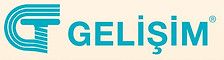


Hidrokarbonlar
Hidrojen ve karbon olmak üzere iki elementten oluşan organik bir bileşiktir. Petrol bileşiminin büyük bir kısmı değişen uzunluklardaki hidrokarbonlardan oluşur.
En küçük hidrokarbon metan, tek bir karbon atomu ve dört hidrojen atomundan oluşur. Bununla birlikte, hidrokarbonlar, zincirler, daireler ve diğer karmaşık şekiller dahil olmak üzere birçok yönden birbirine bağlanmış yüzlerce veya binlerce bireysel atomdan oluşabilir.
Hidrokarbonların özelliklerini sınıflandırmak için birkaç temel türe ayrılırlar.
Alkanlar: Bunlar doymuş hidrokarbonlar olarak adlandırılır. Yani sadece tüm karbon atomları arasında tek bağlar içerirler. Alkanlar, petrol yakıtlarının temelidir ve doğrusal ve dallı formlarda bulunurlar.
Doymamış Hidrokarbonlar: Karbon atomları arasında bir veya daha fazla çift bağa sahip olan hidrokarbonlara alken denir.
Sikloalkanlar: Bir veya daha fazla halka yapısı içeren herhangi bir hidrokarbon.
Aromatik Hidrokarbonlar: Areneler olarak da adlandırılan aromatik hidrokarbonlar, karbon atomlarının birbirini izleyen çift ve tek bağlarla bağlandığı benzersiz bir karbon molekülleri sınıfıdır. Bu molekül sınıfı, karbon atomları arasındaki bağların tek ve çift bağlar arasında bir ara bağ olduğu özel halka yapılarına sahiptir.
Bu sınıftaki moleküller, endüstriyel çözücü «benzen» içerir.
Benzen (C6H6): Diğer hidrokarbonlar gibi benzen de petrolün doğal bir bileşenidir. Oda sıcaklığında renksiz, yanıcı, tatlı kokulu bir sıvıdır ve yüksek oktan sayısına sahip olduğu için çoğu benzin karışımının bir bileşenidir.
Benzen de oldukça kanserojendir ve kemik iliği yetmezliği ve kemik kanserine neden olduğu iyi bilinmektedir. Elbette, “hoş aroması” nedeniyle tıraş sonrası ve diğer kozmetiklerde bir katkı maddesi olarak kullanıldığında kanserojenliği iyi bilinmemektedir.
En büyük benzen kullanımı (% 50), stiren ve polistren plastiklerinin ürünüdür. Ayrıca Naylon üretiminde önemli olan sikloheksan olarak bilinen bir moleküle dönüştürülür. Siklohekzan üretmek için benzenin yaklaşık% 15'i kullanılır. Böcek ilaçlarından kauçuğa kadar her şeyde daha küçük miktarlar kullanılır.
Benzen yapısı iki şekilde çizilebilir. İlkinde, çift bağ karakteri açıkça çizilir. Kısa elli versiyonda, yapıyı göstermek için halkanın içine bir daire çizilir. Benzen içindeki her bir karbon atomuna bağlı tek bir hidrojen vardır.
Aşağıdaki I. ve II. çizimleri eştir. Pratikte III. çizim kullanılır.
Benzen, renksiz, alevlenebilen, kaynama noktası 80,1 °C, erime noktası 5,5 °C olan bir sıvıdır.
Binükleer Aromatik Hidrokarbonlar: Molekülünde iki benzen halkası içeren bileşiklerdir.
Hidrokarbonlar
Hidrojen ve karbon olmak üzere iki elementten oluşan organik bir bileşiktir. Petrol bileşiminin büyük bir kısmı değişen uzunluklardaki hidrokarbonlardan oluşur.
En küçük hidrokarbon metan, tek bir karbon atomu ve dört hidrojen atomundan oluşur. Bununla birlikte, hidrokarbonlar, zincirler, daireler ve diğer karmaşık şekiller dahil olmak üzere birçok yönden birbirine bağlanmış yüzlerce veya binlerce bireysel atomdan oluşabilir.
Hidrokarbonların özelliklerini sınıflandırmak için birkaç temel türe ayrılırlar.
Alkanlar: Bunlar doymuş hidrokarbonlar olarak adlandırılır. Yani sadece tüm karbon atomları arasında tek bağlar içerirler. Alkanlar, petrol yakıtlarının temelidir ve doğrusal ve dallı formlarda bulunurlar.
Doymamış Hidrokarbonlar: Karbon atomları arasında bir veya daha fazla çift bağa sahip olan hidrokarbonlara alken denir.
Sikloalkanlar: Bir veya daha fazla halka yapısı içeren herhangi bir hidrokarbon.
Aromatik Hidrokarbonlar: Areneler olarak da adlandırılan aromatik hidrokarbonlar, karbon atomlarının birbirini izleyen çift ve tek bağlarla bağlandığı benzersiz bir karbon molekülleri sınıfıdır. Bu molekül sınıfı, karbon atomları arasındaki bağların tek ve çift bağlar arasında bir ara bağ olduğu özel halka yapılarına sahiptir.
Bu sınıftaki moleküller, endüstriyel çözücü «benzen» içerir.
Benzen (C6H6): Diğer hidrokarbonlar gibi benzen de petrolün doğal bir bileşenidir. Oda sıcaklığında renksiz, yanıcı, tatlı kokulu bir sıvıdır ve yüksek oktan sayısına sahip olduğu için çoğu benzin karışımının bir bileşenidir.
Benzen de oldukça kanserojendir ve kemik iliği yetmezliği ve kemik kanserine neden olduğu iyi bilinmektedir. Elbette, “hoş aroması” nedeniyle tıraş sonrası ve diğer kozmetiklerde bir katkı maddesi olarak kullanıldığında kanserojenliği iyi bilinmemektedir.
En büyük benzen kullanımı (% 50), stiren ve polistren plastiklerinin ürünüdür. Ayrıca Naylon üretiminde önemli olan sikloheksan olarak bilinen bir moleküle dönüştürülür. Siklohekzan üretmek için benzenin yaklaşık% 15'i kullanılır. Böcek ilaçlarından kauçuğa kadar her şeyde daha küçük miktarlar kullanılır.
Benzen yapısı iki şekilde çizilebilir. İlkinde, çift bağ karakteri açıkça çizilir. Kısa elli versiyonda, yapıyı göstermek için halkanın içine bir daire çizilir. Benzen içindeki her bir karbon atomuna bağlı tek bir hidrojen vardır.
Aşağıdaki I. ve II. çizimleri eştir. Pratikte III. çizim kullanılır.
Benzen, renksiz, alevlenebilen, kaynama noktası 80,1 °C, erime noktası 5,5 °C olan bir sıvıdır.
Binükleer Aromatik Hidrokarbonlar: Molekülünde iki benzen halkası içeren bileşiklerdir.
Hakkında
Kyäni, faydalı bileşenlerden oluşan besin takviyesi ürünlerini; benzersiz iş fırsatıyla birlikte dünya çapında 50'den fazla ülkeye ulaştırmaktadır. İdeal sağlığımızı korumak için günlük olarak Kyäni ürünlerini kullanırız, bu ürünleri başkalarıyla paylaşırız, işimizi inşa etmek ve sürdürmek için neredeyse her gün belirli bir saatimizi işe adarız ve başkalarını da Kyäni fırsatına dahil ederek veya Potato Pak ve Caring Hands programlarına katkı sağlayarak başarımızı başkalarıyla paylaşırız.
Hakkında
Kyäni, faydalı bileşenlerden oluşan besin takviyesi ürünlerini; benzersiz iş fırsatıyla birlikte dünya çapında 50'den fazla ülkeye ulaştırmaktadır. İdeal sağlığımızı korumak için günlük olarak Kyäni ürünlerini kullanırız, bu ürünleri başkalarıyla paylaşırız, işimizi inşa etmek ve sürdürmek için neredeyse her gün belirli bir saatimizi işe adarız ve başkalarını da Kyäni fırsatına dahil ederek veya Potato Pak ve Caring Hands programlarına katkı sağlayarak başarımızı başkalarıyla paylaşırız.
Sayfa Yapım Aşamasındadır.
Sayfa Yapım Aşamasındadır.
Schulungs- / Wissens- / Lösungsplattform
Einführung in Polymeradditive
Warum Additive zu Polymeren hinzufügen:
Zunächst sollte festgestellt werden, dass das Polymer in seiner Rohform sehr schwach ist und nicht den Zweck erfüllt, wenn eine Stabilisierung nicht durch Zugabe von Additiven zu mehr als 95% der Polymere erreicht wird. Zum Beispiel; Reine Polyolefine wie PE und PP oxidieren sehr schnell. Aus diesem Grund werden sie durch Hinzufügen externer Additive funktionsfähig gemacht. Reines PVC kann ohne Hochtemperaturabbau nicht extrudiert und geformt werden und weist sehr schlechte mechanische Werte auf, die nach dem Prozess fast keinen Zweck erfüllen.
Für den grundlegendsten Zweck werden Additive verwendet, um die Verarbeitungsschwierigkeiten von Polymeren zu beseitigen. Es bewahrt seine Leistungswerte und schützt das Polymer. Unerwünschte Umwelteinflüsse werden mit Additiven vermieden.
Welches Additiv zu welchem Polymer, in welchem Verhältnis:
Die Art des zu verwendenden Additivs hängt von mehreren Parametern ab. Zunächst sollte die chemische Zusammensetzung des Polymers mit den Additiven vergleichbar sein. Es sollte nicht aktiv mit der Polymerstruktur reagieren, um seine Polymereigenschaften nicht zu beeinträchtigen. Es sollte genau bekannt sein, mit welchem Verfahren das Polymer verarbeitet wird. Wie viel Temperatur es im thermischen Prozess ausgesetzt sein wird, sollte bestimmt werden. Andernfalls kann das Problem der Verschlechterung des Additivs auftreten. Oder wenn die Temperaturen für das Polymer geeignet sind, aber nicht für das Additiv geeignet sind, sollte vorhergesagt werden, dass das Additiv bei hoher Temperatur brennen kann und wenn die Temperatur niedrig ist, das Additiv am Ende des Additivs möglicherweise nicht wirkt Prozess.
Polymere ; Sie verschlechtern sich, wenn sie Hitze, Licht, Schnitt und Feuchtigkeit ausgesetzt werden. Der endgültige Punkt, an dem die Produktion angestrebt wird, muss festgelegt werden. Unabhängig davon, welcher Faktor zur Gewährleistung der Stabilisierung vermieden werden soll, sollte festgelegt werden, dass der hinzuzufügende Beitrag für diese Richtung gilt. (Zum Beispiel wäre es bei der Herstellung eines Kunststoffprodukts, das in Wasser läuft, ein wenig sinnlos, dem Polymer ein flammhemmendes Additiv zuzusetzen).
In Polyolefin (PE, PP), Polystyrol (PS) (PVC), bei denen es sich um normale Kettenwachstumspolymere handelt, sind Kohlenstoff-Chlor- und Kohlenstoff-Wasserstoff-Bindungen sehr anfällig für eine Verschlechterung durch Umweltfaktoren. Daher muss es vor Oxidation, Licht, UV-Strahlung und thermischer Zersetzung geschützt werden.
Es gibt jedoch keine Bindungen, die zum Abbau in Polymeren mit allmählichem Wachstum geeignet sind. Sie hydrolysieren sehr schnell als Ester-, Amid- und Carbonatgruppen. Polymere werden während der Verarbeitung in Gegenwart von Feuchtigkeit molekular abgebaut.
Typischerweise enthält eine Polymerformulierung mehr als ein Additiv. Es; Es wird für eine optimale Formulierungssoftware mit der Wechselwirkung zwischen Additiven angewendet. Und diese Beiträge in fast kleinen Anteilen arbeiten mit einer Opferlogik. Sie beginnen, das Polymer zu schützen, hören ganz auf, sich selbst zu schützen und zerstören sie.
Wenn diesen an das Polymer gebundenen Additiven Aufmerksamkeit geschenkt wird, wird bemerkt, dass sie vollständig nach Umweltfaktoren klassifiziert sind. wie Antioxidantien, antibakterielle Mittel, Wärmestabilisatoren, Lichtstabilisatoren, UV-Brecher.
Solange das Produkt seinen Zweck erfüllt, können einem Basenträgerpolymer viele Additive zugesetzt werden, wenn die Prozessbedingungen erfüllt sind. Es sollte jedoch nicht aus dem Speicher genommen werden. Unabhängig davon, wie klein die zuzusetzenden Additivverhältnisse sind, erhöhen sie die Produktionskosten, da ihre Stückkosten viel höher sind als die von Polymeren. Aus diesem Grund sollten auch die Kosten der bevorzugten Additive berücksichtigt werden.
Die Verwendungsrate von Additiven in der Polymerkette ist grundsätzlich direkt proportional zu dem darin enthaltenen Wirkstoffverhältnis. Der Prozentsatz der Verwendung eines Additivs mit einem hohen Prozentsatz an Wirkstoffen sollte niedriger sein als der Prozentsatz der Verwendung eines Additivs, das dem gleichen Zweck dient, aber einen geringen Prozentsatz an Wirkstoffen aufweist. Die Verwendung hoher Mengen an Zusatzstoffen ist gleichbedeutend mit dem Ausdruck "Augenbrauen machen" und "Auge machen". Eine zu hohe Verwendung des Additivs kann die Kosten erhöhen und das Polymer selbst zerstören.
Flüssige Additive sind schwer zu verwenden. Wenn beispielsweise Polymerpulver verwendet wird (wie z. B. gemahlenes PE), kann die Zugabe von flüssigen Additiven aufgrund der homogenen Verteilung und Dispersion beim Mischen und Kneten zu Schwierigkeiten führen.
Verbindung
Die Herstellung von Rohstoffen durch Zugabe verschiedener Zusätze zu den Faktoren wie Hitzebeständigkeit, Schlagzähigkeit, Farbe und Härte des Hauptrohstoffs wird als Compound bezeichnet.
Dieser Rohstoff ist kein reines Material mehr, sondern ein mit Additiven verstärkter Verbundwerkstoff und wird direkt als Rohstoff verwendet. Masterbatch bestimmt Farbe, physikalische Eigenschaften und Kostenmerkmale des Hauptrohstoffs. Zur Entwicklung werden Pigment, Additive und Füllstoffe gemischt und dem Kunden in Granulatform präsentiert. Compound und Masterbatch ähneln sich zwar in der Herstellung, unterscheiden sich jedoch in der Anwendung. Während das Compound zu 100 % als Rohstoff verwendet wird, werden Masterbatches nicht direkt als Rohstoff verwendet. Es wird durch Mischen mit dem Rohstoff in bestimmten Anteilen verwendet.
Compound und Masterbatch ähneln sich zwar in den Herstellungsverfahren, unterscheiden sich jedoch in der Anwendung. Verbindung; Es wird Compound genannt, um einen Rohstoff mit den vom Kunden gewünschten Eigenschaften zu erzeugen, indem verschiedene Zusätze zu den Faktoren wie Wärmebeständigkeit, Schlagzähigkeit und Härte des Hauptrohstoffs hinzugefügt werden. Nach dem Compoundieren ist der an den Kunden gelieferte Rohstoff kein reines Material mehr, sondern ein Verbundwerkstoff, der durch Additive verbesserte Eigenschaften aufweist. Der Kunde kauft dieses Material beim Compound-Hersteller und verwendet es als Rohstoff.
Masterbatch; Farbe, physikalische Eigenschaften und Kostenmerkmale des Hauptrohstoffs Zur Entwicklung werden Pigment, Additive und Füllstoffe gemischt und dem Kunden in Granulatform präsentiert. Im Gegensatz zu Compound verwendet der Kunde es nicht als Rohstoff, sondern mischt es in bestimmten Anteilen dem Rohstoff bei und versucht, seine Farb-, Kosten- und physikalischen Mängel zu beseitigen.
In seiner einfachsten Form ist ein Compound / Masterbatch-Rezept so.
Bei %A+%B+%C+%D=100% gilt die Formel sowohl für Compound als auch für Masterbatch.
Aber wie werden sie voneinander getrennt?
Die Antwort darauf liegt im Anwendungsbereich. Compound und Masterbatch sind bis in den Anwendungsbereich (endgültiger Prozess) zwei synonyme Begriffe. Genauso verhält es sich mit den Herstellungsmethoden.
Mit anderen Worten, diese vom Hersteller hergestellte Mischung wird als 100 % direkt in der Extrusionsmaschine oder als Compound definiert, wenn sie als Trägerrohstoff im größten Anteil in der zu verwendenden Rezeptur verwendet wird, und als Masterbatch wenn es in viel kleineren Anteilen verwendet wird (0,5%, 5%, 20% usw.).
Gelangt das Compound direkt beim Endverbraucher in die Extrusion, welches die Haupttrennstelle ist, geht es als „Compound“ weiter.
Wenn den Rohstoffen jedoch in bestimmten Mengen andere Mischungen oder Trägerstoffe zugesetzt werden, ändert es nun seine Identität und entweder Farbe oder Additiv wird zu "Masterbatch". Eine andere einfache Definition kann als Farb-Masterbatch erfolgen, wenn der Farbstoff in der Rezeptur enthalten ist, und als Additiv-Masterbatch, wenn kein Farbstoff vorhanden ist (dh C=0).
Compound-Produktion; Es wird hergestellt, um die physikalischen Eigenschaften des Kunststoffs mit unzureichenden physikalischen Eigenschaften zu verbessern. Auf Trägerrohstoff geladen Sie erfolgt durch Zugabe von Materialien wie Füllstoffen, Pigmenten, Kohlefasern.
Bei der Verarbeitung von polymeren Werkstoffen und nicht-polymeren Werkstoffen (meist Zusatzstoffe wie Calcit, Talkum, Sägemehl etc.) treten verschiedene Probleme auf. Diese; sie äußert sich vielmehr in der Fließfähigkeit des Materials in der Maschine, der ungleichmäßigen Verteilung der Materialien ineinander, der Nichtverklebung der Mischmaterialien, der Bildung einer Blasenstruktur durch die Feuchtigkeit im Additiv oder Rohmaterial.
Bei der Extrusion erzeugt es aufgrund der Unterschiede zwischen den Partikelgrößen und ihrer nicht schmelzenden Struktur Lufträume. So wie es ist, sind diese Hohlräume mit Polymergas gefüllt und Probleme wie Blasen, nicht schmelzende Partikel, Oberflächenrauhigkeit, Orangenhaut-Erscheinung werden vom Endverbraucher angetroffen. Bei feinen Präzisionsformteilen führt die fehlende Füllung der Form zum Auftreten von Fehlteilen und zum Zusammenfallen.
Abhängig von der Mikrometergröße des Füllmaterials und dem Rezepturverhältnis kann es während des Produktionsprozesses häufiger zu Filterverstopfungen kommen. Das Doppelziehen erfolgt einmal im Compound-Produktionsprozess und einmal im nachfolgenden Produktionsprozess.
Allerdings sind die Extrusionslinie in der Compoundherstellung und die Extrusionslinien und Prozesse im Spritzgussverfahren nicht identisch.
Obwohl das Material während des Einspritzvorgangs zum zweiten Mal extrudiert wird, ist diese zweite Ziehzeit aufgrund der Schneckenlänge und der Zykluszeit kurz. Aus diesem Grund wird bei der Herstellung von Compounds, nachdem das Material einmal gezogen wurde, es ein zweites Mal im Extruder gezogen und doppelt gezogen, was die Gasansammlung im Material und das Problem der ungeschmolzenen Partikel sichtbar verbessert.
Die Verbundstruktur wird viel homogener. Im Endbenutzer Bei dem zum dritten Mal extrudierten Material werden die oben genannten physikalischen Probleme nicht mehr beobachtet.
Masterbatches Während es in allen Kunststoffprozessen problemlos seinen Platz finden kann, wird es meist als Compound in Spritzguss- und anderen "Form"-Prozessen verwendet.
Trägerpolymer:
Compound-Rohstoff wird nach dem Rohstoff, dem das Compound und das Masterbatch zugesetzt werden, und dem Ort, an dem das Endprodukt verwendet wird, bestimmt. Die Compoundherstellung enthält Materialien wie Füllstoffe, Pigmente, Kohlefasern, die dem Kunststoff in großen Anteilen zugesetzt werden, um die physikalischen Eigenschaften des Kunststoffs zu verbessern, dessen physikalische Eigenschaften nicht ausreichen.
Bei der Verarbeitung von Polymermaterial und Nicht-Polymermaterial treten verschiedene Probleme auf. Diese; sie äußert sich vielmehr in der Fließfähigkeit des Materials in der Maschine, der ungleichmäßigen Verteilung der Materialien ineinander, der Nichtverklebung der Mischmaterialien, der Bildung einer Blasenstruktur durch die Feuchtigkeit im Additiv oder Rohmaterial.

Farb-Masterbatches
Kunststoffprodukte hatten anfangs nicht die Farbe und die gewünschten Eigenschaften. Diese Eigenschaften werden durch die Additive bereitgestellt, die in die Verbindung aufgenommen werden sollen, nachdem die Hauptlagerstruktur bestimmt wurde. Diese werden als Masterbatches definiert. Obwohl das Wort Masterbatch "Hauptmischung" bedeutet, ist es ein Begriff, der allgemein verwendet wird, um "Farbe in Form von Granulat zu bedeuten, die dem Kunststoffrohstoff in der Schmelz- und Formungsphase zugesetzt wird". Es ist ein Farbstoff, in dem organische oder anorganische Pigmente oder Additive in einem hochkonzentrierten Polymermaterial (Thermoplast, Kautschuk oder Elastomer) homogen gemischt werden. Es gibt zwei Arten von Masterbatches: Farbmasterbatches und additive Masterbatches. In der integrierten Definition wird der Ausdruck Masterbatch jedoch hauptsächlich für "Farbe" verwendet. Additive Masterbatches werden auch direkt als «additiv» ausgesprochen. Farbmasterbatches werden verwendet, um die gewünschte Farbe und Wirkung (Fluoreszenz, Vergoldung, Perlglanz, Opazität usw.) auf das Produkt zu erzielen. Grundsätzlich besteht der Hauptvorteil von Farbmasterbatches darin, die praktische Verwendung der Pigmente zu gewährleisten, die für die Produktfärbung benötigt werden. Mit anderen Worten, es ist das Pigment, das das Produkt tatsächlich färbt.
Farbmasterbatches bestehen aus drei Grundkomponenten. Trägerrohstoff, Farbpigment und Dispergiermittel zur Unterstützung des Prozesses. Dispergiermittel sind meist Prozessverbesserer oder Additive oder Katalysatoren wie Homogenität, Leitfähigkeit, UV-Beständigkeit.
Farbmasterbatches; Sie sind in drei Hauptüberschriften wie schwarz, weiß und Farbe. Und die gewünschte Farbe des Produkts wird mit den verschiedenen Kombinationen dieser drei Köpfe in einer unendlichen Variation erreicht. Masterbatches werden im Allgemeinen auf der Hauptverbindung mit Raten von 3% oder weniger verarbeitet, können jedoch oberhalb dieser Rate verwendet werden, um die gewünschte Qualität zu erzielen. Der grundlegendste Punkt, der bei Masterbatches berücksichtigt werden muss; Der Masterbatch-Trägerrohstoff ist mit dem Hauptverbundrohstoff kompatibel.
Darüber hinaus ist zu beachten, dass die Oberfläche des Produkts strukturiert und rau mit Mustermarkierungen ist und die Dicke die Wirkung der verwendeten Farbmasterbatches beeinflusst. In neuen Studien zur Bestimmung der richtigen Präferenz und Verwendungsrate sollte vor der Lieferung des Farbmasterbatches die Probe des Produkts an den Lieferanten geliefert werden, und es wäre angebracht, eine Probe von vorne zu entnehmen.
Color Masterbatch ist ein fester oder flüssiger Zusatzstoff, der zum Färben von Kunststoffen verwendet wird. Es ist eine Mischung aus einem eingekapselten Pigment oder Additiv, das während einer Wärmebehandlung zu einem Trägerharz konzentriert wird, das dann abgekühlt und in eine körnige Form geschnitten wird. Mit Masterbatches können Hersteller das Rohpolymer während des Kunststoffherstellungsprozesses wirtschaftlich färben.
Der Masterbatch-Produktionsprozess ist in zwei Teile unterteilt: "Mono" und "Maßgeschneidert".
Mono: Bei der Herstellung werden Farben mit der Haupt- oder der höchsten Verbrauchsrate verwendet.
Maßgeschneidert: Es ist die Arbeit, die durch Abgleichen der erhaltenen Monofarben in verschiedenen Kombinationen oder mit den gewünschten Farben erhalten wird.
Die zu berücksichtigenden Punkte können wie folgt aufgelistet werden.
- Füllstoffe, die speziell in der PVC-Herstellung verwendet werden, verändern den Farbton.
- Der Unterschied in den Kabelproduktionsmustern wirkt sich auf die Farbe der Farbe aus.
- Wenn die Maschinen nicht gut gereinigt werden, führt dies zu Farbentfernung und Narbenbildung.Das Anhalten und Laufen der Maschinen kann zu Kontakt mit Material führen, das zuvor in einem anderen Bereich als dem Strömungsweg vorhanden war. Dies tritt als Trace-Problem im Produkt auf. In Fällen, in denen ein Verdacht auf Maschinenverunreinigung besteht, sollten einige Drucke nur mit dem Rohmaterial erstellt und die Sauberkeit der Durchflussleitung in jeder Phase überprüft werden.
- Die ersten Ausdrucke sollten überprüft werden, wenn die Maschinen länger als 10 Minuten angehalten und wieder eingeschaltet werden. Da das Material lange Zeit Hitze ausgesetzt war, kann es zu Verbrennungen kommen.
- Insbesondere bei einer Änderung des für die Filmherstellung verwendeten Rohmaterials und bei Änderungen im Mikrometerbereich muss eine Versuchsproduktion durchgeführt werden.
- Wenn bei Temperaturen gearbeitet wird, die unter dem Schmelzpunkt des verwendeten Trägers liegen, tritt im Endprodukt kein Schmelzen auf.
- Feuchtigkeitsabsorbierende Rohstoffe müssen vor der Produktion konditioniert werden.
Pigmente
Einige Gesteine, Böden und Mineralien erhalten nach einfachen Verfahren wie Waschen und Mahlen die Eigenschaft, als "mineralisches Pigment" verwendet zu werden. Die angestrebten Eigenschaften sind geeignete Farbe, Deckvermögen, Ölaufnahmevermögen, kein Gehalt an wasserlöslichen Salzen. Es ist auch wichtig, dass der Färbeschmutz Eigenschaften wie Feuchtigkeitsgehalt, Mindestgehalt an Fe2O3, Lichtbeständigkeit und Preis hat. Durch Rösten anorganischer Pigmente ist es möglich, die Farben abzudunkeln und zu stabilisieren. Bei natürlichen Anstricherden ist das färbende Element meist das Eisenelement in den Mineralien.
Mineralien wie Hämatit, Gotit, Limonit werden durch Verwitterung erdig und bilden gelbe, rote und braune Farbstoffe wie Okr und Bernstein. Die Quelle für grün gefärbte Erdfarbstoffe sind Mineralien wie Seladonit, Garnierit und Glaukonit. Vivianit und Azurit werden für blaue Farbstoffe verwendet, während Pyrolusit, Graphit und Magnetit für schwarze Farbstoffe verwendet werden. Kaolin, Schwerspat, Kreide und Anhydrit werden zur Herstellung weißer Farben verwendet. Grautöne werden durch Zugabe von gemahlenem Schiefer erreicht.Mineralfarben werden verwendet, um Putz, Mörtel, Zement, Gummi, Linoleum (Polster) und ähnlichen Materialien Farbe und Dichte zu verleihen.
Eine sehr kostbare Farbe namens Bolus, bestehend aus einer Mischung aus Eisenhydroxid und Montmorillonit, wurde im Mittelalter aus Anatolien entnommen und in Paris gemahlen und über Jahrhunderte als vergoldete rote Auskleidung von Holzskulpturen verwendet. Auch hier wurde ein roter Farbstoff namens Snopia, der aus Anatolien mitgebracht wurde, in Rembrands Gemälden verwendet und war sehr begehrt. Bolus wird immer noch in der Aquarellherstellung durch Mischen mit Gips und Kalk verwendet.
Pigmente und Farbstoffe verleihen Kunststoffen, Textilien und vielen anderen Materialien Farbe, Deckkraft und Schimmer.
Farbstoffe sind organisch lösliche Stoffe, die sich chemisch mit dem Substrat (Bestandteil oder Zersetzungsstoff) verbinden.
Pigmente sind organische oder anorganische teilchenförmige Feststoffe, die im Allgemeinen unlöslich sind und nicht mit dem Substrat reagieren.
Pigmente sind ein Material, das durch wellenlängenselektive Absorption die Farbe von reflektiertem oder transmittiertem Licht ändert. Mit anderen Worten, es ist eine Substanz, die eine bestimmte Farbe aufweist, weil sie Licht bestimmter Wellenlängen selektiv absorbiert. Der Hauptzweck der Verwendung von Pigmenten besteht darin, Materialien, ob Textilien oder Farben, Farbe zu verleihen. Manche Leute denken oft, dass Pigmente und Farbstoffe gleich sind, aber sie sind ziemlich unterschiedlich. Der größte Unterschied zwischen beiden ist ihre Auflösung.
Ein Farbstoff kann sich selbst in einer Flüssigkeit auflösen, während Pigmente mit Hilfe eines Bindemittels in einer Flüssigkeit gelöst werden können. Farbstoffe werden hauptsächlich in der Textil- und Papierindustrie verwendet, während Pigmente in Industrien wie Farbstoffen, Tinten, Kosmetik und Kunststoffen verwendet werden.
Abhängig von den Formulierungsverfahren können Pigmente in zwei Arten unterteilt werden:
organische Pigmente
Anorganische Pigmente.
Abgesehen von diesen beiden grundlegenden Unterscheidungen Es gibt zwei weitere Arten von Pigmenten:
metallische Pigmente
Sie sind Industriepigmente.
Metallische Pigmente :
Wie der Name schon sagt, umfassen Metallpigmente Metallpigmente wie Zink- und Aluminiumpigmente.
Industriepigmente :
Sie sind Pigmente, die in industriellen Anwendungen weit verbreitet sind und organische, anorganische und metallische Pigmente umfassen. In der Industrie gibt es drei Klassen von Pigmenten: Absorptionspigmente (verwendet in Aquarellfarben), Metalleffektpigmente (zur Erzeugung von Oberflächenglanz) und Perlglanzpigmente.
Anorganische Pigmente:
Wie der Name vermuten lässt, ist diese Art von Pigment die entgegengesetzte Art von organischem Pigment. Diese Pigmente werden auch als "synthetische Pigmente" bezeichnet. Sie werden in Laboren formuliert und bieten Herstellern anorganischer Pigmente einen großen Kontrollspielraum. Anorganische Pigmente werden durch relativ einfache chemische Prozesse wie Oxidation hergestellt.
Anorganische Pigmentlieferanten liefern solche Pigmente hauptsächlich an die Farben-, Kunststoff-, Kunstfaser- und Tintenindustrie. In Anwendungen, bei denen leuchtende Farben erforderlich sind, werden organische Pigmente verwendet, da sie eine hohe Farbstärke bieten. Anorganische Pigmente umfassen weiße undurchsichtige Pigmente, die üblicherweise verwendet werden, um andere Farben aufzuhellen sowie Opazität bereitzustellen.
Organische (natürliche) Pigmente:
Solche Pigmente kommen in der Natur vor und werden seit Jahrhunderten verwendet. Ihre chemische Struktur ist recht einfach. Sie werden als organisch bezeichnet, weil sie Mineralien und Metalle enthalten, die ihnen ihre Farbe verleihen. Organische Pigmenthersteller produzieren sie durch einen einfachen Prozess des Waschens, Trocknens, Pulverisierens und Kombinierens zu einer Formulierung.
Im Vergleich zu anorganischen Pigmenten ist diese Verwendung dieser Pigmente seltener und daher gibt es eine begrenzte Anzahl von organischen Pigmentanbietern. Diese Pigmente werden verwendet, wenn die erforderliche Farbintensität nicht zu hoch ist.
Organische Pigmente gehören zu den ältesten vom Menschen verwendeten Pigmenten. Es hat sich gezeigt, dass es zum ersten Mal bei der Vorbereitung menschlicher Begräbnisse in den Überresten vor 60.000 Jahren und in der Kunst der mehrfarbigen Höhlenwände vor etwa 20.000 Jahren verwendet wurde. Viele anorganische Pigmente, die in der Vorgeschichte aus oberflächlichen Ton- und Gesteinsablagerungen gewonnen wurden, haben eine außergewöhnliche Beständigkeit über lange Zeiträume gezeigt.
Anorganische Pigmente sind mit wenigen Ausnahmen Kombinationen eines mineralischen Elements mit Sauerstoff und anderen Elementen (meist Schwefel, Silizium oder Kohlenstoff), die in die chemischen Klassen der Oxide, Oxidhydroxide, Sulfide, Sulfate, Silikate und Carbonate fallen.
Die Haupteinschränkung bei natürlichen anorganischen Pigmenten besteht darin, dass jede Farbe, die sie enthält (insbesondere Siena, Umbra und Ocker), zwischen den Herstellern erheblich variieren kann. 1998 brachte Daniel Smith ein wunderschönes Erdpigment namens "Spanish Gold Impfstoff" auf den Markt, dessen Produktion jedoch eingestellt wurde, da die Tonressourcen erschöpft waren und die Quelle der Materialien nicht identifiziert werden konnte.
Die meisten der traditionell natürlichen anorganischen Farben; gelber Ocker, rohe Siena, gebrannte Siena, rohes Holz, gebranntes Holz und venezianische oder indische Rottöne.
Pigmente in dieser Kategorie umfassen:
Rote Böden:
Eine breite und vielfältige Kategorie von Pigmenten aus Erde (meist Ton) mit hohen Anteilen an Eisenoxid (tiefvioletter bis hellroter Hämatit oder Tagesrost, orange bis gelber Lepidocrosit oder dunkelbrauner Maghemit) wird als verarbeitetes und natürliches Eisenoxid verkauft. Die Pigmentfarbe reicht von mattgelb über mattocker, mattorange, mattrot oder dunkelbraun bis fast schwarz. Die Farbe hängt von der durchschnittlichen Partikelgröße, dem Vorhandensein von Mangan oder anderen Elementen (die die Farbe verdunkeln und trüben) und davon ab, ob das Wasser chemisch an die Eisenoxidkristalle gebunden ist. Obwohl rote Eisenoxide auf der ganzen Welt vorkommen und seit der Antike als Pigmente verwendet werden, findet man heute reiche Vorkommen in der Nähe von Malaga, in Spanien (spanisches Rot mit einem charakteristischen bräunlichen Farbton) und Hormus, im Persischen Golf (persisches Rot). . Historisch gesehen sind die gelbbraunen Bodenressourcen in Europa in der Region Leghorn oder in der Nähe von Siena (Toskana, Italien) reich. Sie enthalten 50 % Eisenoxid und weniger als 1 % Mangandioxid.
Nach dem Brennen oder Polieren um 2000 v. Chr. war die Keramik sichtbar gebräunt oder nachgedunkelt. Und manchmal wurde beobachtet, dass natürliche Manganerze, die roten Böden hinzugefügt wurden, tiefere rote, violette oder schwarze Farben in Ton oder Glasuren erzeugen.
Gelbe Böden:
Natürliche Böden mit Kieselsäure und Ton sind hydratisierte Formen von Eisenoxid (gelbbrauner Limonit oder braungelber bis grüngelber Goethit) und Spuren von Gips oder Mangancarbonat. Sie sind wie rote Eisenoxide weltweit verbreitet und werden seit der Vorgeschichte als Pigmente und Farbstoffe verwendet. Historisch eine der besten Limonit-Qualitäten, enthält französischer Ocker etwa 20 % Eisenoxid und ist reich an Kieselsäure.
Grüne Länder:
Tone mit großen Mengen an Kieselsäure und den grünen Mineralien Glaukonit und Seladonit bestehen hauptsächlich aus hydratisierten Eisen-, Magnesium- und Aluminiumkaliumsilikaten. Die Farbe variiert von dunklem, graublauem Grün bis zu dunklem, mattem Gelbgrün. Völlig lichtecht und chemisch inert wird die grüne Erdung oder Terre seit der Antike weltweit eingesetzt. Die erste dokumentierte Verwendung in der Malerei in Europa findet sich in römischen Fresken; Es wurde auch im Mittelalter häufig als Untermalung für Fleischtöne und Schatten verwendet. Ursprünglich aus Betten in Mitteleuropa (heute Tschechien), in der Nähe von Verona (Italien) oder in Frankreich abgebaut, kommen moderne Materialien aus hochwertigen Betten in Zypern.
Lapislazuli:
Es ist eine komplexe Gesteinsmischung des dunkelblauen Minerals Lazurit (natürliches Ultramarin, das chemisch komplexeste Mineralpigment) mit Calcit oder Kalkspat und Eisenpyrit. Der Name Ultramarin leitet sich von der Bezeichnung azzuro oltramarino (blau über dem Meer) ab, mit der es von azzuro della magna unterschieden wird. Lapis kommt in China, Tibet und Zentralasien vor und wurde in alten babylonischen und ägyptischen Kulturen zur Herstellung von Schmuck, Skulpturen und Gemälden verwendet. über Venedig nach Europa importiert, pulverisiert und von Verunreinigungen getrennt, um als sehr teures rötlich-blaues Pigment in mittelalterlichen Handschriften und Kunst verwendet zu werden.
(Ein viel helleres und blasseres Blau als Marineblau)
(Na, Ca)8(AlSiO4)6(SO4,S,Cl)2
Azurit:
Seltener (grünlich-blau) sind Kupferkarbonat-Kristalle. Azurit ist an der Luft instabil. In der Antike wurde es jedoch als blaues Pigment verwendet, aber oft durch andere synthetische Pigmente (wie Ägyptisches Blau, Kupfer-Calcium-Silikat) ersetzt oder als teurere ultramarine Grundierung bevorzugt. Die Kristalle werden meist grob gemahlen, da sich die Farbe mit abnehmender Partikelgröße von dunkelblau zu schwach hellblau ändert. Azurit wird durch Säuren zersetzt und verdunkelt sich bei Hitze und einigen Ölwerkzeugen und Lacken. Vom 15. bis 17. Jahrhundert war Ungarn in Europa die Hauptquelle für Azurit, ein wichtiges Pigment. Türken in Ungarn Seine Verwendung nahm nach der Eroberung ab.
(Himmelblau, Dunkelblau bis Hellblau; Hellblau im Durchlicht)
Malachit:
Berggrün, auch Mineralgrün oder Verdeazzuro ("grünes Himmelblau") genannt, ist die häufigere (grüne) Form von hydratisiertem Kupfercarbonat, die weltweit in Oberflächenkupfervorkommen gefunden wird. Die alten Ägypter mahlten es zu einem Pulver, um es als grünes Pigment zu verwenden, und seit der Römerzeit wurde es oft für künstlerische Zwecke verwendet. Ende des 18. Jahrhunderts verfiel es vollständig. Mit abnehmender Partikelgröße wird seine Farbe deutlich heller und wird blau.
(Schwarzgrün mit Glasglanz, Smaragdgrün und Seidenglitzer oder matt).
Chemische Zusammensetzung: Cu2CO3
Kristallsystem: Monoklin
Kristallform: Sehr seltene und kleine Kristalle, meist faserig und radial, nadelförmig, kurz-lang prismatisch; meist massiv, renal
Zwillingsbildung: üblich an der Oberfläche {100}
Härte: 3,5 - 4
Spezifisches Gewicht: 4 - 4,05
Meine Sprache: {-201}
Farbe und Transparenz: Hellgrün, Schwarzgrün; transluzent-opak
Linienfarbe: Blassgrün
Glanz: Nadelähnliche Kristalle sind seidig, feste sind matt-matt, andere sind glasig mit Diamantglanz.
Unterscheidungsmerkmale: Farbe, Nierenform und Löslichkeit in HCl
Vorkommen: Malachit ist ein typisches Mineral sekundären Ursprungs, das in der Oxidationszone von Kupferlagerstätten gebildet wird.
Es kommt zusammen mit Azurit, Cuprit und Kupfer vor. Andere Mineralien, die es bildet, sind Calcit, Chrysokoll und Limonit.
Schuppenflechte:
Es ist biologischen Ursprungs. Es entsteht meist durch die konzentrische Ablagerung von Aragonit auf den Innenflächen der Schalenteile von Weichtieren (verschiedene Magenarten)




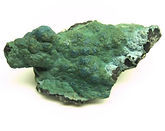
Rote Erde
Gelbe Erde
Lapislazuli
Azurit
Malachit
Formulare ausmalen
Bei der Auswahl des Farbmittels (Color Masterbatc) müssen möglicherweise einige vorläufige Bewertungskriterien berücksichtigt werden.
Diese Kriterien für die Auswahl des richtigen Farbstoffs;
-
Gesundheits- und Sicherheitsbedenken
-
Einfache Verwendung im Produktionsprozess
-
Farbanpassungsgenauigkeit sowie das Verwendungsvolumen bestimmter Farben
-
Beseitigung von Farbqualitätsproblemen
-
Minimale Auswirkungen auf die Kostenrechnung
können Titel wie sein.
Konzentrierte Farbstoffe (Farbmasterbatches):
Ungefähr 70% der weltweit für Kunststoffe verwendeten Farbstoffe liegen in Form von Konzentraten vor. Und fast die Hälfte dieses Verhältnisses ist weiß. Farbkonzentrate sind die führende Form, in der der Verbindung Farbstoffe direkt zugesetzt werden. Ihre physikalische Struktur besteht aus Linsen- oder Spaghetti-Granulat. Es gibt sogar hochkonzentrierte Körnchen unter 1 Millimeter. Es ermöglicht eine einfache Integration in das Basispolymer (Trägerpolymer) durch Verwendung automatischer Messgeräte während der Schmelzverarbeitung im Produktionsprozess. In Anlagen ohne Dosiereinheit wird die Mischung vor der Extrusion von Hand- oder Mischmaschinen vorgemischt. Das basischste ist das Trägerpolymer LDPE in konzentrierten Farbstoffen. Wenn das Verfahren jedoch für Hochleistungsanwendungen vorgesehen ist, ist es bevorzugt, mit dem Grundpolymer (PP, PC usw.) gekoppelt zu werden. Konzentrierte Farbstoffe sind im schnellen Ablauf des Verfahrens bevorzugt.
Normale Pigmentbeladungen in den Konzentraten liegen in der Größenordnung von 20% bis 25%. Es gibt jedoch auch "Superkonzentrate", die bis zu 80% Pigment enthalten. Sie sind kostengünstige Alternativen zu Standardprodukten geworden, weil sie weniger Konzentrat benötigen. Die Formulierung kann angereichert werden, indem dem Gehalt an konzentrierten Farbstoffen zusätzliche Merkmale wie UV-stabilisierende Additive hinzugefügt werden. Auf diese Weise wird die Homogenisierung dieser klein proportionierten Additive bei der Extrusion robuster. Dies führt zu höheren Produktionsraten sowie zu Kosteneinsparungen, da sich die Produkte leichter mit dem Hauptpolymer mischen lassen.
Bewertung: Kosten (2x mittel) / Transportabwicklung (2x mittel) / Volumen (2x mittel)
Dispersion (3x hoch) / Dosierkontrolle (3x hoch) / Leicht zu ändernde Farbe (2x mittel)
Flüssige Farbstoffe:
Sie haben eine hohe Pigmentbeladung von ca. 80%. Da sie flüssig sind, benötigen sie spezielle Geräte zum automatischen Dosieren und Pumpen der Verarbeitungsmaschine zum Reservoirhals. erfordert. Es gibt jedoch technische Entwicklungen, die viel einfacher an Trägerpipelines angeschlossen werden können. Sie ermöglichen eine gute Dispergierung des Pigments. In Abwesenheit einer Pumpeinheit (Dosiereinheit) ist es jedoch schwierig, eine homogenisierte Mischung mit Pulverpolymeren zu erhalten. Dies führt zu Problemen mit der Farbverteilung am Ende der Extrusion und erfordert einen zweiten Schuss (erneutes Extrudieren), um das Ergebnis zu optimieren.
Bewertung: Kosten (2x mittel) / Transportabwicklung (2x mittel) / Volumen (2x mittel)
Dispersion (3x hoch) / Dosierkontrolle (3x hoch) / Leicht zu ändernde Farbe (3x hoch)
Trockenpulverfarbstoffe (Pigmente):
Sie sind die kostengünstigsten Farbstoffe, die es zu kaufen gibt. Sie erfordern jedoch Benetzungseinheiten, die es ihnen ermöglichen, durch vorsichtiges Wiegen und Chargenmischen im Basispolymer dispergiert zu werden, was ihre Verwendung schwierig macht. Gleichzeitig schädigen sie aufgrund ihrer Pulverform die Umwelt wirksam. Dies wirkt sich aufgrund der Luftfederung negativ auf die Bediener aus. Die Arbeitsumgebung sollte aufgrund ihrer beeindruckenden Gesundheit auf jeden Fall über ein Belüftungssystem (Absorptionsventilator) verfügen.
Bewertung: Kosten (3x hoch) / Transportabwicklung (1x schwach) / Volumen (3x hoch)
Dispersion (1x schwach) / Dosierungskontrolle (2x mittel) / Leicht zu färbender Übergang (1x schwach)
Vorgefärbtes Polymer:
Bewertung: Kosten (1x schwach) / Transportabwicklung (3x hoch) / Volumen (1x schwach)
Dispersion (3x hoch) / Dosierungskontrolle (1x schwach) / Leicht zu farbiger Übergang (3x hoch)
Additive Masterbatches
Flammschutzmittel: Enthalten eines oder mehrere Bromid-, Chlor-, Stickstoff-, Aluminium-, Antimon- und Borelemente in seiner Struktur und verringern die Verbrennungswirkung, indem sie in die Polymerkette aufgenommen werden. Einige Hochleistungskunststoffe können als schwer entflammbare Kunststoffe, flammhemmende Kunststoffe, feuerfeste Kunststoffe oder selbstverlöschende Kunststoffe klassifiziert werden, sodass sie für den Einsatz dort geeignet sind, wo Brandschutz wichtig ist. Im Allgemeinen sind thermoplastische Materialien nicht buchstäblich entflammbar, da sie bei direktem Kontakt mit der Flamme zu brennen beginnen. Während die meisten Kunststoffe nach dem Ziehen der Flamme weiter brennen, hören die selbstverlöschenden Kunststoffe nach einer Weile von selbst auf zu brennen.
(Libaid-T 2)> PVC-Kabelmantel und feuerhemmende und rauchunterdrückende (FRLS) Verbindungen sind ebenfalls zur Verwendung geeignet. Es bietet eine bessere Verteilung von Füllmaterialien in PVC-Kabelmantelmischungen mit hoher Füllung (Calcit, Talk, ATH) und erhöht die Durchflusswerte von hochgefüllten PVC-Verbindungen. Glatte glänzende Struktur auf der Kabeloberfläche. Es ist ein wirksames Verarbeitungsmittel in Elastomeren mit hochfüllenden oder feuerhemmenden Additiven. Es ist viel nützlicher bei der Verringerung der Viskosität und der Verbesserung des Flusses, indem die Hälfte der Metallstearate verwendet wird, die in PP / EPDM- und PE / EPDM-Gemischen verwendet werden, die in Automobilteileanwendungen weit verbreitet sind. Es zeigt auch eine sehr gute Formtrennmitteleigenschaft beim Materialformen. Es ist ein geeignetes Verarbeitungsmittel für alle duroplastischen Formanwendungen in Pulverform. Es bietet eine sehr gute Dispersion aller in PF-, UF- und MF-Formmassen enthaltenen Additive. Es verbessert die Fließeigenschaften. Es wird besonders für Injektions- und Hochflüssigkeitstypen empfohlen. Durch die Einbeziehung sehr komplexer Formen wird sichergestellt, dass die Form in kurzer Zeit gleichmäßig und vollständig gefüllt wird.
Antibakterielle Mittel: Verhindert die Bildung von Algen und Bakterien, die in geografischen Regionen mit hoher Luftfeuchtigkeit auf der Oberfläche des Produkts auftreten können.
Antiblöcke: Verhindert das Blockieren während der Produktion des Films und hat einen leichten Gleiteffekt. Es erhöht die Fließfähigkeit, indem es die Bildung gleichmäßig geformter und gleich großer Partikel mit hoher Effizienz ermöglicht. Durch die Minimierung der Luftfeuchtigkeit werden die kleinen perforierten Strukturen auf der Oberfläche, die als Fischauge bezeichnet werden, und die durch das Linsenproblem verursachten Probleme vermieden.
Antifogs: Durch Erhöhen der Oberflächenspannung von Wassermolekülen verhindern sie die Bildung von Wassertropfen auf der Oberfläche. Nutzungsdauer des AF-Additivs; Sie kann je nach Nutzung, Umgebung und klimatischen Bedingungen zwischen 12 und 18 Monaten variieren. Die Gewächshausabdeckung verhindert Sonnenbrand oder Pilzkrankheiten, die durch Wassertropfen auf der Innenfläche des Gewächshauses verursacht werden, und unterstützt Einsparungen in der Agrarmedizin und Qualitätssteigerungen.
Antigasen / Luftentfeuchter: Feuchtigkeit; Sie erschweren den Prozess und verursachen eine Schwäche der mechanischen Eigenschaften. Antigasen und Luftentfeuchter absorbieren die Feuchtigkeit und Gase, die in Kunststoffen während der Wärmebehandlung vorhanden sind, und sorgen für eine homogenere Schmelzbildung. Eines der wichtigsten Probleme des Verbundprozesses ist die Feuchtigkeit. Sie erschweren den Prozess und verursachen Schwächen der mechanischen Eigenschaften, indem sie ihre Wirkung auf die Endprodukthersteller sowohl nach der Verbindung als auch nach der Verbindung zeigen.
Antistatik: Durch die Verhinderung der Bildung statischer Elektrizität auf dem Kunststoffprodukt wird verhindert, dass Staub und Fremdstoffe in der Umwelt am Produkt haften bleiben.
(Libstat 95)> Es handelt sich um ein hochaktives, stickstofffreies GMS der neuen Generation, das Antistatika und Schmiermittel enthält. Insbesondere Materialien wie PP, PE, PVC, die zu den Thermoplasten mit einer Vielzahl von Strukturen gehören, eignen sich auch zur Steuerung der statischen Elektrizität. Es ist für Lebensmittelanwendungen geeignet, da es hinsichtlich seiner Struktur aus pflanzlichen Produkten hergestellt wird.
Essenzen: Dies sind Additive, die verwendet werden, um die vorhandenen Gerüche von Kunststoffen oder schlechte Gerüche von recycelten Rohstoffen zu unterdrücken. Tropisch, Banane, Erdbeere, Rose usw. Sie können vielfältig sein. Sie werden meistens mit Verhältnissen von 1% und 2% verwendet und werden bevorzugt, um schlechte Gerüche zu unterdrücken.
Im Allgemeinen als Produkte zweiter Qualität bezeichnet, werden sie für die Verwendung von gefrorenen Rohstoffen benötigt, die bereits mehrmals Produkte waren.
Infrarotadditive: Dieses Additiv wird hauptsächlich in Gewächshausabdeckungen verwendet. Dadurch können die von der Sonne kommenden Infrarotstrahlen (IR) effektiver und durch Brechung in das Gewächshaus gelangen. Es reduziert das Entweichen des Strahls aus dem Inneren des Gewächshauses durch Strahlung. Entsprechend; Es reduziert Tag-Nacht-Temperaturunterschiede, Sonnenbrand an der Pflanze, Frostrisiko im Gewächshaus und erhöht die Effizienz und Qualität.
Transparenz: Es reguliert die Molekülstruktur der Polymerverbindung und stellt sicher, dass das möglicherweise trübe Bild transparenter und die Lichtdurchlässigkeit höher ist.
Optische Aufheller: Wenn die Produktfarbe nicht ausreicht, erhöht dies die Oberflächenlichtreflexion und sorgt für ein helleres Erscheinungsbild.
Optische Aufheller: (TitanDiOxide)> Es handelt sich um ein Produkt mit einer stabilen chemischen Struktur, das mit Oberflächenbehandlungen mit organischer Struktur mit Silizium- und Zirkonmaterialien angereichert ist. Es ist ein Produkt mit ausgezeichnetem Weißgrad, Helligkeit, Bedeckung und Quetschung, das eine sehr gute Beständigkeit gegen Wetterbedingungen und Faktoren wie Kreiden und Wirkung zeigt. Es ist wasserlöslich.
(Zirtex OB-1)> Geeignet für Bleichanwendungen aus Polyesterfasern, Nylonfasern und PP-Fasern. Es ist für den Einsatz in Kunststoffanwendungen wie Hart-PVC, ABS, EVA, PS, PC geeignet. Es ist zur Verwendung bei der Polyester- und Nylonpolymerisation geeignet. Es ist wasserabweisend, wasserunlöslich, aber auch Paraffin mit hohen Schmelztemperaturen, Mineralölen und organischen Lösungsmitteln kann gelöst werden. Es eignet sich besonders für den Prozess von Kunststoffen, die bei hohen Temperaturen verarbeitet werden.
Lichtsender: Sie werden hauptsächlich zur Lösung der Probleme der Lichtausbreitung bei LED-Beleuchtungsprodukten eingesetzt. Durch Erhöhen der Lichtdurchlässigkeit wird der Bedarf an LED-Verwendung verringert.
Externe Schmiermittel: Reduziert die Reibung und Haftung zwischen Polymermolekülen und dem Zylinder / der Schraube. Der Wirkungsgrad steigt, der Verschleiß der Metalloberflächen wird verringert, die Reinigung der Zylinder / Schrauben wird komfortabler, da die Übergänge, der Reinigungsverbrauch und die Körperhaltung verringert werden.
(Zinkstearat)> Als externes Schmiermittel, Säurereiniger, Formtrennmittel, Prozessmittel in PP-, LLDPE-, HDPE- und PS-Materialien in der Kunststoffindustrie. Es wird als Prozessmittel in Kautschuk, als Formtrennmittel und als Prozessverbesserer in synthetischen und Polyestermaterialien verwendet.
(Lithiumstearat) Unter Prozessbedingungen> 200 ° C ist es für jedes externe Schmiermittel schwierig, ohne Abbau zu arbeiten. Lithiumstearate sind ein externes Schmiermittel mit überlegener Leistung, das bei diesen hohen Temperaturen arbeiten kann.
(PE-Wachs)> Es ist das weltweit am häufigsten verwendete Dispergiermittel und externe Schmiermittel. Es ist ein unverzichtbares Dispergiermittel für fast alle Compound- und Masterbatch-Prozesse. Hier sind jedoch Materialreinheit und -qualität wirksam.
(Libaid-T 2)> Bietet einen sehr guten Schimmelpilzeffekt. Sie müssen der Formulierung keine herkömmlichen Schmiermittel wie PE-Wachs und Metallsterarat hinzufügen. Es bietet weniger Nutzung und effektive Ergebnisse im Vergleich zu traditionell verwendeten Schiebereglern.
Interne Schmiermittel: Es beschleunigt die Homogenisierung, indem es die Reibung zwischen Polymermolekülen verringert. Es hilft den verschiedenen Polymeren in der Verbindung, eine homogene Struktur mit der Abnahme der molekularen Reibung zu bilden. Das gewünschte Ergebnis kann jedoch möglicherweise nicht bei unterschiedlichen MFI-Werten erzielt werden. Darüber hinaus ist hier auch die Viskosität des Schmierstoffadditivs wichtig. ( Viskosität: Dies ist der innere Strömungswiderstand von Flüssigkeiten. Mathematisch ist es offensichtlich, dass Flüssigkeiten mit einem hohen Viskositätswert schwieriger zu fließen sind. Beispielsweise ist die Viskosität von gefiltertem Honig höher als die Viskosität von Wasser. Die Viskosität ändert sich mit Grundsätzlich nimmt die Viskosität vieler Flüssigkeiten mit zunehmender Temperatur ab. Mit zunehmender Temperatur nehmen die Anziehungskräfte zwischen den Molekülen ab und die Moleküle bewegen sich freier, was die Fließfähigkeit erhöht.
In vielen Flüssigkeiten nimmt die Viskosität mit zunehmendem Druck zu. )
(Calciumstearat)> Es wird als internes Schmiermittel in der Kunststoff- und Gummiindustrie, als Trennmittel, Säurereiniger, als Elestomer-Verarbeitungsmittel in Elostomeren und als Verarbeitungsmittel zur Reduzierung des Extruderdrucks bei der Herstellung von PVC-Rohren verwendet , Armaturen und Abstellgleis. Zusätzlich werden Calciumstearate als Antibackmittel in Polyolefinen verwendet.
(Libwax C - Amid Wax)> Es ist ein ausgezeichnetes Formtrenn- und Dispergiermittel in technischen Kunststoffen, die bei hohen Temperaturen verarbeitet werden. Es hat eine viel höhere Wärmebeständigkeit als herkömmliche Schmiermittel. Darüber hinaus kann eine höhere Leistung erzielt werden, indem bis zu 50% weniger als bei herkömmlichen Schmiermitteln verwendet werden. Es zeigt sowohl interne als auch externe Schmiereigenschaften in allen Thermoplasten und Duroplasten. In Compound- und Masterbatch-Prozessen; ABS und PS erhöhen die Fließeigenschaften des Materials. Es wirkt als Dispergiermittel in pigmenthaltigen Materialien. Es kann als Pigmentdispergiermittel in Polyolefinen verwendet werden. Es wirkt als inhärentes Formtrennmittel in Polyamiden. Es wird als Schmiermittel und Formtrennmittel in Acetal Plastics verwendet.
Pigmentbenetzungsmittel (Libnol-101)> Wird als sehr gutes Benetzungs- und Dispergiermittel in Titandioxid- und anderen anorganischen Pigment-Masterbatch-Anwendungen verwendet.
(Libnol - 400)> Es wird als Dispergiermittel und Pigmentbenetzungsmittel in Masterbatches verwendet, die mit schwer dispergierbaren Pigmenten wie Ruß und einigen ganz speziellen organischen Pigmenten hergestellt werden.
Geruchsabsorber: Bei der Wärmebehandlung aller Polymere werden durch die Reaktion von Chemikalien Duftmoleküle freigesetzt. Dies gibt der Umwelt den Geruchssinn. Geruchsabsorber adsorbieren Geruchsmoleküle möglicher Gerüche.
Prozesshilfe / Prozessverbesserer: Erleichtert die Produktion, indem die Reibung zwischen der Polymerverbindung und dem Zylinder / der Schraube verringert wird. Es bietet Energieeinsparungen. Es verhindert Rauheit auf der Filmoberfläche. Es wird auch als Prozessverbesserer bezeichnet.
(Libnol G-7481)> Es ist ein Prozessmittel, das Polymeren bei Compound- und Masterbatch-Prozessen hilft und sicherlich keine signifikanten Änderungen der physikalischen Eigenschaften verursacht. Es verbessert die Fülldispersion, die Fließeigenschaften und die Trenneigenschaften während des Prozesses. Es ist ein ausgezeichnetes Verarbeitungsmittel für Hochtemperatur-Thermoplaste vom Estertyp mit geringer Verdunstung und guter thermischer Stabilität. Es ist ein Formtrennmittel für PC, PET / PBT.
(Libaid-T 2)> Es handelt sich um einen multifunktionalen Prozessverbesserer. Es ist ein multifunktionales Prozessmittel, das eine gleichmäßige Verteilung von Pigment- und Füllmaterialien in der Polymermatrix gewährleistet, insbesondere in hochfüllstoffhaltigen Masterbatches und Verbindungen mit hohem Pigmentgehalt. Es ist auch ein sehr gutes Bindemittel. Daher wirkt es als gutes Bindemittel zwischen dem Füllstoff und dem Polymersystem. Bietet eine homogene Verteilung der Additive in Verbindung oder Masterbatch und eine bessere Bindung von Füllstoffen und Pigmenten an das Hauptträgerpolymer.
In gefüllten Verbindungen; Es reguliert die Vorlauftemperatur. Bietet eine perfekte Verteilung in Additiven und Füllstoffen (Calcit, Talk, ATH). Die Schrumpfrate wird verringert. Es macht die Oberfläche sehr gut aussehen. Es bietet eine einfache Entformung in vielen Systemen, einschließlich TPE. Es verhindert Blüteeigenschaften beim Drucken.
In der Masterbatch-Produktion; Es ist mit allen thermoplastischen Olefinen kompatibel. Es reguliert die Verteilung in organischen und anorganischen Pigmenten, die schwer zu dispergieren sind. Es bietet eine Regulierung der Dispersion bei hoher Pigmentbeladung im Masterbatch. Es bietet eine sehr gute Oberflächenqualität in Granulat. Es verbessert die Fließeigenschaften. Es bietet eine gute Dispersion von Ruß, der im schwarzen Masterbatch schwer zu dispergieren ist, sowie des Trägerrohstoffs.
Fette / Schmiermittel: Bietet eine Schmierwirkung, indem verhindert wird, dass Filmoberflächen aneinander und an Metalloberflächen haften. Es hilft, dünne Filme aufzunehmen und die Filmschichten leicht zu öffnen. Bietet Effizienz bei niedriger Temperatur und erhöht den Glanz der Filmoberfläche.
(Lutamid-P 98)> Es ist ein hochreines Oleamid. Es verringert die Reibungsrate zwischen Filmschichten oder zwischen zwei Filmen und lässt sie übereinander gleiten. Es wird als Formtrennmittel in Druckfarben, Kappenherstellung, EVA-Copolymeren, Kautschukmischungen und Beschichtungen verwendet.
(Libaid-T2)> Nach dem Gebrauch müssen keine anderen herkömmlichen Schieberegler verwendet werden. In TPE- und TPO-Verbindungen ist es im Vergleich zu herkömmlichen Schmiermitteln ein besserer Viskositätsreduzierer. Es bietet eine sehr gute Dispersion von zugesetzten Füllstoffen und anderen Additiven.
Ultraviolette Additive: Kunststoffe für Außenanwendungen können Unwetter ausgesetzt sein. Diese Anwendungen erfordern häufig ein wetterfestes Kunststoffmaterial, das den nachteiligen Auswirkungen ultravioletter Strahlen standhält, die das Aussehen und die mechanischen Eigenschaften von Kunststoffen beeinträchtigen können. Daher ist es oft ein kluges Detail, dass wetterbeständige Kunststoffe etwas UV-beständig sind, da UV-Strahlung einen besonders hohen Einfluss auf Materialien haben kann, die im Freien verwendet werden und Außenelementen ausgesetzt sind.
Diese Stabilisatoradditive verhindern die Oxidation der Polymerkette gegen Sonnenlicht mit niedriger Wellenlänge (UV). Auf diese Weise schützt es das Produkt vor den schädlichen Auswirkungen des Sonnenlichts, verhindert das Ausbleichen und verlängert seine Lebensdauer.
Die UV-Beständigkeit von Kunststoffen wird im Allgemeinen durch die Verwendung von Additiven wie UV-Stabilisatoren, Schwarzfärbung (üblicherweise unter Verwendung von Ruß) oder schützenden Oberflächenbeschichtungen (Farbe oder Metallbeschichtung usw.) erreicht. Additiver Ruß ist eine kostengünstige und oft sehr effektive Methode zur Herstellung von UV-beständigem Kunststoff. Darüber hinaus können fluorierte Polymere wie PTFE und PVDF in ihrem natürlichen Zustand eine sehr gute UV-Stabilität aufweisen. In UV-beständigen Kunststoffen;
-
Eine Vergilbung des Kunststoffs wird nicht beobachtet
-
Lackierte Kunststoffe lecken nicht
-
Die Kunststoffoberfläche wird nicht weiß
-
Keine Spannungsrisse
-
Keine Fragilitätsentwicklung
-
Es gibt keine Abnahme von Festigkeit, Flexibilität und Härte.
Antiozonant-Additive: Dies sind Materialien, die Kunststoff zugesetzt werden, um den durch Ozonexposition verursachten Abbau des Endprodukts zu verlangsamen. Antiozonantien wirken normalerweise, indem sie sich an die Oberfläche des Produkts bewegen und dann eine ozonbeständige Barriere auf der Oberfläche bilden.
Quelladditive: Manchmal auch als chemische Schaumbildner bezeichnet. Sie werden verwendet, um Gas in Kunststoff oder Harz zu trennen. Es wird verwendet, um das Gewicht zu reduzieren, die Weichheit zu erhöhen, eine Isolierung bereitzustellen, Stoßdämpfungseigenschaften hinzuzufügen oder dem Endprodukt Flexibilität zu verleihen.
Kupplungsmaterialien: Sie fördern die physikalische oder chemische Wechselwirkung mit dem Polymer.
Weichmacher / Weichmacher
Weichmacher sind relativ nichtflüchtige organische Substanzen (insbesondere Flüssigkeiten). Wenn sie in einen Kunststoff oder ein Elastomer eingearbeitet werden, unterstützen sie die Flexibilität und Verarbeitbarkeit des Polymers.
Weichmacher erhöhen den Fluss und die Thermoplastizität eines Polymers, indem sie die Viskosität, die Glasübergangstemperatur (Tg), die Schmelztemperatur (Tm) und den Elastizitätsmodul der Polymerschmelze verringern, ohne den chemischen Grundcharakter des plastifizierten Materials zu verändern.
Weichmacher gehören zu den am häufigsten verwendeten Additiven in der Kunststoffindustrie. Sie sind im Allgemeinen auch billiger als andere Additive, die bei der Polymerverarbeitung verwendet werden. Weichmacher werden hauptsächlich in PVC verwendet, dem volumenmäßig drittgrößten Polymer nach PP und PE. Im Gegensatz dazu wird PVC in einer Vielzahl von Produkten verwendet.
In Anwendungen wie Weichmachern, PVC-Rohren (oder Hart-PVC-Rohren), Außen- und Fensterprofilen, PVC-Innenverkleidungen (oder flexiblem PVC), Kabeln, PVC-Folien, Fußböden, Dach- und Wandverkleidungen usw. Sie werden in Bereichen eingesetzt. Acryl, PET, Polyolefine, Polyurethane usw. In solchen Polymeren wird eine signifikante Menge Weichmacher verwendet. Weichmacher werden manchmal auch in Kautschuken verwendet, aber in diesen Fällen besteht der Zweck darin, Streckmittel zu sein.
Der Plastifizierungsprozess wird unter zwei Hauptüberschriften zusammengefasst: intern und extern.
Interne Plastifizierung: Ein Polymer kann intern plastifiziert werden, indem das Polymer oder Monomer chemisch modifiziert wird, wodurch seine Flexibilität erhöht wird. Es beinhaltet die Copolymerisation der gewünschten Polymer- (hohe Tg) und Weichmacher- (niedrige Tg) Monomere, so dass der Weichmacher ein integraler Bestandteil der Polymerkette wird. Die am häufigsten verwendeten internen Weichmachermonomere: Vinylacetat, Vinylidenchlorid. Auch die Komplexität der Reaktion kann zu längeren Reaktionszeiten und erhöhten Kosten führen.
Intern plastifizierte Materialien zeigen Temperaturabhängigkeit und Dimensionsinstabilität bei hohen Temperaturen.
Externe Plastifizierung: Dies ist die am weitesten verbreitete Methode zur Plastifizierung, da sie kostengünstig ist. Sie sind flüssige Weichmacher, die dem Formulierer die Freiheit geben, Formulierungen für eine Reihe von Produkten zu entwickeln (von halbstarr bis extrem flexibel, je nach Menge).
Die am häufigsten verwendeten externen Weichmacher sind Ester von Säuren oder Säureanhydriden, die durch Reaktion mit Alkoholen gebildet werden.
Es gibt zwei Hauptgruppen von äußeren Weichmachern:
1- Primäre Weichmacher erhöhen die Dehnung, Weichheit und Flexibilität des Polymers. Sie sind sehr gut mit Polymeren kompatibel und können in großen Mengen zugesetzt werden.
Zum Beispiel: Bis zu 50% Vinylhandschuhe sind Weichmacher, die PVC flexibel und weich genug machen, um es zu tragen.
2- Sekundärweichmacher ist ein Weichmacher, der typischerweise nicht als einziger Weichmacher in einem plastifizierten Polymer verwendet werden kann. Sekundärweichmacher können eine begrenzte Verträglichkeit mit dem Polymer und / oder eine hohe Flüchtigkeit aufweisen. Es kann funktionelle Gruppen enthalten oder nicht, die es ihnen ermöglichen, das Polymer bei Verarbeitungstemperaturen aufzulösen.
Sekundärweichmacher: Sie werden zum Zwecke der Kostenreduzierung, Viskositätsreduzierung, Arbeitsfestigkeit, Erhöhung der Oberflächenschmierung und Verbesserung der Eigenschaften bei niedrigen Temperaturen bevorzugt.
Eine Untergruppe von sekundären Weichmachern sind ebenfalls Streckmittel. Sie werden üblicherweise mit primären Weichmachern verwendet, um die Kosten für flexibles Allzweck-PVC zu senken. Es handelt sich meistens um kostengünstige Öle mit begrenzter Verträglichkeit mit PVC. Sie werden hinzugefügt, um die Kosten zu senken und in einigen Fällen die Feuerbeständigkeit zu erhöhen. Typische Beispiele sind naphthenische Kohlenwasserstoffe, aliphatische Kohlenwasserstoffe, chlorierte Paraffine (Feuerbeständigkeit).
Weichmacherverlust / Exsudation: Inkompatibilität zwischen Polymer und Weichmacher kann Exsudation verursachen. Es gibt verschiedene Faktoren, die dazu führen können, dass der Weichmacher von der Kunststoffoberfläche (oder in oder in ein Substrat, in dem er in engem Kontakt gehalten wird) wandert, wie z. B. Wärmeaustausch, Feuchtigkeitsänderung, mechanische Beanspruchung, Witterungseinflüsse. Der Verlust von Weichmacher kann zu geringerer Elastizität, Versprödung und Rissbildung führen.
Klassifizierung von Weichmachern: In der Regel nach ihrer chemischen Zusammensetzung klassifiziert. Es ist möglich, die Eigenschaften der Strukturelemente (z. B. verschiedene Alkohole in einer homologen Reihe von Phthalaten, Adipaten usw.) Weichmachern und ihre Wirkung auf Basispolymere zu verstehen.
Unterschiedliche Weichmacher beeinflussen unterschiedliche physikalische und chemische Eigenschaften von Materialien. Daher wird ein spezieller Weichmacher benötigt, um die Eigenschaften in eine bestimmte Richtung zu ändern, um die Anforderungen zu erfüllen.
Es gibt mehrere allgemeine chemische Familien von Weichmachern, die zur Polymermodifizierung verwendet werden.
Unter ihnen sind die am häufigsten verwendeten:
Phthalatester: Sie werden durch Veresterung von Phthalsäureanhydrid oder Phthalsäure hergestellt, die durch Oxidation von Orthoxylin oder Naphthalin erhalten werden. Die am häufigsten verwendeten Phthalatweichmacher umfassen:
DEHP: Orthophthalat mit niedrigem Molekulargewicht. Immer noch der weltweit am häufigsten verwendete PVC-Weichmacher
DINP, DIDP: Orthophthalate mit hohem Molekulargewicht
Aliphatische zweibasige Säureester: Dazu gehören Chemikalien wie Glutarate, Adipate, Azelate und Sebecate. Sie bestehen aus aliphatischen zweibasischen Säuren wie Adipinsäure und Alkoholen.
Benzoatester: Sie sind die Veresterungsprodukte von Benzoesäure und ausgewählten Alkoholen oder Diolen.
Trimellitester: Sie werden durch Veresterung von Trimellithsäureanhydrid (TMA) und typischerweise C8-C10-Alkoholen hergestellt.
Polyester: Sie entstehen durch die Reaktion vieler Kombinationen von Dicarbonsäuren und bifunktionellen Alkoholen.
Citrat: Tetraester, die aus der Reaktion von einem Mol Zitronensäure mit drei Mol Alkohol resultieren. Nur die Hydroxylgruppe der Zitronensäure wird acetyliert.
Biobasierte Weichmacher: Epoxidiertes Sojaöl (ESBO), epoxidiertes Leinöl (ELO), Rizinusöl, Palmöl, andere Pflanzenöle, Stärken, Zucker usw.
Andere: Enthält Phosphate, chlorierte Paraffine, Alkylsulfonsäureester und mehr.
Anwendungsbereiche von Weichmachern: Mehr als 90% der in thermoplastischen Polymeren verwendeten Weichmacher werden in PVC verwendet. Der Markt für plastifizierte Polymere und der Markt für plastifiziertes PVC sind weitgehend gleich, aber einige Weichmacher werden auch in Acrylpolymeren, Polyurethanen, Polystyrol oder sogar Polyolefinen verwendet.
Zu den wichtigsten Endanwendungen gehören:
Folie und Beschichtung: Zu den Produkten aus flexibler PVC- Folie und Folie gehören Dachbahnen, Geomembranen, Fußböden, Gepäck, Werbeschilder, Schwimmbadauskleidungen und andere.
Bodenbeläge: Zu den flexiblen PVC-Bodenbelägen gehören flexible Bodenbeläge, Vinyl-Kompositionsfliesen, Luxus-Vinylfliesen und Teppichfliesen mit Vinylrücken.
Draht und Kabel: Flexibles PVC ist ein guter elektrischer Isolator mit guter Verarbeitbarkeit und einem nützlichen Betriebstemperaturbereich. Daher ist es ein ausgezeichnetes Material für elektrische Anwendungen wie Isolierung und Mantel für elektrische Leiter, Isolierung für Glasfaserkabel.
Beschichtete Stoffe: Synthetisch beschichtete PVC-Stoffe sind wetterbeständig und weisen eine hervorragende Festigkeit und Haltbarkeit auf. Es wird in Branchen eingesetzt, die Architektur, Lifestyle, Sport, Werbung, Verteidigung, Bergbau, Ernährung und Landwirtschaft, Automobile und Transport unterstützen. Zu den Produkten gehören Planen, Zelte und Gartenmöbel.
Konsumgüter: Kleidung, Schuhe, Verpackung
Medizin: Blutbeutel, Infusionsschläuche, biologisch gefährliche Strukturen, andere medizinische Geräte
Nicht-PVCs: Kleine Mengen von Weichmachern vom PVC-Typ werden auch in anderen Polymeren verwendet, einschließlich Acryl, Polyurethanen und Polystyrol. Die meisten Kunststoff-PVC-Produkte sind langlebige Produkte, langlebige Produkte. Phthalate eignen sich aufgrund ihrer geringen Flüchtigkeit, geringen Wasserlöslichkeit, guten Beständigkeit gegen Sonnenlicht und extreme Temperaturen, guten Verträglichkeit mit PVC-Polymer und allgemein guten Beständigkeit gegen biologischen Abbau gut zur Verwendung in solchen Produkten. Zum Beispiel (flexible PVC-Dachbahnen, Geomembranen, Draht- und Kabelisolierung). Es ist sehr schwierig, Phthalatweichmacher bei diesen Endanwendungen zu ersetzen. In ähnlicher Weise wurde gefunden, dass Phthalatweichmacher aufgrund ihres relativ hohen Solvatisierungsvermögens und ihrer relativ niedrigen Viskosität für PVC-Polymere leichter Phthalatersatz in flexiblen PVC-Verbindungen zu verarbeiten sind als zumindest einige.
Antioxidantien
„Es ist sicher, dass ein grundlegendes Wissen über die Oxidation erforderlich ist, um die Rolle von Antioxidantien zu verstehen. In diesem Zusammenhang ist Oxidation, eine der grundlegendsten Reaktionen des Lebens, einfach der Elektronenfluss von einem Atom zum anderen in positiver Ladung (Oxidation) ist der Elektronenfluss aus dem Atom. Ich meine, die negative Ladung des Atoms nimmt ab und die positive Ladung steigt. Sauerstoff ist eines der wichtigsten Oxidationsmittel in der Natur. Das heißt, wenn Sauerstoff in der Umgebung fließen alle Elektronen in Richtung Sauerstoff. Deshalb ist Oxidation ein ähnliches Wort wie Sauerstoff. Das Thema ist am sichtbarsten und am schnellsten zu verstehen. Beispiel: Eisen rostet. Wenn Sauerstoff in der Umgebung vorhanden ist, fließen Elektronen von Eisen zu Sauerstoff, das Eisen oxidiert, das heißt, es rostet. Diese Reaktion setzt sich als Kette fort und nimmt zu. Wenn keine Gegenkraft vorhanden ist, um diese extrem reaktiven Oxidationsmittel zu stoppen, wird diese Auslöschung so lange fortgesetzt, bis kein festes Molekül in der Umgebung vorhanden ist. das ist die Gegenkraft. Sie tragen zum Schutz der Polymerkette bei, indem sie die Elektronen aus der Kette entfernen und den Wunsch, sich mit Sauerstoff zu verbinden, stoppen.
Antioxidantien werden verwendet, um Polymere sowohl vor Oxidation während der Schmelzverarbeitung als auch als „langfristiger thermischer Stabilisator“ während des gesamten Produktlebenszyklus zu schützen. Es verzögert die Verschlechterung des Polymers durch Witterungseinflüsse und verlängert seine Lebensdauer. Solche thermischen Langzeitstabilisatoren unterscheiden sich von Stabilisatoren für die Schmelzverarbeitung. Das heißt, sie müssen bei Temperaturen weit unterhalb des Polymerschmelzpunktes funktionieren.
Antioxidantien werden Kunststoffen zugesetzt, um einen Abbau durch thermomechanische oder thermooxidative Bedingungen zu verhindern. Antioxidantien verlängern die Lebensdauer eines Produkts, verbessern sein Aussehen und erhalten seine Festigkeit, Härte und Flexibilität. Die Art und Weise, wie diese Antioxidantien den Abbauprozess unterbrechen, variiert je nach ihrer Struktur. Verschiedene Amine, Phenole, Phosphite, Thioester etc. als Antioxidantien für Kunststoffe. benutzt.
(Richfos-168)> In vielen Polymermaterialien wirkt es als Hitzestabilisator, indem es verhindert, dass sich das Material bei hohen Temperaturen während des Prozesses zersetzt. Dank seiner geringen Flüchtigkeitsrate ermöglicht es die Verarbeitung des verarbeiteten Polymers bei den erforderlichen hohen Temperaturen und Zeiträumen. Geeignet für den Einsatz auf PP, PE, PC, ABS und Polyester
(Richbox-1010)> Besonders wirksam gegen Polymerabbau bei Langzeitalterung. Es ist auch als Prozessstabilisator sehr wirksam. Es weist eine gute Beständigkeit gegenüber Farbänderungen bei hohen Temperaturen auf, die bei der Verarbeitung von thermoplastischen Polymeren auftreten. Es ist ein Antioxidans mit hohem Molekulargewicht, das eine geringe Flüchtigkeit bietet.
(Richbox-1076)> Es verhindert effektiv den Oxidationsabbau, der bei vielen Polymerprozessen und Endanwendungen auftritt. Anox PP 18 ist ein hervorragender Stabilisator in Polyolefinen, schlagfesten Styrolen, Blockcopolymeren, Elastomeren, PVC und Polyurethanen.
(Richnox-1098)> Es ist ein phenolisches Antioxidans, das eine Stabilisierungsfunktion gegen Polymerverschlechterung während der Langzeitalterung bietet. Insbesondere PA-Compound, Masterbatch zeigt eine gute Beständigkeit gegen Farbwechsel bei hohen Temperaturen, die bei der Herstellung von Teilen auftreten.
Es kann auch in Polyacetalen, Polyestern, Polyurethanen, Klebstoffen und Elastomerprodukten verwendet werden.

Phthalate
Es wird typischerweise durch Veresterung von Phthalsäureanhydrid hergestellt, das durch Oxidation von Orthoxylen erhalten wird. Phthalate erscheinen fast farblos mit einem schwachen Geruch. Ihre Löslichkeit in Wasser ist begrenzt, aber in den meisten organischen Lösungsmitteln (Mineralöl usw.) mischbar.
-
Sie sind eine traditionelle Wahl, da sie der Extraktion, Verdunstung und Migration widerstehen.
-
Phthalate bieten Haltbarkeit, Flexibilität, Witterungsbeständigkeit und halten hohen Temperaturen stand
-
Phthalate sind im Vergleich zu anderen Weichmachern wirtschaftlich
-
In Polymeren wie PVC werden Phthalate nicht chemisch gebunden und aus Kunststoffen ausgelaugt, wodurch sie in der Umwelt auftreten.
-
Einige Phthalatweichmacher können ernsthafte Gesundheitsrisiken darstellen, da sie krebserregend und / oder entwicklungstoxisch sind.
-
Einige Phthalate können sich in geringen Mengen im menschlichen Körper ansammeln.