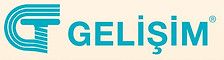


Hidrokarbonlar
Hidrojen ve karbon olmak üzere iki elementten oluşan organik bir bileşiktir. Petrol bileşiminin büyük bir kısmı değişen uzunluklardaki hidrokarbonlardan oluşur.
En küçük hidrokarbon metan, tek bir karbon atomu ve dört hidrojen atomundan oluşur. Bununla birlikte, hidrokarbonlar, zincirler, daireler ve diğer karmaşık şekiller dahil olmak üzere birçok yönden birbirine bağlanmış yüzlerce veya binlerce bireysel atomdan oluşabilir.
Hidrokarbonların özelliklerini sınıflandırmak için birkaç temel türe ayrılırlar.
Alkanlar: Bunlar doymuş hidrokarbonlar olarak adlandırılır. Yani sadece tüm karbon atomları arasında tek bağlar içerirler. Alkanlar, petrol yakıtlarının temelidir ve doğrusal ve dallı formlarda bulunurlar.
Doymamış Hidrokarbonlar: Karbon atomları arasında bir veya daha fazla çift bağa sahip olan hidrokarbonlara alken denir.
Sikloalkanlar: Bir veya daha fazla halka yapısı içeren herhangi bir hidrokarbon.
Aromatik Hidrokarbonlar: Areneler olarak da adlandırılan aromatik hidrokarbonlar, karbon atomlarının birbirini izleyen çift ve tek bağlarla bağlandığı benzersiz bir karbon molekülleri sınıfıdır. Bu molekül sınıfı, karbon atomları arasındaki bağların tek ve çift bağlar arasında bir ara bağ olduğu özel halka yapılarına sahiptir.
Bu sınıftaki moleküller, endüstriyel çözücü «benzen» içerir.
Benzen (C6H6): Diğer hidrokarbonlar gibi benzen de petrolün doğal bir bileşenidir. Oda sıcaklığında renksiz, yanıcı, tatlı kokulu bir sıvıdır ve yüksek oktan sayısına sahip olduğu için çoğu benzin karışımının bir bileşenidir.
Benzen de oldukça kanserojendir ve kemik iliği yetmezliği ve kemik kanserine neden olduğu iyi bilinmektedir. Elbette, “hoş aroması” nedeniyle tıraş sonrası ve diğer kozmetiklerde bir katkı maddesi olarak kullanıldığında kanserojenliği iyi bilinmemektedir.
En büyük benzen kullanımı (% 50), stiren ve polistren plastiklerinin ürünüdür. Ayrıca Naylon üretiminde önemli olan sikloheksan olarak bilinen bir moleküle dönüştürülür. Siklohekzan üretmek için benzenin yaklaşık% 15'i kullanılır. Böcek ilaçlarından kauçuğa kadar her şeyde daha küçük miktarlar kullanılır.
Benzen yapısı iki şekilde çizilebilir. İlkinde, çift bağ karakteri açıkça çizilir. Kısa elli versiyonda, yapıyı göstermek için halkanın içine bir daire çizilir. Benzen içindeki her bir karbon atomuna bağlı tek bir hidrojen vardır.
Aşağıdaki I. ve II. çizimleri eştir. Pratikte III. çizim kullanılır.
Benzen, renksiz, alevlenebilen, kaynama noktası 80,1 °C, erime noktası 5,5 °C olan bir sıvıdır.
Binükleer Aromatik Hidrokarbonlar: Molekülünde iki benzen halkası içeren bileşiklerdir.
Hidrokarbonlar
Hidrojen ve karbon olmak üzere iki elementten oluşan organik bir bileşiktir. Petrol bileşiminin büyük bir kısmı değişen uzunluklardaki hidrokarbonlardan oluşur.
En küçük hidrokarbon metan, tek bir karbon atomu ve dört hidrojen atomundan oluşur. Bununla birlikte, hidrokarbonlar, zincirler, daireler ve diğer karmaşık şekiller dahil olmak üzere birçok yönden birbirine bağlanmış yüzlerce veya binlerce bireysel atomdan oluşabilir.
Hidrokarbonların özelliklerini sınıflandırmak için birkaç temel türe ayrılırlar.
Alkanlar: Bunlar doymuş hidrokarbonlar olarak adlandırılır. Yani sadece tüm karbon atomları arasında tek bağlar içerirler. Alkanlar, petrol yakıtlarının temelidir ve doğrusal ve dallı formlarda bulunurlar.
Doymamış Hidrokarbonlar: Karbon atomları arasında bir veya daha fazla çift bağa sahip olan hidrokarbonlara alken denir.
Sikloalkanlar: Bir veya daha fazla halka yapısı içeren herhangi bir hidrokarbon.
Aromatik Hidrokarbonlar: Areneler olarak da adlandırılan aromatik hidrokarbonlar, karbon atomlarının birbirini izleyen çift ve tek bağlarla bağlandığı benzersiz bir karbon molekülleri sınıfıdır. Bu molekül sınıfı, karbon atomları arasındaki bağların tek ve çift bağlar arasında bir ara bağ olduğu özel halka yapılarına sahiptir.
Bu sınıftaki moleküller, endüstriyel çözücü «benzen» içerir.
Benzen (C6H6): Diğer hidrokarbonlar gibi benzen de petrolün doğal bir bileşenidir. Oda sıcaklığında renksiz, yanıcı, tatlı kokulu bir sıvıdır ve yüksek oktan sayısına sahip olduğu için çoğu benzin karışımının bir bileşenidir.
Benzen de oldukça kanserojendir ve kemik iliği yetmezliği ve kemik kanserine neden olduğu iyi bilinmektedir. Elbette, “hoş aroması” nedeniyle tıraş sonrası ve diğer kozmetiklerde bir katkı maddesi olarak kullanıldığında kanserojenliği iyi bilinmemektedir.
En büyük benzen kullanımı (% 50), stiren ve polistren plastiklerinin ürünüdür. Ayrıca Naylon üretiminde önemli olan sikloheksan olarak bilinen bir moleküle dönüştürülür. Siklohekzan üretmek için benzenin yaklaşık% 15'i kullanılır. Böcek ilaçlarından kauçuğa kadar her şeyde daha küçük miktarlar kullanılır.
Benzen yapısı iki şekilde çizilebilir. İlkinde, çift bağ karakteri açıkça çizilir. Kısa elli versiyonda, yapıyı göstermek için halkanın içine bir daire çizilir. Benzen içindeki her bir karbon atomuna bağlı tek bir hidrojen vardır.
Aşağıdaki I. ve II. çizimleri eştir. Pratikte III. çizim kullanılır.
Benzen, renksiz, alevlenebilen, kaynama noktası 80,1 °C, erime noktası 5,5 °C olan bir sıvıdır.
Binükleer Aromatik Hidrokarbonlar: Molekülünde iki benzen halkası içeren bileşiklerdir.
Hakkında
Kyäni, faydalı bileşenlerden oluşan besin takviyesi ürünlerini; benzersiz iş fırsatıyla birlikte dünya çapında 50'den fazla ülkeye ulaştırmaktadır. İdeal sağlığımızı korumak için günlük olarak Kyäni ürünlerini kullanırız, bu ürünleri başkalarıyla paylaşırız, işimizi inşa etmek ve sürdürmek için neredeyse her gün belirli bir saatimizi işe adarız ve başkalarını da Kyäni fırsatına dahil ederek veya Potato Pak ve Caring Hands programlarına katkı sağlayarak başarımızı başkalarıyla paylaşırız.
Hakkında
Kyäni, faydalı bileşenlerden oluşan besin takviyesi ürünlerini; benzersiz iş fırsatıyla birlikte dünya çapında 50'den fazla ülkeye ulaştırmaktadır. İdeal sağlığımızı korumak için günlük olarak Kyäni ürünlerini kullanırız, bu ürünleri başkalarıyla paylaşırız, işimizi inşa etmek ve sürdürmek için neredeyse her gün belirli bir saatimizi işe adarız ve başkalarını da Kyäni fırsatına dahil ederek veya Potato Pak ve Caring Hands programlarına katkı sağlayarak başarımızı başkalarıyla paylaşırız.
Sayfa Yapım Aşamasındadır.
Sayfa Yapım Aşamasındadır.
Schulungs- / Wissens- / Lösungsplattform
Ein Überblick über Probleme in Prozessen
Um sicherzustellen, dass die Extrusionsproduktion erfolgreich ist, muss jeder Parameter definiert, gesteuert und überwacht werden. Einige Variablen hängen von der Ausrüstung ab, andere von den Betriebsbedingungen. Alle Variablen variieren von der Formqualität bis zu Temperaturen und Drücken.
Vor Beginn des Produktionsprozesses sollten einige vorbeugende Maßnahmen ergriffen werden.
Alle Geräte, die für Temperatur, Druck, Zyklus und Ampere verwendet werden, sollten regelmäßig gewartet werden.
Ein konstanter Rohstoffprozess minimiert Probleme. Dies beginnt damit, wie das Rohmaterial gelagert wird. Die Lagerung ist an einem sauberen und trockenen Ort ohne extreme Temperaturschwankungen erforderlich. Um sicherzustellen, dass das Harz konsistent ist, führen einige Unternehmen eine Harzanalyse durch, um das Material zu messen und Dichte, Schmelzindex, Schergeschwindigkeit, Viskositätsdaten und Zugfestigkeit aufzuzeichnen. Wenn es zu trocken ist, schmilzt es möglicherweise nicht und das Harz kann nicht verarbeitet werden. Selbst Chargenverschiebungen desselben Rohmaterials können zu Änderungen der Lagerbedingungen führen.
Typische Extrusionsprobleme lassen sich in einige Hauptkategorien einteilen:
Ästhetische Unvollkommenheiten (z. B. Grübchen, schwarze Spezifikationen, Nadellöcher, Zugspuren, Matrizenlinien, Stichspuren) Wie Größe, Formmängel. Wenn ein Problem auftritt, besteht der erste Schritt darin, die Komponenten des Herstellungsprozesses zu untersuchen, die mit der Ausrüstung beginnen. Das Problem kann sein, dass das Schneckendesign und / oder die Temperatur das Problem verursachen oder die Form nicht richtig hergestellt ist oder die Temperatur eines bestimmten Bereichs in der Extrusionslinie falsch ist. Die wichtigsten Variablen, die untersucht werden sollten, wenn sie nach der Extrusion nicht mit den Spezifikationen und Abmessungen des Endprodukts übereinstimmen, sind:
Schmelzdruck, Schmelztemperatur, Manteltemperatur, Formtemperatur, Heizungen, Widerstände, Kühlsystem, Geschwindigkeit und Struktur der Schnecke, Motorlast in Ampere
Produktionsliniengeschwindigkeit, Formverschleiß oder falsches Design.
Bei Extrusionsproblemen; Hersteller beziehen sich normalerweise auf technische Geräte, die in einem stabilen Prozess nicht ordnungsgemäß funktionieren, während Techniker auf eine unsachgemäße Anwendung der aktuellen Produktionsbedingungen (z. B. Temperatur, Druck, Materialmenge usw.) verweisen. Und es wird sich der Lösung des Problems aus dieser Perspektive nähern.
Die mangelnde Kenntnis der technischen Ansätze der Hersteller und der Produktionsprozesse der Techniker zeigt einmal mehr, wie wichtig Teamarbeit bei Extrusionsproblemen ist.
Die Tatsache, dass die Parteien ihre Prozess-, Wartungs- und Ausfallaufzeichnungen nicht auf gesunde Weise geführt haben, wird zur "Entdeckung Amerikas immer und immer wieder" führen.
In dieser Hinsicht besteht die grundlegendste Anwendung bei der Lösung von Extrusionsproblemen darin, alle Entwicklungen in einem «gemeinsamen Pool» unter dem Namen Qualitätsaufzeichnungen zu führen, insbesondere den ersten Schritt, der zur Fehlerbehebung bei Zeitplänen unternommen werden sollte.
Der Extrusionsprozess ist buchstäblich ein "Black-Box" -Prozess.
Was in einem Extruder passiert, ist für das Auge unsichtbar. Um sich vorstellen zu können, was im Zylinder / Ofen vor sich geht, müssen die Extruderkomponenten und ihre Werte bekannt sein.
Schneckendurchmesser, Länge, Charakteristik, Motor- / Reduzierleistung, die der Schraube die Drehbewegung verleiht. Das Hauptargument der Wärmebehandlung sind die Widerstände, ihre Position, Thermoelemente, die den Temperaturwert messen, Wärme- oder Bewegungssensoren, Zeitregler, Kühlleitungstemperaturen, usw.
Am wichtigsten sind digitale / analoge Anzeigen, auf denen die von ihnen erzeugten Werte gelesen werden.
Er muss absolut sicher sein, dass alle Sensoren funktionieren und die Messwerte korrekt kalibriert sind.
Abgesehen von diesen Betreibern; Sie müssen auch über Vor- und Nachextrusionsgeräte wie Trockner, Mischer, Granulatoren, Förderer und Zuführer, Zahnradpumpen, Siebwechsler, Kalibratoren, Wasserbecken und -tröge, Lasermessgeräte, Abzieher und Umhüllungen und sogar die Werkzeugförderung Bescheid wissen. Um Extrusionsprobleme zu lösen, muss der Prozess von Anfang bis Ende verstanden werden. Zu Beginn des Auftrags ist eine Schulung erforderlich, die die Material- und Ausrüstungsspezifikationen abdeckt. Dies ist jedoch normalerweise die am wenigsten wirksame und in gewisser Hinsicht die teuerste Methode.
Ein unsachgemäßer Betrieb eines Extruders durch ungeschultes Personal kann zu kostspieligen Schäden oder sogar zu Verletzungen von Arbeitern führen.
Für ein gutes Prozessmanagement ist dies ein Hinweis darauf, dass die Probleme durch sofortiges Eingreifen sowie die Produktion ohne Probleme vermieden werden.
Der grundlegendste Prozessschritt zur Problemlösung; Es ist ein Vergleich mit den Prozessbedingungen in den reibungslosen Prozessen. Hierzu müssen Transaktionsaufzeichnungen geführt werden, die auch als "Qualitätsaufzeichnungen" geführt werden.
Das Beibehalten eines Zeitplans für die Fehlerbehebung erleichtert den größten Teil der Arbeit.
Zeitleiste für die Fehlerbehebung
Es ist eine historische Aufzeichnung darüber, welche Art von Änderung die Probleme in den am Material / Produkt verursachten Prozessen hatten und mit welchen Eingriffen die Analyse durchgeführt wurde. Mit anderen Worten, wenn alle Fehleraufzeichnungen aufbewahrt werden, werden alle auf den Prozess angewendeten Änderungen und Ergebnisse tabellarisch dargestellt und in ein Flussdiagramm umgewandelt. Wenn Sie ein solches Aufzeichnungsdokument erstellt haben, wirkt sich dies definitiv auf Ihre Karriere als «Problemlöser» aus. Alle Prozessdaten ( Temperatur, Druck, Zyklus, Größe, welche Schraube, Form, Rohstoffcharge, Charge, Lösungszeit, Bediener, Schicht usw.) sollten aufgezeichnet werden. Notizen wie was getan wurde und wie viel Zeit es dauert, sollten hinzugefügt werden. Später sind diese Daten wichtig, wenn dieses oder ein ähnliches Problem auftritt. Was zuvor getan wurde, was getan werden sollte, um das Problem zu lösen, hilft Ihnen, rechtzeitig einzugreifen. Es sollte jedoch nicht vergessen werden, dass die Ursache des Problems möglicherweise nicht nur vor, sondern vor dem Problem entstanden ist sollte bedacht werden, dass ein längerer historischer Prozess nachträglich bewertet werden kann. Zeitpläne bieten eine Arbeitsmethode, die bei der Problemlösung hilfreich ist. Es hilft der intellektuellen Organisation. Es bietet keine Lösungen für das absolute Problem. Zeitpläne unterstützen die Teamarbeit, die Suche nach der Wahrheit, die Offenheit für unterschiedliche Ansichten und die Entstehung gegensätzlicher Ansichten oder des Bewusstseins. „Fishbone“ -Diagramme, die effektiv und einfach zu verwenden sind, können bevorzugt werden. Der allgemeine Anwendungsbereich in diesen Diagrammen besteht darin, Produktdesign- und Qualitätsfehler zu vermeiden. Während Sie die Gründe untersuchen, die Meinungen verschiedener Segmente berücksichtigen, ein Umfeld schaffen, in dem jeder seine Meinung leicht und ohne zu zögern äußern kann, unparteiisch sein, die Gründe schreiben, auf ihre Löslichkeit achten und insbesondere das Diagramm entsprechend den sich ändernden Bedingungen auf dem neuesten Stand halten Datenakkumulation, die bei der Fehlerbehebung hilft.

Probleme im Extrusionsprozess
Schmelzbruch:
Schmelzbruch kann verschiedene Erscheinungen haben. Es kann als Slip Stick (oder Bambus), Palme, Spirale oder zufällige gemischte Rauheit gesehen werden. Im Allgemeinen beinhaltet der Schmelzbruch Kopf- / Düsenspannungen und ist im Allgemeinen mit Polymermaterial verbunden. Es kann durch Material oder mechanische Mittel ausgehärtet werden. Es ist immer eine gute Idee, den Kopfströmungskanal zu rationalisieren, um einen Schmelzbruch zu stoppen. Die Verringerung der Scherbeanspruchung kann durch Erhöhen des Formhohlraums, Verringern der Extrusionsgeschwindigkeit, Erhöhen der Kopftemperatur, Erhöhen der Schmelztemperatur oder Verringern der Schmelzviskosität erfolgen. Die Viskosität kann durch Verwendung eines Verarbeitungshilfsmittels oder eines Schmiermittels verringert werden. Eine andere übliche Lösung für den Schmelzbruch besteht darin, eine Heizung zu installieren, um die Kopftemperatur so weit zu erhöhen, dass die Scherspannung für das Versagen der Schmelze unter die kritische Scherspannung fällt. Die Verweilzeit der Schmelze im Kopfbereich ist so kurz, dass die Temperaturen relativ hoch sein können. Die Kopfflächenheizung kann auch den Kopfdruck reduzieren und eine um bis zu 20% höhere Extrusionseffizienz bieten, während ein gutes Produktaussehen und Maßtoleranzen beibehalten werden. Auch die Ultraschallvibration des Kopfes mit extern montierten Wandlern führt dazu, dass Kunststoffe durch Schneiden dünner werden. Bei dieser Technik sind nur begrenzte Informationen verfügbar, aber wenn die Verformungsrate hoch genug ist, kann sie die Schmelzviskosität um eine Größenordnung verringern.
Die Kunststoffschmelzschicht in der Kopfwand wird sehr hochfrequent verformt, was zu einem starken Abfall der Schmelzviskosität an der Kopfwand führt. Diese Anwendung reduziert auch den Kopfdruck, das Quellen, den Schmelzbruch und das Absacken der Schimmelpilze.
Geringe Effizienz:
Zunächst sollte geprüft werden, ob das verwendete Material trocken ist. Das Erhöhen der Schneckendrehzahl erhöht den Wirkungsgrad.
Im Fall einer Schneckendrehungssonde führt eine Verringerung des Kompressionsverhältnisses zusätzlich zur Verringerung der Filtration dazu, dass das geschmolzene Material schneller aus dem Kopf austritt. Das Erhöhen der Kopf- / Formtemperatur wirkt sich auch auf die Effizienz aus.
Keine homogene Schmelze:
Für die Verarbeitung unterschiedlicher Rohstoffe sind unterschiedliche Schneckeneigenschaften erforderlich. Wenn die zur Verarbeitung des Rohmaterials verwendete Schraube nicht zur Verarbeitung geeignet ist, erfüllt das aus der Form entfernte Produkt nicht die gewünschten Eigenschaften. Wählen Sie die Schraube aus, die für die Verarbeitung des zu verarbeitenden Rohmaterials geeignet ist, indem Sie die Schraube überprüfen. Wenn der Druck in der Schraube niedriger als erforderlich ist, wird die Homogenisierung und Plastifizierung des Rohmaterials verhindert. Der Druck in der Schraube wird durch Erhöhen der Schneckendrehzahl erreicht. Überprüfen Sie die Schneckendrehzahl und erhöhen Sie sie um den entsprechenden Betrag. In einer schlecht gestalteten Form kommt das Produkt möglicherweise nicht homogen heraus. Die Verarbeitungstemperatur ist nicht geeignet
Sorgen Sie für eine angemessene Verarbeitungstemperatur, da dies eine Plastifizierung und Homogenität verhindert. Überprüfen Sie die Schneckendrehzahl.
Fehler beim Ändern der Temperaturen:
Heizungen sind möglicherweise defekt. Möglicherweise sind die elektrischen Anschlüsse unterbrochen. Die Verarbeitungstemperatur des Rohmaterials wird durch Heizungen bereitgestellt. Wenn eine oder alle Heizungen nicht betrieben werden, kann das Produkt die Verarbeitungstemperatur nicht erreichen.
sollte nicht vergessen werden. Überprüfen Sie aus diesem Grund, ob die Temperaturwerte nach dem Einschalten der Maschine ansteigen, und wechseln Sie die Heizungen, indem Sie die elektrische Einheit informieren, wenn eine defekte Heizung vorhanden ist, deren Temperaturwerte nicht ansteigen. Ein weiterer Grund, warum die Heizungen nicht heizen, kann ein elektrischer Verbindungsfehler sein. Informieren Sie in solchen Fällen erneut die strombezogene Einheit und fordern Sie die Behebung des Fehlers an.
Häufige Ausfälle der Produktionslinie:
Die Geschwindigkeit des Hammers ist möglicherweise zu hoch. Eine zu hohe Geschwindigkeit des Hammers kann zu einer Ausdünnung und einem Bruch des Produkts führen, das beim Ziehen überdehnt wird. Reduzieren Sie in solchen Fällen die Geschwindigkeit des Hammers, um ein Reißen und Ausdünnen zu verhindern. Wenn das Produkt bricht, obwohl der Traktor mit normaler Geschwindigkeit zieht, ist ein weiterer Grund für diese Situation, dass die richtige Schneckendrehung nicht gewährleistet ist. Erhöhen Sie in diesem Fall die Schneckendrehzahl entsprechend der Menge an Rohmaterial, die pro Zeiteinheit erhalten werden soll. Wenn die Geschwindigkeit der Abschleppeinheit während des Schießens unabhängig zunimmt oder abnimmt oder zeitweise stoppt und wieder zu arbeiten beginnt, kann das Produkt brechen. In solchen Fällen sollten die pneumatischen Verbindungen des Schlepptraktors überprüft werden. Einer der Gründe für das Brechen des Produkts ist, dass die Kühlung unzureichend ist. In solchen Fällen sollten das Kühlsystem und die kalibrierten Kühlkanäle überprüft werden. Wenn ein Kühlkanal blockiert ist, sollte dieser gereinigt und geöffnet werden. Ein weiterer Grund für unzureichende Kühlung ist Kühlwasser
Temperatur liegt über den gewünschten Werten. Dies kann daran liegen, dass das zum Kühlen verwendete Wasser im System nicht ausreichend gekühlt wird. Es sollte überprüft werden, ob die Wasserkühlung funktioniert oder nicht. Die Kontrolle der Kältemaschinen sollte nicht übersprungen werden. Einer der Gründe für den Bruch des Produkts während der Verarbeitung sind die hohen Verarbeitungstemperaturen. In diesem Fall ist das Produkt möglicherweise nicht ausreichend gekühlt und gehärtet, sodass es platzen kann. Stellen Sie die richtigen Verarbeitungstemperaturen sicher, indem Sie die Verarbeitungstemperaturen steuern. Eine unzureichende Plastifizierung und mangelnde Homogenität sind ein weiterer Faktor, der zum Bersten des Produkts führt.
Schlechte Adhäsion oder Nichtadhäsion bei Co-Injektion:
Es besteht die Notwendigkeit, die Schmelztemperatur und die Kompression im Kopf zu erhöhen.
Sehr glänzend:
Senken Sie die Schmelztemperatur. Den Inflationsdruck verringern. Erhöhen Sie die Schraubstockkraft.
Matt / stumpfe Oberfläche:
Durch Erhöhen der Schmelztemperatur durch Erhöhen der Anfangs- und Endtemperatur wird das matte Aussehen der Oberfläche verbessert. Das Kompressionsverhältnis muss gegebenenfalls erhöht werden.
Schweißlinien:
Bild in Form von Fremdmaterial oder Verformungslinie auf dem Kaliber oder der Formoberfläche. Erhöhen Sie die Schmelztemperatur. Kopftemperatur erhöhen. Reinigen Sie den Kopf und die Kopfteile. Überprüfen Sie das Sieb und ersetzen Sie es gegebenenfalls. Überprüfen Sie die Form und das Kaliber. Alle Fremdkörper, die sich möglicherweise in der Form oder im Kaliber befinden
Reinigen Sie das Material mit weichen Materialien, die die Form und das Kaliber nicht beschädigen.
Verzerrte Dickenverteilung:
Die Produktdicke wird durch den Kopf / die Form bestimmt. Die Wärme wird in der Form, dem Produkt, nicht homogen verteilt
Dies kann dazu führen, dass die Ausgabe an einigen Stellen in der Form schnell und an einigen Stellen langsam ist. Die Kopftemperaturregelung und die Kopfeinstellung sollten durchgeführt werden.
Verbrennungsspuren: Ein über den Verarbeitungstemperaturen eingestellter Temperaturwert kann zu Verbrennungsspuren am Produkt oder zum Verbrennen des Produkts führen. Dies kann auch zu langen Wartungsarbeiten führen. In solchen Fällen steuern und senken Sie die Verarbeitungstemperaturwerte. Wenn die Schneckendrehzahl langsamer als erforderlich ist, kann sich das für längere Zeit in diesem Bereich verbleibende Rohmaterial überhitzen und zum Verbrennen führen. Erhöhen Sie die Schneckendrehzahl entsprechend den entsprechenden Werten.
Schnittprobleme:
Lang verwendete Schneidwerkzeuge können nach einer Weile stumpf werden und ihre Schneideigenschaften verlieren. In solchen Fällen müssen die Klingen geschärft werden. Die geringe Kraft der Andruckrolle im Granulator kann das Schneiden verhindern. In diesem Fall erhöhen Sie die Schneidpresskraft.
Pause bei Shear:
Übermäßiger Druck, den der Fräser auf das Produkt ausübt, um das Produkt zu schneiden, kann dazu führen, dass das Produkt aus den Schneidbereichen bricht, indem es diesem Druck nicht standhält. Reduzieren Sie in solchen Fällen die Schneidpresskraft. Ein weiterer Grund für das Brechen des Produkts während des Schneidens ist die schnelle Schneidwirkung des Fräsers während des Schneidens. Die Schnittgeschwindigkeit sollte verringert werden, um ein Brechen des Produkts zu verhindern.
Übermäßige Bestäubung:
Dies kann daran liegen, dass die Partikelgröße der eingegebenen Rohstoffe zu klein ist, Staub vorhanden ist und die Plastifizierung nicht ausreicht.
Probleme während des Injektionsprozesses
Stromlinien:
Es erscheint als Streifen auf der fließenden Lösung. Es tritt auf, wenn die Schmelze im Formhohlraum nicht richtig unter Druck gesetzt wird. In dieser Situation spielt auch die Füllgeschwindigkeit eine Rolle. Das Trocknen des Materials, das Steuern der Gasfreisetzung aus der Form, das allmähliche Erhöhen der Einspritzgeschwindigkeit oder das Erhöhen der Temperatur der Form kann die Lösung sein. Die Temperatur des Materials und / oder der Form sollte ebenfalls kontrolliert werden.
Die Düsen- und Hülsen-Temperaturen sollten erhöht werden. In einigen Fällen ist es auch ein Problem, das durch das Formdesign verursacht wird. Durch Ändern der Gate-Eingänge und Verbreitern der Gate-Eingänge wird eine Lösung geschaffen. Eine unzureichende Belüftung verursacht ebenfalls diesen Fehler. Entlüftungsabzieher sollten sauber sein und regelmäßig überprüft werden. Die Füllgeschwindigkeit ist wichtig für die Beseitigung von Siedelinien. Wenn Sie so schnell wie möglich füllen, wird so viel Schmelze wie möglich in den Formhohlraum eingeführt. Je höher die Schmelze des Materials während des Füllens ist, desto geringer ist das Risiko, dass dieser Fehler auftritt.
Verzerrungen:
Dies ist der Fall, wenn die Dichte der Teile unter den Standards liegt. Extrem trockener Materialverbrauch, Zylindertemperaturen und Formtemperaturen können ebenfalls Faktoren sein. Es tritt auf, wenn die physikalische Dichte des Formteils erheblich geringer ist als zuvor. Eine Übertrocknung des Materials ist ebenfalls eine Ursache für diesen Fehler. Wenn Sie das Material zu lange trocknen lassen (z. B. einige Tage bei der höchsten Temperatur), tritt dieser Fehler auf. Dies wird durch die Überhitzung der Heizungen in Heißkanalformen und durch die sehr unterschiedliche Wärme verursacht, die dem Material beim Schmelzen in Kaltkanalformen zugeführt wird. Überprüfen Sie die Schmelztemperatur und die Heizungen der Maschine oder Form.
Grate:
Beim Schließen der Form reicht der Druck nicht aus oder der Einspritzdruck ist größer als der Formschließdruck.
Die überschüssige Schmelze, die die Form füllt, verursacht diesen Überlauf, da der Injektionsprozess mehr als der Formzyklusprozess ist.
Das Verringern des Einspritzdrucks und der Einspritzgeschwindigkeit und das Erhöhen des Schließdrucks sind die ersten Schritte, die unternommen werden müssen.
Möglicherweise müssen auch die Düsen-, Zylinder- und Formtemperaturen gesenkt werden. Sie können auch die Geschwindigkeit der Schraube verringern, um das Problem zu beheben. Wenn keine ordnungsgemäße Ladekontrolle durchgeführt wird, kann der Formhohlraum mit überschüssigem Material gefüllt werden, was dazu führen kann, dass dieser Fehler auftritt.
Es sollte das gleiche Materialvolumen in die Form injizieren, indem in jedem Zyklus der Schraube der gleiche Vorschub und die gleiche Spannung vorgenommen werden.
Silberne Spuren:
Es ist in Form von Spuren, die wie Silber auf der Oberfläche des Stückes leuchten. Das Polymermaterial kann überhitzt sein. Das kondensierte Gas wird in der Formoberfläche eingeschlossen. Auch die Abkühlzykluszeit ist keine angemessene Zeit. Überprüfung der Ausrüstung des Kühlkreislaufs
Muss. Die Ausrüstung sollte auf konstanten Durchfluss und konstante Kühltemperatur eingestellt werden. Die Verwendung der Mischung, sobald sie im Fertigungsbereich ankommt, kann ebenfalls diesen Fehler verursachen. Die Mischung sollte mindestens 8 Stunden gewartet werden, bevor sie im Herstellungsbereich verwendet wird. Somit nähert sich die Temperatur des Materials der Umgebungstemperatur.
Blasen:
Es ist die Bildung kleiner Luft / Gas-Blasen auf der Oberfläche des Teils.
Gutes Staubsaugen oder nicht genügend Luft / Gas-Evakuierungsprozess ist der Faktor. Darüber hinaus erhöht die Tatsache, dass das verwendete Rohmaterial nass und feucht ist, die Bildung von Luft / Gas. Wenn das in einem kalten Lager oder Silo gelagerte Material in einer heißen oder warmen Pressumgebung verarbeitet wird, ohne dass Feuchtigkeit verdunsten kann, können verdampfende Wasserblasen Blasen im Material verursachen.
Aus diesem Grund sollte das Material gründlich getrocknet oder trocken gehalten und vor Beginn der Produktion auf Umgebungstemperatur gebracht werden.
Adhäsionen an der Form: Wenn die Form geöffnet wird, ist die Absaugung im Formhohlraum nicht beendet und das Teil wird an der Seite gezogen und festgeklebt, an der keine Drücker vorhanden sind. Ein an der Form haftendes Teil kann auch auf einen übermäßigen Haltedruck zurückzuführen sein. Auch das Stück ist noch sehr heiß. Die Form braucht etwas mehr Kühlung. Oder der Kühlzyklus kann erhöht werden. Schließlich gibt es eine Unannehmlichkeit bei der Formgestaltung. Konische Winkel müssen möglicherweise erweitert werden. Wenn es sich um ein Problem handelt, das nur bei bestimmten Materialverwendungen auftritt, können Maßnahmen wie die sofortige Freigabe der Form in Abhängigkeit von der Art des Polymermaterials ergriffen werden. Darüber hinaus bietet die Steuerung der Temperatur des Kühlwassers, die Verringerung der Temperatur der Form und die Reinigung der Injektionsteile Lösungen.
Schichtungen:
Das Stück sieht aus, als wäre es aus getrennten Schichten gedruckt worden, und diese Schichten verursachen leicht Bruch und Trennung. Wenn die Einspritzgeschwindigkeit niedrig oder die Form extrem kalt ist, beginnt das in die Form eintretende Material sehr schnell zu gefrieren. Die von hinten kommende Schmelze löst sich mit den gefrorenen Schichten. Im Allgemeinen bilden sich bei langsamen Füllungen geschmolzene kalte Schichten auf dem Teil. Es basiert hauptsächlich auf PE und PP als Allzweckfarbstoffe. Meistens können sich diese Farbstoffe nicht an die farblose Mischung anpassen. Übermäßiger Schimmelpilzspray kann diesen Fehler verursachen. Sobald das Material in die Form gelangt, gefriert es fast. Wenn mehr Material eintritt, gefriert es als nicht verschmelzende Schicht, genau wie die andere gefriert. Durch Erhöhen der Einspritzgeschwindigkeit wird dieses Problem behoben.
Curl, Warp:
Dies ist der Fall, wenn das fertige Teil nicht mehr in der gewünschten Formform ist. Die Geometrie des Teils ist aufgrund der inneren Spannung des Teils verzerrt. Dieses Problem kann bei Formen mit einer unregelmäßigen Toreingangskonstruktion, einer Toröffnungsgeometrie, Konstruktionen mit hohen Spannungen und defekten oder unzureichenden Toreingangsstellen auftreten. Mit zunehmender Abkühlzeit beginnen die Spannungen im Teil zu quenchen.
Wenn eine Erhöhung der Schmelz- und Formtemperatur und eine Verringerung der Einspritzgeschwindigkeit keine Ergebnisse liefert, sollte die Verträglichkeit der Einspritzzeit und der Formfüllzeit überprüft werden, falls das Teil zu komprimiert ist.
Orangeisierung:
Es ist ein Zustand der Einkerbung und des Vorsprungs auf der Oberfläche des Stücks, wie eine Orangenschale. Auch als «Micro Pitting» bekannt. Die erste auf dem Teil gebildete Oberfläche ist der Fehler, der durch das Drücken durch die hohe Menge an viskosem Material und dessen schnelle Faltenbildung verursacht wird. Die Schmelztemperatur und die Läufertemperatur sind niedrig. Es gibt Verluste im Einspritzdruck, die Schmelze tritt nicht schnell genug in die Form ein. Wir müssen einen höheren Druck ausüben, um die gleiche Füllgeschwindigkeit mit kaltem Material zu erreichen. Die Schmelztemperatur des Materials muss kontrolliert werden. Mit dem eingeschränkten Weg sollte die Schmelztemperatur langsam erhöht werden. Die Formtemperatur muss ebenfalls erhöht werden, um die Druckverluste im Kopf während des Befüllens auszugleichen. Es ist zu prüfen, ob die Geschwindigkeit für die Form ausreicht.
Schlechter Geruch:
Es wird durch brennendes Material verursacht. Insbesondere wäre es angebracht, die Temperaturen im Kopf- und Brustbereich zu senken.
Stellen Sie sicher, dass das Material trocken ist. Dies kann zu einer Verringerung des Haltedrucks führen. Durch Einstellen der Schmelztemperatur auf den niedrigsten Wert wird die Verbrennung von Additiven mit niedrigen Prozesstemperaturen im Polymer verhindert.
Schlechte Farbverteilung:
Die Schmelze wird im Fass nicht homogen gemischt. Die Farbkonzentration ist im gesamten Teil nicht gut verteilt. Auf dem Teil können unterschiedliche Farbverteilungen beobachtet werden. Die Hauptursache des Fehlers; Die Farbkonzentration wird nicht vollständig homogen gemischt, wenn sich die Schmelze in der Schraube befindet. Der gesamte Schmelz- und Mischvorgang erfolgt durch Drehen der Schnecke. Das Inkrementieren des Mischens kann nur durch herkömmliches erreicht werden
Dies geschieht durch die Verwendung von Schrauben, die Verringerung der Zylindertemperaturen und die Erhöhung des Gegendrucks. Je mehr dieses Material in die Schraube schmilzt, desto mehr
zeigt an, dass viel mechanische Wirkung gegeben werden sollte.
Wolfsspuren:
Wenn die Form auf das Teil gelegt wird, werden sie als Spuren gesehen, die während des ersten Drucks gebildet werden.
Beim Formenbau ist es gut, die Form so schnell wie möglich zu füllen, aber diese Schnelligkeit muss mit einem richtig dimensionierten Läufereinsatz sichergestellt werden. Da die Geschwindigkeit des Materials im Läufereingang extrem hoch ist, ist der Fluss beim Eintritt in den Formhohlraum sehr schnell. Wenn die Schmelze schnell in den Formhohlraum eintritt, sprüht sie instabil links und rechts im Hohlraum herum. Um dies zu verhindern, muss ein Widerstand über den Strahl erzeugt werden. Hier geht es auch um das Formdesign.
Abstumpfung:
Es tritt in Form von Fingerabdrücken auf dem Teil auf. Da die Formoberfläche nicht fest oder sauber ist, wirkt sich die Wärmebehandlung auf das Material mit unterschiedlichen Nuancen aus. Die Hauptursache für das Versagen ist normalerweise eine kalte Schnecke oder ein Teil eines kälteren Materials.
ist, dass es hineingespritzt wurde. In einigen Fällen enthält das Material eine übermäßige Menge an Schmiermittel und Schmiermittel, die sich auf der Formoberfläche ausbreiten. Wenn die Formoberfläche nicht gleichmäßig ist, sollte die Schmelztemperatur gesenkt und die Sauberkeit der problematischen Oberfläche überprüft werden. Die Faktoren, die den Übergang der Düsen- und Laufdüsenbuchse verhindern, sollten beseitigt werden. Düse
und die Laufdüsenbuchse muss genau zueinander passen. Wenn es eine andere Situation gibt, liegt ein Fehler im Ablauf vor.
Brustwarzen- / Kopfverschluss:
Wenn Material in die Form eingespritzt wird, wird es als verdünntes, geschmolzenes Material angesehen, das am Formeingang gefriert. Das verwendete Polymermaterial kann feucht sein. Es ist vorteilhaft, den Luftkanälen (Ventil) eine Vakuumeinheit hinzuzufügen. Es kann auch erforderlich sein, den Haltedruck zu erhöhen.
Verschlechterungen im Runner-Eintrag:
Dies ist der Fehler in der Nähe des Läufers. Unmittelbar um den Läufereingang herum ist ein Mikrostrahl aufgetreten. Formoberflächen müssen möglicherweise poliert werden. Laufkanäle können eng oder zu tief sein.
Dieser Fehler tritt normalerweise bei Füllungen mit Glasfaser und Glimmer auf, da diese zu abrasiv sind.
Die Änderung, die in der Form vorgenommen werden muss, besteht darin, die Läufer breit, aber nicht tief zu machen.
Sabbern:
Es sind filamentöse Teile, die beim Öffnen der Form wie Drähte aussehen und sich verlängern. Aus diesem Grund wird dieses Problem auch als "Verkabelung" bezeichnet.
Dies geschieht auch, wenn ein dicker, aber langsamer Materialstrom langsam durch die Angussbuchse fließt. Die Hauptursache für den Fehler ist, dass der Druck des Kunststoffs im Zylinder nicht effektiv entfernt wird. Übermäßiger Einspritzdruck, Verschlechterung der Läufer können ein Faktor sein. Viele Gerätehersteller haben die Reverse-Toper-Düse an der Formmaschine angebracht, um dies zu verhindern. Diese wurden speziell entwickelt, um ein Sabbern zu verhindern. Wenn die Formen in Formen mit geöffneten Heißkanälen nicht ordnungsgemäß funktionieren, kann dies zu Schwankungen und Bespannungen führen. Die Verseilung kann bis zu einem bestimmten Punkt ohne Sabberdüsen gesteuert werden.
Die Schmelzdekompression kann häufig durch Zurückziehen der Schraube im Laufe der Zeit eingestellt werden. Durch Erhöhen der Dekomprimierungszeit wird die Anzahl der Drähte verringert.
Dunkle Stellen:
Der offensichtlichste Grund ist die Verwendung schmutziger Rohstoffe. Wenn das zu verwendende Material ein Farb-Masterbatch enthält, kann der ungeeignete Masterbatch-Träger auch während des Extrusionsprozesses zu Verbrennungen führen.
Kontinuierliches falsches Drucken:
Im Allgemeinen zeigt es sich meist in halbautomatischen Maschinen, indem fehlende oder maßlich falsche Teile gedruckt werden. Der Fehler ist hauptsächlich auf das Fehlen einer konstanten Füllgeschwindigkeit und Änderungen der Schmelzviskosität zurückzuführen. Der Ausfall von undichten Rückschlagventilen aufgrund des Füllens der Rückseite der Schraube führt zu Schwankungen des Einspritzdrucks. Ventile sollten überprüft und gegebenenfalls ausgetauscht werden. Obwohl sich die Schraube dreht, kann es außerdem vorkommen, dass das Material nicht für den nächsten Druck oder zur Hälfte entnommen wird. Es kann zu Verstopfungen im Fütterungs- und Halsbereich kommen. Wenn ein Vakuumlader verwendet wird, kann dieser Lader eine Abweichung seiner Sensoren, Kaliber, aufweisen. Mit anderen Worten, es liegt eine Fehlfunktion im Zuführsystem des Systems vor. Alle Geräte sollten überprüft werden.
Verbrennungen:
Es ist in Form von farbigen Flecken auf dem Stück zu sehen. Flecken
Es tritt aufgrund einer Verbrennung irgendwo darin auf. Betriebstemperaturen oder ein verbranntes Stück am Kopf können dies verursachen. Alte Maschinen mit Schrauben und Lauf können diese Art von Fehler im Teil verursachen. Denn wenn sich genügend verbrannter Teileabfall in der Maschine befindet, um berücksichtigt zu werden, können diese diese Art von Fehler im Teil verursachen. Die einzige Lösung, um dies zu verhindern, ist zu
Suchen und reinigen Sie die Komponente. Flecken entstehen durch Verbrennen irgendwo im Prozess. Eine Überhitzung der Heizbänder verursacht diesen Fehler. Wir müssen die Wärmesteuergeräte steuern, die ständig unter Kontrolle sind. Eine Materialänderung kann diesen Fehler ebenfalls verursachen. Überhitzung und Verbrennung des Materials können aufgrund übermäßiger Geschwindigkeitssteigerungen am Läufereingang auftreten.
Luft oder Gas werden ebenfalls in der Form eingeschlossen, wodurch das Material erhitzt und verbrannt wird. Normalerweise beschädigt es auch die Form. Heiße Luft oder heißes Gas überhitzen das Material und verursachen Verbrennungen. Es gibt keinen oder schlecht konstruierten oder nicht ordnungsgemäß gereinigten Emitter. Dieser Fehler kann auch auf eine übermäßige Schließkraft zurückzuführen sein.
Die Auswerfer der Form, die mit übermäßiger Kraft schließen, können funktionsgestört bleiben. Das Gas wird komprimiert und bleibt im Inneren und verursacht eine Verbrennung durch Überhitzung aufgrund von Kompression. Die Vorbeugung von Verbrennungen erfolgt durch gute Belüftung, dh durch Reinigen und Arbeiten der Abluftöffner.
Vakuumverformung:
Es ist die Änderung, die das Staubsaugen in den Robotereinheiten während des Entfernens des Teils aus der Form der Form des Teils verleiht. Während des Entladens äußert sich dies in der Verformung des Teils mit dem im ersten Moment auftretenden Vakuum.
Die ungeeignete Abkühlzykluszeit ist der größte Faktor. Wenn der Luftdruck auf der Treibmittelseite für das Teil zu niedrig ist, erhöht sich außerdem die Vakuumintensität. Dieser Fehler wird dadurch verursacht, dass der Kühlkreislauf nicht ordnungsgemäß funktioniert, verstopft ist, nicht betrieben wird oder ohne Leistung läuft (dh blind).
Um dies zu verhindern, muss vor dem Ausführen des Kühlkreislaufs überprüft werden, ob alles in Ordnung ist. Wenn die Belüftung erhöht wird, kann dieser Fehler verhindert werden.
Läuferhaftung:
Während des Öffnens der Form trennt sich der Läufer während des Öffnens vom Angusssystem, bricht und bleibt an der Form haften. Der größte Faktor dabei ist, dass die Gate-Verbindungspunkte nicht tief sind. Die Tatsache, dass das Teil zu heiß ist, verursacht auch Adhäsionen. Das Verringern der Düsen- und Zylindertemperaturen oder der Formtemperaturen oder das Verlängern der Abkühlzeit liefert eine Lösung.
Bei der Formkonstruktion müssen möglicherweise die konischen Winkel vergrößert werden. Die Verwendung von Formtrennmitteln verhindert ebenfalls diese Situation. Machen Sie eine tiefe Kanaldüsenkonstruktion oder setzen Sie einen effektiveren Kanaldüsenhammer oder schließlich eine beheizte Kanaldüse ein.
sollte nutzen. Wenn die Düsentemperatur zu niedrig ist, kann es beim Öffnen der Form immer noch zu einem Bruch kommen. Um dies zu verhindern, sollte die Düsentemperatur erhöht werden, um Kaltblitze und Bruch zu vermeiden.
Probleme beim Blasformen
Blasproblem:
Überprüfen Sie die Harzzusammensetzung. Erhöhen Sie die Temperatur des hinteren Zylinders leicht, um Überbrückungslücken im Extruderzufuhrabschnitt zu vermeiden. Reparieren Sie Matrizenränder und -klemmen, um zu verhindern, dass Löcher durch Matrizen beschädigt werden. Der Fülldruck ist möglicherweise zu niedrig. Erhöhen Sie den Packungsdruck, bis Luft gefüllt ist, um Lufteinschlüsse zu vermeiden. Die Schließgeschwindigkeit der Form kann sehr hoch sein. Reduzieren Sie die Schließgeschwindigkeit der Matrize, um eine schlechte Schweißnahtbildung zu vermeiden. Die Quetschung ist möglicherweise zu scharf oder zu heiß. Erhöhen Sie die Breite des Landes, um die Pergamentfläche nicht zu verkleinern. Erhöhen Sie die Kühlung im Staubereich. Verringern Sie die Temperatur des Zylinders / Kopfes. Reduzieren Sie die Anzahl der Zyklen
Blasen / Blasen:
Das Harz enthält Feuchtigkeit. Wenn Nebel auftritt, reduzieren Sie die Kühlung am Einfüllstutzen.
Überprüfen Sie die Harzfeuchtigkeit und stellen Sie sicher, dass das Harztransportsystem wasserdicht ist. Erhöhen Sie die hintere Lauftemperatur leicht. Erhöhen Sie den Packungsdruck, bis Luft gefüllt ist, um Lufteinschlüsse zu vermeiden.
Verschmutzung:
Halten Sie den Trichter immer sauber. Installieren Sie Filter an den Staublufteinlässen und reinigen Sie sie regelmäßig. Schmutz auf dem Harz kann durch Verbrennungen verursacht werden, verkürzen Sie die Extrusionszeit oder stellen Sie die Temperaturen ein. Stellen Sie sicher, dass die Schmelzströmungswege sauber sind.
Unregelmäßiges Vorformling-Volumen:
Das unregelmäßige Volumen ergibt sich aus dem ungleichmäßigen Gewichtsfluss. Dies wirkt sich auch auf die unregelmäßige Größe des Vorformlings aus. Das Gewicht ist nicht immer in jedem Zyklus gleich. Die Ursache des Problems sollte durch regelmäßige Überprüfung der Vorformlinggewichte geklärt werden. Überprüfen Sie die Kompatibilität der Gewichte mit dem Formvolumen. Unregelmäßigkeiten der Zykluszeit und Temperaturschwankungen können die Materialmenge beeinflussen. Die Druckeinstellungen müssen angemessen sein, um einen vollständigen Kontakt zu gewährleisten. Aufgrund des schlechten Vorformlings, der Lockerheit des Formkontakts, keine sauberen Formlöcher. Die Extruderprofiltemperatur führt zu einer höheren Schmelztemperatur, was zu einem höheren Vorformling führt. Die Formtemperatur ist auch eine Ursache für dieses Problem. Der Kühlmechanismus und seine Temperaturen sollten überprüft werden. Aufgrund der Glühbedingungen kann ein Problem auftreten. Arbeiten Sie bei höheren Temperaturen und langsameren Geschwindigkeiten. Zylindertemperatur verringern. Kopf- / Formtemperatur erhöhen. Reinigen Sie die Form / den Kopf. Auf verschlissene Axiallager- und Zentrierbuchsen prüfen.
Halskrümmung:
Der intumeszierende Vorformling führte zu falschem Schneiden. Die Ausrichtung der Sprühspitze ist möglicherweise nicht in Ordnung oder beschädigt. Stellen Sie sicher, dass der Sprühstift zentral ist. Muster können falsch ausgerichtet sein. Überprüfen Sie die Stifte und Buchsen.
Durchhängen:
Eine falsche Formeinstellung ist fällig. Der außermittige Druckring ist nicht zentriert. Kopf- und Verteilerheizungen prüfen.
Es ist auch wichtig, die Luftkanäle und den Formhohlraum zu reinigen.
Ungleichheit in der Rohrlänge:
Am Ende ist es das physische Problem. Überprüfen Sie zunächst, ob das Sägeblatt gedehnt ist. Wählen Sie dickere, größere Blätter. Der Sägearm kann zu schnell, manchmal langsamer in das Rohr eindringen. Stellen Sie sicher, dass der Zyklus stabil läuft. Der Sägearm kann abgenutzt sein und sich in eine Gratfläche verwandeln. Die Schleifringe können abgenutzt oder locker sein.
Die Tatsache, dass sich das ziehende oder schneidende Auto nicht immer mit der gleichen Geschwindigkeit bewegt, ist ein Faktor in dieser Situation. Stellen Sie sicher, dass die Ziehgeschwindigkeit immer mit der gleichen Geschwindigkeit läuft. Effizienz steigern. Abgesehen von den Betriebswerten kann das Arbeitstempo über der Schnittkapazität des Sägerohrs liegen.
Wandstärke Unregelmäßigkeit:
Aus der Form entfernte unregelmäßige Schmelze, unausgeglichene Startgeschwindigkeit, Fehlausrichtung der Form und der Zieheinheiten, Fehlausrichtung oder Verzerrung der Waage, Form und Stift zentrieren sich nicht gleichmäßig, und selbst der Spalt, der in der Form auftreten kann, ist die Ursache für die Unregelmäßigkeit in den Rohrwänden. Wenn die Schmelzpumpe verwendet wird, sollte überprüft werden, ob die Pumpendrehzahl stabil ist, und dann sollte festgestellt werden, ob die Zahnräder im Inneren abgenutzt sind.
Bei mehrschichtigen Schläuchen ist möglicherweise eine falsche Polymeranpassung aufgetreten. Es sollte keinen großen Unterschied zwischen den Viskositätswerten der im coextrudierten Verfahren bevorzugten Polymere geben. Andernfalls; Es wird Unterschiede in der Dicke der Schichten geben. In diesem Fall ist es nicht klar, dass die andere Schicht diesen abnehmenden Raum ausfüllt, während die Dicke einer Schicht abnimmt.
Während die Dicke einer Schicht abnimmt, kann die andere Schicht stabil bleiben. In diesem Fall ist die ungleichmäßige Wandstärke in der gesamten Querschnittsgröße die Hauptursache. Das Ändern des Temperaturprofils der Schmelze aus den beiden Polymeren kann eine Lösung sein. Der genaueste Ansatz sollte jedoch die Auswahl der Rohstoffe sein, deren MFI-Werte miteinander kompatibel sind. Der Druck, der bei der Co-Extrusion nicht gleichmäßig über die Zeit verteilt ist, wirkt sich auch nachteilig auf die Dickenverteilung aus, da er sich direkt auf die Menge der fließenden Schmelze auswirkt. Obwohl angenommen wird, dass es durch dieselbe Form geht und die Dicke gleich ist, ist die Schmelzverteilung im Schichtabschnitt nicht stabil. Dies führt zu einem ungleichmäßigen Fortschreiten der Dicke. In diesem Zusammenhang muss sichergestellt sein, dass alle Extruder in der Coextrusionseinheit mit konstantem Druck arbeiten.
So reduzieren Sie die Probleme, die im Laufe der Zeit während des Verwendungsprozesses auftreten können:
Das Rohrleitungssystem sollte so kurz und direkt wie möglich sein. Scharfe und mehrfache Biegungen sollten vermieden werden. Die Biegungen sollten sanft sein und einen großen Durchmesser haben, idealerweise das 10-fache der Schlauchnummer.
Es sollten "Y" -Verbindungen verwendet und "T" -Verbindungen so weit wie möglich vermieden werden.
Der saugseitige Rohrverlauf sollte niemals klein sein (die Mindestbohrung sollte dem Innendurchmesser des Schlauchs entsprechen).
Es ist vorteilhaft, Dehnungsfugen im Rohrleitungssystem zu installieren, um Vibrationsströmungseffekte in der Rohrleitung zu reduzieren.
Bei Verwendung flexibler Schlauchanschlüsse muss sichergestellt sein, dass der Schlauch mit einem geeigneten Elastometer aufgebaut ist und das System für den maximalen Saug- und Druck ausreichend geeignet ist. Um den Austausch von Teilen zu vereinfachen, sollten nach Möglichkeit abnehmbare flexible Teile an den Anfangs- und Endpunkten verwendet werden.
Depressionen:
Es kann als eine Art unvollständiger Druck angesehen werden, aber der höhere Haltedruck (fälschlicherweise als Bügeldruck bezeichnet) ist unzureichend. Die Außenwände des Teils sind fest. Durch Trennen einiger Moleküle in der inneren Struktur des Teils wurden jedoch Lücken gebildet. Abschnitte, die zu dick als nötig sind, enge Passagen oder Übergänge, die eine plötzliche Ausdehnung verursachen, verursachen ebenfalls Vertiefungen.
Eine Erhöhung des Gegendrucks, eine Erhöhung des Einspritzdrucks, eine Erhöhung des Haltedrucks und der Haltezeit wäre die Lösung.
Es sollte nicht vergessen werden, dass der Kunststoff beim Abkühlen im Formhohlraum schrumpft. Der Haltedruck sollte geregelt werden, um den Formhohlraum gut und vollständig auszufüllen und diesen Schrumpfungen gerecht zu werden. Unzureichender Druck führt zu Lücken. Da der Kunststoff beim Abkühlen schrumpft, muss er vorverifiziert werden, damit die Form ihre volle Form annimmt.
Dies gleicht das Schrumpfen der Spannung aus. Daher muss ein ausreichender Haltedruck auf das Teil ausgeübt werden.
Fehlende Drucke:
Es ist der Zustand des geschmolzenen Materials, der den Formhohlraum nicht vollständig ausfüllt. Einspritzdruck, Einspritzzyklus ist unzureichend. Möglicherweise müssen die Auslässe der Entgasungseinheit in der Form gesteuert werden.
Feuchtigkeit verursacht auch unvollständigen Druck, Hohlräume. Trocknen Sie das Material. Wenn Sie eine Entfeuchtungsschnecke verwenden, prüfen Sie, was eine Entfeuchtung verhindert. Möglicherweise müssen die Lüftungskanäle mit einem Zusatzvakuum ergänzt werden. Erhöhen Sie den Haltedruck.
Bei unregelmäßiger Formfüllung kann das Ändern der Läufereintrittspunkte zu Ergebnissen führen. Gleichzeitig muss sichergestellt sein, dass sich die Werkzeugtemperatur nicht ändert.
Dieses Problem hängt auch mit der Menge des eingespritzten Materials zusammen. Die Lösung besteht darin, die Menge des eingespritzten Materials und die Schmelzpolsterung zu erhöhen.
Einer der Gründe für fehlende Drucke ist das Formdesign. Möglicherweise sind die Läufereingänge verstopft. Überprüfen Sie die Verstopfung der Lüftungskanäle und die Richtigkeit ihrer Position. Bei Bedarf kann den Lüftungskanälen zusätzliches Vakuum hinzugefügt werden.
Wenn keine ordnungsgemäße Vorschubprüfung durchgeführt wird, fehlen möglicherweise Teile beim Überfüllen des Formhohlraums. Die Schraube muss für jeden Zyklus die gleiche Umdrehung drücken, dh das gleiche Materialvolumen. Dies ist ein Faktor, der bei der Konstruktion des Teils einen kurzen Druck verursacht. Scharfe Übergänge und schmale Abschnitte sollten vermieden werden. Oft kann die Form nicht an die Größe der Presse angepasst werden. Die Schließtonnage sollte sorgfältig eingestellt werden.
Drückerspuren:
Es ist zu sehen, dass die Stangen, die das Teil von der Hülse drücken, eine Spur auf dem Teil hinterlassen. Die Temperatur des Teils oder die Kraft der Schubstangen muss eingestellt werden. Dies liegt daran, dass die Stangen zu schnell auf das Teil treffen oder ihr Durchmesser zu klein ist.
Dieser Fehler kann beseitigt werden, indem die Temperatur des Teils und die Kräfte der Schubstangen ausgeglichen werden.
Dieser Fehler tritt auch auf, wenn die Platte (Druckplatte), an der die Schubstangen befestigt sind, das Teil zu schnell trifft und fallen lässt. Die Lösung besteht natürlich darin, die Geschwindigkeit der Drückerplatte zu verringern. Wenn die Form verschiedene Modifikationen erfahren hat, um ein Anhaften an der Form zu verhindern, ist dies der Fall
Wenn das Teil gleichzeitig auf der Drückerseite bleibt, können die Schubstangen Spuren auf dem Teil hinterlassen. Um dies zu verhindern, nimmt bei Verwendung von Schubstangen mit größerem Durchmesser die Kraft pro Flächeneinheit ab und die Möglichkeit, Spuren zu hinterlassen, wird verringert.
Probleme im Rohr- und Profilherstellungsprozess
Harte Oberfläche:
Es kann drinnen oder draußen sein. Der Rohstoff ist nicht trocken. Stellen Sie sicher, dass es ein oder zwei Stunden lang bei 70-90 ° C trocknet. Es fließt nicht genügend Wasser zum Kalibrator. Eine niedrige Schmelztemperatur verursacht ebenfalls dieses Problem. Die Extruder- oder Formtemperaturen sollten erhöht werden.
Deformität:
Es hat eine sehr hohe Schmelztemperatur. Überprüfen Sie die Extruder- und Düsentemperaturen. Dieses Problem kann auch auftreten, wenn die Geschwindigkeit der Extruderschnecke zu hoch ist. Die Ausbeute leicht senken. Je nach Ausbeute können die Formen klein sein. Wenn der Stift zu heiß ist, treten Bilder mit thermischer Verschlechterung auf der Oberfläche auf. Stellen Sie sicher, dass die Stiftkühleinheit ordnungsgemäß funktioniert. Es kann auch durch körperliche Probleme mit Deformitäten verursacht werden.
Überprüfen Sie die Formabmessungen auf Rundlaufgenauigkeit. Stellen Sie sicher, dass es 3%, 5% größer als der endgültige Rohrdurchmesser ist.
Das Rohr ist sehr heiß, wenn es die Entnahmeeinheit erreicht. Sorgen Sie im Voraus für einen ausreichenden Kühlstrom. Es kann mit hoher Effizienz zur Zeicheneinheit fließen. Die Extrusionsgeschwindigkeit sollte verringert und in Vakuumtanks eine geeignete Vakuumeinstellung vorgenommen werden.
Linien, die sich auf der Oberfläche bilden:
Es können Linien vom Kopf ausgehen. Spike auf Kopf / Würfel, Ausgangspunkte prüfen. Wenden Sie bei Bedarf eine schonende Reinigungsmethode an. Verbrannte, klebrige Schmelze im Kopf kann ebenfalls Streifen verursachen. Überprüfen Sie die Temperaturen in Richtung des Formausgangs.
Spuren hinterlassen:
Es wird eine sehr schnelle Zugkraft angewendet. Überprüfen Sie die Zeichengeschwindigkeit und stellen Sie sie ein. Die hohe Materialtemperatur am Formzugang ist ebenfalls ein Faktor. Überprüfen Sie den Wasserfluss.
Extruderfehler:
Der Versuch, eine sehr hohe Extrudereffizienz zu erzielen. Überprüfen Sie die Extruderspezifikationen und die garantierte Extruderleistung und
Lassen Sie den Extruder innerhalb der Spezifikation laufen. Dies kann auf falsche Einstellungen der Extrudertemperatur zurückzuführen sein. Passen Sie die Temperatureinstellung an die vom verwendeten Rohstoffhersteller empfohlenen Prozesswerte an.
Gelieren in der Röhre:
Es kann Fremdpartikel in der Schmelze enthalten. Das verwendete Rohmaterial, Zusatzstoffe usw. Möglicherweise müssen Sie Informationen vom Lieferanten erhalten. Verschlechtertes Harz, das während der Extrusion aus der Form austritt, kann ebenfalls gelieren. Sie müssen die Extrudierzeit und die Temperaturen steuern.
Flecken auf der Oberfläche:
Die Einstellung der Form erfolgt nicht ordnungsgemäß. Die Wärmeverteilung auf der Formprofiloberfläche ist möglicherweise nicht gleichmäßig. Stellen Sie sicher, dass die Homogenität bei Formtemperatur erreicht wird. Flecken neigen dazu, sich nach dem Abkühlen der Bäder zu zeigen, die Funktion des Ziehens, Drückens und Absenkens anzupassen. Unregelmäßige Schmelze und eingeschlossene Gase, die aus der Form austreten, sind Fleckenquellen. Stellen Sie sicher, dass die Staubsauger gut ausbalanciert und positioniert sind.
Durchhängen:
Eine zu hohe Schmelztemperatur ist die Hauptursache für das Durchhangproblem. Überprüfen Sie die Extrudertemperatur und die Extrusionszeit, um die Schmelztemperatur zu senken. Der Formhohlraum ist möglicherweise nicht richtig auf Durchhängen eingestellt. Die natürliche Beständigkeit der Schmelze gegen Durchhängen reicht für die Rohrwandstärke nicht aus. Verwenden Sie Rohstoffe mit geringem Durchhang. In den Leitungen kann keine ausreichende Kühlung bereitgestellt werden. Die Kühlleistung kann erhöht oder die in den Kühlbädern verbrachte Zeit verlängert werden.
Probleme im Blasfolienproduktionsprozess
Ballonsprung:
Eine der möglichen Ursachen ist die geringe Arbeitsgeschwindigkeit. Auch die zu hohe Verarbeitungstemperatur spielt in dieser Situation eine Rolle. Die Luftzirkulation in der Arbeitsumgebung kann zu hoch sein. Neben diesen; entlang des Umfangs der Luftringöffnung
Kühlluft muss kontinuierlich mit gleicher Geschwindigkeit geblasen werden. Außerdem muss die Position der Klapprahmen möglicherweise angepasst werden. Die Vibrationen, die während des Arbeitsprozesses im Extruder oder Turm auftreten, können den Ballon beeinflussen. Vibrationen müssen isoliert werden. Schließlich sollte die Eignung der optimalen Inflationsrate überprüft werden.
Faltiger Film:
Einer der möglichen Gründe ist der Defekt der Ballonform. Dazu sollte die Filmdicke homogen sein, die Kopftemperatur sollte für die Schmelzpolymertemperatur geeignet sein und der Kühlring sollte sauber und eingestellt sein.
Die Kopfeinstellung sollte so erfolgen, dass die Filmdicke gleich ist. Die Einstellung der Kopfhöhe sollte überprüft werden. Spannrollen
Pegelanpassung sollte vorgenommen werden. Möglicherweise hat sich Schmutz auf den Begrenzungswalzen oder -perlen des Ballondurchmessers angesammelt.
Im Falle einer instabilen Ballonsituation kann eine externe mechanische Aussteifung erforderlich sein. Schließlich sollte die Spannung der Wickelrollen gesteuert werden.
Blasprobleme:
Stellen Sie sicher, dass das Material trocken ist. Wenn recyceltes Material verwendet wird, stellen Sie sicher, dass es gereinigt ist. Erhöhen oder verringern Sie den Gegendruck entsprechend dem Inhalt des Inflationsproblems. Erhöhen Sie die Dicke der Schalungswand (stellen Sie den Kopf neu ein).
Nicht schmelzende Partikel:
Das Rohmaterial kann verschmutzt oder für den Prozess ungeeignet sein. Verbrannte Chips können auch an der Filmoberfläche haften, wenn die Verarbeitungstemperatur zu hoch ist. Die Temperaturen müssen kontrolliert werden.
Oder eine der ersten Anwendungen, der Filter, das Sieb ist voll und extrem verschmutzt. Es sollte geprüft werden, ob der Siebdraht Risse oder Löcher aufweist. Die Poren des Siebdrahtes sind groß. Ersetzen Sie ihn durch einen feineren Draht. Verbrannte Partikel können sich im Kopf zwischen den Lippen angesammelt haben. Eine Kopfreinigung ist erforderlich. Wenn der Extruder längere Zeit im Leerlauf war, ist die Schmelze im Inneren möglicherweise verbrannt und haftet an der Schraube. Falls erforderlich, sollte die gesamte Schraube entfernt und gereinigt werden. Wenn in der Formel, dem Rezept, ein Masterbatch verwendet wird, muss möglicherweise neu bewertet werden, ob die Mischung gut gemacht ist und die Arbeitswerte kompatibel sind. Der erste Prozess kann die falsche Wahl der Produktionslinie sein. Wenn Sie den Prozess mit einer Schraube mit besseren Mischeigenschaften in die Produktionslinie bringen, können Sie das Problem lösen.
Starre Filmoberfläche:
Durch Erhöhen der Kopf- / Matrizentemperatur der Zylindertemperaturen wird die Oberflächenhärte entfernt. Es kann auch erforderlich sein, die Extrusionsgeschwindigkeit und die Temperaturen auf der Zufuhrseite zu verringern. Das Erhöhen der Formtemperatur und die Verwendung von Schrauben mit hoher Kompression bieten auch eine Lösung für das Problem der harten Oberfläche.
Schlechte Reißfestigkeit:
Möglicherweise muss die Inflationsrate erhöht werden. Einer der Gründe für das Reißen ist, dass es Streifen auf der Filmoberfläche gibt. Hierzu kann es erforderlich sein, die Kopflippen des Extruders zu reinigen und die Anwendungen im Problem der nicht schmelzenden Partikel zu betrachten. Die Tatsache, dass die Gefrierlinie zu niedrig ist, beeinflusst auch die Reißfestigkeit.
Ballon platzen:
Es kann aus schmutzigen Rohstoffen stammen. Diese Situation löst das Problem nicht schmelzender Partikel aus. Verwandte Lösungen werden auch eine Lösung für das Platzen von Blasen sein. Möglicherweise müssen Sie die Schraube entfernen, den Kopf entfernen und alle Teile reinigen.
Lawinenbildung im Filmjahrhundert:
Zunächst sollte festgestellt werden, ob es sich bei den Leitungen um mechanisch wirksame physikalische oder schmelzbasierte Chemikalien handelt, und die Lösung sollte in dieser Richtung gesucht werden. Der Hauptgrund für die physischen Leitungen ist der Schmutz, der sich auf dem Kopf oder den Rollen angesammelt hat. Die scharfen, harten Enden der mechanischen Teile, die mit dem Film in Kontakt kommen, können aufgrund des Reibungseffekts Linien erzeugen. Maßnahmen wie Schleifen, Komprimieren und Entfernen von Rissen können erforderlich sein. Ihr Kopfdruck kann hoch sein. Die Reduzierung der Schneckendrehzahl und die Erhöhung der Betriebstemperaturen ist die Lösung für chemische Formationen.
Schlechte thermische Haftung:
Die ungeeigneten thermischen Bindungsbedingungen können ein Faktor sein. Hierzu sollte der Schmelzpunkt des Rohmaterials kontrolliert werden und es kann erforderlich sein, die Bindungstemperatur zu erhöhen, wenn die Bindungszeit abnimmt. Es kann auch zu ungeeigneten Lagerbedingungen für Wundspulen kommen. Die Filmoberfläche kann staubig und feucht sein. Der wichtigste Punkt ist, dass die Koronaspannung an der Oberfläche gering ist. Unabhängig davon, ob es sich um eine Korona handelt oder nicht, sollte die Intensität der Korona gemessen werden.
Störung der optischen Eigenschaften:
Der Hauptgrund liegt in der Auswahl fehlerhafter Rohstoffe. Niedrige Prozesstemperaturen und unzureichende Ballonkühlung führen ebenfalls zu einer optischen Verschlechterung. Eine Lösung besteht darin, die Temperaturen zu erhöhen, die Gefrierlinie zu senken und den Ballon mit kälterer Luft zu kühlen.
Probleme im Flexodruckprozess
Back-to-Back beim Drucken:
Das Drucken, bevor der Tintenfilm vollständig trocken ist, das Vorhandensein von Lösungsmittelresten auf dem Druckmaterial und das dichte Aufbringen der Spulenwicklung verursachen Druckspuren auf der Rückseite des Films. Bei beiden seitlich behandelten Filmen steht die bedruckte Oberfläche in Kontakt mit der anderen Oberfläche. Möglicherweise ist eine Verwendung des Beschleunigerlösungsmittels erforderlich. Trocknungstemperaturen und Luftströme zwischen den Geräten sollten überprüft werden. Der Spulenwicklungsdruck sollte verringert werden, wodurch die Dicke des übertragenen Tintenfilms verringert wird.
Die Verwendung von Antiblockierlack ist die Lösung des Problems.
Kratzerstellung beim Drucken:
Dies wird durch Fremdpartikel verursacht, die sich nicht auf der Abstreifklinge des Abstreifers befinden sollten. Das Schaberblatt muss gereinigt oder ersetzt werden. Außerdem sollten die Blade-Einstellungen überprüft werden. Die Eignung der Rasterwalzenhärte sollte überprüft werden.
Übermäßiger Anilox-Verschleiß:
Übermäßiger Druck auf die Abstreiferpresse verschleißt die Rasterwalzen. Treffen Sie Vorsichtsmaßnahmen, indem Sie die Gründe für die Notwendigkeit eines übermäßigen Drucks ermitteln. Die von der Tinte kommenden Füllmaterialien führen dazu, dass sich die Klingenspitze abnutzt. Übermäßiger Druck auf die Rasterwalze infolge der Erhöhung der Blattdruckeinstellungen, auch wenn die abgenutzte Blattspitze nicht funktioniert.
Es verursacht Verschleiß, wie es auftreten wird. Es ist notwendig, den Zustand und den Winkel der Klingen aller Farben zu überprüfen.
Straßenbahnstörung:
Die Straßenbahnpunkte verlängern sich in Richtung des Drucks von rund nach oval
Es ist der Fall, dass es ein Fischauge wird. Sie hängt mit der Höhe der Druckplatte oder der Dicke des verwendeten doppelseitigen Klebebands zusammen. Aus diesem Grund kann die korrekte forse-Einstellung nicht vorgenommen werden. Es gibt einen Unterschied im Zylinderdurchmesser zwischen dem Klischeekessel und dem Druckkessel. Die Gesamthöhe des Klischees (Klischee + Klebeband) sollte überprüft und die gewünschte Dicke sichergestellt werden. Die Druckkrafteinstellungen sollten erneut überprüft werden. Forse-Einstellstreifen, Doppel- und Gleitführungen sollten verwendet werden, um die optimale Krafteinstellung bei der Durchführung von Drucktests zu finden. In Flexodruckeinheiten sind die Zylinder im Allgemeinen mit Zahnrädern verbunden. Die Zahnradien bestimmen die Drehzahl des Zylinders und die Plattenoberflächengeschwindigkeit am Formzylinder zusammen mit dem Gegendruckzylinder, die Gesamtdicke der Druckplatte wird durch die Zahnradien des Druckzylinders und des Plattenzylinders bestimmt. Wenn die Höhe des Klischees höher ist als sie sein sollte, wird die Umfangsrelieffläche (Pressteile) des Klischees größer als der Druckzylinderradius. In diesem Fall wird keine Druckformanpassung mit der gewünschten Präzision vorgenommen, da die Harmonie zwischen den beiden Zylindern gestört wird. In diesem Fall ist die Bildschirmstruktur des runden Punkts, auf dem der Druck erstellt wird, verzerrt und nimmt eine ovale Form an. Dies führt zu einer Verschmutzung des Bildschirms im Druck, wodurch die Bildqualität beeinträchtigt wird.
Klischees im Druck:
Wenn die Klischees kurz nach Beginn des Druckvorgangs weicher und klebriger werden, ergibt sich das Problem aus der unzureichenden Polymerisation des Klischees nach der Rücken-, Haupt- und Endhaltung. Das Klischee war nicht gesättigt, die Leistung der Lampen nahm ab, die Vakuumfolie war sehr verschmutzt oder die vergilbte Folie verhinderte die Belichtung. Die Belichtungszeiten sollten erneut überprüft werden. Die alten Lampen sollten durch Überprüfen der Belichtungslampen ersetzt werden. Alle Lampen müssen gleichzeitig gewechselt werden. Die Vakuumfolie muss erneuert werden. Wenn das Problem in Form von Rissen auf der Plattendruckoberfläche liegt, ist die Ozonrate möglicherweise zu hoch. Die verwendeten Lösungs- und Reinigungsmittel können sehr aggressiv sein. Möglicherweise verwenden Sie das veraltete Klischee. Er macht jetzt die letzte Ausgabe. Wenn es in einer hellen Umgebung gelagert und nach dem Drucken nicht gut auf der Hülle gereinigt wird, läuft es schnell ab. Daher sollte auf der gereinigten Platte kein Lösungsmittelabfall mehr vorhanden sein. Klischees sollten nach dem Drucken lichtgeschützt aufbewahrt werden. Die Platten sollten so flach wie möglich gehalten werden.
Der dunklere Druck:
Von Anfang an sind die Texte angeschwollen
und Zwischentiefen erscheinen als geschlossen. Die Verwendung von Rasterwalze, die überschüssige Tinte überträgt, spielt dabei eine Rolle.
Das Mischungsverhältnis von Tinte und Verdünner ist möglicherweise falsch. Tinte normale Arbeit
Es hat möglicherweise nicht die richtige Viskosität.
Klischees wurden falsch installiert und es gab einen Luftspalt unter dem Klischeeband. Daher wird ein übermäßiger Druck auf den Raster- und Plattenzylinder ausgeübt. Selbst wenn die Einstellung der Druckform normal ist, wirkt sich aufgrund des Unterschieds in der Dicke auf der Oberfläche des Klischees ein übermäßiger Druck auf das Klischee aus.
Außerdem Belichtungsfehler bei der Plattenherstellung, Vakuummangel, Negativfilm
Ein Mangel an ausreichender Dichte kann dieses Problem verursachen, indem die Klischeequalität beeinträchtigt wird.
Wenn es unter den Klischeesätzen erneuerte gibt, kann die Verwendung des neuen Teils und des alten Teils im selben Druck ebenfalls zu diesem Problem führen. Für die Kontinuität der Druckqualität ist es wichtig, dass die Erneuerungsarbeiten als Set für mehrfarbige Platten durchgeführt werden.
Tintenspritzer:
Dies ist der Zustand, in dem Tinte während des Druckens auf die nicht druckenden Teile (Zwischenprodukte) des Klischees spritzt.
Der Hauptgrund ist, dass zu viel Tinte auf das Klischee übertragen wurde. Darüber hinaus spielt auch die Kraftanpassung der Rasterwalze eine Rolle. Die Tintenübertragungsmenge von Anilox sollte überprüft werden. Anilox sollte bei Bedarf geändert werden. Zusätzlich sollte die Rasterwalze gegen die Kraft geprüft werden.
Barcode-Druck liest nicht:
Oder es kann viele Gründe geben, warum die Barcode-Druckqualität nicht mit der gewünschten Qualität erzielt werden kann. Der Barcode-Druck enthält wichtigere Werte als das Druckmuster auf dem Produkt. Die Hauptgründe für dieses Problem sind: Es wird durch zu viel Kraft verursacht.
Die Barcode-Farbe wurde möglicherweise falsch ausgewählt. Barcode-Sticks sind empfindlich. Die Gesamtlänge wurde möglicherweise stärker als normal verengt. Es gibt nicht genügend Kontrast zwischen der Barcode-Farbe und der Druckhintergrundfarbe. Der Rand oder Boden, der den Barcode begrenzt, befindet sich möglicherweise zu nahe an den Barcode-Balken. Die Richtung des Barcodes ist möglicherweise falsch. Barcode-Verifizierer lesen daher nicht richtig und es kann geschlossen werden, dass der Ausdruck nicht gelesen wird. Barcode-Balken haben möglicherweise eine schlechte Auflösung. Eine niedrige Auflösung führt eher zu gezackten als zu scharfen und linearen Strichlinien, was dazu führt, dass der Barcode-Glätteisen ungenau liest.
Markieren:
Das zu bedruckende Material besteht hauptsächlich aus Wellen an den Rändern. Dies wird dadurch verursacht, dass die Spannung des Materials auf der Druckmaschine nicht eingestellt wird. Die Tatsache, dass eine übermäßige Temperatur entsprechend dem Merkmal des Druckmaterials angewendet wird, ist auch ein Faktor bei der Kennzeichnung. Die Spulenführungen sind möglicherweise nicht richtig eingestellt oder funktionieren nicht. Die Einstellungen des Maschinenblutdrucks müssen erneut überprüft werden. Es wird empfohlen, die Vortrocknungstemperaturen auf der Spule etwas zu senken. Außerdem sollte die Sauberkeit der Spulenführungen überprüft werden.
Die Welligkeit der Abstreifer-Rakelklingen beeinflusst auch die homogene Tintenübertragung auf die Filmoberfläche. Dies führt zu einem schwächenden Erscheinungsbild, indem der Druck dunkel und verliebt wird.
Blutung, Farbmischung:
Es ist, wenn eine Farbe mit einer anderen Farbe gemischt wird.
Die erste auf das Druckmaterial übertragene Farbe trocknet nicht aus. Die Tintenviskosität ist hoch, die Tinte ist sehr präzise und dick. Die Lösungsmittelauswahl ist falsch. Lösungsmittelbilanzen sind schlecht. Überprüfen und korrigieren Sie zuerst die Trocknung und lassen Sie die erste gedruckte Farbe trocknen. Überprüfen Sie die Viskosität der Tinte und setzen Sie die Überprüfungen während des gesamten Druckvorgangs fort. Überprüfen Sie die Lösungsmittelverbrauchsraten.
Blockierung:
Beim Materialwickeln haften die Schichten auf der Spule zusammen und zeigen sich. Der Hauptgrund ist zu sehen, dass die Wicklungsdrücke der Spule hoch sind, aber die Tinte, die nicht ausreichend trocknet, ist auch die Ursache für diese Haftung. Die Tinte trocknet langsam, wobei der Hauptfaktor darin besteht, dass entweder die Trocknungstemperaturen niedrig oder die Betriebsgeschwindigkeit sehr hoch sind. Wenn der Feuchtigkeitsgehalt der Druckoberfläche höher als akzeptabel ist, trocknet sie nicht bis zu den Wickelwalzen aus und verursacht ein Blockieren während des Wickelns.
Füllung:
Tinte sammelt sich auf der Oberfläche des Klischees.
Es ist der Zustand der Füllung. Die Tinte kann Pigmentrückstände und Fremdkörper enthalten. Wenn die Klischeeherstellung nicht falsch ist, blockierten die durch den Zupfeffekt zerbröckelten Partikel die Bildschirme. Die Tintenviskosität ist sehr hoch. Überprüfen Sie den Raster- und Blattdruck.
Probleme beim Vliesstoff-Produktionsprozess
Fasertropfen:
Steinstaub wird im Düsenkopf des Extruders eingeschlossen, wodurch der Faden nicht in einen Strom gelangt, was zu ungleichmäßigem Fadenausstoß und Fadenabfall führt. Eine einfache Möglichkeit, dieses Problem zu beheben, besteht darin, die Extruderdüse zu reinigen und sicherzustellen, dass dies beim nächsten Mal nicht auftritt.
Verstopfung des Filtergewebes:
Dies führt zu ungleichmäßigem Fadendruck und Fadenausfall. Hersteller können eine geeignete Lösung finden, indem sie das Filtergewebe reinigen und herausfinden, was das Gewebe verursacht. Der langsame MFI des Calciumcarbonat-Füllstoffs führt zu einem instabilen Fließen. MFI ist ein wichtiger Index, der die Effizienz des Produktionsprozesses bestimmt. Um dies zu beheben, müssen die Hersteller möglicherweise einige Anpassungen an der Temperatur des Extruders vornehmen. Auf lange Sicht wird jedoch empfohlen, die Füllstoffformulierung für eine bessere MFI zu erneuern.
Maschinenparameter sind für Produktionsmaterialien nicht geeignet. In diesem Fall besteht die einzige Möglichkeit darin, die Maschinenparameter einzustellen.
Faser zu weich oder zu hart:
Bei den mechanischen Eigenschaften der Endprodukte liegt der Hauptgrund in der Rezeptur des Calciumcarbonat-Füllstoffs im Vlies. Eine große Menge an Füllstoff-Masterbatch kann zu einer mangelnden Steifigkeit des Gewebes führen, während die rauen Oberflächen der Endprodukte hauptsächlich auf das Fehlen einiger Additivgruppen zurückzuführen sind.
Schwache mechanische Eigenschaften :
Die Hauptgründe für dieses Problem können die Unverträglichkeit zwischen der Art des im Vlies verwendeten Calciumcarbonat-Füllstoffs und den übergroßen Steinstaubpartikeln sein, die eine schlechte Haftfestigkeit des Gewebes verursachen. Daher sollten Hersteller die Füllstoff-Masterbatch-Formel erneut überprüfen, um sicherzustellen, dass sie am besten zu ihrem Endprodukt passt.