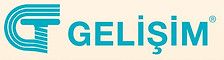


Hidrokarbonlar
Hidrojen ve karbon olmak üzere iki elementten oluşan organik bir bileşiktir. Petrol bileşiminin büyük bir kısmı değişen uzunluklardaki hidrokarbonlardan oluşur.
En küçük hidrokarbon metan, tek bir karbon atomu ve dört hidrojen atomundan oluşur. Bununla birlikte, hidrokarbonlar, zincirler, daireler ve diğer karmaşık şekiller dahil olmak üzere birçok yönden birbirine bağlanmış yüzlerce veya binlerce bireysel atomdan oluşabilir.
Hidrokarbonların özelliklerini sınıflandırmak için birkaç temel türe ayrılırlar.
Alkanlar: Bunlar doymuş hidrokarbonlar olarak adlandırılır. Yani sadece tüm karbon atomları arasında tek bağlar içerirler. Alkanlar, petrol yakıtlarının temelidir ve doğrusal ve dallı formlarda bulunurlar.
Doymamış Hidrokarbonlar: Karbon atomları arasında bir veya daha fazla çift bağa sahip olan hidrokarbonlara alken denir.
Sikloalkanlar: Bir veya daha fazla halka yapısı içeren herhangi bir hidrokarbon.
Aromatik Hidrokarbonlar: Areneler olarak da adlandırılan aromatik hidrokarbonlar, karbon atomlarının birbirini izleyen çift ve tek bağlarla bağlandığı benzersiz bir karbon molekülleri sınıfıdır. Bu molekül sınıfı, karbon atomları arasındaki bağların tek ve çift bağlar arasında bir ara bağ olduğu özel halka yapılarına sahiptir.
Bu sınıftaki moleküller, endüstriyel çözücü «benzen» içerir.
Benzen (C6H6): Diğer hidrokarbonlar gibi benzen de petrolün doğal bir bileşenidir. Oda sıcaklığında renksiz, yanıcı, tatlı kokulu bir sıvıdır ve yüksek oktan sayısına sahip olduğu için çoğu benzin karışımının bir bileşenidir.
Benzen de oldukça kanserojendir ve kemik iliği yetmezliği ve kemik kanserine neden olduğu iyi bilinmektedir. Elbette, “hoş aroması” nedeniyle tıraş sonrası ve diğer kozmetiklerde bir katkı maddesi olarak kullanıldığında kanserojenliği iyi bilinmemektedir.
En büyük benzen kullanımı (% 50), stiren ve polistren plastiklerinin ürünüdür. Ayrıca Naylon üretiminde önemli olan sikloheksan olarak bilinen bir moleküle dönüştürülür. Siklohekzan üretmek için benzenin yaklaşık% 15'i kullanılır. Böcek ilaçlarından kauçuğa kadar her şeyde daha küçük miktarlar kullanılır.
Benzen yapısı iki şekilde çizilebilir. İlkinde, çift bağ karakteri açıkça çizilir. Kısa elli versiyonda, yapıyı göstermek için halkanın içine bir daire çizilir. Benzen içindeki her bir karbon atomuna bağlı tek bir hidrojen vardır.
Aşağıdaki I. ve II. çizimleri eştir. Pratikte III. çizim kullanılır.
Benzen, renksiz, alevlenebilen, kaynama noktası 80,1 °C, erime noktası 5,5 °C olan bir sıvıdır.
Binükleer Aromatik Hidrokarbonlar: Molekülünde iki benzen halkası içeren bileşiklerdir.
Hidrokarbonlar
Hidrojen ve karbon olmak üzere iki elementten oluşan organik bir bileşiktir. Petrol bileşiminin büyük bir kısmı değişen uzunluklardaki hidrokarbonlardan oluşur.
En küçük hidrokarbon metan, tek bir karbon atomu ve dört hidrojen atomundan oluşur. Bununla birlikte, hidrokarbonlar, zincirler, daireler ve diğer karmaşık şekiller dahil olmak üzere birçok yönden birbirine bağlanmış yüzlerce veya binlerce bireysel atomdan oluşabilir.
Hidrokarbonların özelliklerini sınıflandırmak için birkaç temel türe ayrılırlar.
Alkanlar: Bunlar doymuş hidrokarbonlar olarak adlandırılır. Yani sadece tüm karbon atomları arasında tek bağlar içerirler. Alkanlar, petrol yakıtlarının temelidir ve doğrusal ve dallı formlarda bulunurlar.
Doymamış Hidrokarbonlar: Karbon atomları arasında bir veya daha fazla çift bağa sahip olan hidrokarbonlara alken denir.
Sikloalkanlar: Bir veya daha fazla halka yapısı içeren herhangi bir hidrokarbon.
Aromatik Hidrokarbonlar: Areneler olarak da adlandırılan aromatik hidrokarbonlar, karbon atomlarının birbirini izleyen çift ve tek bağlarla bağlandığı benzersiz bir karbon molekülleri sınıfıdır. Bu molekül sınıfı, karbon atomları arasındaki bağların tek ve çift bağlar arasında bir ara bağ olduğu özel halka yapılarına sahiptir.
Bu sınıftaki moleküller, endüstriyel çözücü «benzen» içerir.
Benzen (C6H6): Diğer hidrokarbonlar gibi benzen de petrolün doğal bir bileşenidir. Oda sıcaklığında renksiz, yanıcı, tatlı kokulu bir sıvıdır ve yüksek oktan sayısına sahip olduğu için çoğu benzin karışımının bir bileşenidir.
Benzen de oldukça kanserojendir ve kemik iliği yetmezliği ve kemik kanserine neden olduğu iyi bilinmektedir. Elbette, “hoş aroması” nedeniyle tıraş sonrası ve diğer kozmetiklerde bir katkı maddesi olarak kullanıldığında kanserojenliği iyi bilinmemektedir.
En büyük benzen kullanımı (% 50), stiren ve polistren plastiklerinin ürünüdür. Ayrıca Naylon üretiminde önemli olan sikloheksan olarak bilinen bir moleküle dönüştürülür. Siklohekzan üretmek için benzenin yaklaşık% 15'i kullanılır. Böcek ilaçlarından kauçuğa kadar her şeyde daha küçük miktarlar kullanılır.
Benzen yapısı iki şekilde çizilebilir. İlkinde, çift bağ karakteri açıkça çizilir. Kısa elli versiyonda, yapıyı göstermek için halkanın içine bir daire çizilir. Benzen içindeki her bir karbon atomuna bağlı tek bir hidrojen vardır.
Aşağıdaki I. ve II. çizimleri eştir. Pratikte III. çizim kullanılır.
Benzen, renksiz, alevlenebilen, kaynama noktası 80,1 °C, erime noktası 5,5 °C olan bir sıvıdır.
Binükleer Aromatik Hidrokarbonlar: Molekülünde iki benzen halkası içeren bileşiklerdir.
Hakkında
Kyäni, faydalı bileşenlerden oluşan besin takviyesi ürünlerini; benzersiz iş fırsatıyla birlikte dünya çapında 50'den fazla ülkeye ulaştırmaktadır. İdeal sağlığımızı korumak için günlük olarak Kyäni ürünlerini kullanırız, bu ürünleri başkalarıyla paylaşırız, işimizi inşa etmek ve sürdürmek için neredeyse her gün belirli bir saatimizi işe adarız ve başkalarını da Kyäni fırsatına dahil ederek veya Potato Pak ve Caring Hands programlarına katkı sağlayarak başarımızı başkalarıyla paylaşırız.
Hakkında
Kyäni, faydalı bileşenlerden oluşan besin takviyesi ürünlerini; benzersiz iş fırsatıyla birlikte dünya çapında 50'den fazla ülkeye ulaştırmaktadır. İdeal sağlığımızı korumak için günlük olarak Kyäni ürünlerini kullanırız, bu ürünleri başkalarıyla paylaşırız, işimizi inşa etmek ve sürdürmek için neredeyse her gün belirli bir saatimizi işe adarız ve başkalarını da Kyäni fırsatına dahil ederek veya Potato Pak ve Caring Hands programlarına katkı sağlayarak başarımızı başkalarıyla paylaşırız.
Sayfa Yapım Aşamasındadır.
Sayfa Yapım Aşamasındadır.
Schulungs- / Wissens- / Lösungsplattform
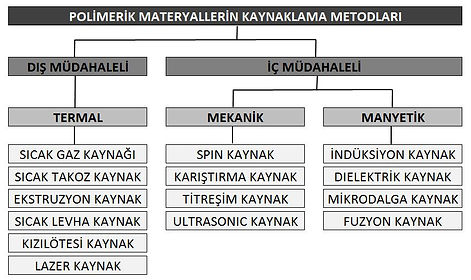
Schweißverfahren in Kunststoffen
Beim Kunststoffschweißen entsteht eine molekulare Bindung zwischen zwei kompatiblen Thermoplasten. Das Schweißen bietet überlegene Festigkeit und verkürzt die Zykluszeiten. Jedes Schweißen besteht aus drei Hauptschritten: Pressen, Heizen und Kühlen. Kunststoffschweißprozesse zeichnen sich vor allem durch ihre Heizmethode aus. Die Zulassungen für Kraftanwendung und Kühlung sind mechanische Überlegungen, die innerhalb der allgemeinen Behandlungskategorie von Maschine zu Maschine variieren können. Es ist zu beachten, dass zum Plastifizieren von Materialien in Hochtemperaturkunststoffen ein sehr hoher Energieeinsatz erforderlich ist. Die anzuwendende Schweißmethode hängt von folgenden Faktoren ab:
-
Teilegeometrie
-
Teilegröße
-
Art des Materials.
Beim Kunststoffschweißen werden Kunststoffmaterialien grundsätzlich mit denselben Metallen, jedoch mit unterschiedlichen Methoden kombiniert. Kunststoffschweißen wird, wie der Name schon sagt, aus Kunststoff hergestellt, aber; es kann nicht auf alle angewendet werden. Die Grundlogik besteht darin, dass das Material geschmolzen und kombiniert wird. Oder mit einem zusätzlichen Kunststoff werden die beiden anderen Hauptmaterialien kombiniert. Diese Schweißmethode kann nur auf thermoplastische Materialien angewendet werden. Diese Verbindungsmethode kann nicht auf duroplastische Materialien angewendet werden.
Der Hauptgrund, warum Kunststoffschweißen nicht auf duroplastische Materialien angewendet werden kann, besteht darin, dass diese Kunststofftypen, sobald sie geformt sind, unabhängig davon, wie stark sie erneut erhitzt werden, niemals schmelzen, sondern nur zu Kohle werden und unbrauchbar werden. Der Hauptgrund dafür ist, dass während thermoplastische Materialien Atombindungen aufweisen, während vernetzte Kunststoffe die Moleküle in duroplastischen Kunststoffen zusammenhalten. Somit sind diese Materialien sowohl steifer als auch einmal geformt, sie können nicht geschmolzen und wieder verwendet werden. Recycling ist also unmöglich.
In thermoplastischen Materialien gibt es andererseits Wan der Waals-Bindungen zwischen den Molekülketten. Diese Art von Bindungen ist weniger widerstandsfähig als Querbinder. Nach dem Formen können sie wiederholt geschmolzen und geformt und auf andere Weise verwendet werden. Recycling ist also möglich. Aufgrund dieser Eigenschaften sind sie umweltfreundlichere Materialien.
Um die beiden thermoplastischen Teile zu verbinden, müssen die Materialien chemisch verträglich sein. Andernfalls wird die molekulare Bindung nicht gebildet, selbst wenn beide Materialien zusammenschmelzen. Ein gutes Beispiel wäre der Versuch, Polyethylen mit Polypropylen zu verschweißen. Diese beiden teilkristallinen Materialien haben ein ähnliches Aussehen und viele gemeinsame physikalische Eigenschaften. Sie sind jedoch chemisch nicht verträglich und können daher nicht miteinander verschweißt werden. Sie schweißen sich wie Thermoplaste (dh Materialien mit den gleichen chemischen Eigenschaften). Beispielsweise wird ein ABS-Teil mit einem anderen ABS-Teil verschweißt. Unähnliche Thermoplaste können nur kompatibel sein, wenn ihre Schmelztemperatur innerhalb von 6 ° C liegt und sie eine ähnliche Molekülstruktur haben. Beispielsweise wird das ABS-Teil wahrscheinlich mit einem Acrylteil verschweißt, da seine chemischen Eigenschaften kompatibel sind. Im Allgemeinen werden wahrscheinlich nur ähnliche amorphe Polymere perfekt miteinander verschweißt. Die chemischen Eigenschaften eines teilkristallinen Materials machen jedes nur mit sich selbst kompatibel. Wenn die zu schweißenden Materialien kompatibel sind, können verschiedene andere Faktoren die Schweißbarkeit der Teile beeinflussen. Diese Faktoren umfassen Hygroskopizität, Formtrennmittel, Schmiermittel, Weichmacher, Füllstoffe, Flammschutzmittel, Nachschleifen, Pigmente und Harzklassen. Wenn die zu schweißenden Materialien kompatibel sind, können verschiedene andere Faktoren die Schweißbarkeit der Teile beeinflussen. Diese Faktoren umfassen Hygroskopizität, Formtrennmittel, Schmiermittel, Weichmacher, Füllstoffe, Flammschutzmittel, Nachschleifen, Pigmente und Harzklassen. Wenn die zu schweißenden Materialien kompatibel sind, können verschiedene andere Faktoren die Schweißbarkeit der Teile beeinflussen. Diese Faktoren umfassen Hygroskopizität, Formtrennmittel, Schmiermittel, Weichmacher, Füllstoffe, Flammschutzmittel, Mahlgut, Pigmente und Harzklassen.
In der Schweißnaht entwickelt sich in der Nähe der Schweißzone eine plastische Wärmebelastung aufgrund des Erhitzens, Schmelzens und Abkühlens der Schweißzone und nahegelegener unedler Metalle. Plastische Beanspruchung führt nach dem Schweißen zu einer dauerhaften Verformung der Schweißkonstruktion. Dies wird als ressourcenbedingte Verschlechterung bezeichnet. Schweißinduzierter Verformungsmodus kann als Spannung wie Biegen, Drehen oder Knicken und Verformung in der Ebene wie Verformung außerhalb der Ebene auftreten. Es ist sehr wichtig, dass der Kunststoffschweißprozess eine Schmelzschicht auf der fehlerhaften Oberfläche bildet, damit die intermolekulare Diffusion eine molekulare Bindung bilden kann. Im festen Zustand fließen die Polymerketten nicht. Daher muss die Verbindungsfläche in beiden Teilen geschmolzen werden, damit die Kunststoffmoleküle über die Grenzfläche diffundieren und sich mit den Molekülen des anderen Teils verbinden können. Je heißer die Schmelze ist, desto mehr molekulare Bewegung wird erreicht und die Schweißung kann in einer kürzeren Zykluszeit durchgeführt werden. Amorphe Polymere teilkristalline Polymere müssen über ihre Schmelztemperatur erhitzt werden.
Die Infrarotlaserquelle von überlappenden Thermoplasten verwendet eine Strahlungsdurchdringungserwärmung. Wenn die Schmelzzone an der Kontaktgrenzfläche erzeugt wird, werden die beiden Teile verbunden.
Beim konventionellen Infrarot-Laserschweißen von Kunststoffen konzentrierte er sich auf die sogenannte Transmission Infrared (TTIr) -Laserquelle. Diodenlaser sind als geeignete Laser für dieses Verfahren weit verbreitet. Es ist wichtig, zwei Materialien zu wählen; Das andere, das bestrahlt wird, ist hochpermeabel, während das andere für Laserlicht stark absorbierend ist. In den meisten Fällen von TTIr-Laserquellen sollte die Pigmentierung die Absorption von Strahlung im absorbierenden Teil erhöhen.
Heizplattenschweißen
Bei diesem Verfahren werden die gegenüberliegenden Oberflächen der beiden Teile durch Leitung, Konvektion und / oder Strahlung durch eine echte beheizte Platte erwärmt. Die beiden Teile werden entweder gegen die Heizplatte gedrückt oder eine Weile daneben gehalten, dann wird die Heizplatte entfernt und die Teile werden zusammengedrückt, um die Schweißnaht zu erzeugen. Das Heizplattenschweißen hat normalerweise Schweißzeiten zwischen 10 und 20 Sekunden.
Die beim Heizplattenschweißen verwendeten Parameter sind Heizplattentemperatur, Druck während des Abgleichs (oder der Verschiebung), Druck während des Erhitzens, Druck und Verschiebung während der Schweißphase sowie Abgleich-, Erwärmungs-, Austausch- und Abkühlzeiten. Diese Parameter wirken sich abhängig auf die Schweißqualität aus und können nicht einzeln eingestellt werden.
Die Heizplattentemperatur wird an der Oberfläche der Platte gemessen. Die Schmelztemperatur wird gemäß der Heizplattenschweißvariante mit den Eigenschaften des Materials einschließlich der Grenzwerte für die Schmelzviskosität und den thermischen Abbau eingestellt. Beim herkömmlichen Heizplattenschweißen werden Temperaturen von 30 bis 100 ° C über der Schmelztemperatur verwendet. Die Hochtemperaturvariante verwendet Temperaturen von etwa 100 bis 200 ° C über dem Schmelzpunkt, über der Zersetzungstemperatur des Materials. Die berührungslose Variante verwendet Temperaturen von 300 bis 400 ° C über ihrem Schmelzpunkt.
Heißgasschweißen
Diese Methode wird unter Verwendung eines zusätzlichen Materials hergestellt. Die Schweißstelle wird mit einer Heißluftpistole beheizt. Nach dem notwendigen Erhitzen wird der Spalt mit zusätzlichem Kunststoff gefüllt. Dies kann in wenigen Durchgängen erfolgen. Das hier verwendete heiße Gas kann Stickstoff sein. Der Hauptgrund dafür ist, zu verhindern, dass Kunststoffe bei hohen Temperaturen oxidieren. Oxidation findet nicht nur bei Metallen statt. Kunststoffe oxidieren ebenfalls und werden spröde.
Wenn die zu schweißenden Kunststoffteile zu hart sind, wird zusätzliches Material zwischen die zu verbindenden Materialien gelegt. Aber; Wenn der zu schweißende Kunststoff ein weicher Thermoplast ist, muss mit einer zusätzlichen Pressvorrichtung Druck auf die Schweißnaht ausgeübt werden.
Ein Heißgasbrenner wird verwendet, um heiße Luft sowohl auf die Verbindungsfläche als auch auf den Schweißstab zu leiten und die Materialien auf Erweichungstemperaturen zu erwärmen. Durch Ausüben von Druck auf die Verbindungsfläche auf den erhitzten Schweißstab werden die Materialien miteinander verbunden, um eine fertige Schweißnaht zu erzeugen. Diese Technik ist nicht einfach zu automatisieren und wird hauptsächlich für Reparaturen kleiner oder komplexer Komponenten oder für individuelle Produktionsanforderungen verwendet.
Beim Heißgasschweißen werden zwei gängige Schweißtechniken verwendet: Handschweißen und schnelles Schweißen.
Handschweißen ist eine Technik, bei der der Schweißstab vom Schweißer direkt auf die Verbindung aufgebracht wird. Der Heißgasbrenner wird mit einer Hand betätigt, um sowohl den Schweißstab als auch die Verbindungsflächen nacheinander zu pendeln. Der Druck wird auf den Schweißstab ausgeübt und ohne Hilfe einer Düse manuell gesteuert. Diese Technik ist für die meisten Konfigurationen geeignet und kann zum Schweißen in engen, engen Räumen oder bei komplexen Verbindungskonstruktionen nützlich sein, da die Anwendung des Schweißstabs nur auf zugängliche Schweißpositionen beschränkt ist.
Beim schnellen Schweißen wird eine speziell entwickelte Düse verwendet, die sicherstellt, dass der Heißgasbrenner und der Schweißstab ein zusammenhängendes System bilden. Die Düse erleichtert das Anbringen des Schweißstabs an der Verbindung über ein Zufuhrrohr. Die Düse erwärmt das Schweißstabmaterial gleichmäßig und ermöglicht eine kontrollierte Druckanwendung. Die Basis der Düse dient dazu, die Verbindungsfläche zu erwärmen und den Schweißstab in die Nut zu führen. Düsen werden hergestellt, um die Zuleitungen an bestimmte Schweißstabformen und -größen anzupassen, und sind für gängige Größen von runden oder dreieckigen Stäben erhältlich. Das schnelle Schweißen ist aufgrund der Größe der Düse und der Manövrierfähigkeit des Systems auf einfache Verbindungskonstruktions- und Verlegungsanwendungen beschränkt.
Gastemperatur, Auftragsdruck, Schweißvorschubrate, Gasdurchflussrate und Brennerorientierung beeinflussen die Integrität und die mechanischen Eigenschaften der fertigen Schweißnaht. Gastemperatur und Durchflussrate sind steuerbare Parameter, die auf Systemeingaben basieren. Der Anwendungsdruck, die Schweißgeschwindigkeit und die Brennerausrichtung hängen vom Bediener ab, der das Schweißen durchführt. Diese Parameter hängen miteinander zusammen und haben alle einen erheblichen Einfluss auf die endgültige Qualität der Schweißnaht.
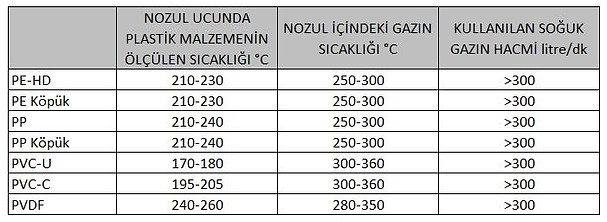
Extrusionsschweißen
Der größte Vorteil ist, dass die Auftragsmenge im Vergleich zum Heißgasschweißen etwa fünfmal schneller ist. Diese Anwendung dient zum Erreichen hoher Einzahlungsraten in einem einzigen Durchgang. Aufgrund der strengeren Kontrolle der Schweißparameter können viel stärkere Schweißnähte erhalten werden.
Der Hauptnachteil dieses Verfahrens besteht darin, dass es aufgrund der Größe der Maschine zu Schwierigkeiten bei der Anwendung kommen kann und es fast notwendig ist, von einem besser ausgebildeten Bediener angewendet zu werden.
Das Extrusionsschweißen wird zum Schweißen von dickwandigen Teilen verwendet. Der Schweißvorgang erfolgt mit einem Schweißstab. Extrusionsschweißgeräte sind kleine Extruder. Das extrudierte Material wird mit einer Schweißhülse gepresst. Der Schweißmantel besteht aufgrund seiner hohen Temperaturbeständigkeit im Allgemeinen aus Teflon. Der Schweißmantel sollte für die Schweißnaht geeignet sein. Die Arbeitsweise ist dem Heißluftschweißen sehr ähnlich. Das Ergebnis sind jedoch eine höhere mechanische Festigkeit, eine bessere Schweißqualität und eine geringere innere Spannung.
Bei diesem Schweißen wird ein Mini-Handextruder für Extrusionsarbeiten verwendet. Die Zylindertemperatur dieses verwendeten Extruders kann elektrisch mit spiralförmig gewickelten Drähten (klassische Methode) sowie einer anderen Zylinderheiztechnik gemessen werden. unter Verwendung des bereits erhitzten heißen Gases. Handextruder werden in der traditionellen Gerätetechnik, im Deponiebau, bei Kunststoffreparaturen und in vielen anderen Branchen eingesetzt. Sie sind überall dort von unschätzbarem Wert, wo Qualität und Leistung erforderlich sind.
Ein anderes Gewinde wird verwendet, um den Schweißstab an der Schraube zu ziehen. Dabei passiert es auch die Zuführhülse, wodurch ein Verbiegen der Stange verhindert wird. Sobald die Klinge eingesetzt ist, schneidet sie die Stange. Dies wird durch die geschraubte Spirale nach vorne gezogen, zusammengedrückt und durch Reibung im Zylinder (Trommel) erwärmt.
In der spiralförmig beheizten Version wird elektrische Energie verwendet, um die äußere Wärme innerhalb der Hülle zu erzeugen, die für den Plastifizierungsprozess erforderlich ist. Der Spiralwiderstand ist um die gesamte Extrudertrommel gewickelt und reguliert die Temperatur des Schmelzspaltes mit außerordentlicher Präzision. Der im Zylinderrohr angeordnete Temperaturfühler misst die Massentemperatur. Dadurch werden die Informationen an elektronische Geräte gesendet, die den gesamten Plastifizierungsprozess in einem geschlossenen Kreislauf steuern.
In der Heißluftversion dringt Wärme von außen in die Extrusionseinheit ein, wodurch der Plastifizierungsprozess eingeleitet und die Fortsetzung während des Betriebs unterstützt wird. Die externe Wärme wird vom Heißgasgerät in Form von Heißluft erzeugt, die dann in der Vorheizkammer um die Heißgaskanäle und die Extrusionseinheit strömt. Reibungswärme wird auch durch Kompression und Reibung erzeugt. Dies bewirkt, dass das Schweißzusatzmetall plastifiziert und sich zu einer homogenen Masse vermischt.
Letztendlich tritt das Extrudat dann aus der Düse aus und kriecht auf die zuvor mit heißem Gas erweichte Oberfläche.

Laserquelle
Es handelt sich um eine berührungslose Verbindungsmethode, bei der ein Laserstrahl verwendet wird, um Kunststoff im Verbindungsbereich zu schmelzen, indem eine kontrollierte Energiemenge an einen genauen Ort übertragen wird. Die Präzision bei der Steuerung des Wärmeeintrags basiert auf der einfachen Einstellung der Laserstrahlgröße und den verfügbaren Methoden zur Positionierung des Strahls. Die meisten Thermoplaste können mit einer geeigneten Laserquelle und einem geeigneten Verbindungsdesign geschweißt werden.
Das Laserschweißen von Kunststoffteilen hat sich als robuster, flexibler und präziser Fügeprozess erwiesen. Es bietet eine hocheffiziente und flexible Montage von der Herstellung von Kleinteilen mit komplexen Geometrien bis zur Massenproduktion in der Industrie, die problemlos in Automatisierungslinien integriert werden kann. Dieser Prozess verwendet einen Laserstrahl, um Kunststoff im Verbindungsbereich zu schmelzen, indem eine kontrollierte Energiemenge an einen genauen Ort übertragen wird. Diese Präzision bei der Steuerung des Wärmeeintrags basiert auf der einfachen Einstellung der Strahlgröße und den verfügbaren Methoden zur präzisen Positionierung und Bewegung des Strahls.
Das Verfahren basiert auf der gleichen Kompatibilität des Grundmaterials wie andere Kunststoffschweißtechniken, es wird jedoch häufig festgestellt, dass es die Unterschiede in der Harzchemie und der Schmelztemperatur besser verzeiht als die meisten anderen Kunststoffschweißverfahren. Fast alle Thermoplaste können mit einer geeigneten Laserquelle und einem geeigneten Verbindungsdesign geschweißt werden.
Es gibt drei Haupttypen von Lasern, die im Handel erhältlich sind, um qualitativ hochwertige Verbindungen in thermoplastischen Bauteilen herzustellen.
CO2-Laser:
Es ist ein etabliertes Materialhandhabungswerkzeug, das jetzt mit einer Leistung von bis zu 60 kW erhältlich ist und am häufigsten zum Schneiden von Metall, Kunststoff und Keramik verwendet wird. CO2-Laserstrahlung (Wellenlänge 10,6 μm) wird schnell von den Kunststoffoberflächenschichten absorbiert. Die Absorption bei diesen Photonenenergien (0,12 eV) basiert auf der Schwingung molekularer Bindungen. Kunststoffe werden aufgrund der laserinduzierenden Resonanzfrequenz in Molekülen heiß. Daher ist eine sehr schnelle Verarbeitung von dünnem Kunststofffilm (<0,2 mm) möglich (Hochgeschwindigkeitsschweißen von bis zu 500 m / min wurde nachgewiesen).
Zwei Polyethylenfolien können mit 100 m / min lasergeschweißt werden. Der CO2-Laserstrahl kann nicht unter einer Silica-Faseroptik übertragen werden, sondern kann in einem komplexen Prozess unter Verwendung von Spiegeln und Portalen oder Roboterbewegungen angewendet werden.
Nd: YAG Laser:
Es ist auch gut für die Materialbearbeitung geeignet und die jüngsten Fortschritte können zu einer Erhöhung der verfügbaren Leistung auf bis zu 6 kW und einer Verringerung der Lasergröße führen.
Der Grad der Energieabsorption bei der Nd: YAG-Laserwellenlänge (1,064 um, 1,2 eV Photonenenergie) hängt weitgehend von der Anwesenheit von Additiven in Kunststoffen ab. Wenn kein Füllstoff oder Pigment vorhanden ist, kann der Laser einige Millimeter in das Material eindringen. Der Absorptionskoeffizient kann durch Additive wie Pigmente oder Füllstoffe erhöht werden, die diese Photonenenergie direkt absorbieren und Strahlung für eine effizientere Massenabsorption nachhallen oder streuen.
Quellen können durch Positionieren von Infrarotabsorbern zur Erzeugung von Wärme an einer Verbindungsschnittstelle hergestellt werden. Dieser Prozess wird üblicherweise als "Transmissionslaserschweißen" bezeichnet, da die Laserenergie durch einen Teil des Kunststoffs auf die Verbindungsstelle übertragen wird.
Der Nd: YAG-Laserstrahl kann durch eine Silica-Glasfaser nach unten übertragen werden, was eine einfache und flexible Bedienung ermöglicht.
Diodenlaser:
Verfügbar seit Anfang 1997. Es ist kostengünstiger als CO2- und Nd: YAG-Laser. Typischerweise emittieren Diodenlaser Strahlung mit einer Wellenlänge von 0,8 bis 0,95 um.
Daher ist die Wechselwirkung mit Kunststoffen dem Nd: YAG-Laser sehr ähnlich und seine Anwendungen überlappen sich.
Der Strahl eines Diodenlasers ist normalerweise rechteckig, und obwohl dies für einige Anwendungen bevorzugt wird, begrenzt er die minimale Punktgröße und die maximal verfügbare Leistungsdichte. Die Diodenlaserquelle ist klein und leicht genug, um für komplexe Operationen auf einem Skid oder Roboter montiert zu werden.
Nd: YAG- und Diodenlaser können zum Durchführen von Transmissionslaserschweißen verwendet werden, vorausgesetzt, einer der Kunststoffe passiert den Laser und der andere absorbiert ihn. Das Verfahren bietet ein Mittel, mit dem Kunststoffteile mit unterschiedlichen Absorptionseigenschaften ohne Schmelzblitz, ohne Streifenbildung an den Außenflächen und nur mit einer kleinen Wärmeeinflusszone geschweißt werden können.
Transmissionslaserschweißen (TTLW):
Die Teile sind vormontiert und verriegelt, um einen engen Kontakt zwischen den Passflächen zu gewährleisten. Der Laserstrahl wird durch den oberen "transparenten" Teil zur Teileschnittstelle übertragen und vom unteren absorbierenden Teil absorbiert, der IR-Energie in Wärme umwandelt. Die Wärme wird vom unteren absorbierenden Teil zum oberen Teil geleitet und ermöglicht es der Schmelze, sich über die Grenzfläche zu bewegen und eine Bindung zu bilden. Eine genaue Positionierung und Klemmung der Baugruppe ist wichtig, da für die Wärmeübertragung zwischen den Teilen ein enger Kontakt erforderlich ist. Ruß und speziell entwickelte Absorber werden in das Harz eingemischt oder auf die Oberfläche aufgetragen, um IR-Strahlung am Boden der Baugruppe zu absorbieren. Die TTLW-Schweißtechnik ist abhängig von der Anwesenheit eines absorbierenden Materials in der Unterkomponente, was die Durchführbarkeit des Prozesses einschränkt, wenn für die Herstellung von medizinischen Geräten, elektronischen Geräten und bestimmten Verbrauchern eine "transparente" oder "farbtransparente" Baugruppe erforderlich ist Waren. Ingenieure haben diese Hürde erfolgreich überwunden, indem sie einen kürzlich entwickelten 2-Mikron-Laser integriert haben, der von klaren Polymeren leicht absorbiert wird und dank der Dicke optisch klarer Partikel ein hochkontrolliertes Schmelzen ermöglicht. Dies verbessert und vereinfacht das Laserschweißen von transparenten Polymeren für die Medizintechnikindustrie erheblich und ermöglicht dank der Dicke der optisch klaren Teile, die von den klaren Polymeren leicht absorbiert werden, ein stark kontrolliertes Schmelzen. Dies verbessert und vereinfacht das Laserschweißen von transparenten Polymeren für die Medizintechnikindustrie erheblich und ermöglicht dank der Dicke der optisch klaren Teile, die von den klaren Polymeren leicht absorbiert werden, ein stark kontrolliertes Schmelzen. Dies verbessert und vereinfacht das Laserschweißen von transparenten Polymeren für die Medizintechnikindustrie erheblich.
Konturschweißen:
Insbesondere kreisförmige Teile, wobei der Laserstrahl durch das Gold wirbelt und Geschwindigkeiten von bis zu 25 m / min erreicht. In der Zwischenzeit wird der Laserstrahl über die zu schweißende Kontur geleitet und die Kontur erwärmt. Große dreidimensionale Bauteile sowie runde Teile eignen sich für das Konturschweißverfahren. Das größte Problem bei diesem Verfahren besteht darin, dass bei Bauteilen mit Übervolumen Spannungen auftreten können, da die Konturen der geschweißten Teile nicht gleichzeitig erwärmt werden können.
Gleichzeitige Quelle :
Der Laserstrahl wird optimal auf das Bauteil abgestimmt erzeugt. Somit wird die zu schweißende Kontur gleichzeitig erwärmt. Das Ergebnis: sehr kurze Prozesszeiten von ca. 100 ms. Die Verwendung dieser Methode eignet sich hervorragend für Komponenten, die nicht sehr komplex sind und in großen Stückzahlen hergestellt werden sollen. Wenn sich jedoch die Bauteilgeometrie ändert, muss auch die Trägerform entsprechend geändert werden.
Semisimultanes Schweißen:
Ein Scanner erwärmt die Quellkontur eines Laserstrahls. Da sich der Laserstrahl mit einer Geschwindigkeit von bis zu 15 m / s (900 m / min) fortbewegt, ist er im Vergleich zum Abkühlvorgang so schnell, dass die Kontur fast gleichzeitig erwärmt wird. Dank des programmierbaren Fokussiergeräts ist es möglich, sehr schnell auf sich ändernde Schweißkonturen zu reagieren, was einen deutlichen Vorteil gegenüber dem simultanen Schweißverfahren bietet.
Clearweld-Prozess
Das als "Clearweld" bekannte laserabsorbierende Additiv bietet völlige Unabhängigkeit von den Anforderungen des herkömmlichen durchlässigen Laserschweißverfahrens. Das flüssige Material wird auf die Schweißfläche aufgebracht, bevor die Verbindungspartner verbunden werden. Clearweld absorbiert die einfallende Laserstrahlung und sorgt für die gewünschte Kohäsionsbindung. Im Gegensatz zu anderen IR-absorbierenden Materialien wird Clearweld nach Bestrahlung vollständig klar und bietet ein farbunabhängiges Design im Verbindungsbereich.
Neben diesem neuen Vorteil bietet das Clearweld-System interessante neue Möglichkeiten für die geometrische Gestaltung von Fusionspartnern. Das Erstellen mehrschichtiger Verbindungen bei gleichzeitig hoher Verarbeitungsgeschwindigkeit ist auch mit einem einzigen Vorgang möglich.
Hybridlaser
Diese Technologie verwendet eine Kombination aus Infrarotstrahlung, die von herkömmlichen Halogenheizlampen und Laserlicht emittiert wird. Es wurde bereits nachgewiesen, dass dieses Konzept der doppelten Lichtintensität sowohl die Verarbeitungsgeschwindigkeit als auch die Fehlertoleranz erhöht.
Die Zielanwendungen der Hybridschweißtechnologie sind nicht nur strukturelle Kraftfahrzeugteile wie Kopf- und Rücklichter sowie Kunststoff-Motorteile, sondern auch Verbraucherprodukte und medizinische Anwendungen.

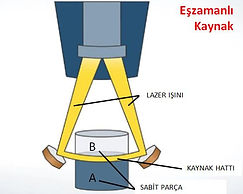

Ultraschallschweißen
Es ist das Fügen oder Reformieren von Thermoplasten unter Verwendung von Wärme, die durch hochfrequente mechanische Bewegung erzeugt wird. Dies wird durch Umwandlung von hochfrequenter (20-40 kHz) elektrischer Energie in hochfrequente mechanische Bewegung realisiert. Diese mechanische Wirkung erzeugt zusammen mit der ausgeübten Kraft Reibungswärme an den Verbindungsflächen (Verbindungsfläche) der Kunststoffkomponenten, wodurch das Kunststoffmaterial schmilzt und eine molekulare Bindung zwischen den Teilen herstellt.
Vibrationsquelle
Dieser Prozess funktioniert durch lineare oder orbitale Bewegung eines Teils relativ zu einem anderen. Dies verursacht Oberflächenreibung, die zur Wärmeerzeugung und zur Bildung einer Schmelzschicht in der Verbindung führt. Die Vibrationsquelle hat typischerweise Schweißzeiten von ein bis fünf Sekunden. Vibrationsschweißgeräte können Teile mit einem Durchmesser von ungefähr 50 mm bis zu einer Länge von 1800 mm bearbeiten.
Infrarot (IR) -Quelle
Ein weiteres berührungsloses Schweißverfahren ist das Infrarotschweißen, bei dem mithilfe von Strahlung Wärme auf Kunststoffteile übertragen wird. Es folgen die gleichen grundlegenden Schritte wie beim Heizplattenschweißen. Für das Infrarotschweißen haben sich zwei verschiedene Ansätze herausgebildet. Eines der Systeme verwendet in einigen Fällen eine elektrisch beheizte Metallplatte, die mit einer Keramik beschichtet ist. In dem anderen System wird die Standardheizplatte durch federbelastete Infrarotstrahler ersetzt, die auf beiden Seiten einer beweglichen Platte zusammengedrückt sind.
IR-Systeme können anstelle von heißen Oberflächen- und Vibrationsschweißverfahren in Kunststoff verwendet werden, wobei viele anspruchsvolle und große Teile zusammengefügt werden.
Beim Schweißen durch Erhitzen mittels heißer Oberflächen kann Kunststoff auf der Heizfläche haften bleiben. Der auf der Heizfläche angesammelte Kunststoff muss 2-3 mal pro Schicht gereinigt werden. Andernfalls wird der Kunststoff möglicherweise nicht auf die zu schweißende Temperatur gebracht, oder die Schweißflächen können rau werden. Da das Erhitzen ohne Kontakt mit dem Kunststoff beim IR-Schweißverfahren durchgeführt wird, entsteht kein Zeitverlust durch Reinigen oder Wechseln der Form. Darüber hinaus werden dank der schnellen Öffnungs- und Schließzeiten von IR-Systemen Energie- und Zeitverluste beim Vorheizen der Form vermieden.
IR-Systeme können zum Schweißen von Kunststoffbatterieteilteilen, zum Schweißen von Kraftstofftankkörpern für Kraftfahrzeuge, zum Verbinden von Kunststoffrohren, die in Infrastruktursystemen oder verschiedenen Einheiten verwendet werden, zum Schweißen von PVC-Fensterrahmen und zum Schmelzen von Kunststoffstiften zum Verbinden von Kunststoffteilen verwendet werden.
Zusammenfassend sind die Vorteile der IR-Schweißanwendung:
-
Schweißen komplexer 2D- und 3D-Teilegeometrien zum Verbinden verschiedener großer Kunststoffteile durch Erhitzen
-
Schweißen Sie die Teile des Kunststoff-Batteriegehäuses nicht
-
Schweißen von Kraftstofftankkarosserien für Kraftfahrzeuge
-
Kombinieren von Kunststoffrohren, die in Infrastruktursystemen oder verschiedenen Einheiten verwendet werden, durch Heizen
-
Schmelzende Kunststoffstifte zum Verbinden von Kunststoffteilen
-
Große Auswahl an akzeptablen Schweißmaterialien, Thermoplasten, Polyethylen, PVC, Polypropylen, Verbundkunststoffen, Polyamiden PC, PCABS.
-
Geringer Stromverbrauch
-
Schneller Temperaturanstieg
-
Elektrisch isolierte Umgebung mit geringem Leckstrom
-
Wartungsarme technische Geräte
-
Berührungsloser Schweißprozess
-
Stärkere Schweißnähte, hermetische Abdichtung.
-
Fähigkeit, PP GF 30 mit verschiedenen Materialien wie TPE zu kombinieren
Bei diesem Verfahren wird Infrarotstrahlung verwendet, die vom thermoplastischen Material absorbiert und in Wärme umgewandelt wird. Dadurch wird die Rissfläche des Kunststoffteils geschmolzen und die Bauteile zusammengepresst. Dies ist eine schnelle, berührungslose, partikelfreie Schweißmethode.
Schleuderschweißen
Dieser Prozess funktioniert durch die Rotationsbewegung eines Teils relativ zu einem anderen. Dies verursacht Oberflächenreibung, die zur Wärmeerzeugung und zur Bildung einer Schmelzschicht in der Verbindung führt. Das Schleuderschweißen hat typischerweise Schweißzeiten von einer halben bis fünf Sekunden. Schleuderschweißgeräte können Teile mit einem Durchmesser von bis zu 12 mm mit Hochgeschwindigkeitsmotoren mit einem Durchmesser von bis zu 225 mm mit Hochdrehmomentmotoren bearbeiten. Der Schleuderschweißprozess besteht aus der Erzeugung von Wärme durch Rotationsreibung zum Schweißen von thermoplastischen Teilen mit kreisförmigen Verbindungen. Das Spinnschweißgerät übt eine axiale Kraft aus, während ein Teil gegen seine feste Matte gedreht wird. Die resultierende Reibung erzeugt Wärme, die Teile an der Grenzfläche zum Schmelzen bringt. Wenn die Drehung stoppt, kühlt das Material ab und verfestigt sich zu einer geschweißten Baugruppe. In Fällen, in denen Teile in einer bestimmten Weise relativ zueinander ausgerichtet sein müssen, stoppt der Schweißer die Drehung in einer präzisen Winkelrichtung.
Geeignete Materialien für das Schleuderschweißen sind im Allgemeinen dieselben wie diejenigen, die durch andere Reibschweißverfahren wie das Vibrationsschweißen verbunden werden können. Teilkristalline Thermoplaste lassen sich durch Schleuderschweißen leichter verbinden als Ultraschall. Durch die Verwendung kompatibler Polymere können durch Schleuderschweißen zuverlässige hermetische Dichtungen hergestellt werden.
Das Verbinden unterschiedlicher Polymere ist unter Verwendung des Schleuderschweißverfahrens möglich, obwohl dies im Allgemeinen Schweißverbindungen mit geringerer Festigkeit erzeugt. Durch die Konstruktion der Schweißverbindung mit Hinterschnitt fließt das Polymer mit der niedrigeren Schmelztemperatur in den Hinterschnitt und bildet eine mechanische Verbindung.
Materialfüllstoffe und Oberflächenverunreinigungen (z. B. Formtrennmittel) sind zwei Faktoren, die die Konsistenz und die Wiederholbarkeit der Schweißnähte beeinflussen. Das Schleuderschweißen ist gegenüber Verunreinigungen toleranter als das Ultraschallschweißen. Das Schleuderschweißen wird auch von hygroskopischen Polymeren weniger beeinflusst, erfordert jedoch möglicherweise eine spezielle Handhabung für kritische Anwendungen.
Zu den Vorteilen des Schleuderschweißprozesses zählen hochwertige dauerhafte Verbindungen, hermetische Dichtungen, geringere Gerätekosten im Vergleich zu anderen Prozessen, einfache Montage, energieeffizienter Betrieb, sofortige Verwendung, Erfassung anderer Teile, Fernfeldschweißfähigkeit und der Wegfall zusätzlicher Materialien wie Klebstoffe.

Alternatives Schweißverfahren für Duroplaste (F & E)
Schweißen der duroplastischen Oberfläche durch Thermoplastisierung:
Michel van Tooren in seiner Forschungs- und Entwicklungsarbeit zum Induktionsschweißen zum Verbinden von duroplastischen und thermoplastischen Verbundwerkstoffen; Thermoplast nur dort auf einen duroplastischen Verbund auftragen, wo er geschweißt werden sollte. Anwendung; Es wurde im Nanopartikelmaßstab als Kreuzpolymerisationspfropfung hergestellt. Das Ergebnis ist, thermoplastische Inseln zu erhalten, die in den duroplastischen Verbundstoff implantiert und chemisch mit diesem verbunden sind. Später wurden thermoplastische Inseln einem Schweißprozess unterzogen. Und mit dieser Studie wurde eine alternative Anwendung für Verbindungen in Form der Verklebung von thermoplastischen Oberflächen eröffnet, die nicht geschweißt oder durchstoßen und mit Befestigungselementen befestigt werden können.
F & E-Anwendungsgrundsätze:
PolyVinylButyral (PVB), ein teilkristallines, kostengünstiges thermoplastisches Polymer mit einer Schmelztemperatur von 150-170 ° C, hat von seiner hervorragenden Bindungs- und Filmbildungsfähigkeit und seiner Fähigkeit, an vielen Oberflächen zu haften, profitiert.
Unter Ausnutzung dieses charakteristischen Merkmals wurde PVB als Verbindungsschicht verwendet. In Form einer 14-lagigen Kohlefaserschicht wurde sie durch Aushärten bei 180 ° C auf die duroplastische Verbundoberfläche laminiert und eine makromechanische Verriegelung erreicht.
Die Bildung von Inseln, die die erste Schicht der duroplastischen PVB-Harzverbundoberfläche mit einer Dicke von 10 bis 200 Mikrometern teilweise durchdringen.
Schließlich wurde der Schluss gezogen, dass die PVB-Harzoberflächen infolge der gegenseitigen Induktionsschweiß- und Ultraschallschweißprozesse sehr stark miteinander verbunden (geschweißt) wurden. Eine Überlappungsscherfestigkeit von 25 MPa wurde erreicht, wie durch typische Kohlenstofffaser / Epoxid-Bindungen veranschaulicht.
