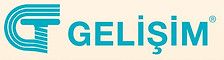


Hidrokarbonlar
Hidrojen ve karbon olmak üzere iki elementten oluşan organik bir bileşiktir. Petrol bileşiminin büyük bir kısmı değişen uzunluklardaki hidrokarbonlardan oluşur.
En küçük hidrokarbon metan, tek bir karbon atomu ve dört hidrojen atomundan oluşur. Bununla birlikte, hidrokarbonlar, zincirler, daireler ve diğer karmaşık şekiller dahil olmak üzere birçok yönden birbirine bağlanmış yüzlerce veya binlerce bireysel atomdan oluşabilir.
Hidrokarbonların özelliklerini sınıflandırmak için birkaç temel türe ayrılırlar.
Alkanlar: Bunlar doymuş hidrokarbonlar olarak adlandırılır. Yani sadece tüm karbon atomları arasında tek bağlar içerirler. Alkanlar, petrol yakıtlarının temelidir ve doğrusal ve dallı formlarda bulunurlar.
Doymamış Hidrokarbonlar: Karbon atomları arasında bir veya daha fazla çift bağa sahip olan hidrokarbonlara alken denir.
Sikloalkanlar: Bir veya daha fazla halka yapısı içeren herhangi bir hidrokarbon.
Aromatik Hidrokarbonlar: Areneler olarak da adlandırılan aromatik hidrokarbonlar, karbon atomlarının birbirini izleyen çift ve tek bağlarla bağlandığı benzersiz bir karbon molekülleri sınıfıdır. Bu molekül sınıfı, karbon atomları arasındaki bağların tek ve çift bağlar arasında bir ara bağ olduğu özel halka yapılarına sahiptir.
Bu sınıftaki moleküller, endüstriyel çözücü «benzen» içerir.
Benzen (C6H6): Diğer hidrokarbonlar gibi benzen de petrolün doğal bir bileşenidir. Oda sıcaklığında renksiz, yanıcı, tatlı kokulu bir sıvıdır ve yüksek oktan sayısına sahip olduğu için çoğu benzin karışımının bir bileşenidir.
Benzen de oldukça kanserojendir ve kemik iliği yetmezliği ve kemik kanserine neden olduğu iyi bilinmektedir. Elbette, “hoş aroması” nedeniyle tıraş sonrası ve diğer kozmetiklerde bir katkı maddesi olarak kullanıldığında kanserojenliği iyi bilinmemektedir.
En büyük benzen kullanımı (% 50), stiren ve polistren plastiklerinin ürünüdür. Ayrıca Naylon üretiminde önemli olan sikloheksan olarak bilinen bir moleküle dönüştürülür. Siklohekzan üretmek için benzenin yaklaşık% 15'i kullanılır. Böcek ilaçlarından kauçuğa kadar her şeyde daha küçük miktarlar kullanılır.
Benzen yapısı iki şekilde çizilebilir. İlkinde, çift bağ karakteri açıkça çizilir. Kısa elli versiyonda, yapıyı göstermek için halkanın içine bir daire çizilir. Benzen içindeki her bir karbon atomuna bağlı tek bir hidrojen vardır.
Aşağıdaki I. ve II. çizimleri eştir. Pratikte III. çizim kullanılır.
Benzen, renksiz, alevlenebilen, kaynama noktası 80,1 °C, erime noktası 5,5 °C olan bir sıvıdır.
Binükleer Aromatik Hidrokarbonlar: Molekülünde iki benzen halkası içeren bileşiklerdir.
Hidrokarbonlar
Hidrojen ve karbon olmak üzere iki elementten oluşan organik bir bileşiktir. Petrol bileşiminin büyük bir kısmı değişen uzunluklardaki hidrokarbonlardan oluşur.
En küçük hidrokarbon metan, tek bir karbon atomu ve dört hidrojen atomundan oluşur. Bununla birlikte, hidrokarbonlar, zincirler, daireler ve diğer karmaşık şekiller dahil olmak üzere birçok yönden birbirine bağlanmış yüzlerce veya binlerce bireysel atomdan oluşabilir.
Hidrokarbonların özelliklerini sınıflandırmak için birkaç temel türe ayrılırlar.
Alkanlar: Bunlar doymuş hidrokarbonlar olarak adlandırılır. Yani sadece tüm karbon atomları arasında tek bağlar içerirler. Alkanlar, petrol yakıtlarının temelidir ve doğrusal ve dallı formlarda bulunurlar.
Doymamış Hidrokarbonlar: Karbon atomları arasında bir veya daha fazla çift bağa sahip olan hidrokarbonlara alken denir.
Sikloalkanlar: Bir veya daha fazla halka yapısı içeren herhangi bir hidrokarbon.
Aromatik Hidrokarbonlar: Areneler olarak da adlandırılan aromatik hidrokarbonlar, karbon atomlarının birbirini izleyen çift ve tek bağlarla bağlandığı benzersiz bir karbon molekülleri sınıfıdır. Bu molekül sınıfı, karbon atomları arasındaki bağların tek ve çift bağlar arasında bir ara bağ olduğu özel halka yapılarına sahiptir.
Bu sınıftaki moleküller, endüstriyel çözücü «benzen» içerir.
Benzen (C6H6): Diğer hidrokarbonlar gibi benzen de petrolün doğal bir bileşenidir. Oda sıcaklığında renksiz, yanıcı, tatlı kokulu bir sıvıdır ve yüksek oktan sayısına sahip olduğu için çoğu benzin karışımının bir bileşenidir.
Benzen de oldukça kanserojendir ve kemik iliği yetmezliği ve kemik kanserine neden olduğu iyi bilinmektedir. Elbette, “hoş aroması” nedeniyle tıraş sonrası ve diğer kozmetiklerde bir katkı maddesi olarak kullanıldığında kanserojenliği iyi bilinmemektedir.
En büyük benzen kullanımı (% 50), stiren ve polistren plastiklerinin ürünüdür. Ayrıca Naylon üretiminde önemli olan sikloheksan olarak bilinen bir moleküle dönüştürülür. Siklohekzan üretmek için benzenin yaklaşık% 15'i kullanılır. Böcek ilaçlarından kauçuğa kadar her şeyde daha küçük miktarlar kullanılır.
Benzen yapısı iki şekilde çizilebilir. İlkinde, çift bağ karakteri açıkça çizilir. Kısa elli versiyonda, yapıyı göstermek için halkanın içine bir daire çizilir. Benzen içindeki her bir karbon atomuna bağlı tek bir hidrojen vardır.
Aşağıdaki I. ve II. çizimleri eştir. Pratikte III. çizim kullanılır.
Benzen, renksiz, alevlenebilen, kaynama noktası 80,1 °C, erime noktası 5,5 °C olan bir sıvıdır.
Binükleer Aromatik Hidrokarbonlar: Molekülünde iki benzen halkası içeren bileşiklerdir.
Hakkında
Kyäni, faydalı bileşenlerden oluşan besin takviyesi ürünlerini; benzersiz iş fırsatıyla birlikte dünya çapında 50'den fazla ülkeye ulaştırmaktadır. İdeal sağlığımızı korumak için günlük olarak Kyäni ürünlerini kullanırız, bu ürünleri başkalarıyla paylaşırız, işimizi inşa etmek ve sürdürmek için neredeyse her gün belirli bir saatimizi işe adarız ve başkalarını da Kyäni fırsatına dahil ederek veya Potato Pak ve Caring Hands programlarına katkı sağlayarak başarımızı başkalarıyla paylaşırız.
Hakkında
Kyäni, faydalı bileşenlerden oluşan besin takviyesi ürünlerini; benzersiz iş fırsatıyla birlikte dünya çapında 50'den fazla ülkeye ulaştırmaktadır. İdeal sağlığımızı korumak için günlük olarak Kyäni ürünlerini kullanırız, bu ürünleri başkalarıyla paylaşırız, işimizi inşa etmek ve sürdürmek için neredeyse her gün belirli bir saatimizi işe adarız ve başkalarını da Kyäni fırsatına dahil ederek veya Potato Pak ve Caring Hands programlarına katkı sağlayarak başarımızı başkalarıyla paylaşırız.
Sayfa Yapım Aşamasındadır.
Sayfa Yapım Aşamasındadır.
Eğitim / Bilgi / Çözüm Platformu
Ekstruzyon
Buraya kadar, Plastik malzemelerin ne şekilde üretildiği, sınıfları hakkında en temel bilgileri gördük. Basit yapıdaki bu temel plastik hammaddelerin yegane ortak paydası; aynı ufak moleküler yapılarının birleşmesiyle oluşmuş büyük moleküler yapıda olmalarıdır. Bu bir, belki iki, tipte moleküler yapılarından dolayı monomerler olarak tanımlanırlar ve polimerizasyon işlemi ile birbirleriyle birleştirilirler. Uygulanan işlemin adından da anlaşılacağı gibi, reaksiyondan çıkan malzeme artık polimer niteliğine geçer. Her ne kadar bileşik yapıda olsa da ilk adımda çıkan bu polimerler ile nihai ürün üretimine çok nadir geçilir. Yani %100 PE (veya PP, SAN vs.) polimerinin kullanımı ile ürün üretimine gidilmez. Üretilecek ürünün niteliği kapsamında, UV direnimi olan, farklı renk tercihi edilen, darbe dayanımı yüksek olması istenen, yanmazlığının olmasının istenmesi gibi bir çok türevde özelliklerinin olması tercihiyle ilave katkılar, renklendiriciler, aromatikler vs. istenilen oranlarla, PE ye (veya PP, SAN vs.) dahil edilir. Başlangıçta %100 PE (veya PP, SAN vs.) artık diğer katılımların oranları toplamı kadar azalarak, ana taşıyıcı polimer niteliğine kavuşur ve polimer; kompleks polimer biçimini alır. Tüm bu işlemler için uygulanan temel uygulama Ekstruzyondur.
Ekstruder: En basit tabirle, farklı polimerlerin birbiriyle veya polimerlerin ek katkı ürünleri ile homojonize olması için ısıl işlemden geçirilerek eriyik formuna dönüştürülmesi işidir ve termoplastiklerin kullanıldığı sahada ana işlemdir. Bu işlemin gerçekleştiği ünite/makine de, ekstruder makinesi olarak tanımlanır. En temel tanımlama ile ekstruderler;
1- Karışım ve basınç için Vida-Kovan
2- Isı aktarımı için Rezistans
3- Mekanik hareket için Redüktör/Motor 'dan ibarettir.
Ekstruder çeşitli bölümleri olan bir işleme makinesidir; madde bir hopperden ısıtılan bir odacığa beslenir; burada ısınır ve yumuşar, sonsuz bir vida sistemiyle homojenleştirilerek ekstruder çıkışına bağlanmış bir kalıba basılır.
Ekstruderde farklı ısı bölgeleri, ısı kontrol panelleri, filtre veya süzgeç gibi sistemler bulunur. Kalıba basılan ergimiş plastik soğuyup sertleştikten sonra kalıp açılır ve malzeme çıkarılır.
Kalıplama prosesi sırasında kimyasal reaksiyon olmaz. Üretilecek nesneye göre değişik ve farklı teknolojilerde kalıplar kullanılır. Ekstruzyon sürekli (kontinü) veya yarı sürekli (semi-kontinü) yapılabilir. Bazı malzemelere sıcak çekme (hot drawn) uygulanırken, bazılarına soğuk çekme (cold drawn) uygulanır.
Soğuk çekme, örneğin kuvvetli naylon flamentlerin üretilmesinde çok uygulanan bir tekniktir`amorf düzendeki polimerik zincirler, soğuk çekme sonucu kristal bir düzenlenmeye girerek kuvvetli bir yapı kazanırlar.

Temel Çalışma Prensibi
Isı ve basınç ile termoplastikleri işlenebilir form haline dönüştürmede en temel yöntem ekstruzyondur.
Motorun verdiği hareket ile bir kovan içerisinde yer alan, sonsuz vida yapısındaki bir milin sürekli dönerek, arkadan aldığı (besleme noktası) (Feeder) polimerik malzemeyi, vida boyunca sarılı olan rezistanslar yardımıyla ısıtarak eriyik formuna getirerek, önden (kafadan) (Die) basınç ve tazyikle dışarı çıkarması mantığıyla çalışır. Beslemeden sürekli, kesintisiz olarak polimerik malzemenin takviye edilmesi ile, sürekli üretim yapılabilme imkanı sağlar.
Kafadan çıkan eriyik, işlenebilir formda hammadde niteliğindedir. Ve hangi üretim gerçekleştirilmek isteniyorsa, o üretim hattına ait üniteler yardımıyla ürün formuna adım adım ilerleme başlanır.
Kafadan çıkan polimerik eriyik doğrudan soğutma ünitesine alınarak, ipliksi bir ürüne/araürüne ya da bir kalıp içine enjekte edilerek doğrudan bir ürüne, ya da film halinde yayılarak başka bir ürüne/araürüne doğru şekillendirilir.
Ekstruzyon işleminde temel arguman ısıl işlemdir. Termoplastikler sıcaklık altında eritildiğinde akışkan forma girerler.
Ekstruderler de işte bu iş için çalışırlar. Kovan etrafına sarılı rezistanslar kovanı ısıtır ve içindeki polimerik malzemeyi akışkan hale getirir.
Ekstruderin ana ekipmanı vida, ekstruzyon işinin temel uygulayıcısıdır. Vida (sonsuz vida) hareketiyle sadece beslemeden aldığı polimerik malzemeyi kafaya doğru taşımakla kalmaz. Aynı zamanda malzeme karışımı yapar, sürekli ileri yönlü malzemeyi taşıyarak basıncı arttırır ve vida-malzeme-kovan sürtünmesi ile ısınmaya katkı sağlar. Vidaya ‹mil›, vidanın içinde döndüğü kovanın ‹ocak›, olarak tanımlandığı da olabilir. Birçok basit ekstruderde vidanın yapısı doğrusaldır. Yani vida dişli aralığı sabittir. Ancak daha gelişmiş modellerde durum bu şekilde değildir. Malzemenin kovan içerisinde biraz daha uzun süre durmasını sağlayarak, beraberinde vida boyunun kısaltılması gerekliliğini getirir ki bu da hacim ve maliyeti düşürür. Ayrıca kafa bölgesine doğru vida dişli sıklığı arttırılıp, beraberinde vida çapının büyütülmesi ile kafa basıncı yükseltilmiş olur. Bunlara ilave olabilecek vida çapını ara bölgede yükseltilmesi ile dekompresyon (geri emiş hazneleri) oluşturularak karışımın daha etkin olması ve oluşan gazların malzemeden uzaklaştırılması gibi kompleks uygulamalara yönelinir.
Ekstruder Sınıfları
Ekstruzyon işinde en temel ünite ekstruderdir. Ancak plastiği ürün niteliğine getirmede, işlemede ve şekil vermede yeterli değildir. Fakat plastik işleme ve şekil verme için en önemli ekipmandır. Çekme, soğutma sarma, kalıplama gibi üniteler ise ekstruzyon sürecinden sonra gelir. İyi bir ekstruder toz, granül ya da eriyik olarak beslenen malzemeyi ideal çalışma sıcaklıklarında eriterek, istenilen basınçta sıkıştırarak, erimiş malzemeyi tam homojenize hale getirerek, içerde hapsolan havayı/gazı dışarı atarak kafa tabir edilen kısımdan dışarıya istenilen basınç ile beslemelidir. Film, kalıplama ve diğer şekil verme işlemleri kafadan sonraki üniteler ile yapılır. Ekstruderler karakteristik olarak 20D, 25D, 30D gibi kodlarla tanımlanır. Bu, vida uzunluğunun vida çapına oranıdır.
Tek Vidalı Ekstruder:
Plastik sanayiinde en çok kullanılan ekstruder tipi tek vidalı olandır. Düşük fiyatı, sağlamlığı, güvenilirlik ve uygun performansı tercih nedenleridir. Kovan içinde bir tek vida vardır. Basınç yaratma etkisinin, sürükleme akışı (drag-flow) adı verile mekanizmanın üzerindeki etkisine bağlıdır. Tek vidalı ekstruderler, yarattıkları basıncın sürükleme akışı adı verilen mekanizmayı etkileme olayı ile açıklanırlar. Artan basıncın nedeni, malzeme ve burgu ile kovan arasındaki etkileşimdir ve çıkış miktarı malzeme ısısı, gövde ısısı ve kayma oranının kompleks fonksiyonudur. Polimerin eritilmesi olayı, malzemenin gövde çeperlerinden geçen ısıyı transfer etmeleri ve kesimden dolayı oluşan ısıtma kombinasyonu ile oluşur. Malzeme makineden geçerken üzerinde bol miktarda kayma ve karıştırma olmaktadır. Kayma miktarı, malzeme ısısı ve karıştırma yüksek oranda birbirinden bağımsızdırlar ve ayrı ayrı kontrol edilemezler. Sonuç olarak bazı durumlarda, özellikle yüksek çıkış miktarlarında sabit işlem yapmak zordur.
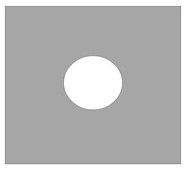

Çift Vidalı Ekstruder:
Ergimiş polimerde basınç oluşturmak için, dişleri birbirinin içine geçecek ya da geçmeyecek şekilde, aynı yönde ya da birbirinin tersi yönünde hareket vardır. Basınç arttırma ve kayma-karıştırma fonksiyonları, aslında birbirinden bağımsızdırlar fakat her birini ayrı ayrı uygun vida dizaynı ve makine kontrolü ile değiştirmek olasıdır. Burada malzemeyi ısıtan ısı, çoğunlukla kovan duvarından sağlanır, göreceli olarak az bir kısmı da kayma sonucu oluşur.. Malzeme gerçekte, vida ve kovan tarafından oluşturulan hareketli bir boşluk içinde az miktarda kayma ve vidalar arasında çimdikleme ile götürülmektedir. Çift vidalı ekstruderler, kaymaya yüksek hassasiyet gösteren polimerik malzemelerde kullanılır, çünkü kayma ve çıkış birbirinden bağımsız olarak kontrol edilebilirler. Çift vidalı ekstruderler; parele çift vidalı ve konik çift vidalı olabilir. Konik çift vidalı ekstruderler küçük devirlerde çok daha yüksek tork üretir. Bu şekilde enerji tasarrufu ve yapısından dolayı daha kaliteli üretim gerçekleşir. Çift vidalı ekstrüderlerin karmaşık PLC sistemleri ve elektronik kartlarla donatılması uygun değildir. Çift vidalı ekstrüderlerin özellikle çok tozlu ortamlarda kullanılmasından dolayı karmaşık PLC sistemleri ve ileri teknoloji elektronik kartlar çok sık arıza yapmaktadır. Renk ve katkı masterbatchlerinin baz polimerden organik/inorganik pigmentler ile üretimi, Beyaz ya da siyah masterbatch üretimi mineral ya da cam-elyaf dolgulu PA ve polyolefin compoundları, Hotmelt compoundları, Geri dönüşüm malzemelerin istenildiğinde katkı eklenerek granül haline getirilmesi proseslerinde tercih edilirler.
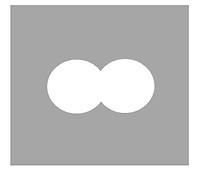

Üç Vidalı Ekstruder:
Zorlu uygulamalar için yüksek verimli üç vidalı ekstrüderler de tercih edilebilir. Bu ekstruderler aynı zamanda çok yönlü karışım reaktörleridir. Plastikleştirme etkisi, çıktı ve enerji tüketimi değerlendirmesinde üç vida ektruderler optimize edilmiş bir denge ve avantaj sunmaktadır.
Üç vidalı ektstruderlerde işlenen malzemeler vida devri başına üç kez kesilir. Vida tasarımları yan yana yada üst üste sıralı olabileceği gibi, yonca oluşturacak şekilde de tasarlanmış olabilir. Geleneksel çift vidalı ekstrüderde yalnızca bir tane kesme noktası mevcutken, yonca dizimli üç vida ekstruderde üç kesme noktası vardır. Üç yollu vidanın birleşik etkileri ve üçlü vida tasarımının kullanılması nedeniyle, sistemlerin L/D oranı, gerekenin yalnızca üçte birine düşmektedir. Bu nedenle, malzemenin kovan içinde tutulma süresi de üçte bire iner. Yani çift vidalı ektsrüzyon süreci ile aynı etkide bir oluşum için zaman ve enerjide de hatırı sayılır bizdüşüş oluşmaktadır. Özellikle polimer harmanlama compound üretimi, toz ve polimer katkı maddelerinin birleştirilmesi ve dağıtılması için üç vida ekstrüzyonlar oldukça uygundur.
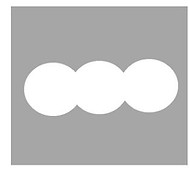
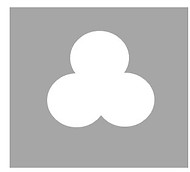

Gezegen Vidalı Ekstruder:
Hammaddeyi çoklu vida sistemi sayesinde homojen bir şekilde karıştırıp, çok daha iyi bir plastifikasyon sağlar. Diğer sistemlerin uzun mesafe ve zamanda yaptığı karışımı, gezegen (planet) sistem çok daha kısa mesafe ve zamanda yapıp, polimerik malzemeyi istenilen kıvama getirir. Temel olarak bir orta vida (güneş) ve bununla uyumlu olarak çalışan daha küçük çaplı uydu vidalardan (satalet) oluşur. Diğer ekstruder sistemleri ile karşılaştırıldığında, çok daha homojen ve çok dahi iyi plastifikasyon sonucu verir. Aynı işi daha kısa zamanda tamamlar, daha kısa vida,kovan boyutları nedeniyle montaj ve temizlik aşamasında, çabuk sökülüp takılır. Ayrıca sistemin kendine has dişli yapısı sayesinde kendi kendini temizleme özelliği bulunmaktadır. Kovanın içindeki dişli yapısı polimerik eriyiği, sürekli ileri ittiği için, kovan içinde herhangi bir ürün kalmaz. Bu sayede, renk değişikliği sırasında minimum fire ile kullanıcılara çok büyük avantaj ve kolaylık sağlar .
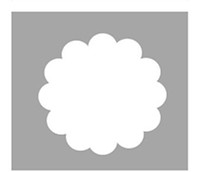

Ram Ekstruder:
Hidrolik bir pompa kuvveti ile polimer kalıp içerisinden geçirmeye zorlanması mantığı ile çalışır. Reçine beslemeden silindir içerisine düşer, ram materyalin kalıp içerisine girmesi için öne ve arkaya kayma hareketi yapar ve malzeme burada şekil verilerek soğutulur.
Ram ekstrüzyon yüksek moleküler ağırlıklı polimerlerden sürekli profil üretimine yönelik basınçlı sinterleme sürecidir. Direct ve Indireck
uygulama yöntemi vardır. Ayrıca süreç yatay ya da düşey olarak kurulabilir.

Ekstruder Vidası
Vida bir konveyördür. Döndükçe, kendini namludan geriye doğru döndürmeye çalışır, ancak bir yatak sırttan dışarı çıkmasını engeller. Temelde polimerik malzemeyi ısıtıp eriyik hale getirerek basınçla dışarı atılmasında kullanılan, kovan/ocak içinde yer alan ekipmandır. Ekstruderin tanımını ve karakteristik özelliğini vida belirler.
Bir vidada;
(1) Besleme Bölgesi
(2) Geçiş/Sıkıştırma Bölgesi
(3) Dozajlama/Basınç Bölgesi
olmak üzere üç ana bölge vardır.
Vidalar tipik olarak iki temel farklı tasarımda sınıflandırılır:
(1) Üç Bölgeli Vida (aynı zamanda “ölçüm vidası” olarak da adlandırılır)
(2) Karıştırma Vidası, İşlem yardımcıları renk ve katkı masterbatcleri (ve ayrıca pigmentler ve dolgu maddeleri) dikkate alındığında, karıştırmanın önemi aşikar hale gelir.
Vidaların çoğu temel aşınma direncini sağlamak için nitrürlenmiştir, fakat aynı zamanda daha fazla aşınma direnci veya kimyasal direnç sağlamak için çok çeşitli yüzey kaplamaları ile de kaplanmış olmaları söz konusudur.
Malzemenin ileriye taşınması (ve kalıbın önünde gerekli basıncın oluşturulması)
Isıtma ve eritme, eriyiklerin karıştırılması ve homojenleştirilmesi tipik vida görevleridir.
Helis Açısı:
Dönerek ilerleyen bir silindirin üzerindeki noktanın meydana getirdiği yay izine ‹helis› denir.
Helisler, sağ ve sol olmak üzere iki yönlü olurlar. Yönün belirlenmesi için dişlnin/vidanın yatırılıp karşıdan bakmak yeterlidir. Vida kesitinde eğim yönü sağ tarafa ise ‹sağ helis›, sol tarafa ise ‹sol helis› olarak tanımlanır. Ekstruzyon mekanik tekniğinde helisel oluklar (vida) hareket ve kuvvet itimi, polimerik malzemenin basınçla öne (kafaya) doğru taşınması amacıyla kullanılmaktadır.
Helisel mekanizmalar geometrik sapmalara daha az duyarlıdır ve özellikle yüksek hızların söz konusu olduğu uygulamalarda kullanılır. Vida merkez dik ekseninden sapma açısı, helis açısına denktir.

Besleme Bölgesi:
Vida besleme bölümü: malzemeyi besleme boğazından almak için derin kanal boşluklarına sahiptir ve katıların taşınması ana görevini yapar. Bu bölge, ekstrüderin toplam çıkış hızının doğrudan bu bölgedeki katı taşıma hızına bağlı olması nedeniyle özellikle önemlidir. Taşınan katıları elde etmek için, malzeme “namluya yapışmalı ve vida üzerinde kaymalıdır”. Bunu başarmak için uygun sıcaklık kontrolü çok önemlidir. Örneğin, besleme bölgesi yanlış sıcaklıklara ayarlanmışsa, malzemenin ilerleme yönünde herhangi bir eğilim olmaksızın besleme boğazının altındaki vida etrafında hareket etmesi mümkündür. Besleme bölümü, bir çok problemin meydana gelebileceği ve vasıflı bir operatörün vidayı, vida kökünün, besleme bölümünün / kovan/ocak doğru sıcaklık kontrolü aracılığıyla itebileceği bölgedir. Vida kanal derinliğini en fazla olduğu, besleme noktasına motora en yakın olan bölgedir. Vidanın polimerik malzemeyi kovan içine aldığı ilk kısımdır. Vida boyunun %25-30 unu oluşturur. Bu bölgede diş dibi derinliği sabittir. Bu dişler sayesinde plastik malzeme belirli bir basınç artışı sağlanarak besleme hunisinden alınarak ileriye, sıcak bölgelere doğru itilir. Malzeme ile vida arasındaki sürtünme de bu bölgede en düşük seviyededir.
Geçiş / Sıkıştırma Bölgesi:
Sıkıştırma bölümünün boşlukları kademeli olarak derinden sığ düzeye değişir. Burada malzeme 5D ila 10D arasında sıkıştırılır ve eritilir. Polimerik malzeme(ler)nin artık erimeye başladığı bölgedir. Vida kanal derinliği daha düşük, eriyik-kovan sürtünmesi daha yüksektir. Malzeme(ler) birbiri ile bileşmeye ve gaz çıkışı olmaya başlar. Vida dişli aralığının büyümesi ya da vida kanal derinliğinin ani yükseltilmesi ile geri emiş hazneleri oluşturulur. Vida üzerindeki bu noktaya denk gelecek şekilde kovan üzerinde kanalların açılması (vent açıklığı) ile çıkan gaz malzemeden uzaklaştırılır. Bu noktalarda kendiliğinden hava basıncı ile bu olay gerçekleşirken, vakumla da gaz tahliyesine destek olunabilir. Özellikle, polimerlere katkı ilavesi yapılıyorsa ventsiz ekstruderlerde işlemek uçucuların polimer içerisinden ayrılmayacağı ve kabarcık şeklinde son ürün içerisine geçeceği için uygun değildir. Mutlaka ventli ekstruder seçilmelidir.
Dozajlama / Basınç Bölgesi:
Ölçüm bölümü son bölümdür ve en sığ uçuş derinliklerine sahiptir. Kalıptan önce gerekli basıncı oluşturmak için bu sığlık gereklidir. Polimerik malzeme(ler)nin artık eriyip, karıştıktan sonra geldiği en son ve kovan içinden artık tahliye olacağı bölgedir. Bu bölgede vida çapının en büyük, başka ifade ile vida kanal derinliğinin en düşüktür. Vidanın besleme noktasındaki (en baştaki) dişli aralığı hacmi ile, kafa noktasındaki (en sondaki) dişli aralığı hacimleri oranı; Vida sıkıştırma oranı olarak tanımlanır. Bu oranın 1/1,5 ile 1/4 arası oranlarda görülmesi sıklıkladır. Kovan içerisinde en düşük basıncın olduğu besleme bölgesinden uzaklaştıkça basınç artmaya başlar, ve bu nihai bölgede basıncın en yüksek olduğu değere ulaşılır. Bu basınç kovan içindeki eriyik polimerik malzemenin kafadan bir sonraki üniteye (kalıp vs.) itmeye/tazyik sağlar. İhtiyaç duyulan bu yüksek basınç; kafada buluna tahliye delikleri (meme) çaplarının/aralıklarının küçültülmesi, memelerden kimilerinin tıkanması ile sayısının azaltılması, bu bölgedeki ısıların geçiş / sıkıştırma bölgesine nazaran ısılarının düşürülmesi,uygulama alanı varsa süzgeç/elek gözeneklerinin küçültülmesi, gibi dışarıdan (vida yapısı haricinde) müdahalelerle arttırılabilir. Meme olarak tanımlanan bu tahliye noktaları ‹dudak› alarak da bilinir. Kimi vidaların dozajlama/basınç bölümlerinde basıncı arttırmak için nihai noktasında ‹tokmak› uygulaması vardır. Tokmak uçlu bu vidalarda; tokmak boyunca polimerik malzemenin kovana yaptığı sürtünme en üst seviyeye çıkar ki bu da; karışımı iyileştirir. Plastiğin erimesi için gerekli ısının bir kısmı vidanın dönmesiyle sağlanır. Dönüş hızı arttıkça sıcaklık artar. Makine vidayı yükseksek hızla döndürebilse bile, vida dönme hızını baskı süresine uygun olarak ayarlamak daha uygundur. Hatta vida dönme hızı olabilecek en küçük değere düşürülmelidir.
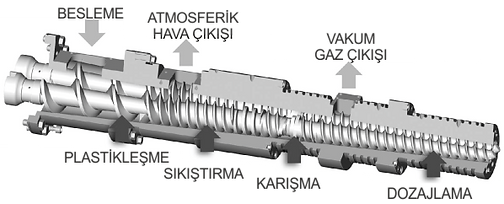
Vida Sıkıştırma (C / R) Oranı
Besleme kanalı derinliği ve ölçüm kanalı derinliği arasındaki orandır.
Üç bölgeli bir vidanın sıkıştırma oranı, farklı viskoelastik özelliklere sahip farklı polimerik malzemeler işlenirken en temel parametre olarak düşünülebilir.
Bu oran tipik olarak 1.5: 1 ile 4.5: 1 arasındadır.
Bazı polimerler, 2.5: 1 sıkıştırma oranına sahip vidalarda daha iyi çalışır, diğer malzemeler ise 4: 1 sıkıştırma oranına sahip vidalarda daha iyi işlem görür. Genellikle daha geniş bir malzeme yelpazesi için uygun olan genel amaçlı 2,5-3: 1 oranındaki vidalar kullanılır.
Bu sıkıştırma oranı, kanalların derinliklerine karşılık gelir. Bu sıkıştırma oranının, vidanın malzemeye ne kadar makaslama yapacağını göstermediğini ve aynı sıkıştırma oranına sahip iki vidanın önemli ölçüde farklı çıktı hızlarına sahip olabileceğini belirtmek önemlidir. Ve bu derinlikler ve sıkıştırma oranının bariyer vidası için bir anlamı yoktur.
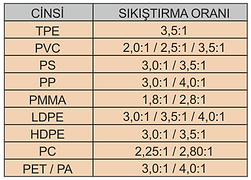
C/R, geçmişte eriyik sıcaklığının ayarlanması için bir temel olarak sıklıkla kullanılmıştır ve daha yüksek işlem sıcaklıklarına sahip polimerler, daha yüksek sıkıştırma oranlarıyla çalıştırılmıştır. Vidalar, genellikle ekstrüderin kapasitesi dahilinde olan beklenen en yüksek çıktıya ve beklenen kafa basıncına dayalı olarak belirli bir hız için tasarlanmıştır. Vidalar tipik olarak geniş bir çalışma hızı aralığına sahip olsalar da, sonsuz bir aralık değildir ve tasarım hızlarından çok daha yüksek veya daha düşük hızlarda kötü çalışabilirler.
Tasarımcılar sık sık C/R'nin 2:1, 3:1 olması gerekip gerekmediğini değerlendirirler.
Polimer, dönen vidadan kesme enerjisini emer ve çıktı ne kadar düşükse, her bir çıktı birimine o kadar fazla enerji veya erime sıcaklığı artar ve bunun tersi olur.
0,500 inç besleme derinliğine ve 0,200 inç ölçüm derinliğine sahip vida, 2,5 C / R değerine sahiptir.
0.375 inç besleme derinliğine ve 0.150 inç ölçüm derinliğine sahip vida da 2,5 C/R değerine sahiptir.
Bu iki tasarımın aynı performansı göstermesini beklemek ne kadar doğru olur. Sonuç olarak, basitçe C/R 'yi belirtmek, vidanın performansı hakkında pek bir şey ifade etmez.
Erime ve taşıma işlevlerini tamamen ayıran bariyer vidalarının popülaritesi ile C/R daha da az anlam ifade ediyor olması bundandır. Bariyer bölümlerinin çoğu 10:1 besleme derinliği / boşaltma derinliğine oranına sahiptir, ancak aynı çıkışta 3:1 oranına sahip geleneksel kanatlı bir vidaya göre daha düşük erime sıcaklığı sağlarlar.
Her polimer, her ekstrüder ve her işlem, performansı optimize etmek için farklı bir tasarım gerektirir. İlk dikkate alınması gereken, beygir gücü, vida hızı, delik boyutu, L / D gibi değerlerdir. Ardından, istenen eriyik sıcaklığı, çıktı, buharlaşma ihtiyacı, homojenlik gibi proses gereksinimleri devreye girer. Son olarak, polimerin termal, reolojik ve katı partikül özellikleri dikkate alınmalıdır.
Vida Boy, Çap (L / D) Oranı
Vidanın boyunun, çapına oranıdır.. Vida boyları daha çok üretici firmalar
tarafından, her biri kendi yöntemleriyle hesaplamaktadır. Kimi üreticileri genellikle kamadan başlayarak, kimi üreticiler kama bitiminden, kimileri besleme boğazının ortasını referans almaktadır.
Ekstrüzyon çıkışında esnekliğin ön planda olduğu profil ekstrüder vidaları için L/D'ler tipik olarak 24: 1 ile 30: 1 arasındayken, yüksek çıkış vidalarnda (örneğin boru ve sac için bariyer vidaları) 35/38: 1 olabilir.
Extruzyon makinelerinde genelde 30:1 ve üzeri,
Enjeksiyon makinelerinde genelde 20:1 veya üzeri oranda olmalıdır.
Ancak plastik enjeksiyon makinelerinde vida çapı daha büyük seçildiğinde L/D oranı 16:1 oranına kadar düşer. Bu da vida içindeki eriyik enjeksiyon gramajını doğru orantılı olarak düşürür. Bu düşüşü dengelemek için besleme bölümüne ek hatveler yapılır ve eriyik miktarı az da olsa çoğaltılır.
Büyük L/D oranının avantajları :
Artan Enjeksiyon oranı sayesinde daha kısa çevrim zamanı, daha az erime sıcaklığı ihtiyacı sayesinde daha az kalıp kapama süresi ihtiyacı, daha az basınç ve istenmeyen ısı değişiklikleri, daha iyi renk karışımı ve enerji tasarrufudur. Sonuç olarak seçilecek makinenin L/D oranını 20:1 den daha aşağıda olmaması ve yüksek karıştırma bölümleri olan bariyer vida kullanılmasıdır.

Ekstrüderler tipik klasik değerle 20:1 L/D oranına sahiptir. 24:1 L/D olanlar "uzun" olarak kabul edilir. Ancak 1960'ların bu değerleri zamanla gelişti, ekstrüderler uzadı ve 30:1 - 38:1 L/D ölçüleri endüstri "standardı" haline geldi. Hatta bazı ekstrüderlerde, çift havalandırma, birleştirme veya yüksek hızlı işleme gibi özel amaçlar için 40:1 L/D oranları endüstriye girdi.
Daha uzun boy ve daha yüksel L/D oranına sahip ekstrüzyon hatları ilk bakışta cazip görülebilir ancak bu cazip ölçüler genel performansı olumsuz da etkiliyor olabilir. Bir ekstrüder boyutunun ve sürücü kombinasyonunun seçildiği gibi, L/D oranını da dikkatlice değerlendirilmek gerekir. Herkes ekstrüderinden en yüksek çıktıyı ister, ancak çıkan malzeme çok sıcak veya bozulmuşsa, o zaman o ekstrüderde hıza odaklanmanın aslında ikinci plana itilmesi gerektiğini gösterir. Yayılma, güç katsayıları, erime noktaları, kafa basıncı, viskozite ve kristallik gibi veriler değerlendirme sürecinin birer argümanlarıdır.
Bazı polimerler diğerlerinden çok daha kolay ve daha hızlı erir. Ayrıca, bazı işlemler tipik olarak düşük kafa basınçlarına sahipken diğerleri çok daha yüksek tahliye basınçlarına sahiptir. İçsel viskozite, polimerler arasında çok farklılık gösterir ve bazılarında kayma açısından önemli diğer taşımazlar. Sonuç olarak, vida performansı herhangi bir standart L/D yerine çeşitli L/D'lerde optimize edilebilir.
Genel işleme durumu için çok uzun olan bir vida aslında çıktıyı sınırlayabilir, verimi düşürür. Sınırlamaya etken faktörler genellikle, polimerin bozulması, renk kayması, katkı etkinliğinin kaybı ve yüksek eriyik sıcaklığı olarak sıralanabilir. En temel belirleyici kriter polimerin Tg, Tm değerleridir. Kolayca eriyen bir polimer için erime uzunluğu ideal olarak daha kısa olmalıdır çünkü aşırı uzun geçişler erime oranını gerçekten azaltabilir. Aynı şey basınç gelişimi için de geçerlidir. Yaygın olarak kullanılan eriyik pompaları, tahliye basıncını yüksek ve sürekli kılmak için vardır ve uzun ölçüm bölümlerine olan vidalara ihtiyacı büyük ölçüde azaltırlar.
L/D ne olursa olsun vidaların besleme bölümleri çok yaklaşık birbirine eşit uzunluktadır. Vidanın geri kalanı eritme ve pompalamaya ayrılmıştır. Vida kanalları ne kadar derinse veya spesifik çıktı ne kadar yüksekse, erimeyi tamamlamak ve polimeri kalıptan dışarı itmek için gerekli basıncı geliştirmek için o kadar uzun süreye ihtiyacınız olur. Bununla birlikte, L/D arttıkça, çıktıyı artırmada sınırlamalar, limitler gündeme gelir. Genellikle bu sınırlar, besleme bölümünün daha fazla polimer verememesinden kaynaklanır. Daha küçük çaplı vidalarda bu sınır genellikle vida mukavemeti ile belirlenir. Küçük vidalarda, vida kanallarında makul derine inebilirsiniz, ama büyük ekstrüderlerde, çıktıda daha fazla artış olmayana kadar kanallar derinleştikçe besleme verimliliği azalır.
Üç Bölgeli Vida
Bu vida, tipik olarak 20D ve 28D uzunluğunda, besleme bölümü, sıkıştırma (veya geçiş) bölümü ve ölçüm bölümü olmak üzere üç farklı bölüme sahiptir.
(1) Besleme Bölgesi:
Besleme bölgesinde granül, kırık veya toz haldeki katı malzeme taşınır ve sıkıştırma bölgesine itilir. Bu bölgede vida akış derinliği, malzeme düşük yoğunlukta olsa bile yeterli miktarda akış sağlanabilmesi için oldukça geniş tutulmuştur.
(2) Sıkıştırma Bölgesi:
Sıkıştırma bölgesinde, besleme bölgesinden alınan malzeme sıkıştırılır. Plastik hammadde ısıtıcılar sayesinde eritilir, vidanın dönme hareketiyle homojen hale getirilir.
(3) Ölçme Bölgesi:
Homojen hale gelmiş olan malzemenin sıcaklığı enjeksiyon yapılacak sıcaklığa yükseltilir (işleme sıcaklığı) ve malzeme kalıplanmaya hazır hale gelir.
Havalandırmalı bir ekstrüderde, vakumlu gaz gidericinin de dahili ile vida/kovan boyu daha uzun olur. Bu uzunluk yukarıda adı geçen üç bölüme ek, gaz giderme ve dekompresyan olmak üzere iki bölüm daha oluşmasına olanak tanır.
Üç bölgeli vidalarla, düşük ve orta çıkış aralığı için ve ayrıca kaymaya duyarlı PVC gibi malzemeler yaygın olarak kullanılır.
Bazı polimerler için vidanın üç bölgeden oluşma şartı olmayıp bölgelerin ikisi veya üçü birleştirilebilir. Burada önemli olan vida tasarımının en çok işlenecek malzemenin cinsine bağlı olduğunu bilmektir.
Buna göre de vida tipleri
(1) Genel termoplastik vidaları
(2) Elastomer vidaları,
(3) Ön plastikasyon vidaları,
(4) Özel tip vidalar olarak da sınıflandırılabilmektedir.
Bu vida tipleri arasındaki farklar, besleme ve ölçme bölgelerindeki akış derinliğinden, sıkıştırma oranından, vida strokundan, vidanın kendi uzunluğundan ve bölge uzunluklarından ileri gelmektedir. Sıkıştırma oranı: vidanın besleme bölgesi hacminin, ölçme bölgesi hacmine olan oranına denir. Sıklıkla 1/2 – 1/4 oranları kullanılır.
Bariyer Vidası
Üç bölgeli bir vida eritme işlemini tamamlayamıyorsa ve daha yüksek çıkış oranları gerekiyorsa, bir “bariyer vidası” kullanılabilir. Bu vida, kanalda alttan kesilmiş ve sadece tamamen erimiş plastiğin geçişine izin veren bir ikincil sığlığa (bariyere) sahiptir. Çok farklı tasarımlıları mevcuttur, ancak hepsi düşük erime sıcaklığında daha yüksek çıktı oranları sağlamayı amaçlamaktadır.

Vida Temizliği
Solventler, tel fırçalar, aşındırıcı aletler ve pürmüzler kullanılarak manuel temizlik işlemi, tercih edilen en yaygın temizleme operasyonudur. Bazen kumlama işlemiyle de bu temizlik işi yapılmaktadır. Ancak bu türde yapılan tüm temizlik operasyonları vida yüzeyinde farkında olunmayacak kadar da olsa izler bırakır. Oluşan bu izler, temizlik operasyonu sayısı arttıkça, zamanla daha da belirginleşir ve nihayetinde vidada hasarlar ortaya çıkartır. Uygun olmayan bu temizlik yöntemleri vidanın daha çabuk kirlenmesine, daha çabuk kir tutmasına neden olacaktır.
Ekstrüzyon sürecinde bu vida yüzeyi üzerindeki izlerde biriken polimerik eriyikler yanacak ve kalıp öncesi filtrelerde birikerek tıkanmaların (filtre dolmalarının) çabuklaşmasına zemin açacaktır. Hassas ölçümler yapıldığı takdirde, makine verimliliğindeki düşüşler de görülebilecektir.
Termoplastiklerin ve termoset plastiklerin ekstrüzyonunda vida üzerinde bozulmuş malzeme birikintileri kalite kaybında da etkindir. Polimerik, kauçuk kalıntıları, yapıştırıcılar, renk ve katkı masterbatchleri bu izlere tutunarak, temiz, pürüzsüz ekstüzyon çıkışı ve renk geçişlerinde geçiş sürecinin kısa olmasında vida temizliğinin etkisi büyüktür.
Özellikle vida uçlarının dikkatli ve hassas bir şekilde temizlenmesi, kaliteli ürün ve uzun hizmet ömrü için dikkat edilmesi gereken husustur.
Vida temizliğinde uygulanabilecek en etkin yöntem piroliz sürecidir.
Piroliz Süreci :
Herhangi bir organik ürüne kolayca uygulanabilen bir termokimyasal işlemdir. Yunanca ısı ve ateş anlamlarına gelen “pyro” ve parçalanmak anlamına gelen “lyse” kelimelerinden oluşur. Organik maddelerin yüksek sıcaklıkta ve oksijensiz ortamda termal kırılmaya uğratılması sürecine piroliz denir. Bu süreç, yaklaşık 430 °C sıcaklıkta, polimerlerden karbonizasyon gazı ve karbon ayrıştırılmasına ve vida (süzgeç, kalıp gibi hangi makine parçasıysa) metalik yüzeyden uzaklaştırılması işidir. Hassasiyet, temizleme kalitesi, temizlik süresi, güvenilirlik, enerji verimliliği, çevresel uyumluluk barındıran piroliz sürecini termal temizleme (oksidasyon) aşaması takip eder.
Piroliz süreci neredeyse akla gelebilecek tüm ekipmalar; ekstrüzyon vidaları, filtreler, kalıp, yolluk bileşenleri, granül nozulları, kalıp plakaları, statik karıştırıcılar vs. için uygulanabilir.
Ana reaktörün içindeki organik ürünler, oksijensiz ortamda 300 °C ile 1000 °C sıcaklıkta termal bozunmaya uğratılır. Termal bozunma sonucunda gaz fazına dönüşen organik ürünler, katalitik konverter ünitesine gelir. Bu aşamada katalizör görevi üstlenen ünite ile işlem hızlandırılır. Yardımcı reaktör bölgesinde uygun sıcaklıkta yoğuşabilen gazlar pirolitik sıvıya, LPG’ye, karbon siyahı ve parafine dönüştürülür.
Piroliz olayında termik olarak madde parçalanması şu aşamalada gerçekleşir:
-
100 °C -120 °C Mutlak kuruma süreci yaşanır.
-
120 °C -250 °C Dezoksidasyon, desülfürleşme (metalden ve üzerindeki polimerik kirden oksijen, sülfür ayrışması) olur.
-
380 °C Karbonlaşma ve zenginleşme aşaması yaşanır.
-
400 °C Karbon-Oksijen ve Karbon-Azot bileşiklerin bağları parçalanmaya başlar.
-
400 °C - 420 °C Bütün maddelerin Piroliz yağına ve katrana dönüşmesi başlar
-
600 °C Bütün maddelerin ısıya dayanımlı maddelere kranklaşması gerçekleşir.
-
600 °C Üzerinde artık kranking süreci yaşanır aromatlar ve etilenler oluşur.
Vida temizliğinin de yapılabildiği Piroliz süreci sonrasında yan ürün niteliğinde, pirolitik yağ, karbon siyahı, parafin, işlemi esnasında yoğunlaştırılamayan gazlar elde edilir. Çıkan gazlar, kalori açısından doğal gazdan daha değerlidir. Birçok farklı sektörde enerji ihtiyacını karşılamak için yakıt olarak kullanılabilir.
Co-Ekstruzyon (CoEx) Tekniği
Tek parçada ancak çok katlı film üretmek için, aynı kalıp içerisinden iki veya daha fazla eriyiğin laminasyonu işlemidir.
Co-ekstruzyon için en az iki ekstrüder gereklidir. Ancak; ekstrüder sayısı, ekstrüzyona tabi tutulan tabaka sayısında olmayabilir.
Yani iki ekstrüder ile iki katlı film yapılabileceği gibi, üç veya dört katlı filmler, hatta kalıbın modeline göre çok daha fazla kat sayılı filmler de yapılabilir.
Bunun nedeni, mevcut besleme bloğu teknolojisinin, bir ekstrüderden gelen eriyiğin, kalıp içerisinde, nihai koekstrüdatta iki veya daha fazla katmana ayrılmasına izin vermesidir.
Her bir kat, orijinal özelliğini korur, ancak bir bileşik malzeme parçasına birleştirilir. Ekstrüzyondan önce bir ekstruder beslemesinde tek tek materyallerin özellikleri değiştirilebilir, ancak sonuç, homojen bir üründür.
Bütün plastikler co-ekstrüzyon için uygun değildir, çünkü bazı polimerler başkalarına yapışmazlar.
Bunun için polimerlerin uyumluluğu hususunda bilgili olmak gerekir. Bununla birlikte, iletken bir orta tabakanın uygulanması bu sorunu sıklıkla çözebilir.
Farklı erime sıcaklıklarına sahip olan plastikler, bu işlem için uygun değildir, çünkü alt erime materyalinde bozulma meydana gelir.
Son olarak, PVC ve asetaller , bir araya geldiklerinde oluşabilecek potansiyel olarak şiddetli reaksiyonlar nedeniyle asla birlikte ekstrüzyon yapılmamalıdır.
Hammadde maliyetini düşürmek için, co-ekstruzyon bire birdir.
Özellikle dolgu maddelerinin orta katmanlarda tutularak hem maliyet düşürülmüş, hem de yüzey pürüzsüzlüğünden ödün verilmemiş olur. Ayrıca renk ve katkı masterbatchleri uygulamasında daha uzun ömürlü, daha canlı sonuçlar söz konusudur.
Avantajları içinde, daha büyük hat hızı ve genişlik çeşitlerinde yüksek kaliteli mono tabaka ekstrüzyon kaplamaları, orjinal hammadde tasarrufu, genel ekstrüzyon işleminde gerekli adım sayısında azalma, belirli katmanlarda belirli polimerlerin kullanımıyla performans arttırma gösterilebilir.
Bunlara ek olarak bazı dezavanjları da vardır.
Bu işlem için, tüm polimerler laminer akışını sürdürmek için benzer erime viskozitelerine sahip olmalıdır.
Viskozite farklılıkları, tabakanın zayıflamasına etken olur. Ancak kompozit yapının içindeki malzeme konumuna göre az ya da çok tolere edilebilir.
Daha gelişmiş ekstrüder yapısı ve operatör bilgisi gerektirir. Bu, ekipmanın ekstra bakım maliyeti anlamına gelir.
Sistem tasarımında da önemli bir planlamaya ihtiyaç duyulur.


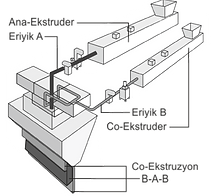
Ekstruzyon Ekipmanları
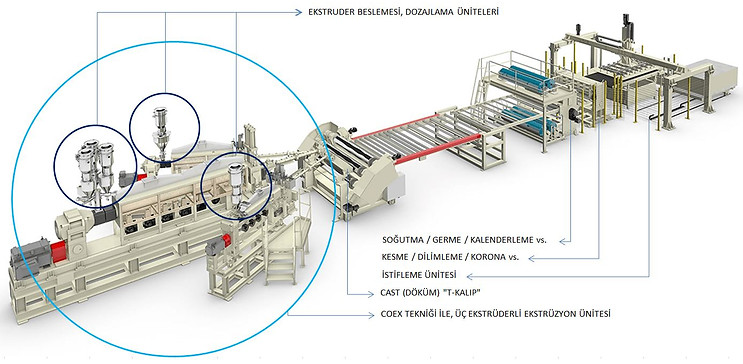
Agromel Makinesi:
Plastik malzemeye, ekstruzyondan önce parçalama, kurutma ve yoğunluk kazandırma işlemini gerçekleştiren makinadır. Kazan içinde bulunan döner ve sabit bıçaklar yüksek devirde ve zemine yakın mesafede dönerek oluşan friksiyon yardımıyla plastiği ısıtarak parçalara ayırır ve nemini alır ardından su ile şoklanarak yoğunluğu artar ve bu sayede ekstruder makinasının beslemesinden daha çok verim alınır.

Besleme:
Ekstruzyon işlemi için ana makinenin polimerik malzemeyi aldığı haznedir. Hazne altında bulunan vida hareketi ve yer çekimi kuvveti ile doğrudan polimerik malzemenin vida-kovan içine akıtılabileceği gibi bir dozaylama ünitesi ile birlikte de kullanılabilir. Dozajlama ünitesi, kompleks polimerik malzemenin (premix), daha önceden bir mikser veya bir tekne içerisinde elle hazırlanması işini ortadan kaldırarak iş akışında kolaylık ve kontrol sağlar.
Ekstruder Makinesi:
Plastik ürün oluşumu sürecinin temel ünitesi ekstruder makinesidir. Bu ünitede hammadde bir kovan/ocak içerisinde önce ısıya maruz bırakılarak eriyik forma dönüştürülür ve içindeki vida/mil hareketi ile ileri yönlü akışı sağlanarak işlenebilir yapıya dönüştürülür.
Bir ekstrüderin ana fonksiyonları, plastik granül taneciklerini eritmek ve elde edilen erimiş polimeri homojen bir eriyik elde etmek için karıştırmaktır. Bu, malzemenin bir döner vida ile ısıtılmış bir namlu boyunca taşınmasıyla yapılır. Ticari olarak kullanılan ekstrüder kovanlarının çapı genellikle 3½ ”(90 mm) ila 6” (150 mm) arasındadır. Vidalar, ekstrüde edilmiş malzemelerin ve işlem parametrelerinin spesifik özelliklerine göre uyarlanır. Vidanın uzunluğu çaplarından büyük ölçüde etkilenir. Vida uzunluk / çap (L / D) oranları genellikle 26: 1 ila 30: 1 aralığındadır.
Ekstrüderden çıkan akışın, vidanın dönme hızındaki ±% 1'i aşmayan varyasyonlarla iyi kontrol edilmesini ve sabit olmasını sağlamak önemlidir. Vida hızının doğru bir şekilde kontrol edilmemesi, genellikle makine yönünde film kalınlığında periyodik değişikliklere neden olabilecek istenmeyen titreşimli akış ile sonuçlanır. Ölçüm bölümü veya ekstrüderin son bölümü, ekstrüderden malzemenin hassas bir şekilde dozlanmasını garanti etmek için tasarlanmıştır. Yukarıdakilere ulaşmak için, vida ile namlu arasındaki boşluk çok küçüktür. Bu, başka bir zorluk yaratır, çünkü döner vida ile namlu arasında sabit bir boşluk sağlamak zordur.
Yukarıda belirtilen potansiyel problemlerin üstesinden gelmek için, ekstrüderin akış aşağısında yaygın olarak bir eriyik pompası kullanılır. Pompa, ekstrüderin tahliye basıncına bakılmaksızın tutarlı bir akış üreten pozitif bir yer değiştirme cihazıdır. Pompa, basınç üretme işini üstlenerek ekstrüder üzerindeki iş yükünü hafifletir. İndirgenmiş ekstrüder kafa basıncı, enerji tüketimi tasarrufuna, eriyik sıcaklığında bir düşüşe ve namlu ile vida arasında daha az yıpranmaya dönüşür. (Ekstrüzyon ekipmanları konusunda detay açıklama mevcuttur).
Statik Mikser:
Polimer eriyiğin kalıplara dökülmeden önce homojen ve etkili biçimde tam olarak karıştırılması ve sıcaklığının sabit tutulması işlemlerinde kullanılır. Statik mikserler enjeksiyon kalıplama işleminin güvenilirliğini artırır, kullanılan masterbatch miktarını azaltır ve enjeksiyon kalıplama sürecini genel anlamda en iyi duruma getirir. Renk çizgileri problemleri için etkin bir çözüm sağlarlar.
Düz (T) Kalıp Sistemi:
Kalıp sisteminin herhangi bir ekstrüzyon hattının kalbi olduğu söylenebilir. Kalıp sistemi, farklı erimiş polimerleri ekstrüderlerden besleme bloğu giriş portlarına taşıyan koekstrüzyon besleme bloğu, düz kalıp ve eriyik transfer adaptörleri tarafından oluşturulur. Birlikte çekilen filmin kalitesi ve işlemin verimliliği büyük ölçüde kalıp sisteminin tasarım ve performans özelliklerine bağlıdır.
Kalıp sisteminin birincil işlevi, endüstride kabul edilen toleranslar dahilinde film üzerindeki kalınlık değişimleri ve her bir katmanda kalınlık değişimleri ile kalıbın genişliği boyunca düzgün bir şekilde dağıtılan çok katmanlı bir film oluşturmaktır ( toplam kalınlık ve her katman için ±% 15 ila ±% 20). Besleme bloğundan yukarı doğru eriyik transfer adaptörleri bulunur. Bu kılcal sistemin tasarım kriterleri, malzeme kalma süresi, basınç düşüşü ve sıcaklık kontrolü gibi parametreleri dikkate almalıdır. Örneğin, boru çapı arttırılarak aşırı bir basınç düşüşü ele alınabilir; bununla birlikte, bu da malzemenin kalış süresini arttıracak ve malzemenin bozulma olasılığını artıracaktır. Ayrıca, boruların taşıdıkları eriyikleri ısıtmasını veya soğutmasını önlemek için doğru duvar kalınlığı boyutlandırması ve uygun ısıtıcı özellikleri gereklidir. Tüm bu değişkenler arasında uygun dengeyi bulmak tasarımcıya aittir.
Koekstrüzyon besleme bloğu:
Farklı eriyik akışlarını önceden belirlenmiş bir katman sekansında düzenler ve katmanların son birlikte-kıvrımda olduğu kadar çok eriyik akımı üretir. Bu yapıldıktan sonra, her akış bir düzlemsel geometri benimser, komşu katmanlarını karşılar ve son düzlemsel eş-ekstrüdat (koekstrüzyon) oluşur.
Koekstrüzyon besleme blokları iki kategoriye ayrılır:
Sabit ve değişken geometri blokları. Bu blokların akış yukarı bölümünde seçici fiş veya seçici makara bulunur. Bu silindirik şekilli çıkarılabilir parça, her bir eriyik akımını birlikte ekstrüdat içindeki son konumuna yönlendirmekten sorumludur. Tapa, gerekirse, bu akımları yapıda birden fazla katman besleyen bir malzeme ile böler. Farklı bir katman sırası gerekiyorsa, sadece tapa değiştirilerek elde edilebilir.
-
Sabit geometri blokları :
Üretim hattı reolojik davranışlarında benzer olan sadece birkaç farklı ürüne ayrıldığında en etkilidir. Bununla birlikte, bu blokların, daha geniş bir malzeme yelpazesini işlemek için gerektiğinde işlenebilen veya değiştirilebilen çıkarılabilir akış eklerine sahip olduğuna dikkat etmek önemlidir.
-
Değişken geometrili bloklar:
yüksek katma değerli malzemelerin birlikte ekstrüzyonu için veya üretim hattının kapsamı daha çeşitlendirildiğinde idealdir. Genel olarak, bu bloklar, komşu katmanlar ve / veya hızı ile buluşmadan önce tek bir katmanın genişlik dağılımını ayarlayabilen, dolayısıyla kesme oranını ve viskozitesini etkileyen hareketli dahili bileşenlere sahiptir. Böylece, tabaka bozulması ve arayüzey kararsızlığı gibi koekstrüzyona özgü problemler, besleme bloğunun ayarlanması ile aşılabilir.
Koekstrüzyon besleme bloğu teknolojisinin koekstrüzyon akışlarının doğasında bulunan akış anormalliklerini ele almadaki tüm kabiliyetlerine rağmen, optimal bir birlikte ekstrüdatın üretilmesi ancak besleme bloğunun bir koekstrüzyon akışını işlemek üzere tasarlanmış ve uygun şekilde tasarlanmış bir kalıpla birlikte çalışması durumunda mümkündür. Kalıp ve besleme bloğu arasındaki mükemmel sinerji, yüksek kaliteli bir ürünü garanti edecek şeydir.
İyi tasarlanmış bir kalıp, besleme bloğundan gelen eş-ekstrüdün yayılması sürecinde, her bir tabakanın düzlüğünün ±% 15 ila ±% 20 tolerans dahilinde tutulduğunu garanti etmelidir. Ayrıca, bozulma sorunlarını önlemek veya bazı durumlarda katmanlar arasında istenmeyen ısı transferini önlemek için kalma süresinin aşırı olmayacağı şekilde tasarlanmalıdır. Kalıp ayrıca, basınç düşüşünün ekstrüzyon işlemi içinde normal bir seviyede tutulacak şekilde tasarlanmalıdır.
Kalıbın, termal kararlılığı garanti etmek ve kalıp olduğunda kalıp dudaklarının aşırı deformasyonu olarak kendini gösteren midye bombardımanı problemini en aza indirmek için uygun boyutta, yeterli çelik kütlesine ve uygun mekanik tasarıma sahip olması da önemlidir. ince filmlerin ekstrüzyonuna özgü yüksek basınçlara maruz bırakılır. Kalıp teknolojisindeki son gelişmeler, döküm film üretim hatlarının verimliliğini artırdı. İç güverteler olarak adlandırılan özel referanslar yapılabilir. Kalıbın her iki ucuna yerleştirilen deckler, film genişliğinde değişikliklere ve bunun sonucunda trimin azalmasına izin verir. Sabit veya ayarlanabilir ve uzunlukları 20 inç'i aşabilir.
Son zamanlarda birlikte kapsülleme teknolojisi geri dönüştürülemediğinde maddi atıkların olumsuz finansal etkisini azaltmak için kenar kapsülleme teknolojisi uygulanmıştır. Önceki şekil, tek bir malzemeden oluşan bir bandın, bir birlikte-ekstrüdat ile yan yana ekstrüde edildiğini göstermektedir. Kapsülleme malzemesi düşük maliyetlidir, geri dönüştürülebilir ve yüksek mekanik özelliklere sahiptir. Kapsülleme malzemesi esas olarak üretim sürecine yeniden yerleştirilmesine ve malzeme maliyetinde büyük tasarruflara olanak tanıyan döşemeyi oluşturur. Ayrıca, kenar kapsülleme teknolojisi dahili deckle teknolojisiyle tamamen uyumludur.
Filtre / Süzgeç:
Filtrasyon sisteminin amacı, ekstrüzyon işlemi sırasında oluşan eriyik katışkılarının ve / veya jellerin aşağı akış geçişini önlemektir. Eriyik kontaminasyonunu önlemek için bu aşamada uygun kontrol şarttır. En yaygın filtreler metalik ağ içeren filtrelerdir. Filtre ortamını barındıran durum, ekstrüzyon işleminin izin verdiği maksimum basınca maruz kaldığında polimer akışı tarafından uygulanan kuvvetleri taşıyabilmelidir.
Elek gözlerine takılan özel filtreler ile eriyik içinde kalan ve ürün kalitesini düşüren kum, metal, erimeyen plastikler gibi kirletici materyalleri temizlemek için kullanılırlar.
Filtre plakaları hidrolik ünite veya azot gazlı üniteler ile hareket ettirilebilir. Özel yalıtımlı rezistanslar ve hassas ısı kontrolü ile ürün kalitesi ve verimde de maksimum seviyeye ulaşılmasına destek olan ünitedir. Dozajlama basıncının artmasına da etkendir. Elek gözeneklerinin proses sürecinde dolması ile değişim ihtiyacı doğar. Bu süreçte prosese Süzgeç Değişimi Duruşları da eklenerek üretim kaybı yaşanmasına etkendir. Bunun için dönen çarklı otomatik süzgeçler vardır. Kesintisiz üretim akışı içinde süzgeç değişimine olanak veren bu sistemler ise başlangıçta pahalı yatırımlardır.

Dozajlama:
Besleme haznesine, bileşen polimerik malzemenin birim miktarda kompleks içinde hangi oranda olacağı doğrultusunda akış sağlar. Gravimetrik ve volumetrik olarak temelde iki çalışma sistemi vardır.
Dozajlama Ünitesi Tercihi :
-
Enjeksiyon makinesi için dozajlama cihazı seçilirken aşağıdaki verilerin bilinmesi gerekir. Makinede üretilecek minimum ve maksimum ürün ağırlığının bilinmesi gerekir (kg/saat). Herbir dozajlanacak katkı veya boyanın minimum ve maksimum dozaj oranı (Ürün gramajına bağlı olarak ) (%).
-
Herbir dozajlanacak katkı veya boyanın (granül, mikrogranül, kırma, sıvı veya toz olmasına bağlı olarak ) dökme yoğunluğu, parça şekli ve sıcaklığı
-
Toplam baskı süresi (saniye)
-
Mal alma süresi (saniye)
-
Enjeksiyon mal alma noktasındaki boğaz flanş ölçüleri
-
Dozajlanacak malzemenin haznesine otomatik taşınmasının gerekliliği
Bu bilgiler dahilinde dozajlama cihazının vida kapasitesi, dozajlanacak malzemenin konulacağı haznenin kapasitesi, dozajlama cihaz boğaz tipi, kontrol paneli gibi detaylar belirlenip cihaz seçilebilir.
Dozajlama mı?, Blender mi?
Blender olarak adlandırılan Gravimetrik Çoklu Dozajlama ve Karıştırma Cihazı ise açıklamasından da anlaşılacağı üzere, bir birçok malzemeyi (ana malzeme dahil..) gravimetrik olarak dozajlayan ve bunları aynı cihaz içinde karıştıran kompleks bir cihazdır. Bir başka deyişle Blender, farklı malzemelerin istenilen oranda hassas olarak dozajlanması ve homojen karıştırılmasını sağlar. Yığın olarak tanımlanan bu karışım içinde bulunan her bir malzeme istenilen oranda karıştırılmış olur.
Bu özelliği ile Blender, gerek ana malzeme ve gerekse katkıların yoğunluk ve şekil değişimlerinden kaynaklanan volümetrik hatalardan etkilenmez. Öte yandan, istenilen ağırlıkta yığını işleme makinesinin boğazında her zaman hazır bulundurduğundan plastik işleme makinesinin hız değişimlerinden kesinlikle etkilenmez.
Blender kullanımının en büyük avantajı ise kırma hammadde kullanımında kesin çözüm olmasıdır. Kırma hammaddesinin engellenemez yoğunluk değişimi sebebi ile özellikle boya katım oranının prensip olarak sürekli değiştirilmesi gerekir. Dozajlama cihazları bunu yapamazlar. Ancak Blender, çalışma prensibi gereği her yığın hazırlamaya başladığında öncelikle kırma malzemeyi tartar. Buna bağlı olarak ana malzeme ve kırma oranını ayarlayarak çok hassas karışım sağlayarak, gereksiz hammadde ve boya kullanımını engeller.
Blender kullanmanın diğer bir avantajı ise, plastik işleme makinesinin vida boğazına direk olarak bağlanabileceği gibi bir platform üzerine de monte edilerek makine yanında veya merkezi olarak kullanılabilme özelliğidir.
(1) Gravimetrik Dozajlama:
Vidalı besleyicinin çalışması ile birlikte sistem her birim zamanda tartılır ve azalan malzeme miktarı hesaplanır.
Sürekli tartım ile yapılan dozajlama anlamına gelir. Hammaddenin dökme yoğunluğu değişmesinden dolayı yaşanan kalite, üretim, renk hatalarını ortadan kaldırmak için malzemenin ağırlığının sürekli tartılarak yapıldığı dozajlama yöntemidir.
Dozajlayıcı her hangi bir katkı veya boyanın plastik işleme prosesine katılması için tasarlanmıştır. En basit anlamı ile dozajlama cihazı plastik makinesinin ana malzemesinin aktığı haznenin vida boğazı ile birleştiği noktaya özel bir flanş ile bağlanan bir cihazdır. Bu noktada başka katkılar da aynı şekilde dozajlanabilir. Ancak her biri birbirinden bağımsız olarak dozajlanabilir.
Bu miktarla hedef değer karşılaştırılır ve motora hesaplanan uygun devir için komut verilir. Tanecikli (granül) ,toz, topraklı, llifli ve pullaşmış yapıdaki malzemelerin sürekli dozajlanmasında uygundur. Sürekli tartım olduğu için besleme miktarı sürekli denetlenir ve ayarlanır. Hassas ve hammadde tüketiminin önemli olduğu proseslerde kesinlikle gravimetrik yöntem tercih edilmelidir. %0,1 'lik hassasiyetlerle çalışılabilir. Bu hassasiyette gerçekleşen proseslerde hem sistem girdisi olan ham maddeden tasarruf edilmekte hem de sistem çıktısında homojenlik elde edilerek verimlilik ve kalite arttırılmak, sürekliliği sağlanmaktadır.
Ekstrüdere beslenen malzeme miktarını hacim olarak değil, ağırlık tartımı ile kontrol eder. Sistem, hacimsel karşıtlığından daha hassastır ve ±% 0,5 oranında azaltılmış hata toleransına sahiptir. Çoğu durumda, film, bir baz polimerin bir veya daha fazla ikincil bileşenle harmanlandığı malzemeler ile imal edilir. En gelişmiş üretim hatlarında, bu harmanlama yerinde gerçekleştirilir. Özellikle düşük erime sıcaklıklarına sahip malzemeler işlendiğinde veya granül boyutu küçük olduğunda granül taneciklerinin erken erimesini önlemek için özel dikkat gereklidir. .
Dozajlama cihazları ana malzeme değişikliklerini takip edemez. Çünkü bünyesinde ana malzemeyi gravimetrik olarak takip eden bir sistem yoktur. Bu sebeple, volümetrik veya gravimetrik tekil dozajlama cihazları harcanan plastik karışımı anlamında herhangi bir garanti vermez. Ancak, örneğin enjeksiyon makine uygulamalarında ana malzeme gramajı kesindir ve hassas dozajlama cihazı seçilirse ana malzeme değişikliğinden kaynaklanan homojenlik problemi yaşanmaz.
Çok hassas dozajlama uygulamalarında ve istatistiksel hammadde takibi yapılması amacı ile tercih edilmelidirler.
Gravimetrik dozajlamanın genel tercih nedenleri:
-
Maliyet : Gravimetrik dozajlama cihazları 6 ay gibi bir sürede kendi yatırım maliyetini amorti eder.
-
Kazanç : Fire azalır, üretim hataları azalır, 50% ye varan katkı/boya tasarrufu sağlanır.
-
Kararlılık : Özellikle adım motorlu çalışan gravimetrik dozajlayıcılar her katkı oranında sabit dozaj yaparlar.
-
Fonksiyon : Load-cell sistemi ile çalışan gravimetrik dozajlayıcılar çok kolay ayarlanır. Ürün gramajı (veya ekstrüder kapasitesi) ve katkı oranı girilmesi yeterlidir. Renk değişimi çok kısa sürede yapılır.
-
Tasarım : Modüler yapıya sahip gravimetrik dozajlayıcılar ile çok farklı kapasitelerde ve şekillerde katkı dozajlaması yapılabilir.
-
Takip : Gravimetrik dozajlayıcılar sürekli tartım yaparak çalıştıklarından vardiya/gün/ay gibi süreçlerde sarfiyat raporu alınabilir.
-
Tasarruf : Garvimetrik dozajlayıcılar sayesinde yüksek oranda geri dönüşüm malzeme kullanılsa dahi homojen ve tasarruflu boya/katkı kullanılır.

(2) Volumetrik Dozajlama: Gravimetrik dozajlamaya göre daha eski bir yöntemdir. Dolayısıyla daha fazla bilinir. Gravimetrikten en belirgin farkı prosesin içinde tartımın olmamasıdır. Gramaj kontrolü yerine sabit bir devirde dönen bir besleme vidası vardır. Prosesin başında malzeme yoğunluğuna göre ve istenen besleme miktarına göre (kg) besleme vidası tercih edilir. Daha sonra yoğunluğa göre "ne kadar hacimde bir vida adımının verilen zaman sonunda istenen kg vereceği" hesaplanır ve sistem buna göre sabit bir devirde çalışır.
Devir sabit olduğu için malzeme yoğunluğundaki küçük farklar bile dozajlanan malzeme miktarını etkiler. Bu da kaba bir tartım anlamına gelir Yaklaşık %10' luk bir hassasiyette çalışır. Sistem çıktısında homojenlik dağılımı dalgalı gir grafik çizebilir.
Maliyeti gravimetrik dozajlamaya göre çok daha düşüktür. Tercih edilmesindeki en önemli sebep de zaten budur.

Eriyik Pompası :
Ekstrüder makinesi eriyiği sabit basınçta ve hacimde kalıplara taşıma işinde yeterli etkiye sahip olmayabilir.
Bu amaç için eriyik pompaları kullanılır. Eriyik pompası karıştırma yada eritme aygıtı değildir fakat basınç yaratmada ve eriyiği ölçerek teslim etmede son derece etkindir. Yeterli miktardaki polimer ekstrüder vidasının hız değişimleri nedeniyle oluşan iç basınç dengesizlikleri ve ekstrüder dalgalanmaları vidanın hızı kapalı devre kontrol edilerek ortadan kaldırır ve kalıp yönünde çok daha yüksek ve değişmez değer basınçla pompalama yapar. Eriyik pompası ile yaşanan basınç değişikliği aşağıda görülmektedir.



Vakum Pompası / Kutusu:
Malzeme kaybının önüne geçilmesinin yanında eriyik plastikten ve kontrolsüz gaz çıkışından kaynaklı zarar görmeleri engeller. Ürün kalitesinde hiçbir sorun yaratmadığı gibi vakum gaz ve nem sıkışmalarından kaynaklı kalite problemlerinin önüne geçilmesini sağlar. Artırılmış ekstrüder basıncı gözenekliliği artırır. Havalandırma portu tıkanıklığı nedeniyle rahatsız edici ve maliyetli bir şekilde zaman aşımını en aza indirir, Hassas toleranslar, Nem ve gazı eriyekten uzaklaştırır.
Sıcak ağ ile rulo arasındaki hava bariyerini en aza indirmek için birincil söndürme rulosu yüzeyi ile film arasındaki sürüklenen havayı uzaklaştırır. Bu hava bariyeri, indirgenmezse, film soğutma işlemini engelleyen bir ısı yalıtım yastığı görevi görür. Kutu ayrıca filmdeki boyun miktarını ve hava boşluğunu azaltır ve daha yüksek hat hızlarının kullanılmasına izin verir.
Vakum kutusu, ağ soğutmasını daha da arttırmak için bir hava bıçağı veya bir hava bölmesi ile birleştirilebilir.
Otomatik Gösterge Kontrol Sistemi: Genişlik boyunca film kalınlığı dağılımının satır içi ölçümü ve kontrolü, gösterge kontrol sisteminin veya APC'nin (Otomatik Profil Kontrolü) fonksiyonudur. Kalıp üzerindeki esnek dudak manuel olarak kontrol edildiğinde ve üretim prosesi iyi ayarlandığında, film kalınlığı değişimleri ±% 3 ila ±% 5 aralığında olacaktır. Otomatik modda, bu varyasyonları yarı yarıya azaltmak mümkündür. Aşağıdaki şekilde, otomatik kontrol modülü kalıbın esnek gövdesi üzerine monte edilmiş olarak otomatik bir kalıp gösterilmektedir. Termal çeviriciler veya termal cıvatalar modülü oluşturur. Cıvatalar arasındaki mesafe tipik olarak 1.125 inçtir. Gösterge kontrol sistemi bir radyasyon emisyon birimi ve bir kontrol konsolu içerir.
Radyasyon ünitesi makineyi çapraz yönde hareket ettirir, filmi döngüler halinde tarar (dakika olarak ölçülür). Yaygın olarak, radyasyon bir beta ışını kaynağından kaynaklanır; bununla birlikte, x-ışını ve kızılötesi kaynaklar da kullanılabilir.
Genel olarak, film kalınlığı, film radyasyon emilim oranının bir fonksiyonu olarak belirlenir. Böylece, emme oranındaki varyasyonlar film kalınlığı varyasyonlarına dönüşür.
Kontrol konsolu, kontrol sistemi ve otomatik kalıp arasındaki ara yüzdür. Kalıp üzerindeki her bir ayar noktası veya termal tercüman, film üzerindeki bir konum ile uzaysal olarak ilişkilidir. Buna haritalama denir. Kontrol sistemi gerektiği gibi termik çeviricilere güç uygular ve dudak boşluğu ayar elemanının termal genleşmesi ile düzenlenir.
APC ile ilişkili önemli bir değişken zaman sabitidir. Bir ayarlama elemanının maksimum uzamasının% 62.3'ünü uzatması için gereken süre olarak tanımlanır. Zaman sabiti ne kadar kısa olursa, sistem o kadar duyarlı olur ve verimlilikteki kazançlara dönüşür.
Granülatör/Kırma:
Ekstrüzyon sonrası spageti hatlarının kesme ve boyut verme işi için döner bıçaklar sistemiyle çalışan, ve ürüne tanecik formu veren ünite granülatörlerdir. Yarı form malzeme yaklaşık olarak makine çıkış hızı ile aynı hızda dönen ofset halkalar arasında kesilmesi ve santrifüj eylemi ile malzemenin tanecik boyutunda dışarı atılması sistemi ile çalışır. Kırma, güçlü rende üniteleri de yaklaşık aynı metod ile daha çok geri dönüşüm, tekrar kullanma amacı ile çalışan ünitelerdir. Kırma ve güçlü rendelerden ürün olma formunu yitirmiş ancak besleme ünitesinde tekrar kullanılabilecek hacimleri sağlamak için istifade edilir.

Korona ünitesi:
Mürekkeplerin veya kaplamaların film yüzeyine yapışmasını kolaylaştırmak için bir yüzey işlemi uygulamak gerekir. Korona tedavisi, mevcut yöntemlerin en yaygın kullanılanıdır. Korona işlemi, film ve çeşitli yüzeylerin baskı veya yapıştırmaya hazırlığı amacı için kullanılır. Korona ünitesi işlenecek yüzeye elektrik kıvılcımları göndererek, yüzeyin pürüzlenmesini ve mürekkep veya tutkalın yüzeye daha iyi tutunmasını sağlar.
Korona işlemi, filmin yüzey enerjisini ve dolayısıyla yüzey gerilimini arttırır. Sistem bir güç kaynağı ve tedavi istasyonu içerir. Güç kaynağı 50/60 Hz bitki gücünü 10 ila 30 KHz aralığında çok daha yüksek frekans gücüne dönüştürür. Bu yüksek frekanslı enerji, tedavi istasyonuna beslenir ve tipik olarak 0.5 inç ila 1 inç arasında değişen bir hava boşluğu yoluyla biri yüksek potansiyeli olan, diğeri düşük potansiyeli olan iki elektrot aracılığıyla film yüzeyine uygulanır.
Üretilen yüksek potansiyel farkı havayı iyonize ettiğinde film yüzeyindeki yüzey gerilimi artar. Korona muamelesi, film üretildikten sonra satıh içi ya da ayrı bir alt akış işlemi olarak yapılabilir. Satıh içi yapılması halinde, potansiyel toksik ozon oluşumuna özel önem verilmelidir. Bazı durumlarda, üretim alanında bir havalandırma sistemi sağlamak gerekir.

Chiller / Soğutma ünitesi:
Makina ve ekipmanlarının soğutulması için kullanılan makina giriş suyunun sıcaklığını stabil tutumak kullanılan "Dış" ünitedir.
Temel amaç, makine, kalıp gibi sıcak ünitelerden çıkan sıcak sudan ısıyı alıp, suyun sıcaklığını düşürüp, tekrar makineye verme ilkesine bağlıdır. Su veya hava soğutmalı olarak farklı çalışma prensiplerinde olabilir. Su soğutmalı soğutucular daha verimlidir. Bu sistemde; soğutma kulesi, kondenser ve makyaj su pompaları, rezervuar temel bileşenlerdir. İç mekanlara yerleştirilebilir daha küçük hacimlerdedir.
Hava soğutmalı soğutucular ise estetik ve çevresel koşullar veya su erişim kısıtlamaları mevcut olduğunda, tercih edilirler.
Farklılık; su soğutmalı soğutma gruplarının veya daha ziyade soğutma kulelerinin nemli bir hava akımı kullanırken, hava soğutmalı soğutucular bir ortam havası akımı kullanmasıdır . Normalde su soğutmalı soğutucular, yüksek su tüketiminin dezavantajına sahip olsalar da daha ucuz ve daha verimlidir.
Hava soğutmalı soğutucuların faydaları şunlardır;
-
Soğutma kulesi ve su israfı yoktur.
-
Düşük bakım maliyetlidir ve kullanımı daha kolaydır.
-
Ayrıca kimyasal maliyetleri de olmaz.
Soğutma kapasitesi, chiller seçimi için ana kılavuzdur .
Su soğutmalı chiller daha enerji verimli olsa da, kurulum maliyeti, bakım maliyeti, ekipman sayısı ve diğer bazı yönleri açısından hava soğutmalı chillerden dezavantajlıdır.
(ChillRoll) birincil söndürme silindiri, ikincil bir rulo, silindirlerin düzgün dikey ve çapraz makine yönü hizalaması için motorlu bir rulo konumlandırma sistemi ve birçok durumda bir vakum kutusu ve / veya hava bıçağından oluşan "İç" ünitedir.
Merdaneler tipik olarak daha iyi bir yüzey kalitesi elde etmek ve film soğutması sırasında ısı transfer işlemini arttırmak için krom kaplıdır. Soğutma maddesi genellikle silindirlerin içinde dolaşan sudur.
Birincil söndürme rulosu filmin bir tarafını, ikincil rulo ise filmin karşı tarafını soğutur. Kalıp, 45 ° ila 90 ° arasında değişen bir açıda birincil söndürme silindirinin üzerine yerleştirilir. Kalıp dudaklarından çıkış ve rulo arasındaki mesafe 0.8 ila 2 inç arasında değişir. Soğutma sistemi hattın yüksek hızlarda çalışmasını sağlar. Hat hızı gereksinimi arttıkça, silindirler için belirtilen çaplar da artar.
Düzgün bir gerginlik sağlamak ve filmin genişliği boyunca kalınlık değişimlerini en aza indirmek için rulolar ağ ile mükemmel bir şekilde hizalanmalıdır.
Ayrıca, makine yönünde film kalınlığı dalgalanmalarını önlemek için ruloların açısal hızı iyi kontrol edilmelidir.
Kalıp sabit gövdeye bağlı bir vakum kutusunun kullanılması, daha verimli bir soğutma gerektiren Cast PP gibi belirli uygulamalarda gereklidir. PP malzemeler, agresif bir şekilde soğutulmadığı takdirde, nihayetinde puslu filmlere yol açan kristaller oluşturma eğilimindedir.

Termokupl:
Sıcaklık kontrolü ve ısı ölçümü, ekstruzyonun en önemli süreç kontrol işlemidir. Bu iş için kullanılan ekipmanlar termokuplardır. Ve termokuplar çeşitli yapı ve ölçüm tekniklerinde olabilir. Makine ile tercih edilen termokuplun uyumluluğu dikkat edilmesi gereken ilk adımdır. Termokupl, bir tür sıcaklık sensörüdür. Farklı iki iletken malzemeden oluşur ve bu bağlamda «Isıl Çift» olarak tanımlanır. Bu malzemelerin iki ucu, sıcaklığa maruz kalacak tarafta birleştirilir. Boşta kalan diğer uçlar daha soğuk olmasından ötürü bir gerilim elde edilir. Kullanılan malzemenin cinsine ve birleşim noktasının ısınma miktarına bağlı olarak gerilim değişkenlik gösterir.
Bilinen soğuk noktadaki değer ile gerilim değerleri mukayesesi ile sıcak nokta değeri tespit edilir. Yani; sıcak noktanın değerini öğrenebilmek için, soğuk noktanın değerinin biliniyor olması gerekir. Bilinmeyen soğuk nokta değeri durumunu bertaraf etmek bilinen bir noktaya kompanzasyon kablosu uzatılmalı ya da çalışma sistemine ayrıca termostat şeklinde bir ünite dahil edilmelidir.
Termokuplda kullanılan malzemin cinsine göre tip tanımlamaları yapılır.
En sık kullanılan malzeme çiftleri;
Bakır-Konstantan, Demir-Konstantan,
Nikel Krom-Nikel, Platin Radyum-Platin,
Kromel-Konstantan, Kromel-Alumel birleşimleri şeklindedir.
Farklı birleşimli yapılar, aynı ölçüm değerlerinde bir kaç °C farklı ölçümler yani sapmalar gösterecektir ki bu da yanlış ölçümler demektir. Bu durum da yanlış müdahalelere neden olacaktır. Termokuplarda ilk kenar her zaman pozitif olandır. Bunun için renk kodlamaları mevcuttur ve bu
kodlar hem temokupl hem de kompanzasyon için geçerlidir. Termokupl telleri renk kodu içermiyorsa pratik bir kaç ipucu tanımlama mecuttur ki bunlar kompanzasyon kablosunda
geçerlilik göstermez.



Sarma ünitesi:
Basit bir ifadeyle, haddelenmiş filmi malzeme rulolarına dönüştürmek için sarıcılar kullanılır. Sarma işlemi, bu rulolar açıldığında ve diğer akış aşağı işlemlerde dönüştürüldüğünde filmin özelliklerini ve boyutlarını koruyacak şekilde olmalıdır.
Üç temel sarıcı türü vardır; yüzey sargıları, taret veya merkez sarıcılar ve merkez / yüzey sarıcılar. Yüzey sargıları, filmi geniş çaplı bir tambur ve tamburun üzerine değişken basınçla bastırılan bir sargı şaftı arasındaki temastan geçirir. Taret sarımları veya merkez sarımları, yapı rulosunun ortasından geçen bir tahrik mili kullanan veya yapı rulosunu çalıştırmak için çekirdeği destekleyen aynalar kullanan herhangi bir sarma makinesidir. Son olarak, bir merkez / yüzey sarıcısının (veya boşluk sarıcısının) birleşik yaklaşımında, yüzey sargı rulosu veya rulo üzerine sarmak ve sargı rulosu arasında küçük bir boşluk korunur. Bir merkezi tahrik sistemi, sarım rulosunu yüzey tamburundan bağımsız olarak tahrik eder.
Filmler yapışkan olabilir veya bir dereceye kadar kayma yapabilir, yüksek veya düşük elastikiyete sahip, ince veya kalın olabilir, gerekli rulo çapı büyük veya küçük olabilir; rulolar dar veya geniş, yumuşak veya sert olabilir. Sarıcı teknolojisi karmaşıktır ve belirli bir uygulamada kullanılan uygun sarıcı türü yukarıdaki değişkenlerin tümüne bağlıdır.
Taret veya merkez sarımların kullanımı dökme film uygulamalarında tipiktir. Bu tür sarıcı ile, rulo çapı arttıkça ağ gerginliği azalır. Bu, sarma milinin dönüş hızı ile kontrol edilir. Yuvarlanan rulo, katmanlar arasında az miktarda havanın sıkışmasını önler veya buna izin verir. İkincisi, yüksek yapışkanlığa sahip filmlerin sarılması veya yumuşak ruloların sarılması için önerilir.
Ekstrüde edilmiş film üzerindeki kusurları eşit olarak dağıtmak için (kalınlık varyasyonları) dağıtıcı merdaneler kullanılır. Film sarılmak üzere merdanelerden geçerken yanlara doğru hareket ettirir. Alternatif bir yöntem de, kesiciyi ve sarıcıyı filme göre ileri geri hareket ettirmektir.

Kontrol Sistemi:
Dökme ekstrüzyon hattının ana bileşenleri numaralandırılmış ve açıklanmıştır. Bu bileşenler kendi başlarına hareket etmezler, ancak bilgisayarlı bir denetim ve kontrol sistemi tarafından entegre edilir ve yönetilirler. Ana bilgisayar, tüm hat bileşenlerinin kontrollerini düzenli bir şekilde birleştiren ve yönlendiren beyindir.
Bilgisayarın ana görevleri şunlardır:
-
Hattın başlatılmasını, kapanmasını ve hızını kontrol etmek için;
-
Ekstrüderlere beslenen malzemenin ağırlığını izlemek ve sabit bir verimi korumak için ekstrüderlerin hızını kontrol etmek;
-
Tüm sıcaklık bölgelerini ve tüm malzemelerin sıcaklıklarını kontrol etmek için;
-
Gösterge kontrol sistemi, otomatik kalıbın yanıtı ve hat hızı arasındaki etkileşimi koordine etmek;
-
Ağ gerginliğini kontrol etmek için; ve
-
Tüm ürün tariflerini saklamak ve işlemek için operasyonel verileri saklayın ve alarm sistemini kontrol edin.
İyi bir kontrol sistemi, operatörlere kullanımı kolay bir grafik arayüz veya monitör sistemi sağlamalıdır.

Ekstrüzyon Üretim Hatları
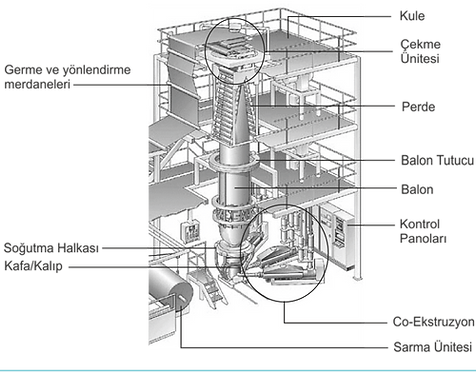
Üflemeli (Blown) Film Hatları
Çok geniş bir uygulama yelpazesini kapsayacak şekilde her yerde kullanım için tasarlanmış üretim hatlarıdır. 250 mikron kalınlığında bariyer filmler, 10 mikron HDPE çöp torbalarına kadar çeşitli ürünler için tercihtir. Yüksek oranda doldurulmuş, saydam olmayan şişirilmiş filmlerin üretimi için Co-Ektruzyon tekniğinde uygulanabilir. Üflemeli film ekstrüzyonu , özellikle ambalaj endüstrisinde plastik filmler yapmak için en yaygın yöntem olarak tercih edilmektedir. İşlem, eriğin ekstrüde edilmesini ve başlangıç (kafa) çapının bir kaç katına kadar geniş olabilecek ince bir film balonu oluşturulmasını ve daha sonrasında da bu balonun söndürülerek düz bir film formuna dönüştürülmesi ilkesine dayanır. Kapalı çift kat şeklinde oluşan film sarma ünitelerinde üç farklı nihai işlemle bitirilir. Film, olduğu gibi sarılarak iki tarafı kapalı tüp şeklinde, bir kenarı kesilerek sarım eninin iki katına eşit genişlikte tek kenarı kesik, yada iki tarafı da kesilerek çift sarma ünitesinde tek katlı olabilir. Arzu edilirse bir dilimleme ünitesiyle de film bir kaç dilime ayrılarak daha dar enli filmler oluşturulabilir. Bu işlemle genellikle polietilen kullanılır.
Tipik olarak, üflemeli film ekstrüzyonu dikey olarak yukarı doğru gerçekleştirilir, ancak yatay ve aşağı ekstrüzyon işlemleri de uygulanabilmektedir. Üflemeli film genel olarak, döküm veya ekstrüde edilmiş filmlerden daha iyi mekanik özellikler dengesine sahiptir, Çünkü hem enine hem de makine yönlerinde uzamaları vardır. İnce filmin mekanik özellikleri, çekme ve eğilme mukavemetini ve tokluğu içerir. Her iki yöndeki neredeyse tekdüze özellikler, filme maksimum dayanıklılık sağlar.
Üflemeli film üretimi, dökme (Cast) ekstrüzyondan daha düşük erime sıcaklıkları gerektirir.
Dökme yönteminde kafa sıcaklığı yaklaşık 220°C iken, üfleme filminin sıcaklığı yaklaşık 135°C 'seviyesindedir. Ayrıca, üflemeli üretim ekipmanları maliyeti, döküm film hattının ekipmanları maliyetinin yaklaşık yarısı kadardır. Üflemeli filmde nihai ürün MFI yaklaşık 1.0 g/10 dk'dır. Bu da film kalınlığını kontrol etme işini daha karmaşık ve daha zor hale sokan etkenlerden biridir. Ayrıca bu düşük MFI değeri ile üflemeli film hatları üretim kapasitesinin, dökme film hatlarına nazaran daha düşük olmasına neden olur. Üflemeli film hatlarından çıkan ürünler doğrudan mamül olabileceği gibi, daha çok yarı mamül / yarı form niteliğinde karşımıza çıkmaktadır.
Mamül olarak, sera örtüsü, branda, çileklik, karpuzluk, nematod, solarizasyon, sulama hortumu, izolasyon su gecirmez örtü ve tabakaları örnek verilebilir. Bunun yanında shrink, stretch/streç, poşet, torba gibi ikinci ve hatta üçüncü kademe işlemler de gerektiren mamüller için ilk proses aşaması yine bu hattan gerçekleşir.
Son yıllarda 0,7 mm’ den düşük kalınlıktaki tabakalar ve plastik film yapımında en çok kullanılan üretim metottur. Proseste özetle erimiş plastik halkasal bir kalıpta yukarıya, doğru dikey olarak ekstrüde edilerek ince bir tüp oluşturulması, ekstrüder kafasına yerleştirilen mekanizma ile, üflenen hava yardımıyla plastik tüpün balon şeklinde şişirilmesi, çekici ve gerici merdaneler ile balonun film formuna sokularak rulo şeklinde sarılması ilkesine dayanır.
Kalıp/kafa noktasından uygulanan hava soğutma etkisiyle balonun yumuşak formdan katı forma dönüştürülmesi hızlandırılır. Dönüşümün yaşandığı bu noktasal hiza, «donma hattı/çizgisi» olarak tanımlanır. Oluşan balon üzerinde kalınlık dağılımının tüm yüzeye eşit olarak yayılması için ya balonun alt ucundan yani kafadan ya da üst ucundan yani çekme merdanelerinden 360° ye kadar dönme, çevirme hareketi uygulanır.
Böylece kalıp/kafa noktasında oluşabilecek kalınlık farkı, tüm film yüzeyine yayılarak bir denge sağlanır.
Plastik balonun içindeki basınç, silindirlerin çekme hızı, balonun soğutulma hızı hem kristaliniteyi hem de oriyantasyonu etkilediklerinden en önemli proses değişkenleri içinde yer alır.
Co-Ekstruzyon uygulaması ile daha çok yönlülük sağlanmaktadır.
-
Daha esnek ekipman daha yapısal değişikliklere uyum sağlayabilir, böylelikle işlemcilerin piyasa ihtiyaçlarına daha iyi yanıt vermesine olanak tanınır.
-
Daha iyi film kalitesine ulaşılır.
-
Daha fazla sayıda katmanın daha muntazam özelliklere sahip daha düz bir film verdiğine dikkat çekilir.
-
Daha düşük malzeme maliyetleri ile üretim gerçekleşir.
-
Daha fazla katman oluşacağından ara katmanların içine, yapılarda daha düşük maliyetli dolgu malzemeleri eklenerek filmin maliyetinin düşürülmesi mümkün hale gelir.
Üflemeli film ekstrüzyonu birçok polimer üretim işleminden biridir. Bu yöntem, tipik olarak büzülme, streç, bariyer filmler (şarküteri etini korumak için kullanılır), dondurulmuş gıda ambalajı ve alışveriş torbaları gibi ambalajlarda kullanılan emtia ve özel polimer filmleri üretmek için kullanılır.
En yaygın olarak polipropilen ve polietilen (LDPE, HDPE ve LLDPE) olmak üzere şişirilmiş film ekstrüzyonunda kullanılabilecek birçok polimer türü vardır. Bu yöntem, tek tabakalı filmlerin yanı sıra, birden fazla plastiği tek bir film halinde birleştirmek için ko-ekstrüzyon içeren daha karmaşık çok katmanlı filmler üretebilir.
Üflemeli film ekstrüzyonu karmaşık olabilir, bu yüzden şimdi sürecin her adımını ayrıntılı olarak açıklayacağız!
İlk adım polimeri bir ekstrüderde eritmektir.
Çoğunlukla boncuk şeklinde olan polimer reçine (granul boyut), bir huni içine yüklenir ve bir vida ile ısıtılmış bir kanala beslenir.
Vida, polimeri hazneden, kanalın diğer çıkış ucuna taşımak için kullanılır. Granul boyutlu taneler eritilmek için kademeli olarak ısıtılır. Isı profili ekstrüzyonun önemli bir parçasıdır çünkü polimer aşırı ısındığında termal olarak bozunabilir. Erimiş malzeme kanal ucuna ulaştığında, bir kalıptan ekstrüde edilir. Bu noktada, üflenen film ekstrüzyonu diğer ekstrüzyon işlemlerinden farklıdır.
Üflemeli film ekstrüzyonunda kullanılan en yaygın halka şeklindeki birkaç farklı tipte kalıp vardır, bu da basit bir daire kalıbıdır. Erimiş polimer kalıp kafasına girer ve polimeri orijinal, ekstrüde çapının birçok katı olan ince bir tüpe radyal olarak şişirmek için kalıp merkezindeki bir delikten hava enjekte edilir. İstenen film kalınlığını ve genişliğini elde etmek için ayarlanabilen işlemin bu adımıdır.
Sıcak tüp filmi daha sonra tipik olarak yüksek hızlı hava ile soğutulur ve kıstırma makaraları adı verilen ekipman ile yukarı doğru çekilir. Çoğu orta ila büyük boyutlu film hattında, bu dikey tüp havaya birkaç kat uzatabilir. Film soğudukça don çizgisi olarak adlandırılan yerde kristalleşir. Boru kıstırma silindirlerine ulaştığında, hattın üstünde, film şimdi düzleşecek kadar serindir ve daha sonra düz ya da çökmüş boru olarak adlandırılır.
Film daha sonra ileri işlemler için silindirler tarafından aşağı doğru nakledilir (örn. Yarık, baskılı, havalandırmalı, torbalara dönüştürülür) ve sonunda rulolara sarılır. Üflemeli film ekstrüzyon işlemini kullanarak film üretmenin, işlem koşullarına ve kullanılan baz polimer (ler) e dayanarak nihai plastiğin mekanik özelliklerini manipüle etme kabiliyeti de dahil olmak üzere birçok avantajı vardır.
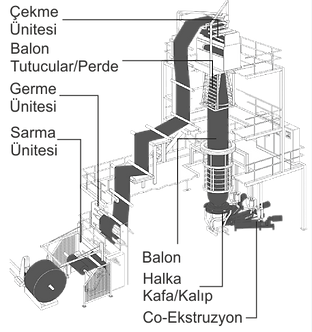
Dökme (Cast) Film Hatları
Dökme film prosesinin ana argümanı düz «T» kalıptır.
Ekstruzyon sonrası eriyik bu T kalıptan düz bir perde gibi çıkar ve derhal soğuk merdanenin (Chill-Roll) üzerine akar. Tipik olarak su soğutmalı ve krom kaplı yüzeye sahip bu tambur, şoklama ile eriyiği soğutur. İşlem; düz çıkan eriyiğin uygun enli merdaneler ile nihai sarma ünitesine taşınması ilkesini içerir. Burada film tek kattır ve tüm merdaneler kalıp eni ile eşdeğerdedir. Doğal olarak sarma ünitesi de tek kat film sarar. Arzu dilmesi halinde dilimleme ile muhtelif film enleri oluşturulabilir. Hızlı söndürme özelliklerinden ötürü, bir döküm film genellikle bir üfleme filminden çok daha iyi optik değerlere sahiptir. Döküm film için eriyik akış endeksi MFI yaklaşık 5.0 g/10 dk'dır. Bu değer daha yüksek hat hızlarına ulaşılmasına etkendir. Döküm film hatları 300 m/dk'ya kadar üretim oranlarına ulaşılabilir.
Makine yönünde uzama değerleri döküm sürecine nispeten çok daha iyidir.
Bununla birlikte, makinenin çapraz doğrultudaki film mekanik özellikleri, üfleme işleminde yaşanan daha yüksek yönelimlerin oluşturduğu değerlere nispeten çok daha düşüktür. Dökme film hatlarında kalınlık kontrolü, film eni boyunca otomatik gerçekleşir. Hareketli bir sensör sürekli ilerleyen hattı kontrol eder ve aldığı verileri otomatik olarak kafa rezistans ve hareketli civatalara ileterek gerekli müdahaleyi yapar. Film kalınlık değişimi yaklaşık %1 ile %2,5 arasındadır ve üflemeli filmelere nazaran çok daha iyidir.
Dökme film hattı; gravimetrik besleme, ekstruder, filtrasyon ve düz kalıp sistemi, soğutma tamburu, otomatik kalınlık kontrol sistemi, haddeleme, sarma/dilimleme ünitesi ve opsiyonel korona ünitesi bileşenlerine sahiptir.
Dökme film hatlarında Co-Ekstruzyon tekniği hakimdir. Streç, slaj sargı filmleri, kişisel bakım filmleri, fırın filmleri ve yüksek netlikte filmler, nematod, sera örtüleri de dahil olmak üzere çeşitli film üretimi mümkündür.
Dökme filmler, gıda ve tekstil ambalajlama, çiçek sarma, fotoğraf albümü sayfa koruyucuları olarak, ekstrüzyon kaplama işlemlerinde kaplama substratları olarak veya daha karmaşık filmlerin oluşumunda diğer malzemelere lamine edilmiş olarak kullanılır. Tipik olarak, döküm film işlemi, çok katmanlı bir film oluşturmak için tek bir kalıptan iki veya daha fazla malzemenin eşzamanlı ekstrüzyonu olan koekstrüzyonun kullanılmasını içerir. Bunun nedeni, çoğu durumda plastik filmin son uygulamasının, film sadece bir malzemeden oluşması halinde elde edilemeyen bir performans gerektirmesidir. Örneğin, birçok durumda gıda paketleme uygulamaları oksijen bariyeri özellikli filmlerin kullanılmasını gerektirir. Gereksinimi karşılamak için EVOH gibi yüksek bir oksijen bariyeri malzemesi, çok katmanlı bir yapıda poliolefin malzemelerle birleştirilir. Birlikte haddelenmiş filmler daha çok yedi katmanlıdır, ancak daha fazla katman kullanımı giderek yaygınlaşmaktadır. Katmanların sayısı, koekstrüzyondaki konumları ve kendi kalınlıkları, filmin özel uygulamasına bağlı olarak değişen değişkenlerdir.
Döküm Ekstrüzyonunun Faydaları / Sınırlamaları
Üflemeli film işleminin aksine, filmin döküm ekstrüzyonu ile soğutulması oldukça verimlidir. Bu, daha yüksek üretim hattı hızlarına izin verir ve bu da ürünün üstün optik özellikleriyle daha yüksek üretim hızlarına neden olur. Çekme ve yönlendirme derecesi, döküm film işleminde üflemeli film işlemine göre önemli ölçüde daha düşüktür. Kalınlık dağılımının nedeni budur
makinede çapraz yön, döküm prosesleri ile daha eşittir (±% 1.5 kadar düşük varyasyonlarla). Bununla birlikte, makinenin çapraz yönündeki film mekanik özellikleri, filmin üflenmiş işlemde deneyimlediği daha yüksek yönelim seviyesi nedeniyle üflenmiş film işlemi ile elde edilenlere kıyasla daha düşüktür.
Dökme ekstrüzyonda filmin kenarları boyutsal düzensizlikler ve / veya zayıf tabaka dağılımı nedeniyle kırpılır. Sonuç olarak, kesilen malzeme geri dönüştürülemezse işlem olumsuz etkilenebilir. Son düz kalıp sistemi teknolojisi, ekstrüzyon işlemlerinde harcanan malzeme miktarını önemli ölçüde azaltarak bu sorunu en aza indirmiştir. Bu konu bir sonraki bölümde bir ölçüde ele alınacaktır.
Döküm Ekstrüzyonunun Temel Kavramları
Dökme film ekstrüzyon işleminde, erimiş polimer nihai düz film şeklini benimsemek için düz bir kalıp sisteminden geçer. Kalıp sistemi, kalıp ve besleme bloğu (işlem birlikte ekstrüzyon gerektiriyorsa) veya işlem, tek katmanlı ekstrüzyon işlemi ise basitçe kalıp tarafından oluşturulur. İşlem, bir veya daha fazla ekstrüdere bir gravimetrik besleme sistemi vasıtasıyla plastik reçinelerin beslenmesi ile başlar. Malzemeler daha sonra eritilir ve ekstrüderlerle karıştırılır, süzülür ve kalıp sistemine beslenir.
Kalıptan çıktıktan hemen sonra, erimiş perde, filmi "dondurmak" için su soğutmalı bir soğutma rulosu ile sıcaklığın düşürüldüğü soğutma birimine girer. Film daha sonra, kenarların kesildiği, korona muamelesi uygulanarak (baskı veya kaplama gibi bir imalat işlemi gerekiyorsa) aşağı doğru geçirilir ve film rulolara sarılır. Tipik bir döküm film hattının ana bileşenlerinin bir açıklaması aşağıda sunulmuştur.






Compound / Masterbatch Üretim Hatları
Temelde, mikser, ekstruder, kurutucu ve granulatör ünitelerinden oluşur. Üretimin hacmine bağlı olarak, agromel, besleme silosu, elek, kırma, dozajlama yan elemanları da bu süreçte yer alabilir. Compound üretimlerinde kullanılacak hammedde çok çeşitlik gösterebileceği gibi, masterbatch üretimlerinde dah çok, LDPE, PP, SAN, ABS, kısmen de PC, PET, EVA, nadiren HDPE ve diğerleri tercih edilmektedir. Compuand ve masterbatch üretim hatlarından nihai üründen ziyade, nihai ürünlerde kullanılacak ara form ürün, nihai ürünün hammaddesi veya ürün kalitesini şekillendirecek ajan ve renk katkıları üretimi gerçekleştirilir. Süreç girdileri temelde mikron partikül boyutlu toz veya granul ölçekli taneciklerden ibarettir. Girdiler belirlenen formülasyon içerisinde miktarları tespit edildilkten sonra, manuel veya mikser ile karıştırılarak elde edilen homojen malzemenin ekstrude edilmesi ve sonrasında çıkan spagetti ürünün granul boyutlarında kesilmesinden ibarettir. Tercih doğrultusunda öğütme işlemi ile granül boyutları toz formuna dönüştürülebilir. Ancak her durumda da çıkan ürün, ara form üründür.
Renk masterbatch, plastikleri renklendirmek için kullanılan katı veya sıvı bir katkıdır. Bir ısı işlemi sırasında kapsüllenmiş bir pigment veya katkı maddesinin bir taşıyıcı reçineye konsantre edilmiş bir karışımıdır, daha sonra soğutulur ve granüler bir şekle kesilir. Masterbatchler, üreticilerin plastik üretim prosesi sırasında ekonomik olarak ham polimeri renklendirmelerine olanak tanır.
Masterbatch üretimi süreç, «mono» ve «tailor made» olarak iki kısıma ayrılır.
Mono üretiminde ana veya en çok sarf oranı olan renkler çalışılır.
Tailor made ise elde dilen mono renklerinin çeşitli kombinasyonlarda eşleştirilmesi, formülasyonu ile elde dilen veya istenilen renklerdeki çalışmadır.
Dikkat edilecek hususlar şu şekilde sıralanabilir.
- Özellikle PVC üretiminde kullanılan dolgular renk tonunu değiştirmektedir.
- Kablo üretim şekillerindeki farklılık boyanın rengini etkilemektedir.
- Makinelerin iyi temizlenmemesi renk sökümüne ve ize neden olmaktadır. Makinelerin durup çalışması daha önceden kalan akış yolu dışındaki alanda var olan malzeme ile temasa neden olabilir. Bu da üründe iz sorunu olarak ortaya çıkar. Makine kirliliğinden şüphelenildiği durumlarda sadece hammadde ile birkaç baskı alınıp, akış hattının temizliği her aşama ile kontrol edilmelidir.
- Makineler 10 dakikadan uzun süre durdurulup tekrar çalıştırıldığında ilk baskılar kontrol edilmelidir. Malzeme uzun süre ısıya maruz kaldığı için yanma gerçekleşebilir.
- Özellikle film üretiminde kullanılan hammadde ve mikron değişikliği olduğu durumlarda mutlaka deneme üretim yapılmalıdır.
- Kullanılan taşıyıcın erime noktasından düşük sıcaklıklarda çalışıldığında nihai üründe erime gerçekleşmeyecektır.
- Nem çeken hammaddeler üretimden önce mutlaka koşullandırılmalıdır.
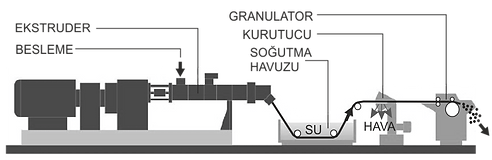

Boru / Profil Üretim Hatları
Boruları sınıflamanın bir yöntemi de kaynaklarına göre yapılmalarıdır. Borular: Kaynaklı (Düz yada Spiral) ve Kaynaksız olarak ikiye ayrılır. Kaynaklı borular metal işlemede yer alır. Yani metallerden hem kaynaklı hem kaynaksız boru üretimi yapılabilir. Ancak plastiklerden üretilen borular tamamen kaynaksız olanlardır. Kaynaksız boru üretiminde kullanılan yöntemler ise özel haddeleme ve ekstrüzyondur. Tipik ekstruzyon işleminden sonra eriyik özel boru/profil kalibrelerinden basınçla geçirilerek boru formunun ana hatları belirlenir.
Başlangıçtaki bu boru profil derhal bir vakumlama ünitesine alınarak hedef boyutlandırma işlemine sokulur.
Burada çeper kalınlığı, iç çap değeri, sızdırmazlığı gibi temel özellikleri biçimlendirilir. Boru, profil yumuşama sıcaklığındadır ve bu üniteden sonra soğutma havuzuna aktarılarak, ısının suya transfer edilmesi sağlanır. Basınçla ekstruderden çıkan profilin hat boyunca ilerlemesi paletli çekici ünitesiyle sağlanır. Caterpiller çekici olarak da tanımlanan bu ünitenin boru, profili ezmeyecek basınçla tutması için aşağıya-yukarıya serbest hareketli olması gerekir. Bu hareket pnömatik, elektrik motorlu ya da pek tercih edilmeyen manuel kontrollü olabilir. Çekici ünitenin çalışma hızı tamamen ekstruder üretim hızı ile senkron olmalıdır. Bu üniteden de geçen boru, profil arzu edildiği takdirde üzerine iz baskı yada mürekkep ile marka, üretim tarihi, seri numarası, teknik ölçü değerleri gibi yazıların yazılabileceği opsiyonel bir üniteden de geçtikten sonra, dilimlemeye alınır.

Tel Kaplama Üretim Hatları
Tel kaplama genellikle, çapraz kafa ekstrüzyon işleminin gerçekleştirildiği tek vidalı ekstrüderlerin kullanılmasıyla yapılır. Prosesin en temel ögesi, kaplama işinin yapıldığı kalıptır. Tipik ekstrzyon işi ile elde edilen polimerik eriyik, kalıp merkezinden geçirilen tel üzerine sürekli aynı basınç ve sıcaklıkla tatbik edilmesiyle, telin sarıp sarmalanması ile temel süreç gerçekleştirilir. Genellikle tel kaplama üretim hatlarında ekstruder ile hat yönü arasında 90° açı vardır. Tel kaplama üretim süreci, hattı beslemek için sarılı tel makaralarının çözümü ve telin kalıp merkezinden geçirilmesi ile başlar.
Gerilimin süreç boyunca ayarlanması için ön gerdirme istasyonuna kadar tel ilerletilir. Kaplama işinin sağlıklı olabilmesi için telin hazırlanması bunun için de ön ısıtmanın yapılması gerekir. Çapraz kafa kalıp istasyonunda üzerine sıcak
polimerik eriyik sarılan tel soğutma havuzundan geçirilir. Telin kaplanmasında herhangi bir zayıflama yada çapta büyüme olmaması için tel gerginliğinin stabil olarak sürekli aynı olması büyük önem taşımaktadır. Bunun için çekme ünitesinin ekstruder ve tel çözücü makaranın senkronizasyonu gereklidir. Soğutma ve çekme ünitelerinden geçen tel, sarma makaralarına alınarak, istenilen metrajlar doluncaya kadar sarılır. Tel kaplama uygulamalarında kullanılan Tipik Polimerler Kablo kılıfı uygulamalarında çapraz kafa ekstrüzyon prosesinde kullanılan polimerlerler çeşitlilik gösterir. Ancak bu polimerlerin, bu amaç için ideal kılan, esneklik, elektriksel direnç, kötü ortam şartlarına mukavemet, dayanıklılık gibi belirgin özelliklere sahip olması gerekir. PE, PVC, PA, PBT, EVA, PP sıklıkla tel kaplama işinde kullanılan polimerlerdir. Bunlardan başka, termoplastik elastomerler, etilen propilen kopolimerleri

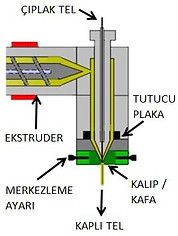
Sürüm / Hot Melt (Sıcak Eriyik)
Nemli iklimlerde yetersiz kalan su bazlı yapıştırıcılara alternatif olarak 1940'larda sıcak tutkal geliştirilmiştir. Bu gün ambalajlama ve paketlemede, tek taraflı, çift taraflı, maskeleme gibi bir çok çeşitle,
bir çok uygulama sahasına hitaben bant üretiminde sıklıkla kullanılmaktadır. Sıcak
eriyik veya sıcak tutkal özünde, erimiş halde sıvı olarak uygulanan ancak
soğudukça tekrar katılaşan termoplastik polimerlerden oluşur. Uygun maliyetli,
kolay kullanımlı, uygulama kullanım sahaları için formül çeşitliliği, saklama
kolaylığı, hepsinden önemlisi yapışma kalitesi bakımından fayda ve özelliklere sahiptir. Çok farklı türlerinden bazıları:
EVA'lı olanlar :
Hem ambalajlama hem de montaj formülleri için uygundur. -20 ile 180 °C arası standart sıcak eriyik sıcaklıklarında ekonomik ve etkilidir. EVA, en yaygın sıcak eriyik tipidir ve paketleme ve ürün montajı gibi uygulamalarda kullanılır.
PA'lı olanlar :
Aşırı sıcaklık ve kimyasallara -80 ila 270 °C arasında daha iyi bir direnç oluşturmak için yapıştırıcıları formüle etmek için kullanılır.
Poliamid'li olanlar :
EVA ürünleri gibi ancak daha yüksek ısı direnci ihtiyacı olduğunda kullanılır.
PP'li olanlar :
Sprey formülasyonlarında sıklıkla, -22 ile 230 °C arasında etkili olan gecikmeli ayar süresi gibi spesifik yapıştırma özellikleri yaratmak için kullanılır.
Poliüretan (PUR) olanlar :
Yüksek kimyasal direç için kullanılır.
PUR, katılaşmasından sonra küçük miktarlarda nem emer. Nem alımı birkaç gün sonra kalıcı bir kimyasal değişim yaratır. Bu kimyasal değişim, yapışkanın hem ısı hem de kimyasal direncini artırır. Kimyasal reaksiyon, PUR'nin epoksilere benzer bir yapı bağı oluşturmasına izin verir. PUR çok sayıda uygulama için mükemmeldir, ancak ağaç işlerinde yaygın olarak tercih edilir.
Sıcaklığa duyarlı doğası nedeniyle, sıcak eriyik yapıştırıcılar genellikle yüksek sıcaklıklı ortamlarda veya ısıya duyarlı alt tabakalarda kullanılmak için uygun değildir. Sıcak eriyik yapıştırıcıların üretiminde kullanılan yaygın polimerler arasında, poliüretan reaktif, stiren-izopren-stiren ve stiren-bütadien-stiren bulunmaktadır, ancak bu polimerler tipik olarak yapıştırıcının kendisi olarak değil, yapıştırıcının taşıyıcısı görevi görür.
Sıcak eriyik yapıştırıcılar genellikle bir tutkal tabancası veya tamburlu boşaltıcı gibi bir dağıtma aleti veya aplikatörü gerektirir. Normalde, esneklik ve mukavemet gibi bazı özellikleri geliştirmek için balmumları, plastikleştiriciler ve diğer malzemeler karışıma eklenir. Bant üretiminde taşıyıcı film olarak genellikle BOPP film tercih edilmektedir.Uygulama esasında ayrıca sarmal katların rahat açılması için bir de Release Katman oluşturulmak zorundadır. Bu katman bir solüsyon şeklinde olabileceği gibi, yağlı, mumlu kağıt da olabilir.
Hot Melt bantların Akrilik olanlardan ayıran en temel özelliklerden biri de en az üç katmanlı olmalarıdır.
BOPP (Biaxially Oriented Polypropylene) Çift Yönlü Polipropilen filmleri, PP filminin hem makine, hem de makine yönüne dik gergilenmesi ile üretilir. Bu sayede geliştirilmiş sertlik, yüksek çekme mukavemeti, mükemmel optik özellik ve iyi su buharı bariyeri sağlama nitelikleri kazanılmış olur.
BOPP filmleri 15 ile 50 mikron arasında değişir ve en yaygın olarak 15 ila 30 mikron arasında tercih edilir. BOPP filmleri tek tabakalı veya co-ex yapılar olabilir. Ek olarak, film niteliğini daha da arttırmak için, akrilik ve PVDC kaplama uygulanabilir. Oluşturulan bu kompozit filmlerde çoğunlukla homopolimer PP ve rasgele kopolimer PP kullanır. Sürüm hatları, çoğunlukla cast film üretim hattı BOPP üretimi sonrası, ya doğrudan ikinci kademe, ya da flekso baskı sonrası üçüncü kademe üretim hatlarıdır. Ve buradan çıkan ürünler, daha çok ambalaj ve paketleme bantları için, dilimlemeye gidecek yarı mamül / yarı form niteliğinde ürünlerdir.

Sürüm için oluşturulan hot melt eriyiğin ana bileşenini, HIKOREZ A-1100 gibi Alifatik Hidrokarbon reçine, KRATON D-1161 gibi stiren ve izopren bazlı, %15'lik bir polistiren içeriğine sahip açık, doğrusal bir triblock kopolimerler oluşturur. Karakteristik özelliği. sakız reçinesinden türetilmiş MEGARA gibi gliserol esterlerden sağlanır. Ayrıca, parafinik proses yağları, renklendirici pigmentler mevcuttur. Release katmanı, çözücü ve taşıyıcı ajanların başında Tolien ve RELEASE PP-100 gibi sentetik ayırıcı polimerler içerir.
Yapışkan bant ailesi yukarıdaki gibidir. Akrilik bantlar sıcak eriyik kapıştırıcılar kadar çabuk bağlanmazlar. İyi bir başlangıç yapışma özelliği vardır, ancak azami yapışma gücü elde etmek için yaklaşık bir günlük kademeli yapışma birikim süreci gerekir. Ancak daha iyi ısı, UV ve kesme dirancine sahiptir. Bu nedenle bu tip bantlar daha uzun süreli paketlemeler için tavsiye edilir.

