbeitung, Mechanik, Lebensmittel, Haushalt, Automobil, Elektronik und viele andere Dinge.
Mit den besten Antihaft-Eigenschaften und der Beständigkeit gegen hohe Temperaturen ist PTFE ein unglaublich vielseitiges Material mit einer Vielzahl bekannter Anwendungen. PTFE zeichnet sich durch folgende Vorteile aus:
-
Es ist hervorragend in der elektrischen Isolierung. Computeranwendungen werden als Isolator für Kabel und Kabel verwendet.
-
Mit seiner geringen Reibungseigenschaft ist es ein beliebtes Material für Maschinenbauanwendungen, einschließlich der Verwendung in Gleitlagern, Gleitplatten, Zahnrädern und anderen Arbeitsteilen.
-
Es ist abriebfest, nicht reaktiv und tolerant gegenüber hohen Temperaturen. Diese Funktion macht es für den Einsatz in Industrierohren und Schlauchleitungen (wo Chemikalien und Säuren verwendet werden) geeignet.
-
Es verträgt hohe Temperaturen. Daher ist es in Säuren und Chemikalien sowie in der chemischen Industrie weit verbreitet.
-
Der Kontakt mit Lebensmitteln schadet nicht und ist daher eine ausgezeichnete Wahl für Anwendungen in Verpackungen.
-
Es ist eine ideale Wahl zum Abdichten von Bauteilen bei chemisch aggressiven Anwendungen.
-
Es hat eine wirtschaftliche Struktur. Es ist weit verbreitet in Parks, Supermärkten, Brückenbau und sogar Autos.
-
Dieses Material hat den höchsten Schmelzpunkt und kann auch bei 260 ° C widerstehen. Aus diesem Grund wird es häufig bei der Herstellung von Folien und Folien verwendet, die für eine Vielzahl von Anwendungen als Endprodukt im Endsegmentmarkt eingesetzt werden. Es wird als Beschichtungsmaterial für verschiedene Anwendungen in verschiedenen Branchen wie Luftfahrt, Elektronik und Automobil bevorzugt.
Reines PTFE:
Es ist eine der bekanntesten chemisch inerten Materialformen, die in vielen verschiedenen Anwendungen und Branchen verwendet werden.
Es wird üblicherweise in elektrischen Hochspannungssteckverbindern, Umfangsdichtungen und kommerziellen Angelrollen verwendet.
Andere Anwendungen umfassen Pumpengehäuse, Ventildichtungen, Zylinderlaufbuchsen, Wellenlager, Filtergehäuse, Pumpen- und Werkzeugbau, Elektroindustrie, Lasertechnologie, Lebensmittel- und Medizintechnik und andere.
-
Es hat eine hohe chemische Beständigkeit über einen weiten Temperaturbereich.
-
Bietet hervorragende Wärmestabilität und elektrische Isolierung.
-
Es hat eine unendliche Haltbarkeit.
-
Es hat einen niedrigen Reibungskoeffizienten.
-
Zugfestigkeit - 20-30 MPa
-
Spezifisches Gewicht - 2,14 - 2,19 g / cm 3
-
Reibungskoeffizient - <0,1
-
Wasseraufnahme - Null
Glasgefülltes PTFE:
Es ist eine Kombination aus Glasfasern gemischt mit reiner PTFE-Form. Es hilft, die Druckfestigkeit zu erhöhen und Verformungen unter Last zu reduzieren. Es wird in den Bereichen Rauchbehandlung, Walzenbeschichtung, Maschinenteile, Chemieingenieurwesen, Reinwasserherstellung und Ätzplatten eingesetzt.
-
Verbesserte Härte und Verschleißfestigkeit.
-
Geringere Wärmeausdehnungseigenschaft mit höherem Reibungskoeffizienten.
-
Nicht für abrasiv gefüllte Anwendungen geeignet.
-
Es hat eine geringere Beständigkeit gegen Gase und ist nicht leitend.
-
Zugfestigkeit - 31 MPa (4600 PSI)
-
Spezifisches Gewicht - 2,23 - 2,26 g / cm 3
-
Wärmeleitfähigkeit - 10,6 x 10 & supmin; & sup4; cal / cm & supmin; ² ° C.
-
Linearer Wärmeausdehnungskoeffizient --7-11,2 x 10 -5 ° C (100 ° C)
Mit Bronze gefülltes PTFE:
Es ist die Zugabe von Bronze zu reinem PTFE-Material, um eine bessere Dimensionsstabilität zu erzielen und die Reibung bei kaltem Fluss und Verschleiß zu verringern. Wie andere PTFE-Typen vermeidet dieser Typ eine Reihe von Variationen, die manipuliert werden können, um die Eigenschaften für die Verwendung zu verbessern.
-
Es hat eine gute elektrische und thermische Leitfähigkeit.
-
Es zeigt eine verbesserte Verschleißfestigkeit, insbesondere unter Last.
-
Es ist sehr sparsam und sehr chemikalienbeständig.
-
Spezifisches Gewicht - 2,05 - 2,12 g / cm 3
-
Zugfestigkeit - 13-18 MPa
-
Dehnung - 90 - 300%
-
Statischer und dynamischer Reibungskoeffizient - 0,14 - 0,16 und 0,12 - 0,14
Mit Kohlenstoff gefülltes PTFE:
In dieser Qualität wird der reinen Form von PTFE Kohlenstoff zugesetzt, was zur Erhöhung der Festigkeit und Verschleißfestigkeit beiträgt. Es hilft auch, Wärmeleitfähigkeit und geringe Permeabilität bereitzustellen. Es ist in der Kompressorindustrie weit verbreitet, seine Hauptanwendung umfasst Verschleißringe, Kolbenringe und Lagerringe. Da es sich um ein äußerst vielseitiges Material handelt, wird es auch für Hochleistungsdichtungen und -wischer verwendet.
-
Es ist ein strapazierfähiges Material mit einem sehr hohen spezifischen Gewicht.
-
Es weist eine gute thermische und elektrische Leitfähigkeit auf.
-
Es hat die besten Trageeigenschaften unter allen Qualitäten.
-
Es hat eine hohe Verformungsbeständigkeit.
-
Spezifisches Gewicht - 3,8 - 3,95 g / cm 3
-
Zugfestigkeit - 10-18 MPa
-
Dehnung - 100% - 200%
-
Shore D-Härte - 65-75
Mit Edelstahl gefülltes PTFE:
Wenn dem reinen PTFE-Material des Polymers Stahl zugesetzt wird, gewinnt er eine ausgezeichnete Festigkeit und Stabilität, selbst um hohen Temperaturen und Überlastungen standzuhalten. Es ist eine vielseitige Form der Qualität, die in Dampf- und Thermofluidanwendungen verwendet werden kann. Aufgrund seiner hohen Verschleißfestigkeit ist es ein sehr gutes Material für flussgesteuerte V-Ball-Kugelhahnanwendungen.
-
Es hat die thermische und elektrische Leitfähigkeit erhöht.
-
Es hat eine ausgezeichnete Struktur unter extremer Belastung und Temperatur.
-
Es ist beständig gegen geringe Reibung, Kältefluss und Abrieb.
-
Obwohl es sehr schwer ist, hat es eine extrem schwierige Tragequalität.
-
Spezifisches Gewicht - 3,35 g / cm 3
-
Zugfestigkeit - min. 22 MPa
-
Dehnung - min. 220%
-
Shore D-Härte - 65-69
Pulver PTFE:
PTFE ist auch in Form eines weißen Pulvers erhältlich, das unter dem Begriff "feines Pulver" bekannt ist. Teflonfeinpulver ist auch der bekannte Markenname für ein pulverförmiges Material. Es wird als Beschichtungsmaterial in Industrie- und Haushaltswaren verwendet.
Diese Pulver werden durch den Pastenextrusionsprozess und anschließendes Erhitzen nach der Extrusion in verwendbare Elemente (Formen, Drähte, Bänder usw.) umgewandelt. Dieses Verfahren wird verwendet, um restliche Lösungsmittel von Kohlenwasserstoffen zu entfernen und zu entwickeln. Dieses Pulver eignet sich für Berührungsgewichtsmessungen bei großen Einwirkungen, da es die Reibung im Vergleich zu anderen Schmiermitteln verringert.
Es wird hauptsächlich als Beschichtungsmaterial in verschiedenen Branchen verwendet. Es hat auch andere Verwendungszwecke, einschließlich Draht- und Kabelisolierung, die in Rohren, Rohrauskleidungen und Folien verwendet wird. Es wird sogar für gesinterte und nicht gesinterte Bänder, mikroporöse Membranen, Schrumpfschläuche, Profilformen, Buchsen, Zug- / Druckkabel und viele andere Komponenten verwendet, die Hochleistungskunststoffe erfordern. Häufig verwendete Pulverbeschichtungstypen sind - Polyester, TGIC-Polyester, Epoxid, Urethane, PVDF (Polyvinylidenfluorid).
-
Attraktiveres, hochwertiges Finish und Langlebigkeit.
-
Wirtschaftlich und umweltfreundlich sein.
-
Längere Korrosionsbeständigkeit.
-
Physikalische Eigenschaft verschiedener Farben oder Glanz.

PA (PolyAmid)
Es ist ein in der Maschinenindustrie weit verbreitetes Material. Es ist als Nylon bekannt. Es gibt Typen wie Nylon6, Nylon6,6, Nylon11. Das Schlimmste an Nylon ist seine hohe Wasseraufnahme. Alle Nylontypen sind mit Fasern verstärkt. Nylon hat eine kristalline Struktur. Nylon6 hat eine Struktur, die zum Gießen kommt. Andere Nylontypen können nur mit Injektions- und Extrusionsverfahren verwendet werden, die einen hohen Druck erfordern, da sie hart fließen. Es ist ein Material mit relativ Härte, Steifheit, Rutschgefahr und guten mechanischen Festigkeitswerten. Es ist nicht so rutschig wie Polyacetal (POM). Seine chemische Beständigkeit ist mittelgroß, es ist beständig gegen einige Säuren und Basen. Polyamid 6 hat die Fähigkeit, Wasser in seinem Körper zu sammeln. Diese Eigenschaften haben gute und schlechte Seiten. Sein guter Aspekt erhöht die Widerstandsfähigkeit des Stücks gegen Vibrationen und plötzliche Stöße. Auf diese Weise können die dynamischen Spannungen, die während der Verwendung des Teils auftreten, im Körper beseitigt werden. Der Nachteil ist, dass es schwierig wird, Dimensionsstabilität im Material zu erreichen. Es wird zur Herstellung von einfachen Zahnrädern, Lagern, Bolzen, Flanschen, Riemenscheiben, Schneidplatten, Filterplatten, Schalen und allen Arten von Teilen verwendet.
Nylon 6 und 6.6 werden mit einer Vielzahl von Verstärkern und Modifikatoren kombiniert, um neue Materialien zu schaffen, die auf die Kunden- und Anwendungsanforderungen sowie auf Kosten- und Leistungsbeschränkungen zugeschnitten sind.
PA 6:
Es ist ein weißer, teilkristalliner Thermoplast, der Nylon 6.6 sehr ähnlich ist und in vielerlei Hinsicht austauschbar ist. Seine geschmolzene Viskosität ist geringer als Nylon 6.6 und daher ist es im Allgemeinen etwas einfacher zu handhaben und wird häufig zum Formen bevorzugt. Es hat auch eine höhere Schlagfestigkeit, aber weniger Steifheit und größere Wasseraufnahme.
Wird im Allgemeinen an Orten verwendet, an denen hohe Betriebstemperaturen erforderlich sind, z. B. bei Zahnrädern, Nocken, Zylindern, Lagern, Schrauben und Muttern, Elektrowerkzeugkörpern, elektrischen Steckverbindern, Kraftstofftanks für Kraftfahrzeuge und Küchenutensilien.
-
Es hat gute Gleit- und Abriebeigenschaften
-
Es ist beständig gegen viele Öle, Fette und Kraftstoffe.
-
Es zeigt hohe Festigkeit.
-
Es ist eine gute Wahl für die Verarbeitung.
-
Es zeigt hohe Leistung.
-
Es zeigt eine gute Abdichtung.
-
Einfacher zu handhaben (geformt) als Nylon 6.6
-
Es ist zum Spritzgießen geeignet.
-
Es hat eine geringere Formschrumpfung als Nylon 6.6.
-
Gute Ermüdungsbeständigkeit
-
Zusätzliche Härte kann durch Einbeziehung von Glasfasern erreicht werden.
PA 6,6:
Nylon 6.6 ist sehr hart und bruchsicher, aber seine dichte Struktur macht es schwierig, seine Fasern zu färben. Einmal gefärbt, hat es jedoch eine hohe Farbechtheit und ändert seine Form unter Sonnenlicht nur sehr wenig. Im Allgemeinen sind es die Anwendungsbereiche, in denen hohe Betriebstemperaturen erforderlich sind, z. B. die Innenausstattung von Kraftfahrzeugen.
-
Es ist hitzebeständig und dies ist besonders vorteilhaft, um eine Torsion zu verhindern
-
Es hat gute Gleit- und Abriebeigenschaften.
-
Beständig gegen viele Öle, Fette und Kraftstoffe
-
Es hat eine hohe Festigkeit.
-
Hat elektrische Isolierung
-
Es erfordert eine höhere Plastifizierungstemperatur als Nylon 6.
DEHP (DiEthylHexylPhthalate)

DEHP (DiEthylHexylPhthalat)
DiEtylhexylphthalat (DEHP, Formel: C6H4 (C8H17COO) 2) ist ein niedermolekulares Orthophthalat, das durch Veresterung von Phthalsäureanhydrid mit 2-Ethylhexanol hergestellt wird. Es ist eine nichtflüchtige, farblose und geruchlose viskose Flüssigkeit, die in Öl löslich ist, aber in Wasser fehlt. Aufgrund seiner geringen Kosten und seiner insgesamt guten Leistung wird DEHP häufig als Weichmacher bei der Herstellung von PVC-Produkten verwendet.
-
Eine gute Gelierung bietet zufriedenstellende elektrische Eigenschaften und trägt zur Herstellung hochelastischer Verbindungen mit angemessener Kältefestigkeit bei.
-
Es hat eine sehr gute Flexibilität bei niedrigen Temperaturen und eine gewisse Beständigkeit gegen hohe Temperaturen.
-
DEHP wird von der IARC als menschliches Karzinogen eingestuft.
-
DEHP wurde in einigen Studien als Hormonmimetikum und Entwicklungstoxin identifiziert.
-
In der EU wird DEHP nach REACH-Gesetzgebung als SVHC (ein sehr wichtiger Stoff) angesehen und kann in den meisten Produkten nicht verwendet werden
-
Es lässt sich leicht in unpolare Lösungsmittel (Öle und Fette in mit PVC verpackten Lebensmitteln) extrahieren. Aus diesem Grund erlaubt die US-amerikanische Food and Drug Administration (FDA), DEHP-haltige Verpackungen nur für Lebensmittel zu verwenden, die hauptsächlich aus Wasser bestehen.
PVC-, Vinylchlorid- und Vinylacetat-Copolymere, Katheter, Röhrchen usw. Medizinprodukte, DEHP wird bei der Entwicklung von Formulierungen verwendet, die von glasartigen Verbindungen bis zu weichen und hochflexiblen Materialien reichen. Es ist der bekannteste Weichmacher der Welt, obwohl seine Verwendung aufgrund von Bedenken hinsichtlich seiner Auswirkungen auf die menschliche Gesundheit reduziert wurde.
Schmelzpunkt -50 ° C, Siedepunkt 250-257 ° C bei 0,5 kPa.
DINP (DiIsoNonylPhthalate)
Diisononylphthalat (DINP, Formel: C26H42O4) ist ein hochmolekulares Orthophthalat, das durch Veresterung von Phthalsäureanhydrid mit Isononylalkohol in einem geschlossenen System hergestellt wird. Es ist eine ölige Flüssigkeit, die fast farblos und geruchlos ist. Es ist in Wasser schwer löslich, aber in Alkohol, Hexan usw. Es ist löslich, mischbar und mit allen in PVC-Zusammensetzungen verwendeten monomeren Weichmachern kompatibel.
-
Bietet Flexibilität und Haltbarkeit für Vinylprodukte
-
Gute Leistung bei niedrigen und hohen Temperaturen
-
Weniger flüchtig als DEHP
-
Eine gute Zahlungsfähigkeit führt zu guten flexiblen PVC-Verarbeitungseigenschaften.
-
Es wird häufig in Innen- und Außenanwendungen eingesetzt. Da es weniger flüchtig ist, ist es bei Anwendungen wirksam, bei denen Produkte relativ hohen Temperaturen ausgesetzt sind und eine größere Beständigkeit gegen Abbau aufweisen.
-
DINP hilft Vinylprodukten, vielen Wetterbedingungen standzuhalten, macht sie wasserdicht und bietet eine hohe Wärmeisolierung und Haltbarkeit
-
DINP wird von Bodenbelagsherstellern mit PVC-Pulver kombiniert, um weiche und flexible Endprodukte herzustellen.
Schmelzpunkt –43 ° C, Siedepunkt 244–252 ° C bei 0,7 kPa,
Flammpunkt 221 ° C (cc)
DINP (DiIsoNonylPhthalate)

DEHP (DiEthylHexylPhthalat)
DiEtylhexylphthalat (DEHP, Formel: C6H4 (C8H17COO) 2) ist ein niedermolekulares Orthophthalat, das durch Veresterung von Phthalsäureanhydrid mit 2-Ethylhexanol hergestellt wird. Es ist eine nichtflüchtige, farblose und geruchlose viskose Flüssigkeit, die in Öl löslich ist, aber in Wasser fehlt. Aufgrund seiner geringen Kosten und seiner insgesamt guten Leistung wird DEHP häufig als Weichmacher bei der Herstellung von PVC-Produkten verwendet.
-
Eine gute Gelierung bietet zufriedenstellende elektrische Eigenschaften und trägt zur Herstellung hochelastischer Verbindungen mit angemessener Kältefestigkeit bei.
-
Es hat eine sehr gute Flexibilität bei niedrigen Temperaturen und eine gewisse Beständigkeit gegen hohe Temperaturen.
-
DEHP wird von der IARC als menschliches Karzinogen eingestuft.
-
DEHP wurde in einigen Studien als Hormonmimetikum und Entwicklungstoxin identifiziert.
-
In der EU wird DEHP nach REACH-Gesetzgebung als SVHC (ein sehr wichtiger Stoff) angesehen und kann in den meisten Produkten nicht verwendet werden
-
Es lässt sich leicht in unpolare Lösungsmittel (Öle und Fette in mit PVC verpackten Lebensmitteln) extrahieren. Aus diesem Grund erlaubt die US-amerikanische Food and Drug Administration (FDA), DEHP-haltige Verpackungen nur für Lebensmittel zu verwenden, die hauptsächlich aus Wasser bestehen.
PVC-, Vinylchlorid- und Vinylacetat-Copolymere, Katheter, Röhrchen usw. Medizinprodukte, DEHP wird bei der Entwicklung von Formulierungen verwendet, die von glasartigen Verbindungen bis zu weichen und hochflexiblen Materialien reichen. Es ist der bekannteste Weichmacher der Welt, obwohl seine Verwendung aufgrund von Bedenken hinsichtlich seiner Auswirkungen auf die menschliche Gesundheit reduziert wurde.
Schmelzpunkt -50 ° C, Siedepunkt 250-257 ° C bei 0,5 kPa.
DINP (DiIsoNonylPhthalate)
Diisononylphthalat (DINP, Formel: C26H42O4) ist ein hochmolekulares Orthophthalat, das durch Veresterung von Phthalsäureanhydrid mit Isononylalkohol in einem geschlossenen System hergestellt wird. Es ist eine ölige Flüssigkeit, die fast farblos und geruchlos ist. Es ist in Wasser schwer löslich, aber in Alkohol, Hexan usw. Es ist löslich, mischbar und mit allen in PVC-Zusammensetzungen verwendeten monomeren Weichmachern kompatibel.
-
Bietet Flexibilität und Haltbarkeit für Vinylprodukte
-
Gute Leistung bei niedrigen und hohen Temperaturen
-
Weniger flüchtig als DEHP
-
Eine gute Zahlungsfähigkeit führt zu guten flexiblen PVC-Verarbeitungseigenschaften.
-
Es wird häufig in Innen- und Außenanwendungen eingesetzt. Da es weniger flüchtig ist, ist es bei Anwendungen wirksam, bei denen Produkte relativ hohen Temperaturen ausgesetzt sind und eine größere Beständigkeit gegen Abbau aufweisen.
-
DINP hilft Vinylprodukten, vielen Wetterbedingungen standzuhalten, macht sie wasserdicht und bietet eine hohe Wärmeisolierung und Haltbarkeit
-
DINP wird von Bodenbelagsherstellern mit PVC-Pulver kombiniert, um weiche und flexible Endprodukte herzustellen.
Schmelzpunkt –43 ° C, Siedepunkt 244–252 ° C bei 0,7 kPa,
Flammpunkt 221 ° C (cc)
ASS (AcrylnitrilStyrenacrylat)
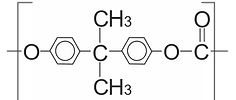
Es wird durch Zugabe eines gepfropften Acrylesterelastomers während der Copolymerisationsreaktion zwischen Styrol und Acrylnitril hergestellt.
Es ist UV-beständig, hat eine gute Fließfähigkeit. Es ist ein Material ähnlich wie ABS.
ASS schmilzt mit anderen Thermoplasten, was zu einer Schwäche führt, wie Polyolefinen, Polystyrolen und Nylons. Es wird von konzentrierten Säuren, aromatischen und chlorierten Kohlenwasserstoffen, Estern, Ethern und Ketonen ausgeschieden. Beim Verbrennen entsteht giftiger Rauch.
PBT (PolyButylenterephthalat)

Es ist ein teilkristallines Polymer, das beim Spritzgießen verwendet wird. Sie zeigen auch bei hoher Leistung und Temperatur eine sehr gute Kriechfestigkeit. Es hat Eigenschaften der Beständigkeit gegen Rissbildung durch Umweltbelastung. Aufgrund seines geringen Ausdehnungskoeffizienten und seiner geringen Wasseraufnahme eignet es sich besonders für technische Anwendungen, die eine hohe Dimensionsstabilität erfordern.
PC (Polycarbonat)

Es ist ein Hochleistungsthermoplast mit einem geringen spezifischen Gewicht.
Er ist nicht nur ein wichtiger technischer Kunststoff mit hoher Schlagfestigkeit, geringer Feuchtigkeitsabsorptionsrate, guter Wärmeisolierung und Wärmestabilität, sondern hat dank seiner einfachen Verarbeitung und Verarbeitbarkeit auch seinen Platz unter den kommerziellen Polymeren eingenommen.
Es wird zur Herstellung von Wasserflaschen, Hochtemperaturkochgeschirr, Schutzgläsern, CDs, DVDs, medizinischen Geräten, Fassadenverkleidungen und Beleuchtungsgehäusen in Kraftfahrzeugen verwendet.
Polycarbonat ist kaum brennbar, geht beim Herausziehen aus der Flamme aus und hat eine austretende Flamme. Es ist glasklar, leicht zu färben, widerstandsfähig gegen Klimawandel, kann bei Temperaturen bis zu 120 ° C verwendet werden, nimmt kein Wasser auf, leitet Elektrizität gut, hat eine sehr hohe Festigkeit und Zähigkeit und seine Abmessungen sind stabil. Sie sind auch von starken Säuren und Basen betroffen, und es besteht die Gefahr von Stressbruch und Schmerzen. Sie werden in feinen Arbeiten und elektronischen Bauelementen, Isolationsschrauben, Beleuchtungsgeräten, Autorückleuchten unter Hitzeeinwirkung und Geschirr verwendet.
Ein weiteres Merkmal von Polycarbonat ist, dass es sehr flexibel ist. Typischerweise kann es bei Raumtemperatur gebildet werden, ohne zu reißen oder zu brechen, wie dies bei einem Aluminiumblech der Fall ist. Auch kleine Winkelbiegungen sind ohne möglich, obwohl die Verformung bei Wärmeeinwirkung einfacher sein kann. Diese Eigenschaft macht Polycarbonat-Blechmaterial besonders nützlich für Prototyping-Anwendungen, bei denen Blech nicht lebensfähig ist (z. B. wenn Transparenz erforderlich ist oder ein nicht leitendes Material mit guten elektrischen Isoliereigenschaften erforderlich ist).
Eigenschaften von Polycarbon:
PC wird als "thermoplastisch" (im Gegensatz zu "duroplastisch") klassifiziert und sein Name hat mit der Art und Weise zu tun, wie der Kunststoff auf Wärme reagiert. Thermoplastische Materialien werden beim Schmelzpunkt flüssig (155 ° C bei Polyamid). Eine wichtige vorteilhafte Eigenschaft von Thermoplasten besteht darin, dass sie ohne signifikanten Abbau auf ihren Schmelzpunkt erhitzt, abgekühlt und wieder erwärmt werden können. Anstatt zu brennen, können Thermoplaste wie die Verflüssigung von Polykohlenstoffen leicht spritzgegossen und dann recycelt werden.
Im Gegensatz dazu können duroplastische Kunststoffe nur einmal erhitzt werden (typischerweise während des Spritzgussprozesses). Beim anfänglichen Erhitzen setzen sich duroplastische Materialien (ähnlich wie zweiteiliges Epoxidharz) ab, was zu einer irreversiblen chemischen Veränderung führt. Wenn Sie versuchen, den duroplastischen Kunststoff ein zweites Mal auf eine hohe Temperatur zu erhitzen, brennt er aus. Diese Eigenschaft macht duroplastische Materialien zu schlechten Kandidaten für das Recycling. Polycarbonat ist auch ein amorphes Material, was bedeutet, dass es nicht die regulären Eigenschaften kristalliner Feststoffe zeigt. Typischerweise neigen amorphe Kunststoffe dazu, allmählich zu erweichen (dh sie haben einen größeren Bereich zwischen ihren Glasübergangstemperaturen und ihren Schmelzpunkten), anstatt einen scharfen Übergang von fest zu flüssig als kristalline Polymere zu zeigen. Schließlich ein Polycarbonatcopolymer, mehrere verschiedene Monomere in Kombination mit es besteht aus dem Typ.
Der Grund, warum Polycarbonat sehr oft verwendet wird; Polycarbonatplatten liefern hervorragende Anwendungsergebnisse und werden im Hinblick auf leichtes Biegen und Wärmedämmung bevorzugt. Aus dem ursprünglichen Rohmaterial hergestellte Polycarbonatplatten weisen Schlagfestigkeit und Nichtentflammbarkeit auf. Es ist ein unglaublich nützlicher Kunststoff für Anwendungen, die Transparenz und hohe Schlagfestigkeit erfordern. Es ist eine leichtere Alternative zu Glas und ein natürlicher UV-Filter, daher wird es häufig in Gläsern verwendet.
Es wird versucht, unbegrenzte Bedürfnisse mit begrenzten Energieressourcen zu befriedigen. An diesem Punkt wird es einen kommerziellen Gewinn bringen, die Effizienz des Energieverbrauchs auf dem höchsten Niveau zu halten. Daher werden Polycarbonatplatten verwendet, um insbesondere in Industriearchitekturen stärker vom Sonnenlicht zu profitieren. Diese Platten, die je nach Einsatzgebiet in verschiedenen Größen und Formen vorliegen, werden insbesondere im Dach- und Wandbau von Industriegebäuden eingesetzt. Somit wird sowohl Solarenergie genutzt als auch Strom gespart.
Merkmale und Vorteile von Polycarbonatplatten;
-
Es ist vorteilhaft für die Wärmedämmung. Mit diesen Platten kann der Temperaturausgleich im Inneren gesteuert werden. Dadurch werden die Umgebungstemperatur und der Kalt- oder Heißluftstrom nach außen verhindert.
-
Bietet mechanische Beständigkeit.
-
Es zeigt Beständigkeit gegen Wasseraufnahme. Somit verschlechtert sich die Polycarbonatplatte nicht und absorbiert kein Wasser im Inneren.
-
Es zeigt Schalldämmeigenschaften.
-
Es zeigt Feuerbeständigkeit. Es ist nicht brennbar.
-
Es kann problemlos auf alle Arten von Schrägdächern angewendet werden.
-
Dank seiner Lichtdurchlässigkeit bietet es Kosteneinsparungen.
-
Es ist bruchsicher mit seiner hohen Schlagfestigkeit.
-
Aufgrund seiner Lichtdurchlässigkeit ist es im Hinblick auf die Helligkeit im Vergleich zu Glasmaterialien bevorzugt. Es ist 6 mal leichter als Glas.
-
Diese transparenten Platten erfüllen die Beleuchtungsbedürfnisse.
-
Es hat eine lang anhaltende und nicht anlaufende Struktur.
Anwendungsbereiche für Polycarbonatplatten:
Es wird in gewünschten Abmessungen und Abmessungen hergestellt. Das Unternehmen, das den Antrag stellt, stellt die Produktion aus den erforderlichen Materialien entsprechend dem Zustand des zu bauenden Gebäudes bereit.
Die Platten werden je nach Einsatzgebiet in flachen, gebogenen, geschnittenen, geometrischen Formen hergestellt und entsprechend dem gewünschten Zweck aufgebracht. Diese Platten können aufgrund ihrer Herstellung miteinander verbunden werden. Dank dieser Funktion ist die Installation sehr einfach und schnell. Es ist jedoch wichtig, dass Fachleute mehr Effizienz erzielen. Zusätzlich zu den verschiedenen Techniken, die zum Zeitpunkt der Montage der Platten angewendet wurden, bleiben die Befestigungsschrauben unten, um eine visuelle Verschmutzung zu vermeiden.
Die Hauptanwendungsbereiche, in denen Polycarbonatplatten vorkommen; Werbetafeln, Parkplätze, Bushaltestellen, Sporthallen, Gewächshäuser, Traufe, Gehwege, Durchgänge zwischen Gebäuden, Veranda- und Terrassendächer, Wintergärten, Fabrikfenster, Fassadenanwendungen
Wellpappe-Polycarbonat- Bildschirme mit großen Anwendungsbereichen werden in Gewächshäusern, Vordächern für Wohneingänge und Dacheindeckungen aus massivem Polycarbonat in Bushaltestellen und Einkaufszentren aufgrund ihrer Beleuchtung und Beständigkeit gegen Unzerbrechlichkeit bevorzugt. Darüber hinaus werden Polizeischilde aus Sicherheitsgründen als Schutz in verwendet Motorrad-Visiere.
Genauer gesagt, das Coronavirus in Polycarbonatfolien hat nach Beginn der Covid-19-Ausbruchspandemie seine Verwendung als Schutzraumschutz verstärkt. Aufgrund seiner Haltbarkeit und seines starren Materials, seiner transparenten und hohen Lichtdurchlässigkeit ist es ein bevorzugtes Material und aufgrund der explosionsartigen Nachfrage das am meisten bevorzugte Produkt nach pet-g-Produkten, insbesondere im Gesundheitssektor.
Während des Polycarbon-Pandemieprozesses war es weiterhin das Hauptmaterial bei der Herstellung von Masken, um das Risiko des Einkaufs in Apotheken und Märkten zu minimieren.
Wir haben Polycarbonat als Schutz gegen die negativen Auswirkungen von Regen, Sturm und Wind in offenen Bereichen wie Gärten verwendet. Bei der Pandemie haben wir sie eher als Schutzschild gegen die von Viren ausgehende Gefahr verwendet.
Während Polycarbon aufgrund seines Schutzes und seiner Langlebigkeit in vielen Bereichen unseres täglichen Lebens verwendet wird, hat seine Verwendung im Kampf gegen Pandemien zugenommen und einen wichtigen Platz im Schutz vor äußeren Gefahren erlangt.
Laut AZO Materials wurde Polycarbonat Mitte des 20. Jahrhunderts gleichzeitig in den USA und in Deutschland entwickelt. In der Neuzeit wird es von einer großen Anzahl von Unternehmen hergestellt, von denen jedes typischerweise seinen eigenen Herstellungsprozess und eine einzigartige Formel aufweist.
Handelsnamen umfassen Lexan® (SABIC) oder Makrolon® (Bayer) bekannte Varianten (oder "Harze").
Es sind verschiedene Industriequalitäten von Polycarbonat erhältlich. Die meisten werden nach ihrem Gattungsnamen (Polycarbonat) benannt und unterscheiden sich typischerweise durch die Menge der enthaltenen Glasfaserverstärkung und die Varianz des Schmelzflusses zwischen ihnen. Einige Polycarbonate enthalten Additive wie "UV-Stabilisatoren", die das Material vor längerer Sonneneinstrahlung schützen. Was in unserem Land als "Leksan" als Missbrauch bezeichnet werden soll, ist eigentlich Polycarbot.
Injizierbares Polycarbonat kann andere Additive enthalten, wie z. B. Formtrennmittel, die das Material während der Verarbeitung schmieren. Fertiges Polycarbonat wird normalerweise in Rollen, Stangen oder Blechen verkauft.
Unten; Es zeigt die relative Schlagfestigkeit von Polycarbon im Vergleich zur Schlagfestigkeit anderer häufig verwendeter Kunststoffe wie ABS, Polystyrol (PS) oder Nylon.
Es zeigt die relative Schlagfestigkeit von Polycarbon im Vergleich zur Schlagfestigkeit anderer häufig verwendeter Kunststoffe wie ABS, Polystyrol (PS) oder Nylon. >>>>

POE (PolyOlefin-Elastomer)
POP (PolyOlefin Plastomer)
Dies sind PP-Elastomere mit einer in die Molekülkette integrierten Propylen- und Ethylenmonomermolekülstruktur mit einer Vielzahl von Anwendungen. Der Ethylengehalt bestimmt den Elastizitätsgrad und hat den Vorteil, dass er mit allen Arten von PE und PP gemischt wird. Stretch-Haubenverpackung, Stretchfolie, Zwischenschicht zwischen PE- und metallisierten PP-Schichten, automatische Verpackungsfolie, Schlagverstärker in PE und PP, Masterbatch-Produktion zur Erhöhung des Füllstands, Spritzguss-Anwendungsbereiche, in denen Flexibilität erforderlich ist
-
Sehr elastisch und bohrfest
-
Es hat gute optische Eigenschaften
-
Sehr niedrige Dichtungsinitiierungstemperatur (SIT)
-
Es hat unmittelbar nach dem Versiegeln einen hohen Wärmeisolationswiderstand
-
Rutschfester, erhöhter Reibungskoeffizient
-
Sehr stoßfest bei niedrigen Temperaturen
-
0,865-0,890 g / cm³ Dichte
-
Geeignet für Extrusion und Injektion
-
Mischt sich sehr gut mit LDPE, HDPE und PP
-
Es entspricht den Transportregeln für Lebensmittel.
POM (PolyOxyMethylen)

Acetal hat einen hohen Kristallinitätswert. Es ist hart, steif und hat eine gute Feuchtigkeits-, Wärme- und Lösungsmittelbeständigkeit. Sie bleiben lange Zeit bei hohen Temperaturen stabil. Sie werden als spritzgegossene Produkte mit Glasfaser hergestellt. Anwendungsbereiche sind Zahnräder, Lager, Hülsen, Taschenschnallen. Da für die Sterilisation von medizinischen Verbrauchsmaterialien eine spezielle POM-Produktion erforderlich ist, ist sie nicht weit verbreitet.
Da seine Dichte höher ist als bei anderen Kunststoffen, ist seine Verwendung in der Automobilindustrie begrenzt. Aufgrund seiner hohen Dichte ist auch der Preis hoch. Aus diesem Grund wird es bei Verpackungen nicht bevorzugt, aber es ist sehr häufig bei der Herstellung von elektrischen Verbindungen und Schaltern, Lagern, Zahnrädern, Nippeln und einigen Sanitärverbindungen.
Siehe auch >> Leitfähige Kunststoffe / POM-C
PSA (PolyPhenylenEther)

Es ist ein linearer, nicht kristalliner Polyether. Polyphenylenether, auch als Polyphenylenoxid bekannt, wird häufig mit Polystyrol (PS) gemischt, um seine Härte und Verarbeitbarkeit zu verbessern. Obwohl PSA auf vielen Chemikalien basiert, wird sie von einigen Kohlenwasserstoffen leicht gelöst.
PPO (Polyphenylenoxid)
Es ist ein schlagfestes, hartes und feuchtigkeitsabsorbierendes Polymer. Wird normalerweise in modifizierter Form verwendet. Die Temperaturbeständigkeit ist sehr gut und kann in einem weiten Temperaturbereich (-40 ° C bis +140 ° C) eingesetzt werden. Es ist ein undurchsichtiges Material und beständig gegen Wasserabbau. Tauch- und Wasserpumpen, Zähler, Beleuchtungskörper, Bürogerätekörper, Steckverbinder sind vorrangige Einsatzbereiche.
TPE (ThermoPlastic Elastomer)

Es ist fast keine Compoundierung erforderlich, sie benötigen keine verstärkenden und stabilitätssteigernden Additive, sie können gefärbt werden, es wird weniger Energie für ihre Herstellung verbraucht und es ist einfacher, die Qualität der Teileproduktion zu kontrollieren. Die Nachteile von TPEs sind, dass sie teure Materialien sind, nicht mit billigen Additiven wie Ruß gemischt werden können und eine geringe Beständigkeit gegen Temperatur und Chemikalien aufweisen.
TPU (Thermoplastisches Polyurethan)
Es hat nicht die Wärmebeständigkeit und die Druckfestigkeit von duroplastischen Polyurethanen, aber viele andere Eigenschaften sind ähnlich. Es hat eine überlegene Verschleißfestigkeit, eine gute Flexibilität bei niedrigen Temperaturen, eine ausgezeichnete Ölbeständigkeit und gehört zu den besten für die Tragfähigkeit.
Schuhe, Rohre, Sportgeräte, Draht- und Kabelanwendungen, Schläuche, Räder, Beschichtungsanwendungen für Filmdichtungen sind seine Arbeitsbereiche.
PEI (PolyEtherImide)
Es ist eine klare viskose Flüssigkeit. Es hat die höchste Kationendichte unter anderen verfügbaren Materialien. Es wird in der Papierherstellung, Wasseraufbereitung, Waschmittel-, Klebstoff- und Kosmetikherstellung verwendet.
PAS (PolyArylsulfon)
PES (PolyEtherSulfone)
PES- und PSU-Typen sind transparente amorphe Hochtemperatur-Thermoplaste, die von Polyethersulfon und Polysulfon abgeleitet sind.
Diese Produktlinie wird in hochbelasteten technischen Teilen verwendet, die eine hohe Dimensionsstabilität und gute mechanische Eigenschaften in einem Temperaturbereich von -58 ° F bis 428 ° F aufweisen müssen.
Das Ultraschall-PES und -Netzteil wurde für den Einsatz in einer Vielzahl anspruchsvoller Anwendungen in Marktsektoren wie Automobil, Membranen, Lebensmittelservice und Sanitär entwickelt. Eine Vielzahl typischer Anwendungen sind: Scheinwerferreflektoren, Milchmembranen, Sensoren, Lebensmittelschalen, Wasseraufbereitungsmembranen, Verteiler. Es ist ideal für hydrophile, proteinarme Bindungen, PES-Membranfilter, Sterilisation von Gewebekulturmedien, Anwendungen in Life Science- und Mikrobiologie-Flüssigkeiten sowie klinische und allgemeine Filtration.
ROST; Es ist hauptsächlich eine chemische Struktur, die Polyethersulfon (PES) sehr ähnlich ist.
PVDF (PolyVinyliDene Fluoride)
Es wird für seine Haltbarkeit, Stabilität und vielfältigen technischen Vorteile geschätzt. Wenn Sie beispielsweise ein Polymer benötigen, das gegenüber rauen thermischen, chemischen oder ultravioletten Bedingungen beständig ist, bietet poröses PVDF eine überlegene Stabilität, ähnlich der Leistung von Fluorpolymeren in diesen Umgebungen. Es hat eine hohe chemische Korrosionsbeständigkeit mit geringem Gewicht und Wärmeleitfähigkeit.
Es ist beständig gegen die meisten Chemikalien und Lösungsmittel. Es wird nicht durch längere Exposition gegenüber ultravioletter Strahlung beeinträchtigt.
PEK (PolyEtherKetone)
PEEK (PolyEtherEtherKetone)

Es ist ein Harz, das für Teilkristall-, Drahtbeschichtungs- und Verbundwerkstoffe geeignet ist.
Es ist ein zäher, starrer Kunststoff bei Raumtemperatur, der lange Zeit sehr abriebfest ist. In die aquatische Umwelt
und ist lösungsmittelbeständig. Polyketone in der Klasse der aromatischen Polyether
Sie werden als Hochleistungskunststoffe verwendet.
Beide Polymere (PEK-PEEK), die auf dem Markt weit verbreitet sind, weisen eine hervorragende Festigkeit und Wärme auf
Aufgrund seiner Beständigkeit gegen Chemikalien ist es in der Flugzeug- und Automobilindustrie weit verbreitet.
benutzt. Es handelt sich um Polymere, die kontinuierlich im Bereich von 240 ° C bis 280 ° C eingesetzt werden können.
Polyetheretherketon, das dort eingesetzt wird, wo überlegene chemische und physikalische Eigenschaften erforderlich sind
Es ist ein thermoplastisches Hochleistungspolymer.
Polyetheretherketon (PEEK) ist ein farbloses organisches thermoplastisches Polymer aus der Polyetherketonfamilie (PAEK), das in technischen Anwendungen verwendet wird.
PEEK ist ein teilkristalliner Thermoplast mit hervorragenden mechanischen und chemischen Beständigkeitseigenschaften, der bei hohen Temperaturen gehalten wird. Die zum Formen des PEEK verwendeten Verarbeitungsbedingungen können die Kristallinität und damit die mechanischen Eigenschaften beeinflussen. Der Elastizitätsmodul beträgt 3,6 GPa und die Zugfestigkeit beträgt 90 bis 100 MPa. PEEK hat eine Glasübergangstemperatur von ca. 143 ° C und schmilzt bei ca. 343 ° C. Einige Typen haben eine nützliche Arbeitstemperatur von bis zu 250 ° C. Es ist sehr beständig gegen thermischen Abbau und Angriff durch organische und wässrige Medien. Es wird bei hohen Temperaturen von Halogenen und starken Säuren sowie einigen halogenierten Verbindungen und aliphatischen Kohlenwasserstoffen angegriffen. Vollständig löslich in konzentrierter Schwefelsäure bei Raumtemperatur.
Aufgrund seiner Robustheit werden mit PEEK Produkte hergestellt, die in anspruchsvollen Anwendungen eingesetzt werden, z. B. Lager, Kolbenteile, Pumpen, HPLC-Säulen, Kompressorplattenventile und Kabelisolierung. Es ist einer der wenigen Kunststoffe, die mit Ultrahochvakuumanwendungen kompatibel sind. Es ist weit verbreitet in der Luft- und Raumfahrt, in der Automobilindustrie und in der chemischen Prozessindustrie.
Betrachtet man die physikalischen und chemischen Eigenschaften von PEEK, so zeigt sich, dass es teilkristallin ist und dank der darin enthaltenen amorphen und kristallinen Bereiche eine hohe Schmelztemperatur von 343 ° C aufweist. Die Glasübergangstemperatur beträgt 143 ° C und liegt weit über der Körpertemperatur von 37 ° C, die für In-vitro- und In-vivo-Anwendungen erforderlich ist. Dadurch können klinische Studien mit aus PEEK hergestellten Biomaterialien problemlos fortgesetzt werden.
Netzteil (PolySUlfone)

Zug-, Druck- und Reibungsfestigkeiten sind sehr hoch. Dieses Material, das gegen Säure-, Basen- und Salzlösungen beständig ist, wird durch Waschmittel, Öl und Alkohol nicht beeinträchtigt. Es wird in medizinischen Geräten, Geräten zur Lebensmittelherstellung, elektrischen Anschlüssen, Sicherungs- und Schaltergehäusen in der Automobilindustrie, korrosionsbeständigen Rohren, Pumpen, Kamera- und Uhrenkörpern, Batterieisolationsplatten, Raumfahrt- und Luftfahrtindustrie verwendet.
PTFE (PolyTetraFloroEthilen)

Es ist ein vielseitiges Polymer, das in einer Vielzahl von medizinischen, elektronischen, automobilen und hochtechnologischen Anwendungen eingesetzt wird. Dies ermöglicht das Arbeiten in Umgebungen mit hohen Temperaturen (260 ° C kontinuierlich), ohne auf die meisten Chemikalien und Medien zu reagieren. Kompatibel mit Dampf- und Ethylenoxidsterilisation.
UHMWPE (ultrahochmolekulares Poliethylen)

Es ist eine Art von Polyethylen mit einer Dichte zwischen 0,930 und 0,935 g / cm³. Hohes Molekulargewicht bedeutet, dass die Polymerketten fest in der Kristallstruktur angeordnet oder verpackt sind. UHMWPE ist sehr hart und hat die höchste Schlagfestigkeit unter thermoplastischen Materialien. In der Verteidigungsindustrie wird es in vielen Zweigen der Industrie eingesetzt, von der Herstellung von Verbundpanzerplatten bis hin zu Allzweckmaschinen, und seine Verwendung nimmt von Tag zu Tag zu. Polyethylen mit ultrahohem Molekulargewicht (UHMW-PE) ist ein thermoplastisches Polyethylen mit einer Molmasse im Bereich von 2 bis 6 Millionen amu. Es ist ein sehr hartes Material mit der höchsten Schlagfestigkeit aller derzeit hergestellten thermoplastischen Materialien. UHMW-PE hat einen niedrigen Reibungskoeffizienten, eine hohe Verschleißfestigkeit und ist extrem
Es hat eine hohe chemische Beständigkeit.