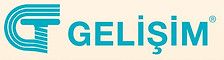


Hidrokarbonlar
Hidrojen ve karbon olmak üzere iki elementten oluşan organik bir bileşiktir. Petrol bileşiminin büyük bir kısmı değişen uzunluklardaki hidrokarbonlardan oluşur.
En küçük hidrokarbon metan, tek bir karbon atomu ve dört hidrojen atomundan oluşur. Bununla birlikte, hidrokarbonlar, zincirler, daireler ve diğer karmaşık şekiller dahil olmak üzere birçok yönden birbirine bağlanmış yüzlerce veya binlerce bireysel atomdan oluşabilir.
Hidrokarbonların özelliklerini sınıflandırmak için birkaç temel türe ayrılırlar.
Alkanlar: Bunlar doymuş hidrokarbonlar olarak adlandırılır. Yani sadece tüm karbon atomları arasında tek bağlar içerirler. Alkanlar, petrol yakıtlarının temelidir ve doğrusal ve dallı formlarda bulunurlar.
Doymamış Hidrokarbonlar: Karbon atomları arasında bir veya daha fazla çift bağa sahip olan hidrokarbonlara alken denir.
Sikloalkanlar: Bir veya daha fazla halka yapısı içeren herhangi bir hidrokarbon.
Aromatik Hidrokarbonlar: Areneler olarak da adlandırılan aromatik hidrokarbonlar, karbon atomlarının birbirini izleyen çift ve tek bağlarla bağlandığı benzersiz bir karbon molekülleri sınıfıdır. Bu molekül sınıfı, karbon atomları arasındaki bağların tek ve çift bağlar arasında bir ara bağ olduğu özel halka yapılarına sahiptir.
Bu sınıftaki moleküller, endüstriyel çözücü «benzen» içerir.
Benzen (C6H6): Diğer hidrokarbonlar gibi benzen de petrolün doğal bir bileşenidir. Oda sıcaklığında renksiz, yanıcı, tatlı kokulu bir sıvıdır ve yüksek oktan sayısına sahip olduğu için çoğu benzin karışımının bir bileşenidir.
Benzen de oldukça kanserojendir ve kemik iliği yetmezliği ve kemik kanserine neden olduğu iyi bilinmektedir. Elbette, “hoş aroması” nedeniyle tıraş sonrası ve diğer kozmetiklerde bir katkı maddesi olarak kullanıldığında kanserojenliği iyi bilinmemektedir.
En büyük benzen kullanımı (% 50), stiren ve polistren plastiklerinin ürünüdür. Ayrıca Naylon üretiminde önemli olan sikloheksan olarak bilinen bir moleküle dönüştürülür. Siklohekzan üretmek için benzenin yaklaşık% 15'i kullanılır. Böcek ilaçlarından kauçuğa kadar her şeyde daha küçük miktarlar kullanılır.
Benzen yapısı iki şekilde çizilebilir. İlkinde, çift bağ karakteri açıkça çizilir. Kısa elli versiyonda, yapıyı göstermek için halkanın içine bir daire çizilir. Benzen içindeki her bir karbon atomuna bağlı tek bir hidrojen vardır.
Aşağıdaki I. ve II. çizimleri eştir. Pratikte III. çizim kullanılır.
Benzen, renksiz, alevlenebilen, kaynama noktası 80,1 °C, erime noktası 5,5 °C olan bir sıvıdır.
Binükleer Aromatik Hidrokarbonlar: Molekülünde iki benzen halkası içeren bileşiklerdir.
Hidrokarbonlar
Hidrojen ve karbon olmak üzere iki elementten oluşan organik bir bileşiktir. Petrol bileşiminin büyük bir kısmı değişen uzunluklardaki hidrokarbonlardan oluşur.
En küçük hidrokarbon metan, tek bir karbon atomu ve dört hidrojen atomundan oluşur. Bununla birlikte, hidrokarbonlar, zincirler, daireler ve diğer karmaşık şekiller dahil olmak üzere birçok yönden birbirine bağlanmış yüzlerce veya binlerce bireysel atomdan oluşabilir.
Hidrokarbonların özelliklerini sınıflandırmak için birkaç temel türe ayrılırlar.
Alkanlar: Bunlar doymuş hidrokarbonlar olarak adlandırılır. Yani sadece tüm karbon atomları arasında tek bağlar içerirler. Alkanlar, petrol yakıtlarının temelidir ve doğrusal ve dallı formlarda bulunurlar.
Doymamış Hidrokarbonlar: Karbon atomları arasında bir veya daha fazla çift bağa sahip olan hidrokarbonlara alken denir.
Sikloalkanlar: Bir veya daha fazla halka yapısı içeren herhangi bir hidrokarbon.
Aromatik Hidrokarbonlar: Areneler olarak da adlandırılan aromatik hidrokarbonlar, karbon atomlarının birbirini izleyen çift ve tek bağlarla bağlandığı benzersiz bir karbon molekülleri sınıfıdır. Bu molekül sınıfı, karbon atomları arasındaki bağların tek ve çift bağlar arasında bir ara bağ olduğu özel halka yapılarına sahiptir.
Bu sınıftaki moleküller, endüstriyel çözücü «benzen» içerir.
Benzen (C6H6): Diğer hidrokarbonlar gibi benzen de petrolün doğal bir bileşenidir. Oda sıcaklığında renksiz, yanıcı, tatlı kokulu bir sıvıdır ve yüksek oktan sayısına sahip olduğu için çoğu benzin karışımının bir bileşenidir.
Benzen de oldukça kanserojendir ve kemik iliği yetmezliği ve kemik kanserine neden olduğu iyi bilinmektedir. Elbette, “hoş aroması” nedeniyle tıraş sonrası ve diğer kozmetiklerde bir katkı maddesi olarak kullanıldığında kanserojenliği iyi bilinmemektedir.
En büyük benzen kullanımı (% 50), stiren ve polistren plastiklerinin ürünüdür. Ayrıca Naylon üretiminde önemli olan sikloheksan olarak bilinen bir moleküle dönüştürülür. Siklohekzan üretmek için benzenin yaklaşık% 15'i kullanılır. Böcek ilaçlarından kauçuğa kadar her şeyde daha küçük miktarlar kullanılır.
Benzen yapısı iki şekilde çizilebilir. İlkinde, çift bağ karakteri açıkça çizilir. Kısa elli versiyonda, yapıyı göstermek için halkanın içine bir daire çizilir. Benzen içindeki her bir karbon atomuna bağlı tek bir hidrojen vardır.
Aşağıdaki I. ve II. çizimleri eştir. Pratikte III. çizim kullanılır.
Benzen, renksiz, alevlenebilen, kaynama noktası 80,1 °C, erime noktası 5,5 °C olan bir sıvıdır.
Binükleer Aromatik Hidrokarbonlar: Molekülünde iki benzen halkası içeren bileşiklerdir.
Hakkında
Kyäni, faydalı bileşenlerden oluşan besin takviyesi ürünlerini; benzersiz iş fırsatıyla birlikte dünya çapında 50'den fazla ülkeye ulaştırmaktadır. İdeal sağlığımızı korumak için günlük olarak Kyäni ürünlerini kullanırız, bu ürünleri başkalarıyla paylaşırız, işimizi inşa etmek ve sürdürmek için neredeyse her gün belirli bir saatimizi işe adarız ve başkalarını da Kyäni fırsatına dahil ederek veya Potato Pak ve Caring Hands programlarına katkı sağlayarak başarımızı başkalarıyla paylaşırız.
Hakkında
Kyäni, faydalı bileşenlerden oluşan besin takviyesi ürünlerini; benzersiz iş fırsatıyla birlikte dünya çapında 50'den fazla ülkeye ulaştırmaktadır. İdeal sağlığımızı korumak için günlük olarak Kyäni ürünlerini kullanırız, bu ürünleri başkalarıyla paylaşırız, işimizi inşa etmek ve sürdürmek için neredeyse her gün belirli bir saatimizi işe adarız ve başkalarını da Kyäni fırsatına dahil ederek veya Potato Pak ve Caring Hands programlarına katkı sağlayarak başarımızı başkalarıyla paylaşırız.
Sayfa Yapım Aşamasındadır.
Sayfa Yapım Aşamasındadır.
Eğitim / Bilgi / Çözüm Platformu
Enjeksiyon Kalıplama

VİDA / KOVAN
ANA MOTOR
ISITICI / REZİSTANSLAR
POLİMER (ERİYİK)
KALIP SOĞUTMA HATLARI
HAREKETLİ PLAKA
SABİT PLAKALAR
KİLİTLEME MOTORU
BESLEME / DOZAJLAMA
RAM VİDA MOTORU
POLİMER (GRANUL)
KİLİTLEME ÜNİTESİ
KALIP
ENJEKSİYON ÜNİTESİ
Erimiş polimerin yüksek basınç altında bir kalıp boşluğuna açık bir kanal (yolluk) boyunca zorlandığı ve polimerik eriğin kalıp formunu almasının sağlandığı işleme tekniğidir. Enjeksiyon kalıplama makinesi ile ekstruderler çok benzerlik gösterir. İki makine arasındaki ana fark vidalama işlem sürecidir. Ekstrüder vidada sürekli ileri yönlü basınç vardır. Enjeksiyon kalıplama makinesinin vidası, sadece ileri yönlü basınç değil, aynı zamanda kalıplama döngüsünün adımlarına göre geri hareket de yapar. Bu ileri geri hareketlilikten dolayı «pistonlu vida» olarak adlandırılır. Tutma Basıncı: Erimiş polimerik malzemenin kalıp içine enjekte edilmesi ve daha sonra bir kaç saniyelik kalıplama sürecinde (kalıp boyutuna, hammadde cinsine göre bu süreç değişiklik gösterir) geriye doğru çekilmesi ile, polimerik malzeme kalıp içinden geriye doğru akma eğilimi gösterir. Kalıp içinden dışarı doğru akmanın önüne geçmek yani eriği kalıp içine hapsetmek için bir süre daha basınç uygulamaya devam edilir. İşte bu tutma basıncı, «ütüleme basıncı» diye de tabir edilir ki bu, yanlıştır. Polimerik malzeme, soğutulan kalıp içinde katılaşana kadar tutulur, çevrim süresi tamamlandıktan sonra kalıplar açılır ve kalıp formunu almış mamül / yarı mamül elde edilir. Enjeksiyon Kalıplamada yaygın olarak kullanılan termoplastikler PP, PC, ABS, N6 'dır. Enjeksiyon Kalıplama esas olarak Termoplastikler için kullanılır , ancak Elastomerler ve Termosetler de ekstrüde edilebilir.
Enjeksiyon Kalıplama ile; boru bağlantı parçaları, batarya gövdeleri, diş fırçası tabanları, şişe kapakları, tek kullanımlık jilet, çatal, kaşık, tabak, otomobil tamponları ve gösterge panoları, elektrikli alet muhafazası, televizyon kabinleri, elektrik anahtarları, oyuncak gibi çok çeşitli ürün yelpazesi oluşturulabilir. Bazı modifikasyonlarla termoset plastikler de işlenebilmektedir. Plastik malzeme, yüksek basınçla bir kalıp içine injekte edilir; kalıp, elde edilmek istenen şeklin negatifidir (tersidir).


Vidalı Enjeksiyon Kalıplama: En çok kullanılan tip, vidalı enjeksiyon makineleridir. Açma-kapama ünitesi, kalıp, enjeksiyon ünitesi, kontrol ünitesi olmak üzere dört temel üniteden oluşur. Huni biçimindeki depoya, granül halindeki plastik hammadde konur. Huninin alt kısmından, vidalı mil üzerine inen plastik granüller, helezonik vidalı milin dönüş hareketi ile enjeksiyon memesine doğru sürüklenir. Vidalı mil silindirinin dışında, çepeçevre bulunan ısıtıcılar, sürüklenen plastik hammaddeyi istenilen sıcaklığa getirir. Sıcaklık, plastik maddeyi eriterek, bal kıvamında akışkan durumuna sokar. Bal kıvamındaki plastik hammadde, enjeksiyon memesinden geçerek kapalı kalıp içerisindeki boşluğa enjekte edilir. Parça kalıptan soğutularak alınır.
Pistonlu Enjeksiyon Kalıplama: Küçük kapasiteli ve basit parçaların kalıplanmasında pistonlu enjeksiyon makineleri kullanılır. Pistonlu makineler malzemeninhomojen ısıtılmaması sebebiyle birkaç gram ağırlığındaki çok küçük parça üretimi dışında günümüzde pek kullanılmamaktadır. Pistonlu makine kullanılması halinde silindirde yaklaşık 10 dozajlık malzeme bulunur ve bu malzeme ısıtılarak eritilir.
Çalışma prensibi,
(1)kalıp kapatılır memeye yaklaştırılır (aynı anda erimiş malzeme sıkıştırılır),
(2) kalıba malzeme enjeksiyonu gerçekleştirilir (aynı anda sonraki dolgu için
özel besleme ayarı yapılır),
(3) da piston geri çekilir, dozaj ayarlı granüller silindire alınır, yolluk memeden
koparılır, kalıp açılır ve parça kalıptan itilir şeklinde özetlenebilir.

Enjeksiyon Kalıplamada Temel Değişkenler
Temel değişkenler üzerinde dikkat edilecek konu başlıkları, Sıcaklık, Basınç, Çevrim Süreleri ve Hız olarak dört temel başlık altındadır.
Sıcaklık:
Malzeme sıcaklığı ve kalıp sıcaklığı olarak iki alt başlıkta toplanır.
Malzemenin sıcaklığı malzemenin cinsine uygun ve uniform olmalıdır. Meme ucundaki malzemenin sıcaklığı mutlaka bilinmelidir. Malzeme sıcaklığı, karışım tedarikçileri tarafından verilen sıcaklık aralığının tam ortasında olmalıdır. Eriyik sıcaklığını öğrenmenin en iyi yolu ise direkt olarak ölçmektir. Bu ölçümü yapmak için iki yöntem vardır.
1- Daldırma/çubuk pirometre ile çekirdek sıcaklıkları
2- Infra red pirometresi ile yüzey sıcaklığını ölçülür.Enjeksiyonda temel prensip, sıcak plastiği kalıp içine gönderip kalıp boşluğunun şeklini alarak bu şekilde kalıp soğuyup sertleşmesi ilkesine bağlıdır. Kalıp sıcaklığı, baskı süresini ve parça kalitesini etkilediğinden önemlidir. Sıcak kalıpta plastik çok kolay akmasına rağmen, baskının soğuyup dışarı atılma süresi uzayacaktır. Buna karşılık, soğuk kalıpta erimiş plastiğin soğuması çabuk olur fakat kalıp boşluğundaki akışkanlığı düşeceğinden kalıbı tam doldurmadan soğuyup sertleşir.
Bu iki durum arasında en iyi koşulları yakalamak için; kullanılacak plastiğin tipine ve çeşidine, plastiğin akma uzunluğuna, plastik parçanın et kalınlığına, kullanılacak yolluk çeşidine ve yolluk uzunluklarına ve istenilen parçanın kalitesine dikkat etmek gerekir. Kalıp dolma esnasında en sıcak erimiş plastik, kalıba girişinde ve en soğuk plastik yolluk girişinden en uzak noktadır. Kalıbın sıcaklığı iyi ayarlanamazsa bu sıcaklık farkı plastik parçada istenmeyen gerilmelerin, zayıf noktaların, malzeme birleşim izlerinin oluşmasına sebep olur. Bunları önlemek için baskıda eşit sıcaklık dağılımı sağlamak gerekir. Bu da kalıpta tasarlanacak en uygun soğutma sistemleri ile gerçekleştirilebilir. Kalıbın sıcak bölgelerine soğuk su, soğuk bölgelerine sıcak su girişi sağlayarak bu mümkündür.
Yavaş akan suyun laminer bir akışa sahip olduğu kabul edilir. Ancak kalıp soğutma çevriminin ve soğutmada türbilanslı akış tercih edilmelidir.
Re <10000 laminer akış
Re >10000 türbilanslı akış olarak ifade edilir.
Kalıp sıcaklığı da ideal olarak enjeksiyon malzeme sıcaklığı gibi plastik üreticileri tarafından verilen sıcaklıktır.
Laminer Akış:
Düzgün akım çizgileriyle belirtilen çok düzenli akış hareketine laminer akış denir. Düşük hızlarda yağ gibi yüksek viskoziteli akışkanların hareketi genellikle laminerdir. Yüksek derecede düzensiz akışkan hareketi genellikle yüksek hızlarda meydana gelir ve türbülanslı denen akış değişimleriyle belirtilir.

Basınç:
Plastik malzeme kalıp boşluğuna belirli bir basınçta enjekte edilir. Bu basınçla plastik malzemenin kalıp boşluğunun şeklini alması sağlanır. Basınç kaldırıldığında plastik hala akışkandır ve bir önceki geometrisine dönmek ister. Plastiğin çok kolay esneyebilme ve uzayabilme kabiliyetinden dolayı kalıp boşluğuna aşırı basınç uygulamalıyız ki malzeme sıcaklığı düştüğünde ve parçanın soğumasından dolayı pres çıkışında boşluklar oluşmasın. Kalıp plastikle dolduğu zaman bu seferde içinde sıkışan havayı dışarı atmak gerekecektir. Kalıp açıldığında ise dikkat edilmesi gereken iki husus vardır:
1- Parçanın kalıbın sabit tarafına (enjeksiyon tarafına) yapışmasını engellemek
2- İtici sistemi tarafından itilen parçayı ayırmak
Bazı kalıpçılar, kalıpların makinelere adapte olamadığını öne sürerler. Yani aynı kalıp ve plastik şartları sağlandığında, farklı makinelere bağlandığında aynı performans elde edilemeyeceği söylenmektedir. Bu bir anlamda saçmadır. Malzeme işlem gördüğü makinenin kimliğini okuyamaz. Yani eğer şartlar aynı ise sonuçta aynı olmalıdır. Bununla beraber bazı farklılıklar vardır. Yapılan ilk hata hidrolik pres başında, basıncı okuyan operatör tarafından, plastiğin üzerindeki basınç yüzünden hata olduğu düşünülür. Hidrolik pres işi, kuvvet katlayıcı denen bir prensiple çalışır. Plastik işinde bu 8:1 ve 12:1 oranındadır. Bununla beraber, bir çok istisna vardır. Çok açıktır ki eğer bir pres 8:1 oranında çalışıyorsa plastiğin 1000 kg‟lık bir basıncı 8000 kg‟lık bir basınca eş değerdir. Aynı makinede kullanılan 12:1‟lik oran 12000 kg‟lık bir basınç oluşturacaktır. Basınçtaki bu fark makinenin hata sinyali vermesine neden olacaktır. Bu basınç oranlarına göre her makine kendi kuvvet katlayıcısına göre sınıflandırılmalı ve buna göre bir tablo yaparak makinenin bu verilere göre ayarlanması gerekmektedir.
Birçok makine bilgisayar kontrollüdür ve bilgi işlemcisi saniyenin 1000‟de bir
aralığında okuma yapmaktadır.
Bununla beraber makine imalatçıları saniyenin sadece 10‟da birinde devreye girebilen valf sistemleri kullanır.
Aradaki bu hassasiyet farkı tabii ki makinenin yavaşlamasına ve problem çıkarmasına sebep olmaktadır. Bu tip makinelerin valfleri de ona göre seçilmelidir. Böylece kontrolde ilerleme yapılmış olacaktır. Parmak kuralına göre, basınç malzemenin üzerine aynı uygulanılırsa, kalıpta aynı büyüklükler ve buna bağlı olarak da parçada aynı ölçüler elde edilir.
Enjeksiyon Basıncı:
Kalıp gözünü doldurmak için ekstruder tarafından kalıp içine uygulan basınç.
Tutma Basıncı: Plastik malzemedeki çekmeleri karşılamak ve eksiksiz olarak şeklini alması için uygulanır. Plastik malzeme kalıp içine enjekte edildikten ve kalıbı tam doldurduktan sonra ikinci fazda kalıptaki giriş noktasından geriye kaçmaya çalışır bu hareketi engellemek amacı ile enjeksiyon basıncı sonrasında tutma basıncı uygulanır. Yani plastik malzeme geri kaçmasın diye tutulur.
Geri Basınç:
Vida geri hareketine direnç olarak tanımlanmaktadır ve malzemenin sürtünme ile ısıtılmasına yardımcı olur. Vidanın geriye giderken mal alma fazında plastik üzerinde oluşturduğu basınçtır. Bu basınç, eğer boyar madde kullanılıyorsa karışımın en uygun seviyede olmasını sağlar. Gereğinden fazla basınç verilmesinde ise sürtünme ısısı nedeni ile malzemenin yapısını bozar.
Çevrim Süresi:
Bir çevrimin başından sonuna kadar tamamlanıldığı aralığa çevrim süresi/zamanı denir. Malzeme eriyik halinde iken kalıbın içini çok iyi doldurması istenir.
Malzeme soğumaya başladığında, yeteri kadar katı hale gelir ve bundan sonraki parça için enjeksiyon makinesi hazırlanmaya başlar. Malzemenin basitçe soğuması önemli değildir. Asıl önemli olan nasıl soğuduğudur. Burada anlatılmak istenileni bir değimle anlatmak istersek “Plastik katı hale gelmeden önce biraz kestirmesi gerekir.” Yani hemen soğutmakta plastik açısından optimal bir durum değildir. Düşük çevrim süreleri için minimum zamanlar kullanılmalıdır.
Doldurma süresi:
Sadece kalıp gözünün doldurulması için geçen süredir.
Tutma süresi:
Çekmeyi azaltmak için parça kalıp içinde tutma basıncı altında bekletilir. Parça çektikçe içeriye yeni eriyik dolması sağlanır. Tutma aşaması yolluk girişinin donmasına kadar devam eder. Daima aynı tutma sürelerinde çalışarak aynı ağırlıklardaki parçalar elde edilebilir.
Ütüleme süresi: Sadece kalıp gözündeki malzemenin sıkıştırılması için gerekli süredir.
Soğutma Süresi:
Parçanın kalıbın içinde yeterli rijitliğe ve soğukluğa sahip oluncaya kadar geçen süredir .
Kalıp Açık Kalma Süresi:
Minimum olmalıdır ve değişmemelidir. Kalıp açık kalma süresi, kalıbın açılması, iticilerin vurması ile parçanın çıkarılması ve kalıbın kapatılma süresinden oluşur.
Hız:
Kalıp gözünü doldurma hızına enjeksiyon hızı denir. Yüksek enjeksiyon hızı kalıp gözünün düşük viskozite ve iyi eritilmiş malzeme ile doldurulmasını sağlar. Küçük yolluk girişleri, yüksek enjeksiyon hızı ile parça da mekanik ve kozmetik hatalar oluşabilir
Sıcaklık, basınç, çevrim süresi ve hız, bu dört değişkenin kullanım sırasında
genellikle hızın birincil derecede değişken olduğunu görülmektedir. Doldurma hızı direkt olarak ergiyin viskozitesine bağlıdır. Bu da istenilen doldurma basıncına bağlıdır. Hızdaki ufak değişiklikler makinenin kalıp boşluğunu doldurma kabiliyetini dramatik bir şekilde etkiler.
Malzemenin viskozitesi bu hıza bağlıdır; büyük bir ihtimalle en kritik ve değiştirilmesi diğerlerine etkisi en az olan değişkendir. Basınç kullanılması gereken ikinci değişkendir. Prosesin genelinde yapacağı az bir etkiyle çok kısa bir zaman periyodu içinde adapte edilebilir. Çevrim zamanındaki değişiklik malzemenin ergime sıcaklığına hemen yansır. Sıcaklıkta yapılan değişiklikler, kolayca viskoziteyi değiştirir. Buda basıncı ve hıza etki eder. Isı ayarlanması gereken en zor değişkendir. Çünkü plastiğe ısı vermek kolaydır ama aynı zamanda ondan ısıyı almak çok zordur.
Plastik işleme tekniklerinden enjeksiyon kalıplama, 7 temel çevrime sahiptir.
(1) Plastikleştirme: Plastik hammaddenin eritilmesi, kalıba enjekte edilmeye hazır hale getirilmesi işi. Önce ocağa granül hammadde alınır, ısıtıcılar ve vida sürtünmesi ile hammadde eritilir, eriyen plastik önde vida boşluğuna ulaştırılır.
(2) Kalıbın Kapatılması: Makinenin mengene ünitesi ile kalıbın iki parçasını birbiri üzerine kapatılır ve yüksek basınç uygulanır. İki kalıp plakası (erkek kalıp ve dişi kalıp) arasında kalan kalıp boşluğunun oluşması sağlanır ve uygulanan yüksek basınç ve hızlara karşı kalıbın açılması, gevşemesi engellenir.
(3) Kalıbın Doldurulması: Önce vida hidrolik piston tarafından ileri itilir. eriyik plastik kalıp boşluğuna doldurulur.
(4) Basınç Tatbiki: Basınç yükseltilir. Kalıbın tam olarak dolması, ince detayların da oluşması için sağlanır.
(5) Tutma: Çekmeyi azaltmak için parça kalıp içinde basınç altında bekletilir. Parça çektikçe içeriye yeni eriyik dolması sağlanır. Tutma aşaması yolluk girişinin donmasına kadar devam eder.
(6) Soğutma: Yolluk donduktan sonra parça kalıp içinde soğur ve çeker. Parçanın soğuyup yumuşama sıcaklığına ulaşıncaya kadar sürece devam edilir.
(7) Kalıptan Çıkarma: Parça itici sistemi yardımı ile kalıptan dışarı çıkarılır.
Görülebileceği gibi yedi temel çevrimin plastikleşme harici altısı kalıp ünitesi üzerinde gerçekleşmektedir.
Enjeksiyon Parametrelerinden Bazıları


Enjeksiyon Kalıplamada Kalıp Elemanları
Enjeksiyon kalıbı, enjeksiyon basıncına karşı koyabilecek nitelikte karmaşık olabilecek bir çok üniteden meydana gelmiştir.
Her şeyden önce kalıplar, «dişi» ve «erkek» olarak iki üniteden oluşmaktadır. Her iki ünite üzerinde çeşitli elemanlar mevcuttur:
Dişi Çekirdek:
Parça geometrisinin işlendiği, genelde yolluk girişinin bulunduğu kalıbın en parlak çeliğidir.
Erkek Çekirdek:
Parça geometrisinin işlendiği, dişi kalıpla kalıp boşluğunu oluşturan, iticilerin ve hareketli diğer elemanların çalıştığı çelik.
Dişi Hamil:
Dişi çekirdeğin etrafındaki ana taşıyıcı çelik.
Erkek Hamil:
Erkek çekirdeğin etrafındaki ana taşıyıcı çelik.
Merkezleme Flanşı:
Kalıbı enjeksiyon makinesi plakasına merkezler.
Merkezleme Milleri:
Kalıbın dişi ve erkek plakalarını merkezleyen millerdir.
Yolluk Burcu:
Enejksiyon makinesinin vidasından kalıp ayrılma hattına eriyik malzemeyi taşır.
Dişi Bağlantı Plakası:
Kalıbın enjeksiyon makinesine bağlanmasını sağlar.
İzolasyon Plakası:
Isı kayıplarını azaltarak kalıbın ısı dengesine yardımcı olur, maliyet kazancı sağlar.
Soğutma Kanalları:
Hamilde ve tercihen çekirdekte yer alan su yolları.
Destek Plakası:
Erkek hamil plakasının yüksek basınçlara dayanabilmesi için destekyen ünite.
İtici Destek Plakası:
Parçayı çıkaran iticilerin bağlandığı, pimlerinin ileri doğru hareketiyle, itici hareketini sağlayan plakalar.
Paraleller:
İtici plakasının hareketi için yeterli boşluğu sağlar.
Destek Sütunu:
Destek plakasının eğilmesini engeller, uygulanan basınçlara karşı dayanım sağlar.
İtici Yataklama Milleri:
İtici plakasının eksenel yönde salınım hareketi yaparak kalıba/parçaya zarar vermesini engeller.
İtici Yataklama Mil Burcu:
İticilerin sadece istenilen eksende hareket etmelerini sağlarlar.
Geri Döndürücü:
Kalıp kapanırken itici plakasını geri döndürür.
O-Ring:
Soğutma kanallarından soğutma sıvısının sızıntı yapmasını engeller.
Şaşırtıcı:
Soğutma kanallarında dolaşan sıvıya yön vermek için kullanılır.
Tıkaç:
Su devresi oluşturmak için belirli kanalların sonlarını tıkamak için tanımlanan parçalar.
Enjeksiyon Kalıplamada Kapama Kilitleme Sistemleri
Enjeksiyon işleminin sürekli bir işlem olmaması, kalıbın ürünün çıkması için açılmasını ve sonraki baskı için tekrar kapanmasını gerektirmektedir. Kapama/Kilitleme sistemleri (Mengene ünitesi) bu işlemi gerçekleştirir. Plastiğin çok yüksek basınçlarda kalıba enjekte edilmesi sebebiyle mengene ünitesi kalıbı, enjeksiyon ve tutma basınçları safhasında sıkıca kapalı tutmalı(kilitlemeli), kalıbın açılıp çapak yapmasını önlemelidir. Bu ünitenin görevi, kalıbı kapamak ve açmak, kalıbın yüksek basınçta kapalı kalmasını sağlayarak kalıp ayrılma hattında çapak oluşmasına izin vermemektir. Hidrolik, hidromekanik ve mekanik kapama kilitleme sistemli olarak üç türde olabilmektedir.
(1) Hidrolik kapama/kilitleme
Sistemi hidrolik kuvvet uygulaması ile çalışır.
Hidrolik piston makinenin hareketli tarafındadır. Plakanın ileri hareketi ve uygulanan kuvvet, kapama silindirindeki sıvıya uygulanan yük basıncıyla kontrol edilir. Plakanın hareket hızı genellikle, sıvının giriş ve çıkış hızlarının oranıyla kontrol edilir. Yüksek tonajlı enjeksiyon kalıplama makinelerinde hidrolik kelepçeler kullanılır.
Tipik olarak 1.300 ila 8.900 kilonewton arasındadır (150 ve 1,000 ton). Üniteler, strok sırasında belirli pozisyonlarda tonajın ayarlanması ile ilgili olarak tokalı kelepçelerden daha esnektir.
(2) Hidromekanik kapama/kilitleme
Hidrolik hareketlendirici, silindir kelebek sistemini ve bağlantılarının hareketini kontrol eder, bu şekilde hareketli plakanın açılıp kapanmasını sağlar. Kilitleme kuvveti, mekanik olarak kelebek sisteminin açılmasıyla sağlanır. Dizayndaki bağlantılar sebebiyle mekanik olarak avantaj sağlanır. Bu da hidrolik olarak uygulanan kuvvetin 1\20‟sinin katlanmasıyla olur. Kilitleme gücü kilitleme yüksekliğinin ayarıyla yapılabilir. Bu da kilitleme vidasındaki bağlantılarının ileri geri çevrilmesiyle sağlanır. Kilitleme tonajı, kolonlardaki uzamalardan hesaplanır. 8,900 kilonewton (1.000 ton) üzerinde büyük tonajlar için tasarlanan hidromekanik kelepçeler, kalıbı kapanış pozisyonuna doğru hızla hareket ettirmek için hidrolik silindirleri kullanır. Kapalı pozisyonun sürekliliğini mekanik kilitlemeler sağlar.
(3) Mekanik kapama/kilitleme
Gnellikle düşük tonajlı makineler için en uygun olanlardır. Elektrik motorları tarafından tahrik edilen hidrolik silindirler veya bilyalı vidalar üzerine çalışma prensibi vardır. Mekanik basıncı sağlayan geçiş kelepçelerinin çok çeşitli tasarımları olabilir. Temelde kafayı ileriye doğru hareket ettiren, mafsallı bağlantılı, makas tekniği ile işleyen hareketli ekipmanları vardır. Ve tüm ekipmanlar ana hareket ettiriciye bağlıdır.Mekanik mafsallı kelepçelerle, ihtiyaç olduğu takdirde çevrimdeki farklı noktalarda hız ve kuvvetin (basıncın) değiştirilmesine olanak sağlar.
Enjeksiyon Kalıplamada Kalıp Sistemleri
Vida Mekanizmalı Kalıplar:
Silindirik iç ve dış yüzeyinde helisel kanalları olan parçalar için özel kalıp dizaynı gereklidir. Vida parçada çıkıntı şeklinde olabilir, bu dizaynı daha da karmaşık hale getirir.
Bu karışıklar;
(1) Vidanın harici dişli, dahili dişli, kesintili veya kesintisiz olması,
(2) Baskıyla veya parça içine sokulan metal parça kullanımıyla vida oluşumu,
(3) İstenen dişli formu baskının kalıptan sıyrılarak çıkmasına müsaade etmesi veya etmemesi şeklinde olabilir. Bu tip kalıpta parçanın kalıptan çıkması için erkek veya dişi kalıbın dönmesi düşünülür. Bu dönme hareketini sağlamak için kalıbın hareketli tarafına dönme hareketini sağlayacak sistem yerleştirilir.
Bunu gerçekleştirecek değişik mekanizmalar kullanılabilir.
(1) Ekseni yönünde sabitli dizayn, vidalı erkek parçayı çıkarmak için az döner.
(2) İtici plakalı dizayn; itici hareket ederken vidalı erkek de döner.
(3) Dönerek çekilen erkek dizayn, dönme hareketine ek olarak erkek plakaya doğru erkeğin çekilmesi ile çalışır ve parça boşta kalır.
(4) Dönen dişli plaka dizaynı, Bu tür kalıpları çalıştırmak için çeşitli hidrolik-pnömatik, elektrik güç kaynakları kullanılır.
Güç sistemleri olarak dişli sistem, zincir ve zincir dişlisi, dişli çubuk ve ufak dişli, kramayer kullanılır. Ekseni yönünde takılmış dönen erkek vidalı döndürüldüğü zaman parça dışarı atılır. Kalıp boşluğu sabit kalır. Baskının dış yüzeyi öyle olmalıdır ki erkeğin dönmesi esnasında parça erkekle birlikte dönmemelidir. Düz dış yüzeyli silindirik parçalar bu sisteme uygun değildir. Çünkü baskının kalıp bağlantısı soğuyup çekmeyle kalktığı için parçanın kalıp boşluğunda dönme eğilimi vardır. Erkeğin vidalı bölümünün uzunluğu idealde kalıp boşluğundan biraz az olmalıdır. Eğer vidalı bölüm kalıp boşluğunun derinliğine göre oldukça kısa ise, vida sökümü tamamlandıktan sonra parçanın kalıptan atılmasını sağlamak için vida merkezine takılmış itici pimi gerekecektir.
İki Plakalı Kalıplar:
Kalıp endüstrisinde en çok kullanılan enjeksiyon kalıbıdır. Kısaca erkek ve dişi kalıptan oluşur. Bu iki kalıp parçasının birleştiği yüzeye kalıp ayırım çizgisi denir. En ucuz ve kolay dizayn edilebilen ve kullanıcıya kolaylık sağlayan kalıplar oldukları için tercih edilmektedir. Kalıp boşlukları bir plaka üzerine monte edilir ve diğer plaka bu plaka üzerine kapanır. Merkezi bir dikey yolluk sabit bir plakaya işlenir. Hareketli kısım, gereken kapama kuvvetini sağlar ve itici sistemlerini çalıştırır.

Üç Plakalı Kalıplar:
Çok gözlü kalıplar için tasarlanan bu tipte, ayrıca bir hareketli plaka daha bulunur. Kalıp üç ayrı plakadan oluşmuştur ve kalıp açıldığında bu üç plaka birbirinden ayrılır. Açıklığın biri, parçanın dışarı atılması için boşluk sağlarken, diğer açıklık, giriş yolluğunun dışarı atılması için boşluk sağlar. İki plakalı kalıba göre yapımı daha çok zaman alır ve maliyeti daha yüksektir. Merkezi veya eksenel kaçık yolluklar, bu tip dizaynda kullanılabilirler. Yolluksuz veya sıcak yolluklu kalıp teknolojisi üç plakalı kalıp kullanma eğilimini azaltmıştır. Sıcak yolluklu kalıplarla karşılaştırıldığında bazı avantajları bulunmaktadır.
(1) Kalıbın kullanılması esnasında malzemenin ve rengin kolayca değiştirilmesine olanak verir. Her baskıda yolluk sistemini temizleyerek, malzemede uzun süreli kirlenme olmadan hızlı renk değişimini sağlar.
(2) Güvenirlik; sıcak yolluk sistemlerinde ısı kontrolü, sistemin ısıtılması, elektrik kesintilerinde ve arızalarında bozulmalara sebep olur. Üç plakalıkalıp daha fazla mekanik parça ile çalıştırılır.
(3) Maliyet; Kalıp ısıtıcıları ve sıcaklık kontrol aletleri (thermocouple, rezistans) çok pahalıdır.

Maçalı Kalıplar:
Açılı hareketli kalıplar olarak da bilinmektedir. Parçanın kalıptan dışarı atılmasına engel olan bölümlerin (undercut) parça üzerinde oluşturulup, parçanın kalıbın açılma yönünde bir zorlamayla karşılaşmadan çıkması için kalıplarda maça sistemi kullanılır. Bu tip dizaynlarda, erkek kalıpta, pres tarafından hareket ettirilmesi mümkün olmayan kısımların hareketi amaçlanır. Kam millerinin veya açılı pimlerin kullanımıyla, kalıp elemanlarının ikincil bir hareket kazanması sağlanır. Bu ikincil hareket pnömatik veya hidrolik silindirler yardımıyla gerçekleştirilir.

Katlı Kalıplar:
İki gözlü yapıldığında kalıp boyutu çok büyük olacak olan kalıpların daha düşük tonajlı makinelerde çalışabilmesini sağlayan kalıplardır. Üretim adetleri yüksek olan parçalar için uygulanabilmektedir. İki ayrı kalıp yapılarak da bu adetler sağlanabilir fakat parça maliyeti yükselecektir ve iki ayrı enjeksiyon makinesi ayrılarak çalışacağından makine kapasitesini olumsuz yönde
etkileyecektir. Yoluk ikinci göze kadar uzanır ve ikinci göz dolduktan sonra ilk gözü doldurur, kalıp plakaları ayrıldığında, ortadaki plaka (dişi plaka) iki erkek plakadan ayrılır ve ikinci erkek kalıptaki mekanik itici plakası yardımıyla ilk parça, ilk erkek kalıptaki hidrolik iticilerin yardımıyla da ikinci parça kalıptan ayrılır. Kalıp maliyeti ile karşılaştırıldığında daha ekonomiktir. Parça maliyeti düşünüldüğünde de iki ayrı kalıptan elde edilecek parça maliyetinden daha düşüktür. Çünkü tek kalıptan tek çevrim süresinde iki adet parça elde edilecektir ve parça maliyetine etki eden makine saat ücreti, işçilik ve çevrim süresi ele alındığında daha ekonomiktir.

Ters Kalıplar:
Bazı uygulamalarda enjeksiyon makinesinin sabit tarafında erkek kalıp ve iticiler, hareketli tarafta ise dişi kalıp yerleşik dizayn olabilmektedir. Bu dizaynda , iticiler mekanik olarakhidrolik, pnömatik sistemler veya yaylar yardımıyla çalıştırılır. Bu uygulamalar, parça dizaynlarından kaynaklıdır. Genelde kozmetik ürün parçalarda uygulanabilen kalıplama sistemidir. Parçanın görünen yüzeyinde hiçbir iz istenmediğinde (yolluk izi, itici izi, çalışan maça izleri vs.), kalıbın erkek tarafından beslenmesi istenebilir. Bu durumda kalıbı ters olarak dizayn etme gereksinimi duyulur. Kalıp maliyetini arttıran ve prosesi zorlaştıran bir yöntem olup, özeldurumlarda haricinde uygulanmaz.

Sıcak Yolluklu Kalıplar:
İdeal bir enjeksiyon prosesinde, kalıplanan parçanın mümkün olduğunca üniform yoğunlukta, yolluklardan ve çapaklardan arındırılmış bir şekilde çıkması istenir. Bu sayede sağlanan malzeme tasarrufu azımsanamayacak düzeylerdedir. Sıcak yolluk sistemli kalıplarda, yolluk etrafına yerleştirilen elektrikli ısıtıcılar, yolluğun belli bir sıcaklıkta tutulmasını sağlayarak yollukların parçayla
çıkmasını önler ve malzeme tasarrufu sağlar. Bu tip kalıpların dizaynı daha karmaşık olduğundan daha pahalıdırlar ve ciddi tecrübe gerektirirler. Parça çıktıktan sonra çapakların ve yollukların temizlenmesi için gereken işçilik masrafları bu sistemde düşüktür. Sıcak yolluk sistemlerinin açık akış kanalı, dengeli malzeme akışı, değişmeyen bir ısıl denge, yeterli ısıtıcı güç kapasitesi, ısıl genleşmelere karşı gerekli önlemler, hızlı renk değişimi sağlama özellikleri vardır. Ayrıca, yolluk temizleme, kırma işçiliği olmamaısndan dolayı işçilikten tasarruf, açma mesafesinin kısa olmasından dolayı düçük çevrim süresi, malzemeden tasarruf, makine kapasitesinden tasarruf, yüksek parça kalitesi avantajlarına sahiptir.

Soğuk Yolluklu Kalıplar:
Soğuk yolluklar, genelde sıcak yollukların kullanıldığı parçalara göre daha küçük boyutlardaki parçalar için ve buna bağlı olarak göz sayısı 2 ve 2‟den fazla olan kalıplarda kullanılır. Parça için harcanan malzeme dışında hurda olacak olan yolluk kısmı için de malzeme gereklidir. Polimer enjeksiyon vidasının çıkış noktasına kadar ısıtılır ve kalıpla temas ettiği noktada soğumaya başlar ve soğuyarak dağılır. Yolluk yüzeyine temas eden polimer donarak kabuk oluşturur. Bu kabuk, erimiş plastiğin merkezinin sıcak kalmasını ve akmasını sağlar. Plastiğin soğuması çok hızlı olduğundan ve parçaya ulaşıncaya kadar akış kanallarında da sıcaklık ve basınç kaybı olur, bu yüzden akma mesafesi uzun olan parçalarda tercih edilmezler. Sıcak yolluklu kalıplarda bu sıcaklık ve basınç kaybı parçayı doldurmaya başladığında başlar.

Enjeksiyon Kalıplama Makine ve Türleri
Termoplastik malzemelerin enjeksiyon yöntemiyle kalıplanmasında kullanılan makinelerdir. Tüm enjeksiyon kalıplama makineleri iki parçadan oluşur. Bir enjeksiyon ünitesi ve bir sıkıştırma ünitesi. Farklı sanayi ürünleri için farklı teknolojilerde farklı makineler söz konusudur. Enjeksiyon ve sıkıştırma temel ünitelerinden başka; kontrol ünitesi, tahrik (hareket) sistemi, kalıp ve kalıp elemanları da bileşenlerdir.
Enjeksiyon Ünitesi:
Enjeksiyon grubunun ana amacı, plastik malzemeyi eritmek ve kalıba enjekte etmektir. Sürekli olarak aynı ağırlıkta ve aynı kalitede parça üretimi için kalıba enjekte edilen malzeme miktarı her seferinde aynı olmalıdır. Bunun için enjeksiyon grubu sürekli olarak aynı sıcaklıkta homojen malzeme baskısı yapabilmelidir. Plastik teknolojisinin ilk zamanlarında, piston tipi enjeksiyon makineleri kullanılıyordu. Bu makinelerde, plastik malzeme sadece kovandan aldığı ısı ile eritiliyordu. Günümüzde artık yaygın bir şekilde tercih edilen makinelerde ise enjeksiyon pistonu görevi de gören vidalar kullanılmaktadır. Bu makinelerde vida döner ve aynı anda huniden mal alır. Vidanın dönme hareketiyle ileri doğru itilen malzeme, aynı zamanda hem vidanın oluşturduğu sürtünme ısısı ve kovan (Kovana kimi zaman ocak da denilmektedir.) erir. Eriyerek ileri hareket eden plastik malzeme, meme boşluğuna depolanır. Vida, malzeme boşluğuna doluncaya kadar yani mal alma konumuna ulaşıncaya kadar geri döner. Geri hareket esnasında vidanın arkasında oluşan geri basınç, hidrolik pistonu belli değerde sabit tutar. Bu sayede vidanın geri dönme hızı azaltılarak daha homojen bir karışım elde edilir. Plastikasyon işlemi bitip meme boşluğu yeterince malzemeyle dolduktan sonra vida, bir piston gibi yüksek basınçla ileri doğru hareket ederek plastik malzemeyi meme boşluğundan kalıp içine enjekte eder.
Bir enjeksiyon ünitesinin ana görevleri:
1- Huniden kovana giren plastik malzemeyi ısıtıp eritmek
2- Eriyik malzemeyi kalıba enjekte etmek
3- Malzemenin kalıpta sağlam bir ürün haline gelmesi için gerekli tutma basınçlarını sağlamak
4- Rahatça ileri geri hareket edecek şekilde olmak
5- Memeyle yolluk burcunu gerekli kuvvetle temas halinde tutabilmektir.
Sıkıştırma/Mengene Ünitesi:
Enjeksiyon olayında sürekli bir işlem olmaması, kalıbın ürünün çıkması için açılması ve sonraki baskı için tekrar kapanması gerekmektedir. Mengene ünitesi bu işi yapar. Plastiğin çok yüksek basınçlarda kalıba enjekte edilmesi sebebiyle mengene ünitesi kalıbı enjeksiyon ve tutma basınçları safhasında sıkıca kapalı tutmalı, kalıbın açılıp çapak yapmasını önlemelidir.
Bir enjeksiyon makinesinde mengene ünitesinin başlıca görevleri şunlardır:
1- Kalıbı kapamak
2- Enjekte edilen malzemenin ürün hâline dönüşmesi için kalıbı kilitleyerek kapalı tutmak
3- Ürünün çıkarılması için kalıbı açmak
Kontrol Ünitesi:
Enjeksiyon makinesini bir bütün olarak tüm fonksiyonlarını takip ve belli bir sıraya göre koordine edebilecek, çalışma parametrelerini gözlemleyip sabit tutabilecek ve enjeksiyon çevriminin her safhasını kontrol edebilecek olan bir sisteme, yani kontrol sistemine ihtiyaç duyar. Çünkü bir enjeksiyon makinesindeki tüm fonksiyonlar her makinede olması gerektiği gibi belli bir sıraya göre gerçekleştirilmeli, her fonksiyonun başlama ve bitiş zamanları ve konumları kontrol altında tutulmalı ve takip edilmelidir.
Tam Hidrolik Enjeksiyon Makineleri:
Prosesle ilgili tüm hareketler (geri çekme, enjeksiyon, kalıp açma / kapama) hidrolik motorlar veya pistonlar aracılığıyla gerçekleştirilir. 1890'ların başlarına kadar, tamamen hidrolik enjeksiyon kalıplama makineleri piyasadaki tek makine tipiydi ve bugün dahi en çok tercih edilen seçenektir. Tam hidrolik plastik enjeksiyon kalıplama makinelerinin avantajları şunlardır:
-
Büyük hacimli parçaların, son derece karmaşık parçaların (otomotiv endüstrisi), mükemmel yüzeyli veya kalın duvarlı parçalara sahip yüksek teknoloji ürünü bileşenlerin üretimi için idealdir.
-
Çekirdek çekme ve valf kapılarını harekete geçirmek için tercih edilir
-
Fiyatları genellikle elektrikli modellerden daha düşüktür
-
Yedek parçaların rahatlıkla bulunabilmesi ve düşük maliyetleri sayesinde daha hızlı yatırım geri dönüşü
-
Daha iyi enjeksiyon oranları, hassas enjeksiyon ve yüksek seviyede proses stabilitesi
-
Hidrolik akümülatörler kullanılarak artırılabilir, çok ince duvarlı parçalar için daha yüksek bir enjeksiyon performansı
-
Olağanüstü sıkma kuvveti (55000 kN'ye kadar)
-
Hidrolik parçaların daha yüksek aşınma ve yıpranma direnci
-
Servo hidroliklerin sadece gerektiğinde çalışması nedeniyle enerji tasarrufu - makine parça üretmiyorsa, motorlar da boştadır ve enerji kullanmazlar
-
Az yer kaplayan büyük boyutlu makine olabilmeleri
Tam Elektrikli Enjeksiyon Makineleri:
Prosese ilişkin tüm hareketler (geri çekme, enjeksiyon, kalıp açma / kapama) elektrikli (servo) motorlar aracılığıyla gerçekleştirilir. Makine, maça çekme gibi hareketler için harici bir hidrolik güç paketi ile donatılmadığı sürece, bu tür makinelerde hiçbir hidrolik sistem kullanılmaz. Elektrik motorlarının kullanımı, sadece hareket gerektiğinde motorlar çalıştırıldığı için yüksek enerji verimli bir makineye izin verir. Ayrıca, yenilikçi enerji geri kazanım sistemi kinetik enerjiyi yakalar, depolar ve bu enerji makineye güç vermek için kullanılabilir.
1980 lerde küçük makineler olarak başlayan elektrikli enjeksiyon kalıplama makineleri tarihi, artık pazarın neredeyse yarısını kapsamakta. Ve mümkün olan her boyut aralığında ve uygulama alanına hitap edebilmekte.
Tüm elektrikli plastik enjeksiyon kalıplama makinelerinin avantajları:
-
Yüksek tekrarlanabilirlik ve hassasiyet - elektrik üniteleri dijital olarak kontrol edilir ve bu nedenle üretim süreci tahmin edilebilir ve konumlandırma hassasiyeti son derece yüksektir (± 0.0001 inç)
-
Enerji verimliliği çok yüksektir. Enerjinin sadece makine hareketlerinde kullanılmasıyla %30 ila %70 arasında enerji tasarrufu
-
Paralel hareket yapabilme özelliği sayesinde daha hızlı ve daha verimli işlem
-
Erken Start. Isınması gereken daha az bileşen ve sıvı (yağ) nedeniyle daha kısa başlatma süreleri
-
Genellikle daha sessiz çalışma (<65 dbA)
-
Temiz oda üretimi için ideal. Hidrolik sızıntıların olmaması ile tertemiz ortam
-
Üretim süresi boyunca maliyet tasarrufu - enerji tasarrufu, daha düşük yağ filtresi değişimi, daha az birim maliyet ve daha az malzeme maliyeti nedeniyle daha düşük işletme maliyetleri
-
Genellikle daha yüksek enjeksiyon hızları (800 mm / sn'ye kadar) ve daha hızlı kelepçe hareketi
Hibrit Enjeksiyon Makineleri:
Bazı hareketler elektrik motorları tarafından yürütülür ve bazıları hidroliklerle (bazı nadir durumlarda hava) tahrik edilir. Bu, bu tür sistemlerin daha yüksek maliyetine maruz kalmadan elektrikli tahrik sistemlerinin bazı avantajlarından yararlanmaya izin verir. Bu makine tipleri, her iki sistemi tek bir makinede kullanmanın avantajlarını sağlayan uygulamalar için çok iyi bir çözümdür.
Daha çok, Enjeksiyon bölümü elektrikli, mengene, taşıma ve çıkartma grupları ise hidrolik sistemden oluşur.
Normal elektrikli enjeksiyon makinelerinde genellikle mengene sistemlerinden şikayet edilir. Sıkıştırma oranları daha azdır, yüksek hızlarda daha büyük giderlere sebep olabilirler. Enjeksiyon hızlı olabilir fakat mengene eksi yanıdır. Normal hidrolik enjeksiyon makinelerinde mengene istenildiği gibidir fakat, enjeksiyon hızı ile ilgili şikayetler çoğunluktadır. Max. hızları 100mm/s ile 200mm/s aralığındadır.
Dikey Enjeksiyon Makineleri:
Geleneksel yatay makinelerle aynı işlev görür, ancak dikey eksende çalışacak şekilde konumludur. Bu tip makine, çeşitli müşteri gereksinimlerini karşılamak için hidrolik , elektrikli ve hibrit uygulamalarda mevcuttur . Dikey enjeksiyon kalıplama makineleri, makinenin yönü nedeniyle çok az zemin alanı gerektirir. Dikey enjeksiyon kalıplama makineleri kesici uç kalıplama uygulamaları için özellikle uygundur. Bileşenler kalıba kolayca yüklenebilir ve aşırı kalıplamadan önce yerçekimi ile yerinde tutulabilir. Dikey enjeksiyon kalıplama makineleri genellikle bir mekik veya döner tabla içerir.
Tam Elektrikli Enjeksiyon Makineleri:
Prosese ilişkin tüm hareketler (geri çekme, enjeksiyon, kalıp açma / kapama) elektrikli (servo) motorlar aracılığıyla gerçekleştirilir. Makine, maça çekme gibi hareketler için harici bir hidrolik güç paketi ile donatılmadığı sürece, bu tür makinelerde hiçbir hidrolik sistem kullanılmaz. Elektrik motorlarının kullanımı, sadece hareket gerektiğinde motorlar çalıştırıldığı için yüksek enerji verimli bir makineye izin verir. Ayrıca, yenilikçi enerji geri kazanım sistemi kinetik enerjiyi yakalar, depolar ve bu enerji makineye güç vermek için kullanılabilir.
1980 lerde küçük makineler olarak başlayan elektrikli enjeksiyon kalıplama makineleri tarihi, artık pazarın neredeyse yarısını kapsamakta. Ve mümkün olan her boyut aralığında ve uygulama alanına hitap edebilmekte.
Tüm elektrikli plastik enjeksiyon kalıplama makinelerinin avantajları:
-
Yüksek tekrarlanabilirlik ve hassasiyet - elektrik üniteleri dijital olarak kontrol edilir ve bu nedenle üretim süreci tahmin edilebilir ve konumlandırma hassasiyeti son derece yüksektir (± 0.0001 inç)
-
Enerji verimliliği çok yüksektir. Enerjinin sadece makine hareketlerinde kullanılmasıyla %30 ila %70 arasında enerji tasarrufu
-
Paralel hareket yapabilme özelliği sayesinde daha hızlı ve daha verimli işlem
-
Erken Start. Isınması gereken daha az bileşen ve sıvı (yağ) nedeniyle daha kısa başlatma süreleri
-
Genellikle daha sessiz çalışma (<65 dbA)
-
Temiz oda üretimi için ideal. Hidrolik sızıntıların olmaması ile tertemiz ortam
-
Üretim süresi boyunca maliyet tasarrufu - enerji tasarrufu, daha düşük yağ filtresi değişimi, daha az birim maliyet ve daha az malzeme maliyeti nedeniyle daha düşük işletme maliyetleri
-
Genellikle daha yüksek enjeksiyon hızları (800 mm / sn'ye kadar) ve daha hızlı kelepçe hareketi