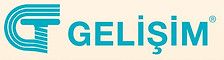


Hidrokarbonlar
Hidrojen ve karbon olmak üzere iki elementten oluşan organik bir bileşiktir. Petrol bileşiminin büyük bir kısmı değişen uzunluklardaki hidrokarbonlardan oluşur.
En küçük hidrokarbon metan, tek bir karbon atomu ve dört hidrojen atomundan oluşur. Bununla birlikte, hidrokarbonlar, zincirler, daireler ve diğer karmaşık şekiller dahil olmak üzere birçok yönden birbirine bağlanmış yüzlerce veya binlerce bireysel atomdan oluşabilir.
Hidrokarbonların özelliklerini sınıflandırmak için birkaç temel türe ayrılırlar.
Alkanlar: Bunlar doymuş hidrokarbonlar olarak adlandırılır. Yani sadece tüm karbon atomları arasında tek bağlar içerirler. Alkanlar, petrol yakıtlarının temelidir ve doğrusal ve dallı formlarda bulunurlar.
Doymamış Hidrokarbonlar: Karbon atomları arasında bir veya daha fazla çift bağa sahip olan hidrokarbonlara alken denir.
Sikloalkanlar: Bir veya daha fazla halka yapısı içeren herhangi bir hidrokarbon.
Aromatik Hidrokarbonlar: Areneler olarak da adlandırılan aromatik hidrokarbonlar, karbon atomlarının birbirini izleyen çift ve tek bağlarla bağlandığı benzersiz bir karbon molekülleri sınıfıdır. Bu molekül sınıfı, karbon atomları arasındaki bağların tek ve çift bağlar arasında bir ara bağ olduğu özel halka yapılarına sahiptir.
Bu sınıftaki moleküller, endüstriyel çözücü «benzen» içerir.
Benzen (C6H6): Diğer hidrokarbonlar gibi benzen de petrolün doğal bir bileşenidir. Oda sıcaklığında renksiz, yanıcı, tatlı kokulu bir sıvıdır ve yüksek oktan sayısına sahip olduğu için çoğu benzin karışımının bir bileşenidir.
Benzen de oldukça kanserojendir ve kemik iliği yetmezliği ve kemik kanserine neden olduğu iyi bilinmektedir. Elbette, “hoş aroması” nedeniyle tıraş sonrası ve diğer kozmetiklerde bir katkı maddesi olarak kullanıldığında kanserojenliği iyi bilinmemektedir.
En büyük benzen kullanımı (% 50), stiren ve polistren plastiklerinin ürünüdür. Ayrıca Naylon üretiminde önemli olan sikloheksan olarak bilinen bir moleküle dönüştürülür. Siklohekzan üretmek için benzenin yaklaşık% 15'i kullanılır. Böcek ilaçlarından kauçuğa kadar her şeyde daha küçük miktarlar kullanılır.
Benzen yapısı iki şekilde çizilebilir. İlkinde, çift bağ karakteri açıkça çizilir. Kısa elli versiyonda, yapıyı göstermek için halkanın içine bir daire çizilir. Benzen içindeki her bir karbon atomuna bağlı tek bir hidrojen vardır.
Aşağıdaki I. ve II. çizimleri eştir. Pratikte III. çizim kullanılır.
Benzen, renksiz, alevlenebilen, kaynama noktası 80,1 °C, erime noktası 5,5 °C olan bir sıvıdır.
Binükleer Aromatik Hidrokarbonlar: Molekülünde iki benzen halkası içeren bileşiklerdir.
Hidrokarbonlar
Hidrojen ve karbon olmak üzere iki elementten oluşan organik bir bileşiktir. Petrol bileşiminin büyük bir kısmı değişen uzunluklardaki hidrokarbonlardan oluşur.
En küçük hidrokarbon metan, tek bir karbon atomu ve dört hidrojen atomundan oluşur. Bununla birlikte, hidrokarbonlar, zincirler, daireler ve diğer karmaşık şekiller dahil olmak üzere birçok yönden birbirine bağlanmış yüzlerce veya binlerce bireysel atomdan oluşabilir.
Hidrokarbonların özelliklerini sınıflandırmak için birkaç temel türe ayrılırlar.
Alkanlar: Bunlar doymuş hidrokarbonlar olarak adlandırılır. Yani sadece tüm karbon atomları arasında tek bağlar içerirler. Alkanlar, petrol yakıtlarının temelidir ve doğrusal ve dallı formlarda bulunurlar.
Doymamış Hidrokarbonlar: Karbon atomları arasında bir veya daha fazla çift bağa sahip olan hidrokarbonlara alken denir.
Sikloalkanlar: Bir veya daha fazla halka yapısı içeren herhangi bir hidrokarbon.
Aromatik Hidrokarbonlar: Areneler olarak da adlandırılan aromatik hidrokarbonlar, karbon atomlarının birbirini izleyen çift ve tek bağlarla bağlandığı benzersiz bir karbon molekülleri sınıfıdır. Bu molekül sınıfı, karbon atomları arasındaki bağların tek ve çift bağlar arasında bir ara bağ olduğu özel halka yapılarına sahiptir.
Bu sınıftaki moleküller, endüstriyel çözücü «benzen» içerir.
Benzen (C6H6): Diğer hidrokarbonlar gibi benzen de petrolün doğal bir bileşenidir. Oda sıcaklığında renksiz, yanıcı, tatlı kokulu bir sıvıdır ve yüksek oktan sayısına sahip olduğu için çoğu benzin karışımının bir bileşenidir.
Benzen de oldukça kanserojendir ve kemik iliği yetmezliği ve kemik kanserine neden olduğu iyi bilinmektedir. Elbette, “hoş aroması” nedeniyle tıraş sonrası ve diğer kozmetiklerde bir katkı maddesi olarak kullanıldığında kanserojenliği iyi bilinmemektedir.
En büyük benzen kullanımı (% 50), stiren ve polistren plastiklerinin ürünüdür. Ayrıca Naylon üretiminde önemli olan sikloheksan olarak bilinen bir moleküle dönüştürülür. Siklohekzan üretmek için benzenin yaklaşık% 15'i kullanılır. Böcek ilaçlarından kauçuğa kadar her şeyde daha küçük miktarlar kullanılır.
Benzen yapısı iki şekilde çizilebilir. İlkinde, çift bağ karakteri açıkça çizilir. Kısa elli versiyonda, yapıyı göstermek için halkanın içine bir daire çizilir. Benzen içindeki her bir karbon atomuna bağlı tek bir hidrojen vardır.
Aşağıdaki I. ve II. çizimleri eştir. Pratikte III. çizim kullanılır.
Benzen, renksiz, alevlenebilen, kaynama noktası 80,1 °C, erime noktası 5,5 °C olan bir sıvıdır.
Binükleer Aromatik Hidrokarbonlar: Molekülünde iki benzen halkası içeren bileşiklerdir.
Hakkında
Kyäni, faydalı bileşenlerden oluşan besin takviyesi ürünlerini; benzersiz iş fırsatıyla birlikte dünya çapında 50'den fazla ülkeye ulaştırmaktadır. İdeal sağlığımızı korumak için günlük olarak Kyäni ürünlerini kullanırız, bu ürünleri başkalarıyla paylaşırız, işimizi inşa etmek ve sürdürmek için neredeyse her gün belirli bir saatimizi işe adarız ve başkalarını da Kyäni fırsatına dahil ederek veya Potato Pak ve Caring Hands programlarına katkı sağlayarak başarımızı başkalarıyla paylaşırız.
Hakkında
Kyäni, faydalı bileşenlerden oluşan besin takviyesi ürünlerini; benzersiz iş fırsatıyla birlikte dünya çapında 50'den fazla ülkeye ulaştırmaktadır. İdeal sağlığımızı korumak için günlük olarak Kyäni ürünlerini kullanırız, bu ürünleri başkalarıyla paylaşırız, işimizi inşa etmek ve sürdürmek için neredeyse her gün belirli bir saatimizi işe adarız ve başkalarını da Kyäni fırsatına dahil ederek veya Potato Pak ve Caring Hands programlarına katkı sağlayarak başarımızı başkalarıyla paylaşırız.
Sayfa Yapım Aşamasındadır.
Sayfa Yapım Aşamasındadır.
Schulungs- / Wissens- / Lösungsplattform
Polymerisation
Die Reaktionen, die zur Gewinnung von Polymereinheiten ausgehend von Monomereinheiten führen, werden als Polymerisation bezeichnet. Mit anderen Worten; Die Polymerisation ist die Kombination vieler identischer oder unterschiedlicher Monomere, um lange Ketten zu bilden, indem sie durch einen chemischen Prozess miteinander kombiniert werden.
In den meisten handelsüblichen Polymeren liegt das durchschnittliche Molekulargewicht zwischen 10 und 4 und zwischen 10 und 7. Polymer ist eine Mischung von Makromolekülen mit einer Molekulargewichtsverteilung. Die Viskosität ihrer geschmolzenen Formen und Lösungen ist ziemlich hoch. Da die Polymerisationsreaktion exotherm ist, muss die resultierende Wärme aus der Umgebung abgeführt werden, um die isothermen Bedingungen aufrechtzuerhalten.
Polymerisationsprozess, der bestimmte Katalysatoren erfordert; Es ist eines der beiden Hauptverfahren bei der Kunststoffherstellung (das andere ist die Polykondensation).
Monomere wie Ethylen und Propylen sind im Polymerisationsreaktor miteinander verbunden und bilden lange Polymerketten. Da das Monomermaterial in der Industrie nicht in einer Form vorliegt, die den Zweck erfüllen und verarbeitet werden kann, sind die zu verwendenden Rohstoffe Polymere (: Polymermaterialien). Polymermaterialien können bei niedrigeren Temperaturen verarbeitet werden und zeigen eine viel geringere Druck- und Wärmebeständigkeit als die beiden anderen.
Diese Situation, die auf den ersten Blick als Nachteil erscheint, wird als vorteilhaft beurteilt, wenn erkannt wird, dass polymere Materialien bevorzugter sind. Da sie bei niedrigeren Temperaturen verarbeitet werden können und eine geringere Dichte haben, sind sie leicht und daher viel besser in unser tägliches Leben integriert.
Sie haben auch den Luxus, an fast jedem Punkt zu erscheinen, den unsere Augen berühren. Tatsächlich können wir Dutzende, Hunderte von Polymermaterialien in derselben Umgebung erkennen, während unsere Metall- und Keramikmaterialerkennung die Finger einer Hand nicht überschreitet. Polymermaterial ist für fast jedes Produkt verfügbar, z. B. Stifte, Computer, Stühle, Verpackungsmaterialien, Halter, Kleiderbügel, Akten usw.
Wie oben angegeben, ist der Hauptgrund dafür, dass die Verarbeitbarkeit des Polymermaterials einfach und praktisch ist. Die folgende Situation sollte jedoch nicht vergessen werden; Es ist auch nicht bevorzugt, dass polymere Materialien direkt im Produktprozess verwendet werden. Im täglichen Leben, im Bereich der Partikelanwendung, sind eine Reihe von Additiven im Inhalt enthalten, um die Verwendbarkeit, Ästhetik, mechanische und thermische Beständigkeit des Produkts zu verbessern.
Monomer Bei der Polymerisation von Ethylen werden alle Monomere kombiniert, um eine Polymerstruktur zu erhalten, die ein Multimonomer ist.
Polymere können je nach Herstellungsverfahren und Interessen der Anwender auf verschiedene Weise klassifiziert werden. Beispielsweise befassen sich organische Chemiker mit der Anordnung von Atomen in Polymerketten; Für den Hochbau sind die Zugfestigkeit und Dichte des Polymers wichtig. Es gibt kein einzelnes System, das bei der Klassifizierung angewendet werden kann.
Es gibt Klassifikationen nach Polymerisationsmechanismus, Stöchiometrie / Additionsprozess, Struktur proliferierter Partikel, Ausgangsmethode, Reaktionsumgebung, Produktstruktur und Struktur der Reaktionssubstanz.


Polymerklassen
Polymere können je nach Herstellungsverfahren und Interessen der Anwender auf verschiedene Weise klassifiziert werden. Beispielsweise befassen sich organische Chemiker mit der Anordnung von Atomen in Polymerketten; Für den Hochbau sind die Zugfestigkeit und Dichte des Polymers wichtig. Es gibt kein einziges System für die Klassifizierung. Einige Klassifikationen werden in diesem Abschnitt kurz beschrieben.
Einstufung nach chemischen Anleihen:
(1) Duroplaste: Es tritt nicht in die Form einer Schmelze ein, die mit Wärme wiederaufbereitet werden kann.
(2) Thermoplaste: Sie können immer wieder einer Wärmebehandlung unterzogen werden. Es gibt keine Vernetzungen zwischen Polymerketten.
Klassifizierung nach Erhalt:
(1) Natürliche Polymere: aus Bäumen gewonnen.
(2) Synthetische Polymere: Als Beispiel kann Polyethylen angegeben werden, das das einfachste synthetische Polymer ist.
(3) Halbsynthetische / natürliche Polymere: Sie werden durch Modifizierung natürlicher Polymere erhalten.
Klassifizierung nach chemischen Eigenschaften:
(1) Organische Polymere: Sie enthalten Atome wie Wasserstoff, Sauerstoff, Stickstoff und Halogengase wie Fluor, Chlor, Brom, Jod, hauptsächlich Kohlenstoffatome in ihren Strukturen.
(2) Anorganische Polymere: Das Periodensystem enthält Elemente der 4. und 6. Gruppe anstelle von Kohlenstoffatomen in der Hauptkette des Polymers. Wie Silizium, Bor, Germanium.
Klassifizierung nach physikalischen Eigenschaften:
(1) Amorphe Polymere: Molekülketten liegen in Form von Wollkugeln vor, die zufällig miteinander verflochten sind.
(2) Kristalline Polymere: Alle Polymerketten sind in eine bestimmte Reihenfolge eingetreten oder kristallisiert.
Klassifizierung nach der Synthesemethode:
(1) Kondensationspolymere: Polymere, die durch Reaktion von zwei Monomeren und Freisetzung von Wasser gebildet werden.
(2) Kettenpolymere: Sie sind Polymere, die durch die Synthesereaktion des Öffnens einer Doppelbindung und des Verbindens von Monomeren wie Kettenringe gebildet werden.
Klassifizierung nach Anleihenstruktur:
(1) Lineare Polymere: wie Polyethylen hoher Dichte.
(2) Verzweigte Polymere: wie Polyethylen niedriger Dichte.
(3) Vernetzte Polymere: Wie vulkanisierter Kautschuk.
Klassifizierung nach dem Polymerisationsmechanismus: Die Klassifizierung ist eine vorteilhafte Methode; Denn bei dieser Art der Klassifizierung können wichtige Informationen über Reaktionsgeschwindigkeiten und Molekulargewichte von Polymeren erhalten werden.
Polymerisationen werden gemäß dem Bindungsbildungsmechanismus in zwei Grundklassen unterteilt:
(1) Stufenwachstumsreaktionspolymerisation,
(2) Polymerisation der Kettenwachstumsreaktion; Diese wiederum werden entsprechend der Struktur der Monomere und den Polymerisationsbedingungen in verschiedene Untergruppen unterteilt.
Die Stufenreaktionspolymerisationsmechanismen können in sechs Gruppen eingeteilt werden:
1. Carbonyladditionsspaltungsreaktionen: Direktreaktion, intermolekulare Austauschreaktion, Säurechlorid- oder Säureanhydridreaktion, Kondensationsreaktion zwischen Oberflächen, Ring- und Kettenbildungsreaktion.
2. Carbonyladditions-Substitutionsreaktionen.
3. Nucleophile Substitutionsreaktionen.
4. Doppelbindungsadditionsreaktionen.
5. Radikalbindung
6. Aromatische elektrophile Substitutionsreaktionen.
Einteilung nach Stuichiometrie:
Die klassische Klassifikation der Polymerisation basiert auf der Stöchiometrie. Die Additionspolymerisation wird gemäß IUPAC als "Polymerisation, die durch ein wiederholtes Additionsverfahren durchgeführt wird" definiert. Zusätzlich zur Polymerisation sind die Monomereinheiten miteinander verbunden und die wachsende Kette ist die Summe aller Atome in den Monomeren. Dies trennt die gesamte Additionspolymerisation von der Kondensationspolymerisation; Im letzteren Fall wird ein kleines Molekül wie Wasser, Chlorwasserstoff oder Ammoniak abgetrennt, während sich das Monomer in Polymeren verbindet.
In diesem Fall ist das Gewicht der durch Zugabe erhaltenen Polymere gleich der Summe des Gewichts der Monomereinheiten, während das Gewicht der durch Kondensation erhaltenen Polymere geringfügig geringer ist als die Summe der Gewichte der Monomere.
Die Begriffe "Zugabe" und "Kondensation" beziehen sich nur auf die stöchiometrische Bedeutung der Reaktion; Das heißt, es zeigt an, ob ein kleines Molekül wie Wasser in der Reaktion abgetrennt wird, beschreibt jedoch nicht den Reaktionsmechanismus. Die Begriffe Kettenreaktion und Stufenreaktion beschreiben den Reaktionsmechanismus.
Die Kondensationspolymerisation erfolgt durch Kondensationsprozesse durch Abtrennung einfacher Moleküle (IUPAC); Die gebildeten Produkte werden als Kondensationspolymer bezeichnet. Ester und Amide aus einfachen Kondensationsreaktionen von monofunktionellen Monomeren, Polyestern und Polyamiden werden aus den Reaktionen von difunktionellen Säuren und difunktionellen Alkoholen oder Aminen erhalten.
Klassifizierung nach der Struktur der reproduzierenden Partikel: Die chemische Struktur des aktiven Zentrums in der Proliferation schafft ein weiteres Klassifizierungsschema, insbesondere für die Vinylpolymerisation. Dementsprechend werden Polymerisationen als ionisch, radikalisch usw. klassifiziert. Ionenreaktionen werden auch in anionische, kationische und zwitterionische Polymerisation unterteilt. Ladungstransferkomplexe sind eine weitere Gruppe von Partikeln, die sich vermehren. Die Koordinationspolymerisation ist ebenfalls eine bekannte Art der Reaktion; Im proliferativen Schritt wird durch koordinierte Bindung ein Komplex gebildet. Diese Art der Polymerisation ist besser geeignet, um Additionspolymerisation zu nennen. Die Polymerisation mit Ziegler-Natta-Katalysatoren ist typisch. Wenn der Ausbreitungsschritt die Stereoregulation des Polymers beeinflusst, wird die Reaktion als stereopezifische Polymerisation bezeichnet.
Klassifizierung nach Startmethode:
Entsprechend der Wirkung des angewandten Polymerisationsverfahrens auf die Ausgangsreaktion werden Polymerisationen in verschiedene Klassen unterteilt, die katalysiert, thermisch, enzymatisch, elektrochemisch, mechanochemisch und strahlenbeeinflusst sind. Der Plasmazustand kann auch zum Starten verwendet werden. Das Wort Katalysator wird nicht viel für Initiationsreaktionen verwendet. Der Unterschied zwischen echten Katalysatoren und Initiatoren muss bekannt sein; Initiatoren befinden sich im Polymermolekül oder werden mit anderen Worten während der Reaktion verbraucht. Wenn eine Photonenquelle mit oder ohne chemische Initiatoren verwendet wird, spricht man von Photopolymerisation.
Klassifizierung nach Reaktionsumgebung:
Es gibt wichtige praktische und meist theoretische Unterschiede im Verhalten von Polymerisationen in Abhängigkeit von der Umgebung, in der die Reaktion durchgeführt wird. Daher wird die nach dem Polymerisationsmedium vorgenommene Klassifizierung häufig verwendet. In industriellen Anwendungen werden vier Polymerisationsverfahren verwendet. Dies sind Masse, Lösung, Suspension und Emulsion. In begrenztem Umfang werden auch Oberflächen- und Festkörperpolymerisationen angewendet. Polymerisationen können je nach Löslichkeit der Rohstoffe und des Produkts auch als homogen oder heterogen definiert werden.
Klassifizierung nach der Struktur des Produkts: Die am Ende der Polymerisation erhaltenen Produkte werden in verschiedene Klassen unterteilt. Klassifizierungen wie stereoregulär, Vernetzung, Isomerisierung, Ringöffnungspolymerisationen, Block- und Pfropfcopolymerisation können vorgenommen werden.
Die Struktur funktioneller Gruppen in Polymeren kann den Namen einer Polymerisationsreaktion bestimmen; wie Polyamidbildung und Polyesterisierung. Die physikalischen Eigenschaften der erhaltenen Polymere können auch zur Beschreibung von Reaktionen verwendet werden; Wie Perlenpolymerisation, Popcornpolymerisation.
Klassifizierung nach der Struktur der reagierenden Substanzen: Je nach Art der Reaktanten werden Polymerisationsprozesse in zwei wichtige Klassen unterteilt;
(1) Homopolymerisation ( Sie werden durch Wiederholen einer einzelnen Monomereinheit gebildet.)
(2) Copolymerisation ( Es ist ein Polymer, das aus einer Mischung von zwei Monomeren besteht.)
Abgesehen davon können einige einfache Klassifizierungen gemäß der Art der Reaktanten vorgenommen werden: Vinyl, Dien, Allyl, Harnstoff-Formaldehyd, Ethylenoxid-Polymerisation usw.
Polymerisation von PE
Polyethylen (: PE) ist ein thermoplastisches Polymer, dargestellt durch die allgemeine Formel (C 2 H 4) n, die als Ergebnis der Polymerisation von Ethylen aus Ethylen erhalten wird. (Gasförmiges Ethylen wird am Ende des Crackprozesses von Rohöl erhalten.
Eine sehr wenig angewandte Methode; Es ist eine Methode zur katalytischen Dehydrierung von Alkohol (: Ethanol). Es gibt drei Verarbeitungsmethoden.
Ethylen, das nach einem dieser Verfahren polymerisiert werden soll, wird zu einer festen Substanz, wenn es im gasförmigen Zustand hohem Druck und hoher Temperatur ausgesetzt wird. Die Polymerisation kann auf verschiedene Arten initiiert werden; durch Katalysatoren, Sauerstoff, Wärme oder Strahlung (Strahlung). Meist werden organische Peroxide als radikalische Katalysatoren bei der Herstellung von LDPE verwendet; Dazu gehören Peroxydicarbonate, Hydroperoxide und langkettige Peroxide. In der kommerziellen Produktion beträgt die Retentionszeit in der Reaktion 3 bis 15 Sekunden.
1- Hochdruck- und Temperaturmethode LDPE (0,910-0,925 g / cm3)
Bei diesem Verfahren wird Ethylen unter Atmosphärendruck von 1.000 bis 3.000 atm durch Erhitzen auf 150 bis 300 ° C mit Sauerstoff oder anderen Katalysatoren polymerisiert. Später, wenn es sich verfestigt, wird es hart und ölig. Schmelzpunkt
Es bleibt unter 110-120 ° C.
Andererseits ist zu sehen, dass die Verzweigungsrate in Molekülketten hoch ist. Beispielsweise werden in einer Kette von 1000 Kohlenstoffatomen etwa 80 Verzweigungen gebildet. Ihre Dichte ist gering. Polyethylen niedriger Dichte ist bis zu 75 ° C beständig und kann bei Temperaturen bis zu diesem Grad kontinuierlich verwendet werden. Polyethylen in dieser Gruppe ist zu 50-85% transparent. Der Transparenzgrad hat mit der Dichte zu tun. Je höher die Dichte, desto höher die Transparenz.
Polyethylen niedriger Dichte hat Eigenschaften wie Eignung für die Lebensmitteltechnologie, Eignung für die Verarbeitung und gute Formfüllung, da es nicht unter Spannung steht.
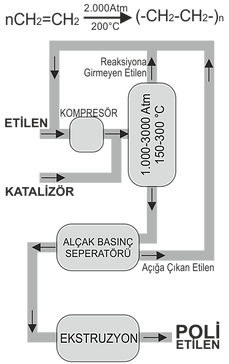
2- Mitteldruck- und Temperaturmethode MDPE (0,926-0,940 g / cm3)
Es wird bei 1.000-1.500 atm Atmosphärendruck und 100-150 oC polymerisiert.
3- Niederdruck- und Temperaturmethode HDPE (0,941 - 0,965 g / cm3)
Es wird durch Erhitzen unter 100 ° C und unter Verwendung verschiedener Katalyse-Systeme, die nur für diesen Zweck verwendet werden, polymerisiert.
Massenpolymerisation
Bei der Massenpolymerisation enthält das Reaktionsmedium nur Monomere, keine Lösungsmittel und suspendierende Flüssigkeiten. Die Ladung ist nur ein Monomer mit wenig Additiv. Bei den meisten Massenpolymerisationen ist der Polymerisationsinitiator im Monomer löslich. Es gibt jedoch auch Massenpolymerisationen unter Verwendung fester Katalysatoren, die in Monomeren unlöslich sind, wie bei der Herstellung von Polyethylen hoher Dichte (HDPE), das durch Polymerisation von Ethylen in der Gasphase erhalten wird.
Bei der Massenpolymerisation nimmt mit zunehmender Polymerkonzentration und Molekulargewicht die Viskosität des Mediums zu, die Mischeffizienz und die Wärmeübertragungsrate nehmen ab. Bei Massenpolymerisationen, bei denen die Umwandlungsmenge begrenzt ist, wird der Reaktorinhalt in einen zweiten Behälter überführt, um die Umwandlung zu vervollständigen oder das überschüssige Monomer zu entfernen.
Bei einigen Massenpolymerisationen wird der anfänglichen Ladung ein inertes Lösungsmittel zugesetzt, um eine Überhitzung zu verhindern und den Beginn der Polymerisation zu steuern; Das Lösungsmittel wird jedoch allmählich durch die Standardladung ersetzt. Einige Massenpolymerisationen können wie eine Lösungspolymerisation initiiert werden. Beispielsweise wird Poly (hexamethylendipamid) (Nylon 66) in einer wässrigen Lösung gestartet und dann als Massenpolymerisation abgeschlossen. Mit fortschreitender Reaktion werden das Verdünnungswasser und das bei der Polymerisation als Nebenprodukt gebildete Wasser abgedampft. Am Ende des Prozesses ist die Menge an Wasser, die in der Umwelt verbleiben kann, unbedeutend. Da das Verdampfen von Wasser die Polymerisationswärme verbraucht, wird Wärme hinzugefügt, um die erforderliche Umgebungstemperatur aufrechtzuerhalten.
Die Trennung des Nebenprodukts Ethylenglykol, das bei der Herstellung von Poly (ethylenterephthalat) entsteht, ist wichtig, da die Trennrate die Polymerisationsrate und -zeit beeinflusst. Da Ethylenglykol unter normalen Bedingungen nicht von der viskosen Polymerlösung abgetrennt werden kann, wird die letzte Stufe der Polymerisation im Vakuum durchgeführt.
Wenn das Polymer wie Polyvinylchlorid im Monomer unlöslich ist, wird am Ende der Reaktion eine Aufschlämmung erhalten, die das Polymer in fester Form im Monomer enthält. In diesem Fall wird ein zweistufiger Prozess angewendet. Im ersten Reaktor wird der Umsatz auf dem Niveau von 7-12% und im zweiten Reaktor auf dem Niveau von 80-85% gehalten. Die Polymeraufschlämmung fließt immer noch bei geringen Umsätzen. Polymerniederschläge setzen sich zusammen und halten das Monomer. Bei 15 bis 20% Umsatz enthält der Reaktor das mit Monomer gequollene Polymer in einer Monomeratmosphäre. Mischer verhindern die Bildung großer Polymermassen. Das in das ausgefällte Polymer diffundierte aktive Monomer polymerisiert, das nicht umgesetzte Monomer wird gewonnen.
Massenpolymerisation ist in kommerziellen Anwendungen aufgrund ihrer Volumeneffizienz, geringen Verschmutzung und der Notwendigkeit von Lösungsmittelrückgewinnungs- und -reinigungsprozessen ziemlich häufig. Studien zur Suche nach neuen Technologien zu diesem Thema sind ebenfalls im Gange.
Lösungspolymerisation
Es gibt keine klare Unterscheidung zwischen Lösungspolymerisation und Massenpolymerisation; manchmal wird Massenpolymerisation in Lösungspolymerisation klassifiziert. Die Lösungspolymerisation verwendet ein Lösungsmittel, das das Monomer und das Polymer löst; Das Lösungsmittel / Monomer-Verhältnis ist bei der Massenpolymerisation viel größer als das Verhältnis "Lösungsmitteladditive" / Monomer. Die Lösung ist eine homogene Phase, deren Viskosität mit zunehmendem Molekulargewicht und zunehmender Konzentration des Polymers zunimmt.
Die Lösungspolymerisation ähnelt der Massenpolymerisation; Selbst inerte Lösungsmittel beeinflussen jedoch die Reaktionsgeschwindigkeit oder den Diffusionsprozess. Wenn das Verdünnungsmittel nicht inert ist (Eigenschaften wie Kettenübertragung, polare Effekte usw.), ändern sich die Reaktionsgeschwindigkeit und die Eigenschaften des Polymers erheblich.
Wenn das Monomer ein Gas ist, kann das Lösungsmittel nur einen Teil des Monomers halten. Während das lösliche Monomer infolge der Polymerisation abgetrennt wird, gelangt etwas Monomer aus der Gasphase in das Lösungsmittel. Die effektiven Stoffübergangsraten hängen hier vom Mischungsgrad, dem Reaktordruck und der Viskosität der Polymerisation ab.
Der bei der Lösungspolymerisation verwendete Initiator oder Katalysator ist im Verdünnungsmittel löslich oder unlöslich. Unlösliche Katalysatoren komplexieren mit dem Monomer und lenken es, so dass die wachsenden Polymerketten und damit das Polymer eine glatte Struktur aufweisen. Der bei der Polymerisation von Propylen verwendete Katalysator vom Ziegler-Typ ist in Verdünnungsmedien unlöslich. Lineares Polyethylen wird auch mit unlöslichen Katalysatoren hergestellt. Die Entfernung des Katalysators aus der Lösung nach der Polymerisation ist ein schwieriger Prozess.
Die Verdünnung von Monomer und Polymer mit Lösungsmittel verringert die Wärmebelastung und Viskosität im Vergleich zur Massenpolymerisation. Einige Lösungsmittel beeinflussen die Geschwindigkeit, den Grad, die Molekulargewichtsverteilung und die Produkteigenschaften der Polymerisation.
Lösungspolymerisationen, bei denen das Polymer und seine Lösung zusammen verwendet werden, sind sehr vorteilhaft, wie bei der Herstellung von Schutzbeschichtungen. Diese Methode ist in der Textilindustrie weit verbreitet. Nachdem das nicht umgesetzte Monomer abgetrennt wurde, wird die Polymerlösung direkt verwendet, indem es in einen Weichmacher (z. B. DOP) gegossen wird.
Damit das Polymerprodukt in fester Form vermarktet werden kann, muss es von seinem Lösungsmittel und seinem Katalysator getrennt werden. Diese Prozesse erfordern sehr teure Ausrüstung und Energieverbrauch. Aus diesem Grund werden Studien durchgeführt, um das Lösungsmittel / Monomer-Verhältnis bei Lösungspolymerisationen zu verringern. Das optimale Lösungsmittel / Monomer-Verhältnis wird gemäß dem wirtschaftlichen Gleichgewicht zwischen dem Preis des Produkts, das aus Lösungen mit hoher Viskosität und hohem Polymer erhalten wird, und dem Preis für die Trennung und Rückgewinnung des Lösungsmittels bestimmt. Möglicherweise ist eine Reinigung erforderlich, um das Lösungsmittel wiederzuverwenden.
Suspensionspolymerisation (oder Niederschlagspolymerisation)
Sie traten in die Suspensionspolymerisation ein und das Polymer wird in einem nicht lösungsmittelhaltigen Medium (meistens Wasser) dispergiert, kräftig gerührt, um das Monomer in kleinen Tröpfchen zu dispergieren und die dispergierten kleinen festen Polymerteilchen suspendiert zu halten. Die Suspensionspolymerisation wird aufgrund der kugelförmigen Struktur der Polymerteilchen auch als "Perlen" - oder "Perlen" -Polymerisation bezeichnet. Die Polymerteilchen haben einen Durchmesser von 0,15 bis 5 mm und setzen sich ab, sobald das Mischen gestoppt wird. Der Initiator löst sich häufig im Monomer; Die Polymerisation wird in Monomertröpfchen initiiert und verläuft wie eine Miniaturmassenreaktion. In dem Fall, in dem sich das Monomer in der Wasserphase löst, sich das Polymer jedoch nicht löst, wird die Polymerisation in der wässrigen Phase eingeleitet. Die wachsende Polymerkette kollabiert zu einem Polymerkern, absorbiert Monomer- und Initiatorradikale und wächst zu körnigen Polymerteilchen.
Suspendierer (Stabilisatoren) verhindern die Dispersion des Monomers, die Anordnung von Monomertröpfchen und Polymerteilchen untereinander. Die Größe der Monomertröpfchen und die Größe, Porosität und Schüttdichte der Polymerteilchen variieren in Abhängigkeit vom Wasser / Monomer-Verhältnis, der Art und Konzentration des Initiators, der Struktur und Konzentration des Stabilisators, der Mischgeschwindigkeit und der Polymerisationstemperatur . Die Suspensionspolymerisation wird insbesondere bei der Polymerisation von reaktiven Monomeren angewendet, die durch radikalische Polymerisation erhalten werden. Das Wasser schluckt die Hitze sofort; Das Fluidgemisch überträgt die Wärme an die Reaktoroberfläche. Das Gemisch kann in normalen Systemen gepumpt und gehandhabt werden.
Ein Nachteil der Suspensionspolymerisation besteht darin, dass ein zusätzlicher Prozessschritt erforderlich ist, der die Trennung des Polymers vom Verdünnungsmittel und damit von Vorrichtungen erfordert. Die Trennung kann durch Zentrifugation oder Filtration erfolgen, dann wird das Polymer getrocknet; Diese Methode ist eine Methode, bei der die geringste Energie und Vorrichtung verwendet wird. Partikelgröße und -dichte beeinflussen die Trennleistung und die Retention der wässrigen Phase zwischen Polymerpartikeln. In Polymeren mit hoher Dichte ist sehr wenig Wasser enthalten. Wenn das Polymer später mit Weichmachern imprägniert werden soll, ist auch die hohe Viskosität des Polymers ein wünschenswertes Merkmal. Das Verdünnungsmittel / Monomer-Verhältnis muss verringert werden, um die Reaktoreffizienz und die Polymerdichte zu erhöhen. Wasser wird hauptsächlich als Verdünnungsmittel bei Suspensionspolymerisationen verwendet. Es gibt Suspensionspolymerisationen unter Verwendung organischer Lösungsmittel (mit Methanol) sowie bei der Copolymerisation von Styrol und Acrylnitril.
Emulsionspolymerisation
Die Emulsionspolymerisation hat ein Dispergiermedium, hauptsächlich Wasser. Monomertröpfchen und Polymerteilchen sind viel kleiner als bei der Suspensionspolymerisation; Mit einem Emulgator wird eine stabile Umgebung namens "Latex" geschaffen. Der Durchmesser der Monomertröpfchen, die durch anfängliches Mischen bereitgestellt werden, beträgt 1 bis 10 mm. Der Emulgator verteilt eine kleine Menge Monomer in Clustern, die als "Mizellen" bezeichnet werden. Mit fortschreitender Polymerisation werden Polymerkerne durch Wachstum kolloidal dispergierter Polymerteilchen mit einem Durchmesser von 0,1 bis 0,3 mm gebildet. Ein mäßiges Mischen ist ausreichend, um das Monomer, den Initiator und das Polymer homogen zu verteilen und die freigesetzte Wärme an die Reaktoroberfläche zu leiten. Ein kräftiges Mischen ist nicht geeignet, da es die Koaleszenz der Polymerteilchen verursacht. Die Emulsionspolymerisation ist hochkomplex und es wurden verschiedene Mechanismen zur Initiierung von Polymerteilchen vorgeschlagen. Normalerweise ist die Viskosität der Emulsionspolymerisation sehr niedrig und das flüssige Medium überträgt die freigesetzte Wärme auf die Kühlflächen des Reaktors. Mit dieser Methode werden handelsübliche Mischungen hergestellt, die direkt aufgetragen werden können, z. B. Farben, Papierüberzüge, Teppichunterlagen und verschiedene Klebstoffe.
Wenn das Polymer in fester Form erhalten werden muss, wird die Suspensionspolymerisation häufig der Emulsionspolymerisation vorgezogen; Da die suspendierten Partikel größer sind, sind die Trenn- und Trocknungsprozesse einfacher. Kolloidal dispergierte Polymerteilchen müssen ausgefällt werden, damit die Teilchen groß genug sind, um das Polymer von der Emulsion zu trennen. Einige Elastomere wie Butadienkautschuke und Acrylelastomere werden durch ein Emulsionspolymerisationsverfahren hergestellt. Der Kautschuklatex wird ausgefällt, um Partikel zu erhalten, die für Filter- und Trocknungsprozesse geeignet sind.
Polymerisation zwischen Oberflächen
Die Polymerisation zwischen den Oberflächen findet an der Oberfläche zwischen zwei unlöslichen Flüssigkeiten statt; Eines der Lösungsmittel löst ein Monomer (A) und das andere ein anderes Monomer (B). Das zwischen den Oberflächen der Lösungsmittel gebildete Polymer ist fest. Wenn die Flüssigkeiten nicht gemischt werden, wird ein fester Polymerfilm zwischen der Oberfläche erhalten. Der Film kann in Form einer durchgehenden Schnur durch die Oberfläche gezogen werden. Die Polymerisation wird fortgesetzt, da die Flüssig-Flüssig-Oberfläche durch Entfernen des Films aus den Flüssigkeiten wieder gebildet wird.
Durch Schütteln der nicht mischbaren Flüssigkeiten können Polymere mit verbesserten Eigenschaften erhalten werden. Das Verfahren ist im Allgemeinen die Reaktion zwischen dem Disäurechlorid einer in einem inerten Lösungsmittel gelösten Dicarbonsäure und einem in Wasser gelösten Bisphenol oder Diamin mit einer anorganischen Base. Die Reaktionsgeschwindigkeit des Prozesses bei niedrigen Temperaturen ist hoch.
In Japan und Russland werden nach dieser Methode große Mengen aromatischer Amine hergestellt. Die Polymerisation zwischen den Oberflächen wird in den USA bei der Herstellung von Polycarbonaten verwendet. Eine typische Herstellung von Polycarbonat ist mit Phosgen und Bisphenol A. Phosgen wird zu Bisphenol A gegeben, das in einem gemischten inerten organischen Lösungsmittel und einer wässrigen Natriumhydroxidlösung dispergiert ist. An der Oberfläche findet eine Reaktion zwischen organisch-wässrigen Phasen statt. Die Polykondensation kann durch ein tertiäres Amin katalysiert werden. Durch Abschließen der Ketten mit einer monofunktionellen Hydroxyverbindung wie Phenol kann das Molekulargewicht des erhaltenen Produkts gesteuert werden. Das Polymer löst sich in der organischen Phase.
Festkörperpolymerisation
Festkörperpolymerisation wird in der Industrie verwendet, um das Molekulargewicht von Kondensationspolymeren zu erhöhen. Es gibt bifunktionelle Endgruppen an den Kondensationspolymerketten, sofern sie nicht mit einer Verunreinigung oder einem Stopfen reagieren. Diese Endgruppen können es Polymermolekülen ermöglichen, sich miteinander zu verbinden. Polymere mit höherem Molekulargewicht werden erhalten, indem einige feste Polymere wie Nylon-66 unter ihren Schmelzpunkt erhitzt werden.
Prozesse
Stapelbetrieb:
Im Batch-Verfahren werden zunächst alle Substanzen in den Reaktor gegeben und bleiben bis zum Ende der Reaktion zusammen. Ein stabiler Zustand kann nicht erreicht werden. Während der Polymerisation ändert sich die Polymerisationstemperatur. Oft gibt es eine Einarbeitungszeit; Zuerst wird eine schnelle Zunahme der Polymerisationsrate und dann eine Abnahme mit der Abnahme des Monomers beobachtet. Daher muss der Reaktor in der Lage sein, schnell zu heizen, ausreichend zu kühlen und die Temperatur zu steuern. Das Chargensystem eignet sich für Polymerisationsprozesse, bei denen hohe Umsätze erwünscht sind. Es treten jedoch Probleme bei der Steuerung der Reaktionen auf, so dass jede Charge die gleichen Eigenschaften enthält. Diese können durch verbesserte Steuerungssysteme minimiert werden.
Semi-Stack (oder Semi-Continuous) -Prozess:
In einem Semi-Batch-Verfahren können einige der Substanzen in Portionen oder zu unterschiedlichen Zeiten zugesetzt oder einige Nebenprodukte entfernt werden. Um die Reaktionsbedingungen gut zu kontrollieren, werden Katalysator, Monomer usw. nach einem festgelegten Zeitplan zugegeben.
Bei der radikalischen Polymerisation von Copolymeren ist es wichtig, Monomere in Portionen zuzugeben, wenn sich ihre Monomerreaktivität zu stark ändert; Die freigesetzte Wärme wird gleichmäßig verteilt.
Bei einigen Halbchargenpolymerisationen werden zunächst alle Substanzen in den Reaktor gegeben. Damit die Reaktion abgeschlossen sein kann, müssen die entstehenden Nebenprodukte möglicherweise aus der Umgebung entfernt werden. Während diese durch Verdampfung abgetrennt werden, wird in einigen Fällen auch die Polymerisationswärme abgeführt, in einigen Fällen ist zusätzliche Wärme erforderlich, um die Reaktion zu vervollständigen.
Dauerbetrieb:
In einem kontinuierlichen Prozess werden Materialien kontinuierlich durch Messsysteme in den Reaktor eingespeist und das Material wird kontinuierlich entfernt. Wenn der Polymerisationsprozess einen stabilen Zustand erreicht, ist die an jedem Punkt im System freigesetzte Wärmemenge konstant.
Der kontinuierliche Betrieb ist einfach und eine Produktionsmethode, die die Kosten senkt. Aus diesem Grund werden kontinuierliche Systeme empfohlen, insbesondere für großvolumige Polymerisationsprozesse. Für kleine Mengen von Spezialprodukten werden Batch- oder Semi-Batch-Verfahren bevorzugt, die flexibler als die kontinuierliche Verarbeitung sind und die Herstellung vieler verschiedener Polymerqualitäten ermöglichen. Einige kommerzielle Polymere werden nur unter Verwendung von Chargentechniken hergestellt, um die gewünschten physikalischen Eigenschaften zu erfüllen.
Struktur von Polymeren
Molekulargewichtsdurchschnitte und -verteilungen
Nur weil alle Polymerketten in einem Polymer aus einer einzigen Baueinheit bestehen, bedeutet dies nicht, dass alle Ketten gleich sind. Die Unterschiede sind hauptsächlich auf die Abmessungen der Ketten und ihre Abweichung von der Linearität zurückzuführen. Dies ist ein Ergebnis der statistischen Bildung und Kinetik des Polymerisationsprozesses.
Es sei angenommen, dass die im Polymerisationsprozess gebildeten Polymerketten linear sind und unterschiedliche Anzahlen von Struktureinheiten enthalten. Die Anzahl der Gebäudeeinheiten wird als "Polymerisationsgrad (DP)" bezeichnet und ist der quantitativste Ausdruck, der eine Polymerkette beschreibt. In der Praxis wird das Konzept des Molekulargewichts (MW) für den gleichen Zweck verwendet. Wenn die chemische Struktur der Baueinheit bekannt ist, ist die Berechnung des Molekulargewichts recht einfach; für Polystyrol zum Beispiel das Molekulargewicht der Baueinheit,
Da M1 = 104 g / g mol ist, beträgt das Molekulargewicht der Polymerkette:
MW = M1 x DP
Für eine Polystyrolkette mit MW = 100000:
DP = 100000/104 ~ 1000
Ein Polymer ist eine Sammlung von Polymerketten, die etwa 1019 verschiedene Längen pro 1 cm³ enthalten. Der Begriff "Durchschnitt" wird benötigt, um das Molekulargewicht der Ketten in einem solchen Polymer zu beschreiben.
Struktureinheiten in einer Polymerkette weichen vom "linearen" Muster entlang der Skelettkette ab. Neben- oder Nebenreaktionen während der Polymerisation führen zur Bildung von Seitenketten oder zur Verzweigung. Abhängig von den Polymerisationsbedingungen zeigen die Verzweigungen unterschiedliche Formen. Zweige können in Form von wenigen, aber langen Zweigen sowie in Form von vielen, aber kurzen Zweigen vorliegen. Diese beiden Fälle sind Beispiele für zwei Extremfälle. Eine normale Verzweigung ist ein gemischter Verzweigungszustand mit langen und kurzen Seitenketten.
Amorphe Struktur:
Abhängig von der Konformation (Form) der Polymerketten liegen Polymere in zwei Formen vor: amorph oder kristallin. Das Wort "amorph" bedeutet amorph und bedeutet das Fehlen einer speziellen Ordnung für das Polymer.
Es gibt keine organisierte Ordnung in der Molekülstruktur eines amorphen Polymers. Amorphe Polymere bestehen hauptsächlich aus ataktischen Polymerketten. Dies führt dazu, dass es nicht kristallin ist. Daher ist es eine schwache Struktur. Da es sich um amorphe Polymere handelt, da sie keinen Kristallinitäts- oder Kristallinitätsgrad aufweisen, weisen sie im Vergleich zu kristallinen Polymeren eine geringe Dichte auf. Daher ist die chemische Beständigkeit gering und transparent. Es gibt schwache Anziehungskräfte unter Polymerketten aufgrund des Fehlens einer strukturierten Struktur. Beispiele für amorphe Polymere umfassen Polyethylen, PVC usw. Es gibt. Der Kristallinitätsgrad wird durch den Polymerisations- und Herstellungsprozess beeinflusst. Amorphe Polymere können unter Bildung von Kristalliten oder regelmäßigen Bereichen Kristallinität aufweisen. Diese sind weicher und weniger beständig gegen das Eindringen von Lösungsmitteln.
Alle Polymere sind in Lösung bei ausreichend hohen Temperaturen amorph und einige (fast die Hälfte) der wichtigsten kommerziellen Polymere sind amorph. Die amorphe Form einer einzelnen Polymerkette kann mit einer Perlenkette verglichen werden, die verschiedene Konfigurationen annehmen kann. Wenn eine solche Kette zu Boden geworfen wird, kann sie verstreut, aber in der Handfläche gesammelt werden. In diesen beiden Fällen sind die Detaileigenschaften der Kette unterschiedlich, aber die allgemeine Struktur ist dieselbe.
Vernetzung und molekulares Netzwerk (Netting):
Bisher wurde erwähnt, dass ein Polymer eine Ansammlung von Polymerketten ist, die unabhängig voneinander sind, und dass in jeder Kette nur intramolekulare chemische Bindungen existieren. Diskontinuierliche physikalisch-chemische Wechselwirkungen zwischen Ketten sind sehr schwach und nehmen mit zunehmender Temperatur ab; Die Abnahme setzt sich bis zu der Temperatur fort, bei der sich die unabhängigen Ketten auseinander bewegen und sich frei bewegen und flüssig werden.
Diese Art von Polymer wird auch als "thermoplastisches" oder "lineares Polymer" bezeichnet.
Geklemmte polymere Netzwerke (IPN):
Einige kommerzielle Polymersysteme werden mit der Technologie des interpenetrierenden Netzwerks hergestellt. Obwohl chemische Netzwerke sich mit stabilen chemischen Bindungen oder Vernetzungen befassen, bilden sich manchmal physikalische Netzwerke, die bei hohen Temperaturen verschwinden. Das Polymersystem ist in chemischen Netzwerken duroplastisch und in physikalischen Netzwerken thermoplastisch.
Es gibt viele kommerzielle IPN-Systeme. Einige von ihnen sind eine Kombination aus Silikonnetzwerken, Thermoplasten (PA, PET, PBT, PP, PMO usw.), herkömmlichen Elastomeren (EPDM, Ethylenacrylat, EVA usw.), thermoplastischen Elastomeren (TPE) oder Duroplasten (Polyurethane) ). Ein weiterer Teil sind die Kombinationsprodukte von Urethanen mit Acryl-, Epoxid- oder Polyesterharzen, PS usw.; Bei einigen Produkten handelt es sich um Dreikomponentensysteme. Sie verbinden sich mit Isocyanaten und Dicyanaten, Acrylaten, PC, PESU und Polyestercarbonaten.
Kristallstruktur
Es zeigt eine geordnete Reihenfolge der Polymermoleküle. Kristalline Polymere haben eine geordnete Struktur aus syndiotaktischen und isotaktischen Polymerketten. Diese geordnete Struktur bewirkt, dass das Polymer durchscheinend ist. Es gibt auch starke Anziehungskräfte zwischen Molekülen. Daher ist es chemikalienbeständig und hat im Vergleich zu amorphen Polymeren eine hohe Dichte. Obwohl kristalline Polymere gut sortiert sind, kann es auch amorphe Bereiche geben. Daher werden diese Polymere als teilkristalline Materialien bezeichnet.
Kunststoffmaterialien wie Nylon und andere Polyamide weisen kristalline Strukturen auf. Andere Beispiele umfassen lineares Polyethylen, PET (Polyethylenterephthalat), Polypropylen usw. Stattfinden. Dies sind starre Strukturen, die weniger vom Eindringen von Lösungsmitteln betroffen sind.
Amorpher und Kristallunterschied
Geometrie / Struktur:
Amorphe Feststoffe: Amorphe Feststoffe haben keine regelmäßige Struktur. Ihnen fehlt jede Anordnung oder Anordnung von Atomen oder Ionen oder irgendeine geometrische Form.
Kristallfeststoffe: Kristalline Feststoffe haben aufgrund der regelmäßigen Anordnung von Atomen oder Ionen eine präzise und regelmäßige Geometrie.
Schmelzpunkt:
Amorphe Feststoffe: Amorphe Feststoffe haben keinen scharfen Schmelzpunkt.
Kristallfeststoffe: Es hat einen scharfen Schmelzpunkt, bei dem Kristallfeststoffe flüssig werden.
Schmelzwärme:
Amorphe Feststoffe: Amorphe Feststoffe haben nicht die charakteristische Schmelzwärme und werden daher als unterkühlte Flüssigkeiten oder Pseudofeststoffe betrachtet.
Kristalline Feststoffe: Kristalline Feststoffe haben eine gewisse Schmelzwärme und gelten daher als echte Feststoffe.
Anisotropie und Isotropie:
Amorphe Feststoffe: Amorphe Feststoffe sind isotrop, da sie in alle Richtungen die gleichen physikalischen Eigenschaften aufweisen.
Kristallfeststoffe: Kristallfeststoffe sind anisotrop und daher unterscheiden sich ihre physikalischen Eigenschaften in verschiedene Richtungen.
Häufige Beispiele:
Amorphe Feststoffe: Glas, organische Polymere usw. sind Beispiele für amorphe Feststoffe.
Kristallfeststoffe: Diamant, Quarz, Silizium, NaCl, ZnS, Cu, Zn, Fe usw. Metallelemente sind Beispiele für kristalline Feststoffe.
Interpartikelkräfte:
Amorphe Feststoffe: Amorphe Feststoffe haben kovalent gebundene Netzwerke.
Kristallfeststoffe: Kristallfeststoffe haben kovalente Bindungen, Ionenbindungen, Van-der-Waal-Bindungen und Metallbindungen.
Einige Kondensationspolymere: Polymerisationsmethoden und -eigenschaften
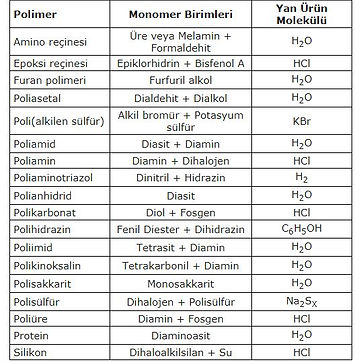

Copolymer / Homopolymer
Die Polymerkette, die aus Einheiten vom einen Typ besteht, wird als Homopolymer bezeichnet, und Polymere, die zwei oder mehr Monomere enthalten, werden als Copolymere bezeichnet.
Wenn ein einzelner Monomertyp in die Polymerisation übergeht, um ein Makromolekül zu bilden, nennen wir es Homopolymer. Mit anderen Worten, es gibt eine sich wiederholende Einheit. Polystyrol ist beispielsweise ein Homopolymer, bei dem die Wiederholungseinheit Styrolreste sind.
(Einige übliche Beispiele für Homopolymere umfassen Nylon 6, Nylon 11, Polyethylen, Polypropylen, PVC oder Polyvinylchlorid, Polyacrylnitril usw.)
Copolymere bestehen jedoch üblicherweise aus statistischen Kombinationen verschiedener Monomere, um ein statistisches Copolymer zu bilden. Alternative Block-, Transplantat- und Steroblockcopolymere sind jedoch von dieser Regel ausgeschlossen. In dem alternativen Copolymer kommen die Monomereinheiten nacheinander. Das Blockcopolymer enthält lange Segmente verschiedener Homopolymere. Das Pfropfcopolymer oder mit anderen Worten das Pfropfcopolymer enthält ein zweites Monomer als Verzweigung an einer im wesentlichen vorhandenen Polymerkette.
Polymere werden auch als linear, verzweigt und netzwerkartig definiert. Es gibt keine Verzweigung im linearen Polymer (A). Pfropfcopolymere sind ein Beispiel für verzweigte Polymere (B). Netzwerkpolymere entstehen, wenn anstelle von difunktionellen Monomeren polyfunktionelle Monomere verwendet werden. Netzwerkpolymere umfassen auch vernetzte Polymere (C). Denn durch Vernetzung verlieren Polymerketten ihre Beweglichkeit. Aus diesem Grund können sie nicht geformt werden, da sie nicht schmelzen oder fließen. Mit anderen Worten fallen sie in die oben erwähnte Gruppe von duroplastischen Polymeren.
Der Hauptunterschied zwischen Copolymer und Homopolymer besteht darin, dass in Copolymeren zwei Monomere das Polymer bilden, während in Homopolymer nur ein Monomer das gesamte Polymer wiederholt und bildet. (In einem Homopolymer wiederholt sich ein Monomer und bildet das gesamte Polymer. Im Gegensatz dazu gibt es zwei Monomere im Copolymer, aus denen das Polymer besteht. Dies ist also der Hauptunterschied zwischen Copolymer und Homopolymer. Auch ein weiterer Unterschied zwischen Copolymer und Homopolymer ist Es gibt verschiedene Arten von Copolymeren, abhängig davon, wie die beiden Monomere kombiniert werden. Es gibt verschiedene Möglichkeiten, zwei Monomere zu verbinden. Diese Art der Kopplungsvariation kann jedoch in einem Homopolymer nicht beobachtet werden.)
Polymere und Marken
Die Namen von Polymerverbindungen sind eher eine Terminologie und erfordern eine gewisse Chemie, um sie auszusprechen. Aufgrund der langen und schwierigen Aussprache sind sie auf dem Markt meist mit den von den Erfindern oder Herstellern angegebenen Marken bekannt. Einige davon sind wie folgt;
Phenol-Formaldehyd-Harz >> Bakelit
Para-Aramid >> Twaron
Polyethylenterephthalat >> Mylar
Polychloropren >> Neopren
Meta-Aramid-Polymer >> Nomex
Polyacrylnitril >> Orlon
Polyamid >> Nylon
Polyamid 11 und 12 >> Rilsan
Polytetrafluorethylen >> Teflon
Polyimid >> Ultem
Aromatischer Polyester >> Vectran
Polytetrafluorethylen >> Viton
Polyphenylen-2, Benzobisoxazol >> Zylon


SAP (Super Absorbent Polymer) (Super Absorbent Polymer)
SAP-Materialien sind hydrophile Netzwerke, die große Mengen Wasser oder wässrige Lösungen absorbieren und zurückhalten können. Sie können bis zu 100.000% ihres Volumens aufnehmen. Sie können das 300- bis 1000-fache ihres Gewichts in wässrigen Flüssigkeiten aufnehmen. Sobald sie anfangen zu saugen, fangen sie die Flüssigkeit ein und geben sie nicht ab. Daher ist es ein ideales Material für die Verwendung in Produkten, die Flüssigkeiten wie Windeln / Windeln, Servietten und Papierhandtücher, Inkontinenzprodukte sowie Damenhygienepads und -einlagen enthalten.
Landwirtschaftliche Abdeckungen halten das Wasser im Boden, insbesondere auf Reisfeldern. Die ersten kommerziellen Anwendungen kamen 1978 in unser Leben.
Die meisten bestehen aus Natriumpolyacrylat und sind in Granulatform oder als Fasern erhältlich. Das körnige Material ist ein Polymer, das aus Millionen identischer Natriumacrylateinheiten besteht, die zu einer kettenzaunartigen Struktur geformt sind. Diese werden dann miteinander verbunden, um das Material zu einem dreidimensionalen Netz zu formen. Im trockenen Zustand sind lange Polymerketten gewickelt. Wenn sie Flüssigkeit aufnehmen, lösen sie sich auf und das Netz dehnt sich aus. Die Flüssigkeit wird dann in Hohlräumen im molekularen Netzwerk gespeichert, und das Material bildet ein Gel, das die Flüssigkeit einschließt.
Die Hauptkomponenten sind Acrylsäure, Natriumhydroxid (oder ein ähnliches Neutralisationsmittel) und Wasser sowie ein Vernetzer, der die Brücke bildet, die eine Polymerkette mit einer anderen verbindet. Diese Lösung wird gemischt und durchläuft einen Polymerisationsprozess, um dreidimensionale Polymerkettennetzwerke zu bilden. Und es hat die Form eines wässrigen Gels. Das Granulat wird gemahlen und auf die gewünschte Partikelgröße gesiebt. Zu diesem Zeitpunkt kann das superabsorbierende Material weiter vernetzt werden, um materialspezifische Absorptionseigenschaften zu verleihen.
Viele SAP-Typen können durch monomere und makromolekulare Strukturänderungen hergestellt werden. Zunächst werden superabsorbierende Polymere in zwei Hauptklassen unterteilt: synthetische (auf Petrochemie basierende) und natürliche (auf Polysaccharid und Polypeptid basierende).
Die meisten der vorhandenen Superabsorbentien werden jedoch aus Acrylsäure (AA) durch Lösungs- oder inverse Suspensionspolymerisationstechnik hergestellt. Darüber hinaus sind die Unterklassifizierungskriterien:
-
Entsprechend seinen praktischen Eigenschaften (Absorptionsvermögen)
-
Entsprechend der Quellgeschwindigkeit (Sauggeschwindigkeit)
-
Je nach Stärke der gequollenen (gesättigten) Gelform
-
Je nach Monomer- und Ionenempfindlichkeit
Superabsorbentien haben eine nachgewiesene Geschichte der sicheren Anwendung und werden von Kinderärzten in den Bereichen Toxikologie, Allgemeinmedizin, Krankenpflege und Körperpflege allgemein akzeptiert.
Wenn die Haut zu feucht gehalten wird, können Reizungen und schädliche Bakterien einen Lebensraum finden. Sie halten die Haut trocken, indem sie Flüssigkeit aus der Haut extrahieren und die Essenz des Produkts absorbieren und festhalten. Diese Situation schafft natürlich mehr Komfort für den Benutzer. Sie schützen Windelbenutzer vor Hautreizungen, indem sie die Hautfeuchtigkeit reduzieren. Zusätzlich zu dieser Kette tragen sie dazu bei, die Ausbreitung von Infektionen zu verhindern. Das Zurückhalten von Flüssigkeit im superabsorbierenden Kern verringert die Leckage. Es verringert auch das Risiko einer Vermischung des Urins mit Fäkalien und einer Kontamination mit Mikroorganismen, was zur Ausbreitung von Krankheiten wie Durchfall und Gastroenteritis führen kann. Viele Menschen leiden aufgrund von Krankheit, Behinderung oder Alter an einem Mangel an Blasen- oder Darmkontrolle. Einwegprodukte, die Superabsorber enthalten, helfen vielen dieser Personen und ihren Betreuern, ihre Lebensqualität mit größerer Mobilität und Unabhängigkeit aufrechtzuerhalten.

.png)
Polykondensation
Polymerisation; Es ist das grundlegendste der Polymerisationsarbeiten und wurde oben in vielen Details erklärt. Die Polymerisationsreaktion ist jedoch nicht auf die Polymerisation beschränkt.
Grundsätzlich werden Polymerisationsreaktionen unter drei Hauptüberschriften zusammengefasst.
-
Die Polymerisation ist die Reaktion des Kombinierens derselben Monomere unter Bildung einer Monomerkette (Polymer). (Polyacrylnitril, Polyvinylchlorid, Polyvinylidenchlorid, Polyvinylalkohol, Polyolefin, Polytetrafluorethylen)
-
Polyaddition sind die Polymerisationsreaktionen, bei denen ein anderes Molekül an ein Molekül gebunden wird, das eine Doppelbindung enthält. (Polyurethan)
-
Die Polykondensation ist eine Reaktion, bei der Monomere mindestens zwei reaktive Gruppen aufweisen, was zu niedermolekularen Verbindungen wie Wasser und Ammoniak führt. (Polyester, Polyamid 6,6)
+
+

Polykondensationsreaktionen hängen mit der kovalenten Bindung von Monomermolekülen zusammen, was zu Polymeren mit hohem Molekulargewicht oder einem Alkohol mit niedriger Kohlenstoffzahl unter Freisetzung eines kleinen Moleküls wie Wasser führt.