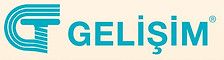


Hidrokarbonlar
Hidrojen ve karbon olmak üzere iki elementten oluşan organik bir bileşiktir. Petrol bileşiminin büyük bir kısmı değişen uzunluklardaki hidrokarbonlardan oluşur.
En küçük hidrokarbon metan, tek bir karbon atomu ve dört hidrojen atomundan oluşur. Bununla birlikte, hidrokarbonlar, zincirler, daireler ve diğer karmaşık şekiller dahil olmak üzere birçok yönden birbirine bağlanmış yüzlerce veya binlerce bireysel atomdan oluşabilir.
Hidrokarbonların özelliklerini sınıflandırmak için birkaç temel türe ayrılırlar.
Alkanlar: Bunlar doymuş hidrokarbonlar olarak adlandırılır. Yani sadece tüm karbon atomları arasında tek bağlar içerirler. Alkanlar, petrol yakıtlarının temelidir ve doğrusal ve dallı formlarda bulunurlar.
Doymamış Hidrokarbonlar: Karbon atomları arasında bir veya daha fazla çift bağa sahip olan hidrokarbonlara alken denir.
Sikloalkanlar: Bir veya daha fazla halka yapısı içeren herhangi bir hidrokarbon.
Aromatik Hidrokarbonlar: Areneler olarak da adlandırılan aromatik hidrokarbonlar, karbon atomlarının birbirini izleyen çift ve tek bağlarla bağlandığı benzersiz bir karbon molekülleri sınıfıdır. Bu molekül sınıfı, karbon atomları arasındaki bağların tek ve çift bağlar arasında bir ara bağ olduğu özel halka yapılarına sahiptir.
Bu sınıftaki moleküller, endüstriyel çözücü «benzen» içerir.
Benzen (C6H6): Diğer hidrokarbonlar gibi benzen de petrolün doğal bir bileşenidir. Oda sıcaklığında renksiz, yanıcı, tatlı kokulu bir sıvıdır ve yüksek oktan sayısına sahip olduğu için çoğu benzin karışımının bir bileşenidir.
Benzen de oldukça kanserojendir ve kemik iliği yetmezliği ve kemik kanserine neden olduğu iyi bilinmektedir. Elbette, “hoş aroması” nedeniyle tıraş sonrası ve diğer kozmetiklerde bir katkı maddesi olarak kullanıldığında kanserojenliği iyi bilinmemektedir.
En büyük benzen kullanımı (% 50), stiren ve polistren plastiklerinin ürünüdür. Ayrıca Naylon üretiminde önemli olan sikloheksan olarak bilinen bir moleküle dönüştürülür. Siklohekzan üretmek için benzenin yaklaşık% 15'i kullanılır. Böcek ilaçlarından kauçuğa kadar her şeyde daha küçük miktarlar kullanılır.
Benzen yapısı iki şekilde çizilebilir. İlkinde, çift bağ karakteri açıkça çizilir. Kısa elli versiyonda, yapıyı göstermek için halkanın içine bir daire çizilir. Benzen içindeki her bir karbon atomuna bağlı tek bir hidrojen vardır.
Aşağıdaki I. ve II. çizimleri eştir. Pratikte III. çizim kullanılır.
Benzen, renksiz, alevlenebilen, kaynama noktası 80,1 °C, erime noktası 5,5 °C olan bir sıvıdır.
Binükleer Aromatik Hidrokarbonlar: Molekülünde iki benzen halkası içeren bileşiklerdir.
Hidrokarbonlar
Hidrojen ve karbon olmak üzere iki elementten oluşan organik bir bileşiktir. Petrol bileşiminin büyük bir kısmı değişen uzunluklardaki hidrokarbonlardan oluşur.
En küçük hidrokarbon metan, tek bir karbon atomu ve dört hidrojen atomundan oluşur. Bununla birlikte, hidrokarbonlar, zincirler, daireler ve diğer karmaşık şekiller dahil olmak üzere birçok yönden birbirine bağlanmış yüzlerce veya binlerce bireysel atomdan oluşabilir.
Hidrokarbonların özelliklerini sınıflandırmak için birkaç temel türe ayrılırlar.
Alkanlar: Bunlar doymuş hidrokarbonlar olarak adlandırılır. Yani sadece tüm karbon atomları arasında tek bağlar içerirler. Alkanlar, petrol yakıtlarının temelidir ve doğrusal ve dallı formlarda bulunurlar.
Doymamış Hidrokarbonlar: Karbon atomları arasında bir veya daha fazla çift bağa sahip olan hidrokarbonlara alken denir.
Sikloalkanlar: Bir veya daha fazla halka yapısı içeren herhangi bir hidrokarbon.
Aromatik Hidrokarbonlar: Areneler olarak da adlandırılan aromatik hidrokarbonlar, karbon atomlarının birbirini izleyen çift ve tek bağlarla bağlandığı benzersiz bir karbon molekülleri sınıfıdır. Bu molekül sınıfı, karbon atomları arasındaki bağların tek ve çift bağlar arasında bir ara bağ olduğu özel halka yapılarına sahiptir.
Bu sınıftaki moleküller, endüstriyel çözücü «benzen» içerir.
Benzen (C6H6): Diğer hidrokarbonlar gibi benzen de petrolün doğal bir bileşenidir. Oda sıcaklığında renksiz, yanıcı, tatlı kokulu bir sıvıdır ve yüksek oktan sayısına sahip olduğu için çoğu benzin karışımının bir bileşenidir.
Benzen de oldukça kanserojendir ve kemik iliği yetmezliği ve kemik kanserine neden olduğu iyi bilinmektedir. Elbette, “hoş aroması” nedeniyle tıraş sonrası ve diğer kozmetiklerde bir katkı maddesi olarak kullanıldığında kanserojenliği iyi bilinmemektedir.
En büyük benzen kullanımı (% 50), stiren ve polistren plastiklerinin ürünüdür. Ayrıca Naylon üretiminde önemli olan sikloheksan olarak bilinen bir moleküle dönüştürülür. Siklohekzan üretmek için benzenin yaklaşık% 15'i kullanılır. Böcek ilaçlarından kauçuğa kadar her şeyde daha küçük miktarlar kullanılır.
Benzen yapısı iki şekilde çizilebilir. İlkinde, çift bağ karakteri açıkça çizilir. Kısa elli versiyonda, yapıyı göstermek için halkanın içine bir daire çizilir. Benzen içindeki her bir karbon atomuna bağlı tek bir hidrojen vardır.
Aşağıdaki I. ve II. çizimleri eştir. Pratikte III. çizim kullanılır.
Benzen, renksiz, alevlenebilen, kaynama noktası 80,1 °C, erime noktası 5,5 °C olan bir sıvıdır.
Binükleer Aromatik Hidrokarbonlar: Molekülünde iki benzen halkası içeren bileşiklerdir.
Hakkında
Kyäni, faydalı bileşenlerden oluşan besin takviyesi ürünlerini; benzersiz iş fırsatıyla birlikte dünya çapında 50'den fazla ülkeye ulaştırmaktadır. İdeal sağlığımızı korumak için günlük olarak Kyäni ürünlerini kullanırız, bu ürünleri başkalarıyla paylaşırız, işimizi inşa etmek ve sürdürmek için neredeyse her gün belirli bir saatimizi işe adarız ve başkalarını da Kyäni fırsatına dahil ederek veya Potato Pak ve Caring Hands programlarına katkı sağlayarak başarımızı başkalarıyla paylaşırız.
Hakkında
Kyäni, faydalı bileşenlerden oluşan besin takviyesi ürünlerini; benzersiz iş fırsatıyla birlikte dünya çapında 50'den fazla ülkeye ulaştırmaktadır. İdeal sağlığımızı korumak için günlük olarak Kyäni ürünlerini kullanırız, bu ürünleri başkalarıyla paylaşırız, işimizi inşa etmek ve sürdürmek için neredeyse her gün belirli bir saatimizi işe adarız ve başkalarını da Kyäni fırsatına dahil ederek veya Potato Pak ve Caring Hands programlarına katkı sağlayarak başarımızı başkalarıyla paylaşırız.
Sayfa Yapım Aşamasındadır.
Sayfa Yapım Aşamasındadır.
Schulungs- / Wissens- / Lösungsplattform
Tiefziehen (Wärmebehandlung)
Das Thermoformen ist ein Verfahren zum Formen einer zweistufigen flachen thermoplastischen Folie. Der Prozess beginnt mit dem Erhitzen und Erweichen der Folie und dem anschließenden Formen des Formhohlraums. Das Material wird auf die Temperatur erhitzt, bei der es gebildet wird, und dann auf (oder innerhalb) einer temperaturgesteuerten Form geformt; Die Form wird gewartet, bis sie abgekühlt ist und das Formteil aus der Form entfernt wurde.
Elastomer- und duroplastische Kunststoffe werden bei Tiefziehverfahren nicht verwendet, da sie aufgrund ihrer vernetzten Struktur nicht erneut wärmebehandelt werden können.
Thermoplaste, die durch Tiefziehen verarbeitet werden können; PP, PS, PVC, LDPE, LLDPE, HDPE, PMMA, ABS.
Thermoformen, Eis- und Margarinebecher, Fleischschalen, Mikrowellenbehälter, Snackbecher, Sandwichpacks usw. in der Lebensmittelverpackungsindustrie Es ist in Produktionen bevorzugt.
Thermoform wird auch zur Herstellung einiger pharmazeutischer und elektronischer Waren, kleiner Geräte, Befestigungselemente, Spielzeuge und Bootsrümpfe verwendet.
Es gibt drei verschiedene Techniken, die in der Umformphase verwendet werden, nämlich Vakuum, Druck und Mechanik.
Vakuum-Thermoform:
Wenn die Thermoformplatte die Kunststoffformoberfläche berührt, kühlt sie ab und härtet aus, und die Thermoformplatte hat die Form eines Produkts / Halbzeugs. Thermoformen (Thermoformen) ist das Formen des halbfertigen thermoplastischen Produkts bei hohen Temperaturen und das Erhalten von Formteilen. Das Halbzeug besteht normalerweise aus granulat- oder pulverhaltigen Filmen und Folien. Die Tiefziehmaschine ist für die Verwendung des Tiefziehverfahrens beim Verpacken ausgelegt. Verpackte Produkte sind in der Regel Endprodukte, die direkt verwendet werden können und nicht weiter verarbeitet werden müssen. Der Tiefziehprozess besteht darin, das Halbzeug (thermoformische Folie / Folie) der Maschine zuzuführen, um es mit Wärmeenergie "umzuformen". Die Filmoberfläche wird erwärmt und erweicht. Wenn die Form geschlossen ist, wird die Wärme abgeschnitten und die Luft in der Form wird mit Vakuum angesaugt. In der Zwischenzeit wird der erweichte Film in die Form gezogen, nimmt die Form der Form an und behält die Form durch Abkühlen bei. Viele Arten von Produkten können beim wärmebehandelten Formen verwendet werden. Dazu gehören dünne Kunststofffolien in Schokoladenboxen, Kunststoffbehälter für heiße oder kalte Getränke sowie einige Produkte und Komponenten, die in Spielzeugverpackungen verwendet werden.


Unter Druck stehende Thermoform:
Diese Verarbeitungstechnik auch; Es handelt sich um einen ähnlichen Prozess wie bei der Vakuum-Tiefziehtechnik. Ebenso wird die Thermoformplatte zunächst mit heißer Luft erwärmt und auf der Form verschlossen. Diesmal wird die Luft in der Form jedoch nicht mit Vakuum angesaugt, und es wird ein hoher Luftdruck in die Form über der Platte aufgebracht. Der Luftdruck zwingt die weiche Schicht, sich zu verformen, um sich gemäß den Formhohlräumen zu verteilen. Bei dieser Verformung berührt die Schicht die Formoberfläche, nimmt die Form der Form an und härtet durch Abkühlen aus.
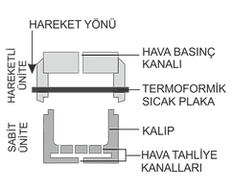

Mechanisches Tiefziehen:
Bei diesem Verfahren wird auch die thermoforme Platte vorgewärmt, um eine bearbeitbare Weichheit zu erzielen, und die Schicht wird direkt mit einer mechanischen Kraft geformt. Die männliche Form der Produktform wird auch beim mechanischen Tiefziehen benötigt. Die männliche Form geht mit hohem Druck in die weibliche Form über und die dazwischen liegende thermoformische Platte wird auf den Raum zwischen den Formen verteilt. Mechanischer Tiefziehprozess; Es ermöglicht genauere Maßtoleranzen und Oberflächendetails als Vakuum- und Druck-Tiefziehverfahren.

Formpressen
Dieses Verfahren wird hauptsächlich zum Formen von duroplastischen Harzen (Duroplasten) verwendet, es können jedoch auch einige thermoplastische Teile durch dieses Verfahren hergestellt werden. Es wird angewendet, indem ein vorgewogenes, erhitztes Polymermaterial, das mit Additiven und Füllstoffen gemischt ist, einem hohen Druck zwischen auf einer hydraulischen Presse montierten geteilten Matrizen ausgesetzt wird.
Ladung: Polymermaterial, das sich in ein Produkt / Halbzeug verwandelt, wird als "Ladung" definiert. Normalerweise wird die Form vorgewärmt, bevor sie in die untere Hälfte gelegt wird. Oder die Formen haben ihre eigenen Heizgeräte. Aufladen; Es kann in Form von Pulver, Gel, Paste, Pellet, Harz vorliegen. Die obere Hälfte der Form bewegt sich nach unten, übt Druck auf die Ladung aus und drückt das Material in Richtung des Füllens des Formhohlraums. Nach dem Zyklusvorgang wird die Form geöffnet und das Teil mittels des Auswerferstifts entfernt. Die Druckformzykluszeit ist länger als der Spritzgusszyklus.
Diese Methode eignet sich besser zum Formen großer flacher oder mittel gekrümmter Teile. EP (Epoxy), UF (Ure Formaldehyd), MF (Melamin Formaldehyd), PF (Phenol) Elastomermaterialien werden üblicherweise durch Formpressen verarbeitet.
Im Formpressprozess; elektrische Steckdosen, Messboxen, Tabletts, Leistungsschalter, Kochtöpfe, Lüfterflügel des Wäschetrockners, Elektronik- und Kochutensilien, Einstellrad für Fräsmaschinen, Autoteile, Fernsehschränke, Geschirr, Gerätegehäuse, Funkboxen, Gehäuse des Hauptstrom-Terminals des Flugzeugs, Hauben, Topfgriffe, Kotflügel, Geschirrteller, Schöpflöffel können hergestellt werden. Das wichtigste Kriterium, das bei dieser Methode berücksichtigt werden muss; Es ist die Anforderung, dass die Menge (Ladungsmenge) des zu formenden Materials sehr gut kontrolliert werden muss, um den Formhohlraum vollständig auszufüllen.
Es kann gezeigt werden, dass die Grundmerkmale des Formpressverfahrens, das einfachere Auftragsverfahren als das Spritzgussverfahren, die Verwendung von duroplastischem Elastomer (höherviskose Materialien im Vergleich zu Thermoplasten) Produkte mit einfacherer Geometrie bevorzugen. Die Applikationsform wird im Allgemeinen durch elektrische Widerstände, Dampf- oder Heißölzirkulation erwärmt.

Formteil übertragen
Das Verfahren wird hauptsächlich zum Formen von duroplastischen Harzen verwendet, aber einige thermoplastische Teile können auch durch dieses Verfahren hergestellt werden. Wie beim Formpressen wird bei diesem Verfahren «Charge» verwendet. Zunächst wird die Ladung in die vorgewärmte Übergabekammer geleitet, die dem Formprozess den Namen gibt. Bei der RAM-Extrusionsmodellierung wird Polymermaterial mit hohem Druck entlang des Kanals (Läufers) in die Form eingespritzt. Hier gibt es eine dritte Matrizenplatte, die sich vom Formpressen unterscheidet. Nachdem die Ladung, die in Form von Pulver, Gel, Paste, Klumpen, Harz vorliegen kann, in der Formform eingefroren ist, wird diese dritte Platte abgetrennt und das Produkt wird erneut mit einem Auswerferstift versehen.
oder das Halbzeug wird aus der Form entfernt. Nach dem Formvorgang werden die Restschrottschmelzen in der Übergabekammer und im Kanal gereinigt.
Diese Teile sind Schrott, da duroplastische Polymere nicht wieder durch Wärme recycelt werden. Zykluszeit des Transferformens; Es ist kürzer als der Formpresszyklus und es können komplexere geformte Produkte erhalten werden. Es hat jedoch eine längere Arbeitszeit als der Spritzgusszyklus und kann keine Produkte mit komplexen Formen sowie Spritzguss herstellen.
Buchstäblich; Es ist ein Verfahren zwischen Spritzgießen und Formpressen in Bezug auf Produktform und Zyklusprozess. Beim Spritzgießen können keramische oder metallische Materialien, die in den Formhohlraum eingebracht werden, beschichtet werden, und es ist ein Verfahren zur Herstellung von Radio- und Fernsehschränken und Karosserien Teile. Vinylester wie EP (Epoxide), UP (ungesättigte Polyester), PF (Phenole) und Duroplaste sind Materialien, die üblicherweise durch Formpressen verarbeitet werden.

Rotationsformen
Der Prozess, auch als Rotationsformen definiert, besteht im Wesentlichen aus 4 Phasen.
(1) Pulverharz wird in die Form gegeben.
(2) Nach dem Schließen der Form wird der Erwärmungsprozess durchgeführt. Während des Erhitzungsprozesses wird die Form um die horizontale und vertikale Achse gedreht. Kunststoff schmilzt dabei und haftet an den Oberflächen der Form. Die Drehzahl ist relativ langsam. Dies liegt daran, dass die Schwerkraft ohne Zentrifugalkraft bewirkt, dass die Formoberflächen richtig beschichtet werden. In der Station mit einer Heizkammer, in der die Heißluftkonvektion die Form beim Drehen erwärmt, erreichen die Temperaturen in der Form je nach Polymer und Formmaterial bis zu 375 ° C.
(3) Der Abkühlvorgang beginnt. Bei großen Lüftern oder Wassersprays wird Luft auf die Wände der Form geblasen oder die Kühlung wird durch Sprühen / Gießen erreicht.
(4) Das Produkt wird aus der Form entfernt. Das Rotationsformen ist ein Formverfahren, das bei hohen Temperaturen und niedrigen Drücken hergestellt wird und im Allgemeinen bei der Herstellung großer Materialien verwendet wird. Heiz- und Abkühlzeiten sowie die Drehzahl der Form sind sehr wichtig, damit das erhaltene Material sauber ist.
Mit dieser Technik werden meist hohle und sperrige Produkte mit konstanter Wandstärke hergestellt. Bootsrümpfe, Kanus, Möbel, Container, Verkehrszeichen, Wassertank, Pontons, Tierheime und Spielzeug können gegeben werden. PE, insbesondere HDPE, PP, ABS, PS sind die am häufigsten verwendeten Materialien in dieser Technik.
Rotationsformen sind im Vergleich zum Spritzgießen und Blasformen einfach und kostengünstiger. Der Produktionszyklus dauert jedoch länger (zehn Minuten oder länger).

Blasformen
Es ist ein Prozess, bei dem ein erhitztes hohles thermoplastisches Rohr in eine geschlossene Form geblasen wird, die der Form des Formhohlraums entspricht. Das für den Spritzguss zu verwendende Teil wird als "Vorformling" definiert. LDPE, HDPE, PP, PVC, PET werden hauptsächlich zum Blasformen verwendet. Nach diesem Verfahren werden verschiedene Produkte in verschiedenen Größen und Formen wie Fässer, Lagertanks, Wasser- oder Kraftstofftanks, recycelbare Flaschen, Spielzeug, Badewannen, Einwegbehälter, Türen und Barrieren in kleinen Booten hergestellt. Es gibt drei verschiedene Formverfahren: Extrusionsblasformen, Spritzblasformen und Streckblasformen.
Extrusionsblasformen:
Es ist weit verbreitet für die Massenproduktion von Plastikflaschen. Das Kunststoffmaterial wird geschmolzen und in Form eines Hohlrohrs (Vorformlings) in eine kalte Metallform gepresst, wo es mit Druckluft aufgepumpt wird, um die Form der Form anzunehmen. Der Vorformling wird zwischen den beiden Matrizenhälften nach unten (vertikal) extrudiert. Wenn der Vorformling die gewünschte Länge erreicht, stoppt die Extrusionsarbeit, die beiden Formhälften verbinden sich und schließen sich. Wenn die Luft aus dem Luftblashohlraum geblasen wird, wird der Vorformling aufgeblasen, bis er vollen Kontakt mit der Formoberfläche hat. Mit dem Abkühlen der Form werden die Formhälften geöffnet und das Produkt / Halbzeug entfernt.
Stretch Blow Moulding:
Dabei wird ein Vorformling spritzgegossen, der mit einer Lanze nach unten gespannt wird.
Der expandierte Vorformling wird dann in einer Blasform aufgeblasen.
Die spezifische molekulare Orientierung gewährleistet eine höhere mechanische Festigkeit, Steifheit und Transparenz des Materials. Dieses Verfahren, das bei der Herstellung von Behältern mit kohlensäurehaltigen Getränken weit verbreitet ist, verwendet hauptsächlich PET.
Spritzblasformen:
Es wird hergestellt, indem Polymermaterial in eine heiße Spritzgussform um ein Blasrohr oder einen Kernstab injiziert wird. Die Extrusion ist eine ähnliche Anwendung wie das Blasformen. Zum Vergleich Einspritzblasen; Es ist ein genauerer und kontrollierbarer Prozess. Es ermöglicht die Herstellung komplexerer Produkte aus einer größeren Vielfalt von Polymermaterialien.
Die Produktionsrate des Spritzblasformens ist jedoch niedriger als beim Extrusionsblasformen.

Beutelvakuumformen
Während die Automatisierung in der Kunststoffformindustrie weit verbreitet ist, wird heute noch eine große Anzahl manueller Verfahren eingesetzt. Zum Beispiel ist das Beutelformen ein Verfahren zur Herstellung von duroplastischen Kunststoffmaterialien zu einer Vielzahl von dauerhaften verstärkten Bauteilen, ein Prozess, der hauptsächlich auf manueller Steuerung basiert. Dabei wird ein spezieller Beutel auf ein Kunststoffwerkstück gelegt, während er sich im Formhohlraum befindet, und es wird Vakuum oder Druckluftdruck um den Beutel angelegt. Die Rollen drücken den Airbag zusammen, wenn der Druck auf den Beutel gerichtet ist, und häufig wird Wärme zugeführt, um den Prozess zu unterstützen. Der Beutel selbst ist normalerweise eine undurchlässige und flexible Hülle aus Trennfolie oder einem elastomeren Material.
Beutelformprodukte sind in der Regel kompakt und stark, und die Dickentoleranzen ähneln denen des Spritzgusses. Bag Form traditionell für die Herstellung von Hochleistungs - Bauteile wie Baustoffe, Geräte - Gehäuse, Autokarosserien, Schiffsrümpfe und verschiedene militärische Produkte verwendet. Es wird auch in Verbindung mit anderen Formtechniken verwendet. Diese Kombination aus Maschine und handbetriebenem Gerät achtet auf Qualität und Detailgenauigkeit bei der Herstellung von Kunststoffen.
Beim Standard-Beutelformverfahren bedeckt der elastische Beutel das Kunststoffmaterial im Formhohlraum. Bevor dies geschieht, muss die Form selbst jedoch gereinigt, vorbehandelt und entlang der Kanten versiegelt werden. Die Form ist normalerweise mit einem Trennmittel und einem Gelschmiermittel beschichtet, aber Formen, die eine einzelne Kurve enthalten, können manchmal stattdessen mit einer Kunststofffolie behandelt werden. Eine Schicht aus verstärkender Glasfaser kann platziert werden, um eine glattere Oberflächenqualität zu erzielen. Die Schlüsselverstärkung ist jedoch normalerweise ein Vorformling, der aus einer Glasfadenmatte besteht. Dieser Vorformling wird vor dem Einsetzen in die Form zusammen mit anderen erforderlichen Verstärkungen oder Additiven dimensioniert.
Absacken und Formen:
Sobald die Form für das Absacken vorbereitet und die Glasfaserverstärkungen platziert sind, kann der eigentliche Herstellungsprozess beginnen. Bei einem Standard-Beutelformverfahren ist normalerweise die folgende Ausrüstung erforderlich, um die manuellen Arbeitsschritte durchzuführen:
Metallzylinder in Paddel- und Scheibenkonfiguration, um die eingeschlossene Luft auszugleichen
Laminierwalzen mit langen oder kurzen Haarsträhnen zum Aufbringen von Klebharzen und Gelbeschichtungen
Bürstenreiniger und Bürstenersatz
Laminier- und Beschichtungsbürsten
Und das flüssige Katalysatorharz ist typischerweise die Verbindung, die Pigmente, Farbstoffe und andere Additive enthält, die über der Formverstärkung verteilt sind. Die Bediener wenden dann gerändelte Handwalzen an, um eine gleichmäßige Verteilung des Harzes unter der Oberfläche des Beutels zu erzeugen, während die gesamte Mischung mit einem undurchlässigen Beutel bedeckt ist. Durch manuelles Walzen wird auch sichergestellt, dass die Verstärkung ohne Lufteinschlüsse, die zu einer Verschlechterung des Formprodukts führen können, ordnungsgemäß mit dem Harz verbunden ist. Diese harzverstärkende Krawatte ist für ein effektives Beutelformen unerlässlich.
Abhängig von den Anwendungsanforderungen können der Verstärkung zusätzliche Materialien wie Holz oder Schaum hinzugefügt werden. Ebenso können Metallverstärkungen oder Trägerkomponenten enthalten sein, da sie vollständig in die Harzverstärkungsbindung eingearbeitet werden können. Die gesamte Einheit wird dann in einen anderen Aushärtungsbereich gebracht, der durch Backen oder Infraroterwärmung beschleunigt werden kann. Nach dem Aushärten wird das erstarrte Produkt aus der Form entfernt oder die Form bricht um sie herum auf. Das Produkt kann dann weiter gestylt oder veredelt werden, bevor es gebrauchsfertig ist.
Das Formen von Beuteln bietet ein hohes Maß an Vielseitigkeit bei der Konstruktion und Laminierung von Bauteilen. Ein Teil davon ist auf die Präzision und enge Dickentoleranz zurückzuführen, die durch Beutelformen erreicht werden können. Die Verwendung verschiedener Arten von Harzverbindungen und -verstärkungen kann eine Vielzahl von Komponenteneigenschaften ermöglichen, indem beim Formen bestimmte physikalische Eigenschaften verliehen werden. Das Formen von Beuteln basiert auch auf relativ kostengünstigen Materialien, und die Werkzeug- und Bearbeitungskosten sind tendenziell niedrig. Das Verlassen auf die Fähigkeiten des Bedieners kann jedoch einer der Hauptnachteile des Prozesses sein. Die Einhaltung der entsprechenden Schulungs- und Sicherheitsbestimmungen ist wichtig, aber selbst geringfügige menschliche Fehler können zu unsachgemäßem Formen führen. Inspektion und Qualitätskontrolle können ebenfalls schwierig sein, da das Verlassen auf einzelne Laminatoren und das Handwalzen auf natürliche Weise zu geringfügigen Abweichungen zwischen den Produktionsläufen führt. Schließlich ist der Prozess relativ langsam und erfordert möglicherweise hohe Arbeitskosten.
Kalandrieren / Walzen
Dieser Verarbeitungsprozess; Das Kalandrieren kann in verschiedenen Begriffen als Walzen oder Kalandrieren definiert werden.
Das Polymermaterial in Pulver- oder Granulatform wird mit der geeigneten Menge an Additiven gemischt und weich gemacht. Diese Mischung wird durch erhitzte Rollen (Rollen) von 150 bis 200 ° C geleitet und in einen Film oder eine Folie umgewandelt.
Wenn es um die gewünschte Dicke geht, wird es durch eine Reihe von Kühlwalzen geführt, gehärtet und dann auf eine Trägerwalze gewickelt.
Rollen, die die Rolllinie bilden; Mischer, Weichmacher, der die gewünschte Dicke ausführt, dh kalibriert, kühler und
Es ist für verschiedene Zwecke wie einen Router konzipiert.
Das Mischer-Enthärter-Walzsystem besteht aus mindestens zwei Walzen.
Kühl- und Führungswalzen können aus einer Walze bestehen.
Der Abstand zwischen den Kalibrierwalzen wird entsprechend der Dicke des Produkts eingestellt.
Es wird allgemein auf rollende thermoplastische Materialien und insbesondere bei der Verarbeitung von Polymeren mit geringer Wärmebeständigkeit angewendet. Das typischste Beispiel hierfür ist PVC.
PVC; Es wird auf drei Arten als flexibel, halbstarr und starr verwendet.
Regenmantel, Badvorhang, Tagesdecke, mit flexiblem PVC
mit halbstarrem PVC für Tischdecken, Fußböden, Kreditkarten, Tabletts, Schilder usw. mit starrem PVC. Produktionen werden durchgeführt.
An der Spitze anderer durch Walzen gebildeter Polymermaterialien;
Kommt mit ABS und gefülltem PE
Zusammenfassend: Kalandrieren ist ein Druckanwendungsprozess; Das Material wird durch mehrere beheizte und gekühlte Walzen gepresst und in eine saubere und helle Folie der gewünschten Dicke umgewandelt. Es ist ein Verarbeitungsverfahren, das allgemein bei der Herstellung von Filmen oder Platten aus Gummimaterialien, PVC und einigen anderen Kunststoffen verwendet wird. Aus dem Kalandrieren entnommene Platten werden dem zu formenden Tiefziehen gegeben. Beim Walzen mit metallischem Material ist das Material heiß, während beim Walzen mit Kunststoff die Walzen heiß sind. Mit kalibrierten Walzen wird Druck auf das Material ausgeübt.
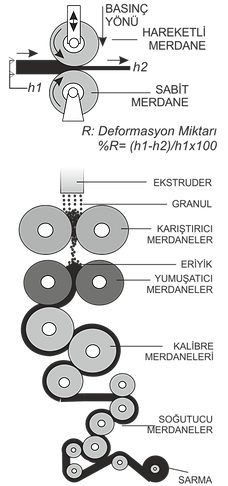
Flüssigkeitsspritzguss
Es ist eine industrielle Herstellungsmethode, bei der Lagermaterialien zu einer Reihe von Komponenten und Produkten geformt werden. Es unterscheidet sich vom Standard-Reaktionsspritzgussverfahren dadurch, dass es eher auf mechanischem Mischen als auf Druckstoßmischen beruht und sich auf Standard-Flüssigspritzgummi und ähnliche elastomere Materialien konzentriert. Es kann eine große Anzahl vielseitiger Produkte wie Dichtungen, O-Ringe, Isolatoren und elektronische Kontakte effizient herstellen.
Ein Großteil der Vielseitigkeit des flüssigen Spritzgießens beruht auf den Materialeigenschaften flüssiger Silikonmaterialien. Diese Silikone weisen ein hohes Maß an Wärme- und Flammwidrigkeit, Zugfestigkeit und Flexibilität auf. Darüber hinaus bieten Silikone nützliche Formbarkeitseigenschaften, die eine Tönung oder Transparenz im fertigen Produkt ermöglichen. Abhängig von ihrer chemischen Zusammensetzung können diese Materialien auch als Isolatoren oder Leiter wirken. Das zur Herstellung von flüssigem Silikon verwendete Flüssigkeitsinjektionsverfahren ist eine empfindliche und andere Methode, mit der äußerst genaue Ergebnisse erzielt werden können.
Flüssiges Spritzgussverfahren: Es konzentriert sich auf das dispergierte Mischen und Verteilen von Materialien auf Kunststoffbasis über eine Reihe von Kolben. Im Allgemeinen enthält ein Kolben Kunststoff, der die Basis bildet und mit Additiven und Fasern verstärkt werden kann, während der andere Kolben einen Katalysator enthält, der die Mischreaktion aktiviert. Das Verbundmaterial wird dann direkt in eine geschlossene Form eingespritzt und nach dem Aushärten wird das nahezu fertige Bauteil aus der Formmaschine entfernt.
Silikone und Acryl sind die am häufigsten im flüssigen Spritzguss verwendeten Materialien. Für die Einspritzstufe kann eine federbelastete Stiftdüse verwendet werden, um zu verhindern, dass die Maschinenausrüstung mit flüssigem Kunststoff verstopft. Durch die Federbelastung wird sichergestellt, dass der Einspritzdruck höher als der der Extruderkammer ist, wodurch verhindert wird, dass der Kanal blockiert wird. Computergestützte Konstruktionswerkzeuge sind auch nützlich, um den Formprozess effizienter zu gestalten. Computerprogramme können Simulationen ausführen, um die effektivsten Verarbeitungsbedingungen zu ermitteln, Ergebnisse auszuwerten und integrierte Geräte zu überwachen. Die Wärmebildtechnologie kann auch Herstellungsfehler wie Formfehler oder Konstruktionsinkonsistenzen identifizieren.
Flüssigkeitsinjektionsmaschinen: Eine Standard-Flüssigkeitsinjektionsformmaschine basiert auf einer Dosierpumpvorrichtung und einer Injektionseinheit, die mit einem dynamischen oder statischen Mischer ausgestattet ist. Im Idealfall werden diese Systeme so kompakt und präzise wie möglich zusammengebaut, während die Umgebungskomponenten so konfiguriert werden, dass sie den Anforderungen eines bestimmten Projekts entsprechen. Die wichtigsten Teile einer typischen Flüssigkeitsinjektionsmaschine sind:
-
Injektoren: Die Injektionsvorrichtung drückt das Formmaterial wie flüssigen Silikongummi unter Druckkraft in den Pumpabschnitt. Der Bediener kann normalerweise den Druck und die Einspritzrate entsprechend den Projektparametern einstellen.
-
Dosiereinheiten: Die Dosiereinheit pumpt zwei flüssige Materialien sorgfältig proportional und gibt sie gleichzeitig mit einer konstanten Geschwindigkeit ab.
-
Fördertrommeln: Materialzufuhrbehälter oder Kolben sind an das Pumpsystem der Maschine angeschlossen. Neben den Fässern mit Mischmaterialien gibt es üblicherweise einen zusätzlichen Behälter für das Pigment.
-
Mischer: Nach dem Durchlaufen der Dosiereinheit werden die flüssigkeitsbildenden Materialien mit einem statischen oder dynamischen Mischer kombiniert. Diese Mischung wird dann unter Druck gesetzt und in die Form gedrückt.
-
Düse: Die Düse, die das flüssige Gemisch in die Form einführt, ist normalerweise mit einem automatischen Absperrventil ausgestattet, das ein Auslaufen der Verbindung oder ein Überfüllen der Form verhindert.
-
Formklemme: Sie wird in Abstimmung mit der Formklemmvorrichtung, dem Injektor, der Pumpe und der Zufuhreinheit ausgelöst. Es fixiert die Form und öffnet sie, wenn der Vorgang abgeschlossen ist.
Lasersintern
Es wird zur Herstellung computergestützter dreidimensionaler Objektobjekte in Schichten von weniger als Millimetern verwendet. In diesem Prozess; Neben polymeren Materialien können auch keramische und metallische Pulver verwendet werden.
Aus Polymermaterialien; Silikon- und Epoxidformen, Funktionsteile aus Nylon, Acrylstyrolteile für Feinguss, Kunstgegenstände aus glasfaserverstärktem PA, PP, PC, ABS und hochfestem kohlefaserverstärktem PA, Architekturmodelle, Zahnschutzprodukte aus Keramikmaterialien, teilweise stabilisierte Zirkonium-Feingussformen, Uuni-Knochen und Gewebegerüste, Prothesen,
Bronzeteile aus metallischen Werkstoffen; Edelstähle und Werkzeugstähle, Bauteile aus Titanlegierungen,
Siliziumkohlenstoffverstärkte Aluminium- und Titankomposite für hochfeste, leichtgewichtige und verschleißfeste Teile für die Automobil- und Elektronikindustrie gehören zu den optionalen Lasersinteranwendungen.
Sintern: Bei dieser Methode werden Pulverpartikel kombiniert, indem das zu verwendende Material unter seiner Schmelztemperatur, jedoch sehr nahe an seiner Schmelztemperatur erhitzt wird.
Prozess; Es beginnt mit dem Verteilen des Pulvers in einer dünnen und gleichmäßigen Schicht auf der Oberfläche der Produktionskammer. Hier beträgt die Dicke der feinen Pulverschicht üblicherweise weniger als 0,1 mm. Hochleistungslaserstrahlabtastung wird auf der Schichtoberfläche gemäß dem CAD-Modell (Computer Aided Design) des herzustellenden Teils durchgeführt. Die Energie des Lasers wird auf einen kleinen Punkt der Blattoberfläche fokussiert, an dem sich das Pulver auf die Sintertemperatur erwärmt. Die Pulverteilchen der Schicht sind aufgrund der Diffusion des Materials aneinander und an die vorherige Schicht gebunden. Die Staubschicht außerhalb des gescannten Bereichs bleibt intakt und trägt den Sinterabschnitt in der Produktionskammer.
Nach dem Pulververteilungsprozess wird der Lasersinterprozess mehrmals wiederholt, bis die Objekterstellung abgeschlossen ist. Nach Abschluss des Vorgangs wird es abkühlen gelassen. Und dann wird das gesinterte Modell aus der Produktionskammer genommen, Luft darauf geblasen und der überschüssige Staub vom Modell entfernt. In diesem Prozess; Die Übergangszeit zur Fertigung mit dem Produktkonzept ist sehr kurz. Es können sehr flexible und detaillierte Designs erstellt werden. Einzigartige Modelle oder ganz spezielle Teile, die benötigt werden, können leicht auf der Basis von Teilen hergestellt werden. Prototypen werden in digitaler Form gespeichert und können bei Bedarf reproduziert werden.

Reaktionsspritzguss
Im einfachsten Sinne ist Reaction Injection Moulding (: REK) die Aufgabe, zwei oder mehr reaktive flüssige Komponenten zu mischen, indem Hochdruck angelegt und bei niedrigem Druck in eine geschlossene Form eingespritzt wird. Mit anderen Worten, es ist eine spezielle Teilmenge der Spritzgusstechnik, die zwei oder mehr Kunststoffe vor dem Formen chemisch an ein Polymer bindet. Während geformte Kunststoffe in einer Vielzahl von industriellen und kommerziellen Anwendungen eingesetzt werden, kann die Auswahl eines bestimmten Formverfahrens die Qualität und Effizienz eines Projekts erheblich beeinträchtigen. Im Allgemeinen werden beim Spritzgussverfahren thermoplastische Harzteile hergestellt, indem geschmolzener Kunststoff in eine Konstruktionsform gedrückt wird. Die verwendeten hohen Drücke erzeugen das Teil, indem der Kunststoff sich an die Form der Form anpassen lässt. Beim Spritzgießen werden wie beim Metallguss typischerweise Bauteile hergestellt, die wenig oder gar keine Arbeit erfordern.
Hersteller, die die Verwendung von REK in Betracht ziehen, möchten möglicherweise bestimmte Eigenschaften untersuchen, die es vom Standard-Spritzguss unterscheiden. Einer der zentralen Unterschiede liegt in der Art der plastischen Polymerisation, die andere Eigenschaften als Basismaterialien aufweisen kann. REK kann auch große Teile mit komplexen Formen herstellen, wodurch es sich gut für industrielle Anwendungen eignet, die sperrige Komponenten erfordern. In ähnlicher Weise können Kosteneffizienz, Produktionszyklusraten und Probleme bei der Maschinenkonstruktion die Entscheidung für diese Technik beeinflussen.
In REK verwendete Kunststoffe:
Polyurethane , Polyamide und Faserverbundwerkstoffe sind die gebräuchlichsten Kunststofftypen im Reaktionsspritzguss. Diese Materialien weisen je nach Anteil der Grundmaterialien oder zusätzlicher Chemikalien, die während der Polymerisation verwendet werden, unterschiedliche Eigenschaften auf. Die verschiedenen Kombinationen können eine Reihe von elastomeren Eigenschaften ergeben, die die Fähigkeit eines Produkts bestimmen, sich mit geringer Spannung zu dehnen und in seine ursprüngliche Form zurückzukehren. Dieser Bereich beeinflusst die Flexibilität von Struktur-, Hart- und Verbundschäumen, die die Hauptprodukte bei der Herstellung von Polyurethan sind.
Da es sich bei dem Verfahren um geschmolzenen Kunststoff handelt, kann REK als eine Form des flüssigen Spritzgießens angesehen werden. Eine der Flüssigkeiten erhält normalerweise Kohlenstoff-Füllstoffe oder Kurzfaserharz, um das Spannungs-Dehnungs-Verhältnis des Produkts zu erhöhen und den Grad der Ausdehnung oder Kontraktion aufgrund thermischer Änderungen zu verringern.
REK-Prozess:
Es ist ein mehrstufiger Prozess, der andere Verfahren als der Standard-Spritzgussprozess umfasst. Zu Beginn werden zwei oder mehr Arten von geschmolzenen Kunststoffen wie Polyisocyanat und eine Harzverbindung in separate Reaktantentanks gegossen, die mit Temperatur- und Beschickungskontrollmechanismen ausgestattet sind. Die Flüssigkeiten werden dann in die jeweiligen Zuleitungen freigesetzt und in eine Messkammer geleitet, die die Druckbeaufschlagung reguliert und den Kunststoff zu einem Mischkopf zurückführt.
Der Mischkopf übt typischerweise Drücke zwischen 1.500 und 3.000 psi aus, um Kunststoffe durch Aufprall zu rühren. Nach dem Mischen der Reaktanten werden sie mit hoher Geschwindigkeit in die Form eingespritzt. Der Mischkopf setzt keine Reagenzien mehr frei, wenn die Form voll ist. Innerhalb der Form findet eine exotherme chemische Reaktion statt, die eine plastische Polymerisation verursacht. Nachdem sich das Polymer verfestigt oder "ausgehärtet" hat, wird es von der Komponente aus der Form entfernt.
REK-Maschinen führen diesen Prozess bei niedrigen Temperaturen durch. Abgesehen von der Wärme, die zur Bildung des geschmolzenen Kunststoffs benötigt wird, ist das Reaktionsspritzgießen ein relativ kühler Prozess. Anstelle von Wärmeenergie erzeugt REK chemische Energie, die durch Polymerisationsreaktionen verursacht wird. Die verwendeten Matrizen bestehen typischerweise aus Stahl, Aluminium oder Nickel und werden mit einer leichten Presse festgeklemmt. Die Aushärtungszeit des Polymers beträgt normalerweise weniger als eine Minute, was zu schnellen Umsätzen und schnellen Produktionszyklen für Operationen mit mittlerem Volumen führt.
REK Industrieanwendungen:
Aufgrund niedriger Verarbeitungstemperaturen und niedriger Einspritzdrücke eignet sich REK gut zum Formen großer Bauteile mit variabler Wandstärke und glatten Oberflächen. Hersteller können auch von der relativ hohen Fluktuationsrate profitieren, die sie für die Abwicklung von Projekten mit geringem und mittlerem Volumen kompetent macht. Darüber hinaus weisen REK-Teile eine hohe Zugfestigkeit, Wärmebeständigkeit und Beständigkeit gegen ätzende Säuren oder Lösungsmittel auf. Eine längere Sonneneinstrahlung kann jedoch Teile auf Polymerbasis verschlechtern, und die Werkzeug- oder Bearbeitungskosten sind für Produkte auf Polymerbasis relativ hoch.
Herstellung von Vliesstoffen
Vliesstoffe (Nonwowen) werden in vielen Arten bewertet und nach ihren Herstellungstechniken kategorisiert.
Produktionstechniken sind hauptsächlich;
-
Schmelzgeblasen
-
Spunbond
-
Spunlace
-
Airlaid
-
Chemisch gebunden
-
Nadel gestanzt - Filze
Einweg-Babywindeln, Harninkontinenzprodukte für Erwachsene, Einweg-Babywindeln, Harninkontinenzprodukte für Erwachsene, medizinische Einwegtextilien, Pflaster, Bandagen, Bett- und Polsterbezüge, Federtaschen, Kissenbezüge, Kissenbezüge, Einnahmen aus Teppichunterlagen.
Für jeden Filtrationstyp, jedes Produkt und jeden Anwendungsbereich gibt es spezielle Vliesarten, die hervorragende Filtrationseigenschaften gemäß internationalen Standards bieten. Darüber hinaus haben Vliesstoffe ein breites Anwendungsspektrum, sei es zur Erhaltung des Bodens, zur Bearbeitung der Landschaft oder zur Verbesserung des Anbaus. Die Tatsache, dass Vliesstoffe an die Landoberfläche transportiert werden und einfach aufzutragen sind, sind ihre größten Vorteile in diesem Bereich.
Abgesehen von diesen sind die Bereiche, in denen Vliesstoffe (Vliesstoffe) verwendet werden, wie folgt:
Filtration:
Auto- und Haushaltsklimaanlagen, Reinraum, Operationssaal-Luftreiniger, Gesichtsmasken, Flüssigkeitsfilterung, Auto-Ölfilter, Maschinenfilter, Ablassfilter, Staubsaugerbeutel, industrielle Staubsammlung und Filterung
Landwirtschaft, Gartenbau:
Mulchen, Ernteabdeckungen, Insektenabdeckungen, Shader, Windabdeckungen, Frostschutz- und Wärmedecken, Schutzabdeckungen für Obst und Gemüse
Geotextilien:
Diese Produkte werden hauptsächlich für den Bau von Autobahnen, Eisenbahnen, Lagerbereichen, Parkplätzen, Lande- und Startpisten am Flughafen, Erdöltransportrohren und -tanks verwendet. Es spielt eine Rolle bei der Stärkung der Bodenmechanik in solchen Konstruktionen. Sie tragen dazu bei, dass plötzliche Belastungen an einem Punkt des Bodens ausgewogen über den gesamten Boden verteilt werden. Darüber hinaus kann es als Bodenverstärker gegen Dammböden oder Erdrutsche eingesetzt werden, da es wasserdurchlässig und für feste Partikel nicht durchlässig ist. Landschaft, Bodenabschnitt, Erdrutschkontrolle, Oberflächen- oder Untergrundbewehrung, Entwässerung, Filtration, Geomembranschutzabdeckung.
Automobilindustrie:
Teppichböden, Innenteppiche, Kofferraummatten und -verkleidungen, Kopf- und Motorhaubenauskleidungen, Sitz- und Türinnenräume, Schalldämmung, Motorhaubenplatzierungspad, Isolierpad für Frontkomponenten und Instrumententafel, Türisolierung, Ölfiltration, Luftfiltration, Batterietrenner.
Verpackung und Verpackung:
Allgemeine Verpackungsbeutel, Einkaufstaschen, Werbe- und Geschenkbeutel und -verpackungen, Lebensmittel- und Getränketaschen, Schutzbeutel und -koffer, elektronische Koffer, Ersatzteilabdeckungen, grundlegende stoßdämpfende Abdeckungen und Abdeckungen, Werbematerialien, Kopfstützen, Eventdekorationen.
Isolierung und Isolierung:
Wärmedämmung, Schalldämmung, Boden- und Wandbeläge, Dacheindeckung, Fliesenunterlage, Feuchtigkeitsbarriere, Feuchtigkeitsstabilisator
Schmelzgeblasener Vlies Anwendung:
Die Schmelzblastechnik zur Herstellung von Vliesstoffen ist eine der am schnellsten wachsenden Techniken in der Vliesstoffindustrie der letzten Jahre, die auf dem Prinzip basiert, dünne Polymerfilamente, die am Ende der Düse selbstklebend sind, mit Hochgeschwindigkeitsluft auf ein sich bewegendes Band (Förderband) oder zu blasen auf einer rotierenden zylindrischen Riemenscheibe (Trommel) ist der Prozess.
Die geblasenen polymeren Filamente bilden ein Netzwerk von Bewegungen mit hoher zufälliger Verschränkung zueinander. Schmelzgeblasene Bahnen bieten eine Vielzahl von Produkteigenschaften, wie zufällige Faserorientierung, geringe bis mittlere Bahnfestigkeit. Ungefähr 40% des schmelzgeblasenen Materials werden im ungebundenen (monolithischen) Zustand verwendet, 60% als Verbund- oder Laminatmaterialkomponente.
(Schmelzgeblasen) Schmelzblasprozess; Es ist einzigartig unter Vliesanwendungen. In seiner einfachsten Form kann es als High-Tech-Version der Zuckerwatteherstellung angesehen werden. Während der Herstellung von Zuckerwatte wird der Zucker durch Druck und Zentrifugalkraft durch kleine Öffnungen in einem rotierenden Spinnrad geschmolzen und in Strängen gedehnt. In ähnlicher Weise wird in dem schmelzgeblasenen System die extrudierte Polymerschmelze mit Luft, die von beiden Seiten mit einer Geschwindigkeit von 300 bis 900 km / h geblasen wird, komprimiert (in die gleiche Richtung kombiniert), während sie dabei ist, den Kopf (die Spitze) mit zu verlassen eine Temperatur von 220-400 ° C. Der sich schnell bewegende Luftstrom streckt und schwächt das geschmolzene Polymer effektiv. Es verfestigt sich mit einer zufälligen Unterbrechung zu feinen Strängen. Diese feinen Polymerfilamente werden dann zu einer zufällig zirkulierenden Bahn verdichtet und zwischen erhitzten Walzen komprimiert, während der effektive Luftstrom zu diesem Zeitpunkt entfernt wird.
Ein typischer Schmelzblasprozess besteht aus Extruder, Schmelzpumpe, Düse, Luftkompressor und Wickeleinheiten.


Der Melt Blown-Prozess hat einen Änderungsprozess, der in zwei Kategorien bewertet werden kann, betrieblich und materiell. Durch Manipulation von Betriebs- und Materialvariablen werden verschiedene schmelzgeblasene Stoffe mit gewünschten Eigenschaften hergestellt.
-
Polymer-Produktionsrate
-
Polymer- und Werkzeugtemperaturen
-
Luftaustrittsgeschwindigkeit
-
Temperatur
-
Sprühabstand
Diese Parameter sind grundlegende Komponenten, die eine Rolle bei der Änderung der wichtigsten Stoffeigenschaften spielen. Dies sind Parameter, auf die online, also während des Betriebs, eingegriffen werden kann.
Die Polymer- und Luftaustrittsgeschwindigkeiten steuern im Wesentlichen den endgültigen Strangdurchmesser, die Verschlingung und das Ausmaß der Schwächungszone.
Polymer-/Form- und Lufttemperaturen beeinflussen in Verbindung mit dem Luftdurchsatz das Aussehen und die Griffigkeit des Gewebes und die Gewebehomogenität in der Produktion.
Der Ausstoßabstand (Abstand von Düsenspitze zu Trommel) beeinflusst im Allgemeinen die Offenheit des Gewebes und die thermische Bindung zwischen den Strängen. Mit zunehmendem Abstand nimmt der Filamentdurchmesser leicht zu.
-
Die Lochgröße
-
Luftraum
-
Luftwinkel
Diese Parameter bestimmen den Netzwerkaggregationstyp. Dies sind Offline-Parameter, die bei Betriebsstopp eingegriffen werden können.
Düsenlochgröße, Düsendesignparameter und Düseneinstellung beeinflussen die Fasergröße. Die Düsenlochgröße sollte groß genug sein, um die Polymerschmelze ohne Verstopfung zu passieren.
Der Luftspalt beeinflusst den Luftaustrittsdruck sowie den Faserbruchgrad.
Prozessrohstoffe:
Grundsätzlich sind Polymere, die bei entsprechender Verarbeitungstemperatur eine niedrige Schmelzviskosität ergeben und innerhalb der Eruptionsstrecke erstarren, sind die bevorzugten Polymere im Verfahren. Polymere werden im Hinblick auf die Korngröße, das schnelle Schmelzen und die Bereitstellung einer gleichmäßigeren Wärmeverteilung bevorzugt.
Polypropylen (PP) besitzt genau diese gewünschten Eigenschaften. Es ist leicht zu verarbeiten und bildet ein gutes Netz.
Polyethylen (PE) ist schwieriger zu schmelzen und zu dünnen Fäden zu blasen als Polypropylen. PE ist aufgrund seiner Elastizität schwer zu ziehen.
PBT Es werden sehr weiche, feinfädige Netze hergestellt.
Nylon 6 ist außerdem leicht zu verarbeiten und erzeugt hochwertige Filamentvliese.
Nylon 11 wird für die Bildung von Bahnen mit einem sehr ungewöhnlichen Ledergefühl bevorzugt.
Mit Polycarbonat (PC) werden sehr weiche Fasergewebe hergestellt.
Polystyrol (PS) ist im Wesentlichen die Wahl, um ein extrem weiches, flauschiges Material ohne Schussfehler herzustellen.
Vliesarten Vliesstoffarten:
Es ist im Allgemeinen in 4 Hauptkategorien unterteilt.
Einweg-Vliesstoffe: Solche Vliesstoffe werden meist für Einwegprodukte oder Mehrwegprodukte (z. B. Staubtücher, die mehrmals gewaschen und wiederverwendet werden können) hergestellt.
Vliesstoffe für allgemeine Anwendungen: Umfasst Körperpflegeprodukte wie Windeln und Damenbinden; medizinische Produkte wie chirurgische Kittel und Abdecktücher; chirurgische und gewerbliche Masken, Bandagen, Taschentücher und Handtücher; Kleider und sogar Kostüme für besondere Anlässe.
Strapazierfähige Vliesstoffe: Weit verbreitet in Haushaltswaren und Einrichtungsgegenständen wie Vorhängen, Möbelpolstern, Matratzenpolstern, Handtüchern, Tischdecken, Decken und Teppichrücken sowie Kleidung und Bekleidung wie Hüte, Futter, Einlagen, Einlagen. Verstärkung anderer Stoffe.
Um die Herstellung von Vliesstoffen zu optimieren, wurde mit dem Einsatz von Calciumcarbonat-Füllstoffen begonnen. Aus Calciumcarbonat-Pulver (CaCO3), Kunstharzen und anderen speziellen Additiven hergestellt, ist Calciumcarbonat-Füllstoff eine der effektivsten Materiallösungen für die Vliesherstellung. Die Anwendung dieses Materials bietet den Endprodukten mehrere Vorteile:
Dies sind Bereiche, in denen Produkte aus Calciumcarbonat-Vliesstoffen von Medizin- und Körperpflege bis hin zu Hygiene, Geotextilien (Gewebe, die in technischen Industrien wie Saugen, Trennen, Filtern, Schutz, Verstärkung und Austrag verwendet werden) reichen.
Vorteile der Zugabe von Calciumcarbonat als Füllstoff zu Vliesstoffen:
-
Verbessert Produktoberflächen
-
Es reduziert den Glanz, macht die Oberfläche matt und blickdicht, was zu einer besseren Deckkraft der Gewebestruktur führt.
-
Verleiht eine natürliche weiße Farbe mit begrenztem Gelbstich
-
Verbessert die Materialstruktur
-
Erzeugt ein angenehmes und baumwolliges Tragegefühl
-
Verhindert den CO2-Fußabdruck bei Berührung
-
Schafft mehr Mikrobereiche für die Luftfilterung und Ölaufnahme
-
Fügt eine erhöhte Wärmeleitfähigkeit und physikalische Festigkeit hinzu
-
Ermöglicht die Senkung der Prozesstemperatur
-
Es ebnet den Weg für eine höhere Produktivität der Produktion, dh es erhöht die Kapazität.
-
Das spart Energie und Produktionskosten.
-
Es kooperiert problemlos mit mehreren Basisharzen (dank seiner guten Dispergierbarkeit) und kann auf verschiedene Weise verarbeitet werden
Empfohlene Verbrauchswerte von Calcium Carbon:
-
5-20% in dünnen Stoffen,
-
20-35% in mittleren Stoffen,
-
bei dicken Stoffen erreicht er 60%.
Wenn eine extrem gute Dispergierung und Stabilität erforderlich ist,
Der Füllstoff-Masterbatch wird typischerweise mit einer Beladungsrate von 78-80% und einem Schmelzindex von 20-40 g/10 min aufgetragen.
Herstellung von Acrylfasern
Bei der Altersaufnahmemethode: Die Faserbildung in der Produktion erfolgt durch das Koagulationsbad.
Daher werden die physikalischen Eigenschaften der durch das Nassspinnverfahren erhaltenen Fasern stark durch die Bedingungen des Koagulationsbades beeinflusst. Daher sollten die Koagulationsbadparameter sehr gut kontrolliert werden. In diesem Artikel werden einige physikalische Ereignisse wie Diffusion und Phasenänderung, die im Koagulationsbad auftreten, und einige Koagulationsbadparameter, die beim Auftreten dieser Ereignisse wirksam sind, zusammengefasst. Außerdem wurde versucht, die Wirkung dieser auf die physikalischen Eigenschaften der Fasern festzustellen.
Polyacrylnitril (PAN)-Polymere, die bei der Acrylfaserherstellung verwendet werden, werden durch radikalische Kettenpolymerisation von Acrylnitrilmonomeren erhalten. Polyacrylnitril-Polymere sind für Schmelzspinnverfahren nicht geeignet, da sie beim Erhitzen auf hohe Temperaturen, die zum Faserspinnen aus der Schmelze verwendet werden, nicht schmelzen und Veränderungen in ihrer chemischen Struktur auftreten. Daher ist es nicht möglich, Fasern aus PAN-Polymeren durch Schmelzspinnverfahren herzustellen. Polyacrylnitril (PAN)-Polymere; Es kann in geeigneten Lösungsmitteln gelöst und in eine Polymerlösung mit geeigneter Viskosität zum Faserspinnen überführt werden. Aus diesen Gründen erfolgt die Faserherstellung aus PAN-Polymeren nach dem Lösungsfaserspinnverfahren.
Das PAN-Polymer ist in vielen bekannten Lösungsmitteln unlöslich. Als Lösungsmittel werden meist Dimethylformamid (DMF) und Dimethylacetatamid (DMAc) verwendet. Diese Lösungsmittel spielen auch eine Rolle bei der Bestimmung der Eigenschaften der hergestellten Fasern.
Zum Faserspinnen aus der hergestellten Polymerlösung werden Spinndüsensysteme mit sehr feinen Löchern verwendet. Die Anzahl der Löcher dieser Düsen variiert stark in Abhängigkeit von der verwendeten Aufnahmemethode. Außerdem werden diese Löcher segmentweise, also gruppenweise, auf der Düse platziert. Auf diese Weise wird ein besseres Eindringen des Koagulans zwischen die aus den Düsen ausgestoßenen Filamente gewährleistet.
Lösungsmittel, die beim Spinnen von Acrylfasern verwendet werden, und Polymergehalt im Ziehdock:

Beim Trockenstreckverfahren: Das Streckmittel wird aus den im Turm angebrachten Düsen in den Streckwerksturm gesprüht.
Gleichzeitig wird dank des in den Turm geleiteten erhitzten Gases das Lösungsmittel im Spinnlösungspolymer weitgehend entfernt und das Polymer verfestigt sich und wird zu einer Faser.
Beim Nassziehverfahren wird die Aspirationslösung aus dem Düsensystem, das in ein koagulierendes Flüssigkeitsbad eingetaucht ist, in das Bad gespritzt. Durch die gegenseitige Diffusion des Nichtlösungsmittels im Bad und des Lösungsmittels im Polymer verfestigt sich das Polymer und wird zu einer Faser. Da bei der Nassspinnen-Acrylherstellung die erste Faserbildung im Koagulationsbad stattfindet, spielen die Koagulationsbadparameter insbesondere für die physikalischen Eigenschaften der Fasern eine entscheidende Rolle.
Die Prozesse von Acrylfasern nach dem Trocken- und Nassspinnen sind im Wesentlichen gleich. Die Reihenfolge dieser Verfahren oder die Anwendungsbedingungen können jedoch etwas abweichen. Diese Prozesse sind Waschen, Strecken, Vorbereiten, Trocknen, Kräuseln und Glühen. Alle diese Prozesse wirken sich auf die physikalischen Eigenschaften der Fasern aus.
Produktionsanlage für Polyacrylnitrilfasern nach dem Nassspinnverfahren:
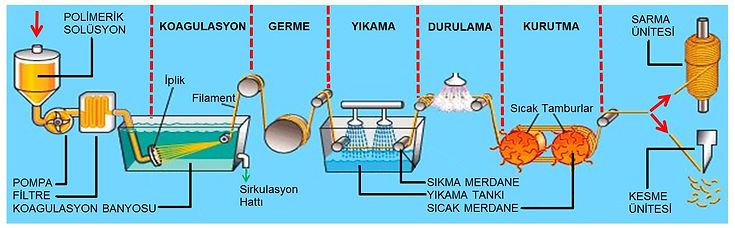
Gerinnung: Es ist der Prozess der Umwandlung des Polymermaterials in Faserform durch Entfernen einer großen Menge des Lösungsmittels in der Polymerlösung, die in Form sehr dünner Flüssigkeitsstrahlen aus den Düsen ausgestoßen wird. Das für dieses Verfahren verwendete Fällbad ist ein flüssiges Medium, das Lösungsmittel und Nichtlösungsmittel enthält. Im Koagulationsbad wird das gleiche Lösungsmittel wie das Lösungsmittel in der Polymerextraktionslösung verwendet. Als Nichtlösungsmittel wird Wasser verwendet, bei dem es sich um eine Flüssigkeit handelt, in der sich das Polymer nicht löst, aber in die Spinnlösung eindringen und sich mit dem Lösungsmittel vermischen kann.
Das Fällbad ist die Phase, in der die erste Faserbildung bei der Faserherstellung stattfindet und spielt eine sehr wichtige Rolle bei der Bildung der Fasereigenschaften. Im Koagulationsbad verwandelt sich das Polymermaterial in eine gelartige Faser, und das Lösungsmittel und das Nichtlösungsmittel werden durch gegenseitiges Fließen ausgetauscht.
Durch die Wechselwirkung Polymer/Lösungsmittel/Nichtlösungsmittel im Koagulationsbad wird die Faser geformt und erhält unterschiedliche Eigenschaften. Bei dieser Wechselwirkung spielen zwei Ereignisse im Koagulationsbad eine besonders wichtige Rolle. Dies sind Diffusions- und Phasenwechselereignisse. Diese beiden wichtigen Ereignisse sind zusammen wirksam bei der Bestimmung der Struktur der Fasern.
Beim Nassspinnen wird aufgrund der Phasenänderung und Diffusionsgeschwindigkeit eine poröse Faserstruktur erhalten.
Während beim Trockenziehen Poren mit einer Größe von 0,1µ gebildet werden, sind diese Poren beim Nassziehen etwa 0,3µ groß und können durch Vergrößerung bis zu 10µ erreichen.
Flush Rate: Die Geschwindigkeit, mit der die Polyacrylnitril-Aspirationslösung (Dope) aus den Düsen in das Bad gespritzt wird (V),
größer ist als die Austrittsgeschwindigkeit (V1) aus dem Fällbad.
2 QV /4 D = π
D: Düsenlochdurchmesser
Q: steht für die Durchflussmenge.
Dies bedeutet nicht, dass das Filament im Zugbad nicht gestreckt wird. Denn wenn das Filament aus der Ebene kommt, quillt es aufgrund des normalen Drucks auf und seine Geschwindigkeit nimmt ab und die freie Geschwindigkeit (Vf) des Filaments wird niedriger sein als die Austrittsgeschwindigkeit aus dem Bad ( Vf < V1 < (V) ). Daher wird das Filament im Bad etwas gestreckt.
Der Durchmesser des durch Quellung in das Koagulationsbad ausgestoßenen Filaments kann bis zum 10-fachen des Durchmessers des Düsenlochs betragen.
Diffusionsereignis: Es ist der gegenseitige Fluss des Lösungsmittels im Filament, das in das Koagulationsbad gesprüht wird, und des Nichtlösungsmittels im Bad. Mit der Diffusion nimmt die Lösungsmittelmenge in der Polymerlösung ab und dank dieser Abnahme wird das Filament zu einem festen Gel. Außerdem verursacht dieses Diffusionsphänomen die Bildung von Poren in der Struktur der durch Naßspinnen erhaltenen Fasern. Obwohl einige dieser Poren in späteren Prozessen eliminiert werden, können sie nicht vollständig eliminiert werden.
Phasenwechsel : Lösungsmittelreiche Filamente, die während des Phasenwechsels aus den Düsen ausgestoßen werden, verwandeln sich zunächst in ein polymerreiches Gel und werden fest, nachdem das Lösungsmittel in nachfolgenden Prozessen vollständig entfernt wurde.
Flexodruckeinheit
Die zweite Stufe, die im Allgemeinen der Blasfolienlinie folgt, sind die Schneid- und Schneideinheiten.
Wenn jedoch ein Druck auf die Produkte gewünscht wird, bilden die Korona- und dann die Druckeinheiten (insbesondere Flexodruckeinheiten) die zweite Stufe. Es ist die am weitesten verbreitete Druckform im Verpackungsdruck. Flexodruck ist ein Verfahren, bei dem ein flexibles geprägtes Blatt verwendet wird, um auf ein Substrat zu drucken, das ein gummibasiertes, synthetisches oder laminiertes Material sein kann. Folien wie Polyester, OPP, Nylon und PE, Papiere, Pappbögen, Vliesstoffe, beschichtete oder unbeschichtete Liner sind die Schichten, die beim Flexodruck verwendet werden können. Heutige Flexodruckmaschinen stellen Fotopolymer-Druckplatten her, die ein Spiegelreliefbild des erforderlichen Drucks enthalten.
Verwendet.
In der Flexodrucktechnik; Es besteht das Prinzip, die Tinte im Tintenreservoir von dort auf die gesiebte (Anilox) Walze auf die Formwalze zu übertragen und auf das Druckmaterial zu übertragen, das in Kontakt mit der Druckwalze durchläuft.
Aus dem Tintenreservoir wird die Tinte durch eine Walze zur Rasterwalze befördert. Überschüssige Tinte wird mit einer Rakel von der Walze abgezogen. Von der Rasterwalze zur Hülse / zum Kessel, um Tinte auf die auf dem Druckkontakt eingravierte Platte zu übertragen
Die Übertragung ist abgeschlossen. Das Klischee, das die Tinte empfängt, überträgt das Muster auf das Druckmaterial, das über die Trommel läuft. Obwohl es sich um ein einfaches Rezept handelt, ist das Flexodruckverfahren ein rein technisches Verfahren. Für die Kontinuität der Druckqualität müssen die Werte für die Tintenviskose kontinuierlich angepasst werden.
Verfolgung von Rakelklingen auf Raster, Raster auf dem Klischee, Druckwerteinstellungen des Klischees auf dem Film, kontinuierliche Kontrolle der Filmqualität (Flaggen, Falten, Koronaintensität), Nachverfolgung der Spannung der Wicklungsspannung und der Spannung auf den Rollen, die Stabilität der Ausrichtungsreferenzpunkte (Kreuz). Es hat empfindliche Punkte, die eine kontinuierliche Überwachung und Messung erfordern. Flexodrucklinien sind Produktionslinien der zweiten Stufe, meist nach der Blasfolienproduktionslinie. Und die Produkte, die hier herauskommen, sind Halbzeuge / Halbformprodukte, die zum Schneiden, Pflügen und Schneiden von Einheiten wie Beuteln, Bändern und Schrumpfbeuteln verwendet werden.
Rasterwalze (Straßenbahnwalze):
Im Flexosystem ist es der Name der Walze, die die Tinte auf die gewünschte Größe der Form befördert. In den letzten Jahren sind sehr dünne Rasterwalzen zum Einsatz gekommen, da im Flexodruck Diadrucke erstellt werden. Rasterwalzen sind in 60, 120, 200 usw. erhältlich. als Zahlen bezeichnet. Mit zunehmender Anzahl nimmt die Dichte der Flusen auf dem Raster zu und ihre Tiefe nimmt ab. Wenn der übertragene Tintenfilm dünner wird, nimmt daher die empfangene Farbintensität ab. Für solche dünnen Aniloxen müssen konzentriertere Tinten hergestellt werden.
Hopper Roller:
Es handelt sich im Allgemeinen um gummibeschichtete Zylinder, die sich innerhalb des Tintenreservoirs drehen, in dem sich die Tinte befindet, und sich je nach System ändern. Die Reservoirwalze ist für die Übertragung der Tinte auf die anderen Elemente des Systems verantwortlich. Es überträgt die Tinte, die es mit Hilfe von Gummi aus dem Reservoir nimmt, auf den Rasterzylinder, mit dem es in Kontakt steht.
Rakelmesser (Doktor. Klinge):
Tintenentferner-Klinge. Es ist einer der wichtigen Teile des Flexodrucksystems. Die von der Walze in der Kammer entnommene Tinte wird mit einer Rakel, die die Rasterwalze berührt, auf die gewünschte Filmdicke verdünnt und auf das Material übertragen. Die Tintendicke auf der Rasterwalze wird durch den Abstreiferdruck, dh die Kraft, bestimmt.
Unterdruckmaterial (Film):
In der Verpackungsbranche ist die Folie eine dünne und elastische Schicht aus einem nicht faserigen organischen Material. Im Flexodruckgeschäft allgemein; Es werden Filme in Rollenform aus Materialien wie Polyethylen, Polyvenylchlorid, Polypropylen, Polyamid, Polyester und Papier verwendet.
Flexo-Form (Klischee):
Flexodruckformen sind Materialien, die unter Verwendung fotografischer und digitaler Verfahren aus Gummi und Fotopolymermaterialien hergestellt wurden, um Bilder und Texte zu übertragen, die auf verschiedene Materialien zur Verwendung in Flexodruckmaschinen gedruckt werden sollen. Es gibt auch Photopolymerformen, die durch photomechanische Verfahren aus Polymermaterialien hergestellt werden.
Diese Formen werden im Allgemeinen biegsam hergestellt. Es kann in Formen aus Zinkplatten durch ein photomechanisches Imprägnierungsverfahren verwendet werden.
Formzylinder (Kessel):
Sie sind Zylinder mit unterschiedlichen Durchmessern, auf denen Klischees montiert sind. Die Durchmesserstärke kann je nach Auftragsgröße variieren. Der Durchmesser und die Länge des Zylinders sind proportioniert.
Diese Teilungen erleichtern das gerade oder diagonale Befestigen der Platte während der Montage.
Sleev (Hemd):
Es sind Werkzeuge, die auf Klischees montiert und an den Zylinder weitergegeben werden. Kurze und sich wiederholende Arbeiten sind Werkzeuge, mit denen die Platte wirtschaftlich gedruckt werden kann, ohne dass eine Neueinstellung und Montage erforderlich ist. Polyester, Stahl, Nickel, Duroflex (Urethan) und beschichtete Hülsen sind erhältlich. Diese Montage erfolgt durch Anbringen der Laufbuchse am Zylinder mit Druckluft.
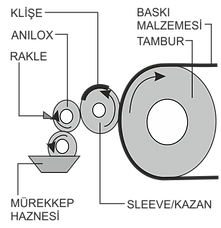
Grundbegriffe für den Flexodruck
Blutdruck:
Es ist die Spannung des Materials während des Druckens in Flexodruckmaschinen. Der Blutdruckwert ist wichtig für kontinuierlichen und ununterbrochenen Druck. Im Allgemeinen kann eine hohe Spannung in dicken Materialien wie Papier und eine niedrige Spannung in dünnen Materialien wie (PE, PP, OPP usw.) angewendet werden. In der Blutdruckeinstellung; Die Dehnbarkeit des Films, seine Wärmebeständigkeit, seine Spannungsempfindlichkeit, seine Dicke und die Grammatikeigenschaften für Papiere sollten berücksichtigt werden.
Viskosität:
Es ist definiert als der Strömungswiderstand von Flüssigkeiten. Die Tintendichte ist beim Flexodruck sehr wichtig. Aus diesem Grund muss die Viskosität der Tinte ständig überwacht werden.
Dichte:
Die Dichte von Substrat und Tinte. Es ist hoch in Gewicht und Fülle, wenig Licht und selten.
Galeerensklave:
Der Druck, den die beiden Zylinder aufeinander oder auf das zwischen ihnen verlaufende Druckmaterial ausüben, wird als Fosa bezeichnet. Forsa, der Raum zwischen den Walzen, wenn sie sich nähern, beeinflusst den Druck während der Verwendung des Druckmaterials oder der Tintenfilmschicht.
Corona:
Es ist der Prozess des Einstellens der Oberflächenspannung, um die Oberfläche der zu bedruckenden Materialien druckbar zu machen. Im Allgemeinen wird für Materialien wie PE, PP, PVC eine Korona von 36 bis 38 dyn / cm angewendet. Eine hohe Korona ist ebenso ein Problem wie nicht niedrig.
Laminierung:
Die Aufgabe, zwei oder mehr Materialien miteinander zu verbinden. Zweck der Laminierung; Es soll den gewünschten Schutz bieten, indem die Durchlässigkeit von Feuchtigkeit, Licht und Gas verringert wird, die zum Verderben von Lebensmitteln in der Verpackung führen kann, und die Attraktivität erreicht werden, die den Verbraucher anzieht.
Blockierung:
Es ist ein Problem, das durch die Übertragung und Haftung der gedruckten Arbeit auf der nicht bedruckten Oberfläche aufgrund von dichtem Aufwickeln, starkem Beschuss, Materialien mit Korona auf beiden Seiten und Hitzeeinwirkung auftritt, wodurch der Druck riecht Schlecht.
Adhäsion:
Es ist die Gravitationskraft, die zwischen zwei verschiedenen Substanzen besteht und die es diesen beiden Substanzen ermöglicht, zusammenzuhalten. Im Flexodruckgeschäft; Es bezieht sich auf die Fähigkeit der Tinte, an dem gedruckten Material zu haften.
Cellophan:
Aus Holz gewonnene Cellulose wird dann durch Reaktion mit Chemikalien in Viskose und dann in Cellulosehydrat umgewandelt und in Form eines Films gepresst. Dieser gepresste Film wird als Cellophan bezeichnet.
Alaun (Säure) Bad:
Es ist der Prozess des Waschens der Zinkform mit Chemikalien.
Emulsion:
Empfindliche Substanz in die Form gegossen. (Lichtempfindliche Substanz)
Ufer:
Die Härte von Klischeeformen.
Linderung:
Entlastungseffekt
Lösungsmittel:
Flüssige Flüssigkeiten wie Verdünner, Naphtha, Terpentin, Lack, Glykol, Ethylalkohol.
Penetration (Penetration):
Es ist die Form des Trocknens, die durch Absorbieren der flüssigen Phase der Tinte durch die Druckoberfläche auftritt.
Blutung:
Das Mischen von Farben auf der bedruckten Oberfläche.
Anilinfarbstoff:
Es ist ein organischer Farbstoff, der aus Steinkohleether gewonnen wird. Wird im Flexodruck verwendet.
UVC-Exposition:
Lichtquelle mit der niedrigsten Wellenlänge, die für die Belichtung von Platten im Flexodruck verwendet wird. UVC-Belichtung beseitigt die Klebrigkeit auf der Plattenoberfläche. UVC-Licht ist für das menschliche Auge äußerst schädlich und sollte nicht direkt mit bloßem Auge betrachtet werden.