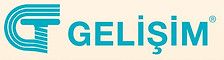


Hidrokarbonlar
Hidrojen ve karbon olmak üzere iki elementten oluşan organik bir bileşiktir. Petrol bileşiminin büyük bir kısmı değişen uzunluklardaki hidrokarbonlardan oluşur.
En küçük hidrokarbon metan, tek bir karbon atomu ve dört hidrojen atomundan oluşur. Bununla birlikte, hidrokarbonlar, zincirler, daireler ve diğer karmaşık şekiller dahil olmak üzere birçok yönden birbirine bağlanmış yüzlerce veya binlerce bireysel atomdan oluşabilir.
Hidrokarbonların özelliklerini sınıflandırmak için birkaç temel türe ayrılırlar.
Alkanlar: Bunlar doymuş hidrokarbonlar olarak adlandırılır. Yani sadece tüm karbon atomları arasında tek bağlar içerirler. Alkanlar, petrol yakıtlarının temelidir ve doğrusal ve dallı formlarda bulunurlar.
Doymamış Hidrokarbonlar: Karbon atomları arasında bir veya daha fazla çift bağa sahip olan hidrokarbonlara alken denir.
Sikloalkanlar: Bir veya daha fazla halka yapısı içeren herhangi bir hidrokarbon.
Aromatik Hidrokarbonlar: Areneler olarak da adlandırılan aromatik hidrokarbonlar, karbon atomlarının birbirini izleyen çift ve tek bağlarla bağlandığı benzersiz bir karbon molekülleri sınıfıdır. Bu molekül sınıfı, karbon atomları arasındaki bağların tek ve çift bağlar arasında bir ara bağ olduğu özel halka yapılarına sahiptir.
Bu sınıftaki moleküller, endüstriyel çözücü «benzen» içerir.
Benzen (C6H6): Diğer hidrokarbonlar gibi benzen de petrolün doğal bir bileşenidir. Oda sıcaklığında renksiz, yanıcı, tatlı kokulu bir sıvıdır ve yüksek oktan sayısına sahip olduğu için çoğu benzin karışımının bir bileşenidir.
Benzen de oldukça kanserojendir ve kemik iliği yetmezliği ve kemik kanserine neden olduğu iyi bilinmektedir. Elbette, “hoş aroması” nedeniyle tıraş sonrası ve diğer kozmetiklerde bir katkı maddesi olarak kullanıldığında kanserojenliği iyi bilinmemektedir.
En büyük benzen kullanımı (% 50), stiren ve polistren plastiklerinin ürünüdür. Ayrıca Naylon üretiminde önemli olan sikloheksan olarak bilinen bir moleküle dönüştürülür. Siklohekzan üretmek için benzenin yaklaşık% 15'i kullanılır. Böcek ilaçlarından kauçuğa kadar her şeyde daha küçük miktarlar kullanılır.
Benzen yapısı iki şekilde çizilebilir. İlkinde, çift bağ karakteri açıkça çizilir. Kısa elli versiyonda, yapıyı göstermek için halkanın içine bir daire çizilir. Benzen içindeki her bir karbon atomuna bağlı tek bir hidrojen vardır.
Aşağıdaki I. ve II. çizimleri eştir. Pratikte III. çizim kullanılır.
Benzen, renksiz, alevlenebilen, kaynama noktası 80,1 °C, erime noktası 5,5 °C olan bir sıvıdır.
Binükleer Aromatik Hidrokarbonlar: Molekülünde iki benzen halkası içeren bileşiklerdir.
Hidrokarbonlar
Hidrojen ve karbon olmak üzere iki elementten oluşan organik bir bileşiktir. Petrol bileşiminin büyük bir kısmı değişen uzunluklardaki hidrokarbonlardan oluşur.
En küçük hidrokarbon metan, tek bir karbon atomu ve dört hidrojen atomundan oluşur. Bununla birlikte, hidrokarbonlar, zincirler, daireler ve diğer karmaşık şekiller dahil olmak üzere birçok yönden birbirine bağlanmış yüzlerce veya binlerce bireysel atomdan oluşabilir.
Hidrokarbonların özelliklerini sınıflandırmak için birkaç temel türe ayrılırlar.
Alkanlar: Bunlar doymuş hidrokarbonlar olarak adlandırılır. Yani sadece tüm karbon atomları arasında tek bağlar içerirler. Alkanlar, petrol yakıtlarının temelidir ve doğrusal ve dallı formlarda bulunurlar.
Doymamış Hidrokarbonlar: Karbon atomları arasında bir veya daha fazla çift bağa sahip olan hidrokarbonlara alken denir.
Sikloalkanlar: Bir veya daha fazla halka yapısı içeren herhangi bir hidrokarbon.
Aromatik Hidrokarbonlar: Areneler olarak da adlandırılan aromatik hidrokarbonlar, karbon atomlarının birbirini izleyen çift ve tek bağlarla bağlandığı benzersiz bir karbon molekülleri sınıfıdır. Bu molekül sınıfı, karbon atomları arasındaki bağların tek ve çift bağlar arasında bir ara bağ olduğu özel halka yapılarına sahiptir.
Bu sınıftaki moleküller, endüstriyel çözücü «benzen» içerir.
Benzen (C6H6): Diğer hidrokarbonlar gibi benzen de petrolün doğal bir bileşenidir. Oda sıcaklığında renksiz, yanıcı, tatlı kokulu bir sıvıdır ve yüksek oktan sayısına sahip olduğu için çoğu benzin karışımının bir bileşenidir.
Benzen de oldukça kanserojendir ve kemik iliği yetmezliği ve kemik kanserine neden olduğu iyi bilinmektedir. Elbette, “hoş aroması” nedeniyle tıraş sonrası ve diğer kozmetiklerde bir katkı maddesi olarak kullanıldığında kanserojenliği iyi bilinmemektedir.
En büyük benzen kullanımı (% 50), stiren ve polistren plastiklerinin ürünüdür. Ayrıca Naylon üretiminde önemli olan sikloheksan olarak bilinen bir moleküle dönüştürülür. Siklohekzan üretmek için benzenin yaklaşık% 15'i kullanılır. Böcek ilaçlarından kauçuğa kadar her şeyde daha küçük miktarlar kullanılır.
Benzen yapısı iki şekilde çizilebilir. İlkinde, çift bağ karakteri açıkça çizilir. Kısa elli versiyonda, yapıyı göstermek için halkanın içine bir daire çizilir. Benzen içindeki her bir karbon atomuna bağlı tek bir hidrojen vardır.
Aşağıdaki I. ve II. çizimleri eştir. Pratikte III. çizim kullanılır.
Benzen, renksiz, alevlenebilen, kaynama noktası 80,1 °C, erime noktası 5,5 °C olan bir sıvıdır.
Binükleer Aromatik Hidrokarbonlar: Molekülünde iki benzen halkası içeren bileşiklerdir.
Hakkında
Kyäni, faydalı bileşenlerden oluşan besin takviyesi ürünlerini; benzersiz iş fırsatıyla birlikte dünya çapında 50'den fazla ülkeye ulaştırmaktadır. İdeal sağlığımızı korumak için günlük olarak Kyäni ürünlerini kullanırız, bu ürünleri başkalarıyla paylaşırız, işimizi inşa etmek ve sürdürmek için neredeyse her gün belirli bir saatimizi işe adarız ve başkalarını da Kyäni fırsatına dahil ederek veya Potato Pak ve Caring Hands programlarına katkı sağlayarak başarımızı başkalarıyla paylaşırız.
Hakkında
Kyäni, faydalı bileşenlerden oluşan besin takviyesi ürünlerini; benzersiz iş fırsatıyla birlikte dünya çapında 50'den fazla ülkeye ulaştırmaktadır. İdeal sağlığımızı korumak için günlük olarak Kyäni ürünlerini kullanırız, bu ürünleri başkalarıyla paylaşırız, işimizi inşa etmek ve sürdürmek için neredeyse her gün belirli bir saatimizi işe adarız ve başkalarını da Kyäni fırsatına dahil ederek veya Potato Pak ve Caring Hands programlarına katkı sağlayarak başarımızı başkalarıyla paylaşırız.
Sayfa Yapım Aşamasındadır.
Sayfa Yapım Aşamasındadır.
Eğitim / Bilgi / Çözüm Platformu
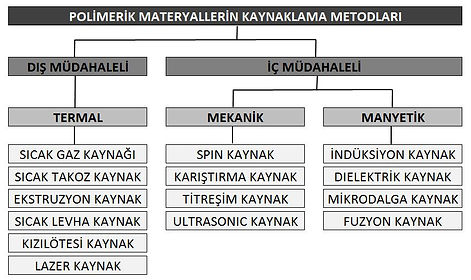
Plastiklerde Kaynak İşlemi
Plastik kaynak, iki uyumlu termoplastik arasında moleküler bir bağ oluşturma işlemidir. Kaynak, üstün güç sağlar ve döngü sürelerini azaltır. Herhangi bir kaynağın üç ana adımı vardır: presleme, ısıtma ve soğutma. Plastik kaynak işlemleri öncelikle ısıtma yöntemleriyle ayırt edilir. Kuvvet uygulaması ve soğutma için paylar, genel işlem kategorisi içinde makineden makineye değişiklik gösterebilen mekanik hususlardır. Yüksek sıcaklık plastiklerinde malzemelerin plastikleşmesi için oldukça yüksek enerji girişi gerektiği unutulmamalıdır. Kullanılacak kaynak yöntemi aşağıdaki faktörlere bağlıdır:
-
Parça geometrisi
-
Parça boyutu
-
Malzeme türü.
Plastik kaynak, temel olarak plastik malzemelerin aynı metallerde olduğu gibi ancak farklı yöntemler ile birleştirilmesi işlemine denir. Plastik kaynak, adından da anlaşılacağı üzere plastik malzemelere yapılmaktadır ancak; hepsine uygulanamamaktadır. Temel mantık olarak, malzemenin eritilip birleştirilmesidir. Ya da ilave bir başka plastik kullanılarak diğer iki ana malzeme birleştirilir. Bu kaynak yöntemi sadece termoplastik malzemelere uygulanabilmektedir. Termoset malzemelere bu birleştirme yöntemi uygulanamaz.
Termoset malzemelere plastik kaynak uygulanamamasının temel nedeni, bu tip plastiklere bir kez şekil verildiğinde, tekrar ne kadar ısıtılırsa ısıtılsınlar asla erimezler, sadece kömür halini alırlar ve kullanılamayacak hale gelirler. Bunun temel nedeni, termoplastik malzemelerde wan der waals atomik bağları var iken, termoset plastiklerde çapraz bağlar molekülleri bir arada tutar. Böylece, bu malzemeler hem daha rijit hem de bir kez şekillendikten sonra tekrar eritilip kullanılamazlar. Yani geri dönüşümleri imkansızdır.
Termoplastik malzemelerde ise, molekül zincirleri arasında wan der waals bağları vardır. Bu tip bağlar çapraz bağlara göre daha az mukavemetlidir. Şekillendirildikten sonra tekrar tekrar eritilip başka şekillerde şekillendirilip kullanılabilirler. Yani geri dönüşümleri mümkündür. Bu özellikleri nedeniyle de çevreye daha duyarlı tip malzemelerdir.
İki termoplastik parçayı birleştirmek için malzemelerin kimyasal olarak uyumlu olması gerekir. Aksi takdirde, her iki malzeme birlikte erise bile, moleküler bağ oluşmayacaktır. İyi bir örnek, polietileni polipropilene kaynaklamaya çalışmak olabilir. Bu yarı kristal malzemelerin her ikisi de benzer bir görünüme ve birçok ortak fiziksel özelliğe sahiptir. Bununla birlikte, kimyasal olarak uyumlu değildirler ve bu nedenle birbirlerine kaynaklanamazlar. Termoplastikler gibi (yani aynı kimyasal özelliklere sahip malzemeler) kendi kendilerine kaynak yapacaklardır. Örneğin, bir ABS parçası başka bir ABS parçasına kaynak yapacaktır. Birbirine benzemeyen termoplastikler ancak eriyik sıcaklıkları 40ºF (6ºC) içindeyse ve benzer moleküler yapıya sahiplerse uyumlu olabilirler. Örneğin, ABS parçasının bir akrilik parçaya kaynaklanması muhtemeldir çünkü kimyasal özellikleri uyumludur. Genel olarak konuşursak, sadece benzer amorf polimerler mükemmel bir şekilde birbirine kaynaklanma olasılığına sahiptir. Herhangi bir yarı kristal malzemenin kimyasal özellikleri, her birini yalnızca kendisiyle uyumlu hale getirir. Kaynaklanacak malzemeler uyumlu olduğunda, diğer birkaç faktör parçaların kaynaklanabilirliğini etkileyebilir. Bu faktörler arasında higroskopiklik, kalıp ayırıcı maddeler, yağlayıcılar, plastikleştiriciler, dolgular, alev geciktiriciler, yeniden öğütme, pigmentler ve reçine sınıfları bulunur. Kaynaklanacak malzemeler uyumlu olduğunda, diğer birkaç faktör parçaların kaynaklanabilirliğini etkileyebilir. Bu faktörler arasında higroskopiklik, kalıp ayırıcı maddeler, yağlayıcılar, plastikleştiriciler, dolgular, alev geciktiriciler, yeniden öğütme, pigmentler ve reçine sınıfları bulunur. Kaynaklanacak malzemeler uyumlu olduğunda, diğer birkaç faktör parçaların kaynaklanabilirliğini etkileyebilir. Bu faktörler arasında higroskopiklik, kalıp ayırıcı maddeler, yağlayıcılar, plastikleştiriciler, dolgular, alev geciktiriciler, yeniden öğütülmüş, pigmentler ve reçine sınıfları bulunur.
Kaynakta, kaynak bölgesinin ve yakındaki baz metallerin ısınması, erimesi ve soğuması nedeniyle kaynak bölgesinin yakınında plastik termal gerinim gelişir. Plastik gerilme, kaynak yapıldıktan sonra kaynaklı yapının kalıcı deformasyonuna neden olur. Buna kaynak kaynaklı bozulma denir. Kaynak kaynaklı bozulma modu, bükülme, döndürme veya burkulma gibi gerilme ve düzlem dışı deformasyon gibi düzlem içi deformasyon olarak ortaya çıkabilir. Moleküler bir bağın oluşması için moleküller arası difüzyona izin vermek için faylanma yüzeyinde bir eriyik tabakası oluşturmak plastik kaynak işlemi için çok önemlidir . Katı halde, polimer zincirleri akmayacaktır. Bu nedenle, plastik moleküllerin arayüz boyunca dağılmasına ve diğer parçanın molekülleri ile bağlanmasına izin vermek için her iki parçadaki eklem yüzeyinin eritilmesi gerekir. Eriyik ne kadar sıcaksa, o kadar çok moleküler hareket elde edilir ve daha kısa bir döngü süresinde kaynak yapılabilir. Amorf polimerler yarı kristal polimerler erime sıcaklıklarının üzerine ısıtılmalıdır.
Üst üste binen termoplastiklerin kızılötesi lazer kaynağı , radyasyon penetrasyon ısıtmasını kullanır. Kontak arayüzünde eriyik bölgesi üretildiğinde iki parça birleştirilir.
Plastiklerin geleneksel kızılötesi lazer kaynağında, Transmisyonlu Kızılötesi (TTIr) lazer kaynağı olarak adlandırılan kaynak üzerine odaklanmıştır . Diyot lazerler , bu yöntem için uygun lazerler olarak yaygın bir şekilde benimsenmiştir. İki malzeme seçmek esastır; ışınlanmış olan yüksek derecede geçirgen, diğeri ise lazer ışığına oldukça emicidir. Çoğu gerçek TTIr lazer kaynağı durumunda, pigmentasyonun emici kısımdaki radyasyon emilimini arttırması gerekir .
Sıcak Levha Kaynak
Bu işlemde, iki parçanın birbirine bakan yüzeyleri gerçek bir ısıtılmış levhadan iletim, konveksiyon ve / veya radyasyon yoluyla ısıtılır. İki parça ya sıcak plakaya bastırılır ya da bir süre onun yanında tutulur, ardından sıcak plaka çıkarılır ve kaynağı oluşturmak için parçalar birbirine bastırılır. Sıcak Levha kaynağı tipik olarak 10 ile 20 saniye arasındaki kaynak sürelerine sahiptir.
Sıcak levha kaynağında kullanılan parametreler, sıcak levha sıcaklığı, eşleştirme sırasındaki basınç (veya yer değiştirme), ısıtma sırasındaki basınç, kaynak aşamasında basınç ve yer değiştirme ve eşleştirme, ısıtma, değiştirme ve soğutma süreleridir. Bu parametrelerin kaynak kalitesi üzerinde birbirine bağımlı bir etkisi vardır ve ayrı ayrı ayarlanamaz.
Sıcak plaka sıcaklığı plakanın yüzeyinde alınır. Erime sıcaklığı, erime viskozitesi ve termal bozunma sınırları dahil olmak üzere malzemenin özellikleri ile birlikte sıcak levha kaynak varyantına göre ayarlanır. Geleneksel sıcak levha kaynağı, erime sıcaklığının 30 ila 100 ° C üzerindeki sıcaklıkları kullanır. Yüksek sıcaklık varyantı, erime noktasının yaklaşık 100 ila 200 ° C üzerinde, malzemenin bozunma sıcaklığının üzerindeki sıcaklıkları kullanır. Temassız varyant, erime noktasının 300 ila 400 ° C üzerindeki sıcaklıkları kullanır.
Sıcak Gazlı Kaynak
Bu yöntem, ilave bir malzeme kullanılarak yapılmaktadır. Kaynak yapılacak yer bir sıcak hava tabancası ile ısıtılır. Gerekli ısıtma yapıldıktan sonra, ilave plastik ile aralık doldurulur. Bu işlem bir kaç pasoda gerçekleştirilebilir. Burada kullanılan sıcak gaz azot olabilmektedir. Bunun temel nedeni, plastik malzemelerin yüksek sıcaklıkta oksitlenmelerini engellemektir. Oksitlenme sadece metallerde olmamaktadır. Plastik malzemeler de oksitlenerek kırılgan hale gelmektedir.
Plastik kaynak yapılacak olan parçalar çok sert ise, ilave malzeme, birleştirilecek malzemeler arasına konur. Ancak; kaynak yapılacak plastikler yumuşak bir termoplastik ise, ek bir bastırma aparatı ile, kaynak dikişine baskı uygulanması gerekmektedir.
Sıcak havayı hem bağlantı yüzeyine hem de kaynak çubuğuna yönlendirmek ve malzemeleri yumuşama sıcaklıklarına ısıtmak için bir sıcak gaz torçu kullanılır. Isıtılmış kaynak çubuğu üzerindeki bağlantı yüzeyine basınç uygulanması, tamamlanmış bir kaynak oluşturmak için malzemeleri birbirine bağlar. Bu teknik kolayca otomatikleştirilmez ve esas olarak küçük veya karmaşık bileşenlerin onarımları veya bireysel üretim ihtiyaçları için kullanılır.
Sıcak gaz kaynağında kullanılan iki yaygın kaynak tekniği vardır: el kaynağı ve hızlı kaynak.
El kaynağı, kaynak çubuğunun doğrudan kaynakçı tarafından ek yerine uygulandığı bir tekniktir. Sıcak gaz torcu, hem kaynak çubuğunu hem de bağlantı yüzeylerini arka arkaya sarkaç şeklinde ısıtmak için tek elle hareket ettirilir. Kaynak çubuğuna basınç uygulanır ve nozul yardımı olmadan elle kontrol edilir. Bu teknik çoğu konfigürasyon için uygundur ve kaynak çubuğunun uygulanması yalnızca ulaşılabilir kaynak pozisyonlarıyla sınırlı olduğundan, dar, kısıtlı alanlar veya karmaşık bağlantı tasarımlarında kaynak için faydalı olabilir.
Hızlı kaynak, sıcak gaz torçunun ve kaynak çubuğunun tek bir kohezif sistem olmasını sağlayan özel olarak tasarlanmış bir nozül kullanır. Nozül, kaynak çubuğunun bir besleme borusu aracılığıyla bağlantıya uygulanmasını kolaylaştırır. Nozul, kaynak çubuğu malzemesini eşit şekilde ısıtır ve kontrollü bir basınç uygulamasına izin verir. Nozulun tabanı, bağlantı yüzeyini ısıtmak ve kaynak çubuğunu oluğa yönlendirmek için tasarlanmıştır. Besleme borularının belirli kaynak çubuğu şekillerine ve boyutlarına uyması için nozullar üretilir ve ortak boyutlardaki yuvarlak veya üçgen çubuklar için mevcuttur. Hızlı kaynak kullanımı, nozulun boyutu ve sistemin manevra kabiliyeti nedeniyle basit bağlantı tasarımı ve yönlendirme uygulamalarıyla sınırlıdır.
Gaz sıcaklığı, uygulama basıncı, kaynak ilerleme hızı, gaz akış hızı ve torç oryantasyonunun tümü, bitmiş kaynağın bütünlüğünü ve mekanik özelliklerini etkiler. Gaz sıcaklığı ve akış hızı, sistem girdilerine dayalı kontrol edilebilir parametrelerdir. Uygulama basıncı, kaynak hareket hızı ve torç oryantasyonu, kaynağı gerçekleştiren operatöre bağlıdır. Bu parametreler birbiriyle ilişkilidir ve tümü kaynağın nihai kalitesi üzerinde önemli bir etkiye sahiptir.
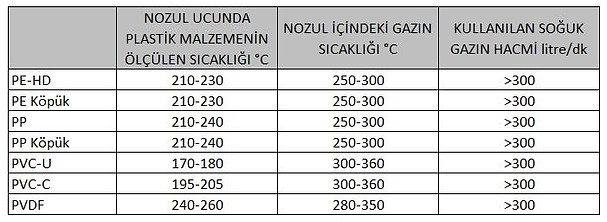
Ekstrüzyon Kaynak
Sıcak gaz kaynağı ile karşılaştırıldığında , yaklaşık beş kat daha hızlı bir uygulama hızının olması en büyük avantajıdır. Bu uygulama tek bir geçişte yüksek depozisyon oranları uygulanmasıyla elde edilmekte içindir. Kaynak parametreleri üzerinde daha sıkı kontrol oluşturulabilmesi nedeni ile nedeniyle çok daha kuvvetli kaynaklar elde edilebilmektedir.
Bu sürecin ana dezavantajı ise makinenin boyutlarından dolayı uygulamada zorluk yaşanabileceğidir ve daha çok bir eğitimli operatör tarafından uygulanmasının neredeyse bir zorunluluk taşıdığıdır.
Ekstrüzyon kaynağı kalın cidarlı kısımların kaynaklanmasında kullanılır. Kaynak işlemi kaynak çubuğu kullanılarak yapılır. Ekstrüzyon kaynak ekipmanı küçük bir ekstrüderdir. Ekstrüde malzeme bir kaynak kılıfı ile preslenir. Kaynak kılıfı genellikle yüksek sıcaklık dayanımı nedeniyle teflondan yapılır. Kaynak kılıfının kaynak dikişine uygun olması gerekir.Çalışma şekli sıcak hava kaynağına oldukça benzer. Ancak sonuçlar daha yüksek mekanik dayanım, daha iyi kaynak kalitesi ve daha düşük iç gerilimdir.
Bu kaynaklamada, ekstrüzyon işi için el içi mini bir ekstruder kullanılmaktadır. Kullanılan bu ekstruderin kovan ısısı, spiral sarımlı tellerle (klasik yöntem) elektrik ile yapılabileceği gibi, bir başka kovan ısıtma tekniği de; zaten ısıtılmış sıcak gazdan istifade etmedir. El ekstrüderleri, geleneksel aparat mühendisliğinde, depolama sahası yapımında, plastik onarımlarında ve diğer birçok sektörde kullanılmaktadır. Kalite ve performansın gerekli olduğu her yerde çok değerlidirler.
Vida üzerindeki kaynak çubuğunu çekmek için bir diş daha kullanılır . İşlemde ayrıca çubuğun bükülmesini engelleyen besleme manşonundan da geçmektedir . Bıçak yerleştirildikten sonra çubuğu keser. Bu, vidalı spiral tarafından ileri doğru çekilir, sıkıştırılır ve sürtünme yoluyla kovan (tambur) içinde ısıtılır.
Spiral ısıtmalı versiyonda, plastikleştirme işlemi için gerekli olan kovan içi harici ısıyı üretmek için elektrik enerjisinden istifade edilir. spiral rezistans tüm ekstrüder tamburu etrafına sarılıdır ve eritme aralığının sıcaklığını olağanüstü bir hassasiyetle düzenler. Silindir tüpüne yerleştirilmiş sıcaklık probu kütle sıcaklığını ölçer. Bu, bilgileri elektronik cihazlara gönderir ve bu da tüm plastikleştirme sürecini kapalı devre olarak kontrol eder.
Sıcak havalı versiyonda, ısı, ekstrüzyon ünitesine dışarıdan nüfuz ederek plastikleştirme sürecini başlatır ve çalışma sırasında devam etmesine yardımcı olur. Dış ısı, sıcak hava şeklinde sıcak gaz cihazı tarafından üretilir ve bu daha sonra sıcak gaz kanalları ile ön ısıtma odasındaki ekstrüzyon ünitesi etrafında akar. Sürtünme ısısı ayrıca sıkıştırma ve sürtünme ile üretilir. Bu, kaynak dolgu metalinin plastikleşmesine ve homojen bir kütle halinde karıştırılmasına neden olur.
Nihayetinde, ekstrüdat daha sonra nozülden çıkar ve daha öncesinde sıcak gaz ile yumaşıtılmış satıha sürünür.

Lazer Kaynak
Kontrollü bir miktarda enerjiyi kesin bir konuma ileterek eklem alanındaki plastiği eritmek için lazer ışını kullanan temassız bir birleştirme yöntemidir. Isı girdisini kontrol etmedeki hassasiyet, lazer ışını boyutunu ayarlama kolaylığına ve ışını konumlandırmak için mevcut olan yöntemlere dayanır. Çoğu termoplastik, uygun bir lazer kaynağı ve uygun bağlantı tasarımı kullanılarak kaynaklanabilir.
Plastik parçaların lazer kaynağı, sağlam, esnek ve hassas bir birleştirme işlemi olarak kendini kanıtlamıştır. Karmaşık geometrilere sahip küçük ölçekli parça üretiminden otomasyon hatlarına kolayca entegre edilebilen yüksek hacimli endüstriyel üretime kadar yüksek verimli ve esnek montaj sağlar. Bu işlem, kontrollü bir miktarda enerjiyi hassas bir konuma ileterek eklem alanındaki plastiği eritmek için bir lazer ışını kullanır. Isı girdisini kontrol etmedeki bu hassasiyet seviyesi, kiriş boyutunu ayarlama kolaylığına ve ışının hassas konumlandırılması ve hareket ettirilmesi için mevcut olan yöntemlere dayanmaktadır.
Süreç, diğer plastik kaynak teknikleriyle aynı temel malzeme uyumluluğuna dayanmaktadır, ancak çoğu zaman reçine kimyası ve erime sıcaklığı farklılıklarını diğer plastik kaynak işlemlerinin çoğundan daha bağışlayıcı olduğu bulunmuştur. Neredeyse tüm termoplastikler, uygun bir lazer kaynağı ve uygun bağlantı tasarımı kullanılarak kaynaklanabilir.
Termoplastik bileşenlerde yüksek kaliteli bağlantılar üretmek için ticari olarak temin edilebilen üç ana lazer türü vardır.
CO2 Lazer:
Artık 60kW'a kadar güç çıkışında bulunan ve en yaygın olarak metal, plastik ve seramik kesmek için kullanılan, köklü bir malzeme işleme aracıdır. CO2 lazer radyasyonu (10.6μm dalga boyu) hızlı bir şekilde plastik yüzey tabakaları emilir. Bu foton enerjilerinde (0.12eV) soğurma, moleküler bağların titreşimine dayanır. Lazerin moleküllerde rezonans frekansı uyandırması nedeniyle plastikler ısınır. Bu nedenle ince plastik filmin (<0,2 mm) çok hızlı işlenmesi mümkündür (500 m / dakikaya kadar yüksek hızlı kaynak kanıtlanmıştır).
100 m / dk'da iki polietilen film lazer ile kaynak yapılabilir. CO2 lazer ışını bir silika fiber optiğin altına iletilemez, ancak aynalar ve portal veya robotik hareket kullanılarak karmaşık bir işlem ile tatbik edilebilir.
Nd: YAG Lazer:
Malzeme işleme için de iyi bir şekilde oluşturulmuştur ve son gelişmeler 6kW'a kadar mevcut güçte artışlara ve lazer boyutunda azalmalara yol açabilir.
Nd: YAG lazer dalga boyundaki (1.064µm, 1.2eV foton enerjisi) enerji absorpsiyonunun derecesi, büyük ölçüde plastiklerdeki katkı maddelerinin varlığına bağlıdır. Hiçbir dolgu maddesi veya pigment yoksa, lazer malzemenin içine birkaç milimetre girebilir. Absorpsiyon katsayısı, bu foton enerjisini doğrudan absorbe eden ve yankılanan veya daha etkili kitle absorpsiyonu için radyasyonu saçan pigmentler veya dolgu maddeleri gibi katkı maddeleri vasıtasıyla arttırılabilir.
Kaynaklar, bir bağlantı arayüzünde ısı üretmek için kızılötesi emiciler konumlandırılarak yapılabilir. Bu işlem genel olarak 'transmisyon lazer kaynağı' olarak adlandırılır çünkü lazer enerjisi plastiğin bir kısmı aracılığıyla bağlantıya iletilir.
Nd: YAG lazer ışını, kolay ve esnek çalışma sağlayan bir silika fiber optikten aşağı iletilebilir.
Diyot Lazer:
1997'nin başından beri mevcuttur. CO2 ve Nd: YAG lazerlere kıyasla daha uygun maliyetlidir. Tipik olarak diyot lazerler 0,8-0,95 um dalga boyunda radyasyon yayarlar.
Bu nedenle, plastiklerle etkileşim, Nd: YAG lazer ile çok benzerdir ve uygulamaları çakışır.
Bir diyot lazerinden gelen ışın genellikle dikdörtgen şeklindedir ve bu, bazı uygulamalar için tercih edilirken, minimum nokta boyutunu ve mevcut maksimum güç yoğunluğunu sınırlar. Diyot lazer kaynağı, karmaşık işlemler için bir kızak veya robota monte edilebilecek kadar küçük ve hafiftir.
Nd: YAG ve diyot lazerler, plastiklerden birinin lazere geçirdiği ve diğerinin absorbe ettiği göz önüne alındığında, transmisyon lazer kaynağı gerçekleştirmek için kullanılabilir. İşlem, farklı soğurma özelliklerine sahip plastik parçaların eriyik flaş olmadan, dış yüzeylerde iz bırakmadan ve sadece ısıdan etkilenen küçük bir bölge olmadan kaynaklanabileceği bir araç sağlar.
Transmisyon Lazerli Kaynak (TTLW) :
Parçalar, birleşme yüzeyleri arasında yakın temas sağlamak için önceden monte edilir ve birbirine kenetlenir. Lazer ışını, üst "şeffaf" kısım yoluyla parça arayüzüne iletilir ve IR enerjisini ısıya dönüştüren alt emici kısım tarafından emilir. Isı, alt emici kısımdan üst kısma iletilir ve eriyiğin arayüz boyunca ilerlemesine ve bir bağ oluşturmasına izin verir. Parçalar arasında ısı transferi için yakın temas gerektiğinden, düzeneğin hassas konumlandırılması ve kelepçelenmesi önemlidir. Karbon siyahı ve özel olarak tasarlanmış emiciler reçineye karıştırılır veya montajın alt kısmında IR radyasyon emilimini sağlamak için yüzeye uygulanır. TTLW kaynak tekniği, alt bileşende bir emici maddenin varlığına bağlıdır, ve bu, tıbbi cihazların, elektronik cihazların ve bazı tüketim mallarının üretimi için "şeffaftan" veya "şeffaftan renkli" bir montaj gerektiğinde işlem uygulanabilirliğini sınırlar. Mühendisler, berrak polimerler tarafından kolayca emilen ve optik olarak berrak parçaların kalınlığı sayesinde yüksek kontrollü erime sağlayan, yakın zamanda geliştirilen 2 mikron lazeri entegre ederek bu engeli başarıyla aştılar. Bu, tıbbi cihaz endüstrisi için şeffaf polimerlerin lazerle kaynağını büyük ölçüde geliştirir ve basitleştirir berrak polimerler tarafından kolaylıkla emilen ve optik olarak berrak parçaların kalınlığı sayesinde oldukça kontrollü erime sağlar. Bu, tıbbi cihaz endüstrisi için şeffaf polimerlerin lazerle kaynağını büyük ölçüde geliştirir ve basitleştirir berrak polimerler tarafından kolaylıkla emilen ve optik olarak berrak parçaların kalınlığı sayesinde oldukça kontrollü erime sağlar. Bu, tıbbi cihaz endüstrisi için şeffaf polimerlerin lazerle kaynağını büyük ölçüde geliştirir ve basitleştirir.
Kontur Kaynağı :
Özellikle de yuvarlak parçalar, 25 m/dak'lık hızlara kadar vararak lazer ışını altından dönerek geçer. Bu esnada, kaynaklanacak konturun üzerinden lazer ışınıyla geçilir ve kontur ısıtılır. Yuvarlak parçaların yanı sıra büyük üç boyutlu bileşenler de kontur kaynak yöntemi için uygundur. Bu yöntemde karşılaşılan en büyük sorun, aşırı hacimli bileşenlerde, kaynaklanan parçaların konturları eşzamanlı olarak ısıtılamadığından gerilimlerin ortaya çıkabiliyor olmasıdır.
Eşzamanlı Kaynak :
Lazer ışını, bileşene optimal bir şekilde uyumlu olarak oluşturulur. Böylelikle kaynak yapılacak kontur eşzamanlı bir şekilde ısıtılır. Sonuç: Yaklaşık 100 ms'lik çok kısa proses süreleri. Çok karmaşık olmayan ve yüksek sayıda üretilmesi planlanan bileşenlerde bu yöntemin kullanılması son derece uygundur. Fakat bileşen geometrisinin değişmesi durumunda ışın şeklinin de buna göre değiştirilmesi gerekir.
Yarı Eşzamanlı Kaynak :
Tarayıcı bir lazer ışını kaynak konturunu ısıtır. Lazer ışını, 15 m/s (900m/dak) oranlarına varan bir hızda dolaştığından, soğuma süreciyle karşılaştırıldığında o kadar hızlıdır ki, kontur neredeyse eşzamanlı olarak ısıtılmış olur. Programlanabilir odaklama tertibatı sayesinde değişen kaynak konturlarına çok hızlı bir şekilde tepki verilebilir, bu da eşzamanlı kaynak yöntemine oranla açık bir avantaj sağlar.
Clearweld Süreci
"Clearweld" olarak bilinen lazer emici katkı maddesi, geleneksel aktarıcı lazer kaynak işleminin gerekliliklerinden tam bağımsızlık sağlar. Sıvı malzeme, birleştirme ortaklarının birleştirilmesinden önce kaynak düzlemine uygulanır. Clearweld, gelen lazer radyasyonunu absorbe ederek istenen kohezif bağlantıyı sağlar. Diğer IR emici malzemelerden farklı olarak Clearweld, radyasyona maruz kaldıktan sonra tamamen berrak hale gelir ve birleşme bölgesinde renkten bağımsız tasarım imkanı sağlar.
Bu yeni avantaja ek olarak, Clearweld sistemi, birleşen ortakların geometrik tasarımı için ilginç yeni olanaklar sunar. Yüksek işlem hızını korurken, çok katmanlı bağlantılar oluşturma da tek bir işlemle mümkün hale gelir.
Hibrit Laser
Bu teknoloji, geleneksel halojen ısıtma lambalarının yaydığı kızılötesi radyasyon ile lazer ışığının bir kombinasyonunu kullanır. Bu ikili ışık şiddeti kavramının hem işlem hızını hem de hata toleransını artırdığı şimdiden kanıtlanmıştır.
Hibrit kaynak teknolojisinin hedef uygulamaları sadece yapısal otomotiv parçaları değil, örneğin kafa ve arka lambalar ve plastik motor parçaları, aynı zamanda tüketici ürünleri ve tıbbi uygulamalardır.

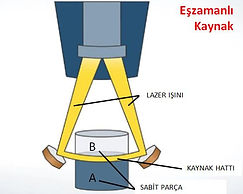

Ultrasonik Kaynak
Yüksek frekanslı mekanik hareketten üretilen ısının kullanılmasıyla termoplastiklerin birleştirilmesi veya yeniden biçimlendirilmesidir. Yüksek frekanslı ( 20-40 kHz ) elektrik enerjisini yüksek frekanslı mekanik harekete dönüştürerek gerçekleştirilir. Bu mekanik hareket, uygulanan kuvvetle birlikte, plastik bileşenlerin birleşme yüzeylerinde (eklem alanı) sürtünme ısısı yaratır, bunun sonucunda plastik malzeme erir ve parçalar arasında moleküler bir bağ oluşturur.
Titreşim Kaynak
Bu süreç, bir parçanın diğerine göre doğrusal veya yörüngesel hareketiyle çalışır. Bu, ısı oluşumuna ve eklemde bir eriyik tabakasının oluşumuna yol açan yüzey sürtünmesine neden olur. Titreşim kaynağı tipik olarak bir ila beş saniye arasındaki kaynak sürelerine sahiptir. Titreşim kaynak makineleri yaklaşık iki inç (50 mm) çaptan altı fit (1800 mm) uzunluğa kadar olan parçaları işleyebilir.
Kızılötesi (IR) Kaynak
Diğer bir temassız kaynak yöntemi, ısıyı plastik parçalara aktarmak için radyasyon kullanan kızılötesi kaynaktır. Sıcak levha kaynağı ile aynı temel adımları takip eder. Kızılötesi kaynak için iki farklı yaklaşım ortaya çıkmıştır. Sistemlerden biri, bazı durumlarda bir seramik ile kaplanmış elektrikle ısıtılan bir metal plaka kullanır. Diğer sistemde, standart ısıtıcı plaka, hareketli bir plakanın her iki tarafında sıkıştırılmış ve yay yüklü kızılötesi yayıcılarla değiştirilir.
IR sistemler plastikte, birçok uğraştırıcı ve büyük parçaların birleştirilmesinde sıcak yüzey ve vibrasyonlu kaynak yöntemlerinin yerine kullanılabilmektedir.
Sıcak yüzeyler vasıtasıyla ısıtılarak kaynak yapıldığında plastik ısıtıcı yüzey üzerine yapışabilmektedir. Yaklaşık her vardiyada 2-3 kez ısıtıcı yüzey üzerinde biriken plastiğin temizlenmesi gerekir. Aksi takdirde plastik, kaynak yapılacak ısıya getirilemeyebilir ya da kaynak yüzeyleri kaba çıkabilir. IR ile kaynak yönteminde plastik malzemeye temas olmadan ısıtma yapıldığı için temizlik veya kalıp değiştirmeden kaynaklanan zaman kayıpları yaşanmamaktadır. Ayrıca IR sistemlerin hızlı açılıp kapanma zamanları sayesinde kalıp ön ısıtma esnasında meydana gelen enerji ve zaman kayıplarının da önüne geçilir.
Plastik akü kasası parçalarının kaynaklanmasında, otomobil yakıt tankı gövdelerinin kaynaklanmasında, alt yapı sistemlerinde veya çeşitli ünitelerde kullanılan plastik boruların birleştirilmesinde, PVC pencere çerçevelerin kaynatılmasında, plastik parçaları birleştirmede kullanılan plastik pimlerin eritilmesinde IR sistemler kullanılabilmektedir.
Özet olarak IR kaynak uygulamasının avantajları şunlardır:
-
Çeşitli büyük plastik parçaların ısıtılarak birleştirilmesinde, karmaşık 2D ve 3D parça geometrilerini kaynaklama
-
Plastik akü kasası parçalarının kaynaklanmasın
-
Otomobil yakıt tankı gövdelerinin kaynaklanması
-
Alt yapı sistemlerinde veya çeşitli ünitelerde kullanılan plastik boruların ısıtılarak birleştirilmesi
-
Plastik parçaları birleştirmede kullanılan plastik pimlerin eritilmesi
-
Kabul edilebilir kaynak malzemelerinin çok çeşitliliği, termoplastikler, polietilen, PVC, polipropilen, kompozit takviyeli plastikler, poliamidler PC, PCABS.
-
Düşük elektrik tüketimi
-
Hızlı sıcaklık artışı
-
Elektriksel olarak yalıtılmış ve düşük kaçak akım ortamı
-
Düşük bakım gerektiren teknik cihazlar
-
Temassız kaynak işlemi
-
Daha güçlü kaynaklar, hermetik sızdırmazlık.
-
PP GF 30 ile TPE gibi farklı malzemeleri birleştirme yeteneği
Bu işlem, termoplastik malzeme tarafından emilen ve ısıya dönüştürülen Kızılötesi radyasyonu kullanır. Sonuç olarak, plastik parçanın çatlama yüzeyi eritilir ve bileşenler birbirine bastırılarak birleştirilir. Bu hızlı, temassız, partikül içermeyen bir kaynak yöntemidir.
Spin (Döndürme) Kaynak
Bu süreç, bir parçanın diğerine göre dönme hareketi ile çalışır. Bu, ısı oluşumuna ve eklemde bir eriyik tabakasının oluşumuna yol açan yüzey sürtünmesine neden olur. Spin kaynağı tipik olarak yarım ila beş saniye arasında kaynak sürelerine sahiptir. Spin kaynak makinaları yüksek torklu motorlar kullanarak dokuz inç (225 mm) çapa kadar yüksek hızlı motorlar kullanarak yaklaşık bir buçuk inç (12 mm) çaptaki parçaları işleyebilir. Döndürme kaynağı işlemi, termoplastik parçaları dairesel eklemlerle kaynaklamak için dönel sürtünme yoluyla ısı üretmekten oluşur. Eğirme kaynak makinesi, bir parçayı sabit matına karşı döndürürken eksenel olarak kuvvet uygular. Ortaya çıkan sürtünme, arayüzdeki parçaları eriten ısı üretir. Dönme durduğunda, malzeme soğur ve katılaşır, kaynaklı bir montaj oluşturur. Parçaların birbirine göre belirli bir şekilde yönlendirilmesi gereken durumlarda, kaynakçı dönüşü kesin bir açısal yönde durdurur.
Döndürme kaynağı için uygun malzemeler genellikle titreşim kaynağı gibi diğer sürtünmeli kaynak işlemleriyle birleştirilebilen malzemelerle aynıdır. Yarı kristal termoplastikler, ultrasoniklere göre döndürme kaynağı kullanılarak daha kolay birleştirilir. Uyumlu polimerler kullanarak spin kaynağı, güvenilir hermetik contalar yapabilir.
Benzer olmayan polimerlerin birleştirilmesi, genellikle daha düşük mukavemetli kaynak bağlantıları üretmesine rağmen, döndürerek kaynak işlemi kullanılarak mümkündür. Kaynak eklemini alttan kesmeli tasarlayarak, daha düşük erime sıcaklığına sahip polimer alttan kesmeye akacak ve mekanik bir birleşim oluşturacaktır.
Malzeme dolgusu ve yüzey kirleticileri (örn. Kalıp ayırıcı), tutarlılığı ve kaynak tekrarlanabilirliğini etkileyecek iki faktördür. Spin kaynağı, ultrasonik kaynaktan daha fazla kirletici maddeye toleranslıdır. Spin kaynağı aynı zamanda higroskopik polimerlerden daha az etkilenir, ancak yine de kritik uygulamalar için özel işlem gerektirebilirler.
Spin kaynak işleminin avantajları arasında yüksek kaliteli kalıcı bağlantılar, hermetik contalar, diğer işlemlere göre daha düşük ekipman maliyetleri, montaj kolaylığı, enerji verimli çalışma, anında kullanım, diğer parçaların yakalanması, uzak alan kaynak kabiliyeti ve yapıştırıcılar gibi ek malzemelerin ortadan kaldırılması sayılabilir.

Termosetler İçin Alternatif Kaynak İşlemi (Ar-Ge)
Termoset Yüzeyinin Termoplastikleştirilerek Kaynaklanması :
Termoset ve termoplastik kompozitleri birleştirmek için indüksiyon kaynağı üzerinde, Michel van Tooren Ar-Ge çalışmalasında; bir termoset kompozite, sadece kaynak yapmak istenen yerde termoplastik uygulamıştır. Uygulama; nanopartikül ölçekte, çapraz polimerizasyon aşılaması şeklinde yapılmıştır. Sonuçta, termoset kompozitin içine implante edilmiş ve bununla kimyasal olarak bağlanmış termoplastik adacıklarının elde edilmesidir. Daha sonra termoplastik adacıklar kaynak prosesine tabii tutulmuştur. Ve bu çalışma ile, kaynak tutturulamayan termoset yüzeylerin, yapıştırılması ya da delinip bağlantı elemanları ile tutturulması şeklindeki birleştirmelere bir alternatif uygulamanın önü açılmıştır.
Ar-Ge Uygulama Esasları :
PoliVinilBütiral (PVB), 150-170 ° C erime sıcaklığına sahip yarı kristal, düşük maliyetli bir termoplastik polimerin, mükemmel bağlama ve film oluşturma yeteneği ve birçok yüzeye yapışması özelliğinden istifade edilmiştir.
Bu karakteristik özelliğinden istifade olarak, PVB bir bağlantı tabakası olarak kullanılmıştır. 14 katlı karbon fiber katman şeklinde, termoset kompozit yüzeye 180°C 'de kürlenerek lamine edilmiş, makro-mekanik kenetlenme elde edilmiştir.
PVB reçinesinin, termoset kompozit yüzeyin ilk tabakasına 10-200 mikron kalınlığında kısmi nüfuz eden adacıkların oluşması sağlanmıştır.
Nihai olarak PVB reçineli satıhların, karşılıklı olarak İndüksiyon kaynağı ve ultrasonik kaynak prosesleri neticesinde oldukça güçlü bir şekilde birbirine tutunduğu (kaynak olduğu) sonuçlanmıştır. Tipik karbon fiber/epoksi bağlantılarının gösterdiği 25 MPa'lık bir bindirme kesme mukavemeti yakalanmıştır.
